Nexen GC300 User manual

1FORM NO. L-20331-J-1107
WEB CONTROL PRODUCTS
User Manual
Web Guide Controller
GC300

2
FORM NO. L-20331-J-1107
In accordance with Nexen’s established policy of constant product improvement, the specifications contained in this
manual are subject to change without notice. Technical data listed in this manual are based on the latest information
available at the time of printing and are also subject to change without notice.
Technical Support: 800-843-7445
(651) 484-5900
www.nexengroup.com
Copyright 2007 Nexen Group, Inc.
Nexen Group, Inc.
560 Oak Grove Parkway
Vadnais Heights, Minnesota 55127
ISO 9001 Certified
Read this manual carefully before installation and operation.
Follow Nexen’s instructions and integrate this unit into your system with care.
This unit should be installed, operated and maintained by qualified personnel ONLY.
Improper installation can damage your system or cause injury or death.
Comply with all applicable codes.
DANGER

3FORM NO. L-20331-J-1107
Table of Contents
INTRODUCTION----------------------------------------------------------------------------------------------------------------4
Edge Position Control-----------------------------------------------------------------------------------------------------4
Center Position Control---------------------------------------------------------------------------------------------------4
INSTALLATION ------------------------------------------------------------------------------------------------------------------5
GC300 Dimensions -------------------------------------------------------------------------------------------------------5
Main Control Board--------------------------------------------------------------------------------------------------------6
ELECTRICAL CONNECTIONS ---------------------------------------------------------------------------------------------7
Wiring Installation Guidelines -------------------------------------------------------------------------------------------7
Sensors-----------------------------------------------------------------------------------------------------------------------8
Remote Offset Pot (Optional) -------------------------------------------------------------------------------------------9
Web Position Signal ----------------------------------------------------------------------------------------------------- 10
Automatic Centering ---------------------------------------------------------------------------------------------------- 10
End-of-Travel Indications ---------------------------------------------------------------------------------------------- 10
Power Supply, Limit Switches, and Actuator ---------------------------------------------------------------------- 11
FRONT PANEL DESCRIPTION------------------------------------------------------------------------------------------- 12
CONFIGURATION------------------------------------------------------------------------------------------------------------ 13
POWER UP, RESET, AND FACTORY RESET ------------------------------------------------------------------------ 14
Power Up------------------------------------------------------------------------------------------------------------------- 14
Reset------------------------------------------------------------------------------------------------------------------------ 14
Factory Reset ------------------------------------------------------------------------------------------------------------- 14
OPERATION MODES ------------------------------------------------------------------------------------------------------- 15
Manual---------------------------------------------------------------------------------------------------------------------- 15
Automatic ------------------------------------------------------------------------------------------------------------------ 15
Automatic Center--------------------------------------------------------------------------------------------------------- 15
Remote Operation ------------------------------------------------------------------------------------------------------- 16
SENSOR CALIBRATION AND ALIGNMENT-------------------------------------------------------------------------- 17
Automatic Sensor Calibration----------------------------------------------------------------------------------------- 17
Sensor Alignment -------------------------------------------------------------------------------------------------------- 19
Manual Adjustment -- Gain -------------------------------------------------------------------------------------------- 19
Manual Adjustment -- Offset ------------------------------------------------------------------------------------------ 20
Remote Offset Control-------------------------------------------------------------------------------------------------- 21
Manual Adjustment -- Deadband ------------------------------------------------------------------------------------ 21
Speed Offset ------------------------------------------------------------------------------------------------------------- 22
INITIAL TEST RUN----------------------------------------------------------------------------------------------------------- 22
TROUBLESHOOTING------------------------------------------------------------------------------------------------------- 23
SPECIFICATIONS ------------------------------------------------------------------------------------------------------------ 24
WARRANTY ------------------------------------------------------------------------------------------------------------------- 25

4
FORM NO. L-20331-J-1107
Nexen’s GC300 Web Guide Controller receives web edge
position signals from position sensors and sends out control
signals to drive an actuator motor to correct the web position.
On opaque webs, the web position signals can be provided
by the PH16, PH21 or AWL280 infrared edge sensors. On
transparent webs and photographic film, the UH21 and UH01
ultrasonic edge sensors are generally used. For line-following
applications, a Second Sensor board is added to the GC300
and an LH100 line or pattern edge-following sensor is used.
NOTE: The Nexen PH, UH, AWL and LH type sensors are
the standard sensors for the GC300. If sensors of other
manufacturers are used, check the sensor specifications for
compatibility with the GC300 or contact Nexen.
EDGE POSITION CONTROL
For Edge Position Control (EPC), a single sensor is mounted
on one side of the web, with its measuring center aligned with
the desired position of the web. The primary purpose for EPC
is to maintain the edge of the web at the measuring center
of the sensor (See Figure 1). When one PH or UH sensor is
the only sensor connected to the GC300, that sensor can be
selected to be either the left or right sensor using the sensor
selection key on the front panel of the unit.
In EPC mode, it is acceptable to connect two different sensors
to the GC300. Each sensor is set up independent of the other
and connected to be either the left or right sensor. In EPC
mode, only one sensor at a time can be used to sense web
position.
CENTER POSITION CONTROL
FIGURE 1
FIGURE 2
FIGURE 3
OFFSET is the fine adjustment of the web edge from the
center-line of the sensor.
DEADBAND is the dead zone of the web position signal. If
the web position error is less than this value, the controller will
ignore the error.
An auto-sensor calibration will calibrate the sensors and
automatically set up the parameters: Gain, Offset, and
Deadband. During operation, the parameters of each sensor
can be manually adjusted and stored in the memory.
When using CPC mode, each sensor should be calibrated
separately.
INTRODUCTION
For Center Position Control (CPC), any two sensors of the
same type (except LH100) can be mounted on opposite
sides of the web and connected to a GC300 equipped with a
Second Sensor board. In this application, the two sensors are
mounted equally spaced from the center-line of the machine
and are used to maintain alignment of the web center-line to
the center-line of the machine (See Figure 2).
NOTE: To determine which sensor is right and which sensor
is left, view the web machine with the web moving away from
the viewer. The sensor on the viewer’s left is the left sensor
and the sensor on the viewer’s right is the right sensor (See
Figure 3).
For each sensor there are three parameters that can be set
automatically or manually. The maximum values of these
parameters are determined by their types:
GAIN is the parameter which determines the proportion of
control output to the sensor error signal.

5FORM NO. L-20331-J-1107
WARNING
An AC power method of disconnect must be wired externally as there is no power
ON/OFF switch on the GC300. Prior to connecting any wires, selecting internal
switch settings or opening the controller cover be sure the AC power is turned off
and locked and proper warning notices are applied according to safety regulations.
NOTE: The GC300 is an electronic component and should be mounted in a shock, vibration, and moisture free area, which has
an ambient temperature greater than 32°F [0°C] and less than 122°F [50°C]. Excessive temperatures will cause the GC300
to stop normal function and give an error signal (See TROUBLESHOOTING).
FIGURE 4a
MOUNTING DIMENSIONS
INSTALLATION

6
FORM NO. L-20331-J-1107
TP1
+5V
TP2
GND
J3
J1
R36 R39
J8
J6
J7 R44 J5
J2
SW2
SW1
RESET
12 3 4 5 6789101112 13 1 2 3 4 5 6 7 8 9 10 11 12
123456789
1234 5
R5
R11
1 2 3 4
SW1
J3
1 Automatic
2 Auto-Center
3 Manual
4 Common
FIGURE 4b
ELECTRICAL CONNECTIONS
Main Control Board
Second
Sensor
Board
Remote
Operator
Board
J8
J7
The Main Control Board is mounted on the inside of the front
cover of the GC300, oriented as shown in Figure 4b.
INSTALLATION -- CONTINued

7FORM NO. L-20331-J-1107
ELECTRICAL CONNECTIONS
WIRING INSTALLATION GUIDELINES
This product is designed to minimize the effects of ElectroMagnetic Interference (EMI) on its operation, but as
with any electronic device, proper installation and wiring methods are necessary to ensure proper operation. By
doing so, the interference from external effects such as electrical line spikes, electrical noise, static electricity, etc.
will be minimized. The following methods outline wiring installation guidelines to protect your system:
• All input and output signal and sensor cables must be
shielded with the shields tied to earth ground at one end.
In case of very high frequency (MHz range) electrical
noise, both ends of the shield need to be tied to earth
ground.
• Keep cable length as short as possible. Think of them as
antennae for noise.
• Use power line filters to suppress interference on the AC
voltage lines that power the unit.
• Place a resistor-capacitor network (snubber) across
inductive coils such as relays and solenoids in order to
stop electrical interference at the source (See Figure 5).
• Isolate signal and sensor cables from cables carrying
AC voltages, power for high current loads or relays and
solenoids. Either relocate the signal and sensor cables
away from other cables or use grounded metal conduits
to shield them. This will reduce the potential for noise
interference between the signal and sensor cables and
the other noisy cables.
Figure 5
For environments that experience high levels of static electricity follow these additional guidelines:
• Remove the static charge from material carrying it. In the
case of webs that carry static charges, there are static
charge removal products available such as static bars and
ionized blowers.
• Ensure that sensors and machine frames are grounded to
earth through a low impedance path.
• Wrap grounding tinsel around sensors and cables that are
close to the source of the static electricity and ground the
tinsel to earth.
• Tie all signal and sensor cable shields directly to earth
ground without passing through the electronic device.
This will help prevent high voltage interference from
coupling into other circuits within the device.
Relay
R
C
Snubber
Snubber applied across relay coil

8
FORM NO. L-20331-J-1107
J8
GC300 Main Control Board
12 3 4 5 6789101112 13
GREEN
RED
BLACK
WHITE
PH SENSOR
SHIELD
COM+12V +-
Sensor
Output
1 2
GREEN
RED
BLACK
WHITE
PH SENSOR
SHIELD
3 4 5 6 7 8 9 10
GC300 Second Sensor Board
COM+12V +-
Sensor
Output
J1
J8
GC300 Main Control Board
12 3 4 5 6789101112 13
BLACK
WHITE
RED
YELLOW
GREEN
UH SENSOR
SHIELD
COM +15V -15V-
+
Sensor
Output
SENSORS
FIGURE 6a
PH SENSOR CONNECTIONS
FIGURE 6b
UH SENSOR CONNECTIONS
WARNING
An AC power disconnect must be wired externally as there is no power ON/OFF
switch on the GC300. Prior to connecting any wires, selecting internal switch
settings or opening the controller cover be sure the AC power is turned off and
locked and proper warning notices are applied according to safety regulations.
1. For Edge Position Control (EPC), only one sensor is
required. Connect this sensor as shown in Figure 6.
2. For systems using two sensors in EPC mode, connect the
“left” sensor to connector J8 on the GC300 Main Control
Board and the “right” sensor to J1 of the Second Sensor
Board (See Figures 7 and 8).
3. For Center Position Control (CPC), two Sensors of
the same type are required. Connect the first Sensor
as described in Step 1 and the second Sensor to the
Second Sensor Board (See Figures 7, 8 and 9).
4. The LH100 Sensor can only be connected to the Second
Sensor Board (See Figure 10).
FIGURE 7 FIGURE 8
FIGURE 9
J8
GC300 Main Control Board
12 3 4 5 6789101112 13 12345678910
GC300 Second Sensor Board
Left Sensor
Output
+-
AS10-D
+-
Right Sensor
Output
10 11 242323
J1
1 2
BLACK
WHITE
RED
YELLOW
GREEN
UH SENSOR
SHIELD
3 4 5 6 7 8 9 10
GC300 Second Sensor Board
COM
+15V -15V-
+
Sensor
Output
J1

9FORM NO. L-20331-J-1107
REMOTE OFFSET POT (OPTIONAL)
1. Connect a customer-supplied, 2000-ohm potentiometer to J8-8 and J8-9 (See Figure 13 and page 16).
FIGURE 10 FIGURE 11
1 2
GREEN
WHITE
RED
BLACK
YELLOW
LH100 Line Following Sensor
SHIELD
3 4 5 6 7 8 9 10
GC300 Second Sensor Board
Com +15V -15V Lock
Alarm
Sig
J1
1 2
+
+
-
-
ACTUATOR LOCK
SIGNAL (LH100 ONLY)
0~10V WEB
POSITION SIGNAL
SHIELD
-15V
+15V
SENSOR
SIGNAL
+12V
POWER COMMON
3 4 5 6
GC300 SECOND SENSOR BOARD
7 8 9 10
J1
J3
Remote Operator Board
12 3 4
** *
*
Customer-Supplied Normally Open (N.O.) contacts
1 - Automatic Positioning Mode
2 - Auto-Centering Mode
3 - Manual Positioning Mode
4 - Common
U14
C24 C21 C22
J8 J7 R44
SHIELD
MAIN CONTROL BOARD
LEFT
RIGHT
COMMON
N.C.
N.O.
COMMON
N.C.
N.O.
COMMON
AUTO
CENTER
LIMIT
SWITCH
AUTO
CENTER
PROX.
SENSOR
LEFT
END
OF
TRAVEL
OUTPUT
RIGHT
END
OF
TRAVEL
OUTPUT
J5
J2
12 3 45678910 1112 13 1 2 3 4 5 6 7 8 910 11 12
REMOTE OFFSET
POTENTIOMETER
SHIELD
0~10VDC
WEB POSITION
OUTPUT SIGNAL
SHIELD
BROWN, +12VDC
BLUE, SIGNAL
+
-
.
* These are for monitoring End-of-Travel
events; DO NOT connect the actuator's End-
of-Travel limit switches to these outputs.
SENSOR CONNECTION
(See ELECTRICAL
CONNECTIONS section.)
J3
Remote Operator Board
12 3 4
** *
*Customer-Supplied Normally Open (N.O.) contacts
1 - Automatic Positioning Mode
2 - Auto-Centering Mode
3 - Manual Positioning Mode
4 - Common
+24V
GND
Customer-supplied
+24VDC Power Supply
FIGURE 13
FIGURE 12b
FIGURE 12a
(Wiring diagram for Remote Operator
Board 16662, rev. C and later)
(Wiring diagram for Remote Operator
Board 16662, rev. A or B)

10
FORM NO. L-20331-J-1107
WEB POSITION SIGNAL
The Web Position Signal is the actual signal from the web
edge sensor that has been converted to a 0~10V range.
This signal, available at J8-11 and J8-12 on the Main Control
Board (See Figure 13), can be used to remotely display the
web edge position or for a statistical process control (SPC)
application. On two-sensor systems, the Web Position Signal
for the second sensor is available at J1-8 and J1-9 on the
Second Sensor Board (See Figure 11).
NOTE: Because different sensors have different output levels,
the Web Position Signal may need to be adjusted to achieve
a true 0 - 10 VDC span.
One-sensor system: Monitor the voltage at connector J8
(See Figure 13), pin 11 (+) and pin 12 (-) on the Main Control
Board (See Figure 4b). First, with the sensor unblocked adjust
potentiometer R39 (See Figure 4b) on the Main Control Board
until the voltage measures 10 VDC. Next, block the sensor
and adjust R36 on the Main Control Board until the voltage
measures 0 VDC. Recheck the voltage by unblocking and
blocking the sensor and repeat the procedure if necessary.
Two-sensor system: Perform the steps for a One Sensor
system, then perform the following. Monitor the voltage at
connector J1 (See Figure 11), pin 8 (+) and pin 9 (-) on the
Second Sensor Board (See Figure 4b). First, with the second
sensor unblocked, adjust potentiometer R5 (See Figure 4b)
on the Second Sensor Board until the voltage measures 10
VDC. Next, block the sensor and adjust R11 on the Second
Sensor Board until the voltage measures 0 VDC. Recheck the
voltage by unblocking and blocking the sensor and repeat the
procedure if necessary.
AUTOMATIC CENTERING
NOTE: There are two methods for Automatic Centering
sensing: proximity sensor or limit switches. Examine the
web guide to determine which type of Automatic Centering
sensing is used. If both types of Automatic Centering
methods are connected, only the Automatic Centering limit
switches will be engaged.
1. Terminal J7-3 is Common for both Left and Right Limit
switches (See Figure 13).
2. Terminal J7-1 is the Left Limit switch for left of center
(See Figure 13).
3. Terminal J7-2 is the Right Limit switch for right of center
(See Figure 13).
4. Terminal J7-4 is the +12 VDC supply voltage for the
proximity sensor (See Figure 13).
5. Terminal J7-5 is the signal from the proximity sensor (See
Figure 13).
END-OF-TRAVEL INDICATIONS
NOTE: The GC300 provides both local and remote indications
of web guide end-of-travel situations. Two SPDT (single-pole,
double-throw) outputs are available to switch small DC loads
(see Specifications section for ratings) for remote indications.
The Bar Graph indicators on the front panel (See Figure 15)
will blink providing a local indication.
NOTE: If the web guide reaches the left end-of-travel, then the
contact at J7-7 is CLOSED and the contact at J7-6 is OPEN,
with J7-8 being the common for both (See Figure 13).
NOTE: If the web guide reaches the right end-of-travel, then
the contact at J7-10 is CLOSED and the contact at J7-9 is
OPEN, with J7-11 being the common for both (See Figure
13).
1. Terminals J2-1 and J2-2 provide the power to drive the
Linear Actuator (See Figure 14).
2. Connect the web guide end-of-travel limit switches as
shown in Figure 14.

11 FORM NO. L-20331-J-1107
FIGURE 14
3. Make AC Power connections at Terminals J3-1, J3-2, and J3-3 (See Note above and Figure 14).
POWER SUPPLY, LIMIT SWITCHES, AND ACTUATOR
NOTE: If the web guide does not have end of travel limit switches for its actuator, connect the following terminals together:
J2-3 to J2-4 and J2-5 to J2-6 in order for the GC300 to operate normally (See Figure 14).
1. Terminals J2-1 and J2-2 provide the power to drive the Linear Actuator (See Figure 14).
2. Connect the web guide end-of travel limit switches as shown in Figure 14.
NOTE: Do not connect the AC supply voltage until you have verified that the supply voltage is the same as listed on the Voltage
Specification decal (See Figure 14) located inside the GC300 enclosure.
For the 120 VAC model, connect J3-1 to the line conductor, J3-2 to the neutral conductor, and J3-3 to the earth ground
conductor.
For the 240 VAC model, connect J3-1 to L1, J3-2 to L2, and J3-3 to the earth ground conductor.
HS1
J2
J4 J3
1234567
SHIELD
RIGHT
LIMIT
POWER SUPPLY
BOARD
Use Normally Closed (N.C.)
Limit Switches.
LEFT
LIMIT
Actuator
Power Output
+
-
123
Earth
Ground
+
-
VAC Supply
Input
Voltage Specification Decal
Actuator End of
Travel Inputs
L1 L2 GND

12
FORM NO. L-20331-J-1107
BAR GRAPH INDICATORS
These indicators display web position error, indicate faults,
and display the values for Gain, Offset, and Deadband during
setup. During operation, the Red indicators represent web
position error and the center Green indicator represents web
at center, no error.
SETUP INDICATORS
During normal operation, all three indicators should be off. If
one of them is lit, it indicates that this value is being set, and
the Bar Graph indicator shows its value. During Auto Sensor
calibration all three indicators will be lit at the same time.
SENSOR INDICATORS
These three indicators stand for Left Sensor, Right Sensor,
and Line Follower Sensor. When any of these indicators is lit,
it indicates this sensor’s position signal is being used as input.
The GC300 is in EPC mode when only one indicator is lit and
is in CPC mode when both the left and right sensor indicators
are lit at the same time.
OPERATION MODE INDICATORS
These three indicators stand for Automatic, Auto Center, and
Manual. When any one of these indicators is lit, it indicates
that this operation mode is selected. The default mode after
power up is Manual. Only one of these indicators should be lit
at any time.
SETUP KEY
The Setup Key has three functions during Automatic and
Manual Mode:
Press and release this button the first time and the Gain
indicator lights up. When it is pressed and released the
second time the Offset indicator lights up. When it is pressed
and released the third time the Deadband indicator lights up,
and when it is pressed and released the fourth time, all three
indicators go off.
When the Setup and Sensor keys are pressed at the same
time, the unit enters the Auto Sensor Calibration mode (See
SENSOR CALIBRATION AND ALIGNMENT ).
When the Setup key and the Reset push-button (located on
the circuit board) (See Figure 4b) are pressed at the same
time, the unit calls for a Factory Reset .
SENSOR KEY
Repeatedly pressing this key enables the user to select the
right or left sensor or line-follower sensor (if present).
OPERATION MODE KEYS
When each of these keys is pressed, its respective indicator
will light, indicating the operating mode. Only one indicator
will be lit for each button pushed. When any of the Setup
indicators are lit, the unit will not respond to these keys.
–, ENTER, + KEYS
The + and - keys are used to change the setup values. After
changing the setup values, press the Enter key to store the
new values into memory.
Also, the + and - keys are also used to move the web right or
left while in Manual Mode.
FIGURE 15
Bar Graph
Operation Mode Indicators
Automatic
Auto Center
Manual
Sensor Indicators
Left
Right
Line Following
Setup Indicators
Gain
Offset
Deadband
Setup key
Value Setting
keys
+
Enter
-
Operation Mode Keys
Manual
Auto Center
Automatic
Sensor key
FRONT PANEL DESCRIPTION

13 FORM NO. L-20331-J-1107
FIGURE 16
NOTE: The GC300 checks DIP switch settings only during power up. If any DIP Switch settings are changed, the GC300 must
go through a power-up cycle in order to recognize the changes.
1. SW2-1 and SW2-2 indicates the Sensor Type connected at Terminal J8 (See Figure 16).
2. SW2-3 is not used and should be set to OFF.
3. SW2-4 is a Lock-Out for the Setup Key and the Sensor Key; when, it is set to ON these two keys are enabled. If it is set to
OFF the Setup Key and the Sensor Key will not respond when pressed (See Figure 16).
4. SW1-1, -2, -3 determine the sensor type connected to J1 on the Second Sensor Board (See Figure 16).
5. SW1-4 enables and disables the LH100 Actuator Lock Function. ON = enable / OFF = disable
6. SW1-5 adjusts gain range of Second Sensor Board. ON = for LH100 / OFF = for all other sensor types.
NOTE: For EPC (single-sensor systems): the sensor is connected to J8 on the Main Control Board (refer to the Electrical
Connections section), and SW2 is used to select the sensor type (See Figure 16).
For CPC (dual-sensor systems): the left sensor is connected to J8 on the Main Control Board (refer to the Electrical Connections
section), SW2 is used to select the left sensor type (See Figure 16), the right sensor is connected to J1 on the Second Sensor
Board (refer to the Electrical Connections section), and SW1 is used to select the right sensor type (See Figure 16). The same
sensor types must be selected with SW1 and SW2 in order to use CPC mode.
For line-following applications: the LH100 must be connected to J1 on the Second Sensor Board (refer to the Electrical
Connections section), and SW1 is used to select the sensor type (See Figure 16).
Mixed sensor type applications (e.g., PH16 and UH21, or PH21 and LH100) are allowed and follow the same rules as in the
CPC application described earlier. However, the GC300 will not allow the user to select CPC mode when two different sensors
are selected with SW1 and SW2. The user can select only left sensor, right sensor, or line-follower mode.
Changes made to DIP Switches SW1 and SW2 are recognized by the GC300 only during power up or after pressing RESET
(See Figure 18) with the exception of SW1-4 & SW1-5 which are recognized immediately.
CONFIGURATION
PH16
ON OFF
1234
UH21
PH16
ON
OFF
AS10/
AWL280
UH21 LH100
ON
OFF
SW2 - Main Control
SW1 - Second Sensor
ON OFF
12354
1234 5
12354 12354
ON
OFF
1234
1234
ON OFF
ON OFF
AS10/
AWL280
PH21
PH21
UH01
1234 5
UH01
1234
ON OFF

14
FORM NO. L-20331-J-1107
C20
SW1
Reset
C20
SW1
Reset
FIGURE 17
FIGURE 18
FIGURE 20
FIGURE 19
POWER UP, RESET AND FACTORY RESET
Reset
Push-button
POWER UP
NOTE: Prior to power up, check all electrical connections,
making sure that the AC power supply is properly
connected.
At power up, all the indicators on the Control Panel will flash
on and off once; then, the GC300 will enter the Auto, Auto-
Center, or Manual Mode that it was in prior to the previous
shutdown. The GC300 will automatically reload the last
settings made to sensor selection, gain, offset, and deadband
(See Figure 17).
NOTE: If all the indicators continue flashing on and off after
power up, there may be a wiring problem with the actuator’s
motor (Refer to TROUBLESHOOTING).
If a sensor has been changed during the power down period, a
factory reset should be performed after power up.
RESET
Reset will reload the Gain, Offset, and Deadband values
stored in memory for each sensor.
Press the Reset Push-button (located on the Main Circuit
Board) and then release it. All the indicators will flash ON and
OFF once (See Figures 17 and 18).
Factory Reset will reload the factory default Gain, Offset, and
Deadband values for each sensor into memory. After a Factory
Reset, the default values will be used until they are changed
either manually or by an automatic sensor calibration.
NOTE: Factory Reset can be entered two ways: by either
holding the Setup Key during power up, or by holding the
Setup Key during Reset. When using the latter method,
press and hold the Setup Key first; then, press and release
the Reset Push-button. After the indicators flash, release
the Setup Key (See Figures 19 and 20).
NOTE: Whenever a Factory Reset is performed, the sensors
will have to be calibrated.
FACTORY RESET

15 FORM NO. L-20331-J-1107
FIGURE 21
FIGURE 22
FIGURE 23
AUTOMATIC
Press the Automatic Key (Figure 22) to place the GC300 in
Automatic Mode.
This is the normal operating mode for the GC300. While in
Automatic Mode, the GC300 senses the web position signal
from the sensors. The edge of the web must be in the center
of the sensor zone. If the web moves off center, the GC300
will issue a corrective signal to the linear actuator, which will
move the roll stand or guide roll mechanism to bring the web
back to center.
The Bar Graph indicators on the front panel show the position
of the web edge within the sensor. If the Bar Graph indicators
flash rapidly from side to side, the system is overcorrecting
or hunting. This can be corrected by decreasing the Gain
setting. A slow variation from side to side indicates the system
is not reacting quickly enough and is corrected by increasing
the Gain setting.
MANUAL
AUTOMATIC CENTER
Press the Auto Center Key (Figure 23) to place the GC300 in
Automatic Centering Mode.
The Automatic Centering Mode is used to lock up the position
of the roll stand or guide roll mechanism while threading a
new web into the machine or at any time Automatic or Manual
control is not desired. Automatic centering can be controlled
with either a Proximity Sensor or Limit Switches.
In this mode the GC300 will direct the web guide or roll
stand’s Linear Actuator to maintain the web guide or roll stand
in its center or neutral position as determined by the Automatic
Centering Sensor or Switches. This position will be maintained
without regard for the actual web’s position.
OPERATION MODES
NOTE: After power-up, the GC400 will restore the operating
mode it was in prior to shutting down.
Press the Manual Key (Figure 21) to place the GC300 in
Manual Mode.
In Manual Mode, the Bar Graph indicators show the web
position within the Sensor. Pressing the + or - key will move
the web in the same direction as the key that is pressed.
In Manual Mode, the GC300 takes no action to correct for
web position errors; however, this mode is useful to verify that
the motor wiring is correct.
Manual Mode is used for running a roll of irregular width
material through the machine. In Automatic Mode, the
controller may be constantly correcting and still be unable to
keep up unless machine speed is drastically reduced.
Manual Mode can also be used for process alignment.

16
FORM NO. L-20331-J-1107
The speed at which the actuator moves the web guide during Automatic Centering can be decreased to prevent any hunting around
the guide’s center position. This is accomplished by placing the GC300 in Automatic Centering mode and then pressing the Setup
key. Next, press the Plus (+) key to increase the actuator speed or press the minus (-) key to decrease the actuator speed. When
satisfied with the actuator speed, press the Enter key to save the setting.
NOTE: Actuator speed settings for Automatic Centering do not affect the actuator speed for web guiding in Automatic
mode.
REMOTE OPERATION
A GC300 equipped with a Remote Operator board enables
the AUTOMATIC, AUTO-CENTER, and MANUAL modes to be
selected externally.
The GC300 operation mode can be changed by closing
customer-supplied, normally-open, dry contacts. The wiring
required depends on the revision level printed on the Remote
Operator Board.
For 16662, rev. A or B:
Select operation modes remotely by momentarily closing a
contact connecting the appropriate terminal (J3-1, -2 or -3) to
COMMON (J3-4). (Refer to figures 12a and 24.)
For 16662, rev. C or later:
Select operation modes by connecting the (+) side of
a customer-supplied 24VDC power supply to J3-4 and
momentarily closing a contact connecting the appropriate
terminal (J3-1, -2 or -3) to the GND (—) side of the power
supply. (Refer to figures 12b and 24).
NOTE: Keeping the contact closed would LOCK the GC300
in the selected operation mode. The GC300 will enter that
mode after powering up, and you will not be able to change
the operation mode using the front panel Operation Mode
keys.
FIGURE 24 - Remote Operator Board
The GC300 will issue an output signal to the Linear Actuator to maintain the Automatic Centering Switch in its center or null
position at all times while in the Automatic Centering Mode.
NOTE: Refer to your Nexen web guide manual to determine if adjustment is necessary for the Auto Centering Limit Switches
or Proximity Sensor.
J3
1
2
3
4
Automatic
Auto-Center
Manual
Common

17 FORM NO. L-20331-J-1107
FIGURE 25
AUTO CALIBRATION —LEFT SENSOR
FIGURE 26
NOTE: If the SETUP Key is pressed instead of the ENTER Key,
the GC300 will exit the Calibration mode and return to the
Normal Operation mode without calculating Gain, Deadband,
or zeroing the Offset (See Figure 25).
Left Right
Line-Following
SENSOR CALIBRATION AND ALIGNMENT
AUTOMATIC SENSOR CALIBRATION
Edge Guide Sensors:
NOTE: Before performing Automatic Sensor Calibration,
verify that only the Sensor selection indicator of the sensor
being calibrated is lit (See Figure 25).
NOTE: When performing Auto-Sensor Calibration, always
press and hold the SETUP key first; then, press and hold
the SENSOR key; then, release both Keys at the same time
(See Figure 25).
Use the following steps for all Sensors except LH100:
1. Press and release the SENSOR key until the indicator for
the first sensor to be calibrated is lit.
2. Press and hold the SETUP Key; then, press and hold the
SENSOR Key (See Figure 25).
3. Simultaneously release both the SETUP Key and the
SENSOR Key. The three Setup indicators will light and
one Sensor indicator will light, indicating that the Sensor
is being calibrated (See Figure 25).
4. Insert the web which the GC300 will guide to block the
light path to the sensor; then, completely remove the web
(See Figure 26).
5. Press the ENTER Key to save the sensor calibration and
cause the GC300 to set the Gain at the minimum value,
Offset at 0, and Deadband at an optimum value (See
Figure 25).
6. If using two sensors, select the second sensor with the
SENSOR Key and repeat steps 1 through 4.
NOTE: After the sensors are calibrated, the Gain may be too
low to move the web guide or actuator at the desired speed.
(See Manual Adjustment - Gain).

18
FORM NO. L-20331-J-1107
AuTOMATIC SeNSOR CALIBRATION -
CONTINued
LH100 Line Following Sensor Only:
NOTE: Before proceeding with LH100 calibration into
the system, familiarize yourself with the LH100 sensor
and determine the appropriate positions for LH100
selector switches by reading the manual (20334).
1. Select the LH100 Sensor by repeatedly pressing the
GC300 Sensor Key until the Line-Following Sensor
indicator is illuminated (See Figure 27A).
2. Set the LH100’s Field-of-View Selector Switch to “10” as
shown in Figure 27B.
3. Move the LH100 slowly in the direction of the arrow
shown in Figure 27C until the web or line edge has fully
passed through the LH100’s field-of-view.
FIGURE 27
5a
5b
Sensors: Left Right Line-Following
A
B
C
Arrow
Focal
Display Indicator Center
Display Indicator
Field-of-View
Selector
Switch
Color
Selector
Switch
Contrast
Selector
Switch
Cable
Connector
4. Position the LH100 with its field-of-view right next to
the target edge, so that when the LH100 moves in the
direction of the arrow, the target edge will enter its field-
of-view (make sure the Focal Display Indicator and Center
Display Indicator lights are off at this point).
5. Press and hold the GC300’s SETUP key; then, press and
hold the SENSOR key. Release both keys at the same
time. This will cause the three Setup indicators to turn on,
and the selected Sensor indicator will blink, indicating that
the LH100 is ready to calibrate.
6. Move the LH100 slowly in the direction of the arrow
until the web or line edge has fully passed through the
LH100’s field-of-view.
7. Press the ENTER Key to complete the calibration
process.
NOTE: Changing the Field-of-View Selector Switch setting
does not require a re-calibration, but may require a Gain
adjustment.
NOTE: If the SETUP Key is pressed instead of the ENTER
Key, the GC300 will exit the Calibration mode and return to
the Normal Operation mode without zeroing the Offset or
calculating Gain or Deadband (See Figure 25).
• The Focal Display Indicator will turn on when the
target edge enters the LH100 field-of-view.
• The Center Display Indicator will turn on when the
target edge is centered within the field-of-view. This
indicator will turn off when the target edge is no
longer centered.
• The Focal Display Indicator will turn off as the target
edge leaves the field of view.

19 FORM NO. L-20331-J-1107
FIGURE 29
FIGURE 28
FIGURE 30
Gain indicator
SENSOR ALIGNMENT
NOTE: The performance of the GC300 is influenced by the
Sensor input. Locate the Sensor at an appropriate position
prior to any adjustments or operation.
1. Install the Sensor according to the Installation Instructions
provided.
2. Thread the web through the web machine (See Figure
28).
3. Power up the GC300; then, set the GC300 to Auto
Centering Mode (See Figure 29), or manually move the
web guide mechanism to the center position.
4. After the web guide moves to the center position, switch
the GC300 to Manual Mode and align the web to the
desired location inside the Sensor; then, if necessary,
apply tension to the web (See Figure 28).
5. Select Right or Left Sensor on the GC300 Control Panel
(See Figure 29).
6. Move the Sensor on its mounting bracket until the Red
Bar Graph indicators are OFF and only the Green
indicator is ON (See Figures 28 and 29). The Sensor
is now aligned with the center of the Sensor’s detection
window.
7. If CPC Mode is required for the GC300, press the
SENSOR Key to select the second Sensor and repeat
steps 1 through 6.
MANUAL ADJUSTMENT — GAIN
NOTE: GC300 Gain is preset during the Automatic Calibration
procedure and may require adjusting afterwards for optimum
controller performance. For two-sensor systems operating in
EPC mode, each sensor can have a different Gain and that
value is used whenever that sensor is selected. For two-
sensor systems operating in CPC mode, the Gain of the Left
sensor is the only value used. Gain can be adjusted manually
while operating in either Automatic or Manual mode.
1. Repeatedly press the SENSOR Key until the indicator of
the sensor, whose gain is to be adjusted, is lit (See Figure
30).
2. Press the SETUP Key once; the indicator for Gain will
light up (See Figure 30).
3. The number of red indicators on the Bar Graph that are lit
indicate the current value of gain for the sensor selected,
compared with its maximum value. If half the indicators
are lit, the gain is at half of the maximum value (See Figure
30).

20
FORM NO. L-20331-J-1107
NOTE: Press and release the - or + key to incrementally
change the value setting. Press and hold the - or + key for
more than one second to ramp the value setting up or down
(See Figure 30).
4. Press the -or + key to increase or decrease the value
setting. The green indicator in the middle of the Bar
Graph should flash while the +or -key is pressed (See
Figure 30).
5. After reaching the desired value, press the ENTER Key to
store the value into memory, the Gain indicator will turn
off, and the GC300 will now return to normal operation
mode (See Figure 30).
NOTE: If SETUP is pressed instead of the ENTER Key, after
the Gain is changed, no change is stored in the GC300
memory and the GC300 will return to Normal Operation
mode (See Figure 30).
NOTE: The Gain setting is unique to each web machine, the
operator must observe the performance of the web guide
after changing the Gain setting. If Gain is too low, it may not
react fast enough to correct the error position: If Gain is set
too high, it may cause overshooting which can be seen as
the Bar Graph indicator’s hunting around the center green
indicator.
MANUAL ADJUSTMENT — OFFSET
KeypAd CONTROL
NOTE: The Offset adjustment enables the user to fine tune
the web position without having to move the web sensor.
GC300 Offset is preset during the Automatic Calibration
procedure and may require adjustment afterwards for
optimum web positioning. For two-sensor systems operating
in EPC mode, each sensor can have a different Offset and
that value is used whenever that sensor is selected. For two-
sensor systems operating in CPC mode, the Offset of the
Left sensor is the only value used. Offset can be adjusted
manually in either Automatic or Manual mode.
1. Repeatedly press the SETUP Key until the indicator for
Offset lights up (See Figure 31). The Bar Graph indicator
shows the percent of offset that is used up in each
direction. The amount of offset available depends on the
sensor type (See Figure 31).
2. Press the + or - key to move the web edge position to the
right or left. When the + or - keys are pressed, the Green
indicator will keep flashing and the Red indicators will
show the Offset distance (See Figure 31).
3. The web movement is updated to the Offset as the
changes are made in Auto mode.
4. If the Offset exceeds the maximum value allowed by
the GC300 while in Setup, the Bar Graph indicators
will rotate on the side of the Offset error (See
TROUBLESHOOTING).
5. Press ENTER (Figure 32) to save any changes, or press
SETUP (Figure 31) to exit without saving the changes.
FIGURE 31
FIGURE 32
Offset indicator
Other manuals for GC300
1
Table of contents
Other Nexen Controllers manuals
Popular Controllers manuals by other brands
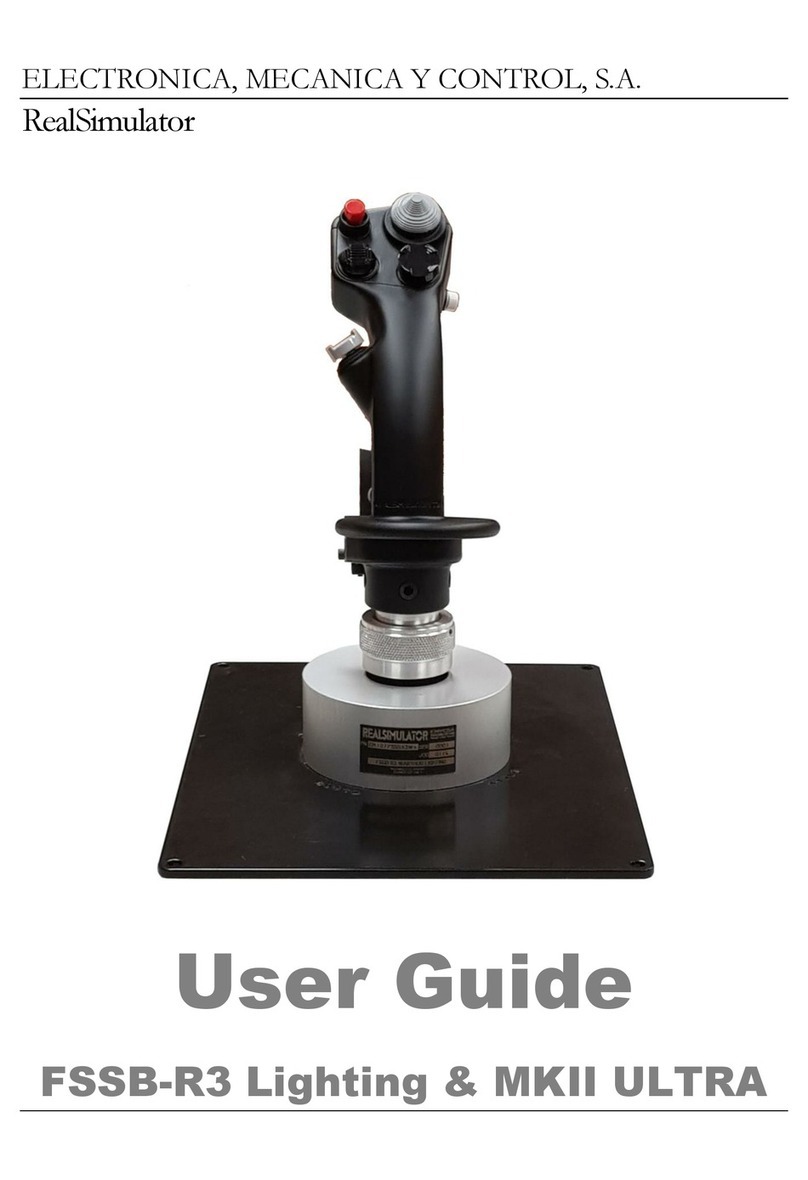
RealSimulator
RealSimulator FSSB-R3 Lighting user guide
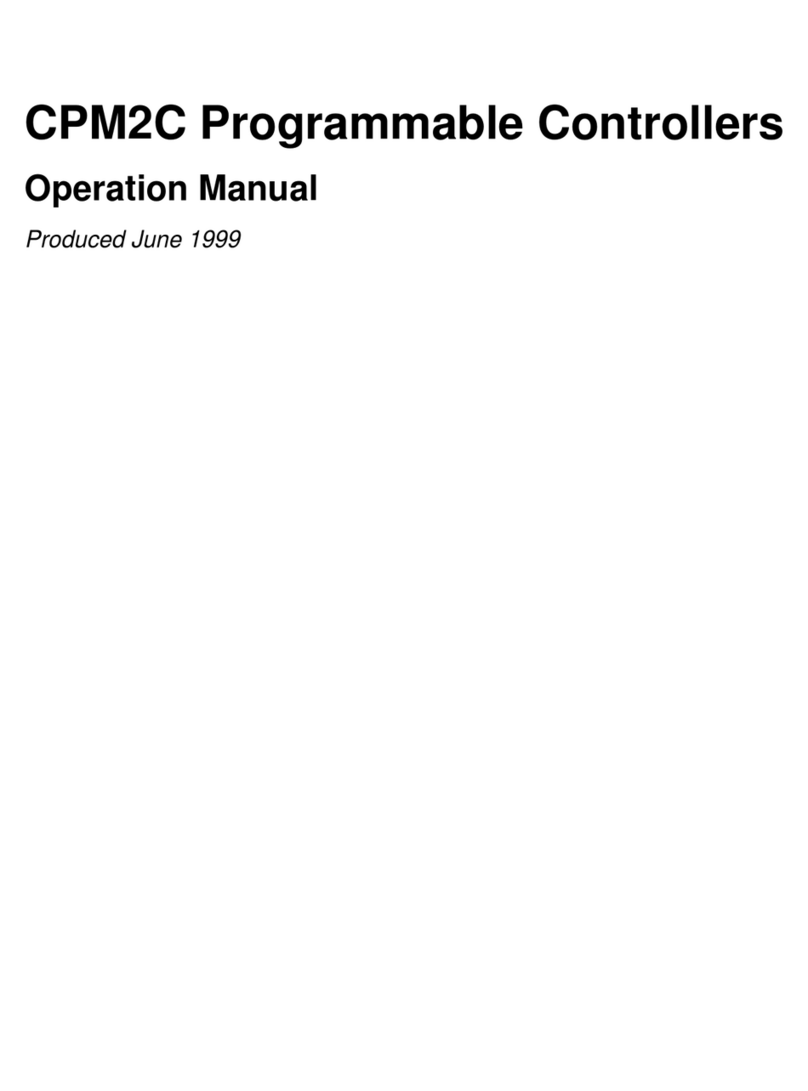
Omron
Omron CPM2C Operation manual
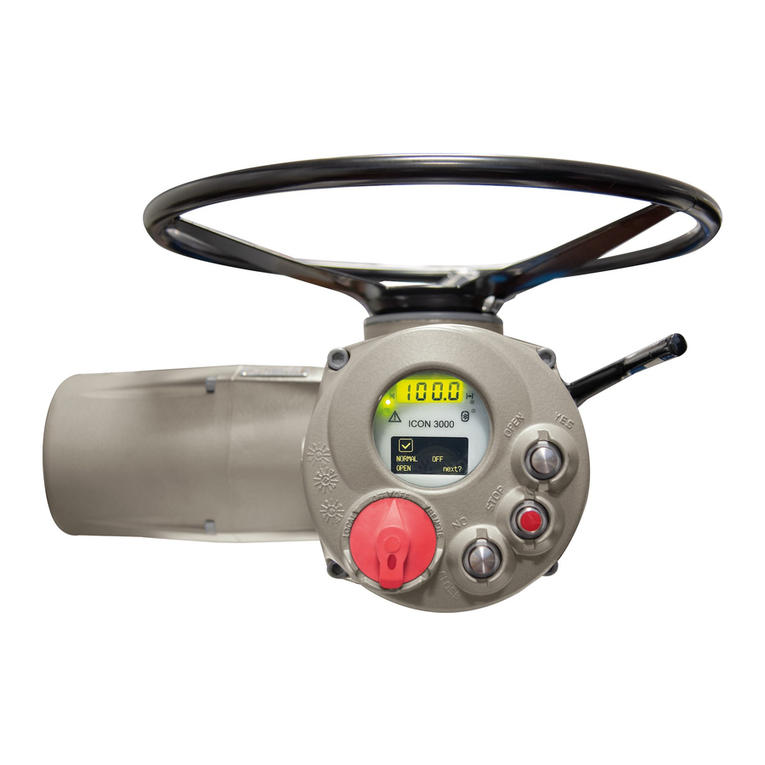
BIFFI
BIFFI ICON3000 Series Installation, operation and maintenance manual

Weathermatic
Weathermatic PROLINE PL800 owner's manual
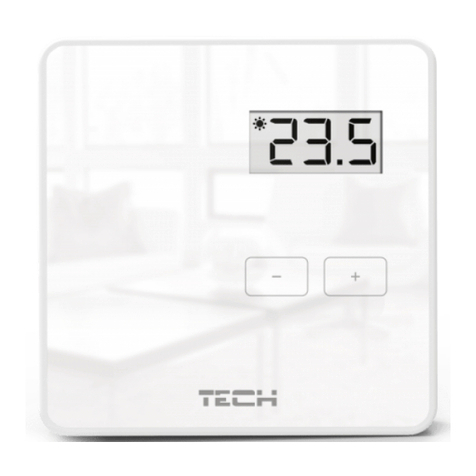
Tech Controllers
Tech Controllers EU-R-8bw user manual

Siemens
Siemens RMU7*B series operating instructions