Mira Coda Plus Operation manual

1
These instructions must be left with the user.
Installation & User Guide
MIRA CODA PLUS
CODA PLUS
THERMOSTATIC BAR VALVE

2
CONTENTS
Introduction .............................................................................................3
Guarantee ............................................................................................4
Recommended Usage..........................................................................4
Patent Application:................................................................................4
Safety : Warnings ....................................................................................5
Pack Contents ......................................................................................... 6
Specications ..........................................................................................7
Pressures ............................................................................................. 7
Temperatures .......................................................................................7
Thermostatic Shut-down ...................................................................... 7
Connections .........................................................................................7
Dimensions...........................................................................................7
Installation ...............................................................................................8
Suitable Plumbing Systems..................................................................8
General.................................................................................................8
Installation ..........................................................................................10
Installation with Fixed Pipework .........................................................15
Commissioning .....................................................................................17
Maximum Temperature Setting ..........................................................17
Operation ...............................................................................................18
Adjusting the Temperature .................................................................18
Adjusting the Flow..............................................................................18
Maintenance...........................................................................................19
Fault Diagnosis...................................................................................19
Lubricants...........................................................................................20
Cleaning .............................................................................................20
Bar Valve Removal.............................................................................20
Maintaining the Non-Return Valves....................................................21
Spare Parts ............................................................................................ 22
Accessories ...........................................................................................23
Customer Service....................................................................Back Page

3
INTRODUCTION
Thank you for purchasing a quality Mira product. To enjoy the full potential of your
new product, please take time to read this guide thoroughly, having done so, keep
it handy for future reference.
The Mira Coda Plus thermostatic bar valve is a shower control designed for wall
mount installations.
The thermostatic bar valve has two knobs, one knob controls the ow and the other
knob controls the temperature.
The thermostatic bar valve incorporates a wax capsule temperature sensing
unit, which provides an almost immediate response to changes in pressures or
temperature of the incoming water supplies, to maintain the selected temperature.
An adjustable maximum temperature stop is provided which limits the temperature
to a safe level. Inlet lters are tted to protect the thermostatic cartridge.
The Mira Coda Plus is supplied complete with a patent applied for xing kit which
has been designed to make the installation of bar valves easier and more secure
and has the following benets over traditional ‘Z’ connectors:
Water connections are made in front of the nished wall surface•
Easy centre and levelling adjustment•
Foam seal to prevent water ingress•
Bar valve is secured to the wall•
Suitable for any bar valve using 3/4” female threads•
Can be used on plastic barrier pipes (with suitable pipe insert)•
If you experience any difculty with the installation or operation of your new
Thermostatic Mixer, please refer to ‘Fault Diagnosis’, before contacting Mira
Showers. Our contact details can be found on the back cover of this guide.

4
Guarantee
For domestic installations, Mira Showers guarantee the Mira Coda Plus against
any defect in materials or workmanship for a period of ve years from the date of
purchase (shower ttings for one year).
For non-domestic installations, Mira Showers guarantee the Mira Coda Plus
against any defect in materials or workmanship for a period of one year from the
date of purchase.
For terms and conditions refer to the back cover of this guide.
Recommended Usage
Application Valve with Fittings
Domestic ü
Light Commercial ü
Heavy Commercial û
Healthcare û
Patent Application:
GB 0818001.0

5
SAFETY : WARNINGS
The function of a thermostatic mixing valve is to deliver water consistently at a safe
temperature. In keeping with every other mechanism, it cannot be considered as
functionally infallible and as such, cannot totally replace a supervisor’s vigilance where
that is necessary. Provided it is installed, commissioned, operated and maintained
within manufacturers recommendations, the risk of failure, if not eliminated, is reduced
to the minimum achievable.
Mira thermostatic mixers are precision engineered and should give continued safe
and controlled performance, provided:
1. They are installed, commissioned, operated and maintained in accordance with
the manufacturer’s recommendations.
2. Periodic attention is given, when necessary, to maintain the product in good
functional order.
Caution!
1. Read all of these instructions.
2. Retain this guide for later use.
3. Pass on this guide in the event of change of ownership of the installation
site.
4. Follow all warnings, cautions and instructions contained in this guide.
5. Anyone who may have difculty understanding or operating the controls of any
shower should be attended whilst showering. Particular consideration should
be given to the young, the elderly, the inrm or anyone inexperienced in the
correct operation of the controls.
6. When this product has reached the end of its serviceable life, it should be
disposed of in a safe manner, in accordance with current local authority
recycling, or waste disposal policy.

6
(Ø6 mm) (Ø6 mm)
(Ø6 mm) (Ø6 mm)
Refer to the installation guide supplied
for full installation instructions
Make sure that the supply pipes are thoroughly flushed
through before connection to the shower control
6.1712.029.2.0
Allow 100 mm
Minimum to Wall
Allow 100 mm
Minimum to Wall
Hot Supply Inlet
(Ø19 mm)
150 mm Pipe Centres
Cold Supply Inlet
(Ø19 mm)
Bar Valve Fixing Kit
Installation Template
PACK CONTENTS
Tick the appropriate boxes to familiarise yourself with the part names and to conrm
that the parts are included.
Documentation
q1 x Guarantee Registration Document
q1 x Mira Coda Bar Valve
Bar Valve Fixing Kit
q2 x Wall Plugs
q2 x Fixing Screws
q2 x Backplates
q2 x Olives
q2 x Nuts
q2 x Offset Connectors
q4 x Screws
q2 x Washers / Filters
q2 x Concealing Plates
q1 x Plastic Pipe Guide
q1 x Installation Template
q2 x Locking Rings (only required in certain installations)

7
SPECIFICATIONS
Pressures
Max Static Pressure:• 10 Bar.
Max Maintained Pressure:• 5 Bar.
Min Maintained Pressure: (Gas Water Heater):• 1.0 Bar. (for optimum
performance supplies should be nominally equal.)
Min Maintained Pressure (Gravity System):• 0.1 Bar. (0.1 bar = 1 Metre head
from cold tank base to shower handset outlet.)
Temperatures
Close temperature control is provided between• 20°C and 50°C.
Optimum Thermostatic Control Range:• 35°C to 45°C. (achieved with supplies
of 15°C cold, 65°C hot and nominally equal pressures.)
Recommended Hot Supply:• 60°C to 65°C. (Note! The mixing valve can operate
at temperatures up to 85°C for short periods without damage. However for
safety reasons it is recommended that the maximum hot water temperature is
limited to 65°C.)
Minimum Recommended Differential between Hot Supply and Outlet•
Temperature: 10°C.
Cold Water Range: up to• 25°C.
Thermostatic Shut-down
For safety and comfort the thermostat will shut off the mixing valve• within
2 Seconds if either supply fails (achieved only if the blend temperature has a
minimum differential of 12°C from either supply temperature).
Connections
Hot: Left• (side nearest ow control), 15 mm compression.
Cold: Right• (side nearest temperature control), 15 mm compression.
Outlet: Bottom• , ½” BSP Male to exible hose.
Note! This product does not allow for reversed inlets and will deliver unstable
temperatures if tted incorrectly.

8
INSTALLATION
Suitable Plumbing Systems
Gravity Fed:
The thermostatic mixer must be fed from a cold water cistern (usually tted in the
loft space) and a hot water cylinder (usually tted in the airing cupboard) providing
nominally equal pressures.
Gas Heated System:
The thermostatic mixer can be installed with a combination boiler.
Unvented Mains Pressure System:
The thermostatic mixer can be installed with an unvented, stored hot water
system.
Mains Pressurised Instantaneous Hot Water System:
The thermostatic mixer can be installed with systems of this type with balanced
pressures.
Pumped System:
The thermostatic mixer can be installed with an inlet pump (twin impeller). The pump
must be installed on the oor next to the hot water cylinder.
150 ± 5
100
80
70
All dimensions in mm
115 Min to Wall100 Min to Wall
Dimensions
5 mm 5 mm
5 mm 5 mm
Adjustment

9
25 mm
Spill Over
Level
Hose Retaining
Ring
General
Installation must be carried out in accordance with these instructions, and must be
conducted by designated, qualied and competent personnel.
The installation must comply with the “Water Supply Regulations 1999 (Water
Fittings)” or any particular regulations and practices, specied by the local water
company or water undertakers.
Note! Make sure that all site requirements correspond to the information given in
section: ‘Specications’.
1. The mixer must not be installed in an area where it may freeze.
2. For stud partitions alternative xings may be required.
3. Isolating valves must be installed close to the mixer for ease of maintenance.
4. Pipework must be rigidly supported and avoid any strain on the connections.
5. Pipework dead-legs should be kept to a minimum.
6. Decide on a suitable position for the
mixer. The position of the mixer and
the shower ttings must provide a
minimum gap of 25 mm between
the spill-over level of the shower
tray/bath and the handset (refer to
illustration). This is to prevent back-
siphonage.
Note! Only use shower fittings
recommended by the manufacturer
or supplier.
7. All pipework must be checked for
leaks before the product installation
is completed. The product should
be pressurised and the inlet & outlet
connections inspected.
8. DO NOT overtighten grubscrews
as product damage may occur.
Use hexagonal key provided and
hand tighten only, do not use power
tools.

10
1. Install the pipework making sure that it is nominally level and set the correct distance
apart (150 ± 5 mm).
Important!
1.1 Pipework should not be secured behind the wall surface within 500 mm
of the bar valve.
1.2 Each pipe should allow a minimum 5 mm horizontal movement (if this is
not possible an alternative xing method for rigid pipes is available).
1.3 Pipes must be left a minimum of 50 mm long.
1.4 Connections are: Hot-Left, Cold-Right. This is very important as the
Mira Coda Plus does not allow for reversed inlets.
1.5 If pipework is chased into a solid wall, in accordance with UK Water
Regulations, it must be accessible.
1.6 Pipes must be straight and at 90° to the nished wall surface.
2. Fit the plastic pipe guide over the inlet
pipes to hold them in position.
50 mm Minimum
Do not secure the
pipework within 500 mm
150 ± 5 mm
Pipe Centres in Wall
HOT COLD
5 mm 5 mm
Plastic Pipe Guide
Inlet Pipes
Installation
3. Leave the plastic pipe guide in place
and nish the wall.
Important! Make sure that when tiling,
5 mm pipe movement remains.
Holes should be drilled/cut between
Ø19 mm and Ø22 mm.
5 mm
5 mm

11
5. Fit the installation template over the
inlet pipes and mark the positions of
the 4 wall bracket xing holes.
4. Important! Make sure that there
is still horizontal movement on the
inlet pipes, if not, continue with the
installation making sure that you
complete section: ‘Installation with
Fixed Pipework’ when instructed, this
will avoid cracking tiles.
6. Mark the pipe distance 25 ± 5 mm from
the nished wall and cut to length.
Important! If using plastic pipes then
they should be cut to suit the insert
supplied with the plastic pipes.
7. Drill the 4 holes for the wall brackets
with a 6 mm drill and insert the wall
plugs (some wall structures may require
alternative xings, not supplied).
Caution! Take care not to drill though
any concealed pipework.
Ø6 mm
25 mm
25 mm
Installation Template
5 mm
5 mm

12
8. Fit the wall brackets (with the arrow
at the top) and olives onto the inlet
pipes and loosely t the nuts.
Caution! Make sure that when
ttingthenutandoliveyoudonot
push the pipe into the wall cavity.
9. Secure the wall brackets to the wall
with the screws supplied.
10. Tighten the nuts.
11. Carefully push the offset connectors
onto the wall brackets. Using the
nger grips rotate them clockwise
until the lug hits the stop.
Important! If, at step 4, there
was no horizontal movement
on the inlet pipes you must
manually level the bar valve, go
to section: ‘Installation with Fixed
Pipework’, otherwise continue with
the installation.
12. Secure the offset connectors to
the wall brackets with the screws
supplied.

13
13. Caution! It is essential at this
point that the supply pipework is
thoroughlyushedthroughbefore
connection to the bar valve.
14. Offer the bar valve up to the offset
connectors, and if necessary using
the nger grips, rotate the connectors
anti-clockwise to adjust the centres.
15. Loosely screw the concealing plates
onto the offset connectors
Important! Do not fully tighten at this
stage.
16. Make sure that the sealing washer/
lter is tted in the correct orientation,
offer the bar valve up to the offset
connectors and tighten the nuts.
Caution! Take care not to damage
the chrome plated surfaces.
Sealing Washer/Filter

14
20. Before using the shower, refer to
section: ‘Commissioning’.
17. Using a spirit level make sure that
the bar valve is level. If adjustment is
required rotate the nut on the highest
side anti-clockwise (up to ½ turn) until
the valve is level.
Note! The nuts can be rotated
anti-clockwise without disengaging
from the offset connector until the
stop point on the wall bracket is
reached, at this point the nut will
start to undo and the bar valve can
be removed from the wall.
18. Tighten the concealing plates until
they are ush with the nished wall.
19. Turn on the hot and cold water
supplies and check for leaks.

15
3. Offer the bar valve up to the offset
connectors, and if necessary using
the nger grips, rotate the connectors
anti-clockwise to adjust the centres
so that they are in line with the bar
valve inlets and are level.
4. Firmly tighten the screws to lock the
offset connectors in position.
1. Fit the locking washers over the offset
connectors.
2. Loosely t the screws to hold the
offset connectors in place.
5. Caution! It is essential at this
point that the supply pipework is
thoroughlyushedthroughbefore
connection to the bar valve.
Locking Washer
This section should be followed in
installations where it has not been possible
to achieve the 5 mm horizontal pipe
movement required to allow automatic
levelling of the bar valve.
Installation with Fixed Pipework

16
6. Tighten the concealing plates until
they are ush with the nished wall.
7. Make sure that the sealing washer/
lter is tted in the correct orientation,
offer the bar valve up to the offset
connectors and tighten the nuts.
Caution! Do not overtighten.
Caution! Take care not to damage
the chrome plated surfaces.
9. Before using the shower, refer to
section: ‘Commissioning’.
8. Turn on the hot and cold water
supplies and check for leaks.
Sealing Washer/Filter

17
COMMISSIONING
Maximum Temperature Setting
Before using the shower, the maximum temperature must be checked to make sure
that it is at a safe level. It has been preset to a safe showering temperature under
ideal conditions at the factory, appropriate for most systems. However, site conditions
and personal preference may make it necessary to reset this temperature.
Note! Make sure that the hot water temperature is at least 55°C and that there is
sufcient supply.
Caution! Before testing the mixer, make sure that the hot and cold water is owing
correctly by exercising the temperature selector knob between the cold and hot
stops.
1. Turn the temperature selector knob to position 7 and test that the temperature
of the water from the shower outlet is hot enough.
2. If not, depress the override button and carefully rotate towards position 9. If the
water temperature is still not hot enough complete the following procedure.
3. Rotate the temperature selector knob back to position 7.
4. Using a suitable screwdriver carefully pry off the concealing cap and unscrew
the xing screw.
5. Pull off the temperature selector knob without disturbing the stop assembly.
6. Replace the temperature selector knob so that the 6 mark is in line with the
stop assembly.
7. Rotate the temperature selector knob to position 7, wait for the water to
stabilise and test that the temperature of the water from the shower outlet is
hot enough.
If the water temperature is still not hot enough repeat the procedure until a
maximum safe temperature is achieved at position 9.
8. Ret and tighten the xing screw, ret the concealing cap.
Fixing Screw
Concealing Cap
Stop Assembly
Temperature
Selector Knob

18
Override
Button
Temperature
Selector Knob
ON / Increase Flow
OFF / Decrease Flow
Flow Selector Knob
Decrease
Temperature
Increase
Temperature
OPERATION
Adjusting the Temperature
The temperature is controlled by rotating the temperature selector knob.
For safety reasons, the temperature is limited by an override stop. To obtain a
higher temperature, press the override button on the temperature selector knob and
continue to rotate the knob.
Adjusting the Flow
The ow is controlled by rotating the ow selector knob.

19
MAINTENANCE
Fault Diagnosis
If you require a Mira trained service engineer or agent, refer to section: ‘Customer
Services’.
Symptom Cause/Rectication
Only hot or cold water
from the mixer outlet.
Outlet temperature too
hot / too cold.
Inlets reversed (hot supply to cold supply). Rework inlet
pipework.
No hot or cold water reaching the mixer.
Check the lters for any blockage.
Installation conditions outside operating parameters, refer
to sections: ‘Specications’ and ‘Commissioning’.
Fluctuating or reduced
ow.
Check the shower handset, hose and filters for any
blockage.
Make sure that the maintained inlet pressures are
nominally balanced and sufficient, refer to section:
‘Specications’.
Make sure that the inlet temperature differentials are
sufcient, refer to section: ‘Specications’.
Air lock or partial blockage in the pipework.
Water leaking from
shower handset.
Normal for a short period after shut off.
Check that the pressures are not in excess of the
specications for the product.
Cartridge inlet seals damaged, renew.
Renew the ow cartridge.
Leak from inlet
connector.
On rare occasions when levelling the valve, the inlet
connectors can become loose. Remove the bar valve
and tighten the inlet connectors. If the inlet connectors
continually become loose follow the instructions in section:
‘Manual Levelling’.

20
Lubricants
Silicone based lubricants must only be used on the rubber seals.
Caution! Oil based or other lubricant types may cause rapid deterioration of
seals.
Cleaning
The chrome plated parts should be cleaned using a mild washing up detergent or
soap solution, rinsed and then wiped dry with a soft cloth.
Warning! Many household cleaners contain abrasive and chemical substances,
and should not be used for cleaning plated or plastic ttings.
Do not use descalents on this product.
Bar Valve Removal
1. Isolate the hot and cold water supplies.
2. Unscrew the concealing plates at least 2 turns to allow the bar valve to be
removed from the wall.
Important! Failure to loosen the concealing plates may result in them becoming
tight to the nished wall.
3. Unscrew the nuts from the offset connectors and remove the bar valve.
4. Beforerettingmakesurethattheinletconnectorsaretight.
Table of contents
Other Mira Control Unit manuals
Popular Control Unit manuals by other brands

Walvoil
Walvoil DPC130X Service manual
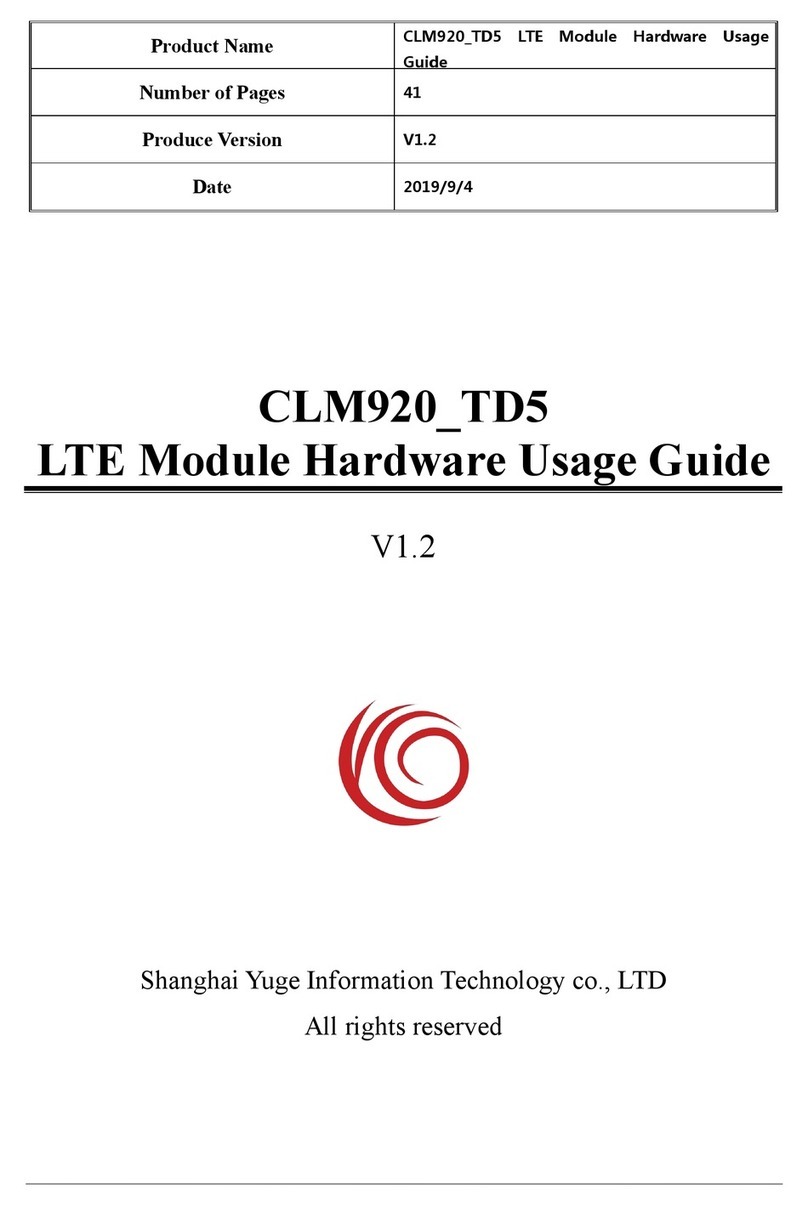
YUGE
YUGE CLM920 TD5 Hardware Usage Guide
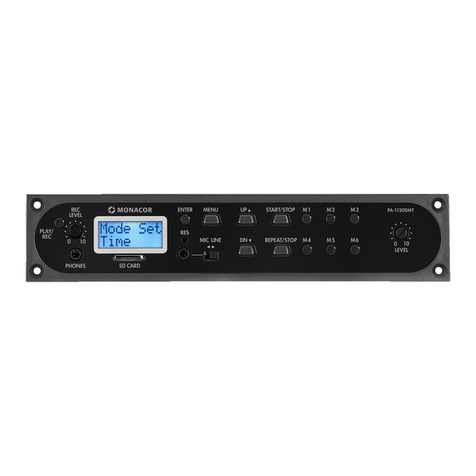
Monacor
Monacor PA-1120DMT Installation and operating instructions
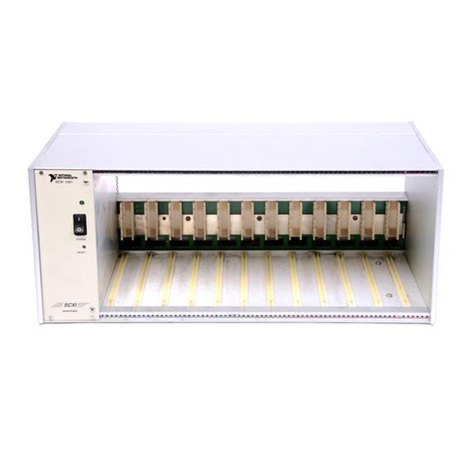
National Instruments
National Instruments SCXI Series quick start guide
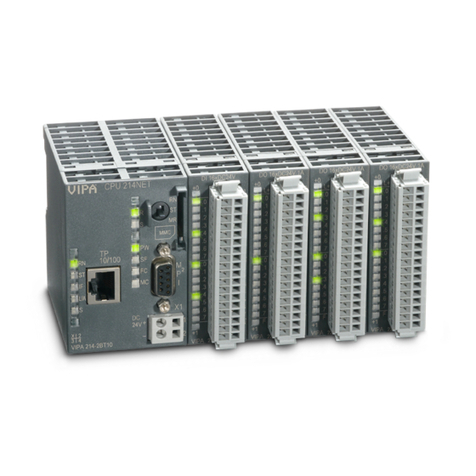
YASKAWA
YASKAWA VIPA System 200V manual
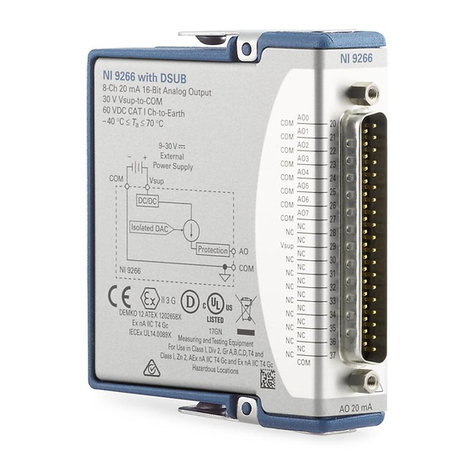
National Instruments
National Instruments 9266 Getting started guide