Kobold KLP User manual

Operating Instructions
for
Butterfly Isolating Valves
with Pneumatic Actuator
Model: KLP

KLP
page 2 KLP K05/0123
1. Contents
1.Contents ........................................................................................................ 2
2.Note .............................................................................................................. 3
3.Instrument Inspection .................................................................................... 3
4.Regulation Use ............................................................................................. 4
5.Safety Regulation .......................................................................................... 4
5.1Personal Advice ................................................................................... 5
5.2Device Safety ....................................................................................... 8
6.Pneumatical Installation ................................................................................ 9
6.1Function “Double-Acting“ ................................................................... 10
6.2Function “Single-Acting“..................................................................... 11
7.Pneumatical Disassembly ........................................................................... 12
8.Operating .................................................................................................... 12
9.Adjustments/Starting ................................................................................... 13
9.1Adjustments ....................................................................................... 13
9.2Starting .............................................................................................. 14
10.Maintenance ............................................................................................... 15
11.Technical Information .................................................................................. 16
12.Order Codes ............................................................................................... 16
13.Dimension ................................................................................................... 16
14.Disposal ...................................................................................................... 17
15.EC Declaration of Conformance ................................................................. 18
Manufactured and sold by:
Kobold Messring GmbH
Nordring 22-24
D-65719 Hofheim
Tel.: +49(0)6192-2990
Fax: +49(0)6192-23398
E-Mail: [email protected]
Internet: www.kobold.com

KLP
KLP K05/0123 page 3
2. Note
Please read these operating instructions before unpacking and putting the unit
into operation. Follow the instructions precisely as described herein.
The instruction manuals on our website www.kobold.com are always for currently
manufactured version of our products. Due to technical changes, the instruction
manuals available online may not always correspond to the product version you
have purchased. If you need an instruction manual that corresponds to the
purchased product version, you can request it from us free of charge by email
([email protected]) in PDF format, specifying the relevant invoice number and
serial number. If you wish, the operating instructions can also be sent to you by
post in paper form against an applicable postage fee.
Operating instructions, data sheet, approvals and further information via the QR
code on the device or via www.kobold.com
The devices are only to be used, maintained and serviced by persons familiar
with these operating instructions and in accordance with local regulations
applying to Health & Safety and prevention of accidents.
When used in machines, the measuring unit should be used only when the
machines fulfil the EC-machine guidelines.
as per PED 2014/68/EU
In acc. with Article 4 Paragraph (3), "Sound Engineering Practice", of the
PED 2014/68/EU no CE mark.
3. Instrument Inspection
Instruments are inspected before shipping and sent out in perfect condition.
Should damage to a device be visible, we recommend a thorough inspection of
the delivery packaging. In case of damage, please inform your parcel service /
forwarding agent immediately, since they are responsible for damages during
transit.
Scope of delivery:
The standard delivery includes:
Butterfly Valve with Pneumatic Actuator, model: KLP

KLP
page 4 KLP K05/0123
4. Regulation Use
Any use of the Butterfly Valves with Pneumatic Actuator, model: KLP, which
exceeds the manufacturer’s specifications, may invalidate its warranty. Therefore,
any resulting damage is not the responsibility of the manufacturer. The user
assumes all risk for such usage.
Ball valves will be used to cut off medium flow.
It should only be used for clean liquids and gases, on which the material of the
ball valve is resistant. Pollution or exceeding the nominal pressure range and/or
the nominal temperature range may lead into damages on the armature
especially on the seals.
5. Safety Regulation
Depending on the technical circumstances under which the armatures and valves
are mounted, adjusted and commissioned, you possibly must take into account
particular safety aspects in each case!
If, for example, a pneumatic actuator works a slide in an operational chemical
plant, the potential hazards of commissioning have another dimension from that
when this is only being carried out for test purposes an a “dry“ part of the plant in
the assembly room!
Since we do not know the circumstances at the time of the mounting/adjustment/
commissioning, you may find advice on hazards in the following descriptions
which are not relevant to you.
Please observe (only) the advice which applies to your situation!

KLP
KLP K05/0123 page 5
5.1 Personal Advice
5.1.1 Safety Advice for Mounting
We wish to point out expressly that the mounting, adjusting
and, with accessories, the pneumatic and electrical installation
of the armatures and valves must be carried out by trained
specialist personnel having mechanical, pneumatical and
electrical knowledge!
Secure that the machine / plant complies with to the Machinery Directive after
the mounting and installing of the armatures and valves.
Switch off all the devices / machines / plant affected by mounting or repair.
If appropriate, isolate the devices / machines / plant from the mains.
Check (for example in chemical plants) whether the switching off of the devices
/ machines / plant will cause potential danger.
If appropriate, in the event of a fault in the armature / valve (in a plant which is
in operation) inform the shift foreman / safety engineer or the works manager
without delay about the fault, in order, for example, to avoid an outflow /
overflow of chemicals or the discharge of gases in good time by means of
suitable measures!
Before mounting or repairing, remove the pressure from pneumatic / hydraulic
devices /machines / plant.
If necessary, set up warning signs in order to prevent the inadvertent starting
up of the devices /machines / plant.
Observe the respective relevant professional safety and accident prevention
regulations when carrying out the mounting / repair work.
Check the correct functioning of the safety equipment (for example the
emergency push off buttons/ safety valves, etc)!

KLP
page 6 KLP K05/0123
5.1.2 Safety Advice for Adjustment / Starting
As a result of the starting (pneumatic, electric or by hand) of the
armatures and valves the flow of gases, steam, liquids, etc. may
be enabled or interrupted! Satisfy yourself that, as a result of the
starting or the test adjustment that no potential hazards will be
produced for the personnel or the environment!
If necessary, set up warning signs in order to prevent the inadvertent starting
up or shutting down of the device / machine / plant.!
After completing the adjustment check the correct function and should the
occasion arise the position of the slide / valve / flap.
Check the function of the limit switches (option)!
Check, whether the slide / valve / flap will be closed totally, if the control
signals the appropriate limit stop!
Through suitable measures, prevent actuating links from being trapped by
moving actuating elements!
Check for correct functioning of all safety devices (for example emergency
push off buttons / safety valves)!
Carry out the starting and the adjustments only in accordance with the
instructions described in this documentation!
Adjustments of switched on (ready to operate) armatures and
valves with options (e.g. actuators, drives, limit switches)
presents the risk that live parts (230 V AC~) can be touched!
Therefore, the adjustments must be carried out only by an
electrician or a person having adequate training, who is aware
of the potential hazard!

KLP
KLP K05/0123 page 7
5.1.3 Safety Advice for Maintaining / Repairing
Do not carry out any maintenance / repairs if the armature / valve will be
under pressure.
Before disassembling of an armature or valve some essential points should be
clarified:
Will the armature/valve to be disassembled be replaced by another
immediately?
If appropriate, does the production process of the plant needed to be stopped?
Is it necessary to inform specific personnel about the disassembly?
If necessary, inform the shift foreman/ safety engineer or the manager about the
maintenance or repair without delay in order, for example, to avoid an outflow/
overflow of chemicals or a discharge of gases in good time by means of suitable
measures!
Observe that some valves / armatures are able to contain the pressured
medium e.g. the ball in the ball valve. You have to relieve the pressure in
the pipes in which the armature/valve is mounted.
Switch off pilot pressure and the power supply and relieve the pressure in the
pipes. If necessary, set up warning signs in order to prevent
the inadvertent starting up of the devices/machines/plants in which the
armature/valve is mounted
the switching on of pilot medium supply, pilot power supply and/or the power
supply of actuators and accessories.
In case of defect in the armature/valve contact the supplier.
If you ascertain a damage of the armature/valve, isolate the device from the
mains. Please observe the safety advices.
Do not mount, start or adjust the armature/valve if it would cause damage
to itself, the pipes or a mounted actuator.
After completing the maintenance or repair, check for correct functioning of the
armature/valve and the tightness of the pipe connections.
Also check the functioning of the accessories e.g. actuators, limit switches, etc.

KLP
page 8 KLP K05/0123
5.2 Device Safety
The armatures/valves
are quality products which are produced in accordance to the recognised
industrial regulations.
left the manufacturer’s work in a perfect safety condition.
In order to maintain this condition, as installer / user you must carry out
your task in accordance with the description in these instructions,
technically correctly and with the greatest possible precision.
We assume, as a trained specialist you are having mechanical and electrical
knowledge! Satisfy yourself that the armatures/vales will only be used within their
admissible limiting value (see the technical data).
The armatures/valves must be used only for purposes corresponding to
their design! The armatures/valves must be used within the values
specified in the technical data! The operating of the armature/valve outside
the nominal temperature range could destroy the sealings and the bearings.
The operating of the armatures/valves outside the nominal pressure range
could destroy the inner parts and the body.
Never remove a cap or any other component part if the
armature/valve is under pressure.
Do not mount, put into operation or adjust the armature/valve if pipes or a
mounted actuator are damaged.
After finishing the assembling and adjustments check for proper functioning of the
armature/valve and the tightness of the pipe connections.
Also check the functioning of the accessories e.g. actuators, limit switches, etc.

KLP
KLP K05/0123 page 9
6. Pneumatical Installation
The installation of the air supply has to be carried out with great
care. Especially the threaded connection, fittings and sealings
have to be clean and free of contaminates. Contamination, which
remains inside the actuator, will cause advanced wear or damage
to the sealings and treads.
The pneumatic actuator ED/EE is available in two operation variants:
function double-acting, or
function single-acting with spring return
Use only adequate hoses and hose connectors for your application.
While passing the hoses please ensure, that they will not be
creased, squeezed or sheared or that the hose will not be laid
over sharp edges. Also take care that there will be no pressure
or traction on the hose.
Pass the hoses to its Basic position, if so possible, within conduits or cable ducts.
As an alternative to the shown variant the control of the actuator could be carried
out by a directly mounted pilot valve.

KLP
page 10 KLP K05/0123
6.1 Function “Double-Acting“
Remove the protection caps from the ports “P1“ and “P2“.
Screw suitable pneumatic fittings (e.g. Art. C12xx or R12xx) into the ports “P1“
and “P2“ and tighten the fittings.
Insert a hose into the fitting at port “P1“ which will supply the actuator with
compressed air during the opening operation.
Insert a hose into the fitting at port “P2“ which will supply the actuator with
compressed air during the closing operation.
Tighten the hoses in the fittings at port “P1“and “P2“.
Check the tightness of all connections.

KLP
KLP K05/0123 page 11
6.2 Function “Single-Acting“
Remove the protection caps from the ports “P1“ and “P2“.
Screw a suitable pneumatic fitting (e.g. Art. C12xx or R12xx) into the port “P1“
by using a fit sealing compound and tighten the fitting.
Insert a hose into the fitting at port “P1“ which will supply the actuator with
compressed air during the opening operation.
Screw a throttle valve with silencer (e.g. Art. AX1000xx) into the port “P2“ by
using a sealing compound and tighten the throttle valve.
Tighten the hose in the fitting at port “P1“.
Check the tightness of all connections.
This completes the mounting and the pneumatical installation of the actuator.

KLP
page 12 KLP K05/0123
7. Pneumatical Disassembly
Turn the actuator with the slide/valve/flap into its fix position!
Switch off the compressed air supply and the control of the actuator!
If necessary, set up warning signs in order to prevent
the inadvertent starting up of the devices / machines / plants, or
the switching on of the power supply the controlling of the actuator.
Release the fittings and pull away the pipes.
Close the open air control pipes if they are not also being disassembled or not
immediately reconnected to another pneumatic actuator.
8. Operating
The butterfly valve will be opened or closed by using the actuator.
Do not clasp – under any circumstances – onto the actuating
element or insert any parts into the actuating element. Heavy
injuries or damages will be the consequence. If necessary,
install a protection device.

KLP
KLP K05/0123 page 13
9. Adjustments/Starting
9.1 Adjustments
The pneumatic actuator ED/EE will be precisely adjusted by the manufacturer
after mounting on a slide/valve/flap. Perhaps readjustment of the actuator may be
necessary after disassembling and mounting on a new slide/valve/flap.
Before you undertake adjustments on actuators which are installed in an
operational plant, find out whether feeding control leads with pressure (e. g. by
“OPEN“ or “CLOSE“ operation) will have influence on other actuators or whether
the closing/opening of limit switches (options) will affect functioning of other
devices.
Where appropriate, disconnect these pipes from the actuator to be adjusted!
Never clasp onto the actuation element and never insert anything
into the slide/valve/flap. Heavy injuries or damages will be the
consequence. Never adjust the adjusting screws against the
efficacy of the pressure.
Move the pistons of the actuator together by feeding the port “P2“ with
compressed air (only function double-acting), or exhausted port “P1“ (only
function single-acting).
Loosen the counter nuts (1) in both covers.
Turn one of the adjustment screws (2) into the cap (3), until the screw aligns
with the cap or the screw will be deeper by about max. 2 mm.
Separate the pistons by feeding the port P1 with compressed air.
Turn out the adjustment screw (2), until the rotation angel of 90° or the desired
rotation angle will be reached.
Tighten the adjustment screw of the second cover against the piston, until you
will feel the increase of the necessary torque moment.
Fix the adjustment screws by tightening the nuts (1). Ensure that the
adjustment screw will not turn.
Check the adjustment and if necessary, correct it.
At this point the adjustment of the pneumatic actuator is completed.

KLP
page 14 KLP K05/0123
9.2 Starting
Before starting the pneumatic actuator EE/ED, you have to read the safety
advice. If you have not read the safety advice until now read these
important precautions now and turn back to this page.
The starting of a pneumatic actuator which is mounted in a plant (e.g. in a
refinery or in a chemical plant) should only happen in accordance with:
the particularly specified instructions of the whole plant!
the adjustments described in section 9.1 Adjustments !
Switch on the power supply of the control unit.
Switch on the compressed air supply.
Actuate the pneumatic actuator via “control by hand” and check the correct
functioning of the actuator and the mounted slide/valve/flap.
Check all pipe connections for tightness.
Check all the control lines for tightness.
Check the functioning of the accessory units.

KLP
KLP K05/0123 page 15
10. Maintenance
Under normal operating conditions the pneumatic actuator EE/ED is maintenance
free.
Regularly check the tightness of the pneumatic actuator. In case of a defect in the
pneumatic actuator contact the supplier.
are the cover seals tight?
are the shaft seals on the top and on the bottom of the actuator tight?
are the hose fittings tight?
is the body or the cover cracked?
is the seal of the limit stop adjusting screw tight or did the counter nut became
loose?
If you determinate that there is damage to the actuator,
disconnect it from the power supply. However, before doing
this, it is essential to refer to the safety advice.
Depending on the environmental and operating conditions the replacement of
the sealings and guide rings may be necessary from approx. 500.000 up to
1.000.000 switching operations.
Appropriate spare part kits are available.

KLP
page 16 KLP K05/0123
11. Technical Information
Operating instructions, data sheet, approvals and further information via the QR
code on the device or via www.kobold.com
12. Order Codes
Operating instructions, data sheet, approvals and further information via the QR
code on the device or via www.kobold.com
13. Dimension
Operating instructions, data sheet, approvals and further information via the QR
code on the device or via www.kobold.com

KLP
KLP K05/0123 page 17
14. Disposal
Note!
Avoid environmental damage caused by media-contaminated parts
Dispose of the device and packaging in an environmentally friendly
manner
Comply with applicable national and international disposal regulations and
environmental regulations.
Batteries
Batteries containing pollutants are marked with a sign consisting of a crossed-out
garbage can and the chemical symbol (Cd, Hg, Li or Pb) of the heavy metal that
is decisive for the classification as containing pollutants:
Cd1 Hg2 Pb3 Li4
1. „Cd" stands for cadmium
2. „Hg" stands for mercury
3. „Pb" stands for lead
4. „Li" stands for lithium
Electrical and electronic equipment

KLP
page 18 KLP K05/0123
15. EC Declaration of Conformance
We, KOBOLD Messring GmbH, Hofheim-Ts, Germany, declare under our sole
responsibility that the product:
Butterfly Isolating Valves with Pneumatic Actuator Model: KLP-...
to which this declaration relates is in conformity with the standards noted below:
DIN EN 12516:2005
Industrial valves - Shell design strength
Also, the following EC guidelines are fulfilled:
2014/68/EU PED
2011/65/EU RoHS (category 9)
2015/863/EU Delegated Directive (RoHS III)
Additional for devices with solenoid valve:
2014/35/EU Low Voltage Directive
2014/30/EU EMC Directive
DIN EN ISO 12100:2011
Safety of machinery - General principles for design - Risk assessment and risk
reduction
DIN EN 60204-1:2014
Safety of machinery - Electrical equipment of machines - Part 1: General
requirements
Additional for devices with limit switch:
2014/35/EU Low Voltage Directive
DIN EN 61058-1:2008
Switches for appliances - Part 1: General requirements
Hofheim, 24 Oct. 2019
H. Peters M. Wenzel
General Manager Proxy Holder
Table of contents
Other Kobold Control Unit manuals
Popular Control Unit manuals by other brands
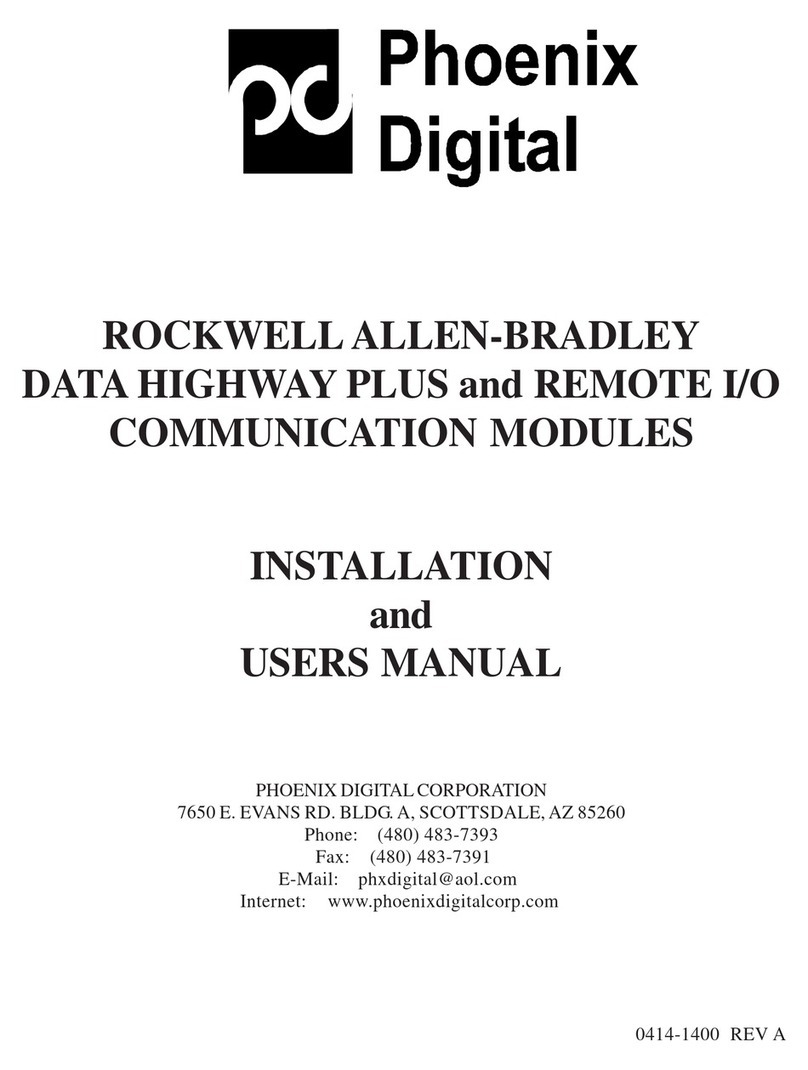
PHOENIX DIGITAL
PHOENIX DIGITAL OCM-DPR-1 Installation and user manual

ANTUMBRA
ANTUMBRA DIST Building instructions

Siemens
Siemens P1 BIM installation instructions
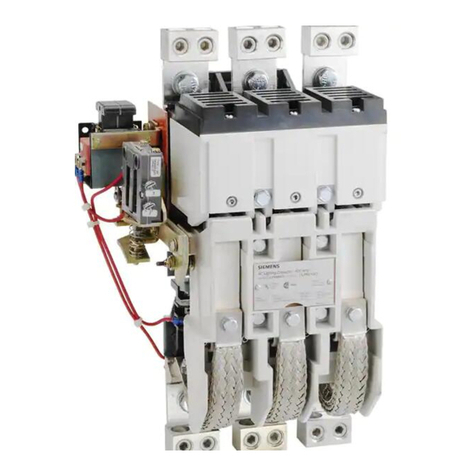
Siemens
Siemens CLM Series Instructions & installation
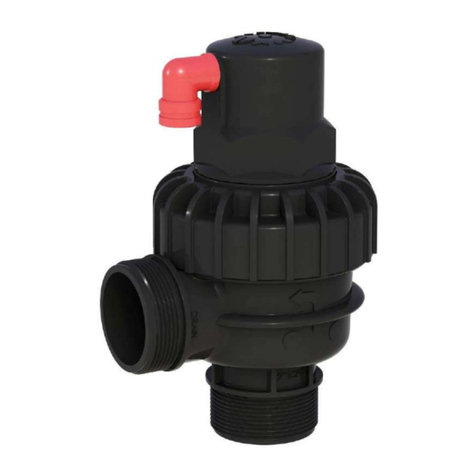
A.R.I.
A.R.I. D-070-P Installation operation & maintenance

Tempo Fitness
Tempo Fitness 521E instruction manual