Hunter DSP9200 Series User manual

OPERATION INSTRUCTIONS Form 5473-T, 01-10
Supersedes Form 5473-T, 09-08
DSP9200 Series
Wheel Balancer
© Copyright 2006 -2010 Hunter Engineering Company

OWNER INFORMATION
Model Number ____________________________________________________________________
Serial Number ____________________________________________________________________
Date Installed _____________________________________________________________________
Software Version Number ___________________________________________________________
Service and Parts Representative _____________________________________________________
Phone Number ____________________________________________________________________
Sales Representative _______________________________________________________________
Phone Number ____________________________________________________________________
Operation Trained Declined
Safety and Maintenance
Equipment Components
Basic Operation
Static vs. Dynamic Balancing
Calibration and Quick Calibration Check
Split Weight Feature
Adhesive Weight (ALU) Procedures
Optimizing Procedures
Patch Balance®Procedures
Inflation Station™/Wheel Lift
Split Spoke®
Servo-Aided Weight Placement
CenteringCheck™
Individuals and Date Trained
___________________________________ ___________________________________
___________________________________ ___________________________________
___________________________________ ___________________________________
___________________________________ ___________________________________
___________________________________ ___________________________________
___________________________________ ___________________________________
___________________________________ ___________________________________

CONTENTS
1. GETTING STARTED ........................................................................................ 1
1.1 Introduction............................................................................................................. 1
References............................................................................................................. 1
1.2 For Your Safety ...................................................................................................... 1
Hazard Definitions.................................................................................................. 1
IMPORTANT SAFETY INSTRUCTIONS............................................................... 2
Electrical................................................................................................................. 3
Decal Information and Placement.......................................................................... 4
Right Side View ............................................................................................... 4
Left Side View.................................................................................................. 5
Back View........................................................................................................ 6
Specific Precautions/Power Source....................................................................... 7
Turning Power ON/OFF ......................................................................................... 7
Equipment Installation and Service ....................................................................... 7
Equipment Specifications....................................................................................... 8
Safety Summary .................................................................................................... 8
Explanation of Symbols................................................................................... 8
1.3 DSP9200 Components........................................................................................... 9
Standard Accessories .......................................................................................... 10
1.4 Operating the Control Panel................................................................................. 11
Control Panel ....................................................................................................... 11
Using the Control Panel ....................................................................................... 11
Using Wheel Dimension Control Knobs............................................................... 12
2. BALANCING OVERVIEW .............................................................................. 13
2.1 Balancing Modes.................................................................................................. 13
Static Balance ...................................................................................................... 13
Dynamic Imbalance ............................................................................................. 14
Static and Dynamic Imbalance Sensitivity ........................................................... 15
2.2 Identifying the Static Balance Weight Plane ........................................................ 15
2.3 Identifying the Dynamic Balance Weight Planes.................................................. 16
2.4 On-Vehicle Wheel Mounting Methods.................................................................. 18
Hub Centric .......................................................................................................... 18
Lug Centric........................................................................................................... 18
3. BALANCING A WHEEL................................................................................. 19
3.1 Mount the Wheel on the Spindle Shaft................................................................. 19
Front/Back Cone Mounting .................................................................................. 20
Using Plastic Wheel Mounting Washer................................................................ 21
Cone/Flange Plate Mounting ............................................................................... 23
Using the Pressure Ring and Spacers................................................................. 24
Pressure Ring................................................................................................ 24
Spacers ......................................................................................................... 24
CenteringCheck®.................................................................................................. 25
3.2 Measuring the Wheel with Inner and Outer Auto Dataset®Arms......................... 26
Measuring Dimensions for Clip-On Weights: ................................................ 26
Mixed Weights and Two Adhesive Weights (Inputting Distance and Diameter for
Both Planes): ....................................................................................................... 27
3.3 Manually Setting Wheel Dimensions.................................................................... 28
Measuring the Wheel at the Inner Rim Lip (Clip-On Weight) .............................. 29
Measuring Wheel Width with Rim Width Calipers ............................................... 30
Measuring the Inside Wheel Surface with the Pointer Disk Edge (Adhesive Tape-
On Weights) ......................................................................................................... 30
DSP9200 Series Balancer Operation Instructions Contents
x
i

ii
x
Contents DSP9200 Series Balancer Operation Instructions
Measuring the Inside Wheel Diameters (For Adhesive Weights) ........................ 31
3.4 Locating the Wheel Weights at the Top Dead Center (“TDC”) and Bottom Dead
Center (“BDC”) ........................................................................................................... 32
3.5 Standard Balancing Procedure (Clip-on Weights) ............................................... 33
3.6 Static / Standard Balancing Procedure (Clip-on Weight) ..................................... 35
3.7 Adhesive Weight Procedures (Combination of Clip-on & Adhesive Weights, or
Two Adhesive)............................................................................................................ 36
3.8 Static / ALU Balancing Procedure (Adhesive Weight) ......................................... 41
3.9 OPT-1 Optimizing Tire & Wheel Imbalances (Wheel with the Tire Mounted
Procedure).................................................................................................................. 42
3.10 OPT-2 Optimizing Tire & Wheel Imbalances (Tire Not Mounted Procedure) .... 43
3.11 Patch Balance®Procedures ............................................................................... 44
Static Patch Balance®(Single Weighted Balance Patch) .................................... 44
Dynamic Patch Balance®(Two Weighted Balance Patches) .............................. 45
4. BALANCING FEATURES AND OPTIONS.................................................... 47
4.1 Servo-Stop............................................................................................................ 47
Servo-Stop Wheel Weight Positioning................................................................. 47
Disabling Servo-Stop..................................................................................... 47
Turning On Servo-Stop.................................................................................. 47
Servo-Stop Aided Clip-On Weight Placement ..................................................... 47
Servo-Stop Aided Adhesive Weight Placement................................................... 47
4.2 Locate the Adhesive Wheel Weights Using the Dataset£Arm Pointer Disk Edge48
Inside of Wheel (Single Row of Adhesive Weights)............................................. 48
Inside of Wheel (Double Row of Adhesive Weights) ........................................... 48
4.3 Quick-Thread™ Feature....................................................................................... 49
4.4 Motor Drive/Servo-Stop........................................................................................ 49
Servo-Stop/Servo-Push ....................................................................................... 49
4.5 Spindle-Lok®Feature ........................................................................................... 50
4.6 Hood Close Autostart Feature.............................................................................. 50
4.7 Loose Hub Detect Feature ................................................................................... 50
4.8 Blinding and Rounding ......................................................................................... 51
4.9 Split Weight®Feature ........................................................................................... 51
Split Weight®Operation ....................................................................................... 52
Correcting Large Imbalances............................................................................... 52
4.10 Split Spoke®Feature .......................................................................................... 53
Re-entering Similar Wheel after Split Spoke® is Enabled................................... 53
Placing Hidden Weight Forward of Obstructions ................................................. 54
4.11 Automatic Weight Recalculation and Dimension Preservation .......................... 55
4.12 Storing and Recalling Wheels ............................................................................ 55
Storing a Wheel into Memory............................................................................... 55
Recalling a Wheel from Memory.......................................................................... 55
5. MAINTENANCE AND CALIBRATION........................................................... 57
5.1 Cleaning the Unit .................................................................................................. 57
5.2 Spindle Hub Face and Shaft Maintenance........................................................... 57
5.3 Mounting Cone Maintenance ............................................................................... 57
5.4 Identifying Software Version and Serial Number ................................................. 57
5.5 Calibration Procedures......................................................................................... 58
Quick Cal Check .................................................................................................. 58
Balancer Calibration............................................................................................. 59
Inner Dataset®Arm (Calibration Tool, 221-672-1, Required) .............................. 60
Outer Dataset®Arm (Calibration Tool, 221-672-1, Required) ............................. 62
6. GLOSSARY ................................................................................................... 63

1. GETTING STARTED
1.1 Introduction
This manual provides operation instructions and information required to operate the
DSP9200 Wheel Balancer. Read and become familiar with the contents of this
manual prior to operating the DSP9200.
The owner of the DSP9200 is solely responsible for arranging technical training. The
DSP9200 is to be operated only by a qualified, trained technician. Maintaining
records of personnel trained is solely the responsibility of the owner and
management.
References
This manual assumes that you are already familiar with the basics of tire balancing.
The first section provides the basic information needed to operate the DSP9200. The
following sections contain detailed information about equipment operation and
procedures. “Italics” are used to refer to specific parts of this manual that provide
additional information or explanation. For example, Refer to “Equipment
Components,” page 9. These references should be read for additional information to
the instructions being presented.
1.2 For Your Safety
Hazard Definitions
Watch for these symbols:
CAUTION: Hazards or unsafe practices, which could result in minor
personal injury or product or property damage.
WARNING: Hazards or unsafe practices, which could result in
severe personal injury or death.
DANGER: Immediate hazards, which will result in severe personal
injury or death.
These symbols identify situations that could be detrimental to your safety and/or
cause equipment damage.
DSP9200 Series Balancer Operation Instructions 1. Getting Started
x
1

IMPORTANT SAFETY INSTRUCTIONS
Read all instructions before operating the DSP9200.
Do not operate equipment with a damaged cord or equipment that has been dropped
or damaged until a Hunter Service Representative has examined it.
Always unplug equipment from electrical outlet when not in use. Never use the cord
to pull the plug from the outlet. Grasp plug and pull to disconnect.
If an extension cord is necessary, a cord with a current rating equal to or more than
that of the equipment should be used. Cords rated for less current than the
equipment may overheat. Care should be taken to arrange the cord so that it will not
be tripped over or pulled.
Verify that the electrical supply circuit and the receptacle are properly grounded.
To reduce the risk of electrical shock, do not use on wet surfaces or expose to rain.
Never direct a hose stream at equipment when cleaning.
Verify the appropriate electrical supply circuit is the same voltage and amperage
ratings as marked on the balancer before operating.
WARNING: DO NOT ALTER THE ELECTRICAL PLUG. Plugging the
electrical plug into an unsuitable supply circuit will
damage the equipment and may result in personal
injury.
To reduce the risk of fire, do not operate equipment near open containers of
flammable liquids or sprays (gasoline, cleaners, fluids, etc.).
Read and follow all caution and warning labels affixed to your equipment and tools.
Misuse of this equipment can cause personal injury and shorten the life of the
balancer.
Keep all instructions permanently with the unit.
Keep all decals, labels, and notices clean and visible.
To prevent accidents and/or damage to the balancer, use only Hunter DSP9200
recommended accessories.
Use equipment only as described in this manual.
Never stand on the balancer.
Wear non-slip safety footwear when operating the balancer.
Keep hair, loose clothing, neckties, jewelry, fingers, and all parts of body away from
all moving parts.
Do not place any tools, weights, or other objects on the safety hood while operating
the balancer.
ALWAYS WEAR OSHA APPROVED SAFETY GLASSES. Eyeglasses that have only
impact resistant lenses are not safety glasses.
Keep the safety hood and its safety interlock system in good working order.
Verify that the wheel is mounted properly and that the wing nut is firmly tightened
before spinning the wheel.
Hood Autostart will cause the balancer shaft to spin automatically upon hood closure.
For the next Autostart, the safety hood has to be lifted to the full up position and then
closed.
Raise safety hood only after wheel has come to a complete stop. If safety hood is
raised before the spin is completed, the weight values will not be displayed.
Do not let cord hang over any edge or contact fan blades or hot manifolds.
SAVE THESE INSTRUCTIONS.
2
x
1. Getting Started DSP9200 Series Balancer Operation Instructions

Electrical
The DSP9200 is manufactured to operate at a specific voltage and amperage rating.
Make sure that the appropriate electrical supply circuit is of the same voltage and
amperage ratings as marked on the balancer.
WARNING: DO NOT ALTER THE ELECTRICAL PLUG. Plugging the
electrical plug into an unsuitable supply circuit will
damage the equipment.
Make sure that the electrical supply circuit and the appropriate receptacle is installed
with proper grounding.
To prevent the possibility of electrical shock injury or damage to the equipment when
servicing the balancer, power must be disconnected by removing the power cord
from the electrical power outlet.
After servicing, be sure the balancer ON/OFF switch is in the “O” (off) position before
plugging the power cord into the electrical power outlet.
This device is rated as Class A for radiated emissions.
In the event of radio interference, the display read out may flicker - this is normal.
DSP9200 Series Balancer Operation Instructions 1. Getting Started
x
3

Decal Information and Placement
NOTE: Decals and their placement may vary due to balancer
configuration and options.
Right Side View
Decal 128-963-2 gives the maximum wheel diameter, maximum wheel weight, and
maximum rotational frequency for the DSP9200.
Decal 128-605-2-00 cautions the user that spindle rotation may occur with foot pedal
depression and to keep clear of clamping components during Quick-Thread™ shaft
rotation.
4
x
1. Getting Started DSP9200 Series Balancer Operation Instructions

Left Side View
Decal 128-391-2-00 cautions that the unit may automatically start upon closing of the
hood when hood Autostart is enabled.
Decal 128-229-2 and decal 128-905-2 work in conjunction to caution the user to not
remove the screw because of the risk of electrical shock.
DSP9200 Series Balancer Operation Instructions 1. Getting Started
x
5

Back View
Decal 128-907-2 warns the user to place the DSP9200 at garage floor level, and not
in a recessed area, to avoid the possibility of flammable fume ignition.
Decal 128-229-2 and decal 128-905-2 work in conjunction to caution the user to not
remove the screw because of the risk of electrical shock.
6
x
1. Getting Started DSP9200 Series Balancer Operation Instructions

Specific Precautions/Power Source
The DSP9200 is intended to operate from a power source that will apply 230VAC
+10% / -15%, 1 phase, 3 amp 50/60 Hz, power cable includes NEMA 20 amp plug,
L6-20P, between the supply conductors of the power cord. The power cord supplied
utilizes a twist lock connector, NEMA L6-20P. This machine must be connected to a
20 amp branch circuit. Please refer all power source issues to a certified electrician.
Refer to Form 5467T, “Installation Instructions for DSP9200 Wheel Balancer.”
or
CAUTION: A protective ground connection, through the grounding
conductor in the power cord, is essential for safe operation.
Use only a power cord that is in good condition.
NOTE: For information on converting from single phase NEMA
L6-20P plug to thee phase NEMA L15-20P plug refer to
Form 5350T, “NEMA L6-20P to NEMA L15-20P Power Plug
Conversion Instructions.”
Turning Power ON/OFF
The ON/OFF switch is located on the back of the balancer cabinet. To turn the
balancer “ON,” press the “I” side of the ON/OFF switch. To turn the balancer “OFF,”
press the “O” side of the ON/OFF switch.
ON
OFF
When the ON/OFF switch is turned “ON,” the display panel segments will begin
lighting individually from left to right presenting a merchandising display. This also
indicates that power is on, the unit has self-checked, and that all displays are
functioning. Pressing any button on the control panel or moving the spindle shaft will
exit the merchandising display and advance the balancer to the default settings:
STANDARD procedure / DYNAMIC mode with the “Blind” and “Rounding” enabled.
Refer to “Blinding and Rounding,” page 51.
Equipment Installation and Service
Installation should be performed by a factory-authorized representative.
This equipment contains no user serviceable parts. All repairs must be referred to a
qualified Hunter Service Representative.
DSP9200 Series Balancer Operation Instructions 1. Getting Started
x
7

Equipment Specifications
Electrical
Voltage: 230VAC +10% / -15%, 1 phase, 50/60 Hz, power
cable includes NEMA 20 amp plug, L6-20P
Amperage: 3 amperes
Wattage: 920 watts (peak)
Atmospherics
Temperature: +32qF to +122qF (0qC to +50qC)
Relative Humidity: Up to 95% Non-condensing
Altitude: Up to 6000 ft. (1829 m)
Sound Pressure Level Equivalent continuous A-weighted sound pressure
at operator’s position does not exceed 70 dB (A).
Safety Summary
Explanation of Symbols
These symbols may appear on the equipment.
Alternating current.
Earth ground terminal.
Protective conductor terminal.
l ON (supply) condition.
OFF (supply) condition.
Risk of electrical shock.
Stand-by switch.
Not intended for connection to public
telecommunications network.
8
x
1. Getting Started DSP9200 Series Balancer Operation Instructions

1.3 DSP9200 Components
DSP9200 Series Balancer Operation Instructions 1. Getting Started
x
9

Standard Accessories
1. 106-82-2 Sleeve, Scratch Guard for Small Cup
2. 175-353-1 Polymer Cup (4.5” O.D.)
3. 76-433-3 Quick Take-Up Wing Nut with Handles
4. 221-658-2 Hammer Heads (4)
5. 46-320-2 Spacer
6. 221-589-2 Weight Hammer/Pliers
7. 221-659-2 Adhesive Weight Scraper
8. 223-68-1 Pressure Ring
9. 65-72-2 Calibration Weight
NOTE: Hunter wheel balancers do not include a standardized set of
mounting adaptors.
For optional accessories, refer to Wheel Balancer Brochure, Form 3203T.
10
x
1. Getting Started DSP9200 Series Balancer Operation Instructions

1.4 Operating the Control Panel
Control Panel
Using the Control Panel
Press the “Standard/ALU” button to select a STANDARD or ALU procedure.
Refer to “Standard Balancing Procedure (Using Clip-on Weights),” page 19 or
“Adhesive Weight Procedures (Combination Of Clip-on & Adhesive Weights, or Two
Adhesive),” page 36.
Press the “Optimize” button to select an Optimize procedure. Refer to “OPT-1
Optimizing Tire & Wheel Imbalances (Wheel with the Tire Mounted Procedure),”
page 42 or “OPT-2 Optimizing Tire & Wheel Imbalances (Tire Not Mounted
Procedure),” page 43.
Press the “Static/Dynamic” button to select the balancing mode. Refer to
“Static / Standard Balancing Procedure (Clip-on Weight),” page 35 or “Static / ALU
Balancing Procedure (Adhesive Weight),” page 41.
Press the “Setup/Cal” button to select from the Setup or Calibration options.
Refer to “Calibration Procedures,” page 58.
Press the “Next” button to change planes (green “weight” will indicate current
plane selected) or scroll through menus, or to select wheel to store/recall.
Press the “Enter” button to enter information and to begin a procedure that has
been selected, or to “Store/Recall” wheels. Refer to “Storing and Recalling Wheels,”
page 55.
DSP9200 Series Balancer Operation Instructions 1. Getting Started
x
11

Press the “Left Plane Split Weight®” button to split weights on the Left Plane.
Refer to “Split Weight®Feature,” page 51.
Press the “Oz/Gm” button to view balancing weights in ounces or grams.
Press the “Right Plane Split Weight®” button to split weights on the Right
Plane. Refer to “Split Weight®Feature,” page 51.
Press the “CenteringCheck®” button to check the accuracy of the mounting of
the tire/wheel assembly on the balancer shaft. Refer to “CenteringCheck®,” page 25.
Using Wheel Dimension Control Knobs
The control knobs are located to the left of the control panel. The control knobs are
used to manually input wheel dimension data. The control knobs are identified as the
distance, width, and diameter control knobs.
Wheel dimension control knobs are used for manual data entry when required.
Changes to wheel dimensions are made by rotating the knobs. The control knobs are
digital encoder design and variable speed. Rotating slowly will change increments in
single digits. Rotating quickly will advance and move increments at an increased rate.
12
x
1. Getting Started DSP9200 Series Balancer Operation Instructions

2. BALANCING OVERVIEW
2.1 Balancing Modes
Static Balance
As the word static implies, the tire will be balanced when at rest. For example, if an
unmoving assembly was centered on a cone and was balanced, it would be statically
balanced. A “bubble balancer” is designed to statically balance a tire/wheel
assembly.
IMBALANCE
FORCE
FRONT VIEW
STATIC IMBALANCE
CUPPING
Static imbalance is where there is one amount of weight located in the center of the
tire/wheel assembly causing an imbalance. As the weight rotates, centrifugal forces
are created causing the wheel to lift as the weight reaches top dead center. This
lifting motion causes the tire/wheel assembly to move “up and down” creating a
bounce to be felt. This static imbalance condition is evident by a “jiggle” or up-down
movement of the steering wheel. These vibrations may also be apparent in the body,
with or without steering wheel shake.
A statically imbalanced tire driven for an extended period may cause “cupping” in the
tire’s tread, create vibration, and adversely effect handling.
Static balancing alone is a seldom-recommended procedure that balances the
assembly using only a single weight plane. For example, a single weight is commonly
placed on the inner clip weight position for cosmetic purposes. This is not a
recommended practice and usually insures the assembly is not properly dynamically
balanced. The assembly may then experience side-to-side imbalance while in
motion, causing a shimmy condition and objectionable vibration.
DSP9200 Series Balancer Operation Instructions 2. Balancing Overview
x
13

Dynamic Imbalance
In general terms, dynamic imbalance is defined as where one or more locations of
the tire/wheel assembly are heavier causing an imbalance force and/or an imbalance
wobble. Shown below is a tire/wheel assembly with two heavy spots of equal weight
which are located 180 degrees radially from each other on opposite sides. As this
assembly rotates, centrifugal forces cause a large imbalance wobble to be created,
but the imbalance force (as well as the static imbalance) will be zero. A wheel with
this condition will cause a wobble or shimmy to be felt in the steering wheel.
Excessive dynamic imbalance of this type creates a shimmy that transfers through
the suspension components to the occupants of the vehicle, especially at higher
speeds.
IMBALANCE WOBBLE
(LATERAL TWIST OR TORQUE)
FRONT VIEW
ZERO STATIC IMBALANCE WITH LARGE
DYNAMIC (COUPLE) IMBALANCE
Modern “dynamic” balancers spin the wheel in order to measure both the up and
down imbalance force and the wobble or shimmy related imbalance (side-to-side).
Dynamic balancers direct the operator to place correction weights on the inside and
outside correction locations of the rim so that both imbalance force and imbalance
wobble will be eliminated.
IMBALANCE WOBBLE
(LATERAL TWIST OR TORQUE)
TOP VIEW
IMBALANCE FORCE
(UP & DOWN)
ZERO STATIC IMBALANCE (UP & DOWN)
+ ZERO COUPLE IMBALANCE (WOBBLE)
_____________________________________
= ZERO DYNAMIC BALANCE
14
x
2. Balancing Overview DSP9200 Series Balancer Operation Instructions

Static and Dynamic Imbalance Sensitivity
As a general rule of thumb, to achieve the best balance on an average sized tire and
wheel assembly:
Residual static imbalance should be less than 1/2 ounce.
Residual dynamic imbalance should be less than 1/4 ounce per plane.
A small amount of residual dynamic imbalance is preferred over a similar amount of
remaining static imbalance.
In general, it takes much more residual dynamic imbalance to cause a vibration than
the same amount of static imbalance.
The larger the diameter used for weight placement, the smaller the amount of
correction weight is required.
The wider the distance between the two weight placement locations, the smaller the
amount of correction weight is required.
If static balance is the only option, always verify that the remaining dynamic residual
imbalance is within acceptable tolerance.
2.2 Identifying the Static Balance Weight Plane
In “STANDARD BALANCE” mode, using only a clip-on weight, the plane is input as
follows:
For static balancing, it is recommended that you place half of the correctional weight
value on each side of the tire to reduce residual dynamic imbalance.
In “MIXED WEIGHTS BALANCE” mode and “ADHESIVE WEIGHTS BALANCE”
mode, using an adhesive weight, the plane is input as follows:
DIAMETER
For static balancing, it is recommended that the adhesive weight be placed as close
to the center of the wheel as possible to reduce residual dynamic imbalance.
DSP9200 Series Balancer Operation Instructions 2. Balancing Overview
x
15

In “PATCH BALANCE” mode, using a patch weight, the plane is input as follows:
DIAMETER
For static balancing, it is recommended that the patch weight be placed as close to
the center of the tread as possible to reduce residual dynamic imbalance.
2.3 Identifying the Dynamic Balance Weight Planes
The balancer must know the location of the two weight circle planes for placement of
correction weights on the wheel assembly.
Each plane is described by a distance from the balancer and a diameter.
MIXED WEIGHTSSTANDARD PATCHADHESIVE WEIGHTS
RIM LIP / RIM LIP RIM LIP / INNER RIM SURFACE INNER RIM SURFACE /
INNER RIM SURFACE
INNER TIRE SURFACE /
INNER TIRE SURFACE
In “STANDARD BALANCE” mode, using only clip-on weights, left and right planes
are input as follows:
16
x
2. Balancing Overview DSP9200 Series Balancer Operation Instructions
Table of contents
Other Hunter Scale manuals
Popular Scale manuals by other brands

Fidelity Electronics
Fidelity Electronics G1-3000 Operation manuals

CAS
CAS 25AC owner's manual
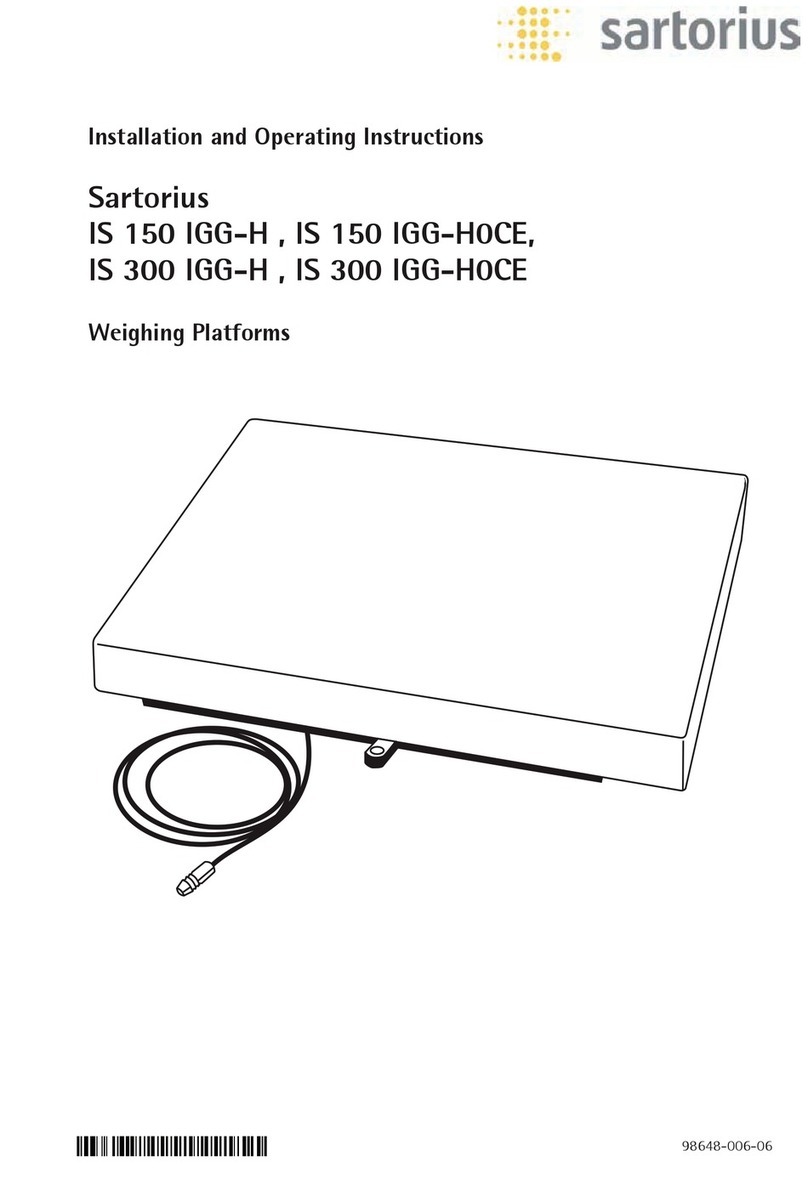
Sartorius
Sartorius IS 300 IGG-H Installation and operating instructions
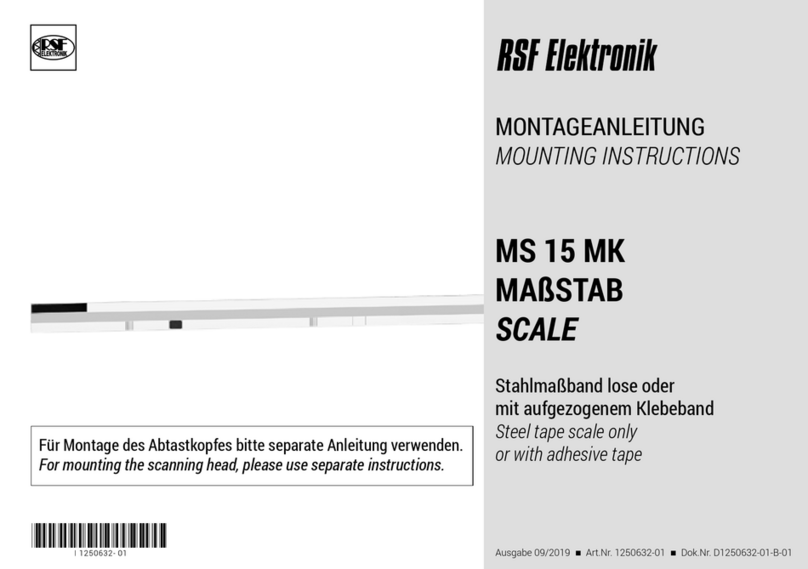
RSF Elektronik
RSF Elektronik MS 15 MK Mounting instructions
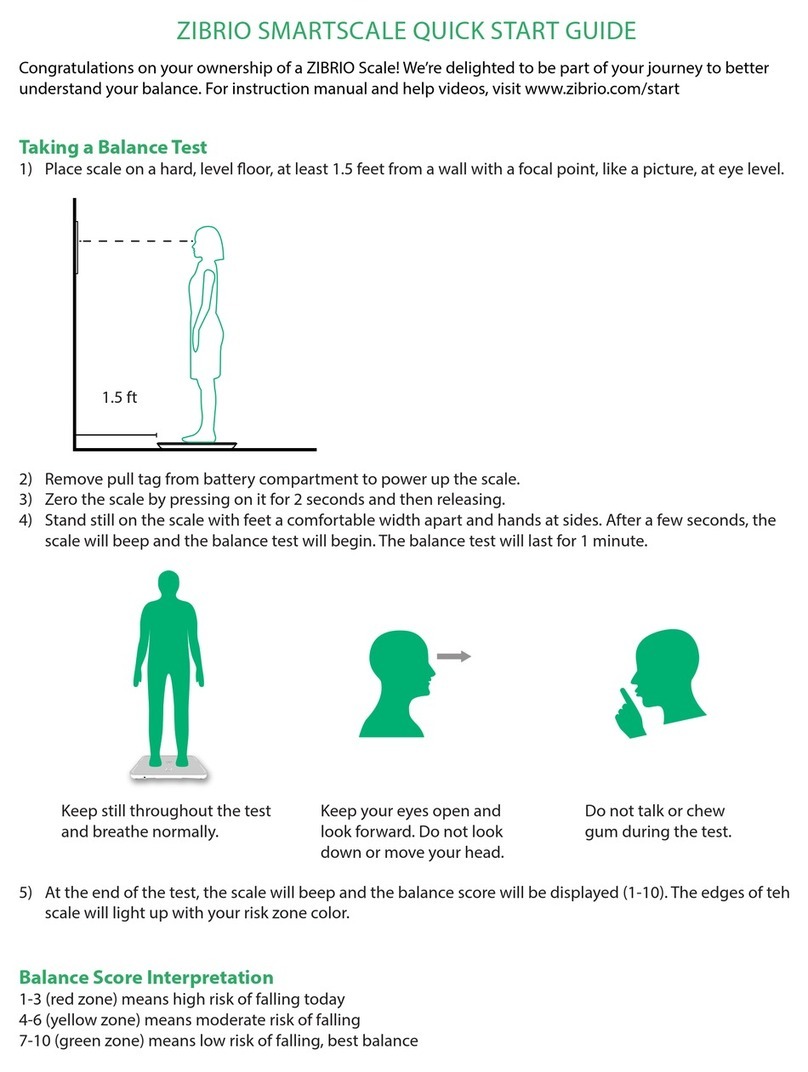
ZIBRIO
ZIBRIO SmartScale quick start guide

American Weigh Scales
American Weigh Scales AWS-55 user manual