Martello Blastrac BMS 220ADB User manual

1 | P a g e
User Guide
Blastrac BMS 220ADB
Martello Hire & Logistics Limited
Unit 12 Riverside Industrial Estate
West Hythe Road
Hythe
Kent
CT21 4NB
Tel: 01303 901399

2 | P a g e
User Guide Blastrac BMS 220ADB
It is important that all persons who are working or maintaining this machine read the manual carefully and understand it fully.
Keep this manual near to the machine, so it can always be consulted.
Only authorised and trained personnel may operate this machine.
Machine Description
The Blastrac BMS 220ADB machine is ideally suited for medium and large sized applications with the added benefit of being battery
operated with built in charger. It is very manoeuvrable with a zero-turn radius, non-mark tyres and complete hydraulic control.
General Safety
•It is the responsibility of the user to risk assess the properties of the floor to be removed.
•Do not use on surfaces that may create dust or atmospheres that pose a fire or explosion risk, or flammable liquids, gases,
or dusts.
•Do not use on surfaces that may pose a risk of carcinogenic or pathogenic materials.
•Do not use machine in wet or damp environments.
•Ensure the area to be scraped is clear from clutter and has adequate ambient lighting.
•Keep all others at least 5m away from machine operating areas, use suitable barriers and signage where necessary.
•Avoid distraction from others during operation.
•Remove all trip hazards.
•Remove any metal objects such as bolts or reinforcing steel protruding from the floor surface.
•Always wear the seatbelt when operating a machine.

3 | P a g e
Electrical Safety
•Use only extension cables supplied with the machine or are, suitably rated for its overall power consumption of 110v 32
amp minimum.
•Extension cables must be fully unwound.
•Do not use damaged cables.
•The voltage on the identification plate must match the supply.
•Use a power supply with earth connection and earth leakage circuit breaker.
•Do not make any changes to the machines electrical system.
•Always call Martello Hire with any questions about the safety of the electrical components.
•Do not use cables to move machine, keep cable away from heat, oil, sharp edges and moving parts.
•Keep cables away from water.
•Ensure main switch is in position ‘0’ before connecting power supply.
•Do not leave plugged in for long periods.
Personal Safety
Always wear Personal Protective Equipment (PPE), whilst working around or when operating the machine.
•FFP2 mask or higher
•EN166 Goggles or glasses with lateral protection are obliged
•Hearing protection is obliged
•EN388 Cut level 3 resistant and vibration dampening gloves
•Safety shoes obliged
•CE –mark on this machine
•Consult the manual before operating the machine
Personnel must tie back long hair/not wear loose clothing or jewellery including rings when operating the machine.
•Stay alert for obstructions or other hazards.
•Seek medical attention for any injuries.
•All persons near the machine need the same PPE.
Machine Safety General
•All safety functions must be checked for correct operation prior to use.
•Ensure all nuts, bolts and other fixings / fasteners are tight.
•Do not operate without all guards and safety devices in place.
•Do not make any changes or adjustments to the machine.
•Machine, and especially hand controls to be free of dirt and grease etc.
•Remove cables by the connector not the cable.
•Do not attempt to repair the machine yourselves. Please contact Martello Hire.

4 | P a g e
•Blastrac supplied parts to be used only.
•Do not use in a manner other than described.
•In the event of malfunction or safety issue shut machine down immediately and contact Martello Hire.
Transport Safety
•Operate on level surfaces, do not operate on steep inclines or side traverses.
•Where possible use lifting aids and the lifting points on the machine to transport. Use existing lifting points on the
machine of the brackets for a forklift underneath.
•Never lift or transport the machine with an exposed blade.
•Chock wheels for transport and keep control handle in neutral.
•Park on a level and horizontally flat surface.
•Clean and dry after use, and store in a humidity free location, protect the motor from moisture, heat dust and shocks.
•Do not use for lifting or transporting people or other items.
•Before lifting, check lifting points and welds for damage, cracks, deformity, corrosion, or wear. Each lug has a WLL of
1500kg, Machine is 1080kg.
•Ensure machine is securely restrained during transport (lifting points can be used for this), and chock wheels.
•If unloading on a ramp or incline, do not do so with wheels disengaged.
•Always drive backwards up an incline, and forwards down.
•Turn the key to off position and press emergency stop down when parked.
•Cover blade or remove blade when parked.
Signs on the Machine
The following stickers are placed on the machine. Meanings of these symbols are:

5 | P a g e
Initial Operation Checks
•Check power supply cable is unplugged, and cable stored in the machine.
•Ensure cables are not damaged.
•Control levers should be in neutral position.
•Hydraulic hose connections are tight and no evidence of leaks.
•Safety functions work correctly.
•No loose bolts, nuts or other fixings.
Seat Adjustment
•Adjust seat to sit up straight.
•Sit well back in seat.
•Ensure seatbelt is suitably adjusted.
Operation
During operating the BMS 220ADB, the following additional safety instructions must be followed closely. Before switching on the
machine make sure that no-one can be endangered when the machine starts up.
1 Control Switch
2 Battery power meter and hour-counter
3 Red mushroom-shaped emergency shutdown push button
4 Seat including presence switch and seatbelt
Switching the Machine On
•Take place on the seat (4) and put your feet on the footrests. Fasten the seatbelt.
•Operating the machine when you are not sitting in the operator seat is not possible because of the safety switch inside
the seat.
•Pull out the emergency switch (3).
•Turn the key contact switch (1) to the right.
•Check battery power on discharge meter.
Driving the Machine
Driving of the machine is controlled by the two outside handles (1 and 3).
•Pushing both handles forwards, the machine drives forwards.
•Pulling both handles backwards, the machine drives backwards.
The driving speed depends on the position of the handles.
•Pushing the right handle forwards the machine turns to the left.
•Pushing the left handle forwards the machine turns to the right.

6 | P a g e
Pushing one handle forwards and pulling another handle backwards the machine will turn around on its axis. Correcting direction
while moving is accomplished by slightly reducing pressure on one handle or the other while moving.
1. Left wheel control handle. Forward/Reverse Neutral=Brake
2. Right wheel control handle. Forward/Reverse Neutral = Brake
Controlling the Tool Angle Cylinder
•Controlled by inner left handle.
•Push forward to angle tool downwards.
•Pull back to angle up.
•Pushing handle will lift front of machine.
•(3) Left inner handle.
•(4) Hydraulic cylinder.
•(5) Debris deflector.
•(6) Blade holder.
Controlling Tool Pitch Cylinder
•Allows adjustment of blade pitch whilst in the seat.
•To adjust move inner right handle forwards or backwards.
•(7) Right hand inner cylinder.
•(8) Hydraulic cylinder.
•(9) Inner plate.
Charger Operation
The BMS 220 is equipped with an on-board battery charger. It is mounted on the back of the machine to have easy access.
Machines are built with a 60A charger E14536 from serial number 31509B and up. Turn the contact switch to ‘off’for charging.
Batteries will not charge when contact switch is in ‘on’position. Put the charger plug into a grounded outlet. Never alter the A/C
cord or plug provided.

7 | P a g e
The charger starts and stops automatically when the contact switch is off, and the plug is in. You can charge the batteries all night
long, when the batteries are full the charger stops automatically.
Warning! Always disconnect on board charger before operating the machine.
Sound and Vibration Data
Sound Level: 77 dB (A) relative to 20uPa.
Ear protection is recommended with the use of this equipment.
Vibration Level:
Declared hand-arm vibration emission in accordance with EN 12096.
The total vibration value to which the hand-arm system is subjected, does not exceed 2,5 m/s².
Vibration test code EN-ISO 20643.
The total vibration value to which the whole body is subjected, does not exceed 0,5 m/s².
Uncertainty K=0,1 m/s²
Surface: Smooth concrete
Declaration in conformance with EN 12096: 1997
Measurement in conformance with EN-ISO 2631-1 and EN 1032 as far as applicable.
Cutting Head and Blades
Weight vs Sharpness
The most common way to compensate for a dull blade is to add more weight and raise the blade angle (see re-scrape setting).
Weight allows dull blades to be used to a point. Weight also causes blades to dull and break easier. Blades of any thickness tend
to catch cracks and expansion joints and will bend or break the blade if set at a high angle. For best results, run a small ditching
blade at a low angle to identify as many cracks and joints as possible. If blades are breaking, you are misunderstanding the
conditions.
Cutting Head Pitch
Set the cutting head angle to where the material comes up the easiest. The lowest is usually the best.
Steep Cutting Head Pitch
The cutting head pitch can be adjusted by simply placing the cutting head axle in 1 of the 4 holes or use the right-hand inner handle
(for dual-lift machines from S.nr.30340 & up). A steep angle is only used for re-scraping. The cutting head has to be raised to the
highest hole. Not raising the cutting head when operating the machine at a steep angle will cause the machine to jump and buck.
It does not give the operator a clear vision of the cutting head and it raises the machine to operate at an unsafe operating height.
Failure to raise the cutting head could cause machine damage and/or bodily injury.
Swivelling Tool Holder
The swivelling tool holder keeps the blade in contact with the floor even when the floor is uneven. When using a flat blade, by
swivelling the head over 180° allows you to use the other sharp edge on the blade without having to replace the blade.
Saving Time with Extra Blades, Blade Holders and Tool Holders

8 | P a g e
The machine is supplied with one tool holder. Having additional tool holders, blade holders and blades will save time on the job.
When the blade is dull, instead of taking the time to replace it or sharpen it on the job, replace it with another prepared set. Or,
when a different type or size of blade is needed, you have them ready to use.
1 Blade –depending on the needs
2 Blade holder –lower part
3 Blade holder –upper part
4 Tool holder
5 Debris deflector –new holder shape
6 Universal lower cutting head support
Blade Choice
Proper blade size and placement, depending on material and sub-floor
type, affects performance.
•Use sharp blades. Dull blades reduce cutting ability.
•The harder the floor to come up, the smaller the
blade needed for best results.
•Start with a narrow blade, then increase the blade
size to find optimum result.
•Narrower blades usually leave a cleaner surface.
•Set blade bevel correctly.

9 | P a g e
Blades Application
Efficient and fast work can be achieved when you use the correct blades and settings. The operator must remember to prepare
the correct angle and keep the blade sharp. During work the blade will become dull. To reduce this process the operator can add
extra weights to the front or change the angle between the blade and the ground. CAUTION! That action makes blades more
potential to break. Important is to understand that when the blades are breaking, some of the conditions of usage or settings are
not correct. In many cases the angle between tool and ground can’t be too big because the machine can jump and even takeover
to the back.
The work area should be kept clean. When a portion of material is removed on the first run, it is always better to clean the floor
before starting the second run. Debris and dirt can make the blade dull really quick.
Blade Changing
•Use an extended wrench to keep hands away from sharp edges
•Wear cut resistant gloves
•Ensure plug is removed from power supply
•Place a block under the front of the machine
•Loosen the 5 bolts
•Remove existing blade if there is one
•Replace with a sharp blade
•Ensure new blade is far enough into blade holder to be secure
•Retighten bolts
•Only replace blades when machine is stable.

10 | P a g e
Always wear cut-resistant gloves when handling blades.
Using Wing Blades
Use only sharp winged blades.
Types of Blades
For different materials special tools need to be mounted. The shape and width are defined by many years of experience. Below
are a few types described:
Self-Scoring Blades. Used for vinyl, carpet tiles, soft to medium PVC, soft cork, linoleum, enhancer and universal bound
hot melts. With this type of blades scoring is make automatically by the “wings”.
Premium Blades. Designed to work on wood, thin ceramic, tiles, VCT, VAT, re-scraping thin set, glued ceramic,
elastomeric coating, rubber epoxy. After some work period the blades need to be sharpened.
Heavy Duty Blades. Designed for wood, VCT, VAT, thin ceramic, re-scraping, all carpets, elastomeric coatings, cork, rubber
and urethane coatings. They are thicker than premium blades.
Premium Chisels. For use on ceramic, thin set, wood, decorative concrete and mud set.
Heavy Duty Chisel (carbide tips). For use on wood, ceramic, elastomeric coatings and epoxy. These blades have carbide
tips to give them a long lifetime.
Using the correct blades is only half of the success. The second most important thing is to put the tool in the optimal geometry
to the ground. Below you will find information about the most popular materials.
VCT –Tile. Cutting head in the lowest hole. It’s better to start with a narrow cutting head. The best option should be
Heavy Duty Blade.
Foam Back Carpet Set-Up. Cutting head in the lowest hole. It is possible to use a blade from 250 to 350mm but in some
situations a good choice can be using a blade from 350 to 700mm.
Ceramic Set-Up. Cutting head in the lowest hole. Usually Premium or Heavy-Duty chisels will be the best for this job.
Secondary Backing Carpet Set-Up. Cutting head in the lowest hole. Proposed settings are a blade-width from 255 to
685mm with Heavy Duty Blades and Self Scoring Blades.
Double Stick Carpet Set-Up. Cutting head in the lowest hole. In this case it is good to start with a blade-width (255 to
355mm) with Self-Scoring Blades. It is important to have sharp blades.
Wood Set-Up. Cutting head in the lowest hole. Preferred are Premium or Heavy-Duty chisels or a blade width (150 to
205mm) with Heavy Duty Blades. The machine needs to have an angle of 45° to the grain of the wood.
Thin Coating Set-Up. Cutting head in the highest hole for the floor or in the lowest hole for wood. The correct distance
needs to be set after tests. Preferred application is a width (200 to 685mm) with Premium Blades.
Re-Scraping Set-Up. Cutting head in the highest hole. A blade width (200 to 685mm) with Premium Blades can be used.
Good to remember that the blade should be one step bigger than the blade holder.
Working Over Concrete. The most important thing is to install the blade bevel up because this kind of material is hard to
remove. The best way is to test different settings with Heavy Duty Blades.
Working over Soft Sub-Floor. Cutting head in the lowest hole. Preferred are a Heavy Duty Blade or a Premium Blade.
Blades need to be installed with bevel up and the position needs to be as flat as possible.
Working Over Wood. In this case it is important to know if the floor is strong enough to put the machine on it. Otherwise,
it is better to take out the weights. Cutting head in the lowest hole. Preferred are Heavy Duty Blades or Premium Blades.

11 | P a g e
Ditching
Cross Room Ditching:
•When removing hard to remove ceramic or VCT
•Cross room ditch with a 50 to 155mm blade
•Ditches 300mm to 600mm apart
•In the same direction as floor removal
•This relieves pressure of tiles holding each other
•If ditching helps, increase blade width if possible
Checker-Board Ditching:
•To make carpet removal and clean up easier
•Use a wide self-scoring blade across the floor
•Remove remaining flooring in the opposite direction,
this will create smaller pieces of debris that are
easier to dispose of.
•Fold debris with sticky side inside
For a fully copy of the User Manual please visit www.martellohire.co.uk
Popular Power Tools manuals by other brands

AEG
AEG BSS 12 C instructions
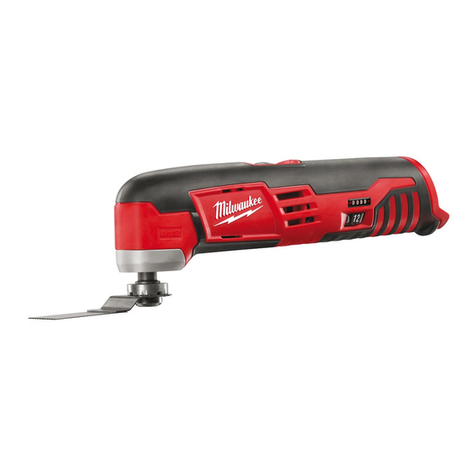
Milwaukee
Milwaukee C12 MT-0 Original instructions
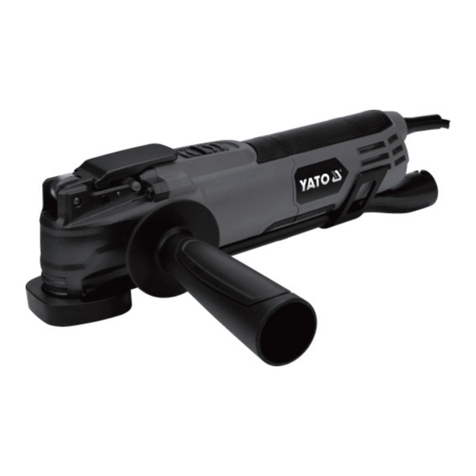
YATO
YATO YT-82223 Original instructions

Malcotools
Malcotools FasGroov FGVK Instruction
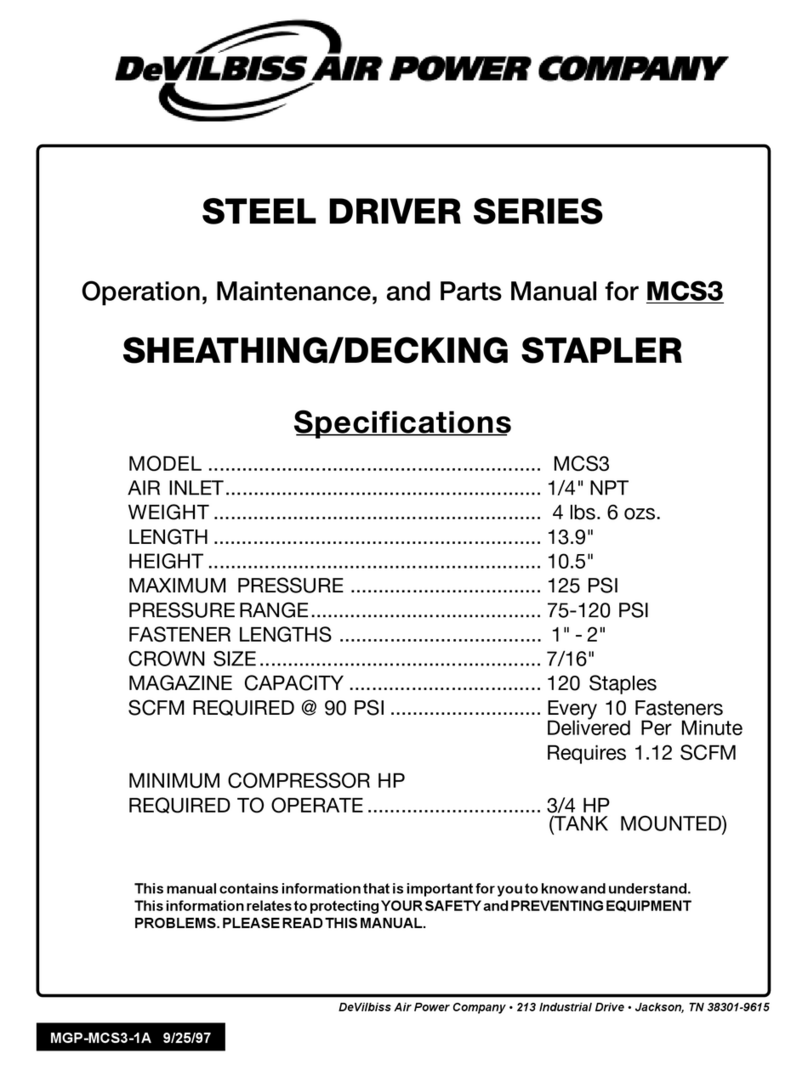
DeVillbiss Air Power Company
DeVillbiss Air Power Company Steel Driver Series Operation, maintenance and parts manual
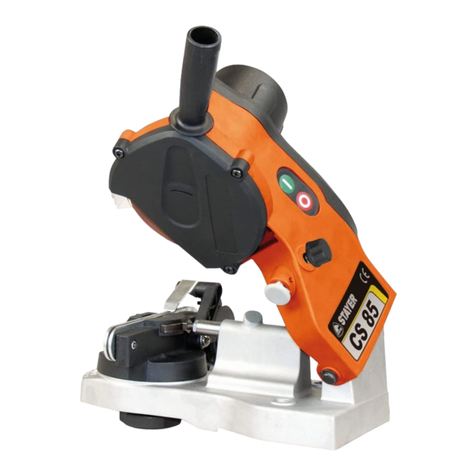
stayer
stayer CS85 operating instructions