Matko XTP Series User guide

Matko XTP Wireless Setup Manual Rev 1.1
XTP Radio Modules:
Transmitter/Receiver Sets
or
Bidirectional


Section 1
Section 2
Section 3
Section 4
Section 5
Section 6
Section 7
Section 8
Wiring Diagrams 4
Specications 5
Conguration 6-8
Example Installations 9-12
Troubleshooting/Before You Call 13-14
Product Comparison/Compatibility 15
Part Numbers/Replacement Parts 16
Manual Revision 16
RF Exposure
WARNING: To satisfy FCC RF exposure requirements for mobile transmitting devices, a
separation distance of 20 cm or more should be maintained between the antenna of this
device and persons during device operation. To ensure compliance, operations at closer
than this distance is not recommended. The antenna used for this transmitter must not be
co-located in conjunction with any other antenna or transmitter. The preceding statement
must be included as a CAUTION statement in OEM product manuals in order to alert users
of FCC RF Exposure compliance.
3

Figure 1.1: Wiring Diagram
For a typical scale applications, Connect one XTP Module as the
transmitter (using BLACK Terminal Block) to the indicator and wire the
second unit as the receiver (using the GREEN Terminal Block) to the
Remote Display
6
7
+20mA
–20mA
Indicators with
Active 20 mA
Output
5
4
RX CL (+)
RX CL (–)
TX 422A (+)
TX 422B (–)
RX 422A
RX 422B
Indicators with
RS422 Output
3
2
TXD
GROUND
Indicators with
RS232 Output
232 RXD
GROUND
Indicator XTPPin Connector Pin Out
1 +9 VDC
2 GROUND
3 232 RXD
4 RX CL(-)
5 RX CL(+)
6 RX 422A
7 RX 422B
1
2
4
5
+20mA
–20mA
+9 VDC
GROUND
RX CL(–)
RX CL(+)
Indicators with
Passive 20 mA
Output
JUMP
The corresponding green LED will blink with every data transmission regardless of any wireless network
being present or conguration settings. *
XTP as Transmitter (Indicator side)
(Black Terminal Block)
XTP as Receiver (Remote Display side)
(Green Terminal Block)
All 3 loops (RS232, RS422, and Current Loop) transmit with every data wireless signal received. *
*DATA RELIABILITY in the following order:
RS422/485 (Up to 4000 feet)
Current Loop (Up to 2000 feet)
RS232 (Up to 50 feet)
4
Section 1: Wiring Diagram
Section 1:
Wiring Diagram

Physical Dimensions
Power
The XTP Module can run on any voltage source 7.5 VDC to 12 VDC with dedicated 250 mA.
Power may be run o of Matko SBL and SSD Displays
Range
The XTP Module was designed under optimal conditions to run up to 2 miles outdoor Line of Sight.
Environments vary and actual range will be less
Figure 2.1: Dimension Chart
XTP
XTP-R4
XTP-R8
W H1 H2 D1Model
8.5” 12” 1.75” 7.85”6.5”5.75”
D2
XTP-R2 8.5” 13.5” 2.25” 7.85”6.5”7.25”
13.5” 13.5” 2.25” 12.85”6.5”7.25”
13.5” 15.5” 2.25” 12.85”6.5”9.25”
M
(Mounting)
5
Section 2: Specications
Section 2:
Specications

6
Section 3: Conguration
Section 3:
Conguration
Conguration
All units must be on the same ID to communicate with each other. There are 16 IDs available ( IDs 0 through 15)
For each Radio in the system:
1. Set the BLACK ID DIP switch to the desired ID
2. Set the BLUE BAUD RATE DIP switch to match the serial device connected to the XTP unit.
*Any change in DIP Switch settings will cause the RED CONFIG LED to turn on. Transmission will be disabled until
step 3 is performed. The BLACK DIP for TEST MODE must be o for normal operation.
3. Press the CONFIG button. The three GREEN conguration LEDs will illuminate as setup progresses.
When all three LEDs light up Conguration is complete. **
If there is a problem with conguration the RED CONFIG LED will blink every 5 seconds up to 6 times. RED CONFIG LED will then
blink several times rapidly. Wait a minimum of 5 seconds before pressing the CONFIG button again.
** It may take up to 30 seconds after conguration before a link is established with other units and data is transmitted between
units.
When the XTP has been properly congured and properly wired according to Section 1 the corresponding GREEN LED (RS232,
CLOOP, or RS422) will blink with each data transmission. The RED Receiving Wireless Signal LED will blink with each data burst
received from the matching transmitter. Ideally with each GREEN blink on the transmit side there will be a corresponding RED blink
on the receiver side. If the receiver side is infrequent the signal is not reliably getting from one unit to the other. Reposition
antennas for direct line of sight as much as is feasible.
Optional IO (Input Output) Cards
The XTP Module has the option to add up to 2 cards used for IO line passing for other XTP units on the same ID. Each card has
either 4 input or 4 outputs. Each system can only have one WHITE input card on IO Card Slot 1 and 1 WHITE input card on IO Card
Slot 2 (See Figure 3.1). These units may be in the same XTP unit or dierent units. Any system can have as many BLACK Output
cards as required on any IO Card Slot without interference
Changing IO cards may require repeating step 3 above as indicated if the RED CONFIG LED turns on..
IO Card Slot 1 controls IO 1 through 4 and IO Card Slot2 controls IO 5-8 (Cards can be used ineither slot.
Only IOs 0-7 are sent using IDs 0-5 and 12-15 (to maintain backwards compatibility with older XT Series models.
If 8 IOs are required use IDs 6-11
The XTP Built in Receiver has IO 1-3 tied into the stoplight controls on SSD series displays.
In 1 controls the red line
In 2 controls the green line
In 3 controls the amber line

Optional IO (Input Output) Cards (Continued)
Connect a switch between GROUND and the desired input line on the BLACK Input Card. When the switch is closed the GREEN
Input LED will light. When the loop is open the light will be o. On the corresponding WHITE Output Card the RED Output LED
will match the state of the GREEN Input LED
Optional Output Relays
The XTP modules may be connected to 5 volt relays. The XTP-R2, XTP-R4 and XTP-R8 have larger versions of the case with built in
relays. Any Output line may be connected to a relay. On the WHITE Output Card connect the +5 VDC line to one side of the relay
coil and the desired output line to the other side of the relay coil.
The provided relays have connections for both NO (Normally Open) and NC (Normally Closed) circuits. This allows easy logic
inversion if needed. The COM (Common) Line is used as the voltage input.
Relays Ratings
30/20 Amps (NO/NC) at 277 VAC
20/10 Amps (NO/NC) at 28 VDC
2/0.5 HP (NO/NC) at 250 VAC
1/0.25 HP (NO/NC) at 125 VAC
Maximum Switching Voltage: 277 VAC, 110 VDC
7
Section 3: Conguration
Section 3:
Conguration Continued

IO 1-4
GROUND
+9 VDC
TX 422B
TX 422A
TX CL(+)
TX CL(-)
RX 422B
RX 422A
+9 VDC
GROUND
232 RXD
232 TXD
RX CL(-)
RX CL(+)
XTP Transceiver R2
+9 VDC
GROUND
S1
IO Card 2
1200
2400
4800
9600
BAUD
19200
RESET
IO 5-8
IO Card 1
Test Mode
ID +8
ID +4
ID +2
ID +1
ID
PWR Signal
Wireless
Receiving
Cong Step
Cong
CONFIG
Figure 3.1: XTP Module (set to 1200 Baud ID1)
Figure 3.2: XTP Built in Receiver
Signal
Wireless
Receiving
Cong Step
XTP Receiver
Test Mode
ID +8
ID +4
ID +2
ID +1
1200
2400
4800
9600
BAUD
ID
Cong
PWR
CONFIG
RESET
19200
Figure 3.4: XTP Input Card
Figure 3.3: XTP Output Card
Board Layout
Input Card R2
In 1/5
In 2/6
In 3/7
GROUND
In 4/8
GROUND
Closed
Loop
ON
OFF
Open
Loop
GROUND
Out 4/8
+5 VDC
Out 3/7
Out 2/6
Out 1/5
Output Card R2
Closed
Loop
ON
OFF
Open
Loop
IO Card Slot 1
IO Card Slot 2
8
Section 3: Conguration
Section 3:
Conguration Continued

TX CL+
TX CL -
RX CL(-)
RX CL(+)
CLOOP LED Blink
TX 422A
TX 422B
RX 422A
RX 422B
Receiving Wireless Signal LED Blink
422 LED Blink
GROUND
TX 232-
232 RXD
GROUND
Receiving Wireless Signal LED Blink
Receiving Wireless Signal LED Blink
Case 1
Typical Setup: Indicator to remote using two XTP Radio Modules. (Indicator wired for
Current Loop and Display wired for RS422)
Case 2
An Indicator transmitting to one or more Remotes with built in XTP Receivers.
(Indicator wired for RS232)
9
Section 4: Examples
Section 4:
Example Installations

Case 3
Networked Indicators with Bi_Directional communication (RS422)
422 LED Blink
TX 422A RX 422A
TX 422B RX 422B
RX 422A TX 422A
RX 422B TX 422B
422 LED Blink
TX 422A RX 422A
TX 422B RX 422B
RX 422A TX 422A
RX 422B TX 422B
Case 4
Indicator with a closed contact switch to operate a stoplight
422 LED Blink
(Installed Input Card)
TX 422A RX 422A
TX 422B RX 422B
GROUND
In 1
Receiving Wireless Signal LED Blink
Receiving Wireless Signal LED Blink
Receiving Wireless Signal LED Blink
10
Section 4: Examples
Section 4:
Example Installations Continued

422 LED Blink
(Installed Output Card)
232 TXD
GROUND
In 1
TX 422A RX 422A
TX 422B RX 422B
Ground GROUND
Input Out 1
232 RXD
GND
232 LED Blink
Case 6
A switch remotely controlling an AC Relay
(Installed Input Card)
GROUND
Out 1
(Installed Output Card)
GROUND
In 1 NO
COM 110 VAC
NC
AC
Relay
Receiving Wireless Signal LED Blink
(Installed Input Card)
Case 5
Indicator with a remote zero/print and button near the receiving XTP. (Indicator wired
for RS422 and Display wired RS232)
11
Section 4: Examples
Section 4:
Example Installations Continued

Case 7
Indicator with a nearby switch to manually control a stoplight.
The remote has a switch to remotely zero the indicator
422 LED Blink
(Installed Input Card in IO Card Slot 1)
(Installed Output Card in IO Card Slot 2)
TX 422A RX 422A
TX 422B RX 422B
Ground GROUND
Input Out 5
In 1
GROUND
232 TXD
GROUND
In 5
232 RXD
GROUND
232 LED Blink
Receiving Wireless Signal LED Blink
(Installed Output Card in IO Card Slot 1)
(Installed Input Card in IO Card Slot 2)
Out 1
RED
12
Section 4: Examples
Section 4:
Example Installations Continued

BEFORE YOU CALL, please see if any of the below problems/solutions match your conditions.
The Red PWR LED doesn’t come on
Verify the power supply is turned on and putting out 7.5 to 12 volts DC and that the wires are securely screwed into the
terminals.
No LEDs are blinking on the unit connected to the indicator/Source Device
Make sure the indicator’s port is enabled for continuous output and that the unit is wired according to section 1. The
indicator’s transmit should be wired into the XTP units receive terminals. The corresponding LEDs will blink with every
data transmission.
No LEDs are blinking on the Receiver/unit connected to the remote display
Make sure there is an LED blinking on the side connected to the indicator rst. If that side does not blink the receiving
side will not blink. If the indicator side is blinking, then make sure both units are set to the same ID and recongure both
units by pressing the CONFIG button on each side. Try unplugging one unit and plugging it back in to have the wireless
units re-establish the network. If the remote display end still does not blink, then the problem may be distance/obstacle
related. Try bringing both sides into an oce and see if they communicate over a short distance. If they do, then
reposition the units for better line of site or add a repeater to the system. Avoid mounting too close to any other RF
transmitters including Ham and CB Radios.
The Receiving Wireless Signal LED blinks on the remote display side of my XTP, but the remote shows“NoData”
The problem is probably with the wiring. Make sure you are coming out a transmit on the XTP unit and going into a
receive on the remote display. Try changing to a dierent transmit port. You do not have to use the same loop on the
remote display side as you use on the indicator side. Try bringing both sides into an oce and see if they communicate
over a short distance. Try using TEST MODE. See next page
The RX LED is blinking on the remote display side, but the remote is blank or shows random numbers.
Verify the baud rate is correct on both ends and press the CONFIG button on both units. Reset the remote display to
factory defaults by holding the LEFT and RIGHT buttons during countdown. After the unit starts to count down for the
second time let go and the remote should display the correct baud rate. If still blank, try shift data over to the left or
right.
The system is reliable except when weight is on the scale
Make sure that when a truck pulls on a scale it does not come between the two antennas. A truck acts as a solid metal
wall blocking the signal
The system sometimes works and sometimes does not.
Make sure nothing has changed at the site such as trees growing into the line of sight or gravel piles growing to block
the signal. If you are at the far edge of the maximum usable range then many things can degrade the signal including,
temperature, humidity, or large equipment being run nearby. In general, make sure both antennas are pointing straight
up and down, are as high above the earth as is reasonably possible and have a clear line of sight to each other. Other
than that you may need a repeater added to the system to extend the range. See next page. Some Indicators will stop
transmitting while the weight is in motion. IDs 6 and 11 work at dierent frequencies than all other IDs, there may be
too much noise/activity on your frequency . Try switching to one of these alternative frequency.
*If you are still unable to get the unit working after going through this list, please call our tech support at 1-800-814-4053
13
Section 5: Trouble Shooting
Section 5:
Trouble Shooting

Repeater
If the system is working but you cannot get the needed range for the job site you can try to add an extra XTP to the
system as a repeater unit. Mount the unit roughly in the middle of the distance with line of site to both ends. You
will need power at this location. Add a jumper wire from 232 RXD to 232 TXD. Any signal that can make it to this
module will then be repeated out. The original transmitting unit will have the data echoed back to it, so this will not
work for applications with bidirectional communication.
TEST MODE
The XTP Modules have a TEST MODE Option located on the bottom of the BLACK DIP Switch. This option will begin
transmitting data out at the last congured ID and Baud Rate. It is recommended that you press the CONFIG button
to verify all settings are known prior to entering TEST MODE.
While in TEST MODE the Module will transmit a data stream twice a second. If the receiving unit is within range and
setup on the same ID the RED Receiving Wireless Signal LED should blink twice a second as well. If you connect the
Receiving unit to a PC or Remote Display the Data Stream will be in the following format:
<STX><Counter>123456<Counter><CR><LF><ETX><CR-P><LF-P><ETX-P>
<STX> = Start of Text - Decimal 2
<Counter> incrementing 1 digit counter“0-9”
<CR> Carriage Return - Decimal 13
<LF> Line Feed - Decimal 10
<ETX> End of Text - Decimal 3
<CR-P> Carriage Return with parity bit - Decimal 141
<LF-P> Line Feed with Parity bit - Decimal 138
<ETX-P> End of Text with Parity Decimal 131
Both Transmitters and receivers can be set to TEST MODE to verify both units can see each other.
14
Section 5: Trouble Shooting
Section 5:
Trouble Shooting Continued

Product Comparison
XT100
Legacy
XT300
Legacy
XTP
Line of Sight Distance
Up to 1 mile
Up to 1 mile
Up to 2 Miles
Baud Rate
1200
2400
4800
9600
19200
9600 (Fixed)
▲
▲
▲
▲
▲
▲
▲
▲
▲
▲
Protocol
RS232
20 mA Current Loop
RS422 /485
▲
▲
▲
▲
▲
▲
▲
Approvals
US (FCC)
Canada (IC)
Europe (ETSI)
▲
▲
▲
▲
▲
▲
▲
Network ID’s
1
16
16
TTL Line Passing
0
0
Up to 4
Up to 8
Conguration Fixed In Field In Field In Field
Enclosure
NEMA 4
IP65
NEMA 4
IP65
NEMA 4
IP65
NEMA 4
IP65
XT400
Legacy
Up to 1 mile
▲
▲
▲
▲
▲
▲
▲
▲
▲
▲
▲
16
Figure 4.1: Comparison Chart
Compatibility:
The XTP Module is compatible with the prior versions XT100/XT200/XT300/XT400 so long as they are on the same
ID with the exception that ID #s 6-11 will not communicate. IDs 0-5 and 12-15 are compatible and should be used
whenever intermixing modules.
15
Section 6: Product Comparison/Compatibility
Section 6:
Product Comparison

Manual Revision
v.1.1 XTP Manual Initial Release
Part Number
Description
Order a standard remote and 2 XTP modules
*This solution allows the most exibility in the eld for moving antennas to areas with the best line of sight,
but adds a third device to the system. (Account for extra power and cabling)
Add“-XTP” to the end of the part number, i.e. SSD-5-XTP to get a package of a remote display with a built in
receiver as well as the external XTP Module to connect to.
**This solution is a streamlined solution with only 2 devices, but does not allow for the exibility of moving
the remote display around easily for better line of sight.
SSD Series Displays can be equipped with wireless capability in 2 ways
1)
2)
Serial Data to Wireless Module
Serial Data to Wireless Module in expanded case. Includes 1
Output Card and 2 Relays
Serial Data to Wireless Module in expanded case. Includes 1
Output Card and 4 Relays
Serial Data to Wireless Module in expanded case. Includes 2
Output Card and 8 Relays
4 Input Expansion Card for XTP Module
4 Output Expansion Card for XTP Module
Replacement Relay
XTP Built in Receiver Card for SSD Series Displays only
(Replacement Part)
XTP Standard antenna with u. cable
9 dBi antenna with magnetic base
24 dBi parabolic antenna with mounting bracket
9 VDC power supply for XTP Module (Replacement Part)
XTP
XTP-R2
XTP-R4
XTP-R8
XTP-INPUT
XTP-OUTPUT
RELAY
XTP-BIR
XTP-ANT
XTP-ANT-9DBI
XTP-ANT-24DBI
PWR-9V
16
Section 7: Part Numbers
Section 7:
Part Numbers
This manual suits for next models
4
Table of contents
Popular Control Unit manuals by other brands
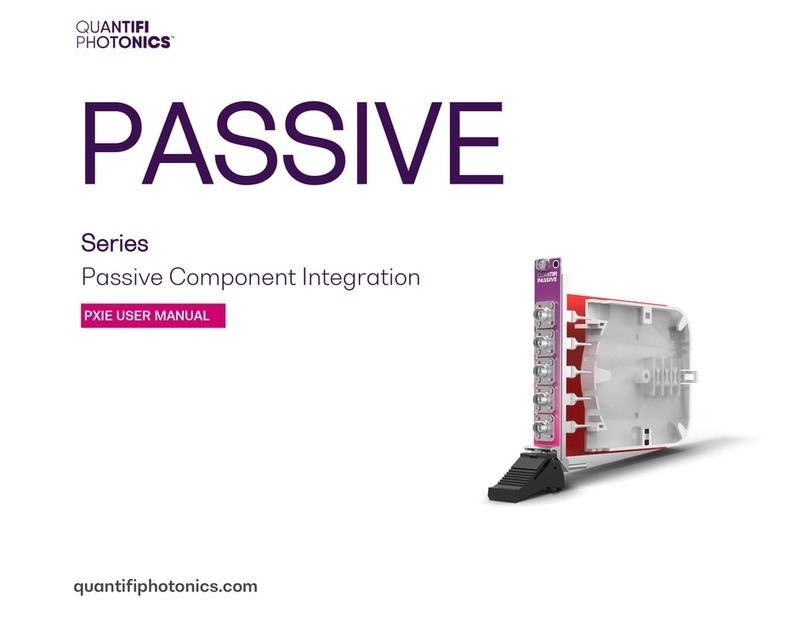
Quantifi Photonics
Quantifi Photonics PASSIVE Series user manual
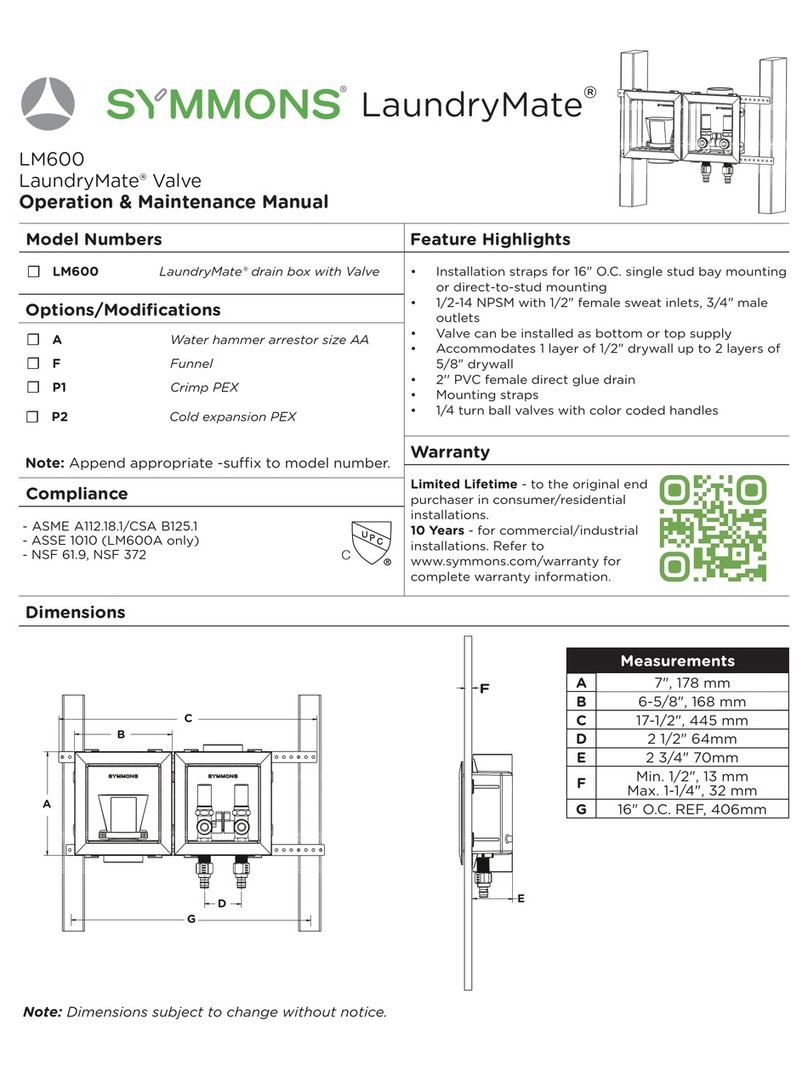
Symmons
Symmons LaundryMate LM600 Operation & maintenance manual
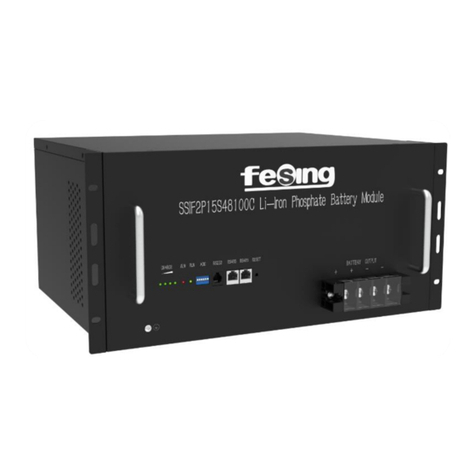
fesing
fesing SSIF2P15S48100C Applications manual
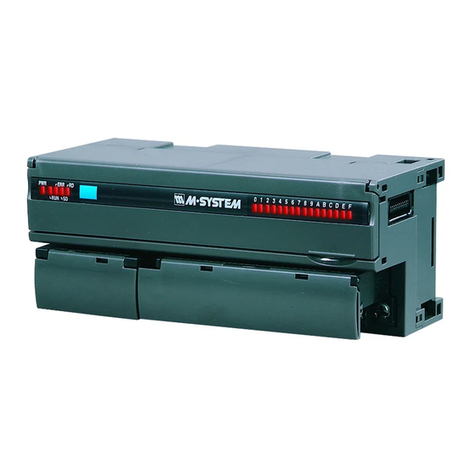
M-system
M-system R7M-EC16A instruction manual
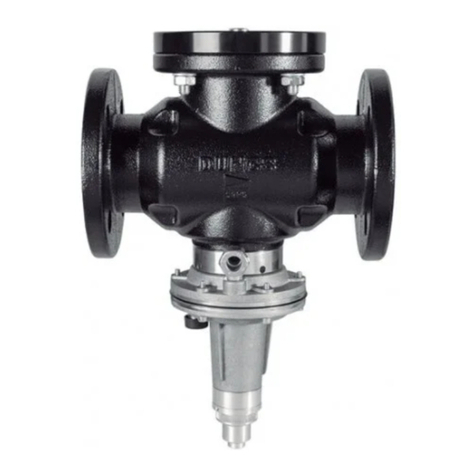
Dungs
Dungs SAV 100065 MD instruction manual

resideo
resideo Braukmann D15S installation instructions
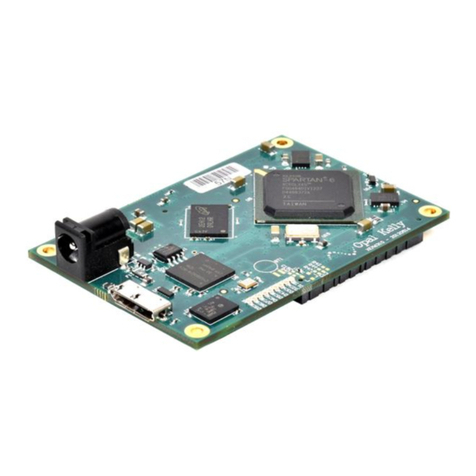
Opal Kelly
Opal Kelly XEM6310 user manual
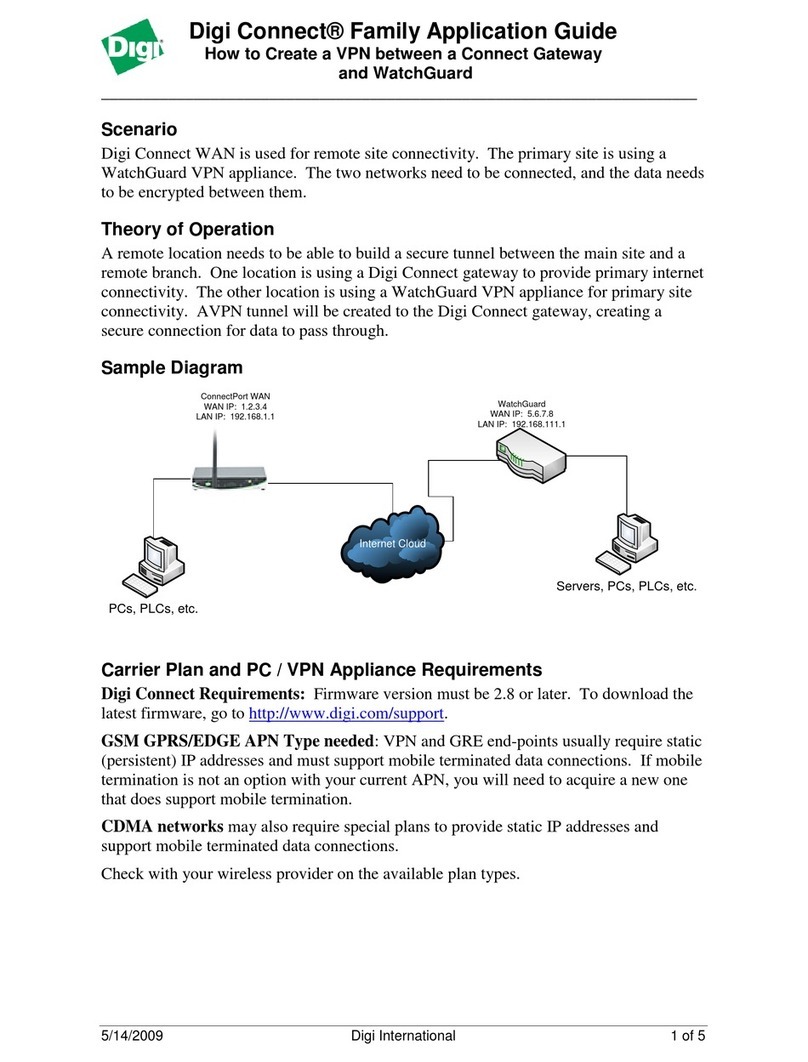
Digi
Digi Connect Series Application guide
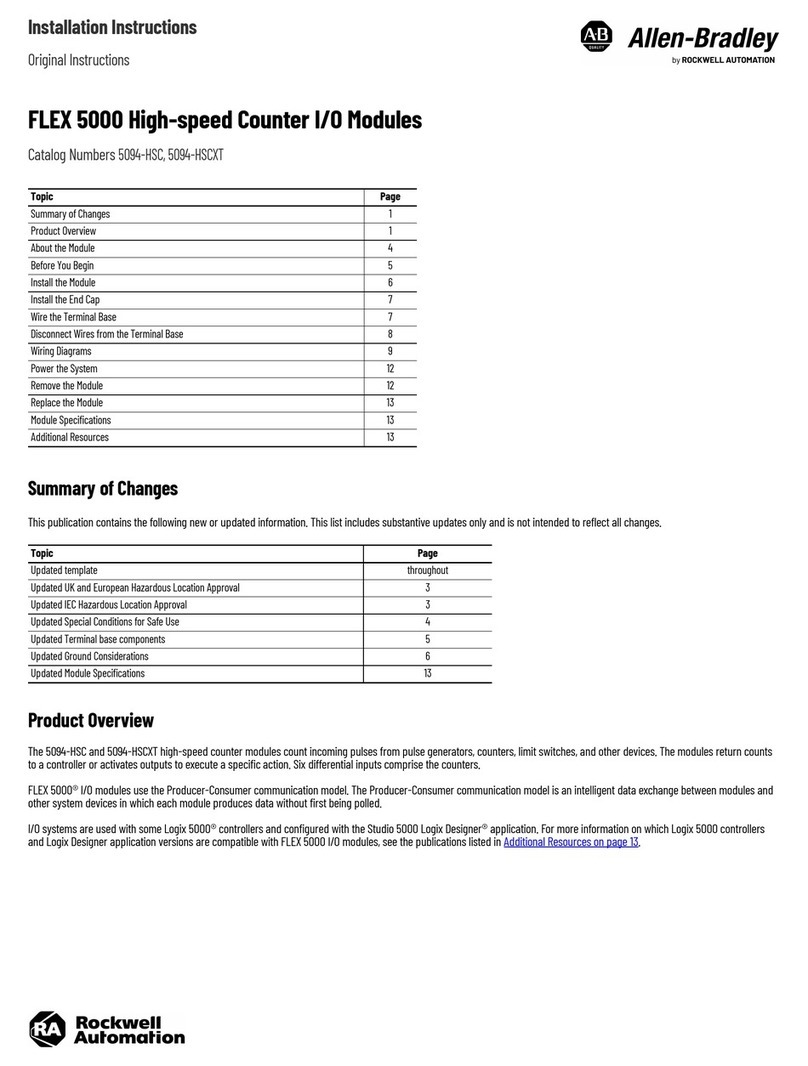
Rockwell Automation
Rockwell Automation Allen-Bradley FLEX 5000 Series installation instructions
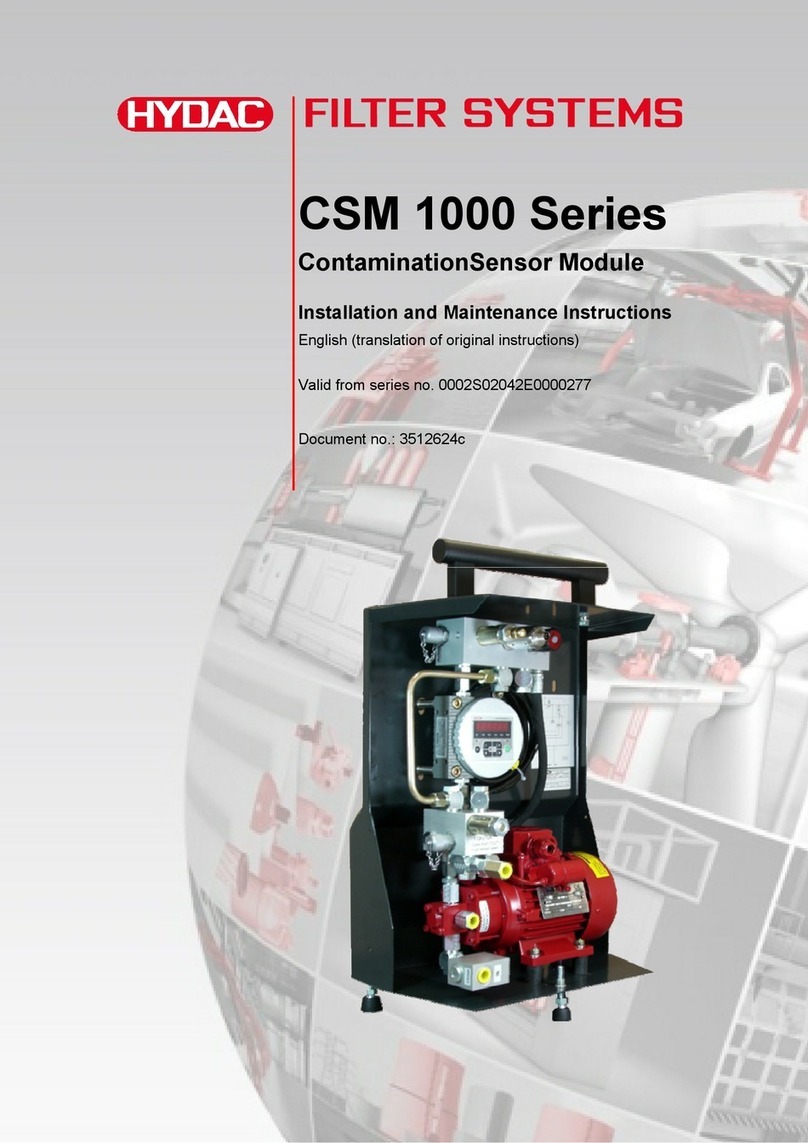
HYDAC FILTER SYSTEMS
HYDAC FILTER SYSTEMS CSM 1000 Series Installation and maintenance instructions
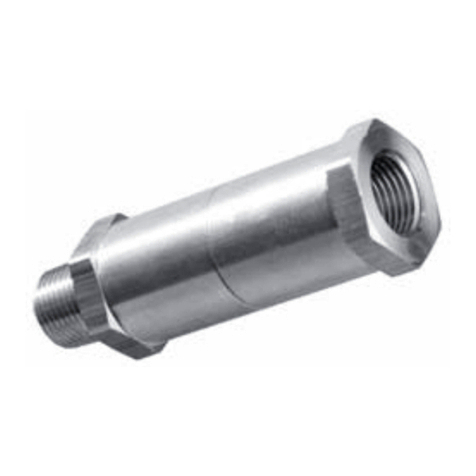
Concoa
Concoa 830-9412 Installation and operation instruction

Grundfos
Grundfos PLV Series instructions