IMI SENSORS 685a User manual

IMI vibration switch
INSTALLATION - OPERATION - MAINTENANCE
Z0929039_A ISSUED 03/2017 READ AND UNDERSTAND THIS MANUAL PRIOR TO OPERATING OR SERVICING THIS PRODUCT.
USER MANUAL

2
contents
Overview
General Features ................................................................................................3
Warnings...............................................................................................................3
Installation
Field Wiring..........................................................................................................5
Internal Switch Rating........................................................................................5
Operation
Switch Setup .......................................................................................................6
Adjustment ...........................................................................................................7
Switches with Remote Reset...................................................................................8
Commissioning.........................................................................................................10
Specifications ...........................................................................................................11
Dimensions................................................................................................................11

3
overview
The IMI 685A mechanical switch is a shock sensitive mechanism for shutdown
of the electric fan motor. This switch uses a patented linear adjustment mag-
netic latch technology to ensure reliable operation. Pushing the reset button
moves the tripping latch into a magnetically held position. A shock/vibration
will move the magnet beyond this holding position, thus freeing the spring
loaded tripping latch to transfer the contacts and shut down the machinery.
General Features
• Designed to detect severe shock/vibration in three planes of motion
• Fully adjustable, with patented linear adjustment technology
• Includes magnetic latching feature
• Accommodates normally open (NO) and normally closed (NC)
wiring schemes
• Manual reset button with red trip indicator
• NEMA 4X (IP66) rated enclosure
• Remote options
- 24VDC Remote Reset
- 120VAC 60Hz Remote Reset
- 240VAC 50Hz Remote Reset
• Top cover is secured with socket head cap screws for easy access to
wiring terminals
If using a VFD to control fan speed, identify and lock out system resonant
frequencies during start up and commissioning. Prolonged operation at
resonant frequencies may lead to excessive vibration, equipment damage
and/or possible injury.
AC and DC input signals and power supply voltages could be hazardous.
• Do not connect live wires to screw terminal plugs
• Do not insert, remove, or handle screw terminal plugs with live wires
connected
• Do not make any adjustments to the set-point with live wires present
• Do not open the unit if fan motor is powered or running
• Do not open the unit if the relays are energized
• Do not open the unit if the reset coil is energized
• Do not make any adjustments if fan motor is energized and/or power
is present anywhere in the switch
Warning
Warning

4
installation
Before Installation
• Stop the fan motor
• Disconnect all electrical power to the fan motor
• Make sure the machine cannot operate during installation by following
proper lock-out tag-out procedures
• Follow all cooling tower safety warnings
• Read and follow all installation instructions
Remove power before opening the cooling tower access door. Stop the
fan motor and disconnect all electrical power before beginning the wiring
operation. It is your responsibility to have a qualified person install and
wire the unit and make sure it conforms with NEC and applicable codes.
The vibration switch is sensitive to shock and vibration in all three planes of
motion – up/down, front/back and side/side.
1. Firmly secure the unit to the equipment using the base foot mount.
2. Mount the enclosure with conduit port located downwards.
3. For retrofit installations, this switch may have a different footprint than an
existing switch. Field drill four holes into the existing mounting plate or me-
chanical beam and mount switch with hardware based on mounting hole
dimensions below. Replacement mounting plate and hardware can also be
purchased through SPX, if desired.
4. Make the necessary electrical connections to the vibration switch. See
Figure 1 for electrical terminal locations and for typical wiring. Do not
exceed voltage or current ratings of the contacts. Follow appropriate
electrical codes/methods when making electrical connections. Be sure that
the run of electrical cable is secured to the machine and is well insulated
from electrical shorting. Use of conduit is recommended.
If the electrical cable crosses a pivot point such as at the pivot of the walk-
ing beam, be sure to allow enough slack in the cable so that no stress is
placed on the cable when the beam moves.
If conduit is not used for the entire length of wiring, conduit should be used from
the electrical supply box to a height above ground level that prevents damage
to the exposed cable from the elements, rodents, etc, or as otherwise required
by applicable electrical codes. If conduit is not attached directly to the switch,
use a strain relief bushing and a weatherproof cap on the exposed end of the
conduit. A “drip loop” should be provided in the cable to prevent moisture from
draining down the cable into the conduit should the weatherproof cap fail.
Warning
Note

5
installation
VFD Safety/Run Circuit or Motor
Starter Contactor Coil Circuit
BMS Alarm
Ground
Sw 1
Sw 2
COMMONNC NO
NC NO COMMON
Figure 1
Field Wiring
Typically this switch is used to shut off the tower fan motor and provide an alarm.
The switch has two SPDT (single pole double throw) contacts operating in
unison providing a contact closure or contact opening in the event of a trip.
The NC contact of Sw 1 may be used to complete a safety/start circuit of a
VFD or motor starter. When the switch trips this contact will open and break
the circuit. The NO contact of Sw 2 may be used to complete the alarm circuit.
When the switch trips this contact will close and complete the alarm circuit.
Internal Switch Contact Ratings
The vibration switch uses two SPDT switch terminals with removable screws
for all connections (see below). Wire the switch contacts depending on ap-
plication, either Normally Open or Normally Closed. The Normally Open and
Normally Closed are referenced to the Common screw terminal connector.
Do not exceed the maximum relay ratings as noted below.
Rated Voltage Resistive Load Inductive Load Motor, Lamp Load
NC NO
AC 125V 15A 10A 4A 2A
AC 250V 15A 10A 3A 1.5A
AC 480V 3A 2A - -
DC 8V 15A 15A - -
DC 14V 15A 10A - -
DC 30V 6A 5A - -
DC 125V 0.5A 0.05A - -
DC 250V 0.25A 0.03A - -
Caution

6
operation
Switch Setup
The IMI switch is factory set to trip in the event of excessive shock/vibration
within its capability and should not require adjustment. If adjustment is required,
either the trip point needs to be adjusted or the switch is being subjected to an
abnormally high vibration or shock. Should adjustment be desired, reference
the procedure below or contact your local Marley representative for assistance.
Adjustment Procedure
Resetting the vibration switch may cause the fan motor to operate. Follow
lock out, tag out procedures.
Press the reset push-button to engage the magnetic latch, Figure 2. Be sure
the reset button remains depressed. If it does not remain depressed, turn
the sensitivity adjustment screw clockwise until it does, Figure 3. Turning the
adjustment screw clockwise increases the set-point at which the switch will
trip making it less sensitive to vibration. Turning the adjustment screw counter-
clockwise reduces the set-point making it more sensitive to vibration. The
adjustment range is 0 to 7g. Refer to Figure 4 for the factory default setting.
Factory Setting
The switch should be factory set. To confirm factory setting remove the lid and
measure the gap distance between the edges of the cylinder and the square
magnet, see Figure 4. If the gap setting is not 1/4" rotate the adjustment screw
clockwise or counter clockwise until a 1/4" (6mm) gap is obtained, Figure 3.
Using a 1/4" wide metal strip as a gauge works best.
Warning
Figure 2

7
operation
A slight difference of 1/16" either way creates a large change in the trip
point setting.
Turning the adjustment screw clockwise increases the trip point making the
switch less sensitive to shock. Turning the adjustment screw counter clockwise
decreases the trip point making the switch more sensitive to shock.
Adjustment — If Required
Make sure the switch is set per “Factory Setting” before making any
adjustments.
Operate fan motor as follows:
Motor starter operation (full voltage or DOL start):
• Start the fan motor. If the switch trips rotate the adjustment screw clockwise
1/4 turn, reset the switch and restart the motor.
VFD operation:
• If the VFD has a bypass motor starter follow the above procedure first using
the bypass motor starter.
• Using the VFD speed control, slowly ramp up the motor speed to full speed
allowing 5 seconds for every 2 hertz of speed change. If the switch trips
during the ramp up procedure, consider performing a vibration analysis on
the tower operation.
Rotating the adjustment screw clockwise increases the trip point. Turning
counter clockwise decreases the trip point
Note
Note
Note
Figure 3

8
Gap Setting
The factory setting is determined by a 1/4" gap measurement illustrated in
Figure 4. Adjust the sensitivity screw clockwise or counter-clockwise to achieve
the dimension shown.
Switches with Remote Reset Option
A switch with the remote reset option uses an internal electrical solenoid with
a plunger to remotely reset the internal trip mechanism. The solenoid requires
electrical power to operate and is typically provided from the starter equipment
in conjunction with a remote reset push-button station.
A mechanical switch is designed to sense a high shock or severe vibration
event and cannot sense low vibration frequencies sometimes associated with
cooling towers. When the switch trips it typically means a catastrophic event
may have occurred. Upon a trip event, a thorough inspection of the tower, fan
and drive train should be performed before restarting the fan motor. The opera-
tor should not simply reset the switch without an inspection being performed.
Figure 4
1/4" GAP
operation
Power Supply Source for
Remote Reset Circuit
Momentary Pushbutton
Operator Station
Note: Add trip delay
timer circuit if
required for hard
starting equipment
Operator staton provided by others
Figure 5

9
operation
The switch can be remotely reset after being tripped by applying the correct
voltage across the reset terminal as shown below in Figure 5.
There is no positive/negative polarity needed for the wiring. While
the power is applied to the remote reset terminals, the switch
cannot be tripped.
24 VDC Switch—A 24VDC power supply is needed to remotely reset the
switch by energizing a solenoid. The 24VDC power source must be capable
of supplying at least 2A of current. Upon power up, the unit will need the 2A
to energize the remote reset coil. Depending on ambient temperature, this will
decrease to approximately 0.4A after 5-10 seconds. After that time, the coil
can be energized indefinitely.
To protect the remote reset solenoid from overheating, the unit has a built in
thermistor that will limit the coil current after a certain amount of time. This
time is dependent on ambient temperature and if the reset coil was recently
energized. Since the coil needs the peak current only for a short period of
time, the thermistor lowers the current but it is still strong enough to hold the
switch in reset mode.
The switch will start feeling warm to the touch if the remote reset coil is
left energized for more than a few minutes.
120 VAC Switch—A 120VAC, 60Hz power supply is needed to remotely reset
the switch by energizing a solenoid. Upon applying 120VAC to the solenoid,
the unit will need 184mA to energize the remote reset coil. At standard ambi-
ent temperature, the solenoid has a 25% “on” 75% “off” cycle.
Maximum allowed On Time (remote reset energized) versus minimum
Off Time (remote reset de-energized).
On Time ( 25% ) Off Time ( 75% ) Total Time( 100%)
4 Minutes ( Max ) 12 Minutes 16 Minutes
2 Minutes 6 Minutes 8 Minutes
1 Minute 3 Minutes 4 Minutes
30 seconds 1.5 Minutes 2 Minutes
If using the solenoid for a power on delay, do not exceed the “on” times
listed. If the “on” time exceeds 4 minutes and/or the “off” time is shortened
before energizing the solenoid again, the solenoid will be permanently
damaged.
Note
Note
Note

10
operation
240 VAC Switch—A 240VAC, 50 Hz power supply is needed to remotely reset
the switch by energizing a solenoid. Upon applying 240VAC to the solenoid,
the unit will need 92mA to energize the remote reset coil. At standard ambient
temperature, the solenoid has a 25% “on” 75% “off” cycle.
Maximum allowed On Time (remote reset energized) versus minimum
Off Time (remote reset de-energized).
On Time ( 25% ) Off Time ( 75% ) Total Time( 100%)
4 Minutes ( Max ) 12 Minutes 16 Minutes
2 Minutes 6 Minutes 8 Minutes
1 Minute 3 Minutes 4 Minutes
30 seconds 1.5 Minutes 2 Minutes
A power ON delay may be required when starting tower fan motor across
the line (DOL). A 15 second delay is suggested to allow the fan to come
up to full speed before allowing the switch to activate.
Commissioning
Before testing the switch make sure it is reset. If the red plunger protrudes
outwards push the reset button inwards to reset the switch, Figure 1.
The switch is shock sensitive. Using a dead-blow hammer strike the lid or switch
support beam to trip the switch. A trip is visually indicated by a protruding
red stem shown in the reset button, Figure 1. Reset the switch for operation.
Note

11
Model Reset Relay Contact Output Measurement Range Frequency Range
2396245 Manual external reset button
One - DPDT form “C”
15 amp at 120 VAC
Inertial 1-7 g pk
0-68.7 m/s2pk
adjustable
0 to 6000 cpm
0-100 Hz
2442494 Manual external reset button and
24 VDC remote reset solenoid
2442495 Manual external reset button and
120 VAC 60 Hz remote reset solenoid
2442496 Manual external reset button and
240 VAC 50 Hz remote reset solenoid
Model Startup Delay Trip indication Enclosure type Conduit fitting Electrical Certification
2396245 No
External
red indicator
NEMA 4X / IP66
epoxy painted
aluminum
One - 3/4 inch NPT
threaded female
connection
2442494 Timer required in
customer’s start
circuit
2442495
2442496
Specifications
Dimensions
3/4 - 14 NPT
CONDUIT PORT
3.70 [94.0]
3.70 [94.0]
.250 [6.35]4X THRU
3.30 [83.8]
SENSITIVITY
ADJUSTMENT
SCREW
GROUND SCREW 4.35 [110.5]
4.35 [110.5]
2.75 [69.9]
RESET SWITCH
2.05 [51.9]
C US
®

Z0929039_A | ISSUED 03/2017
COPYRIGHT © 2017 SPX CORPORATION
In the interest of technological progress, all products are subject to design
and/or material change without notice.
IMI vibration switch
USER MANUAL
SPX COOLING TECHNOLOGIES, INC.
7401 WEST 129 STREET
OVERLAND PARK, KS 66213 USA
spxcooling.com
Table of contents
Other IMI SENSORS Switch manuals
Popular Switch manuals by other brands
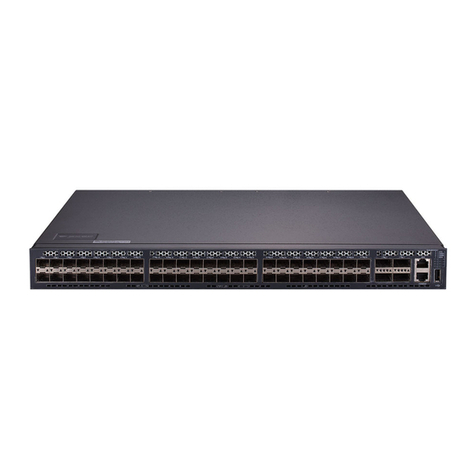
Bdcom
Bdcom S5864 Hardware installation manual
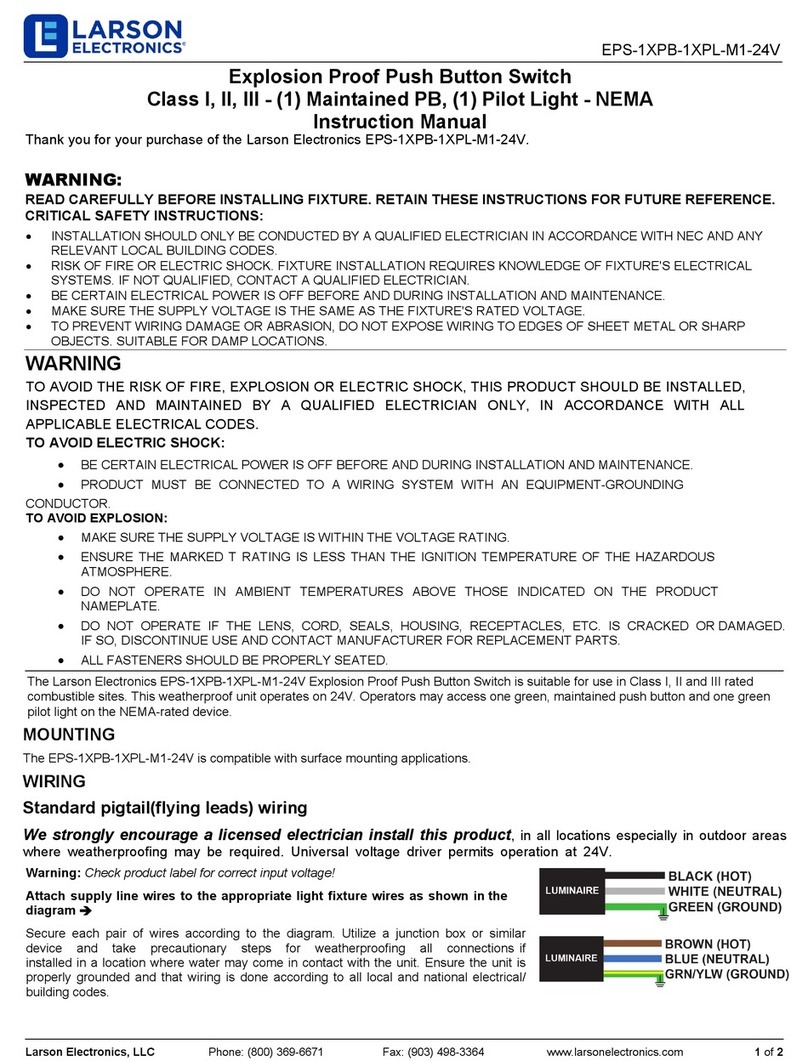
Larson Electronics
Larson Electronics EPS-1XPB-1XPL-M1-24V instruction manual
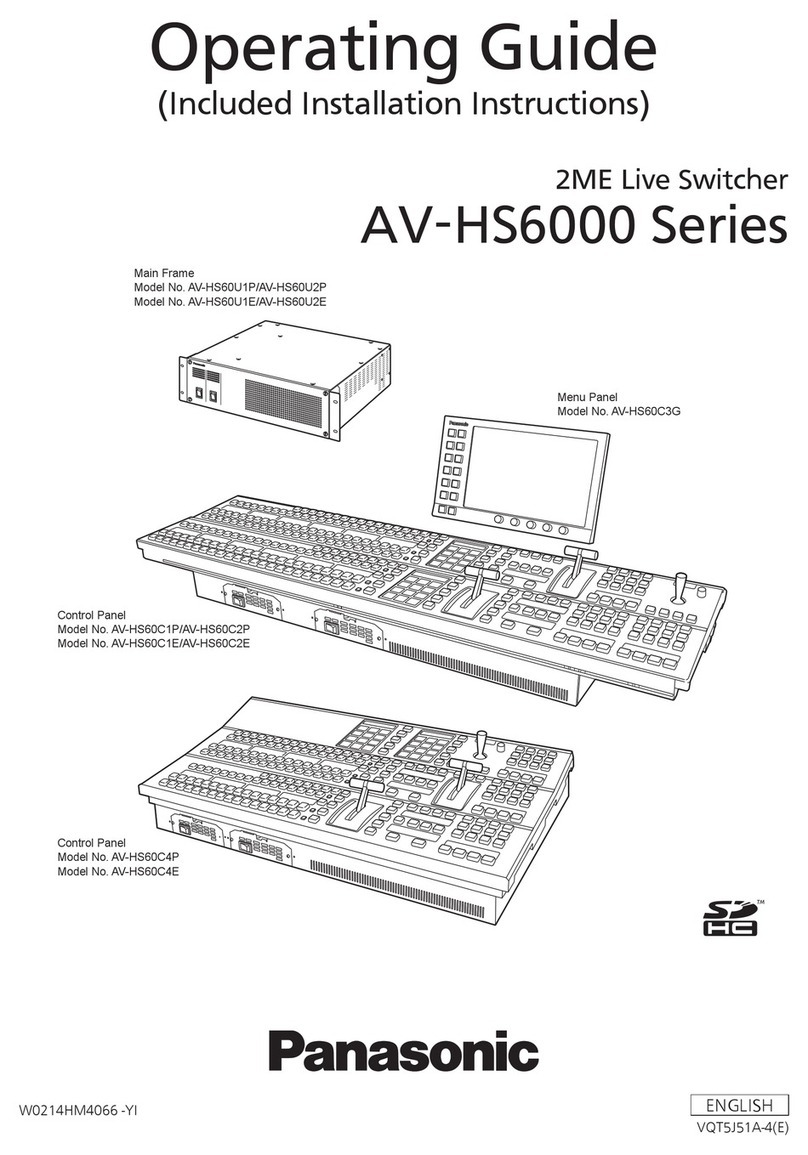
Panasonic
Panasonic AV-HS6000 Operation guide
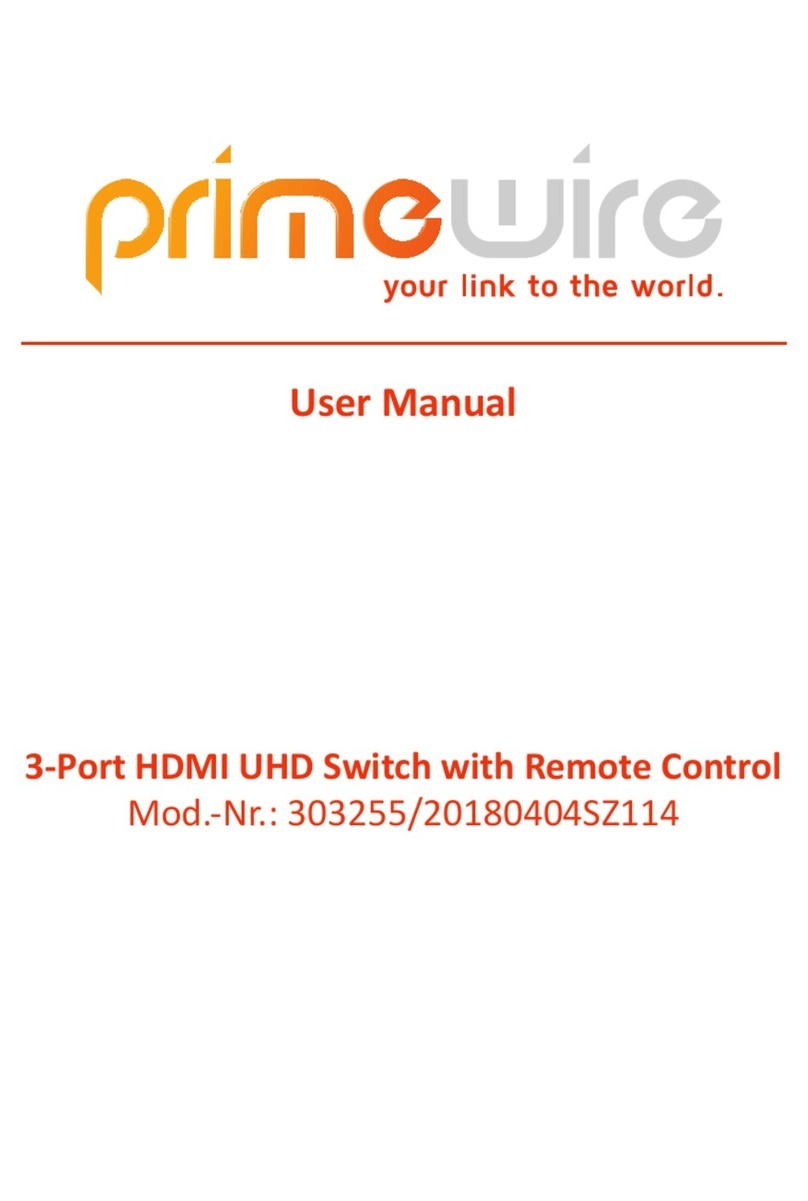
Primewire
Primewire 303255 user manual
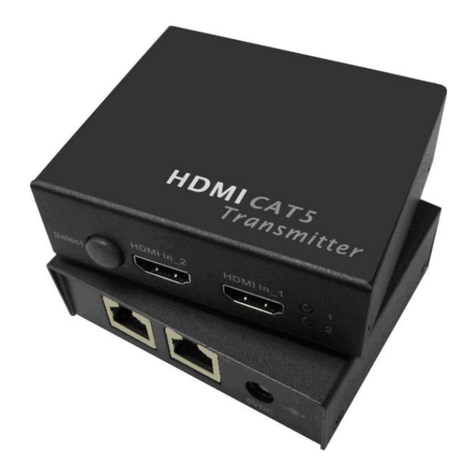
Lindy
Lindy 38000 manual
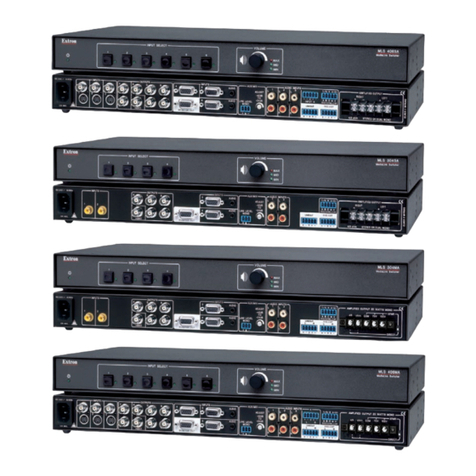
Extron electronics
Extron electronics Extron MediaLink MLS 304MA user manual