LTH MOD53 User manual

MOD53
DISSOLVED OXYGEN MONITOR
OPERATION GUIDE

Preface
1
Preface
Product warranty
The MOD53 has a warranty against defects in materials and workmanship for three
years from the date of shipment. During this period LTH will, at its own discretion,
either repair or replace products that prove to be defective. The associated
software is provided ‘As is’ without warranty.
Limitation of warranty
The foregoing warranty does not cover damage caused by accidental misuse,
abuse, neglect, misapplication or modification.
No warranty of fitness for a particular purpose is offered. The user assumes the
entire risk of using the product. Any liability of LTH is limited exclusively to the
replacement of defective materials or workmanship.
There are no user serviceable parts, including fuses etc., within the unit. Any
attempt to dismantle the instrument will invalidate the warranty.
Disclaimer
LTH Electronics Ltd reserves the right to make changes to this manual or the
instrument without notice, as part of our policy of continued developments and
improvements.
All care has been taken to ensure accuracy of information contained in this
manual. However, we cannot accept responsibility for any errors or damages
resulting from errors or inaccuracies of information herein.
Copyright and trademarks
All rights reserved. Translations, reprinting or copying by any means of this
manual, complete or in part or in any different form requires our explicit approval.
MOD53 is a trademark of LTH Electronics Ltd
Fifth Edition August 2005
Part number : 6136
LTH Electronics Ltd
Chaul End Lane
Luton Telephone: +44 (0)1582 593693
Bedfordshire Fax: +44 (0)1582 598036
England Web: www.lth.co.uk

Preface
2
Manufacturing Standards
Electromagnetic compatibility
This instrument has been designed to comply with the standards and regulations
set down by the European EMC Directive
Safety
This instrument has been designed to comply with the standards and regulations
set down by the European Low Voltage Directive using BS EN 61010-1 : 1993
Quality
This instrument has been manufactured under the following quality standard :
ISO 9001:2001. Certificate No : FM 13843
Note: The standards referred to in the design and construction of LTH products are
those prevailing at the time of product launch. As the standards are altered from
time to time, we reserve the right to include design modifications which are
deemed necessary to comply with the new or revised regulations.

Contents
3
Contents
Preface..................................................................................................................1
Contents ...............................................................................................................3
1 Introduction.....................................................................................................5
About the MOD53 ............................................................................................5
Unit Specification .............................................................................................5
2 Installation – Safety & EMC............................................................................7
Wiring Installation ............................................................................................7
3 Installation – Panel Mount .............................................................................9
Top Connector ...............................................................................................11
Supply Voltage Connections..........................................................................11
Current Output Connections ..........................................................................12
Set Point Relay Connections .........................................................................12
Set Point Relays 3 & 4 Connection ................................................................13
Bottom Connector ..........................................................................................14
Sensor Input Connections..............................................................................14
Sensor Types.................................................................................................15
Temperature Input Connections.....................................................................16
Pressure Transmitter Input.............................................................................17
RC2 Cleaner Connection ...............................................................................17
Digital Inputs ..................................................................................................18
4 Installation – Surface Mount........................................................................19
Pipe Mounting ................................................................................................20
Terminal Connections ....................................................................................21
Supply Voltage Connections..........................................................................21
Current Output Connections ..........................................................................22
Relay Connections .........................................................................................23
Sensor Input Connections..............................................................................24
Sensor Types.................................................................................................24
Temperature Input Connections.....................................................................26
Pressure Transmitter Input.............................................................................27
RC2 Cleaner Connection ...............................................................................27
Digital Inputs ..................................................................................................28
5 User Interface................................................................................................29
The Front Panel .............................................................................................29
The Menu System ..........................................................................................30
Error Messages..............................................................................................30
Access Entry ..................................................................................................30
Unit Configuration ..........................................................................................34
6 Main Display..................................................................................................37
7 Parameters ....................................................................................................41
Units...............................................................................................................43
Sensor Type...................................................................................................44
Temperature Input..........................................................................................44
Salinity............................................................................................................44

Contents
4
Pressure Compensation.................................................................................45
Simulated Input ..............................................................................................45
8 Set Points ......................................................................................................47
Set Point Source ............................................................................................49
Set Point Trigger ............................................................................................49
Set Point Mode...............................................................................................50
Dose Alarm Timers ........................................................................................51
Set Point 4......................................................................................................52
9 Current Output ..............................................................................................53
Input ...............................................................................................................54
Output Range.................................................................................................54
Zero & Span ...................................................................................................54
Dual current outputs.......................................................................................55
Proportional Control .......................................................................................55
Error Condition...............................................................................................55
10 Calibration ...................................................................................................57
On-Line/Off-Line Operation............................................................................59
Calibration Access .........................................................................................59
Automatic Calibration.....................................................................................59
Sensor Calibration..........................................................................................60
Temperature Calibration ................................................................................61
Pressure Input Calibration..............................................................................62
Current Output Calibration .............................................................................63
Resetting The User Calibration ......................................................................64
11 Save & Restore ...........................................................................................65
12 Pressure Input.............................................................................................67
13 Configuration ..............................................................................................71
14 Sensor Cleaning .........................................................................................73
15 Fault Finding ...............................................................................................75
16 OE15 Membrane Replacement ..................................................................79
17 Guarantee and Service...............................................................................81
Appendix A – DO Measurement .......................................................................83
Appendix B – Probe Parameters ......................................................................85
Appendix C – Factory Default Setups..............................................................87
Appendix D – Customer Setup .........................................................................91
Appendix E – Calibration ..................................................................................95
Appendix F – Temperature Sensor Data..........................................................97
Appendix G – Pressure Conversions...............................................................99
Appendix H – Oxygen Solubility.....................................................................101
Appendix I – Error Messages..........................................................................103
Index .................................................................................................................107

1 Introduction
5
1 Introduction
ABOUT THE MOD53
The MOD53 is a microprocessor controlled dissolved oxygen measurement
instrument. It uses a multifunction LCD to display readings and provide feedback
to the operator. Different options provide fully configurable control, alarm and
feedback with up to four relays and two 0/4-20mA current output sources.
UNIT SPECIFICATION
Sensor Input Galvanic (Mackereth) 0 to 9.999mA or Polargraphic
(Clark) 0 to 500.0nA.
Sensor Bias Voltage Software Programmable, -1.000 to +1.000V,
Resolution ±1mV, Output Accuracy ±3mV
Sensor membrane
correction factor
Software Programmable
0 to 9999
Sensor Cable Up to 100 metres
Ranges of
Measurement
0 - 199.9 % saturation, 0 - 30.00 ppm Concentration,
0 – 999.9 mmHg (Calibration specific)
0 – 9999 mBar pO2 (Calibration specific)
Accuracy ±3µA (Galvanic Mode), ±1.0nA (Polargraphic Mode)
Linearity ±0.1% of Range
Repeatability ±0.1% of Range
Temperature Sensor 4 wire interface, operating with up to 100 metres of
cable. Software selectable sensor type including
PT100 & PT1000 RTD.
Measurement Range -50°C to +300°C (when using PT100 or PT1000)
Temperature Accuracy ±0.2°C (Dependant on Sensor Configuration)
Operator Adjustment
(Temperature)
±50°C, or ±122°F
Temperature
Compensation
Automatic, or Manually set from 0°C to 100°C
Pressure
Compensation
Actively from 4-20 mA input (Direct or 24V loop
powered from the MOD53.) Software Scalable.
or User Programmable from 0.50 – 9.99 bar
With user Selectable Pressure Damping
Salinity Compensation User Programmable from 0 – 40.0 ppt
Ambient Operating
Temperature
-20°C to +50°C (-4°F to +122°F) for full specification.
Ambient temperature
variation
±0.01% of range / °C (typical)

1 Introduction
6
User Interface Large 4 character 7-segment display for measured
value, with alphanumeric dot matrix characters for
units, information and programming. Easy to use four
button user interface for programming.
Current output
(optional 1 or 2 outputs)
Selectable 0-20mA or 4-20mA operation into a 1000Ω
maximum load, fully isolated to 2kV. Selectable
transmission of either sensor reading or temperature,
and software scalable within the operating range.
Can be configured as a clean output so that the signal
switches between 0 to 20mA.
Operator adjustment
(Current)
±1mA zero and ±1mA span for remote monitor
calibration
Set Point Relays
(2 standard, 4 optional)
Fully configurable set points with volt free contacts.
Rated 5A 30V DC / 5A 250VAC (non-inductive).
Operating Modes
(Relays 1,2 & 3)
Configurable High, Low, Band or Latch trigger
conditions, with On/Off, Time Proportioning, Pulse
Proportioning, and Cleaning modes for each relay.
Adjustable delay timers up to 10 mins, and hysteresis
in On/Off mode. Adjustable dose alarm timer to 15
mins in all modes. Adjustable cycle time and band in
“Proportioning” modes. Adjustable duration, recovery
and interval periods in “Cleaning” mode.
Operating mode
(Alarm relay 4)
The relay can be set to energise on any one of the
following instrument conditions:- Sensor alarm, Dose
alarm, Calibration, Off line, Any error
Off-Line Facility
(for calibration and
commissioning)
Initiated by remote contact closure or software
selection. Relays 1, 2 & 3 are de-energised and the
current outputs are held at the last On-Line value.
EMC : Immunity BS EN 50082-2 1995
EMC : Emissions BS EN 50081-1 1992
Safety Designed and manufactured in accordance with BS
EN 61010-1 1993
Power Supply
Optional
85 to 250V AC or DC 10W max.
18 to 36V AC or DC 15 W max
Panel Mount Housing Flame retarding ABS plastic, rated to IP66 to the front
when installed in a panel.
Weight Less than 0.6kg
Dimensions 96mm x 96mm x 140mm (H x W x D), including
connectors
Surface Mount Housing Expanded polyurethane foam rated to IP66
Weight Less than 1.5kg
Dimensions
305mm x 200mm x 82mm (H x W x D), excluding
mounting brackets

2 Installation – Safety & EMC
7
2 Installation – Safety & EMC
This chapter describes how to install and mount the MOD53, and how to connect
the unit to a power source and auxiliary equipment.
Although today’s electronic components are very reliable, it should be anticipated
in any system design that a component could fail and it is therefore desirable to
make sure a system will fail safe. This could include the provision of an additional
monitoring device, depending upon the particular application and any
consequences of an instrument or sensor failure.
WIRING INSTALLATION
The specified performance of the MOD53 is entirely dependent on correct
installation. For this reason, the installer should thoroughly read the following
instructions before attempting to make any electrical connections to the unit.
CAUTION ! : ALWAYS REMOVE THE MAIN POWER FROM THE SYSTEM
BEFORE ATTEMPTING ANY ALTERATIONS TO THE WIRING. ENSURE THAT
BOTH POWER INPUT LINES ARE ISOLATED. MAKE SURE THAT THE POWER
CANNOT BE SWITCHED ON BY ACCIDENT WHILST THE UNIT IS BEING
CONNECTED. FOR SAFETY REASONS AN EARTH CONNECTION MUST BE
MADE TO THE EARTH TERMINAL OF THIS INSTRUMENT.
LOCAL WIRING AND SAFETY REGULATIONS SHOULD BE STRICTLY
ADHERED TO WHEN INSTALLING THIS UNIT. SHOULD THESE
REGULATIONS CONFLICT WITH THE FOLLOWING INSTRUCTIONS,
CONTACT LTH ELECTRONICS OR AN AUTHORISED LOCAL DISTRIBUTOR
FOR ADVICE.
To maintain the specified levels of Electro Magnetic Compatibility (EMC,
susceptibility to and emission of electrical noise, transients and radio frequency
signals) it is essential that the types of cables recommended within these
instructions be used. If the installation instructions are followed carefully and
precisely, the instrument will achieve and maintain the levels of EMC protection
stated in the specification. Any equipment to which this unit is connected must also
have the same or similar EMC control to prevent undue interference to the system.
♦ Terminations at the connectors should have any excess wire cut back so that
a minimal amount of wire is left free to radiate electrical pick-up inside or
close to the instrument housing.
♦ The terminal cover of the surface mount unit must be correctly re-assembled
and securely fastened, to maintain a continuous electro-magnetic shield
around the instrument.
N.B. The use of CE marked equipment to build a system does not necessarily
mean that the completed system will comply with the European requirements for
EMC and therefore CE marking.

2 Installation – Safety & EMC
8
Noise suppression
In common with other electronic circuitry, the MOD53 may be affected by high level,
short duration noise spikes arising from electromagnetic interference (EMI) or radio
frequency interference (RFI). To minimise the possibility of such problems occurring,
the following recommendations should be followed when installing the unit in an
environment where such interference could potentially occur.
The following noise generating sources can affect the MOD53 through capacitive or
inductive coupling.
• Relay coils
• Solenoids
• AC power wires, particularly at or above 100V AC
• Current carrying cables
• Thyristor field exciters
• Radio frequency transmissions
• Contactors
• Motor starters
• Business and industrial machines
• Power tools
• High intensity discharge lights
• Silicon control rectifiers that are phase angle fired
The MXD53 series is designed with a high degree of noise rejection built in, to
minimise the potential for interference from these sources, but it is recommended
that you apply the following wiring practices as an added precaution. Cables
transmitting low level signals should not be routed near contactors, motors,
generators, radio transmitters, or wires carrying large currents.
If noise sources are so severe that the instrument’s operation is impaired, or even
halted, the following external modifications should be made, as appropriate:
• Fit arc suppressors across active relay or contactor contacts in the vicinity.
• Run signal cables inside steel tubing as much as is practical.
• Use the internal relays to switch external slave relays or contactors when
switching heavy or reactive loads.
• Fit an in-line mains filter close to the power terminals of the instrument.

3 Installation – Panel Mount
9
3 Installation – Panel Mount
The panel-mounting version is designed to be flush mounted and sealed in a
square cut-out in a panel, and is held in place with the two screw clamps provided.
Figure 1 : Overall dimensions panel-mounting MOD53
• The panel cut-out for mounting the unit should be 92 mm x 92 mm (+1.0 – 0.0).
• A sealing gasket is supplied with the MOD53 to be fitted around the edge of the
cut-out.
• Two screw clamps are supplied and are fitted from the back of the instrument.
• Take care to ensure the gasket is correctly positioned before tightening the
clamps.
• A badly fitted gasket will not give a good seal to the specified IP rating.

3 Installation – Panel Mount
10
Unit Connection
Connections to the panel-mounted version of the MOD53 are made with up to four
plug and socket terminal blocks, accessible to the rear of the unit.
Top Connector
Bottom Connector
Expansion Port
where fitted
Earth Stud
Figure 2 : Panel mount unit, rear view
The top connector houses the power input, relay and current output terminals. The
bottom connector houses the sensor input, temperature sensor input and the
digital inputs. The expansion port provides for additional enhancements such as
the third and fourth relay connection.

3 Installation – Panel Mount
11
TOP CONNECTOR
Figure 3 : Panel mount unit, top connector wiring
SUPPLY VOLTAGE CONNECTIONS
The MOD53 can be powered from either an AC or DC supply voltage. The unit
provides two terminals for each of the input connections (“Live” & “Neutral” for an
AC input,or +& -for a DC Input), plus an “Earth” terminal. This allows the supply
to be “daisy chained” to the relay contacts and/or other instruments. The
instrument uses a universal power supply that accepts a wide range of voltage and
frequency inputs. Refer to the label adjacent to the power supply terminals for
the input voltage limits. Exceeding these limits may damage the instrument.
Figure 4 : Power supply connection
The power supply should be taken from an isolated spur and fused to a maximum
of 3 Amps. If the relays require greater current, then a separate 5A fuse will be
required. The incoming Earth connection must be connected to the “Earth”
terminal.
MOD53
OUT IN
3A
L
N
E

3 Installation – Panel Mount
12
CURRENT OUTPUT CONNECTIONS
The MOD53 can be supplied with up to 2 current outputs designated A and B. It is
shipped with links across the relevant current output pins if the option is fitted. If a
current output is required, remove the link and replace with a cable terminated by a
load resistance not exceeding 1000Ω. For best noise immunity, use a screened
twisted pair cable, with the screen connected to Earth at one end. Use a
sufficiently large cable to avoid a high resistance in the overall current loop. When
either of the outputs is open circuit, in a dual output unit, the other will
indicate a fault by transmitting a 2mA signal. This will be accompanied by a
flashing error message on the Display (E41, see Appendix I)
SET POINT RELAY CONNECTIONS
The relay contacts are connected to the terminals only and are electrically isolated
from the instrument itself. They must be connected in series with a 5 Amp
fuse.
MOD53
Load A
Neutral
Live
Neutral
Load B
5A
Figure 5 : Relay contact connection
A contact arc suppressor may be required to prevent excessive electrical noise,
depending upon the load. To switch more than 5 Amps will require a slave relay.
MOD53 Slave Relay
Neutral
Live
Figure 6 : Slave relay connection

3 Installation – Panel Mount
13
For convenience, the power can be looped across from the supply connections.
SET POINT RELAYS 3 & 4 CONNECTION
When fitted, the expansion port connector houses the additional relay output
terminals. NB The relay contacts are volt free and should be wired in series with a
supply and load { see Figure 5.}
NOTE :
NC = normally closed
NO = normally open
C = common
Figure 7 : Panel mount unit, Relays 3 & 4 wiring

3 Installation – Panel Mount
14
BOTTOM CONNECTOR
The bottom connector houses the sensor input and digital input connections. Two
separate connectors are used, separated by a blanking plug. A 9 way connector is
provided for the sensor input and a 4 way connector for the digital inputs.
Figure 8 : Panel mount unit, bottom connector wiring
SENSOR INPUT CONNECTIONS
The MOD53 has been designed with the flexibility to accept a wide variety of both
Galvanic and Polargraphic Dissolved Oxygen probes. Parameters such as
membrane correction, bias voltage and temperature sensor type can be easily
programmed into the instrument. It will be necessary to identify the sensor type
e.g. Galvanic or Polargraphic, and the temperature sensor type e.g. PT1000 or
thermistor.
Figure 9 : Sensor Connections

3 Installation – Panel Mount
15
SENSOR TYPES
The following figures give the connection details of the most commonly used LTH
cable types. Do not use any other type of cable than those recommended by LTH
or the sensor manufacturer to extend the sensor / instrument distance.
Figure 10 : OE15 Cable
The outer screen/shield should be connected to the centre Earth Stud.
Figure 11 : ProcessProbeTM Cable

3 Installation – Panel Mount
16
TEMPERATURE INPUT CONNECTIONS
The temperature input system is designed to measure resistive temperature
sensors. These can be configured as 2 or 4 wire sensors, although for the specified
accuracy it is necessary to use the 4 wire configuration for cable lengths over 5
metres.
Figure 12 : Standard RTD Temperature Connection
Figure 13 : ProcessProbe 22K Thermistor Connection
The MOD53 can be configured to accept a PT100, PT1000, 1K or 22K thermistor
temperature sensor. (see “Configuration” page)
A A B B A A B B
4 Wire RTD 2 Wire RTD

3 Installation – Panel Mount
17
PRESSURE TRANSMITTER INPUT
The MOD53 can accept a 4-20mA input signal from a pressure transmitter. This
can be scaled within software and permits active pressure compensation of the
dissolved oxygen measurement. The signal can be either 24V loop powered, from
the MOD53, or externally powered from the transmitter. The mode of operation is
selected in the software set-up.
Figure 14 : Pressure Transmitter Connections
{ NB : The negative connection shares the same terminal as the Galvanic sensor
anode connection }
RC2 CLEANER CONNECTION
If the active pressure input is not being used, an RC2 rotary cleaner can be
powered from the “P” terminal. Connect the cleaner terminals through one of the
relay terminals* in the same polarity as for the active pressure input. Set the “P
Mode” function to “Auto” . Set the Pressure “Input” to “24V Loop”. Reset the
“P Mode” function to “Manual” . Configure the chosen relay (*) to “Cleaning” .

3 Installation – Panel Mount
18
DIGITAL INPUTS
The digital inputs are used to externally initiate a clean cycle or take the unit Off-
Line. These inputs are intended to be switched using a volt free link , switch or
relay. Closing the contact will initiate the appropriate action.
Figure 15 : Digital Inputs

4 Installation – Surface Mount
19
4 Installation – Surface Mount
The surface mounting version is designed for fixing to a wall or other flat surface.
Three 6.5 mm diameter holes are provided for this purpose. Note that fasteners
are not provided.
Figure 16 : Overall dimensions surface mounting MOD53
♦ LTH recommend using No. 10 x 1¼ inch round head screws or similar for
mounting.
♦ Care must be taken when fitting the unit to uneven walls or surfaces. Do not
over stress the three mounting lugs.
♦ Over tightening the mounting screws could also break the lugs.
Table of contents
Other LTH Monitor manuals
Popular Monitor manuals by other brands
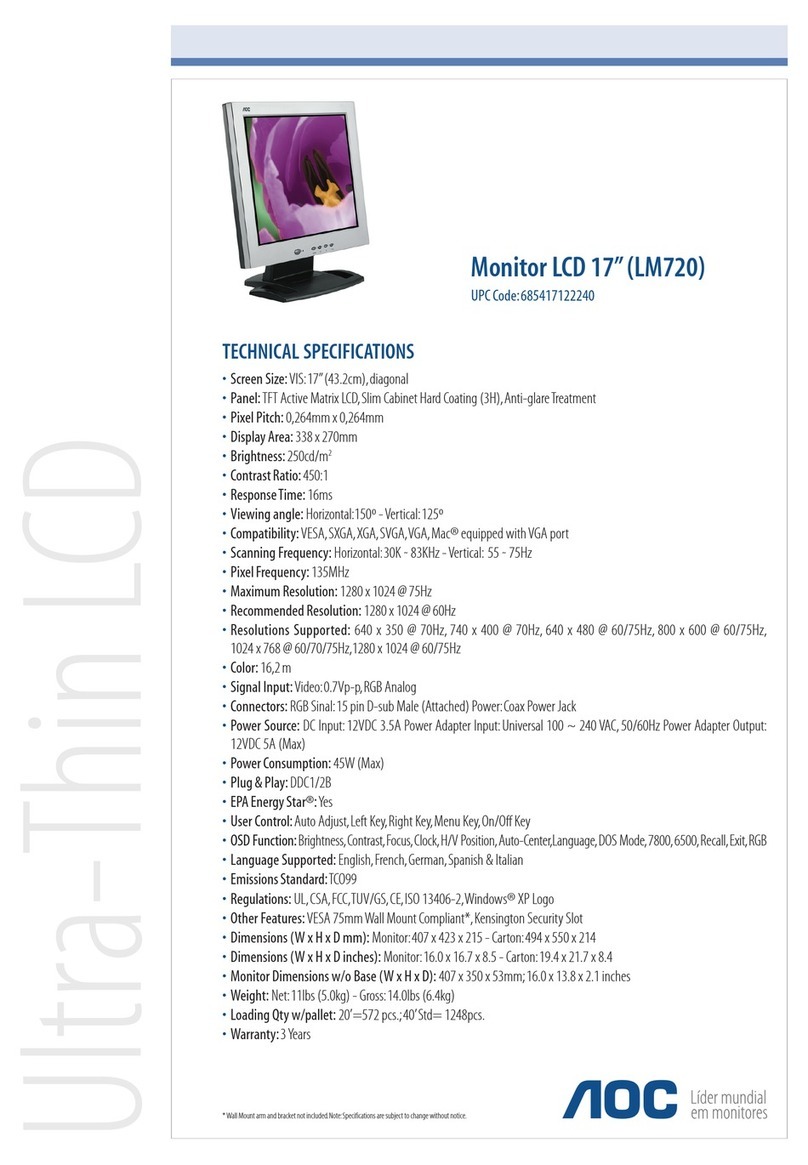
AOC
AOC LM720 - 17" Technical specifications
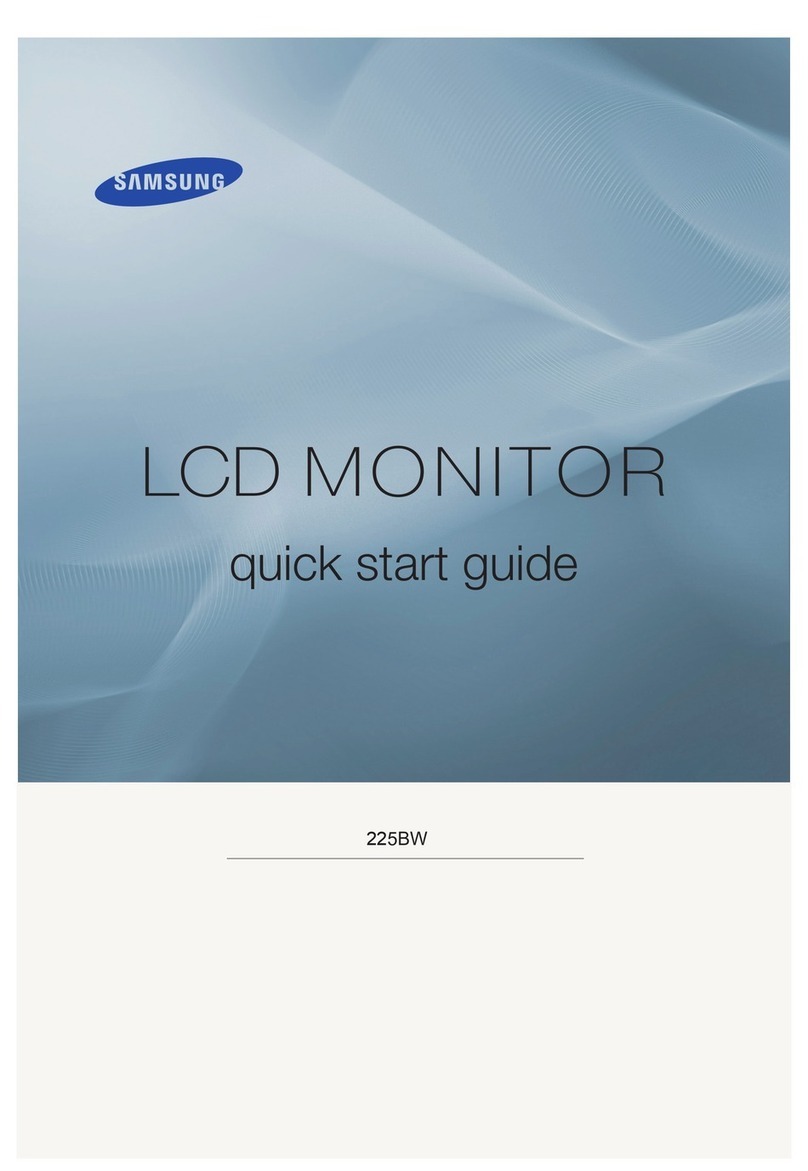
Samsung
Samsung 225BW - SyncMaster - 22" LCD Monitor quick start guide
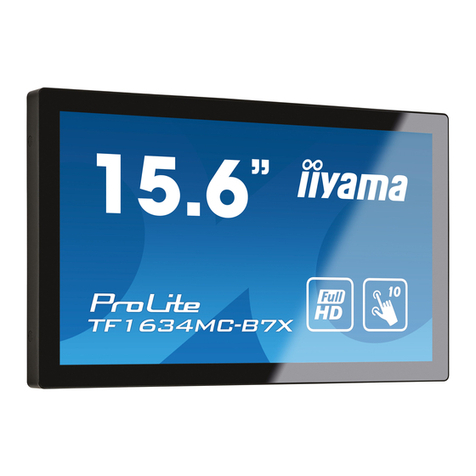
Iiyama
Iiyama ProLite TF1634MC user manual

Pioneer
Pioneer Elite PureVision PRO 1410HD operating instructions

Samsung
Samsung SyncMaster T27A750 E-manual
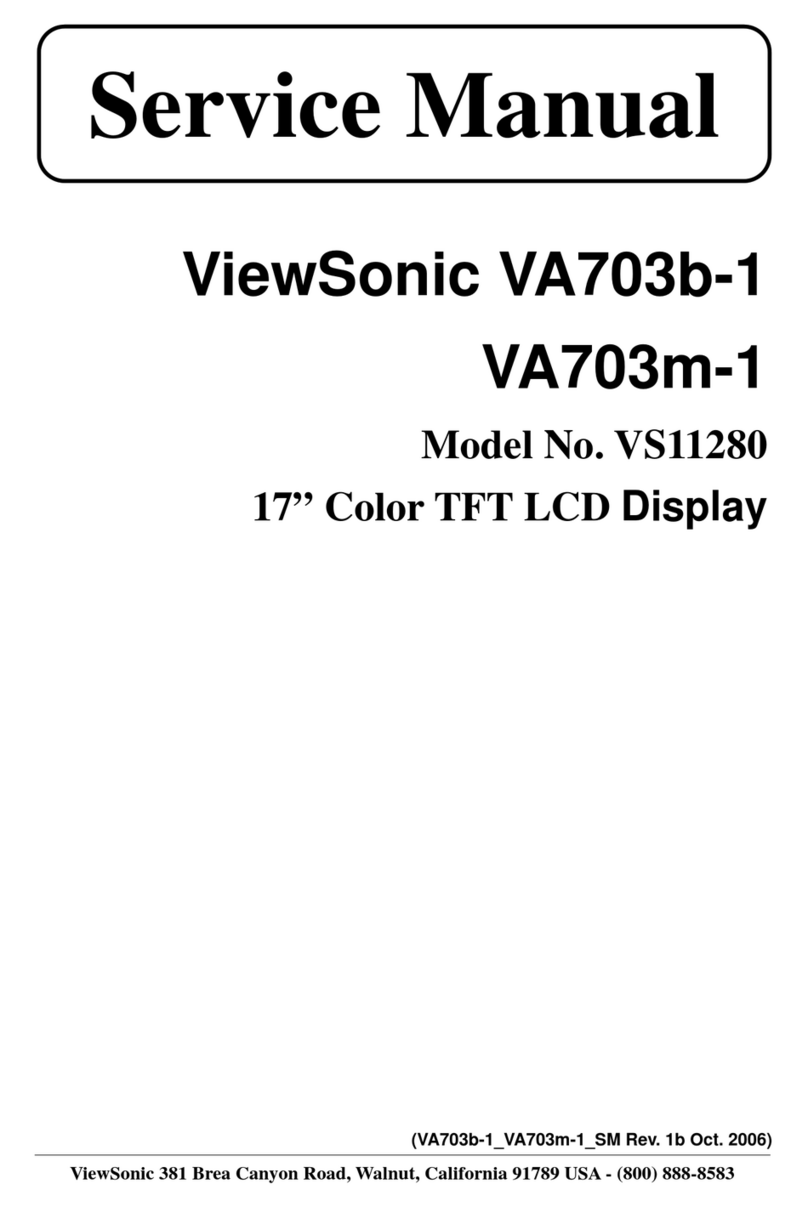
ViewSonic
ViewSonic VA703b-1 Service manual