Idex MICROPUMP EagleDrive MS Instruction Manual

1
DOC No: 8540 REV D
INSTALLATION, OPERATION AND WARRANTY INFORMATION
EaglEDrivETM
EagleDriveTM MS
EagleDriveTM EL
Without Enclosure
Without Enclosure

2
DOC No: 8540 REV D
PUBLISHED BY
MICROPUMP INC.
A Unit of IDEX Corporation
December 2012 © Micropump Inc.
All rights reserved.
This manual contains proprietary information which is protected by copyright.
No part of this publication may be reproduced, transcribed, stored in a retrieval system,
translated into any language (including computer language), or transmitted in any
form without the written consent of the publisher. For further information contact your
local Micropump distributor. Every effort has been made to ensure that the information
contained in this manual is accurate prior to printing. However, the products described
in this manual are subject to continuous development and improvement and Micropump
shall not be liable for any errors contained herein or for incidental or consequential
damages in connection with the furnishing, performance, or use of this manual.

3
DOC No: 8540 REV D
STANDARD LIMITED WARRANTY
The products manufactured by Micropump Incorporated are warranted to be free
from defects in workmanship and material at the time of shipment from the place of
manufacture. Micropump will repair or replace, at its option, any part or component which
fails to conform to this warranty for a period of one year. Micropump’s obligation under
this warranty is limited to the repairs or replacement of defective equipment returned to
Micropump on an F.O.B. destination and freight-prepaid basis. All normal wear and tear
is excepted, and product is subject to examination at Micropump to verify that the parts or
components were defective at the time of sale.
For the purposes of the limited warranties, the “Stator/Controller Assembly” means
only the stator and the printed circuit board and electronic components contained in
the controller housing, plus the connecting control and power cables. The “Power
Supply Assembly” means only the printed circuit board and the electronic or mechanical
components located inside or on the power supply enclosure and the “Pump head
Assembly” means all other parts of the product, including but not limited to, the rotor.
No warranty of any kind is made or shall be imposed with respect to any pump or parts
(1) that have not been properly installed and tested in operation, (2) that have been
subject to misuse, negligence, acts of God or the elements, or any other form of casualty,
or (3) that have been repaired or altered outside Micropump’s facility in a way, so as, in
our judgment, to affect performance or reliability.
The parties agree that the buyer’s sole and exclusive remedy against Micropump shall
be for repair or replacement of defective parts under the conditions stated above. The
buyer agrees that no other remedy (including but not limited to incidental or consequential
damages for lost prots, lost sales, loss of use, injury to person or property, or any other
incidental or consequential loss) shall be available to them.
This warranty shall not apply to prototype pumps, experimental pumps, or brush-type
electric motors. Warranty of equipment or accessories from outside sources, purchased
by Micropump and incorporated into Micropump’s product is subject to the manufacturer’s
standard warranty, unless specically agreed otherwise between Micropump and buyer.
A copy of the warranty on the aforementioned equipment is available on request.
The adjustment or replacement of defective parts made under this warranty will not
extend the original warranty period.
THE WARRANTY DESCRIBED ABOVE IS THE EXCLUSIVE
MICROPUMP WARRANTY AND IS IN LIEU OF ALL OTHER
WARRANTIES, EXPRESSED OR IMPLIED, INCLUDING ANY
WARRANTY OF MERCHANTABILITY OR FITNESS FOR A
PARTICULAR PURPOSE OR ANY WARRANTY PREVIOUSLY
ISSUED. WE NEITHER ASSUME NOR AUTHORIZE ANY PERSON
TO ASSUME FOR US ANY OTHER LIABILITY IN CONNECTION
WITH THE SALE OR USE OF OUR EQUIPMENT.

4
DOC No: 8540 REV D
represents years of uid handling experience and we feel it is the nest product available
of its type.
The product you have purchased was designed and constructed for use within designated
limits and conditions. Staying within performance limits and following the guidelines given
in this manual will result in excellent performance and maximum life.
Should you have a question or a problem, technical assistance is available worldwide.
Micropump products are designed for easy eld servicing with service kits and technical
support available for all products.
The Purpose of this Guide...
is to provide information to enable suitably qualied technicians and tters to install,
operate and maintain the Micropump EagleDrive and common pump/motor combinations.
Use the Guide...
when you have purchased a motor or pump/motor combination. This guide contains
specic information for installation, operation, and maintenance of the EagleDrive and
references some of the most common pump/motor combinations. This guide should
be read in conjunction with the instructions provided with your specic pump. General
information is given on installation within a system, but reference should always be made
to instructions provided with ancillary equipment when installing the unit.
Abbreviations
The following abbreviations are used in this guide:
°C Degrees Celsius °F Degrees Fahrenheit
EMC Electromagnetic Compliance DC Direct Current
LVD Low Voltage Directive
IOM Installation, Operation and Maintenance Manual
Max Maximum Min Minimum
RPM Revolutions Per Minute SELV Safety Electric Low Voltage
V Volt(s) W Watt(s)
Your Micropump Product...

5
DOC No: 8540 REV D
The following are used throughout this guide to indicate procedure that, if not followed
correctly, may result in injury to personnel or damage to equipment.
Warnings are used to alert the reader to a procedure or practice, which if
not followed correctly, could result in personal injury.
Limits of Use 6
Installation in Explosive and Fire Danger Zones 7
Description 7
Function 7
Unpacking and Storage 8
Assembly 8
Space Requirements 8
Location 9
Bulkhead Mounting 9
EMC Compatibility 9
Electrical Connection 10
Lead Assignments 12
Operation 13
Manual Control Adjustment 14
Magnet Decoupling 15
Maintenance 15
Fault Isolation 16
Technical Specication 17-19
Notes 20-22
Table of Contents
CAUTION
NOTE
Warning - Hot Surface is used to alert the reader to a procedure or
practice, which if not followed correctly, could result in personal injury
due to contact with a hot surface.
Cautions are used to alert the reader to a procedure or practice, which
if not followed correctly, could result in damage to the pump, motor, or
ancillary equipment.
Notes are used to highlight important information that may assist the reader in
carrying out a procedure or in understanding the text.
Safety

6
DOC No: 8540 REV D
Limits of Use
The EagleDrive motor is intended for use with pumps handling uids in a variety of pump-
ing systems. These uids may be innocuous or hazardous, depending on the specic
application. You should contact your local Micropump distributor or contact Micropump
directly about special limitations of your pump/motor unit with regard to your specic
system.
To achieve optimum performance and safe operation Micropump products must be
operated with the limits given in the Technical Specication. Operation outside these
limits is not recommended and may result in damage to the pump, motor, and/or ancillary
equipment.
Temperature. Operating beyond the maximum operating temperature
given in the Technical Specication is not recommended and may result
in damage to the product and compromise safety by creating high surface
temperature.
CAUTION
CAUTION
CAUTION
Corrosive Liquids. Corrosive liquids may eventually produce leak paths
around the sealing surfaces of the product. The product should be
inspected for leaks on a regular basis.
Flooding and Water Immersion. The products covered by this guide
are not designed to operate immersed in water. Refer to the Technical
Specication for the environmental rating.
Condensation. When pumping cold liquids ensure that condensation does
not present a safety hazard. Condensation on the external surfaces of the
magnet cup may result in a short-circuit in the motor controller.
Mechanical Danger. The product must be installed in a location that
exposes it to a low risk of external damage.
Hot Surfaces. Under some operating conditions, surface temperatures can
exceed 90°C (195°F.) Do not touch products while operating. Do not touch
within 30 minutes of system shutdown to allow surfaces to reach safe
handling temperature.

7
DOC No: 8540 REV D
Installation in Explosive and Fire Danger Zones
Micropump offers products designed and tested for installation in explosive or re danger
zones. Contact your local Micropump distributor or contact Micropump directly to deter-
mine if your EagleDrive product combination can be certied for this use.
In Addition to the warnings provided throughout this manual, the following must be
considered in any explosion or re danger zone installation:
Ensure the pump head, motor, and any mounting adapter are suitable for
area classication.
Description
The EagleDrive is a brushless DC motor with integrated controller specially designed to
be electromagnetically coupled to a variety of Micropump pump heads. When properly
assembled to the pump head with sealing o-ring, this comprises a sealed unit where
the driven magnet is within a magnet cup that separates the pumped uid from the
atmosphere.
The enclosed versions are within a thermoplastic housing. The motor is capable of
rotating in both directions and has several speed control input options. A tachometer
signal, with a 0-5 V square-wave output provides speed feedback. The tachometer
output has 2 pulses per revolution. The output frequency is multiplied by 30 to obtain
RPM. The main input power is 12-36 VDC from a class 2 (SELV) source.
There are two EagleDrive models, the MS and EL. Both models operate from 12-36
VDC, with speed control input, 0-5V square wave tachometer feedback, and FWD/REV
capabilities. Instructions for utilizing other speed input signals are provided in this manual.
Both EagleDrive models can be controlled using one of these options:
1. Externally applied 0-5 VDC supply
2. Externally applied 4-20 mA signal (conditioned with external resistor)
3. Manually-adjusted speed control (through use of external potentiometer)
Function
The driven magnet is connected to the pumping parts and is sealed in the magnet cup.
This magnet forms the rotor of the brushless DC motor and is driven by the rotating
magnetic eld in the stator. Rotation of the pumping elements produces ow.
The control signal controls pump speed. Internal feedback monitors the rotational speed
of the pump and regulates the speed in relation to the control voltage. The controller
increases current to regulate speed against increasing back pressure (within the
operating limits of the pump and motor).
Ensure that pumping liquid temperature, and motor housing temperature
are maintained within acceptable range as specied by Micropump
Certication of ATEX Conformity.

8
DOC No: 8540 REV D
Before installing the product ensure all transit packaging has been removed.
Remove the blanks from any inlet and outlet ports. If the pump is to be stored prior to
installation, re-pack the pump in its original packing, ret the blanks to the ports and store
in a dry, covered environment.
Protect the pump head from damage during unpacking and installation. Impacts to the
magnet cup can cause internal damage or result in rub between the magnet cup and
driven magnet upon assembly with the motor.
Inspect the magnet cup before assembly with the motor. Replace or
repair if there are signs of damage.
If the pump head housing assembly and EagleDrive motor are supplied separately they
will need to be assembled prior to the installation.
Insert the drive housing seal (1) into the groove in the face of the housing (3). Align the
pump assembly ange (2) so that it ts into the matching recesses and rotate clockwise
to engage the housing. Secure using the two screws (4) supplied with the EagleDrive.
Torque screws to 0.8 N-m (7 in-lbs).
Loose bolts may result in pump/motor misalignment. Tighten bolts
appropriately. Pump/motor misalignment may result in weakening the
sealing of the enclosure.
Assembly
Unpacking and Storage
Space Requirements
Refer to the Technical Specication for overall dimensions and weights of the EagleDrive
and some of the most common pump/motor combinations.
3
1
2
4

9
DOC No: 8540 REV D
The product should be located with the inlet below or even with the liquid level of the uid
supply. The product can be mounted in any position. Ensure that there is adequate space
for operation, inspection and maintenance.
Location
Pump head or adaptor cannot support the weight of the motor. Ensure
the motor is adequately supported by the foundation and/or mounting
bracket.
The foundation must be capable of supporting the combined weight of
the pump and motor and provide a rigid support.
Bulkhead Mounting (EL Model)
If mounting the pump/EagleDrive assembly through a bulkhead, insert the bulkhead
o-ring (1) into the groove in the face of the housing (3). Position the adaptor ange (2)
through the bulkhead hole so that it does not interfere with the sealing of the bulkhead
hole. Secure the pump/EagleDrive assembly using four screws, nuts, and washers as
needed. Tighten screws evenly and in an alternating pattern.
O-Ring 2-040 described below is necessary to ensure bulkhead is
sealed.
CAUTION
Ø68.3 ±1[2.70 ±.04]
70 2.76
Ø5[.20]
1
3
2

10
DOC No: 8540 REV D
Pumping ammable uids without a proper earthing connection may
cause spontaneous ignition.
EagleDrive Electrical Connection
Ensure that the pump motor is earthed. The pump may be electrically
isolated from the motor depending on the mounting conguration. Some
installations may need an earthing connection on the pump head.
Before starting any electrical installation work ensure that the main
electrical supply is adequately isolated.
Electrical installation must be carried out by qualied personnel who are
conversant with local electricity installation regulations.
Ensure that the voltage of the supply is correct for the motor being
connected, and that the source is Class 2 or a Limited Power Source.
CAUTION
Ensure that all electrical connections use a common earth ground to
avoid hazardous ground loops.
Ensure that only power supplies having SELV specication are
connected to the EagleDrive.
CAUTION
Ensure that all associated equipment has a form of overcurrent
protection. If a fuse is used see table below for recommendations.
CAUTION
Power In
The main input power is 12 to 36 VDC from a Class 2 (SELV) source applied across the
power in and common ground leads. This voltage must be maintained within the specied
limits as the motor is loaded to its maximum current of 2A (Model - MS) or 3A (Model -
EL.)
Ensure that the power supply voltage ripple is maintained below 5% peak
to peak.
CAUTION
EaglEDrivE MoDEl rEcoMMEnDED fusE
Ms littlEfusE 0313002 HXP
El littlEfusE 0313003 HXP

11
DOC No: 8540 REV D
EagleDrive Electrical Connection (Continued)
Control Signal In
0 to 5 VDC Speed Control
When the lead is connected to a supply within the range the motor speed is proportional
to the input. The applied voltage must be within -0.3 to +5.1 VDC or the motor will be
irreparably damaged.
Common Ground
The input voltage, control inputs, fault ags, and the tachometer output all use a
common ground. It is possible that ground potential differences between the power
supply, control voltage source and the frequency counter (if used) will be forced to the
same ground reference when connected to the EagleDrive. Ensure only one earth
ground is used to avoid ground loops.
Isolated Ground
The motor common (black) wire is isolated from the motor housing. There is an internal
connection between the cable shield (bare wire) with the common (black) wire. If the
black lead is connected to the shield, EMC will not be affected. This can be done at the
customer input end of the cable.
Using The Tachometer Output
The tachometer output can be monitored using a frequency counter. The tachometer
output is 0-5V square wave pulse that occurs twice per pump drive revolution. To convert
the tachometer output to rpm, multiply the output frequency (Hz) by 30.
Inadvertent connection of the tachometer output (green) wire to ground
or the supply voltage can cause damage to the drive. If the tachometer is
not used, trim and insulate the green lead.
CAUTION
DO NOT reverse the direction of rotation of the drive until the drive has
come to a complete stop. Reversing the direction while the drive is still
turning may damage the motor.
CAUTION
NOTE
NOTE
Inadvertent grounding of the forward/reverse (orange) wire will cause the drive
to operate in reverse. If reverse operation is not required, trim and insulate the
orange lead.
Motor/Pump performance will be different between FWD and REV operating
modes.
Forward/Reverse Operation
The direction of uid ow can be changed by connecting the orange wire to ground.
For FORWARD ow, make NO CONNECTION to the orange wire. For REVERSE ow,
connect the orange wire to GROUND.

12
DOC No: 8540 REV D
The two fault signals provide diagnostic feedback to the user’s control system. These use
the common ground to provide HI or LOW signals. When both Fault Signals indicate HI, the
EagleDrive is operating normally (no faults detected). Signals are driven with 5.6kohm pull-up
resistors to the internal 5V and should be monitored with a high impedance device (Rload >
100kohms).
Fault Signal Out
Fault
Signal 1
Lead 8
Brown
Fault
Signal 2
Lead 7
Blue
Fault
Description
Drive
Condition
Reason for
Fault
Remedy
0 0 Under
Voltage
Disabled Voltage
supply less
than 8.5V
Ensure proper supply voltage,
check power and ground
connections
0 0 Over
Temperature
Operating Internal
component
temperature
greater than
170º C
Reduce load or increase
cooling
0 0 Logic Fault Disabled Drive cannot
locate the
magnets
inside the
pump
Ensure pump is correctly
attached to EagleDrive
1 0 Internal Short Disabled Drive
components
have failed
Reset EagleDrive by
disconnecting and restoring
power supply connection,
if problem persists, contact
Micropump for a replacement.
0 1 Low Load
Current
Operating Drive
components
have failed
Reset EagleDrive by
disconnecting and restoring
power supply connection,
if problem persists, contact
Micropump for a replacement.
1 1 None Operating No Fault
CAUTION
Do not short Fault Signals to ground or EagleDrive will not operate properly.

13
DOC No: 8540 REV D
MODEL MS
1
2
3
4
5
7
8
9
6
1
2
3
4
5
7
8
9
6
MODEL EL
Lead Function Color
1 Power In Red +12 to +36 VDC, Class 2 (SELV),
Reverse-polarity protected
2 Common Black Isolated from motor housing
3 Control Signal In Yellow 0-5 VDC
4 Tachometer Out Green 5 V square wave-2 pulses per
revolution
5 FWD/REV Orange Forward (oat and insulate), Reverse
(ground)
qww Not Connected Violet None
7 Error Out Blue Fault Signal 2
8 Error Out Brown Fault Signal 1
9 Shield - Connected to Common
EagleDrive Lead Wire Assignments
The 0-5 VDC Control Signal In must be within -0.3 to +5.1 VDC or the
motor will be irrepairably damaged.
CAUTION

14
DOC No: 8540 REV D
Flow rate should always be adjusted by controlling motor speed. Ensure
that overpressure does not occur in the discharge pipe. NEVER throttle
ow by an inlet valve.
Starting or running the pump with the discharge valve closed may result
in overpressure in the discharge pipe.
Post Start-up Checks
Once the pump has started, carry out the following checks:
1. Check that the pump and motor operate smoothly and are free from vibration.
2. Check the inlet and discharge ttings are free from leaks.
Operation
Start-up Procedure
Before starting the pump ensure that any valves in the inlet or discharge lines are open
and that any inlet lters are clean and free from obstruction.
1. Set the external control signal input to minimum value (0 VDC.)
2. Set the power supply (12 VDC to 36 VDC) to ON. With the control input set to 0V, the
pump will show a nominal 25mA to 100mA current draw and will not turn.
3. Adjust the control signal input to the required level. Current demand will rise and fall as
the pump load and speed varies.
Once started the pump should prime if it has not already been lled with uid. If the pump
fails to prime, stop the pump and ll the pump head with liquid.
Shut-down Procedure
Switch off the EagleDrive by rst setting the external control signal input to the minimum
value, then switch off the power supply. Check that the unit runs down in a steady
manner. Close the inlet and discharge valves. Drain the pump if it is to be shut-down for
long periods or installed in areas where the liquid may freeze. Refer to the Maintenance
section for instruction on draining.
Extended periods of dry running may result in permanent damage to the
pump and may cause surface temperature to exceed the operating
temperature of the pump. Ensure that the pump head temperature does
not exceed the ash point temperature of the uid or area. Shut down
pump for a no uid condition. Shut down the pump for a no ow condition.
CAUTION
CAUTION
Ensure the pump head temperature does not exceed the ash point
temperature of the uid or area.
Do not operate EagleDrives in two-wire mode (with control input
connected to mains voltage). Contact your local Micropump distributor
or contact Micropump directly about a special pump/motor unit with
regard to your specic system needs.

15
DOC No: 8540 REV D
To maintain protection of internal drive controller, your external resistor
should be tted with appropriate insulation.
4-20mA Control Input
4-20mA Control
Install a 250 Ohm resistor across the yellow Speed Input and black Common lead wires.
Applying current across this resistor will result in a commanded proportional speed from
the Eagle Drive.
CAUTION
Recommended Resistor
VISHAY P/N PTF65250R00AYBF

16
DOC No: 8540 REV D
To maintain protection of internal drive controller, your external
potentiometer should be tted with appropiate Insulation.
Manual Control Conguration
Manual Control
Install a resistor (sized according to your voltage supply input) across the red Power
In and black Common lead wires. The potentiometer wiper is connected to the yellow
Speed Input lead wire. To increase speed, rotate the potentiometer to increase voltage to
the control line. To decrease speed, rotate the potentiometer to decrease voltage to the
control line.
CAUTION
Resistor (38 KOHM) VISHAY CMF5038K300FHEB
Potentiometer (10 KOHM) VISHAY P16NP103KAB15
Recommended Parts (24 VDC Mains)
RED
YELLOW
BLACK

17
DOC No: 8540 REV D
Maintenance
Excessive wear to the pump can result in driven magnet rub on the
magnet cup. This can generate high surface temperatures or degrade the
capability of the pressure boundary. Remove the pump from service and
replace or repair if pump performance degrades signicantly or the pump
becomes noisy.
Ensure that heavy deposits of dust are not allowed to accumulate. Clean
the pump periodically.
The pump cannot be drained completely, a certain amount of liquid will
remain in the magnet cup area. Ensure that the pump is either ushed
with a suitable ushing agent or precautions are taken against the effect
of any remaining liquid during servicing. When the pump has been
handling ammable, toxic or hazardous uid, the pump internals must
be properly decontaminated by suitably qualied personnel. The Material
Safety Data Sheet for the pumped liquid must be referred to for correct
procedures and precautions to be followed when handling the liquid.
Micropump EagleDrive motors are designed to be maintenance free and require no
adjustments. To ensure the motor or pump/motor assembly retains optimum performance
maintain the uid circuit to keep lters clean and prevent abrasive solids from passing
through the pump.
A program that includes periodic monitoring of your Micropump product is
recommended to provide timely detection and assessment of any problem.
NOTE
Magnet Decoupling
The EagleDrive pump/motor combinations do not decouple. If pump load becomes
excessive, current limiting in the controller prevents motor overload. Additional protection
is provided by a thermal sensor which shuts down the drive if the internal temperature
exceeds a preset value.

18
DOC No: 8540 REV D
Fault Isolation
MOTOR WILL NOT OPERATE
Cause Remedy
No power to motor. Ensure proper voltage has been applied to motor power leads.
Check leads to ensure no short circuits are present.
Control Input lead is shorted. Clear and isolate Control Input lead from Tachometer Out lead. Clear and
isolate Control Input lead from Common lead.
No Control Input applied. Ensure proper control input is applied to control Input lead: for 0-5V ensure line
is not shorted. If manual control EagleDrive, adjust potentiometer to increase
control voltage. Ensure control power supply common is connected to the
common lead.
Thermal Limit is active. Turn off motor and wait for temperature to cool. NOTE: If power voltage and
control signals are present, motor will automatically restart when temperature is
reached. Reduce motor load conditions and/or improve cooling of motor hous-
ing if persistent limit occurs.
Motor has been damaged. Contact your Micropump Distributor or contact Micropump directly for
replacement product.
CYCLIC NOISE OR VIBRATIONS
Cause Remedy
Loose motor mounting bolts. Tighten motor mounting bolts.
Foundation not rigid. Relocate motor.
Pump loose on motor. Tighten pump mounting bolts.
Pump is worn. Replace or repair pump.
Tachometer Out lead is shorted
to FWD/REV lead.
Clear and isolate Tachometer Out lead from FWD/REV lead.
NO TACHOMETER SIGNAL
Cause Remedy
No power to motor. Ensure proper voltage has been applied to motor power leads.
Check leads to ensure no short circuits are present.
Improper wiring. Check that the Tachometer Out lead is connected to the positive input of the
frequency counter.
Check that the common lead of the frequency counter is connected to the motor
Common lead.
Check leads to ensure no short circuits are present.
Motor is stopped. Ensure proper voltage has been applied to motor power leads Ensure proper
control input is applied to Control Input lead.
Ensure control power supply common is connected to the Common lead.
MOTOR RUNS IN THE WRONG DIRECTION
Cause Remedy
FWD/REV lead is shorted to
Common lead.
Clear and isolate FWD/REV lead from Common lead or shield. Check leads to
ensure no short circuits are present.
Execution of troubleshooting steps, determination of root cause and
corrective actions should be performed by a skilled maintenance person.
If the EagleDrive does not meet its design performance or fails to operate correctly, refer
to the following tables for assistance in identifying the cause and remedy:

19
DOC No: 8540 REV D
All Dimensions in mm.[inch]
Technical Specication
Not all possible congurations are shown. Contact your local Micropump
distributor or contact Micropump directly for additional versions.
EagleDrive
Model MS
Product Code DEMSE
Speed Range 250 to 10000 rpm
Typical No-Load Speed
(24 VDC Input / 5 VDC Control / 25°C
Ambient)
6000 rpm
Speed @ Rated Torque 3500 rpm @ 70 mNm (10 oz-in)
Input Voltage Range 10 to 38 VDC
Max Full-Load Current @ Nominal Voltage
(25°C Ambient)
2A @ 24 VDC
Speed Control 0 to 5 VDC
Tachometer Out 0 to 5 VDC square wave - 2 pulse per revolution
Thermal Shutdown 135°C
Thermal Restart 120°C
Storage Temperature -40 to +135°C
Maximum Ambient Operating Temperature 85°C at max load
Reversible Yes
Weight 0.3 kg
Model MS
NOTE
NOTE
2.68
1.90
.39
4X .39
4X .24
2.78
3.16
3.95
1.50
CABLE EXIT
1.77
4X .20
1.89
.51
2.17
32
UNLESS OTHERWISE
SPECIFIED:
ALL VIEWS ARE
THIRD-ANGLE
PROJECTION
SOLIDWORKS
1°
A
6DEC2012
P.RODGERS
P.RODGERS
6DEC2012
EAGLE SHORT DRIVE HOUSING
D-1426A
This drawing embodies a proprietary
design owned by Micropump, Inc.
and is submitted under a confidential
relationship. Except for uses expressly
granted in writing, all rights are
reserved by Micropump, Inc.
A Unit of IDEX Corporation.
=
1:2
REFERENCE ASME Y14.5M-1994 FOR THE DIMENSIONING AND
TOLERANCING STANDARD USED ON THIS DRAWING.
REV.
R
SHEET 1 OF 1
A UNIT OF IDEX
CORPORATION
MICROPUMP, INC.
DRAWING SCALE:
B
SIZE
DATE
F-228/REV D 19 OCT 07
PART NUMBER
MATERIAL
UNLESS OTHERWISE SPECIFIED
DRAWN
APPROVED
.005
.015
.030
0.762
ANGLE
0.127
0.381
=
=
=
.XXX
.XX
.X
=
[.X]
=
[.XXX]
[.XX]
TOLERANCES ARE:
DIMENSIONS ENCLOSED BY [ ]
UNLESS OTHERWISE SPECIFIED
FINISHES INDICATED ARE
TOLERANCES ARE:
ARE IN MILLIMETERS:
MAXIMUM VALUES.
DIMENSIONS ARE IN INCHES
PROPRIETARY INFORMATION
DO NOT SCALE DRAWING
APPROVALS

20
DOC No: 8540 REV D
EagleDrive
Model EL
Product Code DEELE
Speed Range 250 to 9000 rpm
Typical No-Load Speed
(24 VDC Input / 5 VDC Control / 25°C
Ambient)
5500 rpm
Speed @ Rated Torque 3500 rpm @ 140 mNm (20 oz-in)
Input Voltage Range 10 to 38 VDC
Max Full-Load Current @ Nominal Voltage
(25°C Ambient)
2.9A @ 24 VDC
Speed Control 0 to 5 VDC
Tachometer Out 0 to 5 VDC square wave - 2 pulse per revolution
Thermal Shutdown 135°C
Thermal Restart 120°C
Storage Temperature -40 to +135°C
Maximum Ambient Operating Temperature 85°C at max load
Reversible Yes
Weight 0.5 kg
Model EL
3.50
2.75
2.75
.79
2.44
4X .50
4X .12
.37
4.97
4X .19
1.89
2.28
2.16
CABLE EXIT
3.91
1.75 .57
D-1425A
32
UNLESS OTHERWISE
SPECIFIED:
ALL VIEWS ARE
THIRD-ANGLE
PROJECTION
SOLIDWORKS
1°
A
6DEC2012
P.RODGERS
P.RODGERS
6DEC2012
EAGLE LONG DRIVE HOUSING
D-1425A
This drawing embodies a proprietary
design owned by Micropump, Inc.
and is submitted under a confidential
relationship. Except for uses expressly
granted in writing, all rights are
reserved by Micropump, Inc.
A Unit of IDEX Corporation.
=
1:2
REFERENCE ASME Y14.5M-1994 FOR THE DIMENSIONING AND
TOLERANCING STANDARD USED ON THIS DRAWING.
REV.
R
SHEET 1 OF 1
A UNIT OF IDEX
CORPORATION
MICROPUMP, INC.
DRAWING SCALE:
B
SIZE
DATE
F-228/REV D 19 OCT 07
PART NUMBER
MATERIAL
UNLESS OTHERWISE SPECIFIED
DRAWN
APPROVED
.005
.015
.030
0.762
ANGLE
0.127
0.381
=
=
=
.XXX
.XX
.X
=
[.X]
=
[.XXX]
[.XX]
TOLERANCES ARE:
DIMENSIONS ENCLOSED BY [ ]
UNLESS OTHERWISE SPECIFIED
FINISHES INDICATED ARE
TOLERANCES ARE:
ARE IN MILLIMETERS:
MAXIMUM VALUES.
DIMENSIONS ARE IN INCHES
PROPRIETARY INFORMATION
DO NOT SCALE DRAWING
APPROVALS
This manual suits for next models
3
Table of contents
Other Idex Engine manuals
Popular Engine manuals by other brands
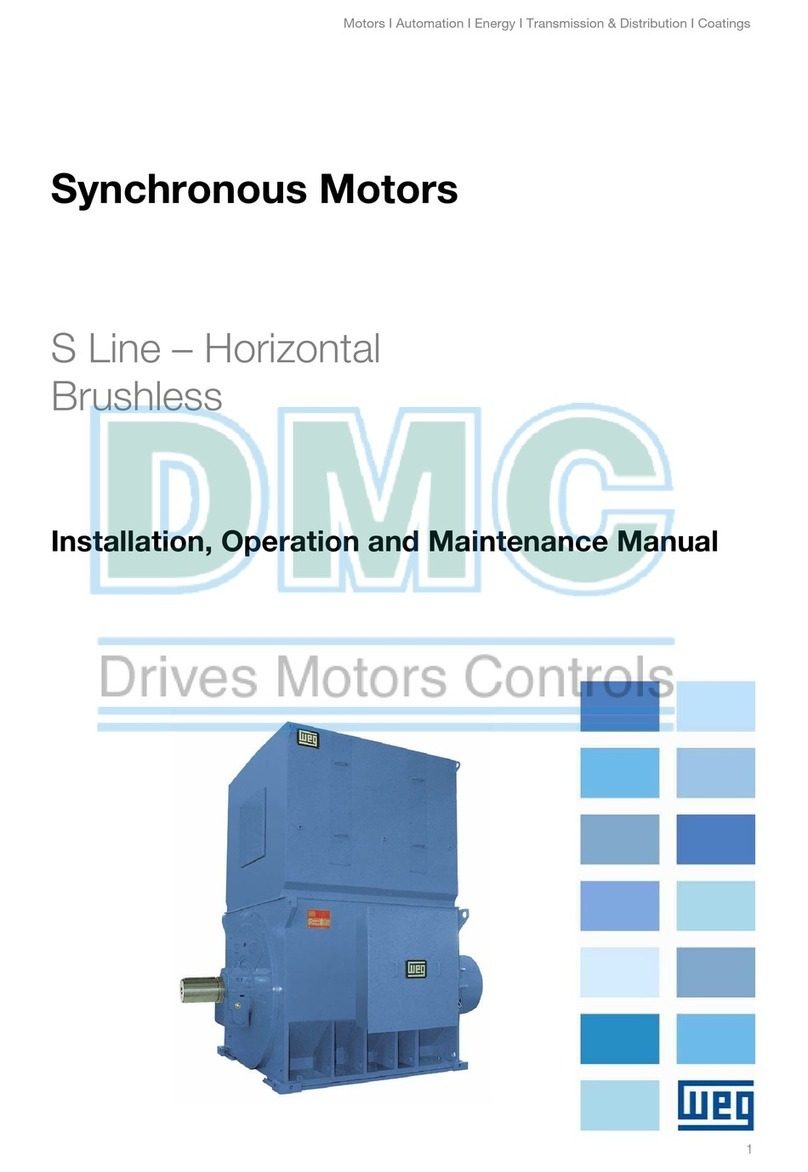
WEG
WEG S Series Installation, operation and maintenance manual

Saito
Saito FG-36 owner's manual

Continental Motors
Continental Motors TSIO-520-BE MAINTENANCE AND OPERATOR'S MANUAL
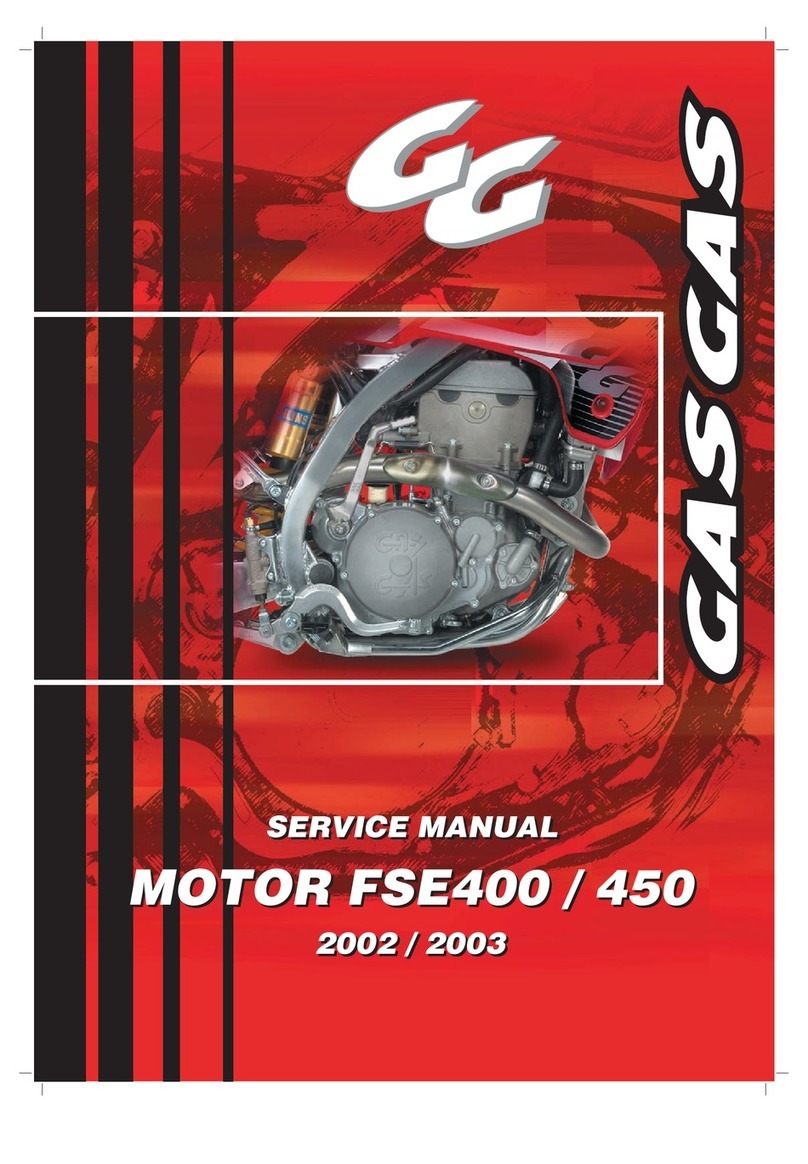
GAS GAS
GAS GAS EC FSE 400 - SERVICE 2002 & 2003 Service manual
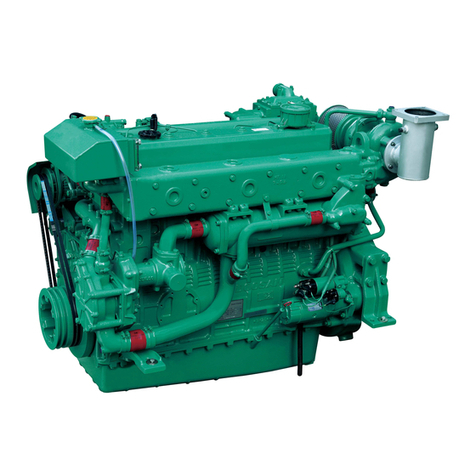
Doosan
Doosan MD Series installation instructions
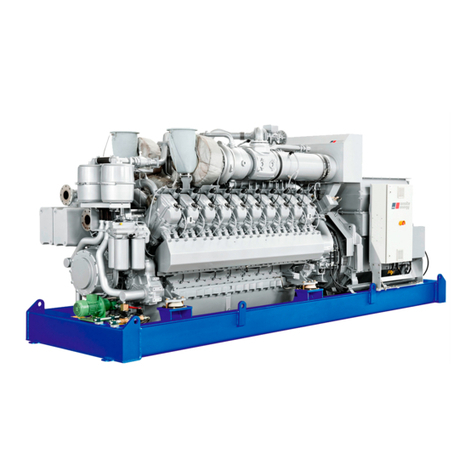
MTU
MTU 12V 4000 L32 F operating instructions
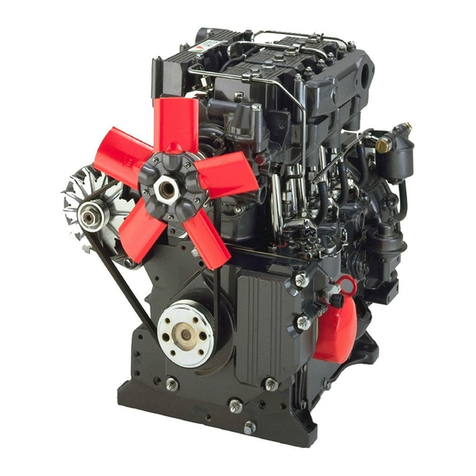
Lister Petter
Lister Petter alpha Series Operator's handbook
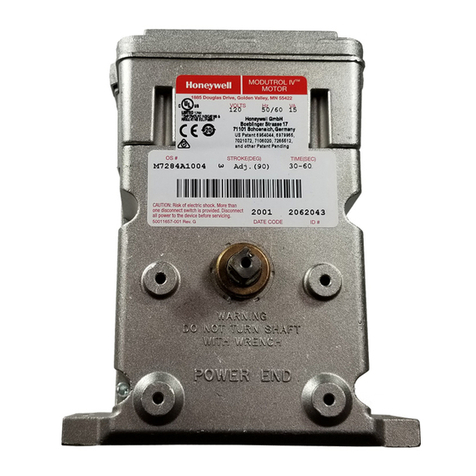
Honeywell
Honeywell Modutrol IV M72 Series manual
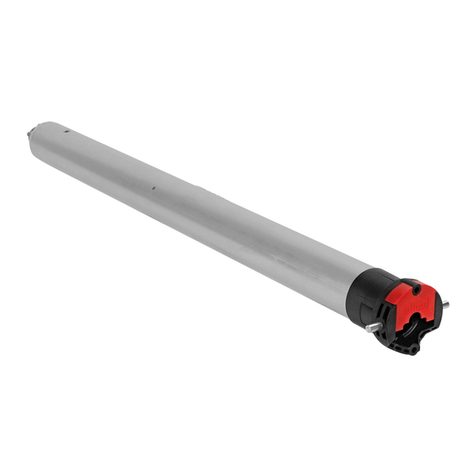
Simu
Simu T5 Hz.02 instructions
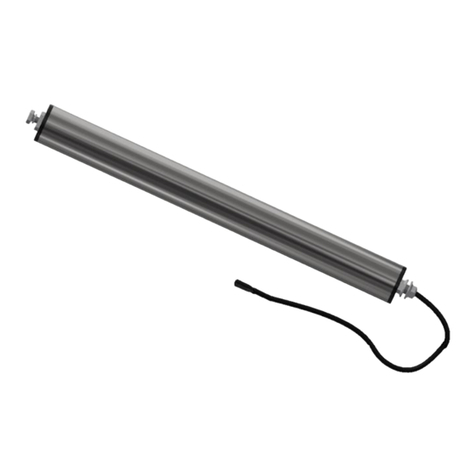
rulmeca
rulmeca RDR BL3 Technical manual
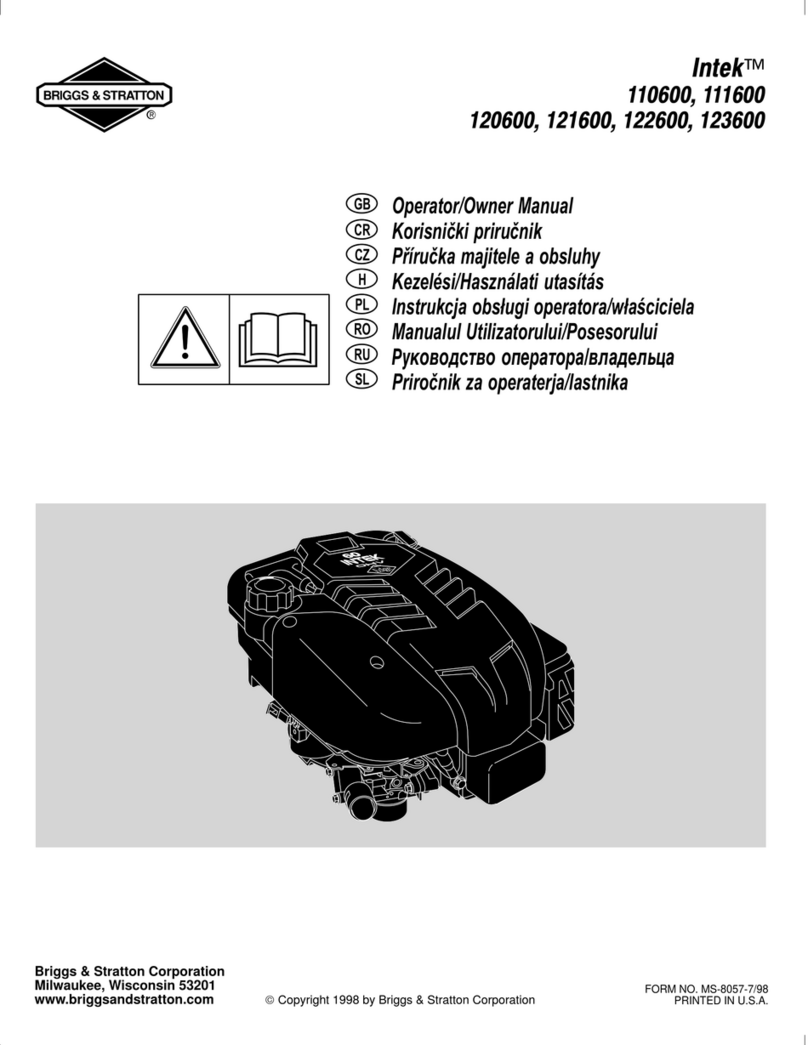
Briggs & Stratton
Briggs & Stratton Intek 110600 Operator owner's manual

SEW-Eurodrive
SEW-Eurodrive PSH CM2H Series operating instructions