Kobold DSV Series User manual

Operating Instruction
for
Float-Type Flow Meter
and Switch
Model: DSV-...

DSV
page 2 DSV K09/0322
1. Contents
1.Contents ........................................................................................................ 2
2.Note .............................................................................................................. 3
3.Instrument Inspection .................................................................................... 3
4.Regulation Use ............................................................................................. 4
5.Operating Principles ...................................................................................... 5
6.Mechanical Connection ................................................................................. 6
7.Electrical Connection .................................................................................... 7
7.1.DSV-2... and DSV-3 ........................................................................... 7
7.2.Note for reed switch ........................................................................... 7
7.3.Examples of contact protection devices ............................................. 7
8.Use in hazardous area .................................................................................. 8
8.1.Statement an apparatus not containing an own potential ignition
source ................................................................................................ 8
8.1.ATEX reed contact 41R57** .............................................................. 9
9.Commissioning............................................................................................ 16
10.Maintenance ............................................................................................... 17
11.Technical Information .................................................................................. 18
12.Order Codes ............................................................................................... 19
13.Recommended Spare Parts ........................................................................ 20
14.Dimensions ................................................................................................. 21
15.EU Declaration of Conformance (DSV) ....................................................... 22
16.UK Declaration of Conformity (DSV) ........................................................... 23
17.EU Declaration of Conformance (Reed contact 41R57**) ........................... 24
18.Statement of conformity reed contact 41R57** ........................................... 25
Manufactured and sold by:
Kobold Messring GmbH
Nordring 22-24
D-65719 Hofheim
Tel.: +49(0)6192-2990
Fax: +49(0)6192-23398
E-Mail: [email protected]
Internet: www.kobold.com

DSV
DSV K09/0322 page 3
2. Note
Please read these operating instructions before unpacking and putting the unit
into operation. Follow the instructions precisely as described herein.
The instruction manuals on our website www.kobold.com are always for currently
manufactured version of our products. Due to technical changes, the instruction
manuals available online may not always correspond to the product version you
have purchased. If you need an instruction manual that corresponds to the
purchased product version, you can request it from us free of charge by email
([email protected]) in PDF format, specifying the relevant invoice number and
serial number. If you wish, the operating instructions can also be sent to you by
post in paper form against an applicable postage fee.
The devices are only to be used, maintained and serviced by persons familiar
with these operating instructions and in accordance with local regulations
applying to Health & Safety and prevention of accidents.
When used in machines, the measuring unit should be used only when the
machines fulfil the EC-machine guidelines.
as per PED 2014/68/EU
In acc. with Article 4 Paragraph (3), "Sound Engineering Practice", of the
PED 2014/68/EU no CE mark.
Table 8, Pipe, Group 1 dangerous fluids
3. Instrument Inspection
Instruments are inspected before shipping and sent out in perfect condition.
Should damage to a device be visible, we recommend a thorough inspection of
the delivery packaging. In case of damage, please inform your parcel service /
forwarding agent immediately, since they are responsible for damages during
transit.
Scope of delivery:
The standard delivery includes:
Float-Type Flow Meter / Switch model: DSV

DSV
page 4 DSV K09/0322
4. Regulation Use
The model DSV is employed for the measurement and monitoring of liquid flows
which are homogeneous, free from impurities and have a low viscosity. In
addition, they must be compatible with the materials used in fabrication of these
units. High viscosity media can introduce considerable measurement errors. Also,
large dust particles can block the float, resulting in error-messages and erroneous
measurements. In addition, ferrite particles that may deposit on the embedded
magnets of the float can trigger the same effect. To overcome this problem, the
installation of a magnetic filter is recommended.
The units are provided as follows:
Flow measurement
The reading of the present media flow takes place on site. The top edge of the
float indicates the flow directly in l/min (water) on the scale attached to the
graduated measuring glass.
Limit-contacts (only with model DSV-2... and DSV-3...)
To monitor the flow values, the units are provided with one or two adjustable limit-
contact(s).
Standard version: Normally Open function (with increasing flow)
Special version: Change-over contact function
The switch contact is adjustable over most of the measuring range of the device,
under consideration of the switch hysteresis.

DSV
DSV K09/0322 page 5
5. Operating Principles
The proven KOBOLD flow meters and switches
model DSV are based on the principle of the
well-known float-type flow meters except for the
conventional tapering measuring tube.
These patented instruments are provided
instead with a cylindrical flow tube with conical
slots around the periphery. This eliminates the
usual problems of guiding the cylindrical float
within a tapering measuring glass. The novel
design including the provision of an
appropriately dimensioned annular gap of
constant width between the float and the flow
tube has enabled the sensitivity to dirt to be
considerably reduced.
The float contains a permanent magnet which
actuates a bistable reed contact external to the
flow circuit, that is, the flowing medium is
hermetically separated from the electrical
contact. In addition, it is embedded in a height-
adjustable switch housing thus ensuring that
the contact is protected even in an aggressive
atmosphere.
As the medium enters the instrument the float
rises. Once its magnetic field reaches the
contact tips of the reed switch the contact
closes. As the flow increases the float rises
further until it reaches its stop. This prevents
the float from going beyond the contact range
of the magnetic operating tube, that is, the
contact remains closed thus ensuring bistable
switching. The top edge of the float serves to
indicate the flow on the measuring glass in
L/min.
Flow

DSV
page 6 DSV K09/0322
6. Mechanical Connection
Before installation:
Make sure that the permitted max. operating pressure and temperature limits
are not exceeded (see section 11. Technical Information)
Remove all transport safety locks and ensure that no remains of packing
material reside inside the unit.
The sealing of union fittings is carried out through Teflon tape or similar
material.
During installation of these devices, attention must be paid that no large
course or pressure-load is exercised on the union fittings. We recommend
fastening the inlet and outlet line at approx. 50 mm distance mechanically,
from the union fittings.
The units may not be installed at a location within an inductive field.
Attention! The union fittings of these devices must be held
fixed by means of a suitable wrench while screwing in.
Otherwise, stresses will transfer to the housing which may
lead to the destruction of graduated measuring glass.
If possible, it should be checked after mechanical installation whether the
connections between union fittings and pipes are properly sealed
Attention! While installing in a free and open environment,
please pay attention to the fact that the freezing of medium
can destroy the measuring tube.

DSV
DSV K09/0322 page 7
7. Electrical Connection
7.1. DSV-2... and DSV-3
Make sure that the electrical supply wires are powerless.
Undo the locking screw on the plug cap and remove the plug
from the socket.
Mount supply line in the plug cap as shown in the wiring
diagram.
If the contact has not been adjusted, adjust it now. (see
section 9. Commissioning).
Place the plug on the socket and fasten it with the safety-
screws. (see section 9. Commissioning).
7.2. Note for reed switch
Attention! Every single specified electrical value for the sealed
contact should not be exceeded even for short periods. We
recommend contact protection relays or other contact protection
device for higher switching values.
When the external devices have been connected to the limit contact and the
switch point has been set, the electrical connection is complete.
The instrument can now be placed into operation.
7.3. Examples of contact protection devices
For capacitive and inductive loads, (long leads and relays/contactors) we
recommend contact protection relays or the following suppressor circuits.

DSV
page 8 DSV K09/0322
8. Use in hazardous area
8.1. Statement an apparatus not containing an own potential
ignition source

DSV
DSV K09/0322 page 9
8.1. ATEX reed contact 41R57**
ATEX N/O contact 41R57
II 3G Ex ic IIC T4 Gc
II 3 D Ex ic IIIC T125 °C Dc
-20 °C ≤Ta≤80 °C
max. 250 VAC/DC/1.5 A/100 W/100 VA
ATEX changeover contact 41R57U
II 3G Ex ic IIC T4 Gc
II 3 D Ex ic IIIC T125 °C Dc
-20 °C ≤Ta≤80 °C
max. 250 VAC/DC/1 A/30 W/60 VA

DSV
page 10 DSV K09/0322
Ex-relevant excerpt of the operating instructions of the reed contact
41R57 **
1. Preambel
This excerpt of the operating instructions only represents the ex-relevant aspects.
It is copied into the original operating manual in the same or analogous form;
Textual changes are permitted; the ex-relevant statements remain.
To ensure the function and for your own safety, please read the enclosed
operating instructions carefully before you begin the installation. If you have any
questions, please contact the KOBOLD Messring GmbH, Hofheim. It applies with
the original operating instructions.
The following standard issues were considered in the evaluation of the product:
a) IEC 60079-0:2017 Ed. 7 / EN 60079-0:2018 Explosive atmospheres –
Part 0: Equipment - General requirements
b) IEC 60079-11:2011 Ed. 6 + Corr. 2012 / EN 60079-11:2012 Explosive
atmospheres - Part 11: Equipment protection by intrinsic safety "i"
2. General information on explosion protection
The reed switches work together with various KOBOLD products and serve there
for monitoring. It is available as N/O contact or changeover contact.
The electrical connection is made via a plug - only in intrinsically safe systems.
The reed switch is intended for commercial use and may only be used in
accordance with the specifications in the technical documentation of Kobold and
the information on the nameplate. It is only operated together with certified
products via an intrinsically safe circuit. They comply with the valid standards and
regulations.
The installation regulations (e.g. EN 60079-14) for systems in potentially
explosive atmospheres must be observed.
Further important details can be found in the corresponding EC-type examination
certificate.
Permitted use
• The intrinsically safe reed switch can be used as follows:
• In Zone 2 (Gas-Ex, EPL Gc) in explosion groups IIA, IIB and IIC
• In Zone 22 (Dust-Ex, EPL Dc) in explosion groups IIIA, IIIB and IIIC
• The requirements for simple electrical equipment for use in intrinsically safe
circuits in zones 1/21 are fulfilled.
• The qualification regarding the surface temperature is T4. For all gases, vapors,
mists with an ignition temperature> 135 ° C the equipment is not an ignition
source.
• In the dust Ex area, 125 ° C is the reference temperature for further
consideration regarding the safety distance from the smoldering temperature.
• The ambient temperature range is -20 ° C ≤ Ta ≤ 80 ° C.

DSV
DSV K09/0322 page 11
2.1. Electrical characteristics for Ex i
Electrical data:
• Rated voltage up to 45 volt AC / DC
• Rated current up to 2 A
• UiIC ≤ 30 V AC / DC, IiIIC ≤ 250 mA
• UiIIB ≤ 45 V AC / DC, IiIB ≤ 2 A
• UiIIIC ≤ 45 V AC / DC, IiIIIC ≤ 250 mA
• Li = negligible, Ci = negligible
• Heating on the outer housing <15 K
2.2 Type code
The equipment is identified by the following type code:
Type Description Item-No. Remarks
41R57 A B
T
y
pe codin
g
41R57 Contact device
A
N/O contact
(
2 wires
)
, Plu
g
with black cap
Change-over contact (3 wires), Plug with grey
cap
B 70
–
75 with markin
g
(
not ex-relevant
)
202.289 N/O
45
–
50 with markin
g
202.285 N/O
50
–
55 with markin
g
202.286 N/O
60 – 65 with marking 202.287 N/O
70
–
75 with markin
g
202.288 Chan
g
e-over
60
–
65 chan
g
e-over contact
202.290 Chan
g
e-over
2.3 Temperature class
The reed switch is suitable for temperature class T4 / T125 ° C.
2.4 General requirements
2.4.1 Intended Use
a) To ensure safe operation, the products may only be used according to the
instructions in the assembly instructions. During use, the legal and safety
regulations required for the respective application must be observed in
addition. This applies analogously when using accessories.
b) Failure to comply with the instructions given in this excerpt or in the case of
improper handling of the product will render our liability null and void. In
addition, the warranty on products and spare parts is void.
c) The products are not safety elements in terms of their intended use.
d) Only original parts of the manufacturer may be used.

DSV
page 12 DSV K09/0322
2.4.2 General safety instructions
The reed switch corresponds to the state of the art and is reliable. The reed
switch may pose a residual hazard if improperly used and operated by untrained
personnel.
Every person, responsible for the installation, commissioning, maintenance or
repair of the reed switch, must have read and understood the assembly
instructions and in particular the safety instructions.
a) Follow the general rules of technology for the selection and proper
operation of a product.
b) All connected electrical and mechanical equipment must be suitable for
the respective application.
c) Observe the notes in these operating instructions as well as the
conditions of use and permissible data that appear from the imprints /
nameplates of the respective products.
d) It must be ensured that only product protection types corresponding to
the zones are installed!
e) The product is only approved for proper and intended use in a normal
industrial atmosphere. Immersion in liquids is not permitted.
f) It must be ensured that no falling objects can hit the product.
g) The operator must ensure the lightning protection for the entire system in
accordance with local regulations.
h) It is the responsibility of the installer to ensure that the function of the
reed switch in conjunction with the individual evaluation devices functions
properly and is approved for the intended use.
i) The intrinsically safe connection - including the reed switches - must be
made via approved / tested evaluation devices, which may need to be
equipped with suitable zener barriers or switching amplifiers.
3. Commissioning, installation
Depending on the IP degree of protection, the time for cleaning the equipment
(dust deposits) must be specified. Other important facts:
a) The product may be put into operation in Zone 2 (Cat. 3G, EPL Gc)
or in Zone 22 (Cat. 3D, EPL Dc in intrinsically safe circuits only by
specialists with a qualification similar to a qualified person according
to TRBS 1203.
b) The requirements for simple electrical equipment that apply to the
hazardous area of Zones 1/21 according to EN 60079-11 are
fulfilled.
c) The products may only be used in the usual industrial atmosphere.
In the presence of aggressive substances in the air, the
manufacturer must always be consulted. The products must be
adequately protected in adverse environmental conditions.
d) Operation of the product is only permitted in fully assembled and
undamaged enclosures. In case of possible damage, a zone
carryover may have to be considered by the operator; Moreover,
operation of the housing is not permitted if the housing is damaged.
e) The environmental conditions specified in the operating instructions
must be adhered to and protected against adverse environmental
conditions.

DSV
DSV K09/0322 page 13
f) Heat radiation from foreign products / components must also be
considered.
g) The reed switch must be protected against inadmissible access of
liquids and / or soiling.
h) Fixed parts (e.g. due to frost or corrosion) must not be loosened by
force in the presence of an explosive atmosphere. Icing must
therefore be avoided.
i) The reed switch may only be subjected to minor vibrations, see also
IEC 34-14.
j) To ensure the discharge of electrostatic charges, the national
requirements must be considered.
k) In particular, isolated capacities must be prevented.
l) Only those zener barriers or switching amplifiers may be used
whose output circuits are approved / tested for use in potentially
explosive atmospheres. In Europe, use in Zones 1/21 requires an
EC type-examination certificate for the equipment concerned issued
by a body designated for explosion protection.
m) The voltage of the supply units must be less than or equal to the
voltage Ui of the reed switch.
n) The total current Io of the supply units must be less than or equal to
the current Ii of the reed switch.
o) For the installation of the intrinsically safe circuit, a control drawing
(system description) to be created by the installer / operator is
required.
p) Equipotential bonding must be established along the intrinsically
safe circuit when using a grounded supply.
q) The certificates must be taken into account, including the special
conditions specified therein.
r) Resistant parts of the product (e.g. due to frost or corrosion) must
not be forcibly loosened in the presence of an explosive
atmosphere.
s) Within the potentially explosive area, installation may only be
carried out taking into account the locally applicable installation
regulations. The following conditions must be observed
(incomplete):
t) Installation and maintenance may only be carried out in an
explosion-free atmosphere and in compliance with the regulations in
force in the country of the operator.
u) Additional precautions must be taken if the presence of hydrogen
sulphide, ethylene oxide and / or carbon monoxide is to be
expected: these substances have very low ignition energy!
v) In the presence of these substances and in the presence of a
substance of the explosion group IIC and in the case of presumably
existing potentially explosive atmosphere, only spark-free tools may
be used!

DSV
page 14 DSV K09/0322
4. Maintenance, servicing
Definition of terms according to IEC 60079-17:
Maintenance and Repair: A combination of all activities performed to maintain or
recover an item in a condition that meets the requirements of the specification in
question and ensures the performance of the required functions.
Inspection: An activity involving the careful examination of an object, with the
aim of obtaining a reliable statement of the condition of the object, carried out
without disassembly or, if necessary, with partial disassembly, supplemented by
measures such as measurements becomes.
Visual inspection: A visual inspection is a test that detects visible faults, such as
missing screws, without the use of access devices or tools.
Close-up Test: A test that identifies, in addition to the aspects of visual
inspection, such errors, such as loose screws, which can only be obtained by
using access devices, such as a screwdriver, e.g. steps (if necessary), and tools
are visible. For close-up tests, housing usually does not need to be opened or the
equipment must be de-energized.
Detail test: A test that detects, in addition to the aspects of close-up testing, such
defects as, for example, loose connections that can only be recognized by
opening housings and / or, if necessary, using tools and test equipment.
a) Maintenance measures may only be carried out by qualified persons.
b) Only use accessories in potentially explosive atmospheres that comply
with all requirements of European directives and national legislation.
c) Maintenance measures with dismantling of the reed switch may only be
carried out in an ex-free atmosphere.
d) The replacement of components may only be carried out with original
spare parts, which are also approved for use in potentially explosive areas.
e) The products must be regularly maintained and cleaned in the Ex area.
The intervals are set by the operator according to the environmental
demands on site.

DSV
DSV K09/0322 page 15
Activity
visual
inspection per
month
Close
inspection
every 6
months
detailed
inspection
every
12 months
1
Visual inspection of the reed
switch for damage, remove
dust deposits
●
2 Check for integrity and
function ●
3 Testing the entire system The responsibility of the operator
5. Troubleshooting
Products operated in conjunction with potentially explosive atmospheres must not
be modified. Repairs to the product may only be performed by specially trained
and authorized personnel.
6. Disposal
Disposal of the packaging and used parts must be in accordance with the
regulations of the country in which the product is installed.
7. Marking of the reed switch (nameplate)
In the serial number the year of manufacture can be coded; optionally, it can also
be specified as plain text.
As a rule, a readable marking has been made for the type of explosion protection
required in field use - even before the product is put into operation for the first
time.
A reed switch that has already been operated in non-intrinsically safe circuits may
no longer be used in intrinsically safe circuits later on.

DSV
page 16 DSV K09/0322
9. Commissioning
Application in machines, according to guidelines 89/392/EWG, the commissioning
of these units is barred until it is determined that the machine is in agreement with
the designations of guidelines.
Adjustment of limit-values
Loosen both safety screws on the contact base clown, with the
help of a screwdriver.
Dislocate the contact base down until it reaches the stop.
Remove the plug-cap after loosening the safety screws.
Connect with PIN 1 + 2 (change-over contact PIN 2 + 3) with a
suitable circuit test unit.
Attention! Sudden opening of the flow supply line can lead to
pressure peaks, which repeatedly exceed the operating pressure
(water hammer!) This can lead to the breakage of the measuring
glass.
Case 1: Device in circuit Case 2: Device outside circuit
Open the supply line. Raise the float with a suitable tool,
Let the medium flow slowly, until the until the top edge of the float shows
top edge of the float shows the flow the desired flow volume of desired
volume of desired switching point. switching point.
The reed contact is now closed (electrically closed-circuit).
Move the switch-housing upwards, until the reed-contact is just open (no
electrical passage). The contact is now adjusted for decreasing flow. If the
contact needs to be adjusted for increasing flow, it must be relocated now
around the hysteresis about 3-5 mm downwards.
Adjust the safety screws in this position by tightening them. Install the plug-
cap. The unit is ready for operation.
On correct adjustment of the limit-contact it has a bistable switching behaviour;
i.e. upon exceeding the adjusted limit, the contact remains closed and below
the adjusted limit, the contact stays open.

DSV
DSV K09/0322 page 17
Hysteresis
Hysteresis reflects the difference between switch-on and switch-off points of a
contact. Through standard tuning of the float magnet and reed contact power
(AW number) a hysteresis of about 3-5 mm float stroke is achieved. Thereby,
ensuring that the contact exhibits bistable behaviour.
Exceeding the measuring range
Attention! Continuously exceeding the measuring range,
especially with pulsating flow and the resulting contact of the
float to the limit-pin, can lead to increase wear and damage to
the unit. In such a case, please consult your supplier.
Non-pulsating flow can essentially exceed the measuring range, merely resulting
in a notable increase in pressure-loss.
(The maximum operational pressure is not to be exceeded.)
10. Maintenance
In the event that the medium to be measured is free from impurities, the model
DSV is almost maintenance free. If lime or other deposits on the measuring glass
or within interior parts develop, the units should be cleaned on a regular basis.
After removing the upper grub-screw, the screw joint can be withdrawn from the
unit, and the inner parts can be extracted for cleaning. The measuring glass can
be cleaned with the help of a suitable brush. After cleaning, the unit must be
reassembled in the correct sequence.

DSV
page 18 DSV K09/0322
11. Technical Information
Housing: Aluminium anodised (not wetted)
Connections: DSV-x1..: Brass MS 58, nickel-plated
DSV-x2..: St. Steel 1.4301
Float: see section 122. Order Codes
Orifice: DSV-x1..: Brass MS 58, nickel-plated
DSV-x2..: St. Steel 1.3955
Measuring glass: Borosilicate glass
Sealing rings: DSV-x1..: NBR
DSV-x2..: FPM
Max. temperature: 100 °C (Metal-float)
70 °C (PP or PVDF float)
Max. pressure: 10 bar
Accuracy: ± 4% (F.S.)
Mounting position: vertical, flow from bottom to top
Contacts (DSV-2..., DSV-3...)
Electrical connection: Connector DIN 175301-803
Electrical switching values:
N/O contact (standard) max. 250 VAC/DC / 1,5 A / 100 W / 100 VA
Changeover contact (standard) max. 250 VAC/DC / 1 A / 30 W / 60 VA
N/O contact and
Changeover contact (cCSAus) max. 230 VDC / 0,26 A / 60 W,
60 VDC / 1 A / 60 W,
max. 240 VAC / 0,42 A / 100 W,
100VAC / 1 A / 100 W
Use in hazardous areas
Mechanics: The apparatus can be used as follows in
explosive atmospheres in accordance with the
applicable erection regulations on machines,
devices and plants, such as e.g. EN 1127-1,
EN 60079-14 etc.:
a) In Zone 1 (gas hazard, category IIG) in the
explosion groups IIA, IIB and IIC
b) In Zone 2 (gas hazard, category IIIG) in the
explosion groups IIA, IIB and IIC
c) In Zone 21 (dust hazard, category IID) in the
explosion groups IIIA and IIIB
d) In Zone 22 (dust hazard, category IIID) in the
explosion groups IIIA and IIIB

DSV
DSV K09/0322 page 19
ATEX N/O contact 41R57
...G0 and GG: II 3 G Ex ic IIC T4 Gc
II 3 D Ex ic IIIC T125 °C Dc
-20 °C ≤Ta≤80 °C
max. 250 VAC/DC/1.5 A/100 W/100 VA
ATEX changeover contact 41R57U
...H0 and HH: II 3 G Ex ic IIC T4 Gc
II 3 D Ex ic IIIC T125 °C Dc
-20 °C ≤Ta≤80 °C
max. 250 VAC/DC/1 A/30 W/60 VA
Hysteresis: approx. 3.5 mm float movement
Protection: IP 65 (electr. contact)
IP 54 (side indicator)
12. Order Codes
Example: (DSV-2101H R0 R08)
Flow meter model: DSV-1...
Measuring
range
L/min.
wate
r
Pressure
loss
Δ P (bar)
Float according
to version
Brass
Stainless
steel
Contact
Connection
Brass St. steel
0.25...1.25 0.04 PP PVDF DSV-1101H... DSV-1201H...
...00..= without contacts
..R08= G 1/4
..R15= G 1/2
..N08= 1/4 NPT
..N15= 1/2 NPT
0.5...2.5 0.06 PP PVDF DSV-1102H... DSV-1202H...
1...4.5 0.04 PP PVDF DSV-1103H... DSV-1203H...
1...10 0.04 PP PVDF DSV-1104H... DSV-1204H... ..R15= G 1/2
..R20= G 3/4
..N15= 1/2 NPT
..N20= 3/4 NPT
2...18 0.07 Brass,
nickel-pl. 1.4301 DSV-1105H... DSV-1205H...
2...25 0.08 PP PVDF DSV-1106H... DSV-1206H... ..R20= G 3/4
..R25= G 1
..N20= 3/4 NPT
..N25= 1 NPT
2.5...50 0.14 Brass,
nickel-pl. 1.4301 DSV-1107H... DSV-1207H...
10...100 0.3 Brass,
nickel-pl. 1.4301 DSV-1108H... DSV-1208H... ..R25= G 1 ..N25= 1 NPT
10...130 0.4 PP PVDF DSV-1109H... DSV-1209H... ..R32= G 1 1/4 ..N32= 1 1/4 NPT
Flow meters and switches with 1 contact model: DSV-2...
Measuring
range
L/min.
wate
r
Pressure
loss
Δ P (bar)
Float according
to version
Brass
Stainless
steel
Contact
Connection
Brass St. steel
0.25...1.25 0.04 PP PVDF DSV-2101H... DSV-2201H... ...R0...= 1 N/O contacts
...U0...= 1 changeover
contact
...C0...= 1 N/O contact
(cCSAus)
...D0...= 1 changeover
contact
(cCSAus)
...G0...= 1 ATEX N/O
contact
(model 41R57)
...H0...= 1 ATEX
changeover c.
(model
41R57U)
..R08= G 1/4
..R15= G 1/2
..N08= 1/4 NPT
..N15= 1/2 NPT
0.5...2.5 0.06 PP PVDF DSV-2102H... DSV-2202H...
1...4.5 0.04 PP PVDF DSV-2103H... DSV-2203H...
1...10 0.04 PP PVDF DSV-2104H... DSV-2204H... ..R15= G 1/2
..R20= G 3/4
..N15= 1/2 NPT
..N20= 3/4 NPT
2...18 0.07 Brass,
nickel-pl. 1.4301 DSV-2105H... DSV-2205H...
2...25 0.08 PP PVDF DSV-2106H... DSV-2206H... ..R20= G 3/4
..R25= G 1
..N20= 3/4 NPT
..N25= 1 NPT
2.5...50 0.14 Brass,
nickel-pl. 1.4301 DSV-2107H... DSV-2207H...
10...100 0.3 Brass,
nickel-pl. 1.4301 DSV-2108H... DSV-2208H... ..R25= G 1 ..N25= 1 NPT
10...130 0.4 PP PVDF DSV-2109H... DSV-2209H... ..R32= G 1 1/4 ..N32= 1 1/4 NPT

DSV
page 20 DSV K09/0322
Flow meters and switches with 2 contacts model: DSV-3...
Measuring
range
L/min.
wate
r
Pressure
loss
Δ P (bar)
Float according
to version
Brass
Stainless
steel
Contact
Connection
Brass St. steel
0.25...1.25 0.04 PP PVDF DSV-3101H... DSV-3201H... ...RR...= 2 N/O contacts
...UU...= 2 changeover
contacts
...CC...= 2 N/O contacts
(cCSAus)
...DD...= 2 changeover
contacts
(cCSAus)
...GG...= 2 ATEX N/O
contact
(model 41R57)
...HH...= 2 ATEX
changeover c.
(model
41R57U)
..R08= G 1/4
..R15= G 1/2
..N08= 1/4 NPT
..N15= 1/2 NPT
0.5...2.5 0.06 PP PVDF DSV-3102H... DSV-3202H...
1...4.5 0.04 PP PVDF DSV-3103H... DSV-3203H...
1...10 0.04 PP PVDF DSV-3104H... DSV-3204H... ..R15= G 1/2
..R20= G 3/4
..N15= 1/2 NPT
..N20= 3/4 NPT
2...18 0.07 Brass,
nickel-pl. 1.4301 DSV-3105H... DSV-3205H...
2...25 0.08 PP PVDF DSV-3106H... DSV-3206H... ..R20= G 3/4
..R25= G 1
..N20= 3/4 NPT
..N25= 1 NPT
2.5...50 0.14 Brass,
nickel-pl. 1.4301 DSV-3107H... DSV-3207H...
10...100 0.3 Brass,
nickel-pl. 1.4301 DSV-3108H... DSV-3208H... ..R25= G 1 ..N25= 1 NPT
10...130 0.4 PP PVDF DSV-3109H... DSV-3209H... ..R32= G 1 1/4 ..N32= 1 1/4 NPT
13. Recommended Spare Parts
Only the unit-parts and materials will be listed. Corresponding to the model
version, parts in different sizes are available.
(Please ensure you mention the model version, when ordering spare parts).
1.1) Float Brass 3.1) O-Ring NBR
1.2) Float Polypropylene 3.2) O-Ring FPM
1.3) Float St. Steel 4.1) Contact (N/O function) (CSA)
1.4) Float PVDF 4.2) Contact (changeover function) (CSA)
2.1) Slotted nozzle Brass 4.3) N/O (UL)
2.2) Slotted nozzle St. Steel 4.4) Changeover (UL)
5.1) Meas. glass with scale
This manual suits for next models
3
Table of contents
Other Kobold Measuring Instrument manuals
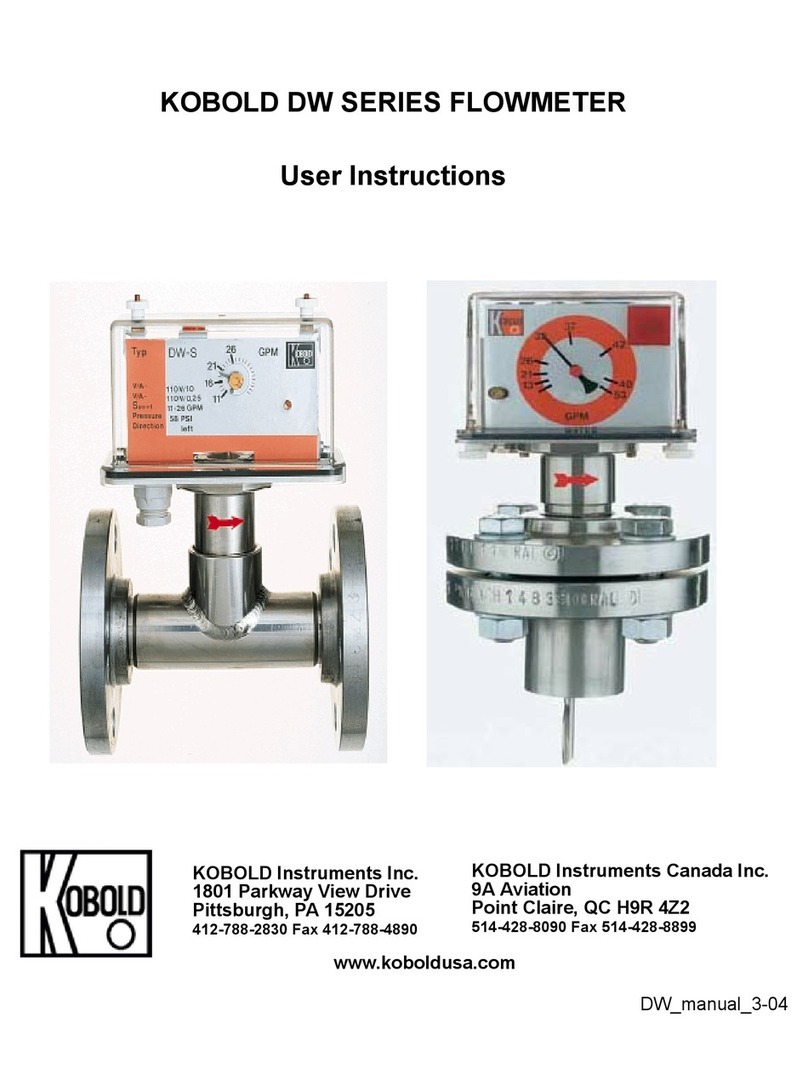
Kobold
Kobold DW Series User manual

Kobold
Kobold OVZ 1 Series User manual
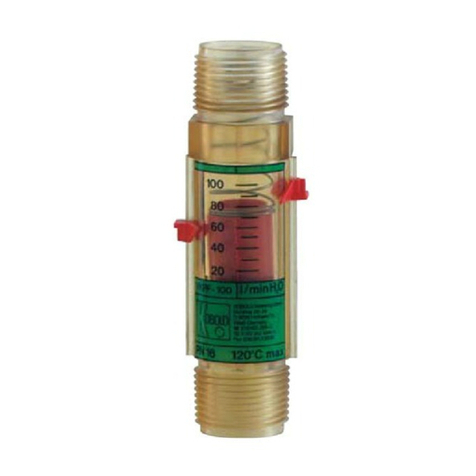
Kobold
Kobold VKP-1020 Series User manual
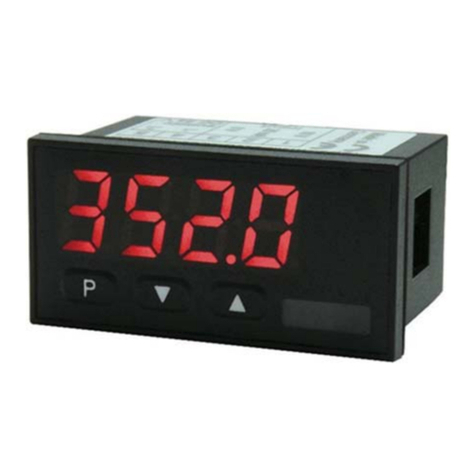
Kobold
Kobold DAG-M12 User manual
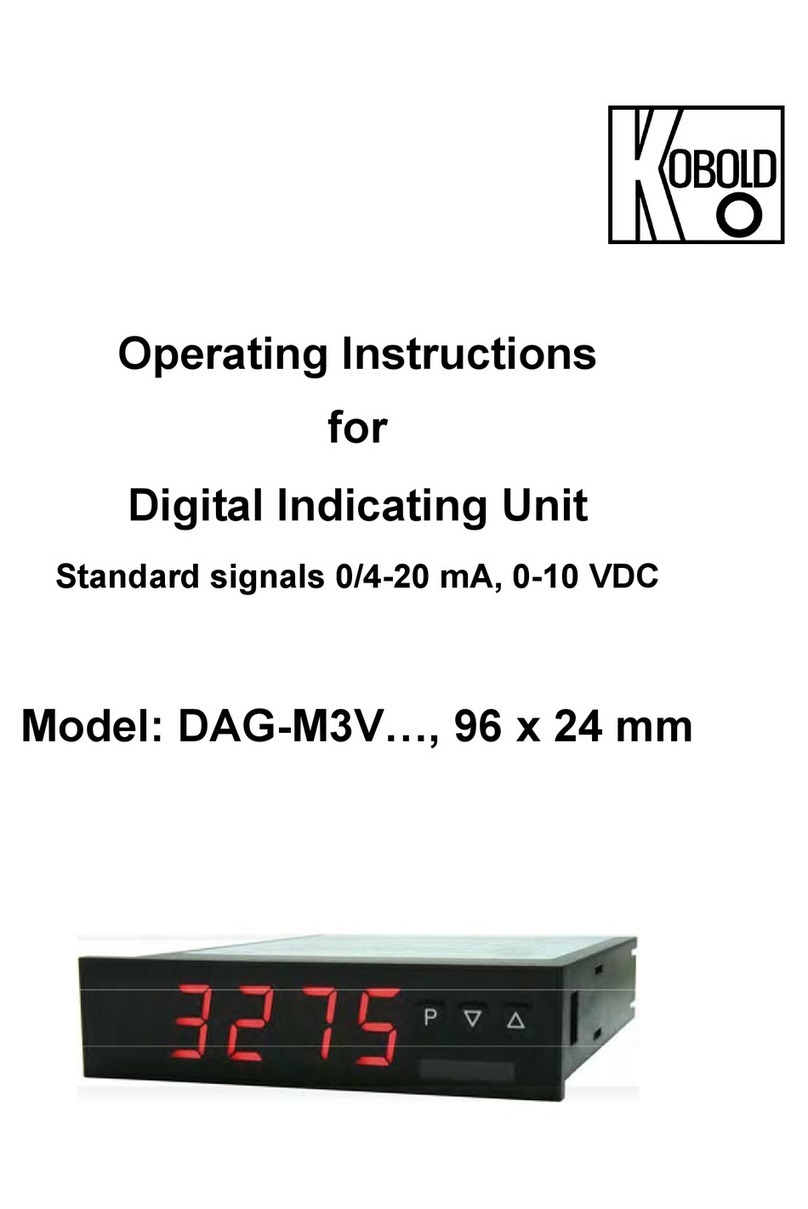
Kobold
Kobold DAG-M3V Series User manual
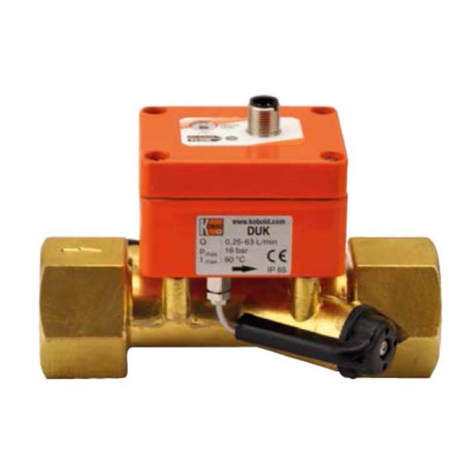
Kobold
Kobold DUK User manual

Kobold
Kobold DRS 0 Series User manual
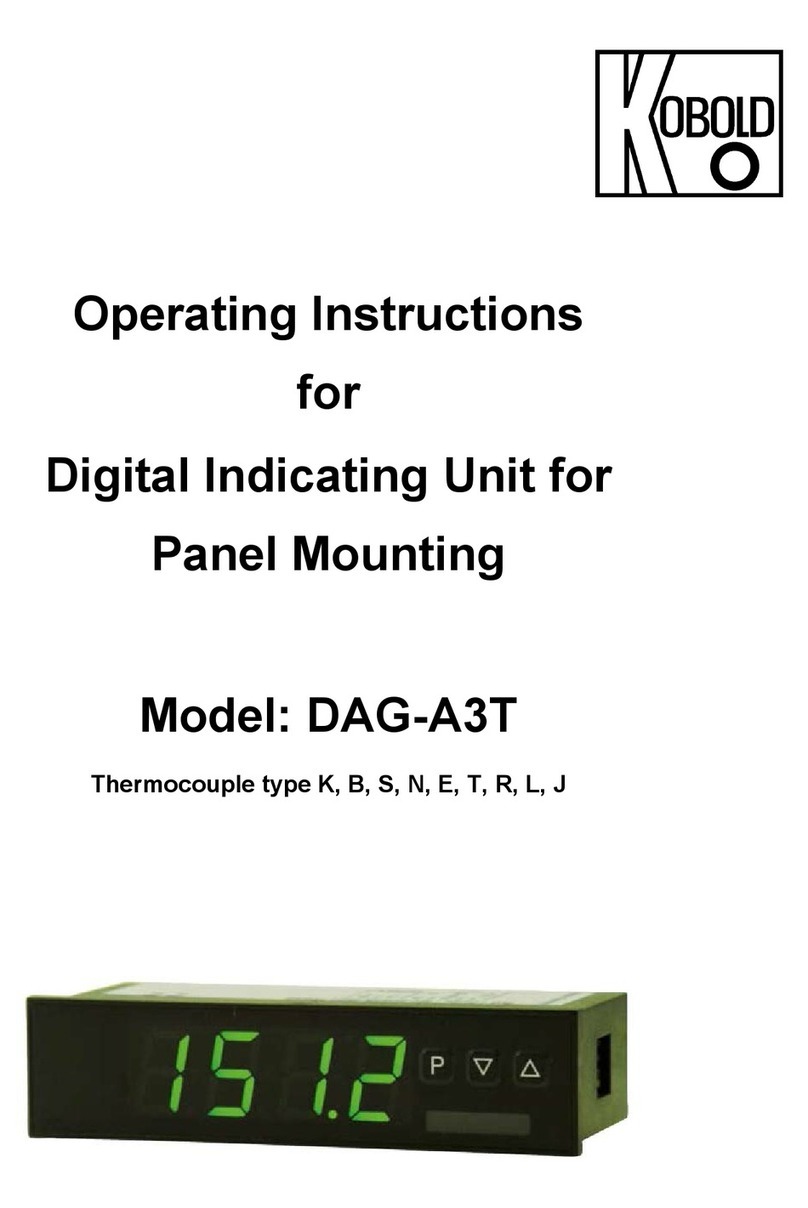
Kobold
Kobold DAG-A3T User manual
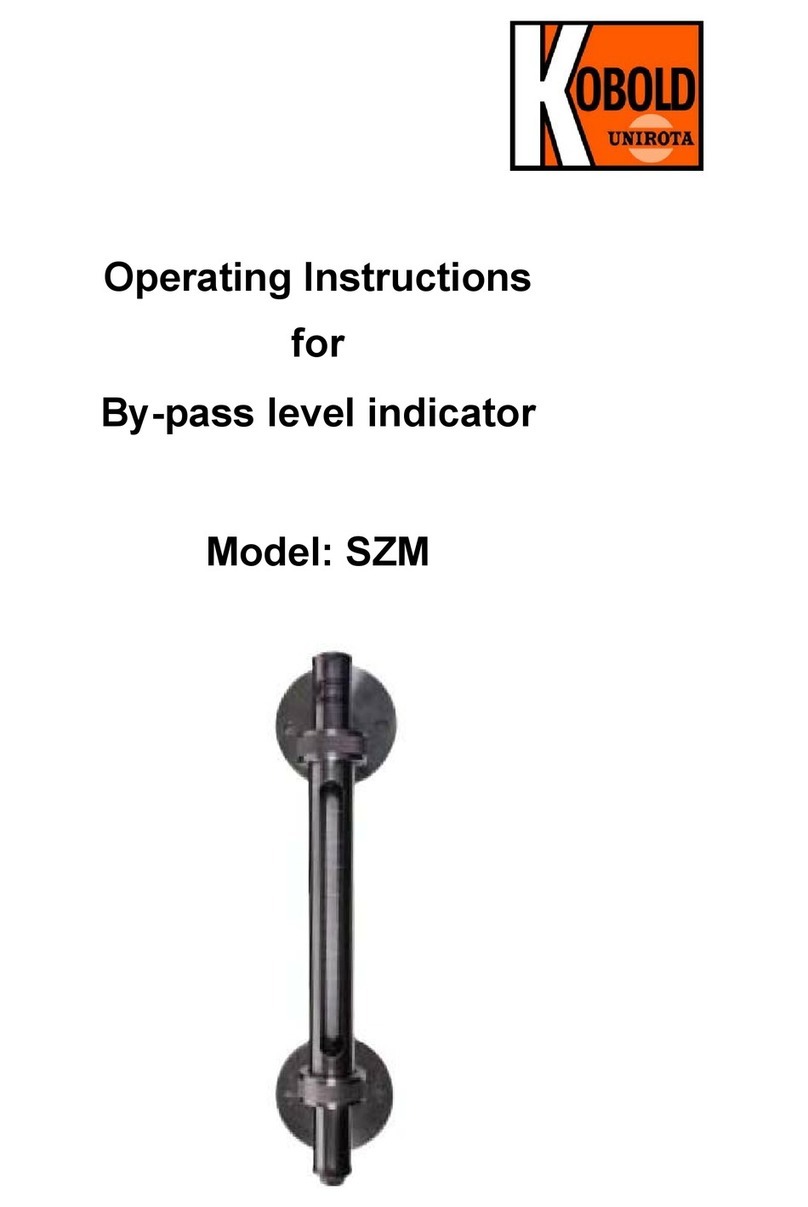
Kobold
Kobold SZM User manual
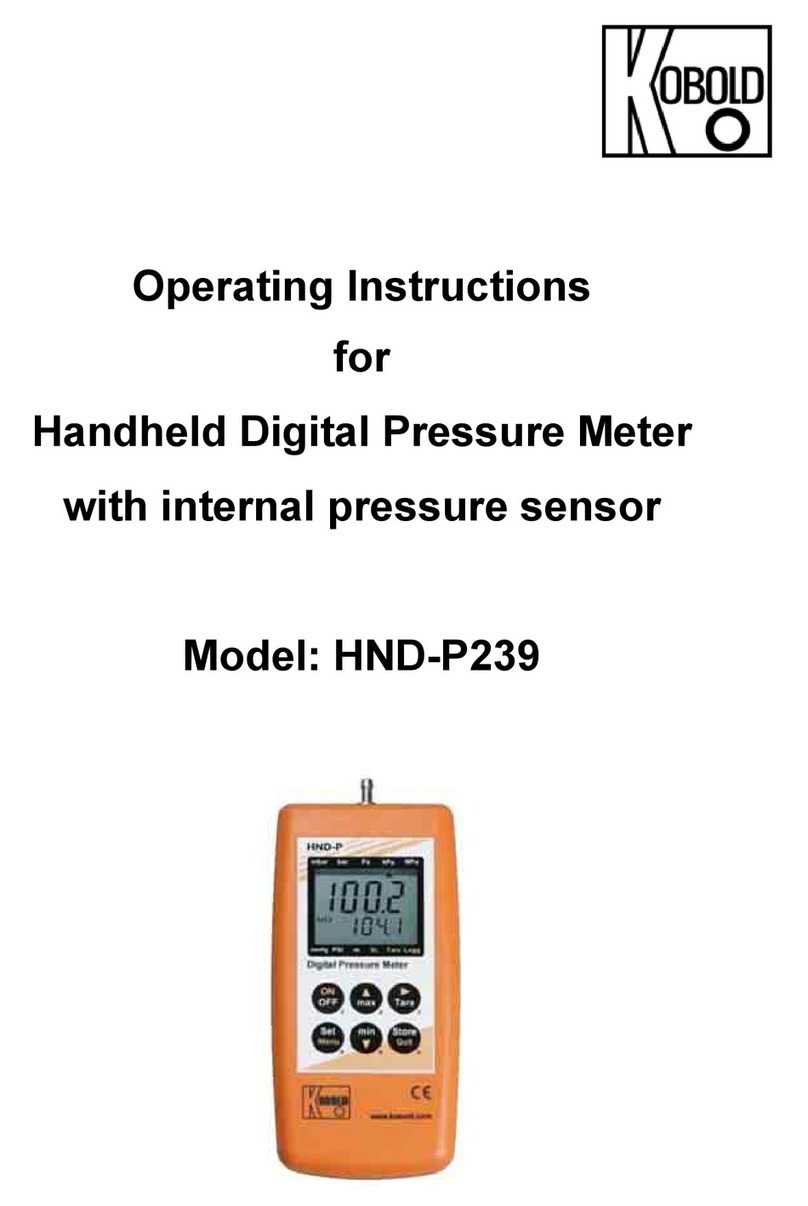
Kobold
Kobold HND-P239 User manual
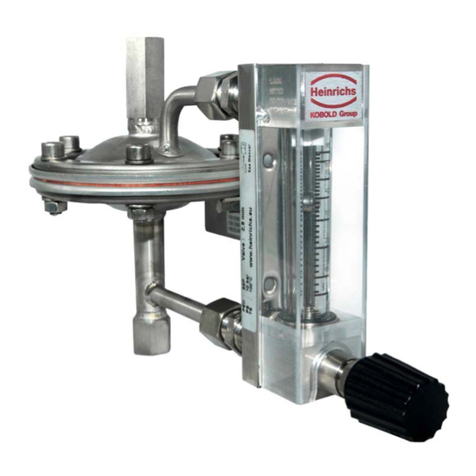
Kobold
Kobold KDF-9 User manual
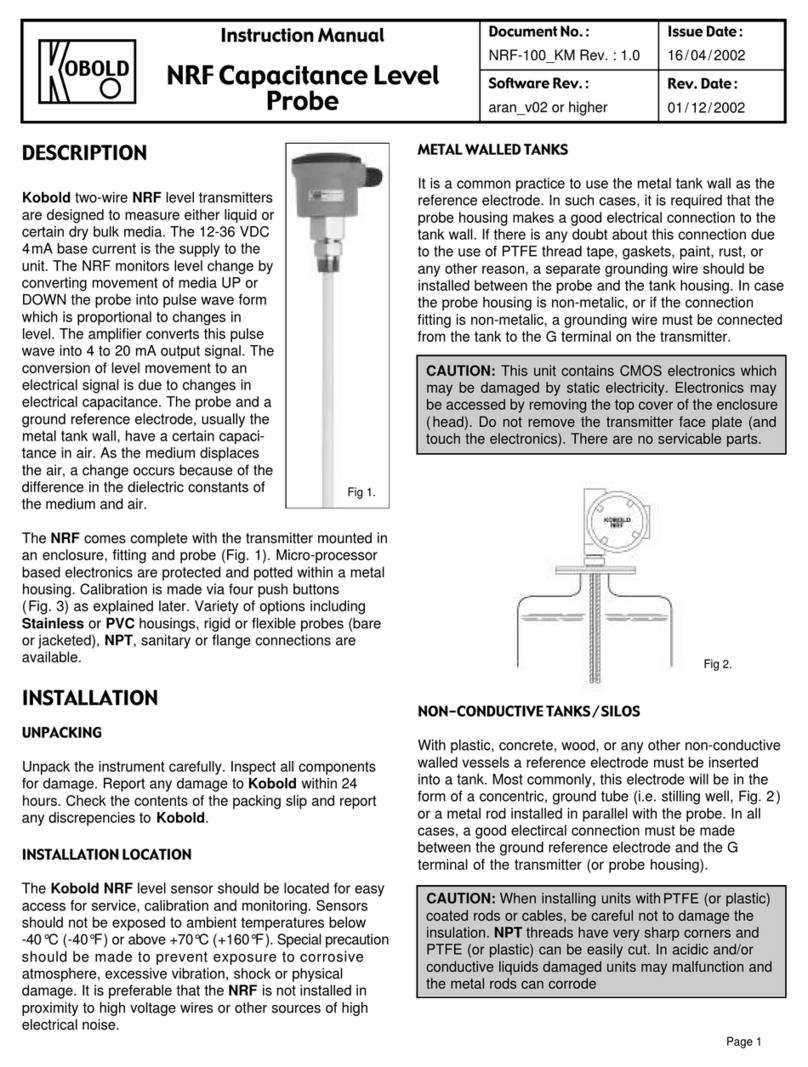
Kobold
Kobold NRF User manual
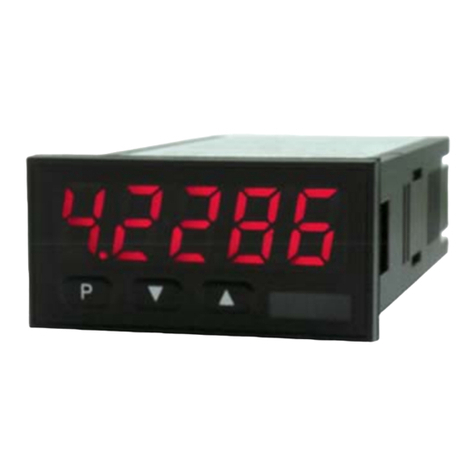
Kobold
Kobold DAG-M1F User manual
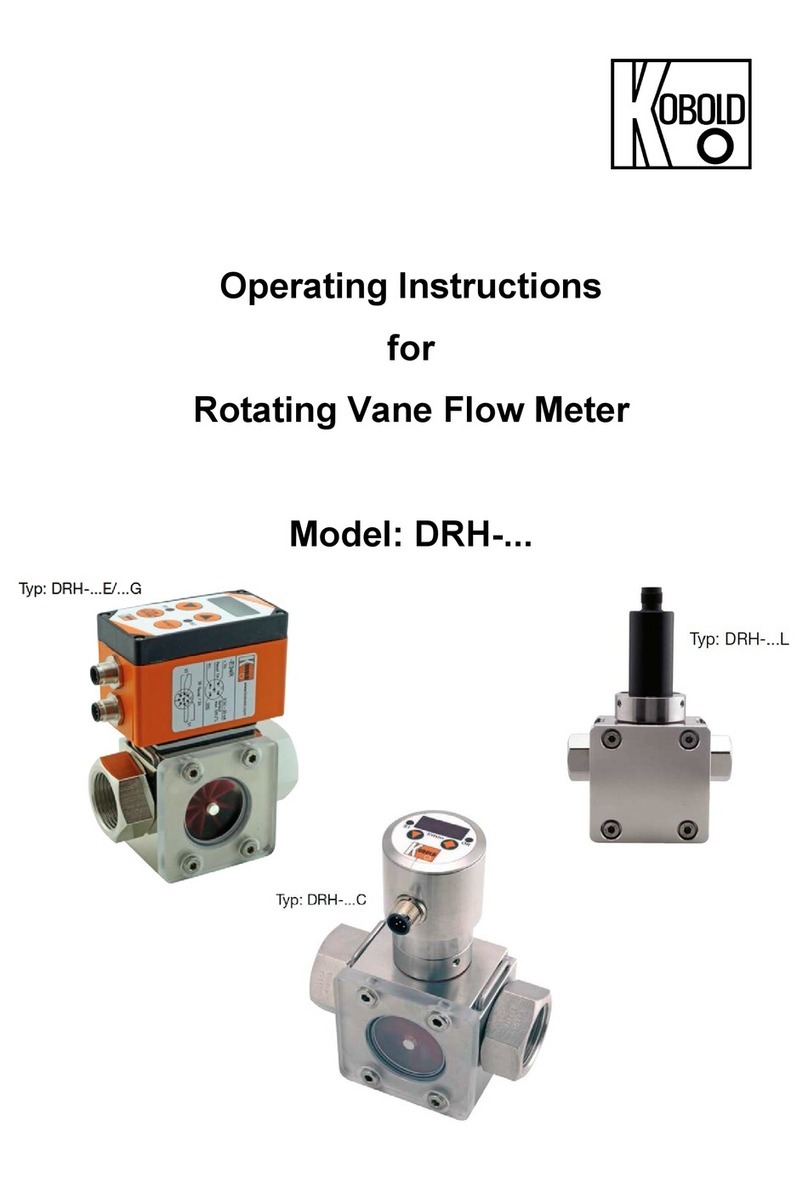
Kobold
Kobold DRH Series User manual
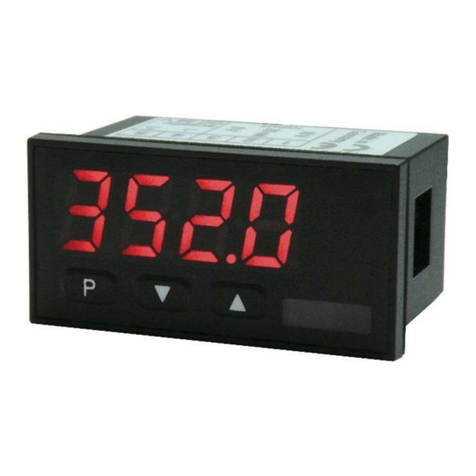
Kobold
Kobold DAG-A1V User manual
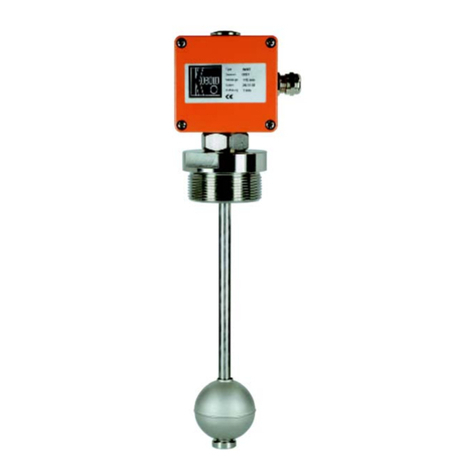
Kobold
Kobold NMT User manual
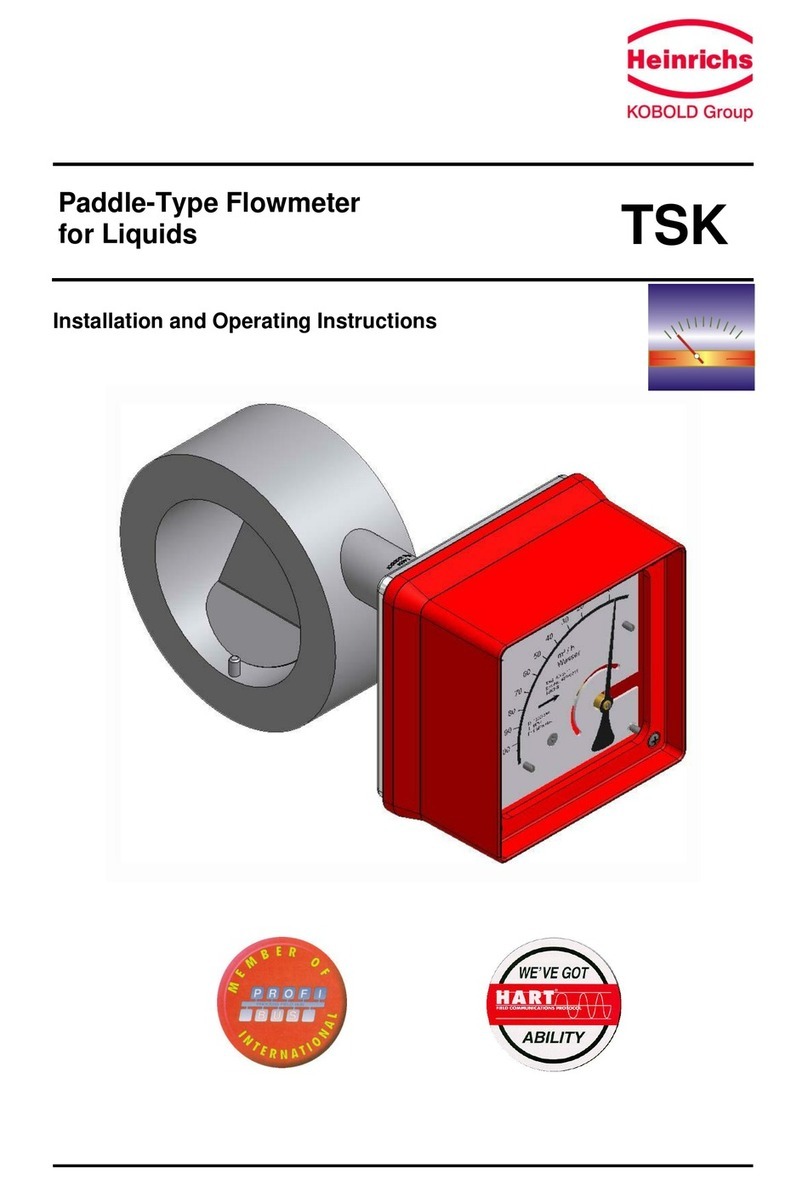
Kobold
Kobold Heinrichs TSK User manual
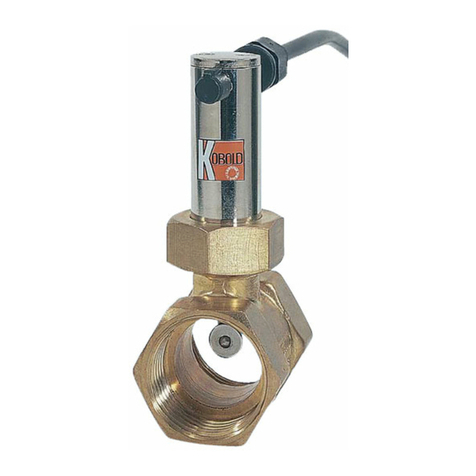
Kobold
Kobold PSR series User manual
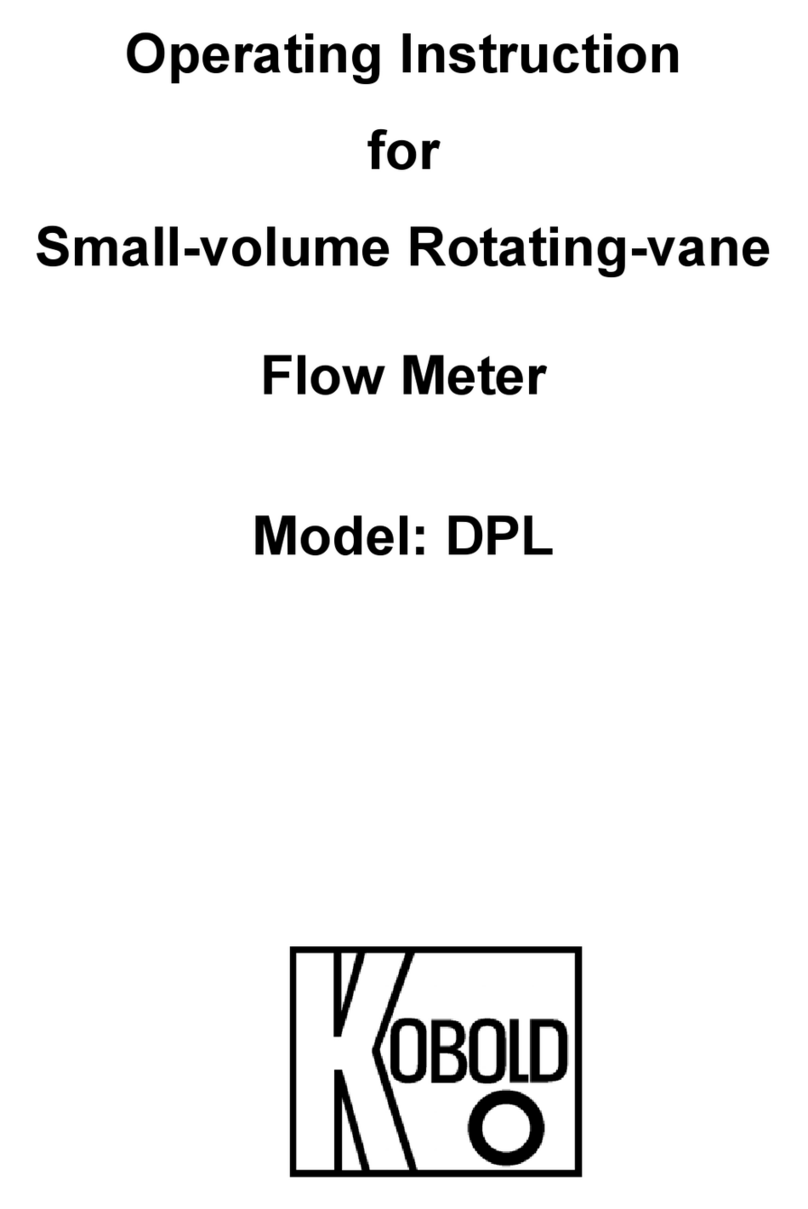
Kobold
Kobold DPL User manual

Kobold
Kobold DOG-4 User manual