IDD Processing & Packaging SQUIRE PLUS 2 User manual

PROCESS &PACKAGING, INC.
Address: 5450 Tech Circle, Moorpark, CA 93021 Tel: (805) 529-9890 Fax: (805) 529-9282
CREATED: May 29, 2015
REVISION: 1.3
SQUIRE “PLUS 2”
2-HEAD WASHER /FILLER
OPERATIONS MANUAL
(Image shows Fill-by-Weight and Double-Doser options)

SQUIRE PLUS 2OPERATIONS MANUAL
TABLE OF CONTENTS
INTRODUCTORY STATEMENTS
1. PREFACE .......................................................................................................................... 4
2. DISCLAIMER ..................................................................................................................... 4
3. CONFIDENTIALITY AND COPYRIGHTS .......................................................................... 4
SAFETY
4. OPERATIONAL SAFETY NOTES ..................................................................................... 5
SYSTEM PROCEDURES & OPERATIONS
5. SERVICES ......................................................................................................................... 6
SQUIRE “PLUS 2” SERVICES ............................................................................................................. 6
SQUIRE “PLUS 2” DRAINAGE ............................................................................................................. 7
DOUBLE DOSER UNIT OPTION .......................................................................................................... 9
SUGGESTED COMPONENTS .............................................................................................................. 10
6. SPECIFICATIONS ............................................................................................................. 14
7. CYCLE TIMES ................................................................................................................... 15
8. SIMPLIFIED START–UP AND SHUT–DOWN PROCEDURES ......................................... 16
9. KEG WASHING & FILLING PROCEDURES ..................................................................... 17
KEG WASHING .................................................................................................................................. 17
END OF DAY CLEANING ................................................................................................................... 25
KEG FILLING .................................................................................................................................... 26
10. CLEANING IN PLACE (CIP) PROCEDURE ...................................................................... 35
CIP SEQUENCE –PRODUCT FILLING SIDE ......................................................................................... 35
EXTERIOR CLEANUP ........................................................................................................................ 36
11. PLANNED MAINTENANCE ............................................................................................... 37
12. QUALITY CONTROL ......................................................................................................... 38
KEG LINE QUALITY ASSURANCE ....................................................................................................... 40
13. OXINE CLEANING/SANITIZING ....................................................................................... 41
OXINE DILUTION AND USE ................................................................................................................ 41
OXINE &PUROGENE SANITIZER SUGGESTED USES ........................................................................... 42
CIO2ACTIVATION ............................................................................................................................ 45
OXINE MATERIAL SAFETY DATA SHEET ............................................................................................. 46
SYSTEM DETAIL INFORMATION
14. PLANT LAYOUT ............................................................................................................... 52
15. FLOW DIAGRAM ............................................................................................................... 53
16. ELECTRICAL .................................................................................................................... 54

SQUIRE PLUS 2OPERATIONS MANUAL
17. MECHANICAL ................................................................................................................... 56
EURO &AMERICAN SANKEY KEG VALVE FLOWS ............................................................................... 56
ARES VALVE –INSTALLATION &MAINTENANCE MANUAL ................................................................... 57
PROCESS VALVE ............................................................................................................................. 60
SOLENOID VALVE ............................................................................................................................. 61
PINCH VALVE .................................................................................................................................. 62
TANK DOSING UNIT .......................................................................................................................... 63
FLOAT VALVE WITH PROPORTIONER ................................................................................................. 65
ADJUSTABLE SINGLE STAGE INJECTORS ........................................................................................... 68
DETERGENT PUMP –NPE/NPE-F INSTRUCTION MANUAL................................................................... 69
PRODUCT PUMP –OPERATION MAINTENANCE,&PARTS LIST ............................................................ 77
18. PNEUMATICS .................................................................................................................. 108
19. DIMENSIONS ................................................................................................................... 109
20. I/O LISTING ....................................................................................................................... 110
GENERAL INFORMATION
21. APPENDICES .................................................................................................................... 112
Appx. A IDENTIFYING AND ANALYZING PROBLEMS .............................................................. 112
Appx. B COMPLETE KEG WASHING & FILLING SEQUENCE CONTROL PROCESSES ....... 118
Appx. C SPARE PARTS ................................................................................................................ 122
Appx. D PROGRAM LISTING ....................................................................................................... 125
Appx. E TRAINING ........................................................................................................................ 125
Appx. F WHICH MASK SHOULD I WEAR? .................................................................................. 125

SQUIRE PLUS 2OPERATIONS MANUAL
PROCESS & PACKAGING, INC. PAGE 4OF 125
www.iddeas.com
INTRODUCTORY STATEMENTS
1. PREFACE
This system has been designed as a self-contained and reliable automatic keg processing
machine. Although kegs are loaded and unloaded manually, all washing, sanitizing, and filling
operations are fully automatic for consistent high quality results.
The information, instructions, and warnings contained in this document have been prepared to
clarify operational and maintenance procedures. If followed carefully, they should provide safe,
long, and reliable service from the machine.
Proper maintenance and the use of approved spare parts will extend the life of the system and
its reliability, while the use of any non-approved spare parts may void any warranties or
guarantees; actual or implied.
2. DISCLAIMER
The customer assumes all responsibility for the system, once delivered. The system is tried and
tested equipment, and as such, IDD Processing & Packaging will not be held responsible for
alterations and modifications carried out by anyone, without the written approval of IDD
Processing & Packaging.
3. CONFIDENTIALITY AND COPYRIGHTS
All information contained within this document is confidential and the copyright of IDD Process
& Packaging, Inc. No portion of this data shall be released, disclosed, used, or duplicated for
use in procurement or manufacturing, without the express written permission from IDD Process
& Packaging, Inc.
Back To TOC

SQUIRE PLUS 2OPERATIONS MANUAL
PROCESS & PACKAGING, INC. PAGE 5OF 125
www.iddeas.com
SAFETY
4. OPERATIONAL SAFETY NOTES
EMERGENCY STOP / MANUAL PROCESS STOPS
To STOP the process sequence at any time for each of the process heads, use the Manual
Stop Process Buttons, located on the system Control Panel.
VENTILATION
The work area should have adequate ventilation approved for use by your Safety and
Operational Procedures Committees. Respirators should be used during cleaning and other
operations where fumes are present.
Refer to APPENDIX F–WHICH MASK SHOULD IWEAR?
WEAR SAFETY GOGGLES
Wear Safety Goggles approved for use by your Safety and Operational Procedures Committees
when operating or observing this system.
WEAR CHEMICAL RESISTANT GLOVES & APRON
Wear Chemical Resistant Gloves and Apron approved for use by your Safety and Operational
Procedures Committee.
WEAR BACK SUPPORT EQUIPMENT
Wear Back Support Equipment and use proper lifting technique as approved by your Safety
and Operational Procedures Committees.
Note: Use only the proper lifting equipment for full kegs, as they weigh up to 165 lbs.
Back To TOC

SQUIRE PLUS 2OPERATIONS MANUAL
PROCESS & PACKAGING, INC. PAGE 6OF 125
www.iddeas.com
SYSTEM PROCEDURES &OPERATIONS
5. SERVICES
SQUIRE “PLUS 2” SERVICES
LINE SUPPLY PRESSURE FLOW RATE CONSUMPTION CONNECTION
1
*
CO2/N230 PSIG 20 SCFM 1.75 SCFM 3/4" N/B Hose
2
*
AIR PURGE 22.23 PSIG
20 SCFM 1.25 SCFM 3/4" N/B Hose
3 (Ambient) WATER 55 PSIG 15 GPM 1.5 SCFM 3/4" N/B Hose
4 (Ambient) WATER 55 PSIG 15 GPM Top Up 1/2" NPTM
5
*
AIR 80 PSIG 2.5 SCFM 0.25 SCFM 1/4" NPTM
6 ELECT. -- -- 208V-240V-1PH-50/60Hz-35A --
7 CAUSTIC -- -- Dosing at 2% V/V 1/4" OD Tubing
8 PRODUCT 15 PSIG 20 GPM 7.5 GPM 1-1/2" TC
9 OXINE -- -- Dosing Nominal 50 ppm 1/4" OD Tubing
10 (Option) ACID -- -- Dosing at 0.5% V/V 1/4" OD Tubing
11 CIP RETURN -- 10 GPM -- 3/4" N/B Hose
12 FILL DRAIN -- -- -- 3/4" N/B Hose
6
3
9
2
1
8
10
74
5
12
11
Back To TOC
*
Customer to provide suggested
components. Refer to Page 8,
Suggested Components
.

SQUIRE PLUS 2OPERATIONS MANUAL
PROCESS & PACKAGING, INC. PAGE 7OF 125
www.iddeas.com
SQUIRE “PLUS 2” DRAINAGE
Page 8

SQUIRE PLUS 2OPERATIONS MANUAL
PROCESS & PACKAGING, INC. PAGE 8OF 125
www.iddeas.com
PREVENTING BACK PRESSURE IN DRAIN LINES
The following model is the IDD suggested method of process and packaging plant drainage for designated non-wet area locations to
prevent back pressure within the drain lines. This method allows enough air-behind-water to prevent backups with 3/4" drain pipes to
enter a 2” PVC drain.
Back To TOC

SQUIRE PLUS 2OPERATIONS MANUAL
PROCESS & PACKAGING, INC. PAGE 9OF 125
www.iddeas.com
DOUBLE DOSER UNIT OPTION
DOUBLE DOSER UNIT OPTION #: MS 50030
DETERGENT TANK LOWER BLEED VALVE :
LEAK RATE: 3 GAL. (11.4 LITERS) PER HOUR
ALLOWS FOR THE AUTOMATIC REFRESHING
OF CAUSTIC OR ACID DOSING.
-
-
DOSERS TO DOSE ACID AND CAUSTIC INTO
THE DETERGENT TANK FOR ALTERNATING
-
YOUR KEG WASHING REGIME IN ORDER TO
RID KEGS OF HEAVY PROTEINS AND CALCIUM
BUILD UP.
ISOLATING VALVE (CHANGEOVER BY OPENING
AND CLOSING FROM CAUSTIC AND ACID)
NOTE:
SQUIRE "PLUS 2" SYSTEM SHOWN.
Back To TOC

SQUIRE PLUS 2OPERATIONS MANUAL
PROCESS & PACKAGING, INC. PAGE 10 OF 125
www.iddeas.com
SUGGESTED COMPONENTS
Water, oil, and random particles are the natural enemies of perfectly prepared compressed air. They will
have an adverse effect on components and cost additional energy. In order to improve process reliability
and machine availability, start by first analyzing the compressed air supply in detail from source.
IDD suggests the following equipment be included in your Purge Air and Inert Gas Regulator
configurations. They are available at www.Grainger.com.
1” NPT AIR REGULATOR
(1 ea. For Air Purge & CO2/N2)
Grainger Item # 4ZM10
•1” NPT
•Adjustment Range 5 to 125 PSI
(Set to 30 PSI, 2 Bar for CO2/N2)
(Set to 22-23 PSI, 1.55 Bar for Air)
•¼” NPT (Female) Gauge Port
PRESSURE GAUGE
(1 ea. For Air Purge & CO2/N2)
Grainger Item # 33HP99
•0 to 60 PSI
•2” Dial
•¼” (Male) NPT Inlet, Back
RELIEF (SAFETY VALVE)
(1 ea. For Air Purge & CO2/N2)
Grainger Item # 15X911
•60 PSI Preset Setting
•½” (Male) NPT Inlet
¼” NPT AIR REGULATOR
(1 ea. For Control Air)
Grainger Item # 4ZM18
•¼” NPT
•Adjustment Range 5 to 150 PSI
(Set to 80 PSI, 5.8 Bar)
•¼” NPT (Female) Gauge Port
PRESSURE GAUGE
(1 ea. For Air)
Grainger Item # 33HR23
•0 to 100 PSI
•2 ½” Dial
•¼” (Male) NPT Inlet, Back
AIR SUPPLY (AIR COMPRESSOR)
Grainger Item # 4ME99
•Electric
•175 PSI Max. Pressure
•5 HP
•2 Stage
•208-230/460V / 3Phase / 60 Hz
/ 13.4-13.2 A
•60 Gallon Tank (Vertical)
•¾” NPT (Female) Outlet

SQUIRE PLUS 2OPERATIONS MANUAL
PROCESS & PACKAGING, INC. PAGE 11 OF 125
www.iddeas.com
CO2AND LOW PRESSURE (PURGE)AIR
• It is suggested that 1" regulators are fitted within 10 feet of the machine and a 3/4" or 1” I/D line
is run between the regulator and machine.
• A minimum 3/4" supply line set at 100 PSIG should run to the 1” regulators stated above.
AIR CONTROLS
3/8” minimum supply line at 100 PSIG and regulated to 80 PSIG at the machine.
NOTE: You MUST use an air dryer on your air supplies to the machine, to prevent pre-lubricated pneumatic
equipment from seizing up due to moisture condensation. In all instances a water separator is NOT
sufficient to ensure dry oil-free air.

SQUIRE PLUS 2OPERATIONS MANUAL
PROCESS & PACKAGING, INC. PAGE 12 OF 125
www.iddeas.com
Dryers
An Air Dryer will remove moisture from compressed air to a certain
degree of dryness and this is referred to as Pressure Dew Point.
Different types of dryers can achieve different dew points and, for the
most part, the drier the air needs to be, the more expensive it is to dry.
Refrigerated Dryers condense the moisture out of the air and
drain it away as liquid. They are limited to about 35° F because
the water freezes if it gets colder
Desiccant Dryers adsorb the moisture in the compressed air and
remove it while it’s still suspended as vapor. They are typically
applied at about -40° F, but may reach below to -100° F
Membrane Dryers use permeability to separate the moisture from
the air and can also achieve low dew points
The selection is made based on personal preferences, the dryness required,
and the affordable cost, which should include such things as operating,
electrical, and/or utility bills.
Reproduced in part from the web site of:
Gulf Atlantic Equipment, Co., Jacksonville, Florida. 904-636-8555 Fax: 904-636-8554 © 2006
Back To TOC

SQUIRE PLUS 2OPERATIONS MANUAL
PROCESS & PACKAGING, INC. PAGE 13 OF 125
www.iddeas.com
Back To TOC

SQUIRE PLUS 2OPERATIONS MANUAL
PROCESS & PACKAGING, INC. PAGE 14 OF 125
www.iddeas.com
6. SPECIFICATIONS
Output is subject to keg size, keg valve style, and wash sequence used.
Use the charts below as an internal reference by inserting your specific optimum and
acceptable values. This becomes the bench mark in the future of your production.
Changes in operating personnel, valves, wash sequences, and mechanical integrity can be
tracked with this bench-marking as well.
Date:
Keg Size:
Valve Style:
Kegs/Hour:
Special Notes:
Date:
Keg Size:
Valve Style:
Kegs/Hour:
Special Notes:
Date:
Keg Size:
Valve Style:
Kegs/Hour:
Special Notes:
Date:
Keg Size:
Valve Style:
Kegs/Hour:
Special Notes:
Date:
Keg Size:
Valve Style:
Kegs/Hour:
Special Notes:
Back To TOC

SQUIRE PLUS 2OPERATIONS MANUAL
PROCESS & PACKAGING, INC. PAGE 15 OF 125
www.iddeas.com
7. CYCLE TIMES
SQUIRE “PLUS 2” SEQUENCE TIMES
Oxine Machine With Allen Bradley PLC
WASH HEAD REGULAR SEQUENCE LONG SEQUENCE
Wash Water Pre-soak 3 sec. 3 sec.
Air Purge Pre-soak Event Event
Wash 1 Water (pulse on long seq.) 7.5 sec. 15 sec.
Low Flow Wash 1 (pulse on long seq.) 7.5 sec. 15 sec.
Air Purge Event Event
Wash 2 Detergent (Pulsed Wash) 15 sec. 30 sec.
Low Flow Wash 2 15 sec. 30 sec.
Air Purge Event Event
Wash 3 Water (Pulsed Wash) 7.5 sec. 7.5 sec.
Low Flow Wash 3 10 sec. 10 sec.
Wash 3 fill 3 sec. 3 sec.
Sterilize Hold 10 sec. 10 sec.
Depressurize 5 sec. 5 sec.
CO2purge 10 sec. / Event 10 sec. / Event
CO2pressurize 2.5 sec. 2.5 sec.
FILL HEAD REGULAR SEQUENCE LONG SEQUENCE
Product Event Event
Gas Scavenge 4 sec. 4 sec.
De-pressurize time 2 sec. 2 sec.
FILL HEAD OUTPUT REGULAR SEQUENCE LONG SEQUENCE
5 gallon and 20 liter kegs Up to 30 per hour Up to 22 per hour
¼ barrel and 30 liter kegs Up to 28 per hour Up to 20 per hour
½ barrel and 50 liter kegs Up to 25 per hour Up to 17 per hour
NOTE: Output is subject to keg, keg valve style, and wash sequence used.
Back To TOC

SQUIRE PLUS 2OPERATIONS MANUAL
PROCESS & PACKAGING, INC. PAGE 16 OF 125
www.iddeas.com
8. SIMPLIFIED START–UP AND SHUT–DOWN PROCEDURES
Refer to Sections #9 and #10 for more detailed steps.
START UP
1. Turn on the CONTROL power supply
2. Open fresh water supply to STERILANT DOSING UNIT
3. Fill the DETERGENT TANK with cold or 120°to 150°F fresh water and dose with 2% v/v Caustic or a
50/50 blend of Phosphoric/Nitric cleaning agent at 0.3-0.5% v/v. If using cold water, turn on Heater
to bring temperature up to required temperature. (120°to 150°F)
4. Turn on the Machine Control Air, Air Purge, CO2 or Nitrogen and Product supplies
5. Start the DETERGENT PUMP
6. Connect the wash coupler to a Keg (ensure any Cap is removed first) and place inverted Keg onto
the wash platform
7. Push washer START button and wait for process to complete
8. Disconnect the WASH COUPLER and replace it on the CLEANING CUP
9. Remove Keg and replace with another
•After the first Keg has been processed on the wash and fill heads, reject it and do not allow it to
enter the full Keg warehouse. This will ensure that all the Machine systems were properly
primed prior to commencing production
SHUT DOWN
Perform these steps after the last keg has been processed and all work is completed for the day.
1. Turn off DETERGENT PUMP and STERILANT supply
2. Turn off the machine water, CO2or Nitrogen, Air purge, and Product supplies
3. Place the FILL CONNECTION HEAD into the CLEANING CAP and tighten clockwise
4. Empty DETERGENT TANK
5. Clean with CIP and outer surfaces washing
NOTE: See Section 21, Appx. B – Complete Keg Washing & Filling Sequence Control
Processes for full operations instructions.
Back To TOC

SQUIRE PLUS 2OPERATIONS MANUAL
PROCESS & PACKAGING, INC. PAGE 17 OF 125
www.iddeas.com
9. KEG WASHING & FILLING PROCEDURES
This section demonstrates the customer operation, without the PLC processes, so that Operator-only
commands are clear. If you need trouble-shooting help to understand what is going on with the valves
and PLC control, specifically, then you need to read APPX B – COMPLETE KEG WASHING &FILLING
SEQUENCE CONTROL PROCESSES.
WARNING: DO NOT Hose Down Electrical Equipment Areas!
This includes the pump motors, control panels, and electrical terminal boxes
Daily washing of the detergent tank and pipes removes scum, scale, or any residuals that may have
formed on the interior.
KEG WASHING
The wash cycle lengths may be selected from the Sequence Select switch, located on the side of the
Control Panel. For specific Cycle Times, see Section 7. Unless specified otherwise, the washes are
performed with High Flow, which sprays the inside of the kegs.
You may wash a keg at the same time as you fill a keg, as the two systems are entirely separate.
In order to control condensates and deposits, IDD suggests that you switch from Acid (0.5%) to Caustic
(2%) every other month, as they may not be used simultaneously. This removes scum, scale, or any
residuals that may have formed on the interior of the keg.
Important: If this is the first time you are using the Squire system after shipment, perform a
CIP to ensure that the filling side is clean and sanitized. See Section 10 - CIP.
The entire wash process happens very quickly. Most of the valve switching and
indicator light changes will occur too fast to follow until you are used to it.
If the system stops working at any time during washing or filling, refer to the
Rejected Keg Occurrence, page 34.
1. Check that services are hooked up correctly
CO2and Purge at 22-23 psig, Control Air at 80 psi, and Water at 15 gpm with 40-60 psi
2. Supply power to the system (208-240v, 1 PH, 60 Hz, 35 Amps)

SQUIRE PLUS 2OPERATIONS MANUAL
PROCESS & PACKAGING, INC. PAGE 18 OF 125
www.iddeas.com
3. Turn on the machine air, air purge, CO2or Nitrogen, and Product supply
4. Set up the wash tank for either Acid or Caustic detergent concentrations:
•Acid: 50/50 blend of Phosphoric/Nitric cleaning agent at 0.3-0.5% v/v
•Caustic: 2% v/v Caustic
Dual-Doser Option shown
5. Prepare the Detergent Tank with clean water:
a. Fill tank with water (or fill with 120°to 150°F water)
b. Turn on tank heater at Motor Control Panel (Top)
c. Set the Heater temperature gauge between 135-155°F (light remains lit while heating)
6. Open fresh water supply to Sterilant Dosing Unit
7. Connect bucket/container of Activated Oxine solution to manifold water dosing pipe
Refer to the setup information provided in Section 12 – OXINE CLEANING/SANITIZING

SQUIRE PLUS 2OPERATIONS MANUAL
PROCESS & PACKAGING, INC. PAGE 19 OF 125
www.iddeas.com
8. Set Sequence Select knob on side of Control Panel to 1(Short wash), or 2(Long wash), for dirtier kegs
The Long Wash rinses and cleans for longer than the Short Wash (See SECTION 7–CYCLE TIMES)
9. Wait for water to be heated within the required range before continuing
10. Prepare the keg:
a. Set keg upright on ground (remove any keg cap, if necessary )

SQUIRE PLUS 2OPERATIONS MANUAL
PROCESS & PACKAGING, INC. PAGE 20 OF 125
www.iddeas.com
b. Lean keg top against padded rack bar
c. Pull the wash coupler off the cleaning cup and attach to the keg
•Half-turn counter-clockwise and lift, then push with a half-turn clockwise to secure
d. Push the fill handle fully down, into lock position (Handle fully down opens to keg)
•Pull trigger and depress the handle fully, until it’s in the locked down position, then release
e. Flip keg over and place upside-down onto the wash platform
Table of contents
Popular Brewing System manuals by other brands

BRAVILOR BONAMAT
BRAVILOR BONAMAT Bolero 20 operating instructions
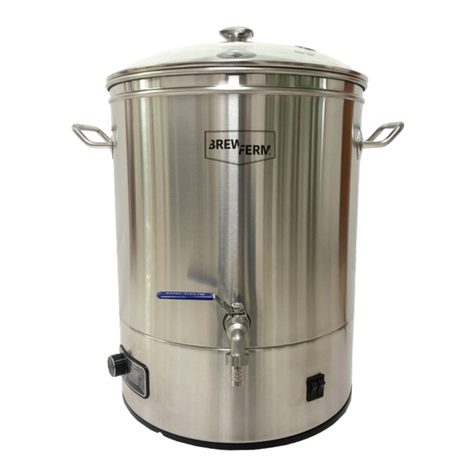
BREWFERM
BREWFERM 057.089.5 user guide
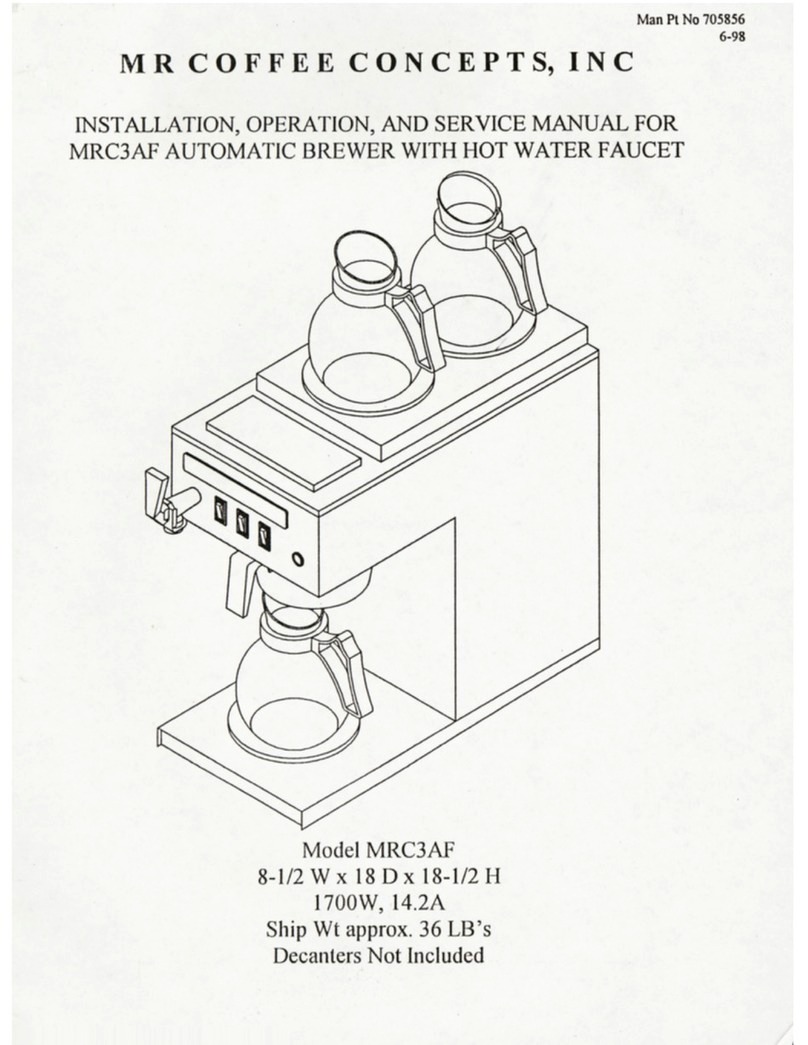
Mr Coffee Concepts
Mr Coffee Concepts MRC3AF Installation, operation and service manual
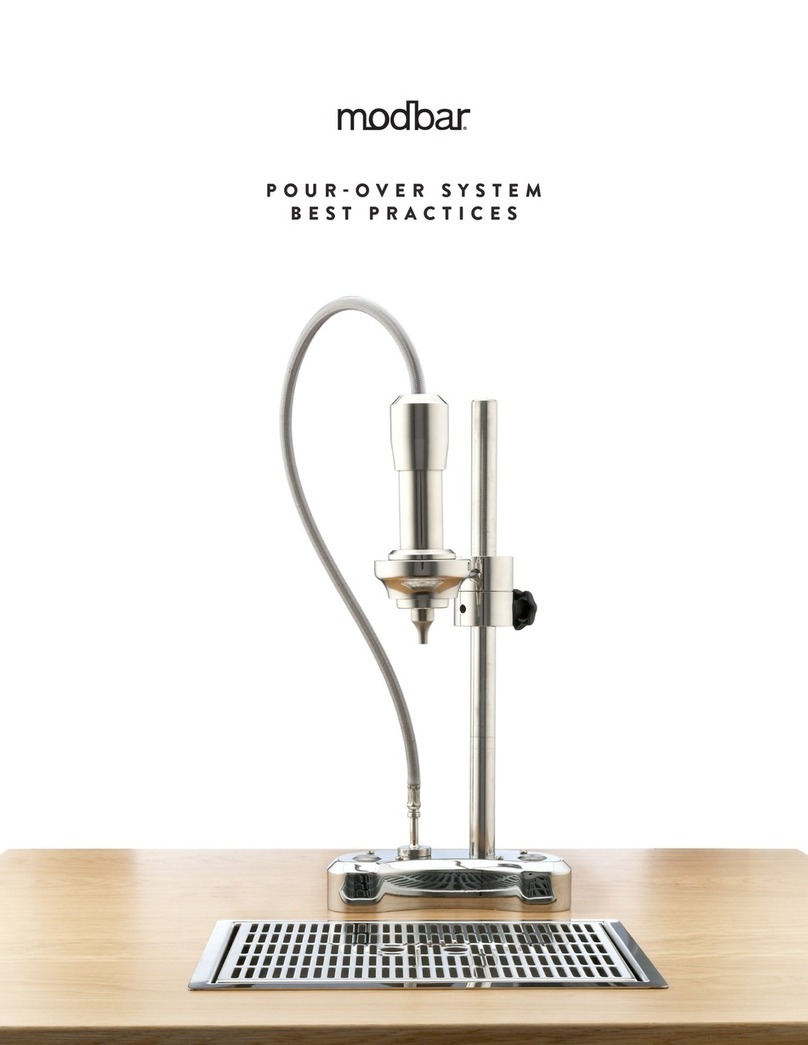
modbar
modbar Pour-Over How-to guide
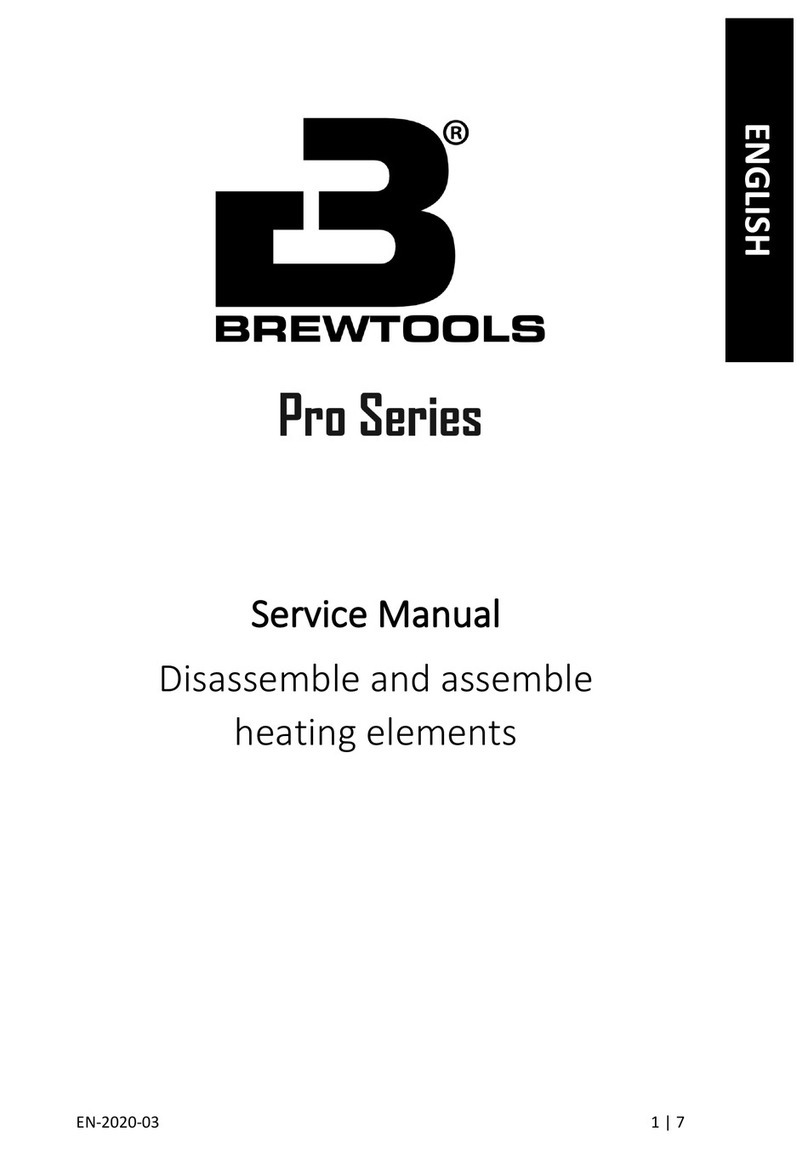
Brewtools
Brewtools Pro Series Service manual
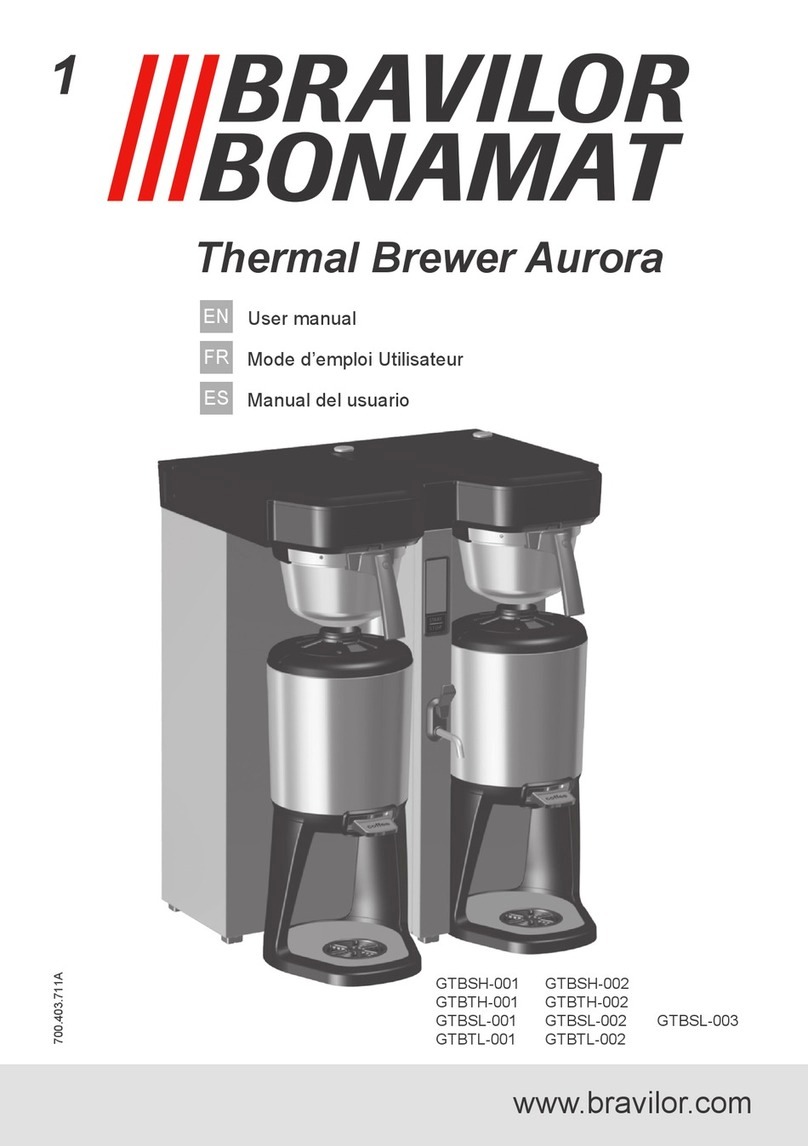
BRAVILOR BONAMAT
BRAVILOR BONAMAT Aurora GTBSH-001 user manual