Maxton UC1A User manual

1728 Orbit Way - Minden, Nevada 89423 P: 775-782-1700 F: 775-782-1701 [email protected]om www.maxtonvalve.com
1
\\SERVER\CATALOG2019\2019CatalogRev2
- Table of Contents
- Terms and Conditions
- Job Specification Sheet
- Application Flow Chart
- Application Flow Chart (Down Speed Regulated Valves)
- UC1A, UC2AB44 Hydraulic Controllers
- Exterior Dimensions UC1AB44
- Exterior Dimensions UC2AB44
- Adjustment Procedure UC1, UC1A, UC2, UC2A (B44)
- Exploded View UC1AB44
- Exploded View Parts List UC1AB44
- Exploded View UC2AB44
UC1A, UC2AB44…………………………………………………………..…………………..…..…..13 – 34
ENGINEERING DATA…………………………………………………………………………….…. 1 – 12
- Exploded View Parts List UC2AB44
- Seal Ring Locations UC1, UC1A, UC2, UC2A (B44)
- Operating Sequence UC1, UC1A, UC2, UC2A (B44)
- Hydraulic Schematic UC1AB44
- Hydraulic Schematic UC2AB44
- Trouble Shooting Procedures UC1, UC1A, UC2, UC2A (B44)
- Static Pressure Table
- Rated Flow Table
- Static Pressure Table (Metric)
- Rated Flow Table (Metric)
- Single Action Cylinder Displacement
- EMV10B44 Hydraulic Controller
- EMV10B44 Specifications
- Operating Sequence
- Hydraulic Schematic UC4, UC4MB44
- UC4MRB44 Hydraulic Controller
- Adjustment Procedure UC4MRB44
- Exploded View UC4MRB44
- Exploded View Parts List UC4MRB44
- Hydraulic Schematic UC4MRB44
- Trouble Shooting Procedures UC4, UC4M, UC4MR (B44),
- UC4, UC4MB44 Hydraulic Controllers
- Exterior Dimensions UC4, UC4M, UC4MR (B44)
- Guide Configurations UC4, UC4M, UC4MR (B44)
- Adjustment Procedure UC4, UC4M, B44)
- Dual Valve Adjustment Procedure
- Exploded View UC4, UC4MB44
- Exploded View Parts List UC4, UC4MB44
- Seal Ring Locations UC4, UC4M, UC4MR (B44)
UC4, UC4M, UC4MRB44……...…………………………………..…………………………………. 35 – 64
EMV10………………………………………………………...…………………………..……..……... 65 – 68
- PSNO-2 (Low Pressure Switch)
- Isolation Coupling
- TDF (Tank Discharge Filter)
- Adapters (Thread to Grooved, 2" to 3/4" )
- Quick Disconnect (Two Way Shut Off)
- MaxGlide (Oil Additive)
MAINTENANCE………………………..………………………………………………………..……… 77– 88
- Seal Kits
- Solenoid, Solenoid Seat and Ball Cage Kits
- Solenoid Kits UC1A/2A, UC4/4M/4MR
- Seal Rings
- Valve Exchange Program (VEP)
- Pump Flange Replacement
- Coil Specifications
- Coil Exterior Dimensions
- Seal Kit and Safe Use Recommendations
- OSV Safety Valve (Pipe Rupture) & Shut Off Valve
- OSV Adjustment Procedure
- OSV Tripping Flow Table
- OSV Tripping Speed Chart
- DUAL OSV Adjustment Procedures
- OSV25 Safety Valve (Pipe Rupture)
- OSV25 Adjustment Procedure
OSV…………….………………………………………………………………………………..…….... 69 – 76
SUPPORT PRODUCTS………………………………………………………………………………. 89 – 102
- Shut Off Ball Valves
- Bleed Port
- Interlock Hydraulic Valve
- SafeTach2
- Water Valve / Explosion Proof Coil Cover
- TA4M (Field Training Unit)
Certifications
Maxton is ISO 9001:2015 certified and all main line products are
CSAB44 and/or UL Listed.
Copyright 2019 Maxton Manufacturing Company All Rights Reserved
TABLE OF CONTENTS
- RV100 Conversion Kit

1728 Orbit Way - Minden, Nevada 89423 P: 775-782-1700 F: 775-782-1701 [email protected]om www.maxtonvalve.com
2
\\SERVER\CATALOG2019\2019CatalogRev2
FORWARD: The products and information contained herein have been developed by MAXTON
MANUFACTURING COMPANY. They are subject to change. The information is intended for use by
professionals trained in the manufacture, installation and maintenance of hydraulic elevator systems. While the
information is deemed reliable, MAXTON disclaims any liability arising from misinterpretation.
LIMITED WARRANTY: All control and safety valves sold by MAXTON are warranted only to purchasers for
resale or for use in business or original equipment manufacture, against defects in workmanship or materials,
under normal use, for two (2) years from date of purchase. Any part, which is determined by MAXTON to be
defective in material or workmanship and returned to MAXTON, shipping costs prepaid, as exclusive remedy,
will be repaired or replaced at MAXTON'S option. This warranty cannot be transferred or assigned to third
parties. All warranties are considered null and void upon transfer unless the intent to transfer to a third party is
expressly indicated in a purchase order or the customer is a known OEM and a user of MAXTON'S products.
Any alteration or removal of designated serial numbers will cause the warranty to be immediately null and void.
WARRANTY DISCLAIMER: MAXTON has made diligent effort to provide illustrations, descriptions and
technical information for the proper use of its products. In addition MAXTON provides on-line and phone
technical support for the use of our various products. Nevertheless, there are no warranties given except such
expressed warranties offered in connection with the sale of a particular product as stated in the Limited
Warranty above. THERE ARE NO EXPRESS OR IMPLIED WARRANTIES OF MERCHANTABILITY OR OF
FITNESS FOR A PARTICULAR PURPOSE GIVEN IN CONNECTION WITH THE SALE OF ANY GOODS. In
no event shall MAXTON MANUFACTURING COMPANY be liable for consequential, incidental, or special
damages. The sole and exclusive remedy, and the limit of MAXTON'S liability for any loss whatsoever, shall
not exceed the price paid by the purchaser for the product to which the claim is made.
PRODUCT SUITABILITY: Many states and localities have codes and regulations governing sales,
construction, installation and/or use of products, which may vary from those in neighboring areas. While
MAXTON attempts to assure that its products comply with such codes, it cannot guarantee compliance, and
cannot be responsible for how the product is installed or used. Before purchase and use of a product, review
the application, and national and local codes and regulations to be sure that the product, installation and use
comply with them.
RETURN/REPAIR INQUIRIES: All in and out-of-warranty repair inquiries are to be directed to the MAXTON
Sales Department. Before returning a product, contact the Sales Department to obtain a return authorization
number (RA #). The designated RA # should then be marked on the outside of the package. To avoid
processing delays, be sure to include the following: Purchase order number and RA #, returnee's name,
address and phone number, the model number and serial number, repair instructions and description of
problem. All pipes, coils and covers must be removed prior to shipping. MAXTON will not be responsible for
lost or damaged pipes, coils or covers. Pipes requiring removal by MAXTON are subject to additional charges.
A valve returned with missing components, including flanges, is subject to replacement charges. All products
must be returned freight prepaid. Brokerage fees, taxes and duties, when applicable, must be paid by
returnee. New product returned for credit is subject to a 15% restocking fee, plus the original freight charge.
MODIFICATION AND/OR UNAUTHORIZED REPAIRS: In the event of modification and/or repair of a
MAXTON product by an unauthorized repair facility, you will indemnify us and hold us harmless from any
liability or damage whatsoever arising out of the subsequent use of the product. Use of an unauthorized repair
facility voids all warranty claims.
PRODUCT PRICING: Product prices are subject to change without notice.
TERMS AND CONDITIONS

1728 Orbit Way - Minden, Nevada 89423 P: 775-782-1700 F: 775-782-1701 [email protected]om www.maxtonvalve.com
3
\\SERVER\CATALOG2019\2019CatalogRev2
In order to properly size and quote a valve(s) for your job, please complete all REQUIRED fields:
*Required fields
* Is this for an order? * Is this for pricing only?
* 1) Piston diameter(s):________ Single____ Dual ____ Telescopic 2 or 3 stage
* 2) Speed of the car (F.P.M.):________ * Capacity of the car: ________
* 3) No load pressure; “B” port reading static: (no load) _________ * or empty car weight:____________
* 4) Is elevator roped 1:2: Yes No * Does this job require down speed regulation: ___________
* 5) Do you require an OSV (pipe rupture or seismic safety valve) for this installation? _______________
* 6) Quantity of valves required for job: __________ If more than 1 is this for Separate Elevators.
Tandem/Dual Pump Units.
*7) If replacing a Maxton valve the serial number is:___________________________________
We Also Carry:
MAXGLIDE OIL ADDITIVE (Eliminates stick slip / chatter)
ISOLATION COUPLINGS (2”, 2.5”, 3” Grooved, 2” NPT)
TDF (Tank discharge filtration system)
SHUT OFF BALL VALVES (2”, 2.5” Grooved or NPT, 3” Grooved)
Remember: You can order on-line or size valves on our website @ www.maxtonvalve.com
24 hrs. a day, 7 days a week! For assistance contact Sales at (775) 782-1700
Name:_____________________________________________________ Phone #:__________________________________
Company Name:_____________________________________________ Fax #:____________________________________
Bill To City Address:____________________________________________________________________________________
Shipping Address:______________________________________________________________________________________
PO# or Credit Card # Name on Credit Card:________________________________
Shipping Instructions: Credit Card Expiration Date
(UPS ground service can take up to 6 business days depending on your location)
* Coil voltage on valve: □ 115VAC (RED) □ 230VAC (GREEN) □ 115VDC (BLACK)
* COMPLETE FOR UC4/ UC4M /UC4MR:
- Facing the adjustments, jack is to the:
□ Left □ Right
- Type of flanges: Pump Jack Tank
2” NPT (Thd)
2” Grooved
LowPressureSwitchYesNo(CIRCLEONE)
QuickDisconnectCoupling(1/8”NPT)YesNo
QuickDisconnectNipples(1/8”NPT)YesNo
* COMPLETE FOR UC1/UC1A/UC2/UC2A:
-The bottom port is the (circle one): PUMP / TANK Flanges:
Flanges: 2” 2.5” 3” 2” 2.5”
Grooved Grooved Grooved NPT NPT
Pump:
Jack:
Tank:
LowPressureSwitchYesNo(CIRCLEONE)
QuickDisconnectCoupling(1/8”NPT)YesNo
QuickDisconnectNipples(1/8”NPT)YesNo
+
++
+ Not recommended on UC2A
++ Not recommended on UC2
JOB SPECIFICATION SHEET
Certifications
Maxton is ISO 9001:2015 certified and
all main line products are CSAB44 and/or UL Listed.
SAFETACH2 ELEVATOR PERFORMANCE METER
Call for more information

This page intentionally left blank

1728 Orbit Way - Minden, Nevada 89423 P: 775-782-1700 F: 775-782-1701 [email protected]om www.maxtonvalve.com
5
\\SERVER\CATALOG2019\2019CatalogRev2
UC4, UC4M, UC1, UC1AB44
APPLICATION FLOW CHART
MAXIMUM OPERATING PRESSURES
UC1 / 1A SERIES VALVES: 600 P.S.I. UC4 / UC4M SERIES VALVES: 800 P.S.I.

1728 Orbit Way - Minden, Nevada 89423 P: 775-782-1700 F: 775-782-1701 [email protected]om www.maxtonvalve.com
6
\\SERVER\CATALOG2019\2019CatalogRev2
Down Speed Regulated Valves
MAXIMUM OPERATING PRESSURES
UC4MR SERIES VALVES: 800 P.S.I.
UC2/UC2A SERIES VALVES: 600 P.S.I. EMV10 SERIES VALVE: 1000 P.S.I.
APPLICATION FLOW CHART

1728 Orbit Way - Minden, Nevada 89423 P: 775-782-1700 F: 775-782-1701 [email protected]om www.maxtonvalve.com
7
\\SERVER\CATALOG2019\2019CatalogRev2
STATIC PRESSURE TABLE
POUNDS PER SQUARE INCH BASED ON NET LOAD (POUNDS)
DIRECT ACTING APPLICATIONS
NET JACK PISTON DIAMETER (INCHES)
22 1/22 3/433 1/244 3/84 1/255 7/165 1/266 1/277 1/288 1/29 1/210 5/812 5/8
100031820416814110480676351434235302623201814118
150047730625321215611910094766563534539343026211712
20006374073372832081591331261028684716052454035282316
2500796509421354260199166157127108105887565575044352820
30009556115054243122392001891531291261069078686053423424
E 3500 71358949536427923322017815114712410591797062493928
M4000 815673566416318266252204172168141121104918070564532
P4500 9177586374683582992832291941891591361171029079635136
T5000 8427075203983333142552152101771511301139988715640
Y5500 92677857243836634628023723119516614312410997786244
6000 849624477399377306258253212181156136119106856848
W6500 920676517432409331280274230196169147129115927352
E7000 990728557466440357301295248211182158139123997956
I7500 7805974994723823233162652261951701491321068560
G8000 8326375325034073453372832412081811591411139064
H8500 8836765655344333663583012562211921691501209668
T9000 93571659956645838837931827123420417915912710272
9500 98775663259748440940033628624721518916713410776
L10000 79666562950943142135430126022619917614111380
B12000 95579875561151750542436231227223921116913596
S14000 931880713603589495422364317279247198158112
16000 815689673566482416362318282226180128
18000 917775758637542468407358317254203144
20000 861842707603520453398352282226160
25000 884753650566497441353282200
30000 904780679597529423338240
ADD PER
100 lbs.
31.820.416.814.110.47.966.656.295.094.314.213.543.012.602.261.991.761.411.130.80
STATIC PRESSURE (P.S.I.)
ENGINEERING DATA

1728 Orbit Way - Minden, Nevada 89423 P: 775-782-1700 F: 775-782-1701 [email protected]om www.maxtonvalve.com
8
\\SERVER\CATALOG2019\2019CatalogRev2
RATED FLOW TABLE
GALLONS PER MINUTE BASED ON CAR SPEED (FEET PER MINUTE)
DIRECT ACTING APPLICATIONS
JACK PISTON DIAMETER (INCHES)
22 1/22 3/433 1/244 3/84 1/255 7/165 1/266 1/2771/288 1/29 1/210 5/812 5/8
10.160.260.310.370.500.650.780.831.021.211.231.471.722.002.302.612.953.684.616.50
50.821.281.541.842.503.263.904.135.106.036.177.348.6210111315182333
101.632.553.093.675.006.537.818.26101212151720232629374665
203.265.106.177.34101316172024252934404652597492130
304.907.659.261115202325313637445260697888110138195
C 406.531012152026313341484959698092104118147184260
A508.16131518253339415160627386100115131147184230325
R609.791519223039475061727488103120138157177221276390
701118222635465558718486103121140161183206258322455
S801320252940526266829799118138160184209236295368520
P90152328334559707492109111132155180207235265331415585
E1001626313750657883102121123147172200230261295368461650
E1101828344055728691112133136162190220252287324405507715
D1202031374460789499122145148176207240275313354442553780
12520323946628298103128151154184215250287326368460576813
F130213340486585102107133157160191224260298339383479599845
P140233643517091109116143169173206241280321366413516645910
M150243846557598117124153181185220259300344392442552691975
16026414959801041251321631931972352763203674184725897371,040
17028435262851111331401732052102502933403904445016267831,106
18029465666901181411491842172222643103604134705316638291,171
19031485970951241481571942292342793283804364965607008751,236
200335162731001311561652042412472943454004595225907369211,301
Flow (GPM)
ENGINEERING DATA

1728 Orbit Way - Minden, Nevada 89423 P: 775-782-1700 F: 775-782-1701 [email protected]om www.maxtonvalve.com
9
\\SERVER\CATALOG2019\2019CatalogRev2
STATIC PRESSURE TABLE
PRESSURE IN BARS BASED ON NET LOAD (KILOGRAMS)
DIRECT ACTING APPLICATIONS
NET JACK PISTON DIAMETER (mm)
E
M
P
T
Y
W
E
I
G
H
T
(kg)
60708090100110120125140150160180200210
1003.48
2006.975.123.92
30010.457.685.884.653.76
40013.9410.247.846.195.024.153.48
50017.4212.809.807.746.275.184.364.01
100034.8525.6019.6015.4912.5410.378.718.036.405.584.903.87
1500 38.4029.4023.2318.8215.5513.0712.049.608.367.355.814.704.27
2000 39.2030.9725.0920.7317.4216.0612.8011.159.807.746.275.69
2500 38.7231.3625.9221.7820.0716.0013.9412.259.687.847.11
3000 46.4637.6331.1026.1324.0819.2016.7314.7011.629.418.53
3500 43.9036.2930.4928.1022.4019.5117.1513.5510.989.96
4000 41.4734.8532.1125.6022.3019.6015.4912.5411.38
4500 46.6539.2036.1328.8025.0922.0517.4214.1112.80
5000 43.5640.1432.0027.8824.5019.3615.6814.22
5500 47.9144.1635.2030.6626.9521.2917.2515.64
6000 48.1738.4033.4529.4023.2318.8217.07
6500 41.6036.2431.8525.1720.3818.49
7000 44.8039.0334.3027.1021.9519.90
7500 48.0041.8136.7529.0423.5221.33
8000 44.6039.2030.9725.0922.76
8500 47.3941.6532.9126.6624.18
9000 44.1034.8528.2225.60
9500 46.5536.7829.7927.02
10000 38.7231.3628.45
15000 47.0442.67
STATIC PRESSURE (bars)
ENGINEERING DATA

1728 Orbit Way - Minden, Nevada 89423 P: 775-782-1700 F: 775-782-1701 [email protected]om www.maxtonvalve.com
10
\\SERVER\CATALOG2019\2019CatalogRev2
RATED FLOW TABLE ( METRIC )
LITERS PER MINUTE BASED ON CAR SPEED (METERS PER MINUTE)
DIRECT ACTING APPLICATIONS
JACK PISTON DIAMETER (mm)
60708090100110120125140150160180200210
C 12.833.855.036.367.859.5011.312.315.417.720.125.431.434.6
A25.657.7010.112.715.719.022.624.530.835.340.250.962.869.3
R38.4811.515.119.123.628.533.936.846.253.060.376.394.2104
411.315.420.125.431.438.045.249.161.670.780.4102126139
S514.119.225.131.839.347.556.561.477.088.4101127157173
P1028.338.550.363.678.595.0113123154177201254314346
E1542.457.775.495.4118143170184231265302382471520
E2056.577.0101127157190226245308353402509628693
D2570.796.2126159196238283307385442503636785866
METERS 3084.81151511912362853393684625306037639421039
PER 3599.013517622327533339643053961970489111001212
MINUTE 4011315420125431438045249161670780410181257
451271732262863534285095526937959051145
5014119225131839347556561477088410051272
551562122763504325236226758479721106
6017023130238247157067973692410601206
FLOW (LITERS PER MINUTE)
ENGINEERING DATA

1728 Orbit Way - Minden, Nevada 89423 P: 775-782-1700 F: 775-782-1701 [email protected]om www.maxtonvalve.com
11
\\SERVER\CATALOG2019\2019CatalogRev2
SINGLE ACTION CYLINDER DISPLACEMENT
PISTON DIAMETER
Inches Millimeters
PISTON AREA
in² cm²DISPLACEMENT
Gallons per foot Liters per meter
250.803.14220.2680.1632.024
2-1/457.153.97625.6520.2062.558
2-1/263.504.90931.6690.2553.167
2-3/469.855.94038.3200.3093.837
376.207.06945.6040.3674.558
3-1/482.558.29653.5210.4315.353
3-1/288.909.62162.0720.4996.197
3-3/492.2511.04566.8380.5747.129
3-7/898.4311.79376.0930.6137.613
4101.6012.56681.0730.6538.110
4-1/4107.9514.18691.5240.7379.153
4-3/8111.1315.03396.9960.7819.699
4-1/2114.3015.904102.6080.82610.258
4-3/4120.6517.721114.3260.92011.425
5127.0019.635126.6771.02012.667
5-1/4133.3521.648139.6611.12413.959
5-7/16138.1123.221149.8101.20614.977
5-1/2139.7023.758153.2791.23415.325
5-3/4146.0525.967167.5301.34916.753
6152.4028.274182.4151.46918.244
6-1/4158.7530.590197.9331.59319.783
6-1/2165.1033.183214.0841.79622.305
6-3/4171.4535.785230.8691.85823.075
7177.8038.485248.2871.99924.826
7-1/2190.5044.179285.0232.29528.502
7-3/4196.8547.173304.3412.45030.427
8203.2050.266324.2932.61132.426
8-1/2215.9056.745366.0962.94736.599
8-3/4222.2560.132387.9483.12338.785
9228.6063.617410.4333.30541.045
9-1/2241.3070.882457.3043.68145.714
9-3/4247.6574.652481.6893.87848.161
10254.0078.540506.7074.09050.794
10-1/4260.3582.516532.3604.29653.352
10-1/2266.7086.590558.6454.50055.886
10-5/8269.8888.664572.0464.60557.190
10-3/4273.0590.782585.5644.71658.568
11279.4095.033613.1164.93761.313
11-1/4285.7599.402641.3025.16064.082
11-1/2292.10103.869670.1215.39567.001
11-3/4298.45108.434699.5735.63669.993
12304.80113.098729.6595.87572.962
12-1/4311.15117.859760.3786.10875.855
12-1/2317.50122.718791.7306.37279.134
12-5/8320.68125.185807.6696.50380.761
Note: Gallons per minute = displacement (gpf) X car speed (fpm).
Liters per minute = displacement (lpm) X car speed (mpm).
ENGINEERING DATA

This page intentionally left blank

1728 Orbit Way - Minden, Nevada 89423 P: 775-782-1700 F: 775-782-1701 [email protected]om www.maxtonvalve.com
13
\\SERVER\CATALOG2019\2019CatalogRev2
JACK
TANK
PUMP
Front View
TANK
PUMP
JACK
UC1A B44 UC2A B44
Specifications Standard Features
*Maximum Flow** 360 gpm (1363 I/min)
Operating Pressure
Minimum 50 psi (3.4 bar)
Maximum 600 psi (41.5 bar)
Note:
Consult factory when applications exceed pressure ratio
over 2.5 to 1, example (Max. / Min. :280 / 100 )
Line Connections
Jack Port (flange) 2, 2 ½” NPT or Grooved
Tank Port (flange) 2, 2 ½” NPT or Grooved
Pump Port (flange) 2, 2 ½” NPT or Grooved
Gauge Ports Pump Pressure: “A” Port (1/8” NPT)
System pressure: “B” Port (1/8” NPT)
Pressure Switch: “S” Port (1/8” NPT)
Operating Temperature 80° – 150° F (26° – 65° C)
Oil Type Hyd. ISO VG 32
150 SUS @ 100° F (38° C)
Solenoid Coils Encapsulated CSA / UL Listed
Overall Dimensions
Width 13 inches (330mm) Height 12 3/8 inches (314mm)
Depth 11 1/4 inches (286mm) Weight UC1A 47 lbs, UC2A 50 lbs.
*Refer to flow Charts (pg.5 & 6)
** To insure proper valve selection please return a completed copy of our Job Specification Sheet (pg. 3) to Maxton.
HYDRAULIC CONTROLLERS, UC1A, UC2A B44
Unit body construction.
Steel sleeve inserts in valve body.
Grooved or threaded line connections.
Feedback control for stall free operation.
Individualized adjustments.
Integrated relief valve.
High efficiency solenoids.
115 VAC / 24 VDC solenoid coils.
Factory tested prior to shipping.
2 year limited warranty.
Additional Standard Features
UC2AB44
Regulated Down Speed Control.
Optional Features
Explosion Proof Coil Cover
3” Grooved Flanges
Low Pressure Switch
1/8” or 1/4” Ball Valves
Quick Disconnect Coupling or Nipple Kit
Solenoid Coils
12 VDC – 120 VAC Dual Voltage Coils
12 VDC Coils
230 VAC Coils
115 VDC Coils
185 VAC Coils
UA US UL
UT

This page intentionally left blank

1728 Orbit Way - Minden, Nevada 89423 P: 775-782-1700 F: 775-782-1701 [email protected]om www.maxtonvalve.com
15
\\SERVER\CATALOG2019\2019CatalogRev2
TANK
JACK
3 1/8"
(79mm) 4 3/4"
(121mm)
8"
(203mm)
11 1/4"
(286mm)
3 1/2"
(89mm)
4 1/2"
(114mm)
Top View
JACK
TANK
12 3/8"
(314mm)
5 3/8"
(137mm)
PUMP
1 29/32"
(48mm)
4 3/4"
(121mm)
7 7/8"
(200mm)
13"
(330mm)
Front View
+
EXTERIOR DIMENSIONS UC1A
PUMP
(BELOW)

1728 Orbit Way - Minden, Nevada 89423 P: 775-782-1700 F: 775-782-1701 [email protected]om www.maxtonvalve.com
16
\\SERVER\CATALOG2019\2019CatalogRev2
EXTERIOR DIMENSIONS UC2A
Top View
TANK
JACK
11 1/4"
(286mm)
3 1/8"
(79mm) 4 3/4"
(121mm)
3 1/2"
(89mm)
4 1/2"
(114mm)
8"
(203mm)
PUMP
Front View
JACK
TANK
12 3/8"
(314mm)
13"
(330mm)
+
7 7/8"
(200mm)
4 3/4"
(121mm)
5 3/8"
(137mm)
PUMP
(BELOW)
1 29/32"
(48mm)
12 3/4"
(324mm)
UA US
UL UT

1728 Orbit Way - Minden, Nevada 89423 P: 775-782-1700 F: 775-782-1701 [email protected]om www.maxtonvalve.com
17
\\SERVER\CATALOG2019\2019CatalogRev2
THE INFORMATION PRESENTED HEREIN IS FOR USE BY SKILLED HYDRAULIC ELEVATOR PROFESSIONALS
SPECIAL CONSIDERATIONS:
Make all adjustments at minimum pressure (no load on elevator) except where noted. “IN” is ALWAYS (CW) clockwise. “OUT” is ALWAYS (CCW)
counterclockwise. THE CONTROL BLOCK ADJUSTERS HAVE SEAL NUTS, NOT LOCK NUTS. Adjust nut only to set seal friction (friction will maintain
adjustment). When adjustment procedure calls for coils to be disconnected, disconnect them electrically. Do not remove them physically. Make adjustments
with a minimum oil temperature of 80˚ F, not to exceed 100˚ F maximum. Maxton recommends the use of a 5-micron filtration system. With the presence of at
least some adverse conditions in most installations, serious consideration should be given to overhaul or replacement of a control valve on a five year cycle.
GAUGE PORTS:
Gauge ports - 1/8” NPT provided at points A, B and S.
A Port: Pump pressure (RELIEF, WORKING PRESSURE).
B Port: Jack pressure (STATIC, DOWN RUNNING).
S Port: Low pressure switch port.
Note: The minimum operating pressure at port B should be at least 50 psi
(3.4 bar) as car is moving down full speed with no load. See flow chart.
OPERATIONAL DATA:
Min. / Max. Pressure:
Max. Rated Flow:
Operating Temperature:
Optimal Temp. Range.
Oil Type:
50-600 psi (3.4-41.5 bar)
360 gpm (1363 l / min.)
80˚-150˚ F (26˚-65˚ C)
100˚-130˚ F (38˚-54˚ C)
Hyd. ISO VG 32
150 SUS @ 100˚ F (38˚ C)
* SAFETACH2 performance meter validates valve adjustment by providing direct
speed and acceleration (g-force) readouts.
Questions: Call Tech Support (775) 782-1700 (7am-4pm PST), use
Maxtonvalve.com or download Maxton Mobile Mechanic from your APP Store
ADJUSTMENT PROCEDURE UC1, UC1A, UC2, UC2A B44
DEFAULT SETTINGS
If valve is received from Maxton, only minor adjustments may be required.
CONTROL BLOCK
US
UP STOP OUT (CCW)
to stop.
(faster rate).
UL
UP LEVEL IN (CW)
to stop.
(slower speed).
UA
UP ACCELERATION IN (CW)
to stop.
(slower rate).
UT
UP TRANSITION OUT (CCW)
to stop.
(faster rate).
R
RELIEF (factory set)
APPROX 450 psi (CW increases pressure)
VALVE BODY
BPS
BY-PASS SIZING OUT (CCW)
to stop
(delays up start)
LS*
LEVEL SPEED (factory set) DOT ON LINE
(set 3-5 fpm)
DEFAULT SETTINGS
If valve is received from Maxton, only minor adjustments may be required.
CONTROL BLOCK
DT
DOWN TRANSITION OUT (CCW)
to stop.
(faster rate)
DA
DOWN ACCELERATION OUT (CCW)
to stop.
(faster rate)
DS
DOWN STOP OUT (CCW)
to stop.
(faster rate)
ML
MANUAL LOWERING IN (CW)
to stop.
VALVE BODY
D
DOWN SPEED Turn OUT (CCW) 4 threads above lock nut.
(faster speed)
DL
DOWN LEVEL Turn OUT (CCW) 2 threads above lock nut.
(faster speed)
DOWN SECTION ADJUSTMENTS (Start with car at upper landing)
7 D Register a down call to set proper down speed with down speed
adjuster D as required. Send car to upper landing.
*(Read high speed).
8 DA Start by turning DA adjuster IN (CW) to stop. Register a down call
and turn the DA adjuster slowly OUT (CCW) until the car
accelerates smoothly. Send car to upper landing.
*(Accel 0.04g-0.09g).
9 DT Register a down call and turn DT IN (CW) so that the car slows to
provide 4 to 6 inches of stabilized down leveling. Send car to upper
landing. * (Decel 0.04g-0.09g).
10 DL Disconnect D coil. Register a down call, hold D adjuster in place
and set down level speed at 6 to 9 fpm with the DL adjuster.
Tighten both D & DL lock nuts (snug tight). Reconnect D coil.
* (leveling speed 6 to 9 fpm).
11 DS Turn DS IN (CW), when necessary, for a softer stop.
MLMANUAL LOWERING: Turn ML screw OUT (CCW) to
lower car downward at leveling speed when necessary.
RRELIEF:
a. Land car in pit and install pressure gauge in A port.
b. Register an up call with a fully loaded car, making note of
Maximum operating pressure.
c. Turn UA adjuster OUT (CCW) to stop. Turn RELIEF
adjuster OUT (CCW) two turns.
d. Close the manual shut off valve to the jack.
e. Register an up call, observe pressure gauge and turn
RELIEF IN (CW) to increase pressure. Final setting should be
in accordance with local code requirement not to exceed
150% of maximum operating pressure.
f. Tighten the lock nut (snug tight).
g. Restart to check the pressure relief setting.
Seal as required.
h. Open the manual shut off valve to the jack.
i. Readjust UA for proper Up acceleration.
*(Accel 0.04g-0.09g).
1
BPS Disconnect the US coil, turn UA IN (CW), register an up call and
turn BPS IN (CW) until the car just moves. Next, turn the BPS
adjuster OUT (CCW) until it stops the movement of the car, then
OUT 1/ 2 turn more. Snug lock nut on BPS adjuster and stop pump.
Reconnect the US coil.
2
UA Register an up call (pump running, U & US coils energized, car
should not move), slowly turn UA OUT (CCW) to attain
full up speed within 24 to 36 inches. * (Accel 0.04g-0.09g).
3
UL Disconnect the U coil. Turn UL adjuster IN (CW) to stop and
register an up call to verify that the LS adjustment is set to
3 to 5 fpm. (If not, readjust LS*). Turn UL adjuster OUT (CCW) to
attain 9 to 12 fpm leveling speed. Reconnect the U coil and lower
the car to lowest landing. *(Read leveling speed).
4
UT Register an up call and turn UT IN (CW) so that the car slows to
provide 4 to 6 inches of stabilized up leveling. Repeat steps 3 and 4
as necessary. *(Decel 0.04g-0.09g).
5
US With US adjuster fully OUT (CCW), car should stop 1/4" to 3/8"
below floor. After a normal up run, turn US IN (CW) as needed to
bring car to floor level. The pump must be timed to run ½ second
after the car has reached the floor.
6 With empty car at bottom floor, disconnect U & US coils and
register a call. The car must not move. If movement occurs, check
BPS and US
LS* Dot on the LS adjuster should be referenced to the line between
F / S. When necessary, disconnect the U coil and turn the UL
adjuster IN (CW) to stop. Unlock the LS adjuster by loosening the
screw next to the symbol 1 turn. Move the LS adjuster slightly
toward S for slower or F for faster leveling speeds. Set adjustment
from 3 to 5 fpm with the LS adjuster, tighten locking screw down,
verify LS speed after tightening screw, then repeat step 3.
* (Level Speed Test 3 to 5 fpm).
ADDITIONAL ADJUSTMENT INFORMATION FOR THE
UC2 / UC2A ON THE BACK SIDE
UP SECTION ADJUSTMENTS (Start with car at lower landing)

1728 Orbit Way - Minden, Nevada 89423 P: 775-782-1700 F: 775-782-1701 [email protected]om www.maxtonvalve.com
18
\\SERVER\CATALOG2019\2019CatalogRev2
THE INFORMATION PRESENTED HEREIN IS FOR THE USE BY SKILLED HYDRAULIC ELEVATOR PROFESSIONALS
UC2 – UC2A CONTROLLERS ONLY
The UC2 – UC2A is down speed regulated to provide a constant rate of speed in the down direction, regardless of varying loads.
Speed will not vary more than five percent. To adjust UC2 – UC2A follow the same procedure used in adjusting the UC1 / UC1A
with the following exceptions.
The Balance Adjuster (BA) located on the side of the bottom closure is factory set.
Systems with operating pressure LESS than 175 psi when Systems with operating pressure MORE than
The car is traveling down empty. 175 psi when car is traveling down empty.
The DOWN SPEED REGULATOR (DSR) adjuster is located on (1) Turn DOWN SPEED REGULATOR (DSR) adjuster IN
the side of the bottom closure next to the BA adjuster. (CW) to stop then back out (CCW) two full turns.
(1) Turn DSR in (CW) to stop at the start of the down section (2) Following the Regulator adjustment procedure, adjust
the adjustment. Set the down speed 10% higher than normal, down section as instructed.
with no load on the elevator, then adjust the down direction in the
normal manner.
(2) After the down section has been adjusted completely, and the
unloaded car is operating 10% above its rated or normal speed,
turn the DSR adjuster OUT (CCW) to slow the car to its normal
operating speed.
ATTENTION: All Maxton Valves MUST be installed with the solenoids in the upright (vertical position).
Prior to 2012 the sleeve and baseplate were an integral part of coil operation.
2012 to current the C-Frame is an integral part of coil operation.
COIL OPERATING SEQUENCE
US For up travel, energize when pump starts and de-energize to stop. With US
energized and pump running, car will move up at leveling speed. For “soft stop”,
pump should run ½ second after US de-energizes.
U Energize with US coil to run up at contract speed. De-energize at slowdown
distance from floor. Slowdown distance = 2 inches for each 10 fpm of car
speed NOT to exceed 6 inches for every 25 fpm of car speed.
If necessary increase slowdown distance to achieve 4-6 inches
of stabilized up leveling.
DL Energize to move car at leveling speed. De-energize to stop.
D Energize with DL coil to run down at contract speed. De-energize at slowdown
distance from floor. Slowdown distance = 2 inches for each 10 fpm of car
speed NOT to exceed 6 inches for every 25 fpm of car speed.
If necessary increase slowdown distance to achieve 4-6 inches
of stabilized down leveling. ELECTRO-MAGNETIC COILS
U = UP COIL D = DOWN COIL
US = UP STOP COIL DL = DOWN LEVEL COIL
CAUTION: On Wye - Delta Up Start do not energize U and US Coils until motor is running on Delta.
With soft starter, energized US coil with motor up to speed signal.
ADJUSTMENT PROCEDURE UC1, UC1A, UC2, UC2A B44

1728 Orbit Way - Minden, Nevada 89423 P: 775-782-1700 F: 775-782-1701 [email protected]om www.maxtonvalve.com
19
\\SERVER\CATALOG2019\2019CatalogRev2
280470
MANUAL LOWERING
SCREW ASSY
28098A *
PISTON RING &
EXPANDER
ASSY
280520
DOWN CLOSURE
ASSY
2059A0
COIL COVER
206400
SCREW
SOLENOID COILS
28082B 115 VAC /
24VDC (RED)
with C-Frame
For Optional Coils
See Page 81
28098A *
PISTON RING &
EXPANDER ASSY
28148A
DOWN
CONTROL
BLOCK ASSY
2138A0
SCREW
215900
SCREW
FLANGE TYPE
2” Grooved 203600
2 ½ Grooved 203500
3” Grooved 2035A0
2” THD 205600
2 ½ THD 205800
206600
SCREW
280480
CHECK
CLOSURE
ASSY
235200
PIPE PLUG
2141A0
SET SCREW
213100
REGULATOR STUD
28006A
UP / DOWN
SEAT ASSY
+ 282920
SOLENOID TUBE
ASSY
+ 28292A
SOLENOID TUBE
ASSY W / STUD
28010A
CHECK
SEAT
ASSY
WARNING &
MANUAL
LOWERING
LABEL
28017B
DOWN PISTON
& GUIDE ASSY
204200
DIFFUSER
Notes:
* = ITEMS INCLUDED IN SEAL KIT #291510,
(REFER TO SEAL RING LOCATIONS SHEET UC1, UC1A, UC2, UC2AB44 FOR PART NUMBER)
+ = ITEMS INCLUDED IN SOLENOID KIT #29292A,
(UC1A SHOWN) (REFER TO THE UC2A EXPLODED VIEW FOR THE UC2A DOWN VALVE SECTION)
+ 292950
BALL CAGE
KIT
208880
C-Frame
280090
SHORT ADJ ASSY
280120
BPS CLOSURE
ASSY
28014B
BPS PISTON
& GUIDE ASSY
208900
BPS SPRING 208800
SPRING
28149A
UP BLOCK
ASSY
28006A
UP / DOWN
SEAT ASSY
216100
213000
LOCK RING
215900
SCREW
212900
SCREW
+ 29298A-2
SOLENOID
SEAT KIT
28011A
CHECK PISTON
ASSY
WHITE TEFLON
SEAL 227000
280070
ADJ. SCREW
ASSY LONG
239513
ORIFICE
239509
ORIFICE
284450
SEAL PLUG
ASSY
28030A
REGULATOR
ASSY
SPECIFICATION
LABEL
281780
COIL BRACKET
ASSY
EXPLODED VIEW UC1A B44

1728 Orbit Way - Minden, Nevada 89423 P: 775-782-1700 F: 775-782-1701 [email protected]om www.maxtonvalve.com
20
\\SERVER\CATALOG2019\2019CatalogRev2
PART # DESCRIPTION PART #DESCRIPTIONPART #DESCRIPTION
28149A UP CONTROL BLOCK ASSEMBLY BPS SECTION (Continued) CHECK SECTION (Continued)
280070Adjuster screw assembly (long)BPS closure assy (continued)28010A Check seat assembly (Continued)
203400Seal nut201200BPS closure2010A0Check seat
227000*Teflon seal201800BPS adjuster screw210370Seal ring
200700Adjuster screw210600*Seal ring
280090Adjuster screw assembly (short)28014B BPS piston & guide assembly205000 VALVE BODY
203400Seal nut204000 Sleeve28030A Regulator assembly
227000*Teflon seal210000* Seal ring2053A0Up leveling speed adjuster
200900Adjuster screw (short)2038B0BPS piston rod210700*Seal ring
Up control block miscellaneous210200*Seal ring2030A0Regulator
282920+Solenoid tube assembly2023A0Piston218800Spring
29298A-2+Solenoid seat kit28098A*Piston ring & expander assy212200Spring
292950+Ball cage kit2057A0*Seal ring214200Spring boss
210800*Seal ring2011E4BPS guide (standard)281610 Up / Down strainer assembly
244500Seal plug2118A0Lock nut210700*Seal ring
2105LC*Seal ring204200 BPS Diffuser216100Strainer
2110LC*Seal ring208900 Spring, BPS diffuser Valve body miscellaneous
238000Ball28006AUp / Down seat assembly203500Flange, 2½" Grooved (Shown)
243300Spring209300Snap ring203600Flange, 2" Grooved
239509Orifice (max UT) (Steel)2006A0Up seat2035A0Flange, 3" Grooved
2379A0Screw, (¼-28 button head)219200Seal ring205600Flange, 2" Threaded
2372LC*Seal ring205800Flange, 2½" Threaded
DOWN SECTION2105LC*Seal ring
Relief block assembly280520Down closure assembly210700*Seal ring
Note: Available in complete up block assy
only.205100Lock nut2379A0Screw (¼-28 button head)
206700Lock nut235200Pipe plug
28148A DOWN CONTROL BLOCK ASSY205200Down closure213100Regulator stud
280070Adjuster screw assy (long)2379A0Screw (¼-28 button head)2141A0Set screw
203400Seal nut202900Down leveling speed adjuster
227000*Teflon seal210600*Seal ring
200700Adjuster screw203700Down speed adjuster MISCELLANEOUS
280470Manual lowering screw assembly210500*Seal ring2059A0Coil Cover
203400Seal nut206400Screw (Down closure)
227000*Teflon seal28017BDown piston & guide assy (std...)206500Screw (BPS closure)
204700Manual lowering screw2038A0 Down piston rod206600Screw (flanges, Check closure)
230000Roll pin210200*Seal ring213000Lock ring
Down control block misc.2023A0Piston210400*Seal ring (flanges)
282920+Solenoid tube28098APiston ring & expander assy212900Screw (regulator cap)
28292A+Solenoid tube w / stud2057A0*Seal ring2138A0Screw (up block)
29298A-2+Solenoid seat kit2017E4Down guide (std.)213900Screw (up block)
292950+Ball cage kit2118A0Lock nut215900Screw (up & down blocks)
210800*Seal ring204000Sleeve205100Jam Nut
244500Seal plug210000*2379A0Screw (Coil Bracket)
263900*Seal ring28006AUp / Down seat assembly
2105LC*Seal ring209300Snap ring28082B Solenoid Coil Assembly
208700Spring2006A0Down seat2082B0Solenoid coil 115 VAC / 24 VDC (Red)
238000Ball219200Seal ring208880C-Frame
238100Screw (10/32 button head) CHECK SECTION
2379A0Screw (¼-28 button head)280480Check closure assembly
239513Orifice (max DS)204800Check closure
210370*Seal ring
208800 Spring, check piston
28011ACheck piston & guide assy (std.)
281780 COIL BRACKET ASSEMBLY2021A0Lock nut Notes: -
REFER TO THE UC2A EXPLODED
VIEW PARTS LIST FOR THE UC2A
DOWN VALVE SECTION.
*= PARTS INCLUDED IN
SEAL KIT # 291510
+ = PARTS INCLUDED IN
SOLENOID KIT # 29292A
217800Conduit Bracket200200Spacer
207700Grommet2025A0Check piston
207900Ground screw2057A0*Seal ring
2011E4Check guide (std.)
281510Check linkage assembly
BPS SECTION210200*Seal ring
280120BPS closure assembly 28010ACheck seat assembly
2067A0 Lock nut 2095A0 Snap ring
Seal ring
EXPLODED VIEW UC1A B44 PARTS LIST
This manual suits for next models
10
Table of contents
Other Maxton Control Unit manuals
Popular Control Unit manuals by other brands
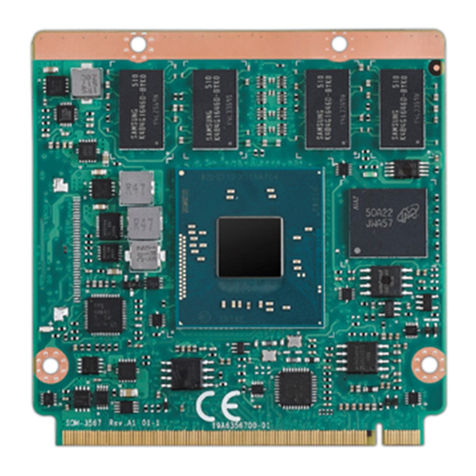
Advantech
Advantech Qseven SOM-3567 user manual

Mr. FILL
Mr. FILL Heavy Harry H.22 operating manual

LEYBOLD
LEYBOLD LEYCON BAV P AL Series user manual
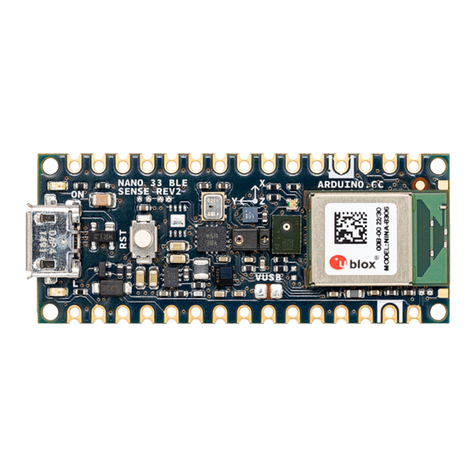
Arduino
Arduino Nano 33 BLE Sense Rev2 Product reference manual
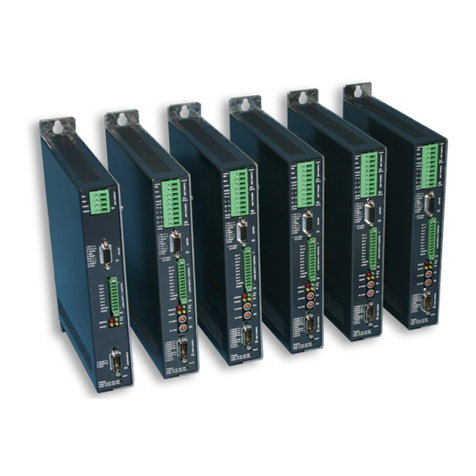
LinMot
LinMot E1100 Series user manual
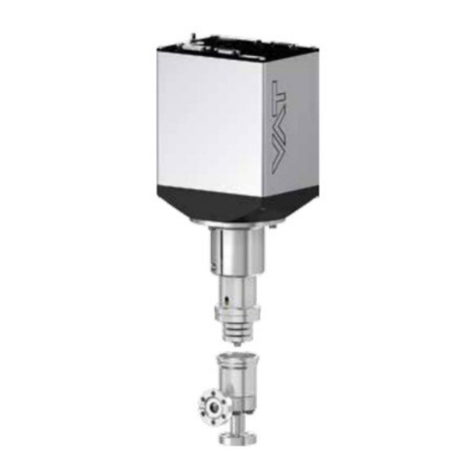
VAT
VAT 590 Series Installation, operating, & maintenance instructions