Metronix DIS-2 310/2 FB FS STO User manual

Metronix Meßgeräte und Elektronik GmbH Telefon: +49-(0)531-8668-0
Kocherstraße 3 Telefax: +49-(0)531-8668-555
D-38120 Braunschweig E-mail: vertrieb@metronix.de
Germany http://www.metronix.de
Product Manual
Servo Positioning Controller DIS-2 310/2 FB

Seite 2
Product Manual “Servo Positioning Controller DIS-2 310/2 FB“ Version 4.0
Copyrights
2018 Metronix Meßgeräte und Elektronik GmbH. All rights reserved.
The information and data in this document have been composed to the best of our knowledge. Howev-
er, deviations between the document and the product cannot be excluded entirely. For the devices and
the corresponding software in the version handed out to the customer, Metronix guarantees the con-
tractual use in accordance with the user documentation. In the case of serious deviations from the user
documentation, Metronix has the right and the obligation to repair, unless it would involve an unrea-
sonable effort. A possible liability does not include deficiencies caused by deviations from the operating
conditions intended for the device and described in the user documentation.
Metronix does not guarantee that the products meet the buyer’s demands and purposes or that they
work together with other products selected by the buyer. Metronix does not assume any liability for
damages resulting from the combined use of its products with other products or resulting from improp-
er handling of machines or systems.
Metronix Meßgeräte und Elektronik GmbH reserves the right to modify, amend, or improve the docu-
ment or the product without prior notification.
This document may, neither entirely nor in part, be reproduced, translated into any other natural or
machine-readable language nor transferred to electronic, mechanical, optical or any other kind of data
media, without expressive authorisation by the author.
Trademarks
Any product names in this document may be registered trademarks. The sole purpose of any trade-
marks in this document is the identification of the corresponding products.
ServoCommander™ is a registered trademark of Metronix Meßgeräte und Elektronik GmbH.

Seite 3
Product Manual “Servo Positioning Controller DIS-2 310/2 FB“ Version 4.0
Revision log
Author:
Metronix Meßgeräte und Elektronik GmbH
Manual name:
Product Manual „Servo Positioning Controller DIS-2 310/2 FB“
File name:
P-HB_DIS-2_310_2_FB_3p0_EN.doc
File location:
Series no.
Description
Revision index
Date of change
001
Release for distribution
1.0
31.03.2009
002 Update Corporate Identity – No technical
changes
2.0 18.04.2011
003
Changes in chapter 2.2
3.0
28.06.2011
004 Page 48 – Figure 9., Schematic modified.
Connections controller / PLC for +24V and
0V changed.
4.0 15.11.2018
005
Latest Metronix Company Logo inserted
4.0
15.11.2018

Seite 4
Product Manual “Servo Positioning Controller DIS-2 310/2 FB“ Version 4.0
TABLE OF CONTENTS:
1GENERAL...........................................................................................................10
1.1 Documentation.................................................................................................10
1.2 Scope of supply ...............................................................................................11
2SAFETY NOTES FOR ELECTRICAL DRIVES AND CONTROLLERS..............13
2.1 Used symbols...................................................................................................13
2.2 General notes...................................................................................................13
2.2.1 Danger resulting from misuse.............................................................................15
2.3 Safety notes......................................................................................................15
2.3.1 General safety notes...........................................................................................15
2.3.2 Safety notes for assembly and maintenance......................................................17
2.3.3 Protection against contact with electrical parts...................................................18
2.3.4 Protection against electrical shock by means of protective extra-low voltage
(PELV) ................................................................................................................19
2.3.5 Protection against dangerous movements .........................................................19
2.3.6 Protection against contact with hot parts............................................................20
2.3.7 Protection during handling and assembly...........................................................20
3PRODUCT DESCRIPTION.................................................................................22
3.1 General .............................................................................................................22
3.1.1 Basic information................................................................................................22
3.1.2 Area of application and intended use .................................................................22
3.1.3 DIS-2 310/2 FB features.....................................................................................23
3.2 Power supply....................................................................................................25
3.2.1 Single-phase AC supply......................................................................................25
3.2.2 DC bus coupling, DC supply...............................................................................25
3.2.3 Mains fuse ..........................................................................................................25
3.3 Brake chopper..................................................................................................25
3.4 Communication interfaces..............................................................................25
3.4.1 RS232 interface..................................................................................................25
3.4.2 CAN-Bus.............................................................................................................26
3.4.3 Profibus...............................................................................................................26
3.4.4 EtherCAT............................................................................................................26
3.4.5 I/O functions and device controller .....................................................................26
4TECHNICAL DATA.............................................................................................27
4.1 Ambient conditions and qualification.............................................................27
4.2 Performance data power supply [X1] .............................................................28
4.3 Motor connection [X6] .....................................................................................28
4.4 Motor feedback connection [X2].....................................................................29
4.5 Communication interfaces..............................................................................31
4.5.1 RS232 [X5] .........................................................................................................31
4.5.2 I/O- interface [X1]................................................................................................31
4.5.3 Incremental encoder input and output [X1].........................................................32
4.6 Technical data fieldbus interfaces..................................................................34
4.6.1 CAN-Bus [X401] / [402] ......................................................................................34
4.6.2 Profibus [X401] / [402]........................................................................................34
4.6.3 EtherCAT [X401] / [402]......................................................................................34
5FUNCTION OVERVIEW .....................................................................................35
5.1 Motors...............................................................................................................35
5.1.1 Synchronous servo motors.................................................................................35
5.2 Current and speed controlled mode...............................................................35

Seite 5
Product Manual “Servo Positioning Controller DIS-2 310/2 FB“ Version 4.0
5.3 Function overview............................................................................................38
5.3.1 Synchronisation, electrical transmissions...........................................................39
5.3.2 Pulse direction Interface.....................................................................................40
5.3.3 Cycle times .........................................................................................................40
5.3.4 Homing ...............................................................................................................40
5.3.5 Relative positioning.............................................................................................40
5.3.6 Absolute positioning............................................................................................41
5.3.7 Driving profile generator .....................................................................................41
5.3.8 Positioning sequences........................................................................................41
5.3.9 Software limit switches (positioning range).........................................................42
5.3.10 Brake management ............................................................................................42
5.4 Use of digital and analogue in- and outputs..................................................42
5.5 Jogging and Teaching.....................................................................................42
6MECHANICAL INSTALLATION .........................................................................43
6.1 Important notes................................................................................................43
6.2 Position and alignment of the connectors.....................................................43
6.2.1 Connectors on the main board: ..........................................................................44
6.2.2 Connectors for RS232 and fieldbus-modules (CANopen, PROFIBUS,
EtherCAT):..........................................................................................................44
6.3 Dimensions of the housing .............................................................................45
6.4 Mounting...........................................................................................................46
7ELECTRICAL INSTALLATION...........................................................................48
7.1 Connection to Power Supply and control in system.....................................48
7.2 Pin configuration main board DIS-2 310/2 FB................................................51
7.2.1 Pin configuration Power supply and I/O [X1] ......................................................51
7.2.2 Pin configuration motor phases [X6]...................................................................53
7.2.3 Pin configuration Encoder Interface [X2]............................................................53
7.2.4 Pin configuration holding brake [X3]...................................................................55
7.2.5 Pin configuration brake resistor [X300]...............................................................55
7.2.6 Pin configration expansion interface for the fieldbus-modules [X8]....................56
7.3 Pin configuration fieldbus-modules DIS-2 310/2 FB......................................58
7.3.1 Pin configuration RS232 interface [X5]...............................................................58
7.3.2 Pin configuration CANopen [X401] and [X402]...................................................59
7.3.3 Pin configuration PROFIBUS [X401] and [X402]................................................60
7.3.4 Pin configuration EtherCAT [X401] and [X402] ..................................................61
7.4 Notes concerning safe and EMC-compliant installation...............................62
7.4.1 Definitions and terminology ................................................................................62
7.4.2 General information concerning EMC ................................................................62
7.4.3 EMC ranges: First and second environment ......................................................62
7.4.4 EMC-compliant cabling.......................................................................................63
7.5 EMERGENCY OFF / EMERGENCY STOP – terminology and standards ......63
7.6 EMERGENCY OFF / EMERGENCY STOP wiring examples...........................65
7.6.1 EMERGENCY OFF (stop category 0): ...............................................................67
8INITIAL OPERATION..........................................................................................68
8.1 General notes on connection..........................................................................68
8.2 Tools / material.................................................................................................68
8.3 Connecting the motor......................................................................................68
8.4 Connecting the servo positioning controller DIS-2 310/2 FB to the power
supply, control panel or plc ............................................................................68
8.5 Connecting the PC...........................................................................................69

Seite 6
Product Manual “Servo Positioning Controller DIS-2 310/2 FB“ Version 4.0
8.6 Checking operability........................................................................................69
9SERVICE FUNCTIONS AND ERROR MESSAGES...........................................70
9.1 Protection and service functions....................................................................70
9.1.1 Overview.............................................................................................................70
9.1.2 Overcurrent and short-circuit monitoring............................................................71
9.1.3 DC bus voltage monitoring .................................................................................71
9.1.4 Logic supply monitoring......................................................................................71
9.1.5 Heat sink temperature monitoring ......................................................................71
9.1.6 Motor monitoring.................................................................................................72
9.1.7 Motion sequence monitoring...............................................................................72
9.1.8 Additional internal monitoring functions..............................................................72
9.1.9 Operating hour meter..........................................................................................73
9.2 Error messages................................................................................................74

Seite 7
Product Manual “Servo Positioning Controller DIS-2 310/2 FB“ Version 4.0
TABLE OF FIGURE S:
Figure 1: Control scheme of the controller cascade ....................................................................37
Figure 2: Positioning control block diagram .................................................................................38
Figure 3: Driving profiles of servo positioning controller DIS-2 310/2 FB.....................................41
Figure 4: Course program............................................................................................................42
Figure 5: DIS-2 310/2 FB view into the housing – location of the connectors..............................43
Figure 6: DIS-2 dimensions of the housing..................................................................................45
Figure 7: DIS-2 310/2 FB mounting example – synchronous servo motor, mounting plate with
brake resistor and servo positioning controller DIS-2 310/2 FB....................................46
Figure 8: Example of a mounting plate for a motor......................................................................47
Figure 9: Connection to power supply, control and motor............................................................48
Figure 10: Connector and pin configuration [X1]............................................................................51
Figure 11: Pin configuration motor phases ....................................................................................53
Figure 12: Pin configuration Encoder Interface..............................................................................53
Figure 13: Pin configuration holding brake.....................................................................................55
Figure 14: Pin configuration brake resistor ....................................................................................55
Figure 15: Position and pin configuration technology module........................................................56
Figure 16: Position and pin configuration RS232 interface............................................................58
Figure 17: Position and pin configuration CAN interface ...............................................................59
Figure 18: Position and pin configuration Profibus interface..........................................................60
Figure 19: Position and pin configuration EtherCAT interface.......................................................61
Figure 20: Wiring example for the power supply and EMERGENCY OFF / EMERGENCY STOP66

Seite 8
Product Manual “Servo Positioning Controller DIS-2 310/2 FB“ Version 4.0
TABLE OF TABLES:
Table 1: Scope of supply DIS-2 310/2 FB CANopen.......................................................................11
Table 2: Scope of supply DIS-2 310/2 FB PROFIBUS ....................................................................11
Table 3: Scope of supply DIS-2 310/2 FB EtherCAT.......................................................................11
Table 4: Scope of supply DIS-2 310/2 FB........................................................................................11
Table 5: Technical data: Ambient conditions and qualification ........................................................27
Table 6: Technical data: Dimensions and weight.............................................................................27
Table 7: Technical data: Performance data [X1]..............................................................................28
Table 8: Technical data: Motor connection specifications [X6]........................................................28
Table 9: Technical data: Motor temperature monitoring [X2]...........................................................28
Table 10: Technical data: Resolver evaluation [X2]...........................................................................29
Table 11: Technical data: Evaluation of analogue Hall sensor signals [X2].......................................29
Table 12: Technical data: Evaluation of Six-Step-Sensors (Hall) and block commutation mode [X2]30
Table 13: Technical data: Evaluation of Incremental encoder [X2]....................................................30
Table 14: Technical data: Evaluation of HIPERFACE®Encoders [X2]..............................................30
Table 15: Technical data: RS232 [X5] ...............................................................................................31
Table 16: Technical data: Digital inputs and outputs [X1]..................................................................31
Table 17: Technical data: Analogue inputs and outputs [X1].............................................................32
Table 18: Technical data: Incremental encoder input [X1] (DIN4, DIN5, DIN6):................................32
Table 19: Technical data: Incremental encoder output [X1] (DOUT1, DOUT2): ...............................33
Table 20: Technical data: CAN-Bus [X401] / [X402]..........................................................................34
Table 21: Technical data: Profibus [X401] / [X402]............................................................................34
Table 22: Technical data: EtherCAT [X401] / [X402].........................................................................34
Table 23: Pin configuration [X1].........................................................................................................51
Table 24: Pin configuration [X6].........................................................................................................53
Table 25: Pin configuration [X2].........................................................................................................54
Table 26: Pin configuration [3] ...........................................................................................................55
Table 27: Pin configuration [X300].....................................................................................................55
Table 28: Pin configuration [X8].........................................................................................................56
Table 29: Pin configuration [X5].........................................................................................................58
Table 30: Pin assignment to set up an RS232 adapter cable for connection to a PC/notebook .......58
Table 31: Pin configuration [X401] and [X402]...................................................................................59
Table 32: Pin configuration [X401] and [X402]...................................................................................60

Seite 9
Product Manual “Servo Positioning Controller DIS-2 310/2 FB“ Version 4.0
Table 33: Pin configuration [X401] und [X402]...................................................................................61
Table 34: Description of the requirements for the categories in accordance with EN 954-1.............63
Table 35: EMERGENCY OFF and EMERGENCY STOP as per EN 60204-1...................................64
Table 36: Stop categories ..................................................................................................................65
Table 37: Error overview....................................................................................................................74

Seite 10
Product Manual “Servo Positioning Controller DIS-2 310/2 FB“ Version 4.0
1 General
1.1 Documentation
This product manual serves the purpose of a safe use of the DIS-2 310/2 FB series servo positioning
controller. It contains safety notes, which must be complied with.
Further information can be found in the following manuals of the DIS-2 310/2 FB product range:
“Mounting Instructions Decentral Intelligent Servo DIS-2 310/2 FB”: Instruction manual
concerning the installation of the DIS-2 310/2 FB servo positioning controller.
CANopen Manual “Servo Positioning Controller DIS-2“: Description of the implemented
CANopen protocol as per DSP402.
PROFIBUS Manual “Servo Positioning Controller DIS-2”: Description of the implemented
PROFIBUS-DP protocol.
EtherCAT Manual “ Servo Positioning Controller DIS-2”: Description of the implemented
EtherCAT protocol.
Software manual "Servo Positioning Controller DIS-2": Description of the device function-
ality and the software functions of the firmware including the RS232 communication. Descrip-
tion of the DIS-2 ServoCommander™ parameterisation program with instructions concerning
the start-up of DIS-2 servo positioning controllers.
All manuals are available for download on the Metronix website under www.metronix.de.
Further, the manuals are located on the CD ROM DIS-2 ServoCommander™.
The described functionality in this manual are based on the product step 3.3.

Seite 11
Product Manual “Servo Positioning Controller DIS-2 310/2 FB“ Version 4.0
1.2 Scope of supply
The DIS-2 310/2 FB is available in three different versions. The technology modules (CAN, Profibus,
EtherCAT) are factory integrated and not provided by an exchange by the users.
Table 1: Scope of supply DIS-2 310/2 FB CANopen
1x DIS-2 310/2 FB CANopen servo positioning controllers Metronix order no: 9019-3103-00
Table 2: Scope of supply DIS-2 310/2 FB PROFIBUS
1x DIS-2 310/2 FB PROFIBUS servo positioning controllers Metronix order no: 9019-3103-04
Table 3: Scope of supply DIS-2 310/2 FB EtherCAT
1x DIS-2 310/2 FB EtherCAT servo positioning controllers Metronix order no: 9019-3103-05
Counterplugs, control panel, line filter, cable for communication and brake chopper are not included in
the standard scope of supply. They can be ordered as accessories:
Table 4: Scope of supply DIS-2 310/2 FB
1x Connector set: DIS-2 310/2 FB Metronix order no: 9019-3120-00
Content: 1x 22-pin Phoenix connector, consist of:
VARICON mating connector, Sleeve
frame and sleeve housing
1x 16-pin mating connector for angle encod-
er, incl. crimp contacts from company
Molex
1x 2-pin mating connector for holding brake,
incl. crimp contacts from company JST
1x 5- pin mating connector for motor incl.
crimp contacts from company JST
1x Control panel DIS-2 310/2 FB Metronix order no: 9019-0330-00
1x External line filter
Necessary to fulfill the EMC regulations EN 61800-3
Metronix order no: 9504-0005

Seite 12
Product Manual “Servo Positioning Controller DIS-2 310/2 FB“ Version 4.0
1x RS232 connecting cable for DIS-2 310/2 FB
Assembled connecting cable for the controller parameter
configuration, length approx. 150 cm, M8 circular con-
nector for connection to the controller, DSUB 9-pin con-
nector for connection to the COM port of the PC.
Metronix order no: 9019-0221-00
1x Braking resistor for DIS-2 310/2 FB
Plate resistor assembled, company Metallux PLR
100.61.41, 100 Ω± 10%, 30 W continuous power, dimen-
sions 61 mm x 40,5 mm, height: approx. 1.5 mm, height
in the area of the connecting cable: 4 mm, with strands l =
105 mm + connector from company JST (VHR-2N and
contacts SVH-41T-P1.1)
Metronix order no: 9519-0002-00

Seite 13
Product Manual “Servo Positioning Controller DIS-2 310/2 FB“ Version 4.0
2 Safety notes for electrical drives and
controllers
2.1 Used symbols
Information
Important information and notes.
Caution!
Nonobservance may result in severe property damages.
DANGER!
Nonobservance may result in property damages and in personal injuries.
Caution! Dangerous voltages.
The safety note indicates a possible perilous voltage.
2.2 General notes
In case of damage resulting from non-compliance with the safety notes in this manual, Metronix
Meßgeräte und Elektronik GmbH will not assume any liability.
Prior to the initial use you must read the chapters 2Safety notes for electrical drives and
controllers and chapter 7.4 Notes concerning safe and EMC-compliant installation.
If the documentation in the language at hand is not understood accurately, please contact and inform
your supplier.
Sound and safe operation of the servo drive controller requires proper and professional transportation,
storage, assembly and installation as well as proper operation and maintenance. Only trained and
qualified personnel may handle electrical devices:

Seite 14
Product Manual “Servo Positioning Controller DIS-2 310/2 FB“ Version 4.0
TRAINED AND QUALIFIED PERSONNEL
in the sense of this product manual or the safety notes on the product itself are persons who are suffi-
ciently familiar with the project, the setup, assembly, commissioning and operation of the product as
well as all warnings and precautions as per the instructions in this manual and who are sufficiently
qualified in their field of expertise:
Education and instruction concerning the standards and accident prevention regulations for the
application, or authorisation to switch devices/systems on and off and to ground them as per the
standards of safety engineering and to efficiently label them as per the job demands.
Education and instruction as per the standards of safety engineering regarding the maintenance
and use of adequate safety equipment.
First aid training.
The following notes must be read prior to the initial operation of the system to prevent personal injuries
and/or property damages:
These safety notes must be complied with at all times.
Do not try to install or commission the servo drive controller before carefully reading all
safety notes for electrical drives and controllers contained in this document. These safety
instructions and all other user notes must be read prior to any work with the servo drive
controller.
In case you do not have any user notes for the servo drive controller, please contact your
sales representative. Immediately demand these documents to be sent to the person
responsible for the safe operation of the servo drive controller.
If you sell, rent and/or otherwise make this device available to others, these safety notes
must also be included.
The user must not open the servo drive controller for safety and warranty reasons.
Professional control process design is a prerequisite for sound functioning of the servo
drive controller!
DANGER!
Inappropriate handling of the servo drive controller and non-compliance of the
warnings as well as inappropriate intervention in the safety features may result in
property damage, personal injuries, electric shock or in extreme cases even death.

Seite 15
Product Manual “Servo Positioning Controller DIS-2 310/2 FB“ Version 4.0
2.2.1 Danger resulting from misuse
DANGER!
High electrical voltages and high load currents!
Danger to life or serious personal injury from electrical shock!
DANGER!
High electrical voltage caused by wrong connections!
Danger to life or serious personal injury from electrical shock!
DANGER!
Surfaces of device housing may be hot!
Risk of injury! Risk of burning!
DANGER!
Dangerous movements!
Danger to life, serious personal injury or property damage due to unintentional move-
ments of the motors!
2.3 Safety notes
2.3.1 General safety notes
The servo drive controller corresponds to IP20 class of protection as well as pollution
level 1. Make sure that the environment corresponds to this class of protection and pollu-
tion level.
Only use replacements parts and accessories approved by the manufacturer.
The devices must be connected to the mains supply as per EN regulations, so that they
can be cut off the mains supply by means of corresponding separation devices (e.g. main
switch, contactor, power switch).
The servo drive controller may be protected using an AC/DC sensitive 300mA fault cur-
rent protection switch (RCD = Residual Current protective Device).
Gold contacts or contacts with a high contact pressure should be used to switch the con-
trol contacts.
Preventive interference rejection measures should be taken for control panels, such as
connecting contactors and relays using RC elements or diodes.

Seite 16
Product Manual “Servo Positioning Controller DIS-2 310/2 FB“ Version 4.0
The safety rules and regulations of the country in which the device will be operated must
be complied with.
The environment conditions defined in the product documentation must be kept. Safety-
critical applications are not allowed, unless specifically approved by the manufacturer.
For notes on installation corresponding to EMC, please refer to chapter 7.4 Notes con-
cerning safe and EMC-compliant installation. The compliance with the limits required by
national regulations is the responsibility of the manufacturer of the machine or system.
The technical data and the connection and installation conditions for the servo drive con-
troller are to be found in this product manual and must be met.
DANGER!
The general setup and safety regulations for work on power installations (e.g. DIN, VDE,
EN, IEC or other national and international regulations) must be complied with.
Non-compliance may result in death, personal injury or serious property damages.
Without claiming completeness, the following regulations and others or standards apply:
VDE 0100 Regulations for the installation of high voltage (up to 1000 V) devices
EN 60204-1 Electrical equipment of machines
EN 50178 Electronic equipment for use in power installations
EN ISO 12100 Safety of machinery – Basic terminology, general principles for design
EN 1050 Safety of machinery – Principles for risk assessment
EN 1037 Safety of machinery – Prevention of unexpected start-up
EN 954-1 Safety-related parts of control systems

Seite 17
Product Manual “Servo Positioning Controller DIS-2 310/2 FB“ Version 4.0
2.3.2 Safety notes for assembly and maintenance
The appropriate DIN, VDE, EN and IEC regulations as well as all national and local safety regulations
and rules for the prevention of accidents apply for the assembly and maintenance of the system. The
plant engineer or the operator is responsible for compliance with these regulations:
The servo drive controller must only be operated, maintained and/or repaired by person-
nel trained and qualified for working on or with electrical devices.
Prevention of accidents, injuries and/or damages:
Additionally secure vertical axes against falling down or lowering after the motor has
been switched off, e.g. by means of:
Mechanical locking of the vertical axle,
External braking, catching or clamping devices or
Sufficient balancing of the axle.
The motor holding brake supplied by default or an external motor holding brake driven by
the drive controller alone is not suitable for personal protection!
Render the electrical equipment voltage-free using the main switch and protect it from
being switched on again until the DC bus circuit is discharged, in the case of:
Maintenance and repair work
Cleaning
long machine shutdowns
Prior to carrying out maintenance work make sure that the power supply has been turned
off, locked and the DC bus circuit is discharged.
The external or internal brake resistor carries dangerous DC bus voltages during opera-
tion. Contact may result in death or serious personal injury.
The servo drive controllers can carry voltage until up to 5 minutes after being switched off
(residual capacitor charge). Please wait this time until you work to implement appropriate
connections. For safety reasons, control the intermediate circuit by measurement. Con-
tact may result in death or serious personal injury.
Be careful during the assembly. During the assembly and also later during operation of
the drive, make sure to prevent drill chips, metal dust or assembly parts (screws, nuts,
cable sections) from falling into the device.
Also make sure that the external power supply of the controller (24V) is switched off.
The DC bus circuit or the mains supply must always be switched off prior to switching off
the 24V controller supply.

Seite 18
Product Manual “Servo Positioning Controller DIS-2 310/2 FB“ Version 4.0
Carry out work in the machine area only, if AC and/or DC supplies are switched off.
Switched off output stages or controller enablings are no suitable means of locking. In
the case of a malfunction the drive may accidentally be put into action.
Initial operation must be carried out with idle motors, to prevent mechanical damages
e.g. due to the wrong direction of rotation.
Electronic devices are never fail-safe. It is the user’s responsibility, in the case an electri-
cal device fails, to make sure the system is transferred into a secure state.
The servo drive controller and in particular the brake resistor, externally or internally, can
assume high temperatures, which may cause serious burns.
2.3.3 Protection against contact with electrical parts
This section only concerns devices and drive components carrying voltages exceeding 50 V. Contact
with parts carrying voltages of more than 50 V can be dangerous for people and may cause electrical
shock. During operation of electrical devices some parts of these devices will inevitably carry danger-
ous voltages.
DANGER!
High electrical voltage!
Danger to life, danger due to electrical shock or serious personal injury!
The appropriate DIN, VDE, EN and IEC regulations as well as all national and local safety regulations
and rules for the prevention of accidents apply for the assembly and maintenance of the system. The
plant engineer or the operator is responsible for compliance with these regulations:
Before switching on the device, install the appropriate covers and protections against
accidental contact. Rack-mounted devices must be protected against accidental contact
by means of a housing, e.g. a switch cabinet. The regulations VGB4 must be complied
with!
Always connect the ground conductor of the electrical equipment and devices securely to
the mains supply.
Comply with the minimum copper cross-section for the ground conductor over its entire
length as per EN60617!
Prior to the initial operation, even for short measuring or testing purposes, always con-
nect the ground conductor of all electrical devices as per the terminal diagram or connect
it to the ground wire. Otherwise the housing may carry high voltages which can cause
electrical shock.

Seite 19
Product Manual “Servo Positioning Controller DIS-2 310/2 FB“ Version 4.0
Do not touch electrical connections of the components when switched on.
Prior to accessing electrical parts carrying voltages exceeding 50 Volts, disconnect the
device from the mains or power supply. Protect it from being switched on again.
For the installation the amount of DC bus voltage must be considered, particularly re-
garding insulation and protective measures. Ensure proper grounding, wire dimensioning
and corresponding short-circuit protection.
2.3.4 Protection against electrical shock by means of protective extra-low
voltage (PELV)
All connections and terminals with voltages between 5 and 50 Volts at the servo drive controller are
protective extra-low voltage, which are designed safe from contact in correspondence with the follow-
ing standards:
International: IEC 60364-4-41
European countries within the EU: EN 50178/1998, section 5.2.8.1.
DANGER!
High electrical voltages due to wrong connections!
Danger to life, risk of injury due to electrical shock!
Only devices and electrical components and wires with a protective extra low voltage (PELV) may be
connected to connectors and terminals with voltages between 0 to 50 Volts.
Only connect voltages and circuits with protection against dangerous voltages. Such protection may be
achieved by means of isolation transformers, safe optocouplers or battery operation.
2.3.5 Protection against dangerous movements
Dangerous movements can be caused by faulty control of connected motors, for different reasons:
Improper or faulty wiring or cabling
Error in handling of components
Error in sensor or transducer
Defective or non-EMC-compliant components
Error in software in superordinated control system
These errors can occur directly after switching on the device or after an indeterminate time of opera-
tion.
The monitors in the drive components for the most part rule out malfunctions in the connected drives.
In view of personal protection, particularly the danger of personal injury and/or property damage, this

Seite 20
Product Manual “Servo Positioning Controller DIS-2 310/2 FB“ Version 4.0
may not be relied on exclusively. Until the built-in monitors come into effect, faulty drive movements
must be taken into account; their magnitude depends on the type of control and on the operating state.
DANGER!
Dangerous movements!
Danger to life, risk of injury, serious personal injuries or property damage!
For the reasons mentioned above, personal protection must be ensured by means of monitoring or
superordinated measures on the device. These are installed in accordance with the specific data of the
system and a danger and error analysis by the manufacturer. The safety regulations applying to the
system are also taken into consideration. Random movements or other malfunctions may be caused
by switching the safety installations off, by bypassing them or by not activating them.
2.3.6 Protection against contact with hot parts
DANGER!
Housing surfaces may be hot!
Risk of injury! Risk of burning!
Do not touch housing surfaces in the vicinity of heat sources! Danger of burning!
Before accessing devices let them cool down for 10 minutes after switching them off.
Touching hot parts of the equipment such as the housing, which contain heat sinks and
resistors, may cause burns!
2.3.7 Protection during handling and assembly
Handling and assembly of certain parts and components in an unsuitable manner may under adverse
conditions cause injuries.
DANGER!
Risk of injury due to improper handling!
Personal injury due to pinching, shearing, cutting, crushing!
The following general safety notes apply:
Other manuals for DIS-2 310/2 FB FS STO
3
Table of contents
Other Metronix Controllers manuals
Popular Controllers manuals by other brands
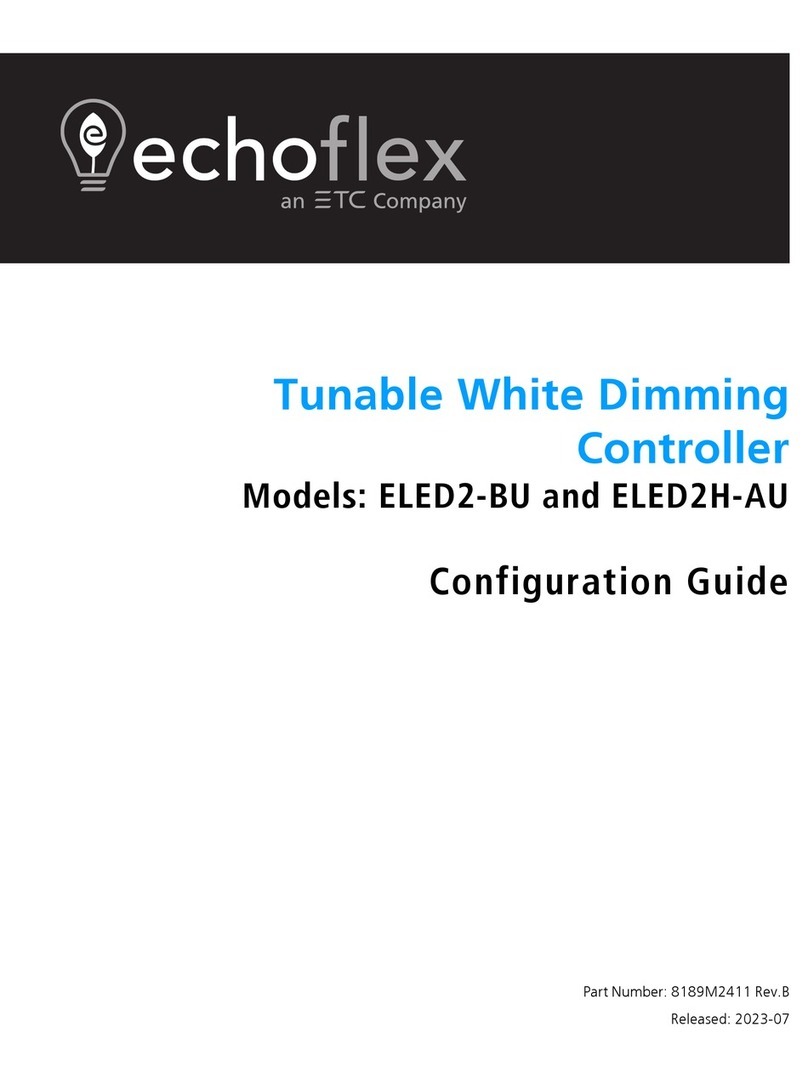
ETC
ETC Echoflex ELED2-BU Configuration guide
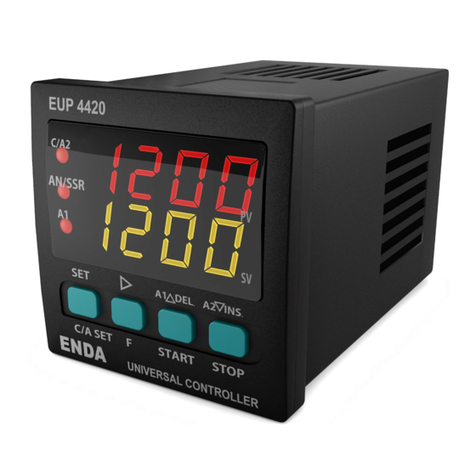
sisel
sisel ENDA EUP Series manual
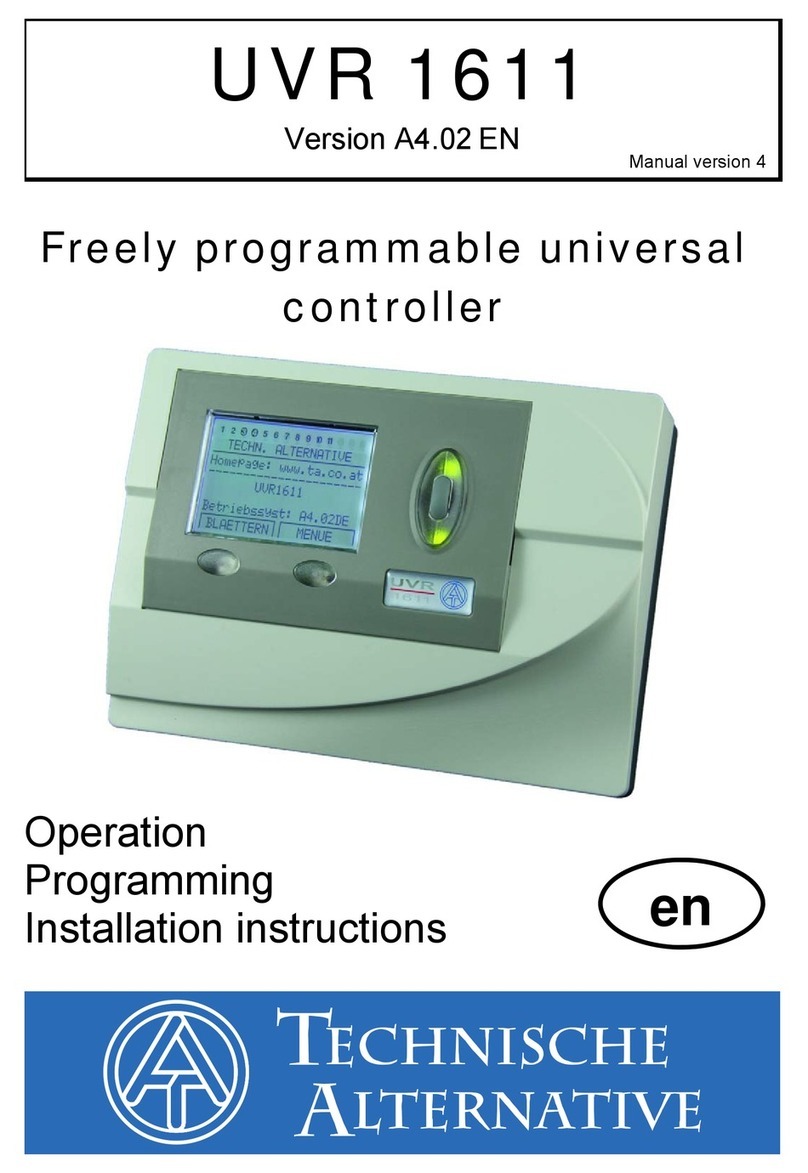
Technische Alternative
Technische Alternative uvr1611 Operation, Programming, Installation Instructions
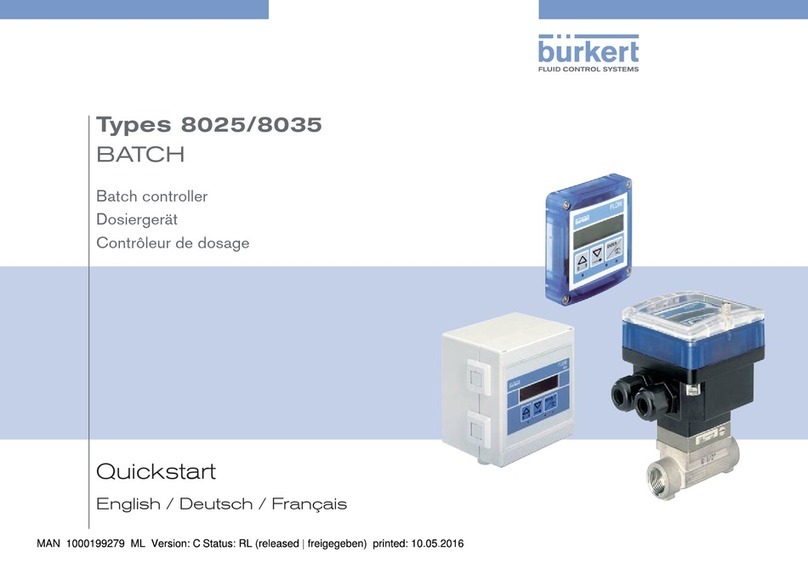
Burkert
Burkert 8025 BATCH quick start
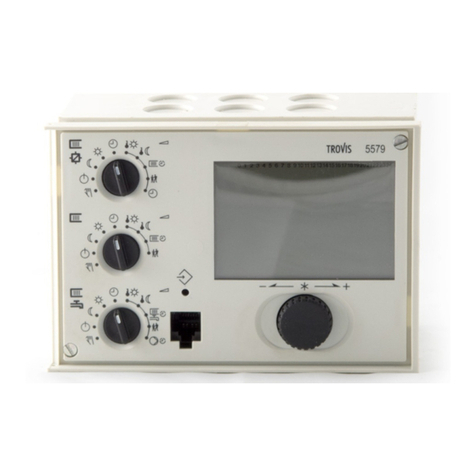
Samson
Samson TROVIS 5579 Mounting and operating instructions
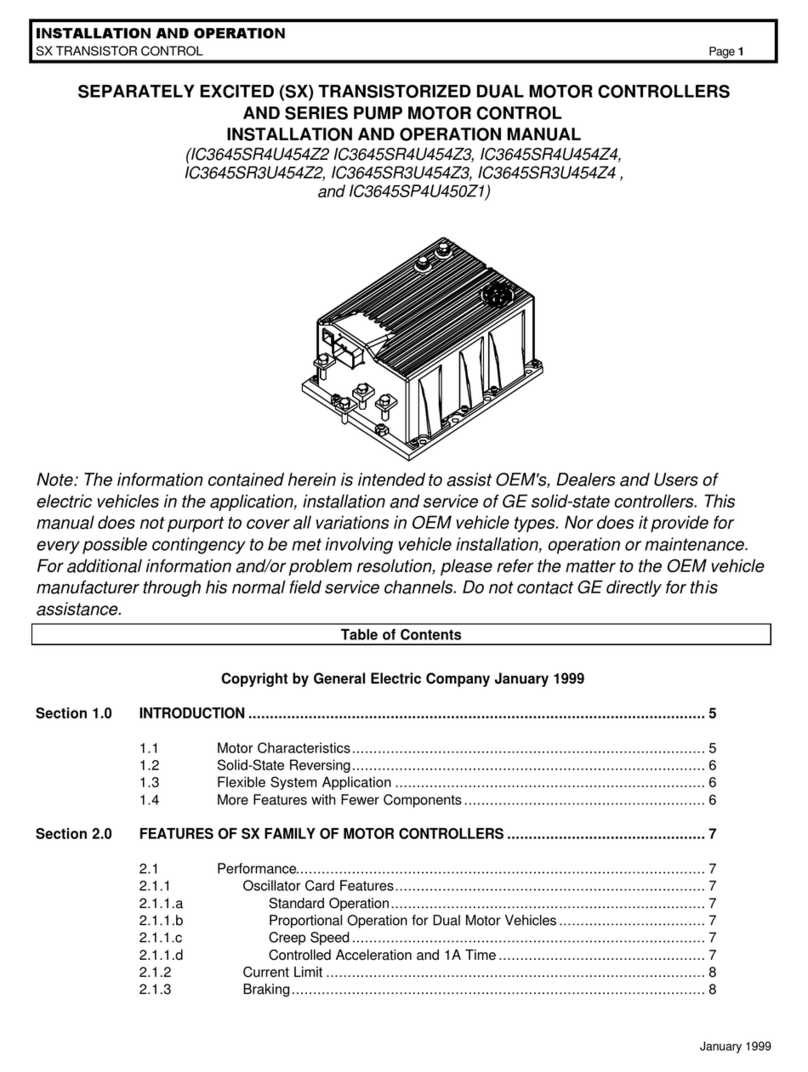
GE
GE IC3645SR4U454Z2 Installation and operation manual