Jeffco CG02 Technical specifications

CUTTER GRINDER
Model CG02
Cutter Blade
Maintenance
Instructions

2h
© Copyright 2010
Edition 1.3April 2010
Trade Mark and Design Registrations Apply
Designed and Manufactured in Australia by
JEFFRESS Engineering Pty Ltd
ACN 009 668 562
29 Churchill Road North
(PO Box 195)
DRY CREEK SA 5094
AUSTRALIA
Phone: +61 8 8262 8311
Fax: +61 8 8262 8355
E-mail: [email protected]om.au
WWW: http://www.jeffress.com.au

h3
CONTENTS
CONTENTS ..................................................................................................... 3
CUTTING SYSTEM MAINTENANCE ................................................................... 4
Maintenance .......................................................................................................4
The Cutting System.............................................................................................5
Cutting System Maintenance – Step 1..................................................................6
Cutting System Maintenance – Step 2..................................................................6
Cutting System Maintenance – Step 3..................................................................6
Cutting System Maintenance – Step 4..................................................................7
Cutting System Maintenance – Step 5..................................................................7
Cutting System Maintenance – Step 6..................................................................7
Cutting System Maintenance – Step 7..................................................................8
Cutting System Maintenance – Step 8..................................................................8
Cutting System Maintenance – Step 9..................................................................8
Cutting System Maintenance – Step 10................................................................8
MAINTAINING THE CUTTING COMPONENTS ..................................................... 9
RECOMMENDED SPARE PARTS..................................................................... 12

4h
CUTTING SYSTEM MAINTENANCE
The hCutter Grinder Model CG02 has been designed from the ground up to
have a long service life with minimum maintenance, however as with all me-
chanical systems, there are some routine operations that will help you keep your
Cutter Grinder in top condition.
WARNING: NEVER OPEN THE HEAD OR TOUCH, ADJUST OR REPLACE THE
BLADES WITHOUT USING THE KEYLOCKED MAINTENANCE SWITCH ON THE
CONTROL BOX.
NEVER disable or obstruct the safety systems on the machine.
NEVER use non-standard parts or accessories.
ALWAYS WEAR SUITABLE HEARING AND EYE PROTECTION.
Maintenance
BEFORE beginning any maintenance on the Cutter Grinder always carry out the
following. Make sure that the Cutter Grinder is switched off at the Control
Panel. Use the MAINTENANCE position of the keyswitch on the Control Panel if
you need to move the drive spindle. Check that all rotation has ceased by insert-
ing a long thin wooden stick into the inlet funnel or chute until it reaches to the
screen plate in the cutting head. If all rotation has stopped, lower the safety
handle and undo the knurled head locking nuts. Swing the head right back and
place a wooden wedge (100mm long and 50mm square at the thick end) in the
gap between the head and the midbody so that the head cannot close acciden-
tally. Put the locking bar in place to lock the spindle.
Figure 1. Locking Bar and Inspection Port

h5
The Cutting System
The most critical adjustments in the Cutter Grinder are the location and condi-
tion of the cutter blades. If these are maintained correctly, the hCutter
Grinder Model CG02 will give long and effective performance. Incorrectly ad-
justed blades can cause motor overload and could pose a safety hazard, so note
these steps carefully. The cutter blades should be sharpened regularly according
to the directions in the section MAINTAINING THE CUTTING COMPONENTS.
The cutter blades must always have the correct angles and sizes maintained, and
have a clearance from the screen plate and head inserts of between 0.125mm and
0.375mm. This clearance is maintained through the brass spacer rings under the
ejector and the adjusting screws in the end of each cutter blade.
The clearance should be minimal to provide optimum performance and careful
adjustment will be rewarded with excellent performance. For machines doing
heavy duty, a light touch up for the blades each day on a fine grinding stone will
ensure an uninterrupted work cycle.
Never allow the cutter blades to be sharpened beyond their useful, safe life – re-
fer the section entitled MAINTAINING THE CUTTING COMPONENTS. When re-
placing cutter blades onto the ejector during reassembly make sure that they are
matched by the numbers to the correct key. The head inserts do not accomplish
the cutting within the Cutter Grinder so they should not need to be kept as sharp
as the cutter blades and should have a longer life.
Always keep the mating surfaces of the head and midbody free of any foreign
matter and never allow contamination of the grease in the area of the bearing.
Figure 2. Section of Head & Midbody with Cutter Blades, Inserts & Screen Plate

6h
Cutting System Maintenance – Step 1
Refer to the above section to provide access to the Cutting System. Strip the cut-
ting components down to the bare spindle state. If the cutter blades have been
scraping on the screen plate, it may be necessary to renew the brass spacer rings
(shims) or to add an extra one (Part No E535 contains a set of four different
spacers).
Cutting System Maintenance – Step 2
Place the ejector (C290) over the spline on the drive spindle and make sure it is
seated firmly.
Cutting System Maintenance – Step 3
Check the screen plate for wear. Some versions are double sided and may be
turned over to extend the life. Replace it if there is excessive wear. Screw down
the plate into the recess in the midbody using the four countersunk screws.
Figure 3. Bare Spindle showing Brass Spacers
Figure 4. Ejector C290 Fitted to Spindle Spline
Figure 5. Fitting the Screen Plate

h7
Cutting System Maintenance – Step 4
Place the cutter blades on the keyed seats of the ejector so that the numbers im-
printed on them line up with the correct position on the ejector. Make sure that
the long horizontal adjusting screw in the end of each blade has been withdraw
sufficiently to allow the cutter blades to extend further than required. Do NOT
loosen the short grubscrew which retains the nylon locking pad.
Cutting System Maintenance – Step 5
Place the agitator collar over the spindle and check that the keys locate between
the cutter blades. There are different collars but the key system is the same.
Cutting System Maintenance – Step 6
Screw the spindle nut into place, checking that all the various component parts
of the Cutting System are located correctly.
Figure 6. Locating the Cutter Blades
Figure 7. Locating the Agitator Collar
Figure 8. Adding the Spindle Nut

8h
Cutting System Maintenance – Step 7
Using the supplied ring spanner and holding the locking bar through the spindle
to stop it rotating, screw the nut VERY TIGHTLY. Locate the feeler gauge set and
measure the clearance between the bottom of the Cutter Blades and the screen
plate – it should be no more than 0.375mm. Preferably the clearance should
only be 0.125mm for the best performance. If necessary, disassemble and re-
move (or add) one or more brass spacer rings till this specification is met.
Cutting System Maintenance – Step 8
It is now necessary to locate the cutter blades in the correct aspect to the head
inserts. To accomplish this, loosen off the spindle nut then hand tighten only.
Slide the cutter blades into the fully retracted position (close to the spindle) and
close the head ensuring that all mating surfaces are clean. Swing the knurled
head holding nuts into position and tighten very firmly. Unscrew the four (4)
screws holding the plate covering the midbody inspection port and remove the
plate and the locking bar – this should allow you to turn the spindle by hand
(provided the Control Panel Keyswitch is set to the MAINTENANCE position).
Working through the head opening(s), push the cutter blades out until they snap
against the machined surfaces inside the head.
Cutting System Maintenance – Step 9
Carefully rotate the spindle clockwise through the midbody inspection port till
the cutter blades are approximately in line with the knurled head holding nuts.
Open the head and tighten the spindle nut slightly with the ring spanner. Using
the supplied allen key, screw in the long grubscrews in the end of each of the
cutter blades until you feel them start to retract slightly – just enough to give
clearance against the head inserts. Carefully rotate the spindle to allow the lock-
ing bar to be slid into place then tighten the spindle nut VERY TIGHTLY. Re-
move the locking bar, close the head, tighten the head holding nuts and check
that there is NO METAL–TO–METAL CONTACT. If necessary, repeat this a num-
ber of times till there is no metal-to-metal contact between the cutter blades and
the head inserts but with the least clearance possible – preferably less than
0.250mm.
Cutting System Maintenance – Step 10
When you are sure that the above procedures are completed, check that the
spindle nut is VERY TIGHT. REMOVE THE LOCKING BAR and support wedge,
close and secure the head, screw on the plug which covers the locking bar access
hole, screw the midbody inspection port cover back into position and proceed to
test the Cutter Grinder under power.

h9
MAINTAINING THE CUTTING COMPONENTS
THE BLADES ON THE CUTTER GRINDER ARE VERY SHARP. ALWAYS TAKE
GREAT CARE WHEN WORKING WITH THEM TO AVOID INJURY.
The cutter blades, the head inserts and their alignment are the most important
things in the continuing high performance of the hCutter Grinder Model
CG02.The maintenance of the cutting faces of the cutter blades in particular is
of critical importance. This section will outline the procedure to be followed to
gain the best duty and life from the blades and inserts.
It is extremely important that the angles shown for the cutter blades are main-
tained. Only a properly qualified tradesperson should be assigned to perform
this work.
The diagram below shows the technical specifications for angles and dimensions
of the cutter blades. Note that the lock screw and nylon pad in the top of the
blade are only to provide tension for the adjusting screw and should not nor-
mally need to be touched.
The cutter blades and head inserts on the hCutter Grinder Model CG02 are
made from high quality precision ground and hardened tool steel.
To maintain the best performance, it is only necessary to grind the forward cut-
ting face of the cutter blades as shown in the diagrams below. To assist in keep-
ing the precise angles and dimensions, every hCutter Grinder is shipped
with a precision laser cut gauge plate (Part No E565).
Figure 9. Cutter Blade Specifications

10 h
The diagrams below show the cutting faces and the basic grinding procedure to
be followed when using the gauge (Part No E565) to set the correct angles and
dimensions.
Figure 10. Grinding Details for Cutter Blades
Figure 11. Using the E565 Gauge

h11
The diagram below illustrates how to use a fine grinding or sharpening stone to
hone the cutter blade by hand. It is imperative that the correct angles are main-
tained by using the gauge. Use a square to keep the cutting face perpendicular to
the base of the cutter blades.
DO NOT GRIND ANY OTHER FACES THAN THOSE SHOWN.
Ensure that the cutting edge never comes closer than 6mm from the seating key-
ways on the underside. Replace the cutter blades at or before this stage.
The diagram below illustrates how to touch up the head inserts. Be aware that
the inserts only act as stops for the cutter blades so they do not need to be as
sharp as the blades. Do not grind the facing edge more than 3mm deep – replace
the insert at this point – and do not exceed a cut of 6mm in the flat area as
shown.
DO NOT GRIND ANY OTHER FACES THAN THOSE SHOWN.
Figure 12. Sharpening the Cutter Blades
Figure 13. Grinding the Inserts

12 h
RECOMMENDED SPARE PARTS
The hCutter Grinder Model CG02 is a very reliable machine, but like all me-
chanical devices, there are components which are subject to wear. The following list
shows the components most likely to require replacement although you should ex-
perience a long service life from all parts if the recommended maintenance proce-
dures are carried out.
3209A Bearing – Main Spindle
BLU001 Brake Rotor Pad for Brake Motor
C194/7 19mm Screen Plate (CG02DF, CG02TT)
C290 Ejector
D373 Hardened Steel Cutter Set (matched pair)
D373RF Cutter Set Refurbishment and Regrind (pair)
D378 Head Insert Set (4 inserts per set)
E703 Agitator Collar (CG02TT)
E1150 Agitator Collar (CG02DF only)
E1380 Spindle Seal
These parts are available from the hDistributor in your country or directly
from Jeffress Engineering Pty Ltd. Speedy delivery to any part of the world can be
arranged at short notice.
We also provide refurbishment services for the cutter blades.
Figure 14. Some Components of the Tool & Spare Parts Kits
Table of contents
Popular Grinder manuals by other brands
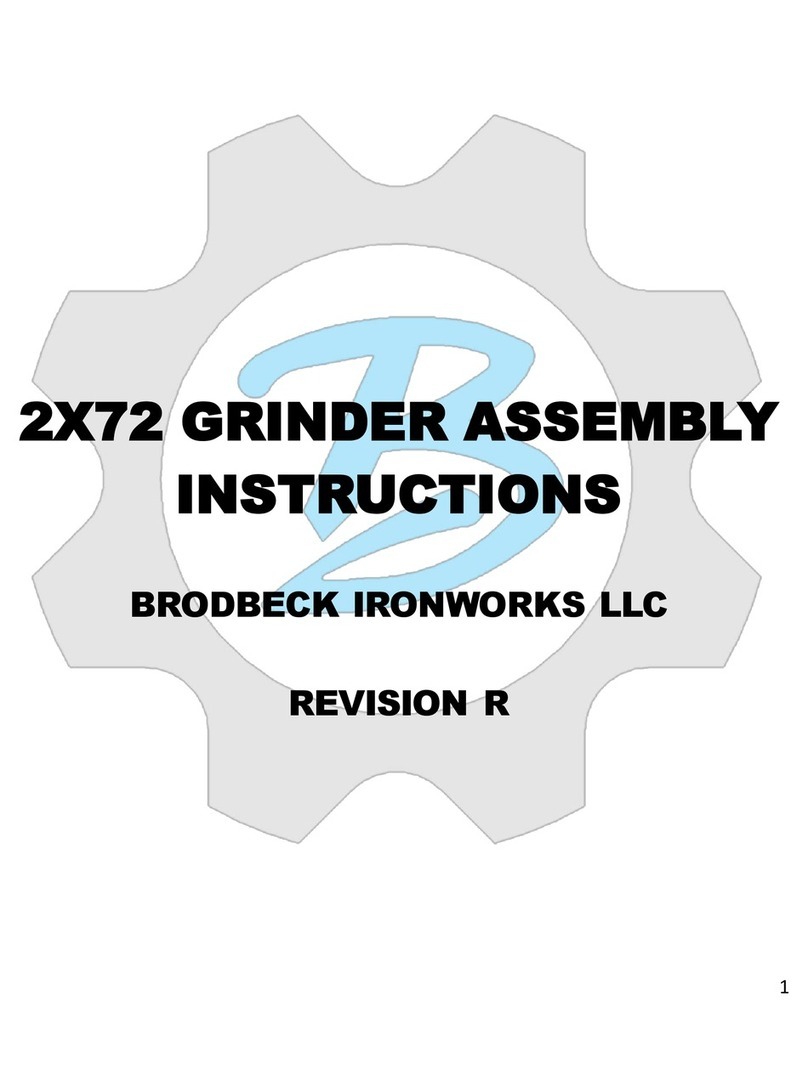
BRODBECK IRONWORKS
BRODBECK IRONWORKS 2X72 GRINDER Assembly instructions

Worx
Worx WX710 Original instructions

Lux Tools
Lux Tools WIS-750/115 Original instructions
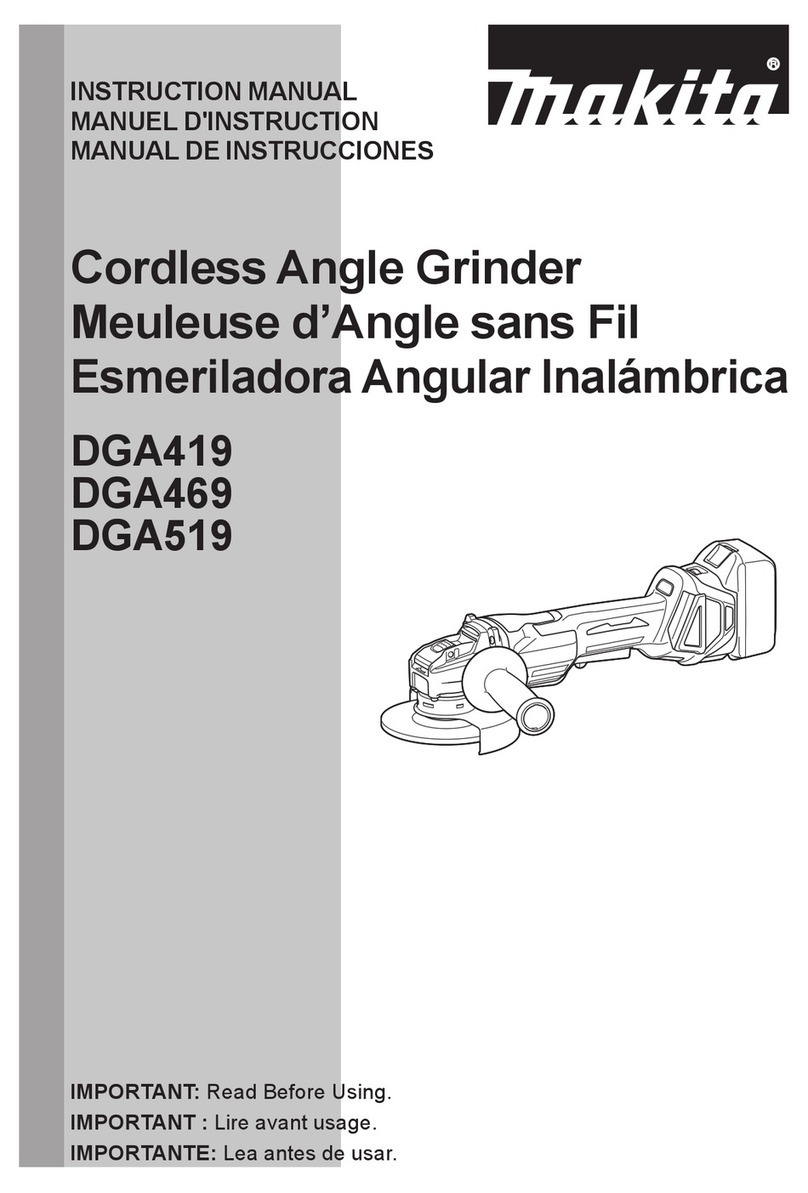
Makita
Makita DGA419 instruction manual

Chicago Pneumatic
Chicago Pneumatic CP7500D instruction manual

DeWalt
DeWalt XR LI-ION DCG405N Original instructions