Maxim MAX16067 User manual

_______________________________________________________________ Maxim Integrated Products 1
For pricing, delivery, and ordering information, please contact Maxim Direct at 1-888-629-4642,
or visit Maxim’s website at www.maxim-ic.com.
MAX16067
6-Channel, Flash-Configurable System Manager
with Nonvolatile Fault Registers
19-5028; Rev 2; 6/10
Note: This device is specified over the -40NC to +85NC extended temperature range.
+Denotes a lead(Pb)-free/RoHS-compliant package.
*EP = Exposed pad.
Ordering Information/Selector Guide
General Description
The MAX16067 flash-configurable system manager
monitors and sequences multiple system voltages. The
MAX16067 manages up to six system voltages simulta-
neously. The MAX16067 integrates an analog-to-digital
converter (ADC) and configurable outputs for sequenc-
ing power supplies. Device configuration information,
including overvoltage and undervoltage limits, time
delay settings, and the sequencing order is stored in
nonvolatile flash memory. During a fault condition, fault
flags and channel voltages can be automatically stored
in the nonvolatile flash memory for later readback.
The internal 1% accurate, 10-bit ADC measures each
input and compares the result to one overvoltage and
one undervoltage limit. A fault signal asserts when a
monitored voltage falls outside the set limits.
The MAX16067 supports a power-supply voltage of up to
14V and can be powered directly from the 12V interme-
diate bus in many systems.
The integrated sequencer provides precise control over
the power-up and power-down order of up to six power
supplies. Three outputs (EN_OUT1 to EN_OUT3) are
configurable with charge-pump outputs to directly drive
external n-channel MOSFETs.
The MAX16067 includes six programmable general-
purpose inputs/outputs (GPIOs). GPIOs are flash con-
figurable as a fault output, as a watchdog input or output,
or as a manual reset.
The MAX16067 features nonvolatile fault memory for
recording information during system shutdown events.
The fault logger records a failure in the internal flash
and sets a lock bit protecting the stored fault data from
accidental erasure.
An SMBus™ or a JTAG serial interface configures the
MAX16067. The MAX16067 is available in a 32-pin, 5mm
x 5mm, TQFN package and is fully specified over the
-40NC to +85NC extended temperature range.
Features
SOperates from 2.8V to 14V
S1% Accurate, 10-Bit ADC Monitors 6 Voltage
Inputs
SAnalog EN Monitoring Input
S6 Monitored Inputs with Overvoltage and
Undervoltage Limits
SNonvolatile Fault Event Logger
SPower-Up and Power-Down Sequencing
Capability
S6 Outputs for Sequencing/Power-Good Indicators
S3 Configurable Charge-Pump Outputs
SSix General-Purpose Inputs/Outputs Configurable
as:
Dedicated Fault Output
Watchdog Timer Function
Manual Reset
SMBus Alert
Fault Propagation Input/Output
SSMBus and JTAG Interface
SSupports Cascading with MAX16065/MAX16066
SFlash-Configurable Time Delays and Thresholds
S-40NC to +85NC Extended Operating Temperature
Range
Applications
Networking Equipment
Telecom Equipment (Base Stations, Access)
Storage/RAID Systems
Servers
Typical Operating Circuit appears at end of data sheet.
SMBus is a trademark of Intel Corp.
PART PIN-PACKAGE VOLTAGE-
DETECTOR INPUTS
GENERAL-PURPOSE
INPUTS/OUTPUTS
SEQUENCING
OUTPUTS
MAX16067ETJ+ 32 TQFN-EP* 6 6 6

2 ______________________________________________________________________________________
MAX16067
6-Channel, Flash-Configurable System Manager
with Nonvolatile Fault Registers
Stresses beyond those listed under “Absolute Maximum Ratings” may cause permanent damage to the device. These are stress ratings only, and functional
operation of the device at these or any other conditions beyond those indicated in the operational sections of the specifications is not implied. Exposure to absolute
maximum rating conditions for extended periods may affect device reliability.
VCC to GND...............……………………………….-0.3V to +15V
MON_, SCL, SDA, A0 to GND ................................-0.3V to +6V
EN, TCK, TMS, TDI to GND ....................................-0.3V to +4V
TDO to GND............................................-0.3V to (VDBP + 0.3V)
EN_OUT1, EN_OUT2, EN_OUT3
(configured as open-drain) to GND ..................-0.3V to +15V
EN_OUT1, EN_OUT2, EN_OUT3
(configured as charge pump) to GND..............-0.3V to +15V
EN_OUT4, EN_OUT5, EN_OUT6, RESET, GPIO_
(configured as open-drain) to GND.....................-0.3V to +6V
EN_OUT_, RESET, GPIO_ (configured as push-pull)
to GND .................................................-0.3V to (VDBP + 0.3V)
DBP, ABP to GND .......................................-0.3V to minimum of
(4V and (VCC + 0.3V))
Continuous Current (all other pins)................................. Q20mA
Continuous Current (GND, pin 5).................................... Q30mA
Continuous Power Dissipation (TA= +70NC)
32-Pin TQFN (derate 34.5mW/NC above +70NC)..... 2759mW*
Thermal Resistance (Note 1)
BJA................................................................................29NC/W
BJC .................................................................................2NC/W
Operating Temperature Range.......................... -40NC to +85NC
Junction Temperature .....................................................+150NC
Storage Temperature Range............................ -65NC to +150NC
Lead Temperature (soldering, 10s) ................................+300NC
Soldering Temperature (reflow) ......................................+260NC
ELECTRICAL CHARACTERISTICS
(VCC = 2.8V to 14V, TA= TJ= -40NC to +85NC, unless otherwise specified. Typical values are at VABP = VDBP = VCC = 3.3V,
TA= +25NC.) (Note 2)
ABSOLUTE MAXIMUM RATINGS
*As per JEDEC 51 Standard, Multilayer Board (PCB).
Note 1: Package thermal resistances were obtained using the method described in JEDEC specification JESD51-7, using a four-
layer board. For detailed information on package thermal considerations, refer to www.maxim-ic.com/thermal-tutorial.
PARAMETER SYMBOL CONDITIONS MIN TYP MAX UNITS
Operating Voltage Range VCC RESET output asserted low 1.2 V
2.8 14
Undervoltage Lockout VUVLO Minimum voltage on VCC to ensure the
device is flash configurable 2.7 V
Undervoltage Lockout Hysteresis UVLOHYS 55 mV
Minimum Flash Operating Voltage VFLASH Minimum voltage on VCC to ensure flash
erase and write operations 2.7 V
Supply Current
ICC1 No load on any output 2.8 4
mAICC2 No load on any output, during flash writing
cycle 7.7 14
VCC = VABP = VDBP = 3.6V (Note 3) 5
DBP Regulator Voltage VDBP VCC = 5V, CDBP = 1FF, no load 2.8 3 3.2 V
ABP Regulator Voltage VABP VCC = 5V, CABP = 1FF, no load 2.85 3 3.15 V
Boot Time tBOOT VCC > VUVLO 100 200 Fs
Flash Writing Time 8-byte word 122 ms
Internal Timing Accuracy (Note 4) -10 +10 %
ADC
Resolution 10 Bits
Gain Error ADCGAIN TA= +25NC0.35 %
TA= -40NC to +85NC0.75
Offset Error ADCOFF 1.50 LSB
Integral Nonlinearity ADCINL 1 LSB

_______________________________________________________________________________________ 3
MAX16067
6-Channel, Flash-Configurable System Manager
with Nonvolatile Fault Registers
ELECTRICAL CHARACTERISTICS (continued)
(VCC = 2.8V to 14V, TA= TJ= -40NC to +85NC, unless otherwise specified. Typical values are at VABP = VDBP = VCC = 3.3V,
TA= +25NC.) (Note 2)
PARAMETER SYMBOL CONDITIONS MIN TYP MAX UNITS
Differential Nonlinearity ADCDNL 1 LSB
ADC Total Monitoring Cycle Time tCYCLE Monitoring all 6 inputs, no MON_ fault
detected 24 30 Fs
ADC MON_ Ranges ADCRNG
MON_ range set to ‘00’ 5.552
VMON_ range set to ‘01’ 2.776
MON_ range set to ‘10’ 1.388
ADC LSB Step Size ADCLSB
MON_ range set to ‘00’ 5.42
mVMON_ range set to ‘01’ 2.71
MON_ range set to ‘10’ 1.35
ADC Input Leakage Current 1 FA
ENABLE INPUT (EN)
EN Input-Voltage Threshold VTH_EN_R EN voltage rising 1.24 V
VTH_EN_F EN voltage falling 1.195 1.215 1.235
EN Input Current IEN -0.5 +0.5 FA
EN Input-Voltage Range 0 3.6 V
OUTPUTS (EN_OUT_, RESET, GPIO_)
Output Voltage Low VOL
ISINK = 2mA 0.4
VISINK = 10mA, GPIO_ only 0.7
VCC = 1.2V, ISINK = 100FA (RESET only) 0.3
Maximum Output Sink Current Total current into EN_OUT_, RESET, GPIO_,
VCC = 3.3V 30 mA
Output-Voltage High (Push-Pull) VOH ISOURCE =100FA2.4 V
Output-Voltage High (EN_OUT1,
EN_OUT2, EN_OUT3 Configured
as Charge Pumps)
VOH_CP IEN_OUT_= 1FA11 11.7 13 V
EN_OUT_ Pullup Current
(Charge Pump) ICH_UP VEN_OUT_ = 1V 5.4 7.9 FA
Output Leakage Current
(Open Drain) IOUT_LKG 1FA
EN_OUT1, EN_OUT2, EN_OUT3 > 11.8V 5
INPUTS (A0, GPIO_)
Input Logic-Low VIL 0.8 V
Input Logic-High VIH 2.0 V
WDI Pulse Width tWDI 100 ns
MR Pulse Width tMR 2Fs
SMBus INTERFACE
Logic-Input Low Voltage VIL Input voltage falling 0.8 V
Logic-Input High Voltage VIH Input voltage rising 2.0 V
Input Leakage Current VCC shorted to GND, VMON_ = 0 or 6V -1 +1 FA
Output Sink Current VOL ISINK = 3mA 0.4 V
Input Capacitance CIN 5 pF

4 ______________________________________________________________________________________
MAX16067
6-Channel, Flash-Configurable System Manager
with Nonvolatile Fault Registers
ELECTRICAL CHARACTERISTICS (continued)
(VCC = 2.8V to 14V, TA= TJ= -40NC to +85NC, unless otherwise specified. Typical values are at VABP = VDBP = VCC = 3.3V,
TA= +25NC.) (Note 2)
Note 2: Specifications are guaranteed for the stated global conditions, unless otherwise noted. 100% production tested at TA=
+25NC and TA= +85NC. Specifications at TA= -40NC are guaranteed by design.
Note 3: For VCC of 3.6V or lower, connect VCC, DBP, and ABP together. For higher supply applications, connect only VCC to the
supply rail.
Note 4: Applies to RESET (except for reset timeout period of 25Fs), fault, autoretry, sequence delays, and watchdog timeout.
PARAMETER SYMBOL CONDITIONS MIN TYP MAX UNITS
SMBus TIMING
Serial-Clock Frequency fSCL 400 kHz
Bus Free Time Between STOP
and START Condition tBUF 1.3 Fs
START Condition Setup Time tSU:STA 0.6 Fs
START Condition Hold Time tHD:STA 0.6 Fs
STOP Condition Setup Time tSU:STO 0.6 Fs
Clock Low Period tLOW 1.3 Fs
Clock High Period tHIGH 0.6 Fs
Data Setup Time tSU:DAT 100 ns
Output Fall Time tOF 10pF PCBUS P400pF 250 ns
Data Hold Time tHD:DAT From 50% SCL falling to SDA
change
Receive 0.15 Fs
Transmit 0.3 0.9
Pulse Width of Spike Suppressed tSP 250 ns
SMBus Timeout tTIMEOUT SMBCLK time low for reset 22 35 ms
JTAG INTERFACE
TDI, TMS, TCK Logic-Low Input
Voltage VIL Input voltage falling 0.8 V
TDI, TMS, TCK Logic-High Input
Voltage VIH Input voltage rising 2.0 V
TDO Logic-Output Low Voltage VOL_TDO ISINK = 3mA 0.4 V
TDO Logic-Output High Voltage VOH_TDO ISOURCE = 200FA2.4 V
TDI, TMS Pullup Resistors RJPU Pullup to DBP 30 50 65 kI
I/O Capacitance CI/O 5 pF
TCK Clock Period t11000 ns
TCK High/Low Time t2, t350 500 ns
TCK to TMS, TDI Setup Time t415 ns
TCK to TMS, TDI Hold Time t515 ns
TCK to TDO Delay t6500 ns
TCK to TDO High-Z Delay t7500 ns

_______________________________________________________________________________________ 5
MAX16067
6-Channel, Flash-Configurable System Manager
with Nonvolatile Fault Registers
Figure 1. SMBus Timing Diagram
Figure 2. JTAG Timing Diagram
STOP
CONDITION
REPEATED START
CONDITION
START
CONDITION
tHIGH
tLOW
tRtF
tSU:DAT
tSU:STA tSU:STO
tHD:STA
tBUF
tHD:STA
tHD:DAT
SCL
SDA
START
CONDITION
TCK
t1
t2t3
t4t5
t6
t7
TDI, TMS
TDO

6 ______________________________________________________________________________________
MAX16067
6-Channel, Flash-Configurable System Manager
with Nonvolatile Fault Registers
Typical Operating Characteristics
(Typical values are at VCC = 3.3V, TA= +25NC.)
MR TO RESET PROPAGATION DELAY
vs. TEMPERATURE
TEMPERATURE (°C)
DELAY (ns)
806040200-20-40
MAX16067 toc07
200
300
400
500
600
700
800
900
1000
1100
100
MAX
MIN
OUTPUT VOLTAGE vs. SINK CURRENT
(OUT = LOW)
ISINK (mA)
VOUT (V)
15105
0.05
0.10
0.15
0.20
0.25
0.30
0.35
0.40
0
0 20
MAX16067 toc08
RESET, GPIO_,
AND EN_OUT4–
EN_OUT6
EN_OUT1–
EN_OUT3
VCC SUPPLY CURRENT
vs. VCC SUPPLY VOLTAGE
MAX16067 toc01
VCC (V)
ICC (mA)
12102 4 6 8
0.5
1.0
1.5
2.0
2.5
3.0
3.5
4.0
0
0 14
TA= -40°C TA= +25°C
TA= +85°C
ABP AND DBP CONNECTED
TO VCC
ABP AND DBP
REGULATORS ACTIVE
NORMALIZED MON_THRESHOLD
vs. TEMPERATURE
TEMPERATURE (°C)
NORMALIZED MON_ THRESHOLD
806040200-20
0.965
0.980
0.995
1.010
1.025
1.040
1.055
0.950
-40
MAX16067 toc02
5.6V RANGE
HALF-SCALE
PUV THRESHOLD
NORMALIZED EN THRESHOLD
vs. TEMPERATURE
TEMPERATURE (°C)
NORMALIZED EN THRESHOLD
806040200-20
0.965
0.980
0.995
1.010
1.025
1.040
1.055
0.950
-40
MAX16067 toc03
TRANSIENT DURATION
vs. THRESHOLD OVERDRIVE (EN)
EN OVERDRIVE (mV)
TRANSIENT DURATION (µs)
10
5
10
15
20
25
30
35
0
1 100
MAX16067 toc04
NORMALIZED TIMING ACCURACY
vs. TEMPERATURE
TEMPERATURE (°C)
NORMALIZED SLOT DELAY
806040200-20
0.965
0.980
0.995
1.010
1.025
1.040
1.055
0.950
-40
MAX16067 toc05
TRANSIENT DURATION
vs. MON_ DEGLITCH
DEGLITCH VALUE
TRANSIENT DURATION (us)
1684
10
20
30
40
50
60
70
80
90
0
2
MAX16067 toc06

_______________________________________________________________________________________ 7
MAX16067
6-Channel, Flash-Configurable System Manager
with Nonvolatile Fault Registers
Typical Operating Characteristics (continued)
(Typical values are at VCC = 3.3V, TA= +25NC.)
RESET OUTPUT CURRENT
vs. VCC SUPPLY VOLTAGE
VCC (V)
OUTPUT CURRENT (mA)
12108642
5
10
15
20
25
0
0 14
MAX16067 toc15
ABP AND DBP CONNECTED TO VCC
ABP AND DBP
REGULATORS ACTIVE
VRESET = 0.3V
OUTPUT-VOLTAGE HIGH vs. SOURCE
CURRENT (CHARGE-PUMP OUTPUT)
ISOURCE (µA)
VOUT (V)
7654321
2
4
6
8
10
12
14
0
0 8
MAX16067 toc09
OUTPUT-VOLTAGE HIGH vs.
SOURCE CURRENT (PUSH-PULL OUTPUT)
ISOURCE (µA)
VOUT (V)
1000800600400200
2.5
2.6
2.7
2.8
2.9
3.0
3.1
3.2
3.3
3.4
2.4
0 1200
MAX16067 toc10
RESET
GPIO_
EN_OUT1,
EN_OUT2,
EN_OUT3
INTEGRAL NONLINEARITY vs. CODE
MAX16067 toc11
CODE (LSB)
INL (LSB)
896768512 640256 384128
-0.8
-0.6
-0.4
-0.2
0
0.2
0.4
0.6
0.8
1.0
-1.0
0 1024
DIFFERENTIAL NONLINEARITY vs. CODE
MAX16067 toc12
CODE (LSB)
DNL (LSB)
896768512 640256 384128
-0.8
-0.6
-0.4
-0.2
0
0.2
0.4
0.6
0.8
1.0
-1.0
0 1024
FET TURN_ON WITH CHARGE PUMP
MAX16067 toc13
VEN_OUT1
5V/div
IOUT
1A/div
VOUT
5V/div
100ms/div
SEQUENCING
MAX16067 toc14
VEN_OUT1
2V/div
VEN_OUT2
2V/div
VEN_OUT3
2V/div
VEN_OUT4
2V/div
200µs/div

8 ______________________________________________________________________________________
MAX16067
6-Channel, Flash-Configurable System Manager
with Nonvolatile Fault Registers
Pin Description
Pin Configuration
MAX16067
TQFN
TOP VIEW
29
30
28
27
12
11
13
GPIO4
GPIO6
GND
AO
SCL
14
GPIO3
GND
VCC
DBP
MON1
EN
EN_OUT1
1 2
MON5
4 5 6 7
2324 22 20 19 18
MON6
RESET
EN_OUT5
EN_OUT6
TMS
TCK
GPIO5 ABP
3
21
31 10
GPIO1 TDI
32 9
GPIO2 TDO
MON4
26 15 EN_OUT4
MON3
25 16 EN_OUT3
SDA EN_OUT2
8
17
MON2
+*EP
*CONNECT EXPOSED PAD TO GND.
PIN NAME FUNCTION
1–4, 31, 32 GPIO3–GPIO6,
GPIO1, GPIO2
General-Purpose Inputs/Outputs. Each GPIO_ can be configured to act as an input, a push-pull
output, an open-drain output, or a special function.
5, 23 GND Ground. Connect all GNDs together.
6 A0 Four-State SMBus Address. Address is sampled upon POR.
7 SCL SMBus Serial-Clock Input
8 SDA SMBus Serial-Data Open-Drain Input/Output
9 TDO JTAG Test Data Output
10 TDI JTAG Test Data Input
11 TCK JTAG Test Clock
12 TMS JTAG Test Mode Select
13–18 EN_OUT6–
EN_OUT1
Outputs. Set EN_OUT_ with an active-high/active-low logic and with push-pull or open-drain
configuration. EN_OUT_ can be asserted by a combination of MON_ voltages configurable
through the flash. EN_OUT1–EN_OUT3 can be configured with a charge-pump output (+12V
above GND) that can drive an external n-channel MOSFET. All EN_OUT_ can be configured as
GPIOs.
19 EN Analog Enable Input. All outputs deassert when VEN is below the enable threshold.

_______________________________________________________________________________________ 9
MAX16067
6-Channel, Flash-Configurable System Manager
with Nonvolatile Fault Registers
Pin Description (continued)
Functional Diagram
GPIO5
WDO
GPIO4
WDI
GPIO6
MR GPIO3
FAULT GPIO2
EXTFAULT
GPIO1
ALERT
AO SCL SDA
REF REG
DECODE
LOGIC
SEQUENCER
STATE
MACHINE
WATCHDOG
TIMER
DIGITAL
COMPARATORS
GPIO
CONTROL
EN_OUT1–
EN_OUT6
RESET
ABP
VCC DBP
RESET
OUTPUT
LOGIC
RAM
REGISTERS
FLASH
REGISTERS
SMBus
INTERFACE
JTAG
INTERFACE
ADC
REGISTERS
10-BIT ADC
(SAR)
EN
VTH_EN
MON1
MON2
MON3
MON4
MON5
MON6
TDO TDI TCK TMSGND
MAX16067
VOLTAGE
AND
SCALING
MUX
PIN NAME FUNCTION
20 DBP Digital Bypass. All push-pull outputs are referenced to DBP. Bypass DBP with a 1FF capacitor
to GND.
21 VCC Power-Supply Input. Bypass VCC to GND with a 10FF ceramic capacitor.
22 ABP Analog Bypass. Bypass ABP to GND with a 1FF ceramic capacitor.
24–29 MON1–MON6
Monitor Voltage Inputs. Set the monitor voltage range through the configuration registers.
Measured values are written to the ADC registers and can be read back through the SMBus or
JTAG interface.
30 RESET Configurable Reset Output
— EP Exposed Pad. Internally connected to GND. Connect to ground, but do not use EP as the main
ground connection.

10 _____________________________________________________________________________________
MAX16067
6-Channel, Flash-Configurable System Manager
with Nonvolatile Fault Registers
Detailed Description
The MAX16067 manages up to six system power sup-
plies. After boot-up, if EN is high and the software-enable
bit is set to ‘1,’ a power-up sequence begins based on
the configuration stored in flash and the EN_OUT_s are
controlled accordingly. When the power-up sequence is
successfully completed, the monitoring phase begins.
An internal multiplexer cycles through each MON_ input.
At each multiplexer stop, the 10-bit ADC converts the
monitored analog voltage to a digital result and stores
the result in a register. Each time a conversion cycle
(5Fs, max) completes, internal logic circuitry compares
the conversion results to the overvoltage and undervolt-
age thresholds stored in memory. When a result violates
a programmed threshold, the conversion can be con-
figured to generate a fault. GPIO_ can be programmed
to assert on combinations of faults. Additionally, faults
can be configured to shut off the system and trigger the
nonvolatile fault logger, which writes all fault information
automatically to the flash and write-protects the data to
prevent accidental erasure.
The MAX16067 contains both SMBus and JTAG serial
interfaces for accessing registers and flash. Use only
one interface at any given time. For more information
on how to access the internal memory through these
interfaces, see the SMBus-Compatible Serial Interface
and JTAG Serial Interface sections. The memory map
is divided into three pages with access controlled by
special SMBus and JTAG commands.
The factory-default values at POR (power-on reset) for all
RAM registers are ‘0’s. POR occurs when VCC reaches
the undervoltage-lockout threshold (UVLO) of 2.7V
(max). At POR, the device begins a boot-up sequence.
During the boot-up sequence, all monitored inputs are
masked from initiating faults and flash contents are
copied to the respective register locations. During boot-
up, the MAX16067 is not accessible through the serial
interface. The boot-up sequence takes up to 150Fs, after
which the device is ready for normal operation. RESET
is asserted low up to the boot-up phase after which it
assumes its programmed active state. RESET remains
active for its programmed timeout period once sequenc-
ing is completed and all monitored channels are within
their respective thresholds. Up to the boot-up phase, the
GPIO_s and EN_OUT_s are high impedance.
Power
Apply 2.8V to 14V to VCC to power the MAX16067.
Bypass VCC to ground with a 10FF capacitor. Two inter-
nal voltage regulators, ABP and DBP, supply power to
the analog and digital circuitry within the device. For
operation at 3.6V or lower, disable the regulators by con-
necting ABP and DBP to VCC.
ABP is a 3.0V (typ) voltage regulator that powers the inter-
nal analog circuitry. Bypass ABP to GND with a 1FF ceram-
ic capacitor installed as close as possible to the device.
DBP is an internal 3.0V (typ) voltage regulator. DBP
powers flash and digital circuitry. All push-pull outputs
refer to DBP. DBP supplies the input voltage to the inter-
nal charge pump when the programmable outputs are
configured as charge-pump outputs. Bypass the DBP
output to GND with a 1FF ceramic capacitor installed as
close as possible to the device.
Do not power external circuitry from ABP or DBP.
Sequencing
To sequence a system of power supplies safely, the out-
put voltage of a power supply must be good before the
next power supply may turn on. Connect EN_OUT_ out-
puts to the enable input of the external power supplies
and connect MON_ inputs to the output of the power
supplies for voltage monitoring. More than one MON_
can be used if the power supply has multiple outputs.
Sequence Order
The MAX16067 provides a system of ordered slots to
sequence multiple power supplies. To determine the
sequence order, assign each EN_OUT_ to a slot ranging
from Slot 1 to Slot 6 (Table 6b). EN_OUT_(s) assigned to
Slot 1 are turned on first, followed by outputs assigned
to Slot 2 through Slot 6. Multiple EN_OUT_s assigned to
the same slot turn on at the same time.
Each slot includes a built-in configurable sequence
delay (registers r77h to r7Dh) ranging from 80Fs to
5.079s. During a reverse sequence, slots are turned off
in reverse order starting from Slot 6. The MAX16067 can
be configured to power down in simultaneous mode or
in reverse-sequence mode as set in r75h[0]. Set r75h[0]
to ‘1’ for reverse sequence power-down.
See Tables 5 and 6 for the MON_ and EN_OUT_ slot assign-
ment bits, and Tables 2 and 3 for the sequence delays.
During power-up or power-down sequencing, the cur-
rent sequencer state can be found in r21h[3:0].

______________________________________________________________________________________ 11
MAX16067
6-Channel, Flash-Configurable System Manager
with Nonvolatile Fault Registers
A sequencing delay occurs between each slot and is
configured in registers 77h–7Dh as shown in Table 2.
Each sequencing delay is stored as an 8-bit value and
is calculated as follows:
( )
( )
6 a
SEQ
t 5 10 2 16 b
−
= × × × +
where tSEQ is in seconds, a is the decimal value of the
4 MSBs and b is the decimal value of the 4 LSBs. See
Table 3 for example calculations.
Enable Input (EN)
To initiate sequencing and enable monitoring, the volt-
age at EN must be above 1.24V (typ) and the software
enable bit in r73h[0] must be set to ‘1.’ To power down
and disable monitoring, either pull EN below 1.215V
(typ) or set the software enable bit to ‘0.’ See Table 4 for
the software enable bit configurations. Connect EN to
ABP if not used.
If a fault condition occurs during the power-up cycle,
the EN_OUT_ outputs are powered down immediately,
regardless of the state of EN. In the monitoring state,
if EN falls below the threshold, the sequencing state
machine begins the power-down sequence. If EN rises
above the threshold during the power-down sequence,
the sequence state machine continues the power-down
sequence until all the channels are powered off and then
the device immediately begins the power-up sequence.
When in the monitoring state, and when EN falls below
the undervoltage threshold, a register bit, ENRESET
(r20h[2]), is set to a ‘1.’ This register bit latches and must
be cleared through software. This bit indicates if RESET
is asserted low due to EN going under the threshold.
The POR state of ENRESET is ‘0’. The bit is only set on a
falling edge of the EN comparator output or the software
enable bit. If operating in latch-on fault mode, toggle EN
or toggle the software enable bit to clear the latch condi-
tion and restart the device once the fault condition has
been removed.
Table 1. Current Sequencer Slot
Table 2. Slot Delay Register
REGISTER
ADDRESS BIT RANGE DESCRIPTION
21h [3:0]
Current-sequencer state
0000 = Slot0
0001 = Slot1
0010 = Slot2
0011 = Slot3
0100 = Slot4
0101 = Slot5
0110 = Slot6
0111 = Power-on mode
1000 = Fault state
1001 to 1111 = Unused
[7:4] Reserved
REGISTER
ADDRESS
FLASH
ADDRESS BIT RANGE DESCRIPTION
77h 277h [7:0] Sequence slot 0 to slot 1 delay
78h 278h [7:0] Sequence slot 1 to slot 2 delay
79h 279h [7:0] Sequence slot 2 to slot 3 delay
7Ah 27Ah [7:0] Sequence slot 3 to slot 4 delay
7Bh 27Bh [7:0] Sequence slot 4 to slot 5 delay
7Ch 27Ch [7:0] Sequence slot 5 to slot 6 delay
7Dh 27Dh [7:0] Sequence slot 6 to power-on state delay

12 _____________________________________________________________________________________
MAX16067
6-Channel, Flash-Configurable System Manager
with Nonvolatile Fault Registers
Monitoring Inputs While Sequencing
An enabled MON_ input can be assigned to a slot
ranging from Slot 1 to Slot 6. EN_OUT_s are always
asserted at the beginning of a slot. The supply voltages
connected to the MON_ inputs must exceed the under-
voltage threshold before the programmed fault timeout
period expires, otherwise, a fault condition occurs. Once
a MON_ input crosses the undervoltage threshold, the
monitoring for overvoltage begins. The undervoltage
and overvoltage threshold checking cannot be disabled
during power-up and power-down. See Tables 5 and
6 for the MON_ slot assignment bits. The programmed
sequence delay is then counted before moving to the
next slot.
Slot 0 does not monitor any MON_ input and does not
control any EN_OUT_. Slot 0 waits for the software
enable bit r73h[0] to be a logic-high and for the voltage
on EN to rise above 1.24V (typ) before initiating the pow-
er-up sequence and counting its own sequence delay.
Any MON_ input that suffers a fault during power-up
sequencing causes all the EN_OUT_s to turn off and
the sequencer to shut down regardless of the state of
the critical fault enables (see the Faults section). If a
MON_ input is less critical to system operation, it can
be configured as “monitoring only” (see Table 6a) for
sequencing. Monitoring for MON_ inputs assigned as
“monitoring only” begins after sequencing is complete,
and can trigger a critical fault only if specifically config-
ured to do so using the critical fault enables.
Table 3. Power-Up/Power-Down Slot Delays
Table 4. Software Enable Configurations
Code Value
0000 0000
•
•
•
•
•
•
1111 1111
( )
( )
( )
( )
6 a 6 0
SEQ
t 5 10 2 16 b 5 10 2 16 0 80 s
− −
= × × × + = × × × + = µ
( )
( )
( )
( )
6 a 6 15
SEQ
t 5 10 2 16 b 5 10 2 16 15 5.079s
− −
= × × × + = × × × + =
REGISTER
ADDRESS
FLASH
ADDRESS BIT RANGE DESCRIPTION
73h 273h
[0]
Software enable
1 = Sequencing enabled
0 = Power-down
[1] Reserved
[2] 1 = Margin mode enabled
[3] Reserved
[4]
Independent watchdog mode enable
1 = Watchdog timer is independent of sequencer
0 = Watchdog timer boots after sequence completes

______________________________________________________________________________________ 13
MAX16067
6-Channel, Flash-Configurable System Manager
with Nonvolatile Fault Registers
Figure 3. Delay and Reset Timing
SLOT 0
EN_OUT1
BOTH ARE
ASSIGNED
TO SLOT 1
MON4
EN_OUT2
MON3
MON5
RESET
EN
SLOT 1
tFAULT
OV
UV
SLOT1-SLOT2
DELAY
SLOT1-SLOT2
DELAY
MON4 MUST
REACH UV
THRESHOLD BY THIS
TIME
UV/OV
MONITORING BEGINS
WHEN MON4
REACHES UV
THRESHOLD
SLOT 2 SLOT 6
RESET
TIMEOUT
BOTH ARE
ASSIGNED
TO SLOT 2

14 _____________________________________________________________________________________
MAX16067
6-Channel, Flash-Configurable System Manager
with Nonvolatile Fault Registers
Table 5. MON_ and EN_OUT_ Assignment Registers
Table 6b. EN_OUT_ Slot Assignment
Codes
Table 6a. MON_ Slot Assignment Codes
REGISTER
ADDRESS
FLASH
ADDRESS BIT RANGE DESCRIPTION
7Eh 27Eh
[2:0] MON1
[3] Not used
[6:4] MON2
[7] Not used
7Fh 27Fh
[2:0] MON3
[3] Not used
[6:4] MON4
[7] Not used
80h 280h
[2:0] MON5
[3] Not used
[6:4] MON6
[7] Not used
81h–83h 281h–283h — Not used
84h 284h [3:0] EN_OUT1
[7:4] EN_OUT2
85h 285h [3:0] EN_OUT3
[7:4] EN_OUT4
86h 286h [3:0] EN_OUT5
[7:4] EN_OUT6
SLOT ASSIGNMENT
CODE MON_ DESCRIPTION
000 Not assigned
001 Slot 1
010 Slot 2
011 Slot 3
100 Slot 4
101 Slot 5
110 Slot 6
111 Monitoring-only state
SLOT ASSIGNMENT
CODE EN_OUT_ DESCRIPTION
0000 Not assigned
0001 Slot 1
0010 Slot 2
0011 Slot 3
0100 Slot 4
0101 Slot 5
0110 Slot 6
1101 General-purpose input
1110 General-purpose output
— All other unspecified codes are not assigned.

______________________________________________________________________________________ 15
MAX16067
6-Channel, Flash-Configurable System Manager
with Nonvolatile Fault Registers
Power-Up
On power-up, when EN is high and the software enable
bit is ‘1’, the MAX16067 begins sequencing with Slot
0. After the sequencing delay for Slot 0 expires, the
sequencer advances to Slot 1, and all EN_OUT_s
assigned to the slot assert. All MON_ inputs assigned to
Slot 1 are monitored and when the voltage rises above
the undervoltage (UV) fault threshold, the sequence
delay counter is started. When the sequence delay
expires, the MAX16067 proceeds to the next slot.
When the tFAULT counter expires before all MON_ inputs
assigned to the slot are above the fault UV threshold, a
fault asserts. EN_OUT_ outputs are disabled and the
MAX16067 returns to the fault state. Register r75h[4:1]
sets the tFAULT delay. See Table 7 for details.
After the voltages on all MON_ inputs assigned to the
last slot exceed the UV fault threshold and the slot delay
expires, the MAX16067 starts the reset timeout counter.
After the reset timeout, RESET deasserts. See Table 22
for more information on setting the reset timeout.
Power-Down
Power-down starts when EN is pulled low or the software
enable bit is set to ‘0.’ Power down EN_OUT_s simul-
taneously or in reverse sequence mode by setting the
reverse sequence bit (r75h[0]) appropriately. Set r75h[0]
to ‘1’ to power down in reverse sequence.
Reverse Sequence Mode
When the MAX16067 is fully powered up and EN is
pulled low or the software enable bit is set to ‘0’, the
EN_OUT_s assigned to Slot 6 deassert, the MAX16067
waits for the Slot 6 sequence delay and then proceeds to
the previous slot (Slot 5), and so on until the EN_OUT_s
assigned to Slot 1 turn off. When simultaneous power-
down is selected (r75h[0] is set to ‘0’), all EN_OUT_s turn
off at the same time.
Voltage Monitoring
The MAX16067 features an internal 10-bit ADC that mon-
itors the MON_ voltage inputs. An internal multiplexer
cycles through each of the enabled inputs, taking less
than 24Fs for a complete monitoring cycle. Each acquisi-
tion takes approximately 4Fs. At each multiplexer stop,
the 10-bit ADC converts the analog input to a digital
result and stores the result in a register. ADC conversion
results are stored in registers r00h–r0Bh (see Table 9).
Use the SMBus or JTAG serial interface to read ADC
conversion results.
The MAX16067 provides six inputs, MON1–MON6,
for voltage monitoring. Each input-voltage range
is programmable in registers r43h–r44h (see Table
8). When MON_ configuration registers are set to ’11,’
MON_ voltages are not monitored and the multiplexer
does not stop at these inputs, decreasing the total cycle
time. These inputs cannot be configured to trigger fault
conditions.
The two programmable thresholds for each monitored
voltage include an overvoltage and an undervoltage
threshold. See the Faults section for more information
on setting overvoltage and undervoltage thresholds. All
voltage thresholds are 8 bits wide. The 8 MSBs of the
10-bit ADC conversion result are compared to these
overvoltage and undervoltage thresholds.
For any undervoltage or overvoltage condition to be
monitored and any faults detected, the MON_ input must
be assigned to a sequence order or set to monitoring
mode as described in the Sequencing section. Inputs
that are not enabled are not converted by the ADC; they
contain the last value acquired before that channel was
disabled. The ADC conversion result registers are reset
to 00h at boot-up. These registers are not reset when a
reboot command is executed.
To temporarily disable voltage monitoring during voltage
margining conditions, set r73h[2] to ‘1’ to enable margin-
ing mode functionality. Faults, except for faults triggered
by EXTFAULT pulled low externally, are not recorded
when the device is in margining mode but the ADC
continues to run and conversion results continue to be
available. Set r73h[2] back to ‘0’ for normal functionality.
Table 7. tFAULT Delay Settings
r75h[4:1] FAULT DELAY
0000 120Fs
0001 150Fs
0010 250Fs
0011 380Fs
0100 600Fs
0101 1ms
0110 1.5ms
0111 2.5ms
1000 4ms
1001 6ms
1010 10ms
1011 15ms
1100 25ms
1101 40ms
1110 60ms
1111 100ms

16 _____________________________________________________________________________________
MAX16067
6-Channel, Flash-Configurable System Manager
with Nonvolatile Fault Registers
Table 8. ADC Configuration Registers
Table 9. ADC Conversion Results (Read Only)
REGISTER ADDRESS FLASH ADDRESS BIT RANGE DESCRIPTION
43h 243h
[1:0]
MON1 full-scale range
00 = 5.6V
01 = 2.8V
10 = 1.4V
11 = Channel not converted
[3:2]
MON2 full-scale range
00 = 5.6V
01 = 2.8V
10 = 1.4V
11 = Channel not converted
[5:4]
MON3 full-scale range
00 = 5.6V
01 = 2.8V
10 = 1.4V
11 = Channel not converted
[7:6]
MON4 full-scale range
00 = 5.6V
01 = 2.8V
10 = 1.4V
11 = Channel not converted
44h 244h
[1:0]
MON5 full-scale range
00 = 5.6V
01 = 2.8V
10 = 1.4V
11 = Channel not converted
[3:2]
MON6 full-scale range
00 = 5.6V
01 = 2.8V
10 = 1.4V
11 = Channel not converted
[7:4] Not used
REGISTER ADDRESS BIT RANGE DESCRIPTION
00h [7:0] MON1 result (MSB)
01h [7:6] MON1 result (LSB)
02h [7:0] MON2 result (MSB)
03h [7:6] MON2 result (LSB)
04h [7:0] MON3 result (MSB)
05h [7:6] MON3 result (LSB)
06h [7:0] MON4 result (MSB)
07h [7:6] MON4 result (LSB)
08h [7:0] MON5 result (MSB)
09h [7:6] MON5 result (LSB)
0Ah [7:0] MON6 result (MSB)
0Bh [7:6] MON6 result (LSB)

______________________________________________________________________________________ 17
MAX16067
6-Channel, Flash-Configurable System Manager
with Nonvolatile Fault Registers
General-Purpose Inputs/Outputs
GPIO1–GPIO6 are programmable general-purpose
inputs/outputs. GPIO1–GPIO6 are configurable as a
manual reset input, a watchdog timer input and output,
logic inputs/outputs, and fault-dependent outputs. When
programmed as outputs, GPIOs are open-drain or push-
pull. See Tables 10 and 11 for more detailed information
on configuring GPIO1–GPIO6.
When GPIO1–GPIO6 are configured as general-purpose
inputs/outputs, read values from the GPIO ports through
r1Eh and write values to GPIOs through r3Eh. Note that
r3Eh has a corresponding flash register, which pro-
grams the default state of a general purpose output. See
Table 12 for more information on reading and writing to
the GPIO.
Table 10. GPIO_ Configuration Registers
Table 11. GPIO_ Function Configuration Bits
Table 12. GPIO_ State Registers
REGISTER ADDRESS FLASH ADDRESS BIT RANGE DESCRIPTION
3Fh 23Fh
[1:0] GPIO1 configuration
[3:2] GPIO2 configuration
[5:4] GPIO3 configuration
[7:6] GPIO4 configuration
40h 240h
[1:0] GPIO5 configuration
[3:2] GPIO6 configuration
[4] ARAEN bit
[7:5] Not used
GPIO1 GPIO2 GPIO3 GPIO4 GPIO5 GPIO6
00 Logic input Logic input Logic input Logic input Logic input Logic input
01 Logic output
(push-pull)
Logic output
(push-pull)
Logic output
(push-pull)
Logic output
(push-pull)
Logic output
(push-pull)
Logic output
(push-pull)
10 Logic output
(open drain)
Logic output
(open drain)
Logic output
(open drain)
Logic output
(open drain)
Logic output
(open drain)
Logic output
(open drain)
11 ALERT (open drain) FAULT (open drain) MR input WDI WDO
(open drain)
EXTFAULT
(open drain)
REGISTER
ADDRESS
FLASH
ADDRESS BIT RANGE DESCRIPTION
1Eh —
[0] GPIO1 input state
[1] GPIO2 input state
[2] GPIO3 input state
[3] GPIO4 input state
[4] GPIO5 input state
[5] GPIO6 input state
[7:6] Not used
3Eh 23Eh
[0] GPIO1 output state
[1] GPIO2 output state
[2] GPIO3 output state
[3] GPIO4 output state
[4] GPIO5 output state
[5] GPIO6 output state
[7:6] Not used

18 _____________________________________________________________________________________
MAX16067
6-Channel, Flash-Configurable System Manager
with Nonvolatile Fault Registers
ALERT
GPIO1 is configurable as the SMBus alert signal, ALERT.
ALERT asserts when any fault condition occurs. When the
SMBus host sends the ARA (Alert Response Address),
the MAX16067 responds with its slave address and
deasserts ALERT. ALERT is an open-drain output.
Set the ARAEN bit in r40h[4] to ‘1’ to disable the ARA
feature. Under these conditions, the device does not
respond to an ARA on the SMBus line.
FAULT
GPIO2 is configurable as a dedicated fault output,
FAULT. FAULT asserts when an overvoltage or under-
voltage condition occurs on the selected inputs. FAULT
dependencies are set using registers r36h and r37h
(see Table 13). When FAULT depends on more than one
MON_, the fault output asserts when one or more MON_
exceeds a programmed threshold voltage. FAULT acts
independently of the critical fault system, described in
the Critical Faults section. Use r37h[7] to set the polarity
of FAULT.
Manual Reset (MR)
GPIO3 is configurable to act as an active-low manual reset
input, MR. Drive MR low to assert RESET. RESET remains
asserted for the selected reset timeout period after MR
transitions from low to high. When connecting MR to a push-
button, use a pullup resistor. See the Reset Output section
for more information on selecting a reset timeout period.
Watchdog Input (WDI) and Output (WDO)
GPIO4 and GPIO5 are configurable as the watchdog
timer input (WDI) and output, WDO, respectively. See
Table 23 for configuration details. WDO is an open-drain,
active-low output. See the Watchdog Timer section for
more information about the operation of the watchdog
timer.
External Fault (EXTFAULT)
GPIO6 is configurable as the external fault input/output,
EXTFAULT. EXTFAULT asserts if any monitored volt-
age exceeds an overvoltage or undervoltage threshold.
EXTFAULT also asserts if a power-up or power-down
sequencing fault occurs. This signal can be used to
cascade multiple MAX16067s.
Pull EXTFAULT low externally to force the sequencer to
enter a fault state. Under these conditions, all outputs
deassert.
Two configuration bits determine the behavior of the
MAX16067 when EXTFAULT is pulled low by an exter-
nal device. Register bit r72h[5], if set to a ‘1’, causes
the sequencer state machine to enter the fault state,
deasserting all the outputs when EXTFAULT is pulled
low. When this happens, the flag bit r1Ch[6] is set to
indicate the cause of the fault. If register bit r6Dh[2] is
set in addition to r72h[5], EXTFAULT going low triggers
a nonvolatile fault log operation.
Table 13. FAULT Dependencies
REGISTER
ADDRESS
FLASH
ADDRESS BIT RANGE DESCRIPTION
36h 236h
[0] FAULT depends on MON1 undervoltage threshold
[1] FAULT depends on MON2 undervoltage threshold
[2] FAULT depends on MON3 undervoltage threshold
[3] FAULT depends on MON4 undervoltage threshold
[4] FAULT depends on MON5 undervoltage threshold
[5] FAULT depends on MON6 undervoltage threshold
[7:6] Not used
37h 237h
[0] FAULT depends on MON1 overvoltage threshold
[1] FAULT depends on MON2 overvoltage threshold
[2] FAULT depends on MON3 overvoltage threshold
[3] FAULT depends on MON4 overvoltage threshold
[4] FAULT depends on MON5 overvoltage threshold
[5] FAULT depends on MON6 overvoltage threshold
[6] Not used
[7] 0 = FAULT is an active-low digital output
1 = FAULT is an active-high digital output

______________________________________________________________________________________ 19
MAX16067
6-Channel, Flash-Configurable System Manager
with Nonvolatile Fault Registers
Table 14. Fault Threshold Registers
Faults
The MAX16067 monitors the input (MON_) channels and
compares the results with an overvoltage threshold and
an undervoltage threshold. Based on these conditions,
the MAX16067 asserts various fault outputs and save
specific information about the channel conditions and
voltages into the nonvolatile flash. Once a critical fault
event occurs, the failing channel condition, ADC conver-
sions at the time of the fault, or both can be saved by
configuring the event logger. The event logger records
a single failure in the internal flash and sets a lock bit
which protects the stored fault data from accidental era-
sure on a subsequent power-up.
The MAX16067 is capable of measuring overvoltage
and undervoltage fault events. Fault conditions are
detected at the end of each ADC conversion. An over-
voltage event occurs when the voltage at a monitored
input exceeds the overvoltage threshold for that input.
An undervoltage event occurs when the voltage at a
monitored input falls below the undervoltage threshold.
Fault thresholds are set in registers r49h–r59h as shown
in Table 14. Disabled inputs are not monitored for fault
conditions and are skipped over by the input multiplexer.
Only the upper 8 bits of a conversion result are com-
pared with the programmed fault thresholds.
REGISTER
ADDRESS
FLASH
ADDRESS BIT RANGE DESCRIPTION
48h 248h [7:0] Not used
49h 249h [7:0] MON1 overvoltage threshold
4Ah 24Ah [7:0] MON1 undervoltage threshold
4Bh 24Bh [7:0] Not used
4Ch 24Ch [7:0] MON2 overvoltage threshold
4Dh 24Dh [7:0] MON2 undervoltage threshold
4Eh 24Eh [7:0] Not used
4Fh 24Fh [7:0] MON3 overvoltage threshold
50h 250h [7:0] MON3 undervoltage threshold
51h 251h [7:0] Not used
52h 252h [7:0] MON4 overvoltage threshold
53h 253h [7:0] MON4 undervoltage threshold
54h 254h [7:0] Not used
55h 255h [7:0] MON5 overvoltage threshold
56h 256h [7:0] MON5 undervoltage threshold
57h 257h [7:0] Not used
58h 258h [7:0] MON6 overvoltage threshold
59h 259h [7:0] MON6 undervoltage threshold

20 _____________________________________________________________________________________
MAX16067
6-Channel, Flash-Configurable System Manager
with Nonvolatile Fault Registers
Deglitch
Fault conditions are detected at the end of each conver-
sion. When the voltage on an input falls outside a moni-
tored threshold for one acquisition, the input multiplexer
remains on that channel and performs several succes-
sive conversions. To trigger a fault, the input must stay
outside the threshold for a certain number of acquisitions
as determined by the deglitch setting in r74h[6:5] (see
Table 15).
Fault Flags
Fault flags indicate the fault status of a particular input.
The fault flag of any monitored input in the device can be
read at any time from registers r1Bh and r1Ch, as shown
in Table 16. Clear a fault flag by writing a ‘1’ to the appro-
priate bit in the flag register. Unlike the fault signals sent
to the fault outputs, these bits are masked by the critical
fault enable bits (see Table 17). The fault flag is only set
when the matching enable bit in the critical fault enable
register is also set.
If GPIO6 is configured as the EXTFAULT input/output
and EXTFAULT is pulled low by an external circuit, bit
r1Ch[6] is set.
The SMB Alert (ALERT) bit is set if the MAX16067 has
asserted the SMBus Alert output. Clear by writing a ‘1’.
See the SMBALERT (ALERT)section for more details.
Table 15. Deglitch Configuration
Table 16. Fault Flags
REGISTER
ADDRESS
FLASH
ADDRESS BIT RANGE DESCRIPTION
74h 274h [6:5]
Voltage comparator deglitch configuration
00 = 2 cycles
01 = 4 cycles
10 = 8 cycles
11 = 16 cycles
REGISTER
ADDRESS BIT RANGE DESCRIPTION
1Bh
[0] MON1 undervoltage threshold
[1] MON2 undervoltage threshold
[2] MON3 undervoltage threshold
[3] MON4 undervoltage threshold
[4] MON5 undervoltage threshold
[5] MON6 undervoltage threshold
[7:6] Reserved
1Ch
[0] MON1 overvoltage threshold
[1] MON2 overvoltage threshold
[2] MON3 overvoltage threshold
[3] MON4 overvoltage threshold
[4] MON5 overvoltage threshold
[5] MON6 overvoltage threshold
[6] External fault (EXTFAULT)
[7] SMB alert
This manual suits for next models
2
Table of contents
Other Maxim Measuring Instrument manuals
Popular Measuring Instrument manuals by other brands
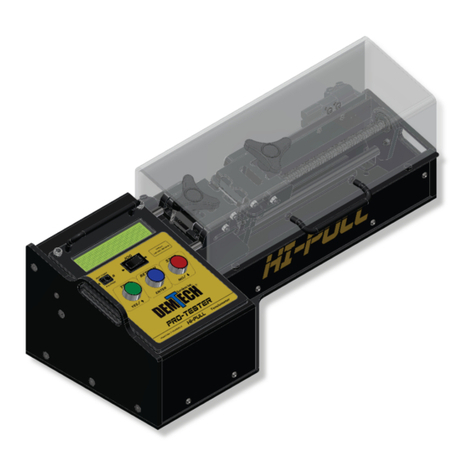
Demtech
Demtech Pro-Tester Hi-Pull Operator's manual
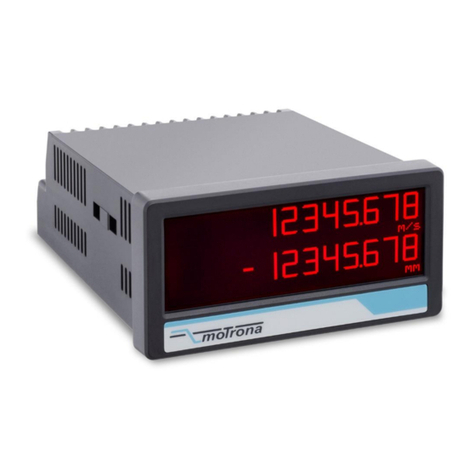
Motrona
Motrona touchMATRIX MX350 operating manual
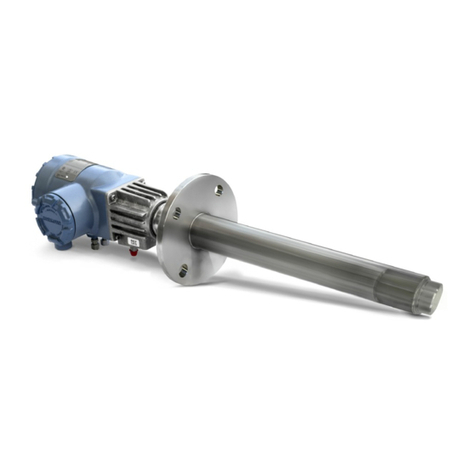
Emerson
Emerson Rosemount 6888C quick start guide

Electro Industries/GaugeTech
Electro Industries/GaugeTech Nexus 1262 quick start guide

NIVELCO
NIVELCO NIVOCONT user manual

ColorLite
ColorLite Rugged 2 user manual