MYTORQ MY-CURRENT User manual

1
INDEX
1. IMPORTANT SAFETY INSTRUCTIONS……………………………………………………….……...........2
2. PRODUCT SPECIFICATION……………………………………………………………………………....3
3. APPEARANCE………………………………………………………………………………………..…4
3.1 PANEL…………………………………………………………………………………………...4
3.2 BOTTOM…………………………………………………………………………………………5
3.3 UPPER COVER……………………………………………………………………………………5
3.4 LCM DISPLAY……………………………………………………………………………………6
4. SYSTEM SETTING METHOD…………………………………………………………………………..….6
4.1 SHORTCUT KEYS……………………………………………………………………………….…6
4.2 ENTER THE SETTING PAGE…………………………………………………………………….….6
5. CONTROLLER SETTING………………………………………………………………………………....7
6. JOBS AND SEQUENCES……………………………………………………………………………..…...8
7. TOOLS AND DATA………………………………………………………………………………..……10
8. DESCRIPTION OF DISPLAY STATUS CODES………………………………………………………….….10
9. DESCRIPTION OF EXTERNAL OUTPUT CONTROL FUNCTION……………………………………….…….12
10. DESCRIPTION OF EXTERNAL INPUT CONTROL FUNCTION…………………………………………..……13
11. MY-CURRENT DATA TRANSMISSION INSTRUCTIONS AND SEQUENCE CONTROL SUGGESTIONS………...14

2
Read all instructions before operation
(Exploded parts diagram attached)
Warning 告
For the sake of safety, read the User Manual carefully before using the current controller; be sure to operate it according to the
instructions in this Manual, and pay attention to all warnings.
1. Important Safety Instructions
1. Use the voltage specified in the current control screwdriver controller manual.
2. When using the power supply of the current controller, ensure the current loop and safety switch device, and connect the earthing
wire properly.
3. Do not place heavy objects or pile up objects on the current controller; keep it working at an appropriate temperature and humidity.
4. Do not place the current controller in a poorly ventilated room or expose it to dust and metal filings.
5. Do not place the current controller in a high temperature and humid environment or a space with flammable gas.
6. Do not install the current controller in a high place; put it in a safe, stable and mounted position to prevent the danger of falling.
7. Do not use the power cord to pull the current controller and power supply or pull the power cord away from the socket.
Precaution 意
1. Use this controller with a set of dedicated current control screwdrivers MY-CURRENT series screwdrivers.
2. Use this current controller with our company's current control screwdriver and power supply. If you use it with a current control
screwdriver, current controller or power supply not produced by our company, or use non-original spare parts for maintenance, the
controller may be damaged. The company will not be responsible for any failure or poor quality and should result in the
invalidation of all our guarantees.
3. While the screwdriver is in progress, if the forward and reverse switches are switched instantaneously, the machine will start the
protection program and the screwdriver will stop running.
4. After the power is turned off, the DC cable can only be plugged and unplugged after the LED light has extinguished.
Grounding description
When using the electric screwdriver controller, it should be grounded to prevent the operator from getting an electric
shock. The controller is equipped with three wires and a three-pin grounding plug suitable for grounding sockets. The
grounding wire of the socket itself must be connected with the grounding wire of the power supply device to be grounded. The
yellow-green wire is the grounding wire. Do not connect this yellow-green wire to the energized connector. In addition to the
leakage safety grounding, the grounding wire in the controller can also eliminate the ESD static electricity generated when the
screwdriver is working by relying on the grounding wire.

3
2. Product specification
1. Read the User Manual carefully before operation and operate the current controller according to the safety regulations.
2. When inserting or unplugging the screwdriver cable and the plug of the power cord, it must grasp the plug part of the cable.
3. Mount the current controller to avoid danger caused by pulling.
4. Do not get close to oil, chemical substances or hot objects; be careful not to let the cable being scratched by sharp object during
work.
5. This type of controller can only be used exclusively for the current control screwdrivers produced by our company. Do not use the
current controller for other machines.
6. If the controller is overheated, or the current under the load exceeds the maximum current of the fuse, the fast fuse will
automatically break off to cut off the power supply; if it continues to trip or the switch action is abnormal, stop the operation
immediately and send the current-control screwdriver and the controller back for repair.
7. While the screwdriver is in progress, if the forward and reverse switch is switched instantaneously, the machine will start the
protection program and the screwdriver will stop running.
8. Do not disassemble the current controller arbitrarily and try to repair it by yourself.
9. When not in use, turn the main power switch "OFF", and unplug the power plug.
Model No. MY-CURRENT
Input voltage AC 115V / 230V Input frequency 50 - 60Hz
Input current 6.3A Output voltage DC 40V
Output current Max 9A Output power 360W
Work cycle 1s ON / 3s OFF
Outer dimension 241 x 185 x 127(mm)
Weight 3.46kg
Screwdriver model No. MY-CURRENT 1.2 series
Operation

4
3. Appearance
3.1 Panel
1.
OK signal indicator 7.
Start signal indicator
2.
NG signal indicator 8.
Reverse signal indicator
3.
OKALL signal indicator 9.
Disable signal indicator
4.
4-position, 7-sect torque display 10.
16X4 LCM display setting
5.
ESC button (return/exit/enter setting mode) 11.
Enter button(select/confirm)
6.
Up, down, right and left buttons
Job: job work JS: job sequence TR: display counting data
Time: display screwdriver acting time
Angle: display screwdriver acting angle
Torque: display torque data
Status: display status (OK, NGHQ, NGLQ, NGHA, NGLA, NG-F, OKALL....)
1.
2.
3.
7.
8.
9.
4.
10.
11.
6.
5.

5
3.2 Bottom
3.3 Upper cover
1.
Micro SD card socket (data storage) 6.
Voltage changeover switch
2.
Protocol output port 7.
Scanner USB type-A socket
3.
Software-updating socket 8.
Wired communication port
4.
Tool connection seat 9.
Output screwdriver signal port
5.
Power cord socket and power switch 10.
Input control screwdriver signal port
1.DCfuse seat (incl. 10A/250 fuse)
2.
Grounding connector seat
(FG)
1.
2.
1.
2.
3.
4.
6.
5.
9.
10.
8.
7.

6
3.4 LCM display
4. System setting method.
4.1 Shortcut keys
4.2 Enter the setting page.
1. Display currently underway job
2. Display current underway sequence
3. Display remaining number of screws
4. Display current system status
5. Display tool actuation time (seconds)
6. Display tool actuating circle number
7. Display tool actuation angle
8. Display tool actuating torque
1. LEFT: Press this key once to clear the counting number of screws; press and hold the key
for three seconds to hear a beep to return to the first sequence
2. DOWN: Press and hold for three seconds to hear a beep to return to the previous sequence
3. UP: Press and release UP and DOWN together to view the speed/torque range of the tool
(screwdriver). Press DOWN on the version information screen to display the controller
version information. Press DOWN again to display the current network IP/ Mask/Gateway
4. RIGHT: Press and hold for three seconds to hear a beep to go to the next
sequence
1. Press and hold "ESC" for three seconds; when hearing the "beep" from the buzzer, enter the
page for verifying the password
2. Enter the password according to the method displayed in the figure, and press "Enter" to
enter the next page after inputting
3. Display according to the figure: controller setting, job and sequence, tools and information
pages; Press "ESC" to return to the status display page; select an item and press “Enter” to
enter the next page
1
2
3
1
4
2

7
5. Controller setting
Name
Data
setting item
Function description
Default value
Controller mode Single Online mode
Single: Single mode
Single
Equipment No. 001~250 Set equipment number 01
Tool activation
setting
Press start/external
start
/
both
Select tool activation method Both
Baud setting 115200/57600/38400
/19200/9600
Select the baud of controller’s data transmission 115200
Back to default
N/Y
Y:
Return back to default status and clear memory data
N
OKALL Single/each time Single: OKALL appears when all sequences in the job
are locked
Each time: When a sequence in the job is locked, an
OKALL will appear
Single
Gate mode None/
First reaction/
Second reaction
None: Do not activate this mode
First reaction: Once the workpiece is in place (short-
circuit signal), the initial state shall be low; when a
lock occurs, it shall be enabled once by operating high.
Second reaction: Trigger-twice workpiece in place
(open circuit signal), the initial state shall be high;
when a lock occurs, it shall be activated for the second
time by operating low.
None
Barcode
activation
OFF/ON Scan barcode before turning on or off job performance.
After it is turned on, the word BS will appear on the
job
screen and locked; the lock will be unlocked when
the barcode is scanned to switch the sequence
. BS will
also appear and locked when the locked number are
completed, which needs to scan the barcode again to
switch to the
sequence
to be run.
OFF
Store job barcode
1~15 After pressing this option, a “scan job code” prompt
appears. After selecting the job
group to be set, use the
barcode machine to scan the barcode, and the scanned
barcode will be automatically stored in the controller.
Set the job group within 1~15, and switch the barcode
used by the job group. Each group of barcodes should
not exceed 54 bytes.
01
Barcode setting Job group: 01~15
From: 01~54
Number: 01~54
Set the interval for barcode judgment of each job
group.
From: Set the first character barcode is to judge from
Number: How many judging characters are to be
counted from the judging character to the end. After
scanning the barcode, the total number of characters in
the barcode will be displayed
Job group: 01
From: 01
Number: 01
Counting method
Count down/count
up
Set the count times Count down
Time setting YYYY/MM/DD
HH:MM:SS
Set controller time.
AD year/month/day/hour/minute/second
2022/01/01
01:01:01

8
Set product serial
number
Product serial
number
Display the product serial number of the device Product serial
number
Change password
0000~9999
Set password
0000
Data export
settings
Wireless/wired
network
/RS
-
232
Select data output by wireless network or wired
network
RS-232
Sound mode
ON
/
OFF
Set the buzzer switch
ON
Select
a language
Chinese
/English
Select language interface
Chinese
LAN: STATIC/DHCP STATIC: Manually set, using a fixed IP
DHCP dynamic: Automatically
obtain, distribute IP via
router. (In the working screen of the controller, press
UP: the UP and DOWN are pressed together and then
release them to enter the version information screen;
then, press DOWN twice to display the current
network IP/Mask/Gateway of the controller)
STATIC
6. Jobs and sequences
Name Data setting
item
Function description Default value
Select job 01~15 Select the job (project) 00
Set job group 01~15 Set the job (project). Here you can select to set up to 15
groups of
job
pages and set the following items
01
Set job name ****** Set the job name, you can set it in number, English capital
(small) letters, or symbols
******
Job sequence
number
01~15 Set the total number of job sequences 01
Job sequence 01/01~15/15 The current sequence /total number of sequences, press
"RIGHT" on the controller to switch and display up to 15
groups of
sequence
pages and set the following items
01/01
Lock group - Set the type of screw lock, press Enter to enter the menu; the
following options are displayed:
Job 01~15 Display job 01
Job sequence 01~15 Display sequence 01
Screw name
(job sequence
name
)
****** Set the sequence name, you can set numbers, English capital
(small) letters, symbols
******
Screw schedule
number
01~05 Sets the total number of schedules used for these screws
in the
operation
01
Optimization OFF/ON
When set to low torque and high speed or high torque and low
speed, the controller will automatically adjust the speed to
make the actual torque
performance more stable
ON
Threshold OFF/ON The function of opening/closing the threshold point
(torque/speed
drop
)
OFF
Schedule
(Screw
schedule)
1/1~5/5 According to the number of screw schedules, display the
current schedule/total number of schedules for these screws.
Press "RIGHT" on the controller to switch and display up to 5
sets of schedule pages and set the following items
1/1
Target Torque/Delay T
/Angle
Select the locking target as Torque (torque), Delay T (delay
time) or Angle (angle)
Torque

9
Torque
Target/Delay
Time/Angle
Target
Target torque
value (kgf.cm)
000.00~550.00
(006.00~030.00)
Delay time:
0.0~9.9
Target angle
value
: 0~9999
Set
the target torque value, delay time or target angle value of the
screwdriver.
The target torque value must be entered in a reasonable torque
range according to the specification of the screwdriver. If the
setting value exceeds the specification far, the screwdriver will
not start.
(Example: 6~30kgf.cm=0. 6~3N.m)
The lower limit
of target torque
value follows the
screwdriver
specification and
displays
automatically
RPM 100~upper limit
of screwdriver
specification
To set the speed (rpm) of the screwdriver lock, it must be set
according to the speed range of the screwdriver specification and
the required speed. It cannot be set to a speed exceeding the
screwdriver specification.
100
Direction CW/CCW Set the rotation direction of the screwdriver lock, CW
(clockwise)/CCW (counterclockwise)
CW
Q Limit (000.00~000.00)
~
(550.00~549.99)
Set the upper limit ~ lower limit of the torque; when the
screwdriver lock value exceeds the upper/lower limit,
NGHQ/NGLQ will be displayed
The upper limit
follows the
screwdriver
specification and
displays
automatically
C Limit (0000~0000) ~
(9999~9998)
Set the upper limit ~ lower limit of the angle, when the
screwdriver lock value exceeds the upper/lower limit,
NGHA/NGLA will be displayed
9999~0000
Threshold torque
000.00~xxx
(Upper limit
cannot exceed
the target torque
value)
After touching the set threshold point of torque, the controller
starts to calculate the locking angle of screwdriver, and it is OK
to stop within the set torque upper/lower limit range
000.00
Torque at speed
drop point
000.00~xxx
(Upper limit
cannot exceed
the target torque
value)
After touching the torque value of the set speed drop point, the
screwdriver speed will drop, and it is OK if it stops within the
range of the set torque upper/lower limit
003.00 (kg-cm)
Speed at speed
drop point
100~xxx
(Upper limit
equals to the set
rpm of screw
sequence)
Set the speed of the screwdriver when the torque value of the
speed drop point is reached
100
Number of
locking screws
00~99 Set the total number of screw locks in the sequence 00
Torque unit Kg/cm; Lb/inch.
Kg/
m.
;
N/m
Set torque display unit Kg/cm
Disable start
when NG
OFF/1~9
Set the processing method selected when screwdriver lock is
wrong
1~9:
Setting 1: lock the screwdriver for first locking error, setting 2: for
continuous locking error, lock the screwdriver when the second
error occurs... and so on; if one of the locking errors is OK, make
recalculation.
Initiate 1-9 functions: When the error signal is "NS", the
screwdriver is locked immediately; user needs to press "ENTER" to
confirm to release it (if it is the I/O part, it is an external CONFIRM
signal, and the screwdriver can still remove the screw before
confirmation is made)
Off: When the error signal "NG" displays, the screwdriver will not
stop, nor affect the next startup of the screwdriver, only a warning
will be issued
OFF

10
OKALL
prohibits the
screwdriver
from starting
OFF/ON Set the processing method selected when the total number of
screws in the sequence is counted and the action is completed.
On: Lock the screwdriver immediately when the number of
pieces in the sequence is completed.
User needs to press the "ENTER" to confirm to cancel the
forward rotation.
(For the I/O part, it is an external CONFIRM signal)
Off: When the action is completed, the screwdriver won’t
stop; nor will it affect the next start of the screwdriver
OFF
OK one duration
0.0~9.9 Set the number of seconds for the OK signal to last each time
a screw lock is completed
9.9
OKALL
duration
0.0~9.9
Set the number of seconds for the OKALL signal to last when the
total number of screws in the sequence is counted and the action is
completed
1.0
Lock
combination
Soft/Hard
According to the hardness of the material to be locked (such as
springs, sheet metal or hard steel plates), set soft binding or hard
binding
Soft
Screw removal
direction
CCW/CW
Set the rotating direction when the screwdriver removes the screw,
CCW (counterclockwise)/CW (clockwise)
CCW
Screw removal
speed
00~10
Set the speed of the screwdriver when removing screws, 00:
screwdriver doesn’t run, 01 (low speed) ~ 10 (high speed) are, in
order, 10% ~ 100% of the maximum speed of the screwdriver
01
Screw removal
force
00~10
Set the force of the screwdriver to remove the screw, 00:
screwdriver doesn’t run, 00 (low torque) ~ 10 (high torque) are, in
order, 10% ~ 100% of the maximum
torque of the screwdriver
01
K 1.5%~999.8% Adjust this value so that the actual torque value of the
screwdriver lock is close to the torque value displayed on the
controller (KTM torque meter is an optional product).
Please gradually adjust this percentage value. If the value is
adjusted too large or too small, the screwdriver torque and
function will be reduced. Can't move normally
100%
Compensate -254 ~ +254 Make fine adjustment, making the actual torque value of the
screwdriver lock closer to the torque value displayed on the
controller (KTM torque meter is an optional product)
+000
7. Tools and data
8. DESCRIPTION OF DISPLAY STATUS CODES
Code Description Lock-release method
C1 Confirmation of trigger-once external sensor mode External sensor mode
Trigger once
C2 Confirmation of trigger-twice external sensor mode External sensor mode
Trigger twice
C3 When the "prohibition to start after sequence completion" is enabled, the LCM
screen will display "C3" when OKALL
Panel Enter key / CONFIRM
key for external switch
Name
Function description
Calibration tool Enter the calibration mode, this function is only available for agents, not for
customers

11
C4
When the "prohibition to start when the sequence is completed" & "sensor
mode trigger-once sense" is turned on;
the LCM screen will display "C4" when OKALL
External sensor mode
Trigger once + panel Enter
key / CONFIRM key for
external switch
C5
When the "prohibition to start after sequence completion" & "sensor mode
trigger-twice sense" is turned on;
the LCM screen will display "C5" when OKALL
External sensor mode
Trigger twice + panel Enter
key/ CONFIRM key for
external switch
NS When an operation error occurs, the LCM screen will display "NS" Panel Enter key/ CONFIRM
key for external switch
BS When the "Barcode Start" is turned on, "BS" will be displayed before running
the
job
Barcode scanning
OK
Each time when the lock is in place, the LCM screen will display "OK"
NA
OKALL
When the set number of screws is completed in each locking sequence, the
LCM screen will display "OK ALL"
NA
NG
NG-F: Screw schedule not completed.
NS-F: This state needs to go through the Confirm/Enter sequence before
starting the next action.
NGLQ/NGHQ: After the screwdriver is started, the stop torque is less than the
"lower limit of judging locking torque” or "greater than the "upper limit of
judging locking torque" (judged according to the setting value of Q Limit).
NGLA/NGHA: After the screwdriver is started, the stop angle is less than the
"lower limit of judging locking angle” or "greater than the "upper limit of
judging locking angle" (judged according to the setting value of C Limit).
NA
E1
Current protection: When the electric screwdriver lock reaches the protection
point of the motor current, it will stop the action of the electric screwdriver and
display this symbol on the LCM, indicating that the screwdriver is currently
under the abnormal protection of motor startup
NA
E4
Temperature protection: When the internal temperature of the electric
screwdriver is too high, the action of the electric screwdriver will be stopped
and this symbol will be displayed on the LCM, indicating that it is under over-
temperature protection now
NA
E5
Stall protection: When the electric screwdriver motor starts abnormally, it will
stop the action of the electric screwdriver and display this symbol on the LCM,
indicating that the screwdriver is under motor start abnormal protection now
NA
E9
Abnormal operation: When the electric screwdriver lock is running
continuously for more than 20 seconds, it will stop the action of the electric
screwdriver and display this symbol on the LCM, and E9 will not be displayed
when removing screws
NA
Err
Abnormal operation of the sensor mode: When the sensor mode is turned on
and operated incorrectly (the sensor high/low initial state is incorrect), the
buzzer will sound
intermittently,
and this symbol will be displayed on the LCM
Check sensor phase (at
normal initiation state) and
setting mode
ES
Communication abnormality at the screwdriver terminal: When the detection of
the communication signal of the electric screwdriver is abnormal, the operation
of the electric screwdriver will be stopped, and this symbol will be displayed on
the LCM
NA
EOC
When the LCM displays the EOC prompt, it means that the SGT-CC
screwdriver needs to be calibrated and maintained.
Note: When the total number of locks are greater than one million times, it will
prompt each time it is booted
NA
ELS
When the LCM displays the ELS prompt, it means that the capacity of the SD
card is lower than 100MB, and the action of the electric screwdriver will stop; it
needs to press “Enter” to release the locked state of the screwdriver.
NA
EPC ADV MODE: communication detection is abnormal. NA

12
9. Description of external output control
※Note:
1. For INPUT contact, if non-isolation (wet contact) control method is used, a 10K resistor needs to be connected in series on the
wiring to prevent equipment damage.
2. ※CN1(V+) and CN14(GND) can supply DC+24V (default). (DC +12V is also applicable)
※If user need other DC voltage, he/she must use step-down circuit to step down voltage
※If user needs input voltage to drive the police instrument, the input voltage should not exceed DV+/-40V, +/-1A, max:10w (use
MOS RELAY I/O version)
Connector
No Definition
Description
Ordinary load Inductive load
CN 1 START RUN FWD:
CN1 and CN2 are connected when a screwdriver is
initiated.
CN1 + CN2 are connected when short-circuited.
CN1 + CN2 are disconnected when open-circuited
CN 2 COM
CN 3 -
CN 4 -
CN 5 REVERSE
RUN BWD:
CN5 and CN6 are connected when screwdriver runs in
reverse direction.
CN5 + CN6 are connected when short-circuited.
CN5 + CN6 are disconnected when open-circuited
CN 6 COM
CN 7 OK OK:
CN7 and CN8 are connected when locking down a
screw.
CN7 + CN8 are connected when short-circuited.
CN7 + CN8 are disconnected when open-circuited
CN 8 COM
CN 9 NG NG:
CN9 and CN10 are connected when error occurs.
CN9 + CN10 are connected when short-circuited.
CN9 + CN10 are disconnected when open-circuited
CN 10 COM
CN 11 OKALL OK Sequence:
CN11 and CN12 are connected when locking down all
screws in the sequence.
CN11 + CN12 are connected when short-circuited.
CN11 + CN12 are disconnected when open-circuited
CN 12 COM
CN 13 Vdc
The voltage output of controller is DC+12V/100mA or
+24V/50mA.
Default
:
+24V/50m
A
(
+12V/100mA
is also applicable
)
CN 14 GND GND of output power
C
N
1
3
C
N6
C
N5
C
N
1
3
C
N6
C
N5
C
N
1
3
C
N7
C
N8
C
N
1
3
C
N7
C
N8
C
N
1
3
C
N9
C
N10
C
N
1
3
C
N9
C
N10
C
N
1
3
C
N11
C
N12
C
N
1
3
C
N11
C
N12
C
N
1
3
C
N1
C
N2
C
N
1
3
C
N1
C
N2

13
10. Description of external input control
Connector
No Definition
Description
CN 1 Input external start signal
START_IN
1. Screwdriver starts to rotate when CN1+CN2 are short-circuited
(CLOSE).
2. Screwdriver stops rotating when CN1+CN2 are open-circuited
(OPEN).
CN 2 GND
CN 3 Input external reverse signal
REVERSE
1. The external reverse signal CN3+CN4 is first short-circuited
(CLOSE), and when the start signal CN1+CN2 is short-circuited
(CLOSE), the screwdriver begins to reverse-start
2. The external reverse signal CN3+CN4 is first opened (OPEN),
and the start signal CN1+CN2 is short-circuited (CLOSE), the
screwdriver starts to rotate forward
CN 4 GND
CN 5
Input external prohibition
signal
DISABLE
1. When CN5+CN6 is short-circuited (CLOSE), the screwdriver
cannot be started
2. When CN5+CN6 is open (OPEN), the screwdriver can start
CN 6
GND
CN 7
Input external conforming
signal
CONFIRM
1. When the system asks to press the confirmation key, it can be
replaced by this CN7+CN8 short circuit (CLOSE)
2. After CONFIRM is performed, the NG signal will also be cleared
CN 8
GND
CN 9 Input external CONFIRM
CLEARED
When the count value needs to be cleared, the function can be
activated through this CN9+CN10 short circuit (CLOSE)
CN 10
GND
CN 11 External sensing switch
GATE
1. Input a confirmation signal to make the machine determine that
the locked object is a valid value
2. Inductive switch: The external switch on the job can connect one
or two switches
CN 12 GND
CN 13 Input external CONFIRM
SEQUENCE CLEARED When the sequence is to be cleared, the function can be activated
through this CN13+CN14 short circuit (CLOSE)
CN 14 GND

14
11. TCC data transmission instructions and sequence control suggestions
VER:20220606
1. Controller booting and time synchronization:
After the controller is turned on, it will automatically send {REQ100,....} data format every second to notify
the externally connected devices (computer, PLC, and AMS, etc.); at this moment, it is necessary to reply
{CMD100,....} indicating that the controller has been booted normally and the current time of the controller.
If the controller does not receive a reply {CMD100,....}, the {REQ100,.....} will be sent again after every 10
seconds
2. When the controller receives the barcode data, it will send the scanned data to the external device in
{REQ101,....} data format for control judgment or storage records. At this moment, it needs to reply
{CMD100,....}
3. After the controller is turned on, when the screwdriver has a locking signal, it will send the locking data in
the data format of {DATA100, ....}, and the 14th column (total locking times of controller) will plus 1. At
this moment, it needs to reply {CMD100,....}, if CMD100 isn’t replied, system will repeatedly send
DATA100 data (only the update time); the total locking times of the controller in the 14th column will
remain unchanged
4. When the next lock is performed, new lock data will be sent, and the 14th column (total lock times of the
controller) can be used to judge whether it is a new lock data or not
5. When the controller receives the reply {CMD100,...} data format from the external device and confirms that
the data has been received, the controller will reply by transmitting {REQ100,...}, and the controller time
can be set
6. It is recommended to apply software sequence control as shown on the following page:
Note: The content of [CMD100] in the sequence is as follows:
{CMD100,yy,mm,dd,hh,mm,ss,0000,0000,0,1,}
Str2: year 0001~9999
Str3: month 01~12
Str4: day 01~31
Str5: hour 00~23
Str6: minute 00~59
Str7: second 00~59
Str8 0000-9999 Check Sum(sum of yy, mm, dd, hh, mm, ss)
Str9 0000-9999 Key Code (Check Sum + 5438)
Str10 (default: 0)
Str11 1~255 command serial number (identical to REQ100 command serial number)
7. When the screwdriver is running, it will start to send {DATA101,....} and will not stop until the screwdriver
status (eg: NG, OK...) is generated.
Note: WIFI and Ethernet will not output {DATA101,....} data.

15
The Company reserves the right to update the technical parameters.
Controller
TCC
(Master)
Host
PC/AMS/PLC
(Slave)
Circulated communication
Controller writes to host
REQ100 (sent per second)
CMD100 (sent per second)
Host response time
Input barcode to host
REQ101
Host response time
CMD100
Write data to host
DATA100 (After DATA101, check the 14
th
column of DATA100 to
judge whether it is new data or not)
CMD100
Host response
Write data to host
DATA101 (screwdriver is running)
Note: It won’t stop until screwdriver status is generated)
Controller
TCC
(Master)
Controller
TCC
(Master)
Host
PC/AMS/PLC
(Slave)
Host
PC/AMS/PLC
(Slave)
Barcode communication
Transmittal of torque deviation during lock
Table of contents
Popular Control Unit manuals by other brands
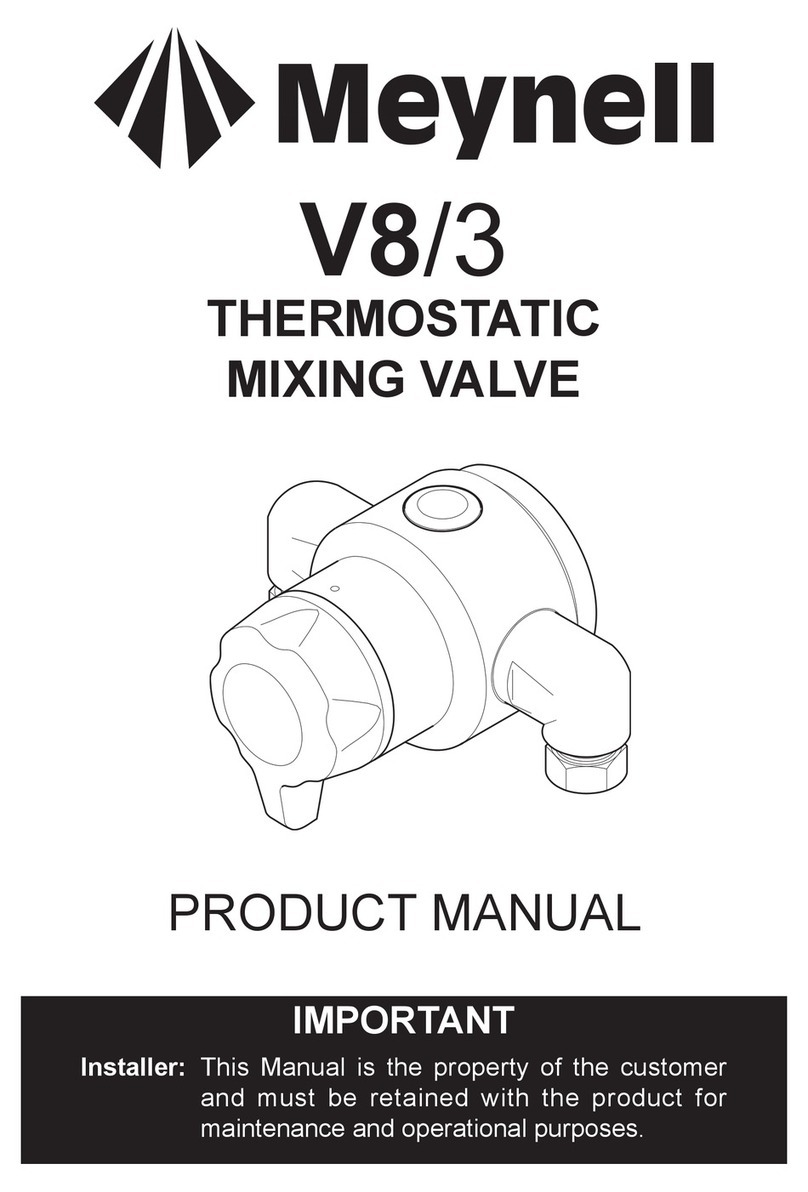
Meynell
Meynell V8/3 product manual
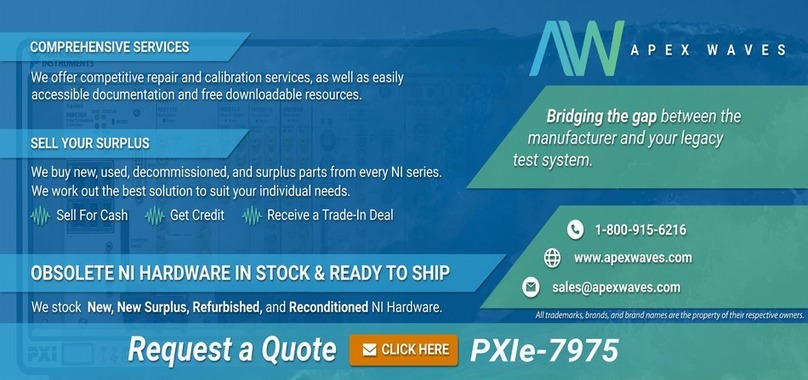
National Instruments
National Instruments FlexRIO PXIe-79 R Series installation guide
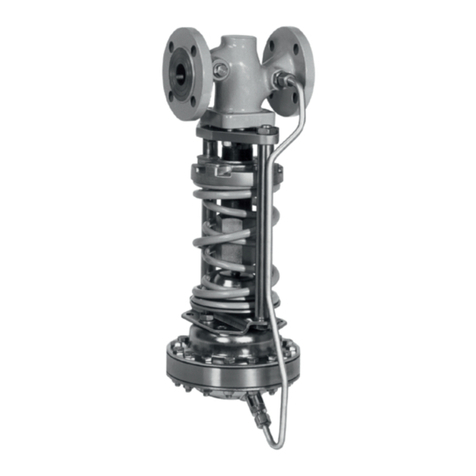
Samson
Samson 36-3 TRANSLATION OF ORIGINAL INSTRUCTIONS
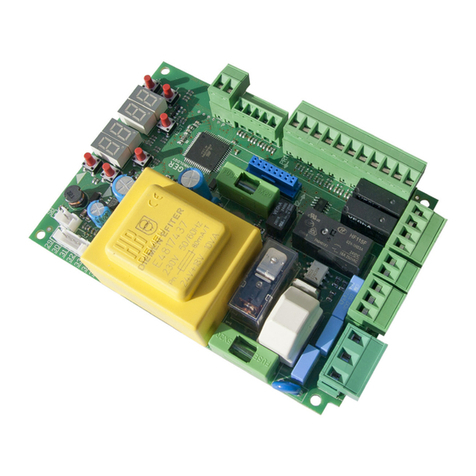
Roger Technology
Roger Technology H70/104AC Instruction and warnings for the installer
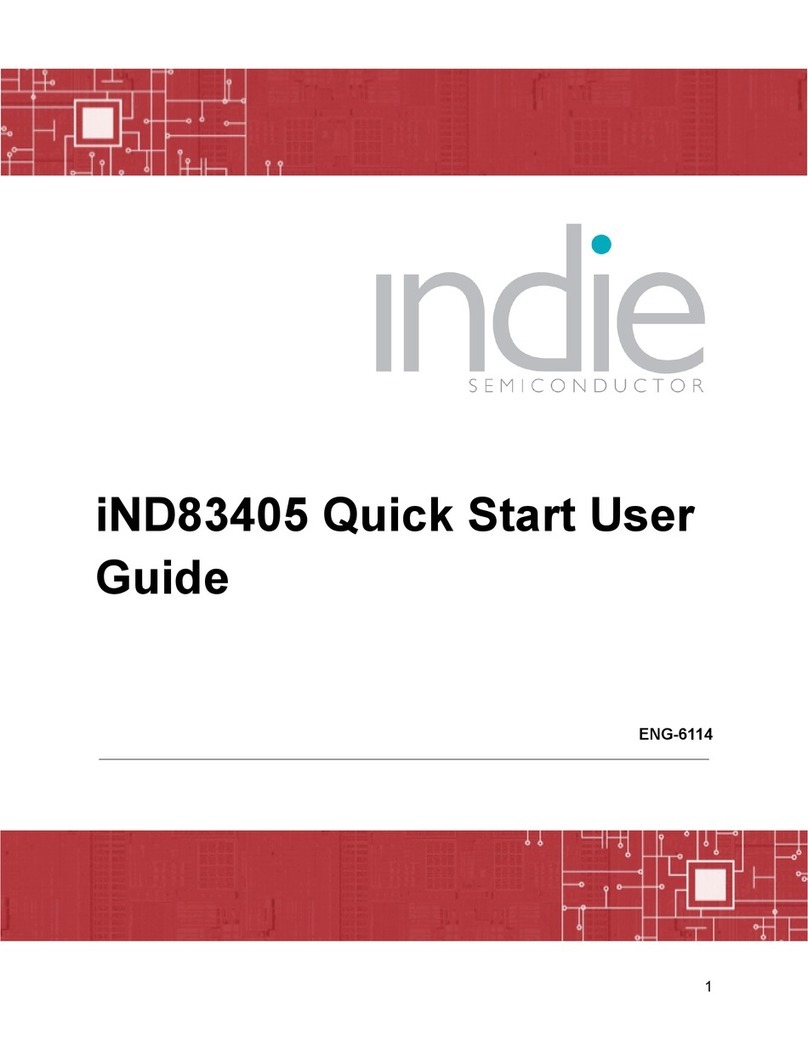
indie
indie iND83405 Quick start user guide

HP
HP Synergy 480 Gen9 Maintenance and service guide
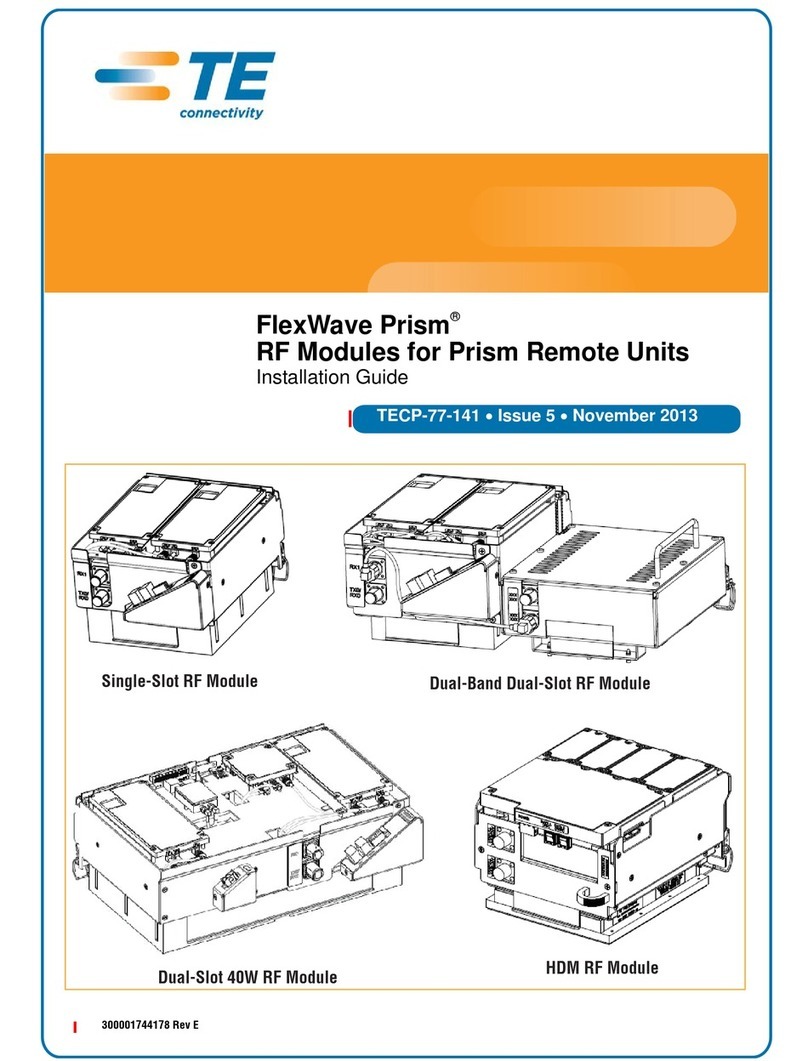
TE Connectivity
TE Connectivity FlexWave Prism installation guide
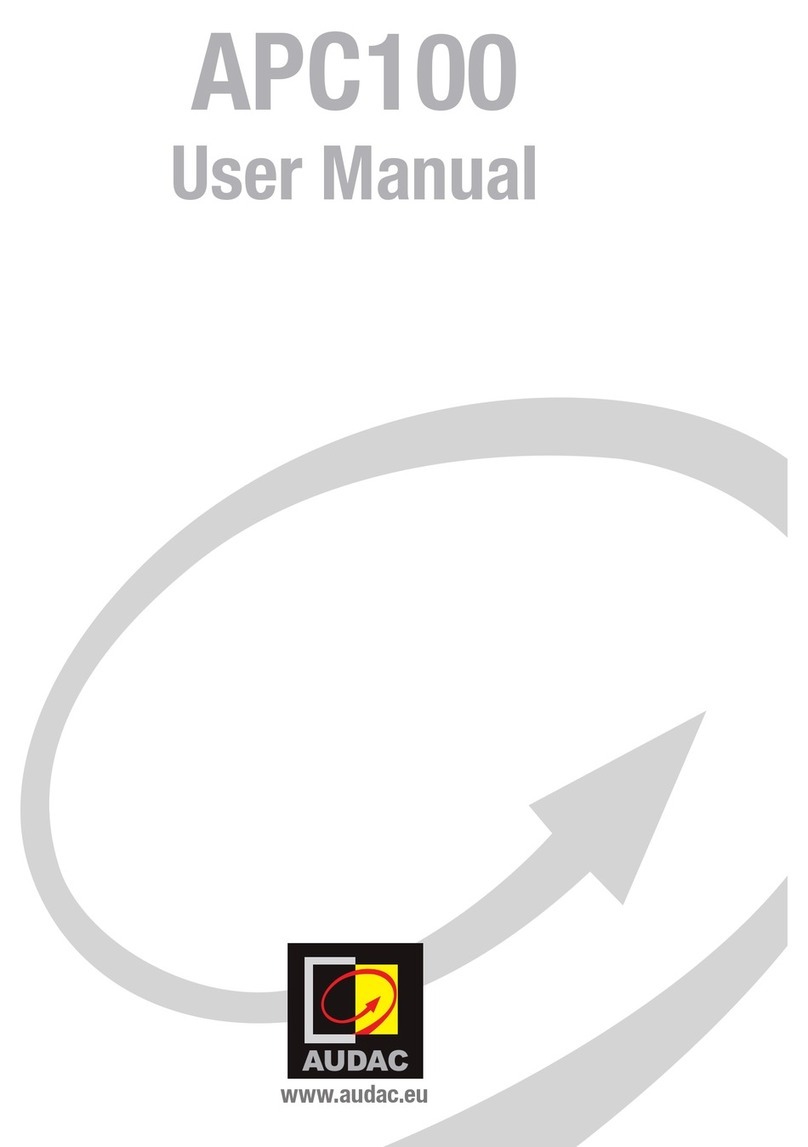
AUDAC
AUDAC APC100 user manual
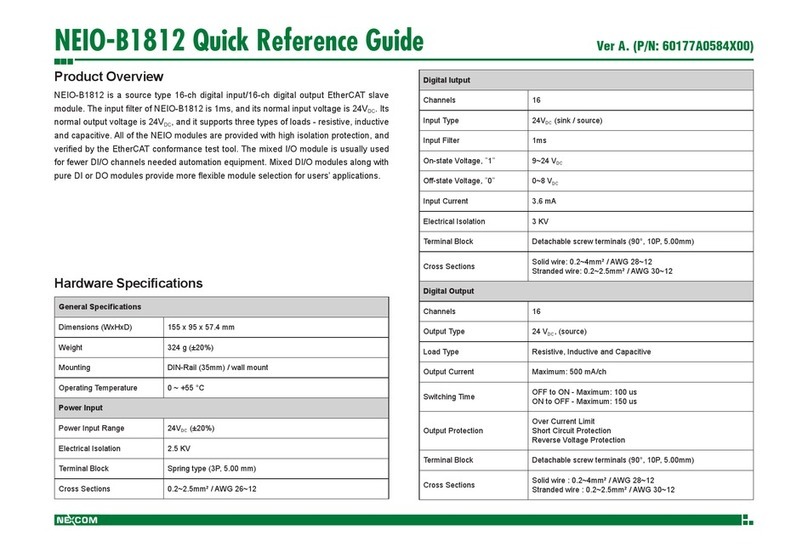
Nexcom
Nexcom NEIO-B1812 Quick reference guide
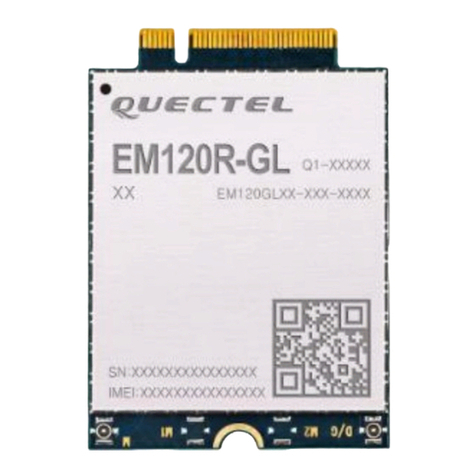
Quectel
Quectel LTE-A Series Hardware design
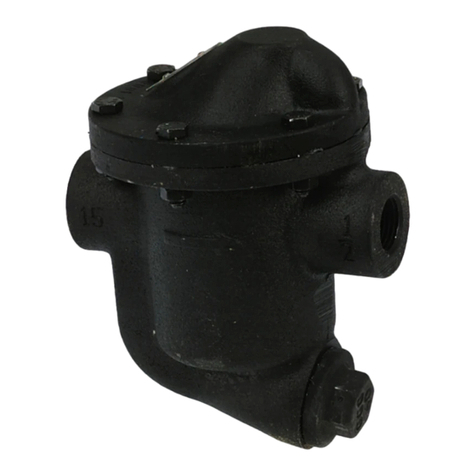
Spirax Sarco
Spirax Sarco HM Series Installation and maintenance instructions
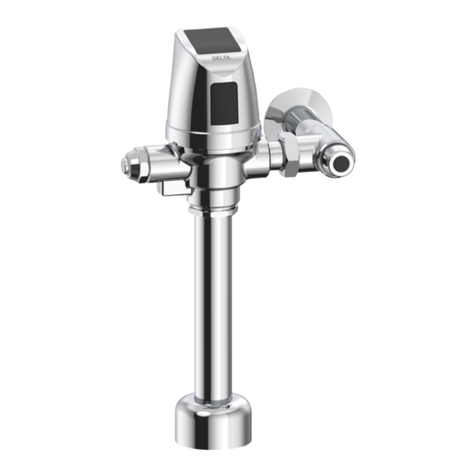
Delta
Delta Electronic Exposed Teck II manual