Major tech MT290 User manual

MT290
TEST ADAPTER FOR ELECTRIC
VEHICLE CHARGING STATIONS
INSTRUCTION MANUAL

2

Contents Page no
3
1. ............... ................................................................ Introduction ..... 4
2. Symbols..........................................................................................4
3. Safety Precautions.............................................................................5
3.1. Work Area Safety.......................................................................5
3.2. Electrical Safety.........................................................................5
3.3. Personal Safety.........................................................................5
4 Available Measurements and Product Description..................................6.
5 Before Use........................................................................................6.
5.1. Standard Equipment..................................................................6
5.2. Optional Accessories..................................................................6
.3. 5 Safety Measures........................................................................6
5.4. Appropriate Usage.....................................................................7
6 Description of Warning Marks..............................................................8.
7. Operation Elements and Connectors....................................................9
8. Testing Charging Stations.................................................................10
8.1. P u r p o s e o f t h e T e s t
A d a p t e r . . . . . . . . . . . . . . . . . . . . . . . . . . . . . . . . . . . . . . . . . . . . . . . . . . . . . . . 1 0
8.2. Connection of the Test Adapter to Charging Station......................11
8.3. Operation of Charging Station to be Tested................................13
8.3.1. PE Pre-Test ....................................................................13
8.3.2. Proximity Pilot (PP) State (Cable Simulation)......................14
8.3.3. Control Pilot (CP) State (Vehicle Simulation).......................14
8.3.4. CP Signal Output Terminals..............................................15
8.3.5. CP Error “E” Simulation...................................................15
8.3.6. PE Error (Earth Fault) Simulation......................................15
8 . 3 . 7 . P h a s e
Indicator...............................................................15
8.3.8. Mains Socket..................................................................15
8.3.9. Measuring Terminals L1, L2, L3, N and PE...........................16
9. Maintenance..................................................................................16
9.1. Cleaning................................................................................16
9.2. Transport and Storage..............................................................16
9.3. Fuse Replacement...................................................................16
10. Specifications.................................................................................17

4
1. INTRODUCTION
The MT290 is an extender for interfacing Electric Vehicle Supply Equipment
(EVSE) to test the socket of an installation tester for verification of electrical
safety and function of all single and three phase EV charge points. This easy-
to-use instrument, used in conjunction with the MT390 or similar meter
offers an electrical contractor a universal tool designed to thoroughly test
Mode 3 AC Electric Vehicle charging stations. The adaptor is designed to
simulate the connection of an electric vehicle to an under-test charging
point, with the safety feature of the PE Pre-Test, the PE conductor can be
tested for possible presence of dangerous voltage against earth. A rotary
switch for the Proximity Pilot (PP) state “Cable Simulation” can simulate
various current capabilities of charging cables, while the rotary switch for
Control Pilot (CP) state “Vehicle Simulation” can select and simulate various
charging states. Measurements on live conductors can be undertaken by
either using the front mounted mains socket or the 4mm measuring
terminals of L1, L2, L3, N and PE of the EVSE adaptor. Standard accessories
include the Type 2 and Type 1 plugs complete with a hard carrying case. The
housing of the MT290 IP54 for dust and splash proof water protection.
2. SYMBOLS
CAUTION Refer to the explanation in this manual.
WARNING Hazardous Voltage, Risk electric shock.
The equipment is protected by double insulation or reinforced
insulation.
Earthing (grounding) terminal.
Reference, please pay utmost attention.
Conformity symbol, confirms compliance with the applicable
European directives. The requirements of the Low Voltage
Directive with the relevant regulations Standards are also
fulfilled.
Symbol for marking of electrical and electronic equipment
(WEEE Directive).

5
V DC or VA C 1000V DC/AC RMS
mA AC/DC 800mA l000V fast acting fuse
A AC/DC 10A 1000V fast acting fuse (20A for
30 seconds max every 10 minutes)
Frequency, Resistance, capacitance, 1000V DC/AC RMS
Duty Cycle, Diode Test, Continuity
Temperature 1000V DC/AC RMS
Surge Protection: 8kV peak per IEC 61010
Maximum InputFunction
Note: Examples include protected electronic circuits.
Equipment of OVERVOLTAGE CATEGORY I is equipment for connection
to circuits in which measures are taken to limit the transient overvoltages to
an appropriate low level.
OVERVOLTAGE CATEGORY II
Note: Examples include household, office, and laboratory appliances.
Equipment of OVERVOLTAGE CATEGORY II is energy-consuming
equipment to be supplied from the fixed installation.
OVERVOLTAGE CATEGORY III
Note: Examples include switches in a fixed installation and some
equipment for industrial use with a permanent connection to the
fixed installation.
Equipment of OVERVOLTAGE CATEGORY III is equipment in
fixed installations.
OVERVOLTAGE CATEGORY IV
Note: Examples include electricity meters and primary over-
current protection equipment
Equipment of OVERVOLTAGE CATEGORY IV is for use at the origin
of the installation.
This meter has been designed for safe use, but must be operated with
caution. The rules listed below must be carefully followed for safe
operation.
NEVER apply voltage or current to the meter that exceeds the specified
maximum:
2.1. Safety Instructions
Input Protection Limits
• This instrument must only be used by suitably trained and competent
persons.
• Read this instruction manual before using the product in order to achieve
maximum performance.
• Keep this manual in a safe place after reading it for future reference
• The user manual contains information and references necessary for safe
operation and maintenance of the adapter.
• Please carefully read the safety information before using the test adapter.
• Failure to follow the warnings and instructions may result in electric shock,
fire, serious bodily injury, or equipment damage.
3.1. Work Area Safety
• Keep your work area clean and well lit.
• Do not operate equipment in explosive atmospheres such as in the
presence of flammable liquids, gases or dust.
• Keep children and bystanders away while operating equipment.
3.2. Electrical Safety
• Do not expose equipment to rain or wet conditions.
• Water entering equipment will increase the risk of electrical shock.
3.3. Personal Safety
• Stay alert, watch what you are doing and use common sense when
operating equipment.
• Do not use equipment while you are tired or under the influence of drugs,
alcohol or medication.
• A lack of attention while operating equipment may result in serious
personal injury.
3. SAFETY PRECAUTIONS
WARNING: Improper use of this meter can cause damage, shock,
injury or death. Read and understand this user manual before operating
the adapter. If the equipment is used in a manner not specified by the
Major Tech, the protection provided by the equipment may be impaired.
Use only accessories that are recommended by the Major Tech for your
equipment. Accessories that may be suitable for one piece of equipment
may become hazardous when used with other equipment.

6
• The adapter can test the electrical safety and function test of mode 3
electric vehicle charging equipment (EVSE) with type 2 connector (or
optional type 1 connector).
• PE Pre-Test (potential presence of dangerous voltage at PE. terminal by
mistake)-touch electrode and led lamp.
• Phase indicator (presence of all three phase voltages measured to N) -
three led lamps.
• PP state simulation (NC, 13A, 20A, 32A, 63A) - rotary switch.
• CP state simulation (A, B, C, D) - rotary switch.
• CP error T simulation (cp signal short-circuited to PEI-push button.
• PE error (earth fault stimulation (interruption of PE conductor) - push
button.
• Measurements on live conductors (L1, L2, L3 and n) and on PE conductor -
five 4 mm safety sockets for connection to installation testers.
• Test of cp signal-two 4mm safety sockets for connection to an oscilloscope.
• Mains socket (on backside) to connect an external load for test purposes
only.
5. BEFORE USE
5.1. Standard Equipment
The following equipment and accessories are included in the package, before
using the unit, make sure that all items are included.
• Main Unit x1
• Type 2 Test Cable x1
• Portable Package x1
• Instruction Manual x1
5.2. Optional Accessories
Type 1 Test Cable for EV charging station cable type 1 with fixed cable and
vehicle connector which fits to all versions of the test adapter.
5.3. Safety Measures
• The test adapter has been built and tested in compliance with the valid
safety regulations and left Major Tech’s warehouse in a safe and perfect
condition.
• In order to maintain this condition and to ensure safe instrument operation,
the user must pay attention to the references and warnings contained
within this user manual.
4. AVAILABLE MEASUREMENTS AND PRODUCT DESCRIPTION

• In order to avoid electrical shock, valid safety and national regulations
regarding excessive contact voltages must receive utmost attention when
working with voltages exceeding 120V DC or 50V RMS AC.
• The respective accident prevention regulations established by the national
health & safety board for electrical systems and equipment must be
strictly met at all times.
• Prior to any operation, ensure that the adapter and cable assemblies are
in perfect condition.
• The adapter may only be connected to charging stations as indicated in
the technical specification section.
• The adapter may only be used within the operating ranges as specified in
the technical specification section.
• The adapter may only be used in dry and clean environments. Dirt and
humidity reduce insulation resistance and may lead to electrical shocks,
particularly for high voltages.
• Never use the adapter in precipitation (e.g., dew or rain). In case of
condensation due to temperature spikes, the adapter may not be used.
• Perfect tests and measurements may only be ensured within the
temperature range of 0˚C to 40˚C.
• If the operator's safety is no longer guaranteed, remove the adapter from
service and protect against use.
• To ensure a safe measurement only use original cable assemblies.
• Safety can no longer be guaranteed if the adapter (or cable assemblies)
show obvious damage. Do not carry out the desired tests or
measurements.
• Have been stored for too long under unfavorable conditions.
• Have been subjected to mechanical stress during transport.
5.4. Appropriate Usage
• The adapter may only be used under conditions and for the purposes for
which it was designed.
• If the adapter is modified, operational safety is no longer ensured.
• The adapter may only be opened by an authorized service technician.
• Before opening the adapter it must be disconnected from any electrical
circuity.
WARNING
Button Operation Performed
HOLD Data Hold
Minus sign Negative reading display
0 to 3999 Measurement display digits
NCV Non-Contact Voltage
AUTO Auto Range mode
DC Direct Voltage
AC Alternating Current/Voltage
Low battery
mV or V Milli-volts or Volts (Voltage)
Ω Ohms (Resistance)
A Amperes (Current)
F Farad (Capacitance)
Hz/% Hertz (Frequency)/Percent(duty ratio)
°C Celsius units (Temperature)
n, m, μ, M, k Unit of measure prefixes: nano, milli, micro, mega, and
kilo
Continuity test
Diode test
4. ACCESSORIES SUPPLIED WITH METER
Ÿ Operating manual
Ÿ 1 x red and 1 x black test lead set
Ÿ Air temperature probe
Ÿ 2 x 1.5V AAA Batteries
Ÿ Carrying case
5. SPECIFICATIONS
3. DISPLAY ICONS
2.000A 1mA ±3.0% of rdg±5 digits
20.00A 10mA
200.0A 100mA ±2.0% of rdg±5 digits
600A 1A
Range Resolution
5.1. AC True RMS Current
Accuracy (% of reading + digits)
Over range protection: Maximum input 600A
Accuracy specified from 5% to 100% of the measuring range
Frequency Response: 50Hz to 60Hz True RMS
7
WARNING DANGER OF ELECTRICAL SHOCK.

8
6. DESCRIPTION OF WARNING MARKS
1. High danger of electric shock is present when PE Pre-Test indicator lights
while performing PE Pre-test, in this case, further testing must be stopped
immediately. Ensure a sufficiently connection of your body to earth while
performing this test.
2. Terminals with low voltage output (Approx. ±12V) powered by the
charging station, terminal marked with “ ” is connected to PE, use for
test purposes only, in the case of wrong wiring or error of the charging
station, these terminals may present a hazard.

WARNING: Risk of Electrocution. The probe tips may not be long
enough to contact the live parts inside some 240V outlets for appliances
because the contacts are recessed deep inside the outlets. As a result, the
reading may show 0V when the outlet actually has voltage present. Make
sure the probe tips are touching the metal contacts inside the outlet
before assuming that no voltage is present.
CAUTION: Do not measure AC
voltages if a motor on the circuit is being
switched ON or OFF. Large voltage
surges may occur that can damage the
meter.
9
7. OPERATION ELEMENTS AND CONNECTORS
1 - CP Error “E” Button
2 - PE Error (Earth Fault) Button
3 - PE Pre-Test Touch Probe
4 - PE Pre-Test Warning Indicator
5 - PP (Proximity Pilot) State Rotary Switch Selector
(NC, 13A, 20A, 32A and 63A)
6 - Mains socket, use for test purpose only, Max allowed current = 10A.
7 - Measuring Terminal PE
8 - Measuring Terminal L1, L2, L3
9 - Phase Indicators of L1, L2, L3 Terminals
10 - Measuring Terminal N
11 - CP (Control Pilot) State Rotary Switch Selector (A, B, C, D)
12 - Test cable for EV charging station Type 2 with socket outlet or fixed
cable with vehicle connector

10
13 - Test Cable Input
14 - CP Signal Output Terminal
15 - CP Signal Output Terminal (Connected to PE)
16 - Fuse 10A/250V, 5x20mm Protects Mains Socket Against Overload
8. TESTING CHARGING STATIONS
8.1. Purpose of the Test Adapter
There are two main purposes of the Test Adapter:
1. To simulate connection of an electrical vehicle to the tested charging
station (the test adapter simulates electrical vehicle and charging cable),
connection of the test adapter to a charging station triggers the charging
process in the charging station (CP switch at the adapter shall be in
appropriate model. various cable charging capabilities can be simulated
(NC, 13A, 20A, 32A and 63A) as well as all possible electrical vehicle
modes (A, B, C, D).

11
2. To provide easy access to charging terminals L1, L2, L3, N, PE and to CP
signal terminals to which additional measuring equipment can be
connected for further testing, charging stations should be tested after
installation and repeated periodically.
Please refer to the manufacturer's recommendation and national standards
which are linked to IEC/HO 60364-6 for initial test or IEC/HD 60364-7-722,
required tests are:
• Visual inspection
• Continuity of protective conductors and protective bonding
• Insulation resistances
• Loop/Line impedance
• RCD test
• Function tests (including but not limited to):
- Vehicle state A, B, C, D
- Error handing (error “E”', PE Error (Earth Fault)
- Communication (PWM signal)
- Mechanical locking of plug
- Rotary field/phase sequence
- Other tests
8.2. Connection of the Test Adapter to Charging Station
The Test Adapter can accept the following two connection cables:
• TYPE 2 test cable - for charging stations type 2 with panel mount, with
socket outlet or a fixed cable with vehicle connector (Included in scope of
supply).
• TYPE 1 test cable - for charging stations type 1 with fixed cable and
vehicle connector (Options).

Steps for connecting the test adapter to the charging station:
12
• Connect corresponding test cable to the test adapter.
• Connect above assembly to the charging station to be tested.
• Correct test adapter connection to the charging station is shown in Figure.

13
8.3. Operation of A Charging Station to be Tested
8.3.1. PE Pre-Test
• Do not touch the PE terminal on the front power socket until the PE pre-
test is successful.
• The PE Pre-Test is a safety feature of the test adapter, it allows the
operator to test the PE conductor for possible presence of dangerous
voltage against earth.
• In normal circumstances, the PE conductor is connected to earth and
therefore has no voltage against earth, however if the PE conductor is not
connected to earth (e.g. connected to phase by mistake or PE is
interrupted) the situation may be hazardous.
• Test procedure:
1 - First connect the adapter firmly to the charging station.
2 - Then touch the probe with a bare finger.
• If light indicator is illuminated, then dangerous voltage is present at PE
conductor. Stop further testing immediately and check for a possible wiring
fault of the tested PE conductor.
• In case of this error, PE terminal carries hazardous voltage, there is a
high risk of electric shock to the operator and other persons nearby!
• Possible errors are: PE interrupted/not connected/PE carries voltage
(e.g. connected to phase).
• Do not wear gloves while performing this test and ensure a proper
connection to earth.
• In case of improper connection to earth (e.g. isolated placement of your
body) this indication may be not reliable.

14
8.3.2. Proximity Pilot (PP) State (Cable Simulation)
• With the PP State rotary switch various current capabilities of the charging
cable can be simulated when the test adapter is connected to the charging
station.
• Current capabilities are simulated with different resistances connected
between PP and PE conductors.
• Correlation between resistance and current capability of the charging cable
is shown in Table below:
8.3.3. Control Pilot (CP) State (Vehicle Simulation)
• With the CP State rotary switch selector various vehicle states can be
simulated, when the test adapter is connected to the charging station.
• Vehicle states are simulated with different resistances connected between
CP and PE conductors.
• Correlation between resistance and vehicle is shown in Table below:
Marking of cable current capability Resistance between PP and PE
No cable Open (∞)
13A 1.5kΩ
20A 680Ω
32A 220Ω
63A 100Ω
Correlation between resistance and current capability of the
charging cable
Marking of Vehicle State Resistance Voltage at CP
Vehicle State between CP and PE terminal (1 kHz)
A Electric vehicle [EV] Open (∞) ±12V
not connected
B Electric vehicle [EV] 2.74kΩ +9V/-12V
connected, not ready
to charge
C Electric vehicle [EV] 882Ω +6V/-12V
connected, ventilation not
required, ready to charge
D Electric vehicle [EV] 246Ω +3V/-12V
connected, ventilation
required, ready to charge
Correlation between resistance, vehicle state and CP voltage Signal

15
8.3.4. CP Signal Output Terminals
• CP output terminals are connected to CP and PE conductors of the tested
charging station via the test cable, the green socket is connected to PE.
• This output is intended for connection of an oscilloscope to check the
waveform and amplitude of the CP signal.
• Control Pilot function uses Pulse Width Modulation (PWM)
• The purpose of the Control Pilot function is communication between a
vehicle and charging station, the duty cycle of the PWM signal defines the
possible available charging current.
• For details of communication protocol please refer to IEC/EN 62851-1 &
IEC/H0 60364-7-722 and the documentation of the manufacturer of the
charging station.
8.3.5. CP Error "E" Simulation
• With the CP Error T’ button CP Error can be simulated (acc. to standard
IEC/EN 6185-1).
• When CP error T’ is pushed, a short circuit between CP and PE through
internal diode is made.
• As a result, the pending charging process is aborted.
8.3.6. PE Error (Earth Fault) Simulation
• With the PE Error button an interruption of the PE conductor is simulated.
• As a result the pending charging process is aborted.
8.3.7. Phase Indicator
• The phase indicator consists of three LED lamps, one for each phase.
• When the test adapter is connected to the charging station and phase
voltages are present at the charging connector, the LED indicators will
illuminate.
Notes:
• In the case neutral (N) conductor is not present or it is interrupted,
LED indicators will not indicate possible voltage presence at L1, L2 and
L3 conductors.
• The LED indicators cannot be used for phase sequence testing.
• If the charging station has only a single-phase output, only one LED
will illuminate.
8.3.8. Mains Socket
• The mains socket is connected to L1, N and PE conductors of the
charging station via the test adapter when it is connected to the charging
station.
• This output is intended for measuring purposes only and offers the

16
possibility to check if the electric power meter works and counts in the
right manner (load test).
• Therefore, an external load can be connected for measuring purposes
only, it is not allowed to supply anything else.
• The max current is limited to 10A, the mains socket is protected against
overload with 10A/250V, 5x20mm fuse.
8.3.9. Measuring Terminals L1, L2, L3, N and PE
• Measuring terminals are directly connected to L1, L2, L3, N and PE
conductors of the tested charging station via the test cable.
• These terminals may be used for measuring purposes only, it is not
allowed to draw current over a longer period or supply anything else.
• An appropriate measurement instrument is needed.
• When using the test adapter in compliance with the user manual, no
special maintenance is required.
• However, should functional errors occur during normal operation, the after
sales service will repair your instrument.
• Please contact Major Tech to find out more.
9.1. Cleaning
• If the test adapter needs to be cleaned after daily usage, use a wet cloth
and a mild household detergent.
• Prior to cleaning, disconnect the test adapter from all measurement
circuits.
• Never use acid-based detergents or dissolvent liquids for cleaning.
• After cleaning, do not use the test adapter until it is dried completely.
9.2. Transport and Storage
• Please keep the original packaging for future transport (e.g. if calibration is
necessary), any transport damage due to faulty packaging will be excluded
from warranty claims.
• The adapter must be shored in a dry, closed areas.
• In case of an adapter being transported in extreme temperatures, a
minimum recovery time of 2 hours is required prior to any operation.
9.3. Fuse Replacement
• The fuse (1 DA (H)/250V, 5x20mm) may be blown if no voltage is present
between the L and N terminals of mains socket when the charging
connector is connected to the charging station and the charging station is
in charging mode.
9. MAINTENANCE

17
• If a fuse blows (due to overload or improper operation), follow the steps
below for replacement:
1. Unscrew the fuse holder cap using an appropriate screwdriver.
2. Remove the defective fuse and replace it with a new one.
3. Replace the fuse holder cap.
If the fuse blows several times the adapter must be sent to the service
department in order to be checked.
Use only fuses as defined in technical specification, using alternative
fuses may create a safety risk!
Functions
PE Pre-Test Yes
PP Simulation NC / 13A / 20A / 32A / 63A
CP States A (Electric vehicle not connected)
B (Electric vehicle connected, not ready to
charge)
C (Electric vehicle connected, ventilation not
required, ready to charge)
D (Electric vehicle connected, ventilation
required, ready to charge)
CP Error “E” On/Off
PE Error (Earth Fault) On/Off
Outputs
(for test purpose only)
Measuring Terminals Max. 250/430V, CAT II 300V, max. 10A
L1, L2, L3, N and PE
Mains Socket Max. 250V, CAT II 300V. Allowed current max.
10A. Note: Do not load mains socket
simultaneously with measuring terminals!
Mains Socket Protection Fuse 10A / 250V, 5x20mm, Magnetic tube
produced by Xunlibang.
CP Signal Output Approx, ±12V, CAT0 (Under normal condition).
Terminals In case of wrong wiring or error of the charging
station these terminals may become hazard
=>up to max. CAT II 300V against PE.
10. SPECIFICATIONS

18
General Features
Input Voltage Up to 250V (Single phase system)/up to 430V
(Three phase system). 50/60Hz, max 10A.
Type 2 Test Cable AC charging mode 3, suitable to IEC62196-2 type
2 socket outlet or fixed cable with vehicle
connector (Type 2, 7P three-phase).
Type 1 Test Cable AC charging mode 3, suitable to IEC62196-2 type
1 or SAE J1772 with vehicle connector (Type 1.5P
single-phase).
Weight Approx. 1kg
Dimensions (LxWxH) Adapter size: 227x109x63mm (Length without
connection test cable)
Handle size: 250x115x61mm (Length without
connection cable)
Safety IEC/EN 62851-1/IEC/HD 60364-7-722
Measurement Category 300V CAT II
IP-Rating IP54
Pollution Degree 2
Protection Class II
Working Temperature 0°C to 40°C
Range
Storage Temperature -10°C to 50°C
Range
Reference Humidity 10% to 60% relative humidity w/o condensation
Range
Working Humidity 10% to 85% relative humidity w/o condensation
Range
Altitude Above Sea Max. 2000m

19

www.major-tech.com www.majortech.com.au
MAJOR TECH (PTY) LTD
South Africa Australia
Table of contents
Popular Adapter manuals by other brands
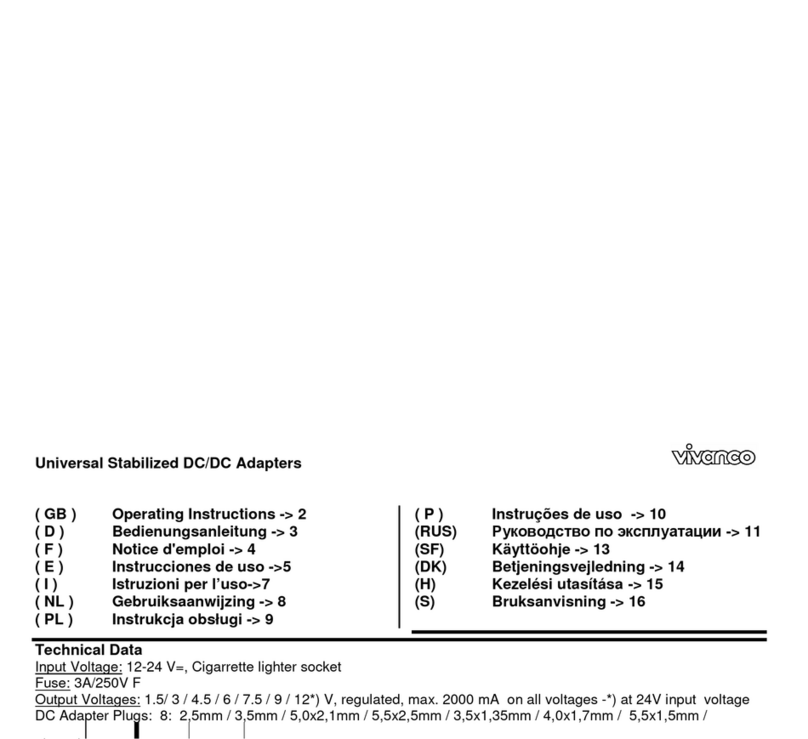
Vivanco
Vivanco UNIVERSAL STABILIZED HIGH-POWER DC ADAPTER operating instructions

Conrad
Conrad 87 23 00 operating instructions
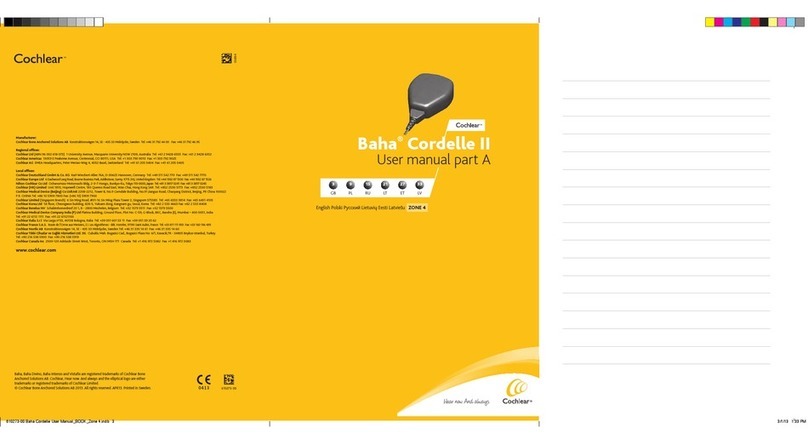
Cochlear
Cochlear baha cordelle ii user manual
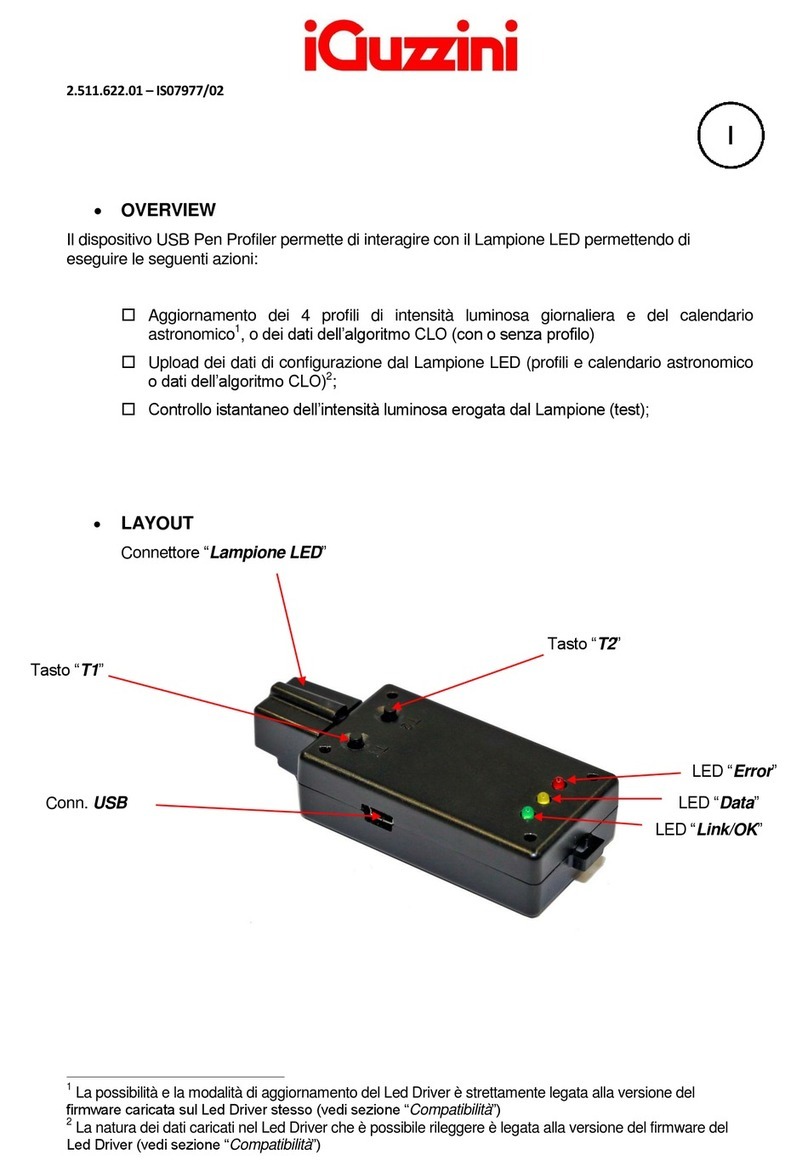
iGuzzini
iGuzzini USB Pen Profiler manual
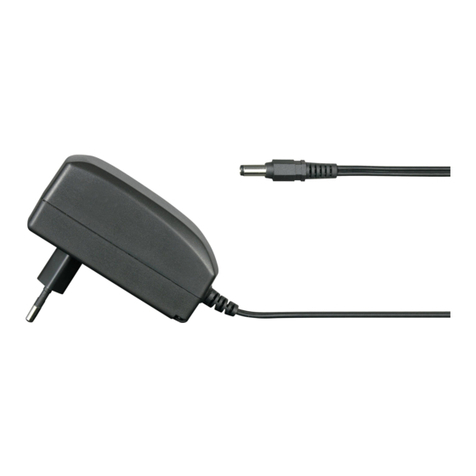
VOLTCRAFT
VOLTCRAFT FPPS 12-27 W operating instructions

Edimax
Edimax EW-7833UAC Quick installation guide