M-Elec GDB-5F40 User manual

-phase Stepping Motor Driver
GDB-5F40
Instructions Manual
(
For desi
g
ners' use
)
MN0091-1

Introduction
This Instructions Manual describes the safe and proper method of handing
"5-phase Stepping Motor Driver GDB-5F40" with emphasis on the specifications,
assuming that our readers are engaged in designing of control devices
incorporating stepping motors.
Please ensure to read and understand this Instructions Manual
before using the product.
Please keep this Instructions Manual at hand
so that it is always available for reference.
-2-

Descriptions in this manual on safety matters:
This product must be operated and used properly.
Otherwise, or when it is operated and used erroneously, unforeseen accidents
may occur, causing physical injuries or property damages.
Majority of these accidents can be avoided if you are well informed of
hazardous circumstances in advance.
Consequently, this instructions manual describes all the hazardous and
dangerous circumstances and situations which can be foreseen and anticipated
as well as necessary precautions.
All the above descriptions are being titled by the following symbol-marks and
signal-words, namely:
Represents warnings ignorance of which can cause accidents
involving fatal or serious physical injuries.
Represents cautions ignorance of which can cause accidents
involving minor physical injuries or property damages.
-3-

Introduction
Descriptions in this manual on safety matters:
CONTENTS PAGE
1. Safety
Overview
3. Name and Function of Each Section
4. Setting
5. Installation
6. Connection
7. Confirmation of Setting and Connection
2.
6
Safety Precautions
7Safety Information for Handling
10
Characteristics
10Product Configuration
10
Appearance
Signal I/O Connector(J1)
DC Input/Motor Output Connector (J2, J3)
POWER LED
Operating Section
Setting STEP TABLE switch and STEP ANGLE SELECT switch
Setting HOLD CURRENT SELECT switch
Setting DRIVE CURRENT SELECT switch
Setting PULSE INPUT TYPE SELECT switch
Setting HOLD SWITCHING TIME SELECT switch
Conditions for Installation
Mounting Method
Overview of Connection Configuration
Connecting Signal I/O Connector (J1)
Connecting DC Input/Motor Output Connector (J2, J3)
Inputting Power
Check Points
11
12
12
13
15
16
17
18
19
20
21
22
23
24
25
26
O.H.A LED 12
1-1.
1-2.
2-1.
2-2.
2-3.
3-1.
3-3.
3-2.
3-4.
3-5.
4-2.
4-3.
4-4.
4-5.
4-6.
5-1.
5-2.
6-1.
6-2.
6-3.
6-4.
7-1.
Setting MOTOR SELECT switch 144-1.
-4-

Instructions Manual
PAGE
8. Maintenance and Check-up
9. Storing and Disposal
10. Specifications
The main parts which revised by this manual
Maintenance and Check-up
Troubleshooting
Storing
Disposal
I/O Signal
General Specifications
Drive pulse input
Example Circuit Connection
Motor excitation stop input
Step angle switch input
Phase signal output
Overheat alarm signal output and overheat alarm LED
Dimensions
Applicable Motors
Torque Characteristics
(CW,CCW)
(M.F)
(C.S)
(P.O)
(O.H.A)
27
28
29
29
30
36
34
35
37
38
39
32
33
31
8-1.
8-2.
9-1.
10-2.
10-1.
10-3.
10-4.
10-5.
(5)
(4)
(6)
(3)
(2)
(1)
9-2.
45
10-6. Conforming to Europe standards
-5-

1.Safety
1-1.Safety Precautions
(1) This product is not designed or manufactured for application for equipment
requiring high level of reliability such as equipment related to nuclear
energy, aeronautics-related equipment, automobiles, ships, medical appliances
directly handling the human body and equipment that might seriously affect
properties.
(2) Do not use or keep the product in explosive or corrosive environments,
in the presence of flammable gases, locations subjected to splashing water,
fine particles, soot, steam, or exposed to radiation or direct sunshine.
Doing so may cause injury or fire.
(3) For the driver's power supply, use a DC power supply with reinforced insulation
on its primary and secondary sides.
Failure to do so may cause electric shock.
(4) This product is designed for use within machinery, so it should be installed
within an enclosure.
Failure to do so may cause injury.
(5) Do not transport, move, install the product, perform connections or inspections
when the power is on.
Doing so may cause electric shock, injury or fire.
(6) Only qualified personnel are allowed to transport, move, install the product,
perform connections or inspections.
Failure to do so may cause injury or fire.
(7) Do not touch the driver during operation or immediately after stopping.
Doing so may cause burn on the skin due to overheating of the driver.
(8) Ensure to use this product according to the method specified
in the Instructions Manual and within the specifications.
(9) Depending on the operational conditions, the stepping motor may step out when
it is on holding-state or driving-state.
In particular, the load in transport may fall if the motor steps out on the
vertical drive (such as the Z-axis).
Start operation after test run for deliberate confirmation of operation.
(10) Provide fail-safe measures so that the entire system may operate in a safe
mode even in cases of the external power supply failure, disconnection of the
signal line, or any failure on the driver.
-6-

1-2.Safety Information for Handling
●Overall:
Do not touch the driver during operation
or immediately after stopping.
it may cause burn on the skin due to
overheating of the driver.
●When setting up the MOTOR SELECT switch:
Erroneous setting may cause burn on the
skin due to overheating of the motor.
Ensure correct setting.
●When setting up the STEP ANGLE SELECT switch:
Erroneous setting may cause breakage of
the machine or injury due to unexpected
rotation of the motor.
Ensure correct setting.
●When setting up the HOLD CURRENT SELECT switch:
A high setting value may cause burn on the
skin due to overheating of the motor.
Do not select a high value beyond the
required.
-7-

●When setting up the DRIVE CURRENT SELECT switch:
A high setting value may cause burn on the
skin due to overheating of the motor.
Do not select a high value beyond the
required.
●When setting up the PULSE INPUT TYPE SELECT switch:
Erroneous setting may cause breakage of
the machine or injury due to unexpected
rotation of the motor.
Ensure correct setting.
●When installing:
Overheating may cause fire.
Mount it on a noncombustible member.
Keep it away from combustibles.
●When connecting the DC Input/Motor Output Connectors (J2, J3):
Erroneous connection may cause
breakage of the motor or the driver.
Correctly connect the DC Input/Motor
output connector.
●When inputting power:
Breakage of the machine or injury is
apprehended due to unexpected behavior of
the motor. Maintain the state where
emergency stop is enabled at any time.
-8-

●When inputting the motor excitation stop (M.F) signal:
Deterioration of the holding power with
the motor may cause breakage of the machine
or injury.
Check safety before inputting.
●When the overheat alarm (O.H.A) signal is output:
Overheating may cause fire.
Stop operation upon output of this signal.
●When performing maintenance and checking:
Injury or fire is apprehended due to
unexpected behavior.
Do not replace fuse.
Do not disassemble, repair or modify.
-9-

2.
O
verv
i
ew
2-1.Characteristics
GDB-5F40 is a driver for a 5-phase stepping motor with DC +24V input.
It can drive a 5-phase stepping motor with 0.75A/phase and 1.4A/phase.
Step angles can be selected from seventeen step angles ranging from 1 division to
4000 division of the basic angle.
HOLD CURRENT and DRIVE CURRENT can be set up.
● Applicable motors and setting for each motor are given in the table
"10-4. Applicable Motors".
2-2.Product Configuration
The product consists of the main frame and the accessories.
●GDB-5F40 One unit
●Housing for J1 (51103-1200:Molex) One unit (accessory)
●Housing for J2 (51067-0200:Molex) One unit (accessory)
●Housing for J3 (51067-0500:Molex) One unit (accessory)
●Contact for J1 (50351-8100:Molex) 14 contacts (accessories,2 for spares)
●Contact for J2,J3 (50217-9101:Molex) 9 contacts (accessories,2 for spares)
2-3.Appearance
-10-

3.Name and Function of Each Section
3-1.Signal I
/
O Connector(J1)
GDB-5F40
J1
CW+
●Directs the motor to operate CW.
CW-
CCW+
●Directs the motor to operate CCW.
CCW-
M.F+
●Shuts off output current to drive the motor.
M.F-
P.O ●Outputs the signal when the motor-excitation
state is the excitation home position.
R.GND
O.H.A ●Outputs the signal when internal temperature
of the driver has reached approx. 70℃ or more.
R.GND
C.S+
●Switches the step angle by 20 division.
C.S-
4
3
2
1
12
11
6
5
10
9
8
7
CW drive pulse signal input terminal
CCW drive pulse signal input terminal
Motor excitation stop signal input terminal
Step angle switching signal input terminal
Phase signal output terminal
GND terminal for P.O signal.
Overheat alarm signal output terminal
GND terminal for O.H.A signal.
-11-

3-2.DC In
p
ut/Motor Out
p
ut Connector(J2,J3)
GDB-5F40
J3
●Outputs current to drive the motor.
●Power input terminal.
DC power supply is connected.
3-3.POWER LED
POWER LED(GREEN) comes on upon inputting power.
3-4.O.H.A LED
O.H.A LED(RED)comes on when internal temperature
of the driver has reached approx. 70℃ or more.
RED GRN 2
GRY
VIO BLK 1
BLU
ORN 3
YLW
WHT RED 4
ORN
BLK
GRN BLU 5
BRN
0V DC- 2
J2
DC+24V DC+ 1
DC input terminal
Motor output terminal
-12-

3-5.Operating Section
4
1
4
3
2
1
Name of Operating Section
STEP ANGLE SELECT switch
[OFF]
[OFF]
Sub adjustment switch
STEP TABLE switch
Name of Operating Section
Name of Operating Section Function
Sub adjustment switch
[OFF]
Factory
Setting
Factory
Setting
Function
Selects a step angle.
Function
[OFF(DH1)]
〔No.1〕
Factory
Setting
HOLD CURRENT SELECT switch Selects HOLD CURRENT. 〔No.3〕
DRIVE CURRENT SELECT switch Selects DRIVE CURRENT. 〔No.F〕
[OFF]
2
3 PULSE INPUT TYPE
SELECT switch Selects a pulse input type. 〔OFF(2P)〕
Use it with OFF.
HOLD SWITCHING TIME
SELECT switch
MOTOR SELECT switch
DRIVE/HOLD CURRENT automatic switching
time is selected.
Selects STEP TABLE. 〔OFF(S.T1)〕
Sub adjustment switch Use it with OFF. [OFF]
Use it with OFF.
Use it with OFF.
Use it with OFF. Sub adjustment switch
-13-

4.Setting
4-1.Setting MOTOR SELECT switch
Erroneous setting may cause burn on
the skin due to overheating of the
motor.
Ensure correct setting.
Set this switch with power OFF.
The switch is factory-set to [OFF].
(1) Use it with [OFF].
-14-

4-2.Setting STEP TABLE switch and STEP ANGLE SELECT switch
Erroneous setting may cause breakage of
the machine or injury due to unexpected
rotation of motor.
Ensure correct setting.
The step angle is set up with the S.T SEL switch and
the STEP SEL switch.
The step angle can be selected from seventeen different
types of step angles.
The switch is factory-set to [S.T1] [No.1].
Set S.T SEL switch with power OFF.
(1) Turn power [OFF].
(2) Set the step angle required by combining the S.T SEL switch
and the STEP SEL switch No.
●Step angles are theoretical values.
●Drive with two types of step angles are provided by combining the C.S signal.
●When the step angle is switched from the setting of 1000, 2000 or 4000
divisions to other number of divisions(1~800), change of the excitation position
may be caused.
●Relationship between the S.T SEL switch, the STEP SEL switch No. and the step
angle.
0 1/1 0.72 0
S.T SEL switch〔OFF:S.T1〕 S.T SEL switch〔ON:S.T2〕
STEP SEL No. 1/
Divisions
step angle(°) STEP SEL No. 1/
Divisions
step angle(°)
0.72°motor 0.72°motor
--
1 1/2 0.36 1
--
--
--
2 1/4
3 1/10 0.072 3
0.18 2
4 1/20 0.036 4
--
5 1/40 0.018 5
--
--
--
6 1/100
7 1/200 0.0036 7
0.0072 6
8 1/400 0.0018 8
--
9 1/800 0.0009 9
--
--
--
A 1/1000
B 1/2000 0.00036 B
0.00072 A
C 1/4000 0.00018 C
1/80 0.009
D- -D
1/8 0.09
1/16 0.045
1/160 0.0045
E-
F- -F
-E
-15-

4-3.Setting HOLD CURRENT SELECT switch
A high setting value may cause burn on the
skin due to overheating of the motor.
Do not select a high value beyond the
required.
HOLD CURRENT is set up with the HOLD I. SEL switch.
The ratio of HOLD CURRENT to DRIVE CURRENT can be selected.
The switch is factory-set to [No.3 (approx 40%)].
(1)
●Relationship between the HOLD CURRENT.
HOLD CURRENT
DRIVE CURRENT
Ratio of HOLD CURRENT
(Factory setting)
●
HOLD CURRENT changes relative to DRIVE CURRENT setting.
The ratio of HOLD CURRENT set the switch No. to [No.9] : 100% represents
the same as the setting for DRIVE CURRENT.
● When the DRIVE I.SEL switch is set to No.0 ~ No.2, the useful range
of the HOLD I.SEL switch becomes No.1 ~ No.9.
●The greater the ratio of HOLD CURRENT grows, the more heat the motor
generates when is on holding-state.
9 100
890
780
670
560
450
340
0-
230
120
Set the HOLD I.SEL switch No. to the ratio of HOLD CURRENT to DRIVE CURRENT
required.
×100=Ratio of HOLD CURRENT(%)
DRIVE I.SEL〔No.0~No.2〕
Ratio of
HOLD CURRENT(%)
DRIVE I.SEL〔No.3~No.F〕
HOLD I.SEL No. Ratio of
HOLD CURRENT(%)
HOLD I.SEL No.
010
120
230
340
450
560
670
780
890
9 100
-16-

4-4.Setting DRIVE CURRENT SELECT switch
A high setting value may cause burn on the
skin due to overheating of the motor.
Do not select a high value beyond the
required.
DRIVE CURRENT is set up with the DRIVE I.SEL switch.
The switch is factory-set to [No.F].
(1) Set the switch No. to the setting specified in the table "10-4. Applicable Motors."
●Relationship between the DRIVE I.SEL switch and DRIVE CURRENT.
(Factory setting)
switch No. A/phase
0
1
0.30
0.325
2
3
0.35
0.40
4
5
0.50
0.60
8
9
0.80
0.90
6
7
0.70
0.75
1.20
1.25
C
D
E
F
1.30
1.35
A
B
1.05
1.15
-17-

4-5.Setting PULSE INPUT TYPE SELECT switch
Erroneous setting may cause breakage of
the machine or injury due to unexpected
rotation of motor.
Ensure correct setting.
Pulse input method is set up with the SPI SEL switch.
Set this switch with power OFF.
The switch is factory-set to 2-pulse input method[2P].
(1) Turn power [OFF].
(2) Set the SPI SEL [2P/1P] switch.
●When the motor is operated with two pulse signal inputs of CW and CCW,
set the SPI SEL switch to [OFF(2P)].
●When the motor is operated with the pulse signal and direction signal
input, set the SPI SEL switch to [ON(1P)].
● In the case that 1-pulse input method is selected, the CCW terminal becomes
direction signal input designating the direction of the motor rotation.
Drive pulse set to the CW terminal(CW+,CW-).
● The input timing is same with 2-pulse input method and 1-pulse input method .
As for input timing, refer to "10-2. (2)Drive pulse input(CW, CCW)"
SPI SEL
ON
OFF
Input type
1PULSE (1P)
2PULSE (2P)
CCW terminal(CCW+,CCW-)
direction set
Photo-cou
p
ler OFF: CCW direction
Photo-cou
p
ler ON : CW direction
-18-

4-6.Setting HOLD SWITCHING TIME SELECT switch
DRIVE/HOLD CURRENT automatic switching time is set up
with the DHT SEL switch.
The switch is factory-set to [DH1].
(1) Set the DHT SEL [DH1/DH2] switch.
Hold Switching
Time
DHT SEL
ON
OFF
DH2(16ms)
DH1(150ms)
-19-

5.
I
nsta
ll
at
i
on
5-1.Conditions for Installation
Overheating may cause fire.
Mount it on a noncombustible member.
Keep it away from combustibles.
(1) Designed for incorporating into equipment used indoors, this product requires
to be installed in the following environment:
●Indoors (where it is not exposed to direct sun).
●Where ambient temperature and humidity are controlled within the range set
out in the specifications.
●Where there is no explosive, corrosive or inflammable gas.
●Where it can be protected from dust, salt or iron powder.
●Where the product main frame is not exposed to direct vibration or shock.
●Where it is not exposed to splashes of water, oil or chemicals.
(2) Install the driver at least 15mm away from other equipment.
(3) Considering heat release, control the ambient temperature around the driver
within the specified value.
●
Take measures against accumulation of heat such as allowing generous space
around the driver or installing a fan so that heat release is taken care of.
●
Install the driver securely in contact with metal or other substance with
adequate heat conductivity.
(4) In the case that the overheat alarm signal is output, perform the cooling measure
of the mounting plate is enlarged or compulsion air cooling etc.
Use the driver on the condition that the overheat alarm signal is not output.
(5) Do not allow standing or placing anything heavy on the product.
15mm or more
15mm or more
15mm or more
GDB-5F40 GDB-5F40
15mm or more
-20-
Table of contents
Popular Industrial Electrical manuals by other brands
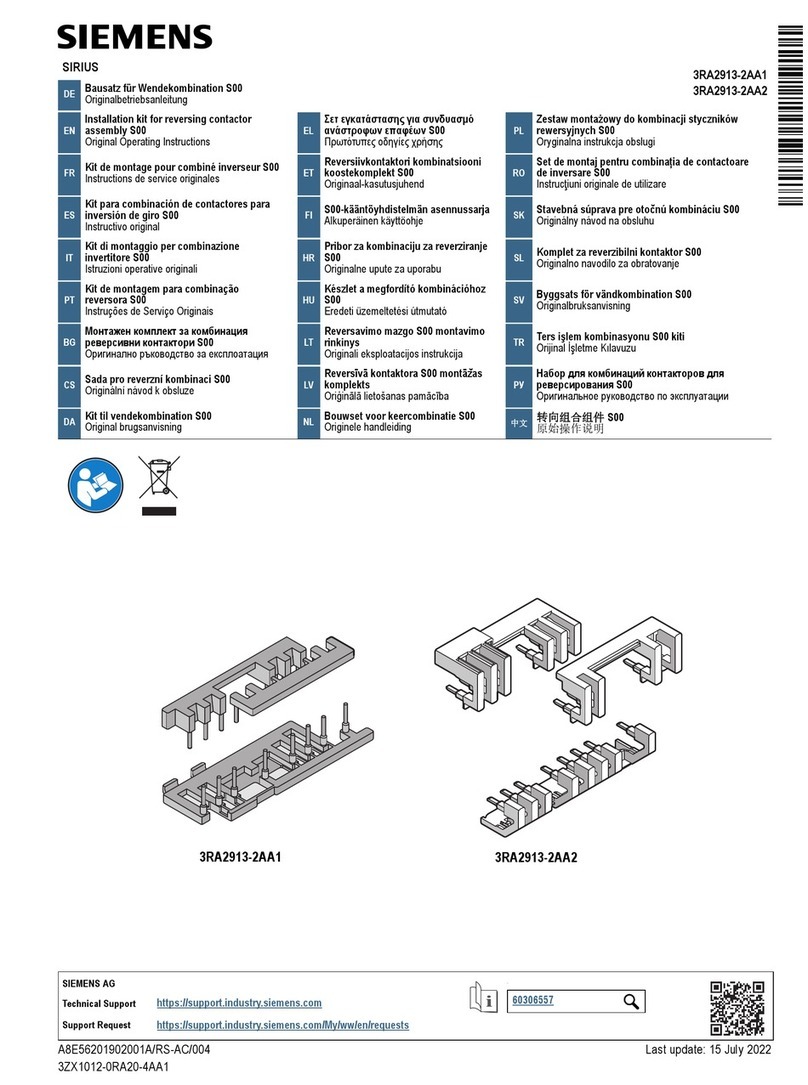
Siemens
Siemens SIRIUS S00 Original operating instructions

Murata
Murata LLA219R70J105MA01 Series Reference sheet
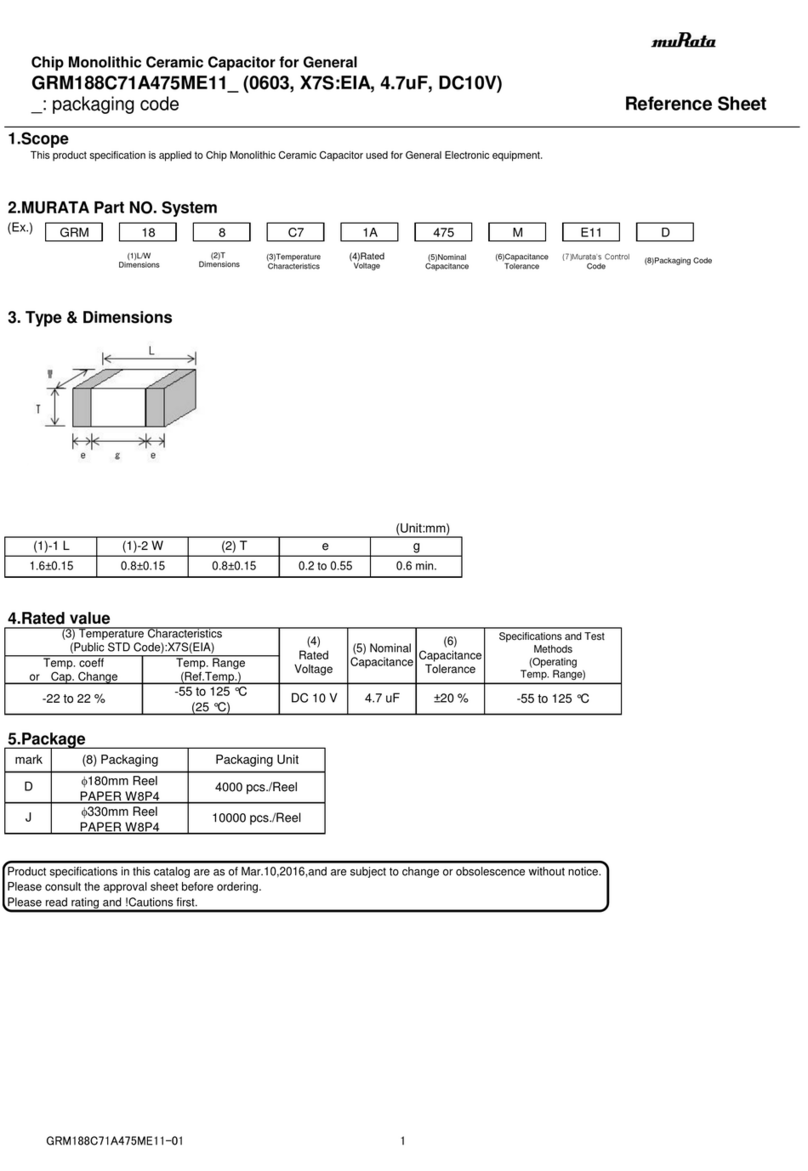
Murata
Murata GRM188C71A475ME11 Series Reference sheet

Daniamant
Daniamant ODEO Strobe Installation and maintenance instructions
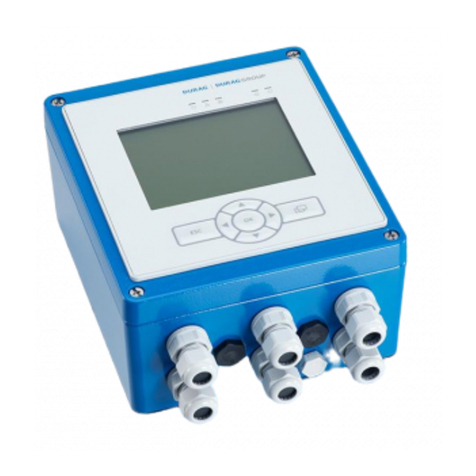
DURAG
DURAG D-TB 100 Series operating manual
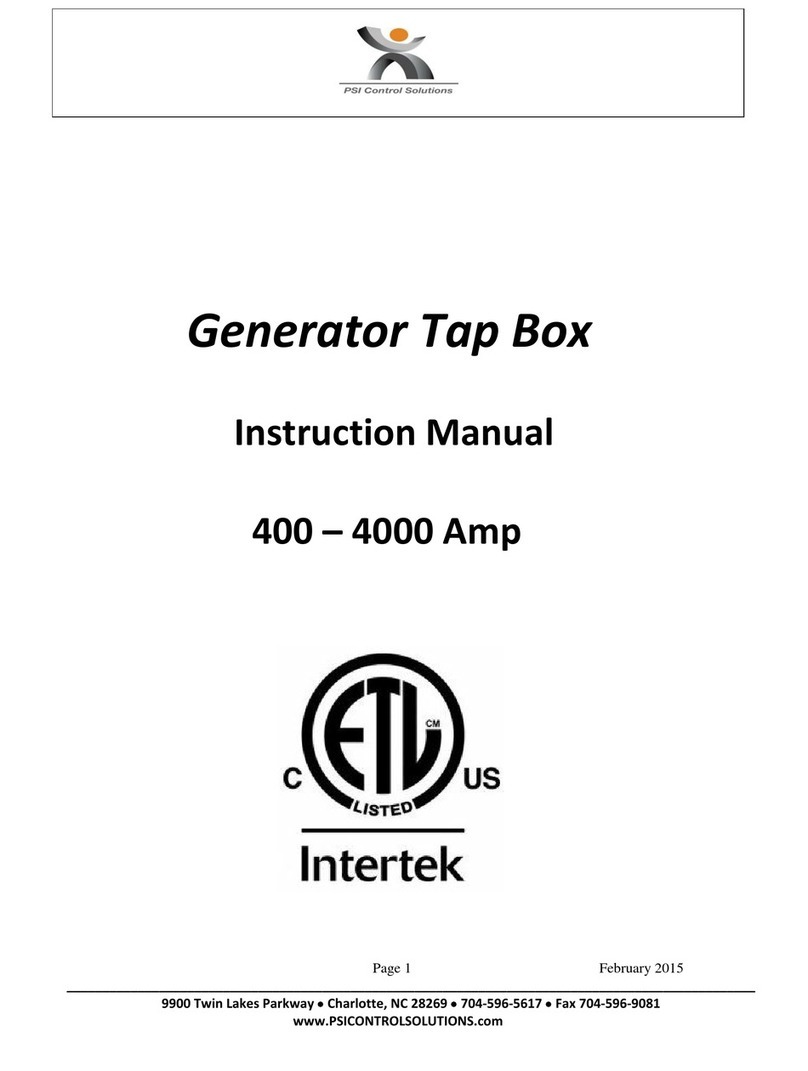
PSI
PSI Generator Tap Box instruction manual
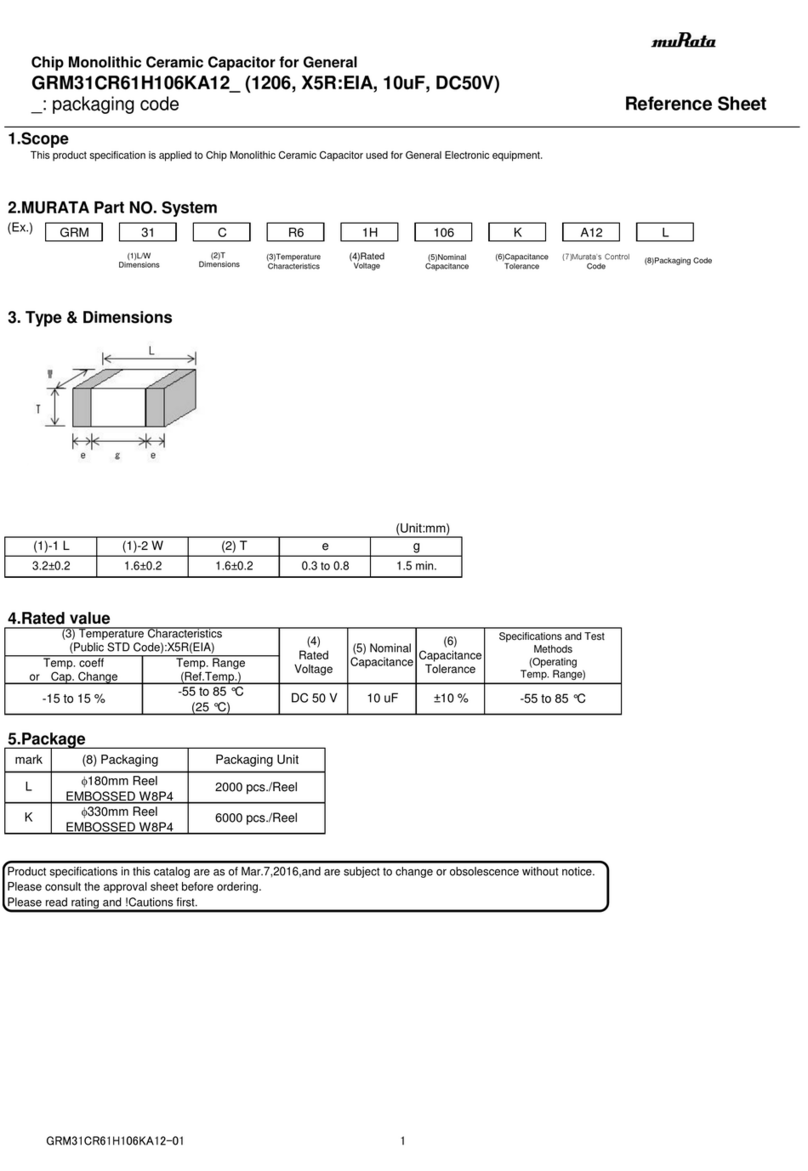
Murata
Murata GRM31CR61H106KA12 Series Reference sheet
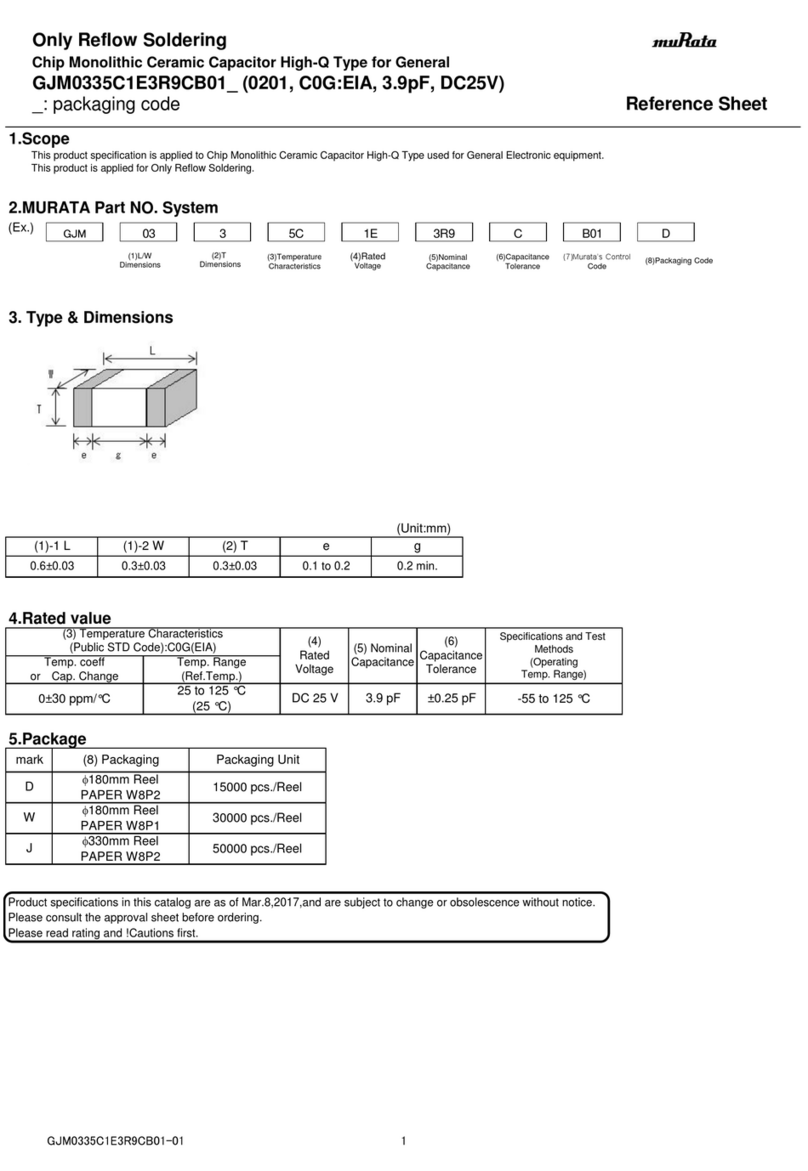
Murata
Murata GJM0335C1E3R9CB01 Series Reference sheet

Spectrum Industries
Spectrum Industries 55114 Assembly instructions
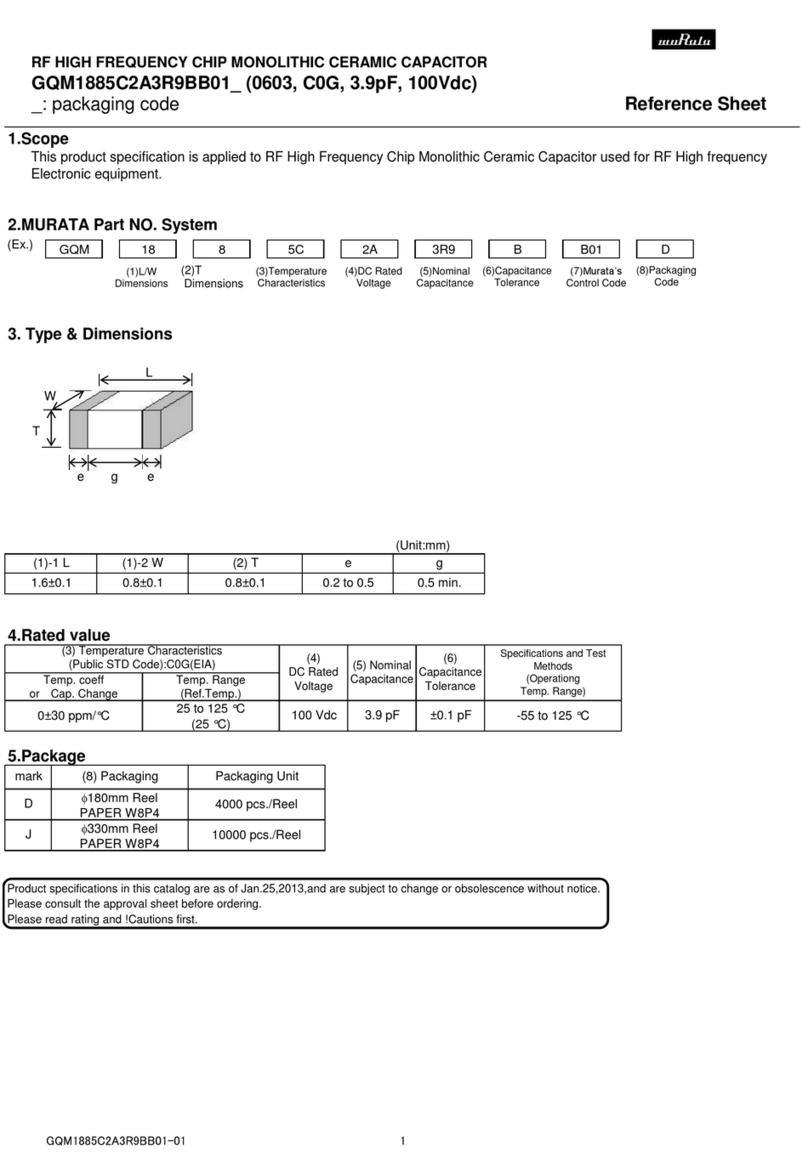
Murata
Murata GQM1885C2A3R9BB01 Series Reference sheet
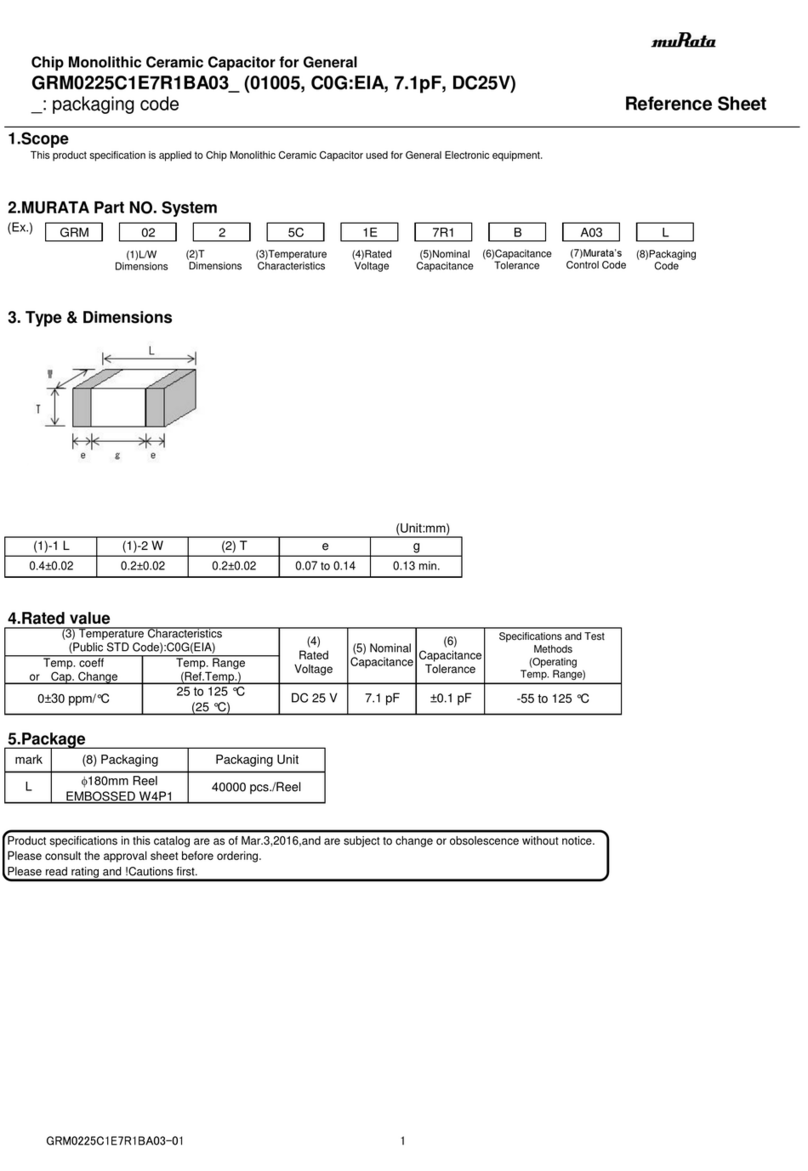
Murata
Murata GRM0225C1E7R1BA03 Series Reference sheet

hager
hager univers IP44 Mounting instructions