Lippert Titan Leveling Systems User manual

Titan Leveling Systems™
Sprinter Cab Mount
(4 Valve/4 Jack)
OEM INSTALLATION MANUAL

Rev: 10.23.23 Page 2 CCD-0005481
TABLE OF CONTENTS
System Information 3
Component Description 3
Safety 4
Resources Required 4
Preparation 5
Installation 6
Prior to Installation 6
Jack Specications 6
Jack Fittings 6
Hydraulic power unit Installation 7
Hydraulic Hoses 8
Prepping the Front Jack Bracket Installation 9
Front Jack Bracket Installation 10
Rear Jack Bracket and Jack Installation 12
LED Touch Panel / Controller Installation 13
System Wiring Requirements 14
Prior to Operation 15
LED Touchpad Controller Operation 15
Level Zero Point Calibration 19
Installing the Aluminum Crossbars 22
Installing the Steel Front Crossbar 23
Troubleshooting 25
Manual Override - Jacks 25
Manual Override - Power System 25
Audible Alarm Modes 26
Preventative Maintenance Procedures 26
Fluid Recommendation 26
Solutions to Possible System Errors 27
Hydraulic Plumbing Diagram 28
LED Wiring Diagram 29
Notes 30

Rev: 10.23.23 Page 3 CCD-0005481
System Information
The four-point, four-valve hydraulic leveling system is a hydraulic system which includes four points of
contact utilizing jacks (Fig. 1) and a four-valve system. A 12V DC electric motor drives a hydraulic pump (Fig.
6) that moves fluid through a system of hoses, fittings and jacks to level and stabilize the coach. Mechanical
portions of the hydraulic leveling system are replaceable. Contact Lippert to obtain replacement parts. The
hydraulic leveling system is primed and tested at the factory. However, the system is shipped dry to avoid
hazardous material restrictions.
Component Description
1. Jacks
A. (4) 8K, 13" stroke , aluminum jacks (Fig. 1)
B. Rated at a lifting capacity for the coach.
C. Standard 9-inch diameter (63.5 square inch) footpad on a ball swivel for maximum surface contact
on all surfaces.
D. Operational powered from a 12V DC motor/pump assembly.
2. Motor/Pump Assembly
A. 12V DC motor
B. Hydraulic fluid reservoir tank
C. Control valve manifold
D. Solenoid valve
3. System Controls
A. Controlled electronically from the touchpad.
B. Touchpad can be operated in manual mode or fully automatic mode.
4. Fittings and Hoses
A. Fittings - J.I.C. - Size 4
B. Hose - ¼" I.D., 3000 psi - W.P. Rated
Fig. 1
18"

Rev: 10.23.23 Page 4 CCD-0005481
Always wear eye protection when performing service, maintenance or installation procedures.
Other safety equipment to consider would be hearing protection, gloves and possibly a full face
shield, depending on the nature of the task.
The “CAUTION” symbol above is a sign that a safety risk is involved and may cause personal injury
and/or product or property damage if not safely adhered to and within the parameters set forth
in this manual.
During servicing make sure that the coach is supported according to the manufacturer's
recommendation. Lift the coach by the frame and never the axle or suspension. Do not go under
the coach unless it is properly supported. Unsupported coaches can fall causing death or personal
injury or product or property damage. Use proper personal protective equipment.
Moving parts can pinch, crush, or cut. Keep clear and use caution
Resources Required
• 1 to 2 people, depending on task
• Cordless or electric drill or
screw gun
• Appropriate drive bits
• Appropriate drill bits
• Assorted deep well sockets
• Ratchet wrench
• Torque wrench
• Open end wrenches
• 13mm socket
• 1/2" socket
• 15/16" wrench
• 3/8" drive 6" long extension
• 7/32" allen head
• 1/2" wrench
• 5/8" socket
• 9/16" wrench
• 9/16" socket
• 3/4" wrench
• 3/4" socket
• Pliers
• Flathead screwdriver / knife
• Permanent marker or grease pencil
• Tape measure
• Assorted screwdrivers
• (4) #8 x 1" fasteners
• (4) #6 x 1" Wood Screws
• T-25 torx bit (3" long)
• Labels for hoses
• Zip ties
• White spray paint
• Extend (black) and
retract (orange) hydraulic
hoses and fittings
Safety
Read and understand all instructions before installing or operating this product. Adhere to all safety labels.
This manual provides general instructions. Many variables can change the circumstances of the instructions,
i.e., the degree of difficulty, operation and ability of the individual performing the instructions. This
manual cannot begin to plot out instructions for every possibility, but provides the general instructions,
as necessary, for effectively interfacing with the device, product or system. Failure to correctly follow the
provided instructions may result in death, serious personal injury, severe product and/or property damage,
including voiding of the Lippert limited warranty.
The "WARNING" symbol above is a sign that a procedure has a safety risk involved and may cause death
or serious personal injury if not performed safely and within the parameters set forth in this manual.
Failure to follow instructions provided in this manual may result in death, serious personal injury
and/or severe product and property damage, including voiding of the component warranty.

Rev: 10.23.23 Page 5 CCD-0005481
Preparation
1. Make sure to park the coach on solid and level ground.
2. Clear all jack landing locations of debris and obstructions.
3. Keep hands and other body parts clear of fluid leaks. Hydraulic system leaks in the hydraulic leveling
system may be under high pressure and can cause serious skin-penetrating injuries.
Never lift the coach completely o the ground. Lifting the coach so the wheels are not touching the
ground will create an unstable and unsafe condition. Do not lift the coach by the axles.
The axles were not designed as a viable lift point.
1. Using the properly-rated floor jack, support framework and lift the coach according to the
manufacturer's recommendations.
NOTE: A recommended minimum ground clearance between the bottom of the jack footpad and the
ground is 7-9" (Fig. 2). Rear jacks are not adjustable in height, recommend proving optimum range
of 7-9" of ground clearance for the rear jacks. Front jacks have two positions, typically use 2nd hole
in jack to 2nd hole in bracket, optimum ground clearance of 6-7.5" up front.
2. Determine how and where the jack will be bolted to the frame of the coach.
3. Check for any obstructions, such as slide-out cross shafts, outriggers or manual override connections
for slide-outs that will require modification of the brackets prior to bolting on.
4. Locate and move any wires, hoses, etc. that could be damaged while bolting on the jack brackets to
the frame. Check both the inside and outside of the frame.
Fig. 2
Recommended 7-9"
Minimum Clearance
Departure Angle
Rear Tire
Ground
Rear of
Coach

Rev: 10.23.23 Page 6 CCD-0005481
Fig. 3
Installation
Prior to Installation
Refer to the Hydraulic Plumbing Diagram (Fig. 51) for the following steps:
1. Identify where the extend (Fig. 3A) and retract ports (Fig. 3B) are on the jack.
2. Verify that the ports are clear of any residual machining metal debris.
3. Label each jack Left Front (LF), Right Front (RF), Right Rear (RR) or Left Rear (LR).
Jack Specifications
Because of various possible configurations, this manual will provide instructions with the hydraulic power unit
mounted near the center of the coach frame, roadside frame rail. Fittings and hose configurations may be OEM
specific. Under normal installation procedures, the jacks closest to the hydraulic power unit get plumbed first.
See the Hydraulic Plumbing Diagram (Fig. 51) for the hydraulic power unit located on the left side of the coach.
CAPACITY - 8,000 lbs. max. STROKE - 13" FOOTPAD 9" DIA. STANDARD
Extend Port
Extend Port Retract Port
Retract Port
AB
Top view of the
jack, without
hydraulic fittings.
Jack Fittings
1. The hydraulic fittings (Fig. 4) for the hydraulic power unit (Fig. 6) can be installed per figure 6 and the
the Hydraulic Plumbing Diagram (Fig. 51). Remove the port plugs corresponding to the appropriate
hoses needed for each jack at their respective location, see Hydraulic Plumbing Diagram (Fig. 51).
Use JIC swivel 90° elbow fittings (Fig. 5) for the jacks and jack hose connections. All jack fittings should
be on the inside face of the jack, towards the center of the coach.
Fig. 4
JIC Elbow Fitting JIC Swivel 90° ElbowJIC Straight Fitting
Fig. 5

Rev: 10.23.23 Page 7 CCD-0005481
Hydraulic Power Unit Installation
NOTE: The location where the hydraulic power unit will be installed should be as near center on the coach
as possible. Install the hydraulic power unit in accordance with RVIA Gas Codes, since the hydraulic
power unit connections are not spark proof.
2. Identify the hydraulic power unit mounting location. This will determine the orientation of the
hydraulic fittings (Fig. 6). For this manual, the hydraulic power unit is mounted on the inside driver's
side frame rail, behind the fuel tank.
3. Attach hydraulic power unit bracket assembly (Fig. 7A) to the coach frame using the 7/16"-14 x 4 1/2"
bolts on the outer clamp and the 7/16" - 14 x 2" bolts on the inner clamp (Fig. 7).
4. Bolt the hydraulic power unit to the bracket assembly using the provided manufacturer's screws.
Motor
Frame Rail
Driver Side
A
Outer Clamp
Fig. 6
Fig. 7
Reservoir
Pressure
Switch
Hydraulic
Power Unit
Reservoir
Inner Clamp
Motor
Valve Coil
Solenoid
Quick Disconnect
Retract
Fittings
Cartridge Valve
Valve Coil
Extend
Fittings
Valve Coil
Cartridge
Valve
Manifold
Quick
Disconnect
Directional
Valve
Cartridge
Valve
Valve Coil

Rev: 10.23.23 Page 8 CCD-0005481
Hydraulic Hoses
NOTE: Verify that the hydraulic fittings were installed on the four jacks and hydraulic power unit correctly.
A 7/16” port plug (Fig. 8) will be used to seal any ports not used within the system.
When installing hydraulic hoses, avoid areas of high heat, e.g. exhaust outlets. Do not use sharp or abrasive
materials on or near hydraulic hoses.
• Left Front Extend
• Right Front Extend
• Left Rear Extend
• Right Rear Extend
1. Measure the distance between the left front jack and the hydraulic power unit; this is an extend hose
(Fig. 51A).
2. Measure the distance between the right front jack and the hydraulic power unit; this is an extend hose
(Fig. 51B).
3. Measure the distance between the left rear jack and the hydraulic power unit; this is an extend hose
(Fig. 51C).
4. Measure the distance between right rear jack and the hydraulic power unit; this is an extend hose
(Fig. 51D).
5. Measure from the left front jack to the front manifold extend fitting on the hydraulic power unit; this is
a retract hose (Fig. 51E).
6. Measure from the left rear jack to the rear manifold extend fitting on the hydraulic power unit; this is a
retract hose (Fig. 51F).
7. Measure from the right front jack to the front extend fitting on the hydraulic power unit; this is a retract
hose (Fig. 51G).
8. Measure from the right rear jack to the rear extend fitting on the hydraulic power unit; this is a retract
hose (Fig. 51H).
NOTE: Make sure hydraulic hose line fittings are compatible with the hydraulic power unit fittings and the
jack fittings. Make sure hose fittings are securely crimped onto the hose lines.
9. When running the hydraulic hoses from the hydraulic power unit to the jacks, bundle the hoses together.
Secure any loose hoses with zip ties as needed.
10. Install all hoses onto the corresponding jacks and hydraulic power unit fittings.
NOTE: Hose loops should be secured in the horizontal position to prevent trapped air pockets.
NOTE: Before operating the Lippert hydraulic leveling system, make sure the system has been properly
purged of air that was introduced into the hydraulic lines during the installation.
NOTE: If necessary, refer to TI-118 for Hydraulic Operation Fluid Recommendation.
• Left Front Retract
• Right Front Retract
• Left Rear Retract
• Right Rear Retract
NOTE: Refer to the Hydraulic Plumbing Diagram (Fig. 51) for fitting placements and for steps 1 - 8.
Labels on hoses:
Fig. 8

Rev: 10.23.23 Page 9 CCD-0005481
Prepping the Front Jack Bracket Installation
1. Starting with the passenger side, remove the black molded plastic step well cover (Fig. 9D) in the cab
of the coach.
A. Remove the top trim piece (Fig. 9C) located on the top of the step well area (Fig. 9A). There are two
caps (Fig. 9C) and torx screws (Fig. 9D). Use a flathead screwdriver/knife to pry up the caps and a
T-25 torx bit to remove the screws, set trim, caps and hardware aside to re-install.
B. There are three tapered caps (Fig. 10A) in the bottom of the step well area (Fig.10C). Use a flathead
screwdriver/knife to remove them by pulling outward and up to slide the caps out. Remove the
screws (Fig. 10B) black molded plastic step well cover and caps from the chassis frame and set
aside to re-install.
2. Remove any foam material (Fig. 11A) at the side of the stepwell that might impede installation and set
aside to reinstall.
3. Place the drill template (Fig. 11B) on the stepwell making sure the corner of the template (Fig. 11C)
is in the rear corner of the step well and the bottom of the template is setting flat against the floor
of the step. Mark the four holes (Fig. 11D).
4. Remove the template and drill the four holes with a 9/16" drill bit.
5. Apply white spray paint to the four holes (Fig. 12A), let dry.
6. Repeat steps 1-5 for the driver's side, flipping the template for the driver's side.
Fig. 9
D
C
A
B
Fig. 10
A
B
C
Fig. 11 Fig. 12
AB
CDA

Rev: 10.23.23 Page 10 CCD-0005481
Front Jack Bracket Installation
1. Assemble the two jack brackets (Fig. 13A) on the Passenger Side front jack . Secure the brackets by
using two ½” - 13 X 3 1/2” bolts (Fig. 13D) and two ½” - 13 lock nuts (Fig. 13E). Torque to 90 ft/lbs. Take
note that brackets A have two gussets on each bracket.
2. Assemble the two jack brackets (Fig. 13 A and B). Secure the brackets by using two ½” - 13 X 3 1/2” bolts
(Fig. 13D) and two ½” - 13 lock nuts (Fig. 13E). Torque to 90 ft/lbs. Take note that bracket B has one gusset
where the other three have two gussets.
3. At the bottom, rear facing side of the Titan Jack (Fig. 14A), remove the extend port plug and attach a
straight fitting (Fig. 14D) and swivel elbow retract fitting (Fig. 14E). Attach the pre-measured black extend
hose (Fig. 14F).
Fig. 13
C
D
Brackets
installed
against
the coach
cab wall.
Retract Port
NOTE: A recommended minimum ground clearance between the bottom of the jack footpad and the
ground, is 7-9" when the coach is at its maximum rated weight. When installing the jacks on a bare
chassis, keep in mind that some ground clearance will be lost as the coach is built, and to adjust the
installation height accordingly. Make sure that the approach and departure angles are maintained
after the jack is mounted to the jack bracket. Mark the location on both the inside and outside frame
rails that satisfies the minimum clearance requirements.
NOTE: Dry fit the jack bracket assembly on the chassis frame, noting which holes will align with the holes
in the cab step well while satisfying the minimum ground clearance. Note which holes to attach the
bracket to the jack for the opposite side installation.
Mounting hole edges on the backside of the jack (Fig. 13E) may be sharp and should be handled
with care. Serious personal injury may occur if not using safety equipment such as gloves
when handling the jacks.
F
Extend Port
A
A
D
E
Brackets placed
underneath
the chassis frame.
Same extend
and retract ports
on opposite side.
B
A
Brackets
installed
against
the coach
cab wall.
Extend Port
Retract Port
F
C
D
D
E
Passenger Side Driver's Side

Rev: 10.23.23 Page 11 CCD-0005481
Fig. 14
A
C
B
E
D
F
Passenger side
front jack assembly
4. Position the jack assembly (Fig. 15A) onto the frame rail (Fig. 15B). Clamp or have another person hold
the jack in place, making sure the bolting surface of the mounting brackets line up with the holes
drilled in the frame.
5. From the step well side, insert four 7/16"- 14 x 1 1/4" bolts (Fig. 16A) with 7/16" flat washers (Fig. 16B),
through the hole in the cab wall (Fig. 16C), into the appropriate jack bracket holes (Fig. 15F).
6. At the jack bracket, attach but do not tighten the 7/16" lock washers (Fig. 15D) and nuts (Fig. 15C)
on the four bolts (Fig. 15E).
7. Make sure the jack is straight, and the bracket (Fig. 15A) is tight to the bottom of the frame (Fig. 15B)
before tightening the 7/16" bolts with a 11/16" wrench, 5/8" socket to 50 ft-lbs.
8. Re-install step well cover and trim with original torx screws and tapered plugs.
9. Repeat steps 1-8 for the driver's side.
10. Attach the opposite ends of the extend and retract hoses to the hydraulic pump, see the Hydraulic
Plumbing Diagram section, Figure 51.
Fig. 15 Fig. 16
CDF
AB
A
B
E
C

Rev: 10.23.23 Page 12 CCD-0005481
Rear Jack Bracket and Jack Installation
1. Turn the rear jack so that the built-in bracket for the bolts (Fig. 17A) are facing the rear of the coach. At
the bottom of each inside face of the jack (Fig. 17B), remove the retract and extend port plugs and attach
two JIC 90 degree elbow retract fittings (Fig. 17C). Attach the pre-measured orange retract (Fig. 17D)
and black extend hoses (Fig. 17E).
NOTE: Jack brackets can also face the front of the coach, utilizing the front pair of holes in the frame.
Fig. 17
CC
E
Driver's side
rear jack assembly
NOTE: A recommended minimum ground clearance between the bottom of the jack footpad and the
ground, is 7-9" when the coach is at its maximum rated weight. When installing the jacks on a bare
chassis, keep in mind that some ground clearance will be lost as the coach is built, and to adjust the
installation height accordingly. Make sure that the approach and departure angles are maintained
after the jack is mounted to the jack bracket. Mark the location on both the inside and outside frame
rails that satisfies the minimum clearance requirements.
2. At the appropriate height, place the jack assembly up against the inside beam of the extension bracket (Fig 18A).
NOTE: Bolt length may vary depending on OEM frame extension, but must be a grade 8.
3. Insert two 1/2" - 13 x 8" bolts (Fig. 18B) with 1/2" flat washers (Fig. 18C), through the extension and into
the pre-drilled extension jack bracket holes (Fig. 18D).
4. Attach 1/2" - 13 lock nut (Fig. 19A) to each bolt and tighten to 90 ft-lbs.
5. Repeat steps 1-4 for the passenger side.
6. Attach the opposite ends of the extend and retract hoses to the hydraulic pump, see the Hydraulic
Plumbing Diagram section, Figure 51.
A
B
D
Fig. 18
A
B
C
D
B
C
Fig. 19
A
A

Rev: 10.23.23 Page 13 CCD-0005481
LED Touch Panel / Controller Installation
Images used in this document are for reference only when assembling, installing and/or operating this
product. Actual appearance of provided and/or purchased parts and assemblies may differ.
The front panel orientation of the touch panel / controller must be either in an X axis (roadside/curbside)
orientation or Y axis (front/rear) orientation (Fig. 20). It must be placed on a vertical surface. The front panel
screen is splash resistant but is not water proof and should be installed inside of the coach.
1. In the designated mounting location, cut a hole (on a vertical surface) (Fig. 21B), 4 1/4" square, for the
bezel of the LED touch panel/controller (Fig. 21A) to fit into.
2. Attach the LED touch panel/controller 9 pin harness (Fig. 21C) to the 9 pin power unit harness
(Fig. 27D) and feed through the pre-cut hole (Fig. 21A), running the opposite end of the wire harness
to the hydraulic power unit. See the Wiring Diagram section, Figure 47.
3. Attach the LED touch panel/controller 6 pin harness (Fig. 21E) to the 6 pin chassis harness
(Fig. 21F) and feed through the pre-cut hole (Fig. 21A), running the opposite end of the chassis
wire harness to the ignition positive power source and the parking brake ground. See the Wiring
Diagram section, Figure 47.
Fig. 20
Fig. 21
C
E
B
D
F
A
4 1/4"
4 1/4"
Y
X
AXIS
AXIS

Rev: 10.23.23 Page 14 CCD-0005481
Fig. 22
4. Insert the touch panel (Fig. 22A) into the cutout hole, and attach it to the mounting surface with four
#6 x 1" wood screws (Fig. 22B). Verify that the screws are of sufficient length to thread into the
mounting surface.
System Wiring Requirements
NOTE: Ground wires are OEM supplied.
1. Battery power cable with an OEM-supplied breaker (RVIA standard).
2. Battery ground cable (RVIA standard) connecting the 12V DC battery, to the ground post on the
hydraulic power unit motor.
NOTE: Lippert recommends connecting the ground cable directly to the battery, rather than a chassis
ground point.
3. Leveling jack status input - pressure switch.
A. Jacks not all up – switch closed to ground .
B. Jacks all up – switch open.
4. Connect the six-pin chassis harness to the "Ignition On" wire and the parking brake signal wire.
A. White - Parking Brake (open = park brake disengaged, GND = park brake engaged).
B. Red - 12V Ignition, Logic power (ignition switch controlled).
B
A

Rev: 10.23.23 Page 15 CCD-0005481
Prior to Operation
The leveling system shall only be operated under the following conditions:
1. The coach is parked on a reasonably level surface, engine running.
2. The coach “parking brake” is engaged.
3. The coach transmission should be in the park position.
4. Be sure to keep hands and other body parts clear of fluid leaks. Oil leaks in the Lippert Leveling System
may be under high pressure and can cause serious skin penetrating injuries.
5. Never lift the coach completely off the ground. Lifting the coach so the wheels are not touching
ground will create an unstable and unsafe condition.
Lifting all wheels off the ground may result in serious personal injury or death.
LED Touchpad Controller Operation
1. Figure 23 is the default screen when coach ignition is ON and assigned to the “Home” icon (Fig. 23A).
The LED Touchpad Controller is only ON while the coach ignition is ON, no operation of leveling will be
allowed without ignition source. Parking Brake MUST be engaged for the system to operate.
2. Figure 24 is assigned to “menu” icon (Fig. 24A).
A. (Fig. 24B) MANUAL MODE ability to extend jacks in pairs.
B. (Fig. 24C) CONNECT APP with phone Bluetooth on, click button to search on phone for “Auto
Level, Titan” or similar.
C. Select the “menu” icon (Fig. 24A) and then CALIBRATION icon (Fig. 24D) is a required step to
program the control's orientation and define a level plane. Initial calibration will be set by OEM but
operator may perform calibration again at a later date to ensure the system is at a level plane.
D. (Fig. 24E) JACK LIGHTS on/off button, turns on all LED lights located on the front and rear
crossbars, close to each of the jacks. Lights are optional and this button may not be used.
Fig. 23 Fig. 24
AA
B
C
D
E
Home Screen Menu Screen
B
C

Rev: 10.23.23 Page 16 CCD-0005481
3. Figure 25 is assigned to “Manual Mode” button from menu screen (Fig. 24B). Each button, ex. Extend
Front (Fig. 25A) is a button that operates both front jacks. Each button is a pair of jacks and only
extends the jacks.
4. Figure 26 is the screen displayed during the leveling process.
5. During the, “Auto Level” process, (Fig. 23B), the "Leveling Error" screen (Fig. 27) will appear if:
• The control senses movement in the coach during the leveling process.
• Too much time has passed since the procedure started.
• Jack cylinders have reached full stroke so extend cannot occur.
• Coach is parked on too great of an incline (typically over 4.5 degrees) and cannot complete level
process.
6. To exit the Leveling Error screen, press Home (Fig. 27A) or Menu (Fig. 27B) icons.
Fig. 26
Leveling In Progress
Fig. 25
Manual Mode
A
Fig. 27
Leveling Error
Fig. 28
Jacks Are Retracting
A B

Rev: 10.23.23 Page 17 CCD-0005481
7. During the, "Retract Jacks" (Fig. 23C), or in "Manual Mode", (Fig. 24B), Figure 28, "Jacks Are Retracting"
screen is displayed.
8. Figure 29, "Parking Brake Error", will appear when no parking brake signal is received and there is no
pressure switch signal indicating jacks are still retracted. The screen is prompted before auto level and
manual mode functions. The screen is prompted for five seconds, then returns to home screen (Fig.
23).
If jacks are extended and parking brake signal is lost, jacks will automatically retract.
9. Figure 30, "Insufficient Voltage", screen may be prompted before or during “Auto Level”,
“Retract Jacks” or “Manual Mode” functions. This screen is prompted when the control is receiving
less than 10.5 volts for auto level function 7.5 volts.
Fig. 29
Parking Brake Error
Fig. 30
Insufficient Voltage

Rev: 10.23.23 Page 18 CCD-0005481
10. Figure 31, "Retract Error" screen will appear if with ignition on and touchpad on or in “sleep” mode
(display off, power to control still on). If the control receives signal from the pressure switch (meaning
the internal pressure of the hydraulic system has dropped below 2,150 psi, connection lost from
pressure switch to control), the control enters retract all mode. If pressure switch does not open
back up after 10 seconds, the audible alarm can be prompted (2 seconds on, two seconds off, 70-85
decibels), jacks will stop retracting and this screen to be displayed. Alarm to run until coach ignition
is off or pressure switch opens up indicating that optimal pressure is reached. DO NOT ignore this
alarm, there may be a jack down or component failure, possibly making it dangerous to drive. Operator
can use the home or menu icon and reach “retract jacks” function.
Fig. 31
Retract Error
11. Figure 32, "Level Success!" screen is prompted after auto level feature has successfully completed.
Accompanied by an audible charm (3 seconds long). Screen stays active for 5-10 seconds, then returns
to home screen (Fig. 23).
Fig. 32
Level Success!
AB

Rev: 10.23.23 Page 19 CCD-0005481
Level Zero Point Calibration
After the system is installed and power is supplied, the Zero Point needs to be calibrated on the LED
touchpad controller, prior to operating the jacks. Zero Point is the programmed point that the coach will
return to each time the Auto Level feature is used. The Zero Point MUST be programmed prior to using the
Auto Level feature to ensure the proper operation of the system. To set the zero point, the control module
must be fully secured in the production intent location.
NOTE: Parking brake MUST be ON in order to operate the leveling system.
NOTE: The LED touchpad controller is only ON while the coach ignition is ON, no operation of leveling is
allowed without the ignition source. Once power is on, the LED touchpad controller will illuminate.
NOTE: At initial power on, select the arrow (Fig. 33) that represents the orientation of the display
touchscreen. Select the arrow on the touchpad that is facing in the same direction that the display
touchscreen is facing related to the coach (Fig. 20).
NOTE: Do NOT move inside coach while the system is trying to level. A leveling error code screen
(Fig. 34 ) will appear if movement is detected. Press Home (Fig. 34A) or Menu (Fig. 34B) icons to exit
of this page.
Fig. 33 Fig. 34
A B
A

Rev: 10.23.23 Page 20 CCD-0005481
Fig. 35
Fig. 36
A
B C
D
E
1. Follow the directions on the next screen (Fig. 35) to calibrate the LED touchpad controller. Place a level
on the floor of the coach to ensure a level reference point in the coach. Press “LEVEL Coach”
on the touchpad.
2. The next screen that follows (Fig. 36) shows four extend buttons that activate each pair of valves,
directional control valve and solenoid. The "CONFIRM LEVEL" button is a latching button that zeros out
the control accelerometer and stores that exact position as level. After the initial calibration, when the
user presses “AUTO LEVEL”, the control recognizes that position as level and will bring the coach to
that position.
3. Level the coach in the manual "CALIBRATION" mode by using a carpenter’s level on the floor. Level
front to rear and then left to right.
A. Push the "EXTEND FRONT" (Fig. 36A) button until jacks contact the ground and lift the front of the
coach 1-2 inches.
Table of contents
Other Lippert Lifting System manuals
Popular Lifting System manuals by other brands
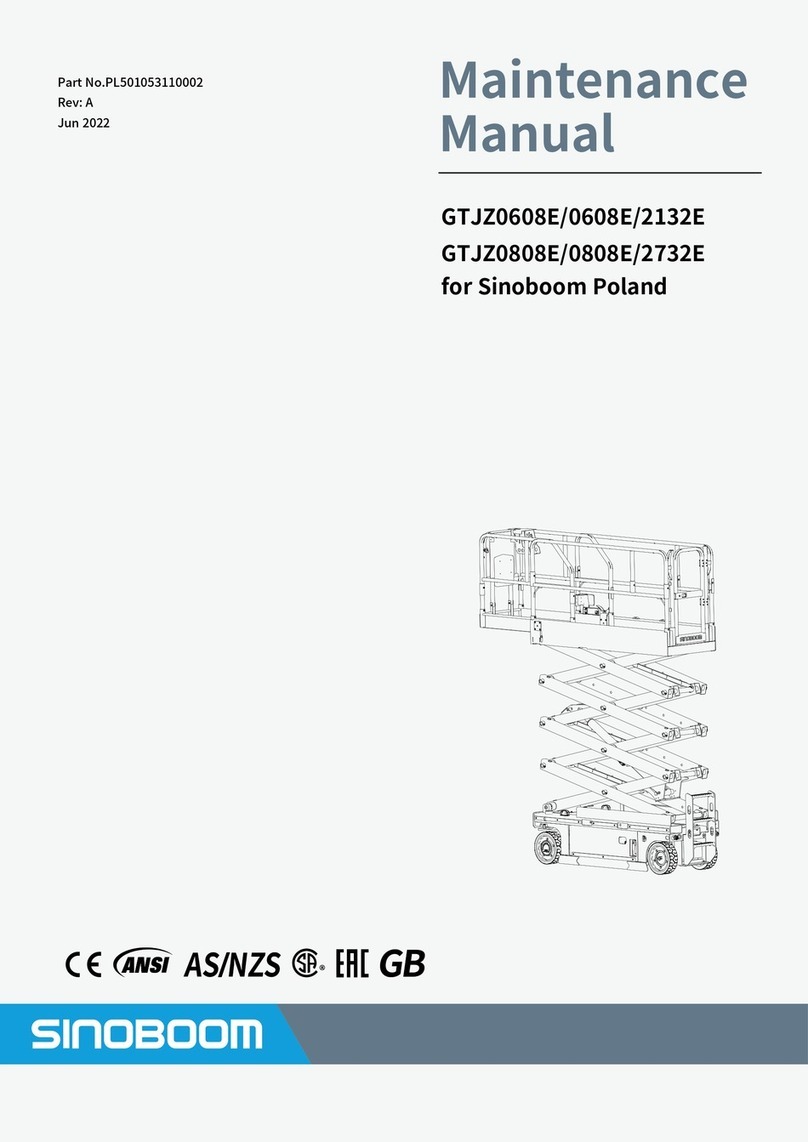
Sinoboom
Sinoboom GTJZ0608E Maintenance manual

Vestil
Vestil CYL-M instruction manual
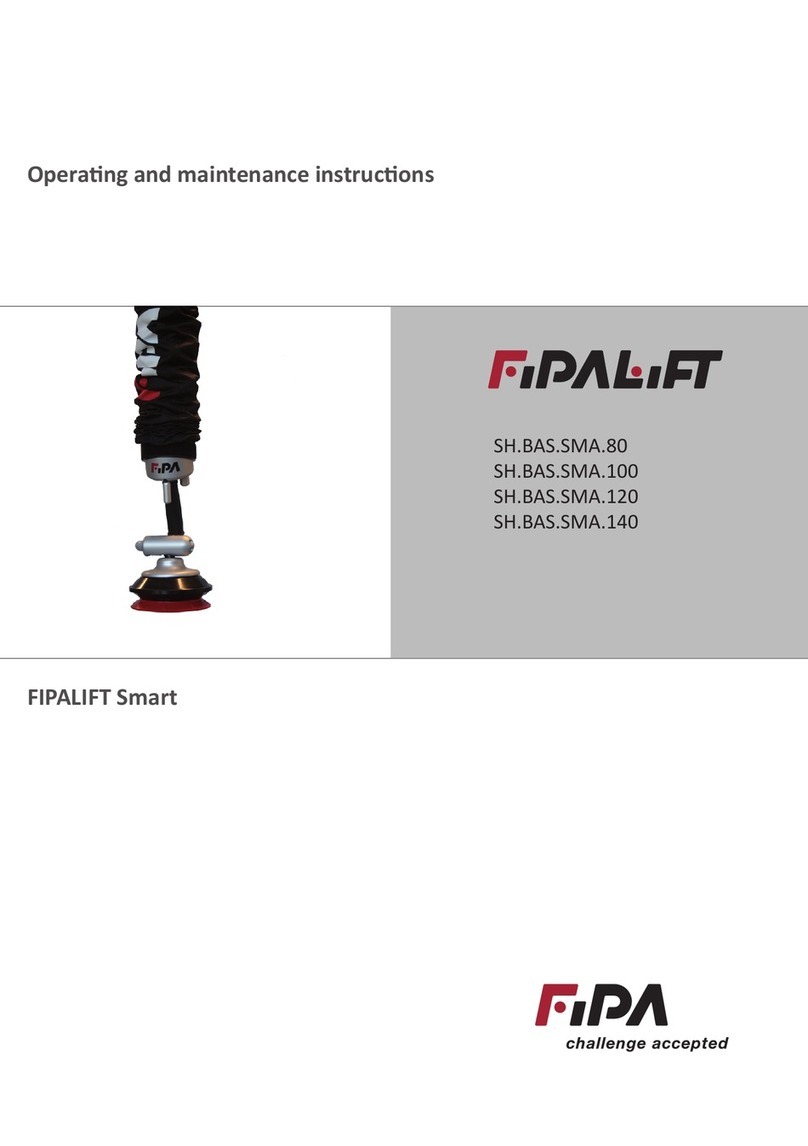
FIPA
FIPA FIPALIFT Smart Series Operating and maintenance instructions

Aqua Creek Products
Aqua Creek Products Ambassador F-PPXRD-R-04 manual
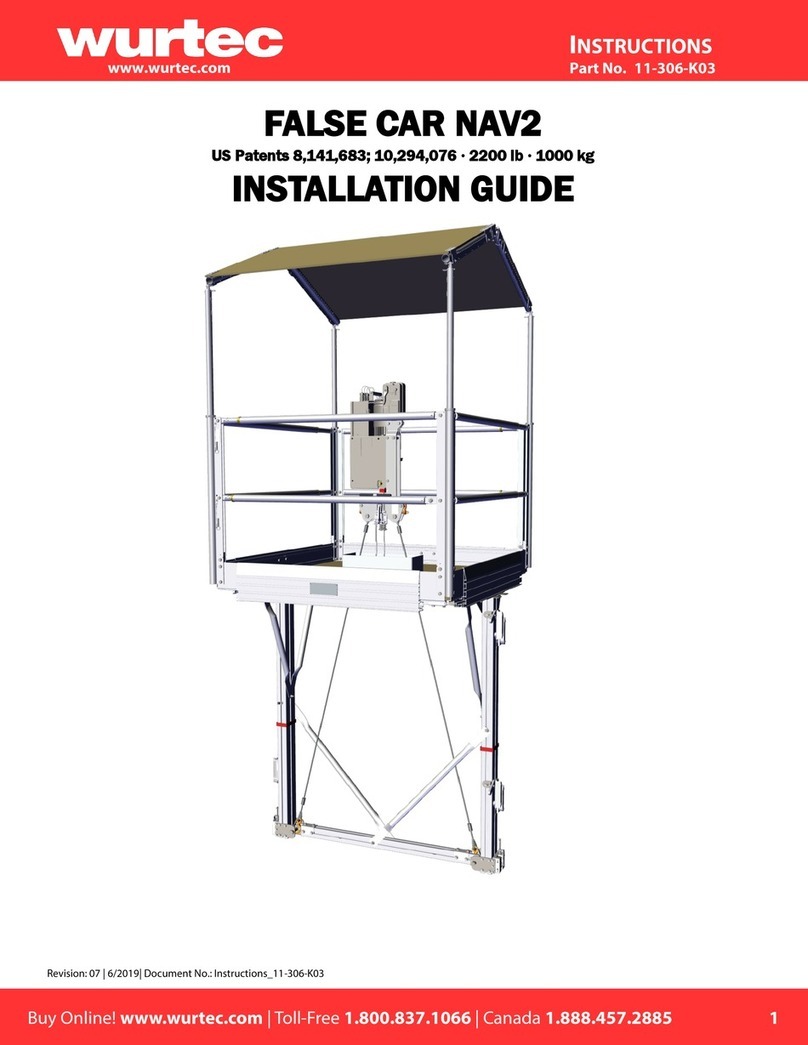
Wurtec
Wurtec FALSE CAR NAV2 installation guide
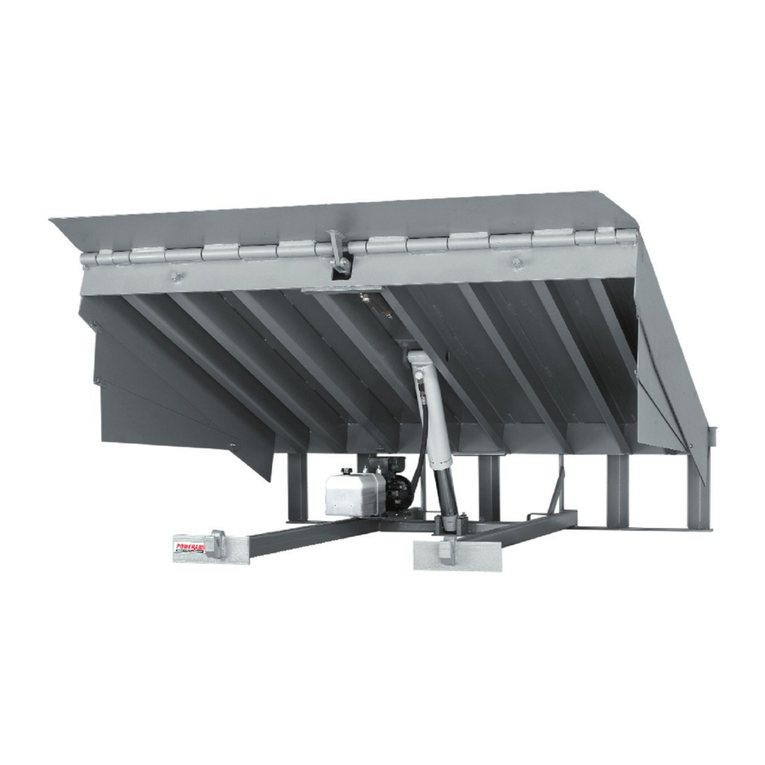
SYSTEMS
SYSTEMS Poweramp EH Series owner's manual