IET Labs VI-700 User manual

Operation Manual
MODEL VI-700
Precision
Manual or Programmable
Voltage and Current Source
♦PRECISION INSTRUMENTS FOR TEST AND MEASUREMENT ♦
VIIM-700/cover.p65
TEL: (516) 334-5959 • (800) 899-8438 • FAX: (516) 334-5988
www.ietlabs.com
IET LABS, Inc.
VI-700 IM/Rev K2
© Copyright- 2005 IET Labs, Inc.

♦PRECISION INSTRUMENTS FOR TEST AND MEASUREMENT ♦
VIIM-700/cover.p65
TEL: (516) 334-5959 • (800) 899-8438 • FAX: (516) 334-5988
www.ietlabs.com
IET LABS, Inc.

iii
WARRANTY
We warrant that this product is free from defects in material and workmanship and, when properly used, will
perform in accordance with applicable IET specifications. If within one year after original shipment, it is found
not to meet this standard, it will be repaired or, at the option of IET, replaced at no charge when returned to IET.
Changes in this product not approved by IET or application of voltages or currents greater than those allowed by
the specifications shall void this warranty. IET shall not be liable for any indirect, special, or consequential
damages, even if notice has been given to the possibility of such damages.
THIS WARRANTY IS IN LIEU OF ALL OTHER WARRANTIES, EXPRESSED OR IMPLIED, INCLUD-
ING BUT NOT LIMITED TO, ANY IMPLIED WARRANTY OF MERCHANTIBILITY OR FITNESS FOR
ANY PARTICULAR PURPOSE.

vii
WARNING
OBSERVE ALL SAFETY RULES
WHEN WORKING WITH HIGH VOLTAGES OR LINE VOLTAGES.
Dangerous voltages may be present inside this instrument. Do not open the case
Refer servicing to qulified personnel
HIGH VOLTAGES MAY BE PRESENT AT THE TERMINALS OF THIS INSTRUMENT
WHENEVER HAZARDOUS VOLTAGES (> 45 V) ARE USED, TAKE ALL MEASURES TO
AVOID ACCIDENTAL CONTACT WITH ANY LIVE COMPONENTS.
USE MAXIMUM INSULATION AND MINIMIZE THE USE OF BARE
CONDUCTORS WHEN USING THIS INSTRUMENT.
Use extreme caution when working with bare conductors or bus bars.
WHEN WORKING WITH HIGH VOLTAGES, POST WARNING SIGNS AND
KEEP UNREQUIRED PERSONNEL SAFELY AWAY.
CAUTION
DO NOT APPLY ANY VOLTAGES OR CURRENTS TO THE TERMINALS OF THIS
INSTRUMENT IN EXCESS OF THE MAXIMUM LIMITS INDICATED ON
THE FRONT PANEL OR THE OPERATING GUIDE LABEL.

Contents
Chapter 1: INTRODUCTION .......................................................................... 1
Chapter 2 : SPECIFICATIONS ...................................................................... 2
2.1 Voltage - Standard ......................................................................................................... 2
2.2 HP - High Power Option - 200 mA Load Current Capacity ......................................... 2
2.3 HV - High Voltage Option - 200 V Output ................................................................... 2
2.4 Current -Standard .......................................................................................................... 2
2.5 HI - High Current Option - 200 mA Output.................................................................. 3
2.6 REMOTE Features ....................................................................................................... 3
2.7 General .......................................................................................................................... 4
Chapter 3 : OPERATION ............................................................................... 5
3.1 Initial Inspection and Setup .......................................................................................... 5
3.2 Power ............................................................................................................................ 5
3.2.1 AC Line Operation .............................................................................................. 5
3.3 Operation Mode: Local or Remote ............................................................................... 5
3.3.1 Local Operation ................................................................................................... 5
3.3.2 Remote Operation, Optional ............................................................................... 5
3.3.2.1 IEEE-488 Control ...................................................................................... 5
3.3.2.2 BCD Control .............................................................................................. 6
3.4 Setting of Output Level ................................................................................................ 6
3.5 Connection to Terminals ............................................................................................... 6
3.6 Overload Indicators....................................................................................................... 7
3.7 HP - High Power Option - 200 mA Load Current Capacity ......................................... 7
3.8 HV - High Voltage Option - 200 V Output (Optional) ................................................. 7
3.9 HI - High Current Option - 200 mA Output (Optional) ................................................ 8
Chapter 4 : IEEE INTERFACE OPTION ........................................................ 9
4.1 Introduction ................................................................................................................... 9
4.2 Capabilities ................................................................................................................... 9
4.3 Address Switch and Communications Settings ........................................................... 9
4.4 IEEE Option Operation ................................................................................................. 9
4.5GPIB Test Keyboard .................................................................................................... 10
Chapter 5 : SERIAL INTERFACE OPTION ................................................. 11
5.1Introduction .................................................................................................................. 11
5.2 Capabilities ................................................................................................................. 11
5.3 Signal Interface and Communications Settings .......................................................... 11
5.4 SERIAL Option Operation ......................................................................................... 11
5.5 Serial Test Keyboard ................................................................................................... 12

Chapter 6: PROGRAMMING ....................................................................... 13
6.1 Introduction ................................................................................................................. 13
6.2 Command String Structure ......................................................................................... 13
6.3 Determining the VI-700 Configuration ...................................................................... 13
6.3.1 Instrument Initialization .................................................................................... 13
Chapter 7: CALIBRATION .......................................................................... 14
7.1 Equipment Required ................................................................................................... 14
7.2 Disassembly Procedure ............................................................................................... 14
7.3 Calibration Steps ......................................................................................................... 14
7.3.1Voltage Calibration............................................................................................. 14
7.3.2 HV (X10) Output - Optional ............................................................................. 14
Figures
Figure 1.1: VI-700 Manual or Programmable Voltage and Current Source ............................. 1
Figure 2.1: Typical OPERATING GUIDE Affixed to Unit....................................................... 3
Figure 5.1: Layout for VI-700 Printed Circuit Board ............................................................. 14
Figure 7.1: Layout for VI-700 Printed Circuit Board ............................................................. 15
Tables
Table 3.1 Digital Input Connector Pin Assignments ................................................................. 8
Appendix A
SCPI COMMAND REFERENCE .......................................................................................... 17
Appendix B
IEEE-488.2 COMMON COMMANDS .................................................................................. 19

VI-700 V&l Source
1
The IET Model VI-700 (Figure 1.1) is a versatile
precision dialable or remotely programmable voltage
and current source. Its three ranges provide up to 20
V full scale (200 V with the HV option), and down to
100 µV resolution; and 20 mA full scale down to 0.1
mA resolution. Both voltage and current outputs are
available simultaneously. The output is set by a range
selector and thumbwheel switches in the LOCAL
mode, or by a digital input at the rear panel. The
REMOTE mode control can be a BCD parallel or
IEEE-488 interface.
The optional HV output extends the range of the out-
put voltage to 200 V at 10 mA. It provides an output
at the rear panel 10 times higher-than that at the front
panel. The optional HI feature extends the output
current to 200 mA.
The optional, HP output extends the output load cur-
rent capacity to 200 mA for all the voltage ranges.
This makes the VI-700 suitable for many precision
low to moderate power applications.
Chapter 1
INTRODUCTION
INTRODUCTION
Figure 1.1: VI-700 Manual or Programmable Voltage
and Current Source
The VI-700 offers many full performance features.
It fulfills a variety of laboratory needs. Its wide out-
put range (up to 200 V), very low output impedance
(5 mΩ, typical), low noise and ripple, and 200 mA
load current capability suit the VI-700 to a variety of
applications, such as simulation, calibration, A/D and
D/A converter evaluations, and product development.
Front panel overload indicator lamps warn of exceed-
ing of voltage load or current compliance limits. This
feature assures the user that the output is within speci-
fications without having to make any measurement
or computations. The standard model may still be
used within the overload condition and will function
for approximately 50-100% overload with only a slight
degradation of specifications.

VI-700 V&l Source
2
For convenience to the user, the pertinent specifica-
tions are given in an OPERATING GUIDE,
shown in Figure 2. 1, affixed to the case of the instru-
ment.
2.1 Voltage - Standard
Output Ranges:
200 mV, 2 V, 20 V, (200 V with HV Option).
Resolution:
100 µV, 1 mV, 10 mV,
(100 mV with HV Option).
Accuracy:
±(75 ppm + 50 µV), 200 mV range;
±(75 ppm + 0.25 mV), 2 V range;
±(75 ppm + 2.5 mV), 20 V range;
at 23°C, no load, after warmup.
Output Current:
70 mA (200 mA with HP Option), maximum load,
with LED overload indicator, for conformance
with accuracy specifications; 50-100% current
overload output is available with slightly reduced
accuracy.
Output Impedance:
5 mΩtypical, 40 mΩfor 20 V range.
Noise and Ripple:
50 µVrms on 200 mV and 2 V ranges, 100 µVrms
on 20 V range; exclusive of random transients.
Temperature Coefficient:
10 ppm/ºC typical, 15 ppm/º C maximum.
2.2 HP - High Power Option - 200 mA
Load Current Capacity
Output Current: 200 mA, maximum load, with LED
overload indicator, on all ranges.
SPECIFICATIONS
Chapter 2
SPECIFICATIONS
Since significant current may be drawn from this unit,
it is advisable to leave the mA terminals open. The
current OVLD LED will remain on if the mA termi-
nals are open, and this indicator may be disregarded.
The OVLD indicator will be off and will behave nor-
mally under normal operation.
2.3 HV - High Voltage Option - 200 V
Output
Output Voltage:
0 to 200 V.
Resolution:
1 mV, 10 mV, 100 mV.
Output Current:
10 mA (may be increased).
Accuracy:
±(0.01% + 0.5 LSD); applies to >20 V.
2.4 Current -Standard
Output Ranges:
200 µA, 2 mA, 20 mA.
Resolution:
0. 1 µA, 1 µA, 10 µA.
Accuracy:
±(75 ppm + .05 µA); 200 µA;
±(75 ppm + 0.25 µA), 2 mA;
±(75 ppm + 2.5 µA), 20 mA;
at 23°C, no load, after warmup.
Compliance:
0-20 V; with LED overload indicator.

VI-700 V&l Source
3SPECIFICATIONS
Figure 2.1:Typical OPERATING GUIDE Affixed to Unit
2.5 HI - High Current Option - 200 mA
Output
Output Current: 200 mA.
Resolution: 0. 1 mA.
Accuracy: ±(0.01%+0.75 LSD)
Compliance:
0- 18 V; with LED overload indicator.
2.6 REMOTE Features:
Front panel switch selects REMOTE (digital in-
terface) or LOCAL (front panel thumbwheel
switch) operation. All front panel controls except
POWER are programmable.
IEEE-488.2 Interface Option:
IEEE-488.2-1987; SCPI 1994.0;
"*IDN" for S/N, Model & REV;
"CAL:DATe?" for last calibration date.
RS232 Interface Option:
RS232.SCPI 1994.0;
"*IDN" for S/N, Model & REV;
"CAL:DATe?" for last calibration date;
25 pin male interface conforming to EIA-STD-
RS-530.
CURRENT
OUTPUT RANGES
RESOLUTION
ACCURACY
COMPLIANCE
OUTPUT RANGES
RESOLUTION
ACCURACY
OUTPUT CURRENT
OUTPUT IMPEDANCE
NOISE and RIPPLE
TEMPCO
CONSULT INSTRUCTION MANUAL FOR PROPER INSTRUMENT OPERATION
VI-700 OPERATING GUIDE
VOLTAGE
1. CNTRL MODE button has no effect for non programmable
units.
2. Make the most secure connection to the V terminals if
significant current is drawn.
3. Current OVLD LED indicator is on if mA terminals are open.
This is of no concern or leads may be shorted together.
4. The ground terminal is connected to earth ground and may
be connected to either VOLTAGE terminal.
MODEL: VI-700 SN: J1-0540317
OPERATION
POWER
FUSE
105-125 V, 50-60 Hz; 5 W.
0.25 A
200 mV, 2 V, 20 V
100 µV, 1 mV, 10 mV
±(75 ppm + 50 µV); 200 mV range;
±(75 ppm + 0.25 mV), 2 V range;
±(75 ppm + 2.5 mV), 20 V range;
at 23°C, no load, after warmup.
70 mA, maximum load; with LED
overload indicator
5 mΩtypical, 40 mΩfor 20 V range
50 µVrms on 200 mV and 2 V
ranges, 100 µVrms on 20 V range
(exclusive of random transients)
±10ppm/°C typical, ±15ppm/°C max.
VILBL/p2/VI-700Rev J3/90-100%12-04
Traceable to SI
IET LABS, INC. 534 Main Street, Westbury, NY 11590 • (800) 899-8438 • (516) 334-5959
CAGE CODE: 62015 www.ietlabs.com
200 µA, 2 mA, 20 mA
0.1 µA, 1 µA, 10 µA
±(75 ppm + .05 µA); 200 µA;
±(75 ppm + 0.25 µA), 2 mA;
±(75 ppm + 2.5 µA), 20 mA;
at 23°C, no load,
after warmup.
0-20 V; with LED overload
indicator

VI-700 V&l Source
4SPECIFICATIONS
2.7 General
Digital Input:
3-1/2 digit parallel BCD or IEEE-488 inter-
face; a front panel pushbutton selects RE-
MOTE or front panel thumbwheel opera-
tion.
Operating Temperature Range:
-20ºC to +40ºC.
-20ºC to +28ºC, for HP -High Power Option.
Power Requirement:
105-125 V or 210-250 V; 50-60 Hz; 5 W.
Recommended Calibration Interval:
12 months.
Dimensions:
7.1 cm W x 22.9 cm D x 12.6 cm H
(8.5"x9.0"x2.8")
with IEEE-488 option:
22 cm W x 24 cm D x 12 cm H
(8.5"x9.25"x4.44")
Weight:
1.6 kg (3.5 lb) with no options;
4.1 kg (9 lb) with HV and IEEE options.

VI-700 V&l Source
5
Chapter 3
OPERATION
OPERATION
3.1 Initial Inspection and Setup
This instrument was carefully inspected before ship-
ment. It should be in proper electrical and mechani-
cal order upon receipt.
An OPERATING GUIDE, shown in Figure 2.1, is
attached to the bottom of the instrument to provide
ready reference to specifications.
3.2 Power
3.2.1 AC Line Operation
For a line powered unit, connect the VI-700 to a
sounded power outlet. Operation at either 110 or 220
Vac is possible by selecting internal straps. Press the
PWR switch which is push-on push-release button;
the PWR LED indicator will light.
3.3 Operation Mode: Local or Remote
Operation of the VI-700 Precision Voltage and Cur-
rent Source is straightforward and is graphically indi-
cated on the front panel.
1. Plug the unit into a sounded ac outlet.
2. Pull out and set the handle for convenient
operation.
3. Turn on the PWR switch. The PWR lamp
(as wll as the READY and LOCAL lamps
if present with the IEEE-488 option) should
come on.
3.3.1 Local Operation
1. Set the CNTRL MODE switch to LOCAL,
i.e. pointing to the thumbwheel switches. The
associated LOCAL lamp (if present with
IEEE-488 option) should come on. For units,
without a remote programming option, this
switch has no effect.
2. Program the output level manually as
described in subsection “Setting of Output
Level” below.
3.3.2 Remote Operation, Optional
The VI-700 provides convenient optional remote con-
trol operation through a choice of optional IEEE-488
bus control or a parallel BCD signal input.
Optical isolation allows the outputs to be floating and
gives the user the option of using the voltage and cur-
rent outputs in either polarity. They may also be tied
to the ground terminal on the front panel.
3.3.2.1 IEEE-488 Control
The VI-700 includes a REMOTE/LOCAL switch
on the front panel. The REMOTE position is a re-
mote enable. When in LOCAL mode, the VI-700
supplies the output value selected using the front panel
thumbwheel switches.
When the switch is in the REMOTE position, the
VI-700 will supply the remote output value only if
that option asserts remote control. If the option does

VI-700 V&l Source
6OPERATION
not assert control, the front panel thumbwheel output
value is supplied. The REMOTE and LOCAL LEDs
always indicate which interface is controlling theoutput
value.
Setting the front panel REMOTE/LOCAL switch
to LOCAL overrides the REMOTE option settings
and always sets the output to the value selected us-
ing the front panel thumbwheels, regardless of the
REMOTE option’s assertion of control.
For IEEE and RS232 units, the LOCAL indicator
remains on until communication with the unit is initial-
ized. The mode changes to REMOTE after con-
troller commands are received.
Set the MULTIPLIER on the front panel manually.
The MULTIPLIER is not under REMOTE con-
trol.
Set the output level remotely, replacing the front panel
thumbwheel setting. See Chapter on IEEE-488 pro-
gramming.
3.3.2.2 BCD Control
Units with a BCD option provide a connector on the
rear panel for inputting a 3-1/2 digit BCD equivalent
of the thumbwheel setting. This digital input is opera-
tive whenever the CNTRL MODE switch is set to
REMOTE. The MULTIPLIER switches must be
manually set.
The digital output pin assignments are given below in
Table 3. 1. The digital output connector is a 26 pin
header on the rear panel. It may be mated to many
popular female connectors such as 3M Company
Model 3399, GTE Sylvania Inc. Model 6BAXX-26-
lXX-Y.X, T&B/Ansley Corp. Model 609-2600M or
equivalent. The rear panel connector pin numbering,
as the connector is viewed straight on, is also shown
in Table 3. 1.
The required input is a 5 V, positive true TTL com-
patible source.
3.4 Setting of Output Level
IMPORTANT: The VI-700 must be allowed
to warm up for 15 minutes to reach specified accu-
racy. For maximum stability and minimum drift, al-
low the unit to warm up for at least one hour.
The front panel controls simultaneously set both the
voltage and current output levels. This output may
be conveniently and directly read on the front panel.
The output in volts and milliamperes is exactly the
MULTIPLIER setting times the number shown on
the thumbwheel switches. For example, a setting of
X10 and 1.335 outputs 13.35 V and 13.35 mA; a set-
ting of X0.1 and .025 outputs 2.5 mV and 2.5 µA.
The range used, i.e. X10, Xl, or X0.l, should be the
one providing the highest resolution. If 10 mV is re-
quired, for example, it should be obtained on the X0.1
range even though it is available on the Xl range. This
allows for maximum accuracy even though all set-
tings on an ranges will meet performance specifica-
tions.
In the case of a REMOTE input being used, it over-
rides the thumbwheel setting.
3.5 Connection to Terminals
Both voltage and current outputs are floating, and in
the case of line operated units, may be connected to
the earth ground terminal on the front panel.
A voltage of the indicated polarity will be present
across the red and black V terminals. Be aware that
the specified voltage exists right at the terminals
only. If leads are used to bring this voltage to some
remote load, then a voltage drop develops across these
leads. Whether this drop is significant or not depends
on the amount of current flowing. If, for example,
the load is a high input impedance meter or other such
device, then the lead potential is safely ignored. If,
however, a large amount of current is drawn through
the connecting leads, then a significant drop may de-
velop across the leads and various contact resis-
tances. The user should be aware of this and note
the following procedures.
Whenever high currents are to be drawn, connec-
tions should be made with heavy cables and heavy
duty spade terminals or banana plugs securely attached

VI-700 V&l Source
7
OPERATION
to the binding posts. If the output voltage is being
monitored, then the voltage at the posts and at the
load should be measured to determine the potential
drop between them. These precautions are espe-
cially important whenever the X0.l range is being used,
because even very small resistances can result in a
significant voltage relative to the least significant digit
resolution of that range, i.e. 100 µV.
If sensing at the load is desired to virtually eliminate
this lead drop, consult IET Labs for instructions on
implementing this technique.
In the case of the current output, no such problem
exists. The current indicated on the front panel is
exactly the current flowing through the test load.
3.6 Overload Indicators
In order to provide the user with certainty that the
output load capability is not being exceeded and that
the VI-700 is performing within specifications, two
OVLD indicator LED lamps are provided. As long
as the appropriate indicator is off, its associated out-
put is accurate as specified.
In the case of the current output, note that it is the
voltage or compliance across the terminals, which
cannot be exceeded, 20 volts in particular. An open
circuit is therefore an overload condition and will cause
that indicator to go on. This condition can be ignored,
or, if desired, a short circuit strap may be placed across
the current terminals to turn off this lamp.
In the case of the HP - High Power Option - where
up to 200 mA may be drawn, a shorting link will cause
this current to be constantly drawn from the current
terminals if the unit is on a high setting. This could
cause overheating, and it is advisable to leave the mA
terminals open. The current OVLD LED will re-
main on if the mA terminals are open, and this indica-
tor may be disregarded. The OVLD indicator will
behave normally under normal operation.
It is important to realize that the OVLD indicators
are conservatively set. The output in the overload
region may be used as long as care is exercised. The
voltage output remains precise for 50-100% current
overload with only a slight degradation in accuracy, of
the order of one LSD (least significant digit.) The VI-
700 can actually be used as a low power program-
mable power supply.
If both voltage and current connectors are used to
supply power simultaneously to outside loads, one or
both overload indicators may come on sooner than at
the limits indicated above since they are deter-mined
by the total output capability of the instrument.
There is a small amount of hysteresis built into the
overload indicator circuits in order to prevent them
from flickering as the limit threshold is approached.
This requires reducing the load substantially below the
limit whenever it is necessary to reset or turn off the
indicator.
3.7 HP - High Power Option - 200 mA
Load Current Capacity (Optional)
A unit with this option may be used in the same way
as a standard unit. Caution should be exercised since
a significant current is available and could overheat
the item under load. The current overload indicator
will be on; see the Overload Indicators section above.
3.8 HV - High Voltage Option - 200 V
Output (optional)
WARNING
OBSERVE ALLSAFETY RULES
WHEN WORKINGWITH HIGH VOLTAGES OR LINE
VOLTAGES.
HIGH VOLTAGE MAY BE PRESENT AT
REAR PANEL WITH HV OPTION.
The rear output voltage is precisely 10 times the volt-
age set at the front panel. Up to 10 mA may be drawn.
Exceeding that current will not turn on the OVLD
indicator. Consult IET Labs if more current is re-
quired.
It is up to the user to consider placing a fuse or a
current limiting resistor in series with the X10 200 V
OUTPUT terminals as a safety measure.

VI-700 V&l Source
8OPERATION
Table 3.1 Digital Input Connector Pin Assignments
Connector Pin Numbering
25 23 21 19 17 15 13 11 9 7 5 3 1
26 24 22 20 18 16 14 12 10 8 6 4 2
(Viewed Straight On)
3.9 HI - High Current Option - 200 mA
Output (optional)
To obtain an X10 higher output current, set the VI-
700 to the X10 Range, and either toggle the 200 mA
toggle switch or depress the 200 mA OUTPUT but-
ton switch to 200 mA. The effective current multi-
plier becomes X100. The 200 mA switch must be
OFF in order to use the X0.1 and X1 current range.

VI-700 V&l Source
9
Chapter 4
IEEE INTERFACE OPTION
4.1 Introduction
The IEEE interface option makes the VI-700 an IEEE-
488.2-1987 and SCPI 1994.0 compatible instrument.
The IEEE STD 488.2 covers the electrical and me-
chanical bus specifications, and state diagrams for
each GPIB bus function. It also establishes data for-
mats, common commands for each 488.2 device and
controller protocols. The standard is available on-line
at http://www.ieee.org or by contacting the IEEE at:
IEEE Corporate Office
3 Park Avenue, 17th Floor
New York, New York
10016-5997 U.S.A.
Tel: +1 212 419 7900
The SCPI standard provides a tree like series of stan-
dard commands for programmable instruments so that
similar instruments by different manufacturers can
be controlled by the same program. SCPI informa-
tion and a command reference are located in Appen-
dix A.
Other tutorials are available on-line; consult IET for
additional information. A software GPIB “keyboard”
may be requested from IET to perform elementary
commands for training and testing. See Section 5.5.
4.2 Capabilities
The IEEE option provides remote control over the
output value; it does not control the range.
Decimal
Address
SWITCH
SETTINGS
5-4-3-2-1
Decimal
Address
SWITCH
SETTINGS
5-4-3-2-1
0 0-0-0-0-0 16 1-0-0-0-0
1 0-0-0-0-1 17 1-0-0-0-1
2 0-0-0-1-0 18 1-0-0-1-0
3 0-0-0-1-1 19 1-0-0-1-1
4 0-0-1-0-0 20 1-0-1-0-0
5 0-0-1-0-1 21 1-0-1-0-1
6 0-0-1-1-0 22 1-0-1-1-0
7 0-0-1-1-1 23 1-0-1-1-1
8 0-1-0-0-0 24 1-1-0-0-0
9 0-1-0-0-1 25 1-1-0-1-0
10 0-1-0-1-0 26 1-1-0-1-0
11 0-1-0-1-1 27 1-1-0-1-1
12 0-1-1-0-0 28 1-1-1-0-0
13 0-1-1-0-1 29 1-1-1-0-1
14 0-1-1-1-0 30 1-1-1-1-0
15 0-1-1-1-1 31 Reserved,
do not use
4.3 Address Switch and
Communications Settings
Each GPIB bus device is identified by a five-bit bi-
nary address. There are 32 possible primary addresses
0 through 31; addresses 0 and 31 are reserved . The
VI-700 BUS ADDRESS switch on the rear panel
establishes the GPIB address of the unit. Bus ad-
dress settings are read at power up. Refer to table
4.1.
4.4 IEEE Option Operation
The IEEE controller asserts the remote mode upon
receipt of a valid command. The REMOTE LED
will light and impedance settings will be controlled
Table 4.1 IEEE Bus Address Settings
IEEE INTERFACE

VI-700 V&l Source
10
through the IEEE interface if the REMOTE/LO-
CAL switch is in the REMOTE position. Remote
control may be dropped by issuing an IEEE GTL com-
mand. Dropping remote sets the VI-700 output to the
value set on the front thumbwheel switches. See
Chapter 3 for information about REMOTE/LOCAL
functionality.
4.5 GPIB Test Keyboard
To aid the user in operating the VI-700, a GPIB “Key-
board” Controller program - the easiest way to con-
trol GPIB devices without writing a program - is avail-
able from IET. This GPIB Keyboard program auto-
matically finds your device at start-up and it lets you
enter just the data that you want to send to the de-
vice. This program works with ICS, Measurement
Computing and National Instruments controllers.
To implement, request a download of
ICS_GPIBkybd_Install.zip from IET Labs Tech
Support.
Unzip the file and follow instructions to install.
Open the application. You may use the Find Listen-
ers button to confirm that the VI-700 unit is recog-
nized. Other instruments may also be recognized at
this time.
Enter and set the Address to the VI-700 address.
Use the window to send a command string to the
VI-700,
where the command string is constructed as described
in Chapter 7. A command string might be, for ex-
ample:
SOURce:DATA output string
IEEE INTERFACE

VI-700 V&l Source
11
Chapter 5
SERIAL INTERFACE OPTION
IET Direction
Pin RS232 Signal Name In / Out
1AA Chassis n/a
2BA Send Data ðð
ðð
ð
3BB Receive Data ïï
ïï
ï
4CA Request to Send ðð
ðð
ð
5CB Clear to Send ïï
ïï
ï
8CF Signal Detected ïï
ïï
ï
20 CD DataTerminal Rdy ðð
ðð
ð
5.4 SERIAL Option Operation
The SERIAL option uses the same command set as
the IEEE option. Additional commands exist for con-
figuring the serial interface. Changes to the serial
UART take place at power-on or after a reset.
SCPI command strings must be followed by a <CR>
to terminate the message. Every command returns a
response that includes a message terminator. The pro-
gram/operator should wait for this message termina-
tor before sending additional commands.
Command characters are not echoed to the interface
on power up. Send <CTRL-E> to force the control-
ler to echo commands back to the interface or
<CTRL-F> to disable echo.
By default, the controller returns ">" and <LF> as a
prompt after executing any command. When echo is
turned 'On', the controller returns <CR><LF> and
">"as a prompt after executing any command.
Echo-back RS232 Message
Mode Prompt Terminator
On CR LF > CR LF
Off >LF LF
5.1 Introduction
The SERIAL option adds RS-232C and SCPI 1994.0
capability to the VI-700 series instruments. The SCPI
standard provides a tree like series of standard com-
mands for programmable instruments so that similar
instruments by different manufacturers can be con-
trolled by the same program. A VI-700 SCPI com-
mand reference is included in Appendix A.
Tutorials are available on-line; consult IET for addi-
tional information. A software Serial “keyboard” may
be requested from IET to perform elementary com-
mands for training and testing. See Section 5.5.
5.2 Capabilities
The SERIAL option provides remote control over the
output value; it does not control the range.
5.3 Signal Interface and
Communications Settings
A 25 pin male DTE interface connector conforming
with EIA-STD-RS-530 is located on the rear-panel.
The default communications parameters are:
Connection of a PC to the VI-700 SERIAL option is
typically made through a simple null-modem or
“LapLink” cable.
Parameter Default Range/Choices
Baud 9600 300 - 115,200
Data Bits 8 7 or 8
Stop Bits 1 1 or 2
Parity None Odd, Even, None
SERIAL INTERFACE

VI-700 V&l Source
12
5.5 Serial Test Keyboard
To aid the user in operating the VI-700, a Serial “Key-
board” Controller program - the easiest way to con-
trol serial devices without writing a program - is avail-
able from IET. This Serial Keyboard program auto-
matically finds your device at start-up and it lets you
enter just the data that you want to send to the de-
vice. This program works with ICS, Measurement
Computing and National Instruments controllers.
To implement, request a download of:
ICS_Serkybd_Install.zip, from IET Labs Tech
Support
Unzip the file and follow instructions to install.
Open the application. Initialize the COM PORT and
use the Device Command window to send a com-
mand string to the VI-700, where the command
string is constructed as described in Chapter 7. A
command string might be, for example:
SOURce:DATA output string
SERIAL INTERFACE

VI-700 V&l Source
13
Chapter 6
PROGRAMMING
6.1 Introduction
VI-700 units equipped with IEEE or SERIAL options
implement a consistent SCPI interface. A SCPI com-
mand reference is included in Appendix A.
6.2 Command String Structure
Output is controlled in the form of a single SCPI com-
mand followed by a space and a 4 character ) Out-
put String. Each character in the string represents
the value of one decade, equivalent to one possible
manual thumbwheel switch on the front of the unit.
This Output String is constructed as:
• The number is in units as in the thumbwheel switch for
the range that is selected, e.g. for the X1.0 range, 1 unit
represents 1 mV.
• All 4 characters must be provided; they represent
3-1/2 digits; The most significant character may be 0 or
1 (all odd digits in the most significant position will
result in a 1 command; all even digits in the most sig-
nificant position will result in a 0 command)
• The decade values are straight-reading, from left to
right. All preceding and trailing zeros must be included
to complete 4 characters; any other characters in those
spaces will be ignored.
• A decimal point may not be included.
• Combine with the “SOURce:DATA ” command.
For example:
Value Command
195 mV SOURce:DATA 0195 in Range X1.0
100.1 mV SOURce:DATA 1001 in Range X0.1
6.3 Determining the VI-700 Configuration
The IEEE 488.2 specification defines the *IDN string
as containing 4 sections separated by commas; the
manufacturer, the model, the serial number and the
revision of the instrument.
The Model section of the *IDN string of the VI-700
has been encoded to provide information about the
characteristics of the specific instrument being used.
For example, a *IDN query to a VI-700 might return:
IET Labs,VI-700-F-4-100m-0-0,K2-
0551324,K2
In our example above, the Manufacturer section con-
tains “IET Labs”, the Model section contains “VI-
700-F-4-100m-0-0”, the Serial Number section “K2-
0551324” and the Revision section “K2”.
6.3.1 Instrument Initialization
Reset the unit to power up defaults using *RST
Check that the instrument is “in cal” by reading the
calibration date and compare it to current date/time
using CALibrate:DATe?
PROGRAMMING

VI-700 V&l Source
14
Chapter 7
CALIBRATION
CALIBRATION
The VI-700 should be calibrated every twelve months
or more frequently if inaccurate outputs are sus-
pected.
7.1 Equipment Required
1. Precision digital dc voltmeter, 4-1/2 digit,
with 0.2 V, 2 V, and 20 V full scale ranges,
accurate to better than 0.01%.
2. Precision digital dc ammeter, 4-1/2 digit, with
0.2 mA, 2 mA, and 20 mA full scale ranges,
accurate to better than 0.01%.
7.2 Disassembly Procedure
WARNING
HIGH VOLTAGES EXIST WITHIN THIS
INSTRUMENT.
REFER SERVICING AND CALIBRATION TO
QUALIFIED PERSONNEL.
OBSERVE ALL APPLICABLE SAFETY PRE-
CAUTIONS.
OBSERVE ALL ESD PRECAUTIONS.
Remove the four screws on the bottom of the unit
that are inside the feet. Carefully lift off the top cover.
All calibration steps are performed on the printed cir-
cuit board. Refer to Figure 5.1 for the locations of
the various test points and trimmer potentiometers.
In the instructions to follow, the notation “A” refers
to an integrated circuit (IC), and an appended num-
ber refers to a particular pin on that IC, e.g. 1-A5/2
refers to pin 2 of IC 5 on the main printed circuit
board. The notation “T” refers to a trimmer potenti-
ometer.
7.3 Calibration Steps
Turn on the VI-700 and allow it to stabilize for one
hour.
7.3.1 Voltage Calibration
1. Attach the digital voltmeter (DVM) leads se-
curely to the voltage output binding posts.
2. Set the VI-700 to 0.000 on the X0.l range.
3. Adjust trimmer 1-T4 to obtain a voltage as
close to zero as possible. 50 µV or less is
satisfactory.
4. Set the VI-700 to 1.799 on the X10 range.
5. Adjust trimmer 1-Tl to obtain a voltage of
17.990 V.
6. Set the VI-700 to 1.799 on the Xl range.
7. Adjust trimmer 1-T3 to obtain a voltage of
1.7990 V.
8. Set the VI-700 to 1.799 on the X0.1 range.
9. Adjust trimmer 1-T5 to obtain a voltage of
179.90 mV.
7.3.2 HV (X10) Output - Optional
The X10 output is calibrated as follows:
1. Set the front panel output to 19.99 V.
2. Monitor the rear panel output.
3. Locate the potentiometer in the center of the
PC board attached to the roof of the unit.
4. Adjust the potentiometer until the X10
output voltage is 199.9 V.
Table of contents
Popular Portable Generator manuals by other brands
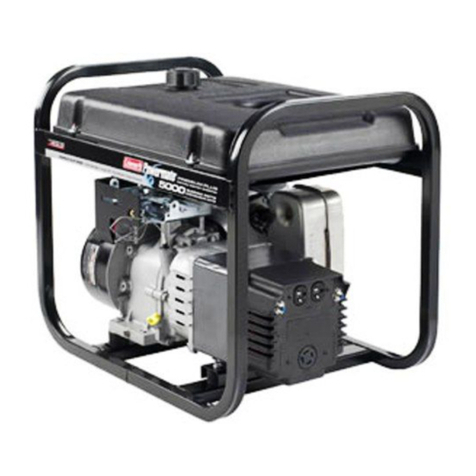
Powermate
Powermate Premium Plus PM0545003 owner's manual
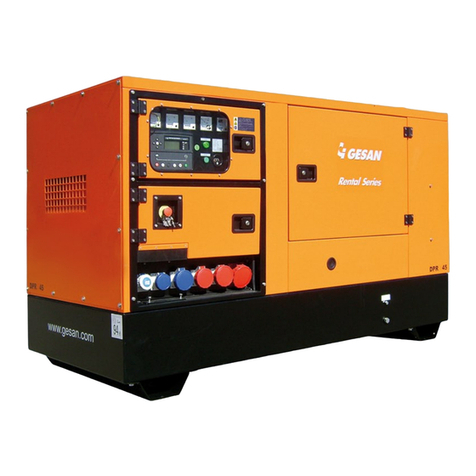
Gesan
Gesan Rental Series user manual
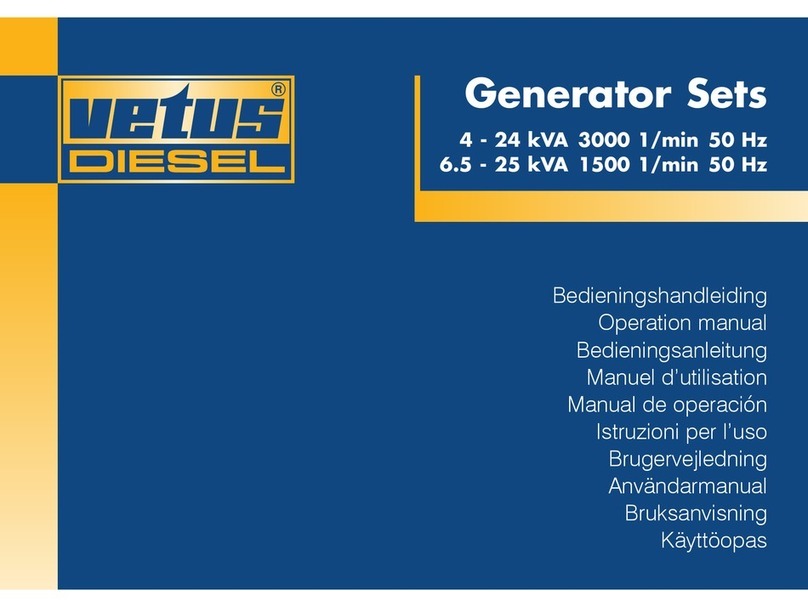
Vetus
Vetus GHS4 Operation manual
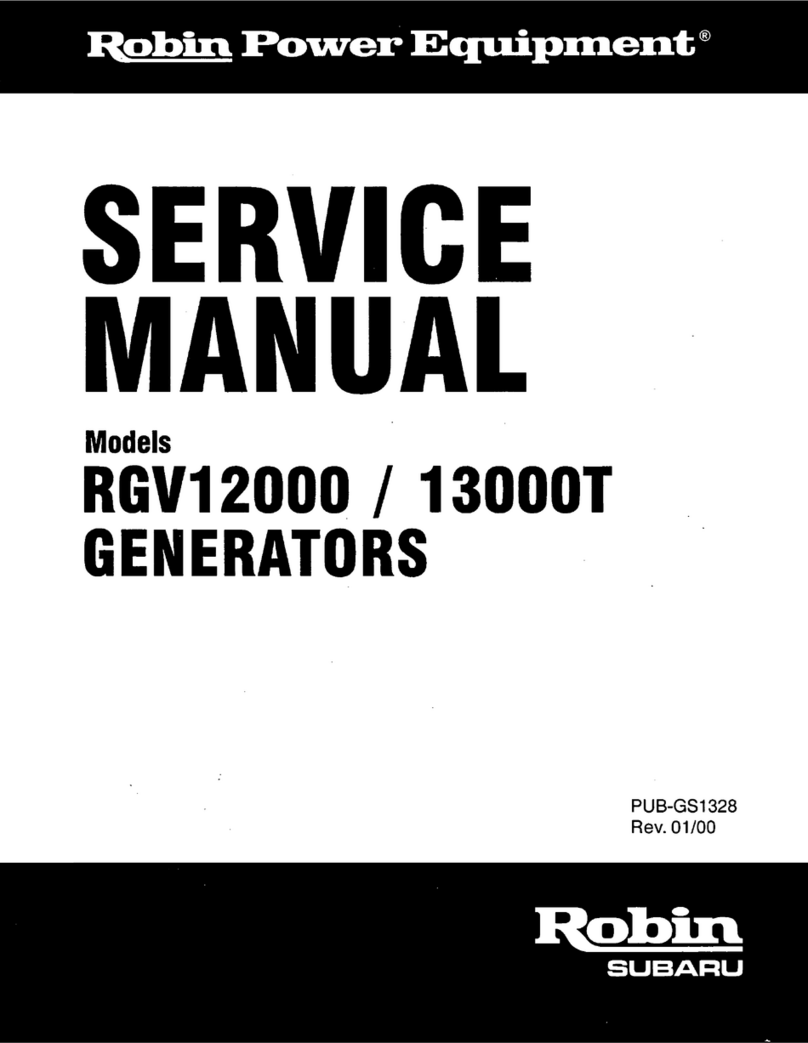
Robin America
Robin America GENERATORS 13OOOT Service manual
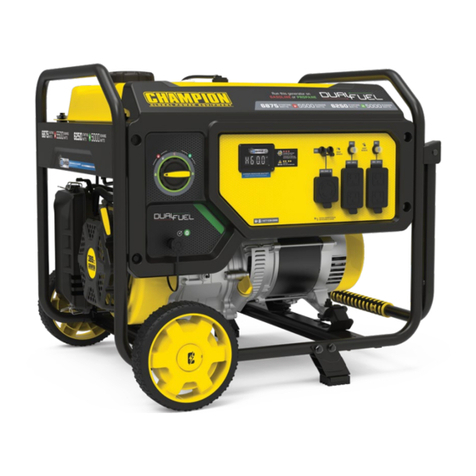
Champion Global Power Equipment
Champion Global Power Equipment 201085 quick start guide
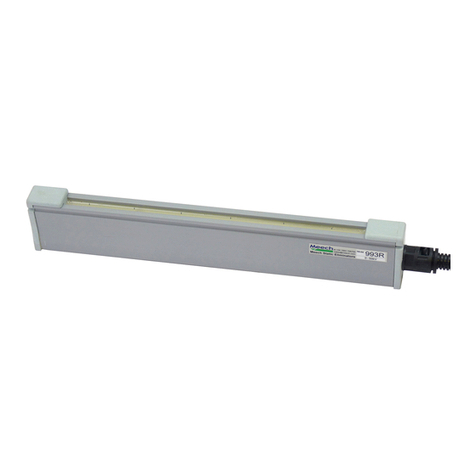
Meech
Meech 993R operating manual

Joy-it
Joy-it JT-DPS6600 manual
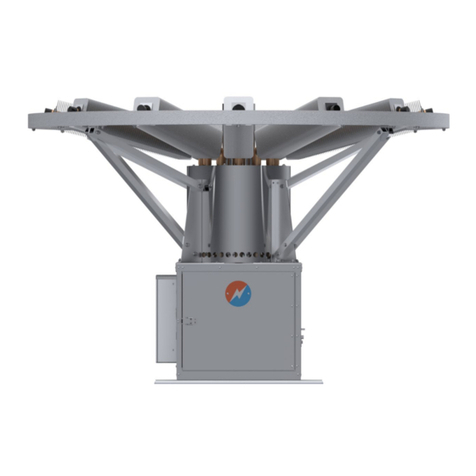
Global
Global 8550-SD operating manual
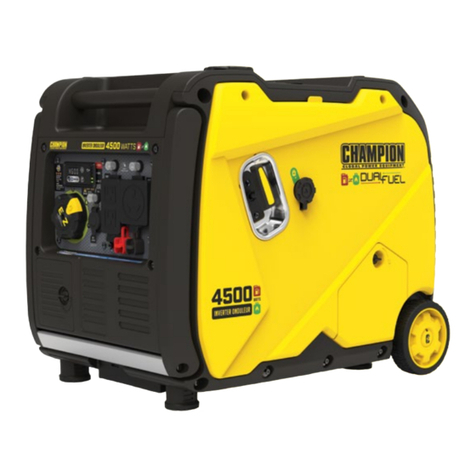
Champion Global Power Equipment
Champion Global Power Equipment 201228 quick start
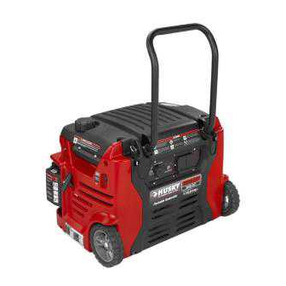
Homelite
Homelite UT902250 Series Operator's manual
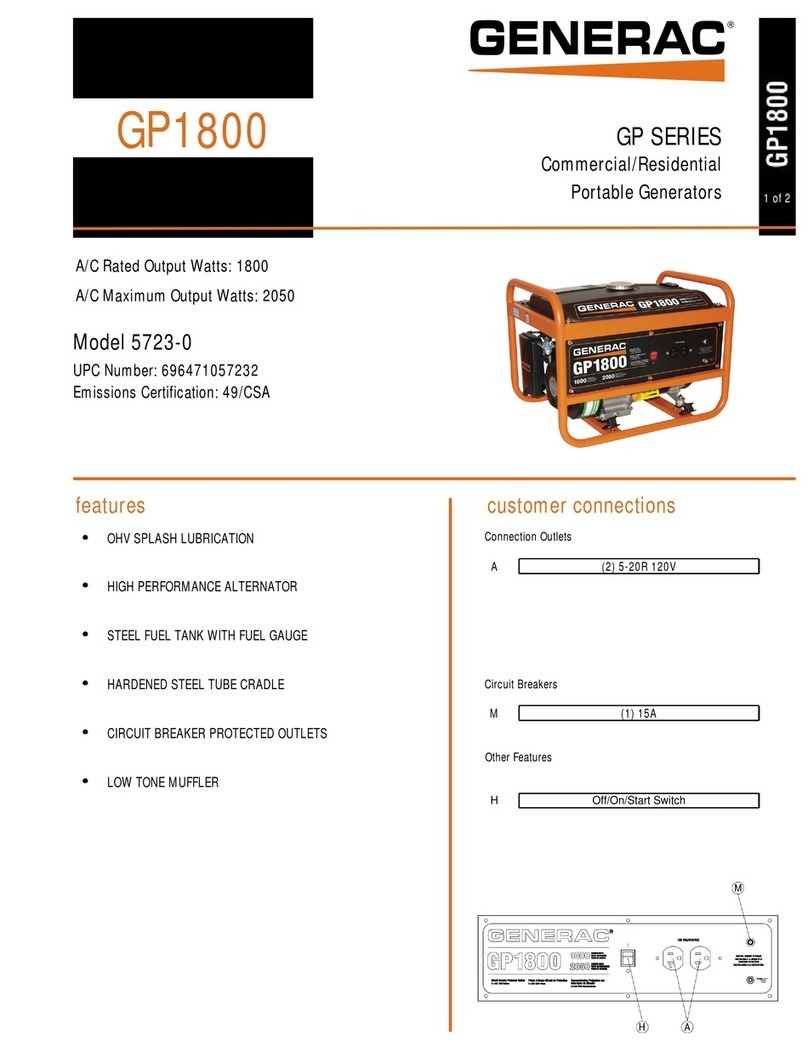
Generac Power Systems
Generac Power Systems GP1800 specification

ACDelco
ACDelco AC-G0002 instruction manual