Leslie K-MAX Manual

12501 Telecom Drive, Tampa Florida
33637
9/0.5.0 Rev.2
Formerly D-10236
INSTALLATION, OPERATING,
AND MAINTENANCE INSTRUCTIONS
PARTS LIST
LESLIE CLASS K-MAX
ROTARY CONTROL VALVES
1" - 8"
ANSI CLASS 150 - 600
DIN 16 - 40
INTRODUCTION . . . . . . . . . . . . . . . . . . . . . . . . . . . .ii
DESCRIPTION . . . . . . . . . . . . . . . . . . . . . . . . . . . . . .ii
INSTALLATION . . . . . . . . . . . . . . . . . . . . . . . . . . . .A1
MOUNTING POSITION . . . . . . . . . . . . . . . .A1
CLEANING . . . . . . . . . . . . . . . . . . . . . . . . .A1
FLANGED VALVE INFORMATION . . . . . . . .A1
FLANGELESS VALVE INFORMATION . . . . .A1
GASKETS . . . . . . . . . . . . . . . . . . . . . . . . . .A1
BOLTS . . . . . . . . . . . . . . . . . . . . . . . . . . . .A1
SUPPLY AIR CONNECTIONS . . . . . . . . . . .A1
OPERATION . . . . . . . . . . . . . . . . . . . . . . . . . . . . . .A1
SYSTEM FLUSH . . . . . . . . . . . . . . . . . . . . .A1
START-UP . . . . . . . . . . . . . . . . . . . . . . . . .A1
PACKING . . . . . . . . . . . . . . . . . . . . . . . . . .A1
MAINTENANCE . . . . . . . . . . . . . . . . . . . . . . . . . . . .A3
LUBRICATION . . . . . . . . . . . . . . . . . . . . . .A3
ADJUSTMENTS . . . . . . . . . . . . . . . . . . . . .A3
PACKING REPLACEMENT . . . . . . . . . . . . .A3
VALVE DISASSEMBLY . . . . . . . . . . . . . .A5-A6
VALVE REASSEMBLY . . . . . . . . . . . . . .A6-A7
SEAT RING LAPPING . . . . . . . . . . . . . . . . .A7
VALVE REMOVAL FROM PIPELINE . . . . . .A7
ACTUATOR REMOVAL FROM VALVE . . . . .A7
TROUBLESHOOTING . . . . . . . . . . . . . . . . . . . .A8-A9
CODE SELECTION CHART . . . . . . . . . . . . . . . . .A10
PARTS LIST . . . . . . . . . . . . . . . . . . . . . . . . . .A11-A12
ILLUSTRATION INDEX
Figure 1 - Actuator Mounting Positions . . . . . . . . . .A2
Figure 2 - K-Max Parts Identification . . . . . . . . . . .A4
Figure 3 - Packing Component Stackup . . . . . . . . .A5
Table A - K-Max Seat Retainer Torques . . . . . . . . .A6
Figure 4A & 4B - Dimensions & Parts List . . . . . . .A11
Figure 5 - Valve Seat Retainer Wrench . . . . . . . . .A13
DIAPHRAGM ACTUATORS
ON K-MAX CONTROL VALVES
MODELS 40, 55 AND 85
DESCRIPTION . . . . . . . . . . . . . . . . . . . . . . . . . . .B14
AIR SUPPLY . . . . . . . . . . . . . . . . . . . . . . . . . . . . .B14
LUBRICATION . . . . . . . . . . . . . . . . . . . . . . . . . . . .B14
OPEN AND CLOSED
POSITION STOP ADJUSTMENTS . . . . . .B14
SPRING-TO-CLOSE ACTUATORS
CLOSED STOP ADJUSTMENT . . . . . . . . .B14
OPEN STOP ADJUSTMENT . . . . . . . . . . .B15
SPRING-TO-OPEN ACTUATORS
CLOSED STOP ADJUSTMENT . . . . . . . . .B15
OPEN STOP ADJUSTMENT . . . . . . . . . . .B15
SIZE 40 ACTUATOR
REMOVAL . . . . . . . . . . . . . . . . . . . . . . . .B15
INSTALLATION . . . . . . . . . . . . . . . . . . . . .B16
SIZE 55 AND 85 ACTUATORS
REMOVAL . . . . . . . . . . . . . . . . . . . . . . . .B16
INSTALLATION . . . . . . . . . . . . . . . . . . . . .B16
SPRING ASSEMBLY REPLACEMENT . . . . . . . . .B17
DIAPHRAGM REPLACEMENT . . . . . . . . . . . . . . .B18
REVERSING THE ACTION . . . . . . . . . . . . . . . . . .B18
CHANGING MOUNTING POSITIONS . . . . . . . . . .B19
PARTS LIST . . . . . . . . . . . . . . . . . . . . . . . . . . . . . .B21
ILLUSTRATION INDEX
Figure 1- Vibration Support & Disassembly Studs .B14
Figure 2A-
Size 40 Actuator Cutaway
. . . . . . . . . . .B15
Figure 2B- Size 55/85 Actuators-Reverse Action .B15
Figure 3- Size 40 Actuator/Spring-To-Close Mode B16
Figure 4- Coupling Clamp Screws . . . . . . . . . . . .B17
Figure 5- Actuator Mounting Positions . . . . . . . . .B17
Figure 6- Link Arm Position . . . . . . . . . . . . . . . . .B19
Figure 7- Stub Shaft Position . . . . . . . . . . . . . . . .B19
Figure 8- Parts Identification for 55 & 85 Actuator .B20
Figure 9- Exploded Drawing of 55 & 85 . . . . . . . .B21
Figure 11- DR 40 Actuator Assembly . . . . . . . . . .B22
TABLE OF CONTENTS

Page ii
INTRODUCTION
The K-MAX Rotary Control valve utilizes state-of-the-art
technology in both design and construction. It will provide
dependable, trouble free service provided the application is
correct and the valve is installed and maintained to Leslie
specifications. Each valve is fully tested and inspected at the
factory to ensure compliance to customer specifications.
A copy of these instructions should be made available to the
personnel responsible for the installation and maintenance of
this equipment. Refer to the data plate attached to the valve
and the applicable sales bulletin for information regarding
materials of construction and product limitations.
DESCRIPTION
The K-MAX Rotary Control Valve is a high performance rotary
Control valve designed to meet an wide range of
applications. It features an eccentric plug that rotates into a
self-aligning orbital seat ring to achieve extremely tight shut
off. The K-MAX valve is also offered with reduced trim
options to match maximum flow capacity (Cv) to the
application.
The plug is attached to a splined shaft which is rotated by a
lever linked to the diaphragm stem of the actuator. Valve
action is available as either air-to-open or air-to--close and is
field reversible. The inherent linear flow characteristic can be
changed to equal percentage or custom characteristic by
simply changing the positioner cam.
The body is designed to ANSI Class 600 standards and is
available with flangeless tie rod construction. Optional slip-
on flanges are available in ANSI Classes 150 and 300; integral
cast flanges are available in ANSI Classes 150, 300 and 600.
INSPECTION
This equipment has been adequately packaged and
protected for shipping; however, due to improper handling,
the possibility of damage in transit exists. When the valve
arrives at its final destination, it should be carefully inspected
for damage and equipment malfunction.
STORAGE
Units should be stored in a clean, cool and dry location and
should be protected from dirt, chips, dust and insects or
other nesting animals.
REPLACEMENT PARTS
It is recommended that one set of Recommended Spare
parts be inventoried for each valve size and type. Recom-
mended Spare Parts are identified on the Assembly Drawing.
Replacement parts can be ordered from your local Leslie
representative. The factory address is listed on the back of
this Instruction Manual.
When ordering parts please include the valve size and valve
number from the data plate. Also include the Assembly
Drawing Number, Part Name, Balloon Number and Quantity
as shown on the Assembly Drawing.
LESLIE SERVICE
Leslie service personnel are available to start up and repair
our products. Leslie can also train your personnel to do this
work. Contact the Leslie representative nearest you for
details.
LESLIE CLASS K-MAX

Page A1
I. INSTALLATION
This installation section has been broken down into
subsections that present a wide range of installation related
requirements.
A. MOUNTING POSITION
Normal valve installation is in the flow-to-open mode of
operation. (see Figure 1, Page A2)
The valve actuator can be mounted in any position to work
around the existing pipeline. (See Actuator Instruction
Manual). Horizontal stem orientation is preferred, with the
plug opening upward. (see Figure 1, Page A2)
B. CLEANING
Before the valve is installed, ensure that it is free of foreign
material which may have been introduced during handling.
Clean the pipeline of all debris such as loose weld spatter,
scale, oil, grease or dirt.
Clean the valve and pipe mating surfaces and always use
new, clean gaskets to ensure a leak proof fit.
C. FLANGED VALVE INFORMATION
Valve flanges conform to ANSI B16.5, Pipe Flanges and
Flanged Fittings specifications.
Support the piping near the valve so strain on the flanges in
minimized. Tighten the bolts with a criss-cross pattern. Do
not use the flange bolts to draw the pipeline flanges into
contact with the valve flanges.
D. FLANGELESS VALVE INFORMATION
For flangeless valves, install the lower tie rods to provide a
cradle to support the valve while installing the remaining tie
rods. Make sure that flange gasket is centered on both ends
of the valve to assure a proper face seal. Tighten the nuts with
a criss-cross pattern.
E. GASKETS
Dimensions are specified in ANSI B16.5, Pipe Flanges and
Flanged Fittings.
F. BOLTS
Bolting specifications can be found in ANSI B16.5, Pipe
Flanges and Flanged Fittings.
G. SUPPLY AIR CONNECTIONS
Valves with positioners - Connect supply air to the positioner
supply port. See the Positioner Instruction manual for proper
identification.
Valves without positioners - Connect supply air to the
actuator supply port.
Supply air should be clean, dry and oil free and must not
exceed the maximum rating of the actuator spring; see the
data plate affixed to the actuator spring case.
II. OPERATION
Connect a regulated air line to the actuator and pressurize to
operate the valve through its full stroke. If it does not operate
smoothly, the packing gland clamp nuts may to too tight and
are causing the packing to bind on the valve shaft.
After the supply air pressure is released, observe the valve
position. The valve should be in the open position for direct
acting or in the closed position for the reverse acting. If the
actuator fails to return to the correct position, check for
obstacles that may be jammed between the plug and seat.
A. SYSTEM FLUSH
It is recommended that the piping system be flushed prior to
initial start-up. Debris in the pipeline could damage valve or
associated components.
Make sure all valves are open during the flushing operation.
B. START-UP
Check the following items prior to placing the valve in service
at either the initial installation or after a valve assembly
rebuild.
C. PACKING
Tighten the packing gland clamp nuts finger tight plus 1/2
turn. After the valve is pressurized to full operating pressure,
check for packing leakage and tighten the packing gland
clamp nuts if necessary.
WARNING
THIS VALVE IS A PRESSURE VALVE. LINE
PRESSURE MUST BE COMPLETELY
RELIEVED BEFORE REMOVING THE VALVE
MOUNTING BOLTS FROM THE PIPELINE OR
BEFORE REMOVING THE ACTUATOR FROM
AN INSTALLED VALVE. FAILURE TO RELIEVE
PRESSURE MAY RESULT IN PERSONAL
INJURY.
WARNING
DO NOT PLACE HANDS, FINGERS OR
OBJECTS INTO VALVE PORTS DURING
OPERATION CHECK.

Page A2
(1) FLOW TENDING TO OPEN VALVE - PREFERRED FOR VALVES WHICH MUST FAIL OPEN
(2) FLOW TENDING TO CLOSE VALVE - PREFERRED FOR VALVES WHICH MUST FAIL CLOSED
DIRECT ACTING ACTUATORS (SPRING-TO-OPEN)
REVERSE ACTING ACTUATORS (SPRING-TO-CLOSE)
STANDARD 180° FROM
STANDARD
90° FROM STANDARD
270° FROM STANDARD
STANDARD 180° FROM
STANDARD
90° FROM STANDARD
270° FROM STANDARD
(1)
(2)
ACTUATOR MOUNTING POSITIONS
FIGURE 1
(1)
(2)
ACTUATORS ARE IN THE FOREGROUND. VALVE BODIES ARE BEHIND THE ACTUATORS.

Page A3
III. MAINTENANCE
Some periodic maintenance of this product is required as
specified in the following subsections.
A. LUBRICATION
This valve has been lubricated at the factory with lithium and
silicone based lubricants. Ensure lubricant to flow media
compatibility prior to start-up. If lubricant is not compatible
with flow media, disassemble the valve and lubricate with
flow media compatible lubricants.
This valve does not require routine maintenance lubrication.
Lubrication is necessary only when valve has been
disassembled to inspect or replace components.
After the supply air pressure is released, observe the valve
position. The valve should be in the open position for direct
acting or in the closed position for the reverse acting. If the
actuator fails to return to the correct position, check for
obstacles that may be jammed between the plug and seat.
B. ADJUSTMENTS
If packing leakage occurs, turn the packing gland clamp nuts
clockwise only until packing leakage stops; do not continue
turning after leakage stops. If packing leakage cannot be
stopped by turning the packing gland clamp nuts clockwise,
the packing must be replaced.
After the supply air pressure is released, observe the valve
position. The valve should be in the open position for direct
acting or in the closed position for the reverse acting. If the
actuator fails to return to the correct position, check for
obstacles that may be jammed between the plug and seat.
C. PACKING REPLACEMENT
During this procedure, you may come in contact with process
fluids, wear adequate protection to protect yourself from the
process fluid.
See Figure 2, Page A4 for parts identification.
1. Depressurize and drain the process line.
2. Remove the actuator from the valve as described in the
ACTUATOR REMOVAL Section of the Actuator
Instruction manual.
3. Slowly and evenly remove the two nuts holding the
packing gland clamp in place.
4. Remove the two nuts that secure the actuator yoke
(shown in Figure 9, Ref. B32) to the valve body, then lift
the yoke and packing gland clamp off the valve. Leaving
the ball bearing in the yoke.
5. Slide the gland off the valve shaft.
6. Remove and discard the packing from the valve body. It
is not necessary to remove the metal backup ring in the
bottom of the packing chamber. Ensure that the shaft
and packing bore are clean and smooth. If a scarred
shaft or packing bore are present, replace the damaged
parts.
7. Slide the new packing, one piece at a time, down the
valve shaft and into the packing chamber. Use the
sequence shown in Figure 3, Page A5. Use the packing
gland to seat each packing ring one at a time. Be sure to
use a compatible lubricant with each piece of packing as
required.
8. Slide the gland and packing gland clamp down the valve
shaft until the gland contacts the packing.
9. While holding the packing gland clamp inside of the
actuator yoke (not shown in Figure 2, Page A4), slide the
packing gland clamp and yoke onto the valve shaft so
the slots in the packing gland clamp slide over two of the
studs. Install yoke nuts and tighten.
10. Screw packing nuts onto the studs to hold the packing
gland clamp down; tighten the nuts finger tight plus 1/2
turn. They will be re-tightened after the valve is
pressurized.
11. Mount the actuator on the valve as described in the
ACTUATOR INSTALLATION Section of the Actuator
Instruction Manual.
12. After the valve is pressurized, turn the gland clamp nuts
clockwise only until packing leakage stops; do not
continue turning after leakage stops. If packing leakage
cannot be stopped by turning the gland clamp nuts
clockwise, the packing must be replaced.
WARNING
UNLESS OTHERWISE SPECIFIED THIS
VALVE HAS BEEN LUBRICATED AT THE
FACTORY WITH LITHIUM AND SILICONE
BASED LUBRICANTS THAT MAY NOT BE
COMPATIBLE WITH YOUR FLOW MEDIA.
ENSURE LUBRICANT COMPATIBILITY PRIOR
TO START-UP. FAILURE TO DO SO MAY
RESULT IN PERSONAL INJURY AND/OR
EQUIPMENT DAMAGE.

Page A4
PARTS LIST FOR K-MAX VALVE
NO. PART NAME
A1 UPPER GUIDE BEARING
A2 PLUG
A3 LOWER GUIDE BEARING
A4 GUIDE BUSHING (3’ THRU 8” VALVES)
A5 PIPE PLUG
A6 BODY
A7 SEAT RING
A8 SEAT RETAINING RING
A9 FLANGE RETAINING RINGS
A10 SEPARABLE FLANGES
A11 BACKUP RING
A12 PACKING
A13 PACKING GLAND
A14 NUT
A15 YOKE/BODY STUD
A16 PACKING GLAND CLAMP
A17 SHAFT
A18 PACKING NUT
A19 PACKING STUD
A21 STUD BLOCK (FLANGELESS VALVES)
K-MAX PARTS IDENTIFICATION
FIGURE 2
*Recommended spare parts.
A19
A18
A16
A13
A12
A11
A14
A15
A6
A21
A17 A10
A1
A2
A7
A8
A5
A4
A3
A9

Page A5
D. VALVE DISASSEMBLY
For your safety it is important that safety equipment be worn
when repairing this valve. The safety equipment must be
adequate to protect you from the process fluid.
1. Depressurize and drain the process line and valve.
2. Shut off the electrical power (units equipped with
switches, pilot valves or electronic positioners) and the
supply air to the valve assembly. Disconnect the air lines
and wiring from the unit
3. Remove the valve assembly from the pipeline as
described in the VALVE REMOVAL FROM PIPELINE
Section of this manual.
4. If your valve is equipped with any accessories (i.e.,
positioner, switches, etc.), remove them from the
actuator before proceeding.
5. Remove the actuator from the valve as described in the
ACTUATOR REMOVAL Section of the Actuator
Instruction Manual.
6. Remove the packing clamp nuts. See Figure 2, Page A4
for component identification.
7. Remove the two nuts that secure the actuator yoke (not
shown in Figure 2, Page A4) to the valve body, then lift
the yoke and packing gland clamp off the valve.
8. Slide the packing gland off the valve shaft.
9. Unscrew the seat ring retainer. A seat retainer wrench
can be fabricated using the dimensions shown in Figure
5 on page A13. For 6” and 8” valves, insert screws in the
holes in the seat ring retainer, hook a pry bar on the
screws and unscrew the retainer.
10. Remove the seat ring from the valve cavity.
11. Pull the shaft out of the body. It may be necessary to
remove the pipe plug from the bottom of the valve body
and drive the shaft from the bottom.
12. Pull the plug out of the valve body.
13. Remove the pipe plug from the bottom of the valve body
if it was not removed in Step 11.
14. If the upper guide bearing does not come out with the
shaft, push it into the valve body cavity from the top.
15. Remove the lower guide bearing by inserting two flat
screwdriver tips in the bearing groove and prying the
bearing out; exercise care to avoid damage to the seat
pocket area of the body.
WARNING
FAILURE TO USE THE PROPER TOOL ON THE
SEAT RING RETAINER CAN DESTROY THE
RETAINER AND/OR MAY RESULT IN
PERSONAL INJURY.
WARNING
THIS VALVE IS A PRESSURE VESSEL. LINE
PRESSURE MUST BE COMPLETELY RELIEVED
BEFORE REMOVING THE VALVE MOUNTING
BOLTS FROM THE PIPELINE OR BEFORE
REMOVING THE ACTUATOR FROM AN
INSTALLED VALVE. FAILURE TO RELIEVE
PRESSURE MAY RESULT IN PERSONAL INJURY.
PACKING COMPONENT STACKUP
FIGURE 3

Page A6
16.
Remove the packing and backup ring from the valve body.
17. Thoroughly clean and inspect the valve components.
Replace all damaged parts.
E. VALVE REASSEMBLY
NOTE: When a hard (all metal) seat ring is to be the seat ring
it should be lapped. Perform the steps in the SEAT RING
LAPPING Section of this Instruction Manual before beginning
REASSEMBLY. (See page A7).
1. Coat the inside and outside diameters of the lower guide
bearing with a lubricant, then install it in the valve body.
2. Coat the inside and outside diameters of the upper guide
bearing with a lubricant, then install it on the valve shaft.
3. Coat the valve shaft splines with a lubricant.
4. While holding the plug inside the body, push the shaft
and upper guide bearing into place.
5. Slide the backup ring and the new packing down the
valve shaft and into the packing chamber in the
sequence shown in Figure 3, Page A5, being sure to use
the proper lubricant if required. Then slide the packing
gland into place.
6. While holding the packing gland clamp inside the
actuator yoke (with ball bearings), slide the packing
gland clamp and yoke together onto the valve shaft so
the slots in the packing gland clamp slide over two of the
studs.
7. Secure the yoke to the valve with two nuts.
8. Screw nuts on the studs to pull the packing gland clamp
down; tighten the nuts finger tight plus 1/2 turn. They will
need to be re-tightened after the valve is pressurized.
9. For valves with service temperature of 400°F or greater,
a .005 inch gap between the plug and bottom bushing
should be adjusted, using a feeler gauge and the set
screws on top of the yoke. For all other valves snug set
screws to remove any gap between bearings and plug.
Plug should rotate freely in either case.
10. If the pipe plug was removed, coat the threads with flow
media compatible pipe compound and reinstall.
11. Lightly lubricate the beveled edge of the seat ring, then
apply a lubricant to a 1/4” wide band around the
circumference along both edges of the set ring O.D.
12. Place the seat ring into the body with the beveled edge
against the plug.
13. Coat the seat ring retainer threads with an anti-seize
compound, then install it in the body. Tighten only finger
tight.
14. Open and close the plug to align the seat to the plug and
body seating surfaces in the body. Leave the plug in the
closed position with the seat ring having both plug
contact and body contact.
15. Tighten the seat ring retainer to the torque specified in
Table A.
16. Open the valve until the plug does not contact the seat.
17. Re-torque the seat ring retainer per Table A.
K-MAX SEAT RETAINER TORQUES
TABLE A
18. The seat ring retainer should rotate less than 20 degrees
after initial torquing (Step 16); retainer movement greater
than 20 degrees may indicate problems that could result
in seat leakage.
19. Mount the actuator on the valve as described in the
Actuator Installation Section of the Actuator Instruction
Manual.
20. Test the seat by applying low pressure (50 PSIG) to the
seat side of the body with the valve in the closed
position. If seat leakage occurs, remove the retainer and
seat ring from the body and begin the reassembly
procedure at Step 11 or lap the plug/seat as described
in the following seat ring lapping section. If leakage
persists after several disassembly/reassembly
sequences, contact your local Leslie/K & M
representative.
21. Thoroughly clean the valve to the standard dictated by
your process flow media.
WARNING
REVERSE ACTUATORS - APPLY AIR TO THE
ACTUATOR TO OPEN AND HOLD THE PLUG
POSITION BEFORE REMOVING THE SEAT
RETAINER.
VALVE SEAT RETAINER TORQUE
SIZE (ft. lbs.)
175
1.5 85
2 100
3 120
4 250
6 450
8 600

Page A7
22. Install the accessories removed in Step 4 of the
DISASSEMBLY Section of this instruction.
23. Install the valve in the pipeline and connect the
permanent pneumatic and electrical connections.
24. Process pressure and flow may now be restored.
25. After the valve is pressurized, turn the packing gland
small clamp nuts clockwise only until packing leakage
stops; do not continue turning after leakage stops. If
packing leakage can not be stopped by turning the
packing gland clamp nuts clockwise, the packing must
be replaced.
F. SEAT RING LAPPING
To ensure a tight shutoff, the seat ring should be hand lapped
to both the body and the plug on metal to metal seated
valves only. Closely adhere to the following procedure to
ensure tight shutoff.
1. Apply a band of lapping compound approximately 1/4”
wide to the outer circumference of the seat ring
beginning with the edge that contacts the valve body.
2. Place the seat ring in the body, then (with light hand
pressure) move the seat ring in an orbital motion for
approximately 30 seconds.
3. Remove the seat ring and wipe off the lapping
compound.
4. Check the seat ring plug for a continuous ‘lap band’.
This appears as a dull “gray” finish on the surface of the
plug.
5. If the ‘lap band’ is incomplete on either the seat ring or
body, repeat steps 1 through 4.
6. Coat the seat ring beveled I.D. with lapping compound.
7. With the plug removed from the body, place the plug
and seat ring together in approximately the seated
position.
8. Move the seat ring against the plug in an orbital motion
for approximately 30 seconds.
F. SEAT RING LAPPING, CONTINUED
9. Separate the seat ring and plug, then wipe off the
lapping compound.
10. Check the seat ring and plug for a continuous ‘lap band’.
11. If the ‘lap band’ is incomplete on either the seat ring or
plug, repeat Steps 6 through 10.
12. Once continuous lap bands have been achieved on all
applicable surfaces, thoroughly clean the seat ring, body
and plug to remove all traces of the lapping compound.
G. VALVE REMOVAL FROM PIPELINE
It is necessary to remove the valve from the pipeline to
inspect or replace the trim components.
For your safety it is important that safety equipment be worn
when repairing this valve. The safety equipment must be
adequate to protect you from the process line medium.
1. Relieve pipeline pressure and drain the portion of the
system where the valve is located.
2. Turn off the supply air and/or electricity to the actuator
or positioner, then disconnect the piping and/or wiring
from the valve assembly.
3. Support the valve assembly to prevent slippage or
rotation, then remove the flange bolts or tie rods.
4. Remove the valve assembly from the pipeline.
5. Remove the gaskets from the valve and pipeline flanges.
Always use new gaskets when re-installing the valve.
6. Clean the flange surfaces with a wire brush to remove all
gasket particles to ensure a leakproof fit when the valve
is reinstalled.
H. ACTUATOR REMOVAL FROM VALVE
Detailed steps on how to remove the actuator from the valve
are in the ACTUATOR REMOVAL Section of the Actuator
Instruction Manual
WARNING
DO NOT LAP NICKEL PLATED PLUGS.

Page A8
TROUBLESHOOTING
The following list identifies problems with some suggestions as to what may be causing the problem. Refer to the
applicable sections of the Valve, Actuator and Positioner Instructions for detailed procedures on repairing or replacing
components.
IF... THEN...
Excessive flow through Low supply air pressure to direct acting actuator. Check air supply and adjust as
valve when closed necessary.
Diaphragm, supply air or instrument air leak on direct acting actuators.
1. Check all air connections with a water and soap mixture for leaks. Tighten or
reduce as necessary.
2. Remove actuator to bench and check for stroke with bench air. If no stroke,
replace diaphragm.
Improperly adjusted positioner. Recalibrate.
Debris in valve interfering with plug movement. Clean and recalibrate.
Insufficient flow through Low supply air air pressure to reverse acting actuator. See above.
valve when open Diaphragm, supply air or instrument air leak on reverse acting actuators.
1. Check all air connections with a water and soap mixture for leaks. Tighten or
reduce as necessary.
2. Remove actuator to bench and check for stroke with bench air. If no stroke,
replace diaphragm.
Improperly adjusted positioner. Recalibrate.
Debris in valve interfering with plug movement. Clean and recalibrate.
Jerky Actuator Motion Valve or trim improperly sized. Consult Plant Engineer.
Valve shaft packing is too tight. Loosen packing nuts.
Low air pressure to actuator. Check air supply and adjust as necessary.
Improperly calibrated positioner. Recalibrate.
Actuator does not move to Valve shaft packing is too tight. Loosen packing nuts.
fail-safe position upon loss Debris in valve interfering with plug movement. Clean and recalibrate.
of air pressure Positioner faulty or improperly adjusted. Remove, replace, recalibrate.
High air consumption Ruptured diaphragm in actuator or positioner. Replace diaphragm.
Leak in supply air system. Replace tubing and fittings.

Page A9
TROUBLESHOOTING, CONTINUED
IF... THEN...
Actuator dies not respond to Ruptured diaphragm in actuator or positioner. Replace and recalibrate.
changes in Instrument Signal Loss of supply air pressure. Restore.
Valve shaft packing is too tight. Loosen packing nuts.
Debris in valve interfering with plug movement. Clean and recalibrate.
Positioner faulty or improperly adjusted. Recalibrate.
Valve not controlling Flow and pressure conditions in flow system have changed. Consult Plant Engineer.
flow properly Malfunctioning controller, recalibrate or repair controller.
Valve shaft packing is too tight. Loosen packing nuts.
Valve or trim improperly sized. Consult Plant Engineer.
Positioner faulty or improperly adjusted. Recalibrate or replace.
Incorrect positioner cam selection. Consult Plant Engineer.
Leakage through packing Worn packing. Replace packing.
Loose gland clamp nuts. Tighten until leak stops.
Pitted or scratched packing area in valve. Replace valve body and packing.
Pitted, scratched or worn valve shaft. Replace shaft and packing.

Page A10
Code Selection Chart
KRC2W1S14TCB6N2
123456789101112131415
Class Material Valve End Valve Trim Trim Shutoff Packing Flow Actuator Spring H.O.D. Actuator
Size Conn. Rating Material Factor Class Direction Bolting
* Separable flanges available
in 1" - 6", ANSI 150-300
only.
***Yoke kit required for
third party actuation.
** Optional in 316 & CS
valves.
*** Use code 6 for shutoff
classification. TFE seats
1" - 2" Full Cv only.
Trim Factor - Position 8
1 = Full
6 = 0.6
4 = 0.4
2 = 0.2
Shutoff - Position 9
Classification (per FCI 70.2)
4 = Class IV, Standard
5 = Class V, Optional
6 = Class VI, soft seat only
Packing - Postion 10
T = Teflon-Chevron
G = Grafoil
Flow Direction - Postion 11
O = Flow to Open
C = Flow to Close
Actuator - Position 12
A = DR-40-D
B = DR-40-R
C = DR55-D
D = DR-55-R
E = DR-85-D
F = DR-85-R
G = DR-145-D
H - DR-145-R
N = None/bare stem***
Spring - Position 13
2 = 20
3 = 35
6 = 60 (Standard)
H.O.D. - Position 14
N = No
H = Handwheel
J = HandJack
Actuator Bolting - Position 15
2 = Stainless Steel
Class - Position 1 & 2
KR
Material - Position 3
C = Steel WCB
S = 316 SS
A = Alloy 20
H = Hast-C
T = Titanium
Valve Size - Position 4
0 = 1"
1 = 11⁄2"
2 = 2"
3 = 3"
4 = 4"
6 = 6"
8 = 8"
End Connection - Position 5
W = Wafer
L = CS separable flanges*
S = SS separable flange
F = Integral flanges
Valve Rating - Position 6
1 = ANSI 150
2 = ANSI 300
3 = ANSI 600
Trim Material - Position 7
S = Std 316 SS
P = Partial Stellite
F = Full Stellite
A = Alloy 20**
H = Hast C**
T = Titanium
R = 316/TFE***

Page A11
Ref.
No. Description Material Qty 1" 1.5" 2" 3" 4" 6" 8"
A1 * Upper Guide Bearing BMtl CS 1 KM1140146 KM1140148 KM1140150 KM1140152 KM1140152 KM1140154 KM1140154
A1 * Upper Guide Bearing BMtl S2 1 KM1192604 KM1192605 KM1192606 KM1192607 KM1192607 KM1192608 KM1192608
A1 * Upper Guide Bearing BMtl HC 1 KM1199622 KM1199623 KM1199624 KM1199625 KM1199625 KM1199626 KM1199626
A1 * Upper Guide Bearing BMtl T3 1 KM1216042 KM5000730 KM1207967 KM1203953 KM1203953 KM1203629 KM1203629
A2 * Plug: Full 316 No Stel S2-N 1 KM1202473 KM1202477 KM12O2481 KM1202485 KM1202489 KM1202493 KM1202497
A2 * Plug: Full 316 Part. S S2-P 1 KM1202501 KM1202502 KM1202503 KM1202504 KM1202505 KM1202506 KM1202507
A2 * Plug: Full 316 Full St S2-F 1 KM1202501 KM1202502 KM1202503 KM1202504 KM1202505 KM1202506 KM1202507
A2 * Plug: Full Hastelloy HC-N 1 KM1202476 KM1202480 KM1202484 KM1202488 KM1202492 KM1202496 KM1202500
A2 * Plug: Full Titanium T3-N 1 KM5000208 Consult Leslie KM1219430 KM1205155 KM1203954 — —
Parts List
Detail A
Flangeless Separable and
Integral Flanged
Valve Size Dimensions - Inches (mm)
ABCDE
1 4 27/16 47/16 5/32 7.62
(25) (102) (62) (113) (4.06) (194)
1.5 41/2 23/4 51/8 1/4 8.75
(40) (114) (69.8) (130) (6.35) (222)
2 47/8 213/16 47/8 7/32 9.12
(50) (124) (71.4) (124) (5.59) (232)
3 61/2 39/16 53/4 5/16 11.50
(80) (165) (90.4) (146( (7.87) (292)
4 75/8 4 7 7/16 13.38
(100) (194) (102) (178) (11.2) (340)
6 9 51/16 99/16 11/16 15.75
(150) (229) (129) (244) (16.8) (400)
8 99/16 6 11 7/8 17.75
(200) (243) (152) (279) (22.4) (438)
Detail A
* Recommended spare parts
* Always reference serial number when ordering parts * Consult factory for o-ring type guide bushings, Ref. A1 & A3.
Also for Teflon-insert seatring Ref. A23.
INSTALLATION DIMENSIONS
FIGURE 4A
PARTS IDENTIFICATION
FIGURE 4B

Page A12
Ref.
No. Description Material Qty 1" 1.5" 2" 3" 4" 6" 8"
A3 * Lower Guide Bearing BMtl CS 1 KM1140136 KM1140138 KM1140140 KM1140142 KM1140142 KM1140144 KM1140144
A3 * Lower Guide Bearing BMtl S2 1 KM1192599 KM1192600 KM1192601 KM1192602 KM1192602 KM1192603 KM1192603
A3 * Lower Guide Bearing BMtl HC 1 KM1199628 KM1199629 KM1199630 KM1199631 KM1199631 KM1199632 KM1199632
A3 * Lower Guide Bearing BMtl T3 1 KM1216056 KM5000731 KM1207971 KM1203956 KM1203956 KM1203630 KM1203630
A4 * Bushing (Plug) Trim CS 1 — — — KM1147238 KM1147238 KM1147241 KM1147241
A4 * Bushing (Plug) Trim S2 1 — — — KM1147238 KM1147238 KM1147241 KM1147241
A4 * Bushing (Plug) Trim HC 1 — — — KM1147239 KM1147239 KM1147242 KM1147242
A4 * Bushing (Plug) Trim T3 1 — — — KM1203957 KM1203957 KM1203632 Consult Leslie
A5 Pipe Plug BMtl CS 1 KM1192699 KM1192699 KM1192699 KM1192699 KM1192699 KM1192699 KM1192699
A5 Pipe Plug BMtl S2 1 KM1192698 KM1192698 KM1192698 KM1192698 KM1192698 KM1192698 KM1192698
A5 Pipe Plug BMtl HC 1 KM1190387 KM1190387 KM1190387 KM1190387 KM1190387 KM1190387 KM1190387
A5 Pipe Plug BMtl T3 1 KM1203633 KM1203633 KM1203633 KM1203633 KM1203633 KM1203633 KM1203633
A6 Body (W1,W2,W3,L1,L2) BMtl CS 1 KM1199301 KM1199302 KM1199303 KM1199304 KM1199305 KM1199306 KM1199307
A6 Body (W1,W2,W3,L1,L2) BMtl S2 1 KM1199439 KM1199440 KM1199441 KM1199442 KM1199443 KM1199444 KM1199445
A6 Body (W1,W2,W3,L1,L2) BMtl HC 1 KM1199561 KM1199562 KM1199563 KM1199564 KM1199565 KM1199566 KM1199567
A6 Body (W1,W2,W3,L1,L2) BMtl T3 1 KM5000225 KM5000022 KM1207972 KM1215100 KM1206349 KM1203635 Consult Leslie
A6 Body (F1) BMtl CS 1 KM1199308 KM1199309 KM1199310 KM1199311 KM1199312 KM1199313 KM1199314
A6 Body (F1) BMtl S2 1 KM1199446 KM1199447 KM1199448 KM1199449 KM1199450 KM1199451 KM1199452
A6 Body (F1) BMtl HC 1 KM1199575 KM1199576 KM1199577 KM1199578 KM1199579 KM1199580 KM1199581
A6 Body (F1) BMtl T3 1 KM5000749 Consult Leslie Consult Leslie KM5000398 KM5000400 Consult Leslie Consult Leslie
A6 Body (F2) BMtl CS 1 KM1199322 KM1199323 KM1199324 KM1199325 KM1199326 KM1199327 KM1199328
A6 Body (F2) BMtl S2 1 KM1199460 KM1199461 KM1199462 KM1199463 KM1199464 KM1199465 KM1199466
A6 Body (F2) BMtl HC 1 KM1199589 KM1199590 KM1199591 KM1199592 KM1199593 KM1199594 KM1199595
A6 Body (F2) BMtl T3 1 Consult Leslie Consult Leslie KM5000396 Consult Leslie Consult Leslie Consult Leslie Consult Leslie
A6 Body (F3) BMtl CS 1 KM1199336 KM1199337 KM1199338 KM1199339 KM1199340 KM1199341 KM1199342
A6 Body (F3) BMtl S2 1 KM1199473 KM1199474 KM1199475 KM1199476 KM1199477 KM1199478 KM1199479
A6 Body (F3) BMtl HC 1 KM1199603 KM1199604 KM1199605 KM1199606 KM1199607 KM1199608 KM1199609
A6 Body (F3) BMtl T3 1 Consult Leslie Consult Leslie Consult Leslie Consult Leslie Consult Leslie Consult Leslie Consult Leslie
A7 * Seat Ring: Full 316 No Stel. S2-N 1 KM1203101 KM1203121 KM1203142 KM1203164 KM1203186 KM1203208 KM1203230
A7 * Seat Ring: Full 316 P. Stel. S2-P 1 KM1203102 KM1203122 KM1203144 KM1203166 KM1203188 KM1203210 KM1203232
A7 * Seat Ring: Full 316 F. Stel. S2-F 1 KM1203102 KM1203122 KM1203144 KM1203166 KM1203188 KM1203210 KM1203232
A7 * Seat Ring: Hastelloy HC-N 1 KM1203105 KM1203125 KM1203150 KM1203172 KM1203194 KM1203216 KM1203238
A7 * Seat Ring: Titanium T3-N 1 Consult Leslie KM5000024 KM1207724 KM1210492 KM1203960 KM5000084 Consult Leslie
A7 * Seat Ring: .6 No Stellite S2-N 1 KM1203106 KM1203126 KM1203151 KM1203173 KM1203195 KM1203217 KM1203239
A7 * Seat Ring: .6 Part. Stellite S2-P 1 KM1203107 KM1203127 KM1204787 KM1204793 KM1204799 KM1204805 KM1204811
A7 * Seat Ring: .6 Full Stellite S2-F 1 KM1203107 KM1203127 KM1204788 KM1204794 KM1204800 KM1204806 Consult Leslie
A7 * Seat Ring: .6 Hastelloy HC-N 1 KM1203110 KM1203130 KM1203154 KM1203176 KM1203198 KM1203220 KM1203243
A7 * Seat Ring: .6 Titanium T3-N 1 KM5000745 Consult Leslie KM5000854 KM1215803 KM5000395 KM1203636 Consult Leslie
A7 * Seat Ring: .4 No Stellite S2-N 1 KM1203111 KM1203131 KM1203155 KM1203177 KM1203199 KM1203221 KM1203244
A7 * Seat Ring: .4 Part. Stellite S2-P 1 KM1203112 KM1203132 KM1204785 KM1204791 KM1204797 KM1204803 KM1204809
A7 * Seat Ring: .4 Full Stellite S2-F 1 KM1203112 KM1203132 KM1204786 KM1204792 KM1204798 KM1204804 Consult Leslie
A7 * Seat Ring: .4 Hastelloy HC-N 1 KM1203115 KM1203135 KM1203158 KM1203180 KM1203202 KM1203224 KM1203248
A7 * Seat Ring: .4 Titanium T3-N 1 KM5000746 Consult Leslie KM1207974 KM1205158 KM5000083 KM5000085 Consult Leslie
A7 * Seat Ring: .2 No Stellite S2-N 1 KM1203116 KM1203136 KM1203159 KM1203181 KM1203203 KM1203225 KM1203249
A7 * Seat Ring: .2 Part. Stellite S2-P 1 KM1203117 KM1203137 KM1204783 KM1204789 KM1204795 KM1204801 KM1204807
A7 * Seat Ring: .2 Full Stellite S2-F 1 KM1203117 KM1203137 KM1204784 KM1204790 KM1204796 KM1204802 Consult Leslie
A7 * Seat Ring: .2 Hastelloy HC-N 1 KM1203120 KM1203140 KM1203162 KM1203184 KM1203206 KM1203228 KM1203255
A7 * Seat Ring: .2 Titanium T3-N 1 KM5000747 Consult Leslie KM1219434 Consult Leslie Consult Leslie Consult Leslie Consult Leslie
A8 Seat Retaining Ring Trim-S2 1 KM1139636 KM1139640 KM1139644 KM1139648 KM1139652 KM1139656 KM1199350
A8 Seat Retaining Ring Trim-HC 1 KM1201697 KM1201696 KM1201693 KM1201692 KM1201694 KM1201695 KM1199617
A8 Seat Retaining Ring Trim-T3 1 KM5000748 KM5000313 KM1208950 KM1205160 KM1203962 KM5000855 Consult Leslie
A9 Flange Retaining Ring Standard 4 KM1139629 KM1139630 KM1139631 KM1139632 KM1139633 KM1139634 —
A9 Flange Retaining Ring Option S 4 KM1150019 KM1150041 KM1154190 KM1150078 KM1150089 KM1154146 —
A10 Separable Flanges (L1) Standard 2 KM1140101 KM1140104 KM1140107 KM1140110 KM1140113 KM1140116 —
A10 Separable Flanges (L1) Option S 2 KM1151699 KM1195975 KM1195976 KM1159874 KM1195977 KM1195978 —
A10 Separable Flanges (L2) Standard 2 KM1200133 KM1200134 KM1200135 KM1140111 KM1140114 KM1140117 —
A10 Separable Flanges (L2) Option S 2 KM1200136 KM1200137 KM1200138 KM1154189 KM1195984 KM1195985 —
A11 Back-Up Ring Trim-S2 1 KM1139687 KM1139687 KM1139687 KM1139688 KM1139688 KM1139689 KM1139689
A11 Back-Up Ring Trim-HC 1 KM1139690 KM1139690 KM1139690 KM1139691 KM1139691 KM1139692 KM1139692
A11 Back-Up Ring Trim-T3 1 KM1207977 KM1207977 KM1207977 KM1203964 KM1203964 KM1203639 KM1203639
A12* Packing Set TC 1 KM83000057 KM83000057 KM83000057 KM83000002 KM83000002 KM83000020 KM83000020
A12 Packing Set G1 1 KM83000058 KM83000058 KM83000058 KM83000019 KM83000019 KM83000029 KM83000029
A13 Gland Trim-S2 1 KM1199369 KM1199369 KM1199369 KM1199370 KM1199370 KM1199371 KM1199371
A13 Gland Trim-HC 1 KM1199619 KM1199619 KM1199619 KM1199620 KM1199620 KM1199621 KM1199621
A13 Gland Trim-T3 1 KM1207979 KM1207979 KM1207979 KM1204060 KM1204060 KM1206326 KM1206326
A14 Nut (Steel) 2 KM1147010 KM1147010 KM1147010 KM1141512 KM1141512 KM1141512 KM1141512
A14 Nut (316 SST) 2 KM1155548 KM1155548 KM1155548 KM1144321 KM1144321 KM1144321 KM1144321
A15 Stud (Steel) 2 KM1140219 KM1140219 KM1140219 KM1140220 KM1140220 KM1140221 KM1140221
A15 Stud (316 SST) 2 KM1192587 KM1192587 KM1192587 KM1192588 KM1192588 KM1192589 KM1192589
A16 Gland Clamp (Steel) 1 KM1139759 KM1139759 KM1139759 KM1139760 KM1139760 KM1139761 KM1139761
A17* Shaft Trim-S2 1 KM1199351 KM1199352 KM1199353 KM1199354 KM1199355 KM1206246 KM1206249
A17* Shaft Trim-HC 1 KM1199430 KM1199431 KM1199432 KM1199433 KM1199434 KM1206247 KM1206250
A17* Shaft Trim-T3 1 Consult Leslie Consult Leslie Consult Leslie Consult Leslie Consult Leslie Consult Leslie Consult Leslie
A18 Packing Nut (316 SST) 2 KM1155548 KM1155548 KM1155548 KM1144321 KM1144321 KM1144321 KM1144321
A19 Packing Stud (316 SST) 2 KM1139762 KM1139762 KM1139762 KM1139763 KM1139763 KM1139764 KM1139764
A21 Stud Block (W1) WCB 1 N/A N/A N/A N/A KM1199360 KM1199363 KM1199366
A21 Stud Block (W2) WCB 1 N/A N/A KM1199358 KM1199359 KM1199361 KM1199364 KM1199367
A21 Stud Block (W3) WCB 1 N/A N/A KM1199358 KM1199359 KM1199362 KM1199365 KM1199368
A22 O-Ring (PTFE Seat Seal † PTFE 1 Consult Leslie Consult Leslie Consult Leslie Consult Leslie Consult Leslie Consult Leslie Consult Leslie
A23 O-Ring (PTFE Seat Seal † PTFE 1 Consult Leslie Consult Leslie Consult Leslie Consult Leslie Consult Leslie Consult Leslie Consult Leslie
A26 O-Ring (Viton) † M1 1 KM1151557 KM1151557 KM1151557 KM1151563 KM1151563 KM1156484 KM1156484
A26 O-Ring (Kalrez) † M2 1 KM1203420 KM1203420 KM1203420 KM1203422 KM1203422 KM1203424 KM1203424
A27 O-Ring (Viton) † M1 1 KM1151560 KM1151560 KM1151560 KM1151566 KM1151566 KM1151636 KM1151636
A27 O-Ring (Kalrez) † M2 1 KM1203421 KM1203421 KM1203421 KM1203423 KM1203423 KM1203425 KM1203425
*Recommended spare parts
† Not Shown

Page A13
VALVE SEAT RETAINER WRENCH
FIGURE 5
DIMENSIONS
DRAWING VALVE
NUMBER SIZE ABCD E FG
.187 .850
A-27099-1 1 1-3/16 1 .200 3/16 x 3/8 1/2
.188 .840
.187 1.225
A-27099-2 1-1/2 1-1/2 5/8 .200 3/16 x 3/8 1/2
.188 1.215
.437 1.660
A-27099-3 2 2-1/2 5/8 .200 7/16 x 7/16 5/8
.438 1.650
.624 2.380
A-27099-4 3 3-3/8 5/8 .250 5/8 x 5/8 5/8
.625 2.370
.624 3.315
A-27099-5 4 4-1/2 3/4 .250 5/8 x 5/8 5/8
.624 3.305
INCHES
MILLIMETERS NO. PART NAME MATERIAL QTY.
1 NUT CARBON STEEL UNPLATED 1
2 DISC CARBON STEEL ANSI 1018 1
3 KEY STOCK M2 TOOL STEEL 1
SEAT RING
WRENCH

AIR SUPPLY
The supply pressure to the actuator must not exceed 60 psig.
The spring rating is either 20 psi, 35 psi or 60 psi and is
specified on the label affixed to the diaphragm cover.
LUBRICATION
This actuator has been lubricated at the factory and does not
require additional lubrication.
OPEN AND CLOSED POSITION STOP
ADJUSTMENTS
The procedure for adjusting the open and closed position
stops depends upon the actuator action. See the appropriate
following section for your actuator.
SPRING-TO-CLOSE ACTUATORS:
CLOSED STOP ADJUSTMENT
This adjustment is not required on valves with metal seats.
1. Relieve the air pressure to the diaphragm.
2. Loosen the jam nut on the closed stop adjusting screw
(see the Exploded Assembly on the last page of this
Instruction for parts identification).
3. Turn the closed stop adjusting screw in or out until the
valve is in the closed position. See the Instruction Manual for
the valve to determine the correct closed position for that
product line. It will be easier to turn the adjusting screw if
slight air pressure is applied to the diaphragm; relieve the air
pressure to check the adjustment.
4. Tighten the jam nut to lock the adjusting screw in place.
PAGE B14
DESCRIPTION
The Leslie Rotary Diaphragm Actuator is designed for the
Leslie K-MAX rotary control valves. It can be used for on-off
or modulating applications in either the Spring-To-Open or
Spring-To-Close mode of operation. Action can be changed
easily in the field without additional parts required.
Note: For high vibration applications, it is important
to support the diaphragm end of the actuator by the
pipeline to prevent actuator damage. Figure 1 shows
the recommended method of attaching the support
to the actuator.
CAUTION
STOP PIPELINE FLOW BEFORE REMOVING THE
ACTUATOR FROM THE VALVE. FLOW IN THE
PIPELINE WITH THE ACTUATOR REMOVED FROM
THE VALVE MAY CAUSE THE VALVE TO SLAM
SHUT. THIS COULD RESULT IN PERSONAL
INJURY AND/OR SYSTEM DAMAGE.
WARNING
THIS ACTUATOR CONTAINS A COMPRESSED
SPRING. THE POTENTIAL FOR PERSONAL
INJURY EXISTS DURING THE DISASSEMBLY /
REASSEMBLY PROCESS. CAREFULLY FOLLOW
THESE INSTRUCTIONS TO ENSURE YOUR
SAFETY.
LESLIE MODELS 40, 55, AND 85 DIAPHRAGM
ACTUATORS ON K-MAX CONTROL VALVES
VIBRATION SUPPORT & DISASSEMBLY STUDS
FIGURE 1

OPEN STOP ADJUSTMENT
1. Apply and maintain maximum supply pressure to the
diaphragm. The supply pressure must not exceed the spring
rating of the actuator.
2. Loosen the jam nut on the open stop adjusting screw.
3. Turn the open stop adjusting screw in or out until the
valve is in the open position. It will be easier to turn the
adjusting screw if air pressure to the diaphragm is relieved;
reapply air pressure to check the adjustment.
4. Tighten the jam nut to lock the adjusting screw in place.
5. Relieve the air pressure to the diaphragm.
SPRING-TO-OPEN ACTUATORS:
CLOSED STOP ADJUSTMENT
The valve seat acts as the closed stop. Do not engage the
closed stop unless shutoff is not desired.
ACTUATOR REMOVAL OF SIZE 40 ACTUATOR
To remove the diaphragm Actuator properly and safely from a
Leslie K-Max Control valve, carefully follow this procedure.
1. Stop pipeline flow. Pipeline flow must be stopped before
actuator disassembly to prevent flow system damage and/or
personal injury.
2. Scribe coinciding lines on the actuator and valve to
ensure correct alignment during actuator Installation.
3. Remove the two side covers from the actuator. See Figure
2 for parts Identification.
PAGE B15
4. Remove the pointer screws and pointer.
5. Remove the top cover from the actuator.
6. Apply air pressure to the diaphragm until the shoulder
screw in the link arm lines up with the 5/8” hole in the top of
the housing.
7.
Remove the shoulder screw and lock nut from the link arm.
8. Turn off the supply pressure to the actuator assembly,
then disconnect the supply line from the actuator.
9. Remove the two screws holding the link arm halves
together and remove the link arm.
10. Remove the two coupling-clamp screws and nuts (one
screw goes in from each side of the housing as shown in
Figure. 4) and remove the coupling clamp.
11. Remove the four bolts securing the actuator to the yoke.
12. Slide the actuator off the coupling.
13. Slide the coupling off the valve shaft.
ACTUATOR INSTALLATION OF SIZE 40 ACTUATOR
1. Turn the valve shaft counterclockwise until the valve is In
the closed position.
2. Install the link arm halves on the coupling.
3. Place the link arm coupling assembly on the valve shaft
as shown in Figure 4, Page B17. The position of the link arm
coupling Is dependent upon actuator action and the mounting
position of the actuator on the valve.
SIZE 40 ACTUATOR CUTAWAY
FIGURE 2A
REVERSING AIR ACTION
SIZE 55 & 85 ACTUATORS-REVERSE ACTION
FIGURE 2B
SPRING–TO–OPEN OPERATION
SPRING–TO–CLOSE OPERATION
SPRING–TO–OPEN OPERATION
SPRING–TO–CLOSE OPERATION

4. Remove the two socket head screws holding the link arm
halves together and remove the link arm from the coupling.
5. Slide the actuator over the coupling until It sets on the
yoke1 then secure It In place with four bolts.
6. Install the coupling clamp on the coupling. The screws
must be installed from opposite sides of the housing as
shown in Figure 4, Page B17.
ACTUATOR REMOVAL OF SIZE 55 & 85 ACTUATOR
To remove the Diaphragm Actuator properly and safely from a
Leslie valve, carefully follow this procedure.
1. Stop pipeline flow. Pipeline flow must be stopped before
actuator disassembly to prevent flow system damage and/or
personal injury.
2. If the unit is equipped with a positioner or switches, turn
off the pneumatic and electrical supplies to these accessories
and remove them from the actuator.
3. Remove the two pointer screws and the pointer.
4. Apply approximately 10 psi air pressure to the diaphragm,
then remove the cast housing cover. Removal or installation of
the housing cover without pressure on the diaphragm is very
difficult and could result in damage to the actuator or valve.
PAGE B16
5. Remove the shoulder screw from the link arm.
6. Relieve the air pressure to the diaphragm.
7. Disconnect the actuator piping.
8. Remove the four screws securing the actuator to the
mounting adaptor, then lift the actuator from the adaptor.
9. Loosen the two screws clamping the link arm to the valve
shaft, then remove the link arm.
ACTUATOR INSTALLATION OF
SIZE 55 AND 85 ACTUATOR
1. Set the valve in the closed position. The valve-closed
position is described in the Valve instruction.
2. Slide the link arm onto the shaft in the position shown in
Figure 5, Page B19.
3. Tip the actuator slightly to get it over the link arm, then set
the actuator on the mounting adaptor.
4. Secure the actuator to the adaptor with four bolts.
5. Position the link arm so its top edge is approximately
3/16” below the top edge of the actuator housing as shown in
Figure 6, Page B19.
SIZE 40 ACTUATOR SHOWN IN THE SPRING-TO-CLOSE MODE OF ACTUATION
(ACTUATOR SHOWN WITH TOP COVER AND POINTER REMOVED)
FIGURE 3

PAGE B17
6. Connect the actuator piping.
7. Apply air pressure to the diaphragm to slide the rod end
into the link arm slot; secure the rod end in place by installing
the shoulder screw.
8. Apply the minimum amount of air pressure necessary to
stroke the actuator so the link arm just contacts the stop.
9. Position the stub shaft as shown in Figure 4. Turn the stub
shaft only, not the link arm.
10. Tighten the screws to clamp the link arm to the valve
shaft.
11. Make sure the stub shaft 0-ring is in place, then place the
gasket and cover on the housing.
COUPLING CLAMP SCREWS
(Size 40 only)
FIGURE 4
ACTUATOR MOUNTING POSITION OF HOLE IN LINK ARM IN
ACTION POSITION RELATIONSHIP TO SEAT END OF VALVE
DIRECT Standard 1 Tooth Counterclockwise from 6 o’clock
DIRECT 90º 1 Tooth Counterclockwise from 9 o’clock
DIRECT 180º 1 Tooth Counterclockwise from 12 o’clock
DIRECT 270º 1 Tooth Counterclockwise from 3 o’clock
REVERSE Standard 1 Tooth Counterclockwise from 12 o’clock
REVERSE 90º 1 Tooth Counterclockwise from 3 o’clock
REVERSE 180º 1 Tooth Counterclockwise from 6 o’clock
REVERSE 270º 1 Tooth Counterclockwise from 9 o’clock
CORRECT POSITION OF LINK ARM ON VALVE SHAFT
FIGURE 5
ACTUATOR MOUNTING POSITIONS
STANDARD 90º 180º 270º
SEAT
END
SEAT
END
SEAT
END
SEAT
END

PAGE B18
12. Relieve the pressure to the diaphragm.
13. Attach the pointer to the stub shaft.
14. Install any accessories removed.
15. Check the open and closed position stops and readjust if
necessary.
16. Pipeline flow may now be restored.
SPRING ASSEMBLY REPLACEMENT
1. Stop pipeline flow. Pipeline flow must be stopped before
actuator disassembly to prevent flow system damage and/or
personal injury.
2. Remove the two pointer screws and the pointer.
3. Apply approximately 10 psi air pressure to the diaphragm,
then remove the cast housing cover. Removal or installation of
the housing cover without pressure on the diaphragm is very
difficult and could result in damage to the actuator or valve.
4. Remove the shoulder screw from the link arm.
5. Relieve the air pressure to the diaphragm.
6. Disconnect the actuator piping.
7. Remove three of the bolts that fasten the diaphragm
cover to the spring case. Equally space the bolts as shown in
Figure 1.
8. For size 40 actuators, use 1/4” threaded rod, 3” long. For
size 55 and 85 actuators, use 3/8” threaded rod, 8” long.
Install the threaded rod about in each of the three holes, then
install and tighten nuts on each end of the rods. Refer to
Figure 1, PAGE B14.
9. Remove the remaining diaphragm cover bolts.
10. Slowly and evenly back out the nuts on the threaded rod
until all the spring pressure is relieved, then remove the nuts
and diaphragm cover.
11. Remove the rubber diaphragm.
12. Pull the spring assembly out of the spring case.
UNDER NO CIRCUMSTANCE IS THE SPRING
ASSEMBLY TO BE DISASSEMBLED. DISAS-
SEMBLY COULD RESULT IN PERSONAL INJURY.
WARNING
THIS ACTUATOR CONTAINS A COMPRESSED
SPRING. THE POTENTIAL FOR PERSONAL INJURY
EXISTS DURING THE DISASSEMBLY/REAS-
SEMBLY PROCESS. CAREFULLY FOLLOW THESE
INSTRUCTIONS TO ENSURE YOUR SAFETY.
13. Remove the rod end from the old spring assembly and
screw it into the new spring assembly until about 1/4” of
threads remain showing.
14. Slide the new spring assembly into the spring case so the
two pins in the spring fit into the two holes in the housing
15. Place the diaphragm on the spring case, then set the
diaphragm cover on the diaphragm.
16. Fasten the spring case, diaphragm and diaphragm cover
together using bolts and nuts, in the reverse of the removal
sequence descibed in 7,8,9,10 above. .Place the CAUTION
tag under one of the bolts.
17. Connect the actuator piping.
18. Apply air pressure to the diaphragm to slide the rod end
into the link arm slot; secure the rod end in place by installing
the shoulder screw.
19. Make sure the stub shaft 0-ring is in place, then place the
gasket and cover on the housing.
20. Relieve the pressure to the diaphragm.
21. Attach the pointer to the stub shaft.
22. Check the open and closed position stops and readjust if
necessary.
23. Pipeline flow may now be restored.
DIAPHRAGM REPLACEMENT
1. To disassemble, follow Steps 1 thru 11 in the REPLACING
THE SPRING ASSEMBLY Section of this Instruction.
2.
To reassemble, follow Steps 15 thru 23 in the REPLACING
THE SPRING ASSEMBLY Section of this Instruction.
REVERSING THE ACTION
1. Stop pipeline flow. Pipeline flow must be stopped before
actuator disassembly to prevent flow system damage and/or
personal injury. Refer to Figure 2, Page B15.
2. Remove the two pointer screws and the pointer.
3. Apply approximately 10 psi air pressure to the diaphragm,
then remove the cast housing cover. Removal or installation of
the housing cover without pressure on the diaphragm is very
difficult and could result in damage to the actuator or valve.
4. Remove the shoulder screw from the link arm.
5. Relieve the air pressure to the diaphragm.
6. Disconnect the actuator piping.
7. Remove the actuator from the adaptor.
8. Loosen the two cap screws on the link arm.
9. Mark the position of the link arm on the shaft. Remove
the link arm, rotate it 180 degrees from its previous position,
then reinstall it on the valve.
Table of contents
Other Leslie Control Unit manuals
Popular Control Unit manuals by other brands
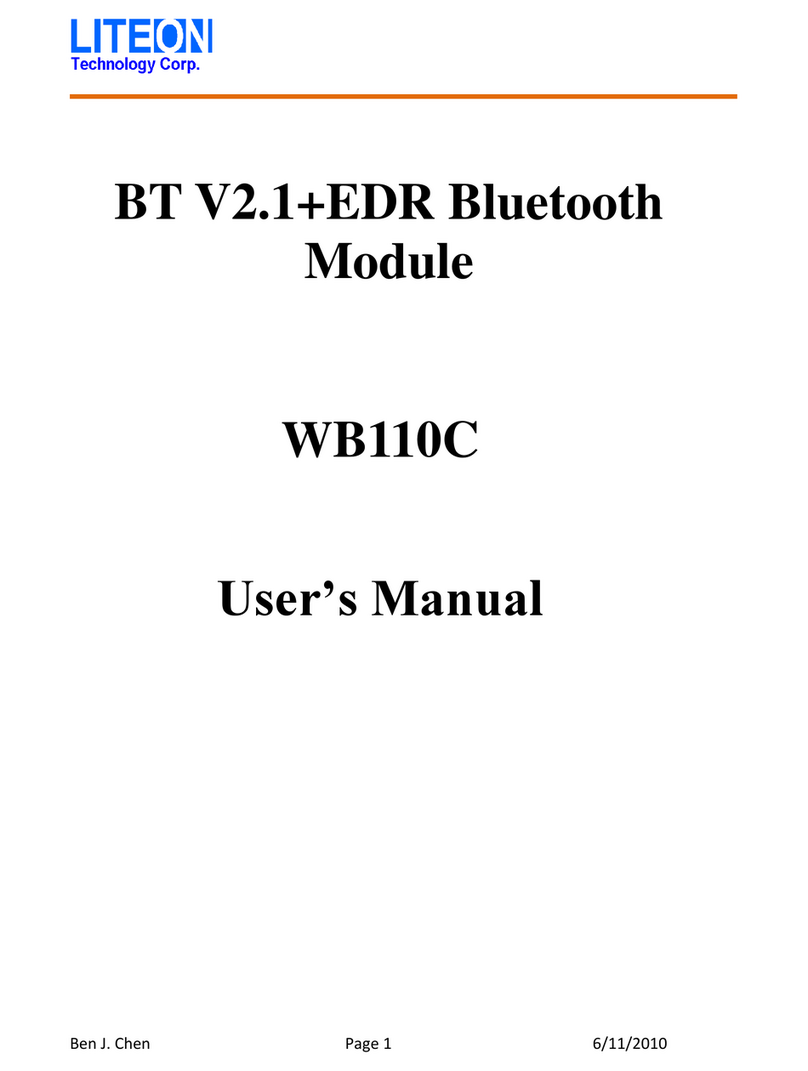
LiteOn
LiteOn WB110C user manual
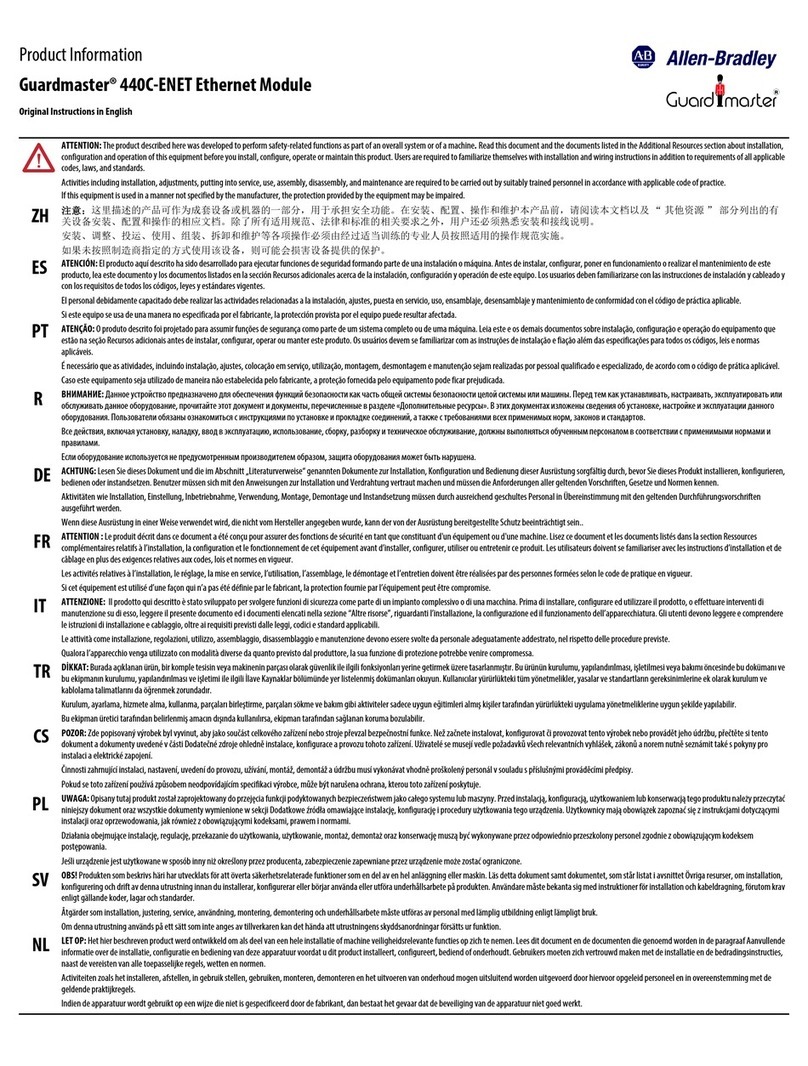
Allen-Bradley
Allen-Bradley Guardmaster 440C-ENET Original instructions
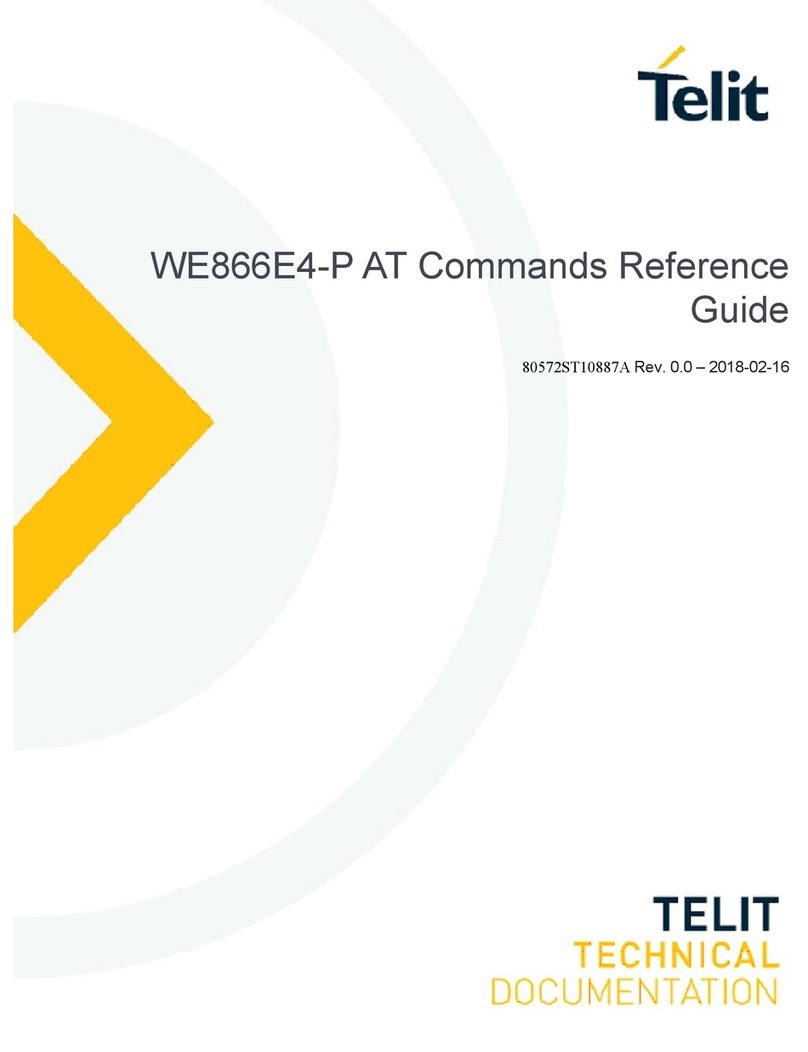
Telit Wireless Solutions
Telit Wireless Solutions WE866E4-P AT Commands Reference Guide
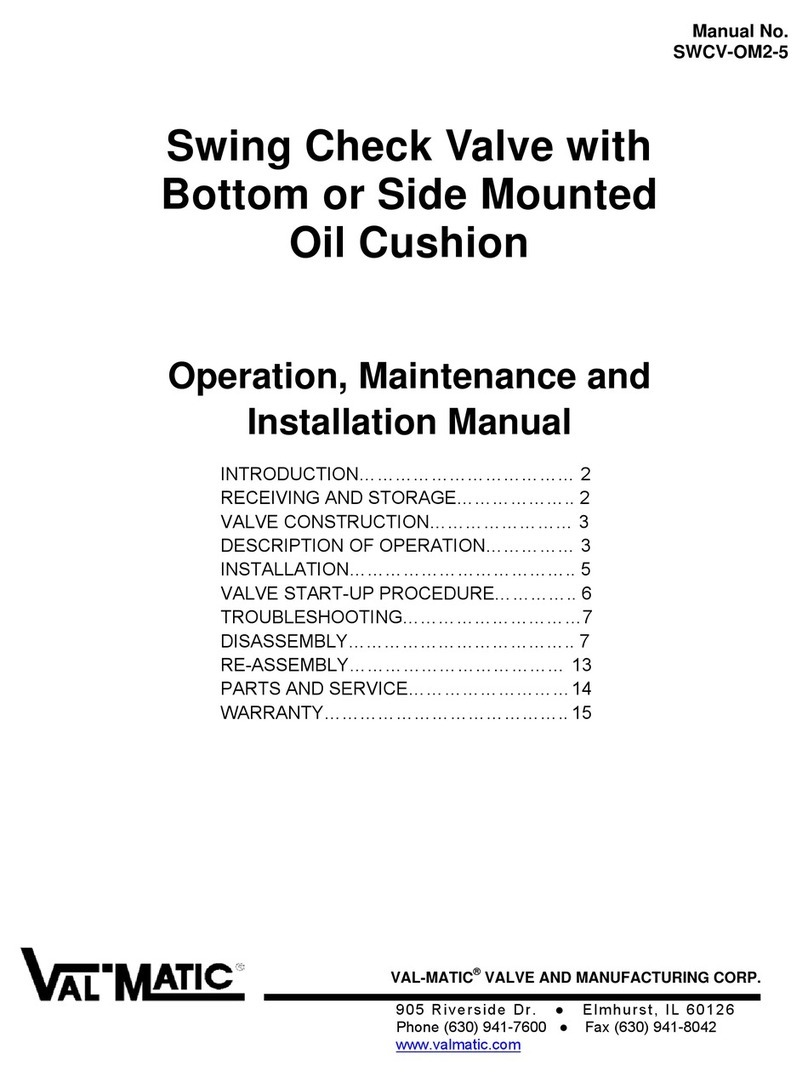
Val-Matic
Val-Matic SWCV-OM2-5 Operation, maintenance and installation manual

Teledyne Lecroy
Teledyne Lecroy SAM40 Operator's manual
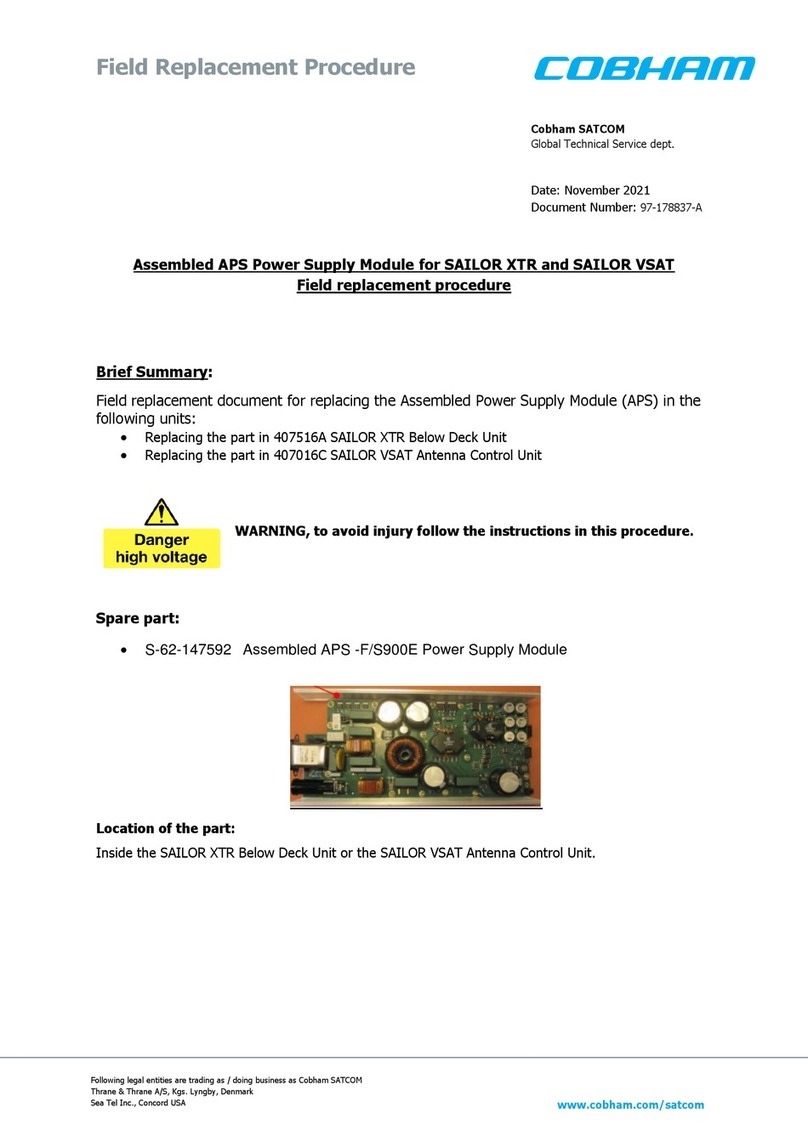
COBHAM
COBHAM SAILOR XTR Field Replacement Procedure