IMS MDrive23 User manual

intelligent motion systems, inc.
Excellence in MotionTM
370 N. MAIN ST., PO BOX 457, MARLBOROUGH, CT 06447
PH: (860) 295-6102, FAX: (860) 295-6107
TM
QUICK REFERENCEQUICK REFERENCE
Software Specifications
Program and Data Storage.............................................Nonvolatile
User Registers............................................................... (4) 32 Bit
Math Functions .........................................+, -, ×, ÷, <, >, =, <=, >=,
& (AND), l (OR), ^ (XOR), ! (NOT)
Branch Functions .................................... Branch & Call (conditional)
Predefined I/O Functions
Inputs............Home, Limit Plus, Limit Minus, Go, Soft Stop,
Pause, Jog Plus, Jog Minus, Analog In
Outputs....................... Moving, Fault, Stall, Velocity Change
Trip Functions ................................... Trip on Input & Trip on Position
Party Mode Addresses............................................................. 62
Encoder Functions .......................................Stall Detection, Position
Maintenance, Find Index
Recommended IMS Power Supplies
IP404 Unregulated Linear Supply
Input Range
120 VAC Versions...................................... 102-132 VAC
240 VAC Versions...................................... 204-264 VAC
Output
No Load Output Voltage*......................43 VDC @ 0 Amps
Continuous Output Rating* ...................32 VDC @ 2 Amps
Peak Output Rating*............................26 VDC @ 4 Amps
ISP200-4 Unregulated Switching Supply
Input Range
120 VAC Versions...................................... 102-132 VAC
240 VAC Versions...................................... 204-264 VAC
Output
No Load Output Voltage*......................41 VDC @ 0 Amps
Continuous Output Rating* ................38 VDC @ 1.5 Amps
Peak Output Rating*............................35 VDC @ 3 Amps
* All measurements were taken at 25°C, 120 VAC, 60 Hz.
A characteristic of all motors is back EMF. Back EMF is a source of cur-
rent that can push the output of a power supply beyond the maximum
operating voltage of the driver. As a result, damage to the stepper
driver could occur over a period of time. Care should be taken so that
the back EMF does not exceed the maximum input voltage rating of the
MDrive23.
FULL PRODUCT NAME
TM
MDrive23 Motion Control Quick Reference Guide
The primary function of this guide is to acquaint the user with the speci-
fications, basic wiring and configuration of the MDrive23 Motion Control.
The product manual in PDF format is on the IMS Product CD or may be
downloaded from the IMS web site at www.imshome.com.
The product manual also contains a “Getting Started” document to guide
you in rapidly setting up and turning your MDrive23.
Notes and Warnings
Please observe the following when handling, connecting and using your
MDrive23. Failure to observe these points may result in damage to the
product. NOTE: The electronics are not removable from the motor in the
field. The entire unit must be sent back to the factory for repair. All war-
ranty and disclaimer information is located in the full product manual and
should be referenced for more information.
Layout and Interface Guide
Logic level cables must not run parallel to power cables. This will introduce
noise and make the system unreliable.
Logic level cables must be shielded to reduce the risk of EMI induced
noise. The shield must be grounded at the signal source to AC ground.
The opposite end of the shield must not be connected which allows it to
float and act as a drain.
The supply to the driver must be a twisted pair. If more than one driver is
being connected, run separate leads to each driver.
General Specifications
Electrical
Input Voltage (+V) Range* ..................................... +12 to +48 VDC
Analog Input
Resolution.....................................................................10 Bit
Voltage Range ...................................0 to +5 VDC or 4 - 20 mA
General Purpose I/O
Number/Type..................................................... 4/Open Collector
Logic Range .......................................................... +5 to +24 VDC
Output Sink Current ..........................................................700 mA
Protection ......................... Over Temp, Short Circuit, Inductive Clamp
Communication Type ..........................................................RS-485
Baud Rate..............................................................4800 to 115K
Motion Specifications
Resolution – Open Loop Configuration
# of Settings................................................................... 14
Steps Per Rev........................ 400, 800, 1000, 1600, 2000,
3200, 5000, 6400, 10000, 12800,
25000, 25600, 50000, 51200
Resolution – Closed Loop Configuration (Optional)
Steps Per Rev........................................................... 51200
Encoder (Optional)
Type ......................................................... Internal, Magnetic
Resolution ............................. 512 Lines/2048 Edges Per Rev
Counters
Type .............................................. Position, Encoder/32 Bits
Edge Rate (Max)......................................................... 5 MHz
Velocity
Range................................. +/- 5,000,000 Steps Per Second
Resolution ......................................0.5961 Steps Per Second
Accel/Decel
Range........................................ 1.5 x 109Steps Per Second2
Resolution .........................................90.9 Steps Per Second2
MOTION CONTROL
For More Information:
See the complete MDrive Motion Control Product Manual
on the IMS Product CD or at www.imshome.com
Recommended Power Supply Connections
MDrive with 7 Pin Pluggable Connector
SCLK
DIR
GND
+V
EN
NC
OPTO
SPLY
Shielded Twisted Pair
Shield to
Earth Ground
GND
+V
MDrive23 Motion Control
with Pluggable Connector (P1)
Pin1
P1
Unregulated
Linear or
Switching
Power Supply
Power
Ground
+VDC
Thermal Specifications
The MDrive consists of two core components, a drive and a motor.
Close attention must be paid to the thermal environment where the
device is used. The maximum temperatures are:
Maximum Heat Sink Temperature .......................................... 85° C
Maximum Motor Temperature............................................. 100° C
© Intelligent Motion Systems, Inc.
Rev. 072705
Unregulated
Linear or
Switching
Power Supply
Power
Ground
+VDC
White/Yellow I/O1
White/Orange I/O2
White/Violet I/O3
White/Blue I/O4
Green Analog Input
AWG 22
WtYel WtOrg WtVio WtBlu Grn Blk Red
I/O1 I/O2 I/O3 I/O4 ANLG GND +V
Power Leads
AWG 20
Shield to
Earth Ground
Ferrite
Beads
πType RFI Filter
≥Required Current
+
–
Shielded Twisted Pair
MDrive Motion Control with
12" (30cm) Flying Leads (P1)
P1
MDrive with Flying Leads
Patent Pending
*Graph at right illustrates
power supply current require-
ments (MAX) per MDrive23.
Actual power supply current
will depend on voltage and
load.
WARNING! When using the MDrive Motion Control with optional
internal magnetic encoder, no axial force may be applied to the
motor shaft without use of a load bearing isolation coupling.

12.00
+1.0/-0.0
(304.8)
(+25.4/-0.0)
Pin 1: N/C
Pin 3: N/C
Pin 5: N/C
Pin 7: RX-
Pin 9: TX+
Pin 2: N/C
Pin 4: N/C
Pin 6: RX+
Pin 8: TX-
Pin 10: CGND
RX
TX
GND
RS-232 to RS-485
Converter
TX+
TX-
RX-
RX+
CGND
TX+
TX-
RX-
RX+
CGND
Host MDrive
Host
Converter
Power
TX
RX
GND
+VDC
RX+
RX-
TX+
CGND
TX-
MDrive
P2
RS-485 Interface
Mechanical Specifications
MDrive23: Linear Actuator
Flying Leads Pluggable Clamp Type
Terminal Strip
Rotary MDrive23:
Single Shaft, Encoder & Control Knob
Dimensions in Inches (mm)
P1 Interface Options
Power Leads
Logic Leads
Adhesive Anchors
& Tywraps
Securing MDrive23 Power Leads
Some applications may require that the MDrive23 move with the
axis motion. If this is a requirement of your application, the motor
leads must be properly anchored. This will prevent flexing and tug-
ging which can cause damage at critical connection points in the
MDrive23 electronics.
DO NOT bunch the Power Leads and the Logic Leads together.
Recommended Connector Wiring
Power Supply and Ground................................................. 20 AWG
Logic Wiring ................................................................... 22 AWG
SPI Communications Wiring .............................................. 24 AWG
General Practices.................................. Wire strip length of 0.250”
(6.0mm) is recommended
1.63
(41.4)
2.22 SQ.
(56.4 SQ.)
1.50
(38.1)
2.92
(74.2)
1.856 ±0.008 SQ.
(47.14 ±0.2 SQ.)
4X Ø 0.197
(Ø 5.0)
0.81 ±0.02
(20.6 ±0.5)
0.59 ±0.008
(15.0 ±0.2)
0.06
(1.6)
LMAX
LMAX2
0.23 ±0.004
(5.8 ±0.1)
Ø 0.250 +0/-0.0005
(Ø 6.35 +0/-0.013)
Interface
Option
P2
P1
Ø 1.500 ±0.002
(Ø 38.10 ±0.05)
0.19
(4.8)
1.63
(41.4)
2.22 SQ.
(56.4 SQ.)
1.50
(38.1)
2.92
(74.2)
1.856 ±0.008 SQ.
(47.14 ±0.2 SQ.)
4X Ø 0.205
(Ø 5.21)
0.06
(1.6)
6.00
(152.4)
1/4-20 UNC-2A
THREAD TO
WITHIN 0.05 (1.3)
OF SHOULDER
0.375
(9.52)
2.64
(
67.1
)
Interface
Option
P1
0.50
(12.7)
Ø 1.500 ±0.002
(Ø 38.10 ±0.05)
P2
Length in
Inches (mm) LMAX LMAX2
SINGLE SHAFT or
ENCODER VERSION
CONTROL KNOB
VERSION
Size 2218 2.63 (66.8) 3.35 (85.1)
2222 3.00 (76.2) 3.70 (94.0)
2231 3.86 (98.0) 4.57 (116.1)
WARNING!
The maximum +48 VDC Input Voltage of the MDrive23
includes motor back EMF, power supply ripple and high line.
WARNING! DO NOT connect or disconnect power leads or motor leads
when power is applied! Disconnect the AC power side to power down the
DC power supply.
For battery operated systems, conditioning measures should be taken to
prevent device damage caused by in-rush current draws, transient arcs
and high voltage spikes.
NOTE: Wire and insulation type are subject to the user’s
application and environment.
0.44
(11.2)
Connector Assignments
CONNECTOR P1
PIN FLYING LEADS FUNCTION
COLOR WIRE SIZE
1 White/Yellow AWG 22 I/O 1
2 White/Orange AWG 22 I/O 2
3 White/Violet AWG 22 I/O 3
4 White/Blue AWG 22 I/O 4
5 Green AWG 22 ANALOG INPUT
6 Black AWG 20 POWER GROUND
7 Red AWG 20 +V (+12 to +48 VDC)
CONNECTOR P2 (RS-485)
PIN FUNCTION
1-5 NO CONNECT
6 RX +
7 RX –
8 TX –
9 TX +
10 GROUND
Communications Converter Cable
This convenient 6' (1.8m) long
accessory cable connects a PC’s
standard DB-9 Serial Comm Port to
the MDrive's P2 Connector. An in-
line RS-232 to RS-485 converter en-
ables parameter setting to a single
MDrive Motion Control. Purchase of
this cable is recommended with first
orders. Part No. MD-CC200-000.
WARNING! DO NOT connect or disconnect the Communica-
tions Converter Cable MD-CC200-000 while power is applied.
Other IMS Control Unit manuals
Popular Control Unit manuals by other brands
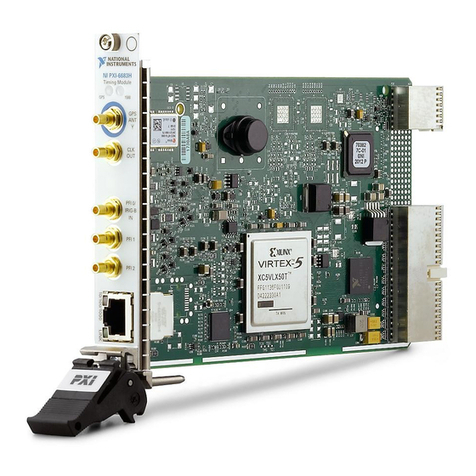
National Instruments
National Instruments PXI-6683 Series user manual

Burkert
Burkert 2000 INOX operating instructions
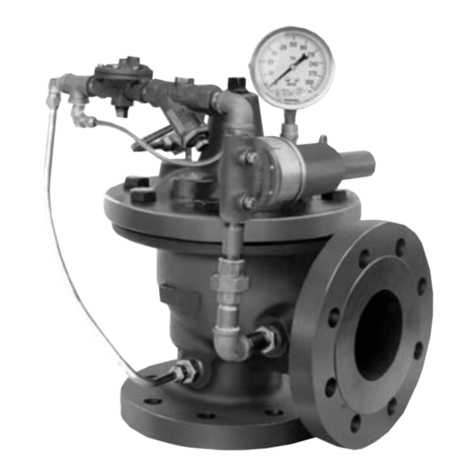
CLA-VAL
CLA-VAL 50B-4KG1 Installation, operation and maintenance
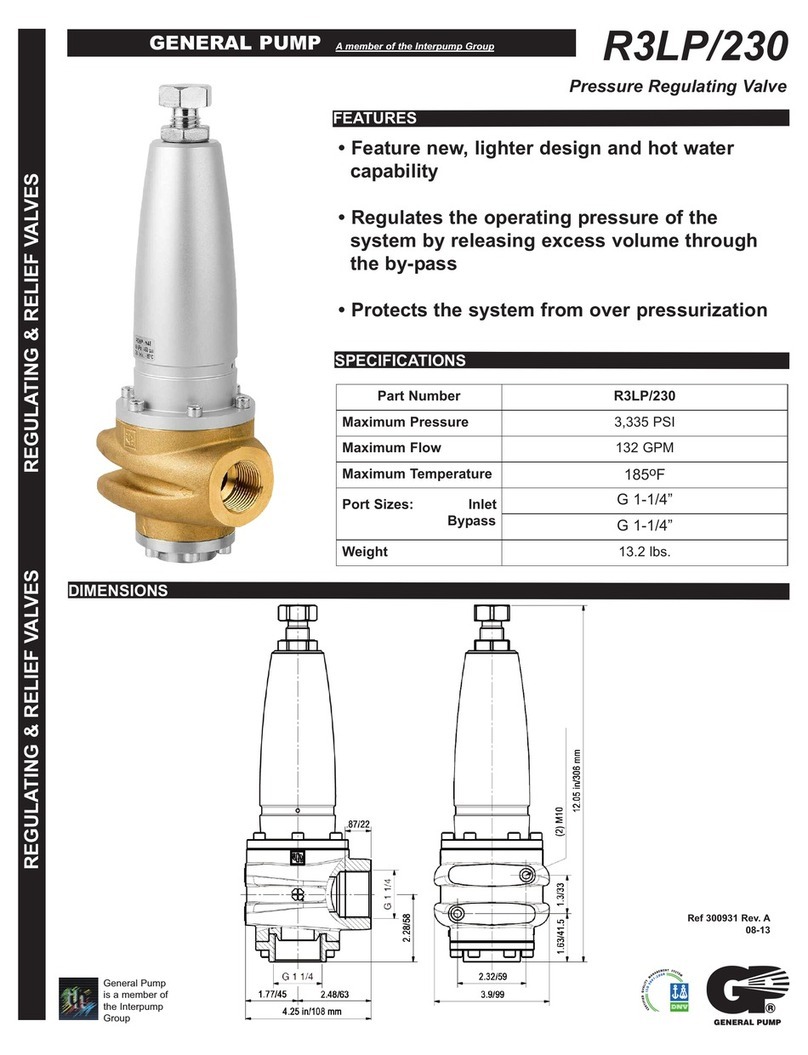
Interpump Group
Interpump Group GENERAL PUMP R3LP/230 quick start guide

Viessmann
Viessmann VITOSOLIC 100 operating instructions

Avaya
Avaya M4648ML-T installation guide