KB Genesis KBAC Series User manual

©2016 KB Electronics, Inc.
(see back cover)
Installation & Operation Manual
KBAC SERIES
Adjustable Frequency Drives for 3-Phase AC Motors
NEMA 4X / IP65
Variable Speed/Soft-Start AC Motor Drive
with Electronic Motor Overload Protection1
Washdown and Watertight for Indoor and Outdoor Use
Rated for 208 – 230, and 400/460 Volt 50 & 60 Hz
3-Phase & PSC2AC Induction Motors from Subfractional thru 10 HP
Operates from 115, 208/230 and 400/460 Volt 50/60 Hz AC Line3
This Manual Covers Models
KBAC-24D, 27D, 29, 29 (1P), 45, 48, 217, 217S, 217F, 217SF, 416, 416S, 416F, 416SF
Notes: 1. UL approved as an electronic overload protector for motors. 2. Special software
is available – contact our Sales Department. 3. GFCI Operation: Models KBAC-24D, 27D, 29,
29 (1P), 45, 48 require custom software – contact our Sales Department. The KBAC-217, 416
Series are jumper selectable (J12) for standard (G1) and sensitive (G2) GFCIs. 4. Installation
of a CE approved RFI lter is required.
The information contained in this manual is intended to be accurate. However, the manufacturer retains
the right to make changes in design which may not be included herein.
NOTE: THE DRIVE IS FACTORY SET FOR
60 Hz MOTORS. FOR 50 Hz MOTORS, SEE
SECTION 6.4 ON PAGE 24.
See Safety Warning
on Page 6.
4
AC MOTOR SPEED CONTROL
KBAC SERIES • NEMA 4X / IP 65
Hybrid Drive
™
AC MOTOR SPEED CONTROL
KBAC SERIES • NEMA 4X / IP 65
Hybrid Drive
™
KBAC SERIES • NEMA 4X / IP65
AC MOTOR SPEED CONTROL
Hybrid Drive™

ii
Table of Contents
Section Page
1 Quick-Start Instructions . . . . . . . . . . . . . . . . . . . . . . . . . . . . . . . . . . . . . . . . . . . . . . . . . . . . . 4
2 Safety Warning . . . . . . . . . . . . . . . . . . . . . . . . . . . . . . . . . . . . . . . . . . . . . . . . . . . . . . . . . . .6
3 Introduction . . . . . . . . . . . . . . . . . . . . . . . . . . . . . . . . . . . . . . . . . . . . . . . . . . . . . . . . . . . . 6
4 Important Application Information . . . . . . . . . . . . . . . . . . . . . . . . . . . . . . . . . . . . . . . . . . . . . 18
5 Wiring Instructions . . . . . . . . . . . . . . . . . . . . . . . . . . . . . . . . . . . . . . . . . . . . . . . . . . . . . . . 18
6 Setting Selectable Jumpers . . . . . . . . . . . . . . . . . . . . . . . . . . . . . . . . . . . . . . . . . . . . . . . . . . 23
7 Mounting Instructions . . . . . . . . . . . . . . . . . . . . . . . . . . . . . . . . . . . . . . . . . . . . . . . . . . . . . 26
8 Recommended High Voltage Dielectric Withstand Testing (Hi-Pot Testing). . . . . . . . . . . . . . . . . . . . 26
9 Reconditioning the Bus Capacitors . . . . . . . . . . . . . . . . . . . . . . . . . . . . . . . . . . . . . . . . . . . . . 26
10 Drive Operation . . . . . . . . . . . . . . . . . . . . . . . . . . . . . . . . . . . . . . . . . . . . . . . . . . . . . . . . . 28
11 AC Line Fusing . . . . . . . . . . . . . . . . . . . . . . . . . . . . . . . . . . . . . . . . . . . . . . . . . . . . . . . . . . 28
12 Diagnostic LEDs . . . . . . . . . . . . . . . . . . . . . . . . . . . . . . . . . . . . . . . . . . . . . . . . . . . . . . . . . 28
13 Trimpot Adjustments . . . . . . . . . . . . . . . . . . . . . . . . . . . . . . . . . . . . . . . . . . . . . . . . . . . . . . 29
Appendix A – Optional SIAC-PS Signal Isolator with Power Supply . . . . . . . . . . . . . . . . . . . . . . . . . . . 33
Limited Warranty. . . . . . . . . . . . . . . . . . . . . . . . . . . . . . . . . . . . . . . . . . . . . . . . . . . . . . . . . . . 36
Tables Page
1 Jumper Selectable Features. . . . . . . . . . . . . . . . . . . . . . . . . . . . . . . . . . . . . . . . . . . . . . . . . . .8
2 Optional Accessories . . . . . . . . . . . . . . . . . . . . . . . . . . . . . . . . . . . . . . . . . . . . . . . . . . . . . . . 9
3 General Performance Specications . . . . . . . . . . . . . . . . . . . . . . . . . . . . . . . . . . . . . . . . . . . . 13
4 Electrical Ratings. . . . . . . . . . . . . . . . . . . . . . . . . . . . . . . . . . . . . . . . . . . . . . . . . . . . . . . . . 14
5 Terminal Block Wiring Information . . . . . . . . . . . . . . . . . . . . . . . . . . . . . . . . . . . . . . . . . . . . . 19
6 Drive Operating Condition and Run/Fault Relay Contact Status . . . . . . . . . . . . . . . . . . . . . . . . . . . 23
7 Drive Operating Condition and Status LED Indicator . . . . . . . . . . . . . . . . . . . . . . . . . . . . . . . . . . 29
Figures Page
1 Quick-Start Connection Diagram . . . . . . . . . . . . . . . . . . . . . . . . . . . . . . . . . . . . . . . . . . . . . . . 4
2 KBAC-24D Control Layout . . . . . . . . . . . . . . . . . . . . . . . . . . . . . . . . . . . . . . . . . . . . . . . . . . . 10
3 KBAC-27D, 29, 29 (1P), 45, 48 Control Layout . . . . . . . . . . . . . . . . . . . . . . . . . . . . . . . . . . . . . . . 11
4 KBAC-217, 416 Series Control Layout . . . . . . . . . . . . . . . . . . . . . . . . . . . . . . . . . . . . . . . . . . . . 12
5 Model KBAC-24D Mechanical Specications . . . . . . . . . . . . . . . . . . . . . . . . . . . . . . . . . . . . . . . 15
6 Models KBAC-27D, 29, 29 (1P), 45, 48 Mechanical Specications . . . . . . . . . . . . . . . . . . . . . . . . . . 16
7 KBAC-217, 416 Series Mechanical Specications. . . . . . . . . . . . . . . . . . . . . . . . . . . . . . . . . . . . . 17
8 Maximum Allowed Motor Torque vs. Speed. . . . . . . . . . . . . . . . . . . . . . . . . . . . . . . . . . . . . . . . 18
9 Open Ventilated Motor with External Fan Cooling. . . . . . . . . . . . . . . . . . . . . . . . . . . . . . . . . . . . 18
10 Models KBAC-24D, 27D, 29 (1P), AC Line Input, Motor, and Ground Connections . . . . . . . . . . . . . . . . 20
11 Models KBAC-29, 45, 48 AC Line Input, Motor, and Ground Connections . . . . . . . . . . . . . . . . . . . . . 20
12 KBAC-217, 416 Series AC Line Input, Motor, and Ground Connections . . . . . . . . . . . . . . . . . . . . . . . 20
13 Remote Main Speed Potentiometer Connection. . . . . . . . . . . . . . . . . . . . . . . . . . . . . . . . . . . . . 21
14 Remote Start/Stop Switch Connection with Normally Open Stop Contact . . . . . . . . . . . . . . . . . . . . 21
15 Remote Start/Stop Switch Connection with Normally Closed Stop Contact . . . . . . . . . . . . . . . . . . . 21
16 Start/Stop Function Eliminated . . . . . . . . . . . . . . . . . . . . . . . . . . . . . . . . . . . . . . . . . . . . . . . 22
17 Voltage Following Connections . . . . . . . . . . . . . . . . . . . . . . . . . . . . . . . . . . . . . . . . . . . . . . . 22
18 Enable Circuit Connection. . . . . . . . . . . . . . . . . . . . . . . . . . . . . . . . . . . . . . . . . . . . . . . . . . . 22
19 Run/Fault Relay Output Contacts Connection . . . . . . . . . . . . . . . . . . . . . . . . . . . . . . . . . . . . . . 23
20 Models KBAC-24D, 27D AC Line Input Voltage Selection (Jumper J1) . . . . . . . . . . . . . . . . . . . . . . . 23
21 Removing Jumper J1 on Models KBAC-24D, 27D . . . . . . . . . . . . . . . . . . . . . . . . . . . . . . . . . . . . 23
22 Motor Horsepower Selection (Jumper J2) . . . . . . . . . . . . . . . . . . . . . . . . . . . . . . . . . . . . . . . . . 24
23 Automatic Ride-Through or Manual Restart Selection (Jumper J3) . . . . . . . . . . . . . . . . . . . . . . . . . 24

iii
24 60 Hz and 50 Hz Motor Selection (Jumpers J4 and J5) . . . . . . . . . . . . . . . . . . . . . . . . . . . . . . . . . 24
25 Available Torque vs. Output Frequency . . . . . . . . . . . . . . . . . . . . . . . . . . . . . . . . . . . . . . . . . . 24
26 120 Hz and 100 Hz Drive Output Frequency Selection . . . . . . . . . . . . . . . . . . . . . . . . . . . . . . . . . 25
27 Fixed or Adjustable Boost Selection (Jumper J6). . . . . . . . . . . . . . . . . . . . . . . . . . . . . . . . . . . . . 25
28 Regenerative or DC Injection Braking Selection (Jumper J7) . . . . . . . . . . . . . . . . . . . . . . . . . . . . . 25
29 “Run”or“Fault” Output Relay Operation Selection (Jumper J8). . . . . . . . . . . . . . . . . . . . . . . . . . . . 25
30 Normally Open or Closed Stop Contact Selection (Jumper J9) . . . . . . . . . . . . . . . . . . . . . . . . . . . . 25
31 Constant or Variable Torque Selection (Jumper J10) . . . . . . . . . . . . . . . . . . . . . . . . . . . . . . . . . . 25
32 Switching Frequency and GFCI Selection (Jumper J12) . . . . . . . . . . . . . . . . . . . . . . . . . . . . . . . . 26
33 Typical Hi-Pot Test Setup. . . . . . . . . . . . . . . . . . . . . . . . . . . . . . . . . . . . . . . . . . . . . . . . . . . . 27
34 Minimum Speed Trimpot (MIN) Range . . . . . . . . . . . . . . . . . . . . . . . . . . . . . . . . . . . . . . . . . . . 30
3 Maximum Speed Trimpot (MAX) Range . . . . . . . . . . . . . . . . . . . . . . . . . . . . . . . . . . . . . . . . . . 30
36 Acceleration Trimpot (ACCEL) Range . . . . . . . . . . . . . . . . . . . . . . . . . . . . . . . . . . . . . . . . . . . . 30
37 Deceleration Trimpot (DEC/I) Range . . . . . . . . . . . . . . . . . . . . . . . . . . . . . . . . . . . . . . . . . . . . 30
38 DC Injection Brake Trimpot (DEC/I) Range. . . . . . . . . . . . . . . . . . . . . . . . . . . . . . . . . . . . . . . . .30
39 Slip Compensation Trimpot (COMP) Range . . . . . . . . . . . . . . . . . . . . . . . . . . . . . . . . . . . . . . . . 30
40 Current Limit Trimpot (CL) Range . . . . . . . . . . . . . . . . . . . . . . . . . . . . . . . . . . . . . . . . . . . . . . 30
41 I2t Trip Time vs. Motor Current . . . . . . . . . . . . . . . . . . . . . . . . . . . . . . . . . . . . . . . . . . . . . . . . 31
42 Boost Trimpot (BOOST) Range . . . . . . . . . . . . . . . . . . . . . . . . . . . . . . . . . . . . . . . . . . . . . . . . 31
43 Jog Trimpot (JOG) Range Run-Stop-Jog Switch Connection . . . . . . . . . . . . . . . . . . . . . . . . . . . . . 32
44 Run-Stop-Jog Switch Connection . . . . . . . . . . . . . . . . . . . . . . . . . . . . . . . . . . . . . . . . . . . . . . 32
Items Included In this Package:
Adjustable Frequency Drive, Installation and Operation Manual, Trimpot Adjustment Tool, CE Approved
Product Information Card, and Warranty Registration Card.
Drive Model Nos. and Part Nos.
Model No.
Part No.
Model No.
Part No.
Gray White* Gray White*
KBAC-24D 9987 9988 KBAC-217 8868 8879
KBAC-27D 9520 9521 KBAC-217S 8863 8855
KBAC-29 9528 9529 KBAC-217F 8861 8853
KBAC-29 (1P) 10001 10002 KBAC-217SF 8869 8880
KBAC-45 9530 9531 KBAC-416 8870 8881
KBAC-48 9540 9541 KBAC-416S 8864 8856
KBAC-416F 8874 8883
KBAC-416SF 8871 8882
*White FDA approved nish.
230 VAC Controls
Suitable For Use on a Circuit Capable of Delivering Not More Than 5 kA RMS Symmetrical Amperes,
230 Volts Maximum.
Use Copper Conductors Rated 75 ºC.
Suitable for Operation in a Maximum Surrounding Air Temperature of 40 ºC.
460 VAC Controls
Suitable For Use on a Circuit Capable of Delivering Not More Than 5 kA RMS Symmetrical Amperes, 460
Volts Maximum.
Use Copper Conductors Rated 75 ºC.
Suitable for Operation in a Maximum Surrounding Air Temperature of 40 ºC.
UL Notice

4
1 QUICK-START INSTRUCTIONS
Important – You must read these simplied instructions before proceeding. These instructions
are to be used as a reference only and are not intended to replace the details provided herein.
You must read the Safety Warning on page 5 before proceeding.
Reconditioning the Bus Capacitors – If this drive has been in storage for over one year, it is
necessary to recondition the power supply bus capacitors. To recondition the bus capacitors, apply the
AC Line with the drive in the Stop Mode for a minimum of one hour. Not following this procedure will
cause the bus capacitors to fail.
See Figure 1. Also see Section 4 - Important Application Information on Page 18.
WARNING! Disconnect main power before making connections to the drive.
1.1 AC Line Input Connection – Wire the AC Line input to Terminal Block TB1. See Section 5.1
on pages 19 and 20.
Application Note: GFCI Operation: Models KBAC-24D, 27D, 29, 29 (1P), 45, 48 require custom
software – contact our Sales Department. The KBAC-217, 416 Series are jumper selectable
(J12) for Standard (G1) or Sensitive (G2) GFCIs.
Note: The rated AC Line voltage of the drive must match the actual AC Line input voltage. On Models
KBAC-24D and 27D, the setting of Jumper J1 must match the AC Line input voltage.
Models KBAC-24D, 27D, 29 (1P): Designed to accept 1-phase (Terminals L1, L2) AC Line input
only. Rated for 208/230 Volt AC Line input with Jumper J1 set to the “230V” position
(factory setting). Rated for 115 Volt AC Line input with Jumper J1 set to the“115V” position.
See Figure 10 on page 20.
Note: Model KBAC-27D is rated for 1½ HP maximum with 115 Volt AC Line input and 2 HP maximum
with 208/230 Volt AC Line input.
Model KBAC-29: Designed to accept 1-phase (Terminals L1, L2) or 3-phase (Terminals L1, L2, L3)
AC Line input. Rated for 208/230 Volt AC Line input only. See Figure 11 on page 20.
see Section 5.2 on page 20.
Ground (Earth):
400/460Volt, 3-Phase, 50/60 Hz, AC Line Input (Terminals L1, L2, L3)
Models KBAC-416 , 416S, 416F, 416SF see Section 5.1 on pages 19 and 20.
Models KBAC-29, 217, 217S, 217F, 217SF see Section 5.1 on pages 19 and 20.
208/230Volt, 3-Phase, 50/60 Hz, AC Line Input (Terminals L1, L2, L3)
(Terminals L1, L2)
see Section 5.1 on pages 19 and 20.
Models KBAC-24D, 27D, 29, 29 (1P):
50/60 Hz, AC Line Input
208/230Volt, 1-Phase,
3-Phase
see Section 5.3 on page 21.
AC Induction Motor:
AC LINEM OTOR
Motor
TB1
L2
L1V WU L3
Figure 1 – Quick-Start Connection Diagram*
*Layout may vary.

5
Note: Rated for 2 HP maximum with 1-phase AC Line input and 3 HP maximum with 3-phase AC Line
input. For 3 HP rating with single-phase input, use Model KBAC-29 (1P).
Models KBAC-217, 217S, 217F, 217SF: Designed to accept 3-phase (Terminals L1, L2, L3) AC Line
input only. Rated for 208/230 Volt AC Line input only. See Figure 12 on page 20.
Models KBAC-45, 48, 416, 416S, 416F, 416FS: Designed to accept 3-phase (Terminals L1, L2, L3)
AC Line input only. Rated for 400/460 Volt AC Line input only. See Figure 12 on page 20.
1.2 AC Line Fusing – It is recommended that a fuse(s) or circuit breaker be installed in the AC Line.
Fuse each conductor that is not at ground potential. For the recommended fuse size, see Table 4
on page 14. Also see Section 11 on page 28.
1.3 Ground Connection – Connect the ground wire (earth) to the ground screw, as shown in Figures
10 -12 on page 20. See Section 5.2 on page 20.
1.4 Motor Connection – Wire the motor to Terminal Block TB1 Terminals U, V, W, as shown in
Figures 10 -12 on page 20. (Special reactors may be required for cable lengths over 100 ft. (30 m) –
consult our Sales Department.) See Section 5.3 on page 21.
1.5 60 Hz And 50 Hz Motor Operation – The drive is factory set for 60 Hz 3-phase motor operation
(Jumper J5 set to the “60Hz” position). For 50 Hz motor operation, set Jumper J5 to the “50Hz”
position. See Section 6.4 on page 24.
1.6 Start/Stop Switch – The drive is supplied with a prewired Start/Stop Switch to electronically
“start” and “stop”the drive, as described in Section 5.5 on page 21. This switch must be used to
“start” the drive each time the AC Line is applied to the drive or to “restart” the drive. Also see
Section 6.8 on page 25.
1.7 Jumper Settings – All jumpers have been factory set for most applications. However, some
jumpers may need to be set in order to tailor the drive for a specic application. See section 6
on pages 23 – 26.
IMPORTANT: In order to ensure that the motor is properly protected with the I2t Overload
Protection feature, it is required that Jumper J2 is set to the corresponding position for the motor
horsepower being used, as shown in Figure 22 on page 24.
1.8 Trimpot Settings – All trimpots have been factory set for most applications. Some applications re-
quire adjustment of the trimpots in order to tailor the drive for a specic requirement. See Section
13 on pages 29 – 32.
1.9 Diagnostic LEDs – After power has been applied, observe the LEDs to verify proper drive
operation, as described in Section 12 on pages 28 and 29.

6
2 SAFETY WARNING
Denition of Safety Warning Symbols
Electrical Hazard Warning Symbol – Failure to observe this warning could result in electrical
shock or electrocution.
Operational Hazard Warning Symbol – Failure to observe this warning could result in serious
injury or death.
This product must be installed and serviced by a qualied technician, electrician, or
electrical maintenance person familiar with its operation and the hazards involved.
Proper installation, which includes electrical connections, fusing or other current protection,
and grounding, can reduce the chance of electrical shocks, and/or res, in this product or
products used with this product, such as electric motors, switches, coils, solenoids, and/or
relays. Do not use this drive in an explosion-proof application. Eye protection must be worn and
insulated adjustment tools must be used when working with drive under power. This product is
constructed of materials (plastics, metals, carbon, silicon, etc.) which may be a potential hazard.
Proper shielding, grounding, and ltering of this product can reduce the emission of radio
frequency interference (RFI) which may adversely aect sensitive electronic equipment. It is the
responsibility of the equipment manufacturer and individual installer to supply this Safety
Warning to the ultimate end user of this product. (SW 8/2012)
This product complies with all CE directives pertinent at the time of manufacture. Contact our
Sales Department for Declaration of Conformity. Installation of a CE approved RFI lter is
required. See RFI Filters & Chokes Selection Guide D-321 (Part No. A42027) for selection of lters that
meet the Industrial or Residential Standard. Additional shielded cable and/or AC Line cables may be
required along with a signal isolator (SIAC-PS).
3 INTRODUCTION
Thank you for purchasing the KBAC Adjustable Frequency Drive. KB Electronics, Inc. is committed to pro-
viding total customer satisfaction by producing quality products that are easy to install and operate. The
KBAC is manufactured with surface mount components incorporating advanced circuitry and technology.
The drives are variable speed controls housed in a rugged NEMA 4X / IP65 washdown and watertight
die-cast aluminum enclosure. They are designed to operate 208 – 230 and 400/460 Volt 50 & 60 Hz
3-phase AC induction motors from subfractional thru 10 HP. The sine wave coded Pulse Width Modulated
(PWM) output operates at a carrier frequency of 16 kHz which provides high motor eciency and low
noise. Adjustable Linear Acceleration and Deceleration are provided, making the drive suitable for
soft-start applications.
Due to its user-friendly design, the KBAC AC drive is easy to install and operate. Tailoring to specic
applications is accomplished with selectable jumpers and trimpots, which eliminate the computer-like
programming required on other drives. However, for most applications no adjustments are necessary.
Main features include adjustable RMS Current Limit and I2t Motor Overload Protection.* In addition,
Adjustable Slip Compensation with Static Auto-Tune and Boost provides high torque and excellent
load regulation over a wide speed range. Power Start™ delivers over 200% motor torque to ensure
start-up of high frictional loads. Electronic Inrush Current Limit (EICL™) eliminates harmful AC Line inrush
current. A Run/Fault Relay is provided, which can be used to turn equipment on or o , to signal a
warning if the drive is put into the Stop Mode, or if a fault has occurred. The drive is suitable for machine
or variable torque (HVAC) applications. Also, a jumper is provided for selection of Regenerative or
DC Injection Braking.
Standard front panel features include Diagnostic LEDs for“Power On” and “Drive Status”, a Start/Stop
Switch, and a Main Speed Potentiometer. Other features include a Barrier Terminal Block to facilitate
wiring of the AC Line and motor, adjustable trimpots (MIN, MAX, ACCEL, DEC/I, COMP, CL, JOG, BOOST),
customer selectable jumpers (Line Voltage - dual voltage models only), Motor Horsepower, Automatic
Ride-Through / Manual Start, Motor Frequency, Frequency Multiplier, Fixed/Adjustable Boost, Regenera-
tive / Injection Braking, “Run” or “Fault” Output Relay Operation, NO/NC Stop Contact, Constant/Variable
Torque, Switching Frequency, and GFCI operation (KBAC-217 Series and KBAC-416 Series only).

7
Optional accessories include: Forward-Stop-Reverse Switch, On/O AC Line Switch, Run-Stop-Jog Switch,
Signal Isolator, Auto/Manual Switch, Class ”A” AC Line Filter, Multi-Speed Board and Liquidtight Fittings.
A connector is provided for easy installation of accessories. Custom software: all models can be factory
programmed for applications which require special timing, PLC functions, and GFCI operation
(Models KBAC-24D, 27D, 29, 29 (1P), 45, 48) – contact our Sales Department.
*UL approved as an electronic overload protector for motors.
3.1 Standard Features
• Industrial Duty Die-Cast Aluminum Case with Hinged Cover – Available in Dark Gray nish or
FDA approved white nish.
• Simple to Operate – Does not require programming. Uses trimpots and jumpers, which are
factory set for most applications.
• Motor HP Selection Jumper (J2) – Allows the drive to be used on a wide range of motors
without recalibration.
• Switching Frequency and GFCI Selection Jumper (J12) – Allows the drive to be operated
at 8 kHz or 12 kHz and on Standard (G1) or Sensitive (G2) GFCIs. (KBAC-217 Series and
KBAC-416 Series only.)
• Diagnostic LEDs – Power on (POWER) and drive status (STATUS).
• Run/Fault Relay Output Contacts – Can be used to turn equipment on or o, to signal a warning
if the drive is put into the Stop Mode, or a fault has occurred.
• Start/Stop Switch – Provides electronic start and stop functions.
• Barrier Terminal Block – Facilitates wiring of motor, AC Line, and Run/Fault Relay Output Contacts.
• Jumper Selection of Drive Output Frequency – Increases the motor speed up to two times the
rated RPM.
• Ride-Through – Provides smooth recovery to the previous set speed during a momentary power
loss (of less than 2 seconds).
• Holding Torque at Zero Speed – Resists motor shaft rotation when the drive is in Stop Mode.
Note: GFCI Operation: Models KBAC-24D, 27D, 29, 29 (1P), 45, 48 require custom software – contact
our Sales Department. The KBAC-217 Series and KBAC-416 Series are jumper selectable (J12) for Stan-
dard (G1) or Sensitive (G2) GFCIs.
3.2 Performance Features
• Power Start™ – Provides more than 200% starting torque which ensures startup of high frictional loads.
• Slip Compensation with Static Auto-Tune and Boost – Provides excellent load regulation over
a wide speed range.
• Speed Range – 60:1
3.3 PROTECTION FEATURES
• Motor Overload (I2t) with RMS Current Limit* – Provides motor overload protection which
prevents motor burnout and eliminates nuisance trips.*
• Electronic Inrush Current Limit (EICL™) – Eliminates harmful Inrush AC Line current during startup.
• Short Circuit – Shuts down the drive if a short circuit occurs at the motor (phase-to-phase).
• Regeneration – Eliminates tripping due to high bus voltage caused by rapid deceleration of high
inertial loads.
• Undervoltage and Overvoltage – Shuts down the drive if the AC Line input voltage goes above
or below the operating range.
• MOV Input Transient Suppression – Protects the drive components against damaging voltage
spikes on the AC Line.
• Microcontroller Self Monitoring and Auto Reboot.
*UL approved as an electronic overload protector for motors.

8
3.4 TRIMPOT ADJUSTMENTS
• Minimum Speed (MIN) – Sets the minimum speed of the motor. See Section 13.1 on page 29.
• Maximum Speed (MAX) – Sets the maximum speed of the motor. See Section 13.2 on page 29.
• Acceleration (ACCEL) – Sets the amount of time for the motor to accelerate from zero speed to
full speed. See Section 13.3 on page 29.
• Deceleration (DEC/I) – Sets the amount of time for the motor to decelerate from full speed to
zero speed. See Section 13.4 on page 27.
• DC Injection Brake (DEC/I) – When the drive is set for DC Injection Braking (Jumper J7 set to
the “INJ” position), the DEC/I trimpot is used to set the DC Injection Brake voltage and time.
See Section 13.5 on pages 29 and 30.
• Slip Compensation (COMP) – Maintains set motor speed under varying loads. See Section 13.6
on page 30.
• Current Limit (CL) – Sets the current limit (overload) which limits the maximum current to the
motor. See Section 13.7 on pages 30 and 31.
• Boost (BOOST) – Sets the amount of Boost which can be used to obtain maximum low speed
performance. See Section 13.8 on pages 31 and 32.
• Jog (JOG) – Sets the “jog” speed of the motor. Must be used with the optional Run-Stop-Jog
Switch Kit (See Table 2 on page 9). See Section 13.9 on page 32.
Table 1 – Jumper Selectable Features
Description1
PC Board
Designation KBAC-24D, 27D KBAC-29, 29 (1P), 45, 48
KBAC-217 Series
KBAC-416 Series
AC Line InputVoltage (115, 230) J1 p— —
Motor Horsepower (seeTable 4 - Electrical Ratings on page 14) J2 p p p
Automatic Ride-Through or Manual Restart (A2, M) J3 p p p
Frequency Multiplier (1X, 2X) J4 p p p
Motor Frequency (50Hz, 60Hz) J5 p p p
Fixed or Adjustable Boost (FIX, ADJ) J6 p p p
Regenerative or DC Injection Braking (RG, INJ) J7 p p p
“Run”or“Fault”Output Relay Operation (R, F) J8 p p p
Normally Open or Closed Stop Contact (NO, NC) J9 p p p
Constant orVariableTorque (VT, CT) J10 p p p
Factory Use Only J11 — — —
Switching Frequency and GFCI (8 kHz, 12 kHz, G1, G2) J12 — — p
Notes: 1. Bold indicates factory setting. 2. In Automatic Ride-Through Mode, the drive will automatically restart due to a momentary power loss of
less than 2 seconds.

9
Table 2 – Optional Accessories
Description KBAC-24D KBAC-27D KBAC-29 KBAC-29 (1P) KBAC-45 KBAC-48
KBAC-217 Series
KBAC-416 Series
Forward-Stop-Reverse Switch – Provides motor
reversing and stop functions. Mounts on the enclosure
cover and is supplied with a switch seal to maintain
liquidtight integrity.
9480 9480 9480 9480 9480 9480 8888
On/O AC Line Switch – Disconnects the AC Line.
Mounts on the enclosure cover and is supplied with a
switch seal to maintain liquidtight integrity.
9482 9523 9532 9532 9532 9532
“S”Sux Models
(Factory Installed
Only)
Run-Stop-Jog Switch – Selects speed
setting from either the Main Speed Potentiometer or
the JOG Trimpot. Mounts on the enclosure cover and
is supplied with a switch seal to maintain liquidtight
integrity.
9340 9340 9340 9340 9340 9340 8889
SIAC-PS Signal Isolator with Power Supply –
Provides isolation between a non-isolated signal source
and the drive. Mounts on the drive’s PC board with
four snap-ins.
9600C* 9600C* 9600C* 9600C* 9600C* 9600C* 8890
Auto/Manual Switch – When used with the Signal
Isolator, it selects remote process signal or the Main
Speed Potentiometer. Mounts on the enclosure
cover and is supplied with a switch seal to maintain
liquidtight integrity.
9481 9481 9481 9481 9481 9481 8891
AC Line Filter* – Provides Class A RFI (EMI)
suppression. Installs onto the drive’s PC board
with quick-connect terminals.
“S”Sux: Filter is used when On/O AC Line
Switch is installed.
“NS”Sux: Filter is used when On/O AC Line
Switch is not installed.
“S”
Sux 9507 9512 9479 — 9479 9479
9516
“NS”
Sux 9507 9512 9515 — 9515 9515
Liquidtight Fittings – Provide a liquidtight seal for
wiring the drive. Kit includes three 1/2”and one 3/4”
liquidtight ttings for case A and case B drives, and one
1/2”and two 3/4”liquidtight ttings for case C drives.
9526 9526 9526 9526 9526 9526 8892
*Complies with CE Council Directive 89/336/EEC Industrial Standard.
*Warning! It is highly recommended that the SIAC-PS Signal Isolator with Power Supply be
installed when using the drive with external control signals. See Appendix A, on Page 33,
for more information.

10
WVU
TB1
L1 L2
AC LINE
L2BL2AL1BL1A
(BLK)
B- B+
(RED)
J1
115V
230V
RG
J6
1/2
3/4
1/4
1HP
AUTO
MAN
60HZ
50HZ
2X
FIX
1X
ADJ
MULT
BST
J3
J5
J4
J9
FREQ
NO
NC
J8
J7
INJ
R
F
CON1
1/8
STOP
VT
CT
2
1
MAX ACCEL DECELMIN CLBOOST
JOGP1P2P3
STATUS
POWER
CON2
FWD
COM
REV
RUN
COM
STOP
N.C.
TB2
N.O.
COM
Start/Stop Switch
Black
White
Red
COMP JOG
J10
J11
RELAY
A
B
J2
M
J
I
D
C
L
L– J11: Not used.
K
H
G
F
E
White (Low)
Violet (High)
Orange (Wiper)
Main Speed Potentiometer
A– JOG Terminal. Used with optional Run/Jog Switch Kit.
See Table 2 on page 9.
B– Adjustable trimpots. See Section 13 on Pages 29 - 32.
C– J3: Automatic Ride-Through or Manual Restart selection.
See Section 6.3 on page 23.
D– J4: 1X or up to 2X Rated Motor RPM Operation selection.
See Section 6.4 on page 24.
E– J2: Motor Horsepower selection.
See Section 6.2 on pages 23 and 24.
F– J5: 60 Hz or 50 Hz Motor Operation selection.
See Section 6.4 on page 24.
J– J9: Normally Open or Closed Stop Contact selection.
See Section 6.8 on page 25.
I– J8: Run or Fault Output Relay Operation selection.
See Section 6.7 on page 25.
K– J10: Constant or Variable Torque selection.
See Section 6.9 on page 25.
M–CON1: Used to connect optional accessories to the drive.
See Table 2 on page 9.
G– J6: Fixed or Adjustable Boost selection.
See Section 6.5 on page 24.
H– J7: Regenerative or Injection Braking selection.
See Section 6.6 on page 25.
See Section 5.5 on page 21.
Output Contacts
See Section 5.4 on page 21.
See Section 12 on page 23.
N
O
O– L1A/L1B and L2A/L2B: For optional On/O AC Line Switch.
See Table 2 on page 9.
N– J1: AC Line Input Voltage selection. (Models KBAC-24D, 27D only.)
See Section 6.1 on page 23.
All jumpers and trimpots are shown in factory set positions.
LED Board
Run/Fault Relay
See Section 5.9 on page 23.
See Table 2 on page 9.
Forward-Stop-Reverse Switch.
Used for optional
See Table 2 on page 9.
SIAC Signal Isolator.
Used for optional
MOTOR
P
P– TB1: Motor and AC Line input connections.
See Sections 5.1 - 5.3 on pages 19 - 21.
CL
JOGCOMP
MAX MIN ACCEL DEC/I BOOST
Figure 2 – KBAC-24D Control Layout

11
Figure 3 – KBAC-27D*, 29, 29 (1P), 45, 48 Control Layout1
P1P2P3
CON2
STATUS
POWER
LED Board
FWD
COM
REV
RUN
COM
STOP
MIN ACCELMAX CLDEC/I BOOST JOG COMP
MIN ACCELMAX CLDECEL BOOST JOG COMP
Start/Stop Switch
Black
White
Red
White (Low)
Violet (High)
Orange (Wiper)
Main Speed Potentiometer
N.C.
TB2
N.O.
COM
E 1/2
A 2
C 1
D 3/4
B 1 1/2
J2
M
A
J3
2X
1X
J4
60Hz
50Hz
J5
ADJ
FIX
J6
RG
INJ
J7
R
F
J8
NC
NO
J9
CT
VT
J10
2 B
1 A
J11
CON1
All jumpers and trimpots are shown in factory set positions.
*On Model KBAC-27D, J11 is Labeled "A" , "B"
*On Model KBAC-27D, J12 is Labeled "2", "1 1/2", "1", "3/4", "1/2"
JOG

12
N.O.
COM
N.C.
JOG
REV
TB2
1X2X
J650Hz 60Hz
J5
J7
NO NC
INJ
FIX
RG
ADJ
J8
J9
J10
J11
RF
J3
J4
21
G2
J2
8K
12K
G1
J12
C
B
A
AUTO MAN
VT CT
CON9
CON1
CON5
CON4
CON2
CON3
CON6
CON8
CON7
MIN ACCELMAX CLDEC/I
MIN ACCELMAX DEC/I
BOOST
BOOST
JOG
JOG
COMP
COMPCL
P3
P2
P1
FWD
COM
COMSTOP RUN
Start/Stop Switch
LED Board
Main Speed
Potentiometer
All jumpers and trimpots are shown in factory set positions.
KBAC-217, 416 Series only.
See Section 6.11
on pages 25 and 26.
J12: Switching Frequency
and GFCI selection.
Figure 4 – KBAC-217, 416 Series Control Layout

13
Table 3 – General Performance Specications
Description Specication Factory Setting
115 Volt AC Line Input Voltage Operating Range (Volts AC) 115 (±15%) —
208/230 Volt AC Line Input Voltage Operating Range (Volts AC) 208 (-15%) / 230 (+15%) —
400/460 Volt AC Line Input Voltage Operating Range (Volts AC) 380 (-15%) – 460 (+15%) —
Maximum Load (% Current Overload for 2 Minutes) 150 —
Switching Frequency (kHz) (Jumper J12) (KBAC-217, 416 Series Only) 8, 12 —
Signal Following InputVoltage Range1(Volts DC) 0 – 5 —
Output Frequency Resolution (Bits, Hz) 10, 0.06 —
Minimum Speed Trimpot (MIN) Range (% Frequency Setting) 0 – 40 0
Maximum Speed Trimpot (MAX) Range (% Frequency Setting) 70 – 110 100
Acceleration Trimpot (ACCEL) and DecelerationTrimpot (DEC/I) Range (Seconds) 0.3 – 20 1.5
Boost Trimpot (BOOST) Range (Volts/Hz) 0 – 30 5
Slip CompensationTrimpot (COMP) Range at Drive Rating (Volts/Hz) 0 – 3 1.5
Current Limit Trimpot (CL) Range (% Full Load) 40 – 200 160
Jog Trimpot (JOG) Range (% Frequency Setting) 0 – 100 35
Motor Frequency Setting (Hz) (Jumper J5) 50, 60 60
Output Frequency Multiplier (1X, 2X) (Jumper J4)21, 2 1
Minimum Operating Frequency at Motor (Hz) 1 —
Speed Range (Ratio) 60:1 —
Speed Regulation (30:1 Speed Range, 0 – Full Load) (% Base Speed)32.5 —
Overload ProtectorTripTime for Stalled Motor (Seconds) 6 —
Undervoltage/Overvoltage Trip Points for 115Volt AC Line Input (± 5%) (Volts AC)⁴ 76 – 141 —
Undervoltage/Overvoltage Trip Points for 208/230Volt AC Line Input (± 5%) (Volts AC)4151 – 282 —
Undervoltage/Overvoltage Trip Points for 400/460Volt AC Line Input (± 5%) (Volts AC)4302 – 567 —
Run/Fault Relay Output Contact Rating (Amps at 30Volts DC, 125Volts AC, 250Volts AC) 1, 0.5, 0.25 —
OperatingTemperature Range (°C / °F)50 – 40 / 32 – 104 —
Operating Humidity Range (% Relative, Non-Condensing) 0 – 95 —
StorageTemperature Range (°C / °F) -2.5 – +85 / -13 – +185 —
Notes: 1. Requires an isolated signal. If a non-isolated signal is used, or if using 0 to ±2.5 thru 0 to ±25 Volts DC, or 4 – 20 mA DC signal input, install
the SIAC-PS Signal Isolator with Power Supply. 2. Allows the motor to operate up to two times the rated RPM. Constant horsepower will result when operating
the drive in the “X2” mode above the motor rated frequency. 3. Dependent on motor performance. 4. Do not operate the drive outside
the specied AC Line input voltage operating range. 5. See Table 4 on page 14.

14
Table 4 – Electrical Ratings
Model No.
Part No. Max. HP AC Line
Voltage
(50/60 Hz)
Phase
(Ø)
Max.
AC Line
Current
(Amps AC)
Fuse or
Circuit
Breaker
Rating
(Amps)
Voltage
Range
(Volts AC)
Max. Load
Current
(Amps/Phase)
Motor
Horsepower
Selection2
(Jumper J2)
Net Wt.
Gray White1HP kW lbs kg
KBAC-24D 9987 9988 1 0.75 115 114.4 20 0 - 208/230 3.6 13/4 1/2 1/4 1/8 5.9 2.7
208/230 8.1 15
KBAC-27D 9520 9521 1½ 1.13 115 122 25 0 - 208/230 5.5 – 1½31 3/4 1/2 10.3 4.7
2 1.5 208/230 16.7 20 6.7 23
A B C D E
KBAC-29 (1P)410001 10002 3 2.25 208/230 1 20.5 25 0 - 208/230 9 32 1½ 1 3/4
10.3 4.7
KBAC-29 9528 9529 2 1.5 208/230 1 16.7 20 0 - 208/230 6.7 – 251½ 1 3/4
3 2.25 3 11.7 15 9 35
KBAC-4569530 9531 3 2.25 400/460 3 7.2 10 0 – 400/460 5.5 32 1½ 1 3/4
KBAC-4869540 9541 5 3.75 400/460 3 11 15 0 – 400/460 8.3 53 2 1½ 1
A B C
KBAC-217 8868 8879
5 3.75 208/230 3 22.1 25 0 - 208/230 17 53 2
22 10
KBAC-217S 8863 8855
KBAC-217F 8861 8853
KBAC-217SF 8869 8880
KBAC-416 8870 8881
10 7.5 400/460 3 20.8 25 0 – 400/460 16 10 7.5 5
KBAC-416S 8864 8856
KBAC-416F 8874 8883
KBAC-416SF 8871 8882
Notes: 1. White FDA approved nish. 2. Bold indicates factory setting. On Model KBAC-24D, Jumper J2 is labeled “1”, “3/4”, “1/2”, “1/4”, “1/8” (factory set to the
“1” position).On Model KBAC-27D, Jumper J2 is labeled “2”, “1½”, “1”, “3/4”, “1/2” (factory set to the “1½” position). On Models KBAC-29, 45, 48, Jumper J2 is
labeled “A”, “B”, “C”, “D”, “E” (factory set according to the table). 3. Model KBAC-27D is rated 1½ HP maximum with 115 Volt AC Line input and 2 HP maximum
with 208/230 Volt AC Line input. 4. Model KBAC-29 (1P) is rated 9 Amps at 35 °C / 95 °F and derated to 8.3 Amps at 40 °C / 104 °F. For ambient temperatures
above 40 °C / 104 °F, the drive is derated 2.5% per °C. 5. Model KBAC-29 is rated 2 HP maximum with single-phase AC Line input and 3 HP maximum with
3-phase AC Line input. 6. Models KBAC-45, 48, KBAC-217 Series and KBAC-416 Series are rated 0 – 400 Volts AC for 50 Hz motor operation and 0 – 460 Volts
AC for 60 Hz motor operation.

15
2X Ø 2.53
0.25
0.31
8.85
2* 3*
4* 1*
225
7.97 6.4 64.4
5.51
129
5.06
140
8.20
208 9.53
242
2.70
68.6
1.35
34.3
1.35
34.3
2.76
70.1
5.97
152
0.875
22.2
3X
*Tighten these screws, inthe sequence shown, to 12 in-lbs(14 kg-cm).
AC MOTOR SPEED CONTROL
KBAC SERIES • NEMA 4X / IP 65
Hybrid Drive
™
Figure 5 – Model KBAC-24D Mechanical Specications (Inches/mm)

16
Figure 6 – Models KBAC-27D, 29, 29 (1P), 45, 48 Mechanical Specications (Inches/mm)
2.97
75.4
3.07
77.9
7.36
187
3.20
81.3
1.60
40.6
1.60
40.6
0.875
22.2
1.09
22.2
2X
8.67
220
9.24
235
9.82
249
7.30
185
7.69
195
4X Ø 6.4
0.25 0.29
7.37
2X 25.4
2X 80.0
1.00
3.15
2X
*Tighten these screws, inthe sequence shown, to 12 in-lbs(14 kg-cm).
AC MOTOR SPEED CONTROL
KBAC SERIES • NEMA 4X / IP 65
Hybrid Drive
™
2* 3*
4* 1*

17
Figure 7 – KBAC-217, 416 Series Mechanical Specications (Inches/mm)
*Tighten these screws, in the sequence shown, to 12 in-lbs (14 kg-cm).
4X Ø
0.313
7.95
6*
2.25
57.2
3.822
97.1
2X
0.346
8.79
2X
3*
311
12.235 335
13.175 351
13.825
1*
5*
4.087
104
2X
9.89
251 10.3
262
1.72
43.7
2*
4*
MAXIMUM DRIVE DEPTH
Models without "S" Sux: 8.5
216
Models with "S" Sux: 9.0
227
1.72
43.7 1.60
40.6
1.08
27.4
2X Ø
0.875
22.2
Ø
9.0
227
3.97
100
KBAC SERIES • NEMA 4X / IP65
AC MOTOR SPEED CONTROL
Hybrid Drive™

18
4 IMPORTANT APPLICATION INFORMATION
4.1 Motor With External Fan Cooling – Most totally enclosed fan-cooled (TEFC) and open ventilated
3-phase AC induction motors will overheat if used beyond a limited speed range at full torque.
Therefore, it is necessary to reduce motor load as speed is decreased.
Note: Some fan-cooled motors can be used over a wider speed range. Consult the motor manufacturer
for details.
WARNING! Some motors have low speed characteristics which cause overheating and
winding failure under light load or no load conditions. If the motor is operated in this manner
for an extended period of time, it is recommended that the unloaded motor current be checked
from 2 – 15 Hz (60 – 450 RPM) to ensure motor current does not exceed the nameplate rating.
Do not use motor if the motor current exceeds the nameplate rating.
It is recommended that the drive be used with Inverter Duty or TENV motors.
Inverter duty and most
totally enclosed non-
ventilated (TENV) motors can
provide full rated torque over
an extended speed range
without overheating.
See Figure 8.
If external fan cooling is
provided, open ventilated
motors can also achieve
an extended speed range
at full rated torque. A box
fan or blower with a
minimum of 100 CFM per
HP is recommended. Mount
the fan or blower so the
motor is surrounded by the
airow. See Figure 9.
4.2 Electronic Motor Overload
Protection – The drive
contains Modied I2t
Overload Protection.* Part
of this function consists of
a Current Limit (CL) circuit,
which limits the drive
current to a factory preset
level of 160% of the rated
drive current. The CL
Trimpot is used to
recalibrate the drive
current from 60% thru 200%. The Power Start™ circuit provides an overshoot function that allows
most motors to develop more than 200% of starting torque and breakdown torque.
Standard I2t is undesirable because it causes nuisance tripping. It allows a very high motor current
to develop and will turn the drive o after a short period of time. KB’s RMS Current Limit Circuit
avoids this nuisance tripping while providing maximum motor protection.
If the motor is overloaded to 120% of full load (75% of the CL setting), the I2t Timer starts. If the
motor continues to be overloaded at the 120% level, the timer will shut down the drive after 30
minutes. If the motor is overloaded to 160% of full load, the drive will trip in 6 seconds.
*UL approved as an overload protector for motors.
and TENV Motors
Inverter Duty
Maximum Allowed
Motor Torque (%)
TEFC and Open Ventilated
Motors
Fan Cooled
100
60 70 805030 40100 20 90
Motor Speed (%)
40
0
20
60
80
100
Figure 8 – Maximum Allowed Motor Torque vs. Speed
Open Ventilated Motor Fan or Blower
(100 CFM Min.
per HP)
Airow
Figure 9 – Open Ventilated Motor with External Fan Cooling

19
5 WIRING INSTRUCTIONS
WARNING! Read Safety Warning, on page 6, before using the drive. Disconnect main
power before making connections to the drive. To avoid electric shock, be sure to properly
ground the drive. It is highly recommended that the SIAC-PS Signal Isolator with Power Supply
(Part No. 9600C) be installed when using signal following.
WARNING! HIGH VOLTAGE – REMOTE CONNECTIONS OF POTENTIOMETER, SWITCHES, ETC.,
WILL HAVE WIRING THAT IS AT LINE POTENTIAL. IT IS REQUIRED THAT THE SIGNAL ISOLATOR
BE INSTALLED FOR REMOTE CONNECTIONS.
Application Note – To avoid erratic operation, do not bundle the AC Line and motor wires with each
other or with wires from signal following, start/stop contacts, or any other signal wires. Also, do not
bundle motor wires from multiple drives in the same conduit. Use shielded cables on all signal wiring
over 12”(30 cm). The shield should be earth grounded on the drive side only. Wire the drive in
accordance with the National Electrical Code requirements and other local codes that may apply.
Be sure to properly fuse each AC Line conductor that is not at ground potential. Do not fuse neutral or
grounded conductors. A separate AC Line switch or contactor must be wired as a disconnect so that
each ungrounded conductor is opened. For fuse or circuit breaker selection, see Table 5. Also see
Section 11 on page 28.
To maintain the watertight integrity of the drive, be sure to use suitable liquidtight ttings and
wiring which are appropriate for the application. Model KBAC-24D contains three holes for standard
1/2” liquidtight ttings (not supplied) (one 1/2” watertight hole plug is provided). Models KBAC-27D,
29, 29 (1P), 45, 48 contain two holes for standard 1/2” liquidtight ttings (not supplied) and one hole
for standard 3/4”liquidtight tting (not supplied) (one 1/2” watertight hole plug is provided).
The KBAC-217, 416 Series contain one hole for standard 1/2”liquidtight ttings (not supplied)
and two holes for standard 3/4”liquidtight ttings (not supplied) (one 1/2” watertight hole plug
is provided).
The drive is designed with a hinged case so that when the front cover is open, all wiring stays intact.
To open the cover, the four screws must be loosened so they are no longer engaged in the case
bottom. After mounting and wiring, close the cover making sure that the wires do not get caught
or crimped as the cover is closed. Tighten the four screws so that the gasket is slightly compressed.
The recommended tightening torque is 12 in-lbs (14 kg-cm). See Figures 5, 6 and 7 on pages 15-17
for the tightening sequence. Do not overtighten.
Table 5 – Terminal Block Wiring Information
Terminal
Block Description Model
Maximum Wire Size (Cu) Recommended Tightening Torque
AWG mm2in-lbs kg-cm
TB1 AC Line Input and
MotorWiring
KBAC-24D 12 3.3 7 8
KBAC-27D, 29, 29 (1P), 45, 48 12 3.3 12 14
TB2 Run/Fault Relay
Output Contacts
KBAC-24D, 27D, 29, 29 (1P), 45, 48 14 2.08 3.5 4
KBAC-217, 416 Series 12 3.3 4.4 5
5.1 AC Line Input Connection – Wire the AC Line input to Terminal Block TB1.
GFCI Operation: Models KBAC-24D, 27, 29, 29 (1P), 45, 48 require custom software – contact
our Sales Department. The KBAC-217, 416 Series are jumper selectable (J12) for Standard
(G1) or Sensitive (G2) GFCIs.
Note: The rated AC Line voltage of the drive must match the actual AC Line input voltage. On Models
KBAC-24D, 27D, the setting of Jumper J1 must match the AC Line input voltage.

20
Models KBAC-24D, 27D: Designed to
accept 1-phase AC Line input only
(Terminals L1, L2). Rated for 208/230 Volt
AC Line input with Jumper J1 set to the
“230V” position (factory setting). Rated
for 115 Volt AC Line input with Jumper J1
set to the “115V” position. See Figure 10.
Model KBAC-29: Designed to accept
1-phase (Terminals L1, L2) or 3-phase
(Terminals L1, L2, L3) AC Line input.
Rated for 208/230 Volt AC Line input
only. See Figure 11.
Model KBAC-29(1P): Designed to
accept 1-phase AC Line input
(Terminals L1, L2). Rated for
208/230 Volt AC Line input only.
See Figure 10.
*Note: Model KBAC-29 is rated 2 HP maximum with 1-phase AC Line input and 3 HP maximum with 3-phase AC Line input.
toTerminals "L1", "L2", as shown below.
Model KBAC-29 Only
Wire the single-phase AC Line input
208/230Volt
AC Line Input
Single-Phase, 50/60 Hz Ground (Earth)
L3L2L1
AC LINE
Ground (Earth)3-Phase, 50/60 Hz
208/230, 400/460Volt
Motor AC Line Input
WU V
MOTOR
TB1
L1 L3L2
AC LINE
Figure 11 – Models KBAC-29*, 45, 48 AC Line Input, Motor, and Ground Connections
AC LINE
MOTOR
Motor
VU W
AC Line Input
115, 208/230 Volt
Single-Phase
Ground (Earth)
L1 L2
TB1
Figure 10 – Models KBAC- 24D, 27D*, 29 (1P)
AC Line Input, Motor, and Ground Connections
*Model KBAC-27D is rated 1½ HP maximum with 115 Volt AC Line input and
2 HP maximum with 208/230 Volt AC Line input.
TB1
L1 L2 L3
AC LINE
U W
MOTOR
V
Ground
Chassis Chassis
Motor
Ground
3-phase, 50/60 Hz AC Line Input
KBAC-217 Series: 208/230Volts AC
KBAC-416 Series: 400/460Volts AC
(Earth)(Earth)
Figure 12 – KBAC-217, 416 Series
AC Line Input, Motor, and Ground Connections
Models KBAC-45, 48: Designed to
accept 3-phase AC Line input only
(Terminals L1, L2, L3). Rated for
400/460 Volt AC Line input only.
See Figure 11.
KBAC-217 Series: Designed to accept
3-phase (Terminals L1, L2, L3) AC Line
input. Rated for 208/230 Volt AC Line
input only. See Figure 12.
KBAC-416 Series: Designed to accept
3-phase (Terminals L1, L2, L3) AC Line
input. Rated for 400/460 Volt AC Line
Input only. See Figure 12.
5.2 Ground Connection – Connect the
Ground Wire (Earth) to the Green
Ground Screw. The Ground Screw is
located next to Terminal Block TB1.
See Figures 10 -12.
This manual suits for next models
18
Table of contents
Popular DC Drive manuals by other brands
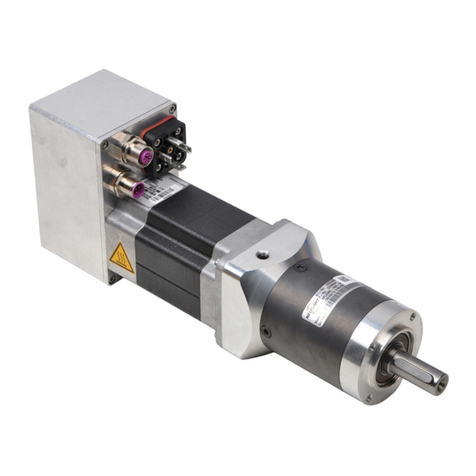
TR-Electronic
TR-Electronic MP-200 user manual
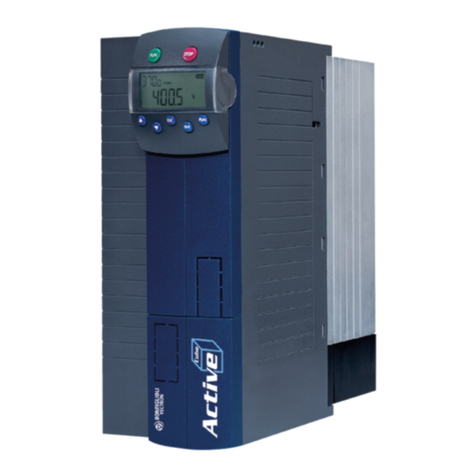
BONFIGLIOLI Vectron
BONFIGLIOLI Vectron ACTIVE CUBE manual
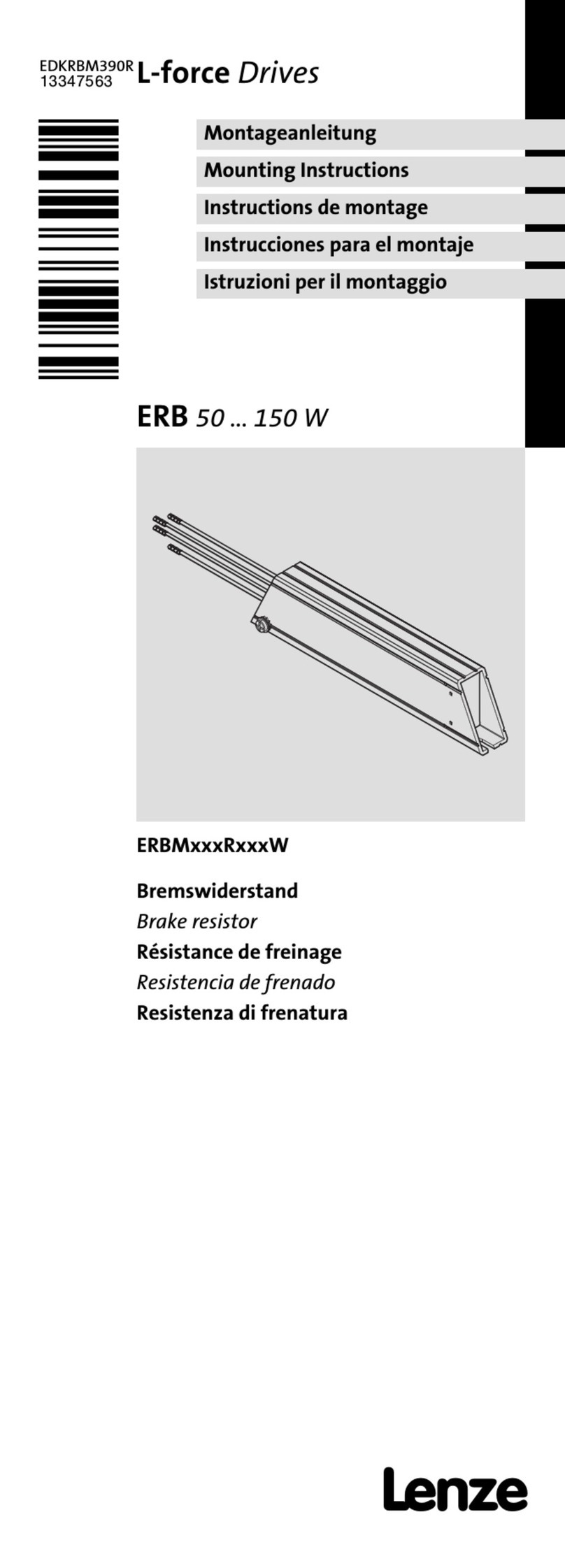
Lenze
Lenze ERBM R Series Mounting instructions
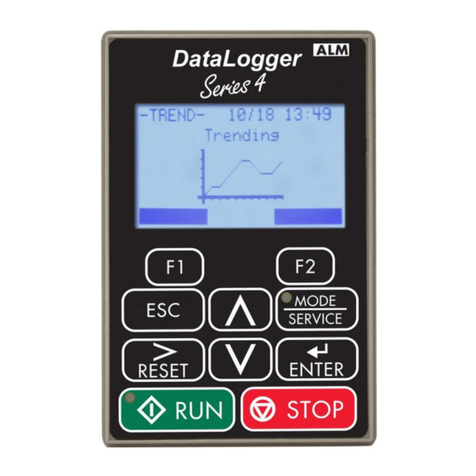
Magnetek
Magnetek DataLogger 4 Series installation manual
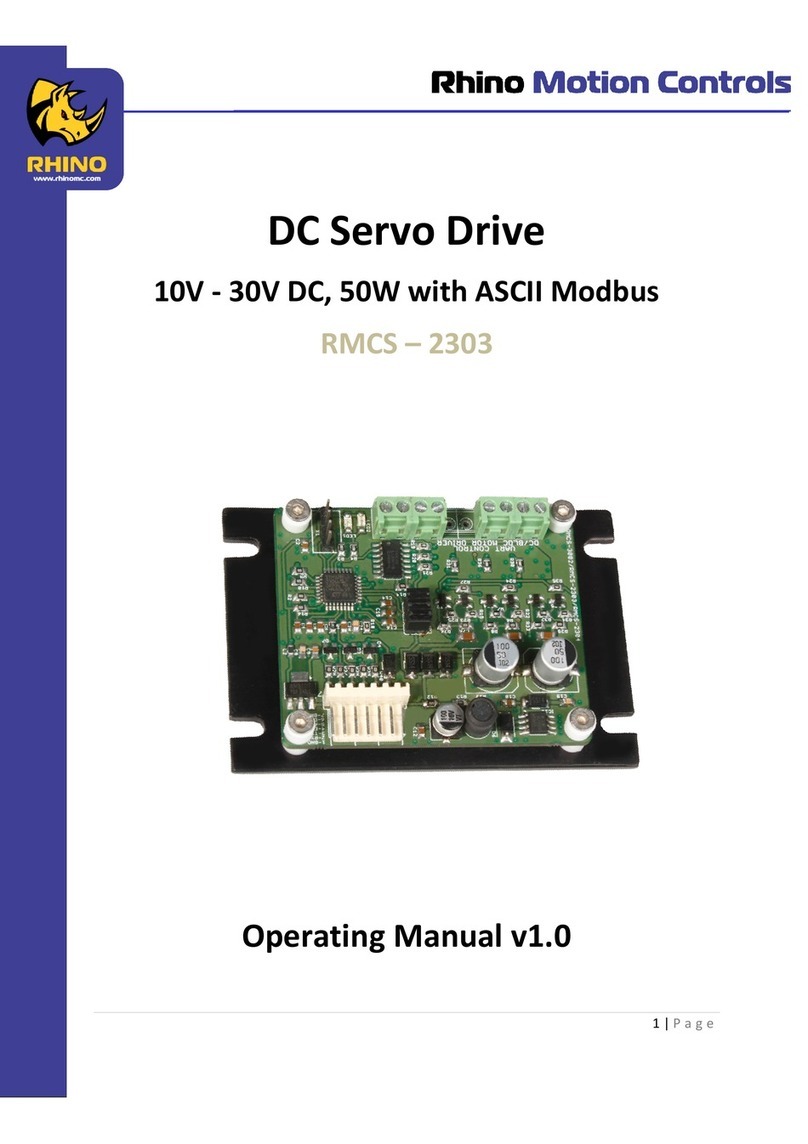
RHINO MOTION CONTROLS
RHINO MOTION CONTROLS RMCS - 2303 operating manual
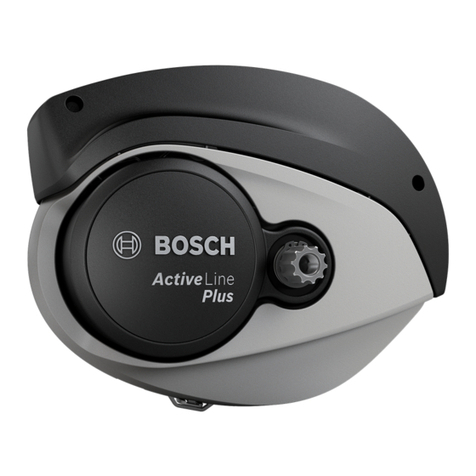
Bosch
Bosch Active Line Original operating instructions