Intech Micro 2100-A16 User manual

INTECH Micro
2100-A16 REV 1.3
Installation Guide.
14.01-1
TECHNOLOGY
& QUALITY
A
W
A
R
D
ISO9001
E
G
I
S
T
E
R
R
E
D
M
A
N
U
A
T
U
R
E
R
C
F
Z985

14.02-2
Section A. Description, Ordering and Specifications.
2100-A16 Installation Guide Index.
Section A. Description, Ordering and Specifications.
Index. Page 2
Features and Ordering Information. Page 3
Specifications. Page 4
Terminals and layout. Page 6
Dimensions. Page 7
Section B: Jumpers and LED Functions Tables.
S1 Function Settings. Page 7
H1 Power Supply Settings. Page 7
H2 Comms Settings. Page 7
H4 RTD Settings. Page 7
LED Descriptions. Page 7
Section C. Input and Output Connection Diagrams.
Milliamp Inputs. Page 8
Millivolts and Voltage Inputs. Page 8
RTD Inputs. Page 9
Thermocouple (T/C) Inputs. Page 9
Thermocouple Upscale (US) / Downscale (DS) Drive. Page 9
Connection Example Diagram for Digital Inputs. Page 10
Connection Diagram Using an LPI-D Current Loop Isolator on the Input. Page 10
Connection Diagram Using an XI-P1 Current Loop Isolator on the Input. Page 10
Connection Example Diagram for Digital Outputs. Page 10
Section D. Connecting to a Microscan Scada System.
Analogue Input Expansion - Using 2100-MAnalogue Input Multiplexer. Page 11
Option 1. 5 Wire Connection Diagram. Page 11
Option 2. 4 Wire Connection Diagram. Page 11
Analogue Outputs Controlled by the Scada. Page 12
2100-RL2 2 Relay Slave Board Connection. Page 12
2100-ME Memory Expansion. Page 12
2100-R2 Relay Expansion. Page 13
RS485 Serial Connection. Page 14
RS422 Serial Connection. Page 14
RS232 Serial Connection. Page 15
RS232 Radio Modem Serial Connection. Page 15
Station Number Programming and Serial Numbers. Page 15
Station Software Programming. Page 15
TXE and TX Delay Settings and Table. Page 16
Section E. Connecting to a PLC.
Mode 3. Clock & Reset Channel Selection. Page 16
Mode 4. Binary Channel Selection. Page 17
Connection examples of a PLC with open collectors
commoned to 24V of an external power supply. Page 18
commoned to the 20V of the first 2100-A16 power supply. Page 18
commoned to 0V of an external power supply. Page 19
commoned to COM of the first 2100-A16 Page 19
PLC RTX Fail Safe System Page 20
Analogue Signal Converted to Frequency for a PLC, using a TWI-FO. Page 20
Section F. Communications.
Modbus RTU Communication Protocol. Page 20
Modbus RTU StationAddresses. Page 21
Using the Modbus Protocol. Page 21
2100-A16 Modbus Notes. Page 23
2100-A16-NET Ethernet 10/100. Page 23
Section G. Wiring, Installation, and Maintenance.
Mounting Page 25
Cover Removal and Fitting. Page 25
Power Supply Wiring. Page 25
RS422/485 Comms Signal Cabling. Page 26
Cautions Using Differential Inputs. Page 26
Cautions UsingAnalogue Inputs. Page 26
Analogue Signal Wiring. Page 26
RTDs Page 27
Thermocouples Page 27
Commisioning. Page 27
Maintenance. Page 28

A-0012rofsnoitpOgnignaR 61
noitpOhtiwdeilppuS O tuOeugolanA OA SMMOC C lppuSrewoP
y
)4(
SP
draoByromeMEM-0012EMAm02~41A 232SR232
)1(
cd/caV462~58H
rednapxEyaleR612R-0012 2R Am02~0 2A 224SR 224 cdV09~32 M
dBevalSyaleR22LR-00122LR V01~21V 584SR584 cd/caV82~01L
snoitpOoN N V01~0 2V tenrehtE TEN
16 Universal Analogue Inputs.
4 Digital Inputs. 2 Analogue
Outputs. 2 Relay Output.
INTECH Micro
2100-A16 Rev 1.3
Features.
z 16 Universal Analogue Inputs.
z Each Input Individually Selected & Scaled.
z 16 Bit Resolution.
z Inputsfor:
z RTD: 0~25C to -200~850C.
z mV: 0~25mV to ±500mV.
z V: 0~1V to ±15V.
z mA: 0~1mA to ±100mA.
zz
zz
z2 Analogue Ouputs.
zz
zz
zFour Digital, Isolated, Optocoupler Inputs.
zz
zz
zTwo Digital, Isolated, Relay Outputs.
zz
zz
zRS422/RS485 Up to 1200m.
zz
zz
zRS232 Cost Effective Radio Installation.
zz
zz
zRS232 Cost Effective PC or PLC AI Expansion.
zz
zz
zModbus RTU and Modbus TCP Options Available.
zz
zz
zClock/Reset Drive up to Four 2100-Ms.
zz
zz
zSelectable Baud Rates.
zz
zz
zDigital Inputs:
- State or Count.
- Speeds to 50Hz.
zz
zz
zInterface for 2100-R2 (16 Relays) or 2100-ME (Memory).
zz
zz
zEasy Programming Via Microscan Maps.
zz
zz
zProgrammable Station Number.
zz
zz
zProgrammable Relay States - NO or NC.
zz
zz
zComms Failure Time-out Using Relay 2.
zz
zz
zComms TXE and TX Delay Programming.
zz
zz
zProgramming Information Retained on Power Down.
zz
zz
zUniversal AC/DC Power Supply.
zz
zz
zEasy to Install.
zz
zz
zCompact DIN Rail Mount Enclosure
Ordering Information.
2100-A16 Rev1 -X Standard Unit: Analogue Inputs Pt100, 0~100C; Analogue Outputs,
4~20mA; RS485 Comms; 85~264Vac/dc Power Supply.
2100-A16 Rev1 O AO C PS
Quality Assurance Programme.
The modern technology and strict procedures of the ISO9001 Quality Assurance Programme applied during design,
development, production and final inspection grant long term reliability of the instrument. This instrument has been
designed and built to comply with EMC and Safety Standards requirements.
Ordering Examples.
1/ 2100-A16-ME-A1-232-L 2100-A16; Memory Board Fitted; 4~20mA AO; RS232 Comms; 10~28Vac/dc PS.
2/ 2100-A16-N-V2-485-H 2100-A16; 0~10V AO; RS485 Comms; 85~264Vac/dc Power Supply.
14.02-3
Note 1. The RS232 Comms. version comes complete with a RS232 kit, required for connecting the 2100-A16 to a PC,
etc. The kit contains: 1 x 5m RS232 cable; (2,10 & 15m available.) 1 x 9 pin D type (25 pin D type available).
Note 2: The 2100-A16 is factory set to RS232 or RS422/485. The 2100-A16-X is field selectable for RS422 or RS485,
and H or M power supply.
Note 3: The Microscan, PLC Message and Modbus RTU Comms Protocols come standard on all units.
Note 4: Power supply ‘H’ is field selectable for ’M’, and ‘M’ for ‘H’. Power supply ‘L’ must be ordered separately.
2100 models include:
2100-4S : RS422 to RS485 Converter.
2100-A16 :16AI, 4DI, 2 Relay Out, 2 AO.
2100-A4 :4AI, 4DI, 4 Relay Out, 2 AO.
2100-A4e :4AI, 4DI, 8 Relay Out, 2 AO.
2100-AO :8 AO, 8 AI, 12 DI, 2 Relay Out.
2100-D :12DI, 12 Relay Out.
2100-IS :Isolated RS232 to RS422/485.
2100-M :16AI Multiplexer.
2100-ME :Memory Expansion for 2100-A.
2100-NET :Isolated Ethernet to RS232/422/485.
2100-NS :Non-Isolated RS232 to RS422/485.
2100-R2 :16 Relay Expansion for 2100-A.
2100-RL2 :2 Relay Expansion for 2100-A.
TECHNOLOGY
& QUALITY
A
W
A
R
D
Z985
ISO9001
E
G
I
S
T
E
R
R
E
D
M
A
N
U
A
T
U
R
E
R
C
F

14.02-4
2100-A16 Input Specifications.
Note: Each input can be individually software selected & scaled within the span limits listed below.
Input Resolution 16 Bits, 50,000 Steps Average. (Some ranges may differ.)
Input Differential 18Vac/dc peak (sum of ac + dc) between any two channels.
Note: RTD Pt100/Pt1000 are single ended.
mV / V Inputs:
- Input Impedance >1M @ 10V to >100k @ 25mV.
- Maximum Over-range 18Vdc Continuous.
- mV Ranges 0~25mV, 0~50mV, 0~100mV, 0~250mV, 0~500mV.
±25mV, ±50mV, ±100mV, ±250mV, ±500mV.
- V Ranges 0~1V, 0~2.5V, 0~5V, 0~10V, 0~15V.
±1V, ±2.5V, ±5V, ±10V, ±15V.
mA Inputs: note 2
- Input Resistance 25
- Maximum Over-range 100mAdc Continuous.
- mA Ranges 0~1mA, 0~2mA, 0~4mA, 0~10mA, 0~20mA, 4~20mA, 0~40mA, 0~100mA.
±1mA, ±2mA, ±4mA, ±10mA, ±20mA, ±20mA, ±40mA, ±100mA.
3-wire RTD Inputs: note 3
All temperature probes must be isolated from each other and earth.
- Inputs 16 Single Ended RTD Inputs. All 2nd ‘B’ Terminals Connected.
- Pt100 RTD Type 3 Wire Pt100 RTD DIN 43760:1980 Standard Input.
- Pt1000 RTD Type 3 Wire Pt1000 RTD Standard Input.
- Sensor current 1mA Multiplexed
- Lead resistance 10/Lead Maximum Recommended.
100/Lead Absolute Maximum.
- Sensor Fail Upscale Drive.
- RTD Ranges 0~25C (32~75F), 0~50C (32~120F), 0~100C (32~200F),
0~250C (32~475F), 0~500C (32~930F), 0~850C (32~1550F).
±25C (-10~75F), ±50C (-50~120F), ±100C (-140~200F),
-200~250C (-320~475F),-200~500C(-320~930F),-200~850C(-320~1550F).
Thermocouple Inputs: Use 2400-A16 model for Thermocouple Input note 3
Mineral Insulated Thermocouples With Isolated Junction Essential.
- Cold Junction Comp. 0~60C.
- CJC Drift <0.03C/C Typical for Input 1.
Refer to notes under 2100-A16 Input Connection Diagram for T/C Inputs.
- Sensor open Circuit Floats to ambient ±10C typical. For Upscale or Downscale Drive
Refer ‘2100-A16 Input Connection Diagram for Thermocouple
Upscale (US) / Downscale (DS) Drive.’
- T/C Lead Resistance 100Maximum.
- Input Impedance >100kMinimum.
- Accuracy <±0.1% FSO ±1C Typical.
- Type B Ranges 0~1800C (32~3250F). Accurate Range 250~1800C
- Type E Ranges 0~300C (32~570F), 0~600C (32~1100F), 0~900C (32~1650F),
±200C (-320~390F).
- Type J Ranges 0~400C (32~750F), 0~800C (32~1450F), 0~1200C (32~2150F),
±200C (-320~390F).
- Type K Ranges 0~500C (32~930F), 0~1000C (32~1800F), 0~1300C (32~2370F),
±200C (-320~390F).
- Type N Ranges 0~600C (32~1100F), 0~1300C (32~2350F), ±200C (-320~390F).
- Type T Ranges 0~400C (32~720F), ±200C (-320~390F).
- Type R Ranges 0~1700C(32~3050F).
- Type S Ranges 0~1700C(32~3050F).
Digital Inputs: 4 Opto Isolated Inputs with LED Indication of Each Input.
-Functions ON / OFF, Count, and Flow Metering.
Count to 16383 & Rolls Over. Over Flow Detection.
-Input Voltage 5~30Vdc.
-Threshold 4.6V Typical.
-Load @ 5V 1.1mA per Channel.
@ 12Vdc 4.2mA per Channel.
@ 20Vdc 8mA per Channel.
@ 24Vdc 9.6mA per Channel.
-Frequency 0~50Hz.
-ChannelSelection CLOCK & RESET Pulse Length = 20msec Minimum.
Settling Time Before Reading = 100msec.
(Multiple readings with averaging recommended.)
Intelligent Multiplexer:
-ChannelSelection Clock and Reset or Binary. (Refer Digital Inputs)
-Cycle Time 4sec. minimum to cycle through all 16 inputs.
-Resolution 12bits, 4000 steps typical.

14.02-5
2100-A16 Output Specifications.
Dual Analogue Outputs: Analogue Outputs supplied from factory as mA. V must be factory fitted.
-Resolution 2 Outputs, 12bits, 4000 Steps Typical. (Some ranges may differ.)
-V Ranges 0~10V, 2~10V. Output Drive = 4mA Maximum. (2k5 @ 10V)
-mA Ranges 0~20mA, 4~20mA. Output Drive = 12V Maximum. (600@ 20mA)
Digital Outputs: 2 Isolated Relays with LED Indication of Each Output.
-Functions 2 on Board Controllers (16 with 2100-R2), Can be used as Set Point (SV)
SwitchingDifferential,Auto/Manual,ManualOutputSetting,DualActionControl,
Single Action Control, Heat/Cool, Cool Only, Heat Only.
-Contact Material Gold Clad Silver.
-RelayRatings 30Vac/dc, 1A Maximum.
-Approved to Standard UL & CSA:.
-Number of Operations 1 x 105Min, at 30Vac/dc, 1A, Resistive Load.
2100-A16 General Specifications.
Comms: -Protocols Intech Scada; PLC Message; Modbus RTU; RS422/RS485 or RS232
-Baud Rate Selectable 2400, 4800, 9600. (Default = 9600).
-Format 8 bit, No Parity, 1 Stop. (Not selectable.)
-Modbus RTU Refer to Modbus section, Page 20, for more details.
-Ethernet10/100 Refer to Ethernet 10/100 section, Page 23, for more details.
Power: -H 85~264Vac/dc;50/60Hz; 10VA.
-M 23~90Vdc;10VA.
-L 10~28Vac/dc; 50/60Hz; 10VA.
Referto‘2100-A16 H1PowerSupplySettings’forvoltageselectioninstructions.
Transmitter Power Supply 20Vdc±5%; Max. Load=50mA; Ripple<20mVrms; Common to Analog Inputs.
Transmitter power supply is not available with Ethernet 10/100 comms option.
Safety and EMC Compliances:
EMC Compliances Emissions EN 55022-A. Immunity EN 50082-1.
Safety Compliance EN 60950.
Mains Isolation 250Vac.
Mains Isolation Test Voltage -To all Inputs and Outputs: 3000Vac 50Hz for 1min.
-To Earth 1500Vac 50Hz for 1min.
Input/Output Isolation Test Voltages -Digital Input to Analogue Input/Output: 1000Vdc for 1min.
-Digital Input to Digital Output: 1000Vdc for 1min.
-Analogue Input/Output to Digital Output: 100Vdc for 1min.
-Comms to Analogue Input/Output: 1000Vdc for 1min.
-Comms to Digital Input/Output: 1000Vdc for 1min.
General Specifications: (Unless otherwise stated in other input specifications.)
Accurate to <±0.1% FSO Typical.
Linearity& Repeatability <±0.1% FSO Typical.
ChannelSeparation <±0.1% FSO Typical.
Ambient Drift <±0.01%/C FSO Typical.
Noise Immunity 125dB CMRR Average Differential Input 18Vpeak.
RF Immunity <±1% Effect FSO Typical.
A01 & AO2 25msec. Nominal Pulse Length.
-(used as CLOCK and RESET) 20mA Nominal Current.
Settling Time and Averaging Software Selectable.
Permanent Memory (E2ROM) 10,000 Writes per Input Parameter.
-(2100-ME fitted) 10 Year Data Retention.
Operating Temperature 0~60C.
Storage Temperature -20~80C.
OperatingHumidity 5~85%RH Max. Non-Condensing.
Housing -Material ABS Inflammability V0 (UL94)
-Dimensions L=195, W=120, H=70mm.
-Mounting 35mm Symmetrical Mounting Rail.
-Weight 800g. Includes Packaging.
Note 1. Contact INTECH INSTRUMENTS for more detailed programming information.
Note 2. For mA inputs a 2 pin jumper must be installed for each input.
Note 3. The 2100-A16 is C and F selectable. This selection affects all temperature readings. (CJC must be calibrated in C.)
Product Liability. This information describes our products. It does not constitute guaranteed properties and is not intended to affirm the suitability
of a product for a particular application. Due to ongoing research and development, designs, specifications, and documentation are subject to
change without notification. Regrettably, omissions and exceptions cannot be completely ruled out. No liability will be accepted for errors, omissions
or amendments to this specification. Technical data are always specified by their average values and are based on Standard Calibration Units at
25C, unless otherwise specified. Each product is subject to the ‘Conditions of Sale’.
Warning: These products are not designed for use in, and should not be used for patient connected applications. In any criticalinstallation
an independant fail-safe back-up system must always be implemented.
CAUTION: Dangerous Voltages may be present. The 2100-A16 has no user serviceable parts.
Protective enclosure only to be opened by qualified personnel.
Remove ALL power sources before removing protective cover.

2100-A16 Terminals and Layout.
14.02-6
Earth ( )
Neutral (-)
Phase (+)
25
26
27
28
29
30
31
32
33
34
35
36
37
38
39
40
41
42
43
44
45
46
47
48
49
70
71
72
73
74
80
81
82
1
2
3
4
5
6
7
8
9
10
11
12
13
14
15
16
17
18
19
20
21
22
23
24
60
61
62
50
51
52
54
55
56
57
58
TXE
TX
RX
0V
20Vdc
RX -
RX +
TX -
TX +
COM
H
M
S1: FUNCTION
JUMPERS
1 2 3 4 5 6
1
2
3
4
5
6
7
8
9
10
11
12
13
14
15
16
A
B
B
A
B
B
A
B
B
A
B
B
A
B
B
A
B
B
A
B
B
A
B
B
A
B
B
A
B
B
A
B
B
A
B
B
A
B
B
A
B
B
A
B
B
A
B
B
AO COM
AO 1
AO 2
Relay COM
Relay 1
Relay 2
DI COM
DI 1
DI 2
DI 3
DI 4
H3: EXPANSION
CONNECTOR
J9
J10
J11
J12
J13
J14
J15
J16
J1
J2
J3
J4
J5
J6
J7
J8
H1: SUPPLY VOLTAGE
SELECTOR
H2: COMMS
SELECTION
DIGITAL
IN RELAY
OUT ANALOGUE
OUT ANALOGUE
IN
ANALOGUE
IN
COMMS
POWER
BEAT
L4
L3 L2
L1
H4: RTD
SELECTION
WARNING.
High Voltages May be
Present in This Area.
Only adjust jumpers
with power OFF.
P/S
Note. 20Vdc Transmitter Power Supply
on Terminal 49, is not available with
the Ethernet 10/100 comms option.
2100-A16 Rev1.1 Dimensions.
195mm
120mm
.
120mm
7
0
mm
Intech
INSTRUMENTS LTD
www.intech.co.nz

14.02-7
Section B: 2100-A16 Jumpers and LED Functions Tables.
* For ALL programming tables. Jumper Status: 0=JUMPER NOT INSERTED 1=JUMPER INSERTED.
* Refer to ‘2100-A16 Terminals and Layout’ for the location of the following jumpers and switches.
2100-A16 S1 Function Jumper Settings.
sgnitteShctiwSpiDnoitcnuF
noitcnuF 1-1S 2-1S 3-1S 4-1S 5-1S *6-1S
duab0069
1eton
000000
duab0084 0 1 0 0 0 0
duab0042 110000
edoMtseT
2eton
0 0 1 0 0 0
EM-0012 xx0100
PCTsubdoM
4eton
0 0 0 0 1 0
UTRsubdoM
5eton
xx0001
Note 1. Factory Default.
Note 2. Factory use ONLY.
Note 3(*). When using Modbus RTU Protocol
S1-6is‘1’.Refer ModbusSection.(Rev1.2)
Note 4. For use with Ethernet (Rev 1.3).
Note 5. For use with 232/422/485 (Rev 1.3).
2100-A16 H1 Power Supply Settings.
sgnitteSrepmuJylppuSrewoP
1H egnaRegatloVylppuSrewoP
Hcd/caV462~58rofrepmuJ
M cdV09~32rofrepmuJ
Note 1. Power must be OFF before changing
H1’s position.
Note 2. Exceeding these parameters may
damage the unit.
Note 3. Ensuretheenclosurelabeliscorrectly
labelled for the jumper position.
Note 4. Low Voltage Power Supply version is
fixed, and has no jumper. This must
be ordered separately.
snoitpircseDDEL
emaNDEL noitcnuFDEL
XR .atadlairesgniviecersinoitatSnehwevitcA
XT .atadlairesgnittimsnartsinoitatSnehwylnoevitcA
EXT .atadtimsnartotydaersinoitatSnehwylnoevitcA
TAEB yhtlaehnoitatSsetacidnignihsalflaunitnoC.taebtraeH
2~1tuptuOlatigiD .dezigrenesiyalertuptuoevitcepserriehtnehwsetacidnI
4~1tupnIlatigiD .gnitnuocro,dezigrenesitupnievitcepserriehtnehwsetacidnI
teseR/kcolC .evitcasirexelpitlumrofteseRrokcolCevitcepsernehwsetacidnI
2100-A16 LED Descriptions.
Note 1. The orientationof thisdrawingis with
P/Sterminaltothetopside(Standard
Mounting)
Note 2. RS232mustbeorderedseparatelyto
RS422/485.
Note 3. RS422 can be jumpered for RS485,
and vice versa.
2100-A16 H2 Comms Settings.
CAUTION: Dangerous Voltages may be present. The 2100-A16 has no user serviceable parts.
Protective enclosure only to be opened by qualified personnel.
Remove ALL power sources before removing protective cover.
2100-A16 H4 RTD Settings.
gnitteSrepmuJDTR4H 001tP1
0001tP 0
Note 1. The H4 jumper affects ALL RTD
channels.
Note 2. The appropriate RTD must be
selected in the Scada software.
sgnitteSrepmuJSMMOC locotorP 1L 2L 3L 4L
DTS232SR0010
OIDAR232SR 1 0 0 0
224SR1100
584SR 0 0 1 1
Linking for RS422
Linking for RS485
L1 L3
L2 L4
.
.
L1 L3
L2 L4
.
.

14.02-8
Section C. Input and Output Connection Diagrams.
2100-A16 Input Connection Diagram for mA Inputs.
Connection configuration for 2 wire, 3 wire and 4 wire transmitters, and digital inputs.
Connection Example 1.
+
Output
-
3-wire
Transmitter
+
-
2-wire
Transmitter
+
-
4-wire
Transmitter
Power
Supply
24Vdc Regulated
Power
+ Supply. -
Voltage Free
Contact
+
Channel 1
-
+
Channel 2
-
+
Channel 3
-
+
Channel 4
-
2100-A16
1k
Current Output
Field Transmitters Note 1. All 2100-A16 analogue inputs are
differential. Exceeding 18V peak between
any 2 inputs, or any single input will cause
errors on ALL channels.
In example 2, the peak voltage is
calculated by multiplying the max mA out
of any transmitter, by the sum of the
resistances in the transmitter loop, then
adding any common peak voltages.
eg:(refer to Connection Example 2)
If the transmitter has a 35mA max, the
2100-A16 has 25input resistance; and if
achart recorder has250inputresistance:
There is a 2V peak common voltage.
=>35mAx(25+ 250) +2V = 11.63V peak.
This is fine, as it is less than 18V.
Note 2. For mAinputs a jumper must be installed.
Failure to install a jumper will cause errors
onALL channels. J1 for channel 1, J2 for
channel 2, etc. The jumpers are located
directly behind the 3 terminals for each
respective channel. They can be installed
without removing the cover.
Note 3. Inputs can be used as digital inputs for
sensing a clean, voltage free, field contact.
Note 4. All cables must be screened, and the
screens earthed at one end only.
Note 5. Voltage freecontactvaluesmustbebrought
in through ‘tags’in the Scada Software.
1
2
4
5
7
8
10
11
Connection Example 2.
+
Output
-
3-wire
Transmitter
+
-
2-wire
Transmitter
+
-
4-wire
Transmitter
Power
Supply
24Vdc Regulated
Power
+ Supply. -
+
Channel 1
-
+
Channel 2
-
+
Channel 3
-
2100-A16
Current Output
Field Transmitters
1
2
4
5
7
8
+ Channel 3
+ Channel 2
+ Channel 1
-Common
eg Single Ended Chart
Recorder.
All negative inputs are
connected together.
Channel1
Channel2
Channel3
2100-A16 Input Connection Diagram for Millivoltage and Voltage Inputs.
Connection configuration for 3 wire and 4 wire transmitters, and digital inputs.
+
Output
-
3-wire
Transmitter
+
Output
-
3-wire
Transmitter
+
-
4-wire
Transmitter
+
-
4-wire
Transmitter
Power
Supply
Power
Supply
24Vdc Regulated
Power Supply.
+ -
+
Channel 1
-
+
Channel 2
-
+
Channel 3
-
+
Channel 4
-
+
Channel 5
-
+
Channel 6
-
2100-A16
Field
Transmitters Note 1. All millivolt and volt inputs are differential.
Exceeding 18V peak between any 2 inputs,
or any single input will cause errors onALL
channels.
Note 2. Inputs can be used as digital inputs for
sensing a clean, voltage free, field contact.
Note 3. Allcablesmustbescreened,andthescreens
earthed at one end only.
Note 4. Input voltages must not exceed 18V.
Note 5. For digital inputs the mA jumper must be
installed.
Note 6. Voltage free contact values must be brought
in through ‘tags’ in the Scada Software.
Voltage Free
Contact
Voltage Free
Contact
1
2
4
5
7
8
10
11
13
14
16
17
1k
1k

14.02-9
2100-A16 Input Connection Diagram for RTD Inputs.
Voltage Free
Contact
Voltage Free
Contact
A
BChannel 1
B
A
BChannel 2
B
A
BChannel 3
B
A
BChannel 4
B
A
BChannel 5
B
2100-A16
3-Wire Field RTD
Internally
connected
1
2
3
4
5
6
7
8
9
10
11
12
13
14
15
2100-A16 Input Connection Diagram for Thermocouple (T/C) Inputs.
+
Channel 1
-
+
Channel 2
-
+
Channel 3
-
2100-A16
Field
Thermocouples
1
2
4
5
7
8
2-Wire Field RTD
3-Wire Field RTD
Note 1. AllT/C inputs are differential.Exceeding18V peak between
any 2 inputs, or any single input will cause errors onALL channels.
Note 2. It is recommended that theT/C’sbeisolatedfromeachother
and earth. Isolated junction, mineral insulated T/C’s are recommended.
Note 3. For accurate T/C measurement, especially low temp: *The
cover must be fitted. *Avoid drafts and temperature differences across
terminals. *Once installation is complete, close the cabinet door and allow
the cabinet to reach equilibrium. This may take several hours. *Place all
theT/Cprobesintoacalibrated thermal bath attemperatureofinterest.
Any errors can be zeroed out in software.
Note 4. All T/C’s are referenced to the on board cold junction
compensation(CJC)temperaturesensor. PriortoRev 1.3theCJC sensor
islocatedbehindterminal24.FromRev1.3onwardstheCJCtemperature
sensor is locatedbehind terminal1. Alternativelyone of inputs 1 to 8 can
be selected in the Scada software as an RTD CJC for inputs 1 to 8,
and one of inputs 9 to 16 can be selected in the Scada software as an
RTDCJC for inputs9 to16.Themounting orientationof the 2100-A16,
(eg vertical or horizontal) affects the CJC accuracy of different inputs.
The affects are more noticeable on small temperature ranges. For
examplemountingthe2100-A16horizontalwill cause the all the upper
terminals to be warmer compared to all the the lower terminals. Any
errors can be zeroed out in software.
Note 5. Cables must be screened & screens earthed at one end only.
Note 1. All RTD inputs are single ended. ie all the
2nd ‘B’ terminals are internally connected.
Note 2. It is recommended that theRTDsbe isolated
from each other and earth.
Note 3. Inputs can be used as digital inputs for
sensing a clean, voltage free, field contact.
Note 4. All RTD cables must be screened, and the
screensearthed at oneendonly.All thethree
wires must be the same resistance. (ie. the
same type and size.) Refer to ‘Wiring and
Installation’for recommended types.
Note 5. To minimise lead resistance errors, 3 wire
RTDs should be used. If 2 wire RTDs are
usedsmall offseterrorscan be compensated
for in software.
Note 6. For voltage free contactsuse RTD60 to 850
forpseudodigitalinputintheScadaSoftware.
* Refer to Wiring & Installation.
2100-A16 Input Connection Diagram Thermocouple Upscale (US) / Downscale (DS) Drive.
To achieve US or DS drive on T/C open circuit resistors must be fitted externally, as shown below.
UPSCALE DOWNSCALE
+
20Vdc
-
+
Channel 1
-
+
Channel 2
-
+
Channel 3
-
2100-A16
Field
Thermocouples
49
48
1
2
4
5
7
8
3k3
220
10M
10M
10M
+
20Vdc
-
+
Channel 1
-
+
Channel 2
-
+
Channel 3
-
2100-A16
Field
Thermocouples
3k3
220
10M
10M
10M
49
48
1
2
4
5
7
8
For US drive: Fit 10Mresistors to +ve terminals. For DS drive: Fit 10Mresistors to -ve terminals.
Refer to Wiring and Installation. Refer to Wiring and Installation.

14.02-10
Note 1. Inputs can be:
State - i.e. ON or OFF.
Count - 0~50Hz
Note 2. LEDindicationper input. LED intensity depends
on voltage level at the input terminals. Refer to
‘Specifications’ for input loads.
Note 3. For scaling of counter inputs, totalising and flow
data conversion, refer to Microscan Configuration
Manual, line setup/counter scaling.
Note 4. Allcables mustbescreened,with screenearthed
atone end only. Refer‘The Proper Installation&
Wiring of the 2100-A16.’
Note 5. Do not fit the 4K7 resistor for 3 wire PNP
transducers.
Note 6. DigitalInputs arenot available when usedas an
intelligentmultiplexer.
2100-A16 Connection Example Diagram for Digital Inputs.
2100-A16
DI4 58
DI 3 57
DI 2 56
DI 1 55
DI COM 54
24Vdc
3 wire proximity transducer,
paddle wheel, etc.
4.7ko/p
Digital Output
5~30Vdc
Open Collector
Reed Switch or
Relay contact.
Note 1. Both relays are Normally Open, and share a common.
Note 2. 30Vac/dc, 1Amaximum contact rating. For individual relay outputs
(ie not sharing a common) and/or a contact rating of 250Vac, use a
2100-RL2.This is a 2 relay slave board that can be wired directly to
the2100-A16.
Note 3. Each relaycan beconfigured for a‘Normally ON’or ‘Normally OFF’
output state. (E.g. for fail safe operation.)The ‘Normally ON/OFF’
settings are retained in software on power down, but the relays are
de-energized.Refer to MicroScan Configuration Manual.
Note 4. Relay 2 can be selected as a Comms failure time-out alarm. The
relayisnormally active and deactivates after5mins if no Comms
messages are received. This function does not detect
microprocessor failure. When used for this function the relay
cannot be used for any other function.
Note 5. LED indication on each output when relay is energized.
Note 6. For additional Relay Expansion refer 2100-R2.
Note 7. Digital Outputs are not available when used as an intelligent
multiplexer.
2100-A16 Connection Example Diagram for Digital Outputs.
2100-A16 Connection Diagram Using an XI-P1 Current Loop Isolator on the Input.
2100-A16 Connection Diagram Using an LPI-D Current Loop Isolator on the Input.
2100-A16
50
51
52
Relay 1
Relay 2
P/S
Audible
Alarm
COOLING
12
12
12
12
12
12
+
Analogue Input
-
1
2
2100-M
24Vdc Regulated
Power Supply.
+ -
LPI-D
+ 4
2 - - 5
1 +
4~20mAloop
COM 51
Analogue Output
Iout 53
4~20mAloop
2100-A16
2kV Isolation Barrier
+
Analogue Input
-
1
2
2100-M
4~20mAloop
COM 51
Analogue Output
Iout 53 4~20mAloop
2100-A16
1kV Isolation Barrier
XI-P1
Input Output
- + - +
4 3 2 1
Input
Output

Section D. Connecting to a Microscan Scada System.
2100-A16 Analogue Input Expansion - Using 2100-M Analogue Input Multiplexer.
Analogue input expansion can be achieved using up to four 2100-M, 16 Channel, Analogue Input Multiplexers. This
gives a total of 76 analogue inputs. Control for the 2100-M is through theAO1 andAO2 on the 2100-A16. (Refer Note
4below.) One analogue input is requiredper2100-M, and each 2100-M input mustbeof the same type and range.The
remaining 2100-A16 analogue inputs can be used for any other type of input.
Option 1. 5 Wire Connection Diagram.
This uses 5 wires for the first 2100-M, with 2 additional wires for each additional 2100-M. In this configuration the
analogue inputs are differential. The maximum peak input voltage is 18V.
-
Analogue Input No.1
+
-
Analogue Input No.2
+
-
Analogue Input No.3
+
-
Analogue Input No.4
+
Third
2100-M
Note 1. The 2100-A16 resolution on 2100-M
multiplexer inputs is 12 bits (4096 steps)
Note 2. All cables must be screened, and the screens
earthed at one end only.
Note 3. Analogue Input expansion is also possible
using the EXPO-3. Refer to the connection
diagram below.
Note 4. When 2100-M multiplexers are used:
AO COM connects to CS COM;
AO 1 is used for the RESET pulse;
AO 2 is used for the CLOCK pulse.
AO1&AO2arenotavailableforanyotheruse.
51 COM
53 Iout
60 CS COM
61 RESET
62 CLOCK
51 COM
53 Iout
60 CS COM
61 RESET
62 CLOCK
2100-A16
Second
2100-M
51 COM
53 Iout
60 CS COM
61 RESET
62 CLOCK
First
2100-M
AO COM 60
AO 1 61
AO 2 62
2
1
5
4
8
7
Fourth
2100-M
51 COM
53 Iout
60 CS COM
61 RESET
62 CLOCK
11
10
EXPO-3
26 COM
28 Iout
29 CS COM
30 RESET
31 CLOCK
OR
The analogue output mode is set in the StationAdvanced Dialog Box ‘AO 1 & AO 2 button’.
For 2100-M Driver select Mode 1.
For detailed programming info, refer to ‘Programming 2100-Series Remote Station’in the Microscan Manual.
14.02-11
Option 2. 4 Wire Connection Diagram.
Thisuses4 wires (2 pair)forthefirst 2100-M, with 1 additional wireforeach additional 2100-M. In this configurationthe
analogue inputs single ended. i.e.All the -ve inputs are all commoned.
-
Analogue Input No.1
+
-
Analogue Input No.2
+
-
Analogue Input No.3
+
-
Analogue Input No.4
+
Third
2100-M
Note 1. The 2100-A16 resolution on 2100-M
multiplexer inputs is 12 bits (4096 steps)
Note 2. All cables must be screened, and the screens
earthed at one end only.
Note 3. Analogue Input expansion is also possible
using the EXPO-3. Refer to the connection
diagram below.
Note 4. When 2100-M multiplexers are used:
AO COM connects to CS COM;
AO 1 is used for the RESET pulse;
AO 2 is used for the CLOCK pulse.
AO1&AO2arenotavailableforanyotheruse.
51 COM
53 Iout
60 CS COM
61 RESET
62 CLOCK
51 COM
53 Iout
60 CS COM
61 RESET
62 CLOCK
2100-A16
Second
2100-M
51 COM
53 Iout
60 CS COM
61 RESET
62 CLOCK
First
2100-M
AO COM 60
AO 1 61
AO 2 62
2
1
5
4
8
7
Fourth
2100-M
51 COM
53 Iout
60 CS COM
61 RESET
62 CLOCK
11
10
EXPO-3
26 COM
28 Iout
29 CS COM
30 RESET
31 CLOCK
OR
The analogue output mode is set in the StationAdvanced Dialog Box ‘AO 1 & AO 2 button’.
For 2100-M Driver select Mode 1.
For detailed programming info, refer to ‘Programming 2100-Series Remote Station’in the Microscan Manual.

Connecting the 2100-A16 to the 2100-ME.
1/ Only fit 2100-ME-32 to 2100-A16 Rev.1.3.
2/ Power must be off before installing the 2100-ME.
3/ Remove the cover off the 2100-A16.
4/ Use antistatic precautions when installing the 2100-ME.
Carefully orientate the 2100-ME board as shown above.
Locatethetwoplasticstand-offsoverthecorrespondingholes
inthe 2100-A16, andthe10pin connector. Onceallthreeare
aligned, push the 2100-ME firmly into the 2100-A16.
5/ Installalinkinposition4ofthe 2100-A16 S1Functionjumper.
6/ Replace the 2100-A16 cover.
7/ When the 2100-A16 is used with the 2100-ME, the 2100-M
and 2100-R expansion options are unavailable.
8/ The 2100-ME can only be fitted to a 2100-A16 REV 1.3.
2100-A16 Memory Expansion - Using 2100-ME Memory Expansion Card.
The2100-MEMemory ExpansionCardis designed to allow the 2100A16 to stand alone, retaining the datacollected for
intermittent download. Data is held in permanent memory.
.
2100-ME
CAUTION: Dangerous Voltages may be present. The 2100-A16 has no user serviceable parts.
Protective enclosure only to be opened by qualified personnel.
Remove ALL power sources before removing protective cover.
14.02-12
2100-A16 Connection Example Diagram for Using the 2100-RL2, 2 Relay Slave Board.
2100-A16
Relay 2 52
Relay 1 51
COM 50
20Vdc 49
0V 48
2100-RL2
52
51
50
49
48
NC
Relay 1 COM
NO
NC
Relay 2 COM
NO
2100-RL2 Relay Specifications:
-Contact Material SilverAlloy
-RelayRatings Rating Approved
250Vac, 2A UL
125Vac, 2A CSA
110Vdc, 0.3A;
30Vdc, 2A;
250Vac,1/6hp;
125Vac, 1/10hp.
-Number of Operations 2 x 105Min, at 1A, 250Vac
Note 1. Activating Relay 1 on the 2100-A16 activates
Relay1onthe2100-RL2.Activating Relay 2 on
the2100A16activatesRelay 2 onthe2100-RL2.
2100-A16 Analogue Outputs Controlled by Scada.
The analogue output mode is set in the StationAdvanced Dialog Box ‘AO 1 & AO 2 button’.
For Scada outputs select Mode 2.
For detailed programming info, refer to ‘Programming 2100-Series Remote Station’ in the Microscan Manual.
AO 1 & AO 2 are controlled by the Scada Software.
12 bit output nominally = 0~4095 for 4~20mA (or 0~10V etc.) out:
0bit = 4mA (0V);
2048 = 12mA (5V);
4095 = 20mA (10V).
For 4~20mA output, Loop Powered Indicators can
be used. 12V maximum at 20mA (600at 20mA)
2100-A16
62
61
60
AO 2
AO 1
AO COM
INDICATOR
INDICATOR

14.02-13
Connecting the 2100-A16 to the 2100-R2.
1/ Power must be off before installing the 10 way ribbon cable and 2100-ARI board
supplied with the 2100-R2.
2/ Remove the cover off the 2100-A16.
3/ An exchange cover, with a precut slot for the ribbon cable, is available free of
charge from your supplier. P/N: 2100-A16-COVERSLOT.
Alternatively you may wish to modify the existing cover:
Cut a 1mm slot, 20mm deep, just below terminal numbers 1, 2 & 3.
Carefully smooth the edges of the cut so the ribbon cable does not get damaged.
4/ The 2100-ARI is supplied with the ribbon cable attached. Use antistatic precautions
when installing. Carefully orientate the 2100-ARI board as shown above. Locate the
two plastic standoffs over the corresponding holes in the 2100-A16, and the 10 pin
connector. Once all three are aligned, push the 2100-ARI firmly into the 2100-A16.
5/ Connect the other end of the cable to the 2100-R2. Ensure both ends of the cable are firmly connected.
6/ Slide the cable into the slot, and replace the cover on the 2100-A16.
7/ The2100-R2 must beenabledintheprogramming dialogueboxes.Advanced ‘2100-R 2RelayExpander’options.
For detailed programming info, refer to
‘Programming 2100-Series Remote Station’in the Microscan Manual.
8/ A 2100-R2 connected to the 2100-A16 must share the same power supply disconnect device and over current
device. Both units must be powered and unpowered at the same time to prevent indeterminate relay states.
2100-A16 Rev1.3 Relay Output Expansion - Using 2100-R2 Relay Expansion.
Output relay expansion is available using the 2100-R2, 16 relay output expansion module. This allows the 2100-A16 to
stand alone as a 16 channel controller / alarm unit. The 2100-R2 relay outputs can be used for any combination of
control and alarm functions. The control parameters for each of the 16 controllers is downloaded from user friendly
Microscan Software, and stored in permanent memory on the 2100-A16. These parameters include Setpoint (SV),
Output Switching Differential,Auto / Manual, Manual Output Setting, DualAction Control, SingleAction Control, Heat /
Cool, Heat Only, Cool Only. The 16 controller / alarms will operate unaffected by computer power downs, reboots, etc.
The relay outputs can also be accessed directly from the Scada.
A B B
INPUT 2
A B B
INPUT 1
1 2 3 4 5 6
1x20mm
SLOT
..
H2 A16
Interface
H3 2ND
2100-R2
H2 A16
Interface
H3 2ND
2100-R2
2100-R2Relay Expander2100-R2Relay Expander
2100-R2Relay Expander2100-R2Relay Expander
2100-R2Relay Expander
Serial No.Serial No.
Serial No.Serial No.
Serial No. 2100-ARI
2100-A16-R1.3
WARNING: The2100-ARIisSTATIC SENSITIVE.
Only touch the edges of the PCB.
Ensurestandoffslockfirmlyinto the2100-A16 board.
2100-R2Relay Expander2100-R2Relay Expander
2100-R2Relay Expander2100-R2Relay Expander
2100-R2Relay Expander
Serial No.Serial No.
Serial No.Serial No.
Serial No.
FIRST 2100-R2
SECOND 2100-R2

14.02-14
OUTSTATION LAYOUT. OUTSTATION LAYOUT.
2-Wire RS485 Serial Connections. 4-Wire RS422 Serial Connections.
4
6
3
9
5
Shimaden FP21
with RS422 option
4
6
3
9
5
Shimaden SR25/253
with RS422 option
25
24
23
22
21
Shimaden SR53/54
with RS422 option
5
4
3
2
1
ShimadenSR73A/74A
with RS422 option
To other INTECH MICRO Remote
Stations & Shimaden Controllers etc.
End of Data
Hi-way
Junction Box.
TWISTED
PAIR
IN-2000-AI
Remote Station.
2100-AO
Remote Station.
IN-2000-DI
Remote Station.
2100-A4
Remote Station.
21
20
23
22
36
35
38
37
70
71
72
73
74
2100-D
Remote Station.
70
71
72
73
74
IN-2000-DO
Remote Station.
26
25
28
27
21
22
1
Shimaden SD20
with RS485 option.
23
22
21
Shimaden SR53/54
with RS485 option.
3
2
1
Shimaden SR73A/74A
with RS485 option.
To other INTECH MICRO
Remote Stations &
Shimaden Controllers etc.
Resistor = 1k
.
2100-A16
Remote Station.
2100-A4
Remote Station.
2100-AO
Remote Station.
70
71
74
70
71
74
70
71
74
Notes:
(i) RS485 can only be used with software release Ver. 4.02 onwards.
(ii) RS485DataHi-wayisnot compatiblewithRS422 DataHi-way devices
such as IN-2000-AI, IN-2000-AO, IN-2000-DI, IN-2000-DO, FP21,
SR25, etc. Use a 2100-4S to interface an RS485 Data Hi-way to an
existing RS422 Data Hi-way
RS232:2100-IS convertor is not required to connect the 2100-232
directly to a PC. Use the RS232 kit to connect the 2100-232
directly to a PC. The PC requires one RS232 port per 2100.
RS485: IftheoutstationisusingRS485, itcannotbe connectedtothesame
data hi-way as an outstations using RS422. In the ‘programming’
box, set the ‘TX delay’ box to 20. Set the Dip switches on the
2100-IS and the jumpers on the 2100 for RS485 operation.
24
23
21
22
1
Shimaden SD20
with RS422 option
3
9
5
Shimaden SR253
with RS485 option.
2100-A16
Remote Station.
70
71
72
73
74
IMPORTANT:
(i) All cables must be
screened.
(ii) All screens must
be connected
together.
(iii) The screen must
not be earthed at
any point.
IMPORTANT:
(i) All cables must be
screened.
(ii) All screens must
be connected
together.
(iii) The screen must
not be earthed at
any point.
2100-D
Remote Station.
70
71
74
70
71
72
73
74
DO NOT GUESS TX OR RX CONNECTIONS. FOLLOW THE TERMINAL NUMBERS IN THE SERIAL CONNECTION DIAGRAMS EXACTLY.
-
+
SG
Shimaden SR80 Series
with RS485 option.
Shimaden SR90 Series
with RS485 option.
SR82
18
17
16
SR83
25
24
23
SR84
22
21
1
-
+
SG
SR91
12
11
1
SR92,93,94
3
2
1
Resistor = 1k
.
TWISTED
PAIR
TWISTED
PAIR
TWISTED
PAIR
TWISTED
PAIR
TWISTED
PAIR
End of Data
Hi-way
Junction Box.
74 71 70 Terminal Numbers
COM TX+ TX-
RS485 DATA HI-WAY.
CABLE POLARITY
MUST BE OBSERVED RS422 DATA HI-WAY.
CABLE POLARITY
MUST BE OBSERVED
RS485 DATA HI-WAY.
CABLE POLARITY
MUST BE OBSERVED
RS422 DATA HI-WAY.
CABLE POLARITY
MUST BE OBSERVED
74 73 72 71 70 Terminal Numbers
com RX+ RX- TX+ TX-
74 71 70
COM TX+ TX- 74 73 72 71 70
com RX+ RX- TX+ TX-
2100-NET
10/100 Ethernet to
RS422/485Converter.
COMPUTER PLC
2100-IS/NS
RS232 to RS422/485
Converter/Isolator.
2100-NET
10/100 Ethernet to
RS422/485Converter.
RS232
ETHERNET
COMPUTER PLC
2100-IS/NS
RS232 to RS422/485
Converter/Isolator.
The2100-IS and 2100-NETare
designedto connect toseperate data
hi-ways and connect to the same
SCADA PC as per the diagram.
RS232
ETHERNET
The2100-IS and 2100-NETare
designedto connect toseperate data
hi-ways and connect to the same
SCADA PC as per the diagram.
70
71
72
73
74
2100-4S RS422
to RS485 Converter
70
71
74
RS485
Only one converter to be
connected to any one data hiway.
OR
Only one converter to be
connected to any one data hiway.
OR

14.02-15
2100-A16 RS232 Serial Connection.
The 2100-A16 with RS232 comes complete with:
zz
zz
z1 x 5m RJ11 RS232 Cable. (2, 10 & 15m available.)
zz
zz
z1 x 9 Pin D-type Connector. (25 pin D-type available.)
zz
zz
zUSB to RS232 convertor available. Part No. BF-810.
Location of RJ11 Socket on 2100-A16 Series.
2100-RS232 Kit-Omron
RS232 Kit for Omron PLC. Includes 2m cable & 9 pin D-type connector.
Installation.
Plug one end of the RS232 Comms cable into the RS232 RJ11
Socketonthe2100Module.Plugtheotherendintoeitherthe9or
25pin D-typeconnector.(CheckforthecorrectD-typeconnector
on the computer (or Omron PLC) RS232 port being used.) For
furthersoftwareandhardwareinformation,RefertotheMicroscan
Manual ‘Programming the 2100 Series Remote Station.’
2100-A16 RS232 Radio Modem Serial Connection.
Note: The ‘2100-RS232-Radio’ 9 pin D connector differs from the
2100-RS232 9 pin D supplied, and must be ordered separately.
It can be exchanged at no charge for the 9 pin and 25 pin D
connectors supplied with the 2100-RS232 Remote Station.
1. Refer to Installation paragraph above.
2. Fit the ‘2100-RS232-Radio’ 9 pin D connector between the
Radio end of the RS232 comms cable, and the Radio. This
connector will work with most types of radio, but this is not
guaranteed. Pin2=TX; Pin3=RX; Pin5=GND; Pin7=RTS.
3. Refer to ‘H2 Comms Settings.’ to jumper as per RS232 Radio.
4. Referto radio manual for hardware handshaking settings for TX control. TXE & TX delay may need to bealtered
intheScadaStationAdvancedDialogboxtosuittheradio.BestcaseTXspeedisonetransmissionpersecond.
(Depends on Radio.) Default settings are: TXE = 25ms; TX = 0ms.
5. Ifusingmorethanonestationataremoteradiosite,2100-RS422RemoteStationswitha2100-ISwithanadaptor
kit must be used. (Do not use 2100-RS485.) Refer to 2100-IS installation Guide.
2100-A16 Station Number Programming and Serial Number.
Important: When commissioning remote stations, you must programme a unique station number before using the
programme setup button in the Scada Software. Requires Microscan Version 4.02 onwards.
For detailed programming info, refer to ‘Programming 2100-Series Remote Station’in the Microscan Manual.
1. ClosetheMicroscanScadadownandturnthepowerofftothe2100422/485converter.ConnectthenewRemote
Station, referring to ‘Wiring and Installation’ and ‘Commissioning’
2. Turn power back on to the 2100 422/485 converter, and start the ‘Setup Manager’ in the Microscan Scada.
3. Select ‘Recorder Setup’, or ‘Tag Setup’.
4. Select ’Program Address’. (Located in ‘Station Programming Panel’, at the bottom right of the window.
5. Enter the 2100-A16 serial number. (Written both on the 2100-A16 cover and the circuit board behind the power
supplyterminals.80, 81 & 82.Ifthecoverhas been removed, thenumberonthecircuit board is alwayscorrect.
Replace with the correct cover to avoid future confusion.) Then enter the desired station number.
6. Select ‘Program’. The station number will now be stored in 2100-A16 permanent memory.
7. A new station number will be created on the outstation map. This is ready for connection to tags or lines.
8. Restart the Microscan Scada.
2100-A16 Station Software Programming.
*Requires Microscan Version 4.02 onwards.
1. If the system is already running, close the Scada down. Start the ‘Setup Manager’.
2. Select ‘Recorder Setup’, or ‘Tag Setup’.
3. Move to the required station number, using ‘next’ or ‘prev’ buttons.
4. Select ‘Program Setup’. The serial number of the 2100-A16 will be recalled automatically. The software recalls
the settings from the outstation, and displays them in the dialogue box.
5. Enter the required options and select ‘Program’ to write the data to the station.
elbaTtuoniPSMMOC 11JR 9BD 52BD
STR:185
DNG:2 5 7
XT:323
STC:4 7 4
c/n:511
XR:6 3 2
RS232 COMMS Hardware.
10VA
50/60Hz
85~264Vac/dc
23~90Vdc
10~28Vac/dc
H
M
L
COMMS
RS232
RS422
RS485
Ph N E RS422/RS485 COMMS
COM TX TX RX RX
82 81 80 74 73 72 71 70 49 48 47
RS232 RJ11 Socket
Radio
RS232
2100-RS232
Remote station.
‘2100-RS232-Radio’
9 pin D-type connector.
Do Not cut RS232 Cable
to extend the length.

Section E. Connecting to a PLC.
Connecting to a PLC as an Intelligent Multiplexer.
To set up the 2100-A16 as an intelligent multiplexer a free software CD is available from Intech Instruments. Place the
CD into the drive and follow the instructions. The analogue output mode must be selected as either Mode 3 or Mode 4.
Thisis setintheStationAdvancedDialogBox‘AO 1&AO2button’.For detailedprogramming info,referto‘Programming
2100-Series Remote Station’ in the Microscan Manual.
14.02-16
)emit(stinUsyaleDSMMOC
locotorP yaleDEXT yaleDXT
oidartiusot-232SR)sm52(01)sm005~05(002~02
224SR )sm52(01 0
584SR)sm52(01)0
2100-A16 TXE and TX Delay Settings.
TheTXEandTXdelaysaresoftwareselectableintheMicroScanOutstationProgrammingBox.Thesedelaysareused
forRS485/RS232operation,tocontrolthebehaviourofthetransmitterontheoutstation,whenitisreadytosenddata.
TheTXEdelaycontrolshowlongthetransmitterwaitsbeforeturningon.TheTXdelaycontrolshowlongthetransmitter
waits before sending data. If the TXE delay is zero, the transmitter turns on immediately. If the TX delay is zero, the
data is sent immediately, upon receiving a command.
RX The period is specified in
TXE units of 2.5ms.
i.e. 10units = 25ms
TX TXE delay TX delay
2100-A16 Delay Settings Table.
Mode 3. 2100-A16 Clock and Reset Channel Selection Mode, PLC Installation Guide.
Mode 3. PLC RTX, CLOCK & RESET Channel Select.
DI COM = CS COM
DI 1 = RESET input.
DI 2 = CLOCK input.
Issue a RESET pulse to select channel 1.
Issue a CLOCK pulse to advance to the next channel.
Specifications.
Clocking speed -Reset pulse length 20msec.
-Clock pulse length 20msec.
Settling times before reading 100msec Min. Multiple readings with averaging recommended.
-Note. Longer times may be required for longer cable lengths and higher resolution.
Binary signal magnitude -All models 5~30Vdc.
Cycle TIme 4sec minimum to cycle through all 16 inputs.
Resolution 12bits, 4000 steps typical.
Sequence:
S R
{
{
S R
{
{
S R
{
{
S R
{
{
S R
{
{
S R
{
{
S R
{
{
S R
{
{
S R
{
{
Operation. Key: S = Settling time.
R = Read value.
Reset
Clock
Channel 1 2 3 4 5 15 16 1 2
Apply a Clock pulse to
advance multiplexer to
channel two.
Each clock advances
theMultiplexer
another channel
Multiplexeroutput
= channel one.
Apply a Reset pulse
to reset 2100-A16
intelligentmultiplexer.
Multiplexeroutput
= channel sixteen.
(Or highest channel
number used.)
Multiplexeroutput
= channel two.
Apply
power.
Note. All TXE and TX Delays are Software Selectable. The Factory Default TXE Setting is 10(25ms).

14.02-17
Notes
Note 1. '0' = No voltage on the terminal.
'1' = 5~30Vdc on the terminal.
Note2.Ensurethatiftheanalogueoutputfromeach2100-A16isfedintothesameunit(egPLC),thenitisrecommended
the analogue inputs to the PLC, etc, be isolated.
Note 3. AO 1 = retransmission of input process value 1~16.
AO 2 = retransmission of controller setpoints 1~16.
Note4.Theinputandoutputalwayssharethesamerange.Eg.Ifinput1isranged0~100Candretransmissionchannel
1 is selected on DI 1 ~ 4, then AO 1 & AO 2 are both transmitted as 4~20mA (or 0~10V etc) = 0~100C. Similarly
if input 2 is ranged for 0~250C, then AO 1 & AO 2 are transmitted as 0~250C.
Note 5. If AO 1 process value or AO 2 setpoint are transmitted to an indicator, then all the inputs must be ranged the
same, unless the indicator is ranged to 0~100%.
Note 6. In the PLC RTX modes,AO 2 always retransmits the controller setpoint regardless if the controller is enabled
or not.
Note 7. The PLC RTX modes can operate simultaneously with the Scada COMMS, allowing a PLC to read back data
that the Scada will be showing.
Note 8. Digital inputs and digital outputs are not available in this mode.
2100-A16 58
57
56
55
54
62
61
60
48
49
Bin
SWITCH
DI 4
DI 3
DI 2
DI 1
DI COM
AO 2
AO 1
AO COM
0V
20Vdc
INDICATOR
INDICATOR
Mode 4. 2100-A16 Binary Channel Selection Mode, PLC installation Guide.
Mode 4. PLC RTX, Bin Channel Select.
Bin channel selection is by digital inputs 1~4.
DI COM = CS COM
DI 1 = BIN 1.
DI 2 = BIN 2.
DI 3 = BIN 4.
DI 4 = BIN 8.
Specifications.
Settling times before reading -All models 100msec Min. Multiple readings with averaging recommended.
-Note. Longer times may be required for longer cable lengths and higher resolution.
Binary signal magnitude -All models 5~30Vdc.
Cycle TIme 4sec minimum to read all 16 inputs.
Resolution 12bits, 4000 steps typical.
2100-A16 Binary Channel Selection Mode Table.
noitceleSlennahCniB noissimsnarteR lennahC
1ID 1NIB 2ID 2NIB 3ID 4NIB 4ID 8NIB
0000 1
1 0 0 0 2
0100 3
1 1 0 0 4
0010 5
1 0 1 0 6
0110 7
1 1 1 0 8
0001 9
1 0 0 1 01
0101 11
1 1 0 1 21
0011 31
1 0 1 1 41
0111 51
1 1 1 1 61

14.02-18
Note 1. Usingthisconfiguration,upto four 2100-A16s
can be connected using Clock/Reset mode,
or 2 using Binary Channel Selection mode,
provided the open collector outputs can
handle the load.
Note 2. Each Digital input draws 8mAat 20Vdc.
Note 3. Allcables must bescreened,andthe screens
earthed at one end only.
Note 4. For Clock/Reset Channel Selection DO NOT
connect PLC outputs 3 and 4 to DI 3 and DI 4
of the 2100-A16.
Important: Do not use the 2100-A16 power supply to
powerupanytransmitterorotherequipment.Anexternal
power supply must be used for this purpose. The 20V
supply is for the 2100A16 Digital Inputs/Outputs only.
* For PLC RTX, CLOCK & RESET Channel Selection
refer to Section D, Mode 3.
* For PLC RTX, Bin Channel Selection refer to Section
D, Mode 4.
PLC Input
Module
-
Analogue Input No.1
+
-
Analogue Input No.2
+
-
Analogue Input No.3
+
-
+
-
+
-
+
-
+
PLC
Output
Module
(Note 4)
OpenCollector
OutputNo.1
OpenCollector
OutputNo.2
OpenCollector
OutputNo.3
OpenCollector
OutputNo.4
Connection Example 2.
Connectionof a 2100-A16 toa PLC with open collectors, commonedto the 20V of the first2100-A16 power supply.
First
2100-A16
49 20V
60 AO COM
61 AO 1
54 DI COM
55 DI 1
56 DI 2
57 DI 3
58 DI 4
Second
2100-A16
60 AO COM
61 AO 1
54 DI COM
55 DI 1
56 DI 2
57 DI 3
58 DI 4
Third
2100-A16
60 AO COM
61 AO 1
54 DI COM
55 DI 1
56 DI 2
57 DI 3
58 DI 4
2100-A16 Used as an Intelligent Multiplexer.
Connection Example 1.
Connection of a 2100-A16 to a PLC with open collectors, commoned to 24V of an external power supply.
PLC Input
Module
-
Analogue Input No.1
+
-
Analogue Input No.2
+
-
Analogue Input No.3
+
-
+
-
+
-
+
-
+
-
+
First
2100-A16
Note 1. Inthisconfiguration the2100-A16 DICOMand
Digital inputs are isolated from the 2100-A16
inputs and outputs. The 24V external power
supply can therefore be used to power
transmittersconnectedtothe2100-A16 inputs.
Note 2. There is no limit to the number of 2100-A16s
thatcanbeconnected,exceptthepowersupply
and open collector outputs must be able to
handle the load.
Note 3. Each digital input draws 10mAat 24Vdc.
Note 4. All cables must be screened, and the screens
earthed at one end only.
Note 5. For Clock/Reset Channel Selection DO NOT
connect PLC outputs 3 and 4 to DI 3 and DI 4
of the 2100-A16.
Important:Donotusethe2100-A16 powersupplytopower
upanytransmitterorotherequipment.Anexternalpower
supply must be used for this purpose. The 20V supply is
for the 2100A16 Digital Inputs/Outputs only.
* For PLC RTX, CLOCK & RESET Channel Selection
refer to Section D, Mode 3.
* For PLC RTX, Bin Channel Selection refer to Section
D, Mode 4.
24Vdc Regulated
Power Supply
PLC
Output
Module
(Note 5)
OpenCollector
OutputNo.1
OpenCollector
OutputNo.2
OpenCollector
OutputNo.3
OpenCollector
OutputNo.4
60 AO COM
61 AO 1
54 DI COM
55 DI 1
56 DI 2
57 DI 3
58 DI 4
Second
2100-A16
60 AO COM
61 AO 1
54 DI COM
55 DI 1
56 DI 2
57 DI 3
58 DI 4
Third
2100-A16
60 AO COM
61 AO 1
54 DI COM
55 DI 1
56 DI 2
57 DI 3
58 DI 4

-
Analogue Input No.1
+
-
Analogue Input No.2
+
-
Analogue Input No.3
+
-
+
-
+
-
+
-
+
-
+
Note 1. This configuration reverses the logic so when
thePLCdigitaloutputisoff,the 2100-A16 ison.
Note 2. With 1kresistor, up to four 2100-A16 can be
connected in this configuration, provided the
open collector outputs can handle the load.
Note 3. Each digital input draws 10mAat 24Vdc.
Note 4. All cables must be screened, and the screens
earthed at one end only.
Note 5. For Clock/Reset Channel Selection DO NOT
connect PLC outputs 3 and 4 to DI 3 and DI 4
of the 2100-A16.
Important: Do not use the 2100-A16 power supply to
powerupanytransmitterorotherequipment.Anexternal
power supply must be used for this purpose. The 20V
supply is for the 2100A16 Digital Inputs/Outputs only.
* For PLC RTX, CLOCK & RESET Channel Selection
refer to Section D, Mode 3.
* For PLC RTX, Bin Channel Selection refer to Section
D, Mode 4.
24Vdc Regulated
Power Supply
PLC
Output
Module
(Note 5)
OpenCollector
OutputNo.1
OpenCollector
OutputNo.2
OpenCollector
OutputNo.3
OpenCollector
OutputNo.4
PLC Input
Module
2100-A16 Used as an Intelligent Multiplexer.
Connection Example 3.
Connection of a 2100-A16 to a PLC with open collectors commoned to 0V of an external power supply.
1k1k1k1k
Note 1. This configuration reverses the logic so when
thePLCdigitaloutput is off, the 2100-A16 ison.
Note 2. For Clock/Reset Channel Selection the
resistors = 1k. Up to four 2100-A16 can be
connected in this configuration provided the
open collectors can handle the load. For
Binary Channel Selection the resistor =
2.2k.Uptotwo2100-A16 canbeconnected
in this configuration provided the open
collectors can handle the load.
Note 3. All cables must be screened, and the screens
earthed at one end only.
Note 4. For Clock/Reset Channel Selection DO NOT
connect PLC outputs 3 and 4 to DI 3 and DI 4
of the 2100-A16.
Important:Donotusethe2100-A16 powersupplytopower
upanytransmitterorotherequipment.Anexternalpower
supply must be used for this purpose. The 20V supply is
for the 2100A16 Digital Inputs/Outputs only.
* For PLC RTX, CLOCK & RESET Channel Selection
refer to Section D, Mode 3.
*ForPLC RTX,BinChannel Selection refer to Section
D, Mode 4.
PLC Input
Module
-
Analogue Input No.1
+
-
Analogue Input No.2
+
-
Analogue Input No.3
+
-
+
-
+
-
+
-
+
PLC
Output
Module
(Note 4)
OpenCollector
OutputNo.1
OpenCollector
OutputNo.2
OpenCollector
OutputNo.3
OpenCollector
OutputNo.4
2.2k2.2k2.2k
2.2k
Resistor Values refer Note 2.
Connection Example 4.
Connection of a 2100-A16 to a PLC with open collectors, commoned to the COM of the first 2100-A16.
First
2100-A16
60 AO COM
61 AO 1
54 DI COM
55 DI 1
56 DI 2
57 DI 3
58 DI 4
Second
2100-A16
60 AO COM
61 AO 1
54 DI COM
55 DI 1
56 DI 2
57 DI 3
58 DI 4
Third
2100-A16
60 AO COM
61 AO 1
54 DI COM
55 DI 1
56 DI 2
57 DI 3
58 DI 4
First
2100-A16
49 20V
60 AO COM
61 AO 1
54 DI COM
55 DI 1
56 DI 2
57 DI 3
58 DI 4
Second
2100-A16
60 AO COM
61 AO 1
54 DI COM
55 DI 1
56 DI 2
57 DI 3
58 DI 4
Third
2100-A16
60 AO COM
61 AO 1
54 DI COM
55 DI 1
56 DI 2
57 DI 3
58 DI 4
14.02-19

2100-A16 Analogue Signal Converted to Frequency for a PLC, using a TWI-FO.
Description.
The TWI-FO converts 4~20mA from a 2100-AO to a frequency output. (Typically 10~1010Hz, but this is rangeable.)
A PLC with two digital outputs and one digital input can receive sixteen multiplexed analogue inputs.
14.02-20
Section F. Communications.
2100-A16 ‘PLC Message’ Communication Protocol.
‘Read Only From 2100-A16’ and ‘Read and Write to 2100-A16’Protocols are both available from Intech Instruments in
‘WORD’ format, free of charge.
Read Message is PLC compatible read DM area. 2100-A16 protocol is the protocol used by Microscan to access data
in stations. Both protocols useASCII, except 2100-A16 uses IEEE754 to represent floating point numbers.
2100-A16 ‘Modbus RTU/TCP’ Communication Protocol.
Note 1: This section only applies to an 2100-A16 with Modbus RTU Protocol.
Note 2: Can be used on Modbus TCP with a Modbus TCP to RTU Bridge. ie Schneider Electric ‘174 CEV 300 20’.
Note 3: 2100-ME Memory Board cannot be used when Modbus RTU protocol is used.
Modbus RTU Comms Specifications:
Error Check Standard Modbus CRC.
End of message framing delay Min 5msec, Max 7.5msec. (Minimum spec is 3.5msec at 9600 baud).
Counting is based on internal 2.5 msec timer.
Product Liability. Due toongoingresearch and development,designs,specifications, and documentationaresubject to changewithoutnotification.
2100-A16 Rev. 1 PLC RTX Fail Safe System
The PLC uses one channel of the 2100-A16 to verify that theA16 is reading the channel correctly,AO1 is working and
the clock and reset/BCD channel select is working.
Test Channel = spare channel on 2100-A16, set to RTD 0-850C.This has a PLC relay connected which is used to short
out A-B, under the PLCs command. Do not use channel 1 as the test channel.
Sequence of operation.
1. The PLC reads the required channels as normal.
2. The PLC then advances to the test channel (the next free channel or channel 16)
3. The test channel is read.
4. The relay changes state to alter the reading of the test channel.
5. 1. to 4. are repeated. If the reading on the test channel does not alternate between 4 mA and 10 mA as the relay
changes state, within the specified tolerances as listed below then there is a fault in the system. The PLC software
should be setup to detect these values as the relay changes state.
etatSyaleR gnidaeRlennahCtseT eulaVtuptuO eulaVtseTCLP
desolC C51-nahtsseL Am4 .wolebdnaAm5roftseT
nepO C01-/+023xorppA Am01 .Am5.01wolebdnaAm5.9evobaroftseT
Eg. 2100-A16
20V
O/P 4~20mA
COM.
49
61
60
1
2
3
P/S2
F/O
COM2
4
5
6
eg. PLC
24Vdc
D/I
COM
1600V Isolation
TWI-FO
P/S1
I/P
COM1
PLC
Analog in -
Analog in +
COM
RST Out
CLK Out
Test relay
Clean Contacts,
Normally Open
60 AO COM
61 AO 1
54 DI COM
55 DI 1 (RST)
56 DI 2 (CLK)
220R
A Test Channel.
B(Eg.Channel 16)
B
46
47
48
2100-A16
Table of contents
Popular Multiplexer manuals by other brands
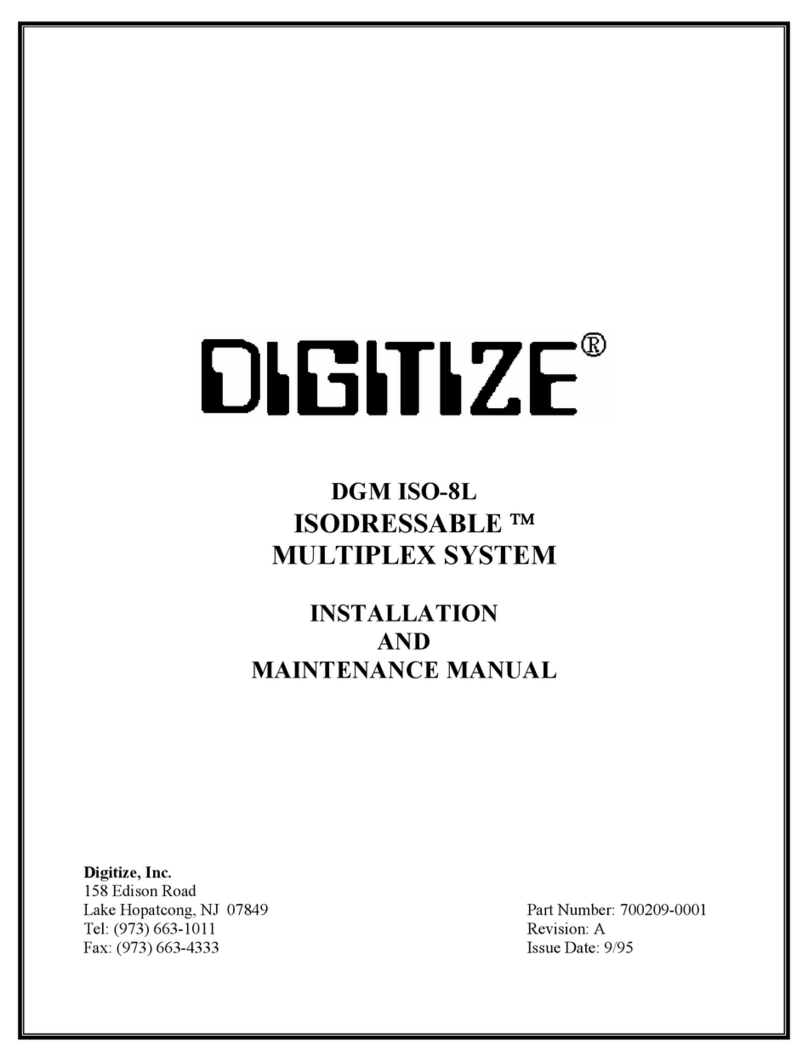
DIGITIZE
DIGITIZE ISODRESSABLE DGM ISO-8L Installation and maintenance manual
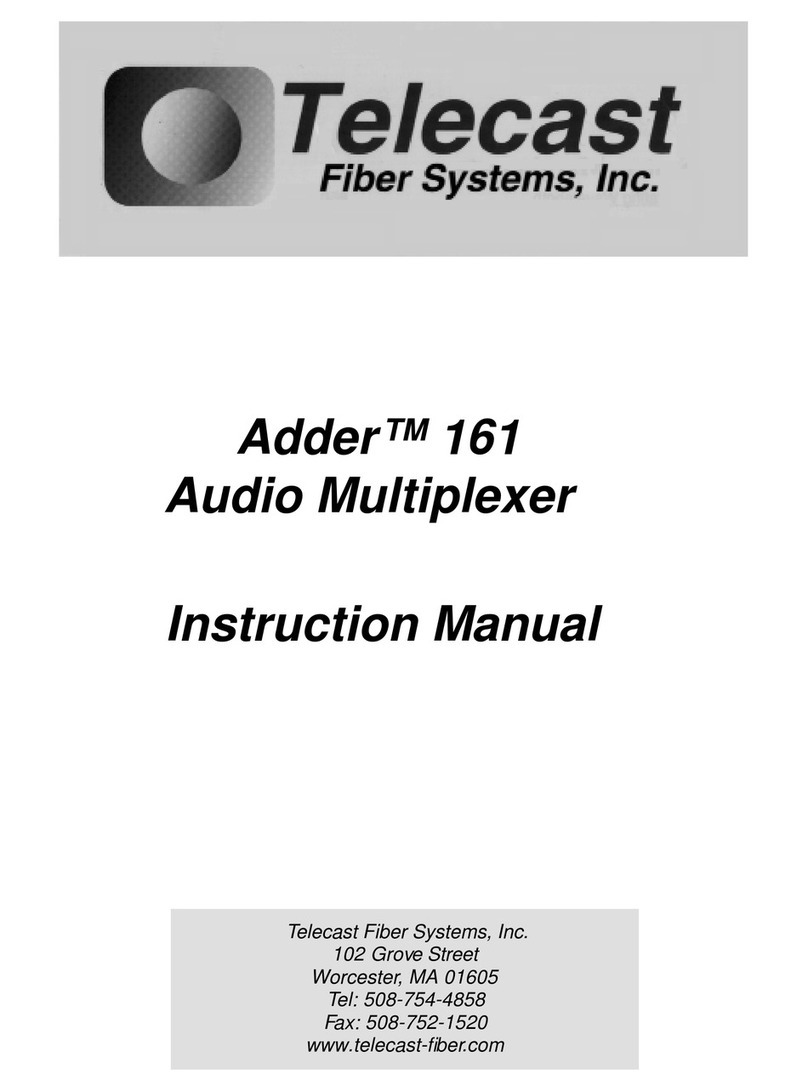
Telecast
Telecast Adder 161 instruction manual

Optostar
Optostar Fiber-30voice-4E1-4FE-4RS232 manual
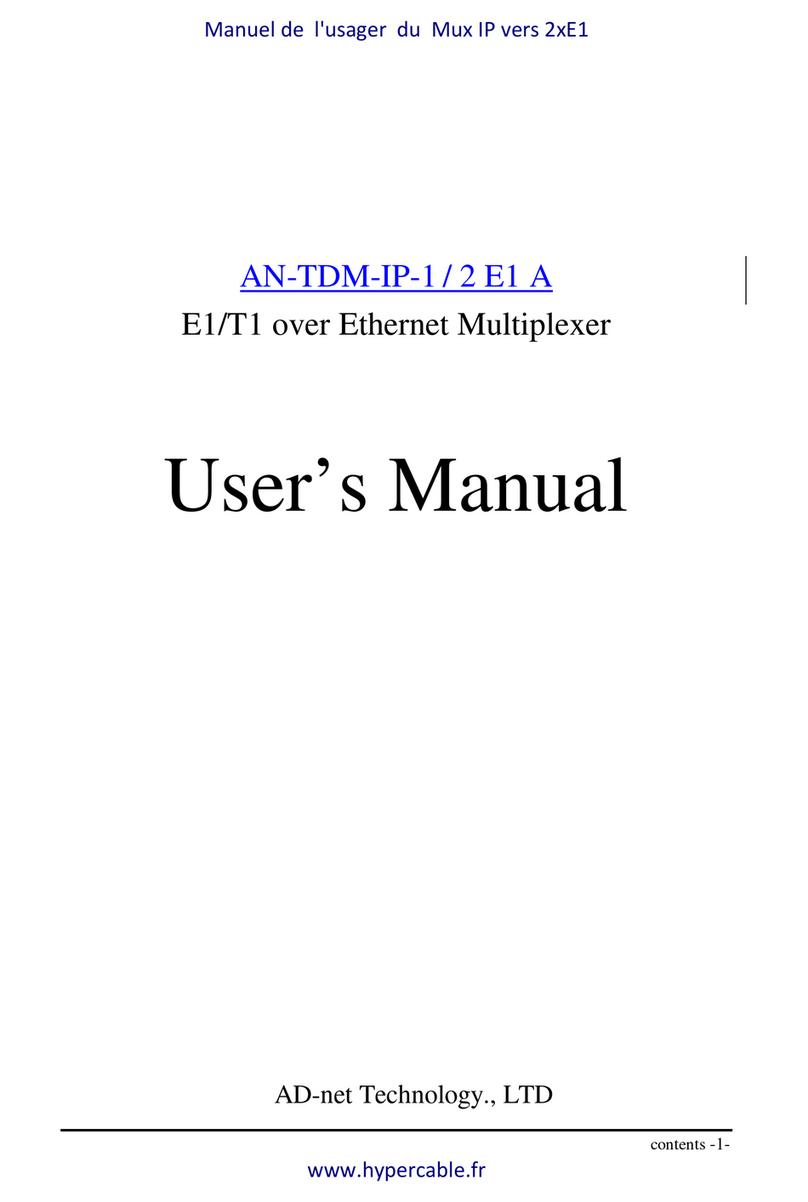
AD-net Technology
AD-net Technology AN-TDM-IP-1E1/2E1-A user manual
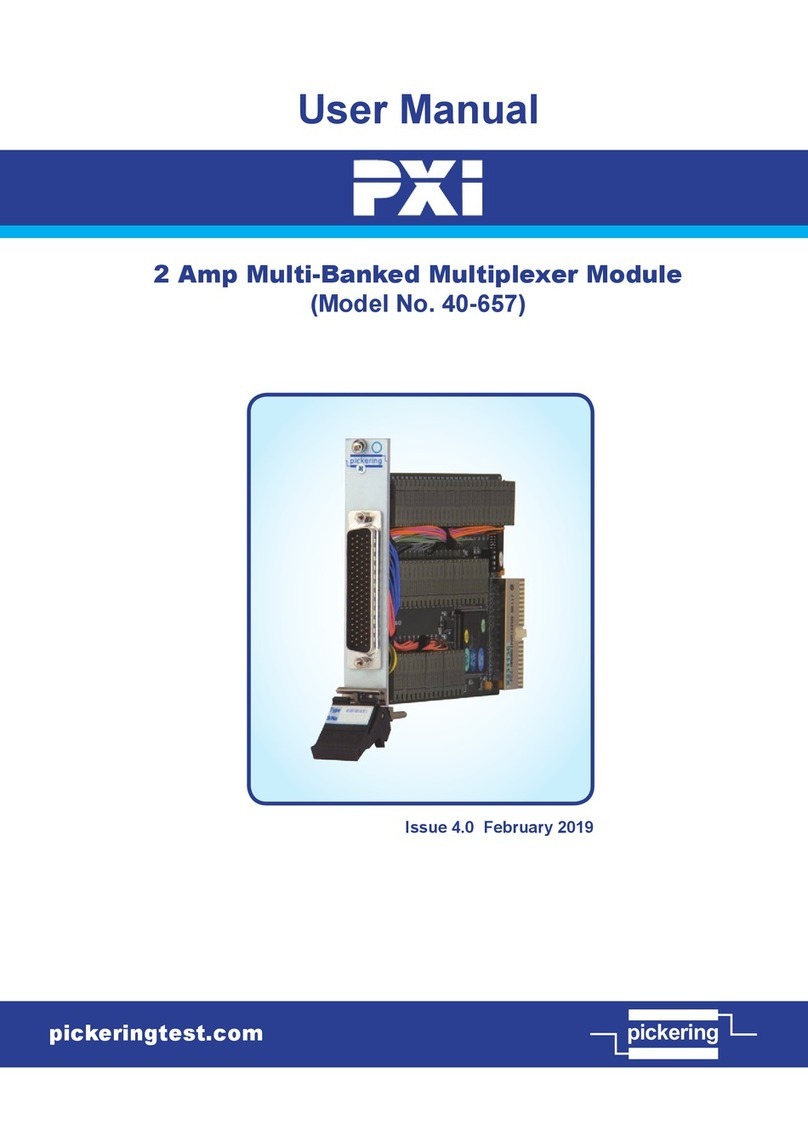
Pickering
Pickering 40-657 user manual
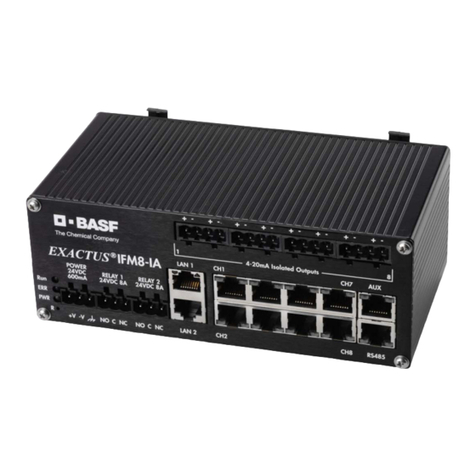
BASF
BASF EXACTUS IFM8-IA user guide