iWorX CCU1 User guide

© 2010 Taco Electronic Solutions, Inc. 1
Application Guide 505-022
CCU1 Chiller Controller
Self-Contained Interoperable Controller Model UCP-1
SUPERSEDES: September 1, 2010 EFFECTIVE: September 23, 2010
Table of Contents
CCU1 . . . . . . . . . . . . . . . . . . . . . . . . . . . . . . . . . . . . . . 3
Overview . . . . . . . . . . . . . . . . . . . . . . . . . . . . . . . . . 3
Features. . . . . . . . . . . . . . . . . . . . . . . . . . . . . . . . . . 3
Purpose of This Guide . . . . . . . . . . . . . . . . . . . . . . . . . 3
Representations and Warranties . . . . . . . . . . . . . . . . . 3
Applicable Documentation . . . . . . . . . . . . . . . . . . . . . . 4
Installation Instructions . . . . . . . . . . . . . . . . . . . . . . . . . 5
Precautions . . . . . . . . . . . . . . . . . . . . . . . . . . . . . . . 5
General . . . . . . . . . . . . . . . . . . . . . . . . . . . . . . . . . . 5
Static Electricity . . . . . . . . . . . . . . . . . . . . . . . . . . . . 5
Location . . . . . . . . . . . . . . . . . . . . . . . . . . . . . . . . . . 5
FCC Compliance . . . . . . . . . . . . . . . . . . . . . . . . . . . 5
Before Installing . . . . . . . . . . . . . . . . . . . . . . . . . . . . . . 5
About this Document . . . . . . . . . . . . . . . . . . . . . . . . 5
Inspecting the Equipment . . . . . . . . . . . . . . . . . . . . 6
What is Not Included with this Equipment . . . . . . . . 6
Equipment Location . . . . . . . . . . . . . . . . . . . . . . . . . 6
Selecting a Power Source . . . . . . . . . . . . . . . . . . . . 6
Installation . . . . . . . . . . . . . . . . . . . . . . . . . . . . . . . . . . 6
Mounting the Device . . . . . . . . . . . . . . . . . . . . . . . . 6
Routing Cabling to the Device . . . . . . . . . . . . . . . . . 7
Grounding the Device . . . . . . . . . . . . . . . . . . . . . . . 7
Wiring Information . . . . . . . . . . . . . . . . . . . . . . . . . . . . 8
Connecting Input Devices . . . . . . . . . . . . . . . . . . . 10
Connecting Output Devices . . . . . . . . . . . . . . . . . . 11
Other Connections . . . . . . . . . . . . . . . . . . . . . . . . . 11
Specifications . . . . . . . . . . . . . . . . . . . . . . . . . . . . . . . . 12
Electrical . . . . . . . . . . . . . . . . . . . . . . . . . . . . . . . . 12
Mechanical . . . . . . . . . . . . . . . . . . . . . . . . . . . . . . 13
Application Description. . . . . . . . . . . . . . . . . . . . . . . . . 14
Sequence of Operation . . . . . . . . . . . . . . . . . . . . . . . . 16
Chiller Activation . . . . . . . . . . . . . . . . . . . . . . . . . . 16
Chiller Setpoint Adjustment . . . . . . . . . . . . . . . . . . 16
Chiller Pump Control . . . . . . . . . . . . . . . . . . . . . . . 16
Condenser Pump Control . . . . . . . . . . . . . . . . . . . 16
Cooling Tower Bypass Valve Control . . . . . . . . . . 16
Cooling Tower Variable Speed Fan Control . . . . . 17
Chiller Low Limit Control . . . . . . . . . . . . . . . . . . . . 17
Chiller Alarm Status. . . . . . . . . . . . . . . . . . . . . . . . 18
Runtime Accumulations. . . . . . . . . . . . . . . . . . . . . 18
Alarms and Events . . . . . . . . . . . . . . . . . . . . . . . . 18
Automatic Configuration . . . . . . . . . . . . . . . . . . . . 19
Networking Controllers . . . . . . . . . . . . . . . . . . . . . 19
Controller Identification . . . . . . . . . . . . . . . . . . . . . . . . 20
Inputs. . . . . . . . . . . . . . . . . . . . . . . . . . . . . . . . . . . 20
Outputs . . . . . . . . . . . . . . . . . . . . . . . . . . . . . . . . . 20
All Settings. . . . . . . . . . . . . . . . . . . . . . . . . . . . . . . 21
Alarms . . . . . . . . . . . . . . . . . . . . . . . . . . . . . . . . . . 23
Troubleshooting . . . . . . . . . . . . . . . . . . . . . . . . . . . . . . 25
Diagnostic LEDs . . . . . . . . . . . . . . . . . . . . . . . . . . 25
Troubleshooting Tips . . . . . . . . . . . . . . . . . . . . . . . 26

iWorX CCU1
2 505-022, Effective: September 23, 2010
© 2010 Taco Electronic Solutions, Inc.
THIS PAGE LEFT BLANK INTENTIONALLY

iWorX CCU1
505-022, Effective: September 23, 2010 3
© 2010 Taco Electronic Solutions, Inc.
CCU1
The iWorX CCU1 chiller controller is a stand-alone microprocessor based controller for supervisory central chiller con-
trol applications that utilize one air-cooled chiller or a water-cooled centrifugal chiller with cooling tower.
Overview
Analog inputs are provided for chiller water supply temperature, chiller water return temperature, condenser water sup-
ply temperature, and condenser water return temperature. Digital inputs are provided for chiller pump flow proof, con-
denser pump flow proof, a cooling water demand proof, and a chiller general alarm.
The CCU1 incorporates digital outputs in the form of triacs for chiller low limit status and the start and stop of the chiller
and condenser pumps. In addition, three analog outputs are provided to control a modulated bypass valve, a variable
speed fan, and set the adjustable setpoint of the chiller.
The controller is based on the LONWORKS®networking technology. The controller can be networked to a higher-level
control system for monitoring and control applications, and provides chilled water in response to demand from other
controllers.
Features
• Adjustable chiller setpoint
• Modulated cooling tower bypass valve
• Modulated cooling tower fan
• Minimum cycle timers for chiller On and Off
• Runtime accumulation for chiller, pumps, and fan
• Lead/Lag operation of water pumps
• Maximum of 60 cooling zones
• Proportional + Integral (P+I) control of the modulated bypass valve
• Proportional + Integral (P+I) control of a variable speed fan
• OAT low limit protection
• Flow proof inputs
• Chiller enable/demand input
• Chiller alarm input
• Automatic configuration with the LCI
• Alarm/Event reporting
PURPOSE OF THIS GUIDE
The iWorX CCU1 Application Guide provides application information for the CCU1 Controller.
The reader should understand basic HVAC concepts, intelligent environmental control automation, and basic LON-
WORKS networking and communications. This Application Manual is written for:
• Users who engineer control logic
• Users who set up hardware configuration
• Users who change hardware or control logic
• Technicians and field engineers
REPRESENTATIONS AND WARRANTIES
This Document is subject to change from time to time at the sole discretion of Taco Electronic Solutions, Inc. All
updates to the Document are available at www.taco-hvac.com. When installing this product, it is the reader’s responsi-
bility to ensure that the latest version of the Document is being used.

iWorX CCU1
4 505-022, Effective: September 23, 2010
© 2010 Taco Electronic Solutions, Inc.
The iWorX CCU1 shall only be used for the applications identified in the product specifications and for no other pur-
poses. For example, the iWorX CCU1 is not intended for use to support fire suppression systems, life support systems,
critical care applications, commercial aviation, nuclear facilities or any other applications where product failure could
lead to injury to person, loss of life, or catastrophic property damage and should not be used for such purposes.
Taco Electronic Solutions, Inc. will not be responsible for any product or part not installed or operated in conformity with
the Document and instructions or which has been subject to accident, disaster, neglect, misuse, misapplication, inade-
quate operating environment, repair, attempted repair, modification or alteration, or other abuse. For further informa-
tion, please refer to the last page of this Document for the company’s Limited Warranty Statement, which is also issued
with the product or available at www.taco-hvac.com.
APPLICABLE DOCUMENTATION
Table 1: Applicable Documentation
Description Audience Purpose
iWorX CCU1 Application Guide,
Document No. 505-022 (this docu-
ment)
– Application Engineers
–Wholesalers
– Contractors
– Start-up Technicians
– End user
Provides instructions for setting up and using the iWorX CCU1
Controller.
iWorX LCI2 Application Guide, Doc-
ument No. 505-002
– Application Engineers
–Installers
– Service Personnel
– Start-up Technicians
– End user
Provides instructions for setting up and using the iWorX Local
Control Interface.
iWorX DXU3 Application Guide,
Document No. 505-004
– Application Engineers
–Installers
– Service Personnel
– Start-up Technicians
– End user
Provides instructions for setting up and using the iWorX Con-
troller.
iWorX DXU4 Application Guide,
Document No. 505-005
– Application Engineers
–Installers
– Service Personnel
– Start-up Technicians
– End user
Provides instructions for setting up and using the iWorX DXU4
Controller.
http://iWorxWizard.taco-hvac.com – Application Engineers
–Wholesalers
– Contractors
An on-line configuration and submittal package generator
based on user input. Automatically generates bill of materials,
sequence of operations, flow diagrams, wiring diagrams,
points and specifications.
Additional Documentation LonWorks FTT-10A Free Topology Transceiver User’s Guide, published by Echelon Cor-
poration. It provides specifications and user instructions for the FTT-10A Free Topology
Transceiver. See also: www.echelon.com/support/documentation/manuals/transceivers.

iWorX CCU1
505-022, Effective: September 23, 2010 5
© 2010 Taco Electronic Solutions, Inc.
INSTALLATION INSTRUCTIONS
Precautions
General
This symbol is intended to alert the user to the presence of important installation and maintenance (servic-
ing) instructions in the literature accompanying the equipment.
WARNING: Electrical shock hazard. Disconnect ALL power sources when installing or servicing this
equipment to prevent electrical shock or equipment damage.
Make all wiring connections in accordance with these instructions and in accordance with pertinent national and local
electrical codes. Use only copper conductors.
Static Electricity
Static charges produce voltages that can damage this equipment. Follow these static electricity precautions when han-
dling this equipment.
• Work in a static free area.
• Touch a known, securely grounded object to discharge any charge you may have accumulated.
• Use a wrist strap when handling printed circuit boards. The strap must be secured to earth ground.
Location
Avoid locations where corrosive fumes, excessive moisture, vibration or explosive vapors are present.
Avoid electrical noise interference. Do not install near large contactors, electrical machinery, or welding equipment.
This equipment is suitable for indoor or outdoor use. Preferably, or as required by National Electrical Code, the unit is
intended to be installed within an electrical control enclosure. Operate where ambient temperatures do not exceed
140 °F (60 °C) or fall below 32 °F (0 °C) and relative humidity does not exceed 90%, non-condensing.
FCC Compliance
This equipment has been tested and found to comply with the limits for a Class A digital device, pursuant to Part 15 of
the FCC rules. These limits are designed to provide reasonable protection against harmful interference. This equip-
ment can radiate radio frequency energy and, if not installed and used in accordance with the instructions, may cause
harmful interference to radio communications. However, there is no guarantee that interference will not occur in a par-
ticular installation. If this equipment does cause harmful interference to radio or television reception, which can be
determined by turning the equipment off and on, the user is encouraged to try to correct the interference by one or
more of the following measures:
• Reorient or relocate the receiving antenna.
• Increase the separation between the equipment and the receiver.
• Connect the equipment to a power source different from that to which the receiver is connected.
• Consult the equipment supplier or an experienced radio/TV technician for help.
You are cautioned that any changes or modifications to this equipment not expressly approved in these instructions
could void your authority to operate this equipment in the United States.
BEFORE INSTALLING
About this Document
The instructions in this manual are for the CCU1 module, which supports one central plant consisting of one air-cooled
chiller or one water-cooled chiller with cooling tower.

iWorX CCU1
6 505-022, Effective: September 23, 2010
© 2010 Taco Electronic Solutions, Inc.
Inspecting the Equipment
Inspect the shipping carton for damage. If damaged, notify the carrier immediately. Inspect the equipment for damage.
Return damaged equipment to the supplier.
What is Not Included with this Equipment
• A power source for the equipment electronics and peripheral devices.
• Tools necessary to install, troubleshoot and service the equipment.
• The screws or DIN rail needed to mount the device.
• Peripheral devices, such as sensors, actuators, etc.
• Cabling, cabling raceway, and fittings necessary to connect this equipment to the power source, FTT-10A network
and peripheral devices.
Equipment Location
Abide by all warnings regarding equipment location provided earlier in this document.
Optimally, the equipment should be installed within a secure enclosure.
If the equipment is to be installed outdoors, it must be contained within a protective enclosure. The enclosure must
maintain internal temperature and humidity within the ranges specified for this equipment.
The equipment must be installed within 500 feet of all input peripherals (smoke detectors, sensors, etc.) that will be
connected to the equipment.
Selecting a Power Source
This equipment requires a UL recognized Class 2 external power source (not supplied) to operate. The controller
power input requires a voltage of 24 Volts AC.
To calculate power source current requirements, add the power consumption of all peripheral devices to that of the
controller.
The controller and triac output loads can use the same power source. If both are using the same power source, the
loads must have EMF protection. This protection can be integral to the load, or installed in the 24 VAC wiring across
the load’s coil.
To provide necessary RFI and transient protection, the controller’s ground (GND) pin (T40) must be connected to earth
ground or the earth ground of the packaged unit’s enclosure ground. Failure to properly ground the controller may
cause it to exceed FCC limits. Excessive noise could also produce inaccurate sensor data. The power source must be
capable of operating with this connection to ground.
INSTALLATION
Warning: Electrical shock hazard. To prevent electrical shock or equipment damage, disconnect ALL
power sources to controllers and loads before installing or servicing this equipment or modifying any wir-
ing.
Mounting the Device
1.Select a mounting location. Enclosure mounting is recommended.
2.Hold the controller on the panel you wish to mount it on. With a marker or pencil mark the mounting locations on
the panel.
3.Using a small drill bit pre-drill the mounting holes.
4.Using two #6 pan head screws, mount the controller to the panel.
5.Wire the controller (See Routing Cabling to the Device).

iWorX CCU1
505-022, Effective: September 23, 2010 7
© 2010 Taco Electronic Solutions, Inc.
Figure 1: Mounting Dimensions
Routing Cabling to the Device
Cabling used to connect the power source and cabling used to connect the FTT-10A network must remain
separated within the control enclosure and wiring conduit.
Grounding the Device
The ground terminal (T40) must be securely connected to earth ground. Failure to properly ground this
equipment will result in improper operation. Improper grounding may also increase the risk of electrical
shock and may increase the possibility of interference with radio/TV reception.
For best performance, connect the power supply common terminal (T38) to the same external point as the
ground terminal (T40).

iWorX CCU1
8 505-022, Effective: September 23, 2010
© 2010 Taco Electronic Solutions, Inc.
WIRING INFORMATION
WARNING: Terminals 6, 9, 12, 15, 18, 33, 36, and 38 are connected internally on all CCU1 controllers.
Disconnect ALL power sources when installing or servicing this equipment to prevent electrical shock or
equipment damage.
Figure 2: Wiring Diagram for Power Sourcing applications

iWorX CCU1
505-022, Effective: September 23, 2010 9
© 2010 Taco Electronic Solutions, Inc.
Figure 3: Wiring Diagram for Power Sinking applications

iWorX CCU1
10 505-022, Effective: September 23, 2010
© 2010 Taco Electronic Solutions, Inc.
Figure 4: Wiring Diagram for Power Isolated applications
Connecting Input Devices
Chiller Water Supply Temperature (CWS)
To connect the chiller water supply thermistor to the unit, attach one wire from the thermistor to CWS (T19) and the
other wire to the adjacent common (T18). The thermistor used must be a 10K Precon Type III.
Chiller Water Return Temperature (CWR)
To connect the chiller water return thermistor to the unit, attach one wire from the thermistor to CWR (T17) and the
other wire to the adjacent common (T18). The thermistor used must be a 10K Precon Type III.
Condenser Supply Temperature (CDS)
To connect the condenser water supply thermistor to the unit, attach one wire from the thermistor to CDS (T16) and the
other wire to the adjacent common (T15). The thermistor used must be a 10K Precon Type III.
Condenser Return Temperature (CDR)
To connect the condenser water return thermistor to the unit, attach one wire from the thermistor to CDR (T14) and the
other wire to the adjacent common (T15). The thermistor used must be a 10K Precon Type III.

iWorX CCU1
505-022, Effective: September 23, 2010 11
© 2010 Taco Electronic Solutions, Inc.
Chiller Flow Proof (CFP)
To connect the chiller flow proof switch to the digital input, attach one wire of the contact to CFP (T13) and the other
wire to the adjacent common (T12). This must be a dry contact, normally open switch which closes when flow is
detected. If a flow proof switch is not installed, the terminals should be connected with a jumper wire.
Condenser Flow Proof (CDFP)
To connect the condenser flow proof switch to the digital input, attach one wire of the contact to CDFP (T11) and the
other wire to the adjacent common (T12). This must be a dry contact, normally open switch which closes when flow is
detected. If a flow proof switch is not installed, the terminals should be connected with a jumper wire.
Chiller General Alarm (ALM)
To connect the chiller’s general alarm output to the digital input, attach one wire of the contact to ALM (T5) and the
other wire to the adjacent common (T6). This output from the chiller must act as a dry contact, normally open switch.
Chilled Water Demand (CWD)
To connect the demand switch to the digital input, attach one wire of the contact to CWD (T8) and the other wire to the
adjacent common (T9). This must be a dry contact, normally open switch.
Connecting Output Devices
Chiller Pumps 1 & 2 (CHP1, CHP2)
The outputs for the pumps must be connected to 24 VAC pilot relays if the load is greater than 1 Amp for each pump. If
the load is less than 1 Amp, connect pump 1 to CHP1 (T31) and TC12 (T30), and connect pump 2 to CHP2 (T29) and
TC12 (T30).
Condenser Pumps 1 & 2 (CDP1, CDP2)
The outputs for the pumps must be connected to 24 VAC pilot relays if the load is greater than 1 Amp for each pump. If
the load is less than 1 Amp, connect pump 1 to CDP1 (T28) and TC34 (T27), and connect pump 2 to CDP2 (T26) and
TC34 (T27).
Chiller Low Limit (CLL)
The output for the chiller low limit interface must be connected to a 24 VAC pilot relays if the load is greater than 1 Amp.
If the load is less than 1 Amp, connect the chiller's low limit input to CLL (T25) and TC56 (T24).
Chiller Setpoint Adjustment (CSP)
The chiller setpoint adjustment output can be set to 0-10 VDC max through the control logic. Connect the positive wire
from the chiller’s setpoint adjustment input to CSP (T37) and the other wire to the adjacent common (T36).
Cooling Tower Valve (CTV)
The cooling tower bypass valve output can be set to 0-10 VDC max through the control logic. Connect the positive wire
from the valve actuator to CTV (T35) and the other wire to the adjacent common (T36).
Cooling Tower Fan (CTF)
The cooling tower fan output can be set to 0-10 VDC max through the control logic. Connect the positive wire from the
fan actuator to CTF (T34) and the other wire to the adjacent common (T33).
Other Connections
Network (LON)
Network wiring must be twisted pair. One network wire must be connected to terminal NETA (T1) and the other network
wire must be connected to terminal NETB (T2). Polarity is not an issue since an FTT-10A network is used for commu-
nications.
Power (PWR)
Connect one output wire from a 24 VAC power supply to PWR (T39) and the other output wire from the power supply to
the adjacent common terminal (T38).

iWorX CCU1
12 505-022, Effective: September 23, 2010
© 2010 Taco Electronic Solutions, Inc.
Ground (GND)
Terminal GND (T40) must be connected to earth ground. Failure to properly ground this equipment will
result in improper operation. Improper grounding may also increase the risk of electrical shock, and may
increase the possibility of interference with radio and TV reception.
SPECIFICATIONS
Electrical
Inputs
• Cabling: twisted shielded pair, 18 AWG recommended—500 feet max. (152 meters)
• Resolution: 10 bit
Chiller Supply Temperature, Chiller Return Temperature, Condenser Supply Temperature, Condenser
Return Temperature
• Precon Type III 10K thermistor
Chiller Alarm, Chilled Water Demand, Chiller Flow Proof, Condenser Flow Proof
•DryContact
• Normally Open
• 5 Volts DC Max
Outputs
Chiller Pumps 1 & 2, Condenser Pumps 1 & 2, Chiller Low Limit
• 24 Volts AC
• 1A @ 50C, 0.5A @ 60C, limited by the Class 2 supply rating
Chiller Setpoint, Cooling Tower Valve, Cooling Tower Fan
• 0-10 Volts DC
• 2K Ohm minimum load
• 8 bit resolution
Recommended Sensor Wire
FTT-10A Network
• Speed: 78KBPS
• Cabling: Maximum node-to-node distance: 1312 feet (400 meters)
• Maximum total distance: 1640 feet (500 meters)
For detailed specifications, refer to the FTT-10A Free-Topology Transceiver User’s Guide published by Echelon Corpo-
ration (www.echelon.com/support/documentation/manuals/transceivers).
Power
Power Requirements
• 24VAC (20VAC to 28VAC), requires an external Class 2 supply
Power Consumption
• 7.2W with no external loads, maximum limited by the Class 2 supply rating
Cable Type Pairs Details Taco Catalog No.
18AWG 1 Stranded Twisted Shielded Pair, Plenum WIR-018
Cable Type Pairs Details Taco Catalog No.
Level 4 22AWG (0.65mm) 1 Unshielded, Plenum, U.L. Type CMP WIR-022

iWorX CCU1
505-022, Effective: September 23, 2010 13
© 2010 Taco Electronic Solutions, Inc.
Mechanical
Housing
• Dimensions: 5.55” (141mm) high, 6.54” (166 mm) wide, 1.75” deep (44 mm)
• ABS
Weight
• Controller Weight: 0.70 pounds (0.32 kilograms)
• Shipping Weight: 1.0 pounds (0.46 kilograms)
Electronics
• Processor: 3150 Neuron 10 MHz
• Flash: 48 Kilobytes
• SRAM: 8 Kilobytes
• Termination: 0.197” (5.0 mm) Pluggable Terminal Blocks, 14-22 AWG
Environmental
• Temperature: 32 °F to 140 °F (0 °C to 60 °C)
• Humidity: 0 to 90%, non-condensing
Agency Listings
• UL Listed for US and Canada, Energy Management Equipment PAZX and PAZX7.
Agency Compliances
• FCC Part 15 Class A

iWorX CCU1
14 505-022, Effective: September 23, 2010
© 2010 Taco Electronic Solutions, Inc.
APPLICATION DESCRIPTION
The CCU1 chiller controller is a stand-alone microprocessor-based controller for supervisory control of central chiller
applications that utilize either an air-cooled chiller or a water-cooled centrifugal chiller with a cooling tower. Two chilled
water pumps are configured for lead/lag operation. The CCU1 provides setpoint adjustment control of the chiller by
integrating to the factory mounted chiller controls with a 0-10 VDC setpoint control signal. For chilled water plant appli-
cations that utilize a cooling tower, the CCU1 controller provides control of the tower bypass valve and two cooling
tower (condenser) pumps configured in a lead/lag configuration. Outputs are provided for control of the cooling tower
bypass valve. Analog outputs are provided to support cooling tower applications with variable fan speed control.
Figure 5: CCU1
Condenser
To w e r
Evaporator
LOAD
DP
DP
Chiller
General
Alarm
Chiller
Ret ur n Temp .
Condenser
Ret ur n Temp.
Chiller
Supply
Te m
p
.
Chiller
Flow Proof
Condenser
Flow Proof
Condenser.
Supply Temp.
Chiller
Pump
1
Chiller
Pump
2
Chiller
Setpt.
Chiller
Low
Limit
Cooling Towe
r
Va l v e
Cooling
To w e r Fa n
Condenser
Pump 1
Condenser
Pump 2
with cooling tower
CCU1 control starts only if there is a cooling water demand and the outside air temperature (OAT) is above the OAT
limits --> Cutoff temp. The CCU1 operates in conjunction with up to 60 controllers that can require chilled water (FCU
Series, DXU Series, HPU Series). The cooling water demand is obtained by the CCU1 from controllers that have been
grouped with the CCU1 at the LCI user interface during initial configuration. Cooling water demand can also be com-
municated through a digital input switch, or through a demand for chiller activation from the LCI.
Initial chiller control activates a chiller pump. The factory-installed chiller controls, as provided by the chiller manufac-
turer, detect water flow in the chilled water loop and activate the chiller. An anti-cycle function provides configurable
chiller minimum On and Off times.
The CCU1 includes support for two chilled water pumps, with only one pump required for normal operation. One of the
pumps is designated the lead pump, with the lag pump only being required in the event of a lead pump alarm. Each
time the chiller is deactivated, the lead pump designation is transferred to the other pump.

iWorX CCU1
505-022, Effective: September 23, 2010 15
© 2010 Taco Electronic Solutions, Inc.
When the chiller is activated, the lead chiller pump is started. If the chiller pump has been commanded on for at least
20 seconds and the Chiller Flow proof is off, an alarm is initiated and the lag pump is started. The lag pump also trig-
gers an alarm if it has been commanded on for 20 seconds and flow proof is not established. If both chiller pumps fail,
all outputs are turned off, all control stops, and a dual pump failure alarm is generated. Manual reset of the CCU1 con-
troller from the operator interface or by cycling power to the CCU1 is required to restart control.
The CCU1 also includes support for two condenser water pumps, with only one pump required for normal operation.
One of the pumps is designated the lead pump, with the lag pump only being required in the event of a lead pump fail-
ure. Each time the system is deactivated, the lead pump designation is transferred to the other pump.
In a water-cooled chiller, when the chiller water pump is started the lead condenser pump is started also. If the con-
denser pump has been commanded on for at least 20 seconds and the condenser flow proof is off, an alarm is initiated
and the lag pump is started. The lag pump also triggers an alarm if it has been commanded on for 20 seconds and flow
proof is not established. If both condenser pumps fail, all outputs are turned off, all control stops, and a dual pump fail-
ure alarm is generated. Manual reset of the CCU1 controller from the operator interface or by cycling power to the
CCU1 is required to restart control.
An analog output is provided for setpoint adjustment utilizing the factory-mounted chiller controls. The chiller setpoint
adjust feature of the CCU1 enables the user to change the chiller water supply setpoint through the LCI.
The bypass valve position is calculated by a Proportional + Integral (P+I) control loop based on the condenser water
return temperature and the condenser water setpoint. The bypass valve control loop is activated 15 seconds after the
condenser water flow proof has confirmed flow. As the temperature increases above the condenser water setpoint, the
bypass valve is modulated open. The bypass valve is modulated closed as the water temperature decreases below the
condenser setpoint. The cooling tower bypass valve control loop is selectable for direct or reverse acting operation.
The cooling tower fan speed is calculated by a P+I control loop based on the condenser water return temperature and
the cooling tower water setpoint. The fan speed control loop is activated 15 seconds after the cooling tower bypass
valve has modulated to its 100% position (full flow through tower). As the temperature increases above the cooling
tower water setpoint, the fan speed is increased. The fan speed is decreased as the water temperature decreases
below the cooling tower setpoint. The fan speed control loop is selectable for direct or reverse acting operation.
The CCU1 provides low limit control. When the outside air temperature (OAT) drops below the low limit setpoint as
sensed by an ASM controller on the system network, the chiller water pump energizes and the chiller low limit output is
enabled. The chiller low limit output is interfaced to the factory supplied chiller controls to signal the chiller to not start in
response to the chiller water pump operation during the low limit condition. The chiller water pump and chiller low limit
output de-energizes when the temperature rises 1 °F above the low limit setpoint.
A digital input is provided on the CCU1 to monitor the status of the chiller's general alarm. An alarm is reported to the
LCI when the chiller reports a general alarm condition.
The CCU1 monitors the runtime of all four pumps, the chiller, and the fan. When any one of the runtimes exceeds a
programmable limit, a maintenance alarm is reported to the LCI.
When the water temperatures exceed a programmable limit, a high limit alarm is reported to the LCI. When the water
temperature drops below a programmable limit, a low limit alarm is reported to the LCI. When the water temperature
returns to the proper range, a return to normal is generated.

iWorX CCU1
16 505-022, Effective: September 23, 2010
© 2010 Taco Electronic Solutions, Inc.
SEQUENCE OF OPERATION
This section describes the detailed sequence of operation for the CCU1 control algorithms.
Chiller Activation
CCU1 control starts only if there is a cooling water demand and the OAT acquired from the network via an auxiliary
sensor module (ASM) is above the OAT limits -> Lockout temp. The CCU1 operates in conjunction with up to 60 con-
trollers that can require chilled water (FCU series, DXU series, HPU series). The cooling water demand is obtained by
the CCU1 from controllers that have been associated with the CCU1 at the LCI user interface during configuration. The
CCU1 polls each associated controller to determine if cooling has been requested.
Cooling water demand can also be communicated to the CCU1 through a digital input switch or a demand for chiller
activation at the LCI. Activation through the digital input switch will not override an OAT limits -> Lockout temp condi-
tion. Activation through the LCI will override an OAT limits -> Lockout temp condition. Initial chiller control activates a
chiller water pump. The factory installed chiller control, as provided by the chiller manufacturer, detects chiller water
loop water flow and activates the chiller. An anti-cycle function provides configurable Chiller settings --> Min On Time
and Min Off Time.
Chiller Setpoint Adjustment
The CCU1 provides setpoint adjustment control of the chiller by integrating to the factory mounted chiller controls with
a 0-10 VDC setpoint control signal. The chiller setpoint adjustment provides the ability for the user to change the chilled
water supply setpoint through the LCI. The analog output has a user adjustable scaling range.
Chiller Pump Control
The CCU1 includes support for two chilled water pumps, with only one pump required for normal operation. One of the
pumps is designated the lead pump, with the lag pump only being required in the event of a lead pump alarm. Each
time the chiller is deactivated, the lead pump designation is transferred to the other pump.
When the system is activated, the lead chiller pump is started. If the chiller pump has been commanded on for at least
20 seconds and the chiller flow is off, an alarm is initiated and the lag pump is started. The lag pump also triggers an
alarm if it has been commanded on for 20 seconds and flow proof is not established. If both chiller pumps fail, all out-
puts are turned off, all control stops, and a dual pump failure alarm is generated. Manual reset of the CCU1 controller
from the operator interface or by cycling power to the CCU1 is required to restart control.
Condenser Pump Control
The CCU1 also includes support for two condenser water pumps, with only one pump required for normal operation.
One of the pumps is designated to be the lead pump, with the lag pump only being required in the event of a lead pump
failure. Each time the chiller is deactivated, the lead pump designation is transferred to the other pump.
When the chilled water pump is started, the lead condenser pump is started also. If the condenser pump has been
commanded on for at least 20 seconds and the condenser flow is off, an alarm is initiated and the lag pump is started.
The lag pump also triggers an alarm if it has been commanded on for 20 seconds and flow proof is not established. If
both condenser pumps fail, all outputs are turned off, all control stops, and a dual pump failure alarm is generated.
Manual reset of the CCU1 controller from the operator interface or by cycling power to the CCU1 is required to restart
control.
Cooling Tower Bypass Valve Control
The cooling tower bypass valve is controlled when the CCU1 is configured for a water cooled chiller. The bypass valve
position is calculated by a Proportional + Integral (P+I) control loop based on the condenser water return temperature
and the condenser water setpoint. The bypass valve control loop is activated 15 seconds after the condenser water
flow proof has confirmed flow.
As the temperature increases above the All Settings -> Cool Tower Valve SP, the bypass valve is modulated open. The
bypass valve is modulated closed as the water temperature decreases below the All Settings -> Cool Tower Valve SP.
The cooling tower bypass valve control loop is selectable for direct or reverse acting operation.

iWorX CCU1
505-022, Effective: September 23, 2010 17
© 2010 Taco Electronic Solutions, Inc.
To prevent the integral component from becoming too large, there is anti-wind up reset protection. This protection
clamps the integral value when all of the components add up to more than 100% or less than 0%. The following equa-
tions are used for P+I control:
KP= Proportional Gain
Ki= Integral Gain
Error = Inputs --> Cond Rtn Temp - All Settings --> Cool Tower Valve SP
I= I + (Kix Error)
Outputs --> Cooling Tower Valve (%) = (KPx (Error + I)) + 50.00%
The valve can be set for reverse action by exchanging the maximum and value settings during configuration. That is, if
the default maximum of 10 Volts and default minimum of 0 Volts are being used for reverse action, set the minimum to
10 Volts and the maximum to 0 Volts.
Cooling Tower Variable Speed Fan Control
The cooling tower variable speed fan is controlled when the CCU1 is configured for a water cooled chiller. The cooling
tower fan speed is calculated by a P+I control loop based on the condenser water return temperature and the cooling
tower water setpoint. The fan speed control loop is activated 15 seconds after the cooling tower bypass valve has mod-
ulated to its 100% position (full flow through tower).
As the temperature increases above the cooling tower water setpoint, the fan speed is increased. The fan speed is
decreased as the water temperature decreases below the Chiller settings --> setpoint. The fan speed control loop is
selectable for direct or reverse acting operation.
To prevent the integral component from becoming too large, there is anti-wind up reset protection. This protection
clamps the integral value when all of the components add up to more than 100% or less than 0%. The following equa-
tions are used for P+I control:
KP= Proportional Gain
Ki= Integral Gain
Error = Inputs --> Cond Rtn Temp - All Settings --> Cool Tower Valve SP
I= I + (Kix Error)
Outputs --> Cooling Tower Fan (%) = (KPx (Error + I)) + 50.00%
Figure 6: Cooling Tower Sequence
0%
100%
Condenser Return
Water Setpoint
T
ower W
ater Bypass Va l ve
Cooling T
ower Fan
Supply Water Temperature
The valve can be set for reverse action by exchanging the maximum and value settings during configuration.
Chiller Low Limit Control
The CCU1 provides low limit control. When the outside air temperature drops below the low limit setpoint as sensed by
the ASM on the network, the CCU1 energizes the chiller low limit output and starts the chilled water pump. The chiller
low limit output is interfaced to the factory supplied chiller controls to signal the chiller to not start in response to the
chilled water pump operation in the low limit condition. The chilled water pump and chiller low limit output de-energizes
when the temperature rises 1 °F above the low limit setpoint.

iWorX CCU1
18 505-022, Effective: September 23, 2010
© 2010 Taco Electronic Solutions, Inc.
Chiller Alarm Status
The chiller alarm status input is monitored to determine if the chiller is operating properly. The input is used to indicate
that an alarm occurred or maintenance is required on the chiller. The unit is not shut down due to a chiller alarm.
Runtime Accumulations
The total runtime is accumulated for the chiller at HVAC Setup -> Runtimes and Limits -> chiller Runtime, chiller pump
1 at HVAC Setup -> Runtimes and Limits -> chlr Pump 1 Runtime, chiller pump 2 at HVAC Setup -> Runtimes and Lim-
its -> chlr Pump 2 Runtime, condenser pump 1 at HVAC Setup -> Runtimes and Limits -> Cond Pump 1 Runtime, con-
denser pump 2 at HVAC Setup -> Runtimes and Limits -> Cond Pump 2 Runtime, and fan at HVAC Setup -> Runtimes
and Limits -> Fan Runtime. The runtimes can be used to indicate that maintenance is required on the equipment con-
trolled by these outputs. An operator or maintenance personnel can reset the runtime once servicing has been per-
formed. The runtimes are accumulated in non-volatile memory (NVRAM).
Alarms and Events
The controller detects certain alarm conditions and sends them to the LCI. Before this can occur, you must use the LCI
to configure the controller.
Digital Input Alarms
The CCU1 monitors the status of the digital inputs and generates alarms for the following events:
• Inputs --> Chiller General Alarm
Maintenance Alarm
A CCU1 provides programmable runtime limits for generating runtime maintenance alarms. When the Runtime Limits -
> chiller, Runtime Limits ->pump or Runtime Limits -> fan exceeds these limits, a maintenance alarm is sent to the LCI.
Water Temperature Alarms
After a 1 minute delay following chiller startup, the CCU1 generates high and low limit alarms for the monitored water
temperatures. A programmable water temperature alarm limit offset is provided. The temperature limits are calculated
based on the alarm limit setpoints and the alarm limit offset.
Chiller Temp High Limit = Chiller Settings -> Max Water Temp + Water Temp Alarm Hys
Chiller Temp Low Limit = Chiller Settings -> Min Water Temp - Water Temp Alarm Hys
When the measured water temperature exceeds the high limit, a high limit alarm is generated. When the water temper-
ature drops below the low limit, a low limit alarm is generated. A return to normal is generated when the water temper-
ature is between the high and low limit.
Pump Alarms
If the chiller pump has been commanded on for at least 20 seconds and the chiller flow proof is off, an alarm is initiated
and the lag pump is started. The lag pump also triggers an alarm if it has been commanded on for 20 seconds and flow
proof is not established. If both chiller pumps fail, all outputs are turned off, all control stops, and a dual pump failure
alarm is generated. Manual reset of the CCU1 controller from the operator interface or by cycling power to the CCU1 is
required to restart control.
If the condenser pump has been commanded on for at least 20 seconds and the condenser flow proof is off, an alarm
is initiated and the lag pump is started. The lag pump also triggers an alarm if it has been commanded on for 20 sec-
onds and flow proof is not established. If both condenser pumps fail, all outputs are turned off, all control stops, and a
dual pump failure alarm is generated. Manual reset of the CCU1 controller from the operator interface or by cycling
power to the CCU1 is required to restart control.

iWorX CCU1
505-022, Effective: September 23, 2010 19
© 2010 Taco Electronic Solutions, Inc.
Automatic Configuration
The CCU1 and iWorX Local Control Interface (LCI) use a self-configuring network management scheme requiring no
external tools, binding, or LONWORKS knowledge. The LCI recognizes and configures the CCU1 when the controller’s
service pin is pressed. The controller’s status light flashes green until the controller is configured, and will be solid
green after the controller is configured. Once the service pin has been pressed, no further action is required by the
user; the controller is fully accessible to the LCI. Users may bind to SNVTs on the CCU1 with LNS or other LONWORKS
tools if they wish.
The LCI also provides network supervision of the CCU1. The LCI periodically sends a "ping" message to the CCU1,
which elicits a response. If the response fails, an alarm is displayed on the LCI. The LCI also uses the "ping" message
to refresh the occupancy mode and other system wide data.
Networking Controllers
Associations can only be done in a network with an LCI2 present. Please refer to the iWorX LCI2 Application Manual
for detailed instructions.
CCU1 can be associated and communicate with other controllers. CCU1 can receive the cooling demands form asso-
ciated control.
Following is a list of the controllers that can be associated with the CCU1.
•DXUseries
•HPUseries
• FCU series
To associate a CCU1 to controllers, start from the LCI main screen; press Controllers and then select the CCU1. From
within the CCU1, select HVAC Setup and then press the Members button. Once the members screen appears, a list of
controllers that the CCU1 can be grouped to will be shown. Press the name of the controller to associate. The selected
controller will turn “RED” color and “Associated” status will be displayed on the right side. To change the member status
of a controller, just press that controller. It will toggle “Member” or “Non-Member” with each press. If a controller has
been selected or deselected, you must press Save afterward to confirm the new setting.

iWorX CCU1
20 505-022, Effective: September 23, 2010
© 2010 Taco Electronic Solutions, Inc.
CONTROLLER IDENTIFICATION
Once the CCU1 is properly installed and recognized by the Local Control Interface (LCI), the LCI can be used to con-
figure the settings of the controller. This section describes the commands available on the LCI for configuration of the
CCU1, and the meanings and default values for controller parameters. For more information on using the LCI, see the
iWorX LCI Application Guide.
Inputs
The Inputs screen displays the current values of the CCU1’s inputs. These values cannot be changed.
Outputs
This screen displays the current values of the CCU1’s outputs. These values cannot be changed.
Input Range Description
Outside Temp -30.00 to 230.00 °F (-34.4 to 110.00 °C) Outside air temperature reported
by an external temperature sensor
over the network.
Chiller Flow Off, On Status of the CFP switch.
Condenser Flow Off, On Status of the CDFP switch.
Chlr General Alarm Off, On Status of the chiller’s alarm output.
Cooling Water Demand Off, On Status of the CWD switch.
Chiller Supply Temp -30.00 to 230.00 °F (-34.40 to 110.00 °C) Temp. reported by CWS sensor.
Chiller Return Temp -30.00 to 230.00 °F (-34.40 to 110.00 °C) Temp. reported by CWR sensor.
Condenser Supply Temp. -30.00 to 230.00 °F (-34.40 to 110.00 °C) Temp. reported by CDS sensor.
Condenser Return Temp. -30.00 to 230.00 °F (-34.40 to 110.00 °C) Temp. reported by CDR sensor.
Occupancy Mode Unocc, Occ Indicates the current occupancy
mode.
Output Range Description
Unit Status
Mode Off, Cooling Current mode of the chiller system.
Cooling Tower Valve 0.00% to 100.00% Status of the cooling tower valve output.
Cooling Tower Fan 0.00% to 100.00% Status of the cooling tower fan output.
In Alarm? On, Off Current alarm status of the chiller.
Output Status
Chiller Pump 1 Off, On Status of chiller pump 1.
Chiller Pump 2 Off, On Status of chiller pump 2.
Condenser Pump 1 Off, On Status of condenser pump 1.
Condenser Pump 2 Off, On Status of condenser pump 2.
Chiller Low Limit Off, On Status of the chiller low limit output.
This manual suits for next models
1
Table of contents
Other iWorX Controllers manuals
Popular Controllers manuals by other brands

Elan
Elan Z-880 installation manual
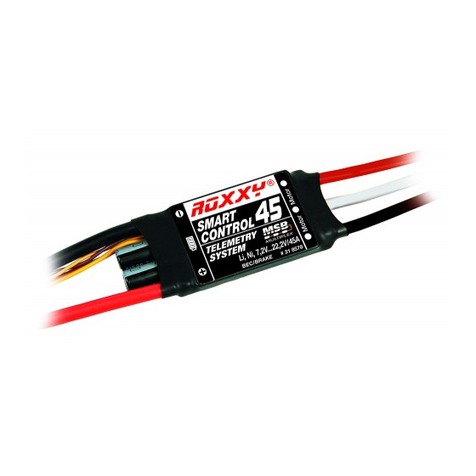
Multiplex
Multiplex ROXXY PROcontrol Series manual
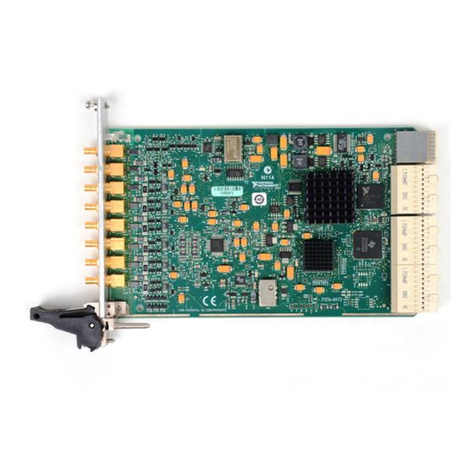
National Instruments
National Instruments Network Adapter NI PXIe-6672 installation guide
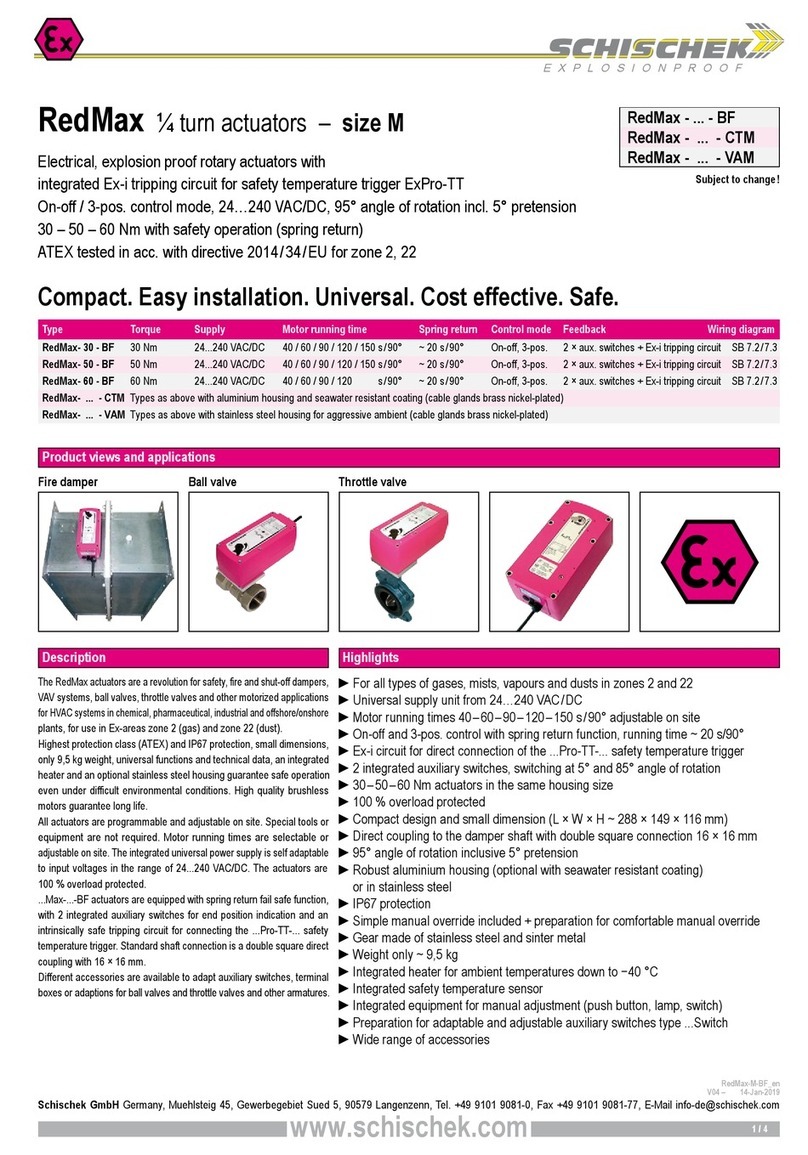
Schischek
Schischek RedMax BF Series quick start guide
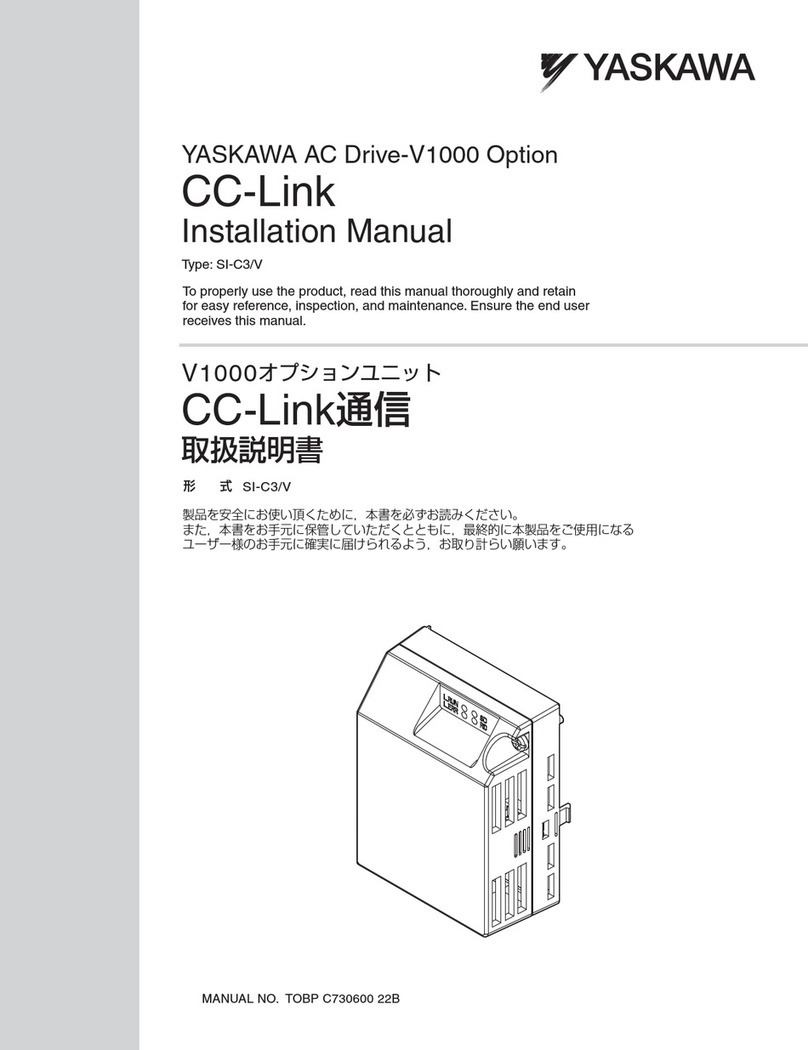
YASKAWA
YASKAWA PROFINET V1000 installation manual
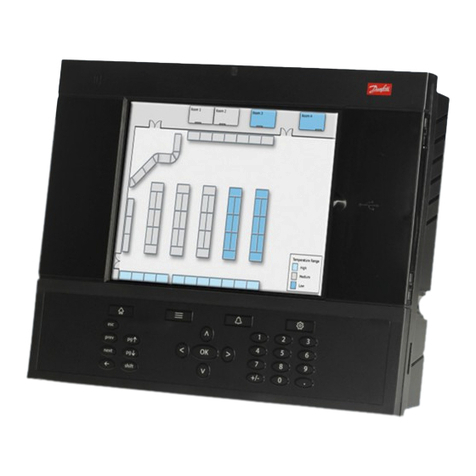
Danfoss
Danfoss AK-SM 800 Quick reference guide