NC SW9 Assembly instructions

1
SW9 Site Dumper
SW9 Site DumperSW9 Site Dumper
SW9 Site Dumper
OPERATORS
OPERATORS OPERATORS
OPERATORS
INSTRUCTION
INSTRUCTION INSTRUCTION
INSTRUCTION
MANUAL
MANUALMANUAL
MANUAL
NC ENGINEERING (HAMILTONSBAWN) LTD
2 Killyrudden Road, Hamiltonsbawn, Co Armagh, BT61 9S
Tel: 028 38871970 ax: 028 38870362
email: [email protected]om www.nc-engineering.com
REVISION B
ORGINAL INSTRUCTIONS

2

3
Dear Customer
Even if you have operated this type of equipment before, it is
very important that your new equipment operations and
instructions are explained to you by a Dealer Representative
following delivery of your equipment.
This will explain the operating controls and enable you to
gain maximum productivity from your new dumper.

4

5
Pre Handover Check List
Return form to
NC ENGINEERING (HAMILTONSBAWN) LTD
2 Killyrudden Road
Hamiltonsbawn
Co Armagh BT61 9S
Delivery on this machine has been completed, including the following items.
Tick check box when each item is completed.
1. Operator Handbook delivered with equipment and operator controls and
warning labels explained to user
2. Maintenance Handbook, service intervals, fluid level checks and adjustments
explained to user.
3. Parts book and information explained (Parts book can be purchased through
dealer)
4. All items on delivery checklist have been completed
Operators signature: …………………………………………
Signature on behalf of Dealer: ……………………………...
DISTRIBUTOR/DEALER:………………
E UIPMENT MODEL: …………………
E UIPMENT SERIAL No:………………
HOURMETER READING: ………………
DELIVERY DATE: ……………………….
TODAYS DATE: ………………………….
Customer Name (Please Print): ………………………………………………………………
Address: ………………………………………………………………………………………
…………………………………………………………………………………………………
Postcode: …………………… Country:…………………………. Tel: ……………………...
Delivery Checklist
(Continued on reverse side)
Complete this form with the user / customer and return it to NC
At Dealership
Make sure any necessary field service instructions have been completed
Make sure all necessary certificates and literature are available
All decals are fitted

6
At Delivery Point with Customer
Explain parts book
Explain all warning labels on equipment
Show location of all serial numbers on equipment
Lubrication & Maintenance
Explain maintenance requirements, fuel & lubricant specifications
Instruct how to use service schedules of maintenance handbook
Show all lubrication points on the equipment
Fluid Levels
Instruct how to measure all fluid levels and fill procedures
uel
Hydraulic Tank
Engine oil
Transmission / Power train
Coolant (inspect with engine stopped & cool)
Brake system reservoir
Show Location of All Filters
Hydraulics system
Engine oil
uel system
Transmission / Power train
Engine air
Water and Sedimentor Drains
uel water separator
uel tank drain bung
Hydraulic tank drain bung
Operation & Demonstration
Review operator handbook
Starting stopping operations
Direction change controls
Gear change operation
Accelerator & braking controls
Warning devices (i.e. horn/ beacon)
Hydraulics controls
Legislation Awareness
Ensure the user is aware of the appropriate local, national, and international Health &
Safety Legislation for the equipment being operated
DEALER STAMP:

7
Contents
Declaration of Conformity
9
Noise Level Declaration
10
Vibration Declaration
11
Post Delivery Checks
12
Machine Data
13
Skip & Loading Information 13
Steering 14
Transmission 14
Brakes 14
Engine 14
Vehicle Identification Plate - VIN 14
Safety Decals and Descriptions
15
Safety Information
17
ROPS 19
Seat Belt Information 20
Seat Adjustment 21
Battery Isolator 22
Steering Wheel Adjustment 22
Warning Others 23
Skip Props 23
uel 24
Engine Canopy
26
Driving Controls
27
Starting Procedure 27
Moving orwards & Backwards 27
Acceleration 28
Slowing Down / Stopping 28
Steering the Dumper 28
Skip Control 28
Dashboard Warning Lights
29

8
Contents
Page No.
Safe Operating Instructions
30
Visibility 30
Climbing / Descending Gradients 31
Crossing Gradients 31
ROPS Bar 32
Towing Loads 33
Transportation 33

9
Engineering
(Hamiltonsbawn)
Ltd.
Manufacturers of Agricultural and Industrial Equipment
2 Killyrudden Road, Hamiltonsbawn, Tel: 028
38871970
Richhill, o. Armagh.
Fax: 028 3887 0362
Northern Ireland. E.mail: info@nc engineering.com
8T619SF www.nc-engineering.com
EC – DECLARATION OF CONFORMITY
Machine description : Site Dumper
Make NC
Type SW9
Manufactured by NC Engineering (Hamiltonsbawn) Ltd
Address: 2 Killyrudden Road, Hamiltonsbawn Richhill,
Co. Armagh. BT61 9S
This machinery has been designed and manufactured in accordance with the following European
Standards: -
2006/42/CE: Machinery Directive
Measured Sound Power Level: 104 dB LWA
Guaranteed Sound Power Level: 104 dB LWA
Net Installed Power: 97kW
A technical construction file for this machine is retained at the above address.
Declaration
Signed: ______________________________________
Name: David Wilson CEng; MSc; MIAgrE
Being the responsible person appointed by the manufacturer (or nominated representative of the manufacturer established in
the EC) and employed by:
NC Engineering (Hamiltonsbawn) Ltd
This declaration of Conformity complies with Regulation 22 of The Supply of Machinery (Safety) Regulations 1992

10
Noise Level Declaration
The noise levels are measured according to ISO6395:1998
The noise level of this machine is
L
WA
104dB ( A )
L
PA
85dB ( A )
L
WA
:- A - Weighted sound power level.
L
PA
:- A - Weighted sound pressure level.

11
Vibration Declaration.
The absence of a harmonised test code together with variable conditions under which this
equipment may be used allows only representative figures to be quotes.
Whole Body Vibration Level : a
w
(m/s²) = 0.25
Hand / Arm : a
ha
( m/s² ) ≤ 2.4
The above figures are for reference purposes only. It is the responsibility of the employer to access
vibration exposure based on the actual site conditions and operating practices at the point of use.
Employers should not rely solely on published vibration figures when undertaking risk assessments.
Depending on the site conditions cycle times may need to be adjusted in order to reduce operator
exposure levels.

12
Post Delivery Checks
•
Check the condition of the machine and make sure it has not been damaged during
delivery.
•
Tightness of wheel nuts.
•
Check the following Oil levels in engine, gearbox and axles.
Hydraulic oil and fuel levels.
Brake fluid level in the reservoir.
Coolant level.
Battery liquid level.
Tyre pressures.
The procedures for checking fluid levels can be found in the maintenance manual
If there are any faults with the machine please report them immediately to your NC dealer
representative.
ROUTINE CHECKS
Before operating the dumper every day visually check the following:
•
Engine oil level.
•
Coolant quality & level.
•
Coolant or Oil leaks.
•
uel filter & water sedimentor bowl.
•
Transmission oil level.
•
Return to tank hydraulic oil filter indicator.
•
Air filter restriction indicator.
•
Parking brake operation (adjust as necessary).
Dumper needs greased every week
Refer to maintenance instruction manual for further details on the above checks.
On delivery of your new machine fully read this handbook:
READ THIS HANDBOOK IN FULL

13
Machine Data
SKIP & LOADING INFORMATION
The machine is fitted with a load carrying skip which is able to swivel to the left and right of
the machine.
CAPACITIES
Max. safe load: 9000 kg
Heaped: 4427 Litres
Struck: 3126 Litres
Water: 2492 Litres
Never attempt to load the skip beyond its rated capacity
This dumper is basically a load carrying vehicle, that can be used for a multitude of
building/contracting site work, but essentially used to transport materials away from
excavators and other building material. The dumper will allow, if used in the correct manner
the operator to accurately place material such as soil, sand, clay, stone, debris etc. in the drop
point without damage to the material or themselves.
In the lowered or load position the skip is seated in such a fashion so that the driver has
ample view ahead. Therefore when loading the skip get off the machine and do not allow
the load to be heaped in such away that will impair view.
Before moving off on the dumper insure that the skip is in the forward facing direction and
locked in to the skip anti rotation lock on the chassis bed. Like wise before side tipping the
load using the swivel function ensure that the skip is elevated enough to clear the anti
rotation lock.
The following information is provided for operators for their own safety.
Stay within the safe working limits of the machine. Never attempt to use
the dumper for any task other than what it was intended for by the
manufacturer. Failure to do so could result in serious injury of DEATH.
Never Elevate The Skip Unless The Machine Is On Level Ground .
Do Not Use The Edge Of The Skip When Raised As A Dozer Blade.
The maximum distance to travel with a fully laden dumper is 1km at 30kph
To stop the tyre overheating.

14
Machine Data
STEERING
Steering of the dumper is by an ‘Orbital’ hydrostatic steering unit, that articulates the centre
of the machine using a hydraulic cylinder which in turn gives a steering motion.
TRANSMISSION
The dumper is fitted with a torque converter transmission coupled to a four speed shuttle
gearbox.
BRAKES
Braking is provided by oil immersed brakes sealed inside on both front and back axles. The
brakes are self adjusting, carbon multi-plate discs which are operated via a single master
cylinder.
Handbrake may be applied to stop the dumper in an emergency.
ENGINE
This machine has a four cylinder diesel engine that transmits power to the wheels via a
mechanical gearbox and axles. The dumper is equipped with electric start from a key on the
steering column. A battery isolator is provided under the bonnet in the engine compartment.
VEHICLE IDENTIFICATION PLATE - VIN
The VIN plate (A) is located on the right hand side of the rear chassis
beside the steps. The number is unique to each machine and must be
quoted when in contact with the manufacturer. rom the VIN the
manufacturer can call up detail relating to each individual machine
i.e. Date sold, customer, serial No., special build features etc.
A

15
Safety Decals and Descriptions
SAFETY DECALS
The Machine is fitted with a number of safety decals placed in areas to draw the attention
of the users. It is important that before using the machine theses decals are read and un-
derstood. The decals must be clean and readable at all times, if they need to be replaced
they can be obtained from NC spares department.
Part No. Symbol. Descriptions.
DEC~1920-002
Hydraulic Oil.
DEC~1920-003
uel.
DEC~1920-004
Stay clear of tipping area.
DEC~1920-005
Skip controls.
DEC~1920-006
Restricted Visibility / No passengers / Towing Loads/ Transport / Read manual
Before operating machine.
DEC~1920-007
Safe gradients / No tipping down a gradient / Lower skip before driving.
DEC~1920-081
it skip prop before access / Slew ring nut torques.
DEC~1920-010
Ignition.
DEC~1920-011
Gear locations.
DEC~1920-012
Seat belt must be worn.

16
Safety Decals and Descriptions
Part No. Symbol. Descriptions.
DEC~1920-013
Don’t operate controls until operators manual has been read.
DEC~1920-014
Recommended brake fluid.
DEC~1920-015
Recommended brake fluid ( Circular )
DEC~1920-016
No repairs to ROPS.
DEC~1920-017
Stay clear of pinch points.
DEC~1920-018
Read manual / Apply handbrake before leaving dumper / Release handbrake
before moving dumper.
DEC~1920-019
Caution moving parts / Do not open when hot.
DEC~1920-020
orward and Reverse.
DEC~1920-022
Maintenance decal.
DEC~1920-023
Tyre pressure and wheel nut torque ( Rear )
DEC~1920-024
Tyre pressure and wheel nut torque ( ront )
Sound level.
DEC~1920-025
Sound levels.
DEC~1920-031
Battery

17
Safety Information
FOR SAFETY & PROTECTION READ THE FOLLOWING
Both operators and maintenance personnel must read the following safety
notice. The information below is given for your own safety. They must be
read before operating or carrying out any maintenance to the machine.
Local site rules must be adhered to at all times.
• Before operating the machine ensure that correct training has been given, and you are fully
conversant with the machine and its controls.
• A full training regime must be put in place for all operators to insure safe use of the machine.
• Do not operate the machine unless trained.
• All personnel must read these instructions before operating the machine. Always ensure instruction
manual is kept with the machine. If it gets lost, damaged or dirty replace it immediately.
• The decals are fitted to the machine for safety, if any become unreadable replace them with new
equivalents.
• Always ensure that the machine is run in a well ventilated area. Never run engine in a confined
space or close to flammable material.
• While refuelling the machine ensure that the engine is stopped. If fuel is split whilst refuelling take
measures to clean it up, do not restart engine until it is safe.
• The exhaust of this machine can reach high temperatures do not place objects close to it or on it.
Do not perform maintenance on a hot engine.
• Operator must be aware of all prohibited areas e.g. slopes, rough or dangerous terrain.
• Do not clean around the machine if the engine is running.
• When carrying out maintenance on the hydraulic system ensure that the oil is cool and that there is
no residual pressure in the circuit. Skin could be penetrated from hydraulic oil under pressure.
• Ensure that the operator wears all the necessary safety equipment at all times.
• Do not operate the machine if it is damaged, incorrectly adjusted or unassembled.
• To prevent an accident, place a warning sign on the machine and remove keys whilst performing
maintenance.
• When filling the skip no persons should be on the machine.
• Do not carry passengers.
• The foot plate should be kept clean from oil or dirt.
• Do not remove the coolant cap when engine is hot. Do not add coolant to the engine when hot.
• The machine should be parked in a safe position on firm level ground. Never leave the engine
running or key in the ignition.
• Before taking the machine onto the public road insure that the vehicle adheres to all road traffic
regulations. When on the road driving laws must be obeyed.
• Tyre repair must only be carried out by trained persons with the correct knowledge and equipment.
A reputable tyre firm with competent staff is recommended for this task.
• If the machine does roll over, the driver should brace themselves, hold tight to the steering wheel,
allow the seat belt to retain them and wait for the machine to come to a halt.
• If replacing parts always use parts supplied or recommended by the manufacturer. Never use parts
of lower specification.
• Always use qualified personnel to carry out repairs on the machine.
• Never over fill the engine with oil or the fuel tank with fuel.
• If the hydraulic oil level is low never start the engine.
• When starting the machine follow the instructions on the manual and on the machine.
• If oil is leaking from the machine report it and get it repaired immediately.

18
Safety Information
This machine is designed to transport free flowing materials. If used in the correct manner it
shall provide a efficient and safe means of transport and meet all performance standards.
The operator of the machine must be an able bodied adult fully trained in its operation.
ALWAYS
•
Perform a daily check of the machine before starting.
•
Ensure instruction manual stays with the machine.
•
Check for children before starting, as they could be out of sight.
•
Have machine in neutral gear before starting.
•
Look for danger in the work area i.e. Holes, trenches, people working in confined area etc.
•
Clear obvious hazards and operate with caution.
•
Ensure visibility is clear when operating the machine.
•
Operate the machine carefully on gradients.
•
If stuck winch the machine free.
•
Wear protective clothing.
•
Wash and clean machine daily keeping water away from electrics.
•
Adjust seat to suit each driver.
•
Reduce load amount if material is of a sticky or non free flowing nature.
NEVER
•
Mount or jump obstacles such as kerbs and manholes.
•
Speed over rough terrain, always approach with caution.
•
Leave unattended the machine with the engine running this is not only dangerous but can
cause engine damage.
•
Attempt any repair to vehicle unless key is removed.
•
Tamper with any safety device on the machine.
•
Remove or tighten any hose when engine is running.
•
Start the machine unless on the drivers seat.
•
Carry any passenger.
•
Load the machine so that visibility is obstructed.
•
Overload the dumper beyond its rated pay load.
•
ill the skip with a load that protrudes over the edge. This will block visibility, make the
dumper unstable and could cause danger to pedestrians.
•
Tip into a trench unless some one is guiding the driver in with signals to prevent the trench
giving way.
•
Move the dumper with the skip in the tip position.
•
Work under the skip unless supplied prop is in place.
Always use the correct fuel, oil and grease specified by the manufacturer.
Check for over head obstructions and never operate the machine unless it is safe
to do so.
Do not use the dumper other than what it was intended for by the
manufacturer.
The driver should make themselves aware to other work colleagues.
Ensure the tyres are run at the correct pressures and well maintained.
Never cross steep inclines.
Never drive the machine close to unsteady ground such as trenches, holes etc.

19
Safety Information
ROLL OVER PROTECTION STRUCTURE (ROPS)
FATIGUE AND FINITE LIFE PROBLEMS WITH ROPS.
ROPS on the whole are maintenance free but in the unlikely event of a failure it is usually
due to the operator not inspecting or periodically checking the ROPS for cracks, loose bolts,
damage or other normal wear and tear. Proper maintenance and routine checks of the ROPS
on the machine will insure lifesaving function and long life of the system.
FACTORS THAT LEAD TO MISUSE OR DAMAGE TO ROPS
•
Vibration can cause structure damage and/or when loading in some instances.
•
A corrosive environment.
•
Continued use of the ROPS after a roll over causing damage to the structure.
•
Unauthorized Modifications to the ROPS.
•
Mount fatigue.
•
Replacing bolts with the wrong grade or wrong torque setting.
•
Incorrect installation.
ATTACHMENT AND/OR MODIFICATIONS
ROPS are not intended as a load carrying member and should not be used to mount things
such as, pull hooks, winches, booms, etc. Non load bearing attachments such as mirrors,
fans, heaters, lights, etc. can be installed using manufacturers guidance.
REPAIR & MAINTENANCE
•
Water drainage holes should be kept free from dirt or blockages so that water does not get
trapped and freeze damaging the structure.
•
Paint peeling or corrosion on the ROPS should get immediate attention.
•
Replacement of the ROPS or mounts should be done in a professional way, replace worn
bolts and re-torque to correct settings.

20
Safety Information
SEAT BELT INFORMATION
•
Improper inspection of the seat belt could cause serious injury or loss of
life in the event of an accident.
•
In the event of an accident the entire seat belt system must be replaced.
•
If needed the seat belt must be replaced throughout the life of the
machine. The belt must get inspected at least once a year or more often
if the belt is exposed to harsh conditions.
•
If the seat belt shows signs of wear it is vital that the entire belt both
sides are replaced.
Before operating the machine it essential that all drivers
put on the seat belt.
To fit the seat belt correctly, pull the belt around your
waist and press buckle blade into buckle lock.
Pull belt webbing through buckle blade to remove slack.
The seat belt must be correctly adjusted every time.
If the belt is worn loose in the event of an accident or roll
over it may cause serious injury.
To release the seat belt press either of the red buttons on
the buckle lock and allow the seat belt to fully retract.
Buckle up it could save your life.
NOTE:
Keep the buckle area clean and dry. Dirt and other foreign items can gum up the works and
prevent your belt from buckling correctly, thereby weakening its ability to hold you firmly in
place during an accident or roll over.
If your seat belt does get dirty and needs cleaning use mild soap and warm water. Do not
use a strong detergent, bleach or dye, since these caustic fluids may weaken the belt's
material.
Table of contents
Other NC Utility Vehicle manuals
Popular Utility Vehicle manuals by other brands
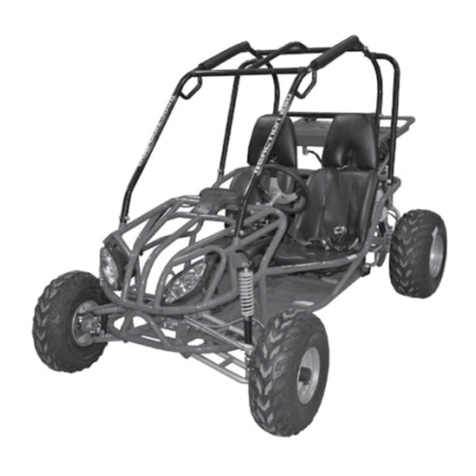
Baja
Baja BR250 Go-Kart owner's manual
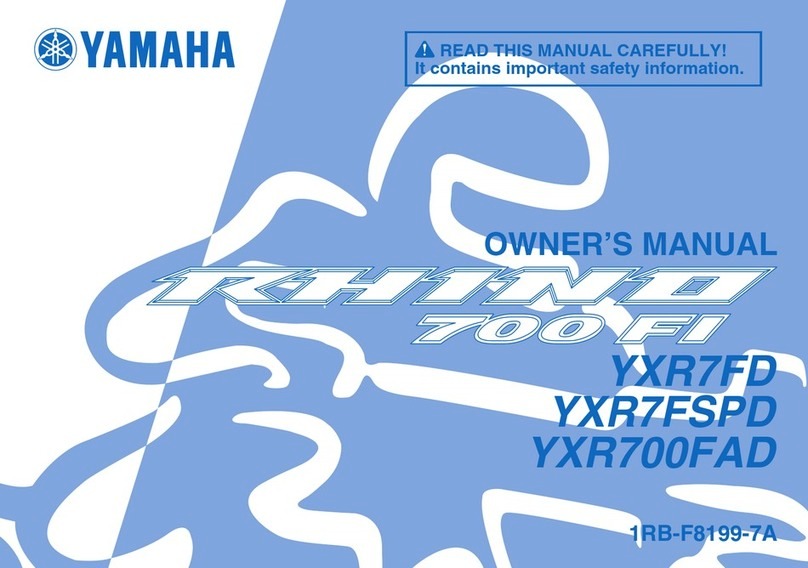
Yamaha
Yamaha YXR7FD owner's manual

Go Kart
Go Kart 500 owner's manual
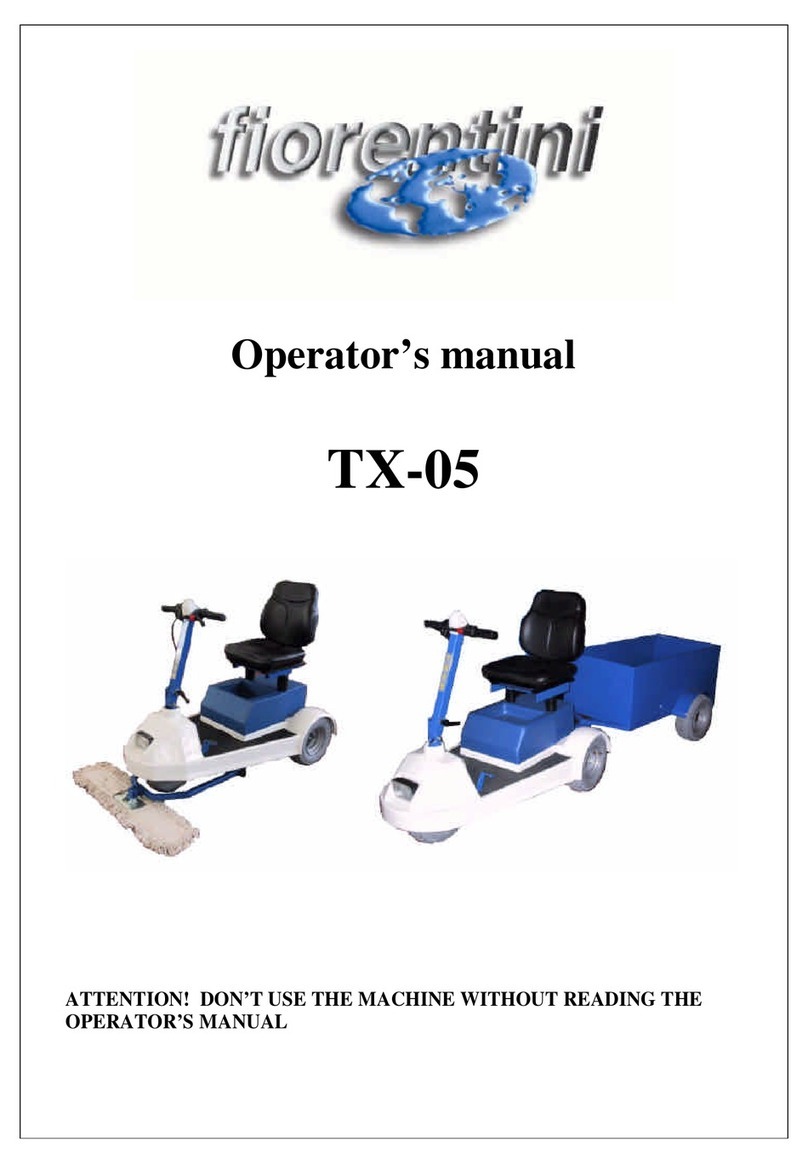
FIORENTINI
FIORENTINI TX-05 Operator's manual
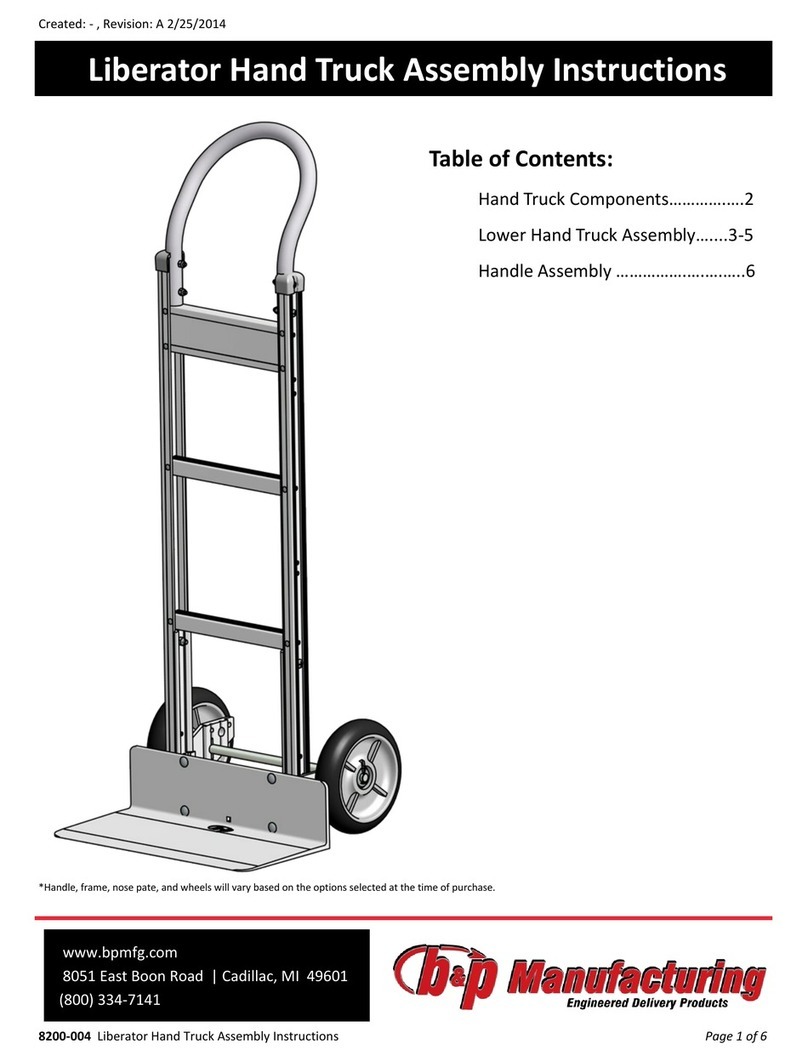
B&P Manufacturing
B&P Manufacturing Liberator Assembly instructions
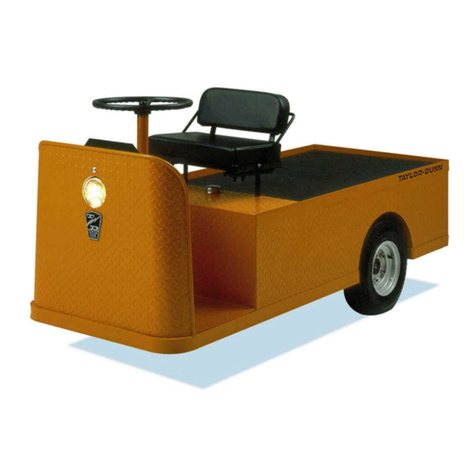
Taylor-Dunn
Taylor-Dunn C0-014-32 Operation, t roubleshooting and replacement parts manual