KAR-TECH CAN RANGER User manual

CAN RANGER
RADIO/CAN REMOTE CONTROL SYSTEM
OPERATION MANUAL

CAN RANGER OPERATION
1
3B1901EJ | REV. DATE: July 23, 2019
TABLE OF CONTENTS
DESCRIPTION ................................................................................... 2
SYSTEM OPERATION ......................................................................... 3
TRANSMITTER AND RECEIVER SYNCHRONIZATION .......................... 5
OUTPUTS .......................................................................................... 8
BATTERY CHARGING ......................................................................... 9
INSTALLATION ............................................................................... 10
BEFORE APPLYING POWER ............................................................ 10
CAN ACTUATOR ID ASSIGNMENT .................................................... 11
ACTUATOR CALIBRATION ............................................................... 13
ACTUATOR CALIBRATION USING THE MANUAL HANDLES ............... 13
ACTUATOR CALIBRATION USING THE TRANSMITTER ..................... 18
RPM CALIBRATION ......................................................................... 19
OPTION SETUP ............................................................................... 23
FACTORY SETTING .......................................................................... 30
EXIT CALIBRATION ........................................................................ 30
USING THE OPTIONAL PALM™ INTERFACE ..................................... 31
DIAGNOSTIC ................................................................................ 31
HISTOGRAM ................................................................................. 34
FILE TRANSFER ............................................................................ 35
CALIBRATION .............................................................................. 35
RECEIVER PINOUT .......................................................................... 38
WIRING BLOCK DIAGRAM .............................................................. 39
WIRING SCHEMATIC ....................................................................... 40
ROUTINE MAINTENANCE ................................................................ 41
MAINTENANCE PRECAUTIONS ........................................................ 41
TROUBLESHOOTING ....................................................................... 42
TROUBLESHOOTING CHART ............................................................ 43
PARTS LIST..................................................................................... 45
TRANSMITTER PICTORIAL .............................................................. 46
RECEIVER PICTORIAL ..................................................................... 47
ACTUATOR PICTORIAL .................................................................... 48
SPECIFICATIONS ............................................................................ 49
INSTRUCTION TO THE USER ........................................................... 50
Appendix A ..................................................................................... 51
Appendix B ..................................................................................... 52

CAN RANGER OPERATION
2
DESCRIPTION
The CAN RANGER is a state of
the art microprocessor based
Radio Fre uency (RF) control
system. It will provide the
operator the ability to
remotely operate e uipment.
The operator is re uired to
follow all OSHA www.osha.gov
safety standards when
operating the e uipment.
This system is designed with
Fre uency Hopping Spread
Spectrum (FHSS) and Phase
Lock Loop (PLL) technology
for the optimum performance
in radio remote products.
The remote control system
consists of several modules:
the radio transmitter, receiver
module, actuators, wiring
harnesses, charger and
associated optional e uipment
such as Palm™ interface tools.
The transmitter is e uipped
with joysticks and toggle
switches for various functions.
It includes a port for charging
the internal battery.
The system’s radio receiver is
designed with 8 ON/OFF
outputs to drive the Horn,
Engine Start, Engine Stop,
RPM+, RPM-, Basket Tilt up,
Basket Tilt Down, Auxiliary
and an Analog RPM. There
are inputs for various options
like ATB/ Swing CW STOP and
OVL/Swing CCW STOP. All
outputs are protected for over
load and short circuit.
The receiver also includes a
CAN bus for communicating
with the CAN Actuators.

CAN RANGER OPERATION
3
The receiver has an RS-232
communication port to
interface with an optional
Palm Pilot diagnostic tool.
The CAN RANGER system
drives and controls the
position of the actuators with
respect to the position of the
transmitter joysticks. The
actuators in turn control the
appropriate valves.
The receiver will automatically
detect the system voltage and
adjust for either 12V or 24V
vehicles.
SYSTEM OPERATION
In the wiring harness, there
are two switches for REMOTE
POWER. They provide power
to the CAN Ranger Receiver if
both are ON. Turning either
switches OFF will power down
the CAN Ranger, and the CAN
Actuators.
To turn on the transmitter,
turn the key switch to the ON
position. To turn it off, turn
the key switch to the OFF
position.
The E-STOP button on the
transmitter must be up to
start engine and operate any
functions. To operate the
boom and winch, press
ENABLE and HORN for at least
1 second. After 1 second, you
can release HORN and use
ENABLE when you want to
operate a function. If the
ENABLE is not used for longer
than 1 minute, you must start
again with both ENABLE and
HORN as before.

CAN RANGER OPERATION
4
If the transmitter is on, and
one or more of the valve
handles/actuators is moved
off center beyond the Engine
Stop position, by means other
than the transmitter (for
example if a spring return
fails or someone moves a
handle) the CAN Ranger will
stop the engine. This is a
safety feature to protect the
person using the transmitter
from someone else operating
the machine without their
knowledge. The Engine STOP
position is configurable for
each valve handle, and for
each direction. They can be
configured via the PALM or by
following the ACTUATOR
CALIBRATION procedure
listed below. NOTE: The
Engine Stop values must be
between 90% and 10% of the
FAST value.
When turning off the
transmitter the STOP ENGINE
output will activate for about
5s and then turn off to
energize the Engine stop relay
on the harness. This action
will open the NC contact on
the relay to stop the engine.
The normal configuration for
the actuators is to have the
actuators release the manual
handles when a function is not
active, or when in E-Stop
mode. For valves with weak
springs, the corresponding
actuator can be configured to
automatically return back to
center.
In order to operate the crane
manually with at least one
actuator in Auto Center mode
enabled, turn off the Receiver.
Otherwise the actuator will

CAN RANGER OPERATION
5
continue to center the
valve/handle.
TRANSMITTER AND
RECEIVER
SYNCHRONIZATION
Each radio transmitter is
preprogrammed with a uni ue
radio ID code. Each receiver is
programmed to respond only
to the radio transmitter with
the ID code for which it is set.
This feature allows multiple
systems to work in close
proximity to one another
without interference. In the
event that a transmitter
becomes damaged and a new
one is needed, the receiver
can be reprogrammed to
respond to the new radio
transmitter. To teach the ID
code to the receiver, use the
following procedure:
1. Receiver and
transmitter power
should be off
2. Press E-STOP switch,
position BOOM toggle
switch to NORMAL,
WINCH switch to FAST,
and BASKET LEVELING
to AUTO
3. Press and hold HORN
button (on side) and all
joysticks down (pull
joysticks)
4. Turn transmitter
POWER on.
5. Release joysticks, Twist
to release the E-Stop
switch. At this point
LEDs on transmitter
should toggle.
6. Apply power to receiver

CAN RANGER OPERATION
6
7.
LEDs on transmitter will
stop toggling and the
green LED will blink
rapidly to indicate that
the teach is complete
INDICATORS
The transmitter has four
indicators. The red
BATTERY/DIAGNOSTIC
indicator, the green
TRANSMIT indicator on top,
and the red and green battery
charger indicators on the side
next to the connector. The
green TRANSMIT indicator
flashes rapidly whenever
there is communication
between the transmitter and
the receiver. The red
BATTERY indicator starts
blinking once every second
when the battery voltage is
low and re uires charging.
If the ATB Input is enabled
in calibration and the ATB
input is driven high (12/24V),
the red and green LEDs on
the transmitter will Flash
Alternately while using a
joystick.
If the OVERLOAD Input is
enabled in calibration and the
input is driven high (12/24V),
the red and green LEDs on
the transmitter will flash
together while using a
joystick.
If the Automatic Tilt feature
has been enabled, the
optional basket angle sensor
needs to be attached to the
transmitter’s charging/CAN
connector. Then the Tilt
Switch should be placed in the
AUTO position to operate.
Switching to Manual mode
disables the feature. To tare

CAN RANGER OPERATION
7
(or zero) the angle sensor,
position the bucket to what
you want level to be. NOTE:
This must be within 5 degrees
of what the sensor thinks is 0.
Then with the transmitter and
receiver on, push E-STOP
down, AUTO TILT, AUX off,
Crane Speed Slow. Then hold
Tilt Up and press the HORN.
The receiver module can
identify problems with the
system in the form of an error
code. Check the red indicator
or display window under the
HISTOGRAM screens to see
the errors. The green LED
indicator will blink on the
receiver during normal
operation.
The display on the receiver
can provide the user with
diagnostic information, and
can be used to set up the
system. The 5 push buttons
on the controller are used to
navigate through the screens.
The five main menus are
DIAGNOSTIC, CALIBRATION,
HISTOGRAM, LCD CONTRAST
and LOCAL OPERATION.
The DIAGNOSTIC menu lets
you see the status of the
inputs and the outputs.
The CALIBRATION Menu lets
you set up the actuators, the
engine RPM, and the other
options.
The HISTOGRAM Menu lets
you check the errors. You can
check on just the active
errors, all the errors, or clear
the error counts.

CAN RANGER OPERATION
8
The LCD CONTRAST Menu
lets you adjust the LCD
Contrast.
The LOCAL OPERATION
Menu lets you use the
Receiver’s buttons to
manually control the
actuators. This option is used
for e uipment without manual
override valve handles.
Use the Left and Right arrows
to select the actuator you
want to control. Hold the SET
button to activate the selected
actuator. Use the Up and
Down arrows to extend and
retract the actuator.
OUTPUTS
Each of the outputs from the
receiver module is designed
with built-in short circuit and
overload protection. The
outputs can also detect a no-
load or broken wire condition.
These error conditions are
evident by the red LED
indicator or the alphanumeric
display on the receiver
module or the HISTOGRAM
page on the optional Palm
Pilot™.
The RPM outputs can be used
as either ON/OFF (RPM +/-),
or variable RPM for connection
to ECM. Analog RPMs provided
are: PWM, inverted PWM or
DC voltage output. There are
preset parameters for
different type of engines (i.e.
Cummins engine) under RPM
calibration.
The ON/OFF outputs will
indicate an error under no
load or broken wire status if

CAN RANGER OPERATION
9
NOT activated, and will detect
a short IF activated. The
proportional outputs will
detect a no-load or short
condition WHEN activated.
BATTERY CHARGING
The transmitter is designed
with a smart battery charger.
The battery can be charged
by connecting the transmitter
to an AC wall charger or a car
charger. The red and green
LED indicators near the
charging port indicate the
status of the charger: The red
LED indicates that the battery
is charging and green LED
indicates that the battery is
fully charged. A complete
charge can be achieved in
about 1 hour.
To save battery life, the
transmitter will turn off when
none of the switches or
joysticks (if e uipped) is used
for period of 10 minutes. The
user must recycle power to
restore transmitter operation.
However, the transmitter will
stay on as long as the
receiver has power applied to
it.
When the battery is new, the
run-time of the transmitter
will be shorter until it has
gone through the
drain/charge cycle several
times. After this point, the
unit’s current drain should
allow at least 20 hours of run-
time before a recharge is
needed.

CAN RANGER OPERATION
10
INSTALLATION
Refer to the KAR-TECH
INSTALLATION manual for
guidance on all aspects of
installation specific to your
truck. Additionally, refer to
the PINOUT sections in this
manual for hookup of the
harness.
All connections must be
properly insulated and sealed
to protect against shorts and
corrosion.
BEFORE APPLYING
POWER
•Check power and ground
for proper polarity.
•Check the wiring harness
for possible shorts before
connecting to output
devices (i.e. valves and
relays) by checking each
mating pin terminal.
•Verify that the transmitter
battery is fully charged. If
it is low, performance may
be erratic.
•Read the rest of this
manual.

CAN RANGER OPERATION
11
CAN ACTUATOR ID
ASSIGNMENT
Kar-Tech CAN Actuators are
pre-assigned at the factory
and labeled for each function.
The following procedure is
only if reassignment is
re uired in case of actuator
replacement or if two identical
actuators are detected.
Note: If the receiver ever
detects two or more
actuators with the same
ID, it will stop operation
and indicate errors. The
receiver tests for this
every time it is powered up
and continually as it runs.
Since all actuators are
identical, they need to be
assigned identification
numbers by the receiver in
order to distinguish which
actuator does what function.
Using the buttons on the CAN
Ranger Receiver, navigate
through the LCD screens to
CALIBRATION. Press <SET>.
Use the arrow buttons to
enter the password 1262.
Enter the password by
pressing <SET>. The first
screen in the Menu is
ASSIGN ACTUATORS
PUSH SET
After selecting this by pushing
SET, the receiver’s LCD will
walk the operator through the
procedure. The basic idea is
that all actuators need to be
disconnected from the
system. This means both
disconnecting the wire
cable and disconnecting
the mechanical linkage
from the shaft of the
actuators. Next, one by one

CAN RANGER OPERATION
12
the actuators are connected
to the system. Each time the
operator tells the receiver
which actuator was added,
the receiver will assign that
actuator the appropriate
function.
Things to keep in mind while
concerning Actuator IDs:
•The receiver will not let
you add more than one
at a time.
•
The receiver cannot
know if you are assigning
the wrong ID to an
actuator. That is, if you
attach the BOOM
actuator and tell the
receiver it is the WINCH,
the receiver will treat
that actuator as the
WINCH and the crane
will not operate
correctly.
•
If you skip an actuator
during the assignment
process, the Receiver will
not know, and will not
assign that actuator.
•
After assigning IDs, you
need to re-calibrate the
actuators, or at least any
new or swapped
actuators.
•
Leave the actuators
plugged in after you add
each one. No need to
remove them after each
step. If you do remove an
actuator that has been
assigned and you still need
to assign other actuators.
Do not plug the taught
actuator back in until you
have completed the ID
Assign procedure and
exited.
•
If you leave the actuators
mechanically linked to the
valves during the ID step,

CAN RANGER OPERATION
13
the actuator’s ZERO
position may not be
correct. If you get
strange/incorrect position
readings, this may be the
reason.
ACTUATOR CALIBRATION
The receiver is programmed
for default values for each
actuator at the factory.
Please refer to Appendix B for
factory setting values.
PLEASE NOTE: IF THE
FOLLOWING PROCEDURE IS
NOT PERFORMED PRIOR TO
OPERATION, THE ENGINE STOP
MAY BE ON CONTINUOUSLY!
ACTUATOR CALIBRATION
USING THE MANUAL
HANDLES
Using the buttons on the CAN
Ranger Receiver, navigate
through the LCD screens to
CALIBRATION. Press <SET>.
Use the arrow buttons to
enter the password 1262.
Enter the password by
pressing <SET>. Then press
the right button (FWD arrow)
to get to:
ACTUATOR SETUP
PUSH SET
Next presses the right button
(FWD arrow) to get to the
actuator you want to
calibrate.
During the calibration you will
be asked to calibrate center,
fast, slow, and engine stop
positions. These positions are
defined as follow:
CENTER POSITION
This is the position the
actuator moves to when the
transmitter is ON and the
joystick is in neutral (center
position). This position is
normally the valve handle in

CAN RANGER OPERATION
14
its neutral position (Valve
center).
FAST POSITION
This is the position the
actuator moves to when the
transmitter’s BOOM SPEED
switch is switched to NORMAL
and a joystick is pushed all
the way in one direction. This
position is normally the
maximum travel of the valve
handle.
SLOW POSITION
This is the position the
actuator will move to when
the transmitter’s BOOM
SPEED switch is switched to
SLOW and a joystick is
pushed all the way in one
direction. This position is
normally slightly below the
maximum travel of the valve
handle.
ENGINE STOP POSITION
This is the position of the
valve handle right before
hydraulics flow or function
movement. The receiver
commands the engine to stop
if the transmitter is ON with
joystick in the center and
valve is moved manually or
the actuator did not return to
center due to mechanical
failure or binding of the valve
components or actuator.
Move valve handle until there
is a slight motion of the boom
or winch function to store
value.
At the end of the calibration
of each actuator, the Auto
Center feature can be Enabled
or Disabled for that actuator.
This feature is generally

CAN RANGER OPERATION
15
enabled if the valve spring is
weak.
SWING CALIBRATION
If this is the first time
calibrating the actuators, start
with SWING SETUP and the
controller will walk you
through all Enabled actuators
in turn (normally 4). Once you
have selected the actuator
you want to calibrate push
<SET> and follow the
instructions on the LCD.
There are several settings for
each actuator. Each has its
own screen. Use the ←→
arrow buttons to scroll
through the settings if you
want to change or look at a
specific setting. If you are
setting up a new actuator,
make sure to configure each
setting to match your crane.
In each setting screen both
the stored value and the
current actuator position are
shown on the second row of
the display.
← (x.xx) x.xx →
The number in parentheses is
the stored value. The other is
the current actuator position.
Push Set to store the current
position into this parameter.
The receiver will automatically
move to the next setting.
For example, if you selected
SWING, the first screen will
be for the center position.
Before pressing <SET>, move
the SWING Handle back and
forth. The displayed position,
shown in inch, should change.
If not, the wrong actuator is
connected to this connection,

CAN RANGER OPERATION
16
or the actuator is not
functioning correctly. Try the
other handles to see if the
one of the other handles
control the displayed position.
If so, swap the actuator
locations or re-ID the
actuators. If no handle
controls the position, make
sure the actuators are linked
to the valves.
If the SWING handle can
change the position on the
display, center the handle. It
should be about 1.5 inch.
Note that the actuator total
travel is 3 inch; therefore 1.5
is the center position. If it is
not close, adjust the linkage
to the valve handles and push
<SET>.
The next screen will be to set
the Fast Counter Clockwise
Swing. Push the SWING
Handle all the way in the
direction for Counter
Clockwise Swing. Hold it there
and push <SET>.
Next the Slow Counter
Clockwise Swing needs to be
set. Hold the SWING Handle
in the position for slow
Counter Clockwise Swing, and
press <SET>.
The next screen will be to set
the Engine Stop Position for
Counter Clockwise Swing.
Hold the SWING Handle in the
position that you want the
Engine to be stopped and
push <SET>.
The next screen will be to set
the Fast Clockwise Swing.
Push the SWING Handle all
the way in the direction for
Clockwise Swing. Hold it there
and push <SET>.

CAN RANGER OPERATION
17
Next the Slow Clockwise
Swing needs to be set. Hold
the SWING Handle in the
position for slow Clockwise
Swing, and push <SET>.
The next screen will be to set
the Engine Stop Position as
described above for Clockwise
Swing. Hold the SWING
Handle in this position, and
push <SET>.
The next screen lets you
Enable or Disable the Auto
Center feature for the Swing
Actuator. Push <SET> to
toggle between ENABLE and
DISABLE. Push → Next menu.
The final step in calibrating
the SWING function is to save
the settings or if you don’t
want to save them, just
escape.
PUSH SET TO SAVE
USE ↑ TO QUIT
Pushing <SET> will save the
settings. Pushing ↑ will exit
the Swing Calibration and will
revert to the previous
settings.
If you push <SET> the
controller will automatic move
to Telescope setup. If you
want to calibrate the
Telescope function next, push
<SET>.
Repeat this procedure for the
Telescope, Winch and Boom
actuators. If enabled, also
repeat this for Boom 2 and
Telescope 2. If this is the
only actuator that re uires
calibration or to exit
calibration keep pressing the
right button (FWD arrow).
The Actuator calibration is
now complete. Make sure

CAN RANGER OPERATION
18
crane works properly with
remote before delivery.
ACTUATOR CALIBRATION
USING THE TRANSMITTER
This procedure is similar to
the calibration using valve
handles, instead you will be
using the joysticks to move
the actuator to the desired
position and pressing Horn
button on the transmitter or
SET button on the receiver
will store the new position in
the receiver. Actuator
calibration using transmitter is
normally used if valve handles
are not present or not
accessible. Be sure the E-
STOP is up before proceeding.

CAN RANGER OPERATION
19
RPM CALIBRATION
PLEASE NOTE: THE KAR-
TECH CAN RANGER CAN BE
CONFIGURED TO PROVIDE
MANY DIFFERENT TYPES
OF RPM SIGNALS. MAKE
SURE THE SYSTEM IS
CONFIGURED FOR THE
CORRECT TYPE OF OUTPUT
FOR YOUR ENGINE.
The CAN Ranger is calibrated
at the factory for Cummins
engine. Refer to appendix B
for factory setting
parameters.
Using the buttons on the CAN
Ranger Receiver, navigate
through the LCD screens to
CALIBRATION. Push <SET>.
Use the arrow buttons to
enter the password 1262.
To enter the password, use
the → button to change which
digit you are changing. Use ↑
to increase the selected digit
or ↓ to decrease it. Use ← to
back out of this screen and
return to the Calibration
Menu. Once you have
changed all 4 digits, push
<SET>. If you entered the
correct password you get the
help screen:
USE ←→ TO PICK
Then push the right button
(FWD arrow) to get to the
RPM SETUP screen:
RPM SETUP
← PUSH SET →
Push <SET>.
Scroll until you get the type of
RPM you want. The options
are:
Caterpillar
Cummins
International
Mercedes
Table of contents
Other KAR-TECH Control System manuals
Popular Control System manuals by other brands
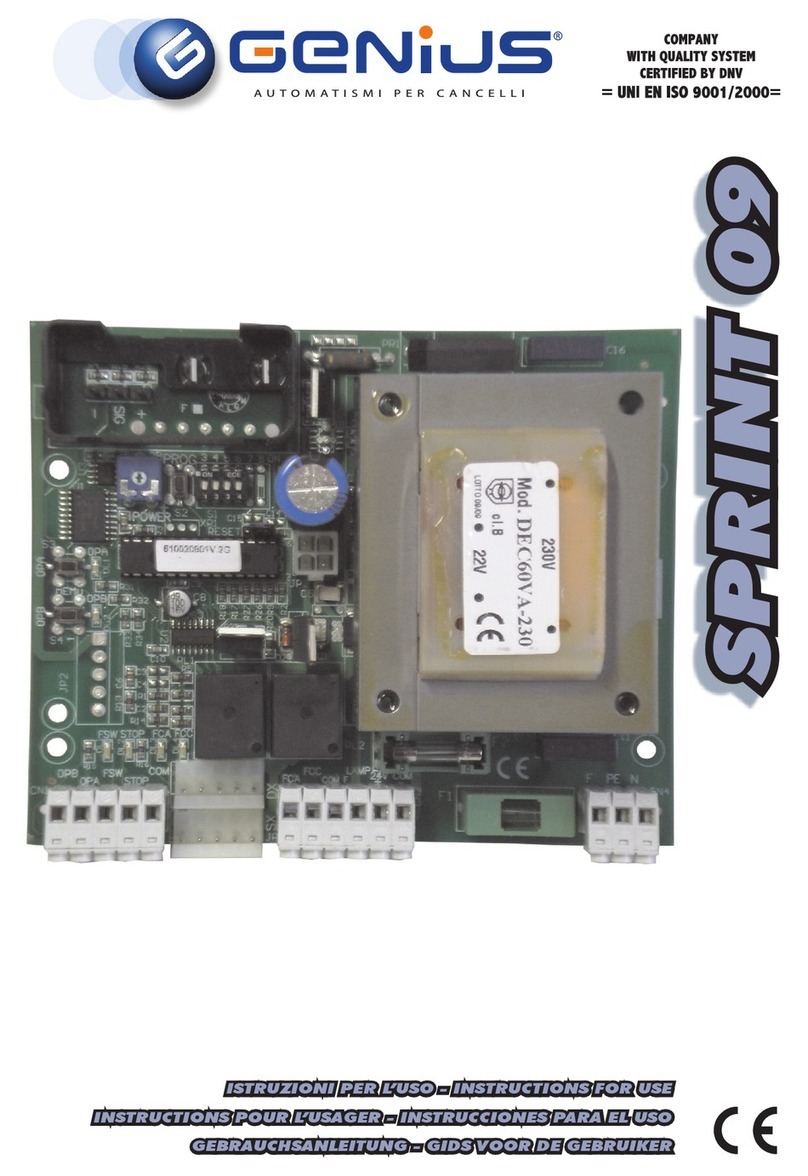
Genius
Genius SPRINT 09 Instructions for use
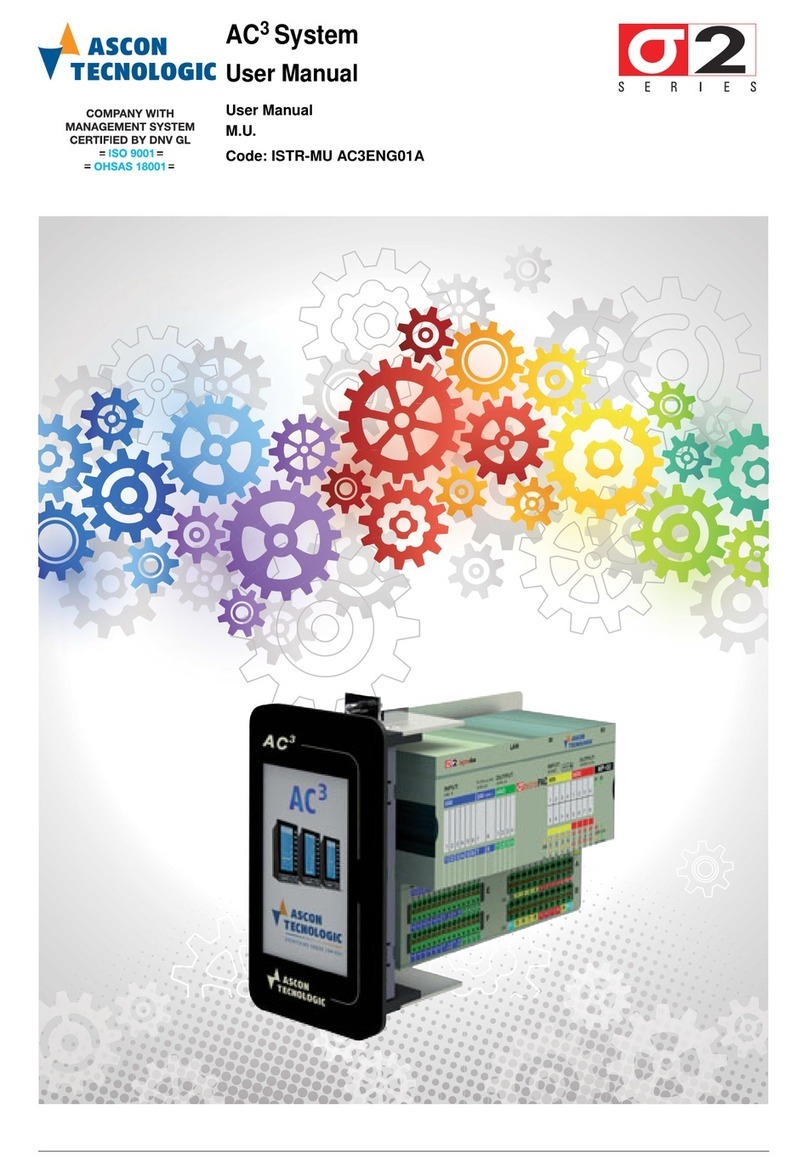
Ascon tecnologic
Ascon tecnologic AC3 user manual
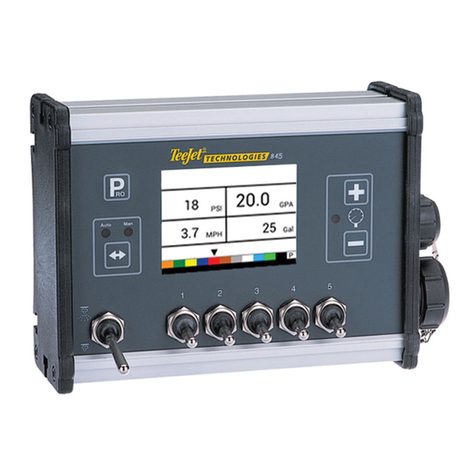
Spraying Systems
Spraying Systems TeeJet 845 user manual
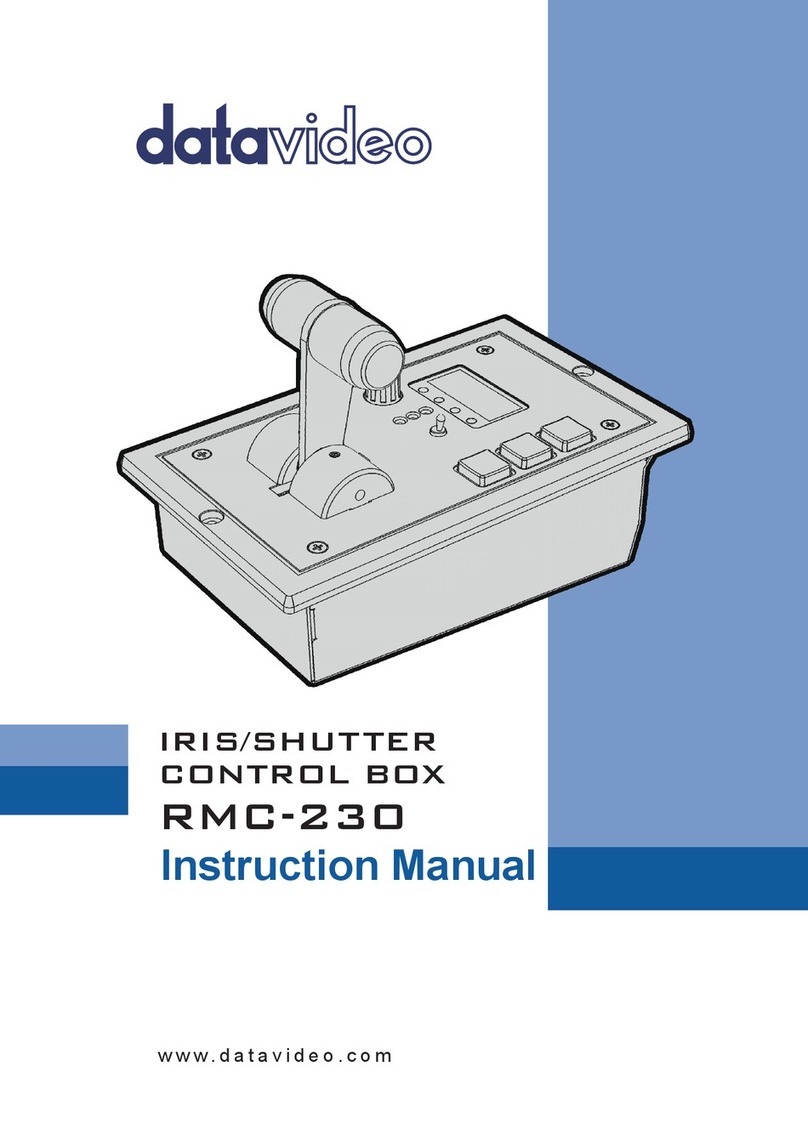
Data Video
Data Video RMC-230 instruction manual

PULSEEIGHT
PULSEEIGHT neo:4Pro quick start guide
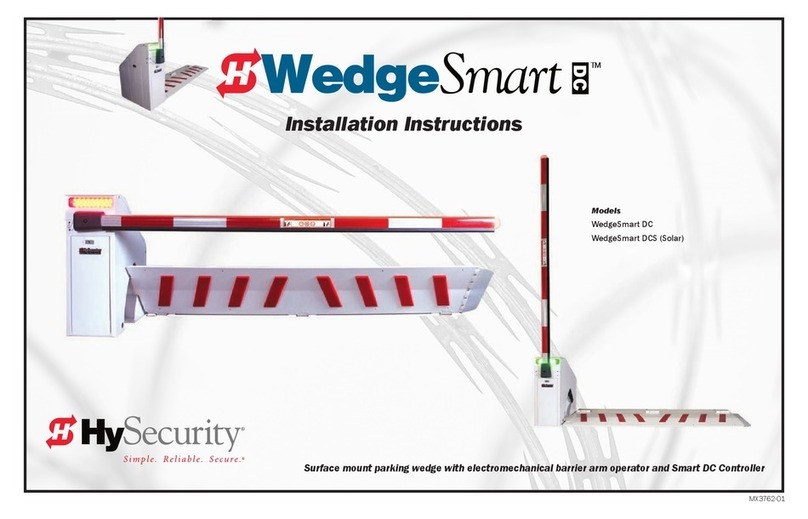
HySecurity
HySecurity WedgeSmart DCS installation instructions