HSA SYSTEMS HS-2000 Parts list manual

SIMATIC HMI)
HSA
Huasheng Automation
____________________
HS-2000
Multi-channel pulse controller
Usage Guide
Version 01/2021

Safety technology tips
For your personal safety and to avoid damage to your property, you must pay attention to the tips in this manual.
Tips for personal safety are indicated by a warning triangle, while tips related to property damage only are
without a warning triangle. The warnings are indicated from highest to lowest hazard level as follows:
Danger
Indicates that death or serious personal injury will result if appropriate care is not taken.
Danger
Indicates that death or serious personal injury may result if appropriate care is not taken.
Beware
With a warning triangle, indicating that minor personal injury may result if appropriate care is not taken.
Beware
Does not carry a warning triangle, indicating that property damage may result if appropriate care is not
taken.
Attention
Indicates that an undesired result or state may occur if the corresponding alert is not heeded.
When multiple hazard levels are present, always use the highest level warning prompt each time. If a
warning prompt is accompanied by a warning triangle warning of possible personal injury, there may be
an additional warning of possible property damage attached to that warning prompt.

Qualified Professional
Installation and driving of ancillary equipment or systems related to this document is only permitted.
Commissioning and operation of equipment or systems is only permitted to be performed by qualified
professionals. Qualified professionals for the purposes of the safety technical tips in this document are
persons qualified to perform the operation, grounding and marking of equipment, systems and circuits in
accordance with the safety technical standards.
Use as required
Please note the following instructions:
Danger
The equipment is permitted to be used only under the conditions of use specified in the catalog and
technical description. The proper and safe operation of the equipment must depend on proper
transportation, proper storage, placement and installation as well as careful operation and maintenance.

Preface
Purpose of this manual
This manual provides the information and documentation required for the construction
of machines according to DIN 8418. This information contained relates to equipment,
installation location, transport, storage, use and maintenance.
This brochure is aimed at the following target groups:
• Users
• Debuggers
• Service Technicians
• Maintenance Engineers
Please read the section "Security and General Information" carefully.
Basic knowledge required
General knowledge of industrial and mining electrical installations, automation
technology and process communications is necessary to better understand this
manual.It is assumed that the user already has a good knowledge of the basic use of
electrical and communications.
Use of manual
This manual applies to the 16-channel AC and DC versions of the HS-2000 multi-
channel pulse controller, the 220AC input version (order number: 6HSA-2000-220/24-
16) and the 24VDC input version (order number: 6HSA-2000-24/24-16), as well as the
12-channel AC and DC versions, the 220AC input version (order number: 6HSA-2000-
220/24-12) and the 24VDC input version (order number: 6HSA-2000-24/24-12)
Disclaimers
We have checked that the contents of this manual match the
hardware and software as described. Since errors are difficult to
avoid completely, we cannot guarantee exact agreement. We
will frequently check the data in the manual and make necessary
corrections in subsequent editions. We welcome your comments.
Technical data is subject to change without prior notice
HS-2000 multi-channel pulse controller
Operating instructions, version 01/2021

Catalog
1 Overview........................................................................................................................................................ 1-1
2 Shipping....................................................................................................................................................... ..2-1
3 Installation..................................................................................................................................................... 3-1
4 Electrical connections.................................................................................................................................4-1
5 Communication function description.................................................................................................. 5-1
6 Parameter setting....................................................................................................................................... 6-1
7 Structural and Electrical Specifications .............................................................................................. 7-1
A Appendix........................................................................................................................................................A-1

Overview
1.1 Introduction
HS-2000 controller is the main control device for bag type pulse dust collector, according to
the set parameters, output pulse signal, control the pneumatic valve or solenoid valve, and then
control the compressed air to blow dust on the filter bag, in order to ensure the dust collector
processing capacity and dust collection efficiency. Bag dust collector cleaning principle: With the
extension of filtration time, the dust layer on the filter bag accumulates thicker and thicker, the
resistance of dust collector equipment rises continuously, when the equipment resistance rises to
the set value, the dust cleaning device starts to clean the dust. First, a chamber lift valve is closed to
cut off the filter airflow, then the electromagnetic pulse valve is opened and the compressed air is
rapidly expanded in the upper box in a very short time and pours into the filter bag, which makes
the bag expand and deform and vibrate, and the dust attached to the outer surface of the filter bag
is stripped and falls into the dust hopper under the action of reverse airflow. After the dust cleaning
is completed, the electromagnetic pulse valve closes, the lift valve opens, the room and restore the
filtration state. Ash cleaning of each chamber in turn, from the first chamber to the start of the next
ash cleaning for an ash cleaning.
HS-2000 controller is widely used in dust removal and ash cleaning system in kiln, cement vertical
kiln, mining, pharmaceutical, food and other industries. And other applications using multi-point cycle
control system.
1、Power Indicator Light
2、Power plug
3、Communication and
enablement interface
4、24V common terminal
5、Q1-Q12 output quick
connect terminals
6、Q1-Q12 output indications
7、Q13-Q16 output terminal
and 24V common terminal
(version 1.0 without this
terminal)
8、Q13-Q16 output indications
9、Rotary button for setup
10、LCD display

1.2 The working principle and parameters of the instrument
Pulse width:Duration of each drive voltage;
Pulse interval: the interval time between the output two adjacent drive voltages;
Pulse lifting interval: the time to wait for the completion of the action of the poppet valve (lifting interval),
and also the time to wait for the poppet valve to close after the output of the pulse valve in the same chamber;
Number of group pulses: the number of pulse valves in a unit chamber;
Number of poppet valves: the number of poppet valves, i.e. the
number of groups or cell chambers;
Room interval: the time between the actions of two adjacent unit
rooms;
Cycle interval: the interval between the completion of dust removal in all cells and the next dust
removal cycle;
Shipping and Storage
Transport and storage in dry, hot and cold environments: -40 °C to +70 °C
Humid environment transportation and storage temperature: 25 ℃ to 55 ℃, 95% humidity

Installation
The HS-2000 multi-channel pulse controller is designed for easy installation. The HS-2000 can be
mounted on a panel or standard rail, and the HS-2000 can be mounted horizontally or vertically.
the small size of the HS-2000 allows users to make efficient use of space.
The electrical equipment standard classifies the HS-2000 system as open equipment. The HS-
2000 must be installed in an enclosure, control cabinet, or electrical control room. Only
authorized personnel may open the enclosure, control cabinet, or access the electrical control
room.
A dry environment should be provided for the HS-2000 during installation.
The installation should provide approved mechanical strength, flammability protection, and
stability protection for open equipment in specific location categories in accordance with
applicable electrical and building codes.
Conductive contamination due to dust, humidity and atmospheric pollution can cause
operational and electrical failures in the HS-2000.
If the HS-2000 is placed in an area where conductive contamination may be present, the HS-
2000 must be protected by an enclosure with the appropriate level of protection. IP54 is a
protection level commonly used for electrical equipment enclosures in dirty environments and
may be suitable for your application environment.
Warning
Improper installation of the HS-2000 can result in electrical failure or unexpected
mechanical operation.
Electrical failure or accidental mechanical operation may result in death, serious injury to persons
and/or property damage.
All installation and maintenance instructions for the proper operating
environment must be followed to ensure safe operation of the equipment.
Insulates the HS-2000 from thermal radiation, high voltage and electrical noise
As a basic rule for arranging various equipment in the system, equipment that generates high
voltage and high electrical noise must be isolated from low voltage logic type equipment such as
HS-2000.
在When configuring the layout of the HS-2000 on the panel, please consider heat generating
devices and locate electronic type devices in cooler areas of the control cabinet. Less exposure to
high temperatures will extend the life of all electronic equipment.

Also consider the wiring of equipment in the panel. Avoid laying low voltage signal and
communication cables in slots with AC power lines and high energy fast switching DC lines.
Allow enough clearance for cooling and wiring
The HS-2000 is designed to be cooled by natural convection. To ensure proper cooling, a
clearance of at least 25 mm must be left above and below the unit. In addition, a minimum
depth of 25 mm should be left between the front of the module and the inner wall of the cabinet.
Beware
For longitudinal installations, the maximum allowable ambient temperature will be reduced
by 10°C.
Please adjust the orientation of the vertically mounted HS-2000 system as shown in the figure
below.
Ensure proper installation of the HS-2000 system.
When planning the layout of the HS-2000 system, sufficient clearance should be left to facilitate
wiring and communication cable connections.

Electrical connection
4.1Wiring Diagram
The operation enable terminal can be connected to a differential pressure sensor for
automatic differential pressure control of ash cleaning. If the sensor is not used, the enable terminal
can be shorted or the operation can be controlled by other dry contact.
The function of each point varies depending on the configuration of the parameters:
Take 10-way as an example: Now the configuration is 2 cells, each cell has 5 pulse valves. The
parameters: number of poppet valves = 2, number of group pulses = 5, and the wiring diagram is as
follows:
When the number of valves exceeds the number supported by one unit, multiple controllers
can be cascaded by means of communication, up to 1024 valves. Wiring method of communication:
Use 1mm2 x2 shielded twisted pair cable to connect A+ of host to A+ of extension and B- of host to
B- of extension. The total length of the communication line does not exceed 5 meters.

Beware
Since the controller comes with its own power supply, the common terminals of multiple controllers cannot
be connected together. The output of each control can only form a loop with its own common terminal,
otherwise the power supply may be damaged. For example, as shown in the diagram above, the common of 1-16
must be connected to the host, common 2 of 17-32 to expansion #1, common 3 of 33-48 to expansion #2, and
so on.

Function Description
5.1 This machine provides 2 communication modes: cascade communication and RS485 slave
communication mode.
Cascade communication is suitable for self-assembling several pulse controllers into a network
to achieve a large number of outputs without a host computer software or PLC. The wiring diagram
for cascade communication is described in Section 3 above: One of the addresses is set to "0" for the
master, and the other extensions set the address of the cascade separately. The modules on the
cascade only use the settings on the master, the settings on the slave are invalid.
In cascade communication mode:
If [Enable] is disconnected or the host is stopped while the host is operating, the output stops and "-
---" is displayed. The operation indicator lights up to represent the corresponding state that it is currently
in.
The extension only displays its own extension address, e.g. "16" means that this machine is the
extension and starts from point 16#; if "Exxxx" is displayed, it means that the extension has a control
fault and the host will also fault alarm and indicate the starting channel address of the failed slave.
Fault descriptions as follows, see 5.2 Alarm list;
RS485 slave communication mode is suitable for networking with a host computer or PLC that
supports Modbus RTU protocol. The address setting "1" means that the RS485 slave address is set to 1. The
communication parameters are baud rate 9600bps, 8 data bits, and no parity.
RS485 communication protocol: Address 0-31 is the read-only status register, and address 32 is
the control command register.
Address
Description
1
Working mode
4
Pulse width. Unit: 10ms.
5
Pulse interval. Unit: s.
6
Lifting pulse interval. Unit: 10ms.
7
Ventricular septum. Units: s.
8
Cycle interval. Unit: minutes
9
Number of output paths.

10
Number of poppet valves.
11
The number of group pulses.
16
Current operating status.
17
The current number of output channels. Start from 0.
18
Current room number. Start from 0.
19
The number of output channels in the current room. Start from 0.
20,21
Countdown counter in ms
32
Control instruction (hexadecimal). This control instruction is in an "or" relationship with the
external run control
relationship, i.e., the controller runs if one of the remote or local controls is true.
0x0100:Start running
0x0200:Stop operation
0xFAFA:Save parameter note
Addresses 62-74 are write status registers.
No
Modus
Address
Parameters
Definition
Unit
Scope
LVZ
Factory
default
1
62
MdAdd
Modus Node Address
Unit
1~254
1
1
2
63
CmTyp
Type of communication
1:485 Slave
2: Cascade
3:Stand-alone
1
3
3
64
ExAdd
Extended Address
0~9999
1
0
4
65
RmInv
Ventricular septum
s
1~9999
1
4
5
66
PlWdh
Pulse width
s
0.01~99.99
0.01
1
6
67
PlInv
Pulse interval
s
1~9999
1
2
7
68
LfInv
Lifting pulse interval
s
0.01~99.99
0.01
1
8
69
CyInv
Cycle interval
min
1~9999
1
6

9
70
LfNum
Number of poppet
valves
0~512
1
0
10
71
OpNum
Total number of output
channels (cascade)
1~9999
1
12
11
72
GpNum
Number of group pulses
1~20
1
3
12
73
ChNum
Number of output
channels of this module
1~16
1
12
13
74
StVlv
Point output
1~16
1
1
14
96
FltRst
Error clearing
15
97
Restore
Factory parameter reset
16
98
Quit
Quit (without saving
changes)
17
99
Save
Exit (save changes)
Note 1: Explanation of "Tap Output" command:
Theuniquepoint-actionoutputfunctionofthismachinecaneffectivelyhelpthecommissioningpersonneltoset
eachchannelindividuallyduringthecommissioningoffieldequipment.Thecommissioningpersonnelcanenterthe
parametersettinginterfacetoselectthechanneltobeoutputthroughparameterNo.74,andthenpressandholdthe
settingbutton,thecorrespondingchannelcanbeoutput;notethatthisfunctionwillbedisabledimmediatelyafterthe
moduleenableisactivated;
Note 2: Explanation of "Error Clear" command:
Whenthemoduleoutputchanneloverloadorshortcircuit,theoutputshortcircuitalarmwillshow"Cxxxx",andthe
alarmclearwillshowthecorresponding"xxxx"value,"xxxx"doublebytebit0~bit15correspondtothe16channelsofthe
module,bit0correspondstochannel1,bit1correspondstochannel2......bit15 correspondstochannel16,whentheshort
circuitfaultofthereportedchannelisremoved,manuallyshortpressthesetbuttoninthisparameterinterface,thealarm
valuewillbecome0again,andthealarmcleariscompleted.
Note 3: Instructions for using the "Save Parameters" command:
Addresses62-74areread-writeregistersthattakeeffectwhenanewvalueiswrittenand,aftersavingtheparameter,
the controller takes effect on the next action. (For example, if the pulse width is changed, the new parameter is applied at
the next pulse width if it is already currently being blown. After the change, 0xFAFA must be sent to address 32 for
parameters62-74tobesaved,otherwisetheparameterswillnottakeeffectandthenewlysetparameterswillbelostaftera
powerfailure.

Beware:Pleaseconfiguretheparametersbydisconnectingtheenable!!!
Whentheenableportison,theHS-2000willpowerupandthenoutputaccordingtothe"factorydefault"!
5.2 Alarm List
No
Alarm name
Description
Causes and Countermeasures
1
Cxxxx
Overcurrent exists in the
corresponding channel of the
module
Check output wiring for short
circuits
2
E0001
Communication data length error
1. 1. Check whether there is
interference in the
communication line
2. Check the communication
wiringCheck the communication
wiring
3
E0002
Communication data validation
error
1. Check whether there is
interference in the communication
line
2. Check the communication wiring
4
E0004
Communication timeout
1. Check whether there is
interference in the communication
line
2. Check the communication wiring
5
Exxxx
Cascade mode, when XXXX is
greater than or equal to the number
of channels of the main module
Cascade channel failure

Parameter Setting
6.1.Buttonactionfunctiondefinition:
Action
Longpress(>3seconds)
ontherotarybutton
Shortpresstherotarybutton
Clockwiserotation
Counterclockwise
rotation
Functions
Enter parameter
settingmode
Enter input mode
Shiftthecursorforward
Exit input mode
Ascending
selection
parameters
Add 1 cursor
positiondata
Descending
selection
parameters
Minus 1 cursor
positiondata
6.2.Setting method
6.2.1Modus Node Address:X X X
1) Long press the button and release it to enter the parameter setting interface, displaying
parameter No. 1 MdAdd;
2) Press the button briefly, the cursor appears in the single digit and flashes;
3) Rotate the button clockwise to adjust the larger number, and counterclockwise to adjust the
smaller number;
4) Short press the button, the cursor shifts to ten and flashes;
5) Rotate the button clockwise to adjust the larger number, and counterclockwise to adjust the
smaller number;
6) Adjust the hundreds digit by 4) and 5) method;
7) After all digits are adjusted, short press the button to exit the input mode, the cursor
disappears and the parameter setting is completed
6.2.2 Extended Addresses:X X X X
1) Press and hold the button button and release it to enter the parameter setting interface,
displaying parameter No. 1 MdAdd;
2) Turn the button one position clockwise to display parameter ExAdd #2;
3) Press the button briefly, the cursor appears in the 2nd decimal place and flashes;
4) Rotate the button clockwise to adjust the larger number, and counterclockwise to adjust the
smaller number;
5) Short press the button, the cursor shifts to the 1st decimal place and flashes;

6) Rotate the button clockwise to adjust the larger number, and counterclockwise to adjust the
smaller number;
7) Short press the button, the cursor shifts to the single digit and flashes;
8) Rotate the button clockwise to adjust the larger number, and counterclockwise to adjust the
smaller number;
9) Short press the button, the cursor shifts to ten and flashes;
10) Rotate the button clockwise to adjust the larger number, and counterclockwise to adjust the
smaller number;
11) After all digits are adjusted, short press the button to exit the input mode, the cursor
disappears and the parameter setting is completed
6.2.3 Communication Type X
Same as 6.2.2
6.2.4 Control Type X
Same as 6.2.2
6.2.5 Ventricular septum X X X X
Same as6.2.2
6.2.6 Pulse width X X . X X S
1) Long press the button and release it to enter the parameter setting interface, displaying
parameter No. 1 MdAdd;
2) Rotate the button 6 positions clockwise to display parameter PlWdh #6;
3) Press the button briefly, the cursor appears in the single digit and flashes;
4) Rotate the button clockwise to adjust the larger number, and counterclockwise to adjust the
smaller number;
5) Short press the button, the cursor shifts to ten and flashes;
6) Rotate the button clockwise to adjust the larger number, and counterclockwise to adjust the
smaller number;
7) Adjust the hundreds digit and thousands digit according to the method of 4) and 5);
8) After all digits are adjusted, short press the button to exit the input mode, the cursor
disappears and the parameter setting is completed.
6.2.7 Pulse interval X X X X

Same as 6.2.2
6.2.8 Lifting pulse interval X X . X X S
Same as 6.2.6
6.2.9 Cycle interval X X X X 0S
1) Long press the button and release it to enter the parameter setting interface, displaying
parameter No. 1 MdAdd;
2) Turn the button clockwise or counterclockwise until parameter CyInv #9 is displayed;
3) Short press the button, the cursor appears in the tens place and blinks;
4) Rotate the button clockwise to adjust the larger number, and counterclockwise to adjust the
smaller number;
5) Short press the button, the cursor shifts to the hundreds place and blinks;
6) Rotate the button clockwise to adjust the larger number, and counterclockwise to adjust the
smaller number;
7) Short press the button, the cursor shifts to the thousandth position and flashes;
8) Rotate the button clockwise to adjust the larger number, and counterclockwise to adjust the
smaller number;
9) Short press the button, the cursor shifts to the 10,000 position and flashes;
10) Rotate the button clockwise to adjust the larger number, and counterclockwise to adjust the
smaller number;
11) After all digits are adjusted, short press the button to exit the input mode, the cursor
disappears and the parameter setting is completed.
6.2.10 Number of poppet valves X X X
Same as 6.2.2
6.2.11 Number of output channels X X
Same as 6.2.2
6.2.12 Number of group pulses X X
Same as 6.2.2
6.2.13 Open valve number X X
Same as 6.2.2

6.3Communicationprotocols
Communication parameters are baud rate 9600bps; 8 data bits, no parity.
485 read register command: Function code 0x03
Address(1B)
Function code(1B)
Register Address(2B)
Number of read registers(2B)
CRC High Byte(1B)
CRC low byte(1B)
485 Read Register Response:Function code0x03
Address(1B)
Function code(1B)
Number of data bytes(B)
Data(2B/4B)
CRC High Byte(1B)
CRC low byte(1B)
Example: Read the number of online output channels:
Send:01 03 00 09 00 01 54 08
Back:01 03 02 00 10 B9 88
485 Write Register Command: Function code 0x06
Address(1B)
Function code(1B)
Register Address(2B)
Data to be written(2B)
CRC High Byte(1B)
CRC low byte(1B)
485 Write Register Response:Function code 0x06
Address(1B)
Function code(1B)
Register Address(2B)
Number of registers(2B)
CRC High Byte(1B)
CRC low byte(1B)
Example: Open valve #2 with address 1:
Send:01 06 00 4A 00 02 29 DD
Back:01 06 00 4A 00 01 69 DC

Structural and Electrical Specifications
7.1 Protection level
● IP20 mechanical protection, EN 60529
● Prevents finger contact with high voltage tested by standard probes. External
protection is required against dust, dirt, water and foreign objects less than 12.5 mm
in diameter.
7.2 Structure Diagram
7.3 General specifications and characteristics
Order number
Product Name
Voltage
Current
No. of
channels
Output
voltage
Output
current
6HSA-2000-220/24-16
HS-2000 multi-
channel pulse
110-240V AC
16
24V DC
0.75
6HSA-2000-220/24-12
110-240V AC
12
24V DC
0.75
Table of contents
Popular Controllers manuals by other brands
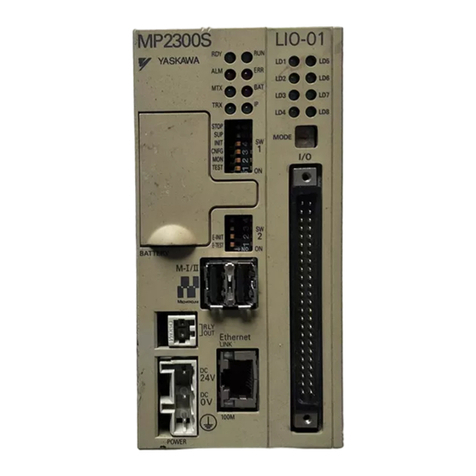
YASKAWA
YASKAWA MP2300S user manual

Circuitron
Circuitron TC-1 quick start guide
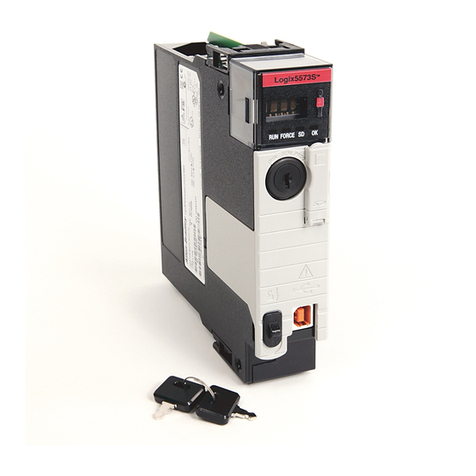
Allen-Bradley
Allen-Bradley 1756 GuardLogix Product information
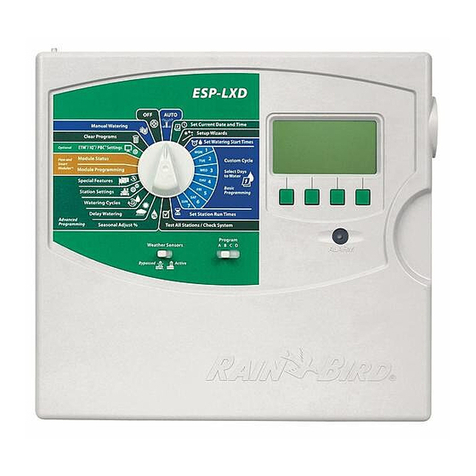
Rain Bird
Rain Bird ESP-LXD troubleshooting guide
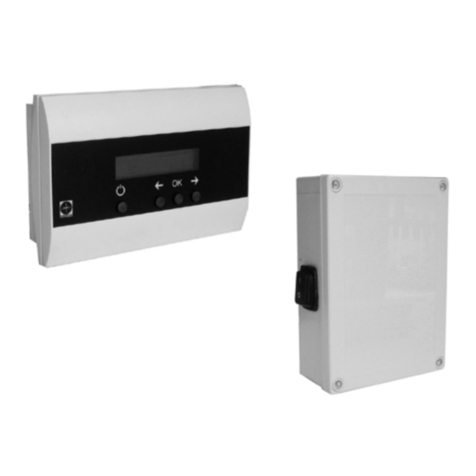
Exhausto
Exhausto EW 40 Installation & operating manual
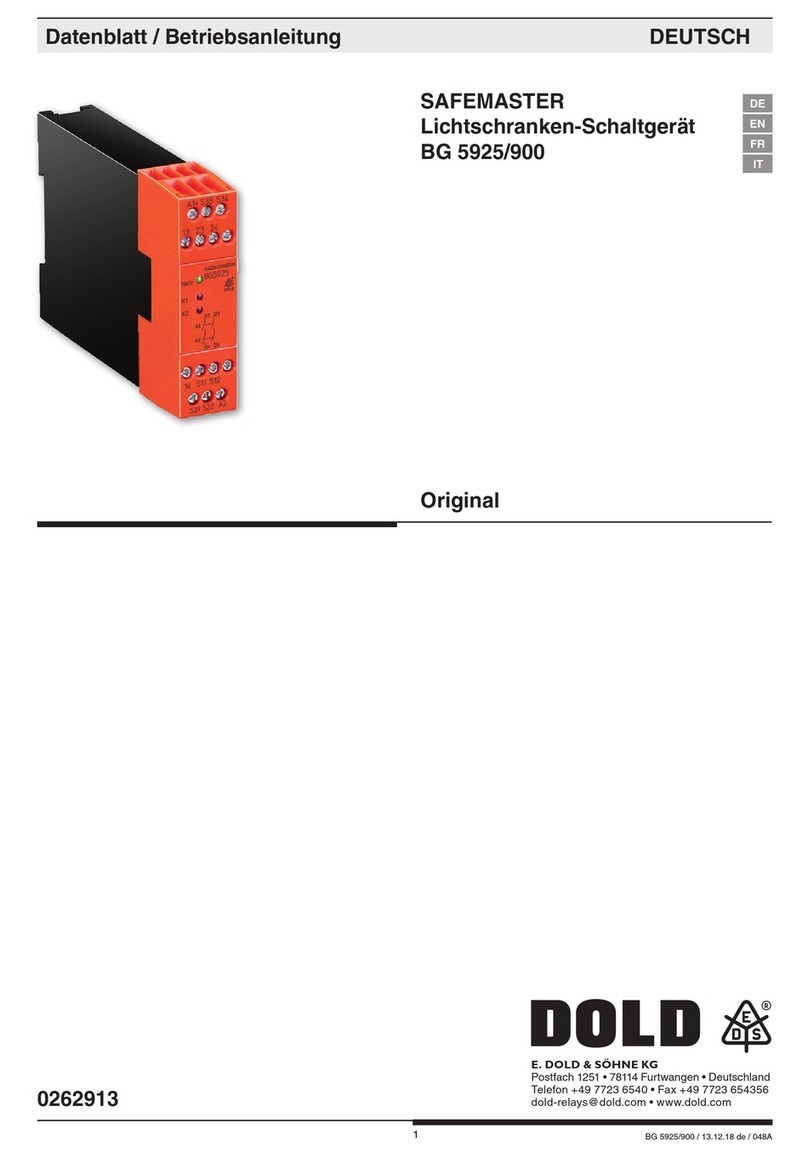
DOLD
DOLD SAFEMASTER BG 5925/900 Datasheet / Operating Instructions