Jäger Z80-K450.102 S5 User manual

Manual
Z80-K450.102 S5
High Frequency Spindle
Pneumatic taper change

Item no. 10404239, Revision 002 ( 40 )
Identification of HF spindle
Spindle type
Pmax S6-60% S1-100%
Item no. .... Serial no.
Rated rotation speed
Serial no.
Item no.
Performance data
Spindle type
As we always ensure that our HF spindles are at the cutting edge of techno-
logical development, we reserve the right to make technical modifications
and variations from the exact design described in the manual.
The text in this manual has been compiled with the utmost care. However, Al-
fred Jäger GmbH cannot assume any legal responsibility or liability of any
kind for incorrect information and any consequences thereof.
Translations and reproductions – including of extracts – are prohibited with-
out the express written approval of Alfred Jäger GmbH.

Item no. 10404239, Revision 00 3 ( 40 )
Contents:
Translation of the original manual
1 Preliminary information 5
1.1 Purpose of the manual ...................................................... 5
1.2 Explanation of symbols used .......................................... 5
2 Transport and packaging 6
2.1 Scope of supply of HF spindle ........................................ 6
2.1.1 Service set................................................................. 6
2.1.2 Optional accessories............................................. 6
2.1.3 Documentation supplied.................................... 7
2.2 Packaging of HF spindle.................................................... 7
3 Designated use 8
3.1 Permissible types of machining ..................................... 8
3.2 Permissible materials ......................................................... 8
4 Safety instructions 9
4.1 Safe working........................................................................10
4.2 Shutdown of HF spindle .................................................11
4.3 Installation and maintenance .......................................11
4.4 Modification and repair...................................................11
4.5 Improper operation..........................................................11
5 Technical description 12
5.1 Connections of HF spindle.............................................12
5.2 Electrical connection........................................................12
5.3 Cooling..................................................................................13
5.4 Sealing air.............................................................................13
5.5 Taper cleaning....................................................................13
5.6 Pneumatic tool change ...................................................13
6 Technical Specifications 14
6.1 Dimensions..........................................................................15
6.2 Motor data ...........................................................................16
6.2.1 Performance Diagram........................................17
6.2.2 Equivalent circuit diagram data .....................17
Parameter.............................................................................18
6.3 Wiring diagram...................................................................19
6.4 Motor protection PTC 130°C..........................................20
6.5 Speed sensor (digital differential magneto resistor)
..................................................................................................21
6.6 Air-borne noise emissions..............................................21
7 Operating location 22
8 Installation 23
8.1 Installing the HF spindle .................................................23
8.2 Diameter of media supply line .....................................23
8.3 Cooling water......................................................................24
8.3.1 Quality of cooling water....................................24
8.3.2 Setting the cooling..............................................24
8.4 Compressed air...................................................................25
8.4.1 Air purity classes (ISO 8573-1).........................25
8.4.2 Setting the sealing air ........................................25
8.4.3 Setting values........................................................26
9 Commissioning 26
9.1 Running-in schedule ........................................................26
9.2 Daily start-up.......................................................................27
9.3 Shutdown signal................................................................27
9.4 Commissioning after storage........................................27
10 Tool change 28
10.1 Clockwise..............................................................................28
10.2 Pneumatic taper change ................................................28
10.2.1 Changing the tool................................................29
10.3 Tool changing station (optional accessory).............30
10.3.1 pneumatic taper change...................................30
10.3.2 Installing the changing station.......................30
10.3.3 Maintenance..........................................................30
11 Tools for high speed cutting 31
12 Maintenance 32
12.1 Ball bearings........................................................................32
12.2 Daily cleaning .....................................................................32
12.2.1 Before commencing work ................................32
12.2.2 With every tool change .....................................33
12.2.3 Every time the clamping device is changed
....................................................................................33
12.3 In the case of storage.......................................................33
12.4 Monthly maintenance .....................................................33
12.5 Long periods of storage..................................................33
12.6 Maximum storage time...................................................33
13 Dismantling 34
13.1 Disposal and environmental protection...................34
14 Service and repairs 35
14.1 Service partners .................................................................35
14.2 Malfunctions........................................................................36
15 Declaration of Incorporation 39

Contents:
Item no. 10404239, Revision 004 ( 40 )

Preliminary information
Item no. 10404239, Revision 00 5 ( 40 )
1 Preliminary information
The high frequency spindle (HF spindle) is a high quality precision tool for
high speed machining.
1.1 Purpose of the manual
The manual is an important component of the HF spindle.
ÜStore the manual carefully.
ÜMake the manual available to all persons who work with the HF spindle.
ÜRead the documentation supplied in full.
ÜBefore carrying out any work, read the corresponding section of the man-
ual carefully again.
1.2 Explanation of symbols used
To enable quick classification of information, this manual uses visual aids in
the form of symbols and text markings.
Notes are marked with a signal word and a colored box:
DANGER
Dangerous situation!
Results in serious injury or death.
uMeasure to avert the danger.
WARNING
Dangerous situation!
May result in serious injury or death.
uMeasure to avert the danger.
CAUTION
Dangerous situation!
May result in minor to moderate injury.
uMeasure to avert the danger.
Note
May result in material damage. This warning symbol is not a warning for per-
sonal injury.
Tip
Tips indicate useful information for users.

Transport and packaging
Item no. 10404239, Revision 006 ( 40 )
2 Transport and packaging
Avoid strong vibrations or impacts during transportation, as these could dam-
age the ball bearings of the HF spindle.
ÜAny damage reduces the accuracy of the HF spindle.
ÜAny damage restricts the functionality of the HF spindle.
ÜAny damage shortens the service life of the HF spindle.
2.1 Scope of supply of HF spindle
The following parts are supplied with the HF spindle:
qHigh Frequency Spindle
qTool taper
qService set
qC-wrench
qTransport packaging
ÜCheck the high frequency spindle for completeness upon delivery.
2.1.1 Service set
qFelt cleaning taper
qCollet grease
2.1.2 Optional accessories
Available on request:
qSpindle holder
qFrequency converter
qChiller
qCollet
qFurther accessories on request.
Only approved accessories have been tested for operational safety and func-
tionality.
ÜDo not use any other accessories – this may invalidate any warranty claims
and compensation claims for damages.
ÜIf the spindle holder is to be produced in-house, it is essential to contact
Alfred Jäger GmbH before starting production to request the tolerances
and production plan for the spindle holder.

Transport and packaging
Item no. 10404239, Revision 00 7 ( 40 )
2.1.3 Documentation supplied
The documents listed below are supplied with the HF spindle:
qManual
qThe declaration of incorporation is part of the manual.
qInspection protocol
ÜCheck that the documentation supplied is complete when the spindle is
delivered. If necessary, request a new copy.
2.2 Packaging of HF spindle
All transport packaging materials can be recycled in appropriate disposal facil-
ities.

Designated use
Item no. 10404239, Revision 008 ( 40 )
3 Designated use
The HF spindle is an “incomplete machine” in accordance with the Machinery
Directive and cannot perform any function independently. The HF spindle can
only be operated in conjunction with a machine tool and a frequency con-
verter.
3.1 Permissible types of machining
The HF spindle has been developed only for the following types of machining.
qCutting
qDrilling
qEngraving
qGrinding
ÜContact Alfred Jäger GmbH if other types of machining are required.
3.2 Permissible materials
The HF spindle has been developed only for the following materials.
qMetals (such as alloys, cast metals etc.)
qSintered materials
qPlastics
qWood
qGraphite
qStone (marble, etc.)
qPaper and cardboard
qCircuit boards
qGlass and ceramic
ÜContact Alfred Jäger GmbH if other materials are to be machined.

Safety instructions
Item no. 10404239, Revision 00 9 ( 40 )
4 Safety instructions
The high frequency spindle is a state of the art product and is safe to operate.
However, the HF spindle may pose a risk in the following cases:
qIf it is installed by untrained personnel.
qIf it is used incorrectly.
qIf it is not used in accordance with its intended use.
The high frequency spindle may only be installed, commissioned, and main-
tained by specialist personnel.
Definition: Specialist personnel are persons who are familiar with the assem-
bly, installation, commissioning, and operation of the product and have the
relevant qualifications for their area of activity. The operator must closely con-
trol the responsibility, training, and monitoring of these personnel.
DANGER: Due to explosion.
HF spindles are not approved for use in areas at risk of explosion. Use in such
areas may result in explosions.
uDo not use the HF spindle in potentially explosive atmospheres.
DANGER: Due to flying parts.
The HF spindle operates at high speeds and may therefore be flung away by
these.
uOperate the HF spindle only if it is installed in the machine or system in a
fixed manner.
Note: Adhere to the limit values.
uObserve the limit values specified in the technical data.
Note: Take account of the machine.
uObserve the manual of the machine in which the HF spindle is installed.
uObserve all safety instructions specified by the machine manufacturer.
uEnsure that the machine does not cause any hazards (e.g. uncontrolled
movements). Do not install the HF spindle in the machine until this has
been done.
Note. Do not damage the HF spindle.
uAny damage reduces the accuracy of the HF spindle.
uAny damage restricts the functionality of the HF spindle.
uAny damage shortens the service life of the HF spindle.

Safety instructions
Item no. 10404239, Revision 0010 ( 40 )
4.1 Safe working
Observe all safety instructions set out in the manual, the applicable national
accident prevention regulations, and the valid company work, operation, and
safety guidelines.
DANGER: Due to flying parts.
Tools that are not clamped correctly will be flung away by the centrifugal
forces that occur during machining.
uUse the full clamping depth of the collet.
uClamp the tool securely.
DANGER: Due to flying parts.
If the wrong rotational direction is used, the clamping system releases and
the tool is flung away.
uIt is essential to adhere to the rotational direction of the HF spindle.
WARNING: Risk of injury due to flying parts.
The HF spindle operates at high speeds which may cause chips to fly out
with great force.
uNever remove the protective devices of the machine or system.
uAlways wear protective goggles during work.
Exampleofdesign: Inserting the
shank
Note: Ensure functionality.
uNever operate the HF spindle without a clamped tool shank.
If no tool shank is clamped:
qThe clamping system is damaged by the centrifugal forces.
qThe clamping system is shifted.
qThe balance of the HF spindle is affected.
qThe bearing is damaged.
ÜTake the relevant measures to protect against splashes and spray accord-
ing to the type of machining, the type of material being machined, and the
type of tool selected.
ÄObserve the manual of the machine in which the HF spindle is installed.
ÜObtain the maximum circumferential speeds of the tools used from the
tool supplier.
Single-point tools are not suitable for high speed cutting.
If they are required for production reasons:
ÜOnly use a balanced tool.
ÄDIN ISO 1940
ÄBalance grade 2,5

Safety instructions
Item no. 10404239, Revision 00 11 ( 40 )
The tool cutting diameter (X) must not be greater than the maximum
clamping range (Y).
ÜAlways clamp the tool so that it is as short as possible.
ÜKeep the dimension (Z) small.
Ä(Y) See section: Technical Specifications [}14].
4.2 Shutdown of HF spindle
The procedure for shutting down the high frequency spindle for installation
and maintenance work is as follows:
ÜCompletely disconnect the power supply.
ÜCompletely disconnect the media supply (air and liquid).
ÜMake sure that the shaft of the HF spindle has come to an absolute stand-
still.
If the HF spindle is being shut down to be cleaned:
ÜReconnect only the sealing air and the taper cleaning air.
Tip: Forward the data to the controller.
uUse the option on the frequency converter of detecting the shutdown
signal from the shaft and forwarding this to the machine controller for
evaluation.
4.3 Installation and maintenance
ÜCarry out installation, cleaning, and maintenance work only after shutting
down the HF spindle and after the shaft has come to a standstill.
ÜInstall all safety and protective devices of the machine immediately after
completing work.
4.4 Modification and repair
Modifications or alterations to the HF spindle are only permitted after prior
consultation with Alfred Jäger GmbH.
Only the service partners listed in the “Service and repair [} 35]” section are
authorized to open and repair the HF spindle.
Only approved accessories have been tested for operational safety and func-
tionality.
4.5 Improper operation
The high frequency spindle is only safe to operate for its designated use.
ÜObserve the safety instructions in all sections of the manual to prevent
hazards to persons, the environment, the machine, or the HF spindle itself.
Failure to observe the safety instructions may invalidate any warranty claims
and compensation claims for damages.

Technical description
Item no. 10404239, Revision 0012 ( 40 )
5 Technical description
5.1 Connections of HF spindle
41
37
2
2
1Electrical connection
2Cooling water G 1/8"
3Sealing air G 1/8"
4Taper cleaning G 1/8"
7Pneumatic system for tool change G 1/8"
5.2 Electrical connection
The HF spindle may only be operated with a frequency converter (FC).
ÜCheck whether the current, voltage, and frequency data of the HF spindle
match the raw data for the frequency converter.
ÜUse a motor supply line that is as short as possible.
ÜAdjust the speed of the HF spindle using the FC.
ÜRefer to the frequency converter manual for further information.
The FC detects the following operating states of the HF spindle, depending on
the version:
qHF spindle rotating.
qHF spindle too hot.
qHF spindle at a standstill, etc.
The FC forwards the operating states of the HF spindle to the machine con-
troller.
Note: Connect the SpeedTEC quick locking connector.
uFor the combination SpeedTEC connector plug/SpeedTEC cable plug:
uRemove the O ring on the SpeedTEC connector plug.

Technical description
Item no. 10404239, Revision 00 13 ( 40 )
5.3 Cooling
Liquid cooling keeps the HF spindle at a constant temperature during opera-
tion.
Note: Extension of the service life through heat dissipation.
Heat is produced during operation of the HF spindle. The temperature of the
HF spindle should not exceed + 45° C as this shortens the service life of the
bearing.
uCheck the temperature of the HF spindle on the housing.
5.4 Sealing air
For guidelines on air quality,
see "Air purity classes (ISO
8573-1) [}25]" section.
The sealing air prevents foreign bodies such as chips and liquids (e.g. emul-
sions) from entering the HF spindle.
ÜCheck that air escapes at the front between the housing and the rotating
parts of the HF spindle.
5.5 Taper cleaning
For guidelines on air quality,
see "Air purity classes (ISO
8573-1) [}25]" section.
Taper cleaning prevents chips and liquids from entering the shaft during a
tool change and causing contamination and damage to the inner taper and
the clamping system.
5.6 Pneumatic tool change
For guidelines on air quality,
see "Air purity classes (ISO
8573-1) [}25]" section.
The tool change or tool taper change is performed pneumatically.
During this, a mechanism is operated inside the HF spindle which clamps, re-
leases, or ejects the tool taper or collet.

Technical Specifications
Item no. 10404239, Revision 0014 ( 40 )
6 Technical Specifications
Bearings Hybrid ball bearing (pcs) 2
Lifetime lubricated maintenance free
Power values
Liquid cooled
Pmax./5s S6-60% S1-100%
Rated power 3,2 2,5 2,3 [kW]
Torque 0,68 0,53 0,47 [Nm]
Voltage 167 167 167 [V]
Current 15,9 12,9 12 [A]
Motor data Motor technology 3-phase asynchronous drive
(no brushes or sensors)
Frequency 833 Hz
Motor poles (pairs) 1
Rated rotation speed 50.000 rpm
Acceleration/braking value
Per second
10 000 rpm
(other values by consultation)
Characteristics Speed sensor Differential magneto resistor (TTL)
Number of signals = 6
Motor protection PTC 130°C
Housing Stainless steel
Housing diameter 80 mm
Cooling Liquid cooled
Ambient temperature + 10°C … + 45°C
Sealing air
Protection category
(sealing air turned on) IP54
Taper cleaning
Tool change Pneumatic taper change
Tool Holder WK 19
Collet type D8
Optional accessories
Clamping range up to 8 mm (5/16" )
Clockwise
Coupler plug 9-pin (SpeedTEC)
Weight ~ 5,3 kg
Inner taper run out < 1 µ

Technical Specifications
Item no. 10404239, Revision 00 15 ( 40 )
Axial run-out < 1 µ
6.1 Dimensions
(*) = Clamping range

Technical Specifications
Item no. 10404239, Revision 0016 ( 40 )
6.2 Motor data
The power values (S1, S6, S2)
are valid for sinusoidal cur-
rents and voltages.
The power values of the HF
spindle are dependent on the
frequency converter used and
may vary from the indicated
values.
Spindle characteristic curve 3704
Motor technology AC Motor
Motor type ACM 48/30/45-2E
Rated power 2,3 kW
Rated rotation speed 50.000 rpm
Cooling Liquid cooled
Motor protection PTC 130°C
Winding resistance (phase-phase) 0,427 Ω
Power dissipation 383 W – max. (S1)
Measured values: S1-100%
Rated rotation speed 5 000 10 000 20 000 30 000 40 000 50 000 rpm
Speed 2 875 8 823 18 500 28 507 38 515 48 522 rpm
Frequency 83 167 333 500 667 833 Hz
Rated power 0,134 0,43 0,91 1,36 1,800 2,242 kW
Torque 0,446 0,466 0,47 0,46 0,45 0,441 Nm
Voltage 24 44 73 104 135 167 V
Current 12 11,9 11,9 11,8 11,8 11,7 A
cos φ 0,96 0,82 0,83 0,82 0,8 0,79
Measured values: S6-60%
Rated rotation speed 5 000 10 000 20 000 30 000 40 000 50 000 rpm
Speed 3 527 8 490 18 277 28 278 38 625 48 279 rpm
Frequency 83 167 333 500 667 833 Hz
Rated power 0,16 0,469 0,989 1,483 1,980 2,471 kW
Torque 0,433 0,526 0,512 0,504 0,49 0,489 Nm
Voltage 24 44 73 104 136 167 V
Current 10,9 12,9 12,9 12,9 12,8 12,8 A
cos φ 0,93 0,86 0,85 0,83 0,82 0,8

Technical Specifications
Item no. 10404239, Revision 00 17 ( 40 )
Measured values: S2-Pmax./5 s
Rated rotation speed 5 000 10 000 20 000 30 000 40 000 50 000 rpm
Speed 3 503 8 046 17 972 27 995 38 017 48 040 rpm
Frequency 83 167 333 500 667 833 Hz
Rated power 0,177 0,574 1,217 1,867 2,52 3,167 kW
Torque 0,483 0,681 0,647 0,64 0,63 0,63 Nm
Voltage 24 44 73 104 136 167 V
Current 12 15,9 15,8 15,8 15,8 15,8 A
cos φ 0,93 0,92 0,88 0,86 0,85 0,83
Note on operation with static frequency converters:
For operation with a frequency converter, the effective fundamental voltage
must correspond to the specified motor voltage.
The measured currents may be greater than the specified values due to the
harmonic content.
6.2.1 Performance Diagram
6.2.2 Equivalent circuit diagram data

Technical Specifications
Item no. 10404239, Revision 0018 ( 40 )
Note: Damage due to incorrect performance data.
The values of the parameters relate exclusively to the motor.
uHF spindle values: See tables S1-100%, S6-60% and S2-Pmax.
Parameter*Meaning Value Unit
p0304 Rated voltage (phase-phase) 167,4 Vrms
p0305 Rated current 11,7 Arms
p0307 Rated power 2,252 kW
p0308 Rated power factor 0,79 cos φ
p0310 Rated frequency 833 Hz
p0311 Rated speed 48.522 rpm
--- Rated power loss 383 W
--- Rated rotation speed 0,441 rpm
p0312 Rated torque 0,441 Nm
p0314 Motor poles (pairs) 1 ---
p0320 Rated magnetization current 6,46 Arms
p0322 Maximum speed 60.000 rpm
p0326 Stalling torque correction factor 100 %
p0335 Cooling type Liquid cooled
p0341 Moment of inertia 0,000121 kgm²
p0348 Field weakening operating speed VDC=600V 71.820 rpm
p0350 Stator resistance, cold (strand) 0,427 Ω
p0353 Series inductance (strand) 0 mH
p0354 Rotor resistance, cold 0,241 Ω
p0356 Stator stray inductance 0,098 mH
p0358 Rotor stray inductance 0,141 mH
p0360 Main inductance 2,601 mH
p0604 Motor temperature warning threshold 110 °C
p0605 Motor temperature fault threshold 130 °C
p0640 Current limit 16 Arms
p1800 Pulse frequency 16 kHz
--- DC link voltage VDC
--- Series capacitance µF
--- Maximum voltage V
--- Idle reduction %
--- Stator stray reactance X1 0,514 Ω
--- Rotor stray reactance X2 0,739 Ω
--- Main field reactance Xh 13,618 Ω
(*) Parameters for Siemens SINAMICS 120

Technical Specifications
Item no. 10404239, Revision 00 19 ( 40 )
6.3 Wiring diagram
Note: Do not change the ex-works configuration.
Any change may cause overvoltage on the electrical components (e.g. PTC,
differential magneto resistor).
g
f
e
d
c
b
a
4 5 6
1 32
a
b
c
d
e
f
g
Bl.von 1
Ü b e r s e t z u n g e n , V e r vi e l f ä l t i g u n ge n u n d d i e W e i te rg a be a n D r i t te , a u c h n u r a us z ug sw e i se ,
i s t o h n e s c h r i f t l i c h e G e h n e h m i g u n g d e r F a . A l f r e d J ä g e r G m b H u n t e rs ag t
Datum
Gepr.
Bearb.
Norm System Technologie
Blatt 1
1.0
Projekt Nr.:
Version Nr.:
Zeichn.Nr.:
18.07.2008
Pinbelegung FS9 M (FP, PTC)
29025570
Alfred Jäger GmbH
Siemensstraße 8
61239 Ober Mörlen
G
E
Spindelstecker FS9M
Spindle plug FS9M
C
B
A
D
H
F
L
siehe Tabelle / see chart
grün-gelb
green-yellow
siehe Tabelle / see chart
siehe Tabelle / see chart
siehe Tabelle / see chart
siehe Tabelle / see chart
gelb
yellow
grün
green
W
VStator
Stator
U
DFP
Digitale Feldplatte
Differential magneto resistor
0,75 mm²
0,14 mm²
0,14 mm²
U
V
W
PIN 3/7-4 pole 4/7-2 pole
2/7-2 pole
2/4-2 pole
3/7-2 pole
AC 7.01-2
PTC+
PTC-
AC 8.01-4
C
B
A
G
blau 0,14mm²
blue 0.14mm²
blau 0,14mm²
blue 0.14mm²
blau 0,14mm²
blue 0.14mm²
rot 0,14mm²
red 0.14mm²
rot 0,14mm²
red 0.14mm²
rot 0,14mm²
red 0.14mm²
blau 0,25mm²
blue 0.25mm²
blau 0,25mm²
blue 0.25mm²
blau 0,25mm²
blue 0.25mm²
weiß 0,20mm²
white 0.20mm²
weiß 0,22mm²
white 0.22mm²
weiß 0,25mm²
white 0.25mm²
braun 0,22mm²
brown 0.22mm²
grün 0,20mm²
green 0.20mm²
lila 0,22mm²
purple 0.22mm²
schwarz 0,5mm²
black 0.5mm²
blau 0,5mm²
blue 0.5mm²
braun 0,5mm²
brown 0.5mm²
blau 0,25mm²
blue 0.25mm²
blau 0,25mm²
blue 0.25mm²
blau 1mm²
blue 1mm²
braun 1mm²
brown 1mm²
schwarz 1mm²
black 1mm²
rot 0,25mm²
red 0,25mm²
rot 0,20mm²
red 0,20mm²
E
Kundenseite
Customer side
Rückseite
Back side
A
B C
E
G
H
F
L
D
G
PTC+
L
---
---
F
Signal Feldplatte
Signal transmitter
C
Motorphase W
Motor phase W
B
Motorphase V
Motor phase V
A
Motorphase U
Motor phase U
D
PE Schutzleiter
PE conductor
E
PTC Masse
PTC earth
H
Feldplatte Masse
Transmitter earth
Kundenseite
Customer side
PTC
PTC

Technical Specifications
Item no. 10404239, Revision 0020 ( 40 )
6.4 Motor protection PTC 130°C
PTC thermistor with protective insulation
Characteristic curves for rated response temperatures 90°C to 160°C in accor-
dance with DIN VDE V 0898-1-401.
Positive temperature coefficient
thermistor resistance (RPTC)
according to the positive
temperature coefficient thermistor
temperature (TPTC) (small-signal
resistance).
Technical Specifications
Type M135
Max. operating voltage (TA = 0 … 40°C) Vmax.30 V
Max. measuring voltage (TA – 25 K … TNAT + 15 K) VMeas, max 7.5 V
Nominal resistance (VPTC ≤ 2.5 V) RN ≤ 250 Ω
Insulation test voltage Vis 3 kV~
Response time ta< 2.5 s
Operating temperature range (V=0) Top -25/+180°C
Resistance values
TNAT ±ΔT R (TNAT – ΔT)
(VPTC ≤ 2.5 V)
R (TNAT – ΔT)
(VPTC ≤ 2.5 V)
R (TNAT + 15 K)
(VPTC ≤ 7.5 V)
R (TNAT + 23 K)
(VPTC ≤ 2.5 V)
130 ±5°C ≤ 550Ω ≥ 1330Ω ≥ 4kΩ ----
Table of contents
Other Jäger Engine manuals
Popular Engine manuals by other brands
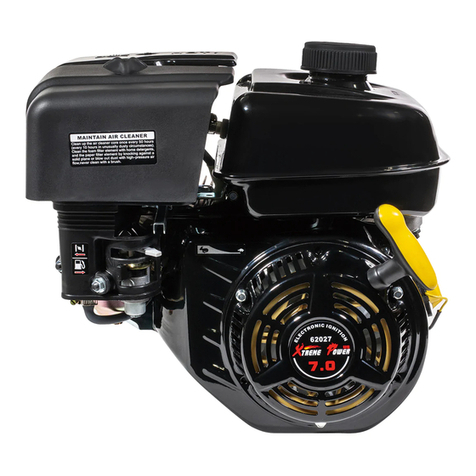
Xtreme Power
Xtreme Power 62027 owner's manual
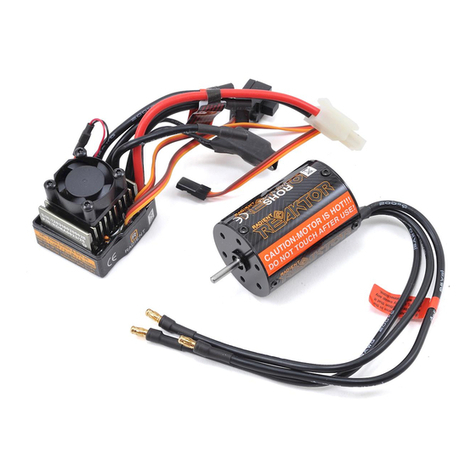
Radient RC
Radient RC Reaktor owner's manual
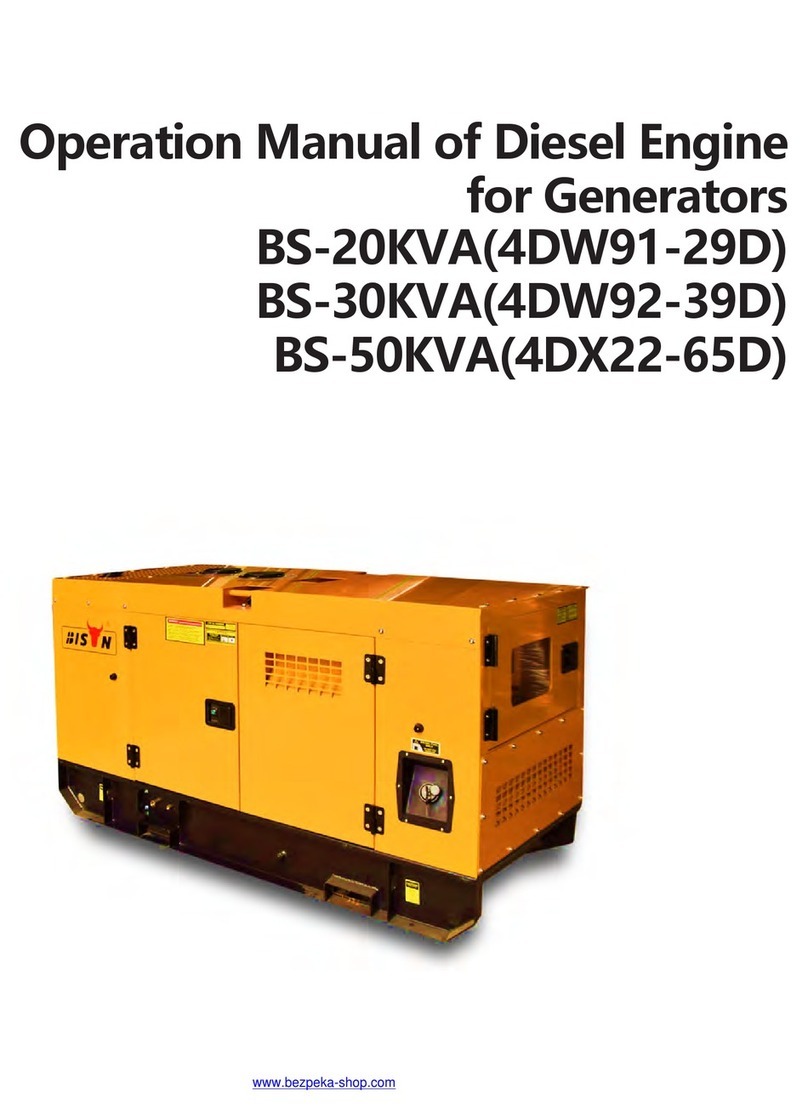
Bison
Bison BS-20KVA Operation manual

Toshiba
Toshiba Stainless Steel Washdown Duty Motor Toshwash... Brochure & specs
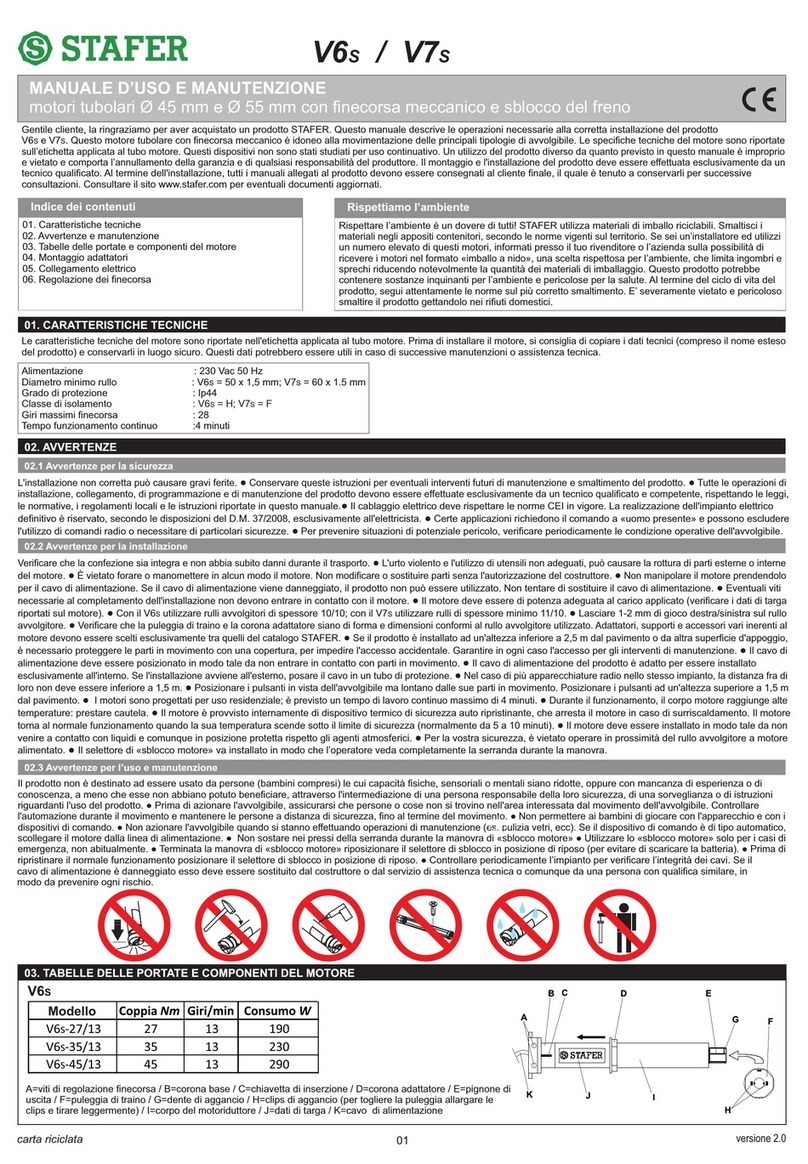
Stafer
Stafer V6S-27/13 user manual

GEIGER
GEIGER GJ5606-DuoDrive Original assembly and operating instructions

MINN KOTA
MINN KOTA ULTREX installation instructions
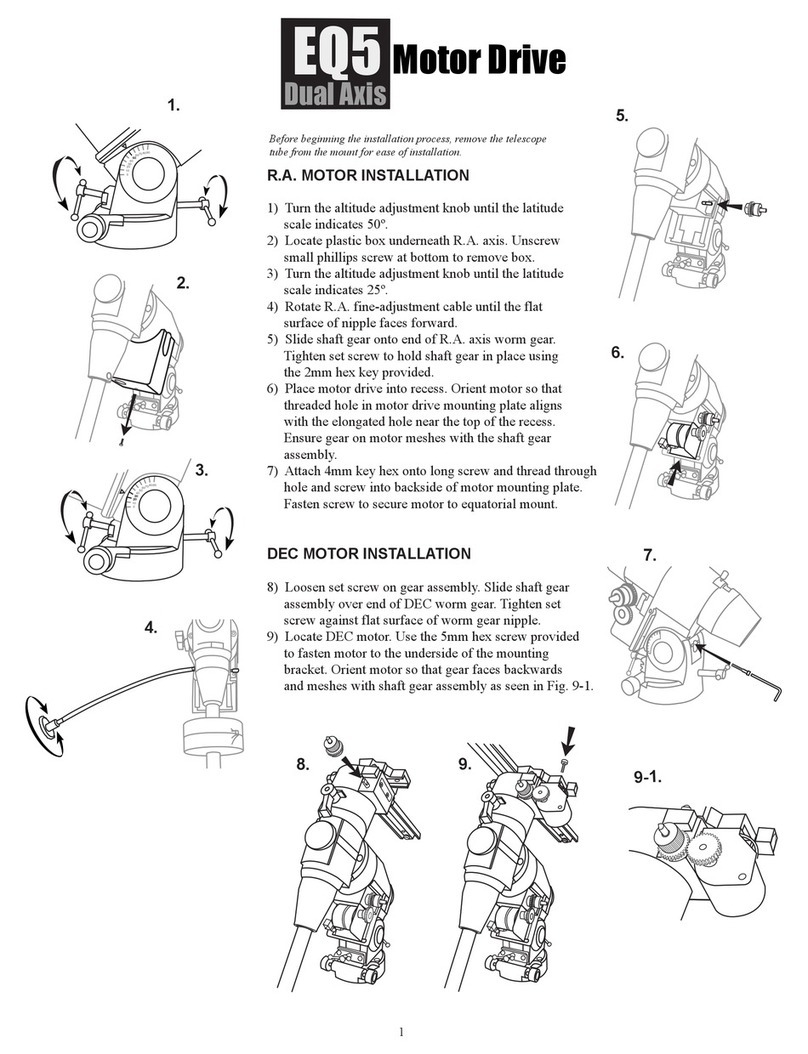
SKY-WATCHER
SKY-WATCHER EQ5 quick start guide
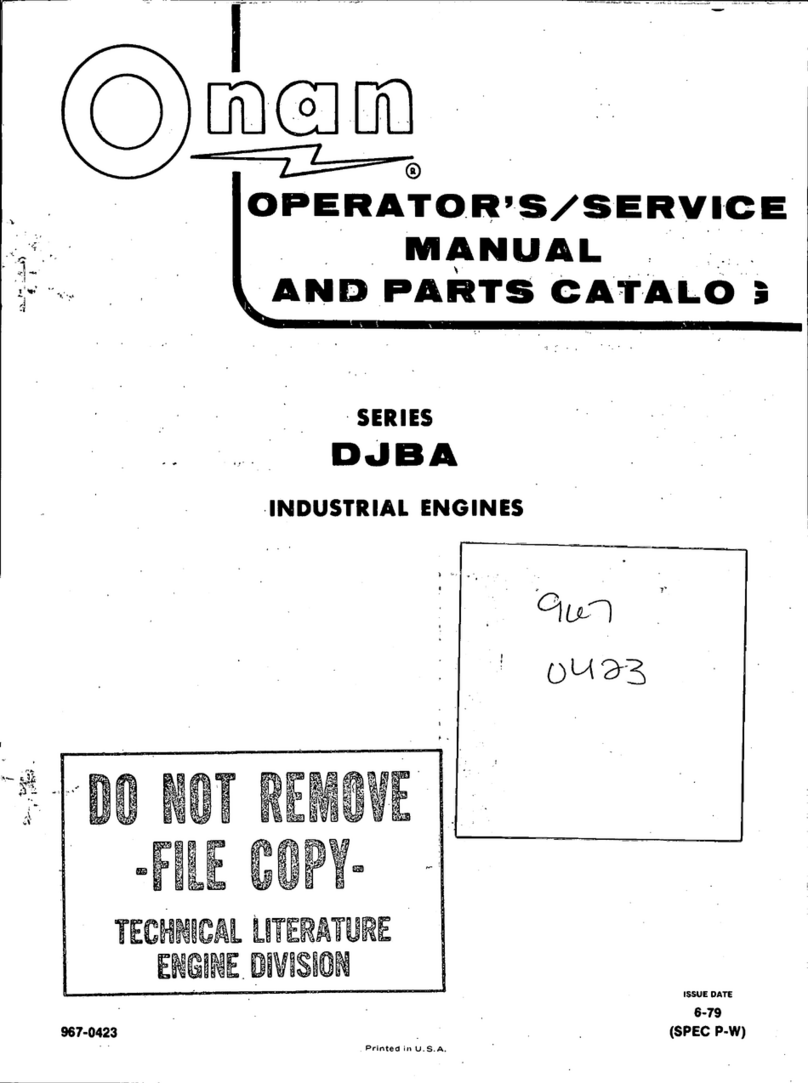
Onan
Onan DJBA Series Operator's/Service Manual and Parts Catalog
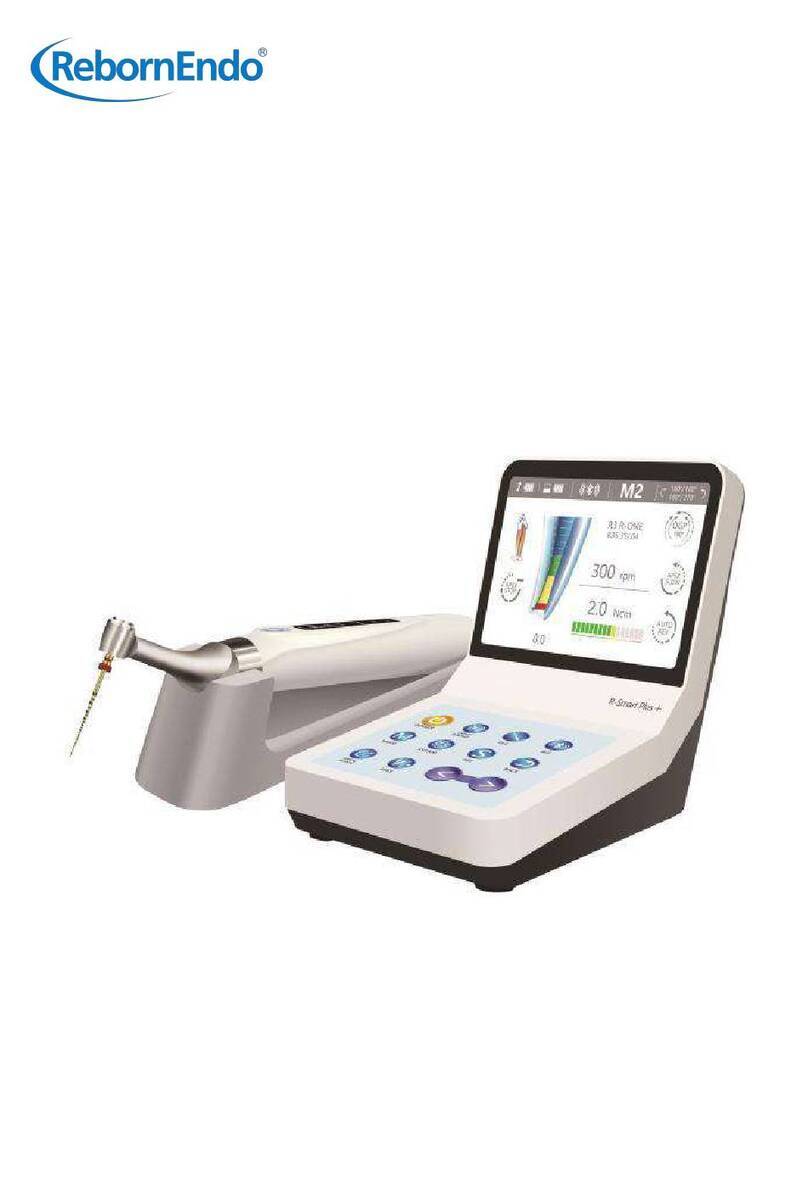
Reborn Endo
Reborn Endo R-Smart Plus+ instruction manual

Saito
Saito FG-33R3 instruction manual
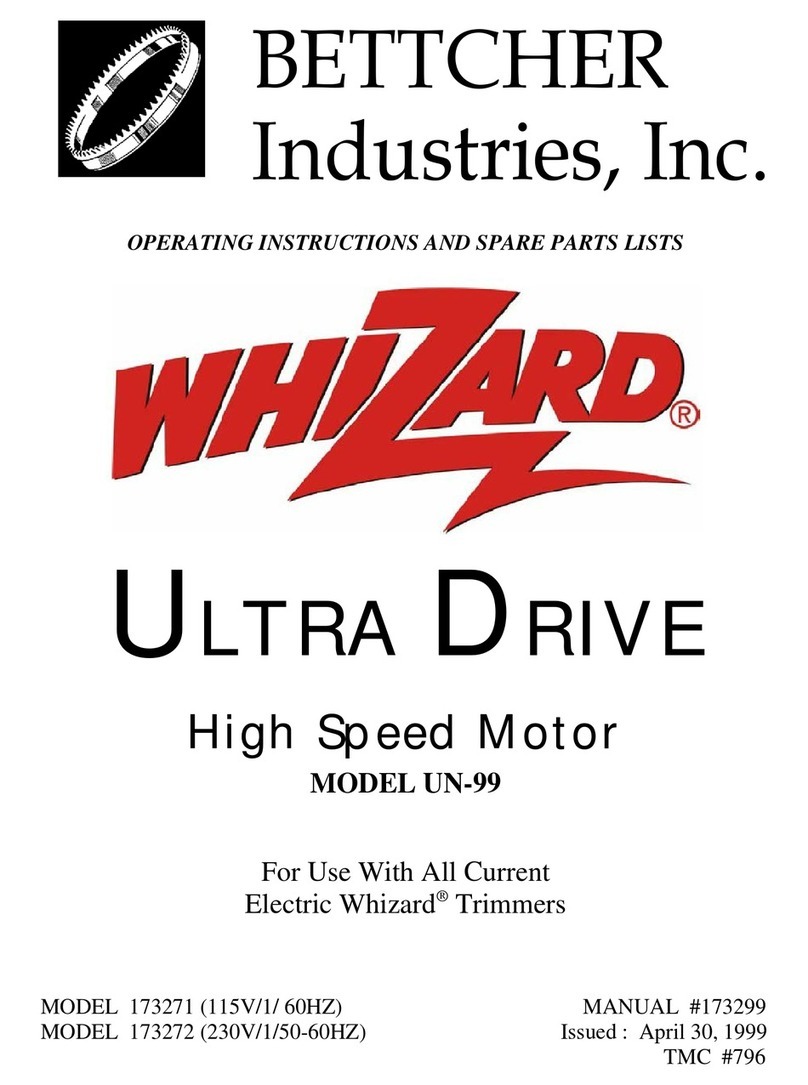
Bettcher
Bettcher Ultra Drive UN-99 Operating instructions and spare parts lists