JVC HR-A60UC User manual

COPYRIGHT © 2003 VICTOR COMPANY OF JAPAN, LTD
SERVICE MANUAL
GENERAL
Power requirement
Power consumption
Power on
Power off
Temperature
Operating
Storage
Operating position
Dimensions (W x H x D)
Weight
Format
Maximum recording time
SP
EP
VIDEO/AUDIO
Signal system
Recording/Playback
system
Signal-to-noise ratio
Horizontal resolution
Frequency range
Normal audio
Hi-Fi audio
Input/Output
TUNER
Tuning system
Channel coverage
VHF
UHF
CATV
RF output
TIMER
Clock reference
Program capacity
Memory backup for timer
ACCESSORIES
Provided accessories
Specifications shown are for SP mode unless specified otherwise.
E. & O.E. Design and specifications subject to change without notice.
: AC 120V, 60 Hz
:
: 1.7 W
:
: –20°C to 60°C
(–4°F to140°F)
: Horizontal only
: 360 mm x 95 mm x 222.5 mm (14-3/16" x 3-3/4" x 8-3/4")
: 3.2 kg (7.1 lbs)
: VHS NTSC standard
: 210 min. with ST-210 video cassette
: 630 min. with ST-210 video cassette
: NTSC-type color signal and EIA monochrome signal, 525 lines/60 fields
: DA-4 (Double Azimuth) head helical scan system
: 42 dB
: 230 lines
: 100 Hz to 10,000 Hz
: 20 Hz to 20,000 Hz
:
RCA connectors (IN x 1, OUT x 1)
: Frequency-synthesized tuner
: Channels 2–13
: Channels 14–69
: 113 Channels
: Channel 3 or 4 (switchable; preset to Channel 3 when shipped) 75 ohms,
unbalanced
: Quartz
: 1-month programmable timer/8 programs
: Approx. 5 sec.
: RF cable (F-type), Infrared remote control unit, “AAA” battery x 2
5°C to 40°C (41°F to 104°F)
9 W
No.82953
2003/01
HR-A60U
C
HR-A60UC V16D0
VIDEO CASSETTE RECORDER
SPECIFICATIONS
MENU
REC
REW FF
CH(AUX)
ENTER
12 3
456
7
0
89
SET
–
TV/VCR TIMER
A.MONITOR SP/EP DISPLAY
CANCEL
C.RESET
TVCH
TVVOL
INPUT
+
–
+
–
+
–
+
PAUSE
PLAY
STOP
TVPOWER
POWER

TABLE OF CONTENTS
Section Title Page Section Title Page
Important Safety Precautions
INSTRUCTIONS
DISASSEMBLY INSTRUCTIONS
1.
REMOVAL OF MECHANICAL PARTS AND P.C.BOARDS ...............
1-1
1-1 TOP CABINET AND FRONT CABINET ............................ 1-1
1-2 FLAP .................................................................................. 1-1
1-3 DECK CHASSIS ................................................................1-1
1-4 SYSCON PCB ...................................................................1-1
2. REMOVAL OF VCR DECK PARTS.........................................1-2
2-1 TOP BRACKET..................................................................1-2
2-2 CASSETTE HOLDER ASS’Y.............................................1-2
2-3 CASSETTE SIDE L/R ........................................................1-2
2-4 LINK UNIT .........................................................................1-2
2-5 LINK LEVER / FLAP LEVER / SENSOR COVER R..........1-2
2-6 LOADING MOTOR / WORM..............................................1-3
2-7 TENSION ASS’Y................................................................1-3
2-8 T BRAKE ARM / T BRAKE BAND......................................1-4
2-9
S REEL / T REEL / IDLERARMASS’Y / IDLER GEAR ..............
1-4
2-10
CASSETTE OPENER / PINCH ROLLER BLOCK / P5ARM ASS’Y.............
1-5
2-11 A/C HEAD ........................................................................1-5
2-12 FE HEAD .........................................................................1-5
2-13 CYLINDER UNITASS’Y ..................................................1-5
2-14 CAPSTAN DD UNIT.........................................................1-6
2-15
MAIN CAM / PINCH ROLLER CAM / JOINT GEAR ............
1-6
2-16 LOADING GEAR S/T UNIT..............................................1-6
2-17
CLUTCH ASS’Y / RING SPRING / CLUTCH LEVER / CLUTCH GEAR ...............
1-7
2-18
CASSETTE GUIDE POST / INCLINED BASE S/T UNIT / P4 CAP..............
1-7
KEY TO ABBREVIATIONS ........................................................1-8
PREVENTIVE CHECKS AND SERVICE INTERVALS.............1-10
CLEANING ...............................................................................1-10
SERVICE MODE LIST.............................................................. 1-11
WHEN “N” IS ALWAYS BEING DISPLAYED ON THE TV MONITOR ..
1-11
SERVICING FIXTURES AND TOOLS...................................... 1-11
MECHANISM ADJUSTMENT PARTS LOCATION GUIDE............
1-11
MECHANICAL ADJUSTMENT ................................................1-12
TAPE REMOVAL METHODAT NO POWER SUPPLY ..........1-12
1. CONFIRMATION AND ADJUSTMENT .................................1-12
1-1
CONFIRMATION AND ADJUSTMENT OF TENSION POST POSITION .
1-12
1-2 CONFIRMATION OF PLAYBACK TORQUE AND
BACK TENSION TORQUE DURING PLAYBACK...........1-12
1-3 CONFIRMATION OF VSR TORQUE...............................1-12
1-4 CONFIRMATION OF REEL BRAKE TORQUE................1-13
2. CONFIRMATION AND ADJUSTMENT OF TAPE
RUNNING MECHANISM .................................................. 1-13
2-1 GUIDE ROLLER ..............................................................1-13
2-2
CONFIRMATION AND ADJUSTMENT OF AUDIO/CONTROL HEAD .
1-14
2-3
TAPE RUNNING ADJUSTMENT(X-VALUE ADJUSTMENT) .
1-14
ELECTRICAL ADJUSTMENTS ...............................................1-15
1. BASIC ADJUSMENT ............................................................ 1-15
1-1 SWITCHING POINT ........................................................1-15
ELECTRICAL ADJUSTMENT PARTS LOCATION GUIDE ............
1-15
IC DESCRIPTIONS ..................................................................1-16
SERVO TIMING CHART ..........................................................1-19
MECHANISM TIMING CHART.................................................1-20
TROUBLE SHOOTING GUIDE ................................................1-21
POWER DOES NOT TURN ON ............................................1-21
POWER SHUTS OFF ............................................................1-22
AUDIO SHAKES ....................................................................1-23
CASSETTE TAPE IS NOTACCEPTED.................................1-24
FF/REW DO NOT WORK ......................................................1-25
WHEN INSERTING CASSETTE, IT EJECTS IMMEDIATELY..
1-25
TAPE LOADING IS OK, BUT UNLOADS IMMEDIATELY......1-26
PLAYBACK PICTURE JITTERS HORIZONTALLY ................1-27
PLAYBACK PICTURE SHAKES ............................................1-27
AUTO TRACKING DOES NOT OPERATE ............................1-28
WHEN PLAYBACK, FAST FORWARD OR REWIND MODE IS ACTIVATED, UNIT STOPS IMMEDIATELY ..
1-28
PLAYBACK PICTURE JITTERS VERTICALLY .....................1-29
NO PLAYBACK PICTURE .....................................................1-30
NO PICTURE DURING PLAYBACK ......................................1-31
NO COLOR DURING SELF RECORDING AND PLAYBACK.
1-31
CYLINDER NOT ROTATING DURING PLAYBACK AND RECORDING ..
1-32
PLAYBACK PICTURE NOISY(EVEN AFTER CLEANING HEADS) .
1-32
NO NORMALAUDIO ON PLAYBACK ...................................1-33
CAPSTAN DD MOTOR NOT ROTATING ..............................1-34
AUDIO CAN NOT BE RECORDED .......................................1-35
CASSETTE IN AND DOWN, UNIT HAS NO FUNCTIONS....1-36
RECORDING MECHANISM WORKS, BUTNO VIDEO RECORDED FROM INPUTJACK OR TUNER ..
1-37
NO E-E (NO VIDEO FROM TUNER).....................................1-38
NO E-E AUDIO (MONO) ........................................................1-39
NO TUNER AUDIO (MONO)..................................................1-40
CHARTS AND DIAGRAMS
INTERCONNECTION DIAGRAM ............................................2-1
Y/C/AUDIO/CCD/HEAD AMP SCHEMATIC DIAGRAM ..........2-3
SYSTEM CONTROL/SERVO SCHEMATIC DIAGRAM ..........2-5
POWER SCHEMATIC DIAGRAM ...........................................2-7
OPERATION/DISPLAY SCHEMATIC DIAGRAM....................2-9
TUNER SCHEMATIC DIAGRAM...........................................2-11
Hi-Fi/DEMODULATOR SCHEMATIC DIAGRAM...................2-13
PRINTED CIRCUIT BOARDS SYSCON/BOT .......................2-15
WAVEFORMS .......................................................................2-18
Y/C/AUDIO/CCD/HEAD AMP BLOCK DIAGRAM .................2-19
SYSTEM CONTROL/SERVO BLOCK DIAGRAM .................2-21
TUNER BLOCK DIAGRAM....................................................2-23
HI-FI/DEMODULATOR BLOCK DIAGRAM ...........................2-25
OPERATION BLOCK DIAGRAM ...........................................2-27
POWER BLOCK DIAGRAM ..................................................2-27
PARTS LIST
3.1 PACKING AND ACCESSORY ASSEMBLY<M1> ................ 3-1
3.2 FINAL ASSEMBLY<M2> ...................................................... 3-2
3.3 MECHANISM ASSEMBLY<M4> .......................................... 3-4
3.4 ELECTRICAL PARTS LIST.................................................. 3-7
SYSCON BOARD ASSEMBLY<03> ........................................ 3-7
BOT BOARD ASSEMBLY<07> ...............................................3-10
REFERENCE
SEMICONDUCTOR BASE CONNECTIONS.......................... 4-1
GENERAL SPECIFICATIONS[HR-A60UC] .............................4-2

Important Safety Precautions
Prior to shipment from the factory, JVC products are strictly inspected to conform with the recognized product safety and electrical codes
of the countries in which they are to be sold. However, in order to maintain such compliance, it is equally important to implement the
following precautions when a set is being serviced.
Fig.1
1. Locations requiring special caution are denoted by labels and
inscriptions on the cabinet, chassis and certain parts of the
product. When performing service, be sure to read and com-
ply with these and other cautionary notices appearing in the
operation and service manuals.
2. Parts identified by the symbol and shaded ( ) parts are
critical for safety.
Replace only with specified part numbers.
Note: Partsin thiscategoryalsoinclude thosespecifiedto com-
ply with X-ray emission standards for products using
cathode ray tubes and those specified for compliance
with various regulations regarding spurious radiation
emission.
3. Fuse replacement caution notice.
Caution for continued protection against fire hazard.
Replace only with same type and rated fuse(s) as specified.
4. Use specified internal wiring. Note especially:
1) Wires covered with PVC tubing
2) Double insulated wires
3) High voltage leads
5. Use specified insulating materials for hazardous live parts.
Note especially:
1) Insulation Tape 3) Spacers 5) Barrier
2) PVC tubing 4) Insulation sheets for transistors
6. When replacing AC primary side components (transformers,
power cords, noise blocking capacitors, etc.) wrap ends of
wires securely about the terminals before soldering.
Power cord
Fig.2
10. Also check areas surrounding repaired locations.
11. Products using cathode ray tubes (CRTs)
In regard to such products, the cathode ray tubes themselves,
the high voltage circuits, and related circuits are specified for
compliancewith recognizedcodespertaining toX-ray emission.
Consequently,whenservicing theseproducts, replacethecath-
ode ray tubes and other parts with only the specified parts.
Under no circumstances attempt to modify these circuits.
Unauthorizedmodification canincrease thehigh voltagevalue
and cause X-ray emission from the cathode ray tube.
12. Crimp type wire connector
Insuchcases aswhen replacingthepower transformerin sets
where the connections between the power cord and power
transformerprimary leadwiresare performedusingcrimptype
connectors, if replacing the connectors is unavoidable, in or-
der to prevent safety hazards, perform carefully and precisely
according to the following steps.
1) Connector part number : E03830-001
2) Required tool : Connector crimping tool of the proper type
which will not damage insulated parts.
3) Replacement procedure
(1) Removethe oldconnectorbycuttingthe wiresat apoint
close to the connector.
Important : Do not reuse a connector (discard it).
Fig.7
cut close to connector
Fig.3
(2) Strip about 15 mm of the insulation from the ends of
the wires. If the wires are stranded, twist the strands to
avoid frayed conductors.
15 mm
Fig.4
(3) Align the lengths of the wires to be connected. Insert
the wires fully into the connector.
Connector
Metal sleeve
Fig.5
(4) As shown in Fig.6, use the crimping tool to crimp the
metalsleeve atthe centerposition. Besuretocrimpfully
to the complete closure of the tool.
1
vPrecautions during Servicing
7. Observe that wires do not contact heat producing parts
(heatsinks, oxide metal film resistors, fusible resistors, etc.)
8. Check that replaced wires do not contact sharp edged or
pointed parts.
9. When a power cord has been replaced, check that 10-15 kg of
force in any direction will not loosen it.
1.25
2.0
5.5
Crimping tool
Fig.6
(5) Check the four points noted in Fig.7.
Not easily pulled free Crimped at approx. center
of metal sleeve
Conductors extended
Wire insulation recessed
more than 4 mm
S40888-01

v Safety Check after Servicing
Examine the area surrounding the repaired location for damage or deterioration. Observe that screws, parts and wires have been
returned to original positions, Afterwards, perform the following tests and confirm the specified values in order to verify compli-
ance with safety standards.
1. Insulation resistance test
Confirm the specified insulation resistance or greater between power cord plug prongs and
externally exposed parts of the set (RF terminals, antenna terminals, video and audio input
and output terminals, microphone jacks, earphone jacks, etc.). See table 1 below.
2. Dielectric strength test
Confirmspecifieddielectric strengthorgreater betweenpowercord plugprongsand exposed
accessible parts of the set (RF terminals, antenna terminals, video and audio input and output
terminals, microphone jacks, earphone jacks, etc.). See table 1 below.
3. Clearance distance
When replacing primary circuit components, confirm specified clearance distance (d), (d’) be-
tween soldered terminals, and between terminals and surrounding metallic parts. See table 1
below.
4. Leakage current test
Confirm specified or lower leakage current between earth ground/power cord plug prongs
and externally exposed accessible parts (RF terminals, antenna terminals, video and audio
input and output terminals, microphone jacks, earphone jacks, etc.).
Measuring Method : (Power ON)
Insert load Z between earth ground/power cord plug prongs and externally exposed accessi-
ble parts. Use an AC voltmeter to measure across both terminals of load Z. See figure 9 and
following table 2.
5. Grounding (Class 1 model only)
Confirm specified or lower grounding impedance between earth pin in AC inlet and externally exposed accessible parts (Video in,
Video out, Audio in, Audio out or Fixing screw etc.).
Measuring Method:
Connect milli ohm meter between earth pin in AC inlet and exposed accessible parts. See figure 10 and grounding specifications.
d'
d
Chassis Power cord,
primary wire
Region
USA & Canada
Europe & Australia
Grounding Impedance (Z)
Z 0.1 ohm
Z 0.5 ohm
≤
≤
AC inlet
Earth pin
Exposed accessible part
Milli ohm meter
Grounding Specifications
Fig. 10
ab
c
V
Externally
exposed
accessible part
Z
Fig. 9
Fig. 8
Clearance Distance (d), (d')
d, d' 3 mm
d, d' 4 mm
d, d' 3.2 mm
1 MΩR 12 MΩ/500 V DC
Dielectric Strength
AC 1 kV 1 minute
AC 1.5 kV 1 miute
AC 1 kV 1 minute
AC Line Voltage
100 V
100 to 240 V
110 to 130 V
110 to 130 V
200 to 240 V
Japan
USA & Canada
Europe & Australia R 10 MΩ/500 V DC
Region
Insulation Resistance (R)
R 1 MΩ/500 V DC
≤
≤
≥≥
≤
≤
≤≤
≤
≤
AC 3 kV 1 minute
(Class 2)
AC 1.5 kV 1 minute
(Class 1)
d 4 mm
d' 8 mm (Power cord)
d' 6 mm (Primary wire)
Table 1 Specifications for each region
a, b, cLeakage Current (i)AC Line Voltage
100 V
110 to 130 V
110 to 130 V
220 to 240 V
Japan
USA & Canada
i 1 mA rms Exposed accessible parts
Exposed accessible parts
Antenna earth terminals
Other terminals
i 0.5 mA rms
i 0.7 mA peak
i 2 mA dc
i 0.7 mA peak
i 2 mA dc
Europe & Australia
Region Load Z
≤
≤
≤
≤
≤
≤
1 kΩ
2 kΩ
1.5 kΩ
0.15 µF
50 kΩ
Table 2 Leakage current specifications for each region
Note: These tables are unofficial and for reference only. Be sure to confirm the precise values for your particular country and locality.
2S40888-01

DISASSEMBLY INSTRUCTIONS
1-1
1.
1-1:
1
1
2
Top Cabinet
Front Cabinet
Fig. 1-1
REMOVAL OF MECHANICAL PARTS
AND P.C. BOARDS
TOP CABINET AND FRONT CABINET
(Refer to Fig. 2-1)
1.
2.
3.
4.
Remove the 4 screws 1.
Remove the Top Cabinet in the direction of arrow (A).
Unlock the 7 supports 2.
Remove the Front Cabinet in the direction of arrow (B).
1-2: FLAP (Refer to Fig. 1-2)
1.
2.
Open Flap to 90˚ and flex in direction of arrow (A), at the
same time slide in direction of arrow (B).
Then lift in direction of arrow (C).
1-3: DECK CHASSIS (Refer to Fig. 1-3)
1.
2.
3.
4.
5.
6.
Remove the screw 1.
Remove the 2 screws 2.
Unlock the 3 supports 3.
Remove the BOT PCB in the direction of arrow (A).
Disconnect the following connectors: (CP1001, CP4001,
CP4002 and CP4003).
Remove the Deck Chassis in the direction of arrow (B).
Fig. 1-2
(A)
Flap
(B)
(C)
1
1
(A)
2
2
2
2
2
2
(B)
Fig. 1-3
1-4: SYSCON PCB (Refer to Fig. 1-4)
1.
2.
3.
4.
Remove the screw 1.
Remove the screw 2.
Remove the 2 screws 3.
Remove the Syscon PCB in the direction of arrow.
Fig. 1-4
1
2
Syscon PCB
2
1
Deck Chassis
Bottom Plate
CP4003
2
CP4001
(B)
(A)
CP4002
CP1001
BOT PCB
33
Bottom Plate
3
3
3

1-2
DISASSEMBLY INSTRUCTIONS
2. REMOVAL OF VCR DECK PARTS
2-1: TOP BRACKET (Refer to Fig. 2-1)
Extend the 2 supports1.
Slide the 2 supports 2and remove the Top Bracket.
1.
2.
NOTE
After the installation of the Top Bracket, bend the support
1so that the Top Bracket is fixed.
1.
11
2
2
Top Bracket
Main Chassis
Top Bracket
Main Chassis
Fig. 2-1
1.
2.
3.
2-2: CASSETTE HOLDER ASS'Y (Refer to Fig. 2-2)
Move the Cassette Holder Ass'y to the front side.
Push the Locker R to remove the Cassette Side R.
Remove the Cassette Side L.
Fig. 2-2
Link Unit Main Chassis
Main Chassis
Cassette Side L
Cassette Side R
Locker R
1.
2.
3.
2-3: CASSETTE SIDE L/R (Refer to Fig. 2-3-A)
Remove the Locker Spring.
Unlock the 4 supports1and then remove the Cassette
Side L/R.
Unlock the support 2and then remove the Locker R.
Locker Spring
Cassette Side L
Cassette Side R
Locker R
Cassette Holder
1
1
1
1
2
In case of the Locker R installation, check if the one
position of Fig. 2-3-B are correctly locked.
When you install the Cassette Side R, be sure to move
the Locker R after installing.
NOTE
1.
2.
Locker R
Check if this position
is locked.
Cassette Side R
Fig. 2-3-B
2-4: LINK UNIT (Refer to Fig. 2-4)
1.
2.
3.
Set the Link Unit to the Eject position.
Unlock the support 1.
Remove the (A) side of the Link Unit first, then remove
the (B) side.
Fig. 2-4
(A)
Link Unit
Main Chassis
(B)
Link Unit
Main Chassis
Fig. 2-3-A
2-5: LINK LEVER/FLAP LEVER/SENSOR COVER R
(Refer to Fig. 2-5)
1.
2.
3.
4.
5.
Unlock the support 1.
Remove the Sensor Cover R.
Extend the support 2.
Remove the Link Lever.
Remove the Flap Lever.
Fig. 2-5
Link Lever
Flap Lever
2
1Sensor Cover R

1-3
DISASSEMBLY INSTRUCTIONS
2-6: LOADING MOTOR/WORM (Refer to Fig. 2-6-A)
1.
2.
3.
Remove the screw 1.
Remove the Loading Motor.
Remove the Worm.
Fig. 2-6-A
Loading Motor
Worm
• Screw Torque: 3 ±0.5kgf•cm
Main Chassis
1
NOTE
1.
2.
3.
In case of the Worm installation, check if the value of the
Fig. 2-6-B is correct.
In case of the Loading Motor installation, hook the wire on
the Cassette Opener as shown Fig. 2-6-C.
When installing the wires between Capstan DD Unit and
Loading Motor, connect them correctly as shown Fig. 2-6-D.
Fig. 2-6-B
19.2 ±0.1mm
Safety surface for pressing
of the insert.
2-7: TENSION ASS’Y (Refer to Fig. 2-7-B)
1.
2.
3.
4.
5.
6.
Turn the Pinch Roller Cam clockwise so that the Tension
Holder hook is set to the position of Fig. 2-7-A to move
the Tension Arm Ass’y.
Remove the Tension Spring.
Unlock the 2 supports1and remove the Tension Band.
Unlock the support 2and remove the Tension Arm Ass’y.
Unlock the support 3and remove the Tension Connect.
Float the hook 4and turn it clockwise then remove the
Tension Holder.
Fig. 2-6-C
Loading Motor
Cassette Opener
Fig. 2-7-B
Tension Band
Tension Connect
Tension Spring Tension Arm Ass’y
Tension Holder
1
1
3
2
4
NOTE
1.
2.
3.
In case of the Tension Band installation, note the direc-
tion of the installation. (Refer to Fig. 2-7-C)
In case of the Tension Band installation, install correctly
as Fig. 2-7-D.
In case of the Tension Connect installation, install as the
circled section of Fig. 2-7-E.
Fig. 2-7-C
Tension Band
Tension Connect
Tension Arm Ass’y
Fig. 2-7-A
Fig. 2-6-D
Pink
Loading Motor
White
Capstan DD Unit
L2
L1
-
+

1-4
DISASSEMBLY INSTRUCTIONS
Fig. 2-7-D
[OK]
[NG]
Tension Connect
Tension Band
Tension Connect Tension Band
Fig. 2-7-E
Tension Connect
Main Chassis
2-8: T BRAKE ARM/T BRAKE BAND (Refer to Fig. 2-8-A)
Remove the T Brake Spring.
Turn the T Brake Arm clockwise and bend the hook
section to remove it.
Unlock the 2 supports 1and remove the T Brake Band.
1.
2.
3.
Fig. 2-8-A
T Brake Band
Hook section
T Brake Arm
T Brake Spring
1
1
NOTE
1. In case of the T Brake Band installation, install correctly
as Fig. 2-8-B.
Fig. 2-8-B
[OK]
[NG]
T Brake Arm
T Brake Band
T Brake Arm
T Brake Band
2-9: S REEL/T REEL/IDLER ARM ASS’Y/IDLER GEAR
(Refer to Fig. 2-9-A)
1.
2.
3.
Remove the S Reel and T Reel.
Remove the 2 Polyslider Washers 1.
Remove the Idler ArmAss’y and Idler Gear.
NOTE
1.
2.
3.
4.
5.
6.
Take care not to damage the gears of the S Reel and T
Reel.
The Polyslider Washer may be remained on the back of
the reel.
Take care not to damage the shaft.
Do not touch the section “A” of S Reel and T Reel. (Use
gloves.) (Refer to Fig. 2-9-A) Do not adhere the stains
on it.
When you install the reel, clean the shaft and grease it
(FG-84M). (If you do not grease, noise may be heard in
FF/REW mode.)
After installing the reel, adjust the height of the reel.
(Refer to MECHANICAL ADJUSTMENT)
Fig. 2-9-A
Idler Gear Idler Arm Ass’y
S Reel
T Reel
(A)
1
1
(A)
NOTE
1.
2.
In case of the S Reel and T Reel installation, check if the
correct parts are installed. (Refer to Fig. 2-9-B)
In case of the Idler Arm Ass’y installation, install correctly
as Fig. 2-9-C. And also set it so that the section “B” of
Fig. 2-9-A is placed under the Main Chassis tab.
Fig. 2-9-B
Big Hole
(S Reel) Small Hole
(T Reel)
Fig. 2-9-C
[OK]
[NG]
Clutch Gear Idler Arm Ass’y
Idler Arm Ass’y
Clutch Gear
(B)

1-5
DISASSEMBLY INSTRUCTIONS
2-10: CASSETTE OPENER/PINCH ROLLER BLOCK/P5
ARM ASS’Y (Refer to Fig. 2-10-A)
1.
2. Unlock the support 1and remove the Cassette Opener.
Remove the Pinch Roller Block and P5Arm Ass’y.
Fig. 2-10-A
Cassette Opener
1
Pinch Roller Block
P5 Arm Ass’y
Main Chassis
NOTE
1.
2. Do not touch the Pinch Roller. (Use gloves.)
In case of the Pinch Roller Block and the Pinch Roller
Cam installation, install correctly as Fig. 2-10-B.
Fig. 2-10-B
Pinch Roller Block Can be seen the hole of
the Pinch Roller Cam.
P5 Arm Ass’y
Can be seen the hole of the
Main Cam.
2-11: A/C HEAD (Refer to Fig. 2-11-A)
1.
2.
3.
4.
Remove the screw 1.
Remove the A/C Head Base.
Remove the 3 screws 2.
Remove the A/C Head and A/C Head Spring.
NOTE
1.
2.
3.
Do not touch the A/C Head. (Use gloves.)
When you install the A/C Head Spring, install as shown in
Fig. 2-11-B.
When you install the A/C Head, tighten the screw (1) first,
then tighten the screw (2), finally tighten the screw (3).
Fig. 2-11-A
(1)
2
A/C Head
A/C Head Spring
A/C Head Base
• Screw Torque: 5 ±0.5kgf•cm (Screw 1)
2
2
(3)
(2)
1
Fig. 2-11-B
Spring Position
2-12: FE HEAD (RECORDER ONLY) (Refer to Fig. 2-12)
1.
2. Remove the screw 1.
Remove the FE Head.
Fig. 2-12
1
FE Head
• Screw Torque: 5 ±0.5kgf•cm
• The FE Head is not installed on the Video Cassette Player.
2-13: CYLINDER UNIT ASS’Y (Refer to Fig. 2-13)
1.
2.
3.
Disconnect the following connector:
(CD2001)
Remove the 3 screws 1.
Remove the Cylinder Unit Ass’y.
NOTE
1. When you install the Cylinder Unit Ass’y, tighten the
screws from (1) to (3) in order while pulling the Ass’y
toward the left front direction.
Fig. 2-13
Cylinder Unit Ass’y
1
(1)
• Screw Torque: 3 ±
0.5kgf•cm
1
1
(2)
(3)
CD2001

1-6
DISASSEMBLY INSTRUCTIONS
2-14: CAPSTAN DD UNIT (Refer to Fig. 2-14-A)
1.
2.
3.
Remove the Capstan Belt.
Remove the 3 screws 1.
Remove the Capstan DD Unit.
Fig. 2-14-A
Capstan Belt
Capstan DD Unit
• Screw Torque: 4 ±0.5kgf•cm
1
11
2-15: MAIN CAM/PINCH ROLLER CAM/JOINT GEAR
(Refer to Fig. 2-15-A)
1.
2. Remove the E-Ring 1, then remove the Main Cam.
Remove the E-Ring 2, then remove the Pinch Roller
Cam and Joint Gear.
Fig. 2-15-A
1
Main Cam
Pinch Roller Cam
Joint Gear
2
NOTE
1. In case of the Pinch Roller Cam and Main Cam installa-
tion, install them as the circled section of Fig. 2-15-B so
that the each markers are met. (Refer to Fig. 2-15-B)
And also can be seen the Main Chassis hole through the
Main Cam maker hole.
Fig. 2-15-B
Pinch Roller Cam
Marker
Main Cam
2-16: LOADING GEAR S/T UNIT (Refer to Fig. 2-16-A)
1.
2.
Remove the E-Ring 1and remove the Main Loading
Gear.
Remove the Main Rod, Tension Lever, Loading Arm S
Unit and Loading Arm T Unit.
1
Main Loading Gear
Main Rod
Tension Lever Loading ArmT Unit
Loading Arm S Unit
Fig. 2-16-A
NOTE
1. In case of the Capstan DD Unit installation, apply the
silicon bond (TSE3843-W) on the position Fig. 2-14-B
correctly. (If no silicon bond applied, abnormal noise will
be heard on the deck operation.)
(Refer to Fig. 2-14-B, C)
Fig. 2-14-B
Applied position of
silicon bond
Be careful not to apply the silicon
bond to the Pinch Roller.
Fig. 2-14-C
Silicon Bond
Main Chassis
Capstan DD Unit

1-7
DISASSEMBLY INSTRUCTIONS
1
Clutch Ass’y
Ring Spring
Clutch Lever
Coupling Gear
Coupling Spring
Clutch Gear
NOTE
1. When you install the Loading Arm S Unit, Loading Arm T
Unit and Main Loading Gear, align each marker. (Refer
to Fig. 2-16-B)
Fig. 2-16-B
Marker
Main Loading Gear
Loading Arm T Unit Loading Arm S Unit
Marker
2-17: CLUTCH ASS’Y/RING SPRING/CLUTCH LEVER/
CLUTCH GEAR (Refer to Fig. 2-17-A)
1.
2.
3.
4.
Remove the Polyslider Washer 1.
Remove the Clutch Ass’y and Ring Spring.
Remove the Clutch Lever.
Remove the Coupling Gear, Coupling Spring and Clutch
Gear.
Fig. 2-17-A
NOTE
1. In case of the Clutch Ass’y installation, install it with
inserting the spring of the ClutchAss’y into the dent of the
Coupling Gear. (Refer to Fig. 2-17-B)
Fig. 2-17-B
Clutch Ass’y
Coupling Gear
2-18: CASSETTE GUIDE POST/INCLINED BASE S/T
UNIT/P4 CAP (Refer to Fig. 2-18-A)
1.
2.
3.
4.
5.
Remove the P4 Cap.
Unlock the support 1and remove the Cassette Guide
Post.
Remove the Inclined Base S/T Unit.
Remove the screw 2.
Remove the LED Reflector.
Fig. 2-18-A
NOTE
1.
2.
3.
Do not touch the roller of Guide Roller.
In case of the P4 Cap installation, install it with parallel
for “A” and “B” of Fig. 2-18-B.
In case of the Cassette Guide Post installation, install
correctly as the circled section of Fig. 2-18-C.
Fig. 2-18-B
“A” “B”
P4 Cap Cassette Opener
Fig. 2-18-C
[OK]
Cassette Guide Post
[NG]
Cassette Guide Post
Cassette Guide Post
Inclined Base S
Unit Inclined Base T
Unit
P4 Cap
1
2
LED Reflector

1-8
KEY TO ABBREVIATIONS
A
B
C
D
E
F
G
H
A/C
ACC
AE
AFC
AFT
AFT DET
AGC
AMP
ANT
A.PB
APC
ASS’Y
AT
AUTO
A/V
BGP
BOT
BPF
BRAKE SOL
BUFF
B/W
C
CASE
CAP
CARR
CH
CLK
CLOCK (SY-SE)
COMB
CONV
CPM
CTL
CYL
CYL-M
CYL SENS
DATA (SY-CE)
dB
DC
DD Unit
DEMOD
DET
DEV
E
EF
EMPH
ENC
ENV
EOT
EQ
EXT
F
FBC
FE
FF
FG
FL SW
FM
FSC
FWD
GEN
GND
H.P.F
:
:
:
:
:
:
:
:
:
:
:
:
:
:
:
:
:
:
:
:
:
:
:
:
:
:
:
:
:
:
:
:
:
:
:
:
:
:
:
:
:
:
:
:
:
:
:
:
:
:
:
:
:
:
:
:
:
:
:
:
:
:
Audio/Control
Automatic Color Control
Audio Erase
Automatic Frequency Control
Automatic Fine Tuning
Automatic Fine Tuning Detect
Automatic Gain Control
Amplifier
Antenna
Audio Playback
Automatic Phase Control
Assembly
All Time
Automatic
Audio/Video
Burst Gate Pulse
Beginning of Tape
Bandpass Filter
Brake Solenoid
Buffer
Black and White
Capacitance, Collector
Cassette
Capstan
Carrier
Channel
Clock
Clock (Syscon to Servo)
Combination, Comb Filter
Converter
Capstan Motor
Control
Cylinder
Cylinder-Motor
Cylinder-Sensor
Data (Syscon to Servo)
Decibel
Direct Current
Direct Drive Motor Unit
Demodulator
Detector
Deviation
Emitter
Emitter Follower
Emphasis
Encoder
Envelope
End of Tape
Equalizer
External
Fuse
Feed Back Clamp
Full Erase
Fast Forward, Flipflop
Frequency Generator
Front Loading Switch
Frequency Modulation
Frequency Sub Carrier
Forward
Generator
Ground
High Pass Filter
I
K
L
M
N
O
P
R
S
H.SW
Hz
IC
IF
IND
INV
KIL
L
LED
LIMIT AMP
LM, LDM
LP
L.P.F
LUMI.
M
MAX
MINI
MIX
MM
MOD
MPX
MS SW
NC
NR
OSC
OPE
PB
PB CTL
PB-C
PB-Y
PCB
P. CON
PD
PG
P-P
R
REC
REC-C
REC-Y
REEL BRK
REEL S
REF
REG
REW
REV, RVS
RF
RMC
RY
S. CLK
S. COM
S. DATA
SEG
SEL
SENS
SER
SI
SIF
SO
SOL
SP
STB
SW
:
:
:
:
:
:
:
:
:
:
:
:
:
:
:
:
:
:
:
:
:
:
:
:
:
:
:
:
:
:
:
:
:
:
:
:
:
:
:
:
:
:
:
:
:
:
:
:
:
:
:
:
:
:
:
:
:
:
:
:
:
:
Head Switch
Hertz
Integrated Circuit
Intermediate Frequency
Indicator
Inverter
Killer
Left
Light Emitting Diode
Limiter Amplifier
Loading Motor
Long Play
Low Pass Filter
Luminance
Motor
Maximum
Minimum
Mixer, mixing
Monostable Multivibrator
Modulator, Modulation
Multiplexer, Multiplex
Mecha State Switch
Non Connection
Noise Reduction
Oscillator
Operation
Playback
Playback Control
Playback-Chrominance
Playback-Luminance
Printed Circuit Board
Power Control
Phase Detector
Pulse Generator
Peak-to Peak
Right
Recording
Recording-Chrominance
Recording-Luminance
Reel Brake
Reel Sensor
Reference
Regulated, Regulator
Rewind
Reverse
Radio Frequency
Remote Control
Relay
Serial Clock
Sensor Common
Serial Data
Segment
Select, Selector
Sensor
Search Mode
Serial Input
Sound Intermediate Frequency
Serial Output
Solenoid
Standard Play
Serial Strobe
Switch

1-9
KEY TO ABBREVIATIONS
S
T
U
V
X
Y
SYNC
SYNC SEP
TR
TRAC
TRICK PB
TP
UNREG
V
VCO
VIF
VP
V. P B
VR
V.REC
VSF
VSR
VSS
V-SYNC
VT
X’TAL
Y/C
:
:
:
:
:
:
:
:
:
:
:
:
:
:
:
:
:
:
:
:
:
Synchronization
Sync Separator, Separation
Transistor
Tracking
Trick Playback
Test Point
Unregulated
Volt
Voltage Controlled Oscillator
Video Intermediate Frequency
Vertical Pulse, Voltage Display
Video Playback
Variable Resistor
Video Recording
Visual Search Fast Forward
Visual Search Rewind
Voltage Super Source
Vertical-Synchronization
Voltage Tuning
Crystal
Luminance/Chrominance

1-10
PREVENTIVE CHECKS AND SERVICE INTERVALS
The following standard table depends on environmental conditions and usage.
Parts replacing time does not mean the life span for individual parts.
Also, long term storage or misuse may cause transformation and aging of rubber parts.
The following list means standard hours, so the checking hours depends on the conditions.
CLEANING
NOTE
After cleaning the heads with isopropyl alcohol, do not
run a tape until the heads dry completely. If the heads are
not completely dry and alcohol gets on the tape, damage
may occur.
1. AUDIO CONTROL HEAD
Clean the Audio Control Head with the cotton stick
soaked by alcohol. Clean the full erase head in the same
manner. (Refer to the figure below.)
Audio Control Head
2. TAPE RUNNING SYSTEM
When cleaning the tape transport system, use the gauze
moistened with isopropyl alcohol.
3. CYLINDER
Wrap a piece of chamois around your finger. Dip it in
isopropyl alcohol. Hold it to the cylinder head softly.
Turn the cylinder head counterclockwise to clean it (in the
direction of the arrow). (Refer to the figure below.)
NOTE
Do not exert force against the cylinder head. Do not move
the chamois upward or downward on the head.
Use the chamois one by one.
Cylinder Head
: Clean
: Check it and if necessary, replace it.
Time
Parts Name 500
hours 1,000
hours Notes
1,500
hours 2,000
hours 2,500
hours
Audio Control Head
Full Erase Head
(Recorder only)
Capstan Belt
Pinch Roller
Capstan DD Unit
Loading Motor
Tension Band
Capstan Shaft
Tape Running
Guide Post
Cylinder Unit
Clean those parts in
contact with the tape.
Clean the rubber, and parts
which the rubber touches.
Replace when rolling
becomes abnormal.
Clean the Head
T Brake Band
Clutch Ass’y
Idler Arm Ass’y

1-11
SERVICE MODE LIST
This unit provided with the following SERVICE MODES so you can repair, examine and adjust easily.
Method Operations
Make the short circuit
between the test point of
SERVICE and the GND.
The BOT, EOT, and the Reel Sensor do not work and the deck can be operated
without a cassette tape.
Refer to the “PREPARATION FOR SERVICING”
SERVICING FIXTURES AND TOOLS
VHS Alignment Tape
MHP Torque Gauge
PUJ48075-2 Roller Driver
PTU94002-2 X-JG153 X Value Adjustment
Screwdriver
Short Jumper
MECHANISM ADJUSTMENT PARTS LOCATION GUIDE
Tension Connect
Tension Arm
Guide Roller
Audio/Control Head
X value adjustment driver hole
P4 Post
T Brake Spring
T Reel
S Reel
Adjusting section for the Tension Arm position
1.
2.
3.
4.
5.
6.
7.
8.
9.
10.
1
2
3
4
5
6
7
8910
VHS Alignment Tape
MHP-L
Torque Tape
PUJ48076-2
<NOTE> WHEN "N" IS ALWAYS BEING DISPLAYED ON THE TV MONITOR.
(REMOTE CONTROLLER FORMAT)
This product is usable the remote controller which is used by VHS of the other brand.
If "N" is always being displayed on the TV monitor, can not control from provided remote controller since this product is other
brand format.
• How to return a JVC format.
Turn off the power of the set and push the CHANNEL+ button and the REC button of the set simultaneously.

1-12
1-3: CONFIRMATION OF VSR TORQUE
1.
2.
Install the Torque Gauge on the S Reel. Set to the Picture
Search (Rewind) mode. (Refer to Fig.1-2-B)
Then, confirm that it indicates 120~180gf•cm.
NOTE
Install the Torque Gauge on the reel disk firmly. Press the
REW button to turn the reel disk.
MECHANICAL ADJUSTMENTS
1. CONFIRMATION AND ADJUSTMENT
Read the following NOTES before starting work.
• Place an object which weighs between 450g~500g on the
Cassette Tape to keep it steady when you want to make
the tape run without the Cassette Holder. (Do not place
an object which weighs over 500g.)
Remove the Top Cabinet and Front Cabinet.
(Refer to item 1 of the DISASSEMBLY INSTRUCTIONS.)
Remove the screw 1of the Deck Chassis and remove the
Loading Motor.
Rotate the Pinch Roller Cam in the direction of the arrow by
hand to slacken the Video Tape.
Rotate the Clutch Ass'y either of the derections to wind the
Video Tape in the Cassette Case.
Repeat the above step 3~4.Then take out the Video
Cassette from the Deck Chassis.
Be careful not to scratch on the tape.
TAPE REMOVAL METHOD AT NO POWER
SUPPLY
1.
2.
3.
4.
5.
Main Cam Clutch Ass'y
Main Chassis (Front Side)
Loading Motor
Capstan DD Unit
Pinch Roller Cam
Screw 1
1-1: CONFIRMATION AND ADJUSTMENT OF TENSION
POST POSITION
1.
2.
3.
Set to the PLAY mode.
Adjust the adjusting section for the Tension Arm position
so that the Tension Arm top is within the standard line of
Main Chassis.
While turning the S Reel clockwise, confirm that the edge
of the Tension Arm is located in the position described
above.
Fig. 1-1-A
Standard line of Main Chassis
Tension Arm
0.5mm (Adjusting range)
Fig. 1-1-B
Adjusting section for the
Tension Arm position
Tension Band
The Tension Arm top will
move to the inside direction
of the Main Chassis.
The Tension Arm top will
move to the outside direction
of the Main Chassis.
Bend
1-2: CONFIRMATION OF PLAYBACKTORQUE AND
BACK TENSION TORQUE DURING PLAYBACK
1.
2.
3.
After confirmation and adjustment of Tension Post
position (Refer to item 1-1), load the cassette type
torque tape and set to the PLAY mode.
Confirm that the right meter of the torque tape indicates
50~90gf•cm during playback in SP mode.
Confirm that the left meter of the torque tape indicates
25~40gf•cm during playback in SP mode.

1-13
MECHANICAL ADJUSTMENTS
1-4: CONFIRMATION OF REEL BRAKE TORQUE
(S Reel Brake) (Refer to Fig. 1-2-B)
1.
2.
3.
4.
Once set to the Fast Forward mode then set to the Stop
mode. While, unplug theAC cord when the Pinch Roller
Block is on the position of Fig. 1-2-A.
Move the Idler Ass’y from the S Reel.
Install the Torque Gauge on the S Reel. Turn the Torque
Gauge clockwise.
Then, confirm that it indicates 60~100gf•cm.
(T Reel Brake) (Refer to Fig. 1-2-B)
1.
2.
3.
4.
Once set to the Fast Forward mode then set to the Stop
mode. While, unplug theAC cord when the Pinch Roller
Block is on the position of Fig. 1-2-A.
Move the Idler Ass’y from the T Reel.
Install the Torque Gauge on the T reel. Turn the Torque
Gauge counterclockwise.
Then, confirm that it indicates 30~50gf•cm.
Fig. 1-2-A
The position at FF mode.
Stop at this position.
The position at
STOP mode.
Capstan DD Unit
Cassette HolderAss’y
Cassette Opener
Pinch Roller Block
Fig. 1-2-B
Torque Gauge
Torque Gauge
S Reel
T Reel
2. CONFIRMATION AND ADJUSTMENT OF
TAPE RUNNING MECHANISM
Tape Running Mechanism is adjusted precisely at the
factory.Adjustment is not necessary as usual. When you
replace the parts of the tape running mechanism because of
long term usage or failure, the confirmation and adjustment
are necessary.
2-1: GUIDE ROLLER
1.
2.
3.
4.
5.
6.
Playback the VHS Alignment Tape (MHP).
Connect CH-1 of the oscilloscope to TP4001 (Envelope)
and CH-2 to TP1002 (SW Pulse).
Trigger with SW Pulse and observe the envelope. (Refer
to Fig. 2-1-A)
When observing the envelope, adjust the Roller Driver
(PTU94002-2) slightly until the envelope will be flat.
Even if you press the Tracking Button, adjust so that
flatness is not moved so much. (Refer to Fig. 2-1-B)
Adjust so that the A : B ratio is better than 3 : 2 as shown
in Fig. 2-1-C, even if you press the Tracking Button to
move the envelope (The envelope waveform will begin to
decrease when you press the Tracking Button).
Adjust the PG shifter during playback.
(Refer to the ELECTRICALADJUSTMENTS)
NOTE
After adjustment, confirm and adjustA/C head.
(Refer to item 2-2)
Fig. 2-1-A
CH-1
Envelope
(TP4001)
CH-1
Track CH-2
Track
CH-2
SW Pulse (TP1002)
NOTE
If the torque is out of the range, replace the following parts.
Check item
1-3 Replacement Part
Idler Ass’y/Clutch Ass’y
S Reel side:
T Reel side:
S Reel/Tension Band/Tension
Connect/Tension Arm Ass’y
T Reel/T Brake Band//T Brake
Spring/T Brake Arm
1-4
Fig. 2-1-C
Entrance
Max
Exit
MaxA B
A : B ≥3 : 2
Fig. 2-1-B
Improper Proper
(a) Guide roller
(b) P4 Cap

1-14
Play MHP
Drum side Control head position Capstan side
X-value adjustment point
Maximum
Waveform output
MECHANICAL ADJUSTMENTS
2-2: CONFIRMATION AND ADJUSTMENT OF AUDIO/
CONTROL HEAD
When the Tape Running Mechanism does not work well,
adjust the following items.
1.
2.
3.
4.
Playback the VHS Alignment Tape (MHP).
Confirm that the reflected picture of stamp mark is
appeared on the tape prior to P4 Post as shown in Fig. 2-
2-A.
a)
b)
Turn the screw 2to set the audio level to maximum.
Confirm that the bottom of the Audio/ Control Head and
the bottom of the tape is shown in Fig. 2-2-C.
c)
When the reflected picture is distorted, turn the screw
1clockwise until the distortion is disappeared.
When the reflected picture is not distorted, turn the
screw 1counterclockwise until little distortion is
appeared, then adjust the a).
When the height is not correct, turn the screw 3to
adjust the height. Then, adjust the 1~3 again.
Fig. 2-2-A
Audio/Control Head
Reflected picture of
Stamp Mark
P4 Cap
Stamp Mark
Fig. 2-2-B
3
Audio/Control Head
2
1
4
Fig. 2-2-C
Audio/Control Head
Tape
0.25±0.05mm
2-3: TAPE RUNNING ADJUSTMENT
(X VALUE ADJUSTMENT)
1.
2.
3.
4.
5.
6.
Confirm and adjust the position of the Tension Post.
(Refer to item 1-1)
Adjust the Guide Roller. (Refer to item 2-1)
Confirm and adjust the Audio/Control Head.
(Refer to item 2-2)
Connect CH-1 of the oscilloscope to TP1002, CH-2 to
TP4001 and CH-3 to HOT side of Audio Out Jack.
Playback the VHS Alignment Tape (MHP).
Set the X Value adjustment driver (X-JG153) to the 4of
Fig. 2-2-B. At first, turn the Audio/Control Head position
fully toward the capstan side. Then adjust X Value to turn
it back gradually toward the cylinder side and stop on the
second peak point position of the envelope.
Fig. 2-3
8.
9.
10.
Perform tracking operation and confirm the envelope is
maximum on the tracking center position.
Playback the VHS Alignment Tape (MHP-L).
Perform tracking operation and confirm the envelope is
maximum on the tracking center position. If envelope is
not maximum, should be fine-tune the X-VALUE.

ELECTRICAL ADJUSTMENTS
1-15
Read and perform this adjustment when repairing the
circuits or replacing electrical parts or PCB assemblies.
1. BASIC ADJUSTMENT
Fig. 1-1-B
6.5H
CH-1
CH-2
CH-1
CH-2
6.5H
Fig. 1-1-A
ELECTRICAL ADJUSTMENT PARTS LOCATION GUIDE (Connector Connections)
TP4001 (ENVELOPE)
TP1001 (SERVICE MODE)
TP1002 (HEAD SWITCHING PULSE)
VR1001
TP4201 (SWITCHING POINT)
J4201
AC IN
CD501
TU6001
J4203
J4204
J4205
FE HEAD
CP4003
CP4002
AC HEAD
CD4001
V651 OS651
CP1001
CAPSTAN DD UNIT
CD1503
CP1004
CP1002
BOT PCB (COMPONENT SIDE)
SYSCON PCB (COMPONENT SIDE)
CAUTION
• When you exchange IC and Transistor for a heat sink,
apply the silicon grease (YG6260M) on the contact section
of the heat sink. Before applying new silicon grease,
remove all the old silicon grease. (Old grease may cause
damages to the IC and Transistor.)
1-1: SWITCHING POINT
CONDITIONS
MODE-PLAYBACK
Input Signal-Alignment Tape (MHP)
INSTRUCTIONS
Connect CH-1 on the oscilloscope to TP1002 and CH-2
to TP4201.
Playback the alignment tape. (MHP)
Adjust the VR1001 until the waveform of the oscilloscope
measures 6.5 ±0.5(H) at both leading and trailing edges.
(Refer to Fig. 1-1-A, B)
1.
2.
3.

1-16
IC DESCRIPTIONS
VCR PCB OEC0131A (IC1001)
No. PORT PIN NAME I/O DESCRIPTION
1 SVSS SVSS - Ground.
2 CTLREF CTLREF Output terminal for CTL amp REF (1/2 SVCC)
3 CTL(+) CTL(+) Input and output terminal of Control Head.
4 CTL(-) CTL(-) Input terminal of Control Head.
5 CTLBIAS CTLBIAS Output terminal for bias.
6 CTLFB CTLFB Input terminal for CTL feedback
7 CTLAMP(O) CTLAMP(O) Output terminal for amp out.
8 CTLSMT(I) CTLSMT(I) Input terminal for CTL shumit amp .
9 CFG CAP FG Input terminal for CAPSTAN FG signal detection.
10 SVCC SVCC + 5V (Servo)
11 AFCPC AFCPC AFC oscilator (external circuit).
12 AFCOSC AFCOSC AFC oscilator (external circuit).
13 AFCLPF AFCLPF LPF connection for AFC OSC.
14 CSYNC/HSYNC CSYNC OUT Output terminal for composite SYNC.
15 VLPF/VSYNC VSYNC IN Input terminal for composite SYNC.(from 14pin)
16 CVIN2 CVIN2 IN Composite Video input terminal.(for data slicer)
17 CVIN1 CVIN1 IN Composite Video input terminal.(for OSD)
18 OSDVCC OSDVCC - + 5V
19 CVOUT CVOUT OUT Composite Video output.(with OSD)
20 OVSS OVSS - Ground.
21 4/2FSCOUT 4/2FSCOUT OUT 4 FSC pulse.
22 4/2FSCIN 4/2FSCIN IN 4 FSC pulse.
23 AVSS AVSS - Ground.
24 ANB PG IN Input voltage from Variable Resistor of PG SHIFTER.
25 ANA AFT S.CURVE IN AFT S CURVE input for tuner.
26 AN9 EOT-H IN Tape end sensor input signal.
27 AN8 ST SELECT IN Input terminal for the judgement of voice reception condition.
28 P07/AN7 HIFI ENV IN Input terminal of HiFi RF envelope.
29 P06/AN6 BOT-H IN Tape start sensor input signal.
30 P05/AN5 V ENV IN Input terminal of video RF envelope.
31 P04/AN4 MS SEN-B IN Input terminal of mecha state sensor.
32 P03/AN3 MS SEN-A IN
33 P02/AN2 KEY-B IN Main unit key input.
34 P01/AN1 KEY-A IN
35 P00/AN0 SLOW OFFSET IN Terminal for the offset of Slow.
36 AVCC AVCC - + 5V
37 P10/IRQ0 POWER FAIL IN Input terminal of Power fail signal.
38 P11/IRQ1 SP-L OUT Tape speed SP mode at the time of LOW.
39 P12/IRQ2 REEL-S IN Input terminal of reel sensor supply.
40 P13/IRQ3 REEL-T IN Input terminal of reel sensor take up.
Table of contents
Other JVC VCR System manuals
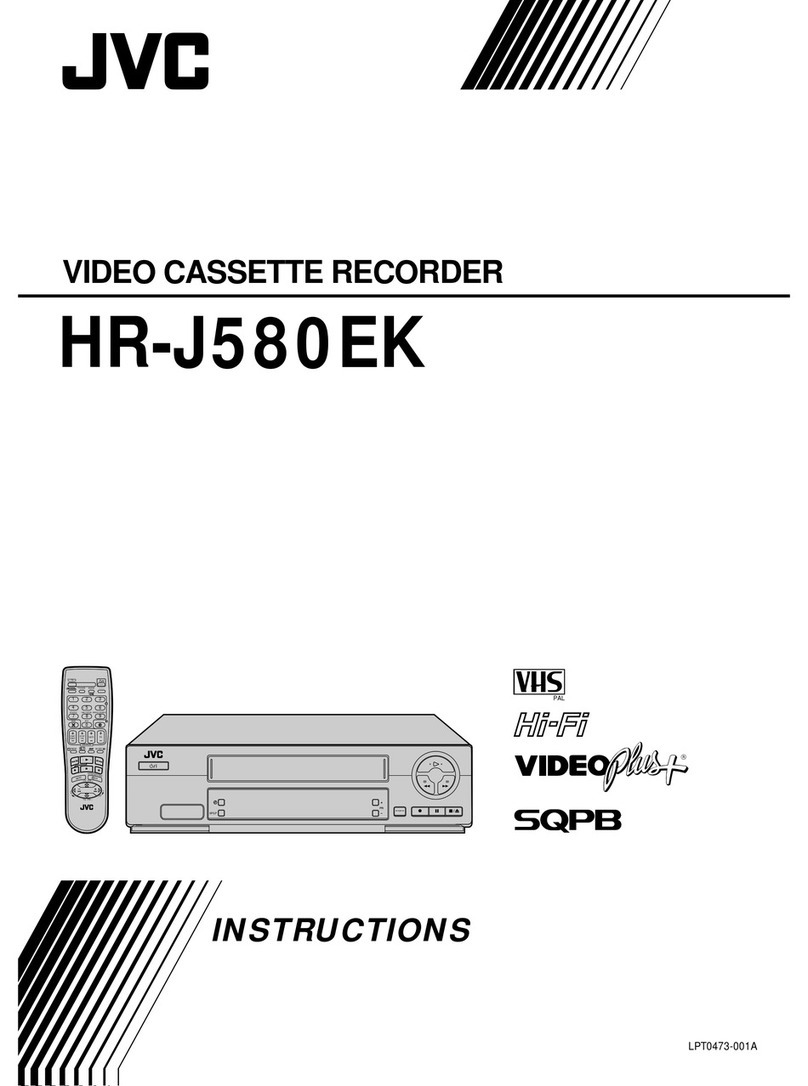
JVC
JVC HR-J580EK User manual
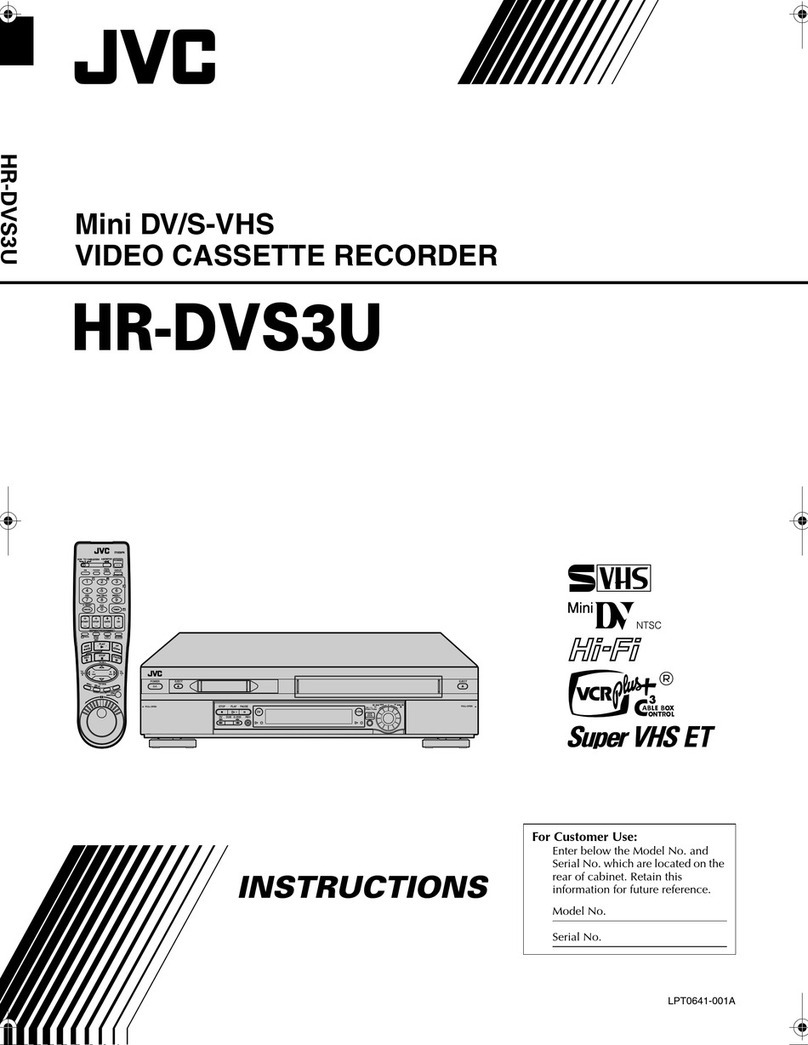
JVC
JVC LPT0641-001A User manual
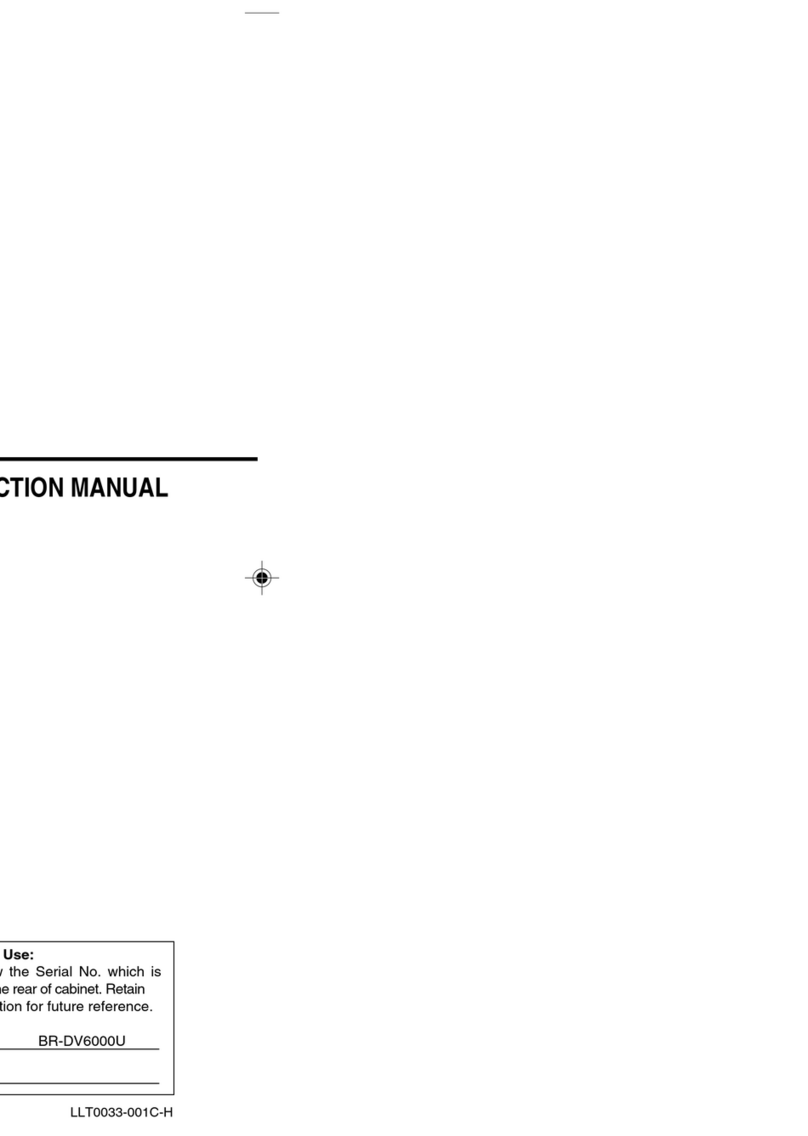
JVC
JVC BR-DV6000U - Advanced Professional DV... User manual
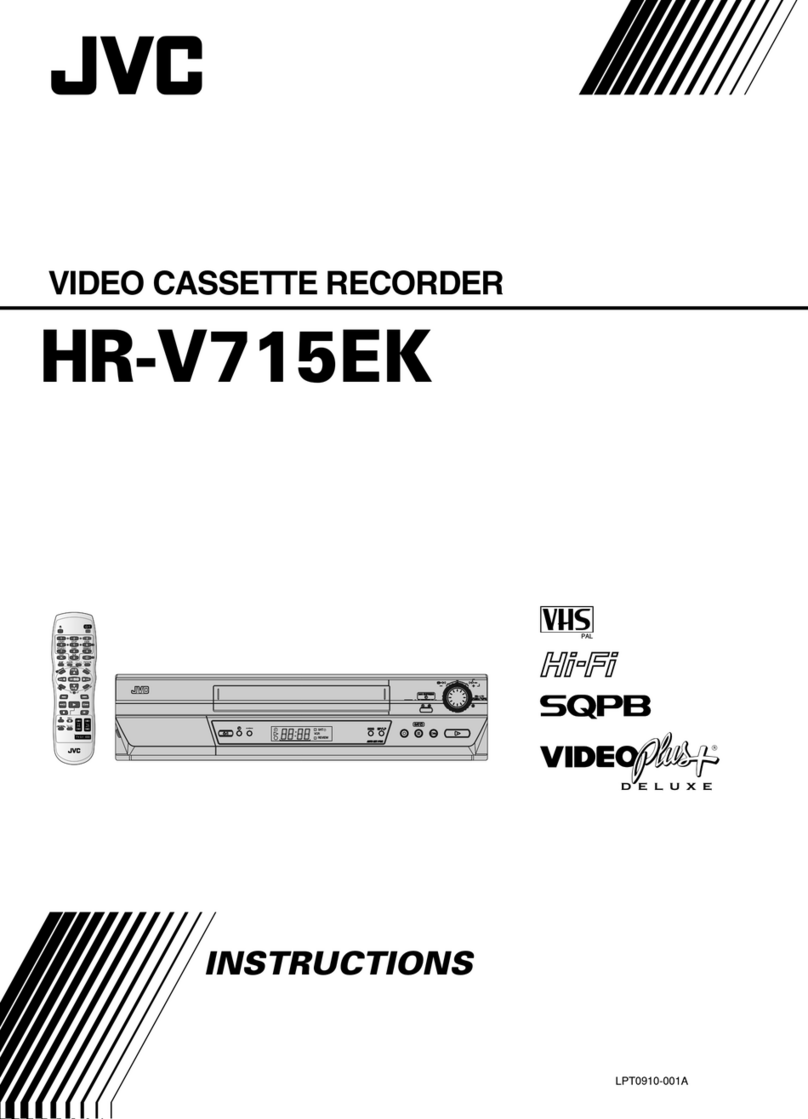
JVC
JVC HR-V715EK User manual
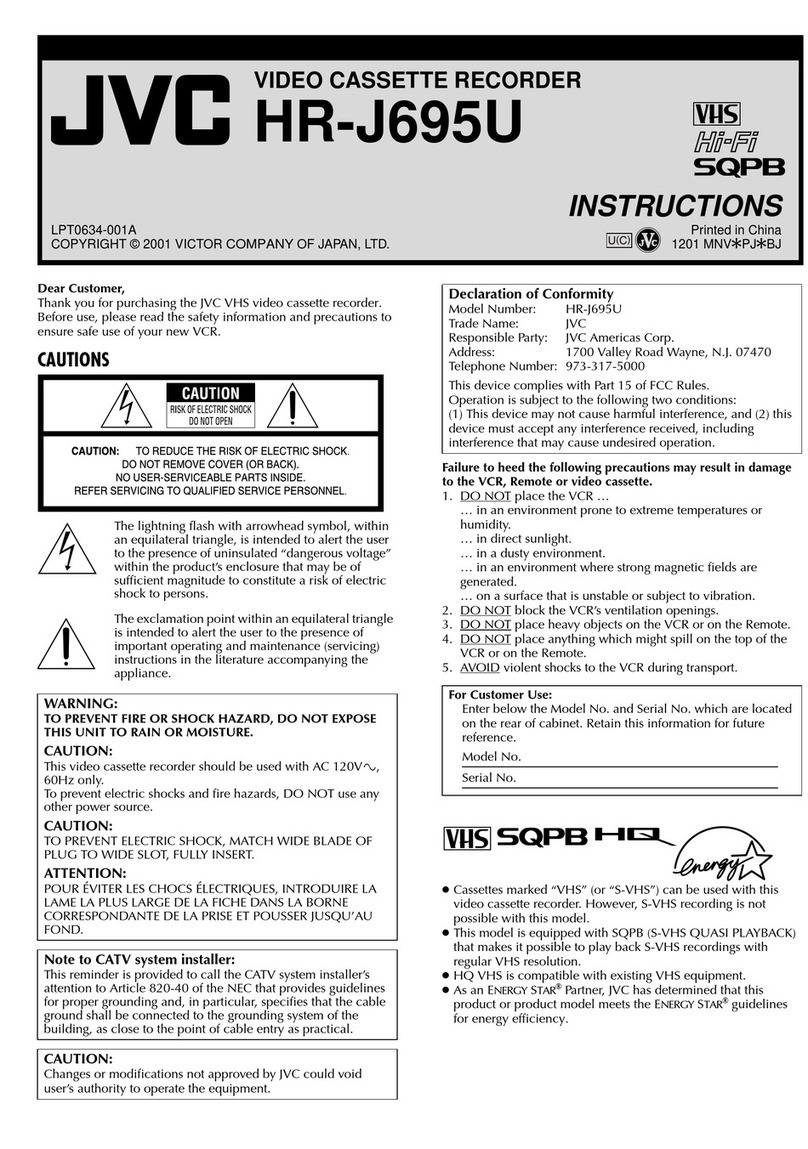
JVC
JVC HR-J695U User manual
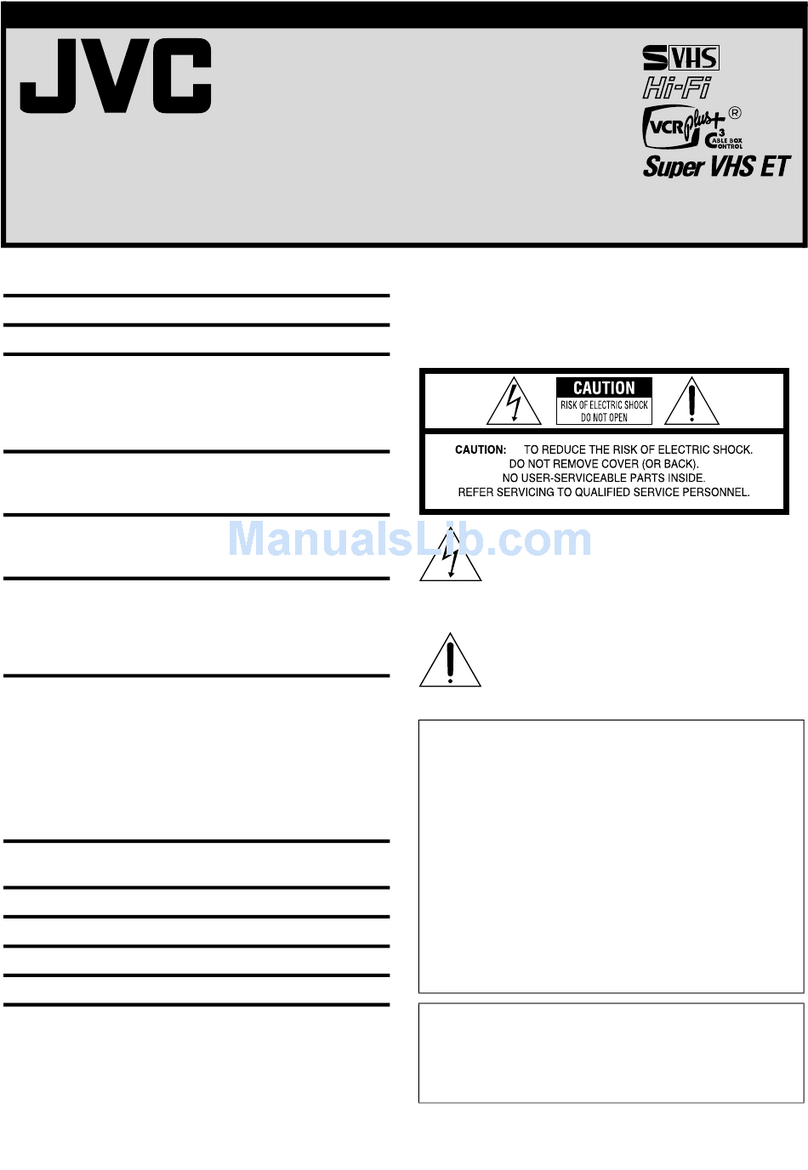
JVC
JVC HR-S3902/3912U User manual
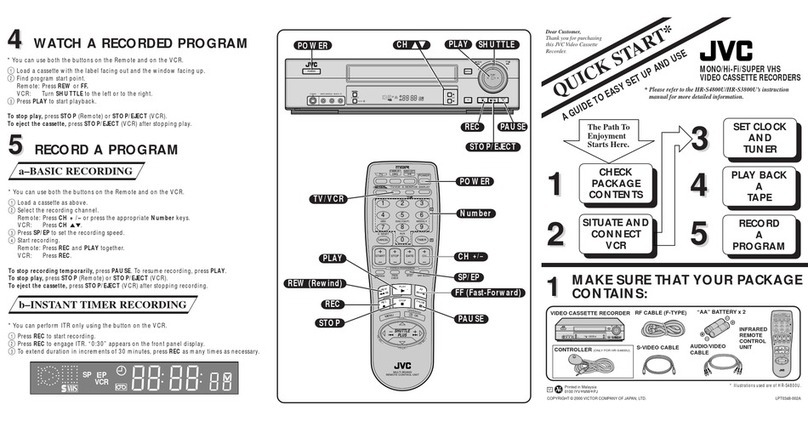
JVC
JVC HR-S3800U User manual
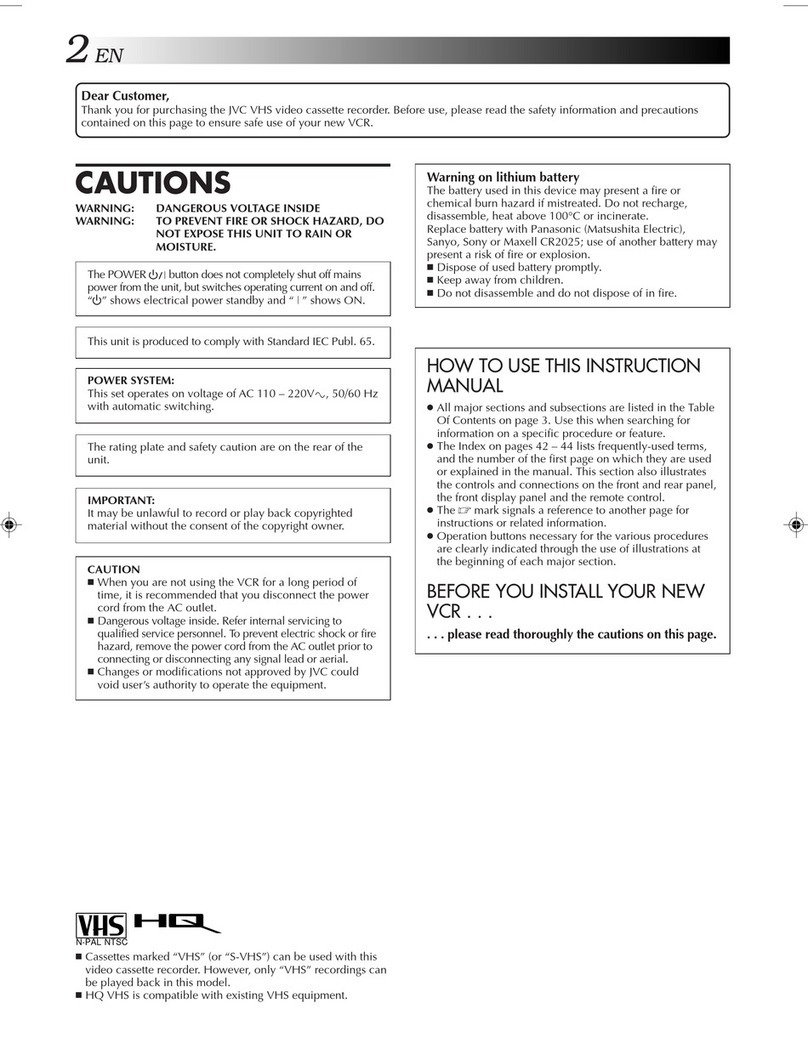
JVC
JVC HR-J456EN User manual
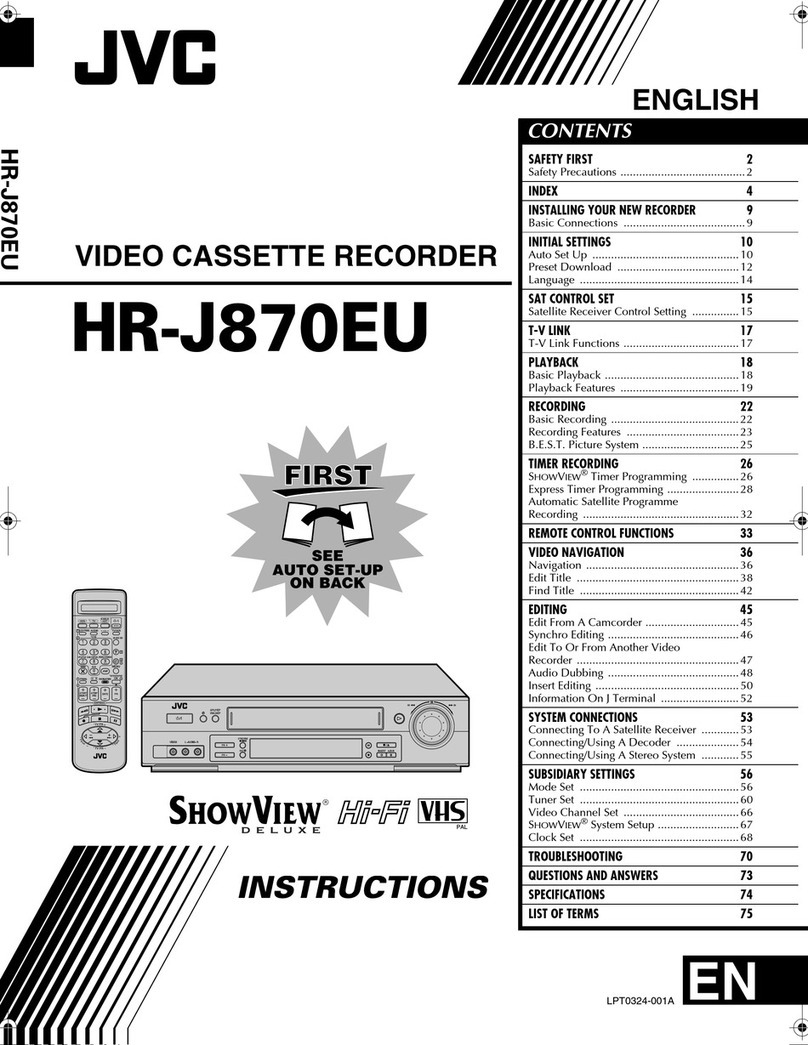
JVC
JVC HR-J870EU User manual
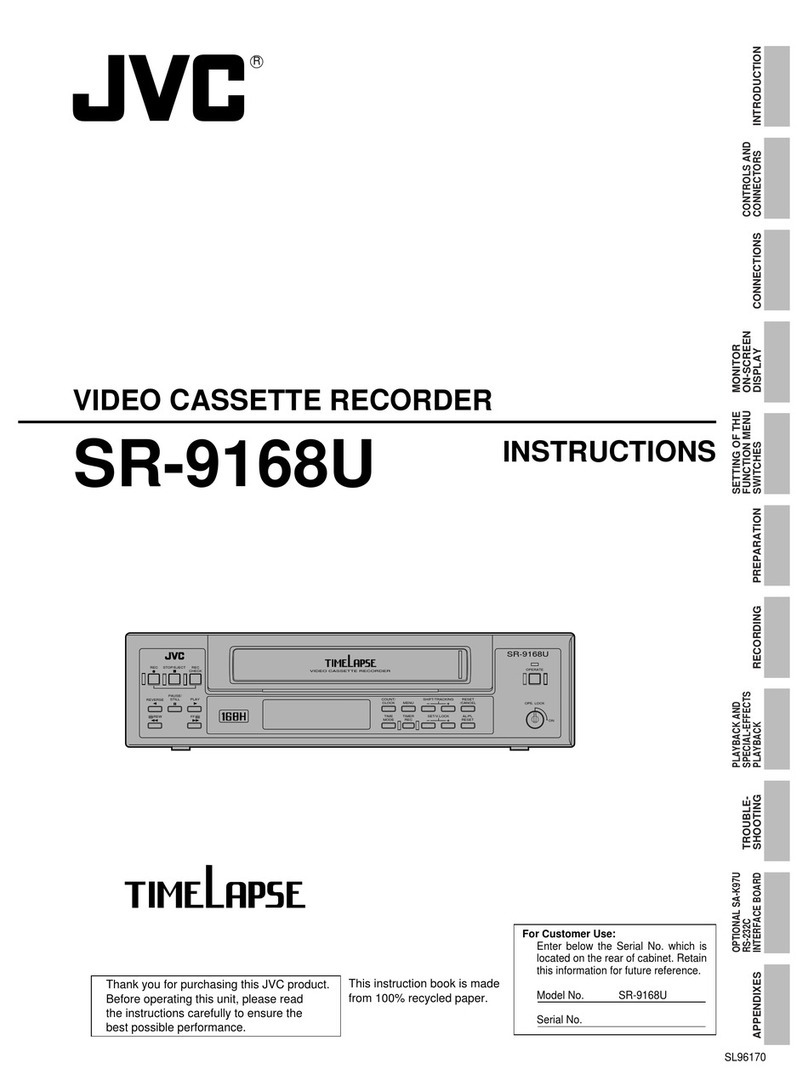
JVC
JVC SR-9168U - 168 Hour Realtime/high Density... User manual
Popular VCR System manuals by other brands
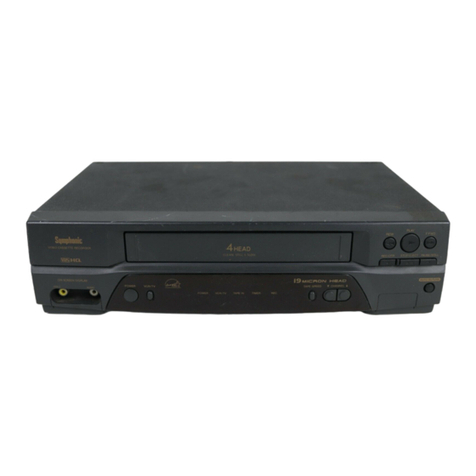
Symphonic
Symphonic SL2940 owner's manual
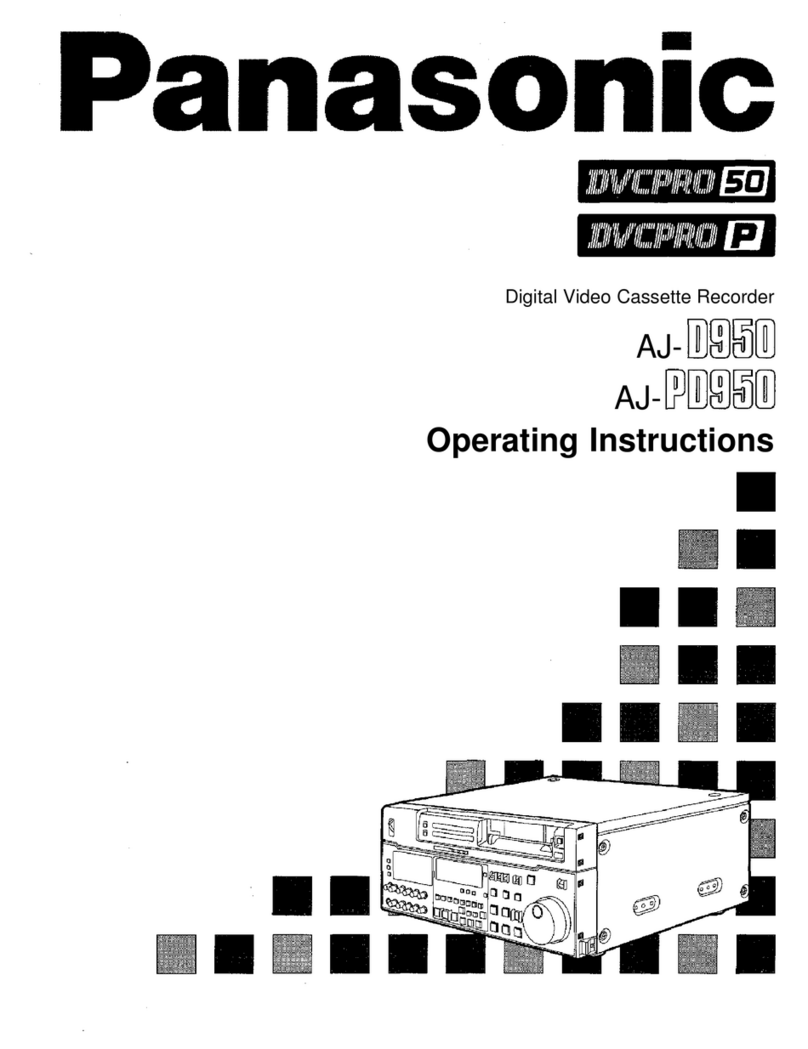
Panasonic
Panasonic AJ-D950 operating instructions
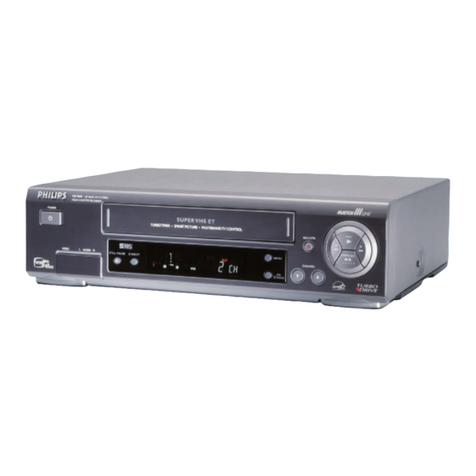
Philips
Philips MatchLine VR960BPH owner's manual

Sony
Sony Super Beta Hi-Fi SL-HF870D operating instructions
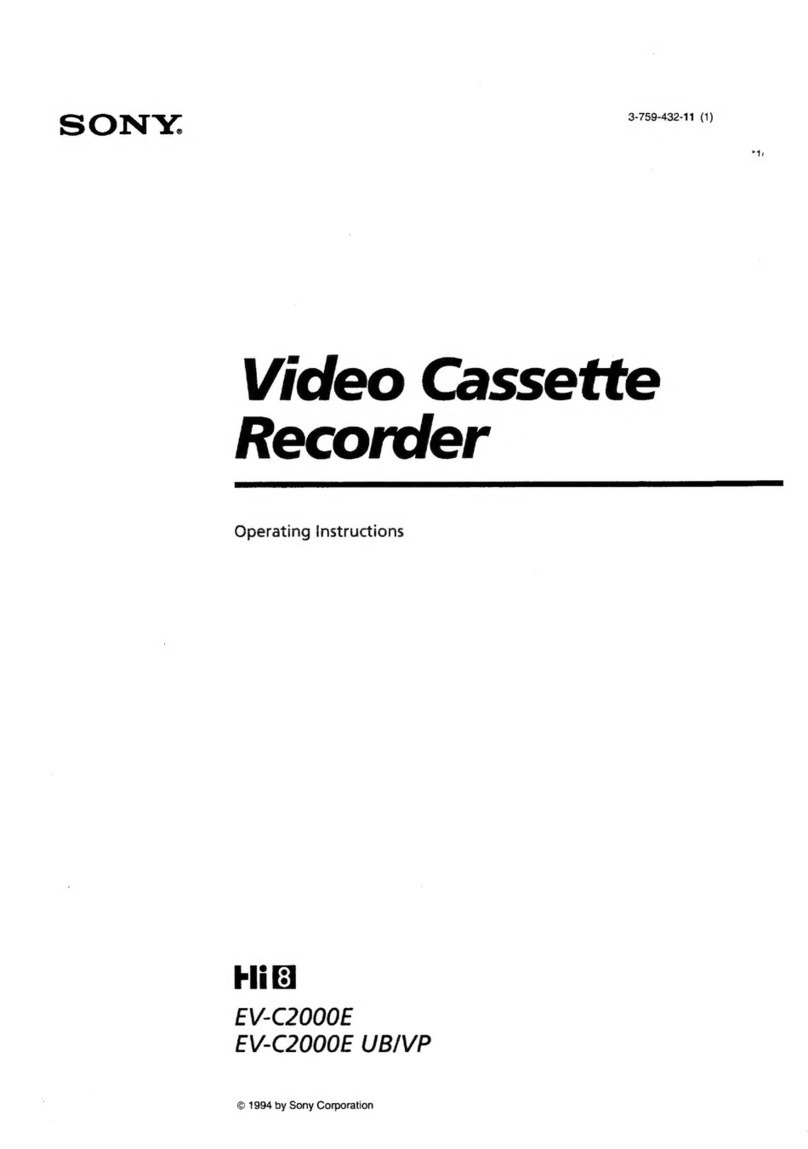
Sony
Sony Hi 8 EV-C2000E Hi 8 EV-C2000E UB operating instructions
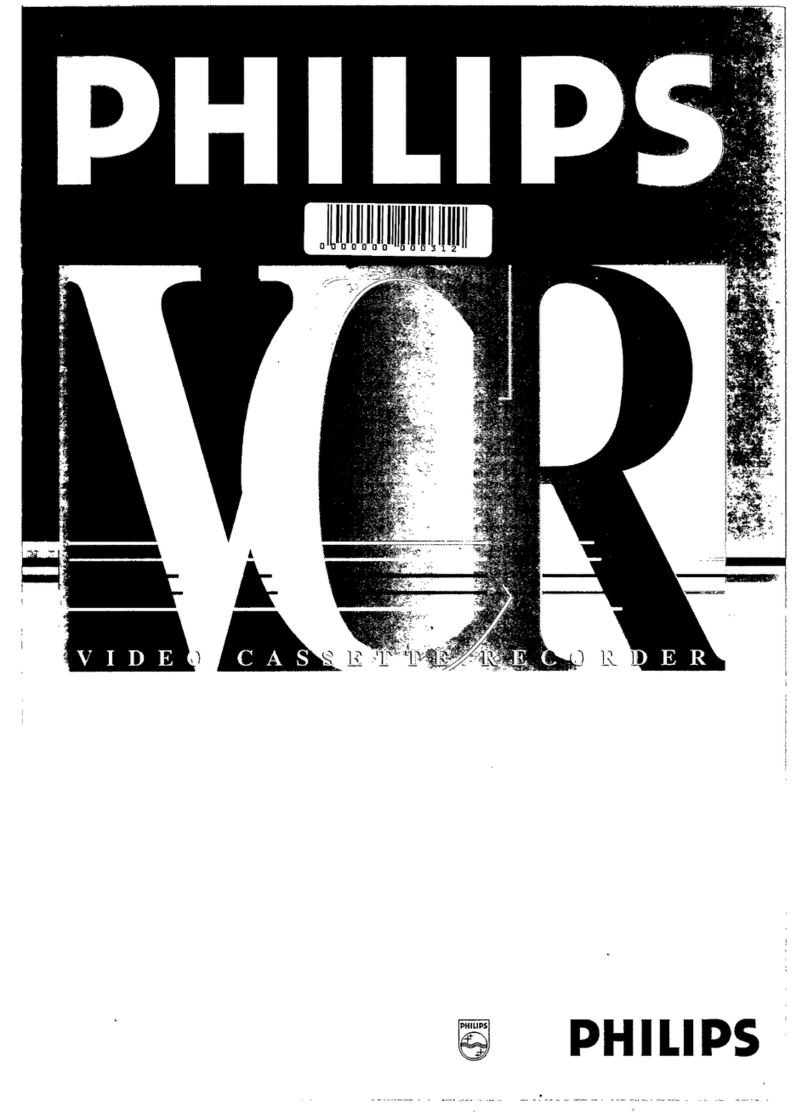
Philips
Philips VR 666/02 operating manual