Hydac RFCS Series Manual

Installation and maintenance manual
for
Stand allone chiller

Installation and maintenance manual
H.I.B Hydac International Page 2 of 36
Version: G/DV
Date: 11.01.2023
1.0 Model code
Example
RFCS-
G4-
013000-
W-
L-
R25-
3-
IW-
Type
RFCS = active cooling
Series
Cooling capacity
in watts(W)
Coolant/refrigerant
W = water
O = oil
C = chemical media
Design of heat-dissipating side (heat exchanger)
W = water-cooled
L = air-cooled
Controller type
Voltage range
IW = non-ferrous metal parts,
in contact with water
DI = free from non-ferrous metal,
in contact with water
C = chemical media
Other information (optional, for example UL)

Installation and maintenance manual
H.I.B Hydac International Page 3 of 36
Version: G/DV
Date: 11.01.2023
Scope of the installation and maintenance manual
This Installation and maintenance manual covers the dry cooler:
See Annex and technical data sheet. Read the Installation and maintenance manual before start-
up. Keep and make available these Installation and maintenance manual for further use!
The unit is not suitable for use in an explosion-endangered atmosphere.
The unit must not be used for cooling flammable or explosive substances.
WARNING
This operating manual was made to the best of our knowledge. Nevertheless and despite the
greatest care, it cannot be excluded that mistakes could have crept in. Therefore please
understand that it the absence of any provisions to the contrary hereinafter our warranty and
liability –for any legal reasons whatsoever –are excluded in respect of the information in this
operating manual. In particular, we shall not be liable for lost profit or other financial loss. This
exclusion of liability does not apply in causes of intent and gross negligence. Moreover, it does
not apply to defects which have been deceitfully concealed or whose absence has been
guaranteed, nor in cases of culpable harm to life, physical injury and damage to health. If we
negligently breach any material contractual obligation, our liability shall be limited to foreseeable
damage. Claims due to the Product Liability shall remain unaffected. In the event of translation,
only the original version of the operating manual in German is legally valid. The operator of the
cooler shall ensure that all written information and warnings are in the official language(s) of the
community where the chiller is placed on the market / put into service.
Manufacturer:
H.I.B Systemtechnik GmbH
Winterbruckenweg 30
86316 Friedberg / Derching
Deutschland
Telefon Zentrale: +49 (8 21) 7 47 71- 4
Service Telefon: +49 (8 21) 7 47 71-5550
Service Telefax: +49 (8 21) 7 47 71-5592
E-mail: Service@h-i-b.de
Internet: www.h-i-b.de
© All rights reserved.
No part of this Installation and maintenance manual may be reproduced or duplicated in any form
(printing, photocopying or any other process) without the permission in writing from the
manufacturer.

Installation and maintenance manual
H.I.B Hydac International Page 4 of 36
Version: G/DV
Date: 11.01.2023
Contents:
1.0 Model code .....................................................................................................................2
2.0 Foreword.........................................................................................................................7
3.0 Machinery Directive 2006/42/EC...................................................................................8
4.0 Warning notes and symbols.........................................................................................8
4.1 Symbols................................................................................................................8
4.1.1 Warning notices and symbols used .....................................................................9
4.1.2 Personal protective equipment (PPE) ............................................................... 10
4.2 Safety / Prevention of accidents ....................................................................... 10
4.2.1 General notes.................................................................................................... 10
4.2.2 Observe regulatory information......................................................................... 10
4.2.3 Qualification and training of personnel.............................................................. 11
4.2.4 Dangers when the notes on safety are ignored ................................................ 11
4.2.5 Safety - conscious working ............................................................................... 11
4.2.6 Notes on safety fort the user / operator ............................................................ 11
4.2.7 Notes on safety for maintenance, inspection and assembly work .................... 12
4.2.8 Unauthorised modification or use of spare parts .............................................. 12
5.0 Reference..................................................................................................................... 13
5.1 Instructions for use ............................................................................................ 13
5.2 Residual risks, arranged by risk reduction measures ....................................... 13
(according to DIN EN ISO 12100) ............................................................................................... 13
5.2.1 Residual risks on the housing ........................................................................... 13
5.2.2 Residual risks in the cooling circuit ................................................................... 13
5.2.3 Residual risks in the water circuit...................................................................... 13
5.2.4 Residual risks of electric system/electronics..................................................... 14
5.3 Safety instructions ............................................................................................. 14
5.3.1 When removing housings.................................................................................. 14
5.3.2 Improper operatinig modes ............................................................................... 15
5.3.3 Handling of refrigerants (optional)..................................................................... 15
5.3.4 Staff qualifications and training ......................................................................... 15
5.3.5 Plant log (Compressor-cooled system)............................................................. 16
5.3.6 Leak check ........................................................................................................ 16
5.3.7 The device’s emission of airborne noise (see technical data sheet) ................ 17
6.0 General description of the unit.................................................................................. 17
6.1 Usage to the intended purpose ......................................................................... 17
6.2 Description of operation of compressor-cooled (RFCS) ................................... 17
6.2.1 Function diagram compressor-cooled system (RFCS):.................................... 18
6.3 Description of operation of water-cooled systems (FWKS) .............................. 18
6.3.1 Functional diagram of water-cooled system (FWKS): ...................................... 18

Installation and maintenance manual
H.I.B Hydac International Page 5 of 36
Version: G/DV
Date: 11.01.2023
6.3.2 Specification of coolant (for mixing water additive) and of external water
(optional)Specification of external water (optional) ..................................................................... 18
6.4 Heating Operation (optional) ............................................................................. 19
6.5 External Control (optional) ................................................................................ 19
7.0 Transport ..................................................................................................................... 19
7.1 Transport monitoring ......................................................................................... 21
(only for devices at risk of tipping over during transport) ............................................................ 21
8.0 Unpacking and handling ............................................................................................ 21
8.1 General information........................................................................................... 21
8.2 Technical Data and type plate .......................................................................... 22
9.0 Use and function......................................................................................................... 22
10.0 Installation / Startup ................................................................................................... 22
10.1 Installation ......................................................................................................... 22
10.2 Hydraulic connection......................................................................................... 23
10.3 Electrical connection ......................................................................................... 24
11.0 Start up and Operation ............................................................................................... 24
11.1 Preparation........................................................................................................ 24
11.2 Commissioning.................................................................................................. 25
11.3 Empty the tank (optional) .................................................................................. 27
12.0 Operation of the temperature controller (optional) ................................................. 27
13.0 Service and maintenance........................................................................................... 27
13.1 Inspection .......................................................................................................... 27
13.2 Maintenance schedule ...................................................................................... 27
13.3 Maintenance generally ...................................................................................... 29
13.4 Cleaning the metal air filter and condenser (optional) ...................................... 29
13.5 Cleaning the dirt trap - external water (optional)............................................... 31
13.6 Replacing the particle filter (optional)................................................................ 33
14.0 Guarantee terms and conditions............................................................................... 33
15.0 Shutdown of the unit .................................................................................................. 34
15.1 Emptying the PHE during shipping or storage below 0 ° C (optional) .............. 34
16.0 Repair and Troubleshooting...................................................................................... 34
17.0 For waste and recycling ............................................................................................. 35
18.0 Dismounting ................................................................................................................ 35
18.1 Electric connection ............................................................................................ 35
18.2 Scrapping .......................................................................................................... 35
18.3 Refrigerant (optional) ........................................................................................ 35
18.4 Coolant .............................................................................................................. 35
18.5 External water (optional) ................................................................................... 35
19.0 Operating faults and causes of faults....................................................................... 35
20.0 Annex ........................................................................................................................... 36

Installation and maintenance manual
H.I.B Hydac International Page 6 of 36
Version: G/DV
Date: 11.01.2023
20.1 Technical data ................................................................................................... 36
20.2 Spare parts list .................................................................................................. 36
20.3 Dimension sheet ............................................................................................... 36
20.4 Flow chart.......................................................................................................... 36
20.5 Wiring diagramm ............................................................................................... 36
20.6 Special functions (optional) ............................................................................... 36
20.7 Test report ......................................................................................................... 36
20.8 Declaration of Incorporation / CE Declaration of Conformity ............................ 36

Installation and maintenance manual
H.I.B Hydac International Page 7 of 36
Version: G/DV
Date: 11.01.2023
2.0 Foreword
The Installation and Maintenance Instructions are intended to help you to become acquainted
with the cooler/system and make use of its possible applications as intended.
The Installation and Maintenance Instructions aim to increase the safety of the workers and
consumers in all life phases of the device.
The Installation and Maintenance Instructions should only be used in conjunction with the
attached additional documents. The additional documents are supplementary. If both documents
describe the same function, the additional documents have a higher priority.
This manual contains important notes which are to be observed during the installation, operation
and maintenance of the unit, in order to guarantee safe, proper and economical use of the system.
The operating manual must always be available wherever the chiller / unit is in use.
The Installation and Maintenance Instructions must be read and applied by everyone:
Operation
Specialist electrician
Specialist personnel
Cooling specialist
Qualified personnel for transport and storage
In addition to the operating manual and to the mandatory rules and regulations for accident
prevention and environmental protection in the country and place of use of the machine / unit, the
generally recognized technical rules for safe and proper working must also be observed.
The marking for transport and stocking indicated on he packaging have to be observed
under all circumstances
WARNING
NOTE
Please check the type of manual (see Annex, Type List) against the label on you
device. This installation and maintenance manual is only valid for the device mentioned
in annex.

Installation and maintenance manual
H.I.B Hydac International Page 8 of 36
Version: G/DV
Date: 11.01.2023
3.0 Machinery Directive 2006/42/EC
The Installation and Maintenance Instructions were revised on 2020-04-29 in accordance with
the Machinery Directive 2006/42/EC.
Equivalent in the Machinery Directive
Implementation measures
Avoid accidents by increasing the safety in
the design of the device
Inherent design, potential hazards are discovered
and reduced in the design process. Design
manual with key information on inherent design
available to all designers.
Provision of safety of persons, in particular
through employees and consumers
Installation of electric and mechanical safety
parts
CE marking in accordance with industrial
standard alongside manufacturer’s
information
CE marking alongside name plate
Risk assessment
Risk assessment and risk minimisation measures
carried out
Documentation
Adapted
Compliance with harmonised industrial
standards
Taken into account in the risk analysis
Table in accordance with number 34 of the Inter-institutional Agreement on Better Lawmaking
Equivalencies between the Machinery Directive 2006/42/EC and implementation measures.
4.0 Warning notes and symbols
4.1 Symbols
WARNING:
This heading is used whenever the ignorance or inaccurate obeying of factory rules,
working rules, laid down work routines, etc. can lead to the death, injury to or an
accident of a person.
WARNING
ATTENTION:
This heading is used whenever the ignorance or inaccurate obeying of factory rules,
working rules, laid down work routines, etc. can lead to damage to the system.
ATTENTION
NOTE
NOTE:
This heading is used when an exceptional feature should be taken notice of.
MANDATORY:
This heading is used when technical rules or regulations require that a course of
action be observed.
MANDATORY

Installation and maintenance manual
H.I.B Hydac International Page 9 of 36
Version: G/DV
Date: 11.01.2023
4.1.1 Warning notices and symbols used
The following warning notices and symbols are used in this manual:
WARNING
WARNING
WARNING
WARNING
General hazards
Hazard by electrical current
Automatic start
Hot surface
WARNING
WARNING
WARNING
WARNING
Danger by suspended load
Explosive substances
Corrosive substances
Danger of freezing
WARNING
INFORMATION
Warning against cuts
Position of the centre of gravity
MANDATORY
Wear protective gloves
MANDATORY
Wear protective clothing
MANDATORY
Wear eye protection
MANDATORY
Wear foot protection

Installation and maintenance manual
H.I.B Hydac International Page 10 of 36
Version: G/DV
Date: 11.01.2023
4.1.2 Personal protective equipment (PPE)
Pictogram
Description
Protective gloves, mechanical hazard (7010-M009) Protective gloves are
used to protect the hands from friction, grazing, piercing injuries or deeper
injuries and from making contact with hot surfaces.
Protective work clothing (7010-M010) Protective work clothing is tight-fitting
work clothing with low tearing strength, with tight sleeves and without any
protruding parts.
Safety goggles (7010-M004) Safety goggles serve to protect the eyes from
flying parts and spraying liquid.
Wear foot protection (7010-M008). The mandatory action signs label work
areas where suitable work protection shoes or boots must be worn.
4.2 Safety / Prevention of accidents
4.2.1 General notes
This installation and maintenance manual contains basic notes to be observed for startup,
operation and maintenance. Read before starting the unit without fail.
Commissioning refers to the initial use, as intended, of a device covered by the Machinery
Directive in the European Community, i.e. the time at which the device must be compliant with
the Machinery Directive and all other EU directives and EU regulations that apply to the device.
The manufacturer declines any responsibility for damage and breakdowns resulting from a
failure to observe this operating manual.
4.2.2 Observe regulatory information
Observe the following regulatory information and directives:
Legal and local regulations for accident prevention
Legal and local regulations for environmental protection
Country-specific regulations, organisation-specific regulations

Installation and maintenance manual
H.I.B Hydac International Page 11 of 36
Version: G/DV
Date: 11.01.2023
4.2.3 Qualification and training of personnel
The personnel for operation, maintenance, inspection and assembly must be adequately qualified
for the work concerned. The user must clearly specify the sphere of responsibility, competence
and supervision of the personnel.
Designation
Description
Operator
Operators have been instructed by the owner about the tasks allocated to
them and possible risks in case of inappropriate behaviour. Tasks which go
beyond the scope of normal operation may only be performed by the
operator if specified in these Operating Instructions and expressly
authorised by the owner.
Specialist
electrician
Specialist electricians have sufficient specialist training, knowledge and
experience and awareness of the relevant industrial standards and
regulations to allow them to perform work on electrical systems and
independently recognise and avoid potential hazards. Specialist
electricians have been specially trained for the specific operating location
in which they work and are aware of the relevant industrial standards and
regulations.
Specialist
personnel
Specialist personnel have sufficient specialist training, knowledge and
experience and awareness of the relevant industrial standards and
regulations to allow them to perform work assigned to them and
independently recognise and avoid potential hazards.
Cooling specialist
Cooling specialists have been trained and certified for the specific operating
area in which they work and are aware of the relevant industrial standards
and regulations. The certification includes the required skills for the
prevention of emissions, the recovery of fluorinated greenhouse gases and
safe handling of cooling equipment of the relevant type and size. Cooling
specialists have sufficient specialist training and experience to allow them
to perform work on cooling systems and independently recognise and avoid
potential hazards.
Skilled personnel
for transport and
storage
These personnel must be familiar with and have received instruction in the
handling of lifting equipment and accessories for transporting machinery
and machine parts, in addition to hydraulic units.
4.2.4 Dangers when the notes on safety are ignored
Ignoring the safety regulations can have a harmful effect on persons or cause damage to the
system or environment. Ignoring the safety regulations may cause a loss of claim for damages.
4.2.5 Safety - conscious working
Observe the notes and safety given in the manual, the national rules for prevention of accidents
in force, as well as any internal instructions by the user for working, operation and safety.
4.2.6 Notes on safety fort the user / operator
Any guard preventing accidental contact of moving parts must not be removed when the system
/ unit is running. Take appropriate steps to preclude any hazard by electric power. (For relevant
details see the rules of the VDE and the local energy supply companies).

Installation and maintenance manual
H.I.B Hydac International Page 12 of 36
Version: G/DV
Date: 11.01.2023
It must not under any circumstances be possible for the following types of
foreseeable misuse to occur:
WARNING
Use as a cooling system for non-approved refrigerants and coolants.
Operating of the cooling system with the tank not filled
Unauthorised modification or conversion of the cooling system and its guard devices
Failure to comply with the prescribed distancing for the waste air when the cooling
system is being set up
Bypassing or deactivation of safety and guard devices
Any alterations and non-conformities with the technical data sheet must be clarified with the
manufacturer in advance
The employer shall instruct the insured person on:
the dangers when handling refrigerating plants and cooling
The safety regulations
the conduct in the case of accidents and failures and the Stepps to be taken in such cases
before they start their work fort the first time and at reasonable intervals, however, at least once
a year. (see VBG 20§19)
4.2.7 Notes on safety for maintenance, inspection and assembly work
On principle, cleaning and maintenance of the chiller / unit must be carried out with the chiller /
unit at standstill only. The procedure for shutdown of the unit given in the operating manual must
be observed without fail. Immediately after completing the work all safety and guarding devices
must be replaced and / or put into service again.
4.2.8 Unauthorised modification or use of spare parts
Modification of or changes to the chiller / unit are only permitted after previous consultation of the
manufacturer. Original spare parts and accessories authorised by the manufacturer serve for
ensuring safety. The use of other parts will void the liability for the resulting consequences.

Installation and maintenance manual
H.I.B Hydac International Page 13 of 36
Version: G/DV
Date: 11.01.2023
5.0 Reference
5.1 Instructions for use
Please find out even before starting up about the measures for installation, set up, operation
and maintenance
These operating instructions contain basic advice that is to be observed during start-up,
operation and maintenance
No liability is accepted by the manufacturer for damage and operating faults that arise from a
failure to observe these manual.
5.2 Residual risks, arranged by risk reduction measures
(according to DIN EN ISO 12100)
5.2.1 Residual risks on the housing
Risk
Risk reduction
Residual risk
Shape, edges, corners
Avoidance of sharp edges and
corners, protective clothing
Quality of sheet metal and
other purchased parts
Mechanical stability
Design-based
Negligent behaviour
Stability against tipping
over
Design-based
Incorrect transport
Kinetic energy, fan
Guard device
Power failure during testing.
Negligence
Hazards arising from
noise
Fans configured in accordance with
legal limits
Personal hypersensitivity
5.2.2 Residual risks in the cooling circuit
Risk
Risk reduction
Residual risk
Mechanical stability
Design-based, according to DIN EN
378-2:2018-04
Transport damage, negligent
behaviour
Pressurised fluid
escaping
Design-based, warning in the
Operating Instructions, protective
equipment, maintenance and service
only by specialist personnel
Negligent behaviour
Components with
extreme temperatures
Maintenance and service only by
specialist personnel, stickers,
protective equipment
Contact during mechanical
maintenance work and
prescribed inspections
5.2.3 Residual risks in the water circuit
Risk
Risk reduction
Residual risk
Shape, edges, corners
Avoidance of sharp edges and
corners, protective clothing
Quality of fittings and other
purchased parts
Mechanical stability
Design-based, components selected
on basis of suitability and specification
Transport damage,
installation error
Contact with coolant
Organisational, maintenance
schedule of the hoses, safe access
for filling and draining
Hoses hard to reach

Installation and maintenance manual
H.I.B Hydac International Page 14 of 36
Version: G/DV
Date: 11.01.2023
5.2.4 Residual risks of electric system/electronics
Risk
Risk reduction
Residual risk
Shape, edges, corners
Design-based, avoidance of sharp
edges and corners
Negligent behaviour, quality
of sheet metal and
purchased parts
Stability against falling
off, breaking off
Design-based, prescribed distancing
and regulations are observed.
Negligent behaviour
Mechanical stability
Design-based, mechanical
components and other purchased
parts are used on basis of suitability
and specification.
Part error, installation error
Live components
Training and instruction,
earthing/protective conductor, secure
covering, use of warning signs
During inspection and
service work, it may be
necessary to work on live
parts.
Live components,
controller in faulty
condition
Training and instruction,
earthing/protective conductor
During inspection and
service work, it may be
necessary to work on live
parts.
Live equipment, faulty
condition
Design-based, coordination between
the grid form, the earthing system and
the fuses, warning signs, electrical
inspections
During inspection and
service work, it may be
necessary to work on live
parts.
Live components,
sensors, faulty condition
Design-based, safety extra-low
voltage, qualified personnel
Negligent behaviour
Short circuit or overload
Design-based, overload protection,
earthing, warning signs
Negligent behaviour
Misuse
5.3 Safety instructions
5.3.1 When removing housings
The device should be disconnected from the
It is possible that the copper wires and the compressor will still have hot surfaces even when
the device is disconnected from the mains
You should check whether the fan has stopped turning. If this is the case, then the repairs
and maintenance may be carried out.
Any guard preventing accidental contact of moving parts must not be removed when the
chiller / unit is running. Take appropriate steps to preclude any hazard by electric power.
Affixed on the packaging instructions for transport and storage must be observed!
WARNING

Installation and maintenance manual
H.I.B Hydac International Page 15 of 36
Version: G/DV
Date: 11.01.2023
On principle, cleaning and maintenance of the chiller / unit must be carried out with the chiller
/ unit at standstill only. The procedure for shutdown of the unit given in the manual must be
observed without fail.
Immediately after completing the work all safety and guarding chiller must be replaced and /
or put into service again.
Modification of or changes to the machine / unit are only permitted after previous consultation
of the manufacturer. Original spare parts and accessories authorized by the manufacturer
serve for ensuring safety.
The use of other parts will void the liability for the resulting consequences.
5.3.2 Improper operatinig modes
The operating safety of the delivered machine / unit is only guaranteed with proper use. The limit
stated in the technical data must never be exceeded.
WARNING
The unit is not suitable for use in an explosion-endangered atmosphere.
The unit must not be used for cooling flammable or explosive substances.
5.3.3 Handling of refrigerants (optional)
The refrigerant has some kind of irritant effect on skin and mucous membranes. Liquid refrigerants
on the skin may cause frostbite.
Refrigerants may decompose and form toxic decomposition products (e.g. hydrogen chloride,
phosgene) in the presence of naked flames or hot surfaces.
The refrigerant volatizes when it escapes in gaseous form the air. Intentionally blowing off and /
or discharging the refrigerant is not permitted.
Transport and / or install refrigerating plants in such a way that they cannot be damaged by
inhouse transportation or traffic.
When refrigerant is escaping the unit, you must never smoke in the vicinity of the
unit / chiller. The gases will decompose to cauterizing acids in the burning
cigarette that will damage your lungs.
WARNING
Repairing the cooling circuit may be by an expert firm only.
WARNING
5.3.4 Staff qualifications and training
The personnel for operation, maintenance, inspection and installation must be suitably qualified
for this work. Work on the system may only be carried out by trained specialists in the fields of
electrical, mechanical or refrigeration engineering. The area of responsibility, competence and
supervision of the personnel must be precisely regulated by the operator.

Installation and maintenance manual
H.I.B Hydac International Page 16 of 36
Version: G/DV
Date: 11.01.2023
5.3.5 Plant log (Compressor-cooled system)
The user is obliged to keep a plant log up to date in accordance with ES 378-2 paragraph 11.5.
The following data shall be entered into the log:
Details of all maintenance and repair work
Amount and kind of (new, re-used or recycled) of the refrigerant filled up, for each filling-up
Amount of refrigerant drained of the plant, for each draining
If there is an analysis of the re-used refrigerant, the results shall also be recorded in the log
Origin of the re-used refrigerant
Changesto and replacement of components of the plant
Results of all periodic routine checks
Prolonged periods of downtime
5.3.6 Leak check
Certified personnel must perform legally prescribed periodic leakage tests on the coolant circuit
at fixed intervals. The personnel must verify their certified status to the owner.
The testing interval is determined by the particular CO2 equivalent of the coolant in the coolant
circuit.
The CO2 equivalent of the cooling system is given on the coolant ID plate (attached next to the
serial no. plate) or the test log.
At 5 metric tons of CO2 equivalent or more, tests must be performed every year, at 50 tons or
more every six months and at 500 tons or more every three months.
Source: Regulation (EU) No. 517/2014 of the European Parliament and of the Council on fluorinated greenhouse gases and repeal ing Regulation (EC) No.
842/2006, Germany (2017)
All European member states have the option of taking stricter protective measures by means of
national law in addition to Regulation (EU) Nr. 517/2014. This may involve a requirement for
shorter leakage test intervals or a complete prohibition of a particular coolant.
The owners are themselves responsible for being adequately informed of the national law in the
country where the coolant circuit is being used.
The tests must be documented in an operator’s manual intended for the system. The operator’s
manual can be ordered from the manufacturer.
This operator’s manual contains the basic technical data and documents the history of the chiller.
The manual must be updated by specialist personnel whenever the coolant circuit is broken into
and whenever repair, maintenance, leak detection and leakage tests are performed.
Such work must always be performed in compliance with state-of-the-art technical standards.

Installation and maintenance manual
H.I.B Hydac International Page 17 of 36
Version: G/DV
Date: 11.01.2023
5.3.7 The device’s emission of airborne noise (see technical data sheet)
As the work area or work areas are not specified or cannot be specified, the measurements of
the A-weighted sound pressure value are taken at a distance of 1m from the device surface and
1.60m above the ground. The highest emission sound pressure value is given (see technical data
sheet).
6.0 General description of the unit
6.1 Usage to the intended purpose
The unit serves for cooling the coolant required for the working or finishing process.
The unit is designed as stand-alone or integrated device, depending on the configuration
concerned. For better understanding of the system, use the flow chart in the appendix.
Unauthorized modifications of and changes to the unit as well as using the chiller
for any other purpose are forbidden for safety reasons.
WARNING
6.2 Description of operation of compressor-cooled (RFCS)
The coolant is supplied to the consumer and back by the circulating pump. The flow controller
(optional) mounted in the coolant-circuit monitors the flow. The absorbed heat is dissipated via
the refrigeration-circuit to the ambient air or an external water circuit. A low-level float switch
mounted in the storage tank protects the circulating pump against running dry.
A flow sensor monitors the level and reports not enough coolant.
Option: Another level sensor monitors the level and automatically fills the cooling system via a
2/2 way valve.
Refrigerating Operation: Absorbed heat is dissipated to the refrigerant gas by the evaporator.
Any refrigerant that evaporates during this process is drawn in and compressed by the
compressor. The compressed refrigerant (hot gas) is then cooled and liquefied in the condenser.
Depending on the refrigerating system, the heat released during this process is dissipated to the
ambient air or an external cooling system. Liquefied refrigerant is again injected into the
evaporator via the expansion valve and absorbs heat during this process. A high-pressure relief
valve integrated in the system protects the cooling system against excess pressure.
Optional: Hot gas bypass operation
A 2/2 way valve mounted in the refrigeration circuit controls the required cooling capacity as a
function of the measured coolant-temperature via the temperature sensor and the temperature
controller.
Optional: Flow control
A motorized control valve mounted in the cooling circuit controls the required cooling capacity as
a function of the measured coolant temperature via the temperature sensor and the temperature
controller.

Installation and maintenance manual
H.I.B Hydac International Page 18 of 36
Version: G/DV
Date: 11.01.2023
6.2.1 Function diagram compressor-cooled system (RFCS):
See Annex (optional)
NOTE
The machine performance of air-cooled cooling units depends on the ambient
temperature and the coolant temperature to a considerable extent. The lower the
ambient temperature, the higher the overall performance of the unit.
NOTE
The machine performance of water-cooled cooling units depends on the external water
temperature. The lower the external water temperature, the higher the overall
performance of the unit.
6.3 Description of operation of water-cooled systems (FWKS)
The coolant is supplied to the consumer and back by the circulating pump. The flow controller
(optional) mounted in the coolant circuit monitors the flow. The heat absorbed in this process is
dissipated to the external water circuit via the plate-type heat exchanger. A flow switch mounted
in the storage tank protects the circulating pump against running dry.
A flow switch monitors the level and reports not enough coolant.
Optional: The flow sensor monitors the level and automatically fills the cooling system via a 2/2
way valve.
Refrigerating Operation: A motorized control valve arranged in the external water circuit controls
the amount of in- water and thus the required refrigerating capacity in dependence on the
measured coolant temperature via the temperature sensor and the temperature controller.
Optional: A 2/2 way valve mounted in the supply line opens or closes the external water circuit
as required at the end or start of work.
Optional: A pressure switch mounted in the external water circuit will give the message „No
external water“.
6.3.1 Functional diagram of water-cooled system (FWKS):
See Annex (optional)
NOTE
The machine performance of water-cooled cooling units depends on the water
temperature. The lower the water temperature, the higher the overall performance of
the unit.
6.3.2 Specification of coolant (for mixing water additive) and of external water
(optional)Specification of external water (optional)
Coolant: contaminant particles <50µm
External water: contaminant particles <200µm
Visual nature: transparent, pure, free from oils and fats.
Dissoved matter in water
Unit
pH-value considering to SI- Index
7 to 9
Saturation index (SI) (Delta pH-value)
-0,2<0<+0,2
Total hardness
°dH
<6
Conductivity
µS/cm
>200
filterable material mg/l
mg/l
<30
Chloride
mg/l
<100
Free chlorine
mg/l
<0,5

Installation and maintenance manual
H.I.B Hydac International Page 19 of 36
Version: G/DV
Date: 11.01.2023
Hydrogen sulfide H2S
mg/l
<0,05
Ammoniac (NH3/NH4+)
mg/l
<2
Sulfate
mg/l
<100
Hydrogen carbonate
mg/l
<300
Hydrogen carbonate / Sulfate
mg/l
>1
Sulfide
mg/l
<1
Nitrate
mg/l
<100
Nitrite
mg/l
<0,1
Dissolved iron
mg/l
<0,2
Manganese
mg/l
<0,1
Dissolved aggressive carbon dioxide
mg/l
<20
6.4 Heating Operation (optional)
After prolonged periods of standstill or under certain operating conditions it may become
necessary to heat the coolant by means of a heating element to reach the coolant temperature
faster or to maintain it. The unit controller will cut the heating element in if required.
6.5 External Control (optional)
The customer may integrate control functions of the cooling device in his control after consultation
with the manufacturer.
ATTENTION
Devices with external control, i.e. devices without integrated control must be adjusted
along with the manufacturer for operational reliability. The user of the control must
ensure that all plant components are operated in accordance with the intended
purpose.
7.0 Transport
The chiller / unit may be transported in the original packing only until the first startup. Empty the
chiller / system before transport.Notify the manufacturer immediately if you detect any damage.
When the chiller / unit is given another place in a plant, all connections of the chiller / unit must
be disconnected. Any dislocating of the chiller / unit must be done in such a way that damage is
excluded.
Should there be a damage despite these notes, have the chiller / unit inspected and/or repaired,
if required, by an expert before you start it again.
WARNING
In the special regulations for individual modes of transport, refrigerating machines
up to 12 kg are not subject to the hazardous goods regulations for road, sea or air
transport. If the individual pre-filled device exceeds this filling limit, however, then
the refrigerating machine (RFCS) is transported as a hazardous good.
Hazardous goods must be classified and sorted. Refrigerating machines are listed
under the UN number UN 2857.
The chiller may only be transported upright and in position for use.
The chiller / unit has a weight of (see appendix, Technical Data).
WARNING
WARNING
All existing eyebolts must be equally loaded!
Use only a portion of the existing lifting lugs are not allowed

Installation and maintenance manual
H.I.B Hydac International Page 20 of 36
Version: G/DV
Date: 11.01.2023
WARNING
For Transport, appropriate tools must be used. Only use suitable and approved
hoists. Don’t step under suspended load. Wear safety shoes. Load-suspension
attachments may only be applied from a vertical line with an angle less than 30°.
Observe all relevant safety regulations without fail.
WARNING
As a rule work on the electrical system must be carried out by expert personnel; the
valid wiring diagram ant the VDE guidelines must be observed.
For transport, observe the location of the centre of gravity
Wear safety boots during transport.
schematic diagrams
Transport of G7/G8 with traverse or forklift!
Transport of S7 with steel tube
(diameter 40 –50mm) and with transport belts
This manual suits for next models
1
Table of contents
Popular Chiller manuals by other brands
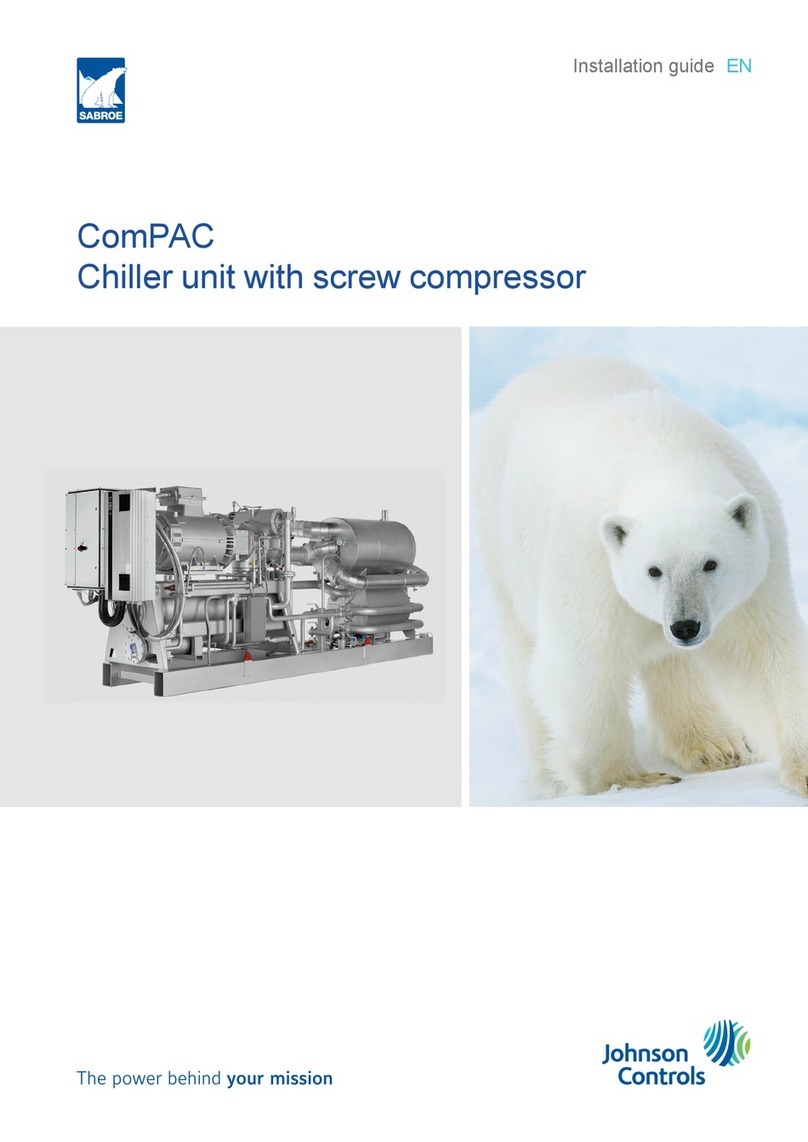
Johnson Controls
Johnson Controls SABROE ComPAC installation guide
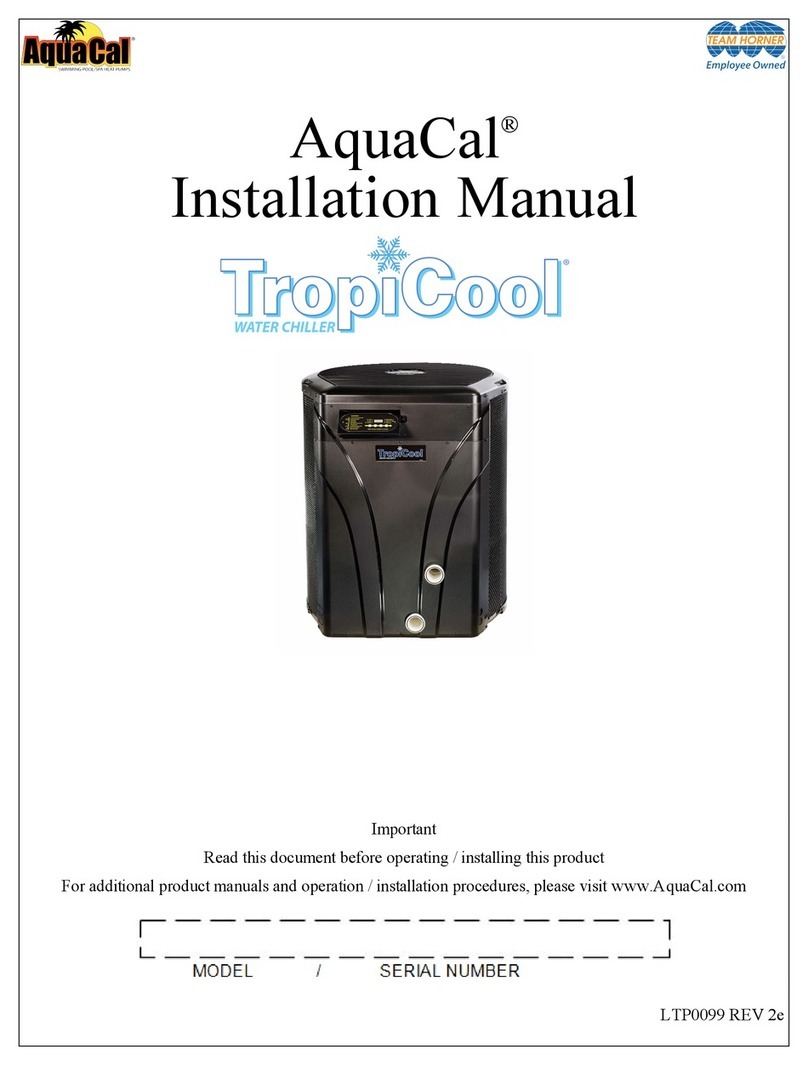
Aquacal
Aquacal TropiCool TC500 installation manual
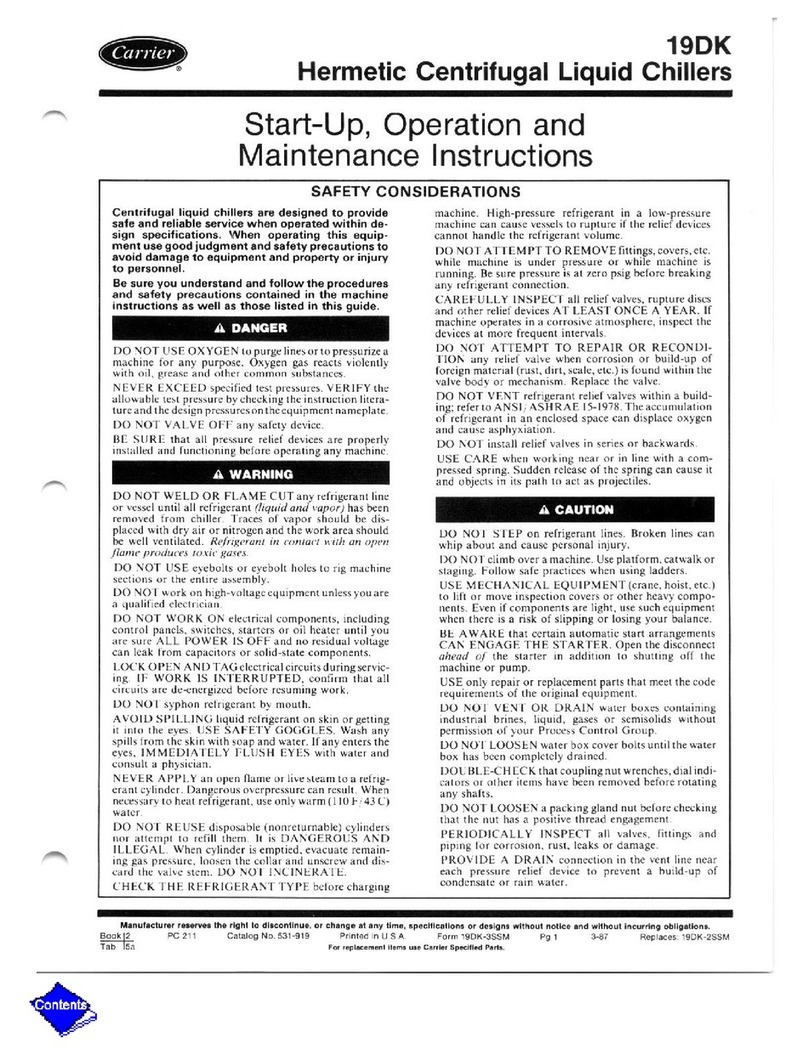
Carrier
Carrier 19DK Operating and maintenance instructions

Trane
Trane OXBOX J4GXCA003EC6HUA Installer's guide
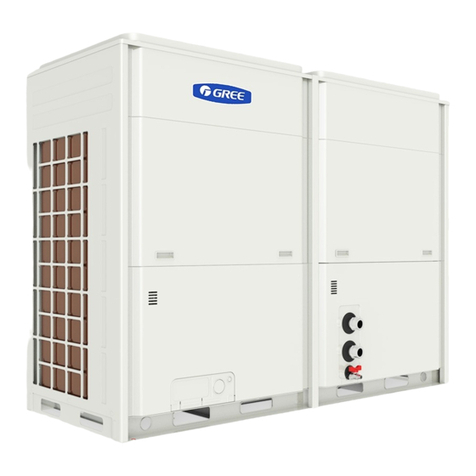
Gree
Gree LSQWRF35VM/NaA-M Service manual

Liebert
Liebert Process Fluid Chiller PS120A Specification sheet