IPS Controllers M820 User manual

M820 pH/Dual ORP Controller
Owner’s
Manual

Table of Contents
I. Introduc on page 2
A. Water Chemistry page 2
B. Safety page 3
C. System Components page 4
D. Speci ca ons page 7
E. Controller Panel Descrip ons page 8
F. Electrical Descrip ons page 10
II. Installa on page 11
A. Setup page 11
B. Tools page 11
C. Procedure page 11
III. Opera on page 15
A. Overview page 15
B. Startup and Shutdown page 15
C. Modes and Adjustments page 17
D. Maintenance page 26
IV. Troubleshoo ng page 28
V. Warranty page 31
1

I. Introducon
A. Water Chemistry
Water chemistry is a complex science that contains many variables.
These variables not only aect the water environment itself, but
they can have adverse eects on your equipment as well as your
health. These are only some of the factors which we follow closely
to ensure the most healthy water interacons:
pH is the measurement of the acidity or basicity in an aqueous
soluon. A measurement below 7 is considered acid, while a
measurement above 7 is base or alkaline. It is a signicant factor
in determining the water quality as it aects sanizer levels, water
color, and human reacon to the water.
ORP (Oxidaon Reducon Potenal) is the measurement of the
oxidizing capacity present in water. ORP cannot be fooled by the
eects of pH, total dissolved solids (TDS), stabilizers, and non-
chlorine oxidizers. A typical ORP sensor measures Hypochlorous
Acid (HOCI), which is the more eecve component of free
chlorine. A higher ORP reading equates to the sanizer working
more eecvely.
Water balance is comprised of pH, calcium hardness, total
alkalinity, temperature, and TDS. When water is balanced, the
Langelier Saturaon Index is 0. Values above +0.3 lead to scaling
and cloudy water, while values below -0.3 can cause corrosion of
pool equipment and surfaces. If the water balance is not xed in
a mely manner, secondary eects can lead to rapidly declining
water condions that can aect the health of the water occupants.
pH and ORP work conversely to one another, and are aected by
other factors such as temperature, Cyanuric Acid, and TDS that can
increase the negave impacts of unbalanced water.
2
M820 pH/Dual ORP Controller Owner’s Manual

3
M820 pH/Dual ORP Controller Owner’s Manual
B. IMPORTANT SAFETY INSTRUCTIONS
1. READ AND FOLLOW ALL
INSTRUCTIONS.
2. Risk of electric shock: Connect the controller to a dedicated ground-
fault circuit interrupter (GFCI) circuit breaker.
a. A green colored terminal or a terminal marked G, GR, Ground,
Grounding, or the symbol* is located inside the supply
terminal box or compartment. To reduce the risk of electrical
shock, this terminal must be connected to the grounding means
provided in the electrical supply service panel with a connuous
copper wire equivalent in size to the circuit conductors
supplying this equipment.
*IEC Publicaon 417, Symbol 5019.
3. Disconnect power before servicing the controller.
4. Inspect all power cords frequently. Any damaged cords should be
replaced immediately to reduce the risk of injury by shock.
5. Always maintain a record of manual water chemistry readings using
an accurate test kit. Automated controllers are not a substute for
this Health Department requirement.
6. WARNING – To reduce the risk of injury, do not permit
children to use this product unless they are closely supervised at all
mes.
7. Danger – Risk of injury.
a. Replace damaged cord immediately.
b. Do not bury cord.
c. Connect to a grounded, grounding type receptacle only.
8. WARNING – Risk of electric shock. Install at least 5 feet
(1.5m) from inside wall of water enclosure using non-metallic
plumbing.
9. Operaon of this controller without a funconing ow-switch will
void the NSF Cercaon.
10. WARNING – Do not install this controller where it is
accessible to the public.
11. SAVE THESE INSTRUCTIONS.

C. System Components
1. IPS M820 pH/Dual ORP Controller
a. Allows automac monitoring of water sanizaon and pH
balance through a simple, user-friendly interface, resulng
in easier management of water balance in swimming
pools, spas, or circulang water environments.
b. Can be easily installed into your exisng pool environment
and equipment, or can be customized to your needs.
c. Monitors and displays the pH and ORP levels using LEDs
and digital readouts on the front panel. If the temperature
sensor is installed, the M820 will monitor temperature
and display on the front panel when in Temp mode.
Addionally, it will monitor up to two chemical tanks
equipped with level switches and displays status using LEDs
on the front panel.
There are six separate funcon buons allow simple
pushbuon control of these individual parameters:
1) Set Level – ORP or pH level to be maintained,
2) Dose Time – Timed or connuous feed modes,
3) Delay Time – Delay me between feed cycles,
4) Over Timer – Maximum feed cycles or me allowed,
5) High Alert – Maximum level of ORP or pH allowed,
6) Low Alert – Minimum level of ORP or pH allowed,
7) pH Cal – pH calibraon for variaon in pH sensors.
d. When the pH level rises above (acid feed) or falls below
(base feed) the set level, the controller will acvate the
chemical feeder for the set dose me. Then the set delay
me will occur. This dose and delay me will occur unl
the set level is reached.
e. When the ORP (sanizer) level reaches the set level, the
controller will acvate the chemical feeder for the set dose
me. Then the set delay me will occur. This dose and
delay me will occur unl the set level is reached.
4
M820 pH/Dual ORP Controller Owner’s Manual

2. Flow Cell with Flow Switch
a. An injecon-molded ow cell with integrated ow
switch houses the pH and ORP sensors, and partners with
the M820 controller to monitor the pH and ORP levels in
the water.
b. The ow switch veries that water is owing during a feed
cycle, and sends the controller instrucons to deacvate
the feed if water is not owing.
c. Operaon of this controller without a funconing ow-
switch will void the NSF Cercaon. Rounely check that
the ow-switch is funconing by closing the le valve on
the boom of the ow-cell (ow light should turn o).
3. pH and ORP Sensors
a. pH Sensor – standard (Use only IPS Controllers part # SXPH
to maintain NSF Cercaon)
b. ORP Planum Sensor – standard (Use only IPS Controllers
part # SXORP to maintain NSF Cercaon)
c. ORP Gold Sensor – for use with Salt Chlorine systems
(Use only IPS Controllers part # SXORP-G to maintain NSF
Cercaon)
4. Fings – tubing connectors (2) for tapping installaon of ow
cell input/output
5. In-line Filter with 2-way valves and mounng clamps (2)
6. Tubing – 25 feet of 3/8”
7. Mounng Board – ABS plasc with mounng holes and
stainless hardware (16” x 12” standard, 24” x 19” oponal for
mounng two chemical pumps)
8. Temperature Sensor – Senses the current water temperature
and displays the temperature in the display when in Temp
mode.
5
M820 pH/Dual ORP Controller Owner’s Manual

Figure 1: This is a typical installa on using IPS’ system package, which consists of an
M820 pH/dual ORP Controller, ow cell with switch, and two pumps mounted on the large board.
6
M820 pH/Dual ORP Controller Owner’s Manual
Chemical
Pump
Chemical
Pump
Flowcell (1)
Sucon Line
FLOW
FLOW
FLOW
Effluent
(to Sucon)
Waste
Influent (to Return Line)
Filter
Pump
FLOW
Filter
(10)
(aach to pipe with clamps)
FLOW
FLOW
Sample
pH sensor (3)
ORP
Sensor
(4)
Typical Installaon
Note: All chemical must be injected downstream from
the heater and flowcell.
Main Drain and Skimmer
Pressure Differenal
Return Line
FC100G
FLSW
SXPH
SXORP
SXORP-G
Valve
Jaco Fing 1/2”
Jaco Fing 1/4”
38tubing
Filter
1
2
3
4
5*
6
7
8
9
10
Flow Cell, Complete
Flow Switch Only
pH Sensor
ORP Sensor (Standard
Planum Tip)
ORP Sensor (Gold-Tip
for Salt Pools)
2-way Flow Cell Valve
1/2” Jaco fing for
sensors
1/4” Jaco fing for
tubing
3/8” tubing for
plumbing to/from
Flow Cell
Filter Strainer
IPS Parts List
Flow
Switch
(2) 1/2” Jaco Fing (7)
38tubing (9)
Valve (6)
* not shown
1/4” Jaco Fing
(7)

D. Specicaons
Enclosure: 7.95”L x 5.98”W x 3.54”D
Electrical Input/Output: 120/240 VAC, 50 - 60 Hz
ORP Set Level: 400 mV to 900 mV
pH Set Level: 7.0 to 8.0
Dose Time: O, Connuous, or Timed cycle
Delay Time: 1 - 99 minutes
Over Timer: O, 20-100 med cycles, or 20-180 connuous min-
utes, default of 60
High Alert: pH default of 8.0, ORP default of 900
Low Alert: pH default of 7.0, ORP default of 100
Readout: Funcon LED and numerical digital displays
Alarm: Red alert LEDs with oponal external audible/visible alarm
7
M820 pH/Dual ORP Controller Owner’s Manual

E. Controller Panel Descrip ons
1. Digital Displays and Func on LEDs
a. pH
1. Alert (High/Low) - red LED
2. Dose - green LED
3. Flashing LEDs - Over Timer Alert
b. ORP
1. Alert (High/Low) - red LED
2. Dose 1 - yellow LED
3. Dose 2 - yellow LED
4. Flashing LEDs - Over Timer Alert
Figure 2: M820 Controller Components Connec ons
8
M820 pH/Dual ORP Controller Owner’s Manual
Electrical
Connec�ons
Flow Cell
Connec�ons
digital display
pushbutton
LEDs
Controller Communication
pH
pH
ORP
AC
Power
ORP2
ORP1
Flow
Switch
Accessory
Temp
Sensor

2. Mode - pushbuon adjustments
a. Auto - red LED
b. pH standby - green LED
c. ORP1 standby - yellow LED
d. ORP2 standby - yellow LED
e. Temp display & calibrate - green LED
f. OFF mode - In standby, press and hold Mode buon for 3
seconds to turn controller o. There is sll power to the
controller in this mode, but no dosing will occur. Press and
hold to turn the controller back on.
3. Up/Down Arrows - pushbuon adjustments of following:
• Set Level
• Dose Time
• Delay Time
• Over Timer
• High Alert
• Low Alert
• pH Cal
4. Flow - green LED
5. Tank 1 - red LED
6. Tank 2 - red LED
7. Electrical Connecons (peripherals)
a. pH output (le receptacle) - max. 3.3 amps @ 110/230 VAC
max
b. ORP1 output (center receptacle)- max. 3.3 amps @
110/230 VAC max
c. ORP2 output (right receptacle) - max. 3.3 amps @ 110/230
VAC max
d. AC power - 120 VAC/240 VAC, 50-60 Hz
e. AC power protecon - Fused at .500 amps (500mA)
f. Flow - from ow cell
g. Tank 1 - from tank level switch (oponal)
h. Tank 2 - from tank level switch (oponal)
9
M820 pH/Dual ORP Controller Owner’s Manual

i. External audible/visible alarm (oponal)
j. pH sensor - BNC connecon
k. ORP sensor - BNC connecon
l. Oponal dry contact ORP1 output (contact factory for
instrucons)
F. Electrical Descripons
1. Power
a. 120 VAC, 50-60 Hz, 3-wire grounded NEMA 5 power cord.
GFCI source required. Note: For 240 VAC, a hardwire
connecon is required. Use only 18AWG stranded copper
wire. The controller’s power supply will automacally
detect the incoming power and will output the same
power to your devices. All output devices (feeders) must
match incoming voltage.
2. Dip Switches (1-4)
1: pH/ORP interlock (default: OFF)
• No ORP1 or ORP2 feed if pH is feeding (ON).
2: pH/ORP alert interlock (default: ON)
• No ORP1 or ORP2 feed if pH is in alert mode (ON).
• No interlock (OFF)
3: Acid/Base default acid (default: OFF)
• Feed base chemical when pH level falls below set
point. (ON)
• Feed acid chemical when pH above set point. (OFF)
4: Not in use.
Figure 3: Dipswitches
10
M820 pH/Dual ORP Controller Owner’s Manual

II. Installaon
A. Setup (Installaon video available at ipscontrollers.com)
1. Turn o all peripheral equipment such as heaters, chemical
feeders, and pumps.
2. Relieve pressure from the ltraon system.
B. Tools
1. Cordless drill
2. 1/4” NPT Tap
3. 7/16” drill bit
4. 1/4” or 3/8” drill bit for Temp Sensor (oponal)
5. Masonry drill bit and anchors, or other appropriate fasteners
6. 13/16” wrench or channel-lock pliers
C. Procedure
1. Locaon
a. Wall area with easy access
b. Within 8 feet of feeder
c. At least 10 feet from water edge
d. Close proximity to me clock
e. Within 6 feet of GFCI power source
2. Mounng
a. Controller and ow cell are factory-mounted to ABS board
for your convenience.
b. Securely mount ABS mounng board with M820 controller
and ow cell on wall (vercal installaon).
c. If applicable, securely aach the peristalc pumps to the
oponal larger ABS mounng board with the provided
hardware.
11
M820 pH/Dual ORP Controller Owner’s Manual

d. Drill a 7/16” hole and tap a 1/4” NPT port to a locaon
downstream from the lter and upstream from the heater
and any chemical introducon points. Install a tubing
connector and ex tubing to be connected to the le
side ow cell port containing the ow switch. The in-line
lter will also be installed in this line and mounted to a
horizontal pipe with band clamps (included). Note: Verify
that the lter is installed with direconal arrows poinng
in the direcon of the ow.
e. Drill a 7/16” hole and tap a 1/4” NPT port to a locaon that
is subject to vacuum or reduced pressure (aer heater).
Install a tubing connector and ex tubing to be connected
to the right-side ow cell port. Note: We recommend that
this tubing connector be installed into the drain hole on
the sucon side of the pump for best performance.
f. Cut a 3” - 6” length of ex tubing and insert into the ow
cell’s sample stream port (center).
3. pH and ORP Sensors
Note: Carefully unpack the pH and ORP sensors and set aside in a
clear area unl ready to install into the ow cell.
a. Verify that the M820 controller power is OFF.
b. Remove the plasc protecve caps from the sensors and
store in a separate locaon for future re-use.
c. Slide the glass end of each sensor (pH and ORP) into one of
the compression ngs located at the top of the ow cell.
Ensure that the p is submerged into the water to within
1/2” from the boom of the ow cell. Hand ghten each
nut ng.
4. Temperature Sensor (oponal)
a. Drill a 3/8” inch hole aer the lter and before the heater.
b. Insert the temperature sensor into the drilled hole and
secure with a band clamp (included).
12
M820 pH/Dual ORP Controller Owner’s Manual

c. Run the sensor cable into the controller through the strain
relief marked “temp” and connect to the terminal block on
the front circuit board marked “Temp”.
5. Electrical Connecons (Should be completed by a licensed
Electrician)
a. Verify that the M820 controller power is OFF.
b. Connect the pH feeder connecon to the appropriate
peristalc pump or other device.
c. Connect the ORP feeder connecon to the appropriate
peristalc pump or other device. Note: There is another
connecon port for ORP2.
d. Method 1 (recommended): Connect the AC power cord to
the load-side of the circulaon pump circuit. This will only
provide power to the M820 when the circulaon pump is
running.
e. Method 2: Connect the AC power cord to a GFCI
power source, or separately purchased IPS Controllers
PressureSwitch (part # PS100).
f. Connect the pH sensor connector to the corresponding
lower port (labeled pH) at the right edge of the controller.
g. Connect the ORP sensor connector to the corresponding
upper port (labeled ORP) at the right edge of the controller.
6. Chemical injecon must be inserted in the return line, aer
(downstream) any equipment.
7. Oponal connecon to a Salt Chlorine Generator (SCG)
The M820 controller is capable of controlling (turning on/o) a
SCG depending on the current ORP reading. This acon can be
accomplished using a 120V or 240V relay, or by connecng the SCG
to the “normally open” dry contact relay (ORP1) included with the
M820 controller. When using the ORP1 Dry Contact Relay, the black
plasc jumper idened as HD2 needs to be reposioned from the
lower posion (see Figure 4) to the open pegs at the top.
13
M820 pH/Dual ORP Controller Owner’s Manual

14
M820 pH/Dual ORP Controller Owner’s Manual
8. Conver ng from Cord to Permanent Connec on
a. Remove cover.
b. Loosen strain relief gland from AC cord.
c. Using a 3/32” (2.44mm) slot screw driver, carefully loosen
terminals that a ach the AC cord to the controller box.
d. Remove the AC cord.
e. Replace the AC cord with a minimum jacketed cord of 18/3 AWG
SW 105º 900 V, then carefully hand- ghten the terminals on the
strain relief gland. Note: For liquid ght installa on connec ons,
replace the strain relief gland with a liquid ght connector and
use a minimum stranded wire gauge of 18 AWG 105º 600 V (do
not use solid conductor) for each conductor: Black (hot), White
(common), and Green (ground).
Important:
The minimum allowable conductor size is 18 AWG with an
ampacity of 10 AMPS, and a ground fault interrupt circuit
breaker of 15-20 AMPS.
Use stranded copper wire only.
Figure 4: HD2 Jumper

III. Operaon
A. Overview
The IPS-M820 compares the readings received from the Ph and
ORP sensors to the Set Levels entered for Ph, ORP1, and ORP2. If
the readings are too low or too high, the controller will turn on
the feed devices for the Dose Time entered during set up. Other
sengs are used to ne tune the delivery of chemical, as well as
prevent over and under dosing.
B. Startup and Shutdown
1. Startup
a. Provide power to the M820 using either Method 1 or 2 as
discussed in step 6d or 6e on page 13.
b. Turn on the lter pump and verify the water ow through
the ow cell by opening the sample port valve (center)
and observing a steady stream of water. The right side
valve may need to be parally closed to produce a steady
stream. Note: Water should pass over the pH and ORP
sensors for a minimum of 5 minutes to allow for accurate,
stable readings of pH and ORP levels from the pool or
spa. ORP readings may take longer to stabilize.
c. Check for leaks and repair if necessary.
d. Manually adjust and balance the pool or spa water to
acceptable ranges using a test kit. Note(s): 1. Use a DPD
based test kit to check the chlorine level. 2. Cyanuric Acid
(Condioner) levels should not exceed 30 ppm for best
results.
e. Verify that the green Flow LED is illuminated. Both the pH
and ORP dose outputs are disabled if there is no water
ow.
15
M820 pH/Dual ORP Controller Owner’s Manual

f. Press the Mode pushbuon momentarily to place the
controller into the pH standby mode. The green pH standby
LED will illuminate. Select the desired pH set level and dose
me (connuous or med). Please call us at 877-693-6903
for assistance with inial sengs.
g. While sll in the pH standby mode, press the pH Cal
pushbuon to calibrate the reading to the value observed
through the manual tesng of the water. Note: Always
calibrate using water from the sample port of the ow
cell.
h. Press the Mode pushbuon momentarily to place the
controller in ORP1 standby mode. The yellow ORP1
standby LED will illuminate. Select the desired ORP1 set
level and dose me (connuous or med). Please call us at
877-693-6903 for assistance with inial sengs.
i. Press the Mode pushbuon momentarily unl the red
Auto LED is illuminated. Note: If pH level in the pool is at
desired set level and chlorine/bromine level is at desired
PPM level in the pool, then the ORP set level should be
the same as the current ORP reading when in Auto Mode.
2. Shutdown
Note: Each me the Mode pushbuon is momentarily pressed,
the mode will cycle from Auto to pH to ORP1 to ORP2, Temp, and
then return to Auto mode.
a. Press the Mode pushbuon momentarily to place the
controller in pH standby mode. The green pH standby LED
will illuminate, and both the pH and ORP digital displays
will show dashes.
b. Press and hold the Mode pushbuon for 2 seconds unl
both the pH and ORP digital displays read OFF.
c. Release the Mode pushbuon. The M820 controller will
turn o, and the digital displays and funcon LEDs will go
blank. The green Flow LED will be illuminated if water is
owing through the ow cell.
16
M820 pH/Dual ORP Controller Owner’s Manual

C. Modes and Adjustments
1. Auto
a. This is the normal operaonal mode of the M820
controller.
b. The controller allows full operaon and monitoring of both
pH and ORP levels.
c. No funcon pushbuons are operaonal in this mode.
d. The red funcon LED next to Auto is illuminated.
e. pH and ORP digital displays monitor the sensor input
levels.
2. pH standby
Note: While in this mode, the green pH standby LED will
illuminate, both the pH and ORP digital displays will show
dashes, and all Auto funcons will be disabled. When a funcon
pushbuon is pressed, the corresponding digital display will show
the funcon. Use the Up or Down arrow buons to the le to
increase or decrease the funcon value.
a. Set Level
1. Default: 7.4 pH
2. Selectable range: 7.0 – 8.0 pH (in 0.1 increments)
b. Dose Time
1. Default: Timed dose of 10-second pH feed relay
energized and 5 minutes pH feed relay de-energized.
In the med dose cycle mode, the dose LED will ash
while dosing and illuminate steadily during the delay
poron of the med cycle. In connuous dose mode,
the dose LED will ash while dosing, and dosing will
connue unl pH is 0.2 below (or above if feeding base)
Set Level.
2. Selectable range: OFF, CON (connuous), and Timed
(10 – 900 seconds ON)
17
M820 pH/Dual ORP Controller Owner’s Manual

c. Delay Time
1. Default: Delay me of 5 minutes between feed cycles
(med feed only). Aer dose me, the controller will
wait (delay) for the specied minutes before checking
the current level and dosing again if necessary.
2. Selectable range: 1 - 99 minutes.
d. Over Timer
1. Default: ON. The Over Timer does not automacally
reset. It must be reset by pressing the Mode buon to
cycle through the Standby mode and back to the Auto
mode.
2. The Over Timer is interlocked with the Dose Time
selecon.
a. If the Dose Time is set to a med cycle, the Over
Timer will count med feed cycles. Every me the
set level is reached the me will reset its count. If
the preset cycle is reached, the pH digital display will
ash, and the pH output relay will de-energize. The
controller must be reset manually by cycling out of
and back into the Auto mode using the mode buon.
- Selectable range: 20 to 100 cycles
b. If the Dose Time is set to a connuous feed mode,
the Over Timer will count in minutes. Default is 60
minutes.
- Selectable range: 20 to 180 minutes
3. When the Dose Time is changed from either med or
connuous feed, the Over Timer is reset to Default.
4. Turning o the Over Timer will void any NSF
Cercaon and is not recommended for safety
reasons.
18
M820 pH/Dual ORP Controller Owner’s Manual

e. High Alert
1. Default: 8.0 pH
2. Selectable range: OFF, 7.5 pH to 8.4 pH (acid feed). A
high alert will occur if the pH level remains above the
High Alert level for 10 connuous minutes, and will
automacally turn o the High Alert when the pH level
falls below the high alert level for 1 connuous minute.
During High Alert, the pH dose output will be disabled,
and by default ORP1 and ORP2 will be disabled (see Dip
Switch #2 sengs).
f. Low Alert
1. Default: 7.0 pH
2. Selectable range: OFF, 6.8 pH to 7.4 pH (acid feed). A
low alert will occur if the pH level remains below the
Low Alert level for 10 connuous minutes, and will
automacally turn o the Low Alert when the pH level
rises above the low alert level for 1 connuous minute.
During Low Alert, the pH dose output will be disabled.
g. pH Cal
1. Use to adjust pH to manually tested value.
2. Maximum increase/decrease is 0.9 pH within the 6.0 to
8.4 display window.
3. ORP1 standby
Note: While in this mode, the yellow ORP1 standby LED will
illuminate, both the pH and ORP digital displays will show dashes,
and all Auto funcons will be disabled. Use the Up or Down
arrow buons to the le to increase or decrease the funcon
value.
a. Set Level
1. Default: 650 mV
2. Selectable range: 400 mV to 900 mV (in 5 mV
increments)
19
M820 pH/Dual ORP Controller Owner’s Manual
Table of contents
Other IPS Controllers Controllers manuals
Popular Controllers manuals by other brands
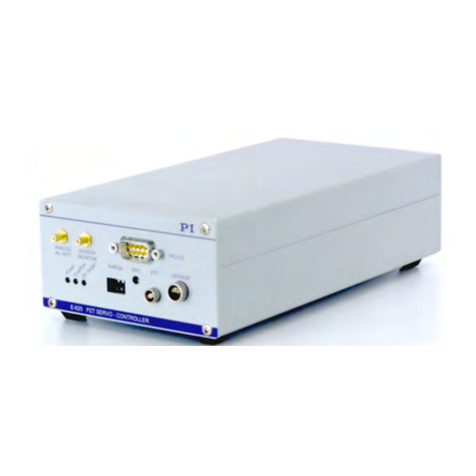
PI
PI E-625 user manual
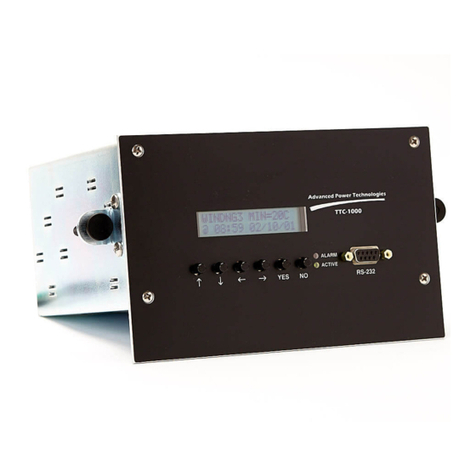
Advanced Power technologies
Advanced Power technologies TTC-1000 instruction & operation manual
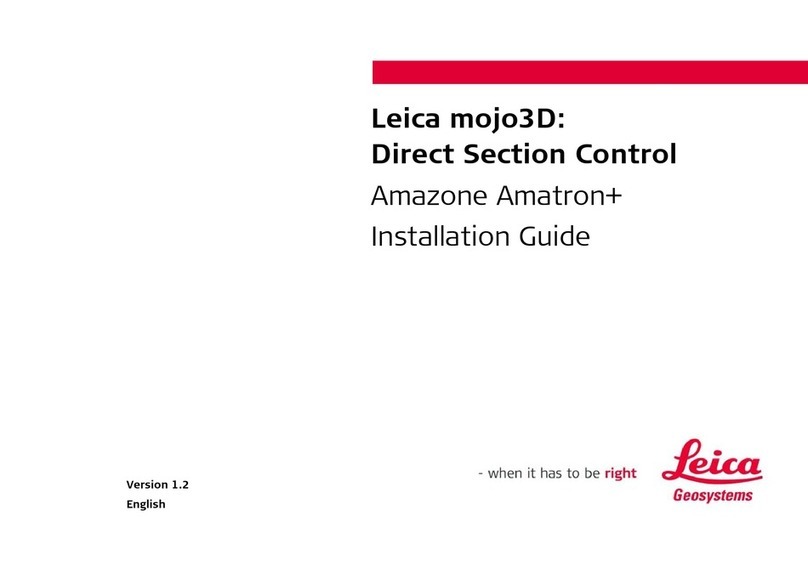
Leica
Leica mojo3D installation guide
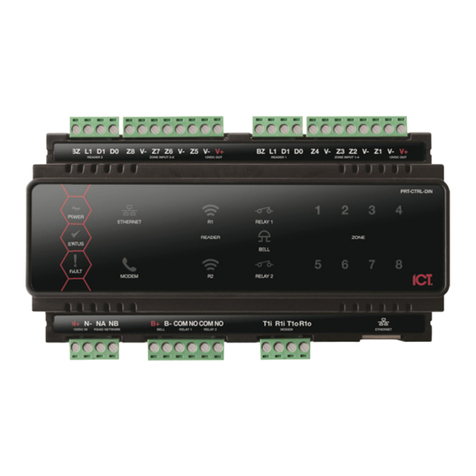
ICT
ICT Protege GX DIN Rail System Controller quick start guide

SMC Networks
SMC Networks E-MY2B Series Operation manual

Honeywell
Honeywell HR 40 Installation and operating instructions
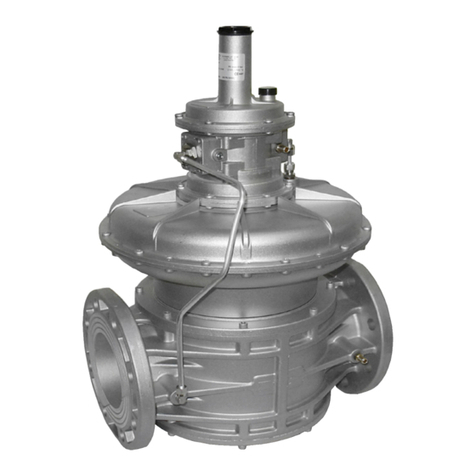
Madas
Madas FRG/2MC manual
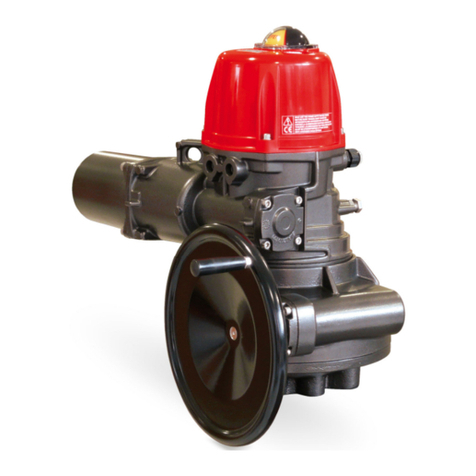
VALPES
VALPES VT1500 Installation and operation manual

Franke
Franke AQUA802 Installation and operating instructions

Tecnosystemi
Tecnosystemi Apply.co ACC600016 user manual
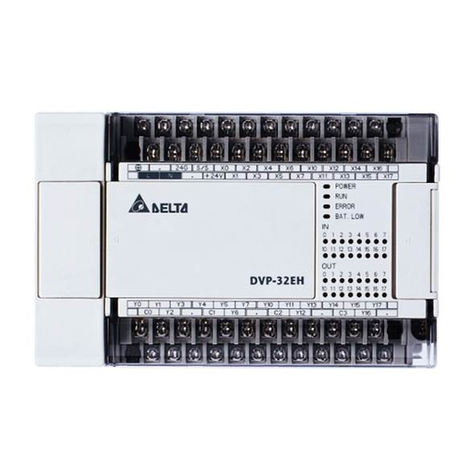
Delta Electronics
Delta Electronics Programmable Logic Controller DVP-EH2-L instruction sheet
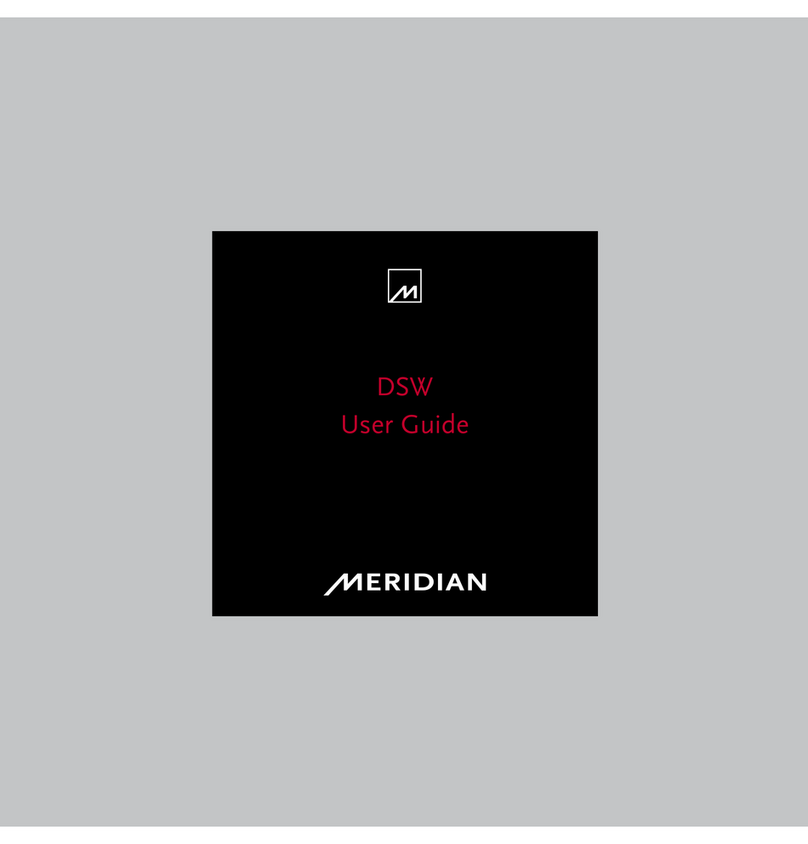
Meridian
Meridian DSW user guide