M-Elec 5411a User manual

5-phase Stepping Motor Driver
GDB-5411A-00
Instructions Manual
(
For desi
g
ners' use
)
PR0819-2
Please ensure to read and understand this
Instructions Manual before using the product.
Please keep this Instructions Manual at hand
so that it is always available for reference.

Introduction
This Instructions Manual describes the safe and proper method of handing
"5-phase Stepping Motor Driver GDB-5411A-00" with emphasis on the specifications,
assuming that our readers are engaged in designing of control devices
incorporating stepping motors.
Please ensure to read and understand this Instructions Manual
before using the product.
Please keep this Instructions Manual at hand
so that it is always available for reference.
-2-

Descriptions in this manual on safety matters:
This product must be operated and used properly.
Otherwise, or when it is operated and used erroneously, unforeseen accidents
may occur, causing physical injuries or property damages.
Majority of these accidents can be avoided if you are well informed of
hazardous circumstances in advance.
Consequently, this instructions manual describes all the hazardous and
dangerous circumstances and situations which can be foreseen and anticipated
as well as necessary precautions.
All the above descriptions are being titled by the following symbol-marks and
signal-words, namely:
Represents warnings ignorance of which can cause accidents
involving fatal or serious physical injuries.
Represents cautions ignorance of which can cause accidents
involving minor physical injuries or property damages.
-3-

Introduction
Descriptions in this manual on safety matters:
CONTENTS PAGE
1. Safety
Overview
3. Name and Function of Each Section
4. Function Set-up by Use
5. Installation
6. Connection
7. Confirmation of Setting and Connection
2.
6
Safety Precautions
7Safety Information for Handling
10
Characteristics
10Product Configuration
10
Appearance
Signal I/O Connector(J1)
DC Input/Motor Output Connector(J2, J3)
POWER LED
Operating Section
Setting MOTOR SELECT switch
Setting STEP ANGLE SELECT switch
Setting HOLD CURRENT ADJUSTMENT trimmer
Setting DRIVE CURRENT SELECT switch
Setting HOLD SWITCHING TIME SELECT switch
Setting Option switch
Conditions for Installation
Mounting Method
Overview of Connection Configuration
Connecting Signal I/O Connector(J1)
Connecting DC Input/Motor Output Connector(J2, J3)
Inputting Power
Check Points
11
12
12
13
14
14
15
16
17
17
18
19
20
21
22
23
24
O.H.A LED 12
1-1.
1-2.
2-1.
2-2.
2-3.
3-1.
3-3.
3-2.
3-4.
3-5.
4-1.
4-2.
4-3.
4-4.
4-5.
4-6.
5-1.
5-2.
6-1.
6-2.
6-3.
6-4.
7-1.
-4-

PAGE
8. Maintenance and Check-up
9. Storing and Disposal
10. Specifications
Maintenance and Check-up
Troubleshooting
Storing
Disposal
I/O Signal
General Specifications
Drive pulse input
Example Circuit Connection
Motor excitation stop input
Step angle switch input
Phase signal output
Overheat alarm signal output
Dimensions
Applicable Motors
Torque Characteristics
(
CW,CCW
)
(
M.F
)
(C.S)
(
P.O
)
(O.H.A)
25
26
27
27
28
34
32
33
35
36
37
30
31
29
8-1.
8-2.
9-1.
10-2.
10-1.
10-3.
10-4.
10-5.
(5)
(4)
(6)
(3)
(2)
(1)
9-2.
-5-

1.Safety
1-1.Safety Precautions
(1) This product is not designed or manufactured for application for equipment
requiring high level of reliability such as equipment related to nuclear
energy, aeronautics-related equipment, automobiles, ships, medical appliances
directly handling the human body and equipment that might seriously affect
properties.
(2) This product is for a devices inclusion.
Please establish it into enclosure without fail.
(3) Ensure to use this product according to the method specified
in the Instructions Manual and within the specifications.
(4) Depending on the operational conditions, the stepping motor may step out when
it is on holding-state or driving-state.
In particular, the load in transport may fall if the motor steps out on the
vertical drive (such as the Z-axis).
Start operation after test run for deliberate confirmation of operation.
(5) The stepping motor may attain high temperature, depending on the operational
conditions.
If the surface temperature exceeds 100℃, provide cooling measures to control
it to operate at 100℃ at the highest.
(6) Please do not touch the driver during after operation for a while,
may cause burn on the skin due to overheating of the driver.
(7) Provide fail-safe measures so that the entire system may operate in a safe
mode even in cases of the external power supply failure, disconnection of the
signal line, or any failure on the driver.
-6-

1-2.Safety Information for Handling
●Overall:
Please do not touch the driver during
after operation for a while,
it may cause burn on the skin due to
overheating of the driver.
●When setting up the MOTOR SELECT switch:
Erroneous setting may cause burn on the
skin due to overheating of the motor.
Ensure correct setting.
●When setting up the STEP ANGLE SELECT switch:
Erroneous setting may cause breakage of
the machine or injury due to unexpected
rotation of the motor.
Ensure correct setting.
●When setting up the HOLD CURRENT ADJUSTMENT trimmer:
A high setting value may cause burn on the
skin due to overheating of the motor.
Do not select a high value beyond the
required.
●When setting up the DRIVE CURRENT SELECT switch:
Erroneous setting may cause burn on the
skin due to overheating of the motor.
Ensure correct setting.
-7-

●When installing:
Overheating may cause fire.
Mount it on a noncombustible member.
Keep it away from combustibles.
●When connecting the DC Input/Motor Output Connectors (J2, J3):
Erroneous connection may result
in breakage of the motor.
Correctly connect the motor wiring.
●When inputting power:
Breakage of the machine or injury is
apprehended due to unexpected behavior of
the motor. Maintain the state where
emergency stop is enabled at any time.
●When performing maintenance and checking:
Injury or fire is apprehended due to
unexpected behavior.
Do not replace fuse.
Do not disassemble, repair or modify.
●When inputting the motor excitation stop (M.F) signal:
Deterioration of the holding power with
the motor may cause breakage of machine
or injury.
Check safety before inputting.
-8-

●When the overheat alarm (O.H.A) signal is output:
Overheating may cause fire.
Stop operation upon output of this signal.
-9-

2.
O
verv
i
ew
2-1.Characteristics
GDB-5411A-00 is a driver for a 5-phase stepping motor with DC +24V input.
It can drive a 5-phase stepping motor ranging from 0.75A/phase ~ 1.4A/phase.
Ten step angles can be selected from angles ranging from a 1/1 division to
a 1/800 division of the basic angle.
HOLD CURRENT and DRIVE CURRENT can be set up.
2-2.Product Configuration
The product consists of the main frame and the accessories.
●GDB-5411A-00 One unit
●Housing for J1 (51103-1200:Molex) One unit (accessory)
●Housing for J2 (51067-0200:Molex) One unit (accessory)
●Housing for J3 (51067-0500:Molex) One unit (accessory)
●Contact for J1 (50351-8100:Molex) 14 contacts (accessories,2 for spares)
●Contact for J2,J3 (50217-9101:Molex) 9 contacts (accessories,2 for spares)
2-3.Appearance
-10-

3.Name and Function of Each Section
3-1.Signal I
/
O Connector(J1)
GDB-5411A-00
J1
CW+
●Directs the motor to operate CW.
CW-
CCW+
●Directs the motor to operate CCW.
CCW-
M.F+
●Shuts off output current to drive the motor.
M.F-
P.O ●Outputs the signal when the motor-excitation
state is the excitation home position.
R.GND
O.H.A ●Outputs the signal when internal temperature
of the driver has reached approx. 70℃ or more.
R.GND
C.S+
●Switches the step angle by 1/20 division.
C.S-
12
11
6
5
10
9
8
7
4
3
2
1CW drive pulse signal input terminal
CCW drive pulse signal input terminal
Motor excitation stop signal input terminal
Step angle switching signal input terminal
Phase signal output terminal
GND terminal for P.O signal.
Overheat alarm signal output terminal
GND terminal for O.H.A signal.
-11-

3-2.DC Input
/
Motor Output Connector(J2,J3)
GDB-5411A-00
●Power input terminal.
J3 DC power supply is connected.
●Outputs current to drive the motor.
3-3.POWER LED
POWER LED(GREEN) comes on upon inputting power.
3-4.O.H.A LED
O.H.A LED(RED)comes on when internal temperature
of the driver has reached approx. 70℃ or more.
2
1BLK
RED
J2
DC+24V
BLU 5
2
1
0V DC-
VIO
ORN
YLW
DC+
ORN 4
3
GRN
BLU
RED
GRY
BLK
BRN
YLW
WHT
Motor output terminal
DC input terminal
-12-

3-5.Operation Section
GDB-5411A-00
[DRIVE I.SEL]
[STEP SEL]
[DHT SEL] 16ms -150ms
[MOTOR SEL] 5L -10L
(ON - 0FF)
[HOLD I.ADJ]
Factory
Setting
Name of Operation Section
Option switch
(Option LED) -
MOTOR
SELECT switch
STEP ANGLE
SELECT switch
Sub adjustment
switch
HOLD CURRENT
ADJUSTMENT trimmer
DRIVE CURRENT
SELECT switch
〔40%〕
〔No.F〕
HOLD SWITCHING TIME
SELECT switch
Function
At present there is not a function.
Adjusts HOLD CURRENT.
Selects DRIVE CURRENT.
〔No.1〕
DRIVE/HOLD CURRENT automatic switching time
is selected.
Selects the applicable motor.
Selects a step angle.
Please use it with OFF. 〔OFF〕
〔150ms〕
〔10L〕
DRIVE CURRENT
SELECT switch
HOLD CURRENT
ADJUSTMENT trimmer
STEP ANGLE
SELECT switch
Sub adjustment
switch
MOTOR
SELECT switch
Option
switch
HOLD SWITCHING TIME
SELECT switch
O.H.A LED(RED)
Option LED
POWER LED(GREEN)
H
L
-13-

4.Function Set-up by Use
4-1.Setting MOTOR SELECT switch
Erroneous setting may cause burn on the
skin due to overheating of the motor.
Ensure correct setting.
The MOTOR SEL switch is turned to the setting
corresponding to the motor in use.
Set this switch with power OFF.
The switch is factory-set to [10L].
(1) Turn power [OFF].
(2) Turn switch1 [10L/5L] to the setting specified in the table
"10-4. Applicable Motors."
4-2.Setting STEP ANGLE SELECT switch
Erroneous setting may cause breakage of
the machine or injury due to unexpected
rotation of motor.
Ensure correct setting.
The step angle is set up with the STEP SEL switch.
The step angle can be selected from ten different
types of step angles.
The switch is factory-set to [No.1].
(2) Set the switch No. to the step angle required.
●Relationship between the STEP SEL switch No. and the step angle.
(Factory setting)
●Drive with two types of step angles are provided by combining
the STEP SEL switch setting and the C.S signal.
0.18
0.072
0.0018
0.0009
0.036
0.018
0.0072
0.0036
6
7
Switch
No.
1
2
3
4
0
8
9
Number of
Divisions
1/1
1/2
1/4
1/10
1/20
1/405
1/100
1/200
1/400
1/800
Step angle(°)
0.72°motor
0.72
0.36
-14-

4-3.Setting HOLD CURRENT ADJUSTMENT trimmer R1
A high setting value may cause burn on the
skin due to overheating of the motor.
Do not select a high value beyond the
required.
HOLD CURRENT is set up with the HOLD I.ADJ trimmer.
This sets the ratio of HOLD CURRENT to DRIVE CURRENT.
The trimmer is factory-set to approx. 40%.
(1) Set the gauge of the trimmer to the required value.
●Relationship between the trimmer scales and HOLD CURRENT.
HOLD CURRENT
DRIVE CURRENT
Ratio of HOLD CURRENT
Trimmer
Scale of the trimmer
● HOLD CURRENT changes relative to DRIVE CURRENT setting.
The ratio of HOLD CURRENT of 100% represents the same as the setting for
DRIVE CURRENT.
● The greater the ratio of HOLD CURRENT grows, the more heat the motor
generates when is on holding-state.
● When the trimmer is set minimum, HOLD CURRENT is approx. 10% or less of
DRIVE CURRENT.
=Ratio of HOLD CURRENT(%) ×100
100%
50%
0% 0234689715 10
Factory setting
-15-

4-4.Setting DRIVE CURRENT SELECT switch
Erroneous setting may cause burn on the
skin due to overheating of the motor.
Ensure correct setting.
DRIVE CURRENT is set up with the DRIVE I.SEL switch.
The switch is factory-set to [No.F].
(1) Set the switch No. to the setting specified in the table "10-4. Applicable Motors."
●Relationship between the DRIVE I.SEL switch and DRIVE CURRENT.
(Factory setting) (Factory setting)
C
D
E
8
9
A
B
4
5
6
7
0
1
2
3
0.44
0.48
0.51
0.54
0.58
0.61
0.64
0.68
switch No.
MOTOR SEL switch
switch1:ON
[5L]setting
F
A/phase
0.17
0.20
0.24
0.27
0.31
0.34
0.37
0.41
switch No. A/phase
MOTOR SEL switch
switch1:OFF
[10L]setting
0
1
0.34
0.40
2
3
0.47
0.54
4
5
0.61
0.67
6
7
0.74
0.81
8
9
0.88
0.95
A
B
1.01
1.08
C
D
1.15
1.21
E
F
1.28
1.35
-16-

4-5.Setting HOLD SWITCHING TIME SELECT switch
DRIVE/HOLD CURRENT automatic switching time is set up
with the HOLD SWITCHING TIME SELECT switch.
The switch is factory-set to [150ms].
(1) Set the switch2 [150ms/16ms].
4-6.Setting Option switch
At present there is not a function.
Hold Switching
Time
switch2
ON
OFF
16ms
150ms
-17-

5.
I
nsta
ll
at
i
on
5-1.Conditions for Installation
Overheating may cause fire.
Mount it on a noncombustible member.
Keep it away from combustibles.
(1) Designed for incorporating into equipment used indoors, this product requires
to be installed in the following environment:
●Indoors (where it is not exposed to direct sun).
●Where ambient temperature and humidity are controlled within the range set
out in the specifications.
●Where there is no corrosive or inflammable gas.
●Where it can be protected from dust, salt or iron powder.
●Where the product main frame is not exposed to direct vibration or shock.
●Where it is not exposed to splashes of water, oil or chemicals.
(2) Install the driver at least 15mm away from other equipment.
(3) Considering heat release, control the ambient temperature around the driver
within the specified value.
●
Take measures against accumulation of heat such as allowing generous space
around the driver or installing a fan so that heat release is taken care of.
●
Install the driver securely in contact with metal or other substance with
adequate heat conductivity.
(4) In the case that an overheat alarm signal is output, perform the cooling measure of
the mounting plate is enlarged or compulsion air cooling etc.
Use the driver on the condition that an overheat alarm signal is not output.
(5) Do not allow standing or placing anything heavy on the product.
15mm or more
15mm or more
15mm or more
GDB-5411A GDB-5411A
15mm or more
-18-

5-2.Mounting Method
The round holes on the main body are used.
The following items are required:
(1) Fix the product at the two round holes on the main body.
●Mounting example
2●M-3 screw (8mm or more in length):
2
2
●M-3 spring washer:
●M-3 flat washer:
GDB-5411A-00
Fixing with a screw x 2
M-3 spring washer
M-3 flat washer
M-3 screw
-19-

6.Connection
6-1.Overview of Connection Configuration
DC Power Supply
0V(GND)
DC+24V
User GDB-5411A-00
Controller
Twisted J2 2 1 J3 54321
pair wire J1
CWP CW+
CWP CW-
CCWP CCW+
CCWP CCW-
+COM M.F+
M.F M.F-
P.O P.O
R.GND R.GND
O.H.A O.H.A
R.GND R.GND
+COM C.S+
C.S C.S-
●Connect only one motor to one driver.
●Do not power ON/OFF by the relay etc. in the output side of the DC power supply.
●Use twisted pair wire for the CW/CCW input signal line.
●Provide shielding for the signal line where considerable noise is generated.
●Use the wire material of the characteristic that is difficult to burn.
●Provide shielding for the motor line if it generates significant noise.
●Use the DC power supply that was reinforced insulation between primary-side
and secondary-side.
〔Example configuration〕
The metallic enclosure and shielded wires work to shield noise.
Metal Enclosure Metal Enclosure
Metal Enclosure
User
Controller
1
2
3
4
5
6
7
8
GDB-5411A
9
10
11
12
MOTOR
MOTOR
Shield Shield
DC-
DC+
Grounding Grounding Grounding
-20-
This manual suits for next models
1
Table of contents
Other M-Elec Engine manuals
Popular Engine manuals by other brands

Castle Creations
Castle Creations Copperhead 10 quick start guide
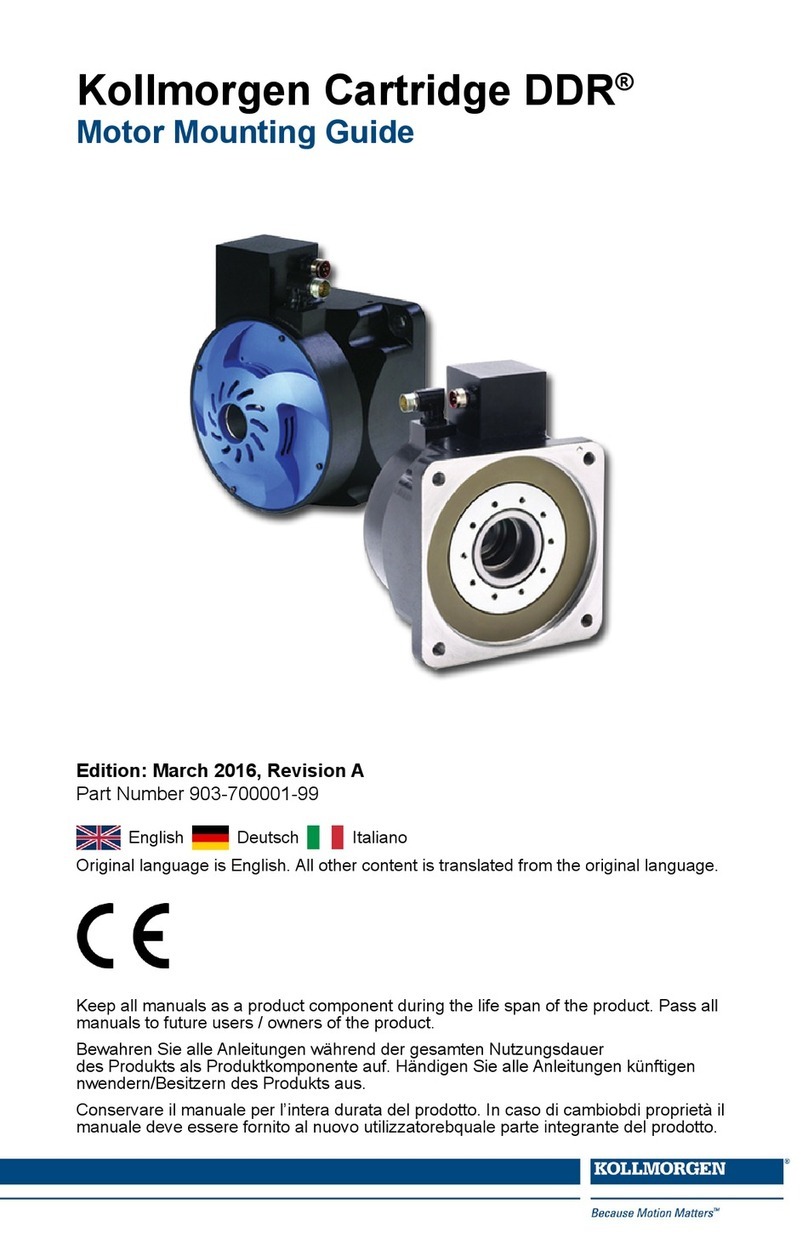
Kollmorgen
Kollmorgen CARTRIDGE DDR Mounting guide

Briggs & Stratton
Briggs & Stratton Vanguard 290000 Operator's manual

Detroit Diesel
Detroit Diesel 60 Operator's guide
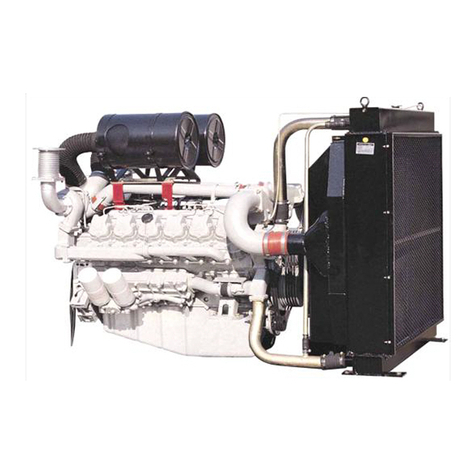
Doosan
Doosan PU158TI Operation & maintenance manual
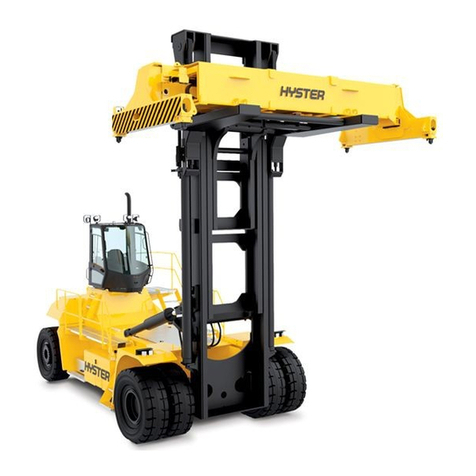
Hyster
Hyster G117 Service & repair manual
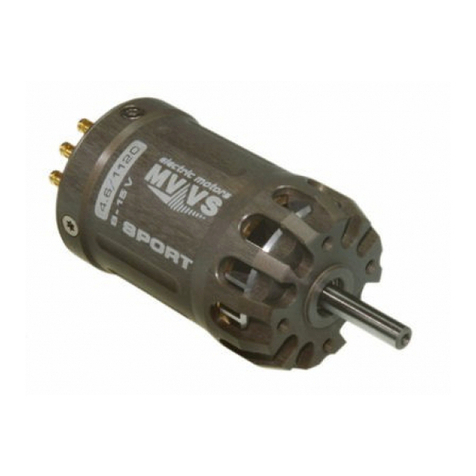
MVVS
MVVS 4.6-1120 SPORT - V1.4 user manual
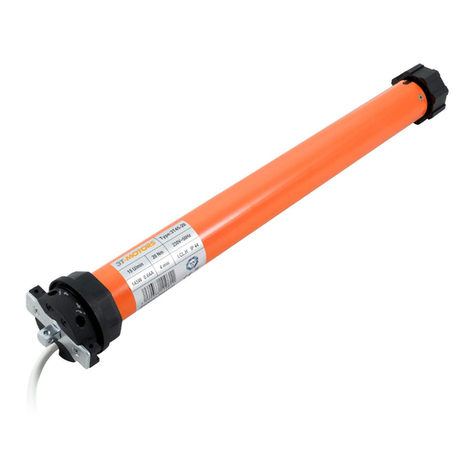
3T-Components
3T-Components 3T-MOTORS 3T45-20 Installation & operating instructions
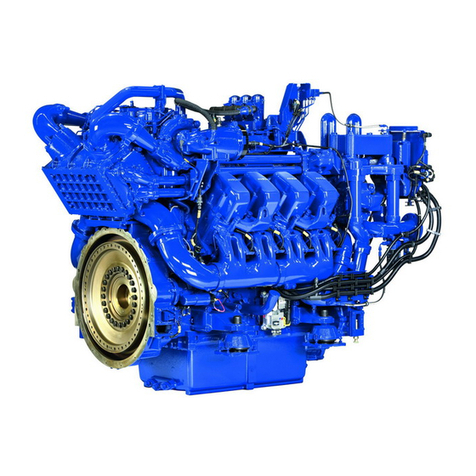
MTU
MTU 8V4000M*3 series operating instructions
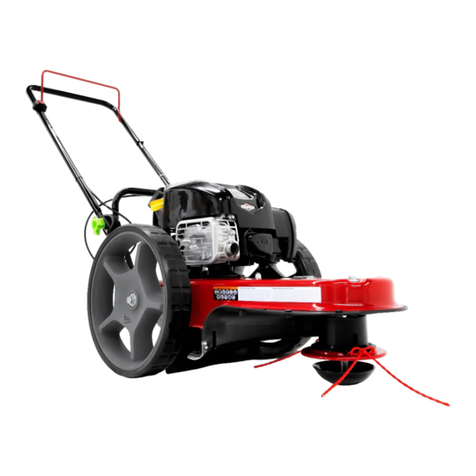
Viper
Viper 163cc Operator's manual
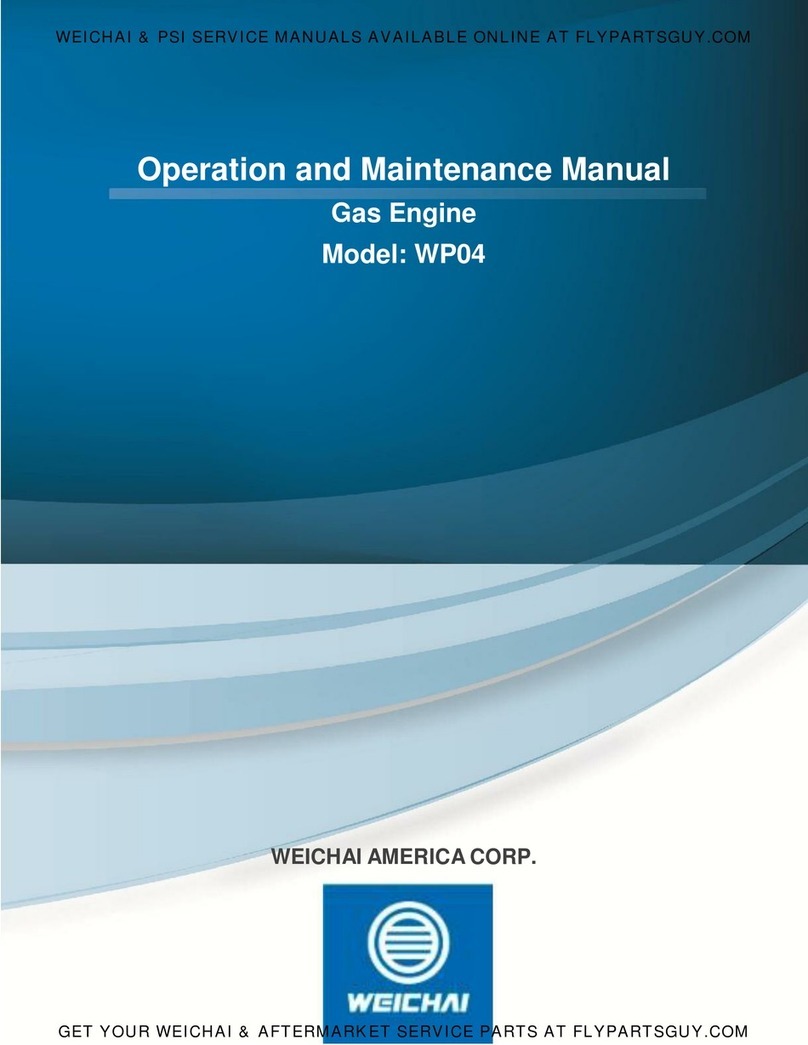
WEICHAI
WEICHAI WP4GNA Operation and maintenance manual
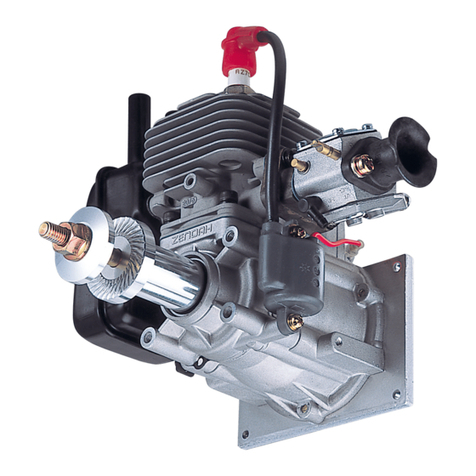
Zenoah
Zenoah G231PUM Owner's service manual