Nexen RSTC1000 User manual

FORM NO. L-21204-D-0418
Tension Controller
RSTC1000
WEB CONTROL PRODUCTS
User Manual

FORM NO. L-21204-D-0419 2
In accordance with Nexen’s established policy of constant product improvement, the specifications contained in this
manual are subject to change without notice. Technical data listed in this manual are based on the latest information
available at the time of printing and are also subject to change without notice.
Technical Support: 800-843-7445
(651) 484-5900
www.nexengroup.com
Nexen Group, Inc.
560 Oak Grove Parkway
Vadnais Heights, MN 55127
Copyright 2018 Nexen Group, Inc.
Read this manual carefully before installation and operation.
Follow Nexen’s instructions and integrate this unit into your system with care.
This unit should be installed, operated and maintained by qualified personnel ONLY.
Improper installation can damage your system or cause injury or death.
Comply with all applicable codes.
DANGER
Manufacturers’ Declaration
In accordance with the CE machine directive 98/37/EC, Appendix II B
We hereby declare that the pneumatic/mechanical components described in this manual as well as their indi-
vidual components are intended, in the configuration in which they have been supplied, to be integrated into
a machine.
They must not be put into service until the machinery into which it is to be incorporated has been declared in
conformity with the provisions of the Directive mentioned above or its amendments.
All Nexen products are designed in accordance with the manufacturing directives for pneumatic systems ac-
cording to EN 983.
ISO 9001 Certified

3FORM NO. L-21204-D-0419
Copyright 2018 Nexen Group, Inc.
Table of Contents
Introduction ----------------------------------------------------------------------------------------------------------------------------------------4
Wiring Installation Guidelines --------------------------------------------------------------------------------------------------5
Installation -----------------------------------------------------------------------------------------------------------------------------6
Electrical Connections------------------------------------------------------------------------------------------------------------7
Network Connections -----------------------------------------------------------------------------------------------------10
Input/Output Descriptions -----------------------------------------------------------------------------------------------11
Setup --------------------------------------------------------------------------------------------------------------------------------- 13
RSTC to PC USB Communications ---------------------------------------------------------------------------------13
Display Window--------------------------------------------------------------------------------------------------------------13
Setup Window----------------------------------------------------------------------------------------------------------------13
Torque Actuator --------------------------------------------------------------------------------------------------------------14
Tension Zone ------------------------------------------------------------------------------------------------------------------14
Alarms ---------------------------------------------------------------------------------------------------------------------------15
Web ------------------------------------------------------------------------------------------------------------------------------15
Outputs -------------------------------------------------------------------------------------------------------------------------15
Signal Calibration-----------------------------------------------------------------------------------------------------------------16
Tension Signal Calibration------------------------------------------------------------------------------------------------16
Diameter Signal Calibration----------------------------------------------------------------------------------------------17
Run/Stop Signal Selection-----------------------------------------------------------------------------------------------17
Tuning ------------------------------------------------------------------------------------------------------------------------------- 19
RSTC Tuning Window -----------------------------------------------------------------------------------------------------19
Tuning Procedure------------------------------------------------------------------------------------------------------------19
Setpoint -------------------------------------------------------------------------------------------------------------------------20
Advanced-----------------------------------------------------------------------------------------------------------------------20
Taper Tension -----------------------------------------------------------------------------------------------------------------20
Network Port Setup -------------------------------------------------------------------------------------------------------------21
Operation----------------------------------------------------------------------------------------------------------------------------21
Manual Control ---------------------------------------------------------------------------------------------------------------21
Unwind Application ---------------------------------------------------------------------------------------------------------22
Splicing Unwind Application --------------------------------------------------------------------------------------------22
Wind Application ------------------------------------------------------------------------------------------------------------23
Splicing Wind Application------------------------------------------------------------------------------------------------23
Spring Disengaged Clutch-----------------------------------------------------------------------------------------------24
Mid-Process Application--------------------------------------------------------------------------------------------------24
Diagnostics --------------------------------------------------------------------------------------------------------------------24
Specifications----------------------------------------------------------------------------------------------------------------------25
Part Numbers ----------------------------------------------------------------------------------------------------------------------25
Troubleshooting -------------------------------------------------------------------------------------------------------------------26
Service Instructions--------------------------------------------------------------------------------------------------------------27
Appendix-----------------------------------------------------------------------------------------------------------------------------27
Warranty -----------------------------------------------------------------------------------------------------------------------------28

FORM NO. L-21204-D-0419 4
INTRODUCTION
Nexen RSTC Tension Controllers are used to control web tension, relying on load cell based tension sensors to measure
web tension. As a part of a tension control system, the RSTC measures the web’s tension and corrects tension errors
by sending a signal to change the torque output of brakes, clutches, and motor drive systems. The RSTC automatically
adapts to changes in inertia and torque as roll diameters change. This ensures constant/stable tension at all times and
allows for faster accelerations and decelerations for a more productive web machine. The RSTC does not require a
diameter sensor for constant tension applications and can adapt to spliced rolls of different diameters automatically
without readjustment.
Applications for the RSTC include unwinding, mid process, constant tension winding, and taper tension winding.
RSTC1000 SYSTEM
The RSTC1000 Tension Control System includes three components: the RSTC1000, RSTC Operator Panel (ROP), and
RSTC Communications Software. The RSTC1000 tension controller can be used as a slave on a Modbus RTU network.
Because of this capability, many Human Machine Interfaces (HMIs) and Programmable Logic Controllers (PLCs) can
communicate directly with it. Web machines that already have a compatible HMI control panel do not require the ROP.
The Communications Software features setup, tuning and diagnostics functions and is available from the Nexen website:
www.nexengroup.com.
MOUNTING
The RSTC is designed to mount inside the machine’s control cabinet alongside other controllers, PLCs, relays, etc. Small
size and its DIN rail mounting capability make installation fast and easy. Pluggable connectors simplify wiring as they can
be removed for convenient access to terminals. Only requiring a commonly available 24 VDC supply, the RSTC requires
no hazardous voltages.
Figure 1

5FORM NO. L-21204-D-0419
WIRING INSTALLATION GUIDELINES
This product is designed to minimize the effects of ElectroMagnetic Interference (EMI) on its operation, but as
with any electronic device, proper installation and wiring methods are necessary to ensure proper operation. By
doing so, the interference from external effects such as electrical line spikes, electrical noise, static electricity, etc.
will be minimized. The following methods outline wiring installation guidelines to protect your system:
• All input and output signal and sensor cables must
be shielded with the shields tied to earth ground at
one end. In case of very high frequency (MHz range)
electrical noise, both ends of the shield need to be
tied to earth ground.
• Keep cable length and unshielded leads as short as
possible. Think of them as antennae for noise.
• Use power line filters to suppress interference on
the AC voltage lines that power the unit.
• Place a resistor-capacitor network (snubber) across
inductive coils such as relays and solenoids in order
to stop electrical interference at the source (See
Figure 2).
• Isolate signal and sensor cables from cables
carrying AC voltages, power for high current loads
or relays and solenoids. Either relocate the signal
and sensor cables away from other cables or use
grounded metal conduits to shield them. This will
reduce the potential for noise interference between
the signal and sensor cables and the other noisy
cables.
Figure 2
For environments that experience high levels of static electricity follow these additional guidelines:
• Remove the static charge from material carrying it.
In the case of webs that carry static charges, there
are static charge removal products available such as
static bars and ionized blowers.
• Ensure that sensors and machine frames are
grounded to earth through a low impedance path.
• Wrap grounding tinsel around sensors and cables
that are close to the source of the static electricity
and ground the tinsel to earth.
• Tie all signal and sensor cable shields directly
to earth ground without passing through the
electronic device. This will help prevent high voltage
interference from coupling into other circuits within
the device.
Relay
R
C
Snubber
Snubber applied across relay coil

FORM NO. L-21204-D-0419 6
INSTALLATION
Figure 3
Mount the RSTC within a user-supplied enclosure, typically
the machine’s controls cabinet. The RSTC can be mounted
on 35 mm DIN rail or panel mounted (Refer to Figure 3).
CAUTION
Mount the RSTC in a shock and vibration free
area with an ambient temperature of less
than 140°F [60 C] and more than 32°F [0 C].
149.0
[5.87]
110.3
[4.34]
13.9
[0.55]
13.9
[0.55]
35.0
[1.38]
75.0
[2.95]
134.1
[5.28]
7. 4
[0.29]
7. 4
[0.29]
1.1
[0.04] 2X
60.2
[2.37]
R2.2
[0.09]
4X

7FORM NO. L-21204-D-0419
ELECTRICAL CONNECTIONS
Figure 4 Electrical Connections
* Power cable must be less than 10 m [390 in].
** There are two terminals that require a low impedance connection
to earth ground.
† For improved signal integrity in noisy environments, tie cable
shields directly to Earth Ground.
46
45
44
43
42
41
40
39
38
37
36
35
34
33
32
31
30
29
28
27
26
25
24
Control Signal Shield & Earth Ground** †
Control Signal Common
Splice B Input
Splice A Input
Run/Stop Input
Signal Shield †
Common
Remote Tension Setpoint Input
+12 VDC Excitation
Common
Diameter Sensor Input
+24 VDC Excitation
Load Cell Shield †
Excitation Common
+6 VDC Excitation
–Sensor Signal
+Sensor Signal
Excitation Common
+6 VDC Excitation
–Sensor Signal
+Sensor Signal
+24 VDC
Common
Earth Ground**
Alarm 1 Out
Alarm 2 Out
Alarm Common
† Alarm Shield
0-10 VDC
Output Common
4–20 mA
Output Common
† Signal Shield
0–10 VDC
Output Common
4–20 mA
Output Common
† Signal Shield
1
2
3
4
5
6
7
8
9
10
11
12
13
14
15
16
17
18
19
20
21
22
23
RSTC
USB
Control
Inputs
Power
Input*
Control
Output B
Control
Output A
Load
Cell 1
Load
Cell 2
Power Indicator
Reset
Network Port and
Indicators

FORM NO. L-21204-D-0419 8
FIGURE 5 Alarm Output Connections
Alarm Out
RSTC
RSTC
To PL C Input
VDC Common
VDC* (See Specifications for
maximum voltage.)
R(See Note.)
User Supplied
User Supplied
NOTE: The minimum value of resistor (R) is 7 x VDC.
VDC Common
VDC*
(See Specifications for
maximum voltage.)
(See Note.)
User Supplied
User Supplied
R
External Indicator
VDC Common
VDC *
(See Specifications for
maximum voltage.)
(See Notes.)
User Supplied
User Supplied
External
Coil
1N4002
Alarm Output Tied to External Indicator
Alarm Output Tied to PLC Input.
Alarm Output Tied to External Inductive Coil
Alarm
Common
Alarm Out
Alarm
Common
RSTC
Alarm Out
Alarm
Common
NOTE: The minimum value of Resistor (R) is equal to VDC divided by the maximum
current limit of the Indicator. Maximum current limit of the indicator must be less
than the current limit of the alarm output (See Specifications for maximum current).
NOTE: Be sure the current requirement of the External Coil does not exceed the
capability of the alarm output (See Specifications for maximum current.
Any inductive load such as relay coil must have a 1N4002, or equivalent, diode
across it as shown.
* To isolate the Alarm Output signals use power
supply that is separate from the RSTC power supply.

9FORM NO. L-21204-D-0419
CFL or Single Full Bridge Strain Gauge Load Cell
24 25 26 27 28 29 30 31 32 33 34
No. 2
Sensor
No. 1
Sensor
BRWGBRWG
Dual MB Single MB
24 25 26 27 28 29 30 31 32 33 34
Sensor
BRWG
Cable
Shield
Add
Sensor 2
RBW
SW Sensor Colors
–Vex+VexVsig
24 25 26 27 28 29 30 31 32 33 34
Sensor 1
BRW
Cable
Shield
Add
Jumpers
SW Sensor Colors
–Vex+VexVsig
SW or Half Bridge Strain Guage Load Cell
24 25 26 27 28 29 30 31 32 33 34
Sensor
BRWG
Cable
Shield
Add
CFL Sensor Colors
–Vex+Vex–Vsig+Vsig
Figure 6 Control Input Signals
NOTE: To isolate the Control Input Signals, use a power
supply that is separate from the RSTC power supply.
Figure 8 Load Cell Connections
40 41 42 43 44 45 46
Cable Shields
+12 to + 24 VDC
DC Common
Run/Stop
Splice A
Splice B
32 33 34 35 36 37 38 39
1–5 kΩ
Potentiometer
NOTE: Potentiometer can be replaced with analog
voltage signal by connecting analog signal (0-12V
maximum) to terminal 37 and signal common to
terminal 38.
Figure 7 Remote Tension Setpoint

FORM NO. L-21204-D-0419 10
NETWORK CONNECTIONS
Modbus RS485 Port: This port is for communicating with
the RSTC1000 using the Modbus RTU protocol over a
2-wire or 4-wire RS485 physical layer (Refer to Figure 10).
Communication Indicator: Yellow indicator, visible
through top cover, will illuminate whenever the RSTC1000
communicates over the RS485 port.
Communication Error Indicator: Red indicator, visible
through top cover, will illuminate whenever the RSTC1000
detects an error with a received message.
Figure 10 Modbus RS485 Connections
DC Common
TxB+
TxA–
RxB+
RxA–
1
2
3
4
5
6
DC Common
RxB+
RxA–
TxB+
TxA–
LTR
RSTC1000
PLC or HMI
Four Wire RS485 Connections
LTR
DC Common
TxB+
TxA–
RxB+
RxA–
1
2
3
4
5
6
DC Common
Non-Inverted Tx/Rx
Inverted Tx / Rx
RSTC1000
PLC or HMI
Two Wire RS485 Connections
+24 VDC
DC Common
TxB+
TxA–
RxB+
RxA–
1
2
3
4
5
6
Red
Black
White (RxB+)
Yellow (RxA–)
Blue (TxB+)
Orange (TxA–)
RSTCROP
ROP - RSTC
LTR
Termination resistors added externally
- Recommend 150 Ω, 0.5 W
LTR = User supplied line termination resistor
Cable Recommendation:
- Shielded
- 24 awg is always sufficient
- 4 wire system, 1000 m (9600 baud)
- 2 wire system, 500 m (9600 baud)
Figure 9 RSTC1000
RSTC1000
USB
RS485
Power Indicator
Reset
Communication Error
Indicator
Communication Indicator

11 FORM NO. L-21204-D-0419
INPUT/OUTPUT DESCRIPTIONS
NOTE: Refer to Figure 4 for RSTC Pinout.
USB Port: This port is used to connect to a personal
computer during setup, tuning, or diagnostic monitoring
of the RSTC and is compliant with USB 2.0.
Network Port: This port is for communicating with the
RSTC using a networking protocol. Refer to NETWORK
CONNECTIONS section or the HMI/PLC Design Guide
for network specific information.
Network Indicators: Indicators will illuminate to show
status of network communications. Refer to NETWORK
CONNECTIONS section or the HMI/PLC Design Guide
for network information.
Power Input: RSTC requires 24 VDC to operate (Refer
to SPECIFICATIONS for current rating). A green indicator
visible through the top cover will illuminate when this
voltage is present. Common is the return line for the
24 VDC power supply. Earth Ground is the terminal for
connection to Earth Ground via a low resistance conductor.
Two terminals, 3 and 46, must be connected to Earth
Ground in order for cable shielding to work properly.
Reset: A reset switch, accessible through the top cover,
will reset the RSTC whenever depressed without having
to cycle power on and off.
Alarms: Transistor outputs that can be configured for
normally open or normally closed operation (Refer to
SPECIFICATIONS for ratings). Alarm 1 is activated
whenever a web break is detected. Alarm 2 is activated
whenever one or more of the following conditions occur:
No Control: control signal output has reached 0% or
100% during automatic operation and web tension is
not at set point. This is often caused by accelerating a
large roll too quickly or excessive web speed near core.
Both cases can cause excessive tension with a control
output at 0% and unable to decrease any further. “No
control” can also be cause by a large roll decelerated
too quickly causing the output to go to 100%, but the
web tension remains below setpoint.
High Tension: Web tension is greater than the high-
tension limit.
Low Tension: Web tension less than low-tension
limit.
Max Output: Control signal output has reached
maximum output limit, typically 100%.
Zero Output: Control signal output has reached
minimum output limit, typically 0%.
The alarm outputs can be isolated from the RSTC power
supply by using a separate power source and common.
Alarm Common is the return line for the alarm signal. Alarm
Shield is the terminal for connecting the alarm cable shield
to chassis ground.
Control Outputs: The Control Output signal is used to
change the torque output of a pneumatic brake or clutch
via an electro-pneumatic converter or a motor drive system
for the purpose of controlling tension. There are two
channels of control outputs, Control Output A and Control
Output B. Each channel has a 0 – 10 VDC and 4 – 20 mA
output signal. All Control Outputs are isolated from the
RSTC power supply. Only one channel at a time can be
used to control tension. When one channel is active the
other channel is in standby mode. The choice of whether a
Control Output is active or in standby mode is made with
the Splice Control Inputs. The 0 – 10 VDC and 4 – 20
mA terminals are the control signal outputs. Common is the
return line for the control signal outputs. Signal Shield is the
terminal for connecting the cable shield to chassis ground.
Load Cell Inputs: The RSTC will accommodate two
web tension sensing load cells. Polarity of the load cell
signals does not matter as long as the polarity of both load
cell input signals are oriented the same. The +/- Sensor
Signal is for the tension level signal from the load cells.
The +6 VDC Excitation is the power supply for the load
cells. Excitation common is the return line for the load cell
power. Load cell cable shields must be tied directly to
Earth Ground for best noise reduction
Diameter Input: This input provides winder roll diameter
measurements for the taper tension algorithm and is not
used for anything else. Diameter signal can be provided
by a diameter sensor or voltage source, such as a PLC’s
analog output card, capable of 0 – 12 VDC maximum signal
range. The +24 VDC Excitation and +12 VDC Excitation
provide power when using a diameter sensor. Common is
the return line for the diameter signal and sensor excitation.
Diameter Sensor Shield is the terminal for connecting the
diameter sensor cable shield to chassis ground.
Remote Tension Setpoint: This 0 - 12 VDC input allows
the tension setpoint to be set by an external potentiometer
or analog signal (See Figure 7). Remote Tension Setpoint
is scaled such that 0 V corresponds to Minimum Tension
Setpoint and 12 V corresponds to Maximum Tension
Setpoint. When using a PLC that outputs lower than 12
V, adjust the Maximum Tension Setpoint to compensate.
Before using Remote Tension Setpoint, it must be enabled,
see TUNING, afterwards tension setpoint changes from
all other sources are ignored.
Web Tension Monitor: Web tension can be monitored as
a 0 – 10 VDC or 4 – 20 mA signal from Control Output
B when enabled, see SETUP. Web Tension Monitor is

FORM NO. L-21204-D-0419 12
INPUT/OUTPUT DESCRIPTIONS (CONT.)
scaled such that 0 V or 4 mA corresponds to Minimum
Tension Setpoint and 10 V or 20 mA corresponds to
Maximum Tension Setpoint. If Control Output B is being
used as a web tension monitoring output, then it is not
available for use as a web tension control output. Only
Control Output A can be used for tension control in this
instance.
Control Inputs
Run/Stop: When 12 – 24 VDC is applied to this digital
input for at least 100 milliseconds, the RSTC will respond
according to Run/Stop option selected during setup of
the RSTC (refer to SIGNAL CALIBRATION) and cause
the RSTC to go into the run mode or the stop mode. The
RSTC will actively control tension in both the run and stop
modes, however the RSTC will only adapt its control gains
in the run mode. During stop mode, all control gains are
held constant.
NOTE: For unwinding applications, do not provide
the Run signal when the web remains stopped. This
will cause the RSTC to increase its gains too much
and produce tension oscillations when the web does
finally move.
Splice A/B: When 12 – 24 VDC is applied to one of these
digital inputs for at least 100 milliseconds, the RSTC will
respond by resetting Adaptation to a level determined by
SPLICE ADAPTATION. The RSTC will also make the cor-
responding Control Output active and the other standby.
The 12 – 24 VDC signal can be momentary or maintained,
however only one Splice Input can have the signal applied
at a time.
After power up, the RSTC will look at the Splice A and
Splice B inputs. If both are high or both are low then
Control Output A is made active and Control Output B
goes to standby. Therefore, apply the splice signal after
power up to insure the proper Control Output is active.
Any output in standby mode will maintain a constant output
level as determined by STANDBY OUTPUT variable. Also,
if Web Tension Output is enabled, then Control Output B
is no longer available for web tension control and Splice
B input is ignored.
The Control Inputs can be isolated from the RSTC power
supply by using a separate power source and common.
Control Signal Common is the return line for the Run/Stop
and Splice A/B input signals. Control Signal Shield is the
terminal for connecting the cable shield to chassis ground.

13 FORM NO. L-21204-D-0419
SETUP
RSTC TO PERSONAL COMPUTER USB
COMMUNICATION
In order to setup the RSTC, a USB cable and the
RSTC Communications Software are required. A Type
A to mini Type B 2.0 USB cable is provided with the
RSTC. RSTC Communications Software is available by
download from Nexen’s website, www.nexengroup.com.
Enter RSTC product number (See PART NUMBER
section) in the product number search window and
press Go; next select Software from the Accessories
menu and finally pick the appropriate software link.
Instructions for installing the software can also be
found here and the instructions for using the RSTC
Communications Software can be accessed in the Help
menu.
1. Connect 24 VDC power supply to Power Input
terminals (Refer to Figure 4).
2. Power up the computer.
3. Connect the USB cable between computer and
RSTC (Refer to Figure 11).
4. Turn on 24 VDC power supply, Power indicator will
be on (Refer to Figure 11).
Note: Refer to the RSTC Communications Software
Help menu for instructions on navigating the program
and accessing its functions. The steps below describe
using the functions to configure the RSTC.
DISPLAY WINDOW
Select the DISPLAY icon from the toolbar (See Figure 12).
Units: Select IMPERIAL if tension and diameter are to be
displayed in units of pounds and inches; Select METRIC
if tension and diameter are to be displayed in units of
newtons and millimeters.
ROP Language: Select the language from the drop-down
menu that the ROP will display.
Press SEND to update the RSTC.
SETUP WINDOW
Select the SETUP icon from the toolbar (See Figure 13).
Note: After changing values, the SEND key must be
pressed to send the values to the RSTC. Figure 13 Setup Screen
Figure 11
Figure 12 Display Window
RSTC
USB
Power Indicator
Reset
Network Port and
Indicators

FORM NO. L-21204-D-0419 14
TENSION ZONE
Select whether the RSTC will control a winder or unwind
tension zone. For mid-process applications select Wind
if the controlled nip is downstream of the leader nip and
select Unwind if the controlled nip is upstream of the leader
nip (Refer to Figure 15).
RSTC
Controlled
Nip
Select
Wind
Load
Cell
RSTC
Controlled
Nip
Select
Unwind
Load
Cell
Leader
Nip
Leader
Nip
Figure 15
Tension Zone Selection for Mid-Process Application
Figure 14 Torque Actuator Selection Screen
TORQUE ACTUATOR
Actuator: Select from the Torque Actuator drop down
menu the type of actuator the RSTC will control.
Actuator Inertia: Enter the rotor inertia of the brake or
clutch in the designated imperial or metric units. The choice
of units is determined by selecting the DISPLAY icon and
then selecting Imperial or Metric in the UNITS pane. Inertia
values for Nexen Brakes and Clutches can be found in the
Nexen catalog or website. For drive systems, enter the mo-
tor rotor, drive pulley, and shaft coupling inertias.
Refer to Appendix for inertia formulas and table of values.
Use an Actuator Inertia value of 1.0 in cases where the
actual value is not known.

15 FORM NO. L-21204-D-0419
ALARMS
NOTE: A web break is detected whenever the web
tension falls below 10% of the Maximum Tension
Setpoint Alarm 1 is used to signal the break.
Tension Tolerance: Enter the tolerance (0–100 %) of
the tension setpoint to establish the limits for the High
Tension and Low Tension alarms. For example, if Tension
Tolerance is set to 10 and the Tension Setpoint was 100,
then the High Tension alarm would be activated if the web
tension exceeded 110 and the Low Tension alarm would
be activated if the web tension fell below 90. These alarms
utilize Alarm 2 to signal their condition.
Alarm Outputs: Select if the alarm outputs are to be
normally open (NO) or normally closed (NC). A normally
open output will close during an alarm condition while a
normally closed output will open.
WEB
Max Diameter: Enter in the maximum full roll diameter that
will be used. For mid-process tension control applications,
enter 1.1 multiplied by the nip roller diameter.
Min Core Diameter: Enter in the minimum core diameter
that will be used. For mid-process tension control
applications, enter the diameter of the nip roller.
Avg Web Width: Enter in the average web width [(maximum
width + minimum width) / 2].
Material: Select the web material to be used: Paper or
Plastic, Steel, or Aluminum from the drop down menu
(See Figure 16).
OUTPUTS
Minimum Output %: Used to specify a minimum output
level, typically set to 0 %. Minimum Output is often set to
a value greater than zero in order to overcome the spring
force in brakes and clutches that are spring disengaged.
Maximum Output %: Used to specify the maximum output
level, typically set to 100%.
Standby Output %: Used to specify the output level in
standby mode (not controlling tension). Standby Output
is often used in splicing unwind applications when it is
desired to have some brake drag on the make ready roll.
Tension Monitor: Select ON and Control Output B
will output web tension monitor signal or select OFF
and control Output B will output web tension control
signal (See Web Tension Monitor in INPUT/OUTPUT
DESCRIPTIONS section).
Figure 16 Web Material Selection Screen

FORM NO. L-21204-D-0419 16
Figure 17 Signal Calibration
TENSION SIGNAL CALIBRATION
Set the Maximum Tension Setpoint before calibrating
tension sensors. Afterwards, re-calibration of tension
sensors is required whenever the Maximum Tension
Setpoint is changed.
Minimum Tension Setpoint: Enter minimum tension level
that will be run on the machine in the designated imperial or
metric units. The choice of units is determined by selecting
the DISPLAY icon and then selecting Imperial or Metric
in the UNITS pane.
Maximum Tension Setpoint: Enter maximum tension level
that will be run on the machine in the designated imperial or
metric units. The choice of units is determined by selecting
the DISPLAY icon and then selecting Imperial or Metric
in the UNITS pane.
NOTE: Selection of tension setpoints outside these
limits will not be allowed by the RSTC and the Minimum
Tension Setpoint will limit taper tension’s minimum
tension.
Calibration Set: Select Set 1, Set 2 or Set 3
The RSTC allows the use of three different sets of
calibration values for converting load cell output voltages
into tension values. These calibration sets can be used for
different web paths that utilize the same set of load cells
and have different web wrap angles.
1. Press TENSION (See Figure 18).
2. Under Calibration Set 1, enter the web tension that
will be used to calibrate the span condition into the
SPAN TENSION box . Span Tension is equal to the
weight as shown in Figure 19 and should be set as
close as practical to MAXIMUM SETPOINT.
3. Press CALIBRATE 1.
4. Unload the tension sensing roller and then press
OK. The tare condition, which is the weight of the
roller, has just been recorded.
5. Load the tension sensing roller, as shown in Figure
17, using the amount of web tension entered for
SPAN TENSION in step 2 and then press OK.
6. Unload the tension sensing roller and then press
OK. The tare condition is rechecked and the
calibration process is completed.
SIGNAL CALIBRATION
SIGNAL CALIBRATION WINDOW
Select the SIGNAL CALIBRATION
icon from the toolbar. (See Figure 17).
Figure 19
For other web paths using the same load cells, repeat
steps 1–6 for Calibration Set 2 and Set 3.
7. To select a calibration set to be used, select
Calibration Set 1, Set 2, or Set 3 and press SEND.
Figure 18 Tension Calibration

17 FORM NO. L-21204-D-0419
RUN/STOP SIGNAL SELECTION
Note: After making a selection, the SEND key must be
pressed to send the values to the RSTC.
The RSTC determines the run and stop state of a web
machine through the Run/Stop signal input and was
designed to accommodate many different types of run and
stop machine state signals.
The following figure and descriptions detail the variations
of Run/Stop signals that the RSTC accepts.
run/stop sIgnal MaIntaIned
When the Run/Stop input signal is maintained low, the
RSTC assumes the machine is stopped. When the Run/
Stop input signal transitions to a maintained high, the
RSTC algorithm will begin adapting to account for the
roll’s diameter and inertia. The web must be in motion
for unwinding applications or in tension for winding
applications when this signal goes high otherwise the
Adaptive Gain will increase to maximum. After the Run/
Stop signal transitions back to low, the Adaptive Gain will
return to Initial Adaptation (See OPERATION section).
Figure 21 Run/Stop Signal Selection Screen
Figure 20 Diameter Calibration
DIAMETER SIGNAL CALIBRATION
1. Press DIAMETER (See Figure 20).
2. Press Yes if a diameter signal is present and
continue with calibration. Press No if there is not a
diameter signal, therefore the calibration procedure
will not continue.
3. Enter the core diameter and large roll diameter
that will be used for calibration. Core and large roll
diameters can be any representative diameter, not
the minimum and maximum diameters used on the
machine.
4. Press CALIBRATE and apply the voltage that
represents the core diameter to the Diameter Input.
5. Press OK and apply the voltage that represents the
large roll diameter to the Diameter Input.
4. Press OK and the calibration is completed.
It does not matter if the diameter signal voltage increases
or decreases with increasing diameter.
CONTINUED

FORM NO. L-21204-D-0419 18
Run Pulsed
(Encoder)
Run Only
(Momentary)
Run / Stop
(Momentary)
Run / Stop
(Maintained)
0%
100%
Machine Speed
Pulse Time (t) must be > 100ms
-t-
Time
run only sIgnal MoMentary
When the Start/Stop input signal pulses high, the RSTC
algorithm will begin adapting to account for the roll’s diam-
eter and inertia. The web must be in motion for unwinding
applications or in tension for winding applications when
this signal goes high otherwise the Adaptive Gain will
increase to maximum. After the machine stops, the RSTC
will continue trying to adapt until the Run/Stop input pulses
high again and forces the adaptation process to start over
from Initial Adaptation.
Figure 22
run/stop sIgnal MoMentary
When the Run/Stop input signal pulses high, the RSTC
algorithm will begin adapting to account for the roll’s
diameter and inertia. The web must be in motion for
unwinding applications or in tension for winding applica-
tions when this signal goes high otherwise the Adaptive
Gain will increase to maximum. After the Run/Stop signal
pulses high a second time, the Adaptive Gain will return
to Initial Adaptation, as the RSTC assumes the machine
has stopped (See OPERATIONS section).
run pulsed (enCoder)
The first time a machine driven encoder pulses Run/Stop
input, the RSTC algorithm will begin adapting to account
for the roll’s diameter and inertia. The web must be in mo-
tion for unwinding applications or in tension for winding
applications when this signal goes high otherwise the
Adaptive Gain will increase to maximum. The RSTC will
continue to actively adapt until the encoder pulsing ceases
for three seconds. At that time, the RSTC assumes the
machine has stopped and the Adaptive Gain will return to
Initial Adaptation (See OPERATION section). The encoder
pulse frequency must be in the range of 1Hz to 10 kHz.
run/stop vIa CoMMunICatIons
Select this option if the Run/Stop signal will be provided
by software command over an industrial network.
After determining the appropriate signal type, make a
selection from the list of options in the Run/Stop Window
(refer to Figure 21) and press SEND.

19 FORM NO. L-21204-D-0419
3. Start the machine and run at a moderate web speed
and tension.
Note if the output oscillates excessively or if the
amount of time taken to reach the tension setpoint
after web speed becomes consistent is too long. It
is normal for the output value to fluctuate as long
as the web tension does not.
• If the output oscillations are not excessive and
the amount of time is too long, stop the machine.
Increase Gain by 0.5 and return to step 3.
• If the output signal begins to oscillate excessively,
stop the machine. Decrease Gain by 0.5 and return
to step 3.
• If performance is satisfactory, proceed to step 4.
4. Load a small roll on to the roll stand.
5. Start the machine and note if there are excessive
output oscillations.
• If the output oscillations are excessive, stop the
machine. Reduce the Gain by 0.5 and return to
step 5.
6. Continue to test for output oscillations until the roll is
as small as practical.
During tuning, if the Gain value reaches 1.0 and further
adjustment is required, then stop the machine, decrease
Stabilization by 1.0, set Gain to 2.5 and return to the
tuning process.
Likewise during tuning, if the Gain values reaches 10.0
and further adjustment is required, then stop the machine,
increase Stabilization by 1.0, set Gain to 2.5, and return
to the tuning process.
TUNING PROCEDURE
Most applications will only require adjustment of
Gain and Stabilization to tune the RSTC. Advanced
tuning parameters are available for more demanding
applications.
Note: To view diagnostics while tuning, select the
DIAGNOSTICS icon from the toolbar; then select
START in the Communication Pane (See Diagnostics
Section).
The RSTC features an adaptive algorithm that is user
tuned. After tuning, the algorithm will automatically adapt
internal gain values to account for changes in roll diameter
and inertia. This algorithm is modeled after unwinding
and winding applications which results in an non-linear
adaptation process that closely follows the actual changes
occurring in a web machine.
Stabilization is an important variable that must be set
properly for the RSTC to perform correctly. If it is set too
low, Gain will not be able to be set high enough for proper
operation and could also cause a high frequency tension
oscillation. If it is set too high, the RSTC could produce a
low frequency tension oscillation.
When tuning it is important to check for output oscillations
during large and small roll machine start conditions.
Further, initial tuning performed for a small roll may not
result in adequate performance with a full roll as the RSTC
could be sluggish. Therefore, start with Gain and Stability
set at their default values and begin tuning with as large a
roll as practical. For winding applications, us the default
Stabilization and Gain value and only change the Gain
as necessary in order to build a large roll then follow the
tuning procedure.
1. Set Stabilization to 15.0 and Gain to 2.5
2. Load as large a roll as practical on to the roll stand.
Figure 23 Tuning Screen
TUNING
TUNING WINDOW
Select the TUNING icon from the toolbar. (See Figure 23).
Note: After changing values, the SEND key must be
pressed to send the values to the RSTC.
Gain: Adjusts response of RSTC to magnitude changes in
tension. Higher values cause a more aggressive response
and lower values cause a lesser response.
Stabilization: Tunes the tension control algorithm to the
natural frequency of the empty core shaft that is being
controlled. When set properly this parameter allows the
gain to be set for best performance.

FORM NO. L-21204-D-0419 20
Tension Setpoint: Enter the desired web tension level.
The Tension Setpoint range is set by the Maximum and
Minimum Tension Setpoint values in the Setup window.
ADVANCED
Initial Adaptation: is the beginning point for the
adaptation process after the RSTC enters Run mode.
Tension oscillations could occur during a machine start
when roll size is near core diameter if this value is set
too high. Tension could be slow to come up to setpoint
after a machine start if this value is set too low. Best
recommendation is to use the default value and only
change if absolutely necessary.
SETPOINT
process is started closer to its final value in order to
arrive at the desired gains quicker. It is important to not
set Splice Adaptation so high that when a smaller than
average roll is spliced the tension begins to oscillate. Best
recommendation is to use the default value and only
change if absolutely necessary. For winding applications,
this value is set equal to Initial Adaptation.
Adaptation Rate: effects how fast the RSTC adapts to a
roll’s diameter and inertia. If set too low, the time taken to
adapt will be long and the tension would be slow to come
up to the setpoint. If set too high, the time taken to adapt
will be short and a high frequency tension oscillation could
result. Best recommendation is to use the default value
and only change if absolutely necessary.
Splice Adaptation: is the beginning point for the adaptation
process after the RSTC receives a Splice signal. For
unwinding applications, this value is typically set higher
than Initial Adaptation and gives the adaptation process
a jump-start as the splice process usually involves larger
rather than smaller rolls. The idea is that the adaptation
Remote SP: Select ON to enable tension setpoint
by external analog signal (See INPUT/OUTPUT
DESCRIPTIONS section) or OFF to disable this feature.
When enabled, tension setpoint changes from all other
sources are ignored.
TAPER TENSION
During winding applications, it is often necessary to re-
duce the tension setpoint as the roll increases in diameter
in order to prevent excessive internal roll stresses from
causing roll defects such as starring, telescoping, and
crushed cores. Decreasing the tension setpoint is handled
automatically when a roll diameter sensor or signal is used
to provide the winding roll diameter to the RSTC.
Taper: Taper determines the amount that the tension
setpoint is reduced, in a linear fashion, as the winding roll
diameter increases. Larger values will increase the rate of
tension setpoint decrease while smaller values will reduce
the rate of tension setpoint decrease (Refer to Figures 24
and 25). The tapering of the web tension will continue until
the roll is finished or Minimum Tension Setpoint is reached.
Taper Delay: Taper Delay will prevent a decrease in ten-
sion setpoint from happening until the roll reaches this
diameter.
Taper Enable: Select ON to enable web tension tapering
or OFF to disable this feature.
Use the following formula to calculate Taper for Roll
Diameter > Delay:
Taper = Desired Tension Change * Unit
Beginning Tension Setpoint * (roll dia. - delay)
Unit = 1000 for imperial units [lb & in]
25400 for metric units [N and mm]
Taper
Tension
Constant
Tension
FullCore Delay
Tension
Roll Diameter
Tension
Setpoint
Large Taper
Value
Small Taper
Value
Constant
Tension
FullCore
Roll Diameter
Minimum
Tension
Setpoint
Tension
Tension
Setpoint
Figure 24 Taper Tension
Figure 25 Taper Tension with Delay
Table of contents
Other Nexen Controllers manuals
Popular Controllers manuals by other brands
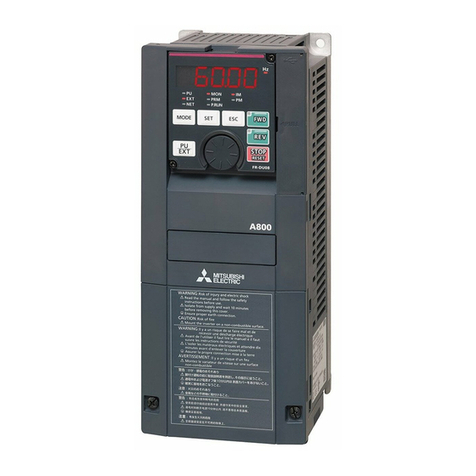
Mitsubishi Electric
Mitsubishi Electric A800 quick start guide
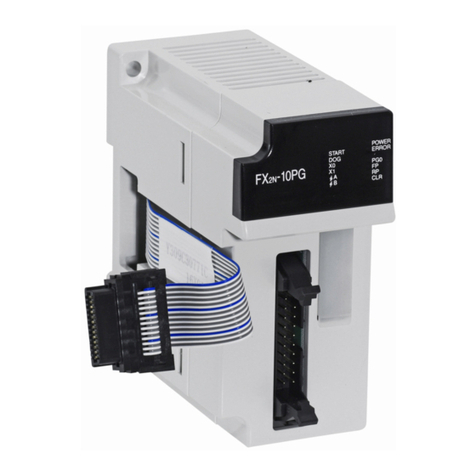
Mitsubishi Electric
Mitsubishi Electric FX2N-10PG user manual

Dantherm
Dantherm 970005 user guide

Pentair
Pentair TRACETEK TTDM-128 installation instructions
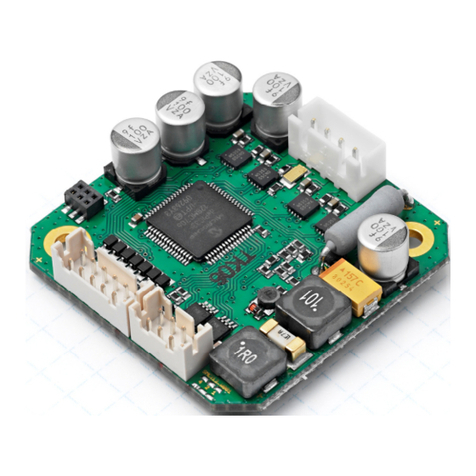
NANOTEC
NANOTEC SMCI12 Technical manual
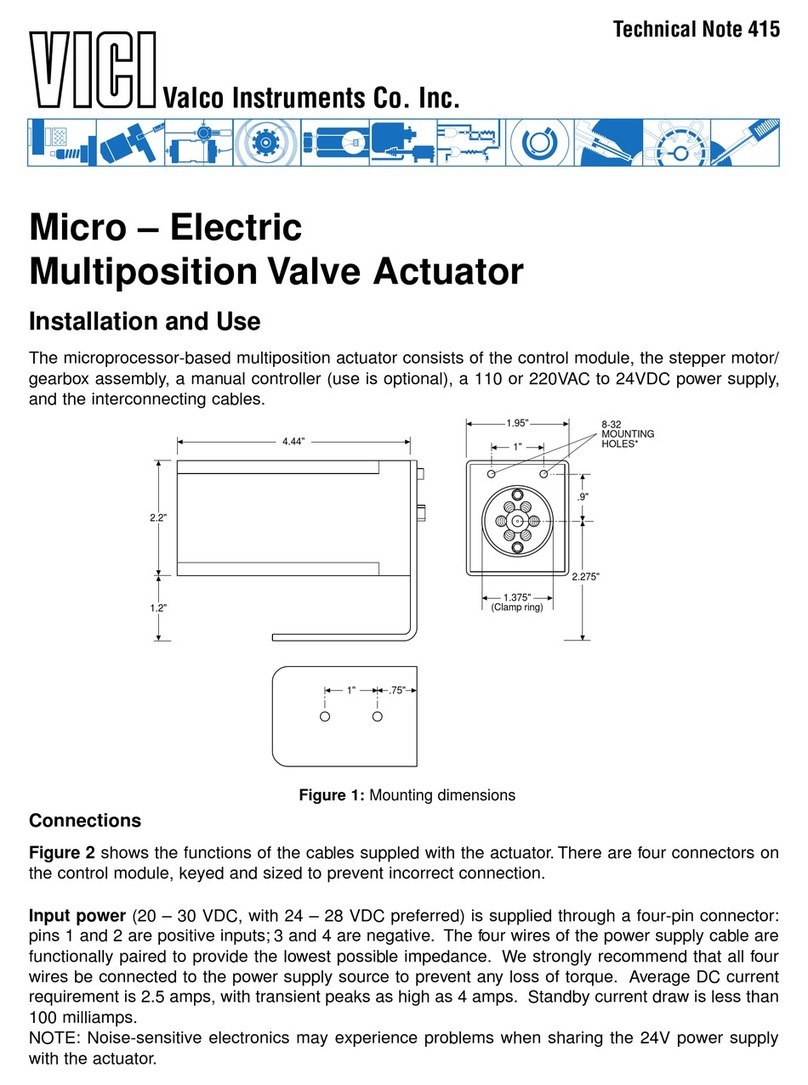
Valco Instruments Co. Inc.
Valco Instruments Co. Inc. VICI EMHCA Installation & use
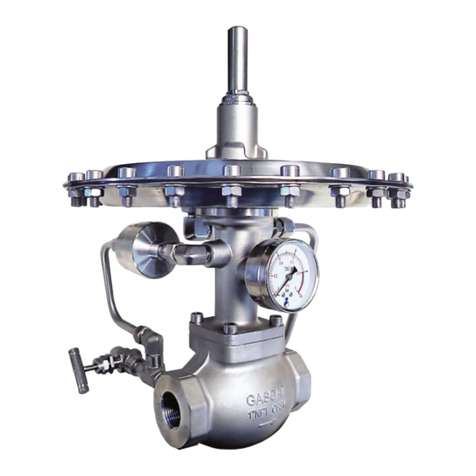
Gascat
Gascat Celtic N Installation, operation & maintenance manual
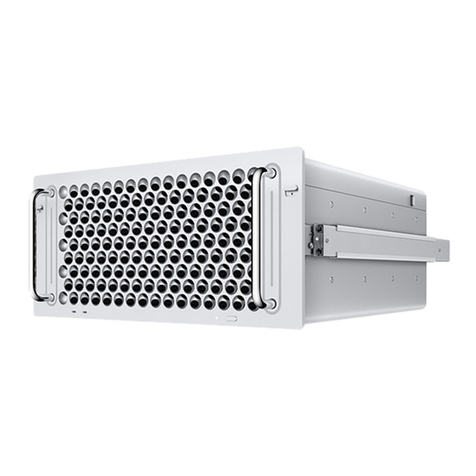
Savant
Savant Super Pro Host v2 SVR-7100S Deployment guide

Dometic
Dometic SC330 Installation and operating manual
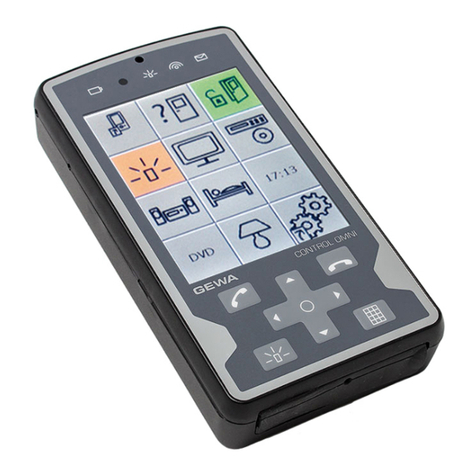
Abilia
Abilia Control Omni Frequently asked questions

IVT-Hirschau
IVT-Hirschau DR-2000 operating instructions

esera automation
esera automation 11320 user guide