MSR ELECTRONIC PolyGard 2 CGC6 User manual

This page intentionally left blank

Table of Contents
1 General................................................................................................................................... 6
1.1 Applicability..........................................................................................................................................6
1.2 Intended Use.........................................................................................................................................6
1.3 Safety......................................................................................................................................................6
1.4 Responsibility Installer and Operator ............................................................................................6
1.5 Services..................................................................................................................................................7
1.6 Limited Warranty.................................................................................................................................7
1.7 Dispose of Device................................................................................................................................7
2 Functional Description ........................................................................................................... 8
2.1 General...................................................................................................................................................8
2.2 Functional Output ...............................................................................................................................8
3 Installation ............................................................................................................................. 9
3.1 Mounting Instructions ........................................................................................................................9
3.2 Installation Work .................................................................................................................................9
4 Electrical Connection ........................................................................................................... 10
4.1 General Notes.................................................................................................................................... 10
4.2 Terminal Connection ....................................................................................................................... 11
4.3 Connection Diagram ........................................................................................................................ 12
5 Commissioning..................................................................................................................... 13
5.1 General Notes.................................................................................................................................... 13
5.2 Registration of a DT6A Unit ........................................................................................................... 14
5.3 Check Registration ........................................................................................................................... 14
5.4 Retrieving the address again......................................................................................................... 14
5.5 Reset to Factory Settings................................................................................................................ 14
5.6 Deregistration of a DT6A Unit ....................................................................................................... 15
6 Operating Modes .................................................................................................................. 15
6.1 Restart (Diagnostic and Warm-up Stage).................................................................................... 15
6.2 Measuring Mode ............................................................................................................................... 16
6.3 Special Mode ..................................................................................................................................... 16
6.3.1 Maintenance and Calibration Mode .............................................................................. 16
6.3.2 Faults .................................................................................................................................... 16
Specicaons subject to change without noce. | GA_MSC2_Compact_E | 2023-03-27 | USA 230717 | Page 3of 60
INTEC Controls | 12700 Stowe Drive, Suite 100, Poway, CA 92064 | (858) 578.7887 & (888) GO.INTEC | inteccontrols.com
CGC6 – UserManual

7.6 Code Levels........................................................................................................................................ 19
Code level 1 (code not changeable) ............................................................................................ 19
Code level 3 (customer password is settable) .......................................................................... 19
8 Menu Overview .................................................................................................................... 19
8.1 Error Status......................................................................................................................................... 22
8.1.1 Error Memory...................................................................................................................... 22
8.1.2 System Messages and System Errors............................................................................ 22
8.2 Alarm Status....................................................................................................................................... 23
8.3 Relay Status ....................................................................................................................................... 24
8.4 Menu Measuring Values.................................................................................................................. 24
8.5 Display Parameters .......................................................................................................................... 25
8.5.1 Software Version ............................................................................................................... 25
8.5.2 Language.............................................................................................................................. 25
8.5.3 Service Phone Number..................................................................................................... 25
8.5.4 Customer Password........................................................................................................... 26
8.5.5 Error Time Delay ................................................................................................................ 26
8.5.6 LCD Function....................................................................................................................... 26
8.6 Installation and Calibration ........................................................................................................... 26
8.7 Installation ......................................................................................................................................... 27
8.8 Deregister Unit.................................................................................................................................. 27
8.9 Relay Parameters.............................................................................................................................. 27
8.9.1 Relay Mode.......................................................................................................................... 27
8.9.2 Relay Operation Mode...................................................................................................... 28
8.9.3 Relay Function Static/Flashing....................................................................................... 28
8.9.4 Signal Source ...................................................................................................................... 29
8.9.5 Alarm Trigger Quantity..................................................................................................... 29
8.9.6 Horn Function ..................................................................................................................... 29
8.9.7 External Override............................................................................................................... 31
8.9.8 Delay Mode of Alarm Relay............................................................................................. 32
8.9.9 Assignment to Fault .......................................................................................................... 32
8.9.10 Assignment to Maintenance Message .......................................................................... 33
7 Display Unit for CGC6 Series ................................................................................................ 17
7.1 Intended Use for the Display Unit................................................................................................ 17
7.2 Description......................................................................................................................................... 17
7.3 Operation ........................................................................................................................................... 17
7.4 Function of the Keys and LEDs on the Keypad.......................................................................... 17
7.4.1 Status LEDs.......................................................................................................................... 17
7.4.2 Setting / Changing of Parameters and Set Points...................................................... 18
7.5 Measuring Point................................................................................................................................ 18
Specicaons subject to change without noce. | GA_MSC2_Compact_E | 2023-03-27 | USA 230717 | Page 4of 60
INTEC Controls | 12700 Stowe Drive, Suite 100, Poway, CA 92064 | (858) 578.7887 & (888) GO.INTEC | inteccontrols.com
CGC6 – UserManual

8.11 System Parameters .......................................................................................................................... 42
8.11.1 System Information........................................................................................................... 42
8.11.2 Maintenance Interval........................................................................................................ 42
8.11.3 Average Function............................................................................................................... 43
8.11.4 Power-On Time................................................................................................................... 43
8.11.5 Deadband ............................................................................................................................ 44
8.11.6 AO Function......................................................................................................................... 44
8.12 Operating Data.................................................................................................................................. 45
8.13 Test Function for Alarm Relays ..................................................................................................... 47
8.14 Test Function for Analog Output .................................................................................................. 48
8.15 Calibration.......................................................................................................................................... 49
8.15.1 Zero Calibration ................................................................................................................. 50
8.15.2 Gain Calibration ................................................................................................................. 51
8.15.3 Burning Clean ..................................................................................................................... 52
8.15.4 Zero Calibration of Analog Output ................................................................................ 53
8.16 Addressing ......................................................................................................................................... 53
9 Configuration and Parameter Cards ..................................................................................... 54
9.1 Configuration Card System Parameters...................................................................................... 54
9.2 Configuration Card Alarm Relays / Signal Outputs .................................................................. 54
9.3 Configuration Card (Digital Measuring Points) ......................................................................... 55
9.4 Stored threshold values for alarm triggering............................................................................ 56
10 Maintenance and Inspection................................................................................................. 57
10.1 Inspection........................................................................................................................................... 57
10.2 Functional Test.................................................................................................................................. 57
10.3 Maintenance and Calibration ........................................................................................................ 58
10.4 Repairs ................................................................................................................................................ 58
11 Technical Data ...................................................................................................................... 59
11.1 CGC6 .................................................................................................................................................... 59
11.2 SB2Unit1.............................................................................................................................................. 60
11.3 System................................................................................................................................................. 60
8.10 MP Parameters .................................................................................................................................. 33
8.10.1 Activate/Deactivate MP.................................................................................................... 33
8.10.2 Selection of Gas Type and Measuring Range.............................................................. 34
8.10.3 Alarm Thresholds / Hysteresis........................................................................................ 38
8.10.4 Delay for Alarm ON and/or OFF...................................................................................... 39
8.10.5 Average Value Overlay (VDI 2053 Functionality)...................................................... 39
8.10.6 Assignment of Latching Mode <> Alarm ...................................................................... 40
8.10.7 Assignment of MP Fault <> Alarm.................................................................................. 40
8.10.8 Assignment of Alarm <> Alarm Relay ........................................................................... 41
8.10.9 Assignment of MP <> Analog Output............................................................................ 41
Specicaons subject to change without noce. | GA_MSC2_Compact_E | 2023-03-27 | USA 230717 | Page 5of 60
INTEC Controls | 12700 Stowe Drive, Suite 100, Poway, CA 92064 | (858) 578.7887 & (888) GO.INTEC | inteccontrols.com
CGC6 – UserManual

1 General
It is important to read this user manual thoroughly and clearly in order to understand the
information and instructions. The PolyGard®2 devices must be used within product specification
capabilities. Due to on-going product development, MSR-Electronic GmbH | INTEC Controls
reserves the right to change specifications without notice. The information contained herein is
based upon data considered to be accurate. However, no guarantee is expressed or implied
regarding the accuracy of these data.
1.1 Applicability
PolyGard2-Series:
•CGC6 Compact Controller
1.2 Intended Use
The PolyGard2 CGC6 Compact Controller is designed for detection and warning detection
of toxic, combustible or dangerous atmosphere in many commercial and industrial applications.
The PolyGard2 CGC6 must not be used in potentially explosive atmospheres.
The intended sites for indoor use within the ambient conditions defined in the technical data are all
areas being directly connected to the public low voltage supply, e.g. residential, commercial and
industrial ranges as well as small enterprises.
1.3 Safety
The operating instructions must be carefully read, understood and followed by all persons who
install, use, maintain and check the product. The product can only fulfil its intended functions if it is
installed, used, maintained, cared for and checked in accordance with the instructions provided by
MSR-Electronic GmbH | INTEC Controls.
1.4 Responsibility Installer and Operator
It is the responsibility of the installer and operator to ensure that all PolyGard®2 equipment is
installed and used in compliance with all national and local codes. The device must be checked for
correct installation and functionality by a qualified person before measurement operation is started.
In Germany, BGR 500 Chapter 2.33 must be applied for this purpose.
The PolyGard®2 devices are tested for function by the manufacturer before delivery. During
commissioning, a documented functional test is also required. The installation should only be carried
out by trained installation technicians, taking into account the current safety procedures for control
installations.
The required equipotential bonding connections (also e.g. secondary potential to ground) or
grounding measures are to be carried out according to the respective project regulations. It must be
ensured that no ground loops are created in order to avoid undesired interference in the
measurement electronics.
It is necessary to follow all instructions as well as the user documentation.
Specicaons subject to change without noce. | GA_MSC2_Compact_E | 2023-03-27 | USA 230717 | Page 6of 60
INTEC Controls | 12700 Stowe Drive, Suite 100, Poway, CA 92064 | (858) 578.7887 & (888) GO.INTEC | inteccontrols.com
CGC6 – UserManual

1.5 Services
It is recommended that PolyGard®2 equipment be inspected on a regular basis. Performance
deviations can be corrected based on regular maintenance. Recalibration and parts replacement can
be performed in the field by a qualified technician using the appropriate tools.
Alternatively, the easily removable, plug-in sensor head can be returned to INTEC Controls for
service.
Regular maintenance is to be carried out according to the instructions.
1.6 Limited Warranty
MSR-Electronic GmbH | INTEC Controls does not assume any liability in case of improper or
incorrect use of the device. The installer and operator are exclusively responsible for the design
and use of the product. If the product is not used, maintained or repaired in accordance with
the instructions for use, warranty and product liability claims as well as claims arising from any
guarantees assumed by MSR-Electronic GmbH | INTEC Controls for the product will be forfeited.
MSR-Electronic GmbH | INTEC Controls warrants PolyGard®2 devices against defects in material or
workmanship for a period of 2 years (1 year for sensors) from the date of shipment. Should a
defect in material or workmanship occur during the warranty period, MSR-Electronic GmbH | INTEC
Controls will repair or replace the unit at its option. This warranty does not apply to units that have
been modified, after repair attempts, or that have been damaged unintentionally or intentionally.
The warranty also does not apply to units in which the sensing element has been poisoned. The
above warranty is in lieu of all other express warranties, obligations or liabilities.
This warranty applies only to PolyGard®2 units. MSR-Electronic GmbH | INTEC Controls is not liable
for consequential damages resulting from the purchase or use of PolyGard®2 devices.
If the PolyGard®2 CGC6 needs to be returned, an authorized RMA number issued by INTEC
Controls is required.
1.7 Dispose of Device
In accordance with Directive 2012/19/EU, the device must not be disposed of as
municipal waste. Return the device for disposal to your national sales organisation,
which you can contact if you have any questions about disposal.
Outside the EU, you have to consider the corresponding directives.
Specicaons subject to change without noce. | GA_MSC2_Compact_E | 2023-03-27 | USA 230717 | Page 7of 60
INTEC Controls | 12700 Stowe Drive, Suite 100, Poway, CA 92064 | (858) 578.7887 & (888) GO.INTEC | inteccontrols.com
CGC6 – UserManual

2 Functional Description
2.1 General
The CGC6 is designed as a gas detection system for connection of max. 10 DT6A Units (DT6A +
Sensor SC2) via its own field bus. The function of the SC2 sensor head series is not the subject of
this user manual but can be found in the respective SC2 User Manual.
The controller monitors the measured values and activates the alarm relays if the specified max.
4 alarm thresholds for pre- and main alarm are exceeded. The analog 4–20 mA output provides
either a sum signal of all or certain measured values or the signal of one measured value.
The SIL2-compliant self-monitoring in the CGC6 as well as in the connected DT6A Units activates
the fault signal in the event of an internal fault as well as in the event of a fault in the field bus
communication (DT6A Unit) and in the event of a fault in the 4–20 mA output current signal.
2.2 Functional Output
SHORT DESCRIPTION OF THE FUNCTION DIGITAL OUTPUTS WITH RELAYS
Action Reaction
(GS = Gas Signal)
(AT =Alarm Threshold)
(HS = Hysteresis)
Alarm LED
Display / WAO
Alarm 1
Relay 1
Alarm 2
Relay 2
Alarm 3
Relay 5
Flashing/
Warning light
Alarm 4
Relay 4
Horn
Relay 3
(collective
fault)
GS < AT1
GREEN
Inactive
Inactive
OFF
OFF
Inactive
GS
AT1
RED slowly
flashing
Active
Inactive
OFF
OFF
Inactive
GS AT2
RED fast
flashing
Active
Active
OFF
OFF
Inactive
GS AT3
RED fast
flashing
Active
Active
ON
OFF
Inactive
GS
AT4
RED fast
flashing
Active
Active
ON
ON
Inactive
GS AT4
Taste Hupe Aus
RED fast
flashing
Active
Active
ON
OFF
Inactive
GS ≤ (AT3 –HS)
RED fast
flashing
Active
Active
OFF
OFF
Inactive
GS ≤ (AT2 –HS)
RED slowly
flashing
Active
Inactive
OFF
OFF
Inactive
GS ≤ (AT1 –HS)
GREEN
Inactive
Inactive
OFF
OFF
Inactive
Maintenance due (no
alarm, no fault)
GREEN flashing
Inactive
Inactive
OFF
OFF
Inactive
Internal error / fault
YELLOW
Inactive
Inactive
OFF
OFF
Active
Table 1: Function Digital Outputs with 3 Relays
Note 1: Relay 1 and 2: Operating mode energized
Status Inactive: Alarm OFF = relay coil energized
Status Active: Alarm ON or device without tension = relay coil de-energized
Relay 3: Operating mode energized
Status Inactive: No fault = relay coil energized
Status Active: Fault or device without tension = relay coil de-energized
Relays 4 and 5: Open-collector / transistor output, operating mode de-energized
Status OFF: Alarm OFF or device without tension
Status ON: Alarm ON
Note 2: Alarm thresholds can have the same value, therefore the relays and/or horn and warning light can be actuated
together.
Specicaons subject to change without noce. | GA_MSC2_Compact_E | 2023-03-27 | USA 230717 | Page 8of 60
INTEC Controls | 12700 Stowe Drive, Suite 100, Poway, CA 92064 | (858) 578.7887 & (888) GO.INTEC | inteccontrols.com
CGC6 – UserManual

3 Installation
Check for completeness and accuracy using the delivery documents and the identification
label on the device.
Electronics can be destroyed by electrostatic discharge (ESD). Therefore, the installation
work should be done only by persons connected to gr
ound, e. g. by standing on a
conductive floor or by taking appropriate grounding measures (acc. to DIN EN 100015).
3.1 Mounting Instructions
When choosing the mounting location, you have to consider the ambient conditions in order to get
representative measurement results. Please pay special attention to the following factors:
•External heat sources are not allowed on the installation site.
•Choose mounting location according to the local regulations.
•Consider ventilation conditions! Do not mount next to air passages or suction holes.
•The sample gas must pass the sensor even under adverse flow conditions. A flow test can be
performed for instance with smoke tubes.
•If the flow conditions are > 6 m/s, it is advisable to use a wind shield.
•Mount the device at a location with minimum vibration and minimum variation in temperature
(no direct sunlight).
•Avoid locations where water, oil etc. may influence proper operation and where mechanical
damage might be possible.
•Provide adequate space around the sensor for maintenance and calibration work.
•Observe possible constructor’s instructions
•The installation height of the DT6A Unit depends on the relative gas density of the
monitored gas type (see SC2 User Manual).
3.2 Installation Work
Assembly work must only be carried out under gas-free conditions.
The housing must neither be spot-drilled nor drilled through outside the knockouts.
The installation position of the gas detector is always with the sensor head downwards,
cables are introduced from above.
The housing is delivered in closed condition. Before breaking out the knockouts, the exact position
and size of the cable entries must be determined.
INTEC Controls recommends using a protective cap (C2-Z1) until commissioning to protect the
sensors on the DT6A Unit from dirt and damage. For sensors that can be poisoned by
silicones, such as all semiconductor and heat tone sensors, it is imperative to use a protective cap
(C2-Z1) and to remove it only after the silicones have dried and the unit is energized.
Specicaons subject to change without noce. | GA_MSC2_Compact_E | 2023-03-27 | USA 230717 | Page 9of 60
INTEC Controls | 12700 Stowe Drive, Suite 100, Poway, CA 92064 | (858) 578.7887 & (888) GO.INTEC | inteccontrols.com
CGC6 – UserManual

Mounting Procedure:
•Open housing cover.
•Break out the required knockouts on the housing for cable entries.
•Fix the CGC6 and the DT6A to the wall through the 4 marked mounting points of the housing
(see Figure 1) .
•The dimensions XX depend on the type and can be read on the back of the housing.
•Close and screw the cover.
Mounting
130 mm (5,12 in.)
115 mm (4,53 in.)
130 mm (5, 12 in.)
115 mm (4,53in.)
Mounting
D = 4 mm
Mounting
Sensorhead
94 mm (3,7 in.)
115 mm (4,53 in.)
130 mm (5,12 in.)
79 mm (3,11 in.)
D = 4 mm
Figure 1: Installation of Controllers
/ of DT6A Unit
4Electrical Connection
Assembly work must only be carried out under gas-free conditions!
Consider static electricity instructions (ESD)!
4.1 General Notes
•Installation and connection of the electrical installation should only be performed by a
professional when de-energized, according to the connection diagram and in accordance with
the relevant regulations.
•The technical requirements and regulations for wiring, electrical security, as well as project
specific and environmental and local conditions etc. must be observed when mounting.
•All terminals are screw type. The permissible conductor cross section can be read from the
Technical Data.
•When selecting and installing the cables you have to comply with the regulations concerning
the RS-485 bus installation. The installations have to be executed in line topology. Cable
lengths and types have to be considered as well.
•Avoid any influence of external interferences by using shielded cables for the bus line, but do
not connect the shield.
Specicaons subject to change without noce. | GA_MSC2_Compact_E | 2023-03-27 | USA 230717 | Page 10 of 60
INTEC Controls | 12700 Stowe Drive, Suite 100, Poway, CA 92064 | (858) 578.7887 & (888) GO.INTEC | inteccontrols.com
CGC6 – UserManual

•It is recommended to use the following cable types1:
Europe
USA/Canada
Power supply 230 V
NYM-J 3 x 1.5 mm2
14 AWG / 300 V
Alarm message 230 V
(also possible together with power supply 230 V)
NYM-J X x 1.5 mm2
14 AWG / 300 V
Signal message, bus connection, warning devices 24 V
J-Y(St)Y 2x2 x 0.8 mm2
min. 300 V
Table 2: Recommended Cable Types
1The recommendation does not consider local conditions such as fire protection etc.
•Strip the wires as shortly as possible. It is important to ensure that bare wires, e.g. wire shields
do not come into contact with the mounted PCB (risk of short-circuit).
•Low voltage wire and mains connected wire must be fixed separately by cable ties or similar,
to secure against looseness.
•The alarm signals are available as potential-free change-over contacts. If required, the power
supply is available at the L1 socket.
•Use copper conductors only, for the terminal is only for connection to copper wire.
•When choosing the option “Power Supply ≥ 90 VAC” you must make sure that a switch or a
circuit breaker is provided in the building automation especially for the unit. It must be
installed easily accessible near the unit. It has to be marked as a disconnecting device for the
unit and shall meet the relevant requirements of UL/IEC 60947 and UL/IEC 60947-3.
•The exact position of the terminals for the transmitters and alarm relays is shown in the
connection diagrams.
4.2 Terminal Connection
Attention:
Connecting the 24 V field bus voltage to the terminals BUS_A / BUS_B
can destroy the
Board completely!
•Open the cover.
•Insert the cables from above and connect them.
•Close the cover.
Specicaons subject to change without noce. | GA_MSC2_Compact_E | 2023-03-27 | USA 230717 | Page 11 of 60
INTEC Controls | 12700 Stowe Drive, Suite 100, Poway, CA 92064 | (858) 578.7887 & (888) GO.INTEC | inteccontrols.com
CGC6 – UserManual

DT6A
DT6A
X4
X4
1
1
2
2
3
3
4
4
GND
GND
24 VDC
24 V DC
Bus_A
Bus_A
Bus_B
Bus_B
Relays drawn de-energized.
Mode = energized
(Alarm ON = Relay OFF, Fault = Relay OFF)
Relay
Alarm 2
Relay
Fault
X2 X3 X41 1 12 2 23 3 3
CGC6 Compact Controller
Field BusX_Bus
1 32 4 5 6 7
X13
24 V DC
BUS_A
BUS_B
NC
GND
Flash
Buzzer
Digital
Input
Analog
Output
BUS_C
BUS_D
4-20 mA
GND
Remove resis tor
when device
is connected.
1 32 4
X12
BUS_C
AO_01
BUS_D
GND
DI_1
DI_2
1 2 3
GND
X11
Daisy-chained configuration
Max. cable length 2,900 ft
Cable: W202P-2288INTEC
Terminating resistor 560 R at the last DT6A Unit
+24 V
GND
NC
X1 23 1
Relay
Alarm 1
560 R
Digital
Input
Max. 10 DT6A Units
Power Supply
24 VDC
Specicaons subject to change without noce. | USA 230717 | Page 5 of 6
INTEC Controls | 12700 Stowe Drive, Suite 100, Poway, CA 92064 | (858) 578.7887 & (888) GO.INTEC | inteccontrols.com
CGC6
ELECTRICAL CONNECTIONS
Specicaons subject to change without noce. | GA_MSC2_Compact_E | 2023-03-27 | USA 230717 | Page 12 of 60
INTEC Controls | 12700 Stowe Drive, Suite 100, Poway, CA 92064 | (858) 578.7887 & (888) GO.INTEC | inteccontrols.com
CGC6 – UserManual

5 Commissioning
5.1 General Notes
All devices without exception run through a complete functional test before delivery.
However, transportation, storage, installation or special environmental conditions may lead to
(mostly small) deviations. It is therefore necessary that a person authorized by the manufacturer or
alternatively an expert puts the device properly into operation and performs a functional test.
Only trained technicians should perform the following when commissioning:
•Check for correct mounting location and height.
•Check if connection is correct according to connection diagram.
•Check that the board is firmly seated in the housing.
•Check power voltage.
•Calibrate the sensors of the DT6A Unit (if not already factory-calibrated).
oSee User Manual SC2.
•For commissioning, the CGC6 and the associated DT6A Units must be wired and ready for
operation according to the wiring diagram.
•During commissioning, all connected DT6A Units (max. 10) are registered on
the CGC6 without tools by assigning an address using the key on the DT6A Unit.
•The DT6A Units are already completely initialised and parameterised at the factory. The
status "Not registered” is indicated by the LED (green=OFF, yellow=ON).
•First, the installation mode is activated on the CGC6 in the "Installation & Calibration"
menu (installation active). This puts the CGC6 into a kind of search mode for the login
request of a new DT6A Unit.
•If the CGC6 detects a registration request, it assigns the smallest free address to it and
transfers the data stored in the DT6A Unit for gas type, measuring range, alarm thresholds, etc.
to the corresponding MP parameter address.
•After registration of the DT6A Unit, standard values for all relevant parameters are
already stored in the CGC6, so that no further adjustments are necessary here. For
project-specific adaptations, the parameters can be changed individually on the display.
•From chapter 8 onwards you will find the menu and parameter description.
•After commissioning, the error memory must be reset in the display (see section 8.1.1).
Specicaons subject to change without noce. | GA_MSC2_Compact_E | 2023-03-27 | USA 230717 | Page 13 of 60
INTEC Controls | 12700 Stowe Drive, Suite 100, Poway, CA 92064 | (858) 578.7887 & (888) GO.INTEC | inteccontrols.com
CGC6 – UserManual

5.2 Registration of a DT6A Unit
Select CGC6 mode "Installation active" (see chapter 8.6 Installation and Calibration).
DT6A Unit: Green LED OFF, yellow LED ON = Not registered
•Start the installation mode on the DT6A Unit by pressing the button for approx. 10 seconds.
The change of the operating mode is signalled by the yellow LED with 2 off-pulses within
the 10 seconds.
•After successful registration, the DT6A Unit signals the address by flashing the 2
LEDs (valency: yellow = 1; green = 5), e.g. 1x green and yellow simultaneously and then 2x
yellow = address 7.
•The DT6A Unit then switches to measuring mode (green LED=ON, yellow LED=OFF).
All further DT6A Units are now registered with the same procedure.
5.3 Check Registration
After registration of all DT6A Units, the "Measured values" menu is used to check whether the
correct gas type and measured value are displayed for all registered DT6A Units.
If an DT6A Unit is missing, the registration procedure must be repeated for this unit.
If the message "Comm. Error" is displayed instead of the measured value, the sensor head
is disconnected, or the field bus connection is interrupted at the DT6A Unit.
5.4 Retrieving the address again
The address can be queried at any time by pressing the button and releasing it after 3 seconds.
5.5 Reset to Factory Settings
Pressing the button for approx. 30 seconds resets the device to the delivery status (no address).
SC 2
432 1
Service Tool
Feldbus
Betriebsspg.
Status
LED
Taster
SC 2
432 1
DT6A
Field Bus
Operating Voltage
Status
LED
Push-
button
Figure 3: DT6A Unit
Installation
inactive
Installation
active
Specicaons subject to change without noce. | GA_MSC2_Compact_E | 2023-03-27 | USA 230717 | Page 14 of 60
INTEC Controls | 12700 Stowe Drive, Suite 100, Poway, CA 92064 | (858) 578.7887 & (888) GO.INTEC | inteccontrols.com
CGC6 – UserManual

5.6 Deregistration of a DT6A Unit
To cancel registration of an DT6A Unit, you must navigate to the "Deregister Unit" menu (see
chapter 8.6 Installation and Calibration).
By pressing the Enter and ↑keys on the display, the desired unit is
selected and deregistered by pressing the Enter key on
the CGC6 again.
On the CGC6, the measuring point of the deregistered unit is set to inactive again and the address
is noted as "Free" again. The deregistered unit can be re-integrated at any time.
If the log off is repeated for a unit that has already been deregistered, the message "Komm. Error" is
displayed.
6 Operating Modes
During operation, the unit can assume different operating modes. A distinction is made between the
warm-up phase, measuring mode and special mode, whereby special mode is divided into 2 different
subcategories.
6.1 Restart (Diagnostic and Warm-up Stage)
The device is designed in a way that it generally runs through all internal device tests (diagnostics)
in the Board and in the connected sensor head(s) after each power-up or processor reset before the
measuring operation starts. That means that the processor's internal components and the associated
program and working memories as well as the other components of the input and output units are
tested. This process takes approximately 0.5 seconds.
When all diagnostics have been successful, the warm-up phase of the sensor element starts. The
warm-up is necessary for the sensor element in the sensor head to assume a stable state after return
of the voltage without triggering a pseudo alarm. The duration of the warm-up phase depends on
the type of sensor used and can be read from the User Manual of the SC2/MC2 or SSAX1-2. If several
sensors are connected, the duration of the warm-up phase depends on the sensor head with the
longest warm-up phase.
During the warm-up phase, the yellow LED flashes every 2 seconds and "Power ON Time" appears in
the display.
Subsequently, the display shows
•the current bus address at the top left,
•the gas type in the top centre and
•the unit at the top right.
“Warm-up Time" appears in the lower section of the display (see starting menu chapter 8).
After the end of the warm-up phase, measurement operation starts and the necessary diagnostic
functions continue to run in the background.
Deregister Unit
U 0
Specicaons subject to change without noce. | GA_MSC2_Compact_E | 2023-03-27 | USA 230717 | Page 15 of 60
INTEC Controls | 12700 Stowe Drive, Suite 100, Poway, CA 92064 | (858) 578.7887 & (888) GO.INTEC | inteccontrols.com
CGC6 – UserManual

6.2 Measuring Mode
In normal operating mode = measuring mode, there are no faults present, the gas concentration of
the active sensors is continuously polled, checked for plausibility, output on the analog output (if
available) and provided on the field bus. The gas concentration is displayed on the built-in display.
When the alarm evaluation is activated, only with alarm threshold > 0, the gas signal is checked with
each measurement cycle, if it is ≥ alarm threshold (alarm evaluation for increasing concentration)
respectively ≤ alarm threshold (alarm evaluation for falling concentration) and if exceeding
respectively falling below, the alarm LED and the optional alarm relay are triggered. If the value falls
below / exceeds the alarm threshold minus / plus the set hysteresis again, the alarm is automatically
cancelled.
The gas detector continuously monitors itself, the measurement signal, the analog output, the alarm
relay and the communication to the sensor head.
The device continuously monitors itself, the measurement signal, the analog output, the alarm relay
and the communication to the sensor head.
If the measurement signal falls below the zero point, this will be tolerated
•for combustible gases with catalytic bead sensor element (Pellistor) up to a limit of - 10 % of
the measuring range (- 10 % LEL), the analog output signal drops down to 2.4 mA and within
this range no error is generated;
•for toxic gases with electrochemical sensor element and gases with IR-Premium sensor
element up to a limit of –4.5 % of the measuring range (- 1.125 % vol for O2), the analog
output signal drops down to 3.3 mA and within this range no error is generated.
Active dead band suppresses the 4–20 mA signal around the zero point (see chapter 8.11.5).
If the measurement signal exceeds the full-scale value, this will be tolerated up to a limit of + 6 %
of the measuring range, the analog output signal increases up to ≥ 21.2 mA and there will be still no
error generated.
6.3 Special Mode
6.3.1 Maintenance and Calibration Mode
The operator may set the gas detector in the Special Mode only when gas-free state is
ensured (no alarm), because the alarm function is not available in this mode.
While the Board is in maintenance/calibration mode (manual Special Mode), the status "Special
Mode" is displayed and/or sent to the GC-06 Controller. In Special Mode operation the query of the
gas concentrations is slightly delayed, but there is no alarm evaluation. The flashing yellow LED and
the display indicate the Special Mode. A fault overlays the LED display by continuous operation of
the yellow LED.
The operator can activate the Special Mode on the internal display. This mode includes
commissioning, calibration, testing, repair and decommissioning.
Pending alarms are held in active Special Mode, but new alarms are not generated.
The operator can exit the Special Mode after completion of work; if there are no further entries or
operations, the unit will automatically return to the measurement mode after 15 minutes.
6.3.2 Faults
See chapter 8.1
Specicaons subject to change without noce. | GA_MSC2_Compact_E | 2023-03-27 | USA 230717 | Page 16 of 60
INTEC Controls | 12700 Stowe Drive, Suite 100, Poway, CA 92064 | (858) 578.7887 & (888) GO.INTEC | inteccontrols.com
CGC6 – UserManual

7 Display Unit for CGC6 Series
7.1 Intended Use for the Display Unit
The display is used as visual indication, operating, commissioning and calibration unit for the
CGC6 series.
7.2 Description
The parameters, gas types, units, etc. specified in the description are only examples.
7.3 Operation
The complete configuration and service are made via operating keys in combination with the LC
display screen. Security is provided via 2 code levels against unauthorized intervention. Operation
is done via 6 pushbuttons.
Figure 4: Display CGC6
7.4 Function of the Keys and LEDs on the Keypad
Exits programming, returns to
the previous menu level.
Enters sub menus and saves parameter settings
.
Navigates within a menu, changes values.
Changes cursor position.
7.4.1 Status LEDs
The status LEDs indicate the operating state.
Green Continuous = Operating voltage
Flashing = Maintenance message
Yellow Continuous = Failure
Slowly flashing = Warm-up
Fast flashing = Special Mode
Red Alarm = Alarm
Specicaons subject to change without noce. | GA_MSC2_Compact_E | 2023-03-27 | USA 230717 | Page 17 of 60
INTEC Controls | 12700 Stowe Drive, Suite 100, Poway, CA 92064 | (858) 578.7887 & (888) GO.INTEC | inteccontrols.com
CGC6 – UserManual

7.4.2 Setting / Changing of Parameters and Set Points
Open desired menu window.
Code input field opens
automatically if no code is approved.
After input of valid code, the cursor jumps onto the first position segment to be changed.
Push the cursor onto the position segment, which is to be changed.
Set the desired parameter / set point with
the keys.
Input of value finished.
Change further parameters in the same menu.
Save the changed value?
YES, and back to higher menu level.
NO, (previous value is not overwritten) and back to higher
menu level.
7.5 Measuring Point
The term measuring point (MP) refers to the representation and processing (parameterization) of the
measured value of a connected gas sensor head.
For a measuring head with digital communication (SC2 series), the display shows:
DP = digital measuring point.
The following number defines the bus address of the gas transmitter at DP.
DP10: This is the measured value of the digital sensor head with bus address 10.
Specicaons subject to change without noce. | GA_MSC2_Compact_E | 2023-03-27 | USA 230717 | Page 18 of 60
INTEC Controls | 12700 Stowe Drive, Suite 100, Poway, CA 92064 | (858) 578.7887 & (888) GO.INTEC | inteccontrols.com
CGC6 – UserManual

7.6 Code Levels
All inputs and changes are protected by a 4-digit numeric code (= password) against unauthorised
intervention according to the regulations of all national and international standards for gas warning
systems. The menu windows of status messages and measured values are visible without entering a
code.
The access to a code level is cancelled if no button is pushed within 15 minutes or if you return to
start menu.
The code levels are classified in order of: code level 1 has top priority.
Code level 1 (code not changeable)
Code level 1 is intended for the service technician of the installer to change parameters and set
points. This password allows working on all settings. For opening the parameter menus, you must
first activate the Special Mode after code release (see chapter 8.6).
Code level 3 (customer password is settable)
Customer password is inactive in delivery state and is activated by entering a value. Same behaviour
as code level 1, only changing the own customer password is not possible.
Only the service technician who has last changed it knows the code since it can only be changed
individually via code level 1.
8Menu Overview
Menu operation is done via a clear, intuitive and logical menu structure. The operating menu
contains the following levels:
•Starting menu with indication of the device type if no MP is registered. Otherwise scrolling
display of the gas concentrations of all registered sensors in consecutive order in 5-second
intervals. If alarms are active, only the values of the sensors currently in alarm status will be
displayed.
•Main menu
•Submenu 1–3
Specicaons subject to change without noce. | GA_MSC2_Compact_E | 2023-03-27 | USA 230717 | Page 19 of 60
INTEC Controls | 12700 Stowe Drive, Suite 100, Poway, CA 92064 | (858) 578.7887 & (888) GO.INTEC | inteccontrols.com
CGC6 – UserManual

Starting Menu
Power-On Time of the master device (CGC6)
Second counter counts down, when communication display <> master device is OK.
In case of communication error, the count-down will stop.
After about 5 sec.
“Warm-up Time” is displayed. As soon as the sensor warm-up period has expired,
the measured value is displayed = measuring mode.
Selection Main Menu
Starting Menu
Main Menu
Submenu 1
Reading and
acknowledgement of errors
(see chapter
8.1)
Display of the alarm status
of active alarms
(see chapter 8.2)
Display of the relay status
(see chapter
8.3)
Display of measured values
(see chapter
8.4)
General display parameters
without safety relations
(see chapter 8.5)
Reading and change of the
relay, measuring point and
system parameters as well
as test and calibration
functions (see from chapter
8.6)
Power On Time
19 s
INTEC Controls
CGC6
D1 CH4 % LEL
Warm-up Time
D1 CH4 % LEL
1.8
Error Status
Alarm Status
Relay
Status
Measuring Values
Display
Parameters
Installation &
Calibration
Specicaons subject to change without noce. | GA_MSC2_Compact_E | 2023-03-27 | USA 230717 | Page 20 of 60
INTEC Controls | 12700 Stowe Drive, Suite 100, Poway, CA 92064 | (858) 578.7887 & (888) GO.INTEC | inteccontrols.com
CGC6 – UserManual
Table of contents
Other MSR ELECTRONIC Controllers manuals
Popular Controllers manuals by other brands
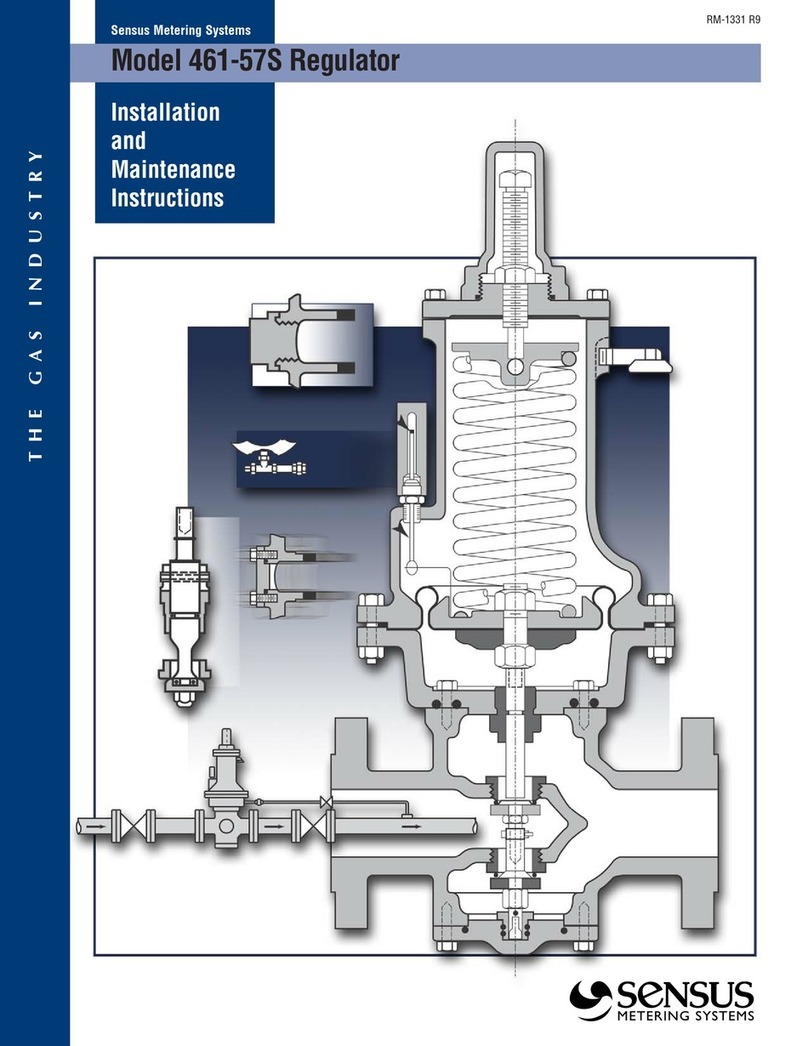
Sensus
Sensus 461-57S Installation and maintenance instructions
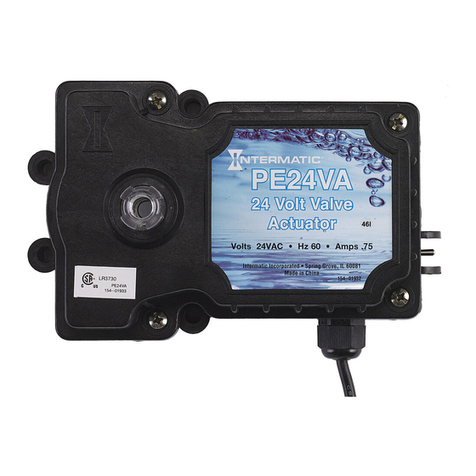
Intermatic
Intermatic PE24VA Installation, operation & service manual
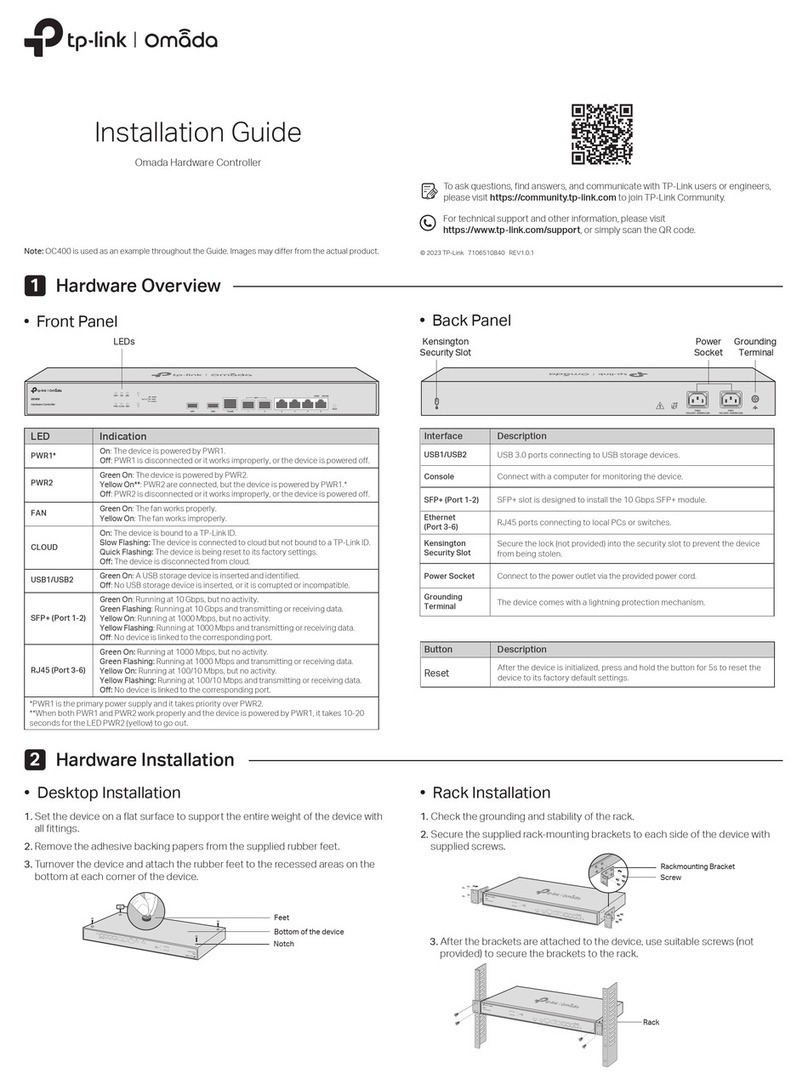
TP-Link
TP-Link Omada OC400 installation guide

Siemens
Siemens SQS35.53 manual
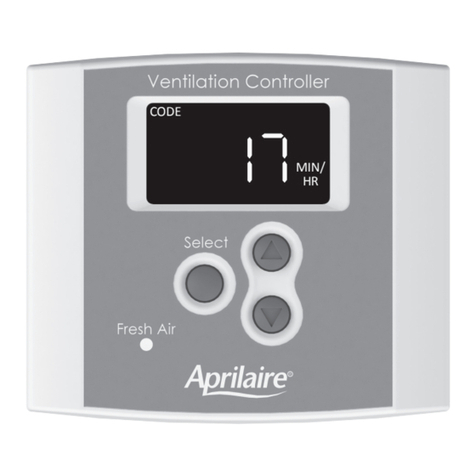
Aprilaire
Aprilaire 8126 Installation and operation manual

Caleffi solar
Caleffi solar iSolar 2 manual