Mocbos DC 3600 XRi User manual

DC 3600 XRi
VARIADOR DE VELOCIDAD
PARA MOTORES DE CC
Manual Completo
D i r ec c i ón: C a r lo s M . R a m ír e z 2 5 5 5 – C P 1 4 3 7 , B s. A s . , A R G E NT I N A
Te l: (0 0 54 1 1) 4 91 8 - 229 9 | What sA pp : + 54 9 11 44 92 - 3 0 70
E-m ail: i nfo@mocbos .com | Web Site: www.mocbos.com
¡Descargar
manual completo!
Mocbos
MOTORTECH S.A. / Enertronica Santerno
Manual Completo
DC 3600XRi
MU 821.20/27
Rev.00
24/08/2023

Mocbos
MOTORTECH S.A. / Enertronica Santerno
Manual Completo
DC 3600XRi
MU 821.20/27
Rev.00
24/08/2023

Installation
• (QVXUHPHFKDQLFDOO\VHFXUHȴ[LQJVDUHLQXVHDVUHFRPPHQGHG
• (QVXUHFRROLQJDLUȵRZDURXQGWKHSURGXFWLVDVUHFRPPHQGHG
• (QVXUHFDEOHVZLUHWHUPLQDWLRQVDUHDVUHFRPPHQGHGDQGDUHWRUTXHGFRUUHFWO\
• (QVXUHWKHSURGXFWUDWLQJLVFRUUHFWGRQRWH[FHHGWKHUDWLQJ
$SSOLFDWLRQ ULVN
Electromechanical safety is the responsibility of the user. 7KHLQWHJUDWLRQRIWKLVSURGXFW
LQWRRWKHUDSSDUDWXVRUV\VWHPVLVQRWWKHPDQXIDFWXUHUVRUGLVWULEXWRURIWKHSURGXFWV
UHVSRQVLELOLW\,WLVWKHXVHUVUHVSRQVLELOLW\WRHQVXUHWKHFRPSOLDQFHRIWKHLQVWDOODWLRQZLWK
DQ\UHJXODWLRQVLQIRUFH
+HDOWK DQG VDIHW\ DW ZRUN
Electrical devices can constitute a safety hazard. 7KRURXJKSHUVRQQHOWUDLQLQJLVDQDLG
WR6$)(7<DQGSURGXFWLYLW\6$)(7<DZDUHQHVVQRWRQO\UHGXFHVWKHULVNRIDFFLGHQWVDQG
LQMXULHVLQ\RXUSODQWEXWDOVRKDVDGLUHFWLPSDFWRQLPSURYLQJSURGXFWTXDOLW\DQGFRVWV
,I\RXKDYHDQ\GRXEWVDERXWWKH6$)(7<RI\RXUV\VWHPRUSURFHVVFRQVXOWDQH[SHUW
LPPHGLDWHO\'RQRWSURFHHGZLWKRXWGRLQJVR,ILQGRXEWUHIHUWRWKH6XSSOLHU
CAUTION!
EQUIPMENT DAMAGE HAZARD
• :HWKRURXJKO\WHVWRXUSURGXFWV+RZHYHUEHIRUHLQVWDOODWLRQDQGVWDUWXS
LQVSHFWDOOHTXLSPHQWIRUWUDQVLWGDPDJHORRVHSDUWVSDFNLQJPDWHULDOVHWF
• ,QVWDOODWLRQPXVWREVHUYHWKHUHTXLUHGHQYLURQPHQWDOFRQGLWLRQVIRUVDIHDQG
UHOLDEOHRSHUDWLRQ
• ,QDGRPHVWLFHQYLURQPHQWWKLVSURGXFWPD\FDXVHUDGLRLQWHUIHUHQFHUHTXLULQJ
DGHTXDWHPHDVXUHVWREHWDNHQ 2EWDLQWKHSHUPLVVLRQRIWKHVXSSO\DXWKRULW\
EHIRUHFRQQHFWLQJWRWKHORZYROWDJHVXSSO\
WARNING!
PERSONAL INJURY AND/OR ELECTRICAL SHOCK HAZARD
• $OZD\VLVRODWHDOOSRZHUVXSSOLHVIURPWKHHTXLSPHQWEHIRUHVWDUWLQJDQ\ZRUN
• 1HYHUSHUIRUPKLJKYROWDJHUHVLVWDQFHFKHFNVRQWKHZLULQJZLWKRXWȴUVW
GLVFRQQHFWLQJWKHSURGXFWIURPWKHFLUFXLWXQGHUWHVW
• 8VHJXDUGLQJDQGDGGLWLRQDOVDIHW\V\VWHPVWRSUHYHQWLQMXU\DQGHOHFWULFVKRFN
• 0HWDOSDUWVPD\UHDFKr&GXULQJRSHUDWLRQ
+D]DUGV
This equipment can endanger life through rotating machinery and high voltages.
WARNING!
2QO\TXDOLȴHGSHUVRQQHOPXVWLQVWDOORSHUDWHDQGPDLQWDLQWKLVHTXLSPHQW
$TXDOLȴHGSHUVRQLVVRPHRQHWHFKQLFDOO\FRPSHWHQWDQGIDPLOLDUZLWKDOOVDIHW\
LQIRUPDWLRQHVWDEOLVKHGVDIHW\SUDFWLFHVLQVWDOODWLRQRSHUDWLRQPDLQWHQDQFH
DQGWKHKD]DUGVLQYROYHGZLWKWKLVHTXLSPHQWDQGDQ\DVVRFLDWHGPDFKLQHU\
*HQHUDOULVNV
Mocbos
MOTORTECH S.A. / Enertronica Santerno
Manual Completo
DC 3600XRi
MU 821.20/27
Rev.00
24/08/2023

Weight
Consideration should be given to the weight of our heavier products when handling.
Risk assessment
Under fault conditions or conditions not intended: the motor speed may be incorrect; the
motor speed may be excessive; the direction of rotation may be incorrect; the motor may be
energised.
,QDOOVLWXDWLRQVWKHXVHUVKRXOGSURYLGHVXɝFLHQWJXDUGLQJDQGRUDGGLWLRQDOUHGXQGDQW
monitoring and safety systems to prevent risk of injury.
NOTE: During a power loss event, the product will commence a sequenced shut-down
procedure. Therefore, the system designer must provide suitable protection for this case.
Maintenance
2QO\TXDOLȴHGSHUVRQQHOVKRXOGPDLQWDLQDQGHIIHFWUHSDLUXVLQJRQO\WKHUHFRPPHQGHG
spares, alternatively return the equipment to the factory for repair. The use of unapproved
parts may create a hazard and risk of injury.
WARNING!
PERSONAL INJURY AND/OR EQUIPMENT DAMAGE HAZARD
:KHQUHSODFLQJDSURGXFWDOOXVHUGHȴQHGSDUDPHWHUVWKDWGHȴQHWKHSURGXFWV
operation must be installed correctly before returning to use. Failure to do so
may create a hazard and risk of injury.
7KHSDFNDJLQJLVLQȵDPPDEOHDQGLQFRUUHFWGLVSRVDOPD\OHDGWRWKHJHQHUDWLRQ
of lethal toxic fumes.
Repairs
5HSDLUUHSRUWVFDQRQO\EHJLYHQLIWKHXVHUPDNHVVXɝFLHQWDQGDFFXUDWHGHIHFWUHSRUWLQJ
Remember that the product without the required precautions can represent an electrical
hazard and risk of injury, and that rotating machinery is a mechanical hazard.
Protective insulation
Isolated product
WARNING!
The drive and motor must be connected to an appropriate safety earth.
Failure to do so presents an electrical shock hazard. Exposed metal work in this
equipment is protected by basic insulation and bonding to a safety earth.
7KLVSURGXFWLVFODVVLȴHGDVDFRPSRQHQWDQGPXVWEHXVHGLQDVXLWDEOHHQFORVXUH
1. This is achieved through basic insulation and protective earth grounding, or double-
insulation to provide SELV Control Circuits.
2. This protection allows a safe connection to other low voltage equipment.
3. Earth bonding is the responsibility of the installer.
Mocbos
MOTORTECH S.A. / Enertronica Santerno
Manual Completo
DC 3600XRi
MU 821.20/27
Rev.00
24/08/2023

Contents
1 Introduction 1
2 Mechanical dimensions 2
3 Guide for systems used in the EU 3
4 Multiple drives 3
5 Requirements for EMC compliance 4
6 Installation 5
6.1 Motor installation.......................................................................................................... 5
6.2 Drive installation ........................................................................................................... 5
6.3 Typical applications....................................................................................................... 6
7 Commissioning 7
7.1 Initial settings - without power.................................................................................... 7
7.2 Block diagram ................................................................................................................ 8
7.3 Terminal descriptions ..................................................................................................11
7.4 Preset, switches and links .......................................................................................... 14
7.5 Pre-operation motor check list ...................................................................................18
7.6 Field and setpoint check ..............................................................................................18
7.7 Operating the drive......................................................................................................18
7.8 Bi-directional operation ..............................................................................................19
8 Options 20
8.1 Torque Control Mode .................................................................................................. 20
8.2 Maximum Current Mode ............................................................................................ 21
8.3 Quench Mode............................................................................................................... 21
8.4 Stall Mode..................................................................................................................... 23
8.5 Optional START (ramp to stop)................................................................................... 24
8.6 FORWARD/REVERSE truth table ................................................................................. 24
9 Trouble shooting 25
6SHFLȴFDWLRQV
7HFKQLFDOVSHFLȴFDWLRQV .............................................................................................. 26
10.2 Rating table .................................................................................................................. 28
Mocbos
MOTORTECH S.A. / Enertronica Santerno
Manual Completo
DC 3600XRi
MU 821.20/27
Rev.00
24/08/2023

1Introduction
1
Introduction
The 3600XRi DC Drive is an isolated, 4 Quadrant speed controller for brushed shunt wound
or permanent magnet DC motors. This Class 1 product has basic insulation and protective
earth. Its control signals are isolated from the mains AC supply, and their connection to
other isolated instruments is permitted.
Electrically isolated control circuits allow interfacing to external sources.
It has both speed and current control modes and can motor or regenerate in both forward
or reverse directions of rotation. The drive incorporates a fully controlled thyristor bridge
with a current loop to protect the drive and motor. It uses an accurate current control loop
to protect itself and the motor.
7KLVFRPSRQHQWLVKD]DUGRXV3OHDVHREWDLQH[SHUWKHOSLI\RXDUHQRWTXDOLȴHGWR
install this equipment. Make safety a priority.
Read about the general risks and warnings at the front of this manual.
This apparatus complies with the protection requirements of the relevant EU
'LUHFWLYHV8/ȴOH(
• All models are of open chassis construction only for use in a suitable enclosure with a
IXVHGVXSSO\)RUVXLWDEOHIXVHVUHIHUWR6SHFLȴFDWLRQVRQSDJH
• The unit uses closed-loop control of both armature current and feedback voltage for
precise control of motor torque and speed.
• A stall timer protects the motor and drive and automatically removes power after 30
seconds if the required speed is not achievable. Durng this period, the unit can provide
up to 150% of the preset maximum current for up to 30 seconds allowing for high, short-
term torques during acceleration etc.
• Electrically isolated control circuits allow interfacing to external sources.
• Independent control of either the current or speed loops by external inputs allows for
torque or speed control applications with overspeed or overcurrent protection.
• Derive the speed demand signal from either a potentiometer, 0-10 V signal or 4-20 mA
current loop. A bipolar speed demand is only possible with a voltage input.
• 6SHHGIHHGEDFNVLJQDOVHOHFWLRQ$50$785(92/7$*(RUVKDIWPRXQWHG7$&+20(7(5
• On-board function switches select the SPEED and CURRENT ranges.
• Independent adjustment presets provide FORWARD UP RAMP, FORWARD DOWN RAMP,
REVERSE UP RAMP, REVERSE DOWN RAMP.
• The positive and negative current limits are independently adjustable.
• Motor braking can be fast or ramped, and provision is made to adjust the motoring and
braking torque independent of rotation direction. The unit returns braking energy to the
supply.
• Control the shaft direction using linear voltage signals or pushbuttons.
• The unit can directly connect to a PLC logic controller.
• The unit has a comprehensive range of extra inputs and outputs.
Mocbos
MOTORTECH S.A. / Enertronica Santerno
Manual Completo
DC 3600XRi
MU 821.20/27
Rev.00
24/08/2023

2Mechanical dimensions
2
Mechanical dimensions
0RXQWWKHXQLWXVLQJWKHWZRFHQWUHȴ[LQJVORWVDQGDOORZVDWLVIDFWRU\FRROLQJDLUWRȵRZ
RYHUWKHȴQVYHUWLFDOO\ZLWKPPHQGVSDFH7KHXQLWPXVWKDYHDVXEVWDQWLDOHDUWK
connection. Connect the earth (cross-sectional area at least 6 mm2) to the heatsink earth
screw provided. Use a star washer to obtain optimum earth continuity.
175 mm 165 mm
70 mm
200 mm
fin
100 mm
side view
plan view
3600XRi
airflow
heatsink earth screw
(90 mm : 36 A)
terminals terminals
terminals
70 61 60 51
1 16
cover
A1+
A2-
L2/N
L
F2-
F1+
Figure 1 Mechanical dimensions
3600XRi
6XLWDEOHȴ[LQJEROWV
$XQLW 0[PP
$XQLW 0[PP
Mocbos
MOTORTECH S.A. / Enertronica Santerno
Manual Completo
DC 3600XRi
MU 821.20/27
Rev.00
24/08/2023

3Guide for systems used in the EU
3
Guide for systems used in the EU
Special consideration must be given to installations in member states of the European Union
regarding noise suppression and immunity. According to IEC 1800-3 (EN61800-3), the drive
XQLWVDUHFODVVLȴHGDVFRPSOH[FRPSRQHQWVRQO\IRUSURIHVVLRQDODVVHPEOHUVZLWKQR&(
marking for EMC.
The drive manufacturer is responsible for the provision of installation guidelines.
The resulting EMC behaviour is the responsibility of the manufacturer of the system
or installation. The units are subject to the LOW VOLTAGE DIRECTIVE 73/23/EEC and
are CE marked accordingly.
Following the procedures outlined below will normally be required for the drive system
to comply with the European regulations, some systems may require different measures.
Installers must have a level of technical competence to correctly install. Although the drive
unit itself is not subject to the EMC directive, considerable development work has been
undertaken to ensure that the noise emissions and immunity are optimised.
(1VSHFLȴHVWZRDOWHUQDWLYHRSHUDWLQJHQYLURQPHQWV7KHVHDUHWKH'RPHVWLF
VWHQYLURQPHQWDQG,QGXVWULDOQGHQYLURQPHQW7KHUHDUHQROLPLWVVSHFLȴHGIRU
conducted or radiated emissions in the industrial environment, hence it is usual for
WKH$&VXSSO\ȴOWHUWREHRPLWWHGLQ,QGXVWULDOV\VWHPV
'HȴQLWLRQRIDQLQGXVWULDOHQYLURQPHQWDOOHVWDEOLVKPHQWVRWKHUWKDQWKRVHGLUHFWO\
connected to a low-voltage power supply network that supplies buildings used for
domestic purposes.
*
4
Multiple drives
7KHDUUDQJHPHQWVKRZQEHORZLVIRUPXOWLSOHGULYHVZLWKRQHȴOWHUVKRZLQJWKHVWDUSRLQW
earthing method.
7KHȴOWHUVKRXOGEHUDWHGIRUWKHZRUVWFDVHWRWDODUPDWXUHFXUUHQWORDG7KHGULYHXQLWV
DUHGHVLJQHGWRIXQFWLRQQRUPDOO\RQXQȴOWHUHG$&VXSSOLHVVKDUHGZLWKRWKHUWK\ULVWRU'&
drives. (Not AC drives).
DRIVE 1
AC SUPPLY
FILTER
UNIT *
DRIVE 2
24V LOGIC CONTROL CLEAN EARTH
INSULATED FROM METAL WORK
ANALOGUE 0V (COM TERMINAL 5 ON DRIVES)
CLEAN EARTH INSULATED FROM METAL WORK
BACKPLATE
METAL WORK
DOORS
110V CONTROL
CUBICLE
METAL WORK
EARTH
STAR
POINT
INCOMING SAFETY EARTH
MOTOR 2 MOTOR 1
Figure 2 Star point connections for multiple drives
Mocbos
MOTORTECH S.A. / Enertronica Santerno
Manual Completo
DC 3600XRi
MU 821.20/27
Rev.00
24/08/2023

4Requirements for EMC compliance
• Keep parallel runs of power and control cables at least
0.3 metres apart. Cross-overs must be at right angles.
• Keep sensitive components at least 0.3 metres from
the drive and power supply cables.
• 7KH$&FRQQHFWLRQVIURPWKHȴOWHUWRWKHGULYHPXVWEH
less than 0.3 metres or, if longer, correctly screened.
• 'RQRWUXQȴOWHUHGDQGXQȴOWHUHG$&VXSSO\FDEOHV
together.
• &RQWUROVLJQDOVPXVWEHȴOWHUHGRUVXSSUHVVHGHJ
control relay coils and current carrying contacts. The
GULYHPRGXOHKDVEXLOWLQȴOWHUVRQVLJQDORXWSXWV
• 7KH$&VXSSO\ȴOWHUPXVWKDYHDJRRGHDUWKFRQQHFWLRQ
to the enclosure back plane. Take care with painted
metal to ensure good conductivity.
• 7KH$&LQSXWȴOWHUKDVHDUWKOHDNDJHFXUUHQWV(DUWK
RCD devices may need to be set at 5% of rated current.
• 7KHPHWDOHQFORVXUHZLOOEH5)JURXQG7KH$&ȴOWHU
drive earth and motor cable screen should connect
directly to the metal cabinet for best performance.
• Linear control signal cables must be screened, with
the screen earthed at the drive end only. Minimise the
length of screen stripped back and connect it to an
analogue earth point.
• (1) The motor cable must be screened or armoured
with 360 degree screen terminations to earth at each
end. The cable must have an internal earth cable and
the screen must extend into the enclosure and motor
terminal box to form a Faraday cage without gaps.
• (2) The internal earth cable must be earthed at each
end. The incoming earth must be effective at RF.
WARNING! The earth safety must always take
precedence.
5
Requirements for EMC compliance
WARNING!
(/(&75,&6+2&.+$=$5'
$&VXSSO\ȴOWHUV
must not be used
on supplies that
are unbalanced or
ȵRDWZLWKUHVSHFWWR
earth.
The drive and AC
ȴOWHUPXVWRQO\
be used with a
permanent earth
connection. No
plugs/sockets are
allowed in the AC
supply.
The AC supply
ȴOWHUFRQWDLQVKLJK
voltage capacitors
and should not
be touched for a
period of at least 20
seconds after the
removal of the AC
supply.
DRIVE
CONTROL
TERMINALS
DRIVE
AC SUPPLY
INPUTS
DRIVE
EARTH
TERMINAL
ARMATURE
AND FIELD
OUTPUTS
CONTROL
SIGNAL
FILTERS
AC SUPPLY
FILTER
UNIT *
dc drive module
User’s metal enclosure
1
2
Figure 3 Connections for EMC compliance
Mocbos
MOTORTECH S.A. / Enertronica Santerno
Manual Completo
DC 3600XRi
MU 821.20/27
Rev.00
24/08/2023

5Installation
6
Installation
WARNING!
ELECTRIC SHOCK HAZARD
Disconnect the mains supply
before working on the unit. DO
127728&+35(6(766:,7&+(6
AND JUMPERS! Always use the
correct insulated adjustment
tools.
6.1
Motor installation
• Foot-mounted motors must be level and
secure.
• Ensure accurate alignment of the motor
shaft and couplings.
• Do not hammer pulleys or couplings
onto the motor shaft.
• Protect the motor from ingress of
foreign matter during installation.
Earthing: Connect the motor to the system
enclosure earth.
6.2
Drive installation
Requirements during installation and
RSHUDWLRQ
• Avoid vibration.
• Protect the drive from pollutants.
• Ambient operating temperature must be
within -10ºC and +40ºC. To comply with
UL requirements, the temperature of the
surrounding air must not exceed 50ºC.
POWER CABLING8VHFRUUHFWO\UDWHG
FDEOHPLQLPXP9DF[DUPDWXUH
current, enclosed in metal conduit or
trunking, or screened. The screen must be
earthed at the motor and drive - refer to "5
Requirements for EMC compliance" on page
4.
FUSING7KHGULYHV0867%()86('
EXTERNALLY with semiconductor fuses. The
fuses must be semiconductor types with
a maximum amps squared seconds rating
according to the Rating table, page 28).
The fuse current rating must be at least
1. 75 times the armature current. The
voltage rating must be suitable for the
AC supply. Failure to use the correct
semiconductor fuse ratings will invalidate
any warranty. Special consideration must
be given to installations in member states
of the EU. Refer to "5 Requirements for EMC
compliance" on page 4.
CONTROL SIGNALS$YRLGUXQQLQJVLJQDO
cables close to power cables. Earth the
screens at the drive end only.
SUPPRESSION7KHGULYHVKDYHH[FHOOHQW
QRLVHLPPXQLW\+RZHYHULQVWDOODWLRQV
involving electrical welding or RF induction
KHDWLQJPD\UHTXLUHIXUWKHUȴOWHUVRQWKH
line and armature terminals. Contactor coils
and sparking contacts may also require
VXSSUHVVLRQ$ȡUHVLVWRULQVHULHVZLWK
a 0.1 µF capacitor is usually adequate in
these situations.
MECHANICAL:2SWLPLVHKHDWVLQNDLUȵRZ
Avoid vibration and ambient temperature
outside -10 to +45°C. Protect the drive from
pollutants.
MOTOR: Ensure the motor is correctly
wired and that the motor and load are
free and safe to rotate. The motor must
ideally have a minimum armature time
constant of approximately 10 ms (T = L/R).
For motors with lower time constants e.g.
servo-motors, use an armature choke in
series with the motor (refer to the motor
supplier for choke data). Failure to do this
may cause damage.
Mocbos
MOTORTECH S.A. / Enertronica Santerno
Manual Completo
DC 3600XRi
MU 821.20/27
Rev.00
24/08/2023

6Installation
6.3
Typical applications
Figure 4 Basic connection
SPRINT ELECTRIC LTD. does not
accept any liability whatsoever for
WKHLQVWDOODWLRQȴWQHVVIRUSXUSRVHRU
application of its products. It is the users
responsibility to ensure that the unit is
correctly used and installed.
Health and Safety at Work
Devices constitute a safety hazard. It is
the responsibility of the user to ensure
compliance with any Acts or By-Laws
in force. ONLY skilled persons should
install this equipment.
1
+10
2
MIN
3
I/P
4
MAX
5
COM
6
AUX
7
RUN
8
COM
9
TAC
10 11 12
F2-
F1+
STA
JOG
FWD
REV
A1+ A2- L2/N L
13 14 15 16
RAMP
quench
RL2
RL2 shown
energised
SP64 XIP +RL2
COIL
RL2
SET
RESET MAX O/P
+10
-10 terminal 4
68
67
IP
66
-IP
65
XIP
64
-12
63
SS
62
+12
61
TIM
60
REV
59
COM
58
DO
57
SO
56
RO
55
IO
54
ZS
53
ST
52
-24
51
70
69
COM +24
IP IO
DC TACHO
(optional)
COM must be earthed for protective class 1
FIELD
AC I/P
DANGER
ELECTRIC SHOCK RISK
MOTOR
RUN
10K
BASIC CONNECTION. FORWARD AND REVERSE SPEED CONTROL BY POTENTIOMETER
ccw
cw
OPTIONAL
START *
(ramp
to stop)
1
+10
2
MIN
3
I/P
4
MAX
5
COM
6
AUX
7
RUN
8
COM
9
TAC
10 11 12
F2-
F1+
STA
JOG
FWD
REV
A1+ A2- L2/N L
13 14 15 16
RAMP
quench
RL2
RL2 shown
energised
SP64 XIP +RL2
COIL
RL2
SET
RESET MAX O/P
+10
-10 terminal 4
68
67
IP
66
-IP
65
XIP
64
-12
63
SS
62
+12
61
TIM
60
REV
59
COM
58
DO
57
SO
56
RO
55
IO
54
ZS
53
ST
52
-24
51
70
69
COM +24
IP IO
DC TACHO
(optional)
COM must be earthed for protective class 1
RUN
ALTERNATIVE FORWARD AND REVERSE SPEED CONTROL BY CENTRE ZERO POTENTIOMETER
ccw
cw 10K
centre zero
SPEED
SPEED If OPTIONAL START (ramp to stop) is not required,
connect START T13 directly to COM
*We recommend two fuses
for line-to-line operation, only
one fuse is necessary on the live
(L) for line-to-neutral operation
incoming
FUSES
OPTIONAL
START *
(ramp
to stop)
If OPTIONAL START (ramp to stop) is not required,
connect START T13 directly to COM
*
FIELD
AC I/P
DANGER
ELECTRIC SHOCK RISK
MOTOR
We recommend two fuses
for line-to-line operation, only
one fuse is necessary on the live
(L) for line-to-neutral operation
incoming
FUSES
We recommend an initial start using the Basic Connection.
WARNING!
PERSONAL INJURY AND/OR
EQUIPMENT DAMAGE HAZARD
To ensure safe operation of the unit, always apply the ac supply before closing the
UXQFRQWDFWWRSUHYHQWVSXULRXVȴULQJGXHWRHUUDWLFPDLQVFRQWDFWRURSHUDWLRQ
'RQRWUHPRYHWKHDFVXSSO\ZKLOHWKHDUPDWXUHFXUUHQWLVȵRZLQJTXHQFKWKH
GULYHȴUVWXVLQJWKHUXQFRQWDFW
1
+10
2
MIN
3
I/P
4
MAX
5
COM
6
AUX
7
RUN
8
COM
9
TAC
10 11 12
F2-
F1+
STA
JOG
FWD
REV
A1+ A2- L2/N L
13 14 15 16
RAMP
quench
RL2
RL2 shown
energised
SP64 XIP +RL2
COIL
RL2
SET
RESET MAX O/P
+10
-10 terminal 4
68
67
IP
66
-IP
65
XIP
64
-12
63
SS
62
+12
61
TIM
60
REV
59
COM
58
DO
57
SO
56
RO
55
IO
54
ZS
53
ST
52
-24
51
70
69
COM +24
IP IO
DC TACHO
(optional)
COM must be earthed for protective class 1
FIELD
AC I/P
DANGER
ELECTRIC SHOCK RISK
MOTOR
RUN
10K
BASIC CONNECTION. FORWARD AND REVERSE SPEED CONTROL BY POTENTIOMETER
ccw
cw
OPTIONAL
START *
(ramp
to stop)
1
+10
2
MIN
3
I/P
4
MAX
5
COM
6
AUX
7
RUN
8
COM
9
TAC
10 11 12
F2-
F1+
STA
JOG
FWD
REV
A1+ A2- L2/N L
13 14 15 16
RAMP
quench
RL2
RL2 shown
energised
SP64 XIP +RL2
COIL
RL2
SET
RESET MAX O/P
+10
-10 terminal 4
68
67
IP
66
-IP
65
XIP
64
-12
63
SS
62
+12
61
TIM
60
REV
59
COM
58
DO
57
SO
56
RO
55
IO
54
ZS
53
ST
52
-24
51
70
69
COM +24
IP IO
DC TACHO
(optional)
COM must be earthed for protective class 1
RUN
ALTERNATIVE FORWARD AND REVERSE SPEED CONTROL BY CENTRE ZERO POTENTIOMETER
ccw
cw 10K
centre zero
SPEED
SPEED If OPTIONAL START (ramp to stop) is not required,
connect START T13 directly to COM
*We recommend two fuses
for line-to-line operation, only
one fuse is necessary on the live
(L) for line-to-neutral operation
incoming
FUSES
OPTIONAL
START *
(ramp
to stop)
If OPTIONAL START (ramp to stop) is not required,
connect START T13 directly to COM
*
FIELD
AC I/P
DANGER
ELECTRIC SHOCK RISK
MOTOR
We recommend two fuses
for line-to-line operation, only
one fuse is necessary on the live
(L) for line-to-neutral operation
incoming
FUSES
Mocbos
MOTORTECH S.A. / Enertronica Santerno
Manual Completo
DC 3600XRi
MU 821.20/27
Rev.00
24/08/2023

7Commissioning
7
Commissioning
7.1
Initial settings - without power
The suggested Comissioning strategy is to start in the safest possible mode of operation and
progressively exercise each element of the system until full functionality has been achieved.
)RUWKLVUHDVRQDOOGULYHXQLWVDUHVKLSSHGWRUXQXVLQJWKH
1. 6HWWKHIROORZLQJVZLWFKHV
• Select the current range using switches S1 and S2 - set to
the minimum motor rating that includes the motor rating
current. Refer to "Figure 6 User adjustments" on page 10.
• Set switches S3 and S4 to OFF to select feedback full scale at
100%, 50 V.
• Set switches S5, S6 and S7 to provide the desired relay
function - Refer to "Figure 6 User adjustments" on page 10.
• Set switch S8 to ON to select Armature Voltage, and the Tach
from T9 must be disconnected.
MAX SPEED
Fully anti-clockwise
MIN SPEED
Fully anti-clockwise
FORWARD UP RAMP
Fully anti-clockwise
FORWARD DOWN RAMP
Fully anti-clockwise
REVERSE UP RAMP
Fully anti-clockwise
REVERSE DOWN RAMP
Fully anti-clockwise
STABILITY
Mid-way
IR COMP
Fully anti-clockwise
MAX CURRENT
Set the MAX CURRENT from your motor rating
plate - clockwise rotation of the potentiometer
gives 0-100% current limit. For example, 50%
rotation provides a 50% current limit for the
selected current range set by switches S1 and S2.
3. /LQNVHQVXUHWKDW
a. The link for the MAX CURRENT potentiometer mode is in the POS I/
NEG I position.
b. The 4Q TORQUE/2Q TORQUE/SPEED link is in the SPEED position.
c. 6DQG=648(1&+OLQNVDUHȴWWHG
• highest supply voltage option at nominal speed • ARMATURE VOLTAGE feedback mode
• lowest speed range • lowest current range
To avoid damage, ensure the supply selection jumper on the drive matches the
incoming ac supply - refer to "Figure 6 User adjustments" on page 10.
2. )RUDQLQLWLDOVWDUWDGMXVWWKHIROORZLQJSUHVHWV
Mocbos
MOTORTECH S.A. / Enertronica Santerno
Manual Completo
DC 3600XRi
MU 821.20/27
Rev.00
24/08/2023

Mocbos
MOTORTECH S.A. / Enertronica Santerno
Manual Completo
DC 3600XRi
MU 821.20/27
Rev.00
24/08/2023

9Commissioning
1
15
16
4
70
66
65
2
3
64
13
14
+10 REF
FWD
REV
MAX
IP
+IP
-IP
I/P
FORWARD
REVERSE
LOGIC
FWD
REV
MIN
XIP
START
JOG
5
COM
7
RUN
8
COM
9
TACH
52
ST
53
ZS
A+
59
REV
11
NO
10
NC
12
CO
56
SO
54
IO
60
TIM
69
IOM
55
RO 57
DO
A-
L2/N
L1/L
F+
F-
+10 V REF
+-++
+++
+
-+
Upper
4-20 mA
links
390R
x 2.5 UP DOWN
RAMP
+10 V REF
-10 V REF
+10 V REF
6
AUX
SPEED
-
+
50K
100K
FORWARD
UP DOWN
P3 P4
P8 P11
REVERSE
Lower
P2
5K
-1
50K
+24 V
FS
1S
ZS
1 s delay
zero setpoint
detect direction
detect
zero speed
detect
P1
MAX
SPEED
P5
IR COMP
switched
inverter
Ia> 110%
50%
STALL
Speed PI Current
Limit
-+
STABILITY
P7 IMAX+
P6
IMAX
P10
Current PI Synch &
Firing
Bridge select
& zero current
detection
-1
2Q
x 0.5
4Q
FWD
REV
Va/50
S4
x4
S3 x2
x1
S8
current
scale
S1
S2 F2
F1
110 V
240 V
+24 V
+12 V
+10 V
STALLED
S6
S5
S7
ZERO
STALL
REVERSE
TACH/AVF
-24 V
STALL
TIMER
RUNNING
x1
Motor
Armature
Mains
Supply
Power
Supply
Motor
Field
Lower control terminal
Upper control terminal
Power terminal
Switch
Link
Preset
KEY
*
*
*
Figure 5 Block diagram
Mocbos
MOTORTECH S.A. / Enertronica Santerno
Manual Completo
DC 3600XRi
MU 821.20/27
Rev.00
24/08/2023

10 Commissioning
Figure 6 User adjustments
WARNING!
When power is applied to the drive,
ALWAYS use an insulated tool when adjusting the presets.
Rotate clockwise to increase
current. S1 and S2 select the
range. Set the PRESET function
using the MODE jumper.
POS I NEG I
MOTOR fwd/rev BRAKE fwd/rev
FWD + and - REV + and -
Rotate clockwise to increase
response. Excessive rotation
may cause instability.
Rotate clockwise to increase
level of armature voltage droop
compensation. Excessive
rotation may cause instability.
Rotate clockwise to increase
drive acceleration in forward
direction from (+) 1 to 30 s.
Rotate clockwise to increase
minimum speed. Use to adjust
4-20 mAloop burden resistor
between 0 and 390 LIP$
mode is selected.
Rotate clockwise to increase
speed. Change the range with
S3 and S4.
MIN SPEED set to give 250 EHWZHHQ7DQG7
P$OLQNERWKDQGWHUPLQDOLVLQSXWLVUHWXUQ
/LQNIRU
67$//
7+5(6+2/'
&855(17
67$//
7$&$9)
'5,9(67$//621
=(5263(('621
0-25% 0-50% 0-75% 0-100%
9 9 9 9
2)) 21
1 2 3 4 5 6 7 8
=(52
5(9(56(
5$1*(
SPEED
5$1*(
S1
S2 &855(17
5$1*(
6HOHFWEHWZHHQIRXUPD[LPXPFXUUHQWUDQJHV
UHSUHVHQWVWKHPD[LPXPXQLWUDWLQJ
8VHWKH0$;&855(1735(6(7WRDGMXVWIURPWR
WKHVHOHFWHGPD[LPXPSHUFHQWDJH
S3
S4 SPEED
5$1*(
6HOHFWEHWZHHQIRXUPD[LPXPIHHGEDFNYROWDJHUDQJHV
8VHWKH0$;63(('35(6(7WRDGMXVWZLWKLQWKH
UDQJH7KHGULYHZLOOFRQWUROIURP9WRWKHVHOHFWHG
PD[LPXP9LQSXW
S5
6
S7
67$//
=(52
5(9(56(
6DQGVHOHFWWKHIXQFWLRQRIWKHUHOD\RQWHUPLQDOV
DQG7KHUHOD\GULYHURXWSXWVDOVRDSSHDURQ
7VWDOO7]HUR7UHYHUVHDQG7WLPHU,I
PRUHWKDQRQHIXQFWLRQLVVHOHFWHGWKHIXQFWLRQVDUH
$1'('UHIHUWRSDJH
S5ZKHQ21WKHUHOD\UHPDLQVHQHUJLVHGXQWLODVWDOO
FRQGLWLRQRFFXUV
S6ZKHQ21WKHUHOD\UHPDLQVHQHHUJLVHGXQWLOWKH
VSHHGIDOOVEHORZ
S7ZKHQ21WKHUHOD\LVHQHUJLVHGIRUVSHHGVDERYH
RIIXOOVFDOHLQWKHIRUZDUGGLUHFWLRQDQG
GHHQHUJLVHVDW]HURRUUHYHUVHVSHHG
S8 7$&$9)
6HOHFWWKHVSHHGIHHGEDFNVRXUFH
:KHQ21$50$785(92/7$*(LVVHOHFWHGGHIDXOW
:KHQ2))7$&+2LVVHOHFWHG
4Q TORQUE
2Q TORQUE
SPEED
WR9IRUWRYHFXUUHQWOLPLW
WR9IRUWR
DANGER!
(/(&75,&6+2&.+$=$5'
SUPPLY
6(/(&7
*
ANTI-CLOCKWISE MID-WAY CLOCKWISE
Stall lamp lights and drive quenches if the stall timer
trips - the time depends on the current demand:
STANDARD WITH 50% THRESHOLD
150% 30 secs 150% 5 secs
125% 60 secs 100% 30 secs
115% 120 secs 75% 60 secs
100% no trip 50% no trip
MAX
SPEED
MIN
SPEED
UP RAMP
DOWN RAMP
STAB
IR
COMP
MAX CURRENT
UP RAMP
DOWN RAMP
FORWARD
REVERSE
POS I
MOTOR
FWD
NEG I
BRAKE
REV
Rotate clockwise to increase
drive deceleration in forward
direction from (+) 1 to 30 s.
Rotate clockwise to increase
drive acceleration in reverse
direction from (-) 1 to 30 s.
Rotate clockwise to increase
drive deceleration in reverse
direction from (-) 1 to 30 s.
WR9IRUWRYHDQGYHFXUUHQWOLPLW
F2-
F1+
A1+
A2-
L2/N
L
1
+10
2
MIN
34
MAX
5
COM
AUX
7
RUN
8
COM
TACH
10 11 12 13 14 15
START
JOG
FWD
REV
10KNO
10 11 12
50%
STALL
LINK
FOR
4-20 mA
FS
1S
ZS
QUENCH
+-TIMER
STALL
*
6(/(&725
7(50,1$/6
7KLVMXPSHUVHOHFWVWKHDSSURSULDWHVXSSO\
WDSRQWKHFRQWUROWUDQVIRUPHU
5HIHUWRWKHVSHFLILFDWLRQIRUWROHUDQFHV
&KHFNWKHPRGHOW\SH
+,*+ /2: +,*+
415
240
/2:
240
110
30
When ON, stall timer tripped.
When ON, positive current demand.
When ON, negative current demand.
When ON, stall timer ticking and tripped.
7,0(5
V21
PV2))
25
*$7(
25
*$7(
)6
1S
ZS
581
=(52
SPEED
4XHQFK
SXOVHV
ZKHQ21
48(1&+FRQWUROVWKHUHPRYDORIWKHILULQJSXOVHV
MODE
See the label on the side of the transformer for the model type.
Mocbos
MOTORTECH S.A. / Enertronica Santerno
Manual Completo
DC 3600XRi
MU 821.20/27
Rev.00
24/08/2023

11 Commissioning
1
+10 +10 V precision reference. 10 mA maximum. Short-circuit proof.
2 MIN
Minimum (ACW) end of setpoint potentiometer, or 4-20 / 0-20 mA current loop input.
3
I/P +/-10 V input for speed setpoint.
4
MAX Maximum (CW) end of setpoint pot in bi-directional systems. Set by FWD/REV inputs to +10 V or -10 V
(defaults to -10 V if T15 and T16 are unused).
5
COM COMMON (4-20 mA / 0–20 mA return). Internally connected to T8, T58 and T68.
6
AUX Auxiliary input. Function set by links – refer to "7.4.3.3 Torque/Speed Mode" on page 16.
7
RUN Connect to COMMON to run. Function set by links – refer to "7.4.3.5 Quench Mode" on page 17. It
is good practice to connect a normally open auxiliary contact of the drive’s supply contactor in series
with this input.
:$51,1*5XQLVDQHOHFWURQLFLQKLELWIXQFWLRQ7KHȴHOGUHPDLQV
energised and all power terminals remain "live". RUN must not be relied
upon during hazardous operations).
8
COM Common - internally connected to T5, T58 and T68.
9
7$&+ Tacho input 25-400 V - negative for forward rotation with positive setpoint.
10
N/C
5HOD\FRQWDFWUDWLQJ$9DF&RQȴJXUDEOHIXQFWLRQȂUHIHUWR666RQSDJH
11
N/O
12
C/O
8
COM N/C STOP pushbutton.
13
N/O START pushbutton.
14
START latch line (JOG).
15
N/C FORWARD pushbutton.
16
N/C REVERSE pushbutton.
STOP
START
COM
8
13
14
15
16
7.3
Terminal descriptions
7.3.1
Control terminals
Mocbos
MOTORTECH S.A. / Enertronica Santerno
Manual Completo
DC 3600XRi
MU 821.20/27
Rev.00
24/08/2023

12 Commissioning
51
-24 -24 V relay supply. 25 mA.
NOT SHORT-CIRCUIT PROOF
52
ST Stall relay driver output. Maximum 25 mA. External relay is de-energised when stall timer trips if
connected as in "Figure 7 Relay circuits" on page 13.
53
=6 =HURVSHHGUHOD\GULYHURXWSXW0D[LPXPP$([WHUQDOUHOD\LVGHHQHUJLVHGDW]HURVSHHGLI
connected as in "Figure 7 Relay circuits" on page 13.
54
IO 6FDOHGFXUUHQWRXWSXWs9IRUsNŶRXWSXWLPSHGDQFH
55
RO 6SHHGVHWSRLQWUDPSRXWSXWs9IRUsNŶRXWSXWLPSHGDQFH
56
SO Speed output. Full-scale reading determined by max speed preset setting. Variable between ±4 V for
sWRs9IRUsNŶRXWSXWLPSHGDQFH7\SLFDOO\9IXOOVFDOH
57
DO ,QYHUWHGWRWDOVSHHGGHPDQGRXWSXW9IRU9IRUNŶRXWSXWLPSHGDQFH
58
COM COMMON. Internally connected to T5, T8 and T68.
59
REV Relay driver. Maximum 25 mA. External relay is de-energised when the speed reverses or at zero
speed if connected as in "Figure 7 Relay circuits" on page 13.
60
TIM Relay driver. Maximum 25 mA. External relay is de-energised when the stall timer is operating
(current demand > 105%) if connected as in "Figure 7 Relay circuits" on page 13.
61
+12 +12 V output. 10 mA maximum.
62
SS Stop/Start input. Close to -12 V to force a stall condition. Close to +12 V to release stall condition.
63
-12 -12 V output. 10 mA maximum.
64
XIP Input to speed setpoint ramp circuit when START relay RL2 is de-energised (T3 is disconnected).
±10 V for ±100%.
65
-IP Auxiliary inverting speed input. 0V to -10 V for 0V to +100% speed; 0V to +10 V for 0 to -100% speed.
66
+IP Auxiliary non-inverting speed input. ±10 V for ±100%.
67
+24 +24 V output. 25 mA maximum.
NOT SHORT-CIRCUIT PROOF
68
COM Drive Common. Internally connected to T5, T8 and T58.
69
IOM Metering output, 0 to 5 Vdc representing 0 to 100% scaled armature current. See SW1 and SW2.
70
IP
Auxiliary input to speed demand scaled ±10 V for ±100%.
Do not use if TORQUE/SPEED link is in the SPEED position as the auxiliary input function is
already being used by the AUX (T6) auxiliary terminal.
7.3.2
Ancillary terminals
Mocbos
MOTORTECH S.A. / Enertronica Santerno
Manual Completo
DC 3600XRi
MU 821.20/27
Rev.00
24/08/2023

13 Commissioning
7.3.3
Power terminals
A1+ Motor armature connection (positive).
A2- Motor armature connection (negative).
L2/N Line ac return; either neutral or L2.
LLine ac supply input.
F2- 0RWRUȴHOGFRQQHFWLRQQHJDWLYH
F1+ 0RWRUȴHOGFRQQHFWLRQSRVLWLYH
Terminals
52, 53, 59, 60
Minimum coil
resistance 2k8 RL
Terminal 51 (-24 V)
Figure 7 Relay circuits
Mocbos
MOTORTECH S.A. / Enertronica Santerno
Manual Completo
DC 3600XRi
MU 821.20/27
Rev.00
24/08/2023

14 Commissioning
7.4
Preset, switches and links
7.4.1
Presets
Preset Description
MAX SPEED Sets maximum speed for 100% demand.
MIN SPEED
Sets minimum speed for application.
1RWH0LQLPXPVSHHGIXQFWLRQRQO\
operates if the speed demand is
from a 10k potentiometer connected
between terminals 1 and 2 with its wiper
connected to terminal 3.
When operating with a 4 – 20 mA or 0 -
20 mA reference, the MIN SPEED preset
is used to adjust the burden resistance.
FORWARD UP RAMP Forward acceleration.
FORWARD DOWN RAMP Forward acceleration.
REVERSE UP RAMP Reverse acceleration.
REVERSE DOWN RAMP Reverse acceleration.
STAB Stability.
IRCOMP IR compensation.
MAX CURRENT 2x current limit presets. Refer to "8.2
Maximum Current Mode" on page 21.
7.4.2
Switches
7.4.2.1
S1 / S2
These two switches set the maximum current as a
percentage of the rated current of the unit. The MAX
CURRENT presets can then adjust the maximum current
between this current to zero.
S1 S2 % of rated
OFF OFF 25%
ON OFF 50%
OFF ON 75%
ON ON 100%
Mocbos
MOTORTECH S.A. / Enertronica Santerno
Manual Completo
DC 3600XRi
MU 821.20/27
Rev.00
24/08/2023

15 Commissioning
7.4.2.2
S3 / S4
These two switches set the range of the speed feedback voltage. Adjustment within the
range is through the MAX Speed preset.
S3 S4 Speed Feedback Voltage
OFF OFF 25 - 50 V
ON OFF 50 - 100 V
OFF ON 100 - 200 V
ON ON 200 - 400 V
7.4.2.3
S5 / S6 / S7
These three switches control the function of the relay on terminals 10 - 12.
S5 S6 S7 Energised relay state
OFF OFF OFF Motor NOT stalled
ON ON OFF Motor speed > ±1%
OFF OFF OFF Motor speed > +5% (forward)
As an example, with S6 ON and S5 and S7 OFF, when the motor speed is greater than
±1%, the relay is energised, terminals 11 and 12 are shorted, and terminals 10 and 12
are open. When the speed is less than ±1%, the relay is de-energised and the opposite is
WUXHWHUPLQDOVDQGDUHVKRUWDQGWHUPLQDOVDQGDUHRSHQ
If more than one of S5 – S7 is ON then the relay operation is the ANDing of the switch
states. For example, if switches S5 and S6 are ON, the relay is only de-energised if the
motor is stalled AND the speed is less than ±1%. In effect, this indicates a failure for the
motor to start.
7.4.2.4
S8
When S8 is ON, speed feedback is taken from the armature voltage. There must be no
connection to terminal T9.
:KHQ6LV2))VSHHGIHHGEDFNLVIURPWKH7$&+WHUPLQDO7
7.4.3
Links
7.4.3.1
Supply Voltage Selector
$OLQNLVSURYLGHGWRFRQȴJXUHWKHXQLWIRUHLWKHU+,*+RU/2:YROWDJHRSHUDWLRQ7KH
DFWXDORSHUDWLQJYROWDJHWKHQGHSHQGVRQWKHGULYHPRGHO
HIGH LOW
LL 415 V 240 V
LN 240 V 110 V
LV60 60 V 30 V
LV48 48 V 24 V
Mocbos
MOTORTECH S.A. / Enertronica Santerno
Manual Completo
DC 3600XRi
MU 821.20/27
Rev.00
24/08/2023
Table of contents
Popular Controllers manuals by other brands
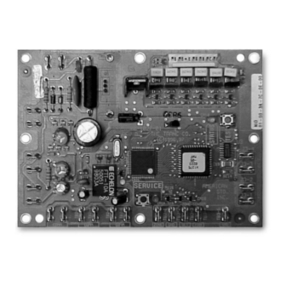
Trane
Trane Tracer ZN510 Installation, operation, and programming

BIFFI
BIFFI GIGS 0.3 Use and maintenance manual

Honeywell
Honeywell KromSchroder IC 40 technical information

IntesisHome
IntesisHome PA-AC-WIFI-1 quick start guide
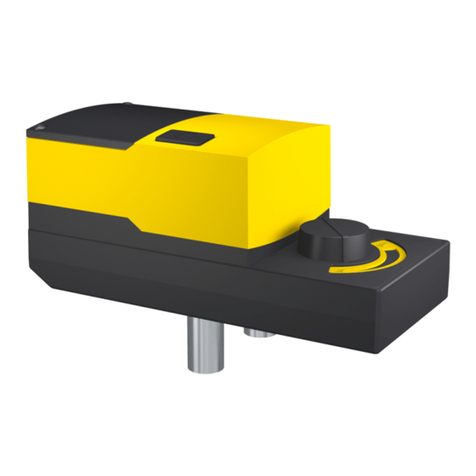
sauter
sauter ADM 322 Series Guidelines for the technician/fitter
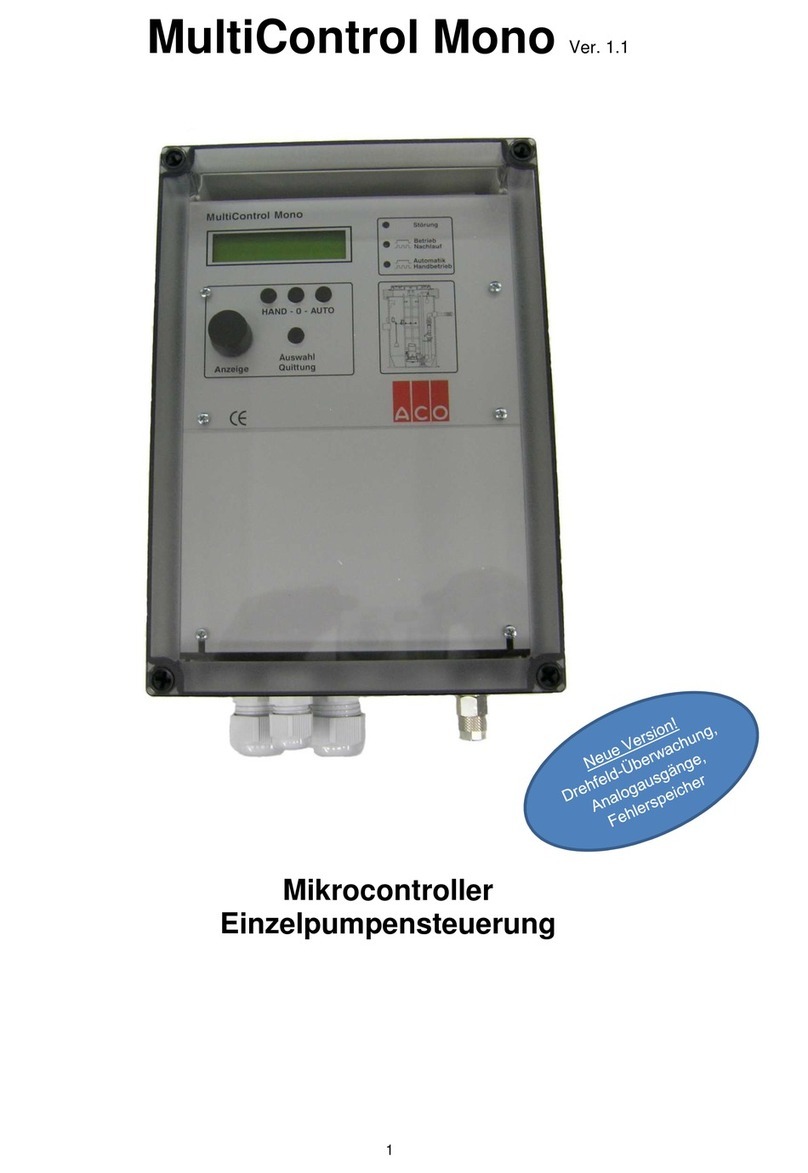
ACO
ACO MultiControl Mono manual