Jersey Instruments Patriot User manual

Jersey Instruments
Patriot
FACETING MACHINE
Features.
Variable Speed Motor, Forward and Reverse Swin in Post. (No clampin or unclampin )
Rack and Pinion to Raise and Lower Head .1 De ree Di ital An le Readout
Includes.
96, 80, 72 Tooth Index Wheels
12 Brass Dops , 3mm. to 8mm. in Flat Cone and V Form
45
0
An le Dop. Two Settin Dops.
Transfer Block.
Available From.
Jersey Instruments
Phone: 256-883-8988
805 Halstead Ct.
Email: chasmusi@knolo y.net
Huntsville, AL USA 35803
Web: www.JerseyInstruments.com
Desi ned and manufactured by Jersey Instruments, 805 Halstead Ct. Huntsville, Al. 35803 USA.

Just a quick note before you get started.
We wish you the best with your new machine.
The owner’s manual attached is NOT a thesaurus for how to cut stones.
Others do a much better job at that than we.
Although we ha e a rather generous drain tube setup, I must caution you NOT to use too much water drip.
Just enough to keep the lap wet. When swarf mixes with the water, it can cause the drain tube to clog and
o er flow. Check the drain flow and make sure there is little standing water on a regular basis.
The machine was calibrated before shipping. You only need to dop a stone and start cutting.
You will notice that we ha e recently upgraded the display. It is now microprocessor controlled and has
se eral unique features. Upon power up the display will show “Err”. This is your prompt to lower the dop
arm to its ertical down position and press the toggle switch on the right side of the control box. The
machine is now calibrated. As described in later text you can also set the desired cut angle and again
toggle the calibration set switch a second time. This will allow you to cut to “0”. There is one other
feature concerning the display. Always turn the speed control to zero “0” before re ersing turntable
direction, If you do not, the microprocessor may reset itself to the “Err” display. If you re erse the motor
while the turn table is rotating, you stand a ery good chance of flipping the dri e belts off of the pulleys.
This will be e ident, because the motor will hum but the lap will not turn. In this case, the “Err” will alert
you to remo e the belt guard and replace the dri e belts.
If you ha e any questions, please contact us at 256-883-8988 or on the web at chasmus[email protected].
Good luck
Charlie

Patriot Calibration
The Patriot was designed for easy calibration. Upon power-up, loosen the large
angle set knob at the back of the head. Depress the dop holder to its most downward
position. At this point, the pi ot block will come in contact with a calibration set
screw. Gently hold the dop arm against the setscrew and depress the
calibration/zero set le er switch, located on the right side of the control box. The
display should reset to zero.
This feature can also be used to “cut to zero”. After completing the procedure
abo e, mo e the dop arm to the desired cut angle. Tighten the angle set knob. Press
the calibration/zero set le er switch. The display will reset to zero. As you approach
the desired cut angle, the display will approach zero. You can cut to the zero mark
or stop short to allow for polishing to bring the facet in to the desired angle.
The proper method to set the desired cut angle is to mo e the dop arm upward as
described in “B” abo e. Stop short of the desired angle and tighten the angle set
knob. (Fig 1). Turn the angle set fine adjust knob (Fig. 1) clockwise until the
display just clicks up to the desired angle. Note the position of the needle on the
dial indicator. Rotate the outer bezel on the dial indicator so that the needle in now
on the last number of the digital display. Continue turning the small black fine
adjustment knob until you reach the desired 100's digit.
Most cutting patterns only specify 1/10 degree settings. This
paragraph is only applicable if 1/100 degree angles are
required.


INSTRUCTION BOOK
(1) UNPACKING Upon arrival, check the condition of the outside of the shipping container. If the shipping
container shows signs of intrusion or damage, STOP. Call the carrier and have them send an inspector to ascertain
inside damage. Call your local sales agent and the factory at U.S. 256 883 8988.
(2) SETTING UP THE MACHINE. The machine should be set on a level working surface with ample room on the
left side and front. Being a three legged machine, it will appear to be level, however water and slurry may not
properly flow out of the splash pan. A little care here can save pain later.
(3) ELECTRICS. One of the features of the Patriot is the digital readout. The digital display and electronics are
contained in the control box, along with the motor speed controller. STOP.
We are proud of the display electronics and the controller; however the unit uses lethal voltage. If you are curious
and just have to look inside the control box, PLEASE disconnect the power cord FIRST. Inside you will find a motor
speed controller board a display readout board and a low voltage power supply.
Now that you have satisfied your curiosity, make sure the wires are in place and replace the back panel screws.
(4) MOTOR AND CONTROL.
The electric motor is a DC permanent magnet motor operating on rectified 110 or 220 Volt AC current. The drive
uses twin belts of 4mm. diameter polyurethane. No belt tension adjustment is necessary.
The Electronic Control is a KBVC Control or equivalent. It incorporates an Off On switch and a speed control
operated by the one knob. The speed range is 20:1 with a maximum no load speed of approximately 1200 rpm.
(5) CONTROL BOX. (FIG. 2)
On the Control Box front panel are a Forward and Reverse Switch with a central off position.
A Speed Control Knob incorporating an Off On Switch.
A Digital Read out displaying the Facet Angle Setting.
Fig 2

The Power Circuit and the Electronic Circuit is shown in (Fi s.3 & 4)
A “zero” set/ cut to zero set lever switch is located on the right side of the control box.
Warnin . When changing Direction of Rotation, switch to the “Off” position and allow the machine to come to a
stop before making the change.
When not in use all switches, Speed Control, Forward- Reverse and Wall Power Point should be switched
off.
Fi 3 Fi 4
(6) WATER BOTTLE.
This is mounted on a post at the back of the machine and is fitted with a drip Tap and tube. The bottle can be
swiveled around and lifted off. There is a tension set screw at the top of the post.
(7) DRAIN TUBE
The drain tube is fitted up through a hole in the base plate onto a ferrule underneath the Splash Bowl.
(8) SPLASH BOWL (Fi 5)
The splash bowl has a cutout with a removable piece. This is to allow the entry of the Dop Arm when cutting the
girdle of a stone. A deflector prevents splash from the Lap throwing out the gap.

Fi 5
(9) SWING ARM AND POST. (Fi 6)
The Swing Arm that carries the Post is mounted below the Base plate on the right side. The Arm is tensioned with
an elastic stop nut. This stop nut is factory set.
Fi 6
(10) VERTICAL ADJUSTMENT SLEEVE. (Fi 7)
This is a bronze bushed sleeve fitted over the Post. A large graduated Knob at the top provides fine Up and Down
feed. A steel ball inside the Knob carries the weight of the Head. Half an inch of vertical down feed is provided.
Before cutting a Facet make sure there is sufficient Down Feed.
Fig 7

(11) VERTICAL SLIDE. (Fi 8)
This moves up and down the Post to position the Stone being faceted in relation to the Lap Plate. A Rack and
Pinion is used to do this, being operated by a Large Knob. In the center of this Knob is a smaller Knob for locking
the Slide once positioned.
If the Head has a tendency to freewheel down when the Lock is released, adjust the small tensioning grub screws
at the back of the Slide. Do not over tighten these screws. This will cause unnecessary wear on the vertical column
(Fig 9).
Fi 8
(12) PIVOT PLATE.
This Plate carries the Pivot Bearing and is secured to the Vertical Slide with four clamp screws and one “jack
screw”. These screws are used to square the Pivot Axis with the Post and SHOULD NOT BE TAMPERED WITH.
Special equipment is required to make this adjustment. If you i nored the above caution and now have the
machine out of ali nment, don’t panic. Just call the factory.
(13) THE HEAD.
On the front of the Head are the two Knobs that raise and lower the Head and lock it in position. On the backside of
the Pivot Axis is another Knob. This knob is used to set the desired cut angle.

Loosen this knob, raise or lower the dop arm to the desired cut angle, tighten the knob. At the approximate center
of the pivot plate is a fine adjust knob used to set the cut angle.
(14) PIVOT BLOCK (Fi 9)
The Pivot block pivots around the Pivot Axis and carries the Dop Arm (Quill) assembly. It swings through just over
180 degrees.
Fi 9
(15) INDEX PAWL and PLATE.
This Plate is secured to the Pivot Block and carries the Index Pawl and the Dop Arm. Micro adjustment, (cheating)
is achieved by a Knob on the left of the Index Pawl Spindle. On this Knob is a setscrew that is aligned with a notch
on the Index Pawl Plate. This is the setting for faceting.
The Index pawl is depressed to lift the Index Pin out of engagement with the Index Wheel and can be clipped back
under a Knurled Knob for freewheeling the Index Wheel.
(16) DOP ARM (Quill)
This is carried on two lightly pre loaded ball bearings. The preloading prevents any end or side play in the Dop Arm.
The Arm carries the Index Wheel that is screwed to a brass ring by two screws. This ring has a grub screw for
locking the Wheel to the Arm. To change Index Wheels the two screws are removed. The Dop Arm is bored to
receive the Dops. A large flat point grub screw locks the Dop in the quill.
(17) INDEX WHEELS.
The machine is fitted with a 96 tooth Index Wheel as standard. 80 and 72 tooth wheels are provided. The Wheels
are secured with two small screws. These must be kept tight.
(18) DOPS.
Dops are flat cone and “V” form. The dops have a 45º chamfer milled at the end that is used for location in the Dop
Arm and the Transfer Block. A “D” dop for setting the cheater square with the Master Plate, a 45
0
Angle Dop and a
large Flat Top Dop

(19) ANGLE DOP (45 De Dop) (Fi 10)
The angle dop is inserted in the Dop Arm, located and locked as above. The dop holding the Gemstone is inserted
in this Dop and locked with the Grub Screw. This arrangement is used to cut the table on the stone.
Fig 10
(20) CHECKING ANGLE DOP SETTING
The 45
0
Angle Dop is inserted in the Dop Arm as described above. The large Flat Top Dop is locked in the Angle
Dop. The Angle is set at 45.0
0
and clamped. Set the Index Pawl pin in the 96 tooth of the Index Wheel and zero the
Index Cheater. The head is then lowered until the Flat Top Dop sits flat on the master plate. If not, adjust the Angle
setting and the Index Cheater. However after cutting and polishing the Table of the Gemstone, the Index Cheater
must be returned to the zero setting before continuing to cut any of the Facets.
(21) TRANSFER BLOCK. (Fi . 11)
This has a “V” grove for holding the dops. Two brass “D” shaped plates clamp the dops. In operation one dop is
placed in the groove. The brass plate is slid forward over it and clamped. The other dop is inserted in the same way
and the plate tightened.
Fig 11

(22) LAP PLATES.
It is essential that Lap Plates run true. They should not be bowed or of uneven thickness. They can be checked
with a straight edge and micrometer. Copper and Tin Laps can be machined to run true. They need to be held
against an accurately machined Master Plate in a lathe to do this.
(23) FITTING LAP PLATES
The lap plates locate on the Spindle projection in the center of the Master Plate. A Knurled Knob holds them. This
should be tightened only sufficient for the plate to drive. Over tightening causes the plate to bow up and create
problems cutting the facets,
(24) CHANGING INDEX WHEELS. (Fi 12)
Depress the Index Pawl and clip it back in the Free Wheeling position. If this is not done the Pawl will spring up and
the spring will fly out. After a new Wheel has been fitted it will be necessary to set it in relation to the Master Plate
using the “D” Dop.
Fi 12
(25) SETTING THE ANGLE.
Always approach the An le Settin from the same direction. Do not come back to it.
(26) POSITIONING THE HEAD.
The Post is swung to bring the end of the Dop Arm over the Lap Plate and the Head racked down until the stone
just clears the Lap Plate. When cutting is commenced, the stone is fed down with the Vertical Feed Knob on top of
the Post.
(27) SETTING INDEX WHEEL AND DOP ARM IN RELATION TO MASTER PLATE. (Fi . 13)
The Index Wheel is set at 96 and the Index Cheater zeroed. This is when the “0” on the Cheater Knob is exactly in
line with the notch in the Index Pawl Plate. Insert the “D” Dop in the Dop Arm, locate and lock. Set the Angle to
approximately 45
0.
Lower the head until the Dop touches the Master Plate. Loosen the Grub Screw in the brass
collar behind the Index Wheel. Press the top of the Dop to sit flat on the Plate. Tighten the Grub Screw. Do not
sweep the dop across the Plate. This will wear the straight edge of the Dop and cause errors in setting.
Note. The Index Cheater must always be set at Zero before commencin cuttin .

Fi 13
(28) CHECKING SQUARENESS OF PIVOT AXIS AND DOP ARM AXIS. (Fi 13) This is done with the “D” Dop.
Locate and lock the Dop in the Dop arm. Lower the head down to approximately 90
0
and adjust the Index Cheater
so that the straight edge of the dop sits flat on the Master Plate. Now move the Head up to an Angle reading of
around 45
0
. The straight edge of the Dop should sit flat on the Plate. To check if the Dop is sitting flat, depress the
Index Pawl while putting a little finger pressure on the top of the Dop. If the Index Wheel kicks then the Dop is not
sitting flat.
(29) INDEXING.
When indexing, depress the Pawl sufficiently to clear the teeth in the Wheel. Do not skid the Index Pin over the
Teeth. The Teeth relate directly to the Facet being cut. If when depressing the Pawl, the Cheater knob turns,
moving it from the Zero setting, it can be tensioned with the ferrule on the opposite end of the shaft.
(30) FREEWHEELING. (Fi 14)
To freewheel the Index Wheel for Preforming the Girdle, the Pawl is depressed and the Catch Knob turned to clip
over the end of the Pawl and free the Wheel.

Fig 14
(31) INDEX MICRO ADJUSTMENT (CHEATER) (Fi .15)
This provides adjustment for aligning the Facets when cutting, if necessary. The cheater also allows the operator to
completely polish the Facets. Turning the Knob towards the operator rotates the Dop counter clockwise, turning the
Knob away from the operator rotates the Dop counter clockwise.
Fig 15

(32) ELECTRIC MOTOR
One Brush wears more than the other, especially during slow speed operation. Periodically they need to be
reversed. This will prolong the life of the brushes.
(33) CARE OF THE MACHINE.
Always keep the machine clean. It is just as important to keep the hands clean also. Avoid placing the hands on the
Vertical Adjustment Sleeve. Do not allow an accumulation of stone residue to build up. Keep the Master Plate
clean. Occasionally polish it with silicon carbide paper. Spray lightly with de watering fluid when not in use. When
finished using the machine switch off all switches.
(34) LUBRICATION.
Motor: - Permanently lubricated ball bearings.
Spindle: - Permanently lubricated ball bearings.
Pivot: - Permanently lubricated ball bearing.
Dop Arm: - Permanently lubricated ball bearings.
Swin Arm: - Requires no lubrication.
Vertical Adjustment Sleeve: - Lift the assembly and apply grease to the inner post.
Micro Hei ht Adjustment: - An occasional smear of light grease on the thread.
Vertical Slide: - A light film of oil on the Vertical Adjustment Sleeve.
Index Pawl Spindle: - An occasional drop of oil in the holes at either end.
Index Cheater: - A smear of grease on the thread.
Note: - No definite period can be given for lubrication frequency. This is something the operator must determine
depending on the use of the machine.
(36) WARRANTIES. We will correct any mechanical fault detrimental to the operation of the machine for
which the manufacturer is responsible.
Motor: - Manufacturer’s warranty is twelve months from date of purchase of the machine.
Control: - Same as motor
Table of contents
Popular Sander manuals by other brands
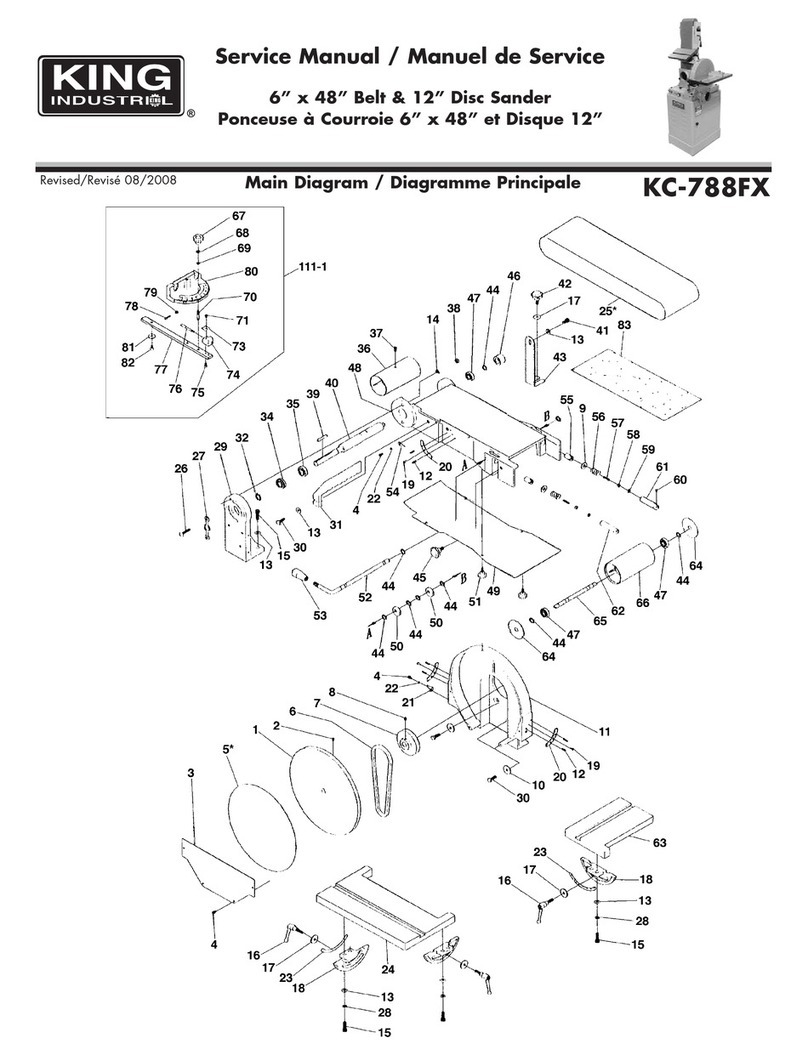
King Industrial
King Industrial KC-788FX Service manual

Sealey
Sealey CP20VOP manual
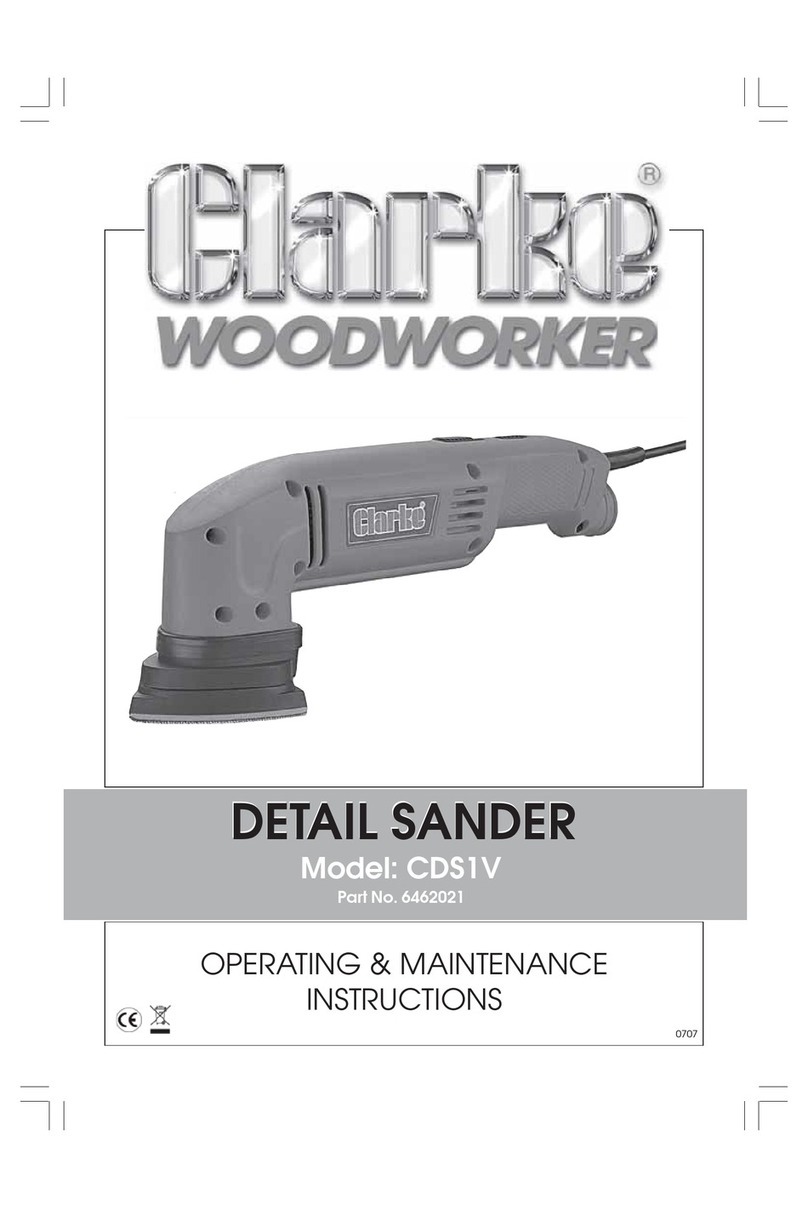
Clarke
Clarke 6462021 Operating & maintenance instructions
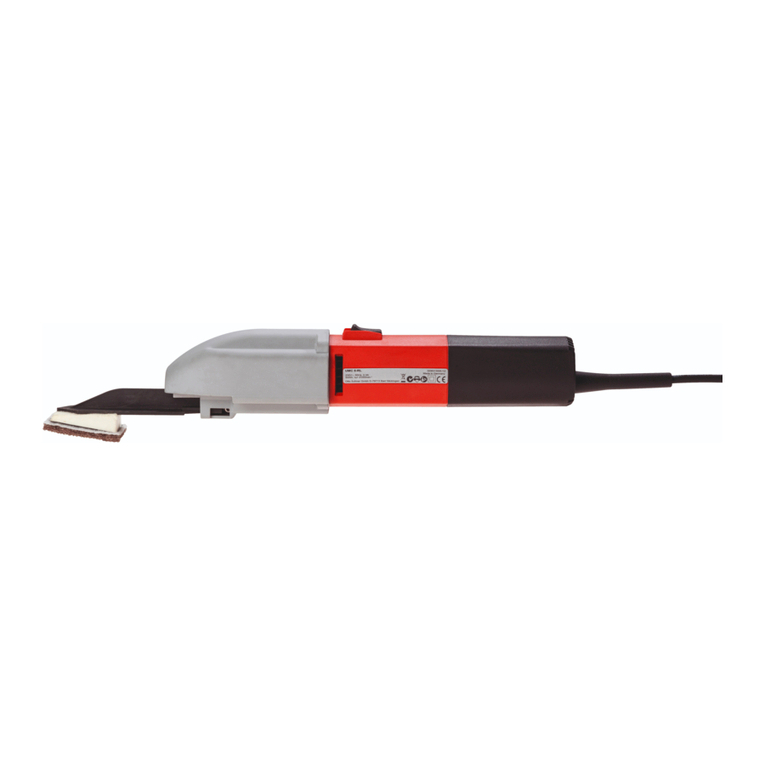
SUHNER
SUHNER UMC 6-RL Additional technical manual
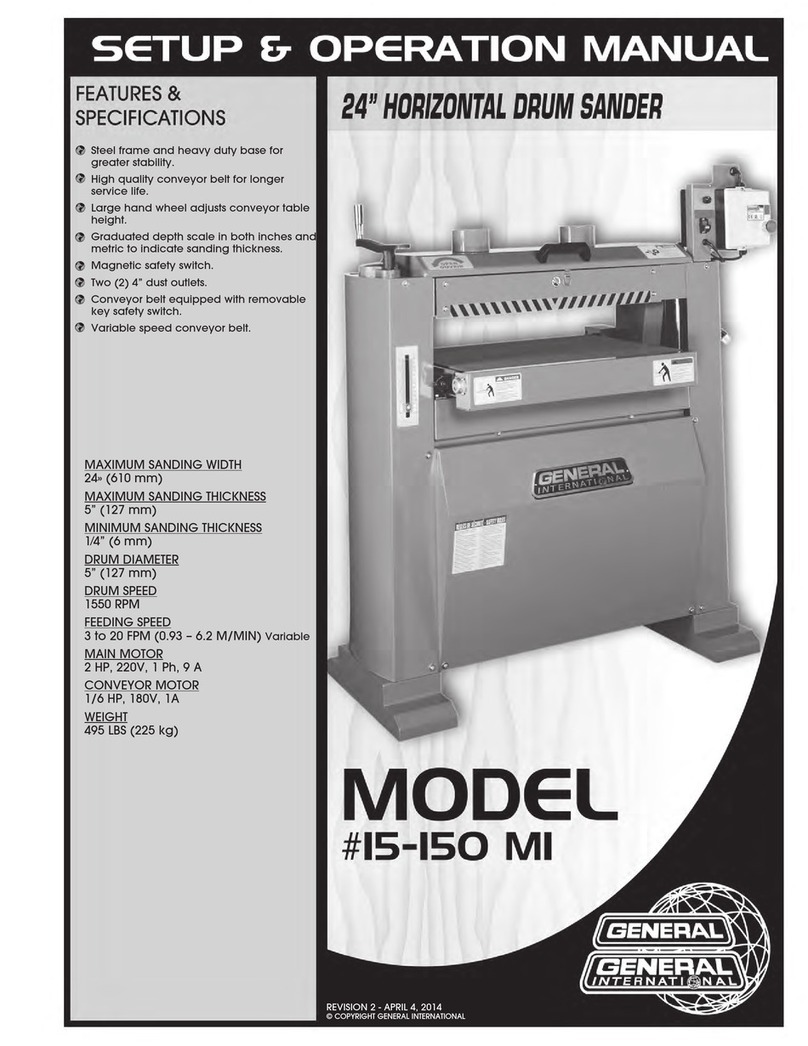
General International
General International 15-150 MI Setup & operation manual
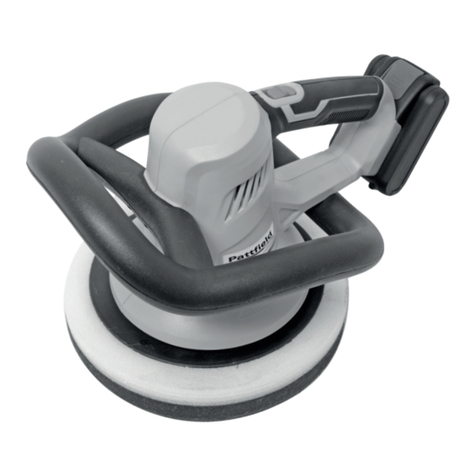
Pattfield Ergo Tools
Pattfield Ergo Tools PE-20PSB Original instructions