Incon 1250-LTC Assembly instructions

1
INSTALLATION AND
PROGRAMMING MANUAL
FOR MODEL
1250-LTC
PROGRAMMABLE POSITION MONITOR
Solid State Indicator for SynchroTransmitter
000-2072 Rev. C

2
INTELLIGENT CONTROLS, INC.
PO Box 638
Saco, Maine 04072 USA
Phone: 207-283-0156 FAX: 207-283-0158
Toll Free: Technical Service & Sales 800-872-3455
This manual applies to all INCON model 1250-LTC monitors.
Copyright 2008, Intelligent Controls, Inc. All rights reserved

3
TABLE OF CONTENTS
Section: Page:
List of Figures…………………………………………………………………… 4
List of Tables……………..……………………………………………………… 4
Introduction……………………………………………………………………... 5
1.0 Installation……………………………………………………………..…… 5 - 8
2.0 Programming…………………………………………………………..…… 9 – 33
2.1 Front Panel Programming…………………………………………….. 9
2.2 Serial Port Programming – ASCII …………………………………… 13 - 17
2.3 Serial Port Programming – MODBUS……………………………….. 18 – 33
2.3.1 MODBUS Packet Format – Read……………………………….. 19
2.3.2 MODBUS Packet Format – Write………………………………. 20
2.3.3 MODBUS Packet Format – Error Exception Response……….. 21
2.4 Operating Modes………………………………………………………. 34 – 37
2.5 Programming Notes……………………………………………………. 38
3.0 Options…………………………………………………………………..….. 39 – 48
3.1 Analog Output……………………………………………………..…… 39
3.2 High / Low Relay Limits………………………………………..……… 40 – 45
3.2.1 Tap Change Acknowledgement.………………………………… 41
3.2.2 High Tap / Low Tap……………………………………………… 41
3.2.3 Total Tap Change Count………………………………………… 42
3.2.4 On-Tap Alarm……………………………………………………. 42
3.2.5 Up-To & Down-To Count………………………………….…….. 44
3.2.6 Pass-Through-Neutral Alarm…………………………….……… 44
3.2.7 One-Direction Change Count…………………………….……… 45
3.2.8 FA 25 & FA 27 Error Alarm…………………….…………….… 45
3.3 Serial RS-232…………………………………………………...……….. 46
3.4 Serial RS-485 .……………………………………...………………….... 47
3.5 Input Isolation…………………………………………………...……… 48
4.0 Field Calibration and Test………………………………………...…….…. 48 – 49
5.0 Error Codes…………………………………………………………….……. 50
6.0 Specifications…………………………………………………………….….. 51

4
LIST OF FIGURES
Figure: Page:
1.1 Mechanical Dimensions…………………………………………………………… 6
1.2 Field Wiring Diagram…………………………………………………………….. 6
1.3 Field Wiring Diagram with 4-20mA Option.…………………………………….. 7
2.1 Simplified Programming Flowchart…...…………………………………………. 12
2.2 Serial Data Dump Example……………………………………………………….. 17
2.3 Base 1 Uni-Polar Mode Analog Output………………………………………….. 35
2.4 Base 0 Uni-Polar Mode Analog Output………………………………………….. 36
2.5 Bi-Polar Mode Analog Output…………………………………………………… 37
3.1 Relay Field Wiring Diagram……………………………………………………... 40
3.2 On-Tap Example………………………………………………………………….. 43
4.1 Analog Output Adjustment Pots…………………………………………………. 49
LIST OF TABLES
Table: Page:
1.1 Terminal Functions……………………………………………………………… 7
1.2 DIP Switch Functions…………………………………………………………... 7
1.3 Analog Output Configuration Jumpers…………………………………………. 8
2.1 Numeric and Alpha-numeric Menu Items……………………………………… 9-12
2.2 Serial Programming ASCII Commands……………………………………….. 13-15
2.3 Read Registers Command Format..……………………………………………. 19
2.4 Read Registers Response Format.…………………………..………………….. 19
2.5 Write Registers Command Format……………………………………………... 20
2.6 Write Registers Response Format……………………………………………… 20
2.7 Error Exception Response Format……………………………………….…….. 21
2.8 RS-485 MODBUS Register Definitions...……………………………………… 22-33
3.1 Analog Output Load Limits……………………………………………………. 39
3.8 Wiring: Digital Connector Pin-Out……………………………………….…….. 47
5.1 Error Codes …………………………………………………………….….……. 50

5
INTRODUCTION
The Model 1250-LTC Programmable Position Monitor is a highly advanced solid-
state instrument, which measures the absolute position of a synchro transmitter. It provides
both a user definable visual panel indication and optional analog and digital signal outputs
suitable for a variety of monitoring and control applications.
The INCON 1250-LTC series is unique in its capability to monitor up to 40 user-
definable position segments. It is specifically designed for monitoring power transformer
load tap changer position, where the desired readout is in whole tap numbers. Its transmitter
can be attached to any operating shaft on the LTC and the 1250 programmed to read out in tap
positions. The display and all outputs follow a “stair step” function defined in the program.
The INCON 1250 has become the industry standard for LTC position monitoring.
In addition to basic LTC tap position, the 1250-LTC can provide useful information
about the movement of the LTC. Beginning with a momentary (optional) relay closure after
each successful tap change, the 1250-LTC keeps records on seven important issues relating to
LTC movement, including: total number of tap changes; number of days since last “pass
through neutral”; number of changes “up to” and “down to” each tap; and more.
Most LTC’s rotate about 9 to 11 degrees with each tap change. The 1250-LTC can
measure in increments of 1/10th of a degree. A special feature of the 1250-LTC is its ability
to monitor small discrepancies in tap position. A programmable limit can be set to give an
alarm when the discrepancy in tap position reaches the limit. Inaccurate tap position can be
an early indicator of wear in the LTC mechanism or possible impending failure.
The 1250-LTC may be wired in parallel with existing synchro transmitter/receiver
pairs or wired directly to the synchro transmitter. Additional 1250’s may be wired to the
same transmitter without compromising the accuracy or reliability of the system.
1.0 INSTALLATION
•The Model 1250-LTC is designed for use in any 50/60 Hz, five-wire synchro system
compatible with electrical specifications given in Section 6.0, page 51. These devices
include CX, TX, CDX, and TDX function synchros, as well as Self-Synchronous
Indicator devices. (INCON’s model 1292 Synchro is a highly specified robust
transmitter with a history of proven performance.)
•The panel-mount case is designed to snap-fit into a standard 1/8 DIN rectangular
cut-out of 44mm (1.73 in.) by 92mm (3.62 in.)
•Wiring is done to the rear of the case. #16 AWG (min.) type THHN, THWN, TFFN,
or equivalent wire is recommended for the five AC synchro lines. #20 AWG (min.)
shielded twisted pair wire is recommended for analog output wiring. Use appropriate
spade lugs (provided) when connecting to the case terminals.
•Contact INCON Technical Service (1-800-872-3455) for application assistance if the
synchro transmitter and the 1250-LTC monitor are separated by a wire run of more
than 1200 feet.

6
Figure 1.1 Mechanical Dimensions
Figure 1.2 Field Wiring Diagram

7
Figure 1.3 Field Wiring Diagram with 4-20mA Output
Table 1.1 Terminal Functions
Terminal Function Terminal Function
A S1 1 Analog Output +
B S2 2 Analog Output –
C S3 3 Program Mode Inhibit
D (Spare) 4 Inhibit Return
E R1 * 5 Line L1 *
F R2 * 6 Line L2 *
7 Chassis Ground
* Terminals E & F are 8 Relay Low Contact N.O.
jumpered to 5 & 6 9 Relay Common
respectively 10 Relay High Contact N.O.
A DIP switch tells the firmware which hardware options are installed, so their function
can be enabled. It is located on the top PCB, above the power transformer and is
accessible through a slot in the left side of the case, towards the rear of the instrument.
Table 1.2 DIP Switch Functions
Switch # Function
1 Serial Communications Option Enable
2 MODBUS Protocol Enable
3 Spare
4 High / Low Relay Limit Option Enable
5 Analog Output Option Enable
6 Spare
7 Spare
8 In-Factory Test & Calibration Menu Enable

8
Installation Notes:
1) A resistor may be wired remotely across the analog output terminals to convert analog
output milliamp current to a voltage. Use Ohm’s Law to calculate the proper resistance
for the desired voltage based upon the 1250-LTC’s rated output current.
2) Maximum analog output load resistance: 0-1mA = 10K ohms; +/-1mA = 10K ohms;
0-2mA = 5K ohms; 4-20mA = 500 ohms.
3) Models with 4-20 mA analog output options must have an EXTERNAL LOOP POWER
SOURCE of 10.0 VDC minimum, 24.0 VDC maximum, in series with the current loop.
The INCON Model 1945 Power Supply is recommended for these installations,
(See Figure 1.3, page 7).
4) When additional remote indication is needed, several 1250-LTC’s may be wired in
parallel to the same transmitter. The 1250-LTC can also be connected via its serial port to
the INCON model RD-4 Remote Display unit.
5) The 1250-LTC and the synchro transmitter MUST BE WIRED TO THE SAME AC
SOURCE. Do not remove the jumpers from terminals E and F.
6) A wire jumper or keyswitch may be installed between terminals 3 & 4 to prevent the
program from being changed. When these terminals are jumpered the menu will read
“EP-x” instead of “OP-x”, which indicates that you can Examine each Parameter, but not
change them.
7) After installation and programming, install the rear terminal guard with screws provided.
8) For models with serial options, plug the cable onto the card edge with the red stripe
towards the outside of the case.
Application Bulletins:
1) If there is a large component of AC “ripple” present on the 1250 analog output, check the
isolation of all wiring with respect to earth ground. R1, R2, S1, S2, and S3 should
measure infinite resistance to earth ground. In applications where external isolation is not
sufficient, the Input Isolation Option (-I) is required to break the ground path that causes
this ripple. See Application Bulletin #000-1150 for more detailed information.
2) Analog outputs of 0-1mA, +/-1mA, and 0-2mA can be changed in the field to any one of
the other two (see Table 1.3). The configuration jumpers are located on the bottom PCB.
See Application Bulletin #000-1151 for more detailed information.
Table 1.3 Analog Output Configuration Jumpers
Output Signal: J8 J10 J12 J13
0-1mA Jumped Jumped Jumped
+/-1mA Jumped Jumped Jumped
0-2mA Jumped Jumped

9
2.0 PROGRAMMING
The Model 1250-LTC has three methods of programming: numeric menu (traditional
1250); alphanumeric menu; and serial port programming commands. The 1250-LTC can be
ordered with either RS-232 or RS-485 serial port hardware. The serial programming
commands can be in the form of ASCII characters or MODBUS packets, depending upon the
position of DIP switch #2. See Tables 2.1, 2.2 & 2.3 for a full listing of all programming
menu items, commands, and syntax. See the simplified programming flowchart for tap
position on page 12, Figure 2.1.
2.1 Front Panel Programming
To access the numeric or alphanumeric programming menu, press the MENU key for
several seconds until the display goes blank, then press the SELECT/ENTER key. The
display should read “OP 0”. The default menu is the numeric menu. To choose the
alphanumeric menu, press the DOWN key to select OP 99. Press the SELECT/ENTER key,
the display should read “to OP”. Press the UP key. The display should read “run”. You are
now in the alphanumeric menu mode.
To change a parameter using the numeric or alphanumeric menus, select the parameter
to be changed from the menu, press the SELECT/ENTER key. The parameter’s present
setting will now be displayed. You can change the setting by pressing the UP or DOWN key.
To store the new setting, press the SELECT/ENTER key, the display will return to the menu.
Table 2.1 Numeric and Alphanumeric Menu Items:
Num-
eric
Alpha-numeric
Protocol
Function: Default
Value:
Programmable
Range:
OP 0 run Press the SELECT/ENTER key to exit the
Program mode
OP 2 Func Select Operating Mode (see pages 34-37) 21 16, 17, 18, 19, 20,
21
OP 3 tCrLY Selects which relay will assert
momentarily, after each tap change
OFF OFF, LO, HI
OP 4 tCrdL Sets the delay time before Tap Change
Acknowledge Relay turns on (Seconds)
0.0 0.0 to 9.9
OP 5 tCrLt Sets duration of time the Tap Change
Acknowledge Relay stays on (Seconds)
0.0 0.0 to 9.9
OP 6 dHF-L Selects which visit to the Draghand
positions (first time or last time) will begin
the day counters
LASt “FirSt”, “LASt”
OP 10 LtCLr Low Tap Alarm Clear CL
OP 11 HtCLr High Tap Alarm Clear CL
OP 15 rL Lt Sets low relay limit tap -16 Any valid tap
number
OP 16 LtrLY Selects which relay will assert when the
“Low Tap” alarm limit is reached
OFF OFF, LO, HI
OP 17 rL Ht Sets high relay limit tap +16 Any valid tap
number
OP 18 HtrLY Selects which relay will assert when the
“High Tap” alarm limit is reached
OFF OFF, LO, HI

10
Num-
eric
Alpha-numeric
Protocol
Function: Default
Value:
Programmable
Range:
OP 19 dEGrE Displays absolute synchro position in
degrees with one decimal place resolution
OP 20 tAPS Number of taps 33 2 to 40
OP 21 d SEG Degrees per tap 10.000 -99999 to +99999
OP 22 nEu Number of neutral taps 1 0 to 8
OP 23 n St Sets lowest neutral tap 0-1 Any valid tap
number
OP 27 S Pt Sets present tap position 0 Any valid tap
number
OP 28 L Pt Loads present tap position into memory Ld
OP 29 dSPrL Enables display of “r” or “L” in Function
Modes 20 and 21
OFF On or OFF
OP 30 CAL E Enables analog output Calibration Mode OFF On or OFF
OP 31 L CAL Forces the analog output to its lowest
signal output
LO
OP 32 H CAL Forces the analog output to its high scale
signal output
HI
OP 33 d CAL Forces the analog output to its mid scale
signal outputs
- -
OP 34 t CAL Forces the analog output to alternate
between high and low scale signal outputs
LO then HI
OP 39 dOG t Forces a Watchdog Reset (Factory use
only)
<<Press ENTER>>
OP 40 LED t Display LED Test: Turns on all LED’s -8.8.8.8.8.
OP 41 rS t RS-232 Echo Test: Re-transmits characters
received through the RS-232 serial port
rS
OP 42 InCAL Calibrates synchro input circuitry CAL
OP 43 rLY t Relay Test: UP and DOWN keys toggle
between LO and HI relays
LO then HI
OP 50 dSPbL Causes the display to go blank after 60 sec. OFF On or OFF
OP 51 SEr Serial Communication Mode:
0=Serial Disabled,
1=Data Logger Mode, 2=Polled Mode,
3=Sampled Mode, 4=Serial Command
Mode, 5=Reserved, 6= MODBUS Mode,
7=Remote Display Driver Mode
0 0 to 4, and 6
OP 53 Aut25 Auto-Reset after “FA 25” Loss of Synchro
Signal Error (page 50)
OFF On or OFF
OP 54 25rLY Selects which relay will assert when the
“FA 25” error is active
OFF OFF, LO, HI
OP 55 ttCLt Sets Total Tap Change counter alarm limit
in THOUSANDS
000.01 000.01 to 999.99
OP 56 ttrLY Selects which relay will assert when the
Total Tap Change counter limit is reached
OFF OFF, LO, HI
OP 57 ttPrE Presets the Total Tap Change counter in
THOUSANDS
000.00 000.00 to 999.99
OP 58 ttdtE Total Tap Change counter reference date
Enter day, month, year
01–01–00
OP 59 ttCdS Displays Total Tap Change Count and
reference date Press ENTER to exit

11
Num-
eric
Alpha-numeric
Protocol
Function: Default
Value:
Programmable
Range:
OP 60 Aut27 Auto-Reset after “FA 27” Unstable
Synchro Signal Error (page 50)
OFF On or OFF
OP 61 27rLY Selects which relay will assert when the
“FA 27” error is active
OFF OFF, LO, HI
OP 62 OtGLt Sets On-Tap guard band limit (Degrees) 0.1 0.1 to 9999.9
OP 63 OtrLY Selects which relay will assert when the
On-Tap guard band limit is reached
OFF OFF, LO, HI
OP 64 OtdtE On-Tap reference date
Enter day, month, year
01–01–00
OP 65 OtdIS Scrolls through the list of taps, to select,
Press ENTER to display the highest
measured deviation, for that tap
Press MENU to escape back to the menu
Any valid tap
number
OP 66 Otdtd Scrolls through the list of taps which have
exceeded the On-Tap alarm limit to select,
Press ENTER to display the highest
measured deviation, for that tap
Press MENU to escape back to the menu
Any valid tap
number
OP 67 OtCLr Clears the On-Tap alarm CL
OP 68 OtrSt Resets all On-Tap logs & alarm rESEt
OP 70 udCLt Sets the alarm limit for the number of
changes UP TO any tap in THOUSANDS
000.01 000.01 to 999.99
OP 71 udrLY Selects which relay will assert when the
“UP TO” change alarm limit is reached
OFF OFF, LO, HI
OP 72 uddtE UP TO & DOWN TO Change counter
reference date Enter day, month, year
01–01–00
OP 73 uddIS Scrolls through the list of taps to select,
Press ENTER to display the Change Up-
To count Press ENTER to display the
Change Down-To count, for that tap
Press MENU to escape back to the menu
0 Any valid tap
number
OP 74 udCLr Clears an active Up-To and Down-To
Change alarm
CL
OP 75 udrSt Resets all Change Up-To and Down-To
counters and alarm
rESEt
OP 80 POrt Sets serial port parameters: (press the UP
or Down key to select a value, press the
enter key to move to the next parameter)
Baud rate
Word length
Parity (n=none, E=even, O=odd)
Stop bits
Address (for RS-485 Multi-drop)
9600
8
n
1
128
2400, 4800, 9600,
14400, 19200,
28800,38400,
57600, 76800
7 or 8
n, E, O
1 or 2
0 to 255
OP 85 PtnLt Sets the limit for number of days without a
“Pass Thru Neutral”
OFF Off, 0.1 to 365.0
OP 86 PtrLY Selects which relay will assert when the
“Pass Thru Neutral” time limit is reached
OFF OFF, LO, HI
OP 87 PtdIS Displays the number of days since the last
“Pass-Through-Neutral”

12
Num-
eric
Alpha-numeric
Protocol
Function: Default
Value:
Programmable
Range:
OP 88 PtrSt Resets the “Pass-Through-Neutral”
counter & alarm
rESEt
OP 90 1dCLt Sets the limit for number of consecutive
tap changes in One Direction
2 2 to 30
OP 91 1drLY Selects which relay will assert when the
“One Direction Change” limit is reached
OFF OFF, LO, HI
OP 92 1ddIS Displays the number of days since the
“One Direction Alarm” was asserted
OP 93 1dCLr Clears “One Direction Change” alarm CL
OP 99 tO OP Toggles between Numeric and
Alphanumeric menus
tO OP
Figure 2.1 Simplified Programming Flowchart

13
2.2 Serial Port Programming - ASCII:
These commands require either the RS-232 (-S) or RS-485 (-M) hardware option. To use
the serial port programming commands, connect a computer terminal to the serial port cable. The
terminal must have the proper Comm port settings to communicate to the 1250-LTC (see Sections
3.3 and 3.4, pages 46 - 47). See Table 2.2 for a full listing of all Serial Programming Commands
and syntax. At the command prompt, type a command followed by the new parameter setting,
using proper syntax as shown in Table 2.2. Typing the command only, without a new para-
meter setting, will cause the 1250-LTC to transmit the present setting for that parameter.
Table 2.2 Serial Programming ASCII Commands:
◊=space ª=enter
Command Syntax: Function: Explanation:
SETUPªEnter the Setup Mode This command must be entered before
any other commands can be made.
EXITªRe-starts the serial connection Changes to comm. port settings will take
effect
RUNªReturn to the Run Mode Changes to settings will take effect
DISPªDisplays all setup parameters Each setup parameter command is dis-
played with the current value following it
DUMPªDisplays all measured LTC
information
(See Figure 2.2, page 17)
Lists: Total tap change count, Days since
Pass-Through-Neutral, High & Low
Draghand positions, Change Up-To and
Down-To counts for each tap, Maximum
On-Tap deviations for each tap, etc…
POSªDisplays present Tap #, synchro
position (in degrees) and current
On-Tap deviation degrees
Reads Tap #, 0.0 to 359.9 degrees, with
one decimal place of resolution
Press ª(enter) to exit
MODE◊nnªSegmented modes See Section 2.4, page 34-37 for details
ACKRLY◊LOªSelects which relay will assert
momentarily after each tap
change
Choose “OFF”, “LO” or “HI” relay to
assert momentarily after each tap change
ACKDLY◊nn.nªSets the delay time, in seconds,
before the ACK relay asserts
n= a number from 0.1 to 9.9 with one
decimal place resolution
ACKHOLD◊nn.nªSets the duration, in seconds,
that the ACK relay remains on
n= a number from 0.1 to 9.9 with one
decimal place resolution
DHCOUNT◊FIRSTªSelects which visit to the
Draghand position to begins the
day counter
Choose “FIRST” or “LAST” visit.
The number of days since the LTC
visited that extreme position the first or
last time
DHLRST Low Draghand Reset Draghand value becomes present tap
DHHRST High Draghand Reset Draghand value becomes present tap
LTLMT◊nnªSet Low Tap alarm limit n= an integer, any valid tap number
LTRLY◊LOªSelects which relay is associated
with the Low Tap alarm
Choose “OFF”, “LO” or “HI” relay to
assert when the alarm limit is reached
LTCLRªClears Low Tap Alarm Also resets “Days Since Alarm” counter
HTLMT◊nnªSet High Tap alarm limit n= an integer, any valid tap number
HTRLY◊LOªSelects which relay is associated
with the High Tap alarm
Choose “OFF”, “LO” or “HI” relay to
assert when the alarm limit is reached
HTCLRªClears High Tap Alarm Also resets “Days Since Alarm” counter
TAPS◊nnªSet number of taps n= an integer from 2 to 40

14
Command Syntax: Function: Explanation:
DEGSEG◊n.nnnnªSet degrees per segment n= a floating point number, 5 digits max,
average number of degrees between taps
NEUTRALS◊nªSet number of neutral taps n= an integer from 0 to 8
NSTART◊nnªSet lowest neutral tap number n= an integer, any valid tap number
SETTAP◊nnªSet present tap position n= an integer, any valid tap number
LDTAPªLoad present tap pos. into memory Must be done for SETTAP to take effect
DISPRL◊ONªEnables the display of “r” (raised)
and “L” (lowered) tap numbers
“ON” or “OFF” When enabled causes
the display to show “r” and “L” in
function modes 20 and 21 only
ANACALªEnter analog calibration mode, the
1250 analog output will be forced
to Low / Mid / High signal output
Press the space bar to toggle between
Low / Mid / High analog output. Press the
enter key to stop calibration
WDOGTESTªForces a Watchdog Reset This command is for factory use only.
LEDTESTªTurns on all display segments Press the enter key to stop the LED test
INCALªSelf-calibrates the input circuitry Outputs “Pass” or “Fail” calibration
result
RLYTESTªForces Hi / Lo relay output to
close
Press the Space Bar to toggle between
Lo or Hi relay Press ª(enter) to exit
DSPBL◊ONªEnables the display blanking
feature
“ON” or “OFF” When enabled causes
the display to go blank after 60 sec.
SERIAL◊nªSet serial communication mode 0=Serial Disabled, 1=Data Logger
Mode, 2=Polled Mode,
3=Sampled Mode,
4=Serial Command Mode, 5= Reserved,
6=MODBUS Mode, 7=Remote Display
Driver
AUTO25◊ONªEnables automatic reset of the
“FA 25” Loss of Synchro Signal
Error (page 50)
“ON” or “OFF” When “ON”, the
“FA 25” alarm will automatically reset
when the condition clears
FA25RLY◊LOªSelects which relay is associated
with the “FA 25” Error
Choose “OFF”, “LO” or “HI” relay to
assert when the FA 25 Error is active
RESET25ªManually clears the “FA 25”
alarm
When AUTO25 is “OFF”, manually
clears the alarm and opens the relay
TTCLMT◊nnn.nnªSets the Total Tap Change count
alarm limit in THOUSANDS
n= a number from 0.00 to 999.99 with
two decimal place resolution
TTCRLY◊LOªSelects which relay is associated
with the Total Tap Change count
alarm
Choose “OFF”, “LO” or “HI” relay to
assert when the alarm limit is reached
TTCPRE◊nnn.nnªPresets the Total Tap Change
counter in THOUSANDS
and clears the alarm
n= a number from 0.00 to 999.99 with
two decimal place resolution
TTCDATE◊mm-dd-yyyyªSets the Total Tap Change
counter reference date
mm-dd-yyyy = Month <hyphen> Day
<hyphen>Year (4 digits)
AUTO27◊ONªEnables automatic reset of the
“FA 27” Unstable Synchro
Signal Error (page 50)
“ON” or “OFF” When “ON”, the
“FA 27” alarm will automatically reset
when the condition clears
FA27RLY◊LOªSelects which relay is associated
with the “FA 27” Error
Choose “OFF”, “LO” or “HI” relay to
assert when the FA 27 Error is active
RESET27ªManually clears the “FA 27”
alarm
When AUTO27 is “OFF”, manually
clears the alarm and opens the relay

15
Command Syntax: Function: Explanation:
OTGDLMT◊nn.nªSets the On-Tap guard band
limit in DEGREES
n= a number of degrees from 0.0 to 99.9
with one tenth degree resolution
OTRLY◊LOªSelects which relay is associated
with the On-Tap alarm
Choose “OFF”, “LO” or “HI” relay to
assert when the alarm limit is reached
OTDVTNªDisplays the tap with the greatest
On-Tap Deviation
Displays Tap Number and Deviation
OTDATE◊mm-dd-yyyyªSets the On-Tap reference date mm-dd-yyyy = Month <hyphen> Day
<hyphen>Year (4 digits)
OTCLRªClears the On-Tap alarm Data is retained, the alarm is cleared
OTRSTªResets all On-Tap logs & alarm All On-Tap data is erased, alarm cleared
UPDNLMT◊nnn.nnªSets the alarm limit for the
number of changes “Up-To”
and “Down-To” any tap
in THOUSANDS
n= a number from 0.00 to 999.99 with
two decimal place resolution
UPDNRLY◊LOªSelects which relay is associated
with the “Up-To / Down-To”
Change alarm
Choose “OFF”, “LO” or “HI” relay to
assert when the alarm limit is reached
UPDNDATE◊mm-dd-yyyyªSets the Up To / Down To
Change counter reference date
mm-dd-yyyy = Month <hyphen> Day
<hyphen>Year (4 digits)
UPDNCLRªClears an active Up-To or
Down-To Change alarm
If a tap with an Up-To or Down-To Change
counter exceeding the programmed limit is
re-visited, the alarm will re-activate
UPDNRSTªResets all Change Up-To and
Down-To counters and alarm
All Up-To and Down-To counters are reset
to zero and an active alarm is turned off
PORT◊bbbb◊w◊p
◊s◊aª
Set comm. port settings: baud
rate, word length, parity, stop
bits, and address
b=2400, 4800, 9600, 14400, 19200,
28800, 38400, 57600, 76800 baud
w=7 or 8 bit word
p=n, E, O
s=1 or 2 stop bits
a= 0 to 255
SITEID◊Abcd-Xyz & 123ªIdentifies installation site on the
“DUMP” header
40 ASCII Characters – Upper / lower case
letters, numbers, punctuation marks
PTNLMT◊nnnªSets the alarm limit for the
number of DAYS without a
“Pass Through Neutral”
n= a number from 0.0 to 365.0 with one
decimal place resolution
PTNRLY◊LOªSelects which relay is associated
with the “Pass-Through-Neutral”
alarm
Choose “OFF”, “LO” or “HI” relay to
assert when the alarm limit is reached
PTNRSTªResets the “Pass-Through-
Neutral” counter & alarm
1DTCLMT◊nnªSets the alarm limit for the
number of consecutive tap
changes in One Direction
n= an integer from 2 to 30, OFF
1DTCRLY◊LOªSelects which relay is associated
with the “One Direction” alarm
Choose “OFF”, “LO” or “HI” relay to
assert when the alarm limit is reached
1DTCCLRªClears a “One Direction” alarm
MENU◊1ªSet the keyboard button menu
type
“1” =Numeric “OP” menu or
“2” = Alpha-numeric menu

16
HELP◊(command) ªProvides on-line help on the
specific command entered or
lists all available commands
An explanation of a command and the
proper entry syntax is given. If no
command is entered, all commands will
be listed with syntax but no explanations
To prevent accidental or unwanted changes to the program parameters, a jumper wire
may be installed across terminals 3 & 4. With this jumper installed, the numeric menu will
read “EP nn” instead of “OP nn”. All parameters can be viewed but no changes can be made.

17
Site ID: Maplewood Sub LTC #2
INCON 1250-LTC Firmware Revision X.xx Copyright 2007
Present Tap: 5
Total Tap Changes: 5729
Low Draghand: -7 35.4 Days Since LAST Visit
High Draghand: 8 17.6 Days Since LAST Visit
ALARMS:
Since activated - Days: Limit: Ref Date:
On-Tap Deviation 0.65 3.0 08-30-2007
Instability -- --
Synchro Signal Lost -- --
1 Direction Change 0.86 04
Up Down Count -- 123456 08-30-2007
Total Tap Changes 0.66 1234567 08-30-2007
Low Tap -- -10
High Tap 0.86 12
Pass Through Neut 0.95 30.0
TAP STATISTICS:
Tap Max. Dev. Change Change
Num: Degrees: Up-To: Dn-To:
-16 + 0.0 0 0
-15 + 0.0 0 0
-14 + 0.0 0 0
-13 + 0.0 0 0
-12 - 0.4 0 1
-11 - 0.4 1 2
-10 - 0.3 2 3
-9 + 0.4 3 9
-8 + 0.5 9 85
-7 + 0.8 85 215
-6 + 0.9 215 608
-5 + 0.9 608 1935
-4 + 1.1 1935 5564
-3 + 1.2 5564 6258
-2 + 1.1 6258 7145
-1 + 1.3 7145 5199
0-1 + 0.0 5199 5199
0-2 - 1.3 5199 8064
0-3 + 0.0 8064 8064
1 + 1.4 8064 40792
2 + 2.2 40792 22186
3 + 1.9 22186 9420
4 + 1.4 9420 7384
5 + 1.2 7384 4008
6 + 0.9 4008 1523
7 + 0.7 1523 407
8 - 0.6 407 115
9 - 0.6 115 11
10 + 0.5 11 4
11 - 0.3 4 2
12 - 0.4 2 1
13 + 0.4 1 0
14 + 0.0 0 0
15 + 0.0 0 0
16 + 0.0 0 0
Figure 2.2 Serial Data Dump Example

18
2.3 Serial Port Programming - MODBUS:
This type of serial communication require the RS-232 (-S) or RS-485 (-M) hardware option. To
communicate to the 1250-LTC with MODBUS protocol, connect a computer with the appropriate
MODBUS communication software and serial port hardware to the 1250-LTC’s serial port cable.
The computer must have the proper Comm port settings to communicate to the 1250-LTC (see
Section 3.3, page 46). See Table 2.3 for a full listing of all MODBUS Registers, the definition
and binary format for each.
In the following Table 2.3 the meanings of the columns is as follows:
Register: MODBUS register address as seen in a MODBUS command beginning with
register 40001 and ending with 45895. These addresses are in decimal.
Hex: The same register’s address in hexadecimal, this value is calculated by
subtracting 40001 from the register number. Thus register 40001 in decimal
becomes 0000 in hex, and 40257 in decimal becomes 0100 in hex.
Function: Defines what each register contains or does when written. Some registers
are read only and have no meaning when written. Others can be written
or read. Others are “write only” special functions and cause actions to be
performed when they are written.
Format: This column defines what a register contains bit-by-bit in binary. A row of 16
symbols shows what each of the 16 bits of the register contain MSB first
and LSB last. A BCD formatted floating point register is shown as
follows (two 16 bit binary words):
Bcdabcdbbcdcbcdd bcde000000vspppp
bcda, bcdb, bcdc, bcdd, bcde are each four-bit BCD digits, as it
would be seen on a display.
000000 are 6 unused bits that report as 0 when read and must be 0
when written.
vis an overflow bit that indicates that the number in the register is too
big to display when it is a 1. 0 indicates a valid register value.
sis the sign bit and is 1 when the value in the register is negative. 0
indicates a positive number.
pppp is the position of the decimal point within the bcd digits.
Most registers are not as complex as a floating-point register.
An alternate floating-point format is supported and selected by writing a 1 to
the 40256d (00ff h) register. This selects an IEEE floating-point format as
follows (two 16 bit binary words):
seeeeeeeemmmmmmm mmmmmmmmmmmmmmmm
The format of the IEEE floating-point number is as follows:
sis the sign bit,
eis the exponent bits, and
mare the mantissa bits.

19
The MODBUS protocol is a master/slave packet based protocol with the 1250-LTC operating
as a RTU slave. The MODBUS function commands recognized by the 1250-LTC are “3”
(read multiple registers) and “16” (write multiple registers). By supporting these two
commands the 1250-LTC is in level 0 compliance. Using these two commands it is possible
to configure the 1250-LTC as well as monitor it for current position. MODBUS RTU
command and response packets are formatted as follows:
2.3.1 MODBUS Packet Format - Read
Reading from Holding Registers:
GAP = A gap in transmission of 3.5 character frames indicates to the slaves that a new packet
is to follow. No transmission gaps within a packet may exceed 1.5 character frames.
Byte 1 = Device Address: Address 0 is a broadcast address that all units respond to regardless
of programmed address. All other addresses can be programmed and used in this mode.
Byte 2 = Function Code: When reading holding registers, this byte is “03h”
Data Block = Begins with the number of the first register (two bytes) in a command packet,
or data from the first register (two bytes) in a response packet. Followed by the number of
registers to be read (two bytes) in a command packet, or by data from subsequent registers.
Last 2 Bytes = Error Checking CRC – Lo Byte & Hi Byte
Table 2.3 Read Registers Command Format
GAP
3.5
Char
Device
Address
Function
Code
# of First
Register
Hi
# of First
Register
Lo
# of
Registers to
Read Hi
# of
Registers to
Read Lo
CRC
Lo
CRC
Hi
Min. 80h 03h 01h 03h 00h 04h xx xx
Table 2.4 Read Registers Response Format
GAP
3.5
Char
Device
Address
Function
Code
Byte
Count
Data from
First Register
Hi
Data from
First Register
Lo
Data from
Second
Register
Hi
Data from
Second
Register
Lo
Min. 80h 03h 08h 01h 03h 00h 03h
…… …… Data from Last
Register Hi
Data from Last
Register Lo
CRC
Lo
CRC
Hi
…… …… 00h 02h xx xx

20
2.3.2 MODBUS Packet Format - Write
Write to Holding Registers:
GAP = A gap in transmission of 3.5 character frames indicates to the slaves that a new packet
is to follow. No transmission gaps within a packet may exceed 1.5 character frames.
Byte 1 = Device Address: Address 0 is a broadcast address that all units respond to regardless
of programmed address. All other addresses can be programmed and used in this mode.
Byte 2 = Function Code: When writing to holding registers, this byte is “10h”
Data Block = Begins with the number of the first register to be written (two bytes), followed
by the number of registers to be written (two bytes), in either command or response packets.
In a command packet the programming data for the first register will be the next two bytes
followed by programming data for subsequent registers.
Last 2 Bytes = Error Checking CRC – Lo Byte & Hi Byte
Table 2.5 Write Registers Command Format
GAP
3.5
Char
Device
Address
Function
Code
# of First
Register to be
written to Hi
# of First
Register to be
written to Lo
# of Registers
to Write Hi
# of Registers
to Write Lo
Min. 80h 10h 10h 00h 00h 04h
Byte
Count
Program Data for
First Register
Hi
Program Data for
First Register
Lo
Program Data for
Second Register
Hi
Program Data for
Second Register
Lo
08h 00h 01h 03h 60h
……
……
Program Data for
Last Register Hi
Program Data for
Last Register Lo
CRC
Lo
CRC
Hi
…… …… 00 01 xx xx
Table 2.6 Write Registers Response Format
GAP
3.5
Char
Device
Address
Function
Code
# of First
Register to
be written to
Hi
# of First
Register to
be written to
Lo
# of
Registers
to Write
Hi
# of
Registers
to Write
Lo
CRC
Lo
CRC
Hi
Min. 80h 10h 01h 00h 00h 04h xx xx
Table of contents
Popular Touch Panel manuals by other brands

Panasonic
Panasonic TY-TP42P30K () operating instructions
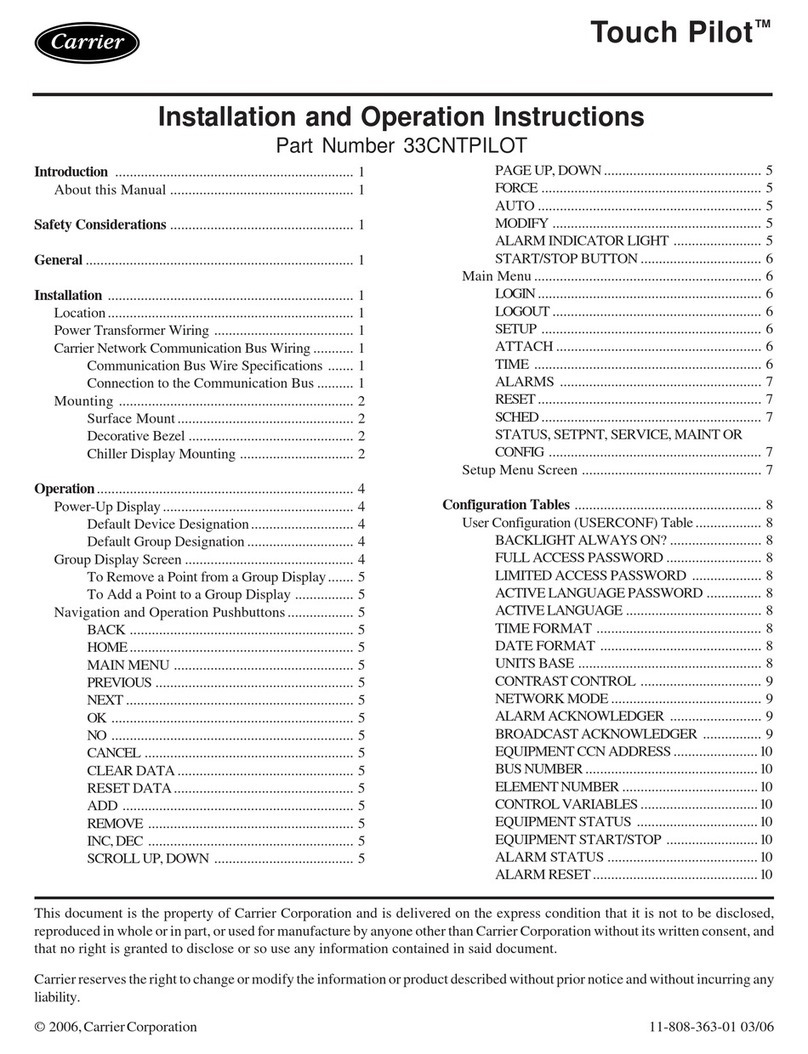
Carrier
Carrier Touch Pilot 33CNTPILOT Installation and operation instructions
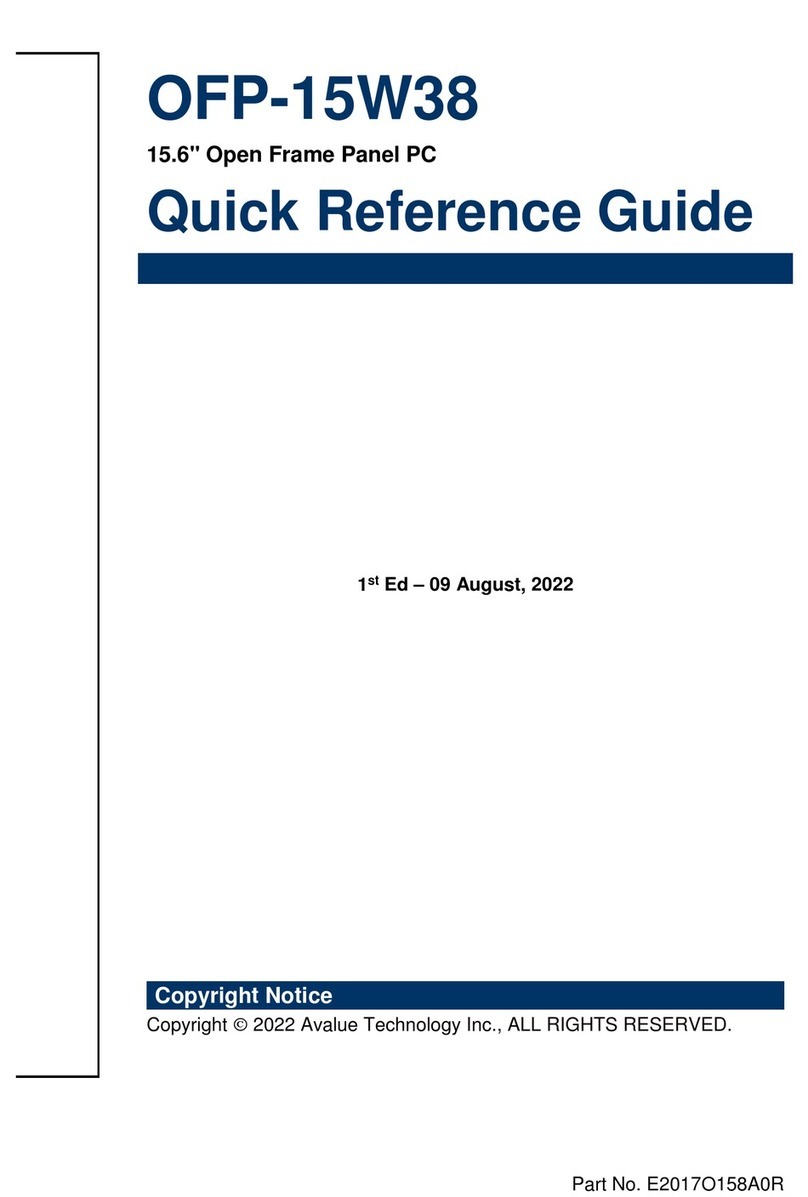
Avalue Technology
Avalue Technology OFP-15W38 Quick reference guide
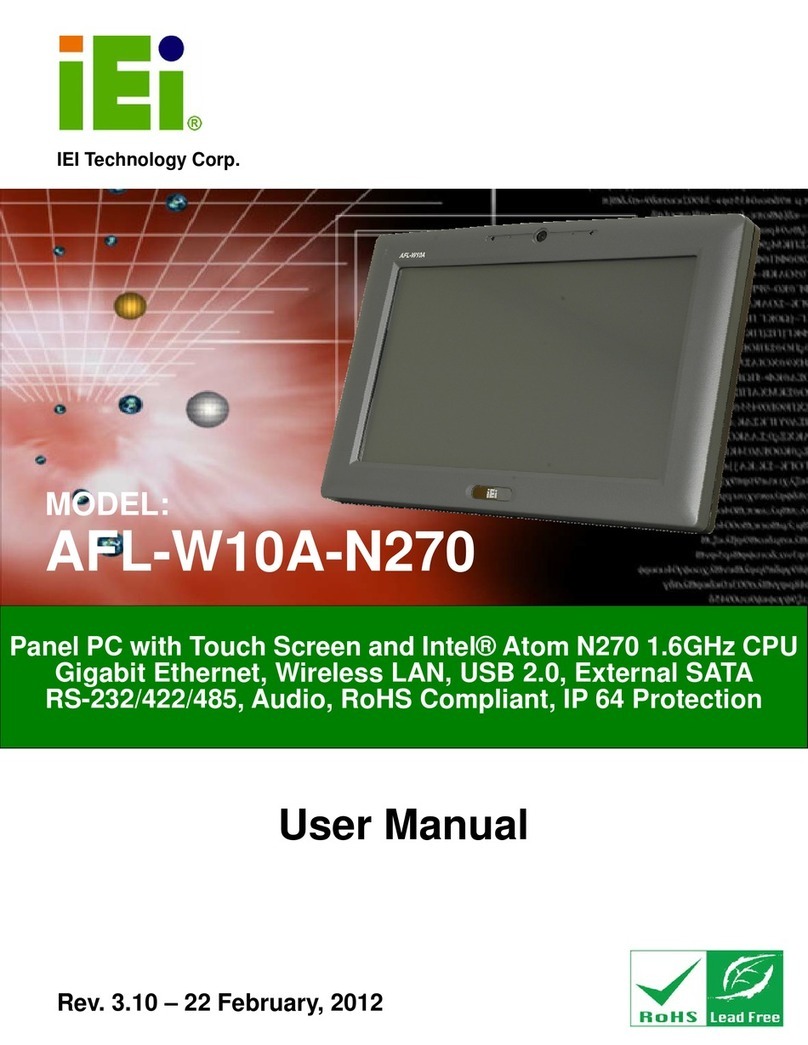
IEI Technology
IEI Technology AFL-W10A-N270 user manual
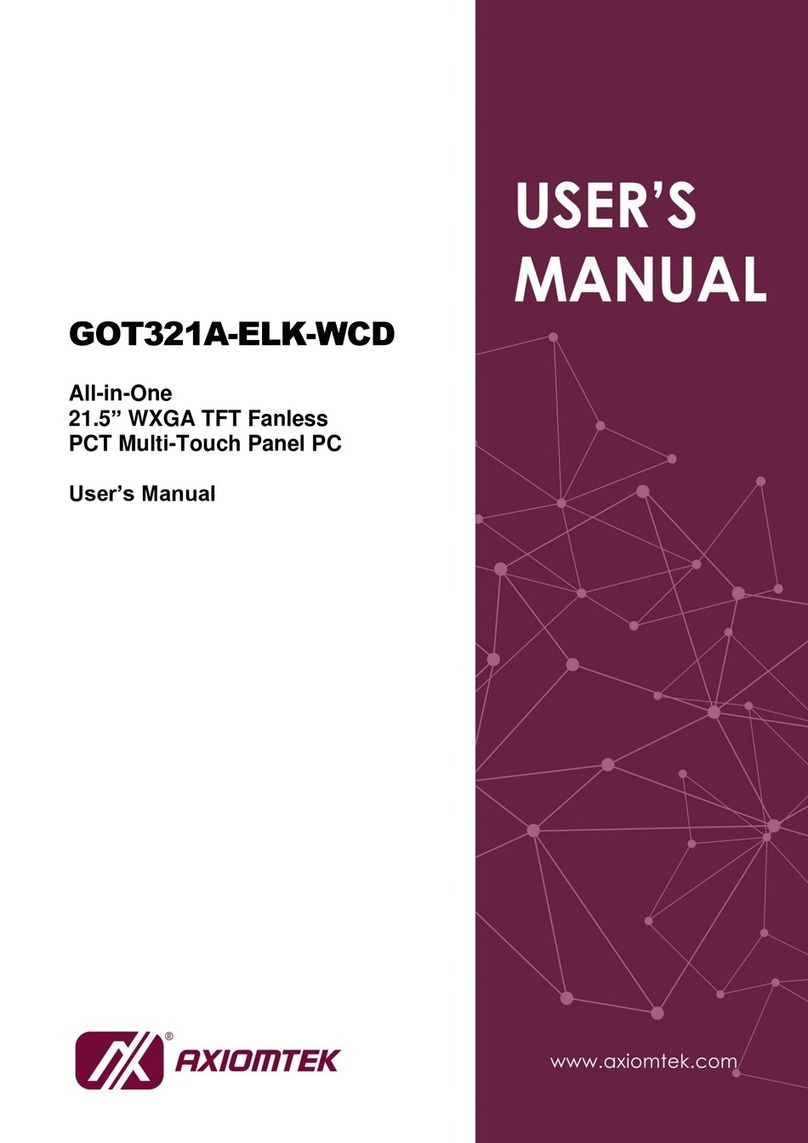
AXIOMTEK
AXIOMTEK GOT321A-ELK-WCD user manual
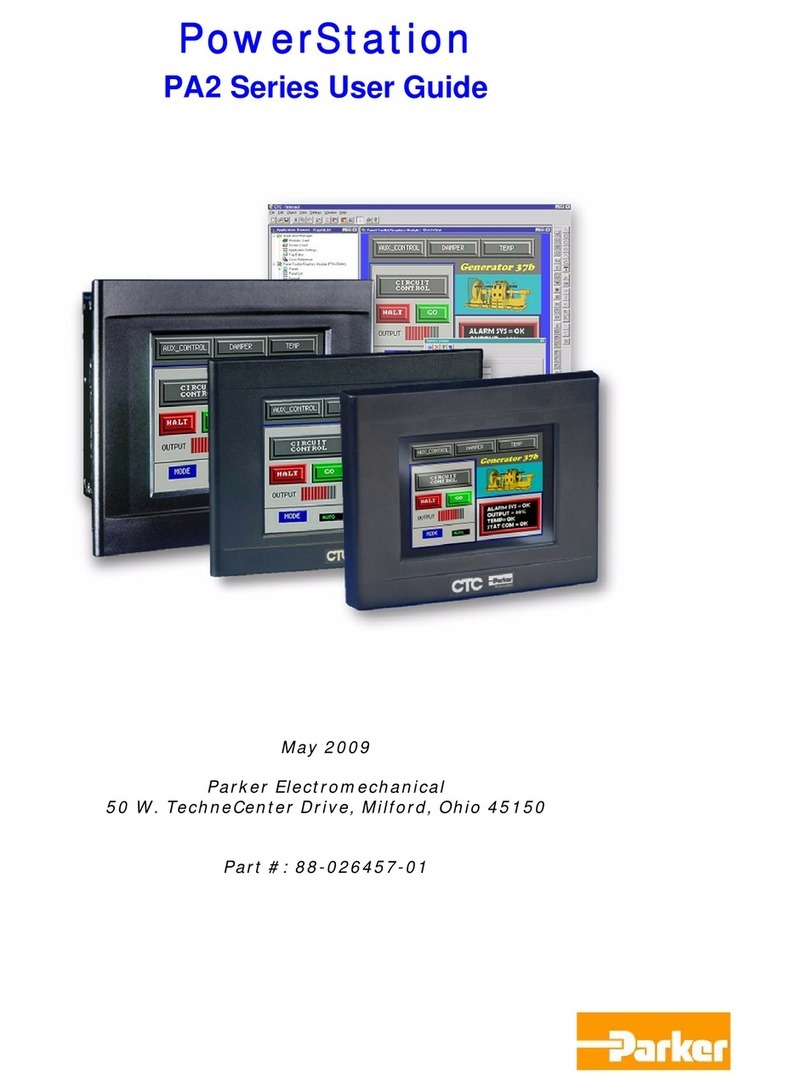
Parker
Parker PowerStation PA2 Series user guide
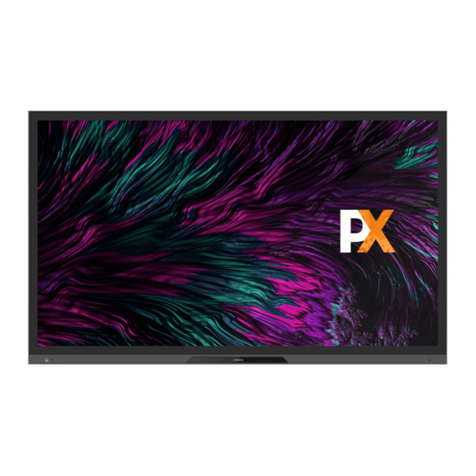
i3-TECHNOLOGIES
i3-TECHNOLOGIES i3TOUCH PX quick start guide
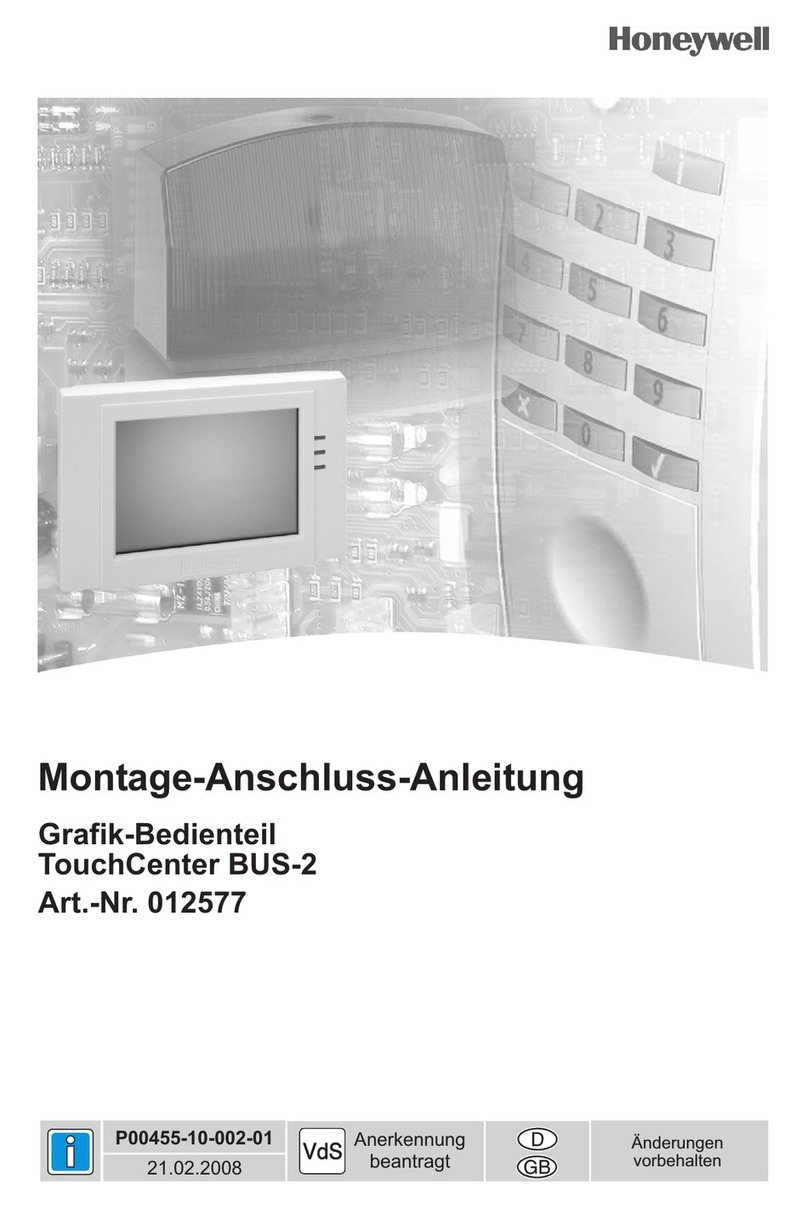
Honeywell
Honeywell 012577 Mounting and Connection Instructions
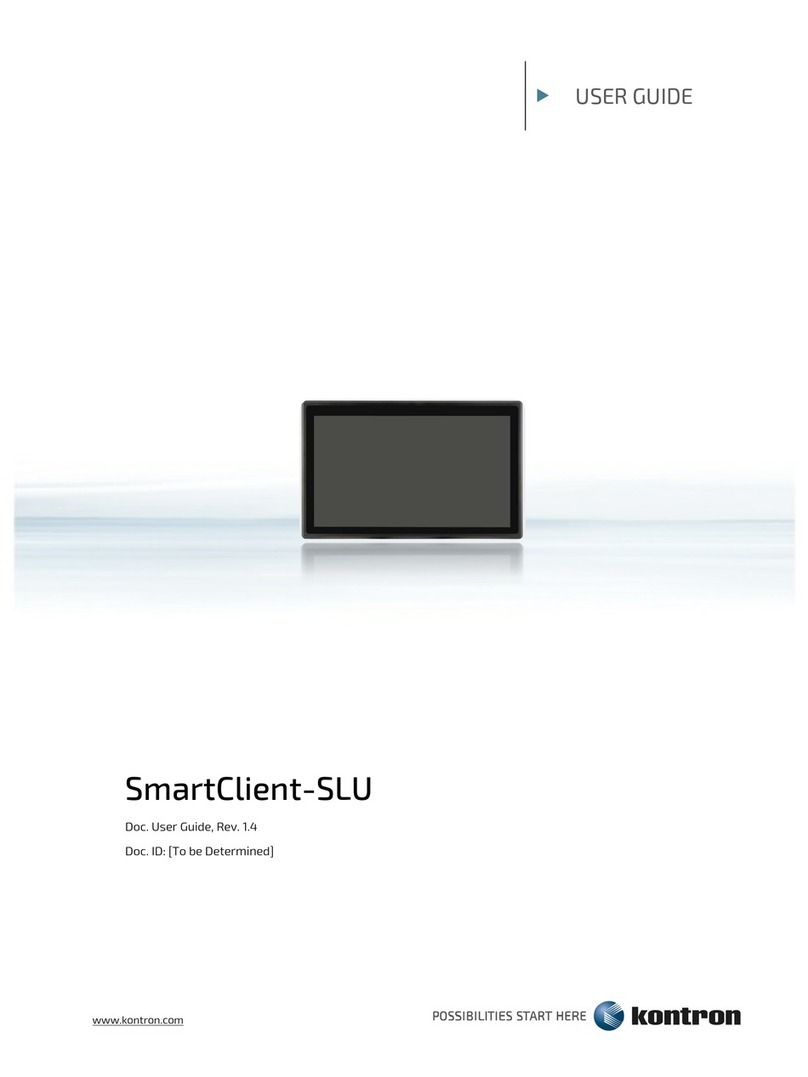
Kontron
Kontron SmartClient-SLU user guide
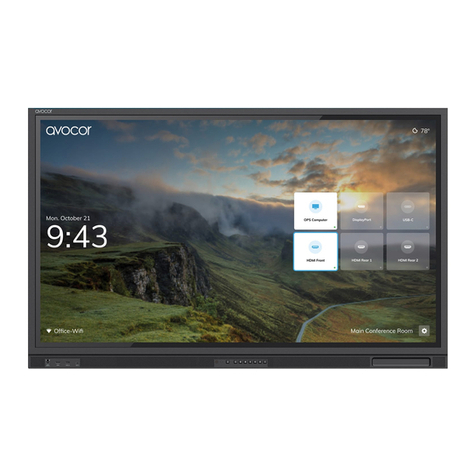
AVOCOR
AVOCOR AVE-5530 user manual
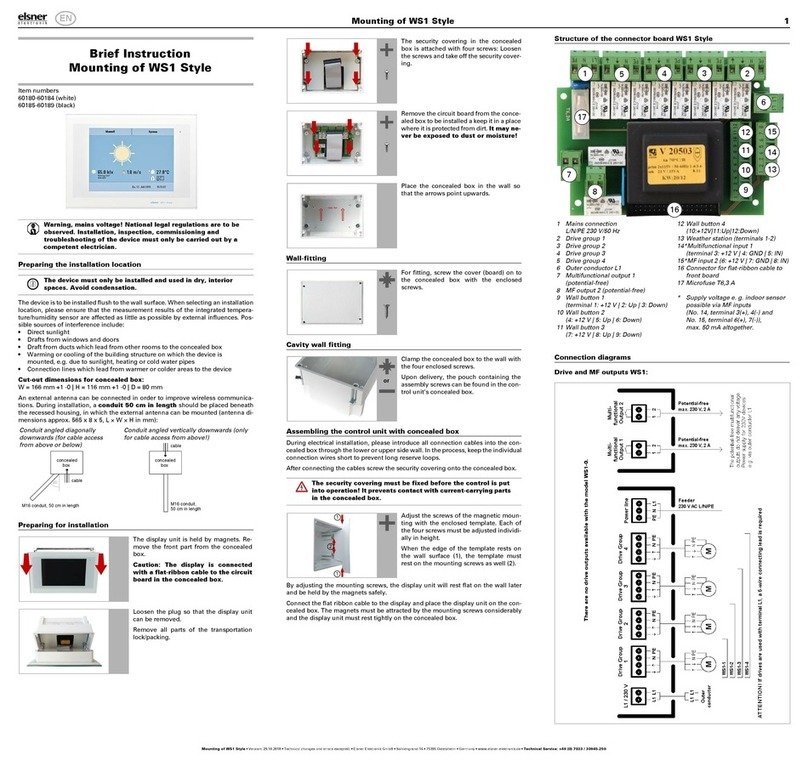
elsner elektronik
elsner elektronik WS1 Style Series Brief instructions
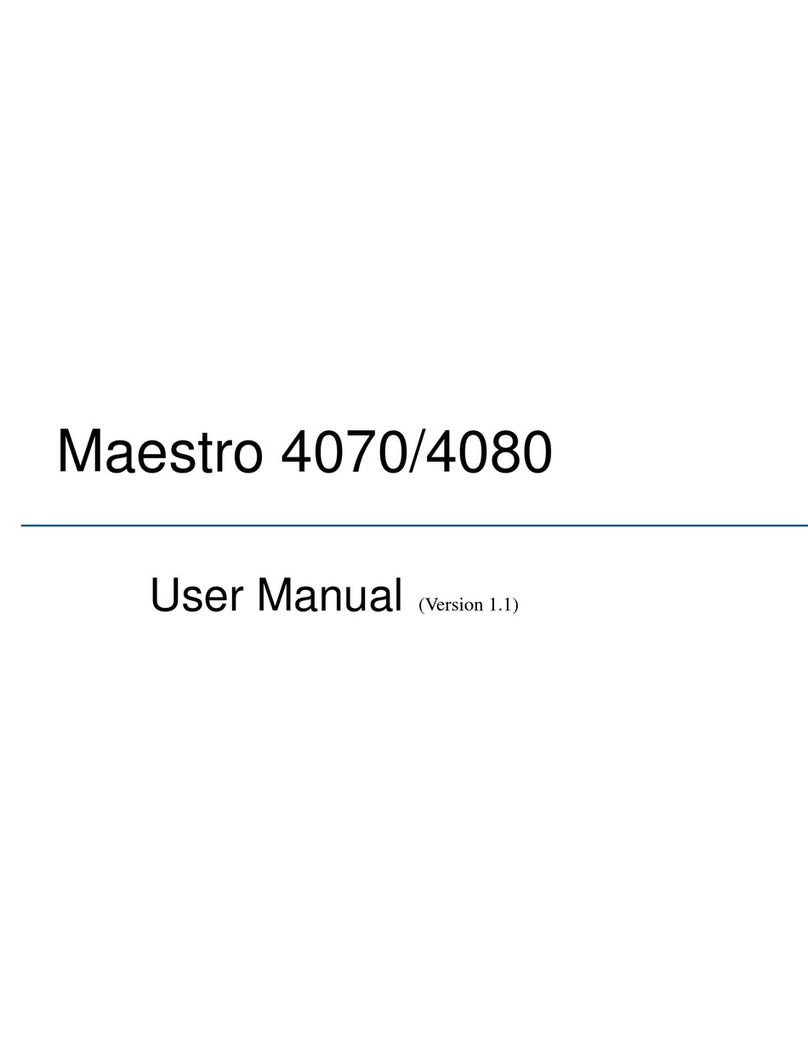
MiTAC
MiTAC Maestro 4070 user manual