Metronix DIS-2 48/10 FB FS STO User manual

Metronix Meßgeräte und Elektronik GmbH Telefon: +49-(0)531-8668-0
Kocherstraße 3 Telefax: +49-(0)531-8668-555
Germany http://www.metronix.de
Servo positioning controller
DIS-2 48/10 FB
PROFIBUS Manual

Page 2
PROFIBUS-Manual Servo positioning controller DIS-2 48/10 FB Version 2.0
Copyrights
2011 Metronix Meßgeräte und Elektronik GmbH. All rights reserved.
The information and data in this document have been composed to the best of our knowledge.
However, deviations between the document and the product cannot be excluded entirely. For the
devices and the corresponding software in the version handed out to the customer, Metronix
guarantees the contractual use in accordance with the user documentation. In the case of serious
deviations from the user documentation, Metronix has the right and the obligation to repair, unless it
would involve an unreasonable effort. A possible liability does not include deficiencies caused by
deviations from the operating conditions intended for the device and described in the user
documentation.
Metronix does not guarantee that the products meet the buyer’s demands and purposes or that they
work together with other products selected by the buyer. Metronix does not assume any liability for
damages resulting from the combined use of its products with other products or resulting from
improper handling of machines or systems.
Metronix Meßgeräte und Elektronik GmbH reserves the right to modify, amend, or improve the
document or the product without prior notification.
This document may, neither entirely nor in part, be reproduced, translated into any other natural or
machine-readable language nor transferred to electronic, mechanical, optical or any other kind of data
media, without expressive authorisation by the author.
Trademarks
Any product names in this document may be registered trademarks. The sole purpose of any
trademarks in this document is the identification of the corresponding products.
ServoCommander™ is a registered trademark of Metronix Meßgeräte und Elektronik GmbH.
Microsoft and Windows are either registered trademarks or trademarks of Microsoft Corporation in the
United States and/or other countries.

Seite 3
Revision Log
Author:
Metronix Meßgeräte und Elektronik GmbH
Manual:
PROFIBUS-Manual Servo positioning controller DIS-2 48/10 FB
File name:
Profi-HB_DIS-2_2p0_EN
No.
Description
Revision
index
Date of change
001
Creation
1.0
06th July 2006
002
Update Corporate Identity –No technical changes
2.0
02.05.2011

Page 4
PROFIBUS-Manual Servo positioning controller DIS-2 48/10 FB Version 2.0
Table of Contents
1General .............................................................................................................................................8
1.1 Documentation..........................................................................................................................8
1.2 PROFIBUS documentation .......................................................................................................8
2Safety notes for electrical drives and controllers ............................................................................10
2.1 Used symbols..........................................................................................................................10
2.2 General notes..........................................................................................................................11
2.3 Danger resulting from misuse.................................................................................................12
2.4 Safety notes ............................................................................................................................13
2.4.1 General safety notes ..................................................................................................13
2.4.2 Safety notes for assembly and maintenance .............................................................14
2.4.3 Protection against contact with electrical parts ..........................................................15
2.4.4 Protection against electrical shock by means of protective extra-low voltage (PELV)16
2.4.5 Protection against dangerous movements.................................................................17
2.4.6 Protection against contact with hot parts....................................................................17
2.4.7 Protection during handling and assembly...................................................................18
3Wiring and pin assignment .............................................................................................................19
3.1 Pin assignment........................................................................................................................19
3.2 PROFIBUS cable ....................................................................................................................19
3.3 Termination and bus terminating resistors..............................................................................20
4PROFIBUS-DP and PROFIdrive.....................................................................................................21
4.1 Overview of DP and its different versions ...............................................................................21
4.2 Basic functions of DP-V0 ........................................................................................................22
4.3 PROFIdrive overview ..............................................................................................................22
5PROFIBUS connection...................................................................................................................24
5.1 Introduction..............................................................................................................................24
5.2 Slave overview........................................................................................................................25
5.3 Master overview......................................................................................................................25
6Telegram editor...............................................................................................................................27
6.1 Introduction..............................................................................................................................27
6.2 Reception telegrams ...............................................................................................................27
6.3 Response telegrams ...............................................................................................................29
7Physical units..................................................................................................................................31
8Operating parameters.....................................................................................................................34
8.1 PROFIBUS operating parameters...........................................................................................34
9Device control .................................................................................................................................36
9.1 Overview .................................................................................................................................36
9.2 Control word 1.........................................................................................................................36
9.3 Status word 1 ..........................................................................................................................40
9.4 State diagram and device control............................................................................................42
9.4.1 State diagram.............................................................................................................43
9.4.2 Device control.............................................................................................................44

Page 5
PROFIBUS-Manual Servo positioning controller DIS-2 48/10 FB Version 2.0
9.4.3 Command overview....................................................................................................46
10 Manufacturer-specific parameter numbers.....................................................................................48
10.1Overview .................................................................................................................................48
10.2PNUs for positioning mode .....................................................................................................50
10.2.1 PNU 1000: Position Set Number................................................................................50
10.2.2 PNU 1001: Position Data............................................................................................50
10.2.3 PNU 1002: Start Set Number.....................................................................................52
10.2.4 PNU 1003: Position Profile Type................................................................................52
10.2.5 PNU 1050: Homing Method .......................................................................................53
10.2.6 PNU 1051: Home Offset.............................................................................................53
10.3PNUs for speed control mode.................................................................................................55
10.3.1 PNU 1010: Target Velocity.........................................................................................55
10.3.2 PNU 1011: Accelerations for Velocity Control............................................................55
10.4PNUs for Different Operating Modes ......................................................................................57
10.4.1 PNU 1022: Current Limitiation....................................................................................57
10.4.2 PNU 1040: Jogging ....................................................................................................58
10.4.3 PNU 1290: Motor Data...............................................................................................58
10.4.4 PNU 1350: Enable Logic............................................................................................59
10.5Actual values...........................................................................................................................60
10.5.1 PNU 1100: Position Actual Value...............................................................................60
10.5.2 PNU 1101: Velocity Actual Value ...............................................................................60
10.5.3 PNU 1102: Current Actual Value................................................................................61
10.5.4 PNU 1140: Digital Outputs .........................................................................................61
10.5.5 PNU 1141: Digital Inputs............................................................................................61
10.6Parameters for the telegram structure....................................................................................62
10.6.1 PNU 2000: PKW Access............................................................................................62
10.6.2 PNU 2010: Placeholders............................................................................................63
10.6.3 PNU 2011: Element 0.................................................................................................64
10.7Parameter for Various Intents.................................................................................................65
10.7.1 PNU 1601: Last Error Code .......................................................................................65
10.7.2 PNU 1610: Error Managment.....................................................................................66
11 Operating modes ............................................................................................................................67
11.1Overview .................................................................................................................................67
11.2Parameters..............................................................................................................................67
11.2.1 PNU 1500: Operating Mode.......................................................................................67
11.3Speed control mode................................................................................................................68
11.4Positioning mode.....................................................................................................................68
12 Profile-specific parameter numbers................................................................................................70
12.1Overview .................................................................................................................................70
12.2PNU description ......................................................................................................................70
12.2.1 PNU 971: Transfer into a Non-Volatile Memory.........................................................70
13 Function and data blocks for SIEMENS S7....................................................................................71
13.1Overview .................................................................................................................................71
13.2Function and data blocks for DIS-2 48/10 FB servo positioning controllers............................72
13.2.1 Function block (FB) overview.....................................................................................72
13.2.2 FBs of DIS-2 48/10 FB servo positioning controllers..................................................73
13.2.2.1 FB_position (FB 41 positioning mode) ............................................................73
13.2.2.2 FB_velocity (FB 43 speed control) ..................................................................76
13.2.3 Integration of FBs and DBs ........................................................................................77
13.2.4 PROFIBUS connection of DIS-2 48/10 FB servo positioning controller.....................80
13.2.4.1 Reception telegram of the speed control example project..............................................80

Page 6
PROFIBUS-Manual Servo positioning controller DIS-2 48/10 FB Version 2.0
13.2.4.2 Reception telegram of the positioning example project ..................................................82
13.2.4.3 Response telegram for the example projects .................................................................83
13.2.5 Creating an S7 program.............................................................................................84
13.2.6 Integrating the GSD file..............................................................................................84
13.2.7 Hardware configuration ..............................................................................................85
13.2.8 Integrating the servo positioning controller.................................................................86
13.2.9 Overview of function and data blocks:........................................................................87

Page 7
PROFIBUS-Manual Servo positioning controller DIS-2 48/10 FB Version 2.0
List of Figures
Figure 3.1: PROFIBUS connector for DIS-2 48/10 FB 19
Figure 5.1: Example of the telegram format for the DIS-2 48/10 FB 24
Figure 5.2: Hardware configuration under SIEMENS S7 26
Figure 6.1: Composition of a reception telegram 28
Figure 6.2: Composition of a response telegram 30
Figure 7.1: Setting of physical units 31
Figure 7.2: Gear ratio 32
Figure 8.1: Setting of operating parameters 34
Figure 9.1: Simplified state diagram 43
Figure 10.1: Interpretation of the home offset 54
Figure 11.1: Uninterrupted sequence of motion tasks 69

Page 8 General
PROFIBUS-Manual Servo positioning controller DIS-2 48/10 FB Version 2.0
1 General
1.1 Documentation
This manual describes the field bus connection of DIS-2 48/10 FB servo positioning controllers under
PROFIBUS-DP. It describes the adjustment of the physical parameters, the activation of the
PROFIBUS communication, the integration into the master connection and the communication with the
servo positioning controller. It is intended for persons who are familiar with this servo positioning
controller model.
It contains safety notes which have to be complied with.
Further information can be found in the following manual:
User Manual “DIS-2 48/10, DIS-2 48/10 IC, DIS-2 48/10 FB”: Description of the device
functionality and the software functions of the firmware including RS232 communication.
Description of the DIS-2 ServoCommander™ parameterisation program with instructions
concerning the start-up of DIS-2 48/10 servo positioning controllers and description of the technical
specifications and the device functionality as well as notes on the installation and the operation of
the servo positioning controller DIS-2 48/10.
1.2 PROFIBUS documentation
PROFIBUS (PROcess FIeldBUS) is a standard defined by the German association of PROFIBUS
users (PROFIBUS Nutzerorganisation e.V.). A complete description of the field bus system can be
found in the following standard:
IEC 61158 „Digital data communication for measurement and control – Fieldbus for use in
industrial control systems“: This standard is divided into several parts and defines 10 “Fieldbus
Protocol Types”. Among these types, PROFIBUS is specified as type 3. PROFIBUS comes in two
versions. One is PROFIBUS-DP for quick data exchange in production and building automation (DP =
decentralized peripherals). The standard also describes the integration of the system into the ISO/OSI
network model.
Further information, contact addresses etc. can be found under www.profibus.com.

General Page 9
PROFIBUS-Manual Servo positioning controller DIS-2 48/10 FB Version 2.0
Further documentation (in German) concerning the use of PROFIBUS-DP:
1. PROFIBUS-DP
Grundlagen, Tips und Tricks für Anwender
Manfred Popp
Hüthig-Verlag, Heidelberg 1998
2. Dezentralisieren mit PROFIBUS-DP
Aufbau, Projektierung und Einsatz des PROFIBUS-DP mit Simatic S7
Josef Weigmann, Gerhard Kilian
Siemens, Erlangen/München 1998
3. Der neue Schnelleinstieg für PROFIBUS DP
Von DP-V0 bis DP-V2
Manfred Popp
PROFIBUS Nutzerorganisation e.V., Karlsruhe 2002
4. PROFIdrive –Profile Drive Technology,
Vers. 3.1,
PROFIBUS Nutzerorganisation e.V., Karlsruhe
5. IEC 61158 - Feldbus für industrielle Leitsysteme

Page 10 Safety notes for electrical drives and controllers
PROFIBUS-Manual Servo positioning controller DIS-2 48/10 FB Version 2.0
2 Safety notes for electrical drives
and controllers
2.1 Used symbols
Information
Important information and notes.
Caution!
Nonobservance may result in severe property damages.
DANGER!
Nonobservance may result in property damages and in personal injuries.
Caution! Dangerous voltages.
The safety note indicates a possible perilous voltage.

Safety notes for electrical drives and controllers Page 11
PROFIBUS-Manual Servo positioning controller DIS-2 48/10 FB Version 2.0
2.2 General notes
In the case of damage resulting from non-compliance of the safety notes in this manual
Metronix Meßgeräte und Elektronik GmbH will assume any liability.
If the documentation in the language at hand is not understood accurately, please contact and inform
your supplier.
Sound and safe operation of the servo drive controller requires proper and professional transportation,
storage, assembly and installation as well as proper operation and maintenance. Only trained and
qualified personnel may handle electrical devices:
TRAINED AND QUALIFIED PERSONAL
in the sense of this product manual or the safety notes on the product itself are persons who are
sufficiently familiar with the setup, assembly, commissioning and operation of the product as well as all
warnings and precautions as per the instructions in this manual and who are sufficiently qualified in
their field of expertise:
Education and instruction or authorisation to switch devices/systems on and off and to ground
them as per the standards of safety engineering and to efficiently label them as per the job
demands.
Education and instruction as per the standards of safety engineering regarding the maintenance
and use of adequate safety equipment.
First aid training.
The following notes must be read prior to the initial operation of the system to prevent personal injuries
and/or property damages:
These safety notes must be complied with at all times.
Do not try to install or commission the servo drive controller before carefully reading all
safety notes for electrical drives and controllers contained in this document. These safety
instructions and all other user notes must be read prior to any work with the servo drive
controller.
In case you do not have any user notes for the servo drive controller, please contact your
sales representative. Immediately demand these documents to be sent to the person
responsible for the safe operation of the servo drive controller.
If you sell, rent and/or otherwise make this device available to others, these safety notes
must also be included.

Page 12 Safety notes for electrical drives and controllers
PROFIBUS-Manual Servo positioning controller DIS-2 48/10 FB Version 2.0
The user must not open the servo drive controller for safety and warranty reasons.
Professional control process design is a prerequisite for sound functioning of the servo
drive controller!
DANGER!
Inappropriate handling of the servo drive controller and non-compliance of the
warnings as well as inappropriate intervention in the safety features may result in
property damage, personal injuries, electric shock or in extreme cases even death.
2.3 Danger resulting from misuse
DANGER!
High electrical voltages and high load currents!
Danger to life or serious personal injury from electrical shock!
DANGER!
High electrical voltage caused by wrong connections!
Danger to life or serious personal injury from electrical shock!
DANGER!
Surfaces of device housing may be hot!
Risk of injury! Risk of burning!
DANGER!
Dangerous movements!
Danger to life, serious personal injury or property damage due to unintentional
movements of the motors!

Safety notes for electrical drives and controllers Page 13
PROFIBUS-Manual Servo positioning controller DIS-2 48/10 FB Version 2.0
2.4 Safety notes
2.4.1 General safety notes
The servo drive controller corresponds to IP54 class of protection as well as pollution
level 1. Make sure that the environment corresponds to this class of protection and
pollution level.
Only use replacements parts and accessories approved by the manufacturer.
The devices must be connected to the mains supply as per EN regulations, so that they
can be cut off the mains supply by means of corresponding separation devices (e.g. main
switch, contactor, power switch).
Gold contacts or contacts with a high contact pressure should be used to switch the
control contacts.
Preventive interference rejection measures should be taken for control panels, such as
connecting contactors and relays using RC elements or diodes.
The safety rules and regulations of the country in which the device will be operated must
be complied with.
The environment conditions defined in the product documentation must be kept. Safety-
critical applications are not allowed, unless specifically approved by the manufacturer.
For notes on installation corresponding to EMC, please refer to User Manual of the servo
positioning controller DIS-2 48/10 FB. The compliance with the limits required by national
regulations is the responsibility of the manufacturer of the machine or system.
The technical data and the connection and installation conditions for the servo drive
controller are to be found in this product manual and must be met.
DANGER!
The general setup and safety regulations for work on power installations (e.g. DIN, VDE,
EN, IEC or other national and international regulations) must be complied with.
Non-compliance may result in death, personal injury or serious property damages.

Page 14 Safety notes for electrical drives and controllers
PROFIBUS-Manual Servo positioning controller DIS-2 48/10 FB Version 2.0
Without claiming completeness, the following regulations and others apply:
VDE 0100Regulations for the installation of high voltage (up to 1000 V) devices
EN 60204 Electrical equipment of machines
EN 50178 Electronic equipment for use in power installations
2.4.2 Safety notes for assembly and maintenance
The appropriate DIN, VDE, EN and IEC regulations as well as all national and local safety regulations
and rules for the prevention of accidents apply for the assembly and maintenance of the system. The
plant engineer or the operator is responsible for compliance with these regulations:
The servo drive controller must only be operated, maintained and/or repaired by
personnel trained and qualified for working on or with electrical devices.
Prevention of accidents, injuries and/or damages:
Additionally secure vertical axes against falling down or lowering after the motor has
been switched off, e.g. by means of:
Mechanical locking of the vertical axle,
External braking, catching or clamping devices or
Sufficient balancing of the axle.
The motor holding brake supplied by default or an external motor holding brake driven by
the drive controller alone is not suitable for personal protection!
Render the electrical equipment voltage-free using the main switch and protect it from
being switched on again until the DC bus circuit is discharged, in the case of:
Maintenance and repair work
Cleaning
long machine shutdowns
Prior to carrying out maintenance work make sure that the power supply has been turned
off, locked and the DC bus circuit is discharged.
Be careful during the assembly. During the assembly and also later during operation of
the drive, make sure to prevent drill chips, metal dust or assembly parts (screws, nuts,
cable sections) from falling into the device.

Safety notes for electrical drives and controllers Page 15
PROFIBUS-Manual Servo positioning controller DIS-2 48/10 FB Version 2.0
Also make sure that the external power supply of the controller (24V) is switched off.
The DC bus circuit or the mains supply must always be switched off prior to switching off
the 24V controller supply.
Carry out work in the machine area only, if AC and/or DC supplies are switched off.
Switched off output stages or controller enablings are no suitable means of locking. In
the case of a malfunction the drive may accidentally be put into action.
Initial operation must be carried out with idle motors, to prevent mechanical damages
e.g. due to the wrong direction of rotation.
Electronic devices are never fail-safe. It is the user’s responsibility, in the case an
electrical device fails, to make sure the system is transferred into a secure state.
The servo drive controller and in particular the brake resistor, externally or internally, can
assume high temperatures, which may cause serious burns.
2.4.3 Protection against contact with electrical parts
This section only concerns devices and drive components carrying voltages exceeding 50 V. Contact
with parts carrying voltages of more than 50 V can be dangerous for people and may cause electrical
shock. During operation of electrical devices some parts of these devices will inevitably carry
dangerous voltages.
DANGER!
High electrical voltage!
Danger to life, danger due to electrical shock or serious personal injury!
The appropriate DIN, VDE, EN and IEC regulations as well as all national and local safety regulations
and rules for the prevention of accidents apply for the assembly and maintenance of the system. The
plant engineer or the operator is responsible for compliance with these regulations:
Before switching on the device, install the appropriate covers and protections against
accidental contact. Rack-mounted devices must be protected against accidental contact
by means of a housing, e.g. a switch cabinet. The regulations VBG 4 must be complied
with!

Page 16 Safety notes for electrical drives and controllers
PROFIBUS-Manual Servo positioning controller DIS-2 48/10 FB Version 2.0
Always connect the ground conductor of the electrical equipment and devices securely to
the mains supply. Due to the integrated line filter the leakage current exceeds 3.5 mA!
Comply with the minimum copper cross-section for the ground conductor over its entire
length as per EN60617!
Prior to the initial operation, even for short measuring or testing purposes, always
connect the ground conductor of all electrical devices as per the terminal diagram or
connect it to the ground wire. Otherwise the housing may carry high voltages which can
cause electrical shock.
Do not touch electrical connections of the components when switched on.
Prior to accessing electrical parts carrying voltages exceeding 50 Volts, disconnect the
device from the mains or power supply. Protect it from being switched on again.
For the installation the amount of DC bus voltage must be considered, particularly
regarding insulation and protective measures. Ensure proper grounding, wire
dimensioning and corresponding short-circuit protection.
2.4.4 Protection against electrical shock by means of protective extra-low
voltage (PELV)
All connections and terminals with voltages between 5 and 50 Volts at the servo drive controller are
protective extra-low voltage, which are designed safe from contact in correspondence with the
following standards:
International: IEC 60364-4-41
European countries within the EU: EN 50178/1998, section 5.2.8.1.
DANGER!
High electrical voltages due to wrong connections!
Danger to life, risk of injury due to electrical shock!
Only devices and electrical components and wires with a protective extra low voltage (PELV) may be
connected to connectors and terminals with voltages between 0 to 50 Volts.
Only connect voltages and circuits with protection against dangerous voltages. Such protection may be
achieved by means of isolation transformers, safe optocouplers or battery operation.

Safety notes for electrical drives and controllers Page 17
PROFIBUS-Manual Servo positioning controller DIS-2 48/10 FB Version 2.0
2.4.5 Protection against dangerous movements
Dangerous movements can be caused by faulty control of connected motors, for different reasons:
Improper or faulty wiring or cabling
Error in handling of components
Error in sensor or transducer
Defective or non-EMC-compliant components
Error in software in superordinated control system
These errors can occur directly after switching on the device or after an indeterminate time of
operation.
The monitors in the drive components for the most part rule out malfunctions in the connected drives.
In view of personal protection, particularly the danger of personal injury and/or property damage, this
may not be relied on exclusively. Until the built-in monitors come into effect, faulty drive movements
must be taken into account; their magnitude depends on the type of control and on the operating state.
DANGER!
Dangerous movements!
Danger to life, risk of injury, serious personal injuries or property damage!
For the reasons mentioned above, personal protection must be ensured by means of monitoring or
superordinated measures on the device. These are installed in accordance with the specific data of the
system and a danger and error analysis by the manufacturer. The safety regulations applying to the
system are also taken into consideration. Random movements or other malfunctions may be caused
by switching the safety installations off, by bypassing them or by not activating them.
2.4.6 Protection against contact with hot parts
DANGER!
Housing surfaces may be hot!
Risk of injury! Risk of burning!
Do not touch housing surfaces in the vicinity of heat sources! Danger of burning!
Before accessing devices let them cool down for 10 minutes after switching them off.

Page 18 Safety notes for electrical drives and controllers
PROFIBUS-Manual Servo positioning controller DIS-2 48/10 FB Version 2.0
Touching hot parts of the equipment such as the housing, which contain heat sinks and
resistors, may cause burns!
2.4.7 Protection during handling and assembly
Handling and assembly of certain parts and components in an unsuitable manner may under adverse
conditions cause injuries.
DANGER!
Risk of injury due to improper handling!
Personal injury due to pinching, shearing, cutting, crushing!
The following general safety notes apply:
Comply with the general setup and safety regulations on handling and assembly.
Use suitable assembly and transportation devices.
Prevent incarcerations and contusions by means of suitable protective measures.
Use suitable tools only. If specified, use special tools.
Use lifting devices and tools appropriately.
If necessary, use suitable protective equipment (e.g. goggles, protective footwear,
protective gloves).
Do not stand underneath hanging loads.
Remove leaking liquids on the floor immediately to prevent slipping.

Wiring and pin assignment Page 19
PROFIBUS-Manual Servo positioning controller DIS-2 48/10 FB Version 2.0
3 Wiring and pin assignment
3.1 Pin assignment
The PROFIBUS interface in the servo positioning controller DIS-2 48/10 FB is in accordance with EN
50170 as 5-pin M12 plug (b-codes, at the technology plug-in module, as socket and as plug)
pin
color of conductor
Signal Profibus
1
-
+5V
2
green
A-line
3
-
0V
4
red
B-line
5
-
shield
Figure 3.1: PROFIBUS connector for DIS-2 48/10 FB
PROFIBUS wiring
Because of the very high baud rates we recommend using standardized cables and
connectors. They offer additional diagnose functionalities and facilitate rapid analysis of
the field bus hardware in the event of malfunctions.
When setting up the PROFIBUS network, compliance with the information given in the
standard literature and the following information and notes is strongly recommended in
order to obtain a stable, trouble-free system. Improper wiring may lead to problems
with the PROFIBUS causing the servo positioning controller to automatically deactivate
itself while signalling an error.
3.2 PROFIBUS cable
PROFIBUS cable:
Bus cable PROFIBUS: Socket straight, shielded M12-B-codiert, 2-pole
Pin straight, shielded M12-B-codiert, 2-pole

Page 20 Wiring and pin assignment
PROFIBUS-Manual Servo positioning controller DIS-2 48/10 FB Version 2.0
Manufacturer: Phoenix Contact
order number:
length in m
15 18 10 6
0,3
15 18 11 9
0,5
15 18 12 2
1
15 18 13 5
2
15 18 14 8
5
15 18 15 1
10
15 18 16 4
15
3.3 Termination and bus terminating resistors
Every bus segment of the PROFIBUS network has to be equipped with bus terminating resistors to
minimize line reflections, to guarantee practically constant load behaviour on the bus and to adjust a
defined rest potential on the line. Termination has to be provided at the beginning and at the end of
every bus segment.
The terminating resistors of the PROFIBUS module of the servo positioning controller DIS-2 48/10 FB
are already integrated in the module so that external connections (special connectors) are not required.
The terminating resistors can be activated by setting the two DIP switches on the module (switches set
to ON).Due to the high class of protection of the servo positioning controller DIS-2 48/10 FB the
terminating resistors can not served from outside. To switch on/off the terminating resistors is only
possible, if the servo positioning controller DIS-2 48/10 FB is removed from the motor.
Therefore a terminal resistance in form of a M12 of plug is recommended to use.
Bus terminating resistors
The DIP switches for activating the bus terminating resistors are already integrated on
the technological modules.
External connection is also possible. The power supply of 5 V required for the externally connected
terminating resistors is supplied to the PROFIBUS connector of the module (see pin assignment).
Faulty or improper bus termination is the most common cause of errors in the event of
malfunctions.
If the adjusted baud rate is > 1.5 MBaud, connectors with integrated line inductors (110 nH) have to be
used because of the capacitive load of the device and the resulting line reflections.
Other manuals for DIS-2 48/10 FB FS STO
2
Table of contents
Other Metronix Controllers manuals
Popular Controllers manuals by other brands
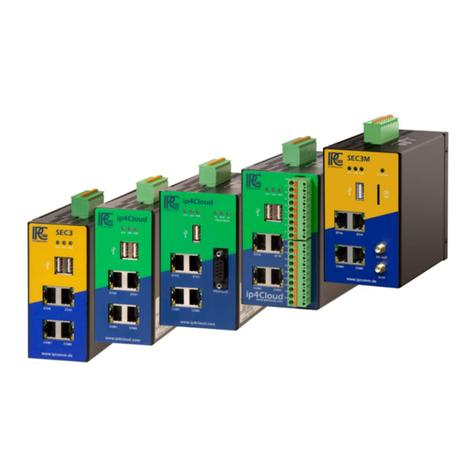
IPCOMM
IPCOMM SEC3M General Operating, Maintenance, and Installation Manual
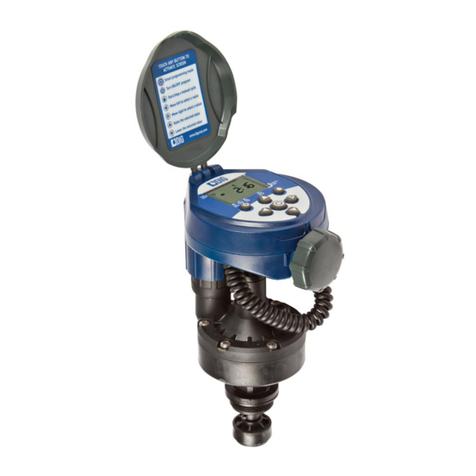
DIG
DIG RBC MVA instruction manual
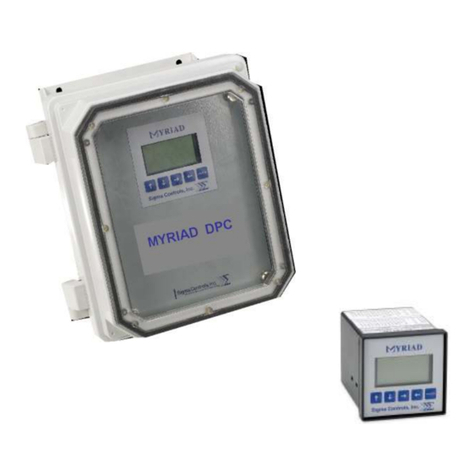
Sigma Controls
Sigma Controls MYRIAD DPC instruction manual
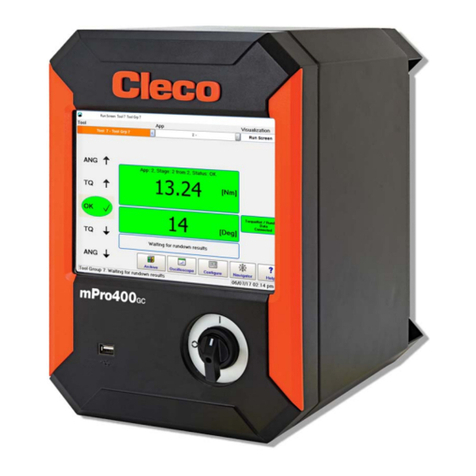
Cleco
Cleco mPro400GCD-P Hardware description
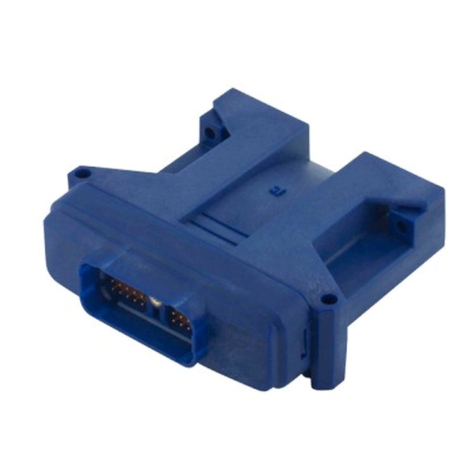
Danfoss
Danfoss PLUS+1 SC0XX-1 Series technical information
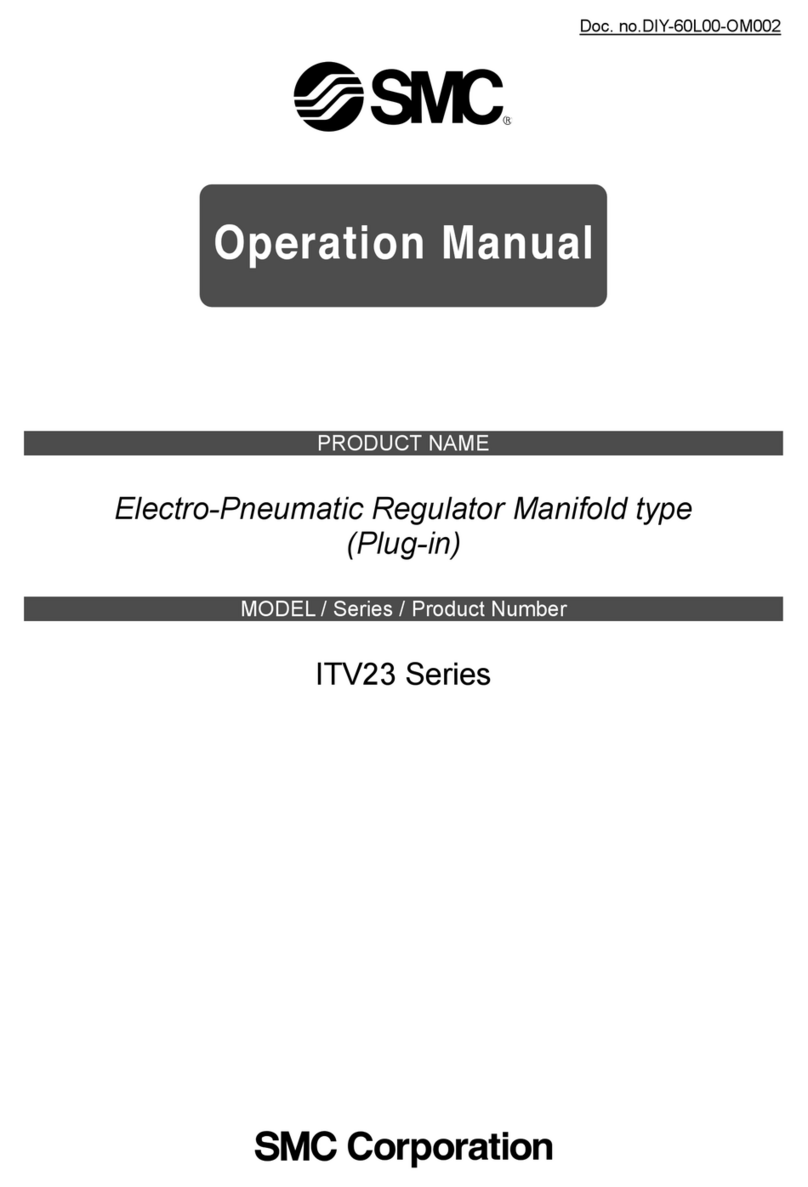
SMC Networks
SMC Networks ITV23 Series Operation manual