National Instruments FlexDMM PXI-4071 Manual

CALIBRATION PROCEDURE
NI 4071 7½-Digit FlexDMM
This document contains instructions for writing an external calibration procedure for the
National Instruments PXI-4071 (NI 4071) 7½-digit FlexDMM and 1.8 MS/s isolated digitizer.
For more information about calibration, visit ni.com/calibration.
Contents
Software Requirements............................................................................................................. 1
Documentation Requirements .................................................................................................. 1
Calibration Function Reference........................................................................................ 1
Password................................................................................................................................... 2
Calibration Interval................................................................................................................... 2
Test Equipment......................................................................................................................... 2
Test Conditions......................................................................................................................... 3
Calibration Procedures ............................................................................................................. 4
Initial Setup....................................................................................................................... 4
Verification Procedures .................................................................................................... 6
Adjustment Procedures...............................................................................................104
Verification Limits .............................................................................................................142
DC Voltage .................................................................................................................143
AC Voltage .................................................................................................................144
4-Wire Resistance.......................................................................................................146
2-Wire Resistance.......................................................................................................147
DC Current .................................................................................................................148
AC Current .................................................................................................................150
Frequency ...................................................................................................................151
Appendix A: Calibration Options.......................................................................................151
Where to Go for Support ....................................................................................................155
Software Requirements
NI-DMM supports a number of programming languages including LabVIEW,
LabWindows™/CVI™, Microsoft Visual C++, and Microsoft Visual Basic. When you install
NI-DMM, you need to install support for only the language you intend to use to write your
calibration utility. The procedures in this document are described using LabVIEW VIs and
C function calls.
Note You must use NI-DMM version 3.0.2 or later with this calibration procedure.
™

2|ni.com |NI 4071 7½-Digit FlexDMM Calibration Procedure
Documentation Requirements
In addition to this calibration document, you may find the following references helpful in writing
your calibration utility. All these documents are installed on your computer when you install
NI-DMM. To locate them, select Start»All Programs»National Instruments»NI-DMM»
Documentation.
•NI Digital Multimeters Help
•NI Digital Multimeters Getting Started Guide
NI recommends referring to the NI 4071 Specifications online at ni.com/
manuals to ensure you are using the latest NI 4071 specifications.
Calibration Function Reference
For detailed information about the NI-DMM calibration VIs and functions in this procedure,
refer to the LabVIEW reference or the C/CVI/VB reference sections of the NI Digital
Multimeters Help, located at Start»All Programs»National Instruments»NI-DMM
»Documentation. Refer to Figure 7 for the procedural flow for verification. Refer to Figure 8
for the procedural flow for adjustment.
Password
The password is required to open an external calibration session. If the password has not been
changed since manufacturing, the password is NI.
Calibration Interval
The accuracy requirements of your measurement application determine how often you should
calibrate the NI 4071. NI recommends performing a complete calibration at least once every two
years. NI does not guarantee the absolute accuracy of the NI 4071 beyond this two-year
calibration interval. You can shorten the calibration interval based on the demands of your
application. Refer to Appendix A: Calibration Options for more information.
Test Equipment
Table 1 lists the equipment required for calibrating the NI 4071. If you do not have the
recommended instruments, use these specifications to select a substitute calibration standard.
Table 1. Required Test Equipment
Required Equipment Recommended Models
Multifunction calibrator Fluke 5720A*
(calibrated within the last 90 days)
Two sets of low thermal electromotive force
(EMF) copper cables
Two sets of Fluke 5440 cables

NI 4071 7½-Digit FlexDMM Calibration Procedure |© National Instruments |3
Test Conditions
Follow these guidelines to optimize the connections and the environment during calibration:
• Ensure that the PXI chassis fan speed is set to HI and that the fan filters are clean.
• Use PXI filler panels in all vacant slots to allow proper cooling.
• Plug the PXI chassis and the calibrator into the same power strip to avoid ground loops.
• Power on and warm up both the calibrator and the NI 4071 for at least 60 minutes before
beginning this calibration procedure.
• Maintain an ambient temperature of 23 ±1 °C.
• Maintain an ambient relative humidity of less than 60%.
A means of creating a short (100 mwith
low thermal EMF (150 nV) across the HI
and LO input banana plug connectors on the
NI 4071
Pomona 5145 insulated double banana plug
shorting bar
Two sets of banana-to-banana cables with
length not to exceed 4 in.
Two Pomona B-4 banana-to-banana patch
cords (cables)
Double banana plug with binding posts Pomona 5405 Binding Post
Insulated low thermal electromotive force
(EMF) spade lugs
Two Pomona 2305 lugs
Chassis National Instruments PXI chassis and
controller
A device capable of generating pulse trains
at the frequencies listed in Table 27
NI PXI-6608 counter/timer module or
Agilent 33250a function/arbitrary waveform
generator
Any additional equipment needed to connect
the external frequency source to the NI 4071
NI TB-2715 terminal block
Shielded cable NI SH68-68-D1 shielded cable
Double banana plug with strain relief Pomona MDP 4892 double banana plug with
strain relief
Coaxial cable RG178
1Greference standard resistor IET Labs SRL-1G
*The 90-day DC current uncertainty of the Fluke 5720A is not adequate to calibrate the 100 µA and
1 mA DC current ranges on the NI 4071. See Table 13 in the Verifying DC Current section for
information on the required uncertainty.
Table 1. Required Test Equipment (Continued)
Required Equipment Recommended Models

4|ni.com |NI 4071 7½-Digit FlexDMM Calibration Procedure
• Allow the calibrator to settle fully before taking any measurements. Consult the Fluke
5720A user documentation for instructions.
• Allow the thermal EMF enough time to stabilize when you change connections to the
calibrator or the NI 4071. The suggested time periods are stated where necessary
throughout this document.
• Keep a shorting bar connected between the V GUARD and GROUND binding posts of the
calibrator at all times.
• Clean any oxidation from the banana plugs on the Fluke 5440 cables before plugging them
into the binding posts of the calibrator or the banana plug connectors of the NI 4071.
Oxidation tarnishes the copper banana plugs so that they appear dull rather than shiny and
leads to greater thermal EMF.
• Keep the blue banana plugs on the Fluke 5440 cables connected to the V GUARD binding
post of the calibrator at all times.
• Prevent the cables from moving or vibrating by taping or strapping them to a nonvibrating
surface. Movement or vibration causes triboelectric effects that can result in measurement
errors.
Calibration Procedures
The calibration process includes the following steps:
1. Initial Setup—Set up the test equipment.
2. Verification Procedures—Verify the existing operation of the device. This step confirms
whether the device is operating within its specified range prior to calibration. Figure 7 in
Appendix A shows the procedural flow for verification.
3. Adjustment Procedures—Perform an external adjustment of the device that adjusts the
calibration constants with respect to standards of known values. Figure 8 in Appendix A
shows the procedural flow for adjustment.
4. Reverification—Repeat the verification procedure to ensure that the device is operating
within its specifications after adjustment.
These steps are described in more detail in the following sections.
Note In some cases, the complete calibration procedure may not be required. Refer
to Appendix A: Calibration Options for more information.
Throughout the procedure, refer to the C/C++ function call parameters for the
LabVIEW input values.
Initial Setup
Note This section is necessary only for pre-adjustment verifications. If you are
performing a post-adjustment verification, skip the setup and go directly to the
Verifying DC Voltage section.

NI 4071 7½-Digit FlexDMM Calibration Procedure |© National Instruments |5
To set up the test equipment, complete the following steps:
1. Remove all connections from the four input banana plug connectors on the NI 4071.
2. Verify that the calibrator has been calibrated within the time limits specified in the Test
Equipment section, and that DC zeros calibration has been performed within the last 30
days. Consult the Fluke 5720A user documentation for instructions for calibrating these
devices.
Note Ensure that both the calibrator and the NI 4071 (installed in a powered-on
PXI chassis) are warmed up for at least 60 minutes before you begin this procedure.
3. Call the niDMM Initialize VI with the Instrument Descriptor of the device to create an
instrument session.
Note You will use this session in all subsequent VI and function calls throughout
the verification procedures. For more information about using the niDMM Initialize
VI or the niDMM_init function, refer to the NI Digital Multimeters Help.
4. Call the niDMM Configure Powerline Frequency VI.
LabVIEW Block Diagram C/C++ Function Call
Call niDMM_init with the
following parameters:
Instrument_Descriptor: The name
of the device to calibrate. You can find
this name under Devices and
Interfaces in Measurement &
Automation Explorer (MAX)
ID_Query: VI_FALSE
Reset: VI_FALSE
LabVIEW Block Diagram C/C++ Function Call
Call
niDMM_ConfigurePowerLineFreque
ncy with the following parameters:
Instrument_Handle:The instrument
handle from niDMM_init
PowerLine Frequency: Set this parameter
to 50 or 60, depending on the powerline
frequency (in hertz) powering your
instruments; select 50 for 400 Hz
powerline frequencies

6|ni.com |NI 4071 7½-Digit FlexDMM Calibration Procedure
5. Call the niDMM Self Cal VI.
Verification Procedures
You can use the verification procedures described in this section for both pre-adjustment and
post-adjustment verification. The verification procedures and the steps within them must be
performed in the order listed; however, you can opt to omit entire sections (for example, the
entire Verifying AC Current section).
The parameters Range, Resolution, and Sample Interval used in VI and function calls
throughout this section have floating point values. For example, if Range = 1, the floating point
value is 1.0. The parameters Trigger Count, Sample Count, Array Size, and ParamValue
have integer values. Refer to the NI Digital Multimeters Help for more information about
parameter values.
Note Many of the parameter values listed in this document are expressed in
scientific notation. Some programming languages do not support the direct entry of
numbers in this format. Be sure to properly enter these values with the appropriate
number of zeros. For example, you must enter the scientific notation number 10e–6
as 0.00001 and the number 100e3 as 100000. If your programming language
supports numeric entries in scientific notation, NI recommends that you use this
feature to minimize possible data entry errors.
Verifying DC Voltage
To verify DC voltage of the NI 4071, complete the following steps:
1. Plug in the insulated banana plug shorting bar across the HI and LO banana plug connectors
on the NI 4071.
2. Wait one minute for the thermal EMF to stabilize.
3. Call the niDMM Reset VI.
LabVIEW Block Diagram C/C++ Function Call
Call niDMM_SelfCal with the following
parameters:
Instrument_Handle:The instrument
handle from niDMM_init
LabVIEW Block Diagram C/C++ Function Call
Call niDMM_reset with the
following parameter:
Instrument_Handle:The instrument
handle from niDMM_init

NI 4071 7½-Digit FlexDMM Calibration Procedure |© National Instruments |7
4. Call the niDMM Config Measurement VI and select the Resolution in Digits instance.
5. Use a writable niDMM property node to set the input resistance of the NI 4071 to >10 G
LabVIEW Block Diagram C/C++ Function Call
Call
niDMM_ConfigureMeasurement
Digits with the following
parameters:
Instrument_Handle:The instrument
handle from niDMM_init
Resolution_Digits:7.5
Measurement_Function:
NIDMM_VAL_DC_VOLTS
Range: 100 mV
LabVIEW Block Diagram
C/C++ Function
Call
Call niDMM
SetAttributeVi
Real64 with the
following
parameters:
Instrument_Handle
:The instrument
handle from
niDMM_init
Attribute_ID:
NIDMM_ATTR_INPU
T_RESISTANCE
Attribute_Value:
NIDMM_VAL_
GREATER_THAN_
10_GIGAOHM

8|ni.com |NI 4071 7½-Digit FlexDMM Calibration Procedure
6. Call the niDMM Read VI. Store the reading or measurement value as the 100 mV >10 G
mode offset.
Note The Measurement output of the LabVIEW block diagram equates to the
Reading function of C++ function call.
7. Use a writable niDMM property node to set the input resistance of the NI 4071 to 10 M.
LabVIEW Block Diagram C/C++ Function Call
Call niDMM_read with the following
parameters:
Instrument_Handle:The instrument
handle from niDMM_init
Maximum_Time: –1
Reading: The measurement returned
by the function. Store the reading or
measurement value as the
100 mV >10 Gmode offset.
LabVIEW Block Diagram C/C++ Function Call
Call niDMM
SetAttributeViRea
l64 with the following
parameters:
Instrument_Handle:
The instrument handle
from niDMM_init
Attribute_ID:
NIDMM_ATTR_INPUT_
RESISTANCE
Attribute_Value:
NIDMM_VAL_10_MEGA
OHM

NI 4071 7½-Digit FlexDMM Calibration Procedure |© National Instruments |9
8. Call the niDMM Read VI.
9. Use a writable niDMM property node to set the input resistance of the NI 4071 to >10 G
LabVIEW Block Diagram C/C++ Function Call
Call niDMM_read with the
following parameters:
Instrument_Handle:The instrument
handle from niDMM_init
Reading: The measurement returned
by the function. Store the reading or
measurement value as the 100 mV
10 Mmode offset.
Maximum_Time: –1
LabVIEW Block Diagram
C/C++ Function
Call
Call niDMM
SetAttributeVi
Real64 with the
following
parameters:
Instrument_Handle
:The instrument
handle from
niDMM_init
Attribute_ID:
NIDMM_ATTR_INPU
T_RESISTANCE
Attribute_Value:
NIDMM_VAL_
GREATER_THAN_
10_GIGAOHM

10 |ni.com |NI 4071 7½-Digit FlexDMM Calibration Procedure
10. Call the niDMM Read VI.
11. Use a writable niDMM property node to set the input resistance of the NI 4071 to 10 M.
LabVIEW Block Diagram C/C++ Function Call
Call niDMM_read with the
following parameters:
Instrument_Handle:The instrument
handle from niDMM_init
Reading: The measurement returned
by the function. Subtract the
previously stored 100 mV >10 G
mode offset value from
this measurement. Verify that this
measurement falls between the limits
listed in Table 20.
Maximum_Time: –1
LabVIEW Block Diagram C/C++ Function Call
Call niDMM
SetAttributeViRea
l64 with the following
parameters:
Instrument_Handle:
The instrument handle
from niDMM_init
Attribute_ID:
NIDMM_ATTR_INPUT_
RESISTANCE
Attribute_Value:
NIDMM_VAL_10_MEGA
OHM

NI 4071 7½-Digit FlexDMM Calibration Procedure |© National Instruments |11
12. Call the niDMM Read VI.
13. Call the niDMM Config Measurement VI and select the Resolution in Digits instance.
LabVIEW Block Diagram C/C++ Function Call
Call niDMM_read with the
following parameters:
Instrument_Handle:The instrument
handle from niDMM_init
Reading: The measurement returned
by the function. Subtract the
previously stored 100 mV 10 M
mode offset value from
this measurement.Verify that this
measurement falls between the limits
listed in Table 20.
Maximum_Time: –1
LabVIEW Block Diagram C/C++ Function Call
Call
niDMM_ConfigureMeasurement
Digits with the following
parameters:
Instrument_Handle:The instrument
handle from niDMM_init
Resolution_Digits:7.5
Measurement_Function:
NIDMM_VAL_DC_VOLTS
Range: 1

12 |ni.com |NI 4071 7½-Digit FlexDMM Calibration Procedure
14. Use a writable niDMM property node to set the input resistance of the NI 4071 to >10 G
15. Call the niDMM Read VI.
16. Use a writable niDMM property node to set the input resistance of the NI 4071 to 10 M.
LabVIEW Block Diagram
C/C++ Function
Call
Call niDMM
SetAttributeVi
Real64 with the
following
parameters:
Instrument_Handle
:The instrument
handle from
niDMM_init
Attribute_ID:
NIDMM_ATTR_INPU
T_RESISTANCE
Attribute_Value:
NIDMM_VAL_
GREATER_THAN_
10_GIGAOHM
LabVIEW Block Diagram C/C++ Function Call
Call niDMM_read with the
following parameters:
Instrument_Handle:The instrument
handle from niDMM_init
Reading: The measurement returned
by the function. Verify that this
measurement falls between the limits
listed in Table 20.
Maximum_Time: –1

NI 4071 7½-Digit FlexDMM Calibration Procedure |© National Instruments |13
17. Call the niDMM Read VI.
18. Call the niDMM Config Measurement VI and select the Resolution in Digits instance.
LabVIEW Block Diagram C/C++ Function Call
Call niDMM
SetAttributeViRea
l64 with the following
parameters:
Instrument_Handle:
The instrument handle
from niDMM_init
Attribute_ID:
NIDMM_ATTR_INPUT_
RESISTANCE
Attribute_Value:
NIDMM_VAL_10_MEGA
OHM
LabVIEW Block Diagram C/C++ Function Call
Call niDMM_read with the
following parameters:
Instrument_Handle:The instrument
handle from niDMM_init
Reading: The measurement returned
by the function. Verify that this
measurement falls between the limits
listed in Table 20.
Maximum_Time: –1
LabVIEW Block Diagram C/C++ Function Call
Call
niDMM_ConfigureMeasurement
Digits with the following
parameters:
Instrument_Handle:The instrument
handle from niDMM_init
Resolution_Digits: 7.5
Measurement_Function:
NIDMM_VAL_DC_VOLTS
Range: 10

14 |ni.com |NI 4071 7½-Digit FlexDMM Calibration Procedure
19. Use a writable niDMM property node to set the input resistance of the NI 4071 to >10 G
20. Call the niDMM Read VI.
21. Use a writable niDMM property node to set the input resistance of the NI 4071 to 10 M.
LabVIEW Block Diagram
C/C++ Function
Call
Call niDMM
SetAttributeVi
Real64 with the
following
parameters:
Instrument_Handle
:The instrument
handle from
niDMM_init
Attribute_ID:
NIDMM_ATTR_INPU
T_RESISTANCE
Attribute_Value:
NIDMM_VAL_
GREATER_THAN_
10_GIGAOHM
LabVIEW Block Diagram C/C++ Function Call
Call niDMM_read with the
following parameters:
Instrument_Handle:The instrument
handle from niDMM_init
Reading: The measurement returned
by the function. Verify that this
measurement falls between the limits
listed in Table 20.
Maximum_Time: –1

NI 4071 7½-Digit FlexDMM Calibration Procedure |© National Instruments |15
22. Call the niDMM Read VI.
23. Call the niDMM Config Measurement VI and select the Resolution in Digits instance.
LabVIEW Block Diagram C/C++ Function Call
Call niDMM
SetAttributeViRea
l64 with the following
parameters:
Instrument_Handle:
The instrument handle
from niDMM_init
Attribute_ID:
NIDMM_ATTR_INPUT_
RESISTANCE
Attribute_Value:
NIDMM_VAL_10_MEGA
OHM
LabVIEW Block Diagram C/C++ Function Call
Call niDMM_read with the
following parameters:
Instrument_Handle:The instrument
handle from niDMM_init
Reading: The measurement returned
by the function. Verify that this
measurement falls between the limits
listed in Table 20.
Maximum_Time: –1
LabVIEW Block Diagram C/C++ Function Call
Call
niDMM_ConfigureMeasurement
Digits with the following
parameters:
Instrument_Handle:The instrument
handle from niDMM_init
Resolution_Digits:7.5
Measurement_Function:
NIDMM_VAL_DC_VOLTS
Range: 100

16 |ni.com |NI 4071 7½-Digit FlexDMM Calibration Procedure
24. Call the niDMM Read VI.
25. Call the niDMM Config Measurement VI and select the Resolution in Digits instance.
26. Call the niDMM Read VI.
27. Remove the shorting bar from the NI 4071.
28. Reset the calibrator.
LabVIEW Block Diagram C/C++ Function Call
Call niDMM_read with the
following parameters:
Instrument_Handle:The instrument
handle from niDMM_init
Reading: The measurement returned
by the function. Verify that this
measurement falls between the limits
listed in Table 20.
Maximum_Time: –1
LabVIEW Block Diagram C/C++ Function Call
Call
niDMM_ConfigureMeasurement
Digits with the following
parameters:
Instrument_Handle:The instrument
handle from niDMM_init
Resolution_Digits:7.5
Measurement_Function:
NIDMM_VAL_DC_VOLTS
Range: 1000
LabVIEW Block Diagram C/C++ Function Call
Call niDMM_read with the following
parameters:
Instrument_Handle:The instrument
handle from niDMM_init
Reading: The measurement returned
by the function. Verify that this
measurement falls between the limits
listed in Table 20.
Maximum_Time: –1

NI 4071 7½-Digit FlexDMM Calibration Procedure |© National Instruments |17
29. Connect the NI 4071 and the Fluke 5720A calibrator using the Fluke 5440 cable, as shown
in Figure 1. Table 2 lists the cable connections.
Figure 1. Cable Connections for Voltage and 2-Wire Resistance
30. Wait two minutes for the thermal EMF to stabilize.
31. Generate 90 mV on the calibrator with the range locked to 2.2 V.
Note This calibrator range prevents a 50 output resistance from creating
a voltage divider with the internal resistance of the NI 4071.
1 NI 4071 2 Fluke 5720A Calibrator 3 Fluke 5440 Cable
Table 2. Fluke 5440 Cable Connections
Banana Plug
Connector
(NI 4071)
Banana Plug Color
(Fluke 5440 Cable)
Binding Post Label
(Fluke 5720A Calibrator)
HI Red OUTPUT HI
LO Black OUTPUT LO
(No connection) Blue V GUARD
HI
LO
AUX
I/O
300V
MAX
5V
MAX
AMPS
NI PXI-4071
71/2-Digit FlexDMM
500V MAX
CAT I
HI
LO
1kV
MAX
3A, 250V
MAX
INPUT
1kV
MAX HI
LO
HI
LO
HI
AUX
CURRENT
GUARD GROUND
1
2
3

18 |ni.com |NI 4071 7½-Digit FlexDMM Calibration Procedure
32. Call the niDMM Config Measurement VI and select the Resolution in Digits instance.
33. Use a writable niDMM property node to set the input resistance of the NI 4071 to >10 G.
LabVIEW Block Diagram C/C++ Function Call
Call
niDMM_ConfigureMeasurement
Digits with the following
parameters:
Instrument_Handle:The instrument
handle from niDMM_init
Resolution_Digits:7.5
Measurement_Function:
NIDMM_VAL_DC_VOLTS
Range: 0.1
LabVIEW Block Diagram
C/C++ Function
Call
Call niDMM
SetAttributeVi
Real64 with the
following
parameters:
Instrument_Handle
:The instrument
handle from
niDMM_init
Attribute_ID:
NIDMM_ATTR_INPU
T_RESISTANCE
Attribute_Value:
NIDMM_VAL_GREAT
ER_THAN_10_GIGA
OHM

NI 4071 7½-Digit FlexDMM Calibration Procedure |© National Instruments |19
34. Call the niDMM Read VI.
35. Use a writable niDMM property node to set the input resistance of the NI 4071 to 10 M.
LabVIEW Block Diagram C/C++ Function Call
Call niDMM_read with the
following parameters:
Instrument_Handle:The instrument
handle from niDMM_init
Reading: The measurement returned
by the function. Subtract the
previously stored 100 mV >10 G
mode offset value from this
measurement. Verify the reading or
measurement value falls between the
limits listed in Table 20.
Maximum_Time: –1
LabVIEW Block Diagram C/C++ Function Call
Call niDMM
SetAttributeViRea
l64 with the following
parameters:
Instrument_Handle:
The instrument handle
from niDMM_init
Attribute_ID:
NIDMM_ATTR_INPUT_
RESISTANCE
Attribute_Value:
NIDMM_VAL_10_MEGA
OHM

20 |ni.com |NI 4071 7½-Digit FlexDMM Calibration Procedure
36. Call the niDMM Read VI.
37. Generate –90 mV on the calibrator with the range locked to 2.2 V.
Note This calibrator range prevents the 50 output resistance of the 220 mV
range from creating a voltage divider with the internal resistance of the NI 4071.
38. Use a writable niDMM property node to set the input resistance of the NI 4071 to >10 G
LabVIEW Block Diagram C/C++ Function Call
Call niDMM_read with the
following parameters:
Instrument_Handle:The instrument
handle from niDMM_init
Reading: The measurement returned
by the function. Subtract the
previously stored 100 mV 10 M
mode offset value from this
measurement. Verify the reading or
measurement value falls between the
limits listed in Table 20.
Maximum_Time: –1
LabVIEW Block Diagram
C/C++ Function
Call
Call niDMM
SetAttributeVi
Real64 with the
following
parameters:
Instrument_Handle
:The instrument
handle from
niDMM_init
Attribute_ID:
NIDMM_ATTR_INPU
T_RESISTANCE
Attribute_Value:
NIDMM_VAL_GREAT
ER_THAN_10_GIGA
OHM
This manual suits for next models
1
Table of contents
Other National Instruments Multimeter manuals
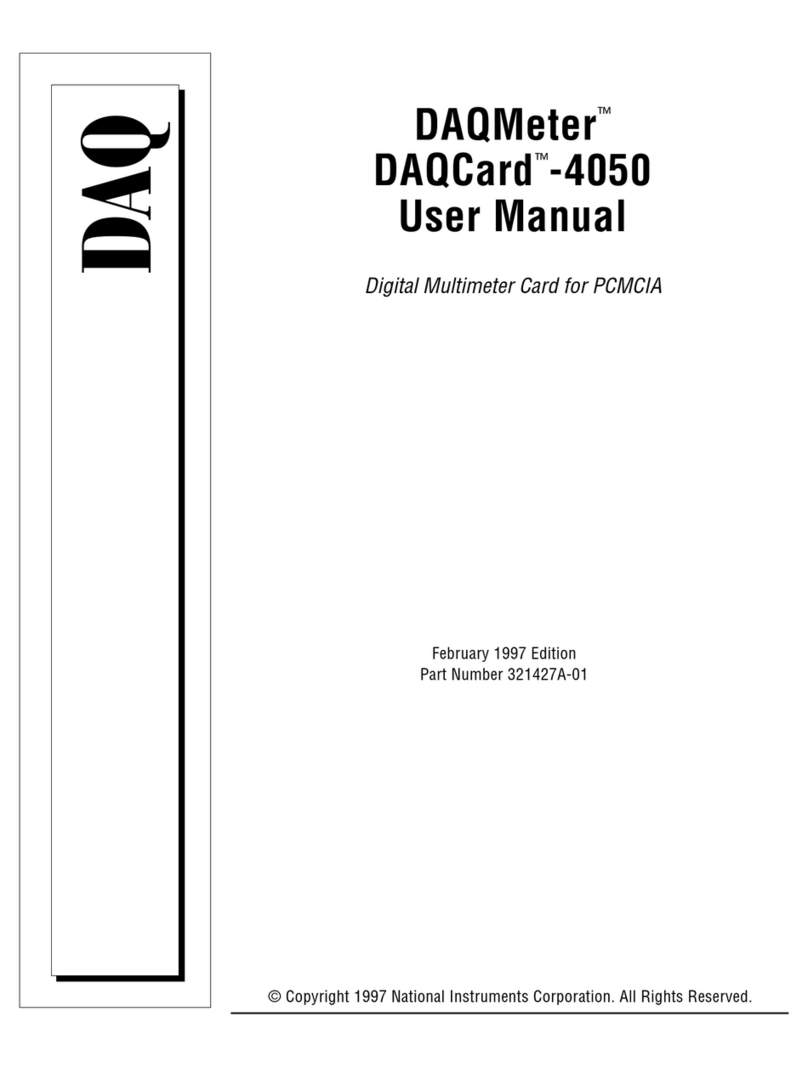
National Instruments
National Instruments DAQMeter DAQCard-4050 User manual

National Instruments
National Instruments 4065 Manual

National Instruments
National Instruments FlexDMM PXI-4070 Manual
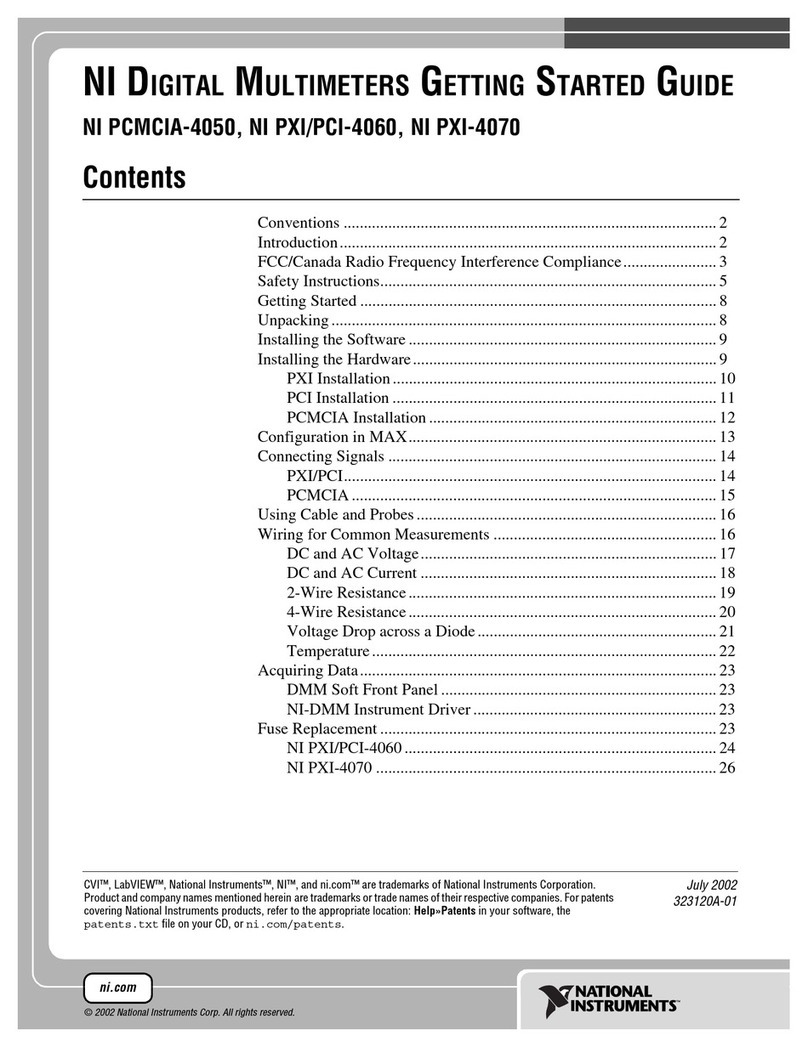
National Instruments
National Instruments NI PCMCIA-4050 User manual
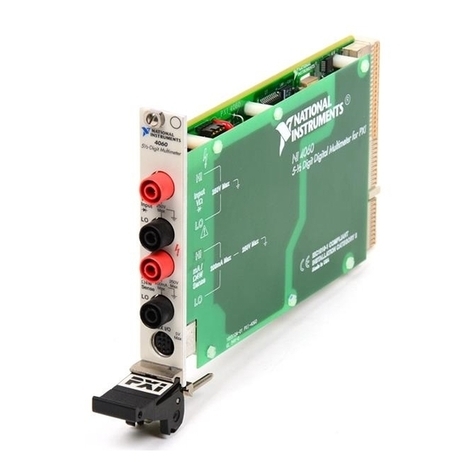
National Instruments
National Instruments NI PXI-4060 User manual