Kondo KXR-R4LL User manual

RoverLongLegType
KXR-R4LL Assembly
Manual
ServiceDept.
KONDOKAGAKUCo.,Ltd.
SupportInformation
www.kondo-robot.com
Ver.1.0© 2017 Kondo Kagaku Co., Ltd.

2
Table of Contents
Work with sufficient space in a physically and emotionally alert and observant state.
There is danger of death or serious injury by unexpected accidents.
Keep all parts away from small children. Small parts can cause injury.
Disconnect the battery connector immediately if any thing abnormal occurs.
*Damage in the robots body. *Foreign objects in the robots body. *Smoke. *Odd smell. *Abnormal heat or warmth. Continued use under such conditions
can result in fire or electric shock. *Should any abnormalities be observed, immediately stop using the product and contact our service section.
Disconnect the power plug from electrical outlets when the charger is not being used.
When plugged to an outlet, a small amount of electricity flows into.
During operation, always exercise caution and be prepared for unforeseen accidents.
Please always remember that due to the nature of this product as an assembly kit, safety is not guaranteed for the movements
resulting from the operation of the product. Please take extra precautions since an injury of the fingertips and fracture of bones
may result when movements of the product greatly differ from what you expect.
Recognize the possibility that components can short circuit.
Short circuit can easily occur since control board terminals are bare. Short circuits can cause thebattery,
components, and wiring materials to ignite. Incorrect wiring can also result in similardanger.
Do not break the charger and cable.
Do not damage, modify, bring in close contact with thermal appliances, or use under forced pressure. Continuous use under such conditions can result in fire or
electric shock. *For repair of cords and cables, please contact our service section. *If the product becomes wet, please consult our service section.
Do not disassemble or modify the servo or board of the finished product.
Disassembly and repair, other than those stated in this Instruction, is prohibited. Incorrect disassembly or assembly can cause
malfunctions, fire and/or electric shock. *In case of any malfunction, please contact our service section.
Do not allow the product to become wet or use under high humidity and conditions where dew condensation occurs.
Such conditions may result in malfunction since this product is composed of electronic parts. Such conditions can
also result in electric shock and fire by electrical shorting.
For overseas use, local approval or license may be needed. Please check.
In certain areas or countries, legal procedures may be necessary prior to using the product. *Our support does not
apply to the use of this product outside of Japan.
When detaching the charger and battery, firmly hold the connectors.
Detachment by holding the cord may cause breaking of wires and a possible short circuit, which can result in electric shock or fire.
Do not operate on an unstable work surface.
The product can lose balance and collapse or fall off causing injury.
The battery included with this product is a nickel-metal hydride
battery. To protect valuable environmental resources, used batter-
ies should be recycled, not disposed of as trash.
This sign indicates that "there is imminent danger of death or severe injury."
This sign indicates that "there is a possibility of death or severe injury."
This sign indicates that "there is a possibility of injury or material damage".
Prohibited
Prohibited
Prohibited
Mandatory
Mandatory
■ Safety Precautions 3
■ Preface 4
■ Prior to Assembly 5
●List of Parts Used 5
●Accessories 8
●Servo Motors 10
●Screw Handling 11
●Frame Parts 12
●Servo ID and Position 14
■ Robot Assembly 15
●Full Robot Assembly Procedures 15
●Servo ID Setting 16
●Body Assembly 21
●Leg and Wheel Assembly 29
●Attaching All Parts 32
■ Robot Operations 38
●Battery Mounting 38
●Connecting with PC 39
●Trim Adjustment 42
●Running Sample Motions 49
●Reduced Voltage Motion Settings 55
■ Options 56
●Option Parts List 56
●Option Mounting Examples 58

3
Safety Precautions
Work with sufficient space in a physically and emotionally alert and observant state.
There is danger of death or serious injury by unexpected accidents.
Keep all parts away from small children. Small parts can cause injury.
Disconnect the battery connector immediately if any thing abnormal occurs.
*Damage in the robots body. *Foreign objects in the robots body. *Smoke. *Odd smell. *Abnormal heat or warmth. Continued use under such conditions
can result in fire or electric shock. *Should any abnormalities be observed, immediately stop using the product and contact our service section.
Disconnect the power plug from electrical outlets when the charger is not being used.
When plugged to an outlet, a small amount of electricity flows into.
During operation, always exercise caution and be prepared for unforeseen accidents.
Please always remember that due to the nature of this product as an assembly kit, safety is not guaranteed for the movements
resulting from the operation of the product. Please take extra precautions since an injury of the fingertips and fracture of bones
may result when movements of the product greatly differ from what you expect.
Recognize the possibility that components can short circuit.
Short circuit can easily occur since control board terminals are bare. Short circuits can cause thebattery,
components, and wiring materials to ignite. Incorrect wiring can also result in similardanger.
Do not break the charger and cable.
Do not damage, modify, bring in close contact with thermal appliances, or use under forced pressure. Continuous use under such conditions can result in fire or
electric shock. *For repair of cords and cables, please contact our service section. *If the product becomes wet, please consult our service section.
Do not disassemble or modify the servo or board of the finished product.
Disassembly and repair, other than those stated in this Instruction, is prohibited. Incorrect disassembly or assembly can cause
malfunctions, fire and/or electric shock. *In case of any malfunction, please contact our service section.
Do not allow the product to become wet or use under high humidity and conditions where dew condensation occurs.
Such conditions may result in malfunction since this product is composed of electronic parts. Such conditions can
also result in electric shock and fire by electrical shorting.
For overseas use, local approval or license may be needed. Please check.
In certain areas or countries, legal procedures may be necessary prior to using the product. *Our support does not
apply to the use of this product outside of Japan.
When detaching the charger and battery, firmly hold the connectors.
Detachment by holding the cord may cause breaking of wires and a possible short circuit, which can result in electric shock or fire.
Do not operate on an unstable work surface.
The product can lose balance and collapse or fall off causing injury.
The battery included with this product is a nickel-metal hydride
battery. To protect valuable environmental resources, used batter-
ies should be recycled, not disposed of as trash.
This sign indicates that "there is imminent danger of death or severe injury."
This sign indicates that "there is a possibility of death or severe injury."
This sign indicates that "there is a possibility of injury or material damage".
Prohibited
Prohibited
Prohibited
Mandatory
Mandatory
Due to the nature of this product as an assembly kit, consequences, damage, or injury
resulting from the use of this product are the user's responsibility. Please use this
product with that in mind. In order to prevent danger to the user and others, as well as
property damages, the safety precautions listed below must be followed.

4
Preface
Thank you for purchasing the KXR robot assembly kit.
The KXR system enables you to create various robots by combining frame parts
with servo motors as a part of the structure. The basic format is provided as a set,
and sample motions are also included, so you can conrm the robot's operations
as soon as it is assembled. Servos and main frame part components are sold as
options, so it is easy to add robots in various formats and also expand the original
robot. If parts wear out or break you can replance only those you need, so repairs
can also be performed inexpensively.
Before beginning to assemble the robot, please closely read through this manual
and the accessory manuals. You may want to print out the manuals to make them
easier to read and reference.
This product is constructed for people of all ages to enjoy a bipedal robot. However, this product is not a toy, and
contains parts and tasks that would be dicult for young children to understand or perform. For those parts and
tasks, parents or teachers should provide assistance.
Please keep in mind that due to the nature of this product as an assembly kit, the motion of the assembled product
cannot be guaranteed. Further, due to the fact that the movements of the assembled product depend in large
part on the method by which it was assembled, we may not be able to provide precise answers to your questions
regarding operations.
The assembly and operation of this product requires the use of a personal computer (Windows Vista or 7,8,8.1,10)
with a USB port. It is assumed that the user has basic computer skills. Please note that we cannot provide
answers to general questions or inquiries regarding computers or Windows.
1
2
3
Caution
The following items are required for the assembly and operation of this product:
●Personal computer
●Tools
Preparation
●#0 and #1 screwdriver
#0 #1
●Small blade
●Nippers
for cutting parts and board cover
●Tape
●Screw locking adhesive
(moderate strength)
convenient for preventing screws and nuts
from loosening.
●All company names, trade names, and logo marks that appear in this Instruction are trade marks or registered trade
marks of each respective company.
●The contents of this Instruction and product are subject to change without notice for improvement or other reasons.
OS: Windows Vista, 7, 8, 8.1, 10
CD-ROM drive(for installation) 1 or more USB 2.0 port(s)
※ Microsoft. NET Frame work 2.0 is required

5
AB
CD
x8
x4
x4
Wheel60 Tire60
No.02320
No.02320
WheelSpacer
No.02320
No.02303
No.02303
No.02306
x4
x4
x4
銘板シール
x8
No.02157
x12 x16
x4
x12
ExampleofIDsticker
application
First,SettingServoIDs.
■FrameParts
*There may be more parts included in the set than the number used.
*No. xxxxx is the option part number. Use this number for searches and inquiries.
No.03115
No.03116(6pcs)
KRS-3301ICS
■Servo
JointBase
CableGuideX
Armsupporter
3300A
UpperArm3300-20
BottomArm3300-20
JointNut
No.02300 No.02301
No.02314
SmallDiameter
HornB
No.02319
No.02316
No.02315
x4 x8
x2x8 x4
*Thistypeusesthespacer2.
No.02315 No.02315
FlatFrame
Armsupporter
3300B
SupporterB
Spacer
SupporterB
Spacer2
BottomSpacer
3300
Prior to Assembly
List of Parts Used (1)
KXR-R4LL

6
EF
G
No.02312 No.02312
No.02313
No.02313 No.02313
No.02313
No.02311
x1 x1
x2
x4 x2 x2
x1
BodyPanel LockRing
BTBoxPlate
BTSidePlate BTHatch
BackPackCover BackPackBase
■FrameParts
*There may be more parts included in the set than the number used.
*No. xxxxx is the option part number. Use this number for searches and inquiries.
Prior to Assembly
List of Parts Used (2)
KXR-R4LL

7
M3 ー 12
No.03120
RCB-4mini
No.03141
ACAdapter(6V2A)
No.02186
LVConversionDCJack
x1 x1
No.02332
No.02330 x8
x4
ZH 接続ケーブル 2A タイプ
x1
x1 x1
x1
■Cable/Screw
No.02177
No.02166
LowHeadScrew LowHeadScrew LowHeadScrew LowHeadScrew
BHScrew
LowHead
HornScrew
LowHead
HornScrew
LowHead
HornScrew
FlatHeadScrew
No.02334
ZHConversionCable
SerialExtensionCable
LVPowerSource
SwitchHarness
No.02116
DualUSBAdapterHS
Length=120mm
Length=200mm
●Decal(forKXR)●CD-ROM●KitGuidance
Length=100mm
Length=1.5m
■Board/ACAdapter
■Accessories
#0#1
(BindHead)
*There may be more parts included in the set than the number used.
*No. xxxxx is the option part number. Use this number for searches and inquiries.
No.02325 No.02326 No.02324
No.02086 No.02164 No.02176 No.02083
M2ー4 M2ー6 M2ー8 M2.6 ー 10 2.6 ー 4 M3ー6 M3ー8
x18 x10 x4x24 x32x52
No.02327
M2 ー 12
x4 x4x16
Prior to Assembly
List of Parts Used (3)
KXR-R4LL

8
KRS-3300SeriesServo
RCB-4miniControlBoard
●Spec
*For part names, refer to the following page.
●Spec
*Computer software is used to operate the robot’s motions.
*For details, refer to the “Heart to Heart4 User’s Manual.”
Servo motors are integrated with gears for raising the output torque and a control board that enables stopping at any angle.
Using servo motors in the robot’s joints makes it easy to send angle commands to the joints and enables multiple motors to be
accurately controlled at the same time. The KRS-3301 ICS servo used in this kit employs half-duplex serial communication, so
operating commands can be sent simultaneously to multiple servos, and this allows cables to be wired using the multi-drop/dai-
sy-chain method (method for connecting servos like a chain of beads). This reduces the number of cables connected to the
control board to make possible a simpler, cleaner layout. You can also easily upgrade to the higher-grade KRS-3304 ICS for
more powerful operating performance.
The RCB-4mini control board used in this kit has a total of six ports, three
SIO (serial) ports for each of two systems of ICS3.0/3.5/3.6 compliant
devices, and can connect up to 36 ICS3.0/3.5/3.6 devices.
There are also five AD (analog) ports, so gyro/acceleration and other analog
sensors can be used.
High-speed, high-capacity EEPROM has been adopted to make it possible
to run multiple, varied motions."
■Size: 35 x 30 x 12 (mm)
■Weight: 7.6 g
■Interface: SIO port x6
AD port x5
COM port x1
(ZH Connecter)
■Proper Voltage: DC 6.0–12.0V
Main Features *For details, refer to the KRS Servo manual.
●Servo characteristics settings can be changed using the ICS manager ●Supports high-speed communications up to 1.25 Mbps
●As a dedicated robot servo, can be mounted using dual axial support ● Compact cubic design
●The higher-grade model is the same shape, so you can easily upgrade for more power
■Size: 32.5 x 26 x 26 (mm) ■Maximum operating angle: 270° ■Proper Voltage: DC 6.0–7.4V
■Weight: 26.4g
■Torque: 6.0kg-cm (7.4V)
■Speed: 0.14s/60° (7.4V)
■Communication standards: ICS3.6
■Gear material: Plastic
KRS-3301 ICS KRS-3304 ICS
■Weight: 33.7g
■Torque: 13.9kg-cm (7.4V)
■Speed: 0.13s/60° (7.4V)
■Communication standards: ICS3.5
■Gear material: Metal
Prior to Assembly
Accessories

9
Prior to Assembly
Accessories
Battery/Charger
*Always refer to the battery and charger manuals before use.
*The included battery and charger differ with the set.
● Remove the battery from the robot when not in use.
If you store or transport the robot with the battery connected and the switch is accidentally turned on, the
servos may be damaged and smoke or fire may result. Always remove the battery when the robot is not in use.
Readthebelowcontentbeforeusingthebattery.
Make sure to charge the battery before assembly and before operation.
▼The following cautions apply when using an Li-Fe battery.
Do not use the included USB charger (BX-31LF/BX-32MH) from the USB port of a computer.
When charging use a commercially available AC adaptor (1-2A) that supports USB.
●Donotuseatlowvoltage.Becarefulofoverdischarging.
Whenbatteriesareusedforalongperiodofthetime,thecapacitymayreduceandvoltagemaydrop.The
sameoccurswithLi‐Fe.Usinga6.6vratedbatteryatlowerthan6.0v(*)maydamagethebattery
causingittoswell.Thisisknownasoverdischarging.Continueduseinthisstatemayresultinfire.
*3.0vfor1cell.
●Donotuseifthebatteryisswollen.
Swellingisasignthatthebatterymustnotbeusedanylonger.Disposeofthebatteryinaccordancewith
thelawsandrulesinyourregion.
Shortingtheterminalscausesdamagetothebattery,whichintheworstcasemayresultinthebatteryemitting
smokeorfire.Holdtheterminalsfirmlywhendisconnectingthebattery.Donotpullonthecables.Nevertryto
modifythegenuineconnectors.Continuedusemayresultintheframeorpartsbecomingscratched,andtheouter
insulationofwiresmaybecomesplit.Checkthewiresperiodicallytoensureashortcircuitdoesnotoccur.
Iftheinteriorofthebatteryisexposed,gasmayleakandignite.Whenusingthebattery,besuretocheckthatthe
outercoveringisundamaged,thatthebatteryisfittedsecurelyintherobotbody,andthatitcannotbedamaged
byimpactduetofalling,etc.beforeturningtheswitchon.Ifthebatteryappearsdamagedduetoimpactorifit
appearsunusualinanyway,donotuseorrechargeit.
Repeatedusemayresultinthewireinsulationbecomingdamagedandsplit.Pullingwiresacrosstheframeburring
orallowingthebatterytofall,etc.withthewiresexposedmaycausedamagetothewires.Checkthewires
periodically,aswiresexposedthroughsmallgapsintheinsulationmayresultinshorting.
Carryingthebatteryaroundinabag,etc.uncoveredmayresultinmetallicobjectscomingintocontactwiththe
batterycausingashortoutordamagingthebatteryresultinginashortout.Furthermore,storinginthewrong
locationsmayresultinitemsfallingonthebatteryorwaterbeingsplashedonthebatteryresultinginashortout.
AlwaysplaceinsideanLi‐Fesafetybagwhencarryingorstoringthebattery.
Therearevarioustypesofchargersavailableatawidevarietyofprices,andsuchchargersaredesignedto
chargespecifictypesofbatteries.BesuretouseanLi‐Fecompatiblechargerthatcanprovidebalancedcharging.
Furthermore,thecapacityofbatteriesdiffers.Besuretosetthechargertotheratedvoltageofthebatteryand
thechargecurrentbelowthecapacityofthebattery.Repeatedlychargingthebatterytounnecessarilyhigh
settingsmaycausedamagetothebatteryorfire.Beextremelycarefulwhenchargingbatteriesanddonotleave
thebatterybyitselfduringcharging.
Donotuseorstoreinalocationthatissubjecttodirectsunlight,orinalocationthatmaybecomehotsuchas
insideacarornearaheater.Donotuseorrechargeinlocationswhereitmaybesplashedwithwaterorwhere
thereisalotofhumidity.
1.Donotreverseconnect/shortthebattery.
2.Donotdamagethebattery.Donotdroporsubjecttostrongimpact.
Donotdisassembleormodify.
3.Donotuseifthewireinsulationissplit.
4.Donotcarryaroundorstoreuncovered.
5.Usethecorrecttypeofcharger,andmakesureallsettingvaluesare
correct.Becarefulnottooverchargethebattery.
6.Donotuse/storeinhightemperature/humidity.
KRS-3300SeriesServo
RCB-4miniControlBoard
●Spec
*For part names, refer to the following page.
●Spec
*Computer software is used to operate the robot’s motions.
*For details, refer to the “Heart to Heart4 User’s Manual.”
Servo motors are integrated with gears for raising the output torque and a control board that enables stopping at any angle.
Using servo motors in the robot’s joints makes it easy to send angle commands to the joints and enables multiple motors to be
accurately controlled at the same time. The KRS-3301 ICS servo used in this kit employs half-duplex serial communication, so
operating commands can be sent simultaneously to multiple servos, and this allows cables to be wired using the multi-drop/dai-
sy-chain method (method for connecting servos like a chain of beads). This reduces the number of cables connected to the
control board to make possible a simpler, cleaner layout. You can also easily upgrade to the higher-grade KRS-3304 ICS for
more powerful operating performance.
The RCB-4mini control board used in this kit has a total of six ports, three
SIO (serial) ports for each of two systems of ICS3.0/3.5/3.6 compliant
devices, and can connect up to 36 ICS3.0/3.5/3.6 devices.
There are also five AD (analog) ports, so gyro/acceleration and other analog
sensors can be used.
High-speed, high-capacity EEPROM has been adopted to make it possible
to run multiple, varied motions."
■Size: 35 x 30 x 12 (mm)
■Weight: 7.6 g
■Interface: SIO port x6
AD port x5
COM port x1
(ZH Connecter)
■Proper Voltage: DC 6.0–12.0V
Main Features *For details, refer to the KRS Servo manual.
●Servo characteristics settings can be changed using the ICS manager ●Supports high-speed communications up to 1.25 Mbps
●As a dedicated robot servo, can be mounted using dual axial support ● Compact cubic design
●The higher-grade model is the same shape, so you can easily upgrade for more power
■Size: 32.5 x 26 x 26 (mm) ■Maximum operating angle: 270° ■Proper Voltage: DC 6.0–7.4V
■Weight: 26.4g
■Torque: 6.0kg-cm (7.4V)
■Speed: 0.14s/60° (7.4V)
■Communication standards: ICS3.6
■Gear material: Plastic
KRS-3301 ICS KRS-3304 ICS
■Weight: 33.7g
■Torque: 13.9kg-cm (7.4V)
■Speed: 0.13s/60° (7.4V)
■Communication standards: ICS3.5
■Gear material: Metal

10
UpperCase
UpperAxis(FinalAxis)
CaseScrew
Framepartinstallationhole
Groovesurroundingtheshaft.
Thetopoftheshafthasaconcave
origin;findthispositionandinstall
thepart.
ThiskitusesM3screws.
Thiskituses2.6-4screws.
Thelightcomeson
whenthepowerison.
KRS-3301ICS:Red
KRS-3304ICS:Blue
ThiskitusesM2screws.
Serration
MiddleCase
BottomCase
ZHconnector
Whicheveritisconnectedto,
thereisnoimpactonoperations.
PartNameofServoMotor(KRS-3300Series)
Origin
M3ScrewHole
2.6TappingScrewHole
LED
Aligntheprotrudingpositionandfirmlyinsertallthewayin.
Becarefulnottopushitinbackward.
FramepartsarelabeledUpperSideandBottomSidetoindicate
theinstallationdirection.
BottomAxis(FreeAxis)
BottomSide
UpperSide
Prior to Assembly
Servo Motor

11
Tighteningscrews Withmultiplescrews
Tightenscrewsthat
arediagonallyaligned
①
②
③
④
①Putthescrewinvertically
②Tightenwithoutapplyingpressure
Right Right
(Exampleortighteningorder)
Alwaysuseascrewdriverthatisrightforthescrewhead.
■
Whenusingseveralscrewsto
secureparts,firsttighteneach
screwlightly,andthentighten
themfurthertosecuretheparts
evenlywithequalforce.
Further,whenusingmorethan
fourscrewstosecurepartsavoid
addingunevenpressuretothe
partsbyalternatelytightening
screwsthatarediagonally
aligned.
Prior to Assembly
Screw Handling

12
Prior to Assembly
Basic Frame Parts
M2 M2.6
①BendtheM2.6end. ②Fitintothejointbase.
Putthetopsidestogetherfacingeachother.
(Thenutsidefacesout)
M2-8x4
CuttheM2end.
Jointnutscrewhole
HowtosetJointNuts
DoubleJointBase(Wheninstallingjointbases)
Makesuretheinstallation
directioniscorrect.
FrontSide(HornSide) BackSide(NutsSide)
■JointBase
Jointpartsforconnectingthearmsandframe,etc.withtheservos.
Putontheplasticjointnutandscrewtosecure.
PlasticjointnutscanbereplacedwithM2/M2.6metalnuts.

13
Prior to Assembly
Basic Frame Parts
■Arm
Thispartsupportsandrotatestheservowithtwoshafts.
Theuppershaftandbottomshaftareusedasapair.
Makesurethepositionofinstallationbearingsandthelength
ofthearmsarecorrect.
Arm-20
Caution:Crossupperarm-28isexclusivelywith
thecrossupperframe.
20mm
Set
(Back)
26mm
38mm
Serration Free
Free
Therearenoscrewholesfor
guidingcables.
Serrationfacesthetopside.
Serration Free
Serration
Serration
Example:CrossFrame
Free
Upper Bottom
Upper Bottom
Upper Bottom
Bottom Upper
Arm-26
Arm-38

14
Prior to Assembly Servo ID and Position
*SIO3isnotused.*SIO7isnotused.
ConnectservotoservoandservotoRCB-4miniusingZH-ZHconnectioncable.
RCB-4minisSIOports(servoconnectors)aredividedintotwosystems,SIO1-3andSIO5-7.
Withinthesamesystem,changingtheportdoesnotimpactoperations,butbeawarethatif
thesystemisincorrect,therobotwontfunctionproperly.ServoIDstickersareclassified
withthesymbols◯and□.*AlwaysconnectID0totheSIO5-7system.
Theexplanationsinthismanualusethefollowingwiringlayout.
PuttingonConnectionCableDecals
①Removethedecal.
*Putthenumberstickerontheblankdecalsticker
orwriteonitdirectlyasnecessary.
*Leavearound1cmopennearthe
terminalsothecablecanbendeasily.
1cm
②Putthedecalaroundthecable.
SIO1〜3
SIO5〜7
200mm
200mm 200mm
200mm
120mm
120mm120mm
120mm
120mm
120mm120mm
120mm
<Front>
<Rear>
<Right><Left>
SIO2 SIO1
SIO5 SIO6
KXR-R4LL

15
Full Body Assembly Procedures
Procedure 1 Body Assembly
Procedure 0
Setting Servo IDs
Procedure 3 Full Assembly
Procedure 2 Arm Assembly
Multiuse parts
1 BT(Battery) Box
2 Joining
1 Wheel Leg
1 Wheel
2 Electronic Compnents
KXR-R4LL
*Reference diagram
KXR-R4LL

16
Setting Servo IDs 1
PC 1.5m
ExampleofIDstickerapplication
1. SettheDualUSBadapterHSswitch
toICSmode,connecttheSerial
ExtensionCable,andthenplugit
intotheUSBportofyourpersonal
computer.Whenconnectedtothe
USBportinICSmode,theDualUSB
AdapterHSLEDlightsupred.
2. WhenconnectedtotheWindowsPC
forthefirsttime,theAddNew
HardwareWizardwillautomatically
run.Completethesetupfollowing
theKODriverInstallationManualin
theUSBfolderintheincluded
CD-ROM.
● KODriverInstallation
● DualUSBAdapterHSCOMConfirmation
DualUSBAdapterHS SerialExtensionCable
Servo
ZHConversionCable
Beawarethatthecableusedforconnectiondiffersfromthesoftwaremanual.
ConnecttheservostotheDualUSBAdaptorHSandserialextensioncablewithZH
conversioncable.
● Connection
WhentheDualUSBAdapterHSdriverinstallationiscompleted,confirmtheCOMPort
Number. Thisnumberisimportantwhenusingthesoftware,sopleasewriteitdown.The
methodofconfirmingtheCOMnumberisincludedintheKODriverInstallationManualin
the USB folder in the included CD-ROM. Point Operation Tips Caution for Breakage
ConfirmationRequired.
First,applyIDstickers
totheservos.
■ SettingServoIDs
KRS-3301
x12
SerialExtensionCable
1.5m
DualUSBAdapterHS
ICSMODE
LED:RED
KXR-R4LL

17
Setting Servo IDs 2
● ChangingServoIDSettings
1.CopytheSerialManagerfolderonthe
CD-ROMincludedwiththesetontothe
PCdesktop.
2.Double-clickICS3.5Manager.exeinthe
copiedSerialManagerfolderandlaunch
ICS3.5SerialManager.ICS3.5Serial
Managerallowsyoutochangesettings
forICS3.5/3.6-spec.servoIDs,
rotationalmodeandvariousparameters.
3.SelecttheCOMnumberconfirmed
aboveinDualUSBAdaptorHSCOM
Confirmation.Intheimage,COM1is
selected,buttheCOMnumberdiffers
dependingonthecomputeryouuse,so
alwaysselecttheconfirmednumber.
4.Setthespeedforservocommunica-
tions.IfyouselectAuto,itwillauto-
maticallyconnectinlinewiththecom-
municationspeed.
Whenthecommunicationspeedis
selected(KRS-3301ICSatfactory
shipmentis115200)andthe
Connectbuttonchangesto
Disconnect,theprocessiscomplete.
Whentheconnectioniscomplete,the
IDswillautomaticallyswitchbasedon
theservos.
The〇and▢markontheIDstickeris
unrelatedtotheID,soconfirmonlythe
number.
KXR-R4LL

18
Setting Servo IDs 3
5. SelectthesetIDnumberfromtheID
pull-downmenu.
7. Justtobesure,confirmtheID.When
youpresstheAcquirebutton,the
writtenIDwillbedisplayedinthe
pull-downmenu.
ConfirmthatID:AcquireCompleteis
displayedinthelower-left,andconfirm
thatthecorrectIDisdisplayedinthe
pull-downmenu.
TheaboveisthemethodforchangingServoIDsettings.Whenalloftheprocesses
arecompleted,alwaysremovetheDualUSBAdaptorHSfromthePCafterclosingthe
software.
*Thisprocessisonlyforchangingsettings,socommunicationsusethePCsbus
power,butwhenconfirmingoperations,connectthebattery.Refertothemanual
includedwithServoManagerforinformationontheconnectionmethodandnecessary
cabletypes.
6.PresstheWritebuttonontheID
menuandwritetheIDontotheservo.
Ifsuccessful,ID:WriteCompletewill
bedisplayedinthelower-leftbox.
Ifitfails,CommunicationFailedwillbe
displayed,soconfirmtheprocedures
andpresstheWritebuttonagain.In
particular,besurethatDualUSBAdap-
torHSisinSerialMode.
KXR-R4LL

19
Setting Rotation Mode 1
DualUSBAdapterHS SerialExtensionCable
Servo
ZHConversionCable
PC 1.5m
ConnecttheservostotheDualUSBAdaptorHSandserialextensioncablewithZH
conversioncable.
● Connection
Next,switchthesettingsofthewheelservotorotationmode.
● ChangetheRotationMode
1.Select the COM number confirmed above in
“Dual USD Adaptor HS COM Confirmation.”
In the image, COM1 is selected, but the COM
number differs depending on the computer
you use, so always select the confirmed
number.
2.Setthespeedforservocommunica-
tions.IfyouselectAuto,itwillauto-
maticallyconnectinlinewiththecom-
municationspeed.
Whenthecommunicationspeedis
selected(KRS-3301ICSatfactory
shipmentis115200)andthe
Connectbuttonchangesto
Disconnect,theprocessiscomplete.
Whentheconnectioniscomplete,the
IDswillautomaticallyswitchbasedon
theservos.
The〇and▢markontheIDstickeris
unrelatedtotheID,soconfirmonlythe
number.
KXR-R4LL

20
Setting Rotation Mode 2
3.Press the “Read” button and incorporate the
servo settings into Manager. If successful,
“Read Complete” will be displayed in the low-
er-left box. If it fails, “Acquire Failed” will be
displayed, so confirm the procedures and
press the “Read” button again. In particular, be
sure that Dual USB Adaptor HS is in “Serial
Mode.”
4.Put a checkmark in “Rotation Mode.” (in the
flag item in the middle of the window)
5.Press the “Write” button. When the “Write Suc-
cessful” dialog box is displayed, the process is
complete. Close the dialog box by pressing the
OK button.
The above is the method for changing the “Rotation Mode” setting. Repeat procedures 3-7 and
change the remaining servos to the rotation mode.
KXR-R4LL
Table of contents
Other Kondo Robotics manuals
Popular Robotics manuals by other brands
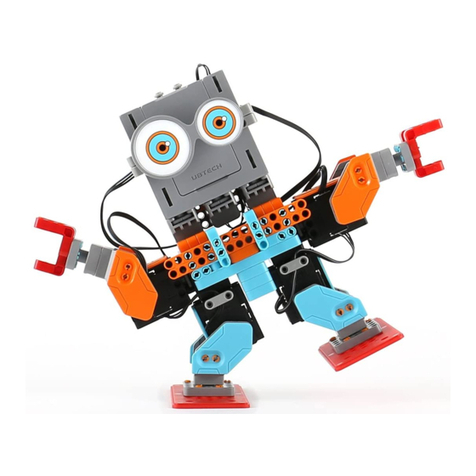
UBTECH
UBTECH Jimu instructions
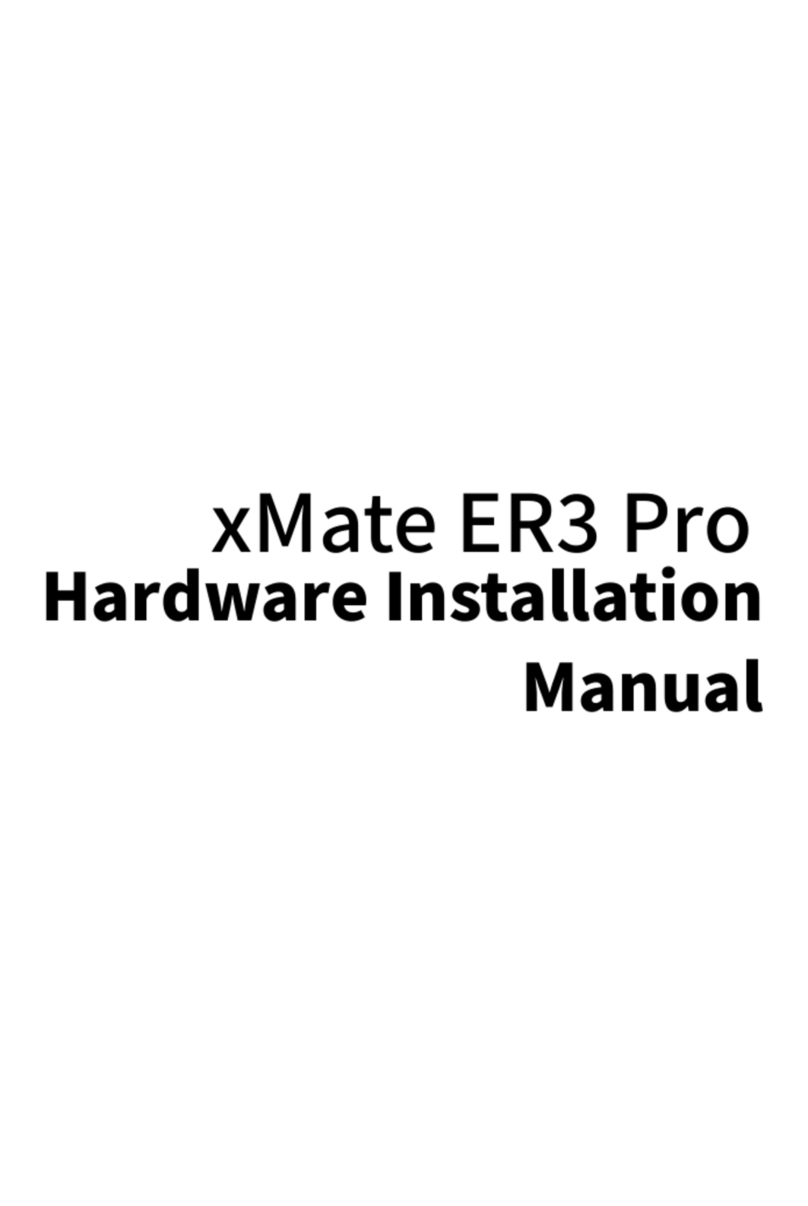
ROKAE
ROKAE xMate ER3 Pro Hardware installation manual
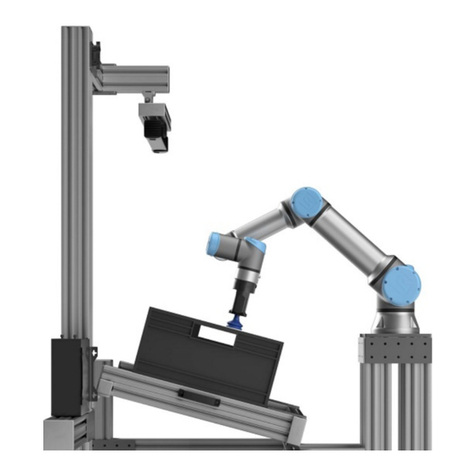
Universal Robots
Universal Robots ActiNav quick start guide
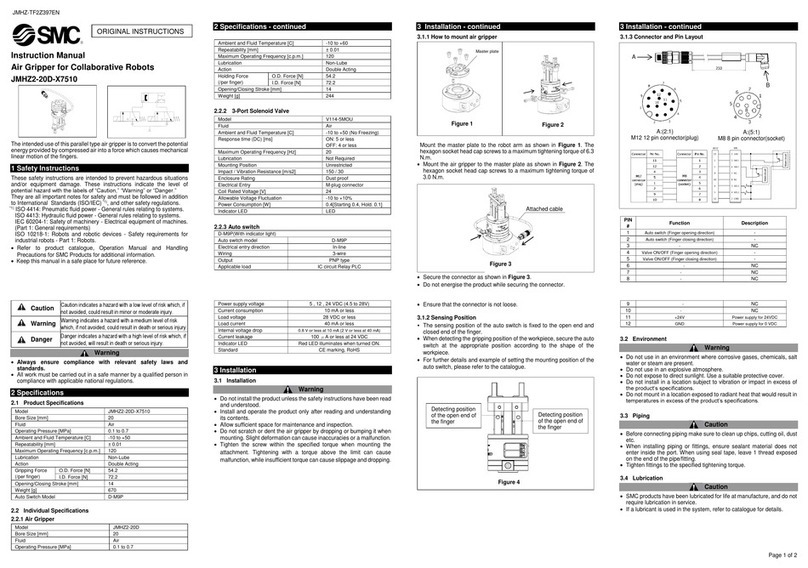
SMC Networks
SMC Networks JMHZ2-20D-X7510 Original instructions
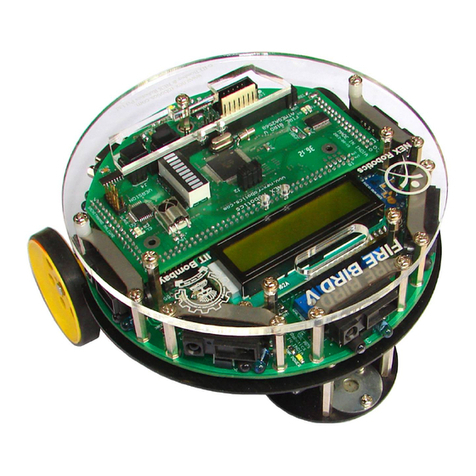
NEX ROBOTICS
NEX ROBOTICS FIREBIRD V ATMEGA 2560 Hardware manual
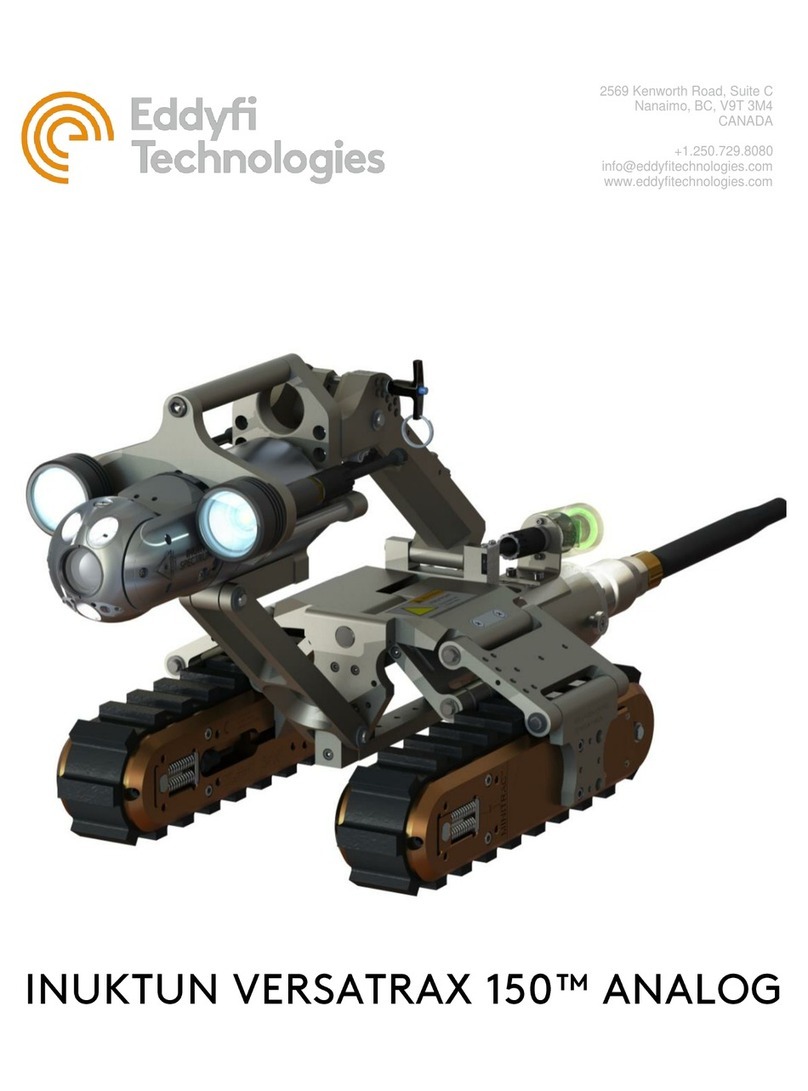
Eddyfi Technologies
Eddyfi Technologies Inuktun Versatrax 150 Analog user manual