Mira Coda Operation manual

1
Installation & User Guide
MIRA CODA
These instructions are to be left with the user
THERMOSTATIC SHOWER
VALVE

2
PATENTAPPLICATION GB 2 407 138A

3
SPECIFICATIONS
Notes
1. The installation, commissioning and maintenance must be carried out in
accordance with instructions supplied by the manufacturer, and be installed by
qualified or competent persons.
2. Installations must comply with the requirements of UK Water Regulations/Bye-
laws(Scotland),BuildingRegulationsor anyparticularregulations andpractices,
specified by the local water supplier.
3. The Mira Coda is supplied and designed to operate with Mira L11 shower
fittings.
Pressure Range
• Minimum maintained pressure: 0.2 bar (2.0 metre head) when used with Mira
L11 shower fittings.
• Maximum maintained pressure: 5.0 bar.
• Maximum static pressure: 10 bar.
Note! Nominally equal inlet supply pressure are recommended for optimum
performance.
Temperature Control
• Close temperature control is provided between 20°C and 50°C.
Note! The temperature control specification, outlined below, is achieved with the
blend between 35°C and 45°C, with supply temperatures of 15°C cold and 65°C
hot, AND, nominally equal inlet supply pressures.
• The blended temperature is maintained within 2°C with a 10°C change in the
hot or cold supply.
• The wax capsule sensor effects a shut down to seepage in approximately
5 seconds if the cold supply fails. Shut down to seepage is only achieved if
the hot supply is 10°C above the blend temperature.
• Minimum hot water supply temperature: 55°C
• Maximum hot water supply temperature: 90°C for short periods.
• BS6700recommendsthat thetemperatureofstored watershouldneverexceed
65°C. A stored water temperature of 60°C is considered sufficient to meet all
normal requirements and will minimise the deposition of scale in hard water
areas.

4
INSTALLATION
General
1. Theinstallation,commissioning and maintenance must becarriedoutaccording
to instructions supplied, and must be conducted by qualified or competent
person.
2. Before starting installation, ensure that all site requirements correspond to
information given in the SPECIFICATION section.
3. DO NOT install product in a position where it could become frozen.
4. Install in a position with easy access for maintenance.
5. Accessible isolating valves MUST be provided for maintenance.
6. The supply pipework MUST be thoroughly flushed to remove any debris before
connection.
7. The hot water supply must be connected to left inlet (next to the flow selector).
This shower does not allow for reversed inlets.
8. Installations must comply with the requirements of UK Water Regulations/Bye-
laws(Scotland), BuildingRegulationsorany particularregulationsand practices,
specified by the local water supplier.
9. No form of outlet flow control should be fitted. Only use L11 shower fittings
recommended by the manufacturer/supplier.
10. Do not install the shower control in a position that restricts service access. A
minimum distance of 150mm is required between the hot and any side wall.
11. Do not use excessive force when making connection.
12. Thesuppliedwall mounting bracket must beusedfor stud partition or laminated
panel walls to ensure the valve is fully supported.

5
Solid Wall Installation
For installation onto a stud partition or laminated panel wall, or onto unfixed rear-
entry pipework, refer to the next section: Stud Partition, Laminated Panel, or
Unfixed Rear-entry Pipework Installation.
1. Make sure that the pipework is set
at the correct distance apart and
solidly fixed as this supports the
valve. Applysuitablethreadsealant
(not supplied) and attach the offset
connectors to the pipework in the
wall.
2. Tighten the offset connectors using
a spanner on the flats. Make sure
that the connectors are level and set
at the correct distance apart when
tightened.
3. Screw the concealing plates onto
theoffsetconnectorsuntiltheycome
into contact with the wall. Seal with
an appropriate sealant.
Pipework
Offset Connector
Wall
Spanner Flats
Offset Connectors
1/2" BSP Female
Connector
150mm
150mm

6
Caution! Ensure supply pipework is
flushed before installing the shower
valve.
4. Assemble the shower valve with a
sealing washer in each inlet and
attach to the offset connectors.
5. Tighten the nuts using a suitable
spanner.
6. Connect the shower fittings to the
shower valve outlet.
7. Turnon thewatersupplies andcheck
for leaks at all pipe connections.
Stud Partition, Laminated Panel, or Unfixed Rear-entry Pipework Installation
1. Screw the mounting bracket onto the
offset connectors.
2. Themountingbracketmustextendin
thesamedirectionas the offsetof the
offset connector. The angle between
theoffsetconnectorandthemounting
bracket must be less than 45°.
Otherwise, the mounting bracket will
not fit under the concealing plate.
3. The mounting bracket boss should
protrude to the rear, facing the wall.
Sealing Washer
Shower Valve
Shower Valve Outlet
Wall Mounting Bracket
Offset Connector
Mounting Bracket
Offset Connector
Offset Connector
Wall
Mounting Bracket
Boss
45°
45°

7
4. Apply suitable thread sealant (not
supplied) and attach the offset
connectors to the pipework in the
wall. Make sure that the connectors
are level and set at the correct
distance apart.
5. Tightentheconnectiontothepipework
whileholdingtheoffsetconnectors in
placeusing aspanneronthespanner
flats.
6. Fix the mounting bracket to the wall
through the small hole, using the
appropriate wall fixings for the type
of wall (not included).
7. Screw the concealing plates onto
the offset connectors until they come
into contact with the wall. Seal with
an appropriate sealant.
Mounting Bracket
Pipework Offset
Connector
Wall
Spanner Flats
Small Fixing Hole
Concealing Plates

8
Caution! Ensure supply pipework is
flushed before installing the shower
valve.
8. Assemble the shower valve with a
sealing washer in each inlet and
attach to the offset connectors.
9. Tighten the nuts using a suitable
spanner.
10. Connect the shower fittings to the
shower valve outlet.
11. Turnon the watersuppliesandcheck
for leaks at all pipe connections.
Setting the Maximum Temperature
The Mira Coda Thermostatic Mixer has been preset to approximately 41°C under
ideal conditions at the factory, which is appropriate for most systems. However,
site conditions and personal preference may make it necessary to reset this
temperature.
Caution! Before testing the mixer, ensure that the hot and cold water are
flowing correctly by exercising the temperature selector knob between the cold
and hot stops.
1. Turn the temperature selector
knob to position 7 and test that
the temperature of the water from
the shower outlet is between 39°C
and 41°C (as measured with a bath
thermometer). If the water is not in
this range of temperatures, proceed
with the following procedure.
2. Turn the temperature selector knob
to the fully cold position.
3. Hold down the temperature override
button and slowly turn the knob
until the output water reaches a
temperature of 41°C.
4. Wait for the water temperature to
stabilise.
Sealing Washer
Shower Valve
Shower Valve Outlet
Stop Assembly
Override Button
Fixing Screw
Cover Plate
Temperature
Selection Knob
COMMISSIONING

9
5. Insert a small screwdriver into the
notch and pry off the cover plate.
6. Unscrew the fixing screw.
7. Remove the temperature selector
knob without disturbing the stop
assembly.
8. Replace the temperature selector
knob so that the 7 mark is level with
the shoulder on the stop assembly .
9. Replace the fixing screw and the
cover plate.
Temperature
Selector Knob
Fixing Screw
Cover Plate
Stop Assembly
(Shoulder)
Stop Assembly

10
Adjusting the Temperature
The temperature is controlled by rotating the temperature selector knob.
For safety reasons, the temperature is limited by a stop. To obtain a higher
temperature, press the override button on the temperature selector knob and
continue to rotate the knob.
Adjusting the Flow
The flow is controlled by rotating the flow selector knob.
Override
Button
Temperature Selector Button
On/Increase Flow
Off/Decrease Flow
Flow Selector Knob
Decrease
Temperature
Increase
Temperature
OPERATION

11
Read the section: Important Safety Information first.
Provided that the Mira Coda has been correctly installed and is operated in
accordance with the instructions contained in this guide, difficulties should not
arise. If any maintenance is required then it must be carried out by a competent
tradesperson for whom the fault diagnosis chart and maintenance instructions are
provided. Before replacing any parts make sure that the underlying cause of the
malfunction has been identified.
FAULT DIAGNOSIS
Symptom Cause / Rectification
1. Only hot or cold
water from mixer
outlet.
a. Inlet supplies reversed.
2. Fluctuating or
reduced flow. a. Check that the Inlet Filters are not blocked.
b. Makesure that the minimum flow rate issufficient for
the supply conditions.
c. Make sure that the maintained inlet pressures are
nominally balanced and sufficient.
d. Make sure that the inlet temperature differentials are
sufficient.
e. Airlock or partial blockage in pipework.
3. Noflowfrommixer
outlet. a. Make sure that the Inlet Isolating Valves are open.
b. Hotorcold supply failure. Make surethatthe hot and
cold supplies are available to the BSM.
c. Refer to symptom 2.
4. Blendtemperature
drift. a. Inlet supplies reversed.
b. Hot supply temperature fluctuation.
c. Supply pressures fluctuating.
d. Thermal Cartridge defective.
e. Inlet Filters Blocked.
5. Maximum blend
temperature
setting too hot or
too cold.
a. Indicates incorrect maximum temperature setting,
refer section: 'Commissioning'.
b. Refer to symptom 4.

12
Symptom Cause / Rectification
6.
Drip from
handset. A small amount of water may be retained in the fitting
after the shower control has been turned off. This
may drain over a few minutes. This is quite normal.
Changing the angle of the shower fitting may vary the
draining time.
Defective ceramic plates within the shower cartridge.
Renew the cartridge assembly.

13
MAINTENANCE
General
This Product is precision engineered and should give continued safe and
controlled performance, provided:
1. It is installed, commissioned, operated and maintained in accordance with
manufacturers recommendations.
2. Periodic attention is given, when necessary, to maintain the product in good
functional order.
Lubricants
Standard silicone-only based lubricants may be used to assist refitting.
Warning! Use silicone-only based lubricants. Do not use oil-based or other
lubricant types as rapid deterioration of seals may occur.
Cleaning
The Mira Coda should be cleaned using a mild washing up detergent or soap
solution, rinsed and then wiped dry with a soft cloth.
Warning! Many household cleaners contain abrasive and chemical substances,
and should not be used for cleaning plated or plastic fittings.

14
Maintaining the Non-Return Valves
The non-return valves are located in the valve body, and are accessible through
the inlet connectors.
Caution! Ensure that the non-return valves are installed correctly to prevent
crossflow or malfunction of the valve.
1. With the water supplies turned off
and the thermostatic mixer removed,
removethewasher,the circlip and the
filter.
2. Remove the non-return valve and
clean any debris.
3. On reassembly ensure that the non-
return valve is fitted the correct way
round (with the arrow indicating the
flow pointing towards the mixer).
Filter
The inlet filters are located in the inlet connector. Clean or renew as necessary.
Thermostatic Cartridge
In hard water areas the filters in the thermostatic cartridge may become blocked
with limescale, which will reduce the flow of water. It is recommended that the car-
tridges are checked regularly and cleaned in a descaling solution (such as kettle
descalent) if necessary. Be sure to follow the manufacturer’s instructions on the
descalent package.
Note! The cartridge is non-servicable and will require replacement should failure
occur.
Flow Arrow
Non-return Valve
Circlip
Filter Washer

15
1630.048
Outlet Connector
SPARES
1630.045
Temperature Knob
Assembly
1630.044
Temperature Stop
1630.043
Thermostatic
Cartridge
1630.046
Flow Cartridge
1630.047
Flow Knob Assembly
456.29
Wall Mounting
Bracket
1630.049
Filter Washer
1630.042
Non Return Valve
1630.041
Offset Connector Kit

16
1065367-W2-A © Kohler Mira Limited, August 2006
CUSTOMER SERVICE
U
K
A
S
Other manuals for Coda
1
Table of contents
Other Mira Control Unit manuals
Popular Control Unit manuals by other brands
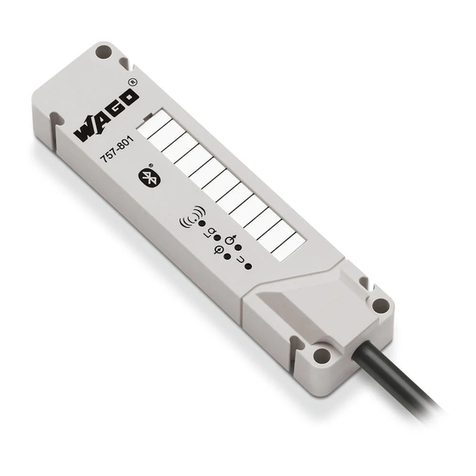
WAGO
WAGO 757-801 manual

United Technologies
United Technologies FSUIM Installation sheet
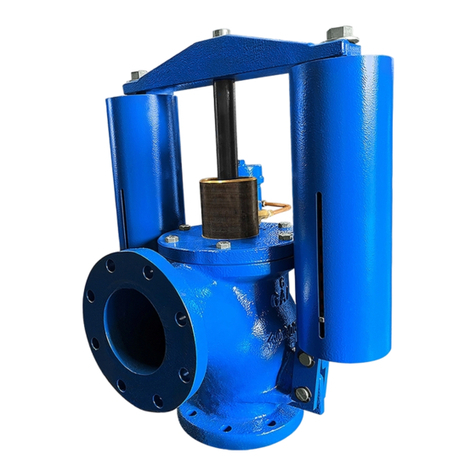
Vag
Vag GA INDUSTRIES Figure 624-D Installation, operation and maintenance manual
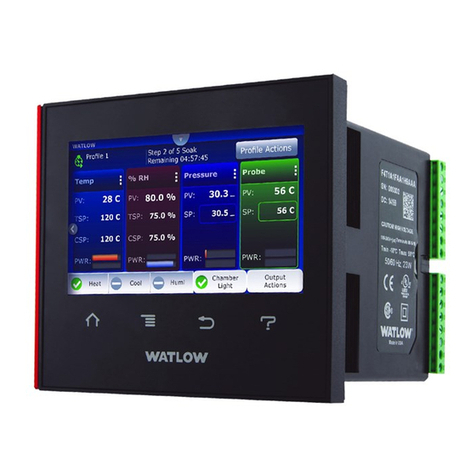
Watlow
Watlow F4T user guide
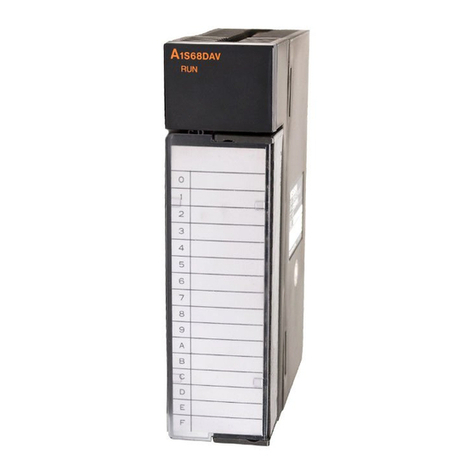
Mitsubishi Electric
Mitsubishi Electric A1S68DAV user manual

VAN DER ENDE
VAN DER ENDE Envalve VK Series installation manual