LS ELECTRIC SV-iS7 Series User manual

LS ELECTRIC strives to maximize your profits in gratitude for choosing us as your partner.
iS7 Rnet/Fnet Option User Mannual
SV-iS7 series

iS7 RNet/FNet Manual
i
Before using the product, thank you for using our SV-iS7 RNet/FNet Option Board.
Safety Instruction
To prevent injury and danger in advance for safe and correct use of the product, be sure
to follow the Safety Instructions.
The instructions are divided as ‘WARNING’ and ‘CAUTION’ which mean as follow.
WARNING
CAUTION
The meaning of each symbol in this manual and on your equipment is as follows.
This is the safety alert symbol.
This is the dangerous voltage alert symbol.
After reading the manual, keep it in the place that the user always can contact easily.
Before you proceed, be sure to read and become familiar with the safety precautions at
the beginning of this manual. If you have any questions, seek expert advice before you
proceed. Do not proceed if you are unsure of the safety precautions or any procedure.
WARNING
Be cautious about dealing with CMOS elements of option board.
It can cause malfunction by static electricity.
Connection changing like communication wire change must be done with power
off.
It can cause communication faulty or malfunction.
Be sure to connect exactly between Inverter and option board.
It can cause communication faulty or malfunction.
Check parameter unit when setting parameter.
It can cause communication faulty.
This symbol indicates the possibility of death or
serious injury.
This symbol indicates the possibility of injury or
damage to property.

iS7 RNet/FNet Manual M
ii
Table of Contents
1. Introduction.................................................................................................................................................1
2. Technical date for RNet/FNet communication board..............................................................................1
3. RNet/FNet cable connection......................................................................................................................2
4. Product Contents........................................................................................................................................2
5. RNet/FNet communication board..............................................................................................................3
6. RNet/FNet LED Information .......................................................................................................................4
7. RNet/FNet related Keypad Parameter.......................................................................................................5
8. Connection to LS ELECTRIC PLC with RNet/FNet.............................................................................. 10

iS7 RNet/FNet Manual
1
1. Introduction
RNet/FNet communication board makes the connection between PLC of LS ELECTRIC and
SV-iS7 inverter by a fast series communication so that PLC sequence program can control
the inverter by high speed communication operation of 1 Mbps. Controlling and monitoring
inverter by PLC sequence program makes it easier to install and modify the system.
A number of inverters can be connected by two communication lines so that saving
installation time through simple wiring and easy replacement can be possible. Using extra
devices of PLC and connecting with various systems including PC, the factory automation
can be easier.
2. Technical date for RNet/FNet communication board
Item
Specifications
Transmission Speed
1Mbps
Encoding type
Manchester Bi-phase-L
Frame synchronization type
Electric
Transmission distance
(*1:per segment)
Maximum 750m
Transmission distance
(If repeater is used)
Maximum 750m x (6 repeaters +1)
= 5.25km
Transmission route
Twisted pair shielded cable
RNet dedicated cable
Cable name: LIREV-AMESB 1
(PC 717 6705)
Manufacturer: LS Cable
Network
terminal resistance
Terminal 120.8ohm 1/2W
with an error range of 5%
Built-in RNet/FNet communication board
Maximum points per station
Master + Slave = 64 points
Master point : 0,Slave points :1~63
Maximum protocol size
256 bytes
Frame format
Field Bus standard
IEC TC65 / SC65C / WG6 65C 90.8

iS7 RNet/FNet Manual M
2
Item
Specifications
Access method to service zone
Token Passing
Communication type
Connection Oriented Service
Connectionless Service
Frame error check
CRC16
*1) Segment
It means local network connecting all stations using the same Token without using any
connecting devices (Gateway, EOC, and repeater).
3. RNet/FNet cable connection
Each two TRX-, TRX+ signals are connected in parallel.
When installed at terminal, if you turn on the 1 switch of RNet/FNet communication board,
terminal resistance of 120.8Ω, 1/2W is connected to communication signal terminal
(TRX- and TRX+).
Frame Ground is connected with inverter body. If inverter body is put to earth, SHIELD
line is to be connected to Frame Ground.
Separation of the communication lines and power lines should be installed at least 10cm
distance over.
4. Product Contents
-. RNet/FNet communication board: 1ea
-. RNet/FNet manual: 1ea
-. Fixed Screw (M3): 2ea
Communication
terminal name
Description
TRX-
Communication signal terminal N
TRX+
Communication signal terminal P
SG
Shield/Signal Ground
TRX-
Communication signal terminal N
TRX+
Communication signal terminal P

iS7 RNet/FNet Manual
3
5. RNet/FNet communication board
Interior and appearance /Installation
(1) Interior
▶SW1 : -. Pin 1 (terminal resistance connecting setting switch)
On : 120.8 Ohm terminal resistance connected.
-. Pin 2 ~ 3 (Not used)
-. Pin 4 (RNet/FNet select switch(On : FNet, Off : RNet)
(2) Appearance/Installation
Option card can be installed only on slot 1.
Remove the cover of the option before installation option card, confirm the
RNet/FNet selection switch and terminal resistance switch state and install the
cover.
<RNet/FNet comm board installed>
<RNet/FNet comm board appearance >
RNet/FNet terminal
Inverter connection
LED Display
Slot 1

iS7 RNet/FNet Manual M
4
6. RNet/FNet LED Information
Four LEDs are installed in iS7 RNet/FNet communication board informing the user of
present RNet/FNet status. In iS7 RNet/FNet communication board, LED is located in the
below turn.
LED name
Color
Function
CPU
Green
ON (0.5sec On, 0.5sec OFF) –It shows that the power
is fed to RNet/FNet communication board and CPU is
operating normally.
TX
Green
TX Led is ON when inverter responds to the request of
PLC.
RX
Green
RX Led is ON when inverter receives the request of
PLC.
Error
Red
Be On with the same period of CPU –Displayed when
Option Trip occurs.
Option Trip is related with the CAN communication
interruption between RNet/FNet card and inverter.
Be On with the opposite period of CPU
–Network Configuration Error is displayed.
Network Configuration Error is related with setting as 0
the address point of inverter or when the setting of
Control Num of inverter is different from the Master.
Green
RX
Red
Error
Green
CPU
Green
TX

iS7 RNet/FNet Manual
5
7. RNet/FNet related Keypad Parameter
Code
Parameter name
Initial value
Setting range
Description
CNF-30
Option Type-1
-
-
RNet/FNet: display the
type of built-in
communication board
DRV-06
Cmd Source
Fx/Rx-1
Keypad
Operation
Source setting
Fx/Rx-1
Fx/Rx-2
Int. 485
FieldBus
PLC
DRV-07
Freq Ref Src
Keypad-1
Keypad-1
Frequency
Source setting
Keypad-2
V1
I1
V2
I2
Int. 485
Encoder
FieldBus
PLC
COM-06
FBus S/W Ver
-
-
Display the version
COM-07
FBus ID
1
0~63
Communication Station
address setting
COM-08
FBus BaudRate
1Mbps
1Mbps
Fixing the
communication speed
setting
COM-09
FBus Led
-
-
Communication
board LED Display
COM-30
ParaStatus Num
3
0~8
Receiving data number
COM-31
Para Status-1
0x000A
0x0000 ~ 0xFFFF
Receiving Address 1
COM-32
Para Status-2
0x000E
0x0000 ~ 0xFFFF
Receiving Address 2

iS7 RNet/FNet Manual M
6
Code
Parameter name
Initial value
Setting range
Description
COM-33
Para Status-3
0x000F
0x0000 ~ 0xFFFF
Receiving Address 3
COM-34
Para Status-4
0x0000
0x0000 ~ 0xFFFF
Receiving Address 4
COM-35
Para Status-5
0x0000
0x0000 ~ 0xFFFF
Receiving Address 5
COM-36
Para Status-6
0x0000
0x0000 ~ 0xFFFF
Receiving Address 6
COM-37
Para Status-7
0x0000
0x0000 ~ 0xFFFF
Receiving Address 7
COM-38
Para Status-8
0x0000
0x0000 ~ 0xFFFF
Receiving Address 8
COM-50
Para Ctrl Num
2
0~8
Transmitting data
number setting
COM-51
Para Control-1
0x0005
0x0000 ~ 0xFFFF
Transmitting Address 1
COM-52
Para Control-2
0x0006
0x0000 ~ 0xFFFF
Transmitting Address 2
COM-53
Para Control-3
0x0000
0x0000 ~ 0xFFFF
Transmitting Address 3
COM-54
Para Control-4
0x0000
0x0000 ~ 0xFFFF
Transmitting Address 4
COM-55
Para Control-5
0x0000
0x0000 ~ 0xFFFF
Transmitting Address 5
COM-56
Para Control-6
0x0000
0x0000 ~ 0xFFFF
Transmitting Address 6
COM-57
Para Control-7
0x0000
0x0000 ~ 0xFFFF
Transmitting Address 7
COM-58
Para Control-8
0x0000
0x0000 ~ 0xFFFF
Transmitting Address 8
PRT-12
Lost Cmd Mode
None
None
Operation method when
losing communication
command
Free-Run
Dec
PRT-13
Lost Cmd Time
1.0 sec
0.1~120.0 sec
Decision time of Lost
communication
command time

iS7 RNet/FNet Manual
7
(1) Option Type-1 (CNF-30)
–Display the type of communication board
Option Type-1 displays the type of communication card built-in inverter
If RNet/FNet communication board is installed properly and there is no error in
RNet/FNet communication board, “RNet”(sw1 : off) or “FNet”(sw1 : on) is displayed.
(2) Cmd Source (DRV-06)
–Operation command Source setting
At Cmd Source parameter, set the inverter operation command source. If you
command operation by communication, set “FieldBus”.
(3) Freq Ref Src (DRV-07)
–Frequency command Source setting
At Freq Ref Src parameter, set inverter frequency command source. If you command
frequency by communication, set “FieldBus”.
(4) FBus S/W Ver (COM-06)
–Display the version of communication board built-in inverter.
Version of communication card installed at inverter is displayed.
(5) FBus ID (COM-07)
–Setting inverter address.
For communicating with Master, set communication address allocated to inverter.
Setting from 1 to 63 is possible.
You must not set the inverter address as 0 only RNet/FNet Master can have the 0
address. If you set address as 0, the LED of RNet/FNet Communication card will
display Network Configuration Error.
(6) FBus BaudRate(COM-08) –Communication speed display
The speed of RNet communication installed in inverter is fixed as 1Mbps. So, setting
is impossible and only can display the speed information.
(7) FBus Led (COM-09) –Communication card LED information display

iS7 RNet/FNet Manual M
8
The state of ON/OFF of TX, RX, ERR, CPU LED of RNet/FNet communication card
is displayed at COM-09 through Keypad parameter.
If you check COM-09 FBus LED through Keypad, LED can be seen. According to
the LED order of COM-09 (left -> right), the information of TX, RX, ERR, CPU LED is
displayed in this order.
COM-09 Led state Example)
(8) ParaStatus Num (COM-30) –Setting receiving data number
Communication Word data number that Master will receive from the inverter through
communication is set.
Inverter can send inverter 8 Words for the maximum.
You must set exactly same with the number of receiving data of Master program.
(9) Para Status-1~8 (COM-31~38) –Receiving address 1~8 setting
Inverter address through which inverter will receive data from Master is set.
It is possible to set inverter address for communicating from COM-31 to COM-38, but
inverter sends Master data as the number of COM-30 ParaStatus Num through
communication.
(10) Para Ctrl Num (COM-50) –Transmitting data number setting
Word data number is set that Master will transmit to inverter through communication.
Inverter can receive 8 Word data from the Master for the maximum.
If you are using “RNet”, You must set exactly same with the number of transmitting
data of Master program.
If you are using “FNet”, you must set the number of transmitting word data –1 of
Master program.
TX LED
RX LED
ERR LED
CPU LED
ON
OFF
ON
OFF

iS7 RNet/FNet Manual
9
(11) Para Control-1~8 (COM-51~58) –Transmitting address 1~8 setting
Inverter address is set for data which Master gives to inverter.
It is possible to set inverter address for communicating from COM-51 to COM-58, but
Master transmits to inverter data as the number of COM-50 Para Ctrl Num through
communication.
(12) Lost Cmd Mode (PRT-12) –Operation method when losing communication
command
Inverter operation method can be set for the case of communication command lost.
Communication command lost is valid if DRV-06 Cmd Source is “FieldBus” or DRV-
07 Freq Ref Src is set as “FieldBus”.
If Lost Cmd Mode is set as “None” and communication command lost happens, Trip
Message doesn’t occur if present operation state is kept.
If Lost Cmd Mode is set as “Free-Run” of “Dec” and communication command lost
happens, Free-Run operation will be done or Dec operation with “Lost Command”
message display can be done.
(13) Lost Cmd Time (PRT-13) –Communication command lost time
The standard time for communication command lost is set.
Communication command lost is valid if DRV-06 Cmd Source is “FielBus” or DRV-
07 Freq Ref Src is set as “FieldBus” and then PRT-12 Lost Cmd Mode is “Free-Run”
or “Dec”.
Lost
Cmd
Lost
Cmd
PRT-13
Lost Cmd Time
PRT-13
Lost Cmd Time
Comm. Cmd
Lost recognition
Comm. Line state

iS7 RNet/FNet Manual M
10
8. Connection to LS ELECTRIC PLC with RNet/FNet
The below describes in brief how to connect LS ELECTRIC PLC XGT with iS7 RNet/FNet
Communication option card.
Visit LS ELECTRIC website and download XG5000 Program and install it.
If you install, XG-PD Program and XG5000 Program are installed in PC.
★) Transmitting and receiving is determined from the view of Master.
8.1 H/W Installation
RNet/FNet Comm. Card is installed in iS7 inverter. When iS7 inverter turns ON, check if
“RNet” or “FNet”message(depending on sw1 state) can be displayed at CNF-30 Option
Type-1.
Install the PLC Hardware. As the picture below, attach power module and CPU to Base
and connect RNet Master module (XGL-RMEA) or FnET Master module(XGL-FMEA) to
base.
Connect RNet/FNet Master module (terminal TRX+, TRX-) to iS7 RNet/FNet
communication card (terminal TRX+, TRX-) using RNet/FNet dedicated cable for creating
network.
<XGT PLC RNet Module>
<IS7 RNet/FNet Comm. card>
TRX+
TRX-
RNet/FNet
dedicated cable

iS7 RNet/FNet Manual
11
8.2 Inverter Parameter setting
Inverter parameter needed to set for RNet/FNet communication is as bellows.
Inverter FieldBus ID
Transmitting data number for communicating with Master
Inverter address information for transmitting
Receiving data number for communicating with Master
Inverter’s address information for receiving.
First, set inverter communication ID. Set COM-07 FBus ID. In the example, inverter
FieldBus ID is set as 1. And set transmitting and receiving data for communicating with
RNet/FNet. Here, 2 Word transmitting and 3 Word receiving communication is done. Set
inverter Address for transmitting andAddress for receiving.
Parameter setting value at the example
8.3 Communicating with PLC
8.3.1 Communicating with PLC FNet
(1) Registrating Para Status, Para Control address
You can register Para Status, Para Control address in the read or write
Code
Parameter name
Value
Range
Description
COM-07
FBus ID
1
1~63
Field Bus ID
Do not set 0
0 is fixed for Master.
COM-30
ParaStatus Num
3
0~8
Receiving data number
COM-31
Para Status-1
0x0007
0x0000 ~ 0xFFFF
Receiving Inverter
Address information
COM-32
Para Status-2
0x0008
0x0000 ~ 0xFFFF
COM-33
Para Status-3
0x000A
0x0000 ~ 0xFFFF
COM-50
Para Ctrl Num
2
0~8
Transmitting data number
COM-51
Para Control-1
0x0005
0x0000 ~ 0xFFFF
Transmitting inverter
Address information
COM-52
Para Control-2
0x0006
0x0000 ~ 0xFFFF

iS7 RNet/FNet Manual M
12
regularly over a high-speed link communication from PLC.
When you register 8-address (M0001 to M0008) to Para Status or Para
Control of the inverter, set high speed link parameters of PLC as shown
below.(GLOFA, GMWIN 4.0)
For registration of Para Status address, the memory address M0000,
must Para Status addresses a registration command 0x0050 is stored,
transmitted size, enter 9 greater than the number of word data (8) to be
transmitted..
For registration of Para Control address, the memory address M0000,
must Para Control addresses a registration command 0x0051 is stored,
transmitted size, enter 9 greater than the number of word data (8) to be
transmitted.
Because storage memory area is independent of the communication,
arbitrarily set. Storage
(2) Para Control data write
Using high speed communication, PLC can periodically writes the
parameter registered in Para Control.
When you register 8-address (M0001 to M0008) to Para Control of the
inverter, set high speed link parameters of PLC as shown below.(GLOFA,

iS7 RNet/FNet Manual
13
GMWIN 4.0)
For Para Control data writing, the memory address M0000, must be
write command Para Control data 0x0052 is stored, transmitted size 9
greater than the number of word data (8) to be transmitted enter.
If FNet option card value obtained by subtracting 1 from the
transmission size is different from the inverter Para Ctrl Num, Error LED
and CPU LED will blink alternately.
Because storage memory area is independent of the communication,
arbitrarily set.
(3) Para Status data read
You can read the parameters that have been registered to the inverter
Para Status via a high-speed link communication on a regular basis in
the PLC.
When you register 8-address (M0000 to M0007) to Para Status of the
inverter, set high speed link parameters of PLC as shown below.(GLOFA,
GMWIN 4.0)

iS7 RNet/FNet Manual M
14
For a read of Para Status data, does not require a separate
Command. Enter the number of words of data to be sent(8).
If iS7 FNet option card that the value of the received size is different
from the inverter Para Status Num, Error LED and CPU LED will blink
alternately.
Because read memory area is independent of the communication,
arbitrarily set.
After finishing PLC RNet/FNet module setting (refer to PLC RNet/FNet module manual) if
Inverter parameter setting is completed as above, communication between PLC and
RNet/FNet is possible.

iS7 RNet/FNet Manual
15
Warranty
Product
Name
LS ELECTRIC Communication
Option Card
Installation
Date
Model
Name
SV-iS7 RNet/FNet
(CR-S7M1)
Communication Card
Warranty
Period
Customer
Name
Address
Tel.
Sales
Office
Name
Address
Tel.
Note
This product has been manufactured through the strict QC control and inspection of LS stems. Warranty
period is 12 months after installation or 18 months after manufactured when the installation date is
unidentified. However, the guarantee term may vary on the sales term.
In-warranty service information
If the defective part has been identified under normal and proper use within the guarantee
term, contact your local authorized LS distributor or LS Service center.
Out-of-warranty service information
The guarantee will not apply in the following cases.
Troubles are attributable to a user’s intentional negligence or carelessness
Damage was caused by abnormal voltage and peripheral devices’ malfunction (failure)
Damage was caused by natural disasters(earthquake, fire, flooding, lightning and etc)
When LS nameplate is not attached

iS7 RNet/FNet Manual
i
제품을 사용하기 전에
먼저 저희 RNet/FNet 옵션보드를 사용하여 주셔서 감사합니다.
안전상의 주의사항
안전상의 주의사항은 사고나 위험을 사전에 예방하여 제품을 안전하고 올바르게
사용하기 위한 것이므로 반드시 지켜주십시오.
주의사항은 ‘경고’와‘주의’의두가지로 구분되어 있으며 ‘경고’와‘주의’의의미
는다음과 같습니다.
경고
주의
제품과 사용설명서에 표시된 그림기호의 의미는 다음과 같습니다.
는위험이 발생할 우려가 있으므로 주의하라는 기호 입니다.
는감전의 가능성이 있으므로 주의하라는 기호 입니다.
사용설명서를 읽고 난후사용하는 사람이 언제라도 볼수있는 장소에 보관 하
십시오.
SV-iS7 시리즈 인버터의 통신옵션 기능을 충분하고 안전하게 사용하기 위하여
이사용 설명서를 잘읽어 보십시오.
지시사항을 위반할 때심각한 상해나 사망이 발생할 가능
성이 있는 경우
지시사항을 위반할 때경미한 상해나 제품손상이 발생할 가능
성이 있는 경우

iS7 RNet/FNet Manual
ii
주의
옵션보드의 CMOS 소자들의 취급에 주의하십시오.
정전기에 의한 고장의 원인이 됩니다.
통신 신호선 등의 변경 접속은 인버터 전원을 내린 상태에서 하십시오.
통신불량 및고장의 원인이 됩니다.
인버터 본체와 옵션보드 커넥터가 정확히 일치하게 접속되도록 하십시오.
통신불량 및고장의 원인이 됩니다.
파라미터를 설정할 때는 파라미터 unit 을확인하시기 바랍니다.
통신불량의 원인이 됩니다.
Other manuals for SV-iS7 Series
5
Table of contents
Languages:
Popular Conference System manuals by other brands

Polycom
Polycom RealPresence Group Series Quick tips
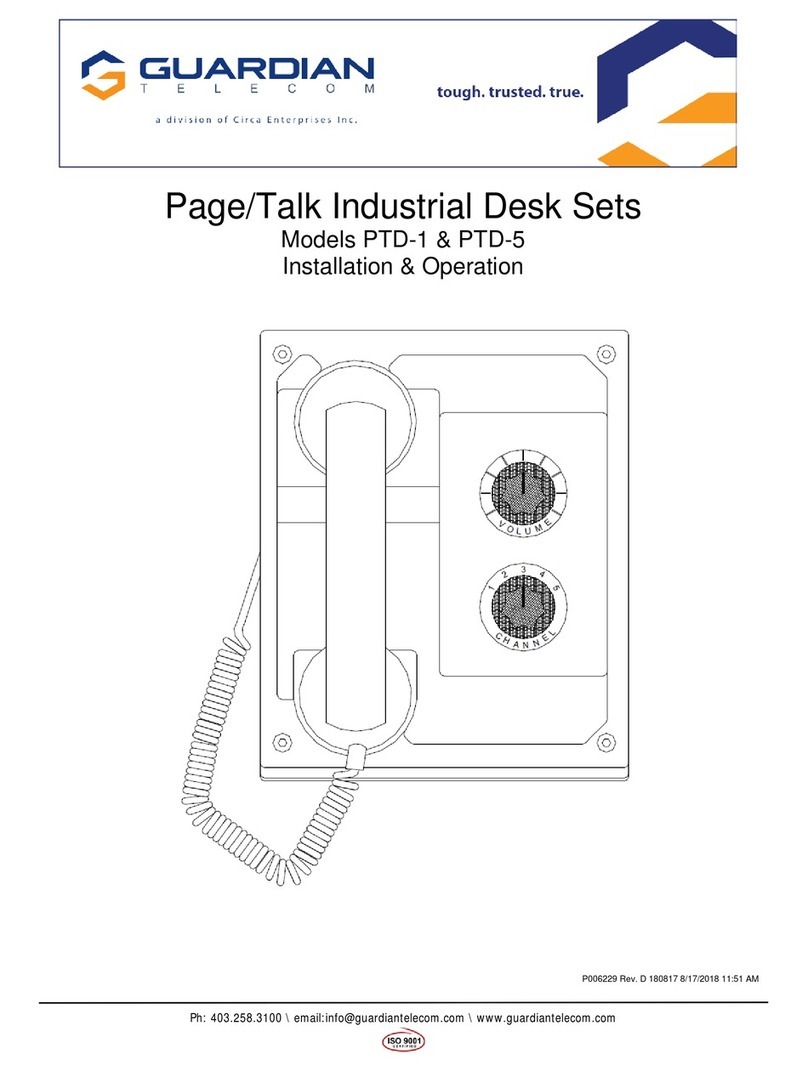
Guardian
Guardian PTD-1 Installation & operation

Current Thinking
Current Thinking VoCALL Compact Installation and maintenance manual
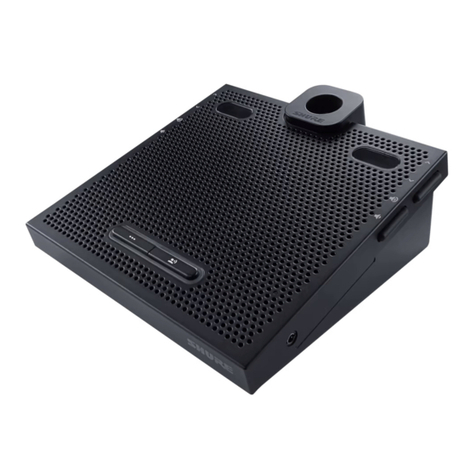
Shure
Shure Microflex Complete MXC Series user guide
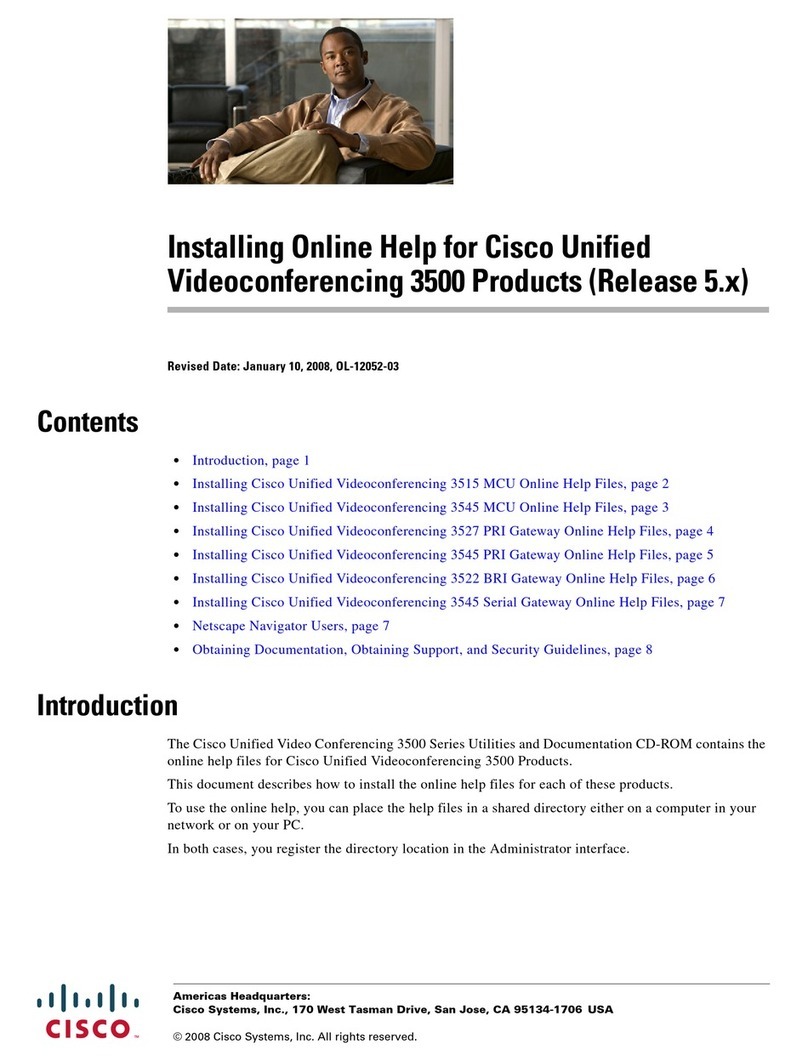
Cisco
Cisco Aironet 3500 Series Online help
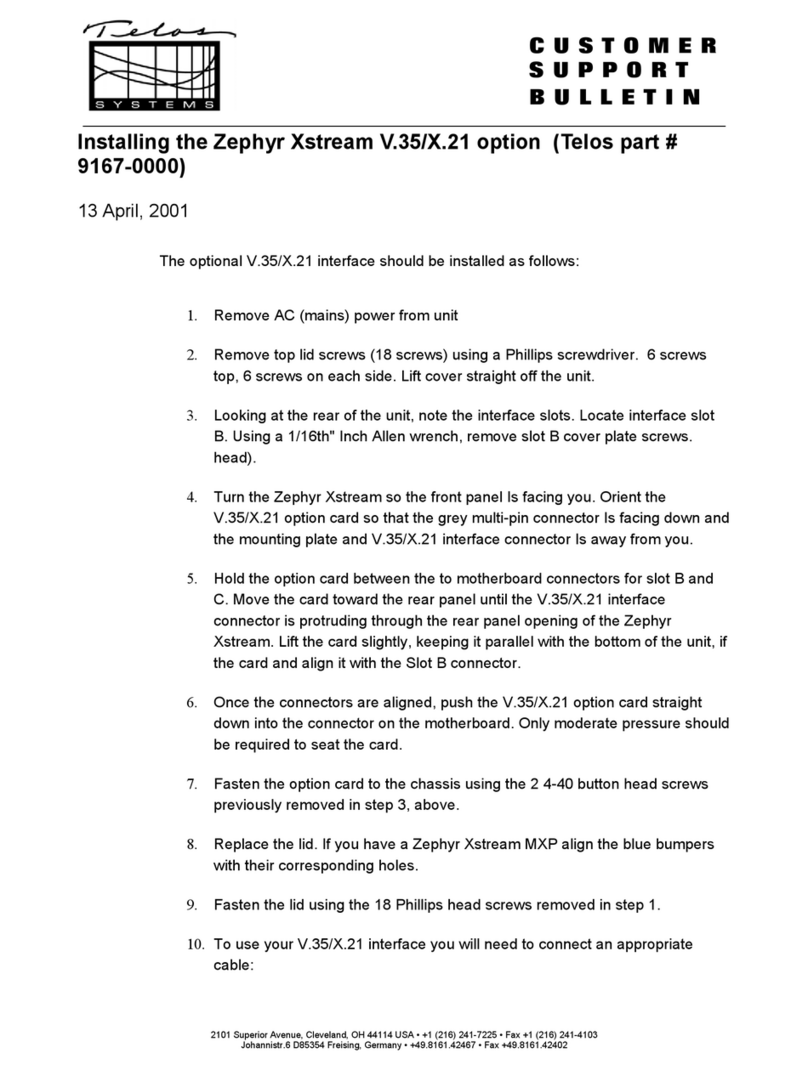
Telos
Telos Zephyr Xstream V.35 CUSTOMER SUPPORT BULLETIN