KELCO T20 Installation manual

KELCO T20 TIMER
INSTALLATION & PROGRAMMING INSTRUCTIONS
KELCO Engineering Pty Ltd
Sydney Australia
www.kelco.com.au

Table Of Contents
Warning Symbols Explained.......................................................... 1
Important Safety Instructions......................................................... 2
Overview........................................................................................ 3
Installing the T20........................................................................... 4
Electrical........................................................................................ 5
Blackout or Brownout.................................................................... 6
Cable Gland Assembly................................................................... 7
The Heavy Duty (HD) Terminal...................................................... 8
Electrical Limitations...................................................................... 9
Circuit Diagrams............................................................................ 10
The 12VDC T20 Timer................................................................... 14
T20 Controls and Terminals........................................................... 15
Remote Flow Switch Input............................................................. 17
Suitable Flow Switches.................................................................. 19
Purging the T20............................................................................. 20
Programming the T20 Timer.......................................................... 21
Basic Operation............................................................................. 22
T20 Table of Limitations................................................................. 23
Advanced Functions...................................................................... 24
Batch Control................................................................................. 25
Delayed Restarting........................................................................ 26
Cyclic Running............................................................................... 27
Anti-Cycling.................................................................................... 28
Burst Pipe Detector........................................................................ 29
LCD Screen Backlight, Program Lock.......................................... 30
Program Lock................................................................................ 30
Maintenance.................................................................................. 30
Warranty......................................................................................... 31
Page

This symbol is intended to alert the user
to the presence of important operating
and maintenance instructions in the lit-
erature accompanying the T20 timer
WARNING
This symbol is intended to alert the user
to the presence of un-insulated “danger-
ous voltage” within the timer’s enclo-
sure that may be of sufcient magnitude
to constitute a risk of severe electric
shock.
WARNING
1

IMPORTANT SAFETY
INSTRUCTIONS
• Read these instructions.
• Keep these instructions.
• Heed all warnings.
• Follow all instructions.
• Do not allow water to enter this timer.
• Install this timer per the manufacturer’s instructions.
• Do not install this timer near any heat source such as
radiators, gas heaters, stoves or any other appliance that produces heat.
• Do not modify this timer in any way.
• Do not drill holes in this timer’s casing.
• Refer all installation and servicing to qualied service personnel.
• Servicing is required when the timer has been damaged in any way,
such as submerged in water, exposed to re, dropped or objects dropped
on it. Exposed to moisture or water when the timer’s lid is removed.
Please read these installation and operating in-
structions carefully and fully before installing or
servicing this timer. The T20 is a mains voltage
device. Death or serious injury may result if this
product is not correctly installed and operated.
WARNING
2

Overview
When connected to an external ow switch the T20 timer provides a pumping
system with a set of useful time and ow based functions. The T20 can be con-
gured in a variety of ways to control the pump and to protect it. It can be set to
start a pump in spite of an initial lack of ow and to then do no more than protect
it against loss of ow. The T20 can also be programmed to simulate a complex
pump control panel. This document sets out in detail the installation and functions
of the T20 timer and some of the main ways in which it can be used in pumping
and irrigation systems.
Without its lid in place the T20 timer is not water
resistant and presents a potential shock hazard.
Take great care not to splash water onto the T20
when the lid is not in place. Always replace the
lid and fully tighten its 6 securing screws imme-
diately after any changes to the timer’s settings
are made.
WARNING
3
INSTALLING THE T20 TIMER
Location
Where possible install this timer in a location that is sheltered from direct expo-
sure to the weather. The T20 is weatherproof and is supplied with a protective clip
on cover. However, to ensure a long reliable life we recommend it be protected
from direct exposure to the sun and rain. Intense sun light will eventually cause
discolouration and degradation of the timer’s housing. It is therefore advisable to
protect the timer from the weather if possible.
The T20 timer should be installed on a wall or on a bracket attached to a pump
or its pipework. Where large pump motors are to be directly controlled, mount the
T20 as close as practical to the supply and pump to keep heavy cable runs to a
minimum.

4
Installing the T20
The T20 timer is supplied as two separate assemblies, the wall mounting bracket
and the electrical housing. The mounting bracket should be installed rst by
securing it to a wall or to a plate attached to the pipework or pump. The drilling
pattern is shown below.
60mm
74mm
Attach the electrical housing to the wall bracket by engaging the two toes on the
bracket into the two notches in the retainer plate on the underside of the electri-
cal housing. Secure the electrical housing to the wall bracket using the large hex
headed red bolt supplied in the kit. Tighten the red bolt using a broad bladed
screwdriver or small socket wrench. Do not overtighten it.
4 X 6mm
Holes

Electrical
All electrical work associated with the T20 must
be carried out by qualied electrical personnel
and all electrical work must conform to AS/NZ
standards and to local wiring rules. For mains
voltage applications we recommend the sup-
ply to the T20 be isolated by an RCD that has a
maximum trip current of 30mA.
WARNING
Introduction
The T20 timer is designed to directly control single-phase pump motors to 3.75kW.
No interposing contactor is required for such applications. If a supply neutral or
transformer is available, the timer can also be used to control 3 phase pump mo-
tors via an appropriate interposing contactor that has a suitable coil voltage.
The T20 timer requires a 220V to 240V AC 50Hz supply when operated from the
mains. It can also be operated from an 18 to 24V AC or DC supply by utilising the
low voltage active terminal LV and common neutral terminal N, see the included
wiring diagrams. When operated from a low voltage DC supply the terminals LV
and neutral N are not polarity sensitive. The T20 timer requires a stable supply
voltage in order to operate correctly. Pay particular attention to cable sizes, and
ensure cables are adequate for the specic pump motor load. This is particularly
important where long cable runs are to be used in the installation. If the voltage
drop associated with the starting of the pump motor is excessive the T20 will au-
tomatically reset and this may cause the pump to jog. Jogging can snap the main
spindle of a pump very easily, so please take all precautions to ensure the voltage
supply to the T20 is stable and that the current carrying capacity of the cable used
is adequate for the job.
5

Brownout Or Blackout
If a blackout or brownout occurs the T20 timer will not retain memory of where in
its run or stop cycles it may have been. When power resumes, the T20 will reboot
and resume running. A manual reboot can be done at any time by pressing the
timer’s reset button.
The T20 timer derives low voltage for its opera-
tion from a non-isolated reactance power sup-
ply (not through an isolated transformer). All
external devices connected to the T20 must be
earthed and must be regarded as operating at
full mains potential. For all mains voltage ap-
plications we recommend the supply to the T20
be isolated by an RCD that has a maximum trip
current of 30mA.
WARNING
Cables
The T20 timer has 3 X M20 cable glands. As supplied the cable glands are
blanked off. To use the glands rst punch out the blanking barriers using a suit-
able punch. The cable glands can accept cable from 7 to 9mm diameter. See
attached sketch for assembling the cable gland components. The timer is sup-
plied with a set of steel crimp rings. The crimp rings are to provide strain relief for
the timers cables. To use the crimps, place one on the cable approximately 4mm
below the end to the cable’s outer sheathing. Crimp the two ears of the ring at
using bull nosed pliers. Pull the cable back through the cable gland until the crimp
ring’s ears are fully engaged in the two slots in the gland housing.
6

Relays
The T20 timer houses 2 relays. The contacts of both relays are voltage free and
are normally open. The relays are marked Relay 1 and Relay 2 on the terminal
block. Relay 1 is the primary relay and is used to control the pump motor. It has
an electrical rating of 30 Amps (resistive) at 240VAC. Relay 2 is a 16 Amp (resis-
tive) 240VAC rated relay and is used for actuating an external alarm. The relays
built into the T20 timer are not suitable for the direct control of DC motors.
7
Cable Gland Assembly

The HD (Heavy Duty) Terminal
The HD terminal must be left unused or only
ever be linked to the relay terminal Relay 1 Nor-
mally Open. It must never be used for any other
purpose and it must never be connected to any
external device. Under no circumstances con-
nect the HD terminal to the terminals of Relay 2.
The HD terminal must be regarded as live at all
times and at full mains potential
WARNING
The T20 timer contains a solid-state switch (HD Heavy Duty drive) that can be
used to protect the contacts of Relay 1 by eliminating the destructive arcing
caused by the starting and stopping of pump motors. The solid-state switch is
accessible from the HD (Heavy Duty) terminal on the terminal block. We recom-
mend the HD drive be used whenever the timer is used to directly control a pump
motor. The HD drive should not be used when the T20 is connected to external
timers, contactors, relays or to any other external device where voltage free con-
tacts are required. It is strictly intended for the direct control of highly inductive
AC motor loads. The HD terminal and the timer’s built in relays must never be
connected to a DC motor under any circumstances.
When the HD terminal is linked to the terminal Relay 1 Normally Open, the HD
drive in effect parallels a 40Amp solid state switch across the relay’s normally
open contacts. This increases the momentary current carrying capacity of the
relay’s contacts to well over 70 Amps. The solid state HD drive is only activated
for a short period when the pump starts and stops. It effectively handles the high
inrush current associated with the pump starting, and it provides a current path for
the destructive back EMF associated with the pump motor stopping.
To use the HD drive place a heavy link wire, 1.0mm or 1.5mm Sq between the HD
terminal and the Normally Open terminal of Relay 1.
8

VOLTAGE LIMITS ON TERMINALS A & N
Maximum Supply Voltage 250VAC 50Hz
Minimum Supply Voltage 160VAC 50Hz
VOLTAGE LIMITS ON TERMINALS LV & N
Maximum Supply Voltage 25VAC 50Hz or 25VDC
Minimum Supply Voltage 18VAC 50Hz or 18VDC
RELAY 1 CONTACT RATING
16A at 250VAC Resistive Load
16A at 30VDC Resistive Load
RELAY 2 CONTACT RATING
16A at 250VAC Resistive Load
16A at 30VDC Resistive Load
Do not connect any supply greater than 25VAC
or DC to the LV terminal on the T20 timer. The
LV terminal is only for use with a low voltage
supply of less than 25V AC or DC. If a voltage
greater than 25V AC or DC is connected to the
LV terminal of the T20 timer the timer will be
damaged and any warranty on the product will
be void.
WARNING
9

10
The following pages give some examples of ways the T20 timer
can be wired.
Please note all electrical work associated with the T20 timer must be car-
ried out by suitably qualied electricians
and must conform to AU/NZ wiring rules.
CONNECTIONS FOR PLUG & PLAY INSTALLATION
FOR PUMP MOTORS TO 2.4 kW
Circuit Diagrams

LOW VOLTAGE AC CONNECTIONS
ACTIVE
NEUTRAL
18 to 25VAC SUPPLY
REMOTE FLOW SWITCH. CONTACTS ARE
NORMALLY OPEN.
RELAY CONTACTS ARE VOLTAGE
FREE AND CAN BE USED TO SWITCH
A CONTACTOR OR TO DIRECTLY
CONTROL A PUMP MOTOR. SEE TEXT
FOR INFORMATION ON THE LIMITA-
TIONS OF THE RELAY CONTACTS AND
HOW TO USE THE HD TERMINAL.
LOW VOLTAGE DC CONNECTIONS
18 TO 25 VDC 150mA MINIMUM
SUPPLY POLARITY IS NOT IMPORTANT BUT
IF THE EXTERNAL INPUT IS USED IT MUST BE
SOURCED FROM THE SUPPLY POSITIVE AS
SHOWN HERE.
RELAY CONTACTS ARE VOLTAGE
FREE AND CAN BE USED TO SWITCH
A CONTACTOR OR TO DIRECTLY
CONTROL A PUMP MOTOR. SEE TEXT
FOR INFORMATION ON THE LIMITA-
TIONS OF THE RELAY CONTACTS AND
HOW TO USE THE HD TERMINAL.
REMOTE FLOW SWITCH. CON-
TACTS ARE NORMALLY OPEN.
11

12
REMOTE FLOW SWITCH. CON-
TACTS ARE NORMALLY OPEN.
SINGLE PHASE 220 ~ 240VAC
MOTOR MAXIMUM MOTOR LOAD
3.75kW
THIS LINK MUST BE USED WHEN-
EVER THE TIMER IS DIRECTLY
CONTROLLING A SINGLE PHASE
PUMP MOTOR, AS SHOWN HERE.
PUMP
MOTOR
CONTROL OF A SINGLE PHASE PUMP MOTOR WITH REMOTE FLOW
SWITCH INPUT AND AN EXTERNAL ALARM
ACTIVE
NEUTRAL
MAINS VOLTAGE SUPPLY
220VAC to 240VAC
ALARM LIGHT OR SIREN 220 ~
240VAC DEVICE 16A MAXIMUM
LOAD RESISTIVE
CONTROLLING A 3 PHASE PUMP WITH REMOTE FLOW SWITCH
INPUT AND AN EXTERNAL ALARM
REMOTE LEVEL OR PRESSURE
SWITCH. CONTACTS ARE
NORMALLY OPEN.
ALARM OR SIREN 220-240VAC DEVICE
16A MAXIMUM LOAD RESISTIVE.
CONTACTOR
3 PHASE PUMP
MOTOR
COIL
N
A1
A2
A3
3 PHASE SUPPLY

13
CONTROLLING A 240VAC SINGLE PHASE PUMP MOTOR WITH THE T20
TIMER POWERED FROM A LOW VOLTAGE AC SUPPLY
THIS LINK MUST BE USED
WHENEVER THE CONTROLLER IS
DIRECTLY CONTROLLING A SINGLE
PHASE PUMP MOTOR, AS SHOWN
HERE.
NEUTRAL
ACTIVE
MAINS VOLTAGE SUPPLY
220VAC to 240VAC
ACTIVE
NEUTRAL
18 to 25VAC SUPPLY
PUMP
MOTOR
SINGLE PHASE 220 ~ 240VAC
MOTOR MAXIMUM MOTOR LOAD
3.75kW
REMOTE FLOW SWITCH. CON-
TACTS ARE NORMALLY OPEN.
3 PHASE PUMP
MOTOR
COIL
CONTACTOR
N
A1
A2
A3
SUPPLY NEUTRAL
3 PHASE SUPPLY
BASIC 3 PHASE PUMP CONNECTIONS

A special 12VDC version of the T20 timer is available for battery operation and
for use in solar pumping systems. Functionally the 12VDC model is exactly the
same as the mains voltage model except for the terminal block markings. On the
12VDC model the active and neutral terminals are replaced by a positive + and
a negative – terminal. Supply voltage across the positive and negative terminals
must never exceed 14VDC or the timer will be damaged. The supply terminals
are reverse polarity protected. However, the timer will simply not operate unless
the supply polarity is correct.
When connecting a remote ow switch to the 12VDC T20 timer the supply to the
ow switch must be taken from the positive terminal on the T20 timer. The ow
switch and its connecting circuit will operate at 12VDC.
12VDC T20 TIMER
14
WIRING DIAGRAM
12VDC CONTROLLER ONLY
THIS LINK MUST BE USED
WHENEVER THE CONTROLLER IS
DIRECTLY CONTROLLING A SINGLE
PHASE PUMP MOTOR, AS SHOWN
HERE.
SUPPLY 11 ~ 14 VDC
REMOTE FLOW SWITCH. CON-
TACTS ARE NORMALLY OPEN.
SINGLE PHASE 220 ~ 240VAC
MOTOR MAXIMUM MOTOR LOAD
3.75kW
ACTIVE
NEUTRAL
MAINS VOLTAGE SUPPLY
220VAC to 240VAC
CONTROLLING A 220 ~ 240 VAC SINGLE PHASE PUMP MOTOR WITH THE T20 TIMER POWERED
FROM A 12V DC SUPPLY
IMPORTANT
THE SUPPLY TO THE REMOTE FLOW
SWITCH MUST BE SOURCED FROM
THE SUPPLY POSITIVE AS SHOWN
HERE.

T20 Controls and Terminals
15

16
No. Description Function
1Mains Voltage Active
Terminal
For all mains voltage applications this is the supply
connection.
2Supply Neutral
Terminal
For all applications this is the supply neutral connec-
tion.
3Low Voltage Active
Terminal
This is the supply active terminal for all low voltage
applications.
4Alarm Relay Terminal
Normally Open
This terminal is for connecting an external alarm. It is
voltage free.
5Alarm Relay Contact
Common
This terminal is for connecting an external alarm. It is
voltage free.
6Remote Input Terminal This is the remote switch input terminal for connection
to an external ow switch.
7Pump Relay Terminal
Normally Open
This terminal is for connection to a pump motor or
contactor.
8Pump Relay Terminal
Common
This terminal is for connection to a pump motor or
contactor.
9Heavy Duty Drive Ter-
minal
Link this terminal to the relay 1 Normally Open terminal
when directly controlling pump motors.
10 Program Button Press this button to program the T20 timer.
11 Timer Light (Red or
Green)
This light is green whenever a run timer is running. It
turns red whenever a stop timer is running.
12 Up Button Use this button when programming the ow switch to
enter data.
13 Pump Start Light (Red or
Green)
This light is red whenever the pump is stopped and it is
green whenever the pump is running.
14 LCD Screen The LCD screen displays information whenever the
timer is switched on.
15 Down Button Use this button when programming the T20 to enter
data. It also turns on the LCD backlight.
16 Reset Button This button reboots the T20 timer each time it is
pressed.
17
Flow Status Light
(Red or Green)
This light is green whenever ow is detected and red
when no ow is detected. It indicates the T20’s micro-
processor has read the true state of the external ow
switch.

Remote Flow Switch Input
An external ow switch with voltage free contacts or a set of external relay con-
tacts can be used to start and stop a pump under the control of the T20. The
supply to the external switch must be taken from the (LV) terminal (Low Voltage
active terminal) of the T20 timer when the timer is powered from the mains or from
a 24VAC source. The T20 must always be powered from the same source as the
supply to the external ow switch. The supply to the remote ow switch on the
T20-12 (low voltage DC model) must be taken from the supply positive terminal.
In all cases the external ow switch return wire must be connected to the Remote
input (R) terminal on the T20. The Supply to the external ow switch will range
from 12 to 24 VDC or from 20V to 35V AC depending on the model of the timer
and on the supply voltage.
WARNING : The low voltage source available at the LV terminal is non-iso-
lated and in terms of insulation must be regarded as operating at full mains
potential whenever the T20 timer is powered from the mains.
The remote ow switch can be installed some distance from the T20 timer. The
maximum distance is limited by cable resistance and capacitance. The total ca-
ble resistance must not exceed 5K Ohms with the remote ow switch’s contacts
closed. The total capacitance of the cable must not exceed 25nF with the re-
mote ow switch’s contacts open. Wires to the remote ow switch should be run
separately from power carrying cables. Do not run the remote ow switch wires
in a conduit that also contains power cables. Capacitive coupling between the
adjacent cables may cause false triggering of the T20’s remote input. For cable
runs longer than 150 metres suggest using 2 separate wires to reduce capaci-
tive coupling between the adjacent wires. When set up this way cable resistance
becomes the limiting factor for distance. The table that follows sets out the resist-
ance of typical copper wire of various diameters.
17

Example
A ow switch is located 1000 metres from the T20 timer. Two separate wires each
0.2mm^2 are run to the remote ow switch (total wire length is 2000 metres). The
resistance as measured across the 2 wires back at the T20 (with the ow switch‘s
contacts closed is 190 Ohms. This is well under the 5,000 Ohm limit. The remote
input to the T20 will operate properly provide the wires are separated by suf-
cient distance that the capacitance between them is less than 25nF. Capacitance
should be measured between the wires when the remote ow switch’s contacts
are open, and it must be less than 25nF.
Remote Flow Switch
The remote ow switch should be suitable for low voltage low current operation.
In particular its contacts should only require a low wetting current. The current in
the remote loop only runs to a few milliamperes and requires a ow switch that
will conduct when closed under low current conditions. Reed switches are the
preferred method of controlling the remote input to the T20 timer. Suitable Kelco
ow switch models are listed in the following table.
18
Note: Resistance may vary depending on the wire standard and the actual con-
struction of the wire. The cable resistance refers to the total resistance out to the
remote ow switch and back again, as measured at the T20 timer across the 2
remote ow switch connection wires with the ow switch contacts closed.
Nominal Cross Section of copper
wire in square millimetres
Resistance in Ohms per 1000 Me-
tres
0.2 95.30
0.5 36.20
0.75 24.13
1.0 18.10
1.5 12.10
Table of contents
Popular Timer manuals by other brands
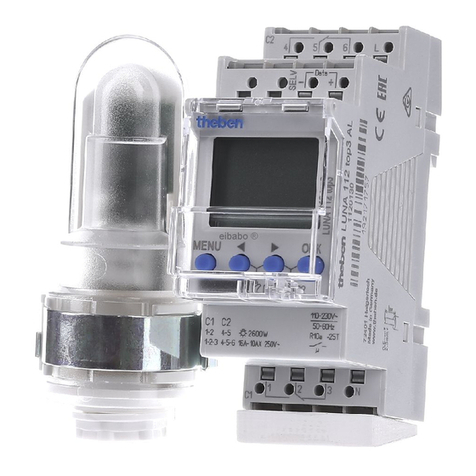
Theben
Theben LUNA 111 top3 AL operating instructions
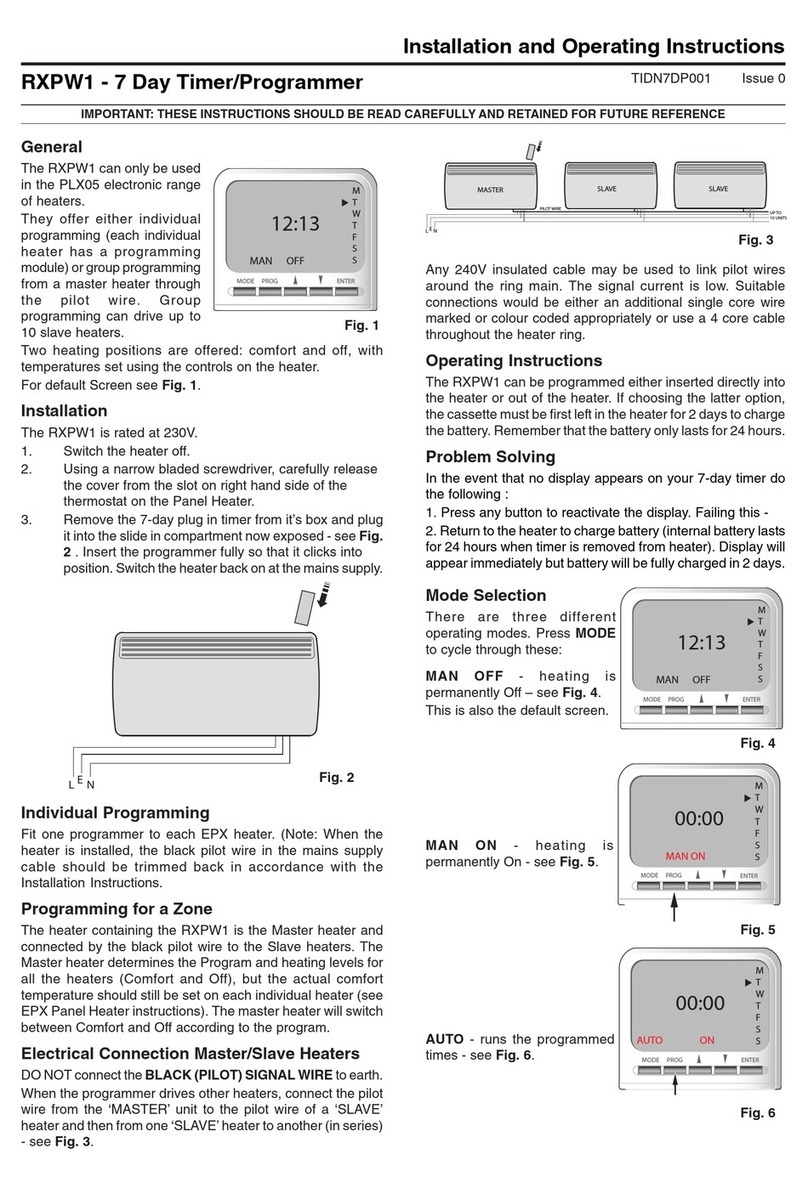
Dimplex
Dimplex RXPW1 Installation and operating instructions

Kärcher
Kärcher WT 5 Original instructions
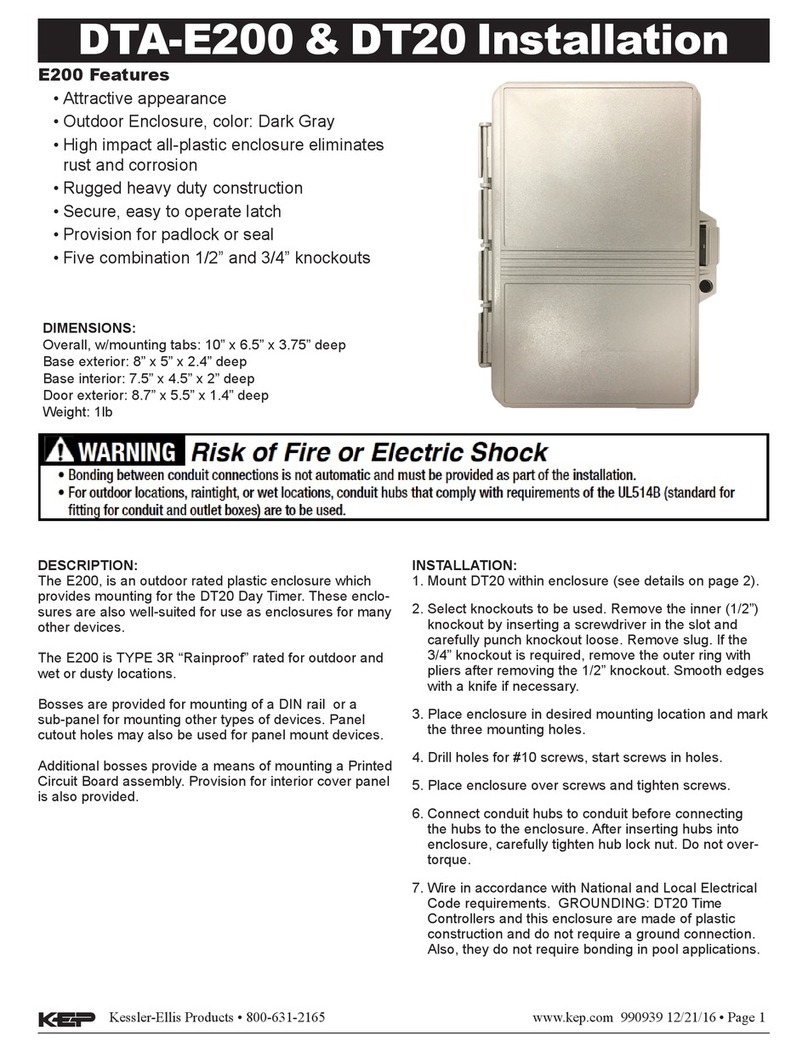
Kessler-Ellis Products
Kessler-Ellis Products DT20 Installation

Jorc
Jorc DLUX Timer 8500 installation instructions
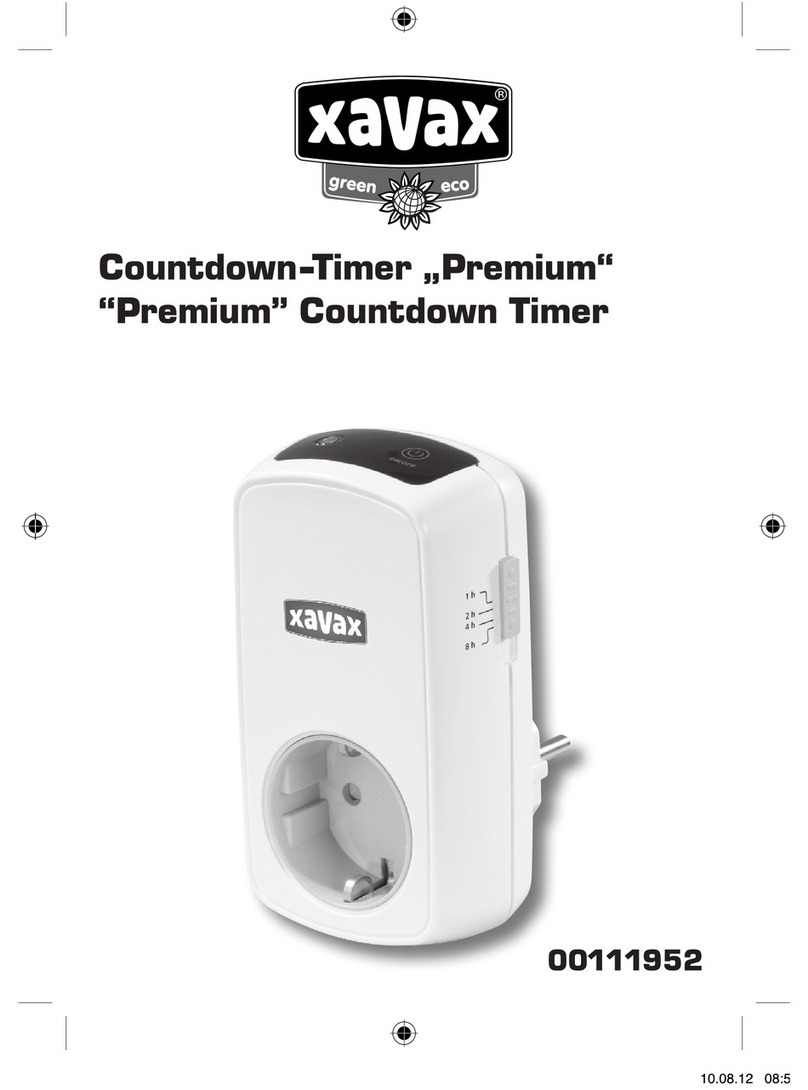
Xavax
Xavax Premium operating instructions