IMC 04 SERIES Installation guide

04 SERIES FOOD WASTE DISPOSERS
INSTALLATION, OPERATING AND MAINTENANCE MANUAL
PLEASE LEAVE WITH OPERATOR
904 SERIES 28
1204 / 1604 SERIES 17
904 / 1204 / 1604 TROUGH UNITS- SERIES 10
Imperial Machine Company Limited
Unit 1, Abbey Road
Wrexham Industrial Estate
Wrexham LL13 9RF
Tel: +44 (0)1978 661155
Fax: +44 (0)1978 729990
Service Fax: +44 (0)1978 667766
Spares Fax: +44 (0)1978 667759
E-mail: info@imco.co.uk
Website: www.imco.co.uk
A34/022 R11 ECN 8482 May 2016


04 SERIES FOOD WASTE DISPOSERS 1
EC DECLARATION OF CONFORMITY
(Guarantee of Production Quality)
We, Imperial Machine Company Limited of:
Unit 1, Abbey Road, Wrexham Industrial Estate, Wrexham, LL13 9RF
Declare under our sole responsibility that the machine
904 –SERIES 28
1204 / 1604 –SERIES 17
904 / 1204 / 1604 TROUGH UNITS –SERIES 10
As described in the attached technical documentation is in conformity with the Machine Safety
Directive 89/392/EEC as amended by 91/368/EEC and 93/44/EEC and is manufactured under a
quality system EN 29001. It is also in conformity with the protection requirements of the Electro
Magnetic Compatibility Directive 89/336/EEC and is manufactured in accordance with
harmonised standards EN 50-081-2 Generic Emission and EN 50-082-2 Generic Immunity (plus
product specific standards).
It also satisfies the essential requirements of the Low Voltage Directive 73/23/EEC amended by
93/68/EEC.
Approved by E Plumb, Engineering Manager
Signed at Wrexham, Date. May 2016

2 04 SERIES FOOD WASTE DISPOSERS
INDEX
MACHINE DIMENSIONS ...................................................................................................3
INSTALLATION AND HEIGHT ADJUSTMENT .................................................................4
FITTING CONTROL BOX AND SAFETY BAFFLE............................................................4
INTRODUCTION................................................................................................................5
ON DELIVERY...................................................................................................................5
GUARANTEE ....................................................................................................................6
INSTALLATION OPTIONS ................................................................................................6
SELECTION OF SITE........................................................................................................6
SILVER SAVER (OPTIONAL EXTRA) ..............................................................................6
ORDER OF CONNECTION FOR ALL INSTALLATION OPTIONS....................................7
INSTALLATION METHOD 1 –FREE STANDING MACHINES .........................................7
INSTALLATION METHOD 2 –UNDER TABLING WITH HOPPER RIM ATTACHMENT..9
INSTALLATION METHOD 3 –UNDER TABLING WITH WELDED ATTACHMENT .......11
ATTACHMENT OF CONTROL BOX ...............................................................................12
SUPPLY CONNECTION ..................................................................................................13
FITTING OF REMOTE CONTROL BUTTON BOX ..........................................................15
TESTING .........................................................................................................................15
OPERATION OF MACHINE.............................................................................................16
RELEASING A JAM ........................................................................................................16
WATER FLOW CONTROL (OPTIONAL EXTRA) ………………………………………..17
MAINTENANCE...............................................................................................................18
USAGE ............................................................................................................................18
ORDERING SPARE PARTS............................................................................................18
WIRING DIAGRAM –SINGLE PHASE............................................................................19
WIRING DIAGRAM –THREE PHASE.............................................................................20
SEAL ASSEMBLY...........................................................................................................21
MODEL 904 .....................................................................................................................22
- PARTS ILLUSTRATION................................................................................................22
- PARTS LIST ..................................................................................................................23
MODELS 1204 & 1604.....................................................................................................25
- PARTS ILLUSTRATION................................................................................................25
- PARTS LIST ..................................................................................................................26
TROUGH ONLY PAGES 28 TO 34..................................................................................28

04 SERIES FOOD WASTE DISPOSERS 3
MACHINE DIMENSIONS

4 04 SERIES FOOD WASTE DISPOSERS
INSTALLATION AND HEIGHT ADJUSTMENT
FITTING CONTROL BOX AND SAFETY BAFFLE

04 SERIES FOOD WASTE DISPOSERS 5
INTRODUCTION
This machine is intended for the disposal of food waste matter by maceration under an
automatic water flow and discharge into the drainage system.
There are three versions: -
904 with motor size 1.5HP (1.1kW)
1204 with motor size 3.0HP (2.2kW)
1604 with motor size 5.5HP (4.0kW)
Please select your preferred installation method and read these instructions carefully for
trouble-free installation and operation.
Please observe these instructions carefully.
The guarantee applies in this form to installations within the United Kingdom. Contact your
Food Waste Disposer supplier first.
ON DELIVERY
Depending on despatch method, the machine may or may not be packaged in a carton.
Please check the contents against the following list and notify both the Carrier and
Supplier within three days if anything is missing or damaged.
EITHER -
Fully assembled 04 Food Waste Disposer with following items loose: -
Description Quantity
Release Key 1
Feeding Pusher 1
Rubber Floor Sealing Gasket 1
Instruction Handbook 1
Self-adhesive Operating Instruction Plaque 1
Plaque 1
Hopper Rim (Optional) 1
Remote Control Button Box (Optional) 1
OR -
Basic unit 04 Food Waste Disposer for connection to hopper already supplied
and welded into tabling: -
Description (All the above items, plus) Quantity
Baffle 1
Control Box 1
Tube of Sealant 1

6 04 SERIES FOOD WASTE DISPOSERS
GUARANTEE
This machine is guaranteed by IMC for 1 Year from the date of its purchase from
IMC, or from one of its stockists, dealers or distributors. The guarantee is limited to
the replacement of faulty parts or products and excludes any consequential loss or
expense incurred by purchasers. Defects, which arise from faulty installation,
inadequate maintenance, incorrect use, and connection to the wrong electricity
supply or fair wear and tear, are not covered by the guarantee.
The guarantee applies in this form to installations within the United Kingdom only.
Please observe the following instructions carefully.
INSTALLATION OPTIONS
For the Installer:
These Instructions contain important information designed to help the user obtain the
maximum benefit from the investment in an IMC Food Waste Disposer.
Please read them carefully before starting work, and consult with the supplier in the event
of any queries.
Be sure to leave this Instruction Manual with the user after the installation of the machine
is complete.
IMC 04 Food Waste Disposers may be installed in three ways: -
Method 1 - Free standing
Method 2 - Under tabling with Hopper Rim attachment
Method 3 - Under tabling with Welded attachment
All machines are operated from the built-in Control Box or, additionally, from a Remote
Control Button Box which can be supplied as an optional extra.
SELECTION OF SITE
Select the site of the 04 Food Waste Disposer with care so that it is convenient both for
the major source of food waste and for access by machine operators.
The machines are designed to be installed with the control buttons on the left hand end of
the unit and facing front. A space of at least 220mm must be left below the control box to
give access for servicing purposes.
SILVER SAVER (OPTIONAL EXTRA)
When waste disposers are installed next to dishwashing machines it is recommended that
they be fitted with silver saver type safety baffles, which prevent the loss of cutlery into the
units.

04 SERIES FOOD WASTE DISPOSERS 7
ORDER OF CONNECTION FOR ALL INSTALLATION OPTIONS
Install in the following sequence:
1 Secure and seal the machine to the floor
2 Adjust height and level, and where appropriate, fit to tabling
3 Connect waste outlet to the drains
4 Connect water supply piping
5 If appropriate, connect Remote Control Button Box
6 Connect the electricity supply
7 Test and make any necessary adjustments
8 Fix self-adhesive Instruction Plaque in a prominent position adjacent to machine
INSTALLATION METHOD 1 –FREE STANDING MACHINES
1. Remove the three-sided section of the upper cladding (A-Fig 2) by undoing the
screws on either side (B). One part of the cladding remains attached at the waste
outlet (C).
2. Remove the lower cladding which is in two parts (D and E) held together by two
crews (F) and attached to the base casting or frame by screw (G).
3. Position the machine with the waste outlet (C) facing in the chosen direction. Allow
space for the necessary trap.
4. If the hopper needs to be moved to a different position relative to the waste outlet,
undo the four hopper retaining nuts (H). Lift the hopper and turn as required.
Replace ensuring that the gasket (J) remains undisturbed. Replace nuts, or bolts
and nuts (H) and tighten up uniformly all round. Do not over tighten but ensure that
the gasket is nipped firmly and the hopper is rigidly fixed without distortion of its
bottom flange.
WARNING - IF THIS JOINT IS NOT CORRECTLY MADE, WATER LEAKAGE MAY OCCUR
5. Clearly mark the floor through the floor fixing holes in the base casting or frame (K)
or mark out the floor in accordance with the dimensions (Fig 4).
MODEL 904 Fig 4 Models 1204 and 1604

8 04 SERIES FOOD WASTE DISPOSERS
6. Drill the floor in the positions marked for the appropriate fixings. These may be
rawlbolts, coach screws, wood screws or whatever is most suitable for the particular
floor surface and sub-structure. The base casting or frame will accept bolts up to
12mm diameter. Ensure that the fixings are of adequate size and that the floor
surface is sound, level and flat.
7. Place the rubber floor-sealing gasket (L) in position over the four floor holes.
8. Position the machine on the rubber floor sealing gasket taking care that it is not
damaged or displaced.
9. Insert and tighten the floor fixing bolts or screws.
10. Using a spirit level, check that the top of the hopper is level in both planes and that it
is at the required height. To adjust height on the 904 models, slacken the nuts (M) at
the top of the three height adjustment legs (N) and adjust as necessary. When
correct, tighten all nuts (M) and re-check levels. On the 1204 and 1604 models,
slacken the top nuts (M) and adjust as necessary. When correct, tighten all nuts and
re-check levels.
11. Replace the motor cladding sections in the reverse order as described for removal in
points 1 and 2.
12. Continue with SUPPLY CONNECTION INSTRUCTIONS.

04 SERIES FOOD WASTE DISPOSERS 9
INSTALLATION METHOD 2 –UNDER TABLING WITH HOPPER RIM
ATTACHMENT
1. A special rim is welded to the cutout in the tabling. The machine hopper is raised
outside it to make an overlapping joint, which is then sealed with suitable mastic.
2. The hopper rim will normally have been welded in place by the fabricator, and the
tabling should be installed and fixed in position prior to installing the IMC food
waste disposer.
3. The necessary cutout in the tabletop is shown in Fig 5 and the hopper rim is
depicted in Fig 7.
4. Remove the motor cladding as for Method 1, 1.
5. Remove the lower cladding as for Method 1, 2.
6. If necessary, lower the height of the machine
until the top of the hopper will just pass below
the bottom of the hopper rim. Allow about 5 mm
clearance.
7. Height is adjusted as for Method 1, 10.
8. Position the machine accurately below the
hopper rim.
9. Clearly mark the floor through the floor fixing holes in the base casting or frame
(K).
10. Drill the floor as for Method 1, 6.
11. If necessary, change the direction of the waste outlet (C) to suit the installation as
for Method 1, 4.
12. Place the rubber floor-sealing gasket (L) in position over the four floor holes.
Minimum height:
904 1ph: 790mm
904 3ph: 800mm
1204 and 1604: 850mm
Dimensions 904 1204/1604
Q 506 684
R 380 456
All dimensions in mm

10 04 SERIES FOOD WASTE DISPOSERS
13. Position the machine below the hopper rim on the rubber floor-sealing gasket,
taking care not to damage or displace the gasket.
14. Insert and tighten the floor fixing bolts or screws.
15. Raise the machine height until the hopper fits snugly around the welded rim (as
shown at Fig 6). If possible adjust the height so that there is a full overlap, but
ensure that there is a least 10mm overlap.
16. Seal the resulting joint (as shown at Fig 6) thoroughly and carefully with suitable
mastic to achieve a complete and hygienic joint.
17. Replace the motor cladding as for Method 1, 11
18. Continue with SUPPLY CONNECTION INSTRUCTIONS.
Dimensions 904 1204/1604
S 494 672
T 368 444

04 SERIES FOOD WASTE DISPOSERS 11
INSTALLATION METHOD 3 –UNDER TABLING WITH WELDED
ATTACHMENT
The waste disposer hopper is welded directly to the cutout in the tabling. The
fabricator of the tabling will normally undertake the necessary welding work, and a
hopper will have been sent in advance to enable this to be done. Where this is not
the case and a complete unit is to be welded into tabling, it is first necessary to
separate the control box, the hopper and the motor unit. The procedure for this is
the reverse of steps 10 to 16 below and in the section headed
'ATTACHMENT OF CONTROL BOX'.
The re-assembly and installation on site should be carried out only after the tabling
is installed and fixed in position.
1 Remove the motor cladding as for Method 1, 1.
2 Remove the lower cladding as for Method 1, 2.
3 Adjust the height of the top of the motor unit in
the same way as for Method 1, 10 until it is 3mm
lower than the square flange at the bottom of the
hopper.
Minimum height of motor unit: 904 3ph: 370mm,
904 1ph: 380mm, 1204 & 1604: 470mm over
studs. Ensure that the top face of the motor unit is
level and parallel with the hopper flange.
4 Position the motor unit under the hopper flange with the waste outlet (C) facing
the required direction.
5 For 904, ensure accuracy of positioning by temporarily inserting the four bolts
(I) from above the hopper flange. On the 1204/1604 the holes in the hopper
flange must be centred on the studs below.
6 Prepare the floor fixing holes as for Method 1, 5-6.
7 Place the rubber floor-sealing gasket (L) in position over the four floor holes.
8 Position the motor unit below the hopper flange on the rubber floor-sealing
gasket (L), taking care not to damage or displace the gasket.
9 Insert the floor fixing bolts or screws but do not tighten.
10 Carefully insert gasket (J) between the top face of the motor unit and the
hopper flange.
On the 1204 and 1604 machines the gasket has to be fitted over the hopper
attachment studs. Ensure that tearing or crinkling does not damage it. It may
be necessary to adjust the height further to accomplish this, particularly for
1204 or 1604 machines.

12 04 SERIES FOOD WASTE DISPOSERS
11 Raise the machine into contact with the hopper by means of the height
adjustment nuts (M) ensuring that the top face of the motor unit remains level.
12 On 904 machines, insert the four bolts (I) from below the motor unit flange, fit
spring washers and nuts (H) and tighten uniformly. On 1204/1604 machines
the hopper-fixing studs will have engaged during the raising of the machine. Fit
washers and nuts (I) and tighten uniformly.
WARNING -IF THIS JOINT IS NOT CORRECTLY MADE,WATER LEAKAGE MAY OCCUR
13 Again using the height adjustment nuts (M), raise the machine evenly to
produce a slight upward pressure on the tabling. Clamp rubber floor sealing
gasket to the floor.
14 Tighten the lower height adjustment nut in each pair, holding the top one firmly.
15 Tighten the floor fixing bolts or screws.
16 Attach the control box in accordance with the instructions under that heading
ATTACHMENT OF CONTROL BOX
1 Apply a 6mm ring of the supplied mastic sealer around the top face of the
interlock shouldered boss (Y) (Fig 3), avoiding contact with the thread.
2 Ensure that the sealing gasket is in place on the motor cable outlet bush and
pass the cable through the hopper skirt. Raise the control box into position,
locating the cable bush and the interlock boss so that the latter protrudes
through the hopper surface and the ring of mastic is compressed. At the same
time, the water pipe (P-Fig 2) on the hopper should be engaged in the solenoid
valve (Q).
3 Keeping the control box pressed upwards fit 4 screws (R) with fibre and flat
washers from the inside of the hopper. Tighten the screws and the water pipe
connector and check other union nuts.
4 Connect the motor supply cable following the appropriate wiring diagram. 904
machines have in-line interconnections with the motor cable: 1204 and 1604
machines should be connected direct to the motor terminal box. Ensure that
the Earth cable is connected.
5 Fit the safety baffle by locating it on the baffle hinge rod (S) and screw home
the spring loaded interlock knob (T).
NOTE- Check that the safety baffle knob lines up properly with the interlock
screw and engages freely.
6 Replace the motor cladding as for method 1,11
7 Continue with the SUPPLY CONNECTION INSTRUCTIONS

04 SERIES FOOD WASTE DISPOSERS 13
SUPPLY CONNECTION
WASTE OUTLET CONNECTION
The machines are fitted with a standard 2”BSP female threaded outlet. The size of these
outlets must not be reduced, and the drainpipe should run in 54mm outside diameter pipe
work as far as its junction with the main pipe or outside manhole connection. The length of
run between the machine and the main junction must be kept to a minimum and the pipe
run must have a fall of at least 1 in 7. A running trap should be fitted, although “P”or “S”
type traps can be used. Do not use bottle traps. Changes of direction should be made by
bends rather than elbows and cleaning eyes should be fitted where possible, in
accordance with standard plumbing practice. Copper pipe and compression fittings should
be used, but plastic tubing is acceptable to most drainage authorities.
IMC 04 Food Waste Disposers must have an independent waste pipe, which does not also
serve sinks, dishwashers and similar equipment. It is imperative that the waste pipe from
the Disposer bypasses any grease trap, which may be present. If this outlet is positioned
below the control box, it is important to use fittings, which give at least the minimum
220mm clearance, required for service access.
WATER SUPPLY CONNECTION
A 15 mm cold water supply is required on 904 machines, 22mm on 1204 and 1604
machines, and the connection should be made to the service valve (V-Fig 2) supplied with
the machine. The head of water should not be less than 0.18 bar (1.8m). The direction of
the water supply connection on the IMC 04 Food Waste Disposers may be altered
between the two positions shown at Fig 9. Loosen the compression-fitting nut (U-Fig 2)
and gently turn the elbow to the required position. If the water pipe is run below the control
box, it is important to give at least the minimum 220mm clearance required for service
access.
When fitted with the standard hopper these machines have approval from the Water
Research Centre for connection to a water supply via a storage cistern to which no other
fittings are to be connected.
An alternative hopper with water inlet is available: it provides a Class A air gap so that the
machine can be connected directly to a mains water supply.
The rate of flow required for normal food waste is as follows:
(1) ASSEMBLE WATER
ASSEMBLY AND CLAMP
NUT LOOSELY TOGETHER
AND PLACE OVER
WATER SUPPLY PIPE AS
FAR AS IT WILL GO
(2) TIGHTEN UP CLAMP
NUT, WITH WATER
ASSEMBLY RUNNING
PARALLEL TO SIDE OF
BAFFLE SLOT, AS SHOWN

14 04 SERIES FOOD WASTE DISPOSERS
Model 904 14-18 litres per minute
Model 1204 18-27 litres per minute
Model 1604 27-36 litres per minute
Every machine is run and tested by IMC
before dispatch. The water flow adjustments
are made then but will require resetting when
installed in the final location. The pipefittings
supplied with the machine include a service
valve (V) and this should be set fully open.
Ensure that water supply demands made by
other equipment served by the same supply
pipe do not starve the Waste Disposer. To
avoid this, run the piping in a size larger than
recommended above and reduce at
connection point to the machine.
ELECTRICITY SUPPLY CONNECTION
All electrical work must be carried out by a qualified electrician and in accordance with
current local regulations.
Examine the rating plate attached to the machine to ensure that the characteristics shown
are correct for the supply available. The rating plate is located on the control box.
Sample Rating Plate
It is recommended that the machine be connected to the electricity mains supply through a
suitable over-current protection and an isolator providing at least 3mm separation in all
poles. The tabulation below illustrates typical fuse ratings for an ambient temperature of
25-35°centigrade. Should the environment temperature be greater than this, de-rate
accordingly.
The mains lead fitted to the machine is the minimum required for individual connection to
the mains supply. Site conditions may vary with additional length of cable run,
encapsulation in trunking bunched with other cables etc. Should this apply, the electrician
must alter the lead accordingly.
W
ARNING –
T
HIS MACHINE MUST BE EARTHED

04 SERIES FOOD WASTE DISPOSERS 15
Machine Ratings and Cable Coding
FITTING OF REMOTE CONTROL BUTTON BOX
In installations where the standard positioning of the control box is inconvenient or
inaccessible, a remote unit may be installed at some other location by connecting into the
control box. The remote button box may also be used as a repeater providing control from
two locations.
1. Fit the remote button box in the required position i.e. on the wall, in tabling apron,
etc.
2. Connect cable into the control box terminal block as wiring diagram, removing the
blanking plug (X-Fig 2) and replacing it with cable gland supplied.
If your IMC 04 Food Waste Disposer was initially ordered with a remote control button box,
this unit will be supplied pre-wired to the control box.
TESTING
Check finally that all supply connections are correctly made and soundly fixed, that nothing
has been left in the grinding chamber, that the rotor is free to rotate (use the release
wrench if necessary) and that the interlock knob is screwed down.
The machine is now ready to operate.
Machine Ratings
Model Electricity
Supply
Volts-Phase-Hz
Output
kW Input
kW Fuse
Rating
Amps
904 230-1-50
220-1-60
254-1-60
1.1
1.45
16
904 400-3-50
220-3-60
440-3-60
480-3-60
1.1
1.45
6
1204 400-3-50
240-3-60
440-3-60
380-3-60
2.2
2.75
16
1604 400-3-60
440-3-60
230-3-60
220-3-50
4
4.82
16
Ma
ins cable coding
3 phase
5 wire 3 phase
4 wire 1 phase
L! Black Blue Brown
L2 Black Black
L3 Brown Brown
N Blue Blue
Earth Green/Yellow Green/Yellow Green/Yellow

16 04 SERIES FOOD WASTE DISPOSERS
OPERATION OF MACHINE
INITIAL OPERATION
1. Switch on the electricity supply
2. Press the green button on the control box. The machine will run and the water will
flow.
3. Inspect the waste piping for leaks. Estimate that the volume of water flowing is
correct for the particular model –refer to WATER SUPPLY CONNECTION. If
adjustments are needed, use a screwdriver to adjust the position of the slot on the
control screw of the service valve (V –Fig 2). Maximum flow is with the slot in line
with the pipe.
4. Try a small amount of food waste to check disposal and that no internal
obstruction in the waste pipe will cause a blockage.
5. With the machine running unscrew the interlock knob (T –Fig 3). The machine
will switch itself off almost immediately. By the time the knob is fully unscrewed and
the safety baffle open, the rotor in the grinding chamber will have completely
stopped.
When these checks, tests and adjustments are completed, the 04 IMC Food Waste
Disposer is ready for use.
NORMAL OPERATION
1. Ensure that safety baffle is closed and the interlock knob is screwed down fully.
2. Press green button to start. This also switches on the water flow
3. Feed waste into the hopper at a uniform rate, using the feeding pusher if necessary.
4. If the machine stalls or is severely overloaded, it may cause the automatic cutout
on the motor to operate. Once the motor has cooled it can be re-started. Note
that stopping the motor and restarting it reverses the direction of the rotor and can
help to relieve an overload. If the machine remains stalled, see RELEASING A
JAM below.
5. If the main rotor seal is damaged and water passes through it, this will be revealed
by water passing through the leak indicator tube and collecting beneath the
machine
RELEASING A JAM
As a result of a jam occurring, the machine will stall and stop. Switch off the machine at
the mains, unscrew the interlock knob and lift the safety baffle. Engage the prongs of the
release key into the vanes of the rotor. Exert pressure in either direction to free the
blockage and remove the offending item by hand. Check that the rotor is free to rotate
through 360°and withdraw the release key. Close the safety baffle and screw down the
knob fully.

04 SERIES FOOD WASTE DISPOSERS 17
WATER FLOW CONTROL (OPTIONAL EXTRA)
Your IMC Food Waste Disposer is equipped with a device with which the operator
can adjust the volume of water that flows through the Food Waste Disposer whilst
it is processing food waste.
To reduce water flow, simply turn the water control knob to the left i.e. anti-
clockwise.
To increase water flow, turn the knob to the right i.e. clockwise.
When operating the FWD, the water flow control should initially be set at its highest
position before turning it down whilst the waste is being processed. The rate of
water flow can be adjusted up or down for each installation to take account of
unique factors such as the length of, and number of bends in, the drainage piping,
the fall of the pipe, the amount of liquid already present in the waste and whether a
Dewaterer and / or Grease Trap is fitted downstream of the FWD.
When operating the system on reduced water flow it is recommended that, at the
end of each “session,”the water flow is turned up full for a minimum of 15 seconds
to ensure that any residue is flushed through the drainage system. A bucket of
warm, soapy water poured into the FWD’s hopper at the end of each day will both
clean the equipment and help disperse any residual solids in the piping.
Note: The control knob operates within an arc from vertical (min water flow) to the
3 o’clock position (max water flow). Please do NOT force the control knob beyond
its end stop positions.
Unless the FWD is being used to process food that is either consistently very wet
or very dry, IMC recommends that the water pressure should be set at the mid-
point of the published scale when the equipment is first installed.

18 04 SERIES FOOD WASTE DISPOSERS
MAINTENANCE
Daily: Clean down thoroughly after use especially inside the hopper. Unscrew the safety
interlock knob and open the baffle to gain access internally
Cleaning is assisted by the use of a low-pressure spray, an IMC Pre-Rinse Spray
or a Reel-Kleen retractable hose reel.
Wipe over the exterior of the machine, including the back areas not normally
visible. Proprietary cleaners may safely be used but avoid particularly aggressive
cleaners and neat bleach solutions.
6 monthly: Clean water supply filter (W –Fig 2)
12 monthly: Check for motor bearing wear by:
-Sound of motor
-Side movement of rotor
WARNING –BEFORE ATEMPTING SERVICE WORK ENSURE THAT ELECTRICITY SUPPLY
AND WATER SUPPLY ARE TURNED OFF AT THE MAIN SUPPLY AND WATER STOPCOCK.
USAGE
1 The IMC 04 Food Waste Disposer is designed for the disposal of food waste.
Fat can safely be disposed off provided it has solidified.
2 DO NOT PUT STRING, CLOTH, PLASTIC, WIRE, GLASS, CORK OR METAL
OBJECTS INTO THE MACHINE.
3 Always start the machine before putting waste into it. Introducing mixed waste
rather than accumulating and introducing waste of a similar nature into the
machine will obtain more efficient disposal.
4 For environmental reasons, the grinding of inorganic materials should be
avoided.
ORDERING SPARE PARTS
In the event that spare parts or accessories need to be ordered, please always quote the
SERIES AND SERIAL NUMBER of the machine. This is to be found on the rating plate
located near the supply cable.
For installations outside the UK please contact your supplier.
For information on IMC spares and service support (if applicable), please call IMC on +44
(0) 1978 661155. Alternatively, contact us via email or fax:
IMC Service Desk Fax: +44 (0) 1978 667766
IMC Spares Desk Fax: +44 (0) 1978 667759
Table of contents
Other IMC Garbage Disposal manuals
Popular Garbage Disposal manuals by other brands
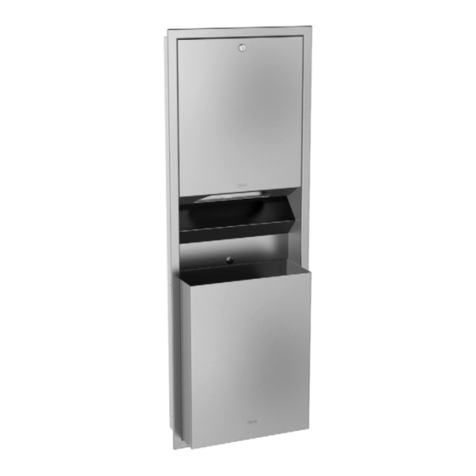
Franke
Franke RODX602E Installation and operating instructions

Altrad
Altrad BELLE SF460 Operator's manual

KitchenAid
KitchenAid KCDB250G - Food Waste Disposer installation instructions

KitchenAid
KitchenAid KCDB250G1 parts list

Weber mt
Weber mt 0116533 Operating and maintenance manual
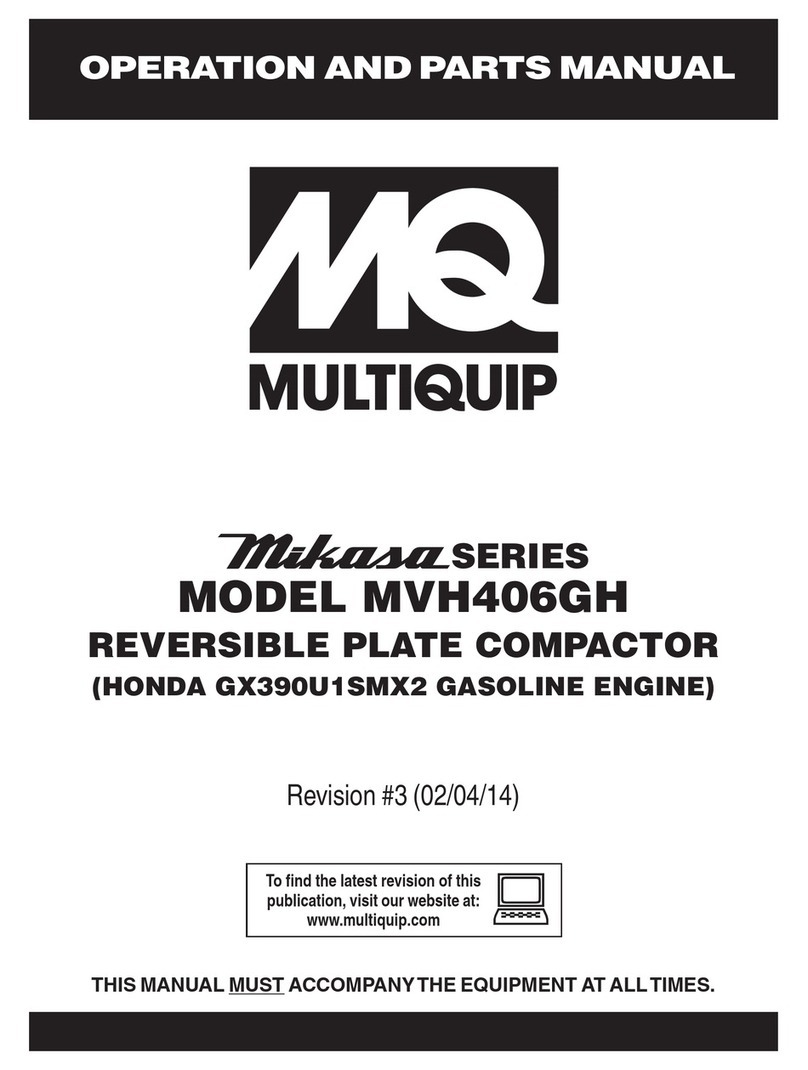
MULTIQUIP
MULTIQUIP Mikasa Series MVH406GH Operation and parts manual
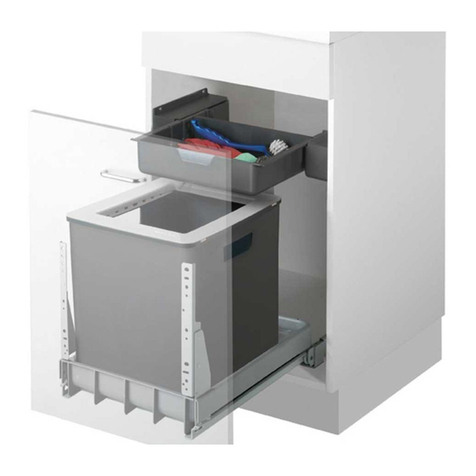
Mullex
Mullex BOXX 40-R Assembly instructions and template

KitchenAid
KitchenAid 4151847 WHITE installation instructions
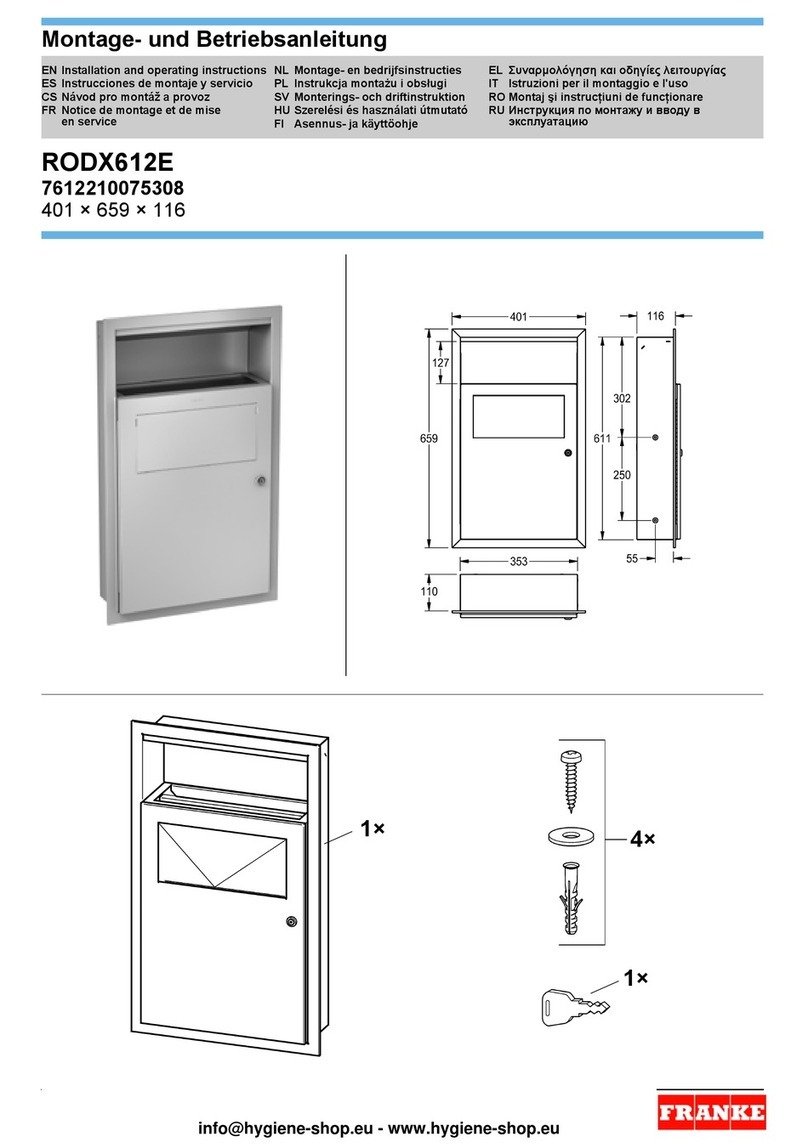
Franke
Franke RODX612E Installation and operating instructions
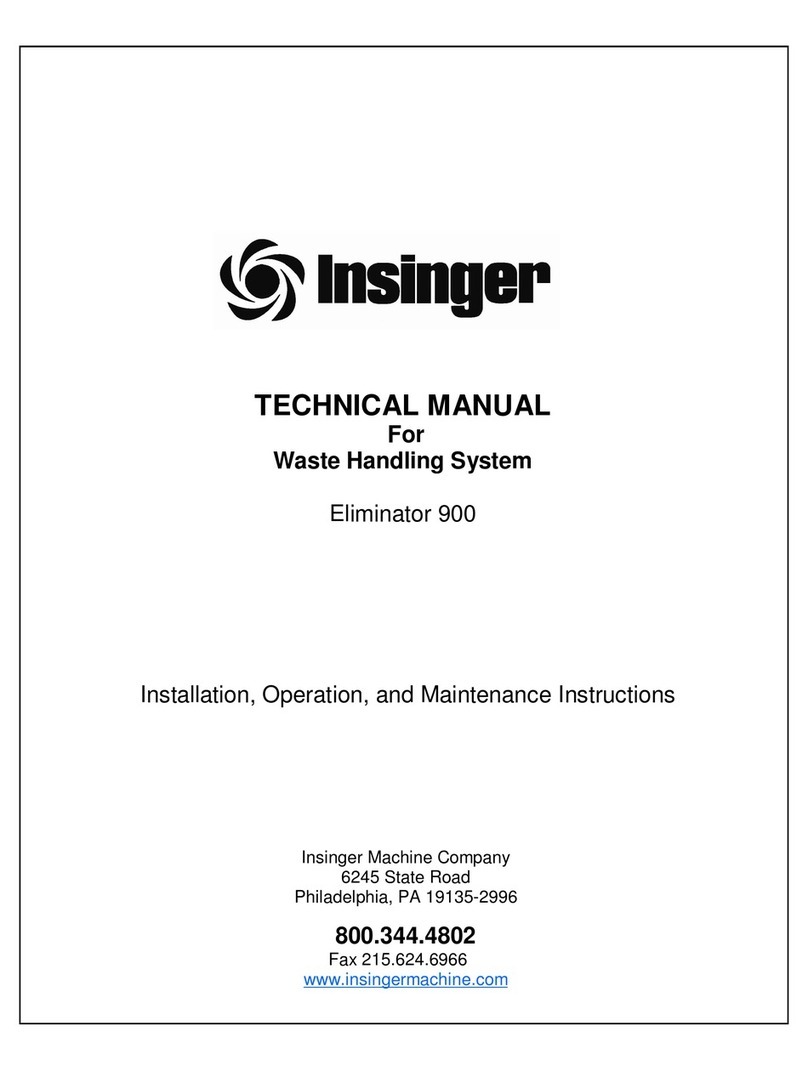
Insinger
Insinger Eliminator 900 Technical manual

KitchenAid
KitchenAid Imperial KCDI250 Use and care guide
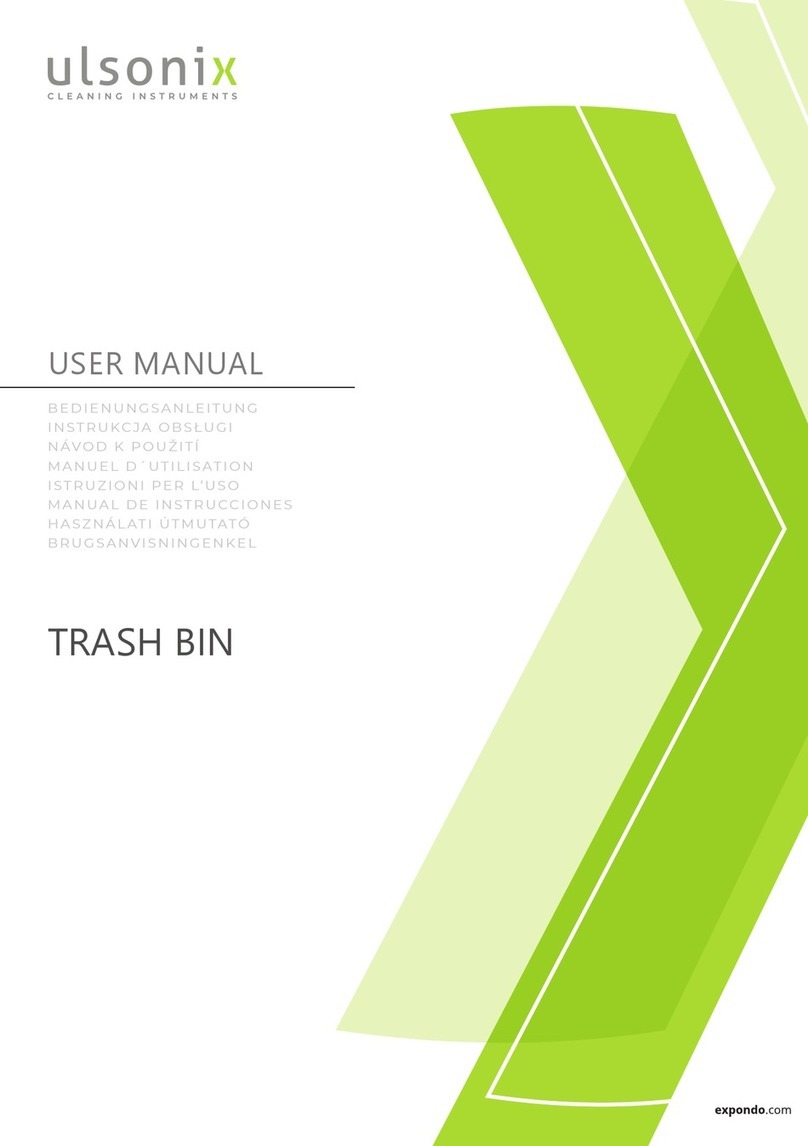
ulsonix
ulsonix ULX-GB28 user manual