lancer DELTA6 Series User manual

FOR QUALIFIED INSTALLER ONLY. This basic Installation Sheet is an initial release. If a complete Operations
Manual (for the unit being installed) is required or needed, please refer to the Lancer web site (lancercorp.com) for
immediate access, or for your convenience, scan this QR code with a mobile device (app required) for immediate
access Contact Lancer Customer Service for assistance as required.
ABOUT THIS MANUAL
This booklet is an integral and essential part of the product and
should be handed over to the operator after the installation and
preserved for any further consultation that may be necessary.
Please read carefully the guidelines and warnings contained
herein as they are intended to provide the user with essential
information for the continued safe use and maintenance of the
product. In addition, it provides GUIDANCE ONLY to the user on
the correct services and site location of the unit.
BEFORE GETTING STARTED
Each unit is tested under operating conditions and is thoroughly
inspected before shipment. At the time of shipment, the carrier
accepts responsibility for the unit. Upon receiving the unit,
carefully inspect the carton for visible damage. If damage exists,
have the carrier note the damage on the freight bill and le a
claim with carrier. Responsibility for damage to the dispenser lies
with the carrier.
The installation and relocation, if necessary, of this product must be carried out by qualied personnel with
up-to-date safety and hygiene knowledge and practical experience, in accordance with current regulations.
IMPORTANT SAFETY INSTRUCTIONS
Lancer PN: 28-2843/04
Revision: October 2017
The dispenser is for indoor use only. This unit is not a toy. Children should not be supervised not to play with appliance. It should
not be used by children or inrm persons without supervision. This appliance is not intended for use by persons (including children)
with reduced physical, sensory or mental capabilities, or lack of experience and knowledge, unless they have been given
supervision or instruction concerning use of the appliance by a person responsible for their safety. Cleaning and user maintenance
shall not be performed by children without supervision. The min/max ambient operating temperature for the dispenser is 40°F to
75°F (4°C to 24°C). Do not operate unit below minimum ambient operation conditions. Should freezing occur, cease operation of
the unit and contact authorized service technician. Service, cleaning and sanitizing should be accomplished only by trained
personnel. Applicable safety precautions must be observed. Instruction warnings on the product being used must be followed.
! Intended Use
The refrigeration system is under high pressure. Do not tamper with it. Contact qualied service personnel before disposal.
! Refrigerant Warning
®
9000

2
Provide an adequate potable water supply. Water pipe connections and xtures directly connected to a potable water supply must
be sized, installed, and maintained according to federal, state, and local laws. The water supply line must be at least a 3/8 inches
(9.525 mm) pipe with a minimum of 25 PSI (0.172 MPA) line pressure, but not exceeding a maximum of 50 PSI (0.345 MPA).
Water pressure exceeding 50 PSI (0.345 MPA) must be reduced to 50 PSI (0.345 MPA) with the provided pressure regulator. Use
a lter in the water line to avoid equipment damage and beverage o-taste. Check the water lter periodically, as required by local
conditions. The water supply must be protected by means of an air gap, a backow prevention device or another approved method
to comply with NSF standards. A leaking inlet water check valve will allow carbonated water to ow back through the pump when it
is shut o and contaminate the water supply. Ensure the backow prevention device complies with ASSE and local
standards. It is the responsibility of the installer to ensure compliance.
! Water Notice
SPECIFICATIONS
DIMENSIONS
Width: 19.5 inches (495 mm)
Depth: 28.5 inches (724 mm)
Height: 27.75 inches (705 mm)
WEIGHT
Shipping: 208 lbs (94.3 kg)
Empty: 163 lbs (73.9 kg)
Operating: 243 lbs (110.2 kg)
CARBON DIOXIDE (CO2) SUPPLY
Min Pressure: 70 PSIG (0.483 MPA)
Max Pressure: 80 PSIG (0.552 MPA)
FITTINGS
Carbonator Inlet: 3/8 inch barb
Plain Water Inlet: 3/8 inch barb
Brand Syrup Inlets: 3/8 inch barb
CO2Inlet: 3/8 inch barb
ELECTRICAL
115 VAC / 60 Hz / 7.9 Amps
230 VAC / 50 Hz / 3.1 Amps
220 VAC / 60 Hz / 3.8 Amps
PLAIN WATER SUPPLY
Min Flowing Pressure: 75 PSIG (0.516 MPA)
CARBONATED WATER SUPPLY
Min Flowing Pressure: 25 PSI (0.172 MPA)
Max Static Pressure: 50 PSI (0.345 MPA)
Metal Bonnet Specications
This unit emits a sound pressure level below 70 dB
DIMENSIONS
Width: 19.5 inches (495 mm)
Depth: 28.5 inches (724 mm)
Height: 28.25 inches (718 mm)
WEIGHT
Shipping: 184 lbs (83.5 kg)
Empty: 139 lbs (63.0 kg)
Operating: 219 lbs (99.3 kg)
CARBON DIOXIDE (CO2) SUPPLY
Min Pressure: 70 PSIG (0.483 MPA)
Max Pressure: 80 PSIG (0.552 MPA)
FITTINGS
Carbonator Inlet: 3/8 inch barb
Plain Water Inlet: 3/8 inch barb
Brand Syrup Inlets: 3/8 inch barb
CO2Inlet: 3/8 inch barb
ELECTRICAL
115 VAC / 60 Hz / 7.9 Amps
PLAIN WATER SUPPLY
Min Flowing Pressure: 75 PSIG (0.516 MPA)
CARBONATED WATER SUPPLY
Min Flowing Pressure: 25 PSI (0.172 MPA)
Max Static Pressure: 50 PSI (0.345 MPA)
This unit emits a sound pressure level below 70 dB
Plastic Bonnet Specications
Check the dispenser name plate label, located behind the splash plate, for the correct electrical requirements of unit. Do not plug
into a wall electrical outlet unless the current shown on the serial number plate agrees with local current available. Follow all local
electrical codes when making connections. Each dispenser must have a separate electrical circuit. Do not use extension cords with
this unit. Do not ‘gang’ together with other electrical devices on the same outlet. The keyswitch does not disable the line voltage to
the transformer primary. Always disconnect electrical power to the unit to prevent personal injury before attempting any internal
maintenance. The resettable breaker switch should not be used as a substitute for unplugging the dispenser from the power source
to service the unit. Only qualied personnel should service internal components of electrical control housing. Make sure that all
water lines are tight and units are dry before making any electrical connections!
F Electrical Warning
• WARNING: Carbon Dioxide (CO2) is a colorless, noncombustible gas with a light pungent odor. High percentages of CO2may
displace oxygen in the blood.
• WARNING: Prolonged exposure to CO2can be harmful. Personnel exposed to high concentrations of CO2gas will experience
tremors which are followed by a loss of consciousness and suocation.
• WARNING: If a CO2gas leak is suspected, immediately ventilate the contaminated area before attempting to repair the leak.
• WARNING: Strict attention must be observed in the prevention of CO2gas leaks in the entire CO2and soft drink system.
5 Carbon Dioxide (CO2)

3
CARBON DIOXIDE (CO2) SUPPLY
Min Pressure: 70 PSIG (0.483 MPA)
Max Pressure: 80 PSIG (0.552 MPA)
FITTINGS
Carbonator Inlet: 3/8 inch barb
Plain Water Inlet: 3/8 inch barb
Brand Syrup Inlets: 3/8 inch barb
CO2Inlet: 3/8 inch barb
DIMENSIONS
Width: 19.5 inches (495 mm)
Depth: 28.5 inches (724 mm)
Height: 27.75 inches (705 mm)
WEIGHT
Shipping: 211 lbs (95.7 kg)
Empty: 166 lbs (75.3 kg)
Operating: 246 lbs (111.5 kg)
ELECTRICAL
115 VAC / 60 Hz / 7.9 Amps
230 VAC / 50 Hz / 3.1 Amps
220 VAC / 60 Hz / 3.8 Amps
PLAIN WATER SUPPLY
Min Flowing Pressure: 75 PSIG (0.516 MPA)
CARBONATED WATER SUPPLY
Min Flowing Pressure: 25 PSI (0.172 MPA)
Max Static Pressure: 50 PSI (0.345 MPA)
Lit Merchandiser Specications
This unit emits a sound pressure level below 70 dB
INSTALLATION
Unpack the Dispenser
1. Cut package banding straps and remove.
2. Open the box and remove the parts tray.
3. Close the lid, then remove using the handle cutouts.
4. Remove accessory kit and loose parts.
Inspect unit for concealed damage. If evident, notify
deliveringcarrierandleaclaimagainstthesame.
NOTE
Ifunitistobetransported,itisadvisabletoleavethe
unitsecuredtotheplywoodshippingbase.
NOTE
5. Remove plywood shipping base from unit by moving unit so
that one side is o the counter top or table allowing access
to screws on the bottom of the plywood shipping base.
6. If leg kit has been provided, assemble legs by tilting unit.
DO NOT LAY UNIT ON ITS SIDE OR BACK
! ATTENTION
Failuretomaintainspeciedclearancewillcausethe
compressortooverheatandwillresultincompressor
failure
! ATTENTION
Selecting/Preparing Counter Location
Thedispensershouldonlybeinstalledinalocation
whereitcanbeoverseenbytrainedpersonnel
NOTE
1. Select a location that is in close proximity to a properly
grounded electrical outlet, within ve (5) feet (1.5 m) of
a drain, and a water supply that meets the requirements
shown in the Specications section found on the previous
page.
2. Select a location for the syrup pumps, CO2tank, syrup
containers, and water lter (recommended).
3. Condenser air is drawn in from the front and side vents
located on the bonnet and dischargede out the rear of the
bonnet. A minimum of eight (8) inches (203 mm) of clearance
must be maintained over the top of the unit and a minimum
of four (4) inches (101.6 mm) clearance behind the unit to
provide for proper air ow and circulation.
Lancerrecommendsplacingcountercut-outtoward
thefrontoftheunit’sdesignatedlocationduetothe
syrup/water/CO2inletsbeinglocatedbehindthe
splashplateinthefrontoftheunit.
NOTE
4. Cut a nine and a half (9.5) inch (241.3 mm) by two (2) inch
(50.8 mm) rectangular hole, one (1) inch (25.4 mm) from the
back wall in the designated dispenser location.
Your Service Agent:
Service Agent Telephone Number:
Serial Number:
Model Numer:
ThismanualwasdevelopedbytheLancerCorporationasareferencefortheowner/operatorandinstallerofthis
dispenser.Pleasereadthisguidebeforeinstallationandoperationofthisdispenser.Ifserviceisrequiredpleasecallyour
LancerServiceAgentorLancerCustomerService.Alwayshaveyourmodelandserialnumberavailablewhenyoucall.
READ THIS MANUAL

4
Iftheunitbeinginstalledutilizesalitmerchandiser,
unhookthemerchandiserfromthebonnetandside
panelsbyliftingup.Unplugmerchandiserwireharness
to remove from dispenser.
NOTE
A
B
A. Lit Merchandiser
B. Unplug to Remove
Dispenser Installation
1. The dispenser is designed to be installed either
permanently to counter or placed on a counter using the four
(4) inch legs (included in the Lancer kit, PN 82-1704)
2. When the dispenser is to be permanently bolted to the count-
er top, the dispenser base must be sealed to the counter top
with a bead of clear silicone caulk or sealant which provides
a smooth and easily cleanable bond to the counter.
3. Once the dispenser is installed to the counter or placed on
the counter using legs provided, remove the splash plate,
cup rest, and drip tray.
Theinstallation,andrelocationifnecessary,must
becarriedoutbyqualiedpersonnelwithup-to-date
knowledgeandpracticalexperience,inaccordancewith
current regulations.
NOTE
NSFlistedunitsmustbesealedtothecounterorhave
four(4)inchlegsinstalled.
NOTE
A
B
A. Bonnet Screw
B. Unlock Bonnet
4. Remove the bonnet screw from the top of the unit and push
the metal bonnet backwards from the front of the unit to
unlock from the dispenser.
6. Once the keyswitch cables are unplugged, remove the
bonnet from the unit.
7. Route appropriate tubing from the syrup pump location to the
syrup inlets located behind the splash plate. Connect tubing
to inlets using the oetiker pliers and ttings. Repeat for all
syrup connections.
Iftheunitbeinginstalledhasbuilt-insyruppumpsor
usesthegalsyrupsupplysystemthenthetubingin
thisstepwillberoutedfromthesyrupsupplylocation
tothesyrupinletsbehindthesplashplate.
NOTE
Thekeyswitchcablesmustbedisconnectedbefore
removalofthemetalbonnet.
! ATTENTION
5. Unplug the keyswitch cables before removal of the bonnet.
8. Route appropriate tubing from the water source to the
carbonator pump inlet at the unit and connect tubing to water
source.
Carefullyreadthisbeforellingthewaterbathtank.
Inordertooptimizethemaximumperformanceofthe
dispenser,thefollowingMUSTbeadheredto:
! CRITICAL - to maximize performance
9. Insert water line into a large bucket, and ll with approx. 5.4
gallons (20.4 L) of distilled water.
10. Add 1/8 oz (4 g) of baking soda to distilled water and stir.
A
B
C
A. Bucket
B. Distilled Water
(approx. 5.4 gal)
C. Baking Soda
(approx. 1/8 oz)
11. Using a conductivity meter, measure the electric conductivity
of the distilled water mixture.
TheE.C.measurementofthedistilledwatermixture
mustbebetween100and300uS/cm.Below100uS/cm,
thecompressorwillnotworkproperlyandabove300
uS/cmcouldcausethelinestofreeze.
! ATTENTION
A
B
C
A. Oetiker Pliers
B. Fitting
C. Tubing
D. Syrup/Water/CO2
Inlet
D
Forproperfunctionoftheelectronicicebankcontrol
thetotaldissolvedsolids(TDS)measurementsshould
be300-500ppm.
! ATTENTION

5
Thewaterbathcompartmentmustbelledwithwater
beforepluggingintheunit,otherwisethecompressor
fanmaynotoperateproperly.DONOTuseROor
puriedwater.
! ATTENTION
12. Remove yellow cap from the water bath ll hole and insert
and insert a funnel into the ll hole.
13. Carefully pour the distilled water mixture into the water bath
tank until water ows out of the overow tube at the front
of the unit. Then replace yellow cap (Repeat steps 9-10 if
needed)
Makesurethetopofoverowtubeisnotcoveredso
thatthewaterfromthewaterbathtankcannotescape.
NOTE
A
C
B
A. Tube from Water Bath
B. Overow Tube
C. Top of Overow Tube
A
B
CA. Line to Water Source
B. Line To Plain Water Inlet
C. Line To Carb Water Inlet
D. “U” Fitting
D
14. Using tubing cutters, cut water supply line and install “U”
tting, (PN 01-2128/01).
15. Route appropriate tubing from the the plain water inlet,
located at the front of the unit, to one side of the “U” tting at
water supply and connect tubing to inlet.
16. Route appropriate tubing from the carbonator pump inlet and
the “U” tting at water supply then connect tubing to inlet
using are seal washer (PN 05-0017). Use a back-up wrench
to prevent damage to carbonator pump.
A
B
C
A. Plain Water Inlet
B. Plain Water Line
C. Oetiker Pliers
D. Fitting
D
17. Route appropriate tubing from the syrup pump/syrup supply
location to the CO2inlet and connect tubing to CO2inlet.
Ifthewatersourceisabove50PSIG(0.345MPA),cut
tubingassemblyandinstallWaterRegulatorKit(PN
18-0253/02, sold separately)asshowninkitinstruction
sheet.Onceinstalled,useatestgaugeassembly(PN
22-0138, sold separately), to set regulator at a
maximumof50PSIG(0.345MPA).
NOTE
A
B
CA. Carbonator
B. Carb Water Inlet
C. Carb Water Line
D. Fitting
18. Connect drain tube to the drain tting located on the bottom
of the drip tray and secure drain tube with clamp.
19. Feed all tubing, power cord, and drain line through the
counter top cutout.
20. Connect tubing routed from carbonated water inlet and plain
water inlet to the “U” tting at the water supply.
21. Turn on water supply and check for leaks.
22. Route the drain line to designated oor drain.
23. Plug in the unit to a grounded electrical outlet then turn the
power switch, at the top of the unit, to begin building an ice
bank.
A
B
C
A. CO2Inlet
B. CO2Line
C. Pressure Relief Valve
Thedispensermustbeproperlyelectricallygrounded
toavoidseriousinjuryorfatalelectricalshock.The
powercordhasathree-pronggroundedplug.Ifa
three-holegroundedelectricaloutletisnotavailable,
useanapprovedmethodtogroundtheunit.Followall
localelectricalcodeswhenmakingconnections.Each
dispensermusthaveaseparateelectricalcircuit.Do
notuseextensioncords.Donotconnectmultiple
electricaldevicesonthesameoutlet.
! WARNING

6
Beforeinstallingregulator,assurethataseal(washer
oro-ring)ispresentinregulatorattachmentnut.
! ATTENTION
Installing CO2Supply
1. Connect high pressure CO2regulator assembly to CO2
cylinder or bulk system.
- Thread regulator nut on to tank, then
tighten nut with wrench
A. CO2Regulator
B. Outlet
C. Wrench
D. CO2 Supply
A
B
C
D
2. Connect a 1/4” nut, stem and seal to CO2regulator outlet.
Then connect tubing routed from tee at syrup pumps.
3. Using a wrench, loosen lock nut on regulator adjustment
screw then using a screwdriver back out lock nut screw all
the way.
A. CO2Regulator
B. 1/4” Nut, Stem & Seal
C. Line to Syrup Pumps
D. Oetiker Pliers
A
B
C
D
DONOTTURNONCO2SUPPLYATTHISTIME
! WARNING
A. CO2Regulator
B. Screwdriver
C. Loosened Lock Nut
D. Regulator Adjustment Screw
A
B
CD
Carbonated Water Setup
1. Purge water to ll carbonator tank by opening carbonator
relief valve. Close relief valve once water comes out.
A. Relief Valve (Open)
B. CO2Inlet
C. CO2Line
A
B
C
2. Activate each valve until a steady ow of water is achieved.
3. Turn power o.
4. Unplug the Pump Motor Connector from the control box. Use
the wiring diagram either on the unit control box or in the
back of this manual for reference.
PumpMotorwillrunforafewsecondstollcarbonator
tank
NOTE
Failuretodisconnectthemotorpowersupplywill
damagethecarbonatormotor,thepumpandvoidthe
warranty.
! ATTENTION
5. Turn on CO2and using a screwdriver, adjust regulator to 75
PSI (0.517 MPA) then tighten lock nut with wrench.
6. Activate each valve until gas-out is achieved.
7. Plug the Pump Motor Connector back into the control box.
8. Turn power on.
A. Regulator Adjustment Screw
B. Adjust to 75 PSI (0.517 MPA)
C. Wrench
A
B
C
9. Activate each valve until a steady ow of carbonated water is
achieved.

7
Adjust Water Flow Rate & Syrup/Water Ratio
Therefridgerationunitshouldhavebeenrunningforat
leastone(1)hourbeforeattemptingtosetowrates
onvalves.Thedrinktemperatureshouldbenohigher
than40°F(4.4°C)whenowratesareset.Thisisbest
doneaftertheunithasalreadymadeanicebank.
NOTE
1. Set the three (3) way back block to dispense plain water or
carbonated water, depending on the type of syrup installed
on the previous page, for each valve.
2. Close syrup shut-o at mounting block for rst valve.
3. Using a Lancer brix cup verify water ow rate (5 oz. in 4
sec.). Use a screwdriver to adjust if needed.
4. Remove nozzle by twisting counter clockwise and pulling
down, then remove diuser by pulling down.
5. Install Lancer (yellow) syrup separator (PN 54-0031) in place
of nozzle.
AB
Increase Decrease
C
E
A. Flow Control, Water
B. Flow Control, Syrup
C. Nozzle (Diuser inside)
D. Mounting Block (not shown)
E. Soda Lever
D
A
B
CA. Syrup Separator
B. Nozzle
C. Soda Lever
6. Re-open syrup shut-o at mounting block.
7. Activate valve to purge syrup until steady ow is achieved.
8. Using a Lancer brix cup, activte the valve and capture a
sample. Verify that the syrup level is even with the water
level. Use a screwdriver to adjust if needed.
AB
A. Plain Water ON
B. Syrup Closed
9. Repeat process for each valve.
10. Re-install the merchandiser, splash plate, cup rest, and drip
tray then reattach bonnet using the top bonnet screw.
A
B
C
A. Syrup Separator
B. Brix Cup
C. Verify Soda/
Water Level
Volumetric Valve Adjustment
TheVolumetricValveisanoptionalvalveforthe
CED-06dispenser
NOTE
1. Remove the ID panel from the front of the rst valve.
2. Insert the programmer’s 10-pin connector into the ID panel
plug located on the front of the circuit board.
3. When properly connected, the programmer will run a self
diagnostic test. The display will show all “8’s” with the
decimal points lighted. After about three (3) seconds, the
display indicates the setting of the dip switches.
Iftheprogrammerdoesnotrunitsdiagnostictest
properly, disconnect it and try plugging it in again. If
theprogrammerstillfails,replacetheprogrammer
NOTE
4. After the programmer is connected, Press the “Read Mem”
button.
5. Press the “Ratio +” or the “Ratio -” key until the desired ratio
is displayed.
6. Verify the drink type by pressing “Carb Toggle” to select “C”
for carbonated or “n” for non-carbonated.
7. Press the “Enter” button to program the valve with the setting
on the display.
8. Verify Ratio by pressing “Read Mem”.
9. Disconnect the programmer and repeat steps 4-9 for each
valve.
- Handheld Programmer
Volumetric Valve

8
SCHEDULED MAINTENANCE
• Usesanitarygloveswhencleaningtheunitandobserveallapplicablesafetyprecautions.
• DO NOTuseawaterjettocleanorsanitizetheunit.
• DO NOTdisconnectwaterlineswhencleaningandsanitizingsyruplines,toavoidcontamination.
• DO NOTusestrongbleachesordetergents;Thesecandiscolorandcorrodevariousmaterials.
• DO NOTusemetalscrapers,sharpobjects,steelwool,scouringpads,abrasives,orsolventsonthedispenser.
• DO NOTusehotwaterabove140°F(60°C).Thiscandamagethedispenser.
• DO NOTspillsanitizingsolutiononanycircuitboards.Insureallsanitizingsolutionisremovedfromthesystem.
! ATTENTION
Thecleaningproceduresprovidedhereinpertaintothe
Lancerequipmentidentiedbythismanual.Ifother
equipmentisbeingcleaned,followtheguidelines
establishedbythemanufacturerforthatequipment.
NOTE
CLEANING AND SANITIZING
General Information
• Lancer equipment (new or reconditioned) is shipped from
the factory cleaned and sanitized in accordance with NSF
guidelines. The operator of the equipment must provide
continuous maintenance as required by this manual and/
or state and local health department guidelines to ensure
proper operation and sanitation requirements are
maintained.
• Cleaning should be accomplished only by trained personnel.
Sanitary gloves are to be used during cleaning operations.
Applicable safety precautions must be observed. Instruction
warnings on the product being used must be followed.
Cleaning Solution
Mix a mild, non-abrasive detergent (e.g. Sodium Laureth
Sulfate, dish soap) with clean, potable water at a temperature
of 90°F to 110°F (32°C to 43°C). The mixture ratio is one ounce
of cleaner to two gallons of water. Prepare a minimum of ve
gallons of cleaning solution. Do not use abrasive cleaners or
solvents because they can cause permanent damage to the unit.
Ensure rinsing is thorough, using clean, potable water at a
temperature of 90°F to 110°F. Extended lengths of product lines
may require additional cleaning solution.
Sanitizing Solution
Prepare the sanitizing solution in accordance with the
manufacturer’s written recommendations and safety guidelines.
The type and concentration of sanitizing agent recommended in
the instructions by the manufacturer shall comply with 40 CFR
§180.940. The solution must provide 100 parts per million (PPM)
chlorine (e.g. Sodium Hypochlorite or bleach) and a minimum of
ve gallons of sanitizing solution should be prepared.
Daily
• Remove each nozzle and rinse well in warm water. DO NOT use soap or detergent. This will cause foam-
ing and o tast in nished product.
• Remove cup rest and wash in warm soapy water.
• Pour warm soapy water into the drip tray and wipe with a clean cloth.
• With a clean cloth and warm water, wipe o all of the unt’s exterior surfaces. DO NOT USE ABRASIVE
SOAPS OR STRONG DETERGENTS.
• Replace the cup rest and nozzles.
Weekly • Taste each product for o tastes.
• Remove cup rest and splash plate to view water level tube indicator, replenish as required.
Monthly
• Unplug the dispenser from the power source.
• Remove the bonnet and clean the dirt from the condenser using a soft brush.
• Replace the bonnet and plug in the unit.
Every Six Months • Clean and sanitize the unit using the appropriate procedures outlined in the Cleaning and Sanitizing
section of this guide.
Yearly • Clean water bath interior, including evaporator coils and refrigeration components.
• Clean the entire exterior of the unit

9
Cleaning and Sanitizing Syrup Lines
1. Disconnect syrup lines from BIB’s
2. Place syrup lines, with BIB connectors, in a bucket of warm
water.
3. Activate each valve to ll the lines with warm water and ush
out syrup remaining in the lines.
4. Prepare Cleaning Solution described above.
5. Place syrup lines, with BIB connectors, into cleaning
solution.
6. Activate each valve until lines are lled with cleaning
solution then let stand for ten (10) minutes.
7. Flush out cleaning solution from the syrup lines using clean,
warm water.
8. Prepare Sanitizing Solution described above.
9. Place syrup lines into sanitizing solution and activate each
valve to ll lines with sanitizer. Let sit for ten (10) minutes.
10. Reconnect syrup lines to BIB’s and draw drinks to ush
solution from the dispenser.
11. Taste the drink to verify that there is no o-taste. If o-taste
is found, ush syrup system again.
Followingsanitization,rinsewithend-useproduct
untilthereisnoaftertaste.Donotuseafreshwater
rinse.Thisisansfrequirement.Residualsanitizing
solutionleftinthesystemcreatesahealthhazard.
! CAUTION
Followingsanitization,rinsewithend-useproduct
untilthereisnoaftertaste.Donotuseafreshwater
rinse.Thisisansfrequirement.Residualsanitizing
solutionleftinthesystemcreatesahealthhazard.
! CAUTION
Cleaning and Sanitizing Nozzles
1. Disconnect power, so as to not activate valve while cleaning.
2. Remove nozzle by twisting counter clockwise and pulling
down.
3. Remove diuser by pulling down.
4. Rinse nozzle and diuser with warm water.
5. Wash nozzle and diuser with cleaning solution then
immerse in sanitizing solution and let sit for fteen (15)
minutes.
6. Set nozzle and diuser aside and let air dry. DO NOT rinse
with water after sanitizing.
7. Reconnect diuser and nozzle.
8. Connect power.
9. Taste the drink to verify that there is no o-taste. If o-taste
is found, ush syrup system again.
Integrity of Plastic Finish
While caring for your Delta-6, please note that there may be
some cleaners that may compromise the integrity of the plastic
nish. Most common cleaners such as Windex, Dawn, 409, etc.
pose no threat to the plastic nish of the unit. However, certain
cleaners with high levels of acetic acid, ethylbenzene,
isopropylamine, etc., at certain temperatures, could cause
aesthetic damage. Please refer to this webpage,
http://www.vita.com.cy/index.php/chemical-resistance-of-lldpe, to
make sure that you are properly caring for your unit.
A
B
CA. Diuser
B. Nozzle
C. Soda Lever
To prevent possible harm to the environment from improper disposal, recycle the unit by locating
an authorized recycler or contact the retailer where the product was purchased. Comply with local
regulations regarding disposal of the refrigerant and insulation.
Dispenser Disposal

10
WIRING DIAGRAM - 115 V/60 Hz, R744
WIRING DIAGRAM - 230 V/50 Hz, 220 V/60 Hz, R744

11
WIRING DIAGRAM - 115 V/60 Hz, 230 V/50 Hz, 220 V/60 Hz, R134A
PLUMBING DIAGRAM
PLAIN WATER
COILS
CARB.
HIGH PRESSURE
WATER PUMP
V6 V5 V4 V3 V2 V1
S1 PW1S2S3S
4S
5S6PLAIN WATER INLET
TO CARBONATOR
PLUMBING DIAGRAM
CED-06
PN 06-3534
®
Table of contents
Popular Other manuals by other brands
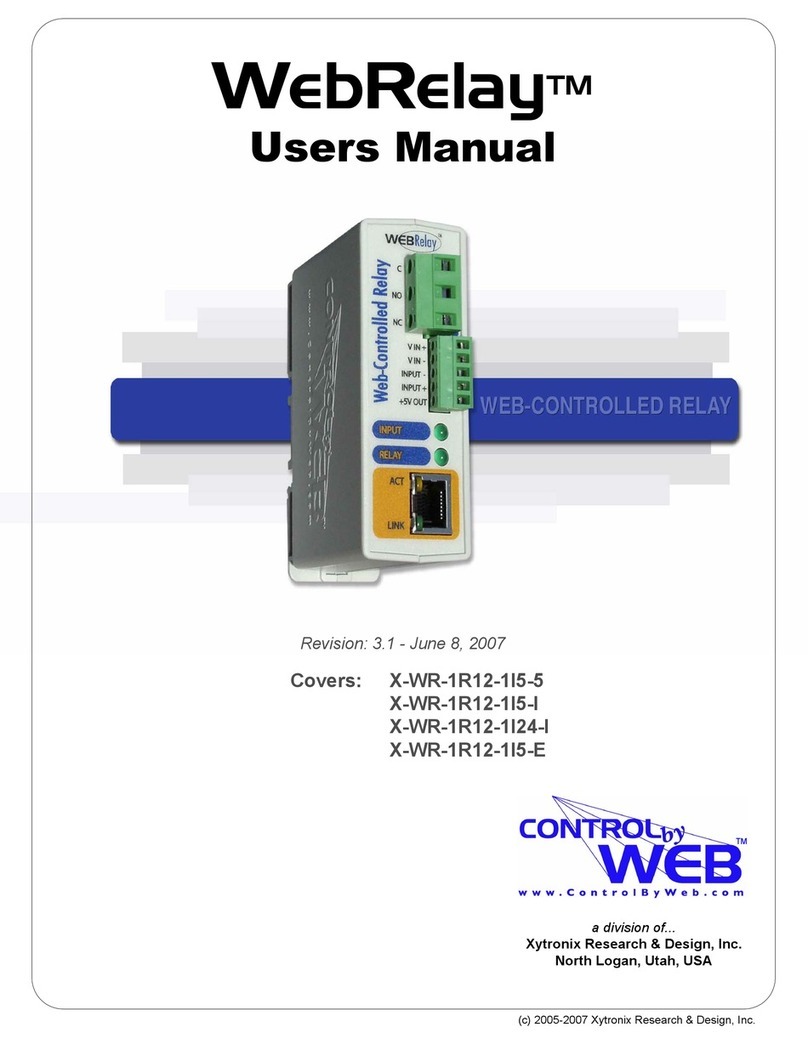
Xytronix Research & Design
Xytronix Research & Design WebRelay user manual

Regalo
Regalo WideSpan Extra Tall 1154 owner's manual
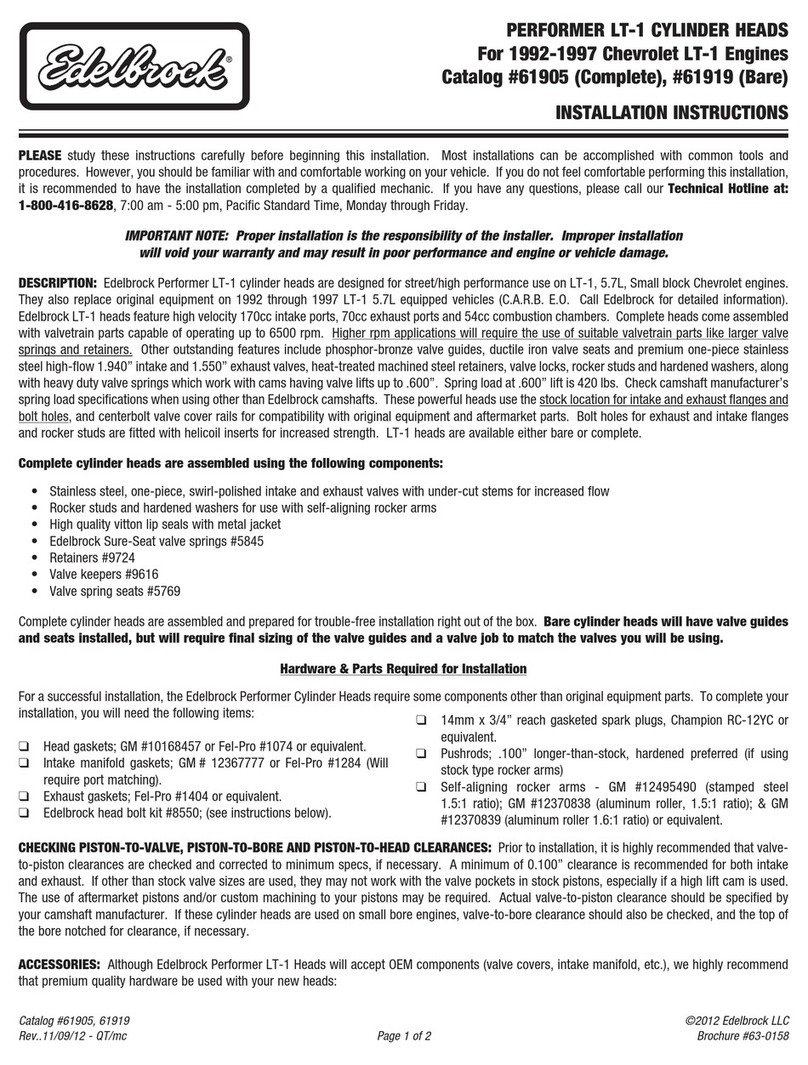
Edelbrock
Edelbrock 61905 installation instructions
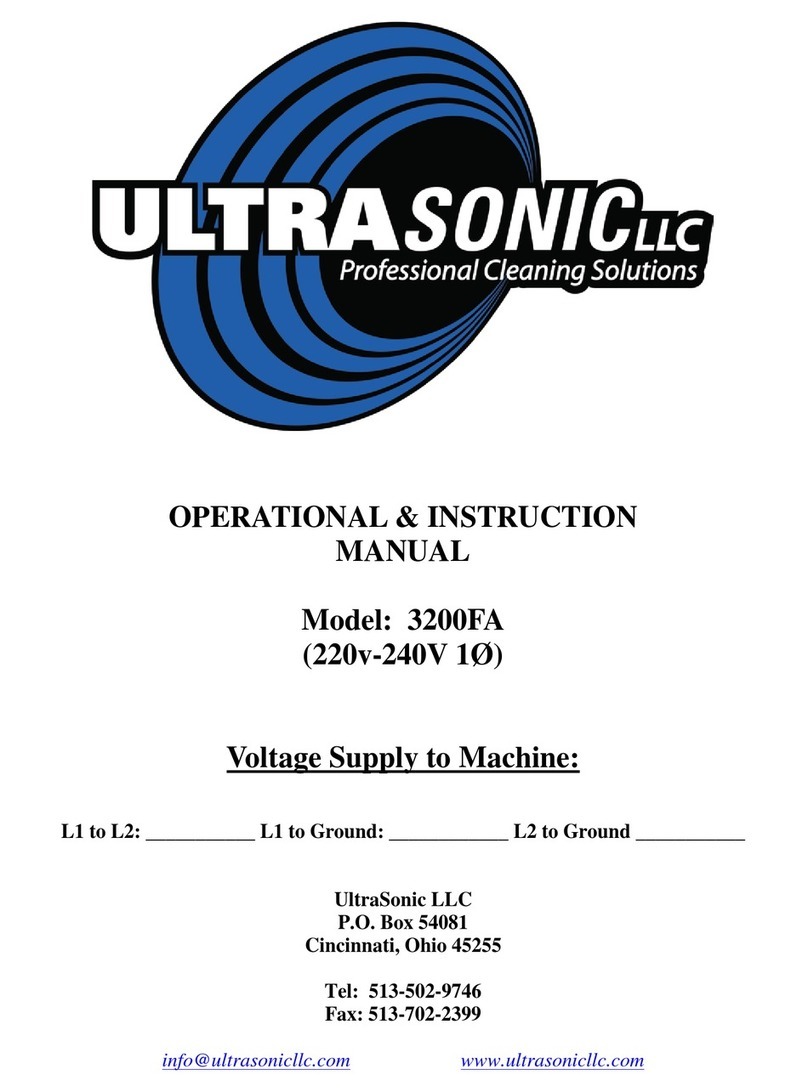
Ultrasonic
Ultrasonic Ultra 3200FA Operational Instruction Manual

PTP Turbo Blankets
PTP Turbo Blankets Turbo Blanket Installation instructions manual
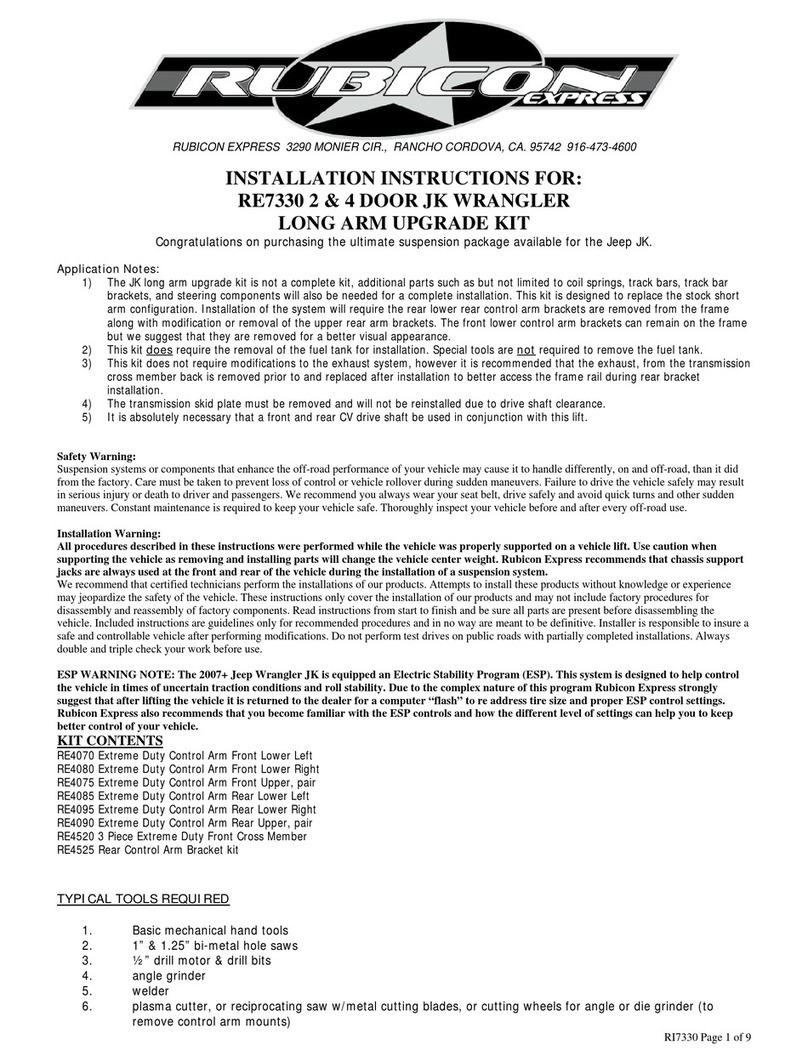
Rubicon Express
Rubicon Express RE7330 installation instructions