Metek 933 Manual

Model 933 UV Analyzer
Operator’s Guide
With Essential Health and Safety Requirements
PN 903-8735, Rev. G
Canada
A DIVISION OF AMETEK PROCESS & ANALYTICAL INSTRUMENTS
Western Research

ii | Model 933 UV Analyzer
© 2012–2018 AMETEK Canada, A Division of AMETEK Process & Analytical Instruments Printed in Canada
This manual is a guide for the use of the Model 933 UV Analyzer. Data herein has been veried and validated and is believed adequate for the intended
use of this instrument. If the instrument or procedures are used for purposes over and above the capabilities specied herein, conrmation of their validity
and suitability should be obtained; otherwise, AMETEK does not guarantee results and assumes no obligation or liability. This publication is not a license
to operate under, or a recommendation to infringe upon, any process patents.
Oces
For other offices not listed here, visit us at www.ametekpi.com.
USA – HEADQUARTERS
150 Freeport Road
Pittsburgh, PA 15238, USA
Tel: 412-828-9040
Toll Free: 800-537-6044
Fax: 412-826-0399
USA – Delaware
455 Corporate Boulevard
Newark, DE 19702, USA
Tel: 302-456-4400 (Main)
800-537-6044 (Service)
800-222-6789 (Ordering)
Fax: 302-456-4444
USA – Texas
4903 West Sam Houston Parkway North
Suite A-400
Houston, TX 77041, USA
Tel: 713-466-4900
Toll Free: 1-800-634-8990
Fax: 713-849-1924
CANADA
AMETEK Canada
2876 Sunridge Way N.E.
Calgary, AB, T1Y 7H9, Canada
Tel: 403-235-8400
Toll Free: 800-661-9198
Fax: 403-248-3550
INDIA
AMETEK Instruments India Pvt. Ltd.
1st Floor, Prestige Featherlite Tech Park
Plot 148, EPIP Phase II
Whitefield, Bengaluru – 560066, Karnataka, India
Tel: 91-80-6782-3200
Fax: 91-80-6782-3232
GERMANY
AMETEK GmbH
Rudolf-Diesel Strasse 16
D-40670 Meerbusch, Germany
Tel: 49-2159-9136-0
Fax: 49-2159-9136-39
FRANCE
AMETEK – APIF
Rond point de l’epine des champs
Buroplus Bat D
78990 Elancourt, France
Tel: 33-1-30-68-89-20
Fax: 33-1-30-68-89-29
CHINA
AMETEK Commercial Enterprise (Shanghai) Co. Ltd.
Part A First Floor, 460 North
Fute Road
Waigaoqiao Free Trade Zone
Shanghai, 200131, China
Tel: 86-21-5868-5111
Fax: 86-28-5866-0969
Beijing Branch
Tel: 86-10-8526-2111
Fax: 86-10-8526-2141
Chengdu Branch
Tel: 86-28-8675-8111
Fax: 86-28-8675-8141
Guangzhou Branch
Tel: 86-20-8363-4768
Fax: 86-20-8363-3701
MIDDLE EAST – Dubai
P.O. Box 17067
Jebel Ali Free Zone
Dubai, UAE
Tel: 971-4-881-2052
Fax: 971-4-881-2053
SINGAPORE
AMETEK Singapore Pte. Ltd.
No. 43, Changi South
Avenue 2, #04-01
486164 Singapore
Tel: 65-6486-2388
Fax: 65-6481-6588

Contents | iii
Contents
Offices .................................................................................................................................. ii
Safety Notes .....................................................................................................................viii
Electrical Safety................................................................................................................viii
Grounding........................................................................................................................viii
Personnel and Equipment Safety Information............................................................. ix
Warnings ...................................................................................................................... ix
Cautions ........................................................................................................................ x
Warning Labels.................................................................................................................. xi
Environmental Information ............................................................................................ xi
UV Source Lamps Disposal ............................................................................................. xi
Electromagnetic Compatibility (EMC).......................................................................... xii
Special Warnings and Information............................................................................... xiii
Equipment Used in Class I, Division 2 Hazardous Locations........................... xiii
EU Declaration of Conformity ...................................................................................... xiv
Warranty and Claims...................................................................................................... xvi
CHAPTER 1 OVERVIEW....................................................................................................... 1-1
About the Analyzer......................................................................................................... 1-2
About the Analyzer Sample System............................................................................. 1-4
Working in This Manual ................................................................................................ 1-6
Supplemental Information – Where Can I Find It?................................................... 1-7
CHAPTER 2 SPECIFICATIONS ........................................................................................... 2-1
Methodology.................................................................................................................... 2-1
Full-Scale Ranges............................................................................................................. 2-1
Standard Range Measuring Cells (40 cm or Smaller)................................................ 2-1
Low Range Measuring (White) Cell Option (81.2 cm).............................................. 2-1
Response Time................................................................................................................. 2-2
Accuracy............................................................................................................................ 2-2
Repeatability .................................................................................................................... 2-2
Calibration........................................................................................................................ 2-2
Linearity............................................................................................................................ 2-2
Stability ............................................................................................................................. 2-2
Sensitivity ......................................................................................................................... 2-3
Cross-Talk.......................................................................................................................... 2-3
Temperature Drift............................................................................................................ 2-3
24-Hour Zero Drift .......................................................................................................... 2-3
Customer Connections................................................................................................... 2-4
Analog Outputs ........................................................................................................ 2-4
Digital Communication ........................................................................................... 2-4
Digital Inputs............................................................................................................. 2-4
Electrical Requirements.................................................................................................. 2-4
Maximum Start-Up Power ...................................................................................... 2-4
Supply Voltage / Maximum Current ..................................................................... 2-4

iv | Model 933 UV Analyzer
Sample Gas Flow Rate.................................................................................................... 2-4
Zero Gas............................................................................................................................ 2-5
Ambient Limits ................................................................................................................ 2-5
Temperature............................................................................................................... 2-5
Humidity.................................................................................................................... 2-5
Maximum Altitude ................................................................................................... 2-5
Sample Pressure Requirement...................................................................................... 2-5
Sample Stream Compatibility ....................................................................................... 2-6
Maximum Sample Gas Temperature............................................................................ 2-6
Maximum Sample Cell Pressure................................................................................... 2-6
Physical Dimensions (on Backpan).............................................................................. 2-6
Options ............................................................................................................................. 2-6
Approvals and Certifications......................................................................................... 2-7
ATEX and IECEx Certificates and Analyzer Markings....................................... 2-8
CSA Certificate and Analyzer Marking............................................................... 2-16
CHAPTER 3 INSTALLATION AND START-UP................................................................... 3-1
Safety Considerations..................................................................................................... 3-2
Pre-Installation Requirements....................................................................................... 3-2
Storage Prior to Installation .................................................................................... 3-2
Uncrating and Inspecting the Analyzer................................................................ 3-3
General Installation Information ........................................................................... 3-4
Tools and Equipment Required.............................................................................. 3-4
Installing the Mechanical Components....................................................................... 3-5
Installing the Analyzer............................................................................................. 3-5
Location and Environment...................................................................................3-5
Installing the Optical Bench Assembly ................................................................. 3-7
Installing the Sample System.................................................................................. 3-9
Installing the Sample Probe..................................................................................3-9
Installing the Sample and Vent Lines...................................................................3-9
Installing the Zero Gas Line...............................................................................3-11
Electrical Connections .................................................................................................. 3-12
Input/Output Signal Connections ....................................................................... 3-12
Digital Communication ......................................................................................... 3-13
Hardware Configuration (Modbus Serial Communication) ..............................3-13
Multiple-Analyzer (Multi-Drop) System Configuration...................................3-17
AC Power Connection and Fusing....................................................................... 3-19
European Installation.........................................................................................3-20
North American Installation ..............................................................................3-20
System 200 Configurator Software Installation........................................................ 3-22
Minimum PC Requirements for Configurator Software.................................. 3-22
Installing the Configurator Software .................................................................. 3-23
Removing the Configurator Software................................................................. 3-24
Start-Up and Verification ............................................................................................. 3-25

Contents | v
Powering Up the Analyzer.................................................................................... 3-25
Start-Up Diagnostic Checklist ...........................................................................3-34
Sample System Leak Check......................................................................................... 3-36
Sample Conditioning System Optimization............................................................. 3-39
Column Switch Time Optimization .................................................................... 3-39
Hold Time Optimization ....................................................................................... 3-44
CHAPTER 4 CONTROLLER / USER INTERFACE............................................................. 4-1
System 200 Configurator Software Overview – Getting Started ............................ 4-2
Navigating in the Software..................................................................................... 4-2
Starting the Configurator Software and Establishing Communication
Between the Analyzer and Computer .................................................................. 4-4
Closing the Configurator Software........................................................................ 4-5
Configurator Software Troubleshooting ...............................................................4-6
General Tab................................................................................................................ 4-8
PC Communication Setup..................................................................................4-10
Device Communication Tab.................................................................................. 4-12
User Interface .......................................................................................................... 4-14
Setting Up the Main Window............................................................................4-14
Viewing Device Activities ..................................................................................4-15
Saving Analyzer Configuration Parameters ......................................................4-16
Restoring Analyzer Configuration Parameters..................................................4-16
Modifying Analyzer Device Settings ......................................................................... 4-17
Working From the Setup Tab ................................................................................ 4-17
Saving Analyzer Configuration Parameters to an ASCII File ...........................4-18
Printing Analyzer Configuration Parameters....................................................4-19
Refreshing Configuration or Calibration Parameters.........................................4-19
Saving Configuration or Calibration Parameters to EEPROM.........................4-19
Setting Gas Calibration Parameters ...................................................................4-20
Modbus Settings.................................................................................................4-23
Temperature Control...........................................................................................4-24
Optical Bench Temperature Control ............................................................4-25
Measuring Cell Temperature Control..........................................................4-26
Column Block Temperature Control ............................................................4-27
Output Setup .....................................................................................................4-28
Analyzer Information .........................................................................................4-31
Optical Bench .....................................................................................................4-32
Matrix ................................................................................................................4-35
Column Timing ..................................................................................................4-36
Compensation Parameters ..................................................................................4-37
Advanced Options ..............................................................................................4-40
Custom Output (Custom Setup)........................................................................4-41
Viewing Analyzer Data ................................................................................................ 4-42
Status Tab ................................................................................................................. 4-42
Optical Bench Data Tab ......................................................................................... 4-44
Analyzer Data Tab................................................................................................... 4-45

vi | Model 933 UV Analyzer
CHAPTER 5 CALIBRATION ................................................................................................. 5-1
Manual Span Gas Calibration ....................................................................................... 5-1
Analog Output Calibration............................................................................................ 5-4
Current Calibration .................................................................................................. 5-4
Voltage Calibration ................................................................................................... 5-6
CHAPTER 6 MAINTENANCE AND TROUBLESHOOTING............................................... 6-1
Safety Considerations..................................................................................................... 6-1
Preventive Maintenance ................................................................................................ 6-2
Analyzer Preventive Maintenance Schedule....................................................... 6-3
Preventing, Detecting, and Locating a Plug in the Sample System................. 6-5
Changing Out Replaceable Parts ........................................................................... 6-6
Measuring Cell Maintenance...............................................................................6-7
Column Block Maintenance ...............................................................................6-15
Source Lamp Replacement..................................................................................6-21
When Do Source Lamps Need to be Replaced?............................................6-21
About the Source Lamps ..............................................................................6-22
Replacing the Source Lamps........................................................................6-22
When is an Auto-Setup Required / Not Required?......................................6-27
PMT Level and PMT Balance .....................................................................6-28
Auto-Setup Fault Message and Corrective Action ......................................6-29
The Auto-Setup Sequence ............................................................................6-29
Cancel Auto-Setup.......................................................................................6-30
Manipulating the PMT Level and PMT Balance........................................6-31
Source Lamp Alignment ..............................................................................6-33
Natural Gas Filterblock Maintenance ................................................................6-35
Filtration Stages...........................................................................................6-36
Vent Flow .....................................................................................................6-36
Replacing Parts in the Filterblock ................................................................6-37
Chopper Assembly Maintenance ........................................................................6-42
Examining and Caring For the Flamepaths ....................................................... 6-50
Upper/Lower Electronics Enclosure Flamepaths (Joining Surfaces)..................6-51
Troubleshooting and Diagnostics ............................................................................... 6-52
Host Controller Board Alarm Conditions and Corrective Action .................. 6-54
Microcontroller Board Alarm Conditions and Corrective Action .................. 6-62
Analyzer Reset ........................................................................................................ 6-70
CHAPTER 7 SERVICE AND PARTS.................................................................................... 7-1
Technical Support............................................................................................................ 7-1
Returning Equipment..................................................................................................... 7-2
?? ANSWERS TO YOUR QUESTIONS ??................................................................... 7-3
AMETEK SERVICE and AFTERMARKET SALES SUPPORT............................ 7-3
Recommended Preventive Maintenance Spare Parts ............................................... 7-4
Optical Bench/Sample System Spare Parts........................................................... 7-4
Spare Analyzer Fuses ............................................................................................... 7-6
Replacement Boards................................................................................................. 7-7
Ordering a Hard Copy of the Analyzer Operator’s Guide ............................... 7-7

Contents | vii
APPENDIX A – DRAWINGS...................................................................................................A-1
Block Diagram, North American Style (WX-933NA-1) ............................................ A-2
Block Diagram, European Style (WX-933ATEX-1) .................................................... A-3
Sample Flow Diagram (Plumbing Schematic), North American Style
(WX-933NA-2)................................................................................................................. A-4
Backpan Dimensions, North American Style (WX-933NA-3) ................................. A-5
Backpan Component Layout, North American Style (WX-933NA-3A) ................ A-6
Conduit Entries, I/O and AC Power Connection Locations, North American
Style (WX-933NA-3B)..................................................................................................... A-7
Lower Enclosure Layout (WX-14838) – North American (CSA)/European
(Zone 1/ATEX)................................................................................................................. A-8
Customer Connections Wiring Schematic, North American Style
(WX-933NA-4)................................................................................................................. A-9
RS-232 Communications Cable Connections (300-9480) ....................................... A-10
Analyzer Wiring Diagram (WX-102860-1) ................................................................ A-11
Optional HMI and Ethernet Gateway Wiring Diagram (WX-102860-4) ............. A-12
Sample Probe – North American (CSA)/European (Zone 1/ATEX)...................... A-13
Sample Probe, Recommended Mounting Details – North American (CSA)/
European (Zone 1/ATEX) ............................................................................................ A-14
Optical Bench Board (P/N 100-1662)......................................................................... A-15
PMT Buffer Board (100-0140) ..................................................................................... A-16
Inlet and Vent Flame Arrestor Locations, Environmental Purge Option
(100-1783-1A)................................................................................................................. A-17
SUPPLEMENTAL INFORMATION ........................................................................................S-1

viii | Model 933 UV Analyzer
Safety Notes
WARNINGS, CAUTIONS, and NOTES contained in this manual emphasize critical instructions
as follows:
An operating procedure which, if not strictly observed, may result in personal injury or envi-
ronmental contamination. Essential Health and Safety Requirements are also included in
– but are not limited to – Warnings.
An operating procedure which, if not strictly observed, may result in damage to the equipment.
Important information that should not be overlooked.
Electrical Safety
High voltages are present in the analyzer housings. Always shut down power source(s) before
performing maintenance or troubleshooting. Only a qualified electrician should make electrical
connections and ground checks.
Any use of the equipment in a manner not specified by the manufacturer may impair the safety
protection originally provided by the equipment.
Grounding
Instrument grounding is mandatory. Performance specifications and safety protection are void if
instrument is operated from an improperly grounded power source.
Verify ground continuity of all equipment before applying power.
!
WARNING
NOTE
!
CAUTION
!
CAUTION

Contents | ix
Personnel and Equipment Safety Information
This section describes important safety information to avoid personal injury and damage to the
equipment while installing, operating, maintaining, or servicing the equipment. All safety regu-
lations, standards, and procedures at the analyzer location must be followed.
All personnel involved with the installation, start-up, operation, maintenance, service, or trou-
bleshooting of the analyzer must review and follow these Warnings and Cautions.
Warnings
Review and follow these Warnings to avoid personal injury or environmental contamination.
Always disconnect main AC power and/or external power sources (example, for relay contacts)
to the analyzer before removing any sample system assemblies and components from the ana-
lyzer, or before opening any covers on the analyzer.
If it is necessary to open the Upper/Lower Ex d Electronics Enclosures while the circuits are
live, test the area for explosive gases and proceed only when the area is safe. When the Enclo-
sures are open, take appropriate precautions to avoid electrical shock. Hazardous voltages are
present inside.
All electrical connections, adjustments, or servicing of the analyzer should be performed only
by properly trained and qualified personnel.
All electrical connections, materials, and methods (plus all safety policies and procedures) must
be made in compliance with local wiring regulations and electrical code for the hazardous area,
and be approved by the Owner Company.
Before working on the sample system, confirm that the system is purged with Zero gas and is
isolated (blocked in) from the process.
Because ultraviolet radiation can harm your eyes, avoid direct viewing of the light emanating
through the end window of the source lamp. If the source lamp must be viewed while ener-
gized, wear safety glasses that block ultraviolet radiation.
For Division 1/Zone 1 Installations, all cable entry glands (one power cable entry and two
signal cable entries) into the flameproof Disconnect Enclosure must be Ex d certified. Conduit
or cable seals that comply with the flameproof enclosure cable entry sealing requirements of the
local authority must be installed at the entries to the enclosure. In all cases, each unused cable
entry port must be plugged with a certified Ex d plug.
WARNING
!
WARNING
!
WARNING
!
WARNING
!
WARNING
!

x | Model 933 UV Analyzer
If the analyzer uses the optional Measuring Cell heater, take precautions to avoid burning
yourself; the Measuring Cell and Heater Assembly are hot.
Cautions
Review and follow these Cautions to avoid damaging the equipment.
The electronic circuit boards and other static-sensitive components should be stored and trans-
ported in static-shielding carriers or packages.
For electrical-shock protection, the analyzer must be operated from a grounded power source
that has a securely connected protective-ground contact.
If it becomes necessary to handle any of the electronic circuit boards, do not subject the boards
to static discharge. The ideal solution is a static-safe work area. Since such areas typically are
not available at field installation sites, the use of a wrist strap connected directly to a ground
is recommended. If a wrist strap is not available, you should at the very least touch the metal
chassis (to ground yourself) before handling or touching the boards.
When handling the source lamps, it is very important not to touch the lamp windows because
residual oils from the fingers will absorb ultraviolet light. The window is the flat surface at the
end of the narrow glass tube. The lamp assembly is fragile and should be handled with care.
Do not exceed the maximum working pressure rating of the sample system under any circum-
stances:
• Systems with Filterblock Assembly: 13 790 KPAG (2000 PSIG).
• Systems without Filterblock Assembly: 20 700 KPAG (3000 PSIG).
If the analyzer is equipped with the Environmental Purge option, clean air or nitrogen can be
supplied to the inlet flame arrester at a pressure of 7–70 KPAG (1–10 PSIG).
!
CAUTION
!
CAUTION
!
CAUTION
!
CAUTION
!
CAUTION
!
CAUTION
WARNING
!

Contents | xi
Warning Labels
These symbols may appear on the instrument in order to alert you of existing conditions.
Protective Conductor Terminal
(BORNIER DE L’ECRAN DE PROTECTION)
Schutzerde
Caution – Risk of electric shock
(ATTENTION – RISQUE DE DÉCHARGE ÉLECTRIQUE)
Achtung – Hochspannung Lebensgefahr
Caution – Refer to accompanying documents
(ATTENTION – SE RÉFERER AUX DOCUMENTS JOINTS)
Achtung – Beachten Sie beiliegende Dokumente
CAUTION – Hot Surface
(ATTENTION – SURFACE CHAUDE)
Achtung – Heiße Oberäche
Environmental Information
This AMETEK product contains materials that can be reclaimed and recycled. In some cases the
product may contain materials known to be hazardous to the environment or human health.
In order to prevent the release of harmful substances into the environment and to conserve
our natural resources, AMETEK recommends that you arrange to recycle this product when it
reaches its “end of life.”
Waste Electrical and Electronic Equipment (WEEE) should never be disposed of in a munici-
pal waste system (residential trash). The Wheelie Bin marking on this product is a reminder to
dispose of the product properly after it has completed its useful life and been removed from
service. Metals, plastics, and other components are recyclable and you can do your part by doing
one of the following steps:
• When the equipment is ready to be disposed of, take it to your local or region-
al waste collection administration for recycling.
• In some cases, your “end of life” product may be traded in for credit towards
the purchase of new AMETEK instruments. Contact your dealer to see if this
program is available in your area.
• If you need further assistance in recycling your AMETEK product, contact our
office listed in this manual.
UV Source Lamps Disposal
AMETEK recommends that all UV lamps – whether they are new, used, or damaged in any way
– need to be disposed of in an environmentally safe manner.
Most UV lamps do not contain restricted substances listed under the European RoHS 2 direc-
tive. However, special handling requirements are required for some lamps if they are broken.
Two examples include Cadmium and Beryllium lamps. Refer to a current Material Safety Data
Sheet (MSDS) for handling any lamp where the glass envelope has been broken and which has
exposed the metal cathode in the centre of the lamp.

xii | Model 933 UV Analyzer
Electromagnetic Compatibility (EMC)
Read and follow the recommendations in this section to avoid performance variations or dam-
age to the internal circuits of this equipment when installed in harsh electrical environments.
The various configurations of the Model 933 Analyzer should not produce, or fall victim to, elec-
tromagnetic disturbances as specified in the European Union’s EMC Directive. Strict compliance
to the EMC Directive requires that certain installation techniques and wiring practices are used
to prevent or minimize erratic behavior of the Analyzer or its electronic neighbors. Below are
examples of the techniques and wiring practices to be followed.
In meeting the EMC requirements, the various Analyzer configurations described in this manual
rely heavily on the use of metallic shielded cables used to connect to the customer’s equip-
ment and power. Foil and braid shielded I/O and DC power cables are recommended for use in
otherwise unprotected situations. In addition, hard conduit, flexible conduit, and armor around
non-shielded wiring also provides excellent control of radio frequency disturbances. However,
use of these shielding techniques is effective only when the shielding element is connected to
the equipment chassis/earth ground at both ends of the cable run. This may cause ground loop
problems in some cases. These should be treated on a case-by-case basis. Disconnecting one
shield ground may not provide sufficient protection depending on the electronic environment.
Connecting one shield ground via a 0.1 microfarad ceramic capacitor is a technique allowing
high frequency shield bonding while avoiding the AC-ground metal connection. In the case of
shielded cables the drain wire or braid connection must be kept short. A two-inch connection
distance between the shield’s end and the nearest grounded chassis point, ground bar or termi-
nal is highly recommended. An even greater degree of shield performance can be achieved by
using metallic glands for shielded cable entry into metal enclosures. Expose enough of the braid/
foil/drain where it passes through the gland so that the shield materials can be wrapped back-
wards onto the cable jacket and captured inside the gland, and tightened up against the metal
interior.
Inductive loads connected to the low voltage “Alarm Contacts” are not recommended. However,
if this becomes a necessity, adhere to proper techniques and wiring practices. Install an appro-
priate transient voltage suppression device (low voltage MOV, “Transzorb,” or R/C) as close as
possible to the inductive device to reduce the generation of transients. Do not run this type of
signal wiring along with other I/O or DC in the same shielded cable. Inductive load wiring must
be separated from other circuits in conduit by using an additional cable shield on the offending
cable.
In general, for optimum protection against high frequency transients and other disturbances, do
not allow installation of this Analyzer where its unshielded I/O and DC circuits are physically
mixed with AC mains or any other circuit that could induce transients into the Analyzer or the
overall system. Examples of electrical events and devices known for the generation of harmful
electromagnetic disturbances include motors, capacitor bank switching, storm related transients,
RF welding equipment, static, and walkie-talkies.
If connecting one or more of the analyzer non-isolated voltage outputs to an external device, a
15 Volt Zener Diode must be connected across the positive and common terminals of each non-
isolated voltage output channel at J108 of the Customer I/O board (Part No. 100-1758).
!
CAUTION

Contents | xiii
Special Warnings and Information
Equipment Used in Class I, Division 2 Hazardous Locations
Refer to Chapter 2 – Specifications for details about the suitability of this equipment in hazard-
ous locations.
EXPLOSION HAZARD – DO NOT DISCONNECT EQUIPMENT UNLESS POWER
HAS BEEN SWITCHED OFF OR THE AREA IS KNOWN TO BE NON-HAZARDOUS.
Risque d’explosion – Avant de déconnecter l’équipement, coupez le courant où vous assurez
que l’emplacement est designé non dangereux.
All input and output wiring must be in accordance with Class I, Division 2 wiring methods
(CEC 18-152) and in accordance with the authority having jurisdiction.
!
WARNING
!
Avertissement

xiv | Model 933 UV Analyzer
EU Declaration of Conformity
PN 903-8595 Rev N
EU Declaration of Conformity
Manufacturer’s Name: AMETEK Canada
A Division of AMETEK Process & Analytical Instruments
(ISO 9001:2008 Registered)
Manufacturer’s Address: 2876 Sunridge Way N.E.
Calgary, Alberta, Canada T1Y 7H9
Phone: (403) 235-8400 / Fax: (403) 248-3550
EU Representative Address: AMETEK Precision Instruments Europe GmbH
Rudolf-Diesel-Str. 16
D-40670 Meerbusch, Germany
Phone: 49-2159 91 36 0 / Fax: 49-2159 91 36 80
Declare under our sole responsibility that the products:
Product Names: Model 93x-Series Photometric Analyzers
Model Numbers: 931/932/933/934
Marking: II 2 G Ex db IIB+H2T3 Gb or
II 2 G Ex db IIB+H2T3 or
II 2 G Ex db IIB T3 Gb or
II 2 G Ex db IIB T3
Conform to the following EU Standards and Directives:
Electromagnetic Compatibility Directive 2014/30/EU using the following standards:
EN 61326-1 Electrical equipment for measurement, control and laboratory use – EMC requirements –
Part 1: General requirements.
EN 55011 (CISPR 55011) Radiated Electromagnetic Emissions, Class A 30 MHz to 1 GHz.
EN 55011 (CISPR 55011) Conducted Electromagnetic Emissions, Class A.
EN61000-3-2 Limitsforharmoniccurrentemissions(equipmentinputcurrent≤16Aperphase).
EN61000-3-3 Limitationofvoltagechanges,voltageuctuationsandickerinpubliclow-voltagesupply
systems,forequipmentwithratedcurrent≤16Aperphaseandnotsubjecttoconditional
connection.
EN 61000-4-2 Testing and measurement techniques – Electrostatic discharge immunity test.
EN61000-4-3 Testingandmeasurementtechniques–Radiated,radio-frequency,electromagneticeld
immunity test.
EN 61000-4-4 Testing and measurement techniques – Electrical fast transient/burst immunity test.
EN 61000-4-5 Testing and measurement techniques – Surge immunity test.
EN 61000-4-6 Testing and measurement techniques – Immunity to conducted disturbances, induced by radio-
frequencyelds.
EN61000-4-8 Testingandmeasurementtechniques–Powerfrequencymagneticeldimmunitytest.
EN 61000-4-11 Testing and measurement techniques – Voltage dips, short interruptions and voltage variations
immunity tests.
Restriction of Hazardous Substances Directive 2011/65/EU (RoHS 2).
Low Voltage Directive 2014/35/EU using the following standards:
EN 61010-1 Safety requirements for electrical equipment for measurement, control, and
laboratory use – Part 1: General requirements.
Pressure Equipment Directive 2014/68/EU
Article 4, Paragraph 3
Page 1 of 2
Canada
A DIVISION OF AMETEK PROCESS & ANALYTICAL INSTRUMENTS
Western Research

Contents | xv
EU Declaration of Conformity
The object of the declaration described [herein] is in conformity with the relevant Union harmonization
legislation (Directive 2014/34/EU):
EN 60079-0:2012 + A11:2013 General requirements
EN 60079-1:2014 Flameproof Enclosures ‘d’
CerticateNumber: KEMA02ATEX2247X
NotiedBody: DEKRACerticationB.V.0344
Meander 1051, 6825 MJ Arnhem
The Netherlands
____________________________
Randy Meads
Quality Assurance Manager
Calgary, Alberta, Canada
June 28, 2017
Page 2 of 2
Canada
A DIVISION OF AMETEK PROCESS & ANALYTICAL INSTRUMENTS
Western Research

xvi | Model 933 UV Analyzer
Warranty and Claims
We warrant that any equipment of our own manufacture or manufactured for us pursuant to our specifications
which shall not be, at the time of shipment thereof by or for us, free from defects in material or workmanship un-
der normal use and service will be repaired or replaced (at our option) by us free of charge, provided that written
notice of such defect is received by us within twelve (12) months from date of shipment of portable analyzers or
within eighteen (18) months from date of shipment or twelve (12) months from date of installation of permanent
equipment, whichever period is shorter. All equipment requiring repair or replacement under the warranty shall be
returned to us at our factory, or at such other location as we may designate, transportation prepaid. Such returned
equipment shall be examined by us and if it is found to be defective as a result of defective materials or workman-
ship, it shall be repaired or replaced as aforesaid. Our obligation does not include the cost of furnishing any labor
in connection with the installation of such repaired or replaced equipment or parts thereof, nor does it include the
responsibility or cost of transportation. In addition, instead of repairing or replacing the equipment returned to us
as aforesaid, we may, at our option, take back the defective equipment, and refund in full settlement the purchase
price thereof paid by Buyer.
Process photometric analyzers, process moisture analyzers, and sample systems are warranted to perform the in-
tended measurement, only in the event that the customer has supplied, and AMETEK has accepted, valid sample
stream composition data, process conditions, and electrical area classification prior to order acknowledgment. The
photometric light sources are warranted for ninety (90) days from date of shipment. Resale items warranty is limited
to the transferable portion of the original equipment manufacturer’s warranty to AMETEK. If you are returning
equipment from outside Canada, a statement should appear on the documentation accompanying the equipment
being returned declaring that the goods being returned for repair are Canadian goods, the name of the firm who
purchased the goods, and the shipment date.
The warranty shall not apply to any equipment (or part thereof) which has been tampered with or altered after
leaving our control or which has been replaced by anyone except us, or which has been subject to misuse, neglect,
abuse or improper use. Misuse or abuse of the equipment, or any part thereof, shall be construed to include, but
shall not be limited to, damage by negligence, accident, fire or force of the elements. Improper use or misapplications
shall be construed to include improper or inadequate protection against shock, vibration, high or low temperature,
overpressure, excess voltage and the like, or operating the equipment with or in a corrosive, explosive or combustible
medium, unless the equipment is specifically designed for such service, or exposure to any other service or environ-
ment of greater severity than that for which the equipment was designed.
The warranty does not apply to used or secondhand equipment nor extend to anyone other than the original
purchaser from AMETEK. Should the Buyer’s technical staff require the on-site assistance of AMETEK’s agents or
employees for service calls covered by this warranty clause, the Buyer shall pay travel time plus actual travel and
living expenses.
THIS WARRANTY IS GIVEN AND ACCEPTED IN LIEU OF ALL OTHER WARRANTIES, WHETHER EXPRESS
OR IMPLIED, INCLUDING WITHOUT LIMITATION AND WARRANTIES OF FITNESS OR OF MERCHANT-
ABILITY OTHER THAN AS EXPRESSLY SET FORTH HEREIN, AND OF ALL OTHER OBLIGATIONS OR LI-
ABILITIES ON OUR PART. IN NO EVENT SHALL WE BE LIABLE UNDER THIS WARRANTY OR ANY OTHER
PROVISION OF THIS AGREEMENT FOR ANY ANTICIPATED OR LOST PROFITS, INCIDENTAL DAMAGES,
CONSEQUENTIAL DAMAGES, TIME CHANGES OR ANY OTHER LOSSES INCURRED BY THE ORIGINAL
PURCHASER OR ANY THIRD PARTY IN CONNECTION WITH THE PURCHASE, INSTALLATION, REPAIR OR
OPERATION OF EQUIPMENT, OR ANY PART THEREOF COVERED BY THIS WARRANTY OR OTHERWISE.
WE MAKE NO WARRANTY, EXPRESS OR IMPLIED, INCLUDING WITHOUT LIMITATION ANY WARRANTIES
OF FITNESS OR OF MERCHANTABILITY, AS TO ANY OTHER MANUFACTURER’S EQUIPMENT, WHETHER
SOLD SEPARATELY OR IN CONJUNCTION WITH EQUIPMENT OF OUR MANUFACTURE. WE DO NOT
AUTHORIZE ANY REPRESENTATIVE OR OTHER PERSON TO ASSUME FOR US ANY LIABILITY IN CON-
NECTION WITH EQUIPMENT, OR ANY PART THEREOF, COVERED BY THIS WARRANTY.

Overview | 1-1
OVERVIEW
The AMETEK Model 933 Analyzer uses photometric analysis to continu-
ously monitor H2S levels in pipeline quality natural gas. It uses AMETEK
Western Research’s proven sample conditioning system based on frontal
elution chromatography. This system separates and eliminates interfer-
ing species to ensure an accurate analysis of the gas. The microprocessor-
based Model 933 Analyzer minimizes the complexity of these tasks and
simplifies operation of the analyzer system.

1-2 | Model 933 UV Analyzer
About the Analyzer
The Model 933 Analyzer is comprised of (see Figure 1-1):
• Two ultraviolet light sources (source lamps)
• Chopper Wheel (Filter Wheel) containing up to six interference filters
• Beam Splitter
• Front-surfaced mirrors
• Gas Measuring Cell
• Two matched Photodetectors
Figure 1-1.
Analytical block
diagram.

Overview | 1-3
Figure 1-2 illustrates a Sample Flow Diagram (plumbing schematic)
for a typical European style analyzer. See Appendix A for a North
American style drawing (or Final “As-Built” drawings in the analyzer
Documentation Package).
NOTE
Figure 1-2.
Sample ow diagram
(Plumbing Schematic).
REFERENCE: CERTIFICATE NO: KEMA 02ATEX2247 X
CERTIFICATE NO: IECEx DEK12.0035X

1-4 | Model 933 UV Analyzer
About the Analyzer Sample System
The sample system is mounted to the Model 933 Analyzer backpan. The
purpose of the system is to maintain constant pressure and temperature,
and to condition the sample to obtain correct analysis.
The sample system consists of (see Figures 1-2 and 1-3):
Component Function
Sample Probe Extends into the sample stream to obtain a representative sample.
Contains a shut-o valve used to isolate the analyzer’s sample system
from the sample stream.
Pressure Regulator The pressure regulator adjusts the sample gas pressure to the ana-
lyzer operating pressure (typically 80 PSIG/550 KPAG) if the process
pressure is higher than the analyzer operating pressure (refer to Final
“As-Built” drawings in the analyzer Documentation Package).
Pressure Gauge The pressure gauge is used to set the proper sample pressure in the
sample system.
Solenoid Block The solenoid manifold block directs ow between the Zero, Column A,
and Column B solenoids. There is also a pressure relief valve to safe-
guard against over pressuring of any components down stream of the
Solenoid Block or if the pressure regulator fails. This valve is factory-
adjusted to open at approximately 150 PSIG (1050 KPAG).
Column Switching Solenoids Solenoids are automatically turned on or o to initiate switching the
sample gas between columns.
Zero Solenoid The zero solenoid allows Zero gas (or Span gas) to ush the sample
system during the Auto-Zero (or Span) process. The column switching
solenoids are closed when the zero solenoid is open.
Column Block The Column Block is where the sample conditioning process takes
place. The Column Block incorporates a proprietary material to permit
correct sample analysis.
Heat Exchanger Block The Heat Exchanger Block reduces the temperature of the conditioned
gas sample prior to it entering the Measuring Cell.
Measuring (Sample) Cell The Measuring Cell is a chamber of known length, with optical-grade
quartz windows, through which the radiation beam passes through the
gas sample. The windows are sealed by means of o-rings and remov-
able end caps.
Flow Indicator The ow meter provides a visual indication of the sample ow rate
in liters/minute through the analyzer. Please note that the scaling on
the ow indicator is for air at standard temperature and pressure. Its
purpose is to indicate and ensure that appropriate ow conditions
are maintained and not to provide an absolute measure of the ow
of sample gas. Some systems use a Rotameter instead of the Flow
Indicator.
Filterblock Assembly (optional)
The Filterblock Assembly removes condensables and particulates from
the sample gas.
Table of contents
Other Metek Measuring Instrument manuals
Popular Measuring Instrument manuals by other brands
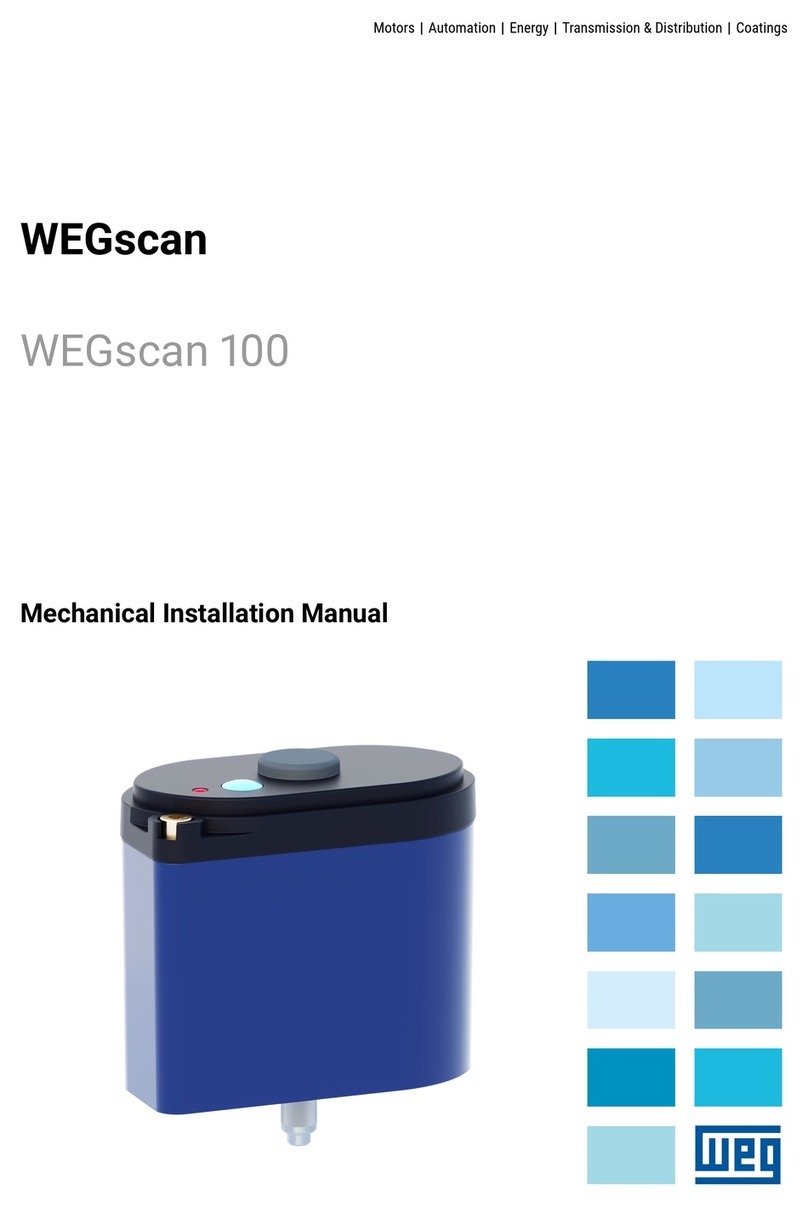
WEG
WEG WEGscan 100 Mechanical Installation Manual
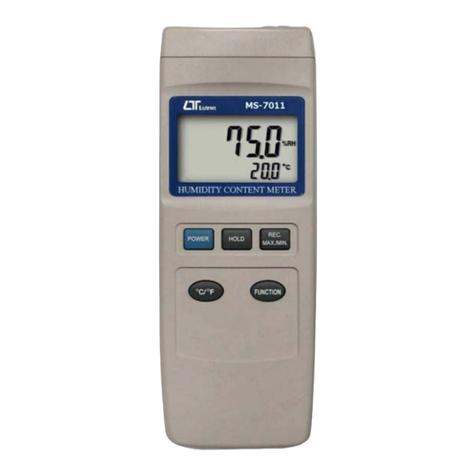
Lutron Electronics
Lutron Electronics MS-7011 Operation manual
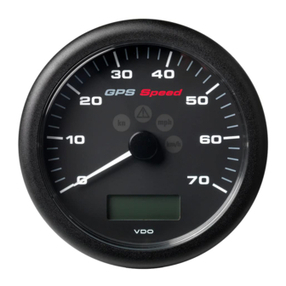
VDO
VDO Viewline 110 mm installation instructions
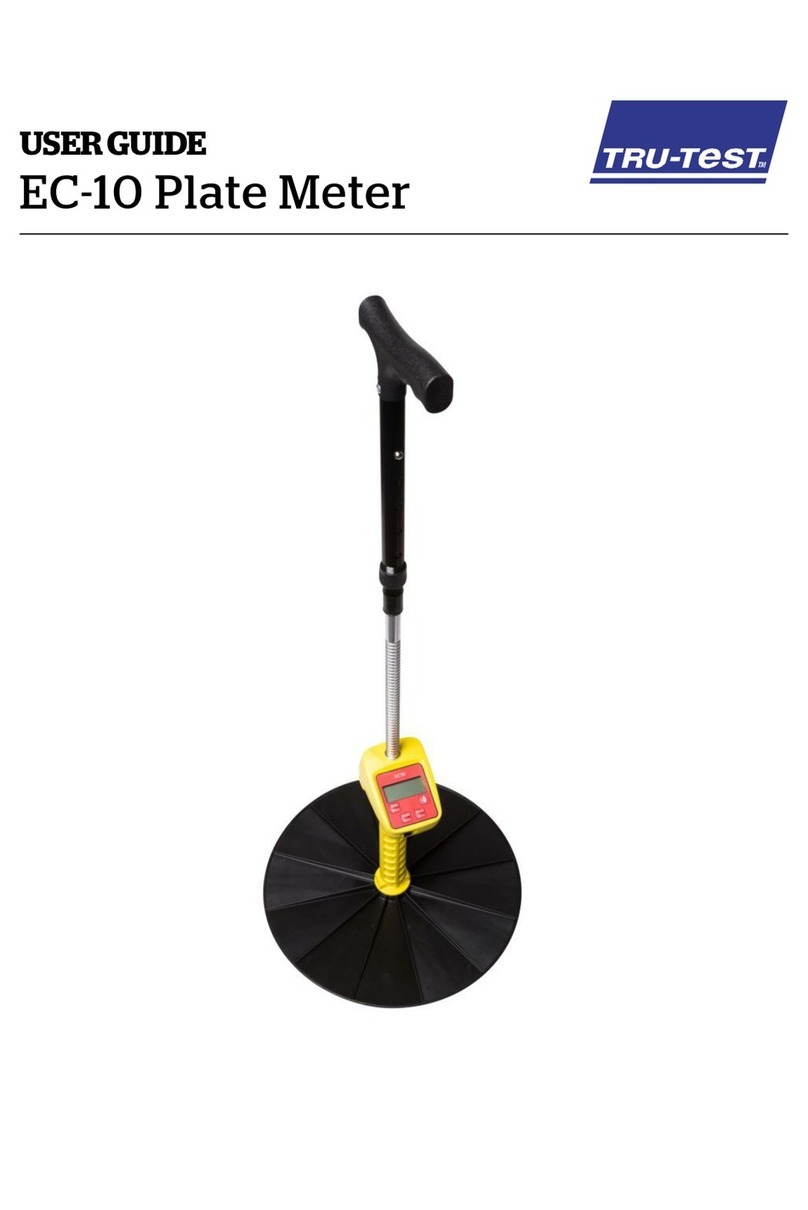
Tru-Test
Tru-Test EC-10 user guide
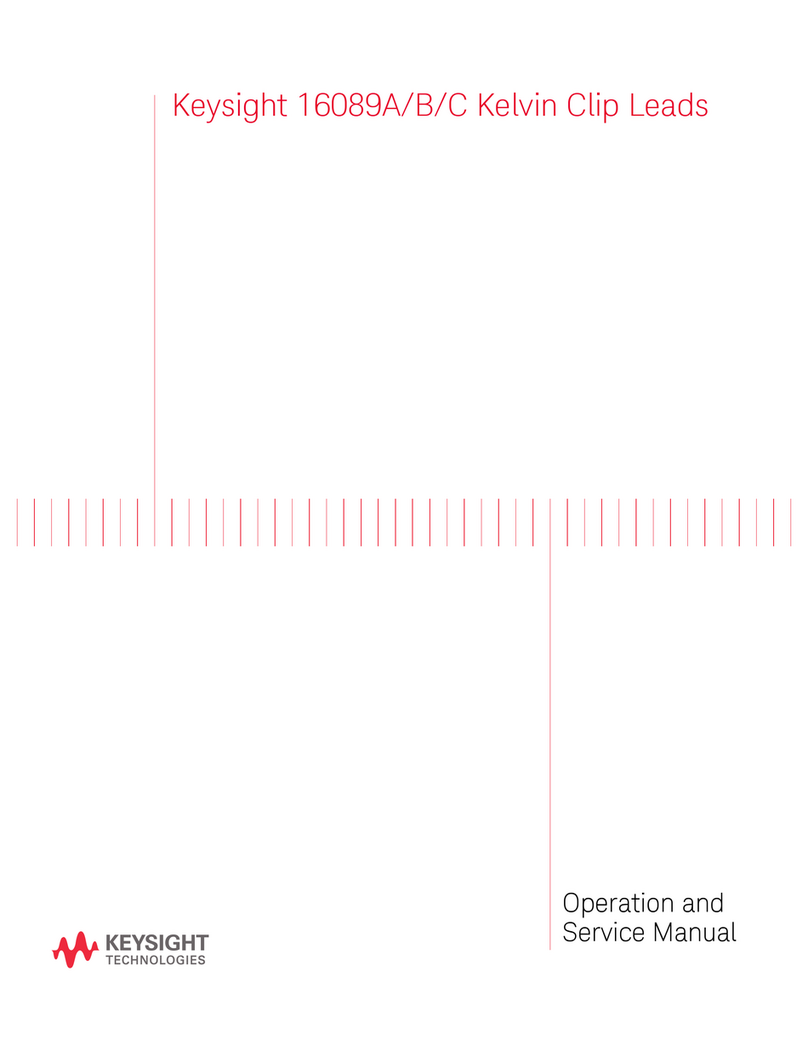
Keysight Technologies
Keysight Technologies 16089A Operation and service manual
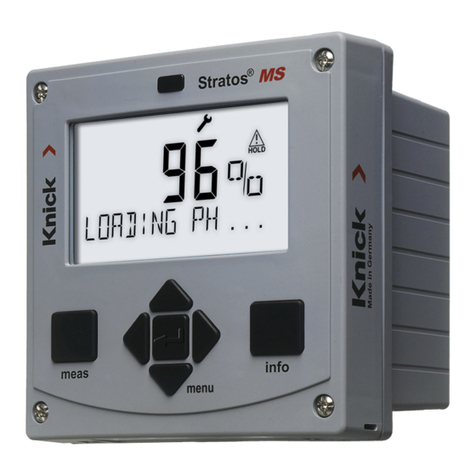
Knick
Knick Stratos MS A405 user manual