IAC INDUSTRIES Quick Value AMERICAN Series User manual

INDUSTRIES
IAC INDUSTRIES
3831 S BULLARD AVE., GOODYEAR, AZ 85338
Phone (714) 990-8997 Fax (714) 990-0557
www.iacindustries.com
915 HAND CRANK ADJ. HI
REV. (010019P65)Assembly Instructions
Quick Value
AMERICAN SERIES 915 ADJ. BENCHES

2
Table of Contents
Page #
2 Pre-assembly Check List
3 915 Parts List
4 915 Hand Crank Assembly Drawing
4-5 915 Hand Crank Adjustable Bench Instructions
6-7 ESD Grounding
7 Cleaning
ATTENTION NOTES:
IAC Industries takes great care in the packing of its products; however damage can occur
during shipment. Check all packages and parts for any signs of damage. If damage is
evident STOP and contact the carrier that delivered your order. Request a freight claim
inspector to document the damage and begin the freight claim process.
Tools required to assemble your products are:
7/16” and 1/2” wrench or socket with ratchet. Phillips screwdriver 8” long.
Utility knife. Safety glasses and light duty protective gloves.
Power tools are NOT recommended unless they are equipped with a torque-limiting device
which can limit the torque to 10-foot lbs maximum.
Unpack your order and separate like parts. Be careful not to damage parts as they are being
moved into position. Also be sure all parts are removed from the packing materials before
these materials are thrown away.
Locate the hardware kits and keep them in a central area. If the assembly is going to take
more than one day, all individual hardware pieces should be returned to a central location.
Check all parts and hardware kits against the itemized packing list found with the assembly
instructions. If you believe there are parts missing from your order please contact IAC
Industries customer service at 800-989-1422.
WARNING:
ALL PARTICLE BOARD USED IN IAC INDUSTRIES PRODUCTS ARE SOURCED ONLY FROM VENDORS THAT ARE CARB
ATCM PHASE 2 AND TSCA TITLE VI COMPLIANT WITH VALID CERTIFICATES.Drilling, Sawing, Sanding or Machining Wood
products can expose you to wood dust, a substance known to the state of California to cause cancer. Avoid inhaling dust generated from wood
products or use a dust mask to other safeguards for personal protection. This product can expose you to chemicals, including formaldehyde, which
is known to the state of California to cause cancer, and methanol, which is known to the state of California to cause birth defects or other
reproductive harm. For more information please visit, www.P65WARNINGS.CA.GOV/WOOD. COPY OF VENDOR CERTIFICATE AVAILABLE UPON
REQUEST.

3
Parts List: 915 Hand Crank Adjustable Bench
(Ref. Figure 1)
Item Description Qty. Item Description Qty.
1 Work surface 1 D Bolt, ¼-20 x .750 SQH Black GR2 6
2 930 Leg Sub-Assy-Rt & Lt 1ea E Screw, 10-32 x 3.00 PHP Black 3
3 Front Support Beam 1.5H 1 F Washer, #10 Flat Zinc 3
4 930 Modesty Panel 930/940 1 G Nut, #10-32 Hex Keps Black 3
H Cap, 2.00 x 3.00 10-14 GA Black 4
A Bolt, ¼-20 x .750 HHW Black 4 J Floor Glide 5/16-18 x 1.75 x 1.625DIA 4
B Washer, ¼ Flat Black 27 K Bracket, 950/960-QS Hand Crank 1.50H 1
C Nut, ¼-20 Hex Keps Black 10 L Screw, #6 x .500 PPH SMS Zinc 1
M Cable Tie, Mount Plastic (#6) 4
N Cable Tie, 8” 4
Hardware Kit QV-HWR4061 P Screw, #14AB x .625 PPH SMS Black 12
1/4-20x .75 1/4-20 ¼-20 ¼-20x.75 10-32x 3L Washer #10 flat zinc
HH Bolt Flat washer Hex keps nut Bolt PHP Blk Screw
#10-32 2X3 10-14 Ga 5/16-18x1.75 950/960 #6x.500 PPH #6 Cable Tie
Nut, Hex Keps Cap, Black Floor Glide Hand Crank Screw SMS Zinc Mount Plastic
Cable Tie, 8” Screw, #14ABx6.25 PPH SMS Blk
CAUTION: Do not operate hand crank cylinders without the weight of the work surface on
the frame. To do so may cause a vacuum in the lines and possible damage to the system.
Be cautious to hold the leg assemblies together when turning workbench over after
assembly making sure they do not separate.

4
Reference Assembly Drawing below:
It may take as many as 4 people to assemble this bench.
1. Place worksurface (item 1) on clean surface underside facing up to be installed later. Install
the four floor glides (item J) and the four black bottom end cap (item H) to each end of the
leg assemblies.
2. Loosely attach front beam (item 3) to leg assemblies (item #2) using (item D) Bolt, ¼-20 x
.750 SQH Black GR2 and Washer 1/4 Flat black (item B).
3. Loosely attach modesty panel (item 4) to leg assemblies using three 1/4-20x3/4 square
head bolts (item D) in the rear slots of each of the legs (note: Square head bolts slides into
the rear of the aluminum channels) and1/4 flat washers (item B) and 1/4-20 hex nuts (item
C). Then, at the top of each end of the modesty panel is another slot that aligns with a hole
in the worksurface support at the top of each leg (item 2). Use a hex head bolt, two washers
and a hex nut to attach at each top end (items A, B, and C).

5
4. Place the worksurface on top of the frame and loosely attach it to the beam and pedestal
legs using the #14AB x .625 screws (Item P) and 1/4 washers (Item B) screwed into the
3/16 pilot holes drilled in the bottom of the worksurface. Do not tighten completely as some
adjustment will be needed later.
5. Loosely attach hand crank rear mounting bracket (item K) to the rear of pump system
using10-32 x 3.00 phillips screw (item E), #10 Washer (item F) and Nut, #10-32 Hex Keps
Black (item G) as shown in Figure 2 below.
6. Square the frame up on the worksurface and tighten up all fasteners. Be careful not to over
tighten as the screws may strip out.
7. Secure the front end of hand crank pump system to front beam using #10-32 x 3.00 phillips
screws (item E) and #10 flat washers (item F) and #10-32 hex nuts (item G). Tighten bolts
and screws as shown in Figure 2 below
Figure 2
8. Raise the leg assemblies to their highest point by turning the hand crank clockwise. Secure
hand crank pump hydraulic lines to underside of worksurface using cable mounts (items M),
cable ties (items N) and #6x.500 Phillips Screws (items L) being sure not to kink or
damage the lines in anyway.
9. Lower the bench slowly making sure to see that the pump hydraulic lines will not hang up on
anything. At this point raise and lower the bench to verify it is operating correctly.
10. When moving bench into it place be sure to lift it by the bottom base part of the leg
assemblies only. DO NOT lift it by the worksurface or the top part of the frame as this can
cause damage to the hydraulic system.

6
ESD GROUNDING: (HWR-014)
ESD refers to the OPTIONAL static dissipative laminate used on the bench. The laminate has a
conductive under layer that comes in contact with the factory installed grounding bolts in the
worksurface. The ESD grounding kit, including the 10 ft. grounding wire must be attached and the
bench must be properly grounded to your facility earth ground. (See below for grounding
cautions!) The eyelet slips over the bolt end and the alligator clip attaches to ground. When tested
with a megohmmeter the ground bolts should test at 1 (1x106) to 1000 (1x109) in accordance with
EOS/ESD standards prescribed in EOS/ESD document S4.1-1990 Worksurfaces-Resistive
Characterization. For specific details on grounding the bench consult EOS/ESD document S6.1-1991
Grounding - Recommended Practice.
GROUNDING CAUTIONS:
1.) Ground each bench individually to ground, NEVER to each other in a continuous daisy chain.
2.) ISOLATED ground receptacles should not be used to derive an ESD ground.
3.) The green wire in a standard wall duplex can be used as a ground if it has been absolutely
determined that the green wire is attached to earth ground in your facility, thereby providing a real
earth ground.
4.) Each component of an ESD station should be connected to the same common ground point. In
other words, use only ONE of the ground bolts as a path to ground. There are 2 installed for
convenience only, or in the event you purchase a continuous resistance monitor.

7
Grounding Cautions (Continued) …………..
5.) DON’T use power tools to install the nuts for the grounding kit. HAND TIGHTEN ONLY. If you
attempt to 'spin' the ground bolt, the serrated teeth under the head of the bolt might strip the thin
conductive layer.
NOTE: If benches are moved to another location, the ground bolts in the worksurfaces should be
re-tested. Refer to EOS/ESD document S4.1-1990 Worksurfaces-Resistive Characterization for
proper testing methods. If ground has been disturbed between the bolt and the static dissipative
laminate, DO NOT OVER TIGHTEN ground bolts to achieve proper ground. If ground cannot be re-
established, loosen nuts underneath bolt and remove ground bolt from hole. It may be necessary to
hold the threads of the bolt with a small screwdriver in order to stabilize it to remove the nuts.
Paint a thin layer of CONDUCTIVE ADHESIVE or CONDUCTIVE PAINT on the small "ledge" of
conductive laminate where the bolt head rests and underneath THE HEAD of the ground bolt. Set
bolt back into the hole while liquid is still wet and test ground immediately. At the point ground is
reestablished, let the liquid dry before reattaching the ground wire.
CLEANING:
Hard surface laminate is designed to resist abrasion, scuffing, scorching, hot solder, flux and most
solvents. Intense exposure, such as from a hot soldering iron is not recommended. The surface
cleans easily with a damp cloth and soapy water. A mild chemical cleaner with no abrasive can be
used for stubborn spots. Remove glue and grease with a non flammable adhesive solvent such as
3M Scotch-Grip Solvent No. 4-F. Stains can be removed with a two minute exposure to a 5% hypo
chloride bleach solution, followed by a clean water rinse. Never wax surface, as waxes may insulate.

INDUSTRIES
Quick Value
QV AMS 925 Motorized Adjustable Bench
IAC INDUSTRIES
3831 S BULLARD AVE., GOODYEAR, AZ 85338
Phone (714) 990-8997 Fax (714) 990-0557
www.iacindustries.com
QV925 HAND CRANK ADJ. HI
REV. (042318P65)Assembly Instructions

2
Table of Contents
Page #
2 Pre-assembly Check List
3 925 Parts List
4-6 925 ADJ MOTOR BENCH Assembly Drawing
4-6 925 ADJ MOTOR Adjustable Bench Instructions
7-8 ESD Grounding
8 Cleaning
ATTENTION NOTES:
IAC Industries takes great care in the packing of its products; however damage can occur during
shipment. Check all packages and parts for any signs of damage. If damage is evident STOP and
contact the carrier that delivered your order. Request a freight claim inspector to document the
damage and begin the freight claim process.
Tools required to assemble your products are:
7/16” and 1/2” wrench or socket with ratchet. Phillips screwdriver 8” long.
Utility knife. Safety glasses and light duty protective gloves.
Power tools are NOT recommended unless they are equipped with a torque-limiting device which
can limit the torque to 10-foot lbs. maximum.
Unpack your order and separate like parts. Be careful not to damage parts as they are being moved
into position. Also be sure all parts are removed from the packing materials before these materials
are thrown away.
Locate the hardware kits and keep them in a central area. If the assembly is going to take more than
one day, all individual hardware pieces should be returned to a central location.
Check all parts and hardware kits against the itemized packing list found with the assembly
instructions. If you believe there are parts missing from your order please contact IAC Industries
customer service at 800-989-1422.
WARNING:
ALL PARTICLE BOARD USED IN IAC INDUSTRIES PRODUCTS ARE SOURCED ONLY FROM VENDORS THAT ARE CARB
ATCM PHASE 2 AND TSCA TITLE VI COMPLIANT WITH VALID CERTIFICATES.Drilling, Sawing, Sanding or Machining Wood
products can expose you to wood dust, a substance known to the state of California to cause cancer. Avoid inhaling dust generated from wood
products or use a dust mask to other safeguards for personal protection. This product can expose you to chemicals, including formaldehyde, which
is known to the state of California to cause cancer, and methanol, which is known to the state of California to cause birth defects or other
reproductive harm. For more information please visit, www.P65WARNINGS.CA.GOV/WOOD. COPY OF VENDOR CERTIFICATE AVAILABLE UPON
REQUEST.

3
Parts List: 925 Motor Adjustable Bench
(Ref. Figure 1)
Item Description Qty. Item Description Qty.
1 Work surface 1 D Bolt, ¼-20 x .750 SQH Black GR2 6
2 940 Leg Sub-Assy-Rt & Lt 1ea E Screw, 10-32 x 3.00 PHP Black 3
3 Front Support Beam 1.5H 1 F Washer, #10 Flat Zinc 4
4 930/940 Modesty Panel 1 G Nut, #10-32 Hex Keps Black 3
H Cap, 2.00 x 3.00 10-14 GA Black 4
A Bolt, ¼-20 x .750 HHW Black 11 J Floor Glide 5/16-18 x 1.75 x 1.625DIA 4
B Washer, ¼ Flat Black 31 K Screw, #6 x .500 PPH SMS Zinc 1
C Nut, ¼-20 Hex Keps Black 11 L Cable Tie, Mount Plastic (#6) 4
MCable Tie, 8” 4
P Screw, #14AB x .625 PPH SMS Black 15
1/4-20x .75 1/4-20 ¼-20 ¼-20x.75 10-32x 3L Washer #10 flat zinc
HH Bolt Flat washer Hex keps nut Bolt PHP Blk Screw
#10-32 2X3 10-14 Ga 5/16-18x1.75 #6x.500 PPH #6 Cable Tie
Nut, Hex Keps Cap, Black Floor Glide Screw SMS Zinc Mount Plastic
Cable Tie, 8” Screw, #14ABx6.25 PPH SMS Blk
CAUTION: Do not operate Adj. motor without the weight of the work surface on the frame. To do
so may cause a vacuum in the lines and possible damage to the system. Be cautious to hold the
leg assemblies together when turning workbench over after assembly making sure they do not
separate.

4
Reference Assembly Drawing below:
It may take as many as 4 people to assemble this bench.
1. Place worksurface (item 1) on clean surface underside facing up to be installed later. Install
the four floor glides (item J) and the four black bottom end cap (item H) to each end of the
leg assemblies.
2. Loosely attach front beam (item 3) to leg assemblies (item #2) using (item D) Bolt, ¼-20 x
.750 SQH Black GR2 and Washer 1/4 Flat black (item B).
3. Loosely attach modesty panel (item 4) to leg assemblies using three 1/4-20x3/4 square
head bolts (item D) in the rear slots of each of the legs (note: Square head bolts slides into
the rear of the aluminum channels) and1/4 flat washers (item B) and 1/4-20 hex nuts (item
C). Then, at the top of each end of the modesty panel is another slot that aligns with a hole
in the worksurface support at the top of each leg (item 2). Use a hex head bolt, two washers
and a hex nut to attach at each top end (items A, B, and C).

5
4. Install the Motor Cover / Pump to the back of the Modesty Panel. There are five threaded
inserts in the front of the Motor Cover that line up with five slots on the Modesty Panel.
Attachwith five 1/4-20 x .75 hex head bolts (Item A) and 1/4 flat washers (Item B).
5. Place the worksurface on top of the frame and loosely attach it to the beam and pedestal
legs as well as the three screws for the motor cover using the #14AB x .625 screws (Item P)
and 1/4 washers (Item B) screwed into the 3/16 pilot holes drilled in the bottom of the
worksurface. Do not tighten completely as some adjustment will be needed later.
NOTE: Before attaching the worksurface, make sure that the hydraulic lines and the switch
cable will not be pinched or crushed by the Modesty Panel.
6. Square the frame up on the worksurface and tighten up all fasteners. Be careful not to over
tighten as the screws may strip out.

6
7. Mount the motor switch at this point. Install the switch to the front beam using
two #10-32 screws (Item E) and #10-32 nuts (Item F) and #10 flat washers (item G).
8. Raise the leg assemblies to their highest point by using the motor control switch . Secure
the motorize pump hydraulic lines to underside of worksurface using cable mounts (items
M), cable ties (items N) and #6x.500 Phillips Screws (items L) being sure not to kink or
damage the lines in anyway.
9. Lower the bench slowly making sure to see that the pump hydraulic lines will not hang up on
anything. At this point raise and lower the bench to verify it is operating correctly.
10. When moving bench into it place be sure to lift it by the bottom base part of the leg
assemblies only. DO NOT lift it by the worksurface or the top part of the frame as this can
cause damage to the hydraulic system.

7
ESD GROUNDING:
HWR014 ESD Hardware Kit
ESD refers to the OPTIONAL static dissipative laminate used on the bench. The laminate has a
conductive under layer that comes in contact with the factory installed grounding bolts in the
worksurface. The ESD grounding kit, including the 10 ft. grounding wire must be attached and the
bench must be properly grounded to your facility earth ground. (See below for grounding
cautions!) The eyelet slips over the bolt end and the alligator clip attaches to ground. When tested
with a megohmmeter the ground bolts should test at 1 (1x106) to 1000 (1x109) in accordance with
EOS/ESD standards prescribed in EOS/ESD document S4.1-1990 Worksurfaces-Resistive
Characterization. For specific details on grounding the bench consult EOS/ESD document S6.1-1991
Grounding - Recommended Practice.
GROUNDING CAUTIONS:
1.) Ground each bench individually to ground, NEVER to each other in a continuous daisy chain.
2.) ISOLATED ground receptacles should not be used to derive an ESD ground.
3.) The green wire in a standard wall duplex can be used as a ground if it has been absolutely
determined that the green wire is attached to earth ground in your facility, thereby providing a real
earth ground.
4.) Each component of an ESD station should be connected to the same common ground point. In
other words, use only ONE of the ground bolts as a path to ground. There are 2 installed for
convenience only, or in the event you purchase a continuous resistance monitor.

8
Grounding Cautions (Continued) …………..
5.) DON’T use power tools to install the nuts for the grounding kit. HAND TIGHTEN ONLY. If you
attempt to 'spin' the ground bolt, the serrated teeth under the head of the bolt might strip the thin
conductive layer.
NOTE: If benches are moved to another location, the ground bolts in the worksurfaces should be
re-tested. Refer to EOS/ESD document S4.1-1990 Worksurfaces-Resistive Characterization for
proper testing methods. If ground has been disturbed between the bolt and the static dissipative
laminate, DO NOT OVER TIGHTEN ground bolts to achieve proper ground. If ground cannot be re-
established, loosen nuts underneath bolt and remove ground bolt from hole. It may be necessary to
hold the threads of the bolt with a small screwdriver in order to stabilize it to remove the nuts.
Paint a thin layer of CONDUCTIVE ADHESIVE or CONDUCTIVE PAINT on the small "ledge" of
conductive laminate where the bolt head rests and underneath THE HEAD of the ground bolt. Set
bolt back into the hole while liquid is still wet and test ground immediately. At the point ground is
reestablished, let the liquid dry before reattaching the ground wire.
CLEANING:
Hard surface laminate is designed to resist abrasion, scuffing, scorching, hot solder, flux and most
solvents. Intense exposure, such as from a hot soldering iron is not recommended. The surface
cleans easily with a damp cloth and soapy water. A mild chemical cleaner with no abrasive can be
used for stubborn spots. Remove glue and grease with a non flammable adhesive solvent such as
3M Scotch-Grip Solvent No. 4-F. Stains can be removed with a two minute exposure to a 5% hypo
chloride bleach solution, followed by a clean water rinse. Never wax surface, as waxes may insulate.

INDUSTRIES
Quick Value
ALL AMERICAN SERIES WORK BENCHES
IAC INDUSTRIES
3831 S BULLARD AVE., GOODYEAR, AZ 85338
Phone (714) 990-8997 Fax (714) 990-0557
www.iacindustries.com
QS Value Line DWR
REV. (042318P65)Assembly Instructions

2
Table of Contents
Page #
2 Attention Notes
3 Pre-assembly Check List
4 QV American Series Drawer Assembly (Steps 1-3)
5-6 Cylinder Lock Assembly Instructions
PLEASE NOTE:
Quick Ship Accessories include assembly instructions
in their own packaging when packed by individually.
Please look for these instructions while unpacking.
ATTENTION NOTES:
IAC Industries takes great care in the packaging of its products; however damage
can occur during shipment. Check all packages and parts for any signs of damage. If
damage is evident STOP and contact the carrier that delivered your order. Request a
freight claim inspector to document the damage and begin the freight claim process.
Tools required to assemble your QV American Series BENCH products are:
7/16” and 1/2” wrench or socket with ratchet.
Phillips screwdriver 8” long.
Utility knife.
Safety glasses and light duty protective gloves.
NOTE: Power tools are NOT recommended unless they are equipped with a torque
limiting device which can limit the torque to 10 foot lbs maximum at aluminum
attachment points, and 15 foot lbs maximum for all other attachment points.
Unpack your order and separate like parts into separate areas. Be careful not to
damage parts as they are being moved around and put into position. Also be sure all
parts are removed from the packing materials before these materials are thrown
away.
Locate the hardware kits and keep them in a central area. If the assembly is going to
take more than one day, all individual hardware pieces should be returned to a
central location.

3
Check all parts and hardware kits against the itemized packing list found with the
assembly instructions. If you believe there are parts missing from your order please
contact IAC Industries customer service HOTLINE at 800-989-1422.
WARNING:
ALL PARTICLE BOARD USED IN IAC INDUSTRIES PRODUCTS ARE SOURCED ONLY FROM VENDORS THAT
ARE CARB ATCM PHASE 2 AND TSCA TITLE VI COMPLIANT WITH VALID CERTIFICATES.Drilling, Sawing, Sanding
or Machining Wood products can expose you to wood dust, a substance known to the state of California to cause cancer. Avoid inhaling
dust generated from wood products or use a dust mask to other safeguards for personal protection. This product can expose you to
chemicals, including formaldehyde, which is known to the state of California to cause cancer, and methanol, which is known to the state
of California to cause birth defects or other reproductive harm. For more information please visit, www.P65WARNINGS.CA.GOV/WOOD.
COPY OF VENDOR CERTIFICATE AVAILABLE UPON REQUEST.
PRE ASSEMBLY CHECK LIST
Your bench has been carefully packed at the factory to prevent damage during shipment. Unpack all parts
and examine them for damage. Contact your freight carrier for freight claims information if your order was
shipped "freight collect" or "pre-pay and add". Contact IAC Industries at 800 989-1422 if parts are missing.
TOOLS NEEDED: Power or hand held Phillips head screwdriver with #2 tip, 7/16" and 1/2" combination
wrench or thin wall sockets.
Single Drawer
Bolt, ¼-20 X 1.00 HH BLK 1/4 Flat Washer 1/4-20 Captive Tinnerman 1/4-20 Hex Keps BLK
#14 X 1.00 PPH Screw Screw, ¼-20 X .500 PPH “F” BLK
Screw, ¼-20 X .500 PPH “F” BLK
HARDWARE KIT QV-HWR4015 QTY
A Bolt, ¼-20 X 1.00 HH BLK 4
B 1/4 Flat Washer 12
C 1/4-20 Captive Tinnerman 2
D 1/4-20 Hex Keps BLK 4
E #14 X 1.00 PPH Screw 2
F Screw, ¼-20 X .500 PPH “F” BLK 2
G Nut, ¼-20 Unistrut Long Spring N-2-4 4
H Brkt, DWR Hanger 3.00X12.00L VL 1

4
STEP #2
STEP #3
STEP #3
STEP #1
Note: Applies to all drawer and suspended cabinet configurations.
It is best to install drawer bracket and drawer(s) while bench in upside down.
Step 1:
Install rear mounting bracket to worksurface as shown on below using hardware listed above.
Note: The position of your bracket will be determined by the size of your front beam. Remove drawer from
drawer case by pulling the drawer body out of the case. Locate the slide release tabs. Lift up on the left side
tab and press down on the right side tab and pull on drawer body.
Step 2: Install the captive retainer nuts onto the bench front beam as shown below.
Step 3: Finish the drawer assembly as shown below using ¼-20 X 1.00 HH bolts and ¼ flat black washer
(items A & B) for the connection of the support beam and drawer case. Using items (F & B) for the connection
of the back of the drawer case and the drawer hanger bracket (H).

5
Cylinder Lock Bill Of Materials
Lock Retainer Lock Body Two Keys
Lock Bill of Materials
Description Qty
Lock Retainer 1
Lock Body 1
Set Of Lock Keys 1
This manual suits for next models
3
Table of contents
Other IAC INDUSTRIES Tools Storage manuals
Popular Tools Storage manuals by other brands

Hilka
Hilka HDPT106 Assembly instructions

HOLZMANN MASCHINEN
HOLZMANN MASCHINEN WB162L Assembly instruction

General International
General International Excalibur 40-100 Setup & operation manual
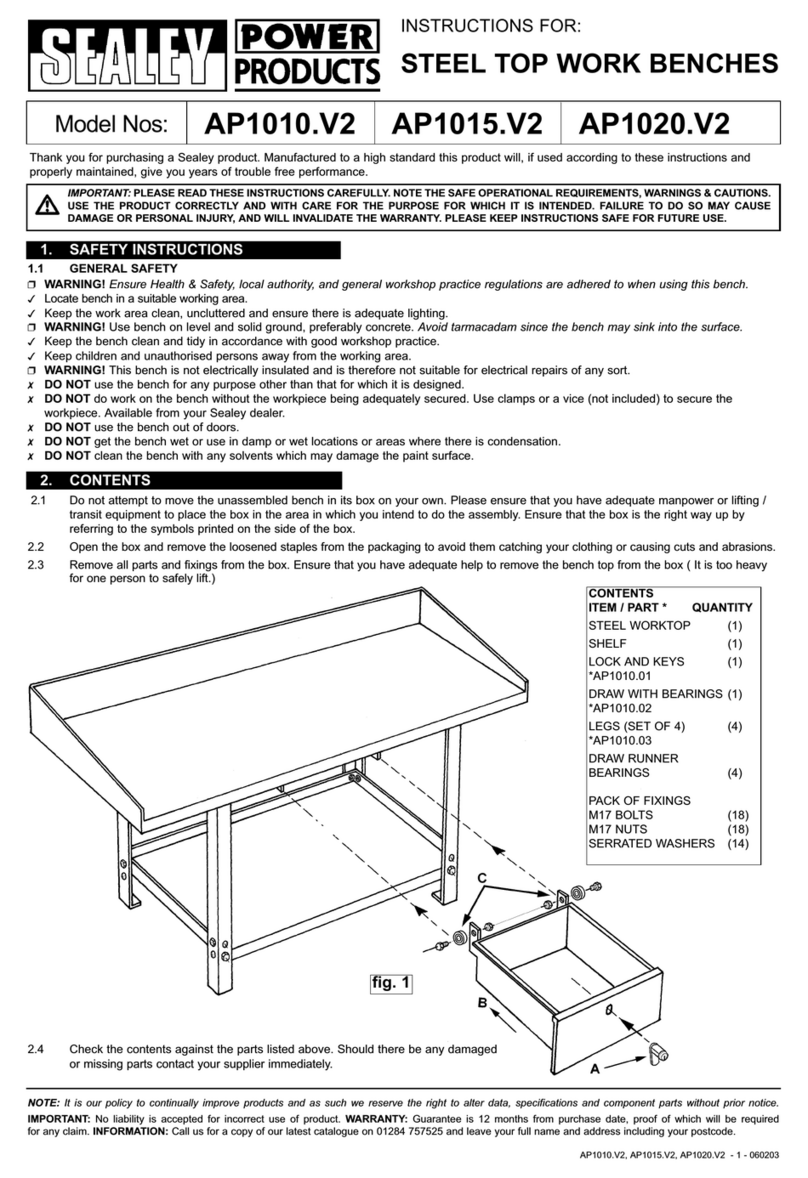
Sealey
Sealey POWER PRODUCTS AP1010.V2 instructions
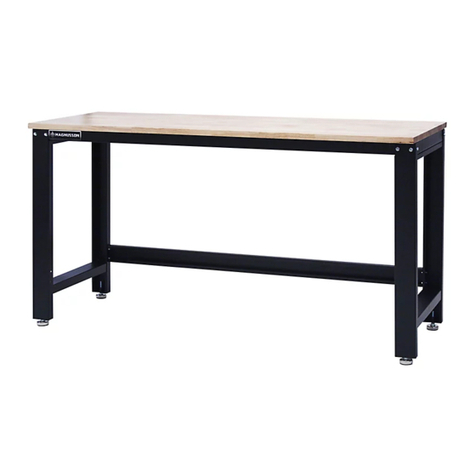
Magnusson
Magnusson MFWB001 manual
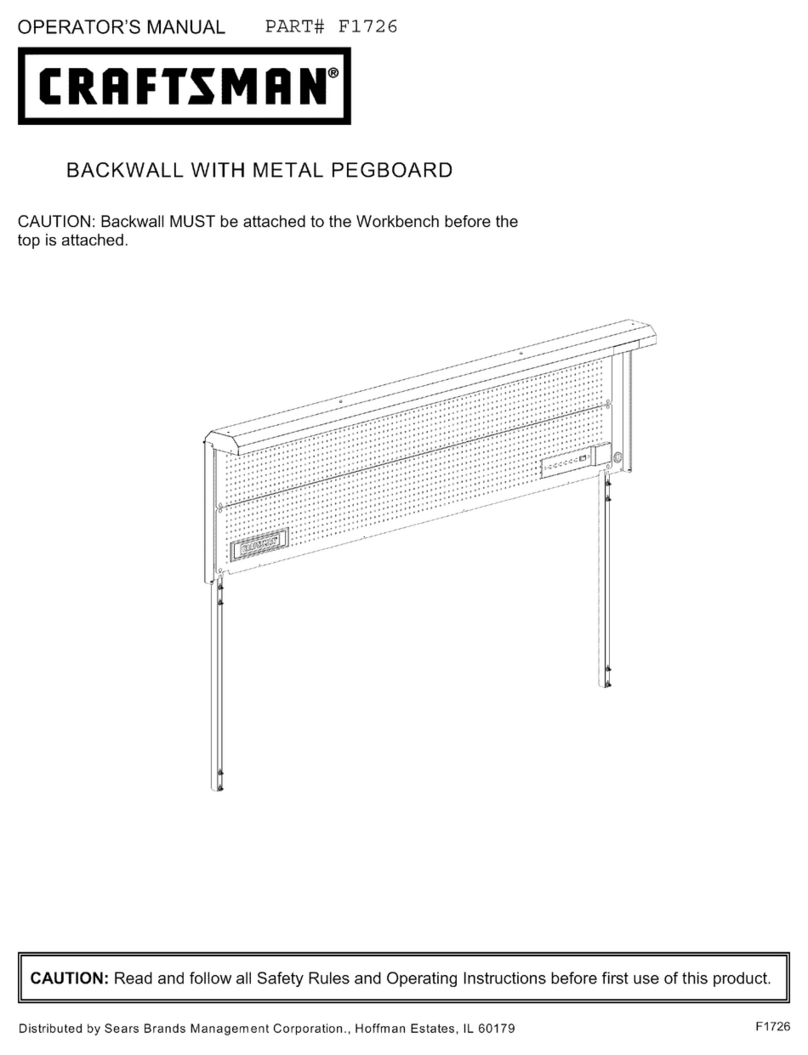
Craftsman
Craftsman F1726 Operator's manual