Nextron MASTERTRACE MS-2101 User manual

MASTERTRACE MS-2101
OPERATOR’S MANUAL
HEAT TRACING CONTROL

MS-2101 Contents
1 Product Overview ......................................................................................................... 1.1
Introduction .............................................................................................................................................. 1.1
Specifications ........................................................................................................................................... 1.2
Summary of Features .............................................................................................................................. 1.3
Use of this Manual ................................................................................................................................... 1.3
Conventions ............................................................................................................................................. 1.3
Shipping Content ...................................................................................................................................... 1.3
Theory of Operation ................................................................................................................................. 1.4
2 Installation .................................................................................................................... 2.1
Unpacking the Controller .......................................................................................................................... 2.1
Control Module ......................................................................................................................................... 2.1
Mounting the Controller ............................................................................................................................ 2.3
Wire Sizing ............................................................................................................................................... 2.3
Conduit and Cabling ................................................................................................................................. 2.3
Power Wiring ........................................................................................................................................... 2.3
Heater Wiring ........................................................................................................................................... 2.3
Ground Connection .................................................................................................................................. 2.3
RTD Sensor Wiring .................................................................................................................................. 2.3
Communication Wiring ............................................................................................................................. 2.4
Alarm Wiring ............................................................................................................................................ 2.4
3 Getting Started.............................................................................................................. 3.1
Introduction .............................................................................................................................................. 3.1
Enabling the Heater ................................................................................................................................. 3.1
Entering Setpoints .................................................................................................................................... 3.1
Testing Heater & Alarms ........................................................................................................................... 3.3
Monitoring System Status ......................................................................................................................... 3.4
4 Front Panel Operation.................................................................................................. 4.1
Overview .................................................................................................................................................. 4.1
Operating the Keypad .............................................................................................................................. 4.1
Status Lights............................................................................................................................................. 4.1
Alphanumeric Display .............................................................................................................................. 4.1
Keypad ..................................................................................................................................................... 4.1
Display Contrast ....................................................................................................................................... 4.1
Heater Numbering .................................................................................................................................... 4.1
Startup Messages .................................................................................................................................... 4.3
Status Messages ...................................................................................................................................... 4.3
Flash Messsages ..................................................................................................................................... 4.4
5 Measured Values .......................................................................................................... 5.1
Overview .................................................................................................................................................. 5.1
Operating ................................................................................................................................................. 5.2
Statistics ................................................................................................................................................... 5.3
6 Setpoint Values............................................................................................................. 6.1
Overview .................................................................................................................................................. 6.1
Setpoints Entering .................................................................................................................................... 6.2
Setpoint Access Security .......................................................................................................................... 6.2
Operating ................................................................................................................................................. 6.2
Heater Setup ............................................................................................................................................ 6.5
System Setup ........................................................................................................................................... 6.8
Setpoint Tests......................................................................................................................................... 6.11

ContentsMS-2101
7 Alarms ........................................................................................................................... 7.1
Overview .................................................................................................................................................. 7.1
Trip or Failure Alarms ............................................................................................................................... 7.1
Process Alarms ........................................................................................................................................ 7.2
Warning Alarms ........................................................................................................................................ 7.3
Reset Alarms............................................................................................................................................ 7.3
8 Communications .......................................................................................................... 8.1
Overview .................................................................................................................................................. 8.1
Physical Layer .......................................................................................................................................... 8.1
Modbus Protocol ...................................................................................................................................... 8.2
Modbus Memory Map .............................................................................................................................. 8.4
Modbus Map Data Format ....................................................................................................................... 8.6
9 Commissioning ............................................................................................................ 9.1
Overview .................................................................................................................................................. 9.1
Requirements ........................................................................................................................................... 9.1
RTD Input Test ......................................................................................................................................... 9.1
Heater Voltage and Current Test .............................................................................................................. 9.2
Ground Fault Current Test ........................................................................................................................ 9.3
Alarm Output Test .................................................................................................................................... 9.3
Override Input Test ................................................................................................................................... 9.4
Placing the Controller in Service .............................................................................................................. 9.4
Completing the Installation ....................................................................................................................... 9.6
Warranty .............................................................................................................Back Cover

1.1
MS-2101 Chapter 1 Product Overview
Introduction
The MS-2101 single-point heat tracing controller uses a
microprocessor and is intended for stand-alone heat trace
applications. It can be for use with mineral-insulated, self-
regulating or constant-wattage cable for freeze protection,
process control and instrument tracing. The MS-2101 is
intended for indoor or outdoor installations in ordinary or
hazardous locations.
MS-2101 offers many advantages over other heat tracing
control schemes, which generally use some combination
of mechanical thermostats, custom-built panels or pro-
grammable controls to provide control, monitoring and
alarm functions. Budgetary constraints usually limit the
degree of system fault monitoring to less than optimal
levels. This results in periodic costly process shutdowns
due to process or hardware malfunctions. Equipment
reliability concerns often force plant procedures to
include annual thermostat performance checks to ensure
that the device is still operating as intended. This can be
a tedious, labour intensive job.
A controller is mounted near the pipe being traced to
monitor the heater point. This controller can communi-
cate with a single master unit to give complete system
monitoring and control from a convenient location. Up to
32 controllers can be monitored on a RS485 data highway
to a centrally located master. By connecting controls to a
data highway, the MS-2101 can immediately flag alarms
caused by heat tracing malfunctions, altered setpoints and
monitor actual values from a central location. Each local
control is completely independent and will continue to
function if the master fails or if the communication link
fails. This ensures maximum reliability and minimizes
vulnerability in the event of a hardware failure. Addi-
tional points can easily be added at any time as easily as a
mechanical thermostat can be installed. Unlike control
schemes using programmable controllers, no software
development is required. The complete system is opera-
tional as soon as it is installed.
Figure 1.1 Typical MS-2101 Installation

1.2
MS-2101 Chapter 1 Product Overview
Specifications
Temperature Input
Range: -50 to +500°C (-58 to 932°F)
Accuracy: ±2°C
Repeatability: ±1°C
RTD: Two, 100 ohm platinum, 3-wire RTD
20 ohms maximum lead resistance
Heater Switching
Configuration: One circuit, Two-pole, one SCR per
phase, 800 amp 1 cycle inrush
Ratings: 85-280Vac, 30A continuous
Line Frequency: 50 or 60Hz
Current Measurement: 0.1 to 30A 3%±0.2A
GF Measurement: 10 to 1000mA 5%±2mA
Voltage Measurement: 0 to 300Vac 3%±2V
Control Power
Power Requirement: Control power from heater voltage
85-280VAC, 10VA max
Protection: Control power from heater voltage
protected by 2A fuse
MOV transient protection
Communications
Port: (1) Serial network connection
Type: RS485
Protocol: Modbus® RTU.
Transmission Rate: 600,1200, 2400, 4800, 9600 baud.
Interconnect: 2-wire, shielded, twisted pair.
Highway Distance: 4,000 feet without repeater.
Modules per Highway: 32 Control Modules.
Measured Values
Temperature: -50 to 500°C (-58 to 932°F)
Minimum Temperature: -50 to 500°C (-58 to 932°F)
Maximum Temperature: -50 to 500°C (-58 to 932°F)
Heater Current: 0.1 to 60A
Ground Fault Current: 10 to 1000mA
Min. Heater Voltage: 85 to 300Vac
Max. Heater Voltage: 85 to 300Vac
Power Consumption: 0 to 1,000 MWh
Operating Cost: 0 to $1,000,000.00
User Interface
Display: 16-character x 2-line LCD Alpha-
numeric display
Keypad: 9 tactile keys, polyester faceplate
- Setpoint, measured, status
- Message Up, Message Down
- Value Up, Value Down
- Reset
- Store
Contrast: Adjustable by potentiometer
Panel Indicators: Power on
Heater on
Serial communication active
System fail
Process alarm
Security: Controller parameters password protected
Environment
Approvals: CSA NRTL/C and FM
Class I, Div. 2, Groups A,B,C,D
Class I, Zone 2, Groups IIC
Class II, Div. 2, Groups F and G
Class III
Operating Temperature: -40°C to +50°C (LCD: -20°C to +50°C)
Conformal Coating: Boards conformal coated for hostile
environments
Enclosure
Type: Nema-4X steel, painted black
Size: 10”Hx8”Wx6”D
Features: Quick release latches to open door
Flat aluminum plate to act as heatsink
and mounting flange for mounting on
Uni-Strut.
One 3/4” conduit knockout for power
and three 1/2” conduit knockouts for RTD
and signal wiring.
Alarm Output
Alarm: Programmable for NO or NC contact
One Mechanical (dry) contact
Alarm Rating: Mechanical contact: 30Vdc/100mA,
120Vac/0.52A, 62.5W Max
Alarm Output: LED Indicator: 5Vdc/50mA
Alarm Function
Temperature: High Temperature Alarm
Low Temperature Alarm
Current: Low Current Alarm
High Current Alarm
Ground Fault Current: Ground Fault Current Alarm
Ground Fault Current Trip
Voltage: High Voltage Alarm
Low Voltage Alarm
Hardware: Self-Check Failure
Switch Shorted
RTD Open
RTD Shorted
Continuity
User-Definable Options
Heater Status: Enable or Disable
Heater Name or Tag: 16 Character Alphanumeric
Temperature Units: °C or °F
Proportional Control: on or off
Deadband: 1 to 50C° (2 to 90F°)
PowerLimit: 0.1 to 30A, off
SoftStart: 10 to 999s, off
TraceCheck: 1 to 24hrs, off
Temperature Setpoint: -50 to 500°C (-58 to 932°F), off, none
High Temp Alarm: -50 to 500°C (-58 to 932°F), off
Low Temp Alarm: -50 to 500°C (-58 to 932°F), off
High Current Alarm: 0.1 to 30A, off
Low Current Alarm: 0.1 to 30A, off
Ground Fault Alarm: 10 to 1000mA, off
Ground Fault Trip: 10 to 1000mA, off
High Voltage Alarm: 85V to 300V, off
Low Voltage Alarm: 85V to 300V, off
RTD Definition: Single, Backup, Highest, Lowest,
Average or High Temperature Cutout
RTD Fail-safe: Heater On or Heater Off
Heat Trace Curve: disable, user, LT3, 5, 8, 10
HLT3, 5, 8, 10, 12, 15, 18, 20
Override: On or Off
Alarm Contacts: NO or NC for each contact
Alarm Light: Alarm on, Alarm off, Flash during alarm
then on, Flash during alarm then off
Ground Fault
Maximum Trip Time: 3.7 seconds

1.3
MS-2101 Chapter 1 Product Overview
Inputs
y2-RTD Sensors
y1-Override
Monitoring
yRTD Temperatures
yHeater Current
yHeater Voltage
yGF Current
Alarms
yLow and High Current
(Compensated by heat trace curve for
Self-regulating cable)
yLow and High Temperatures
yContinuity
yGF Alarm
yGF Trip
ySwitch Failure
ySensor Failure
ySelf-Test Failure
Outputs
y1-Mechanical (dry) Contact
y1-LEDAlarm Indicator
Statistics
yMinimum and Maximum Temperatures
yMaximum Current
yMaximum Ground Fault
yMinimum and Maximum Voltage
yEnergy (MWh)
yEnergy Cost
Control
yTemperature (On/Off- Deadband)
yTemperature -Proportional
yPowerLimiting
ySoftstart
Early Warning (TraceCheck)
yLow and High Current
yContinuity
yGF Alarm
yGF Trip
Communications
y1-RS485
yModbus Protocol
Environment
yCSA Certified and FM Approved for Hazardous
Locations
yWeatherproof, NEMA-4X Enclosure
y-40°C to +50°C Operating Temperature Range
(LCD: -20°C to +50°C)
User Interface
y32 Character LCD Display
yLED Indicators on Faceplate
yClear, English Language Messages
yIntuitive Message Structure
yTactile Keys
yAccess Security
Summary of Features
Using This Manual
Detailed information relating to switch and output ratings,
accuracy and so forth are detailed in Chapter 1 Specifica-
tions.Chapter 2 Installation discusses important mount-
ing and wiring issues for reliable operation. Chapter 3
Getting Started provides a step-by-step tutorial for a heat
trace application. The remainder of this manual should be
read and kept for reference to provide the maximum
benefit of the MS-2101.
Conventions
The following conventions are used in this manual.
"User Changeable Values
Retrieved Data
[ ] Key Press
Shipping Content
MS-2101 Heat Trace Controller
MS-2101 Instruction Manual with Warranty Card

1.4
MS-2101 Chapter 1 Product Overview
Theory of Operation
Controller functions are controlled by a Intel 80C32 8-bit
microprocessor that measures all analog signals and logic
inputs, control heater output and alarm contacts, and
reads all user input including communications and outputs
to the faceplate display and LEDs. Consult the hardware
block diagram in figure 1.8 for details. The remainder of
this chapter describes the algorithms and operation of
some of the controller functions.
RTD Sensing
An RTD changes its resistance in a precision relationship
to temperature. This resistance is sensed by passing a
constant current through the RTD and measuring the
resulting voltage across the RTD (resistance = voltage/
current). The voltage appearing across RTD1 terminals
6&8 and RTD2 terminals 10&12 also includes the
resistance of the inter-connecting wiring to the RTD,
which varies with wire length, size and ambient tempera-
ture. By using a three-wire sensing scheme and a lead
resistance compensation circuit, the lead resistance is
cancelled out to give a voltage proportional to the true
RTD sensor temperature.
RTDs respond in a known but non-linear fashion to
temperature, which if uncorrected could lead to signifi-
cant errors over the temperature range of the controller.
Consequently, some means is needed to convert the input
voltage to a linear and useful range. The CPU applies
gain, offset and non-linearity corrections through a
linearization algorithm.
Current, Ground Fault and Voltage Sensing
Current transformers and high impedance voltage dividers
are used to scale-down the incoming heater current,
ground fault current and voltage. All three signals are then
passed through a full wave rectifier and filter to obtain a
DC signal. The DC signals are then converted to digital
values by a 10 bit A/D converter before finally being
passed on to the CPU for analysis.
Each of the three DC signals are sampled 300 times with
zero cross synchronization so that the sampling covers an
exact span of ten power cycles. This is to ensure that
heater current values are consistently measured when the
heater output cycle is modulated by the powerlimit,
softstart or proportional control functions.
Powerlimit
The powerlimit function allows the heater to operate
below its rated power by cycle modulation. Cycle
modulation is accomplished by controlling the integral
number power cycles into the heater over a periodic time
frame. The MS-2101 uses a ten cycle time frame. The
integral number of power cycles per time frame is called a
duty cycle. With a ten cycle time frame, there are ten duty
cycles possible. For each duty cycle, there is a fixed
pattern that defines the number of power cycles in which
the heater is on and off. This is shown in figure 1.2:
Figure 1.2 Cycle Modulation - 10 Cycle Frame

1.5
MS-2101 Chapter 1 Product Overview
Cycle modulating the current through the heater has the
effect of turning the heater on and off rapidly and
therefore, power output is reduced in the long run. Since
the switching is zero-cross controlled, the controller
knows exactly when power cycles start and finish. Zero-
cross switching also helps reduce power harmonics that
generate unnecessary interference.
The heater current (average current) measured by the
controller while cycle modulation is in effect may be
approximated as follows:
Heater Current at 100% x Duty Cycle = Average Current
When powerlimit is enabled, a powerlimit current is set
by the user. This is essentially the desired average current.
The powerlimit control algorithm ensures that the actual
current will not exceed the powerlimit setting while
optimizing the maximum duty cycle possible. When the
average current exceeds the powerlimit setting, the duty
cycle is reduce by 10%. When the average current is
below the powerlimit setting, the duty cycle is increased
by 10%. Before the algorithm increases or decreases the
duty cycle, the controller waits until the heater current has
reached steady-state at the current duty cycle setting. If
the heater is initially off and the controller calls for heat,
the duty cycle starts at zero and increases by 10%
increments until it reaches a steady-state value. This
ramping up effect provides a current-driven softstart
whenever the controller calls for heat unlike the softstart
function, which is time driven.
Softstart
During cold temperature startups with self-regulating heat
trace cables, the current driven softstart built into the
powerlimit function may not be long enough to overcome
the inrush current. The softstart function is separate from
powerlimit and is time driven where for when you set the
softstart period. Having the two separate functions is
desirable when powerlimit may not be required by the
application but softstart is essential to avoid nuisance
breaker trips during cold startups. The controller applies
the softstart function initial startup when the controller is
powered up.
Operation of the softstart function varies depending on
whether or not powerlimit and/or proportional control are
enabled. When powerlimit and proportional control are
off, operation is simplified. The softstart function uses
cycle modulation to gradually increase power output over
the softstart period. Since most circuit breakers are the
thermal type, the cycle modulated output appears as a
reduced load to the circuit breaker.
During controller power-up and assuming the controller is
calling for heat, the duty cycle starts at 10% and incre-
ments by 10% until full power is reached. Since there are
ten duty cycle increments, the time that the controller
maintains each duty cycle setting is the softstart setting
(softstart period) divided by 10. The softstart operation
powerlimit and proportional control off is shown by the
curve in figure 1.3.
Figure 1.3 Softstart Curve with Powerlimit and
Proportional Control Disabled
With powerlimit enabled, the only difference is that
instead of the duty cycle ramping to 100%, it stops at the
value determined by the powerlimit function such that the
average current does not exceed the powerlimit current
set by the user. The maximum duty cycle setting is
approximated by the controller initially so that the time
period for each duty cycle increment can be determined.
The softstart operation with powerlimit enable is shown
by the curve in figure 1.4.
Figure 1.4 Softstart Curve with Powerlimit Enabled
When proportional control is turned on, the maximum
duty cycle available to the controller is constrained by the
powerlimit current if enabled and softstart.

1.6
MS-2101 Chapter 1 Product Overview
Proportional Control
Unlike on/off control where the heater is fully on or off,
proportional control can partially turn on the heater. The
heater output is proportional to the difference between
actual temperature and heater setpoint. The relationship is
expressed as follows:
(actual temperature – heater setpoint) x k = heater output
where k is the proportional gain
To partially turn on the heater, the proportional control
function uses cycle modulation in the powerlimit function.
By incorporating cycle modulation into the proportional
control equation, the algorithm is expressed using the
following equations:
secondsintime
C)(
C)(peratureheater tem
C)(emperaturesetpoint theater
cycle)C/duty(infactordeadband)(
cycleduty)(Where
)()(1)(
)()(0
)(
)(
0)(0)(
=
°==
°=
°=
°=
=
≥=
<<=
≤=
t
∆TTs-T(t)e(t)
T(t)
Ts
tDB
td
tDBteiftd
tDBteif
DB(t)
te
td
teiftd
The deadband factor DB(t) is a time constant that
determines the slope of change of the proposed heater on
duty cycle with the temperature difference. It is adjusted
between 1 to 10 each hour to minimize the difference
between the measured temperature and the temperature
setpoint. Every hour after power up, the controller
calculates the absolute values of the temperature
differences e(t) and sums them during the hour. Then the
total absolute temperature difference is divided by the
number of temperature readings taken during the hour.
The result is called the Average Absolute Temperature
Difference (AATD) for the hour. If current AATD is
smaller than the AATD in the previous hour, the deadband
factor will be increased or decreased in the same
direction. If current AATD is larger than the AATD in the
previous hour, the deadband factor will be increased or
decreased in the reversed direction. At steady state, the
deadband factor used will fluctuate around a optimum
value.
Figure 1.5 shows the relationship between the proposed
heater on duty cycle and the temperature difference for
different deadband factors used.
Figure 1.5 Proportional Control
Duty Cycle vs. Temperature Difference
On/Off Control with Deadband
The default control mode of the controller is deadband
control or simply on/off control with the proportional
control setting turned off. On/off control without
deadband (that is deadband set to 0 C° or 0 F°; note that
these units denote the temperature differential with “°”
placed to the right of the unit) means that the heater turns
on when actual temperature is below setpoint and turns
off when above setpoint. However, this causes oscillations
when the actual temperature is very close to setpoint. To
eliminate oscillations, hysterisis is applied to the on/off
control by a deadband value. The on/off control with
deadband operation is described by the hysterisis curve in
figure 1.6. Assume that actual temperature is well below
(setpoint - deadband setting), the controller calls for heat.
As the actual temperature rises, the controller continues to
call for heat until the actual temperature has reached
(setpoint + deadband setting). The controller no longer
calls for heat and the heater is off. As the actual
temperature cools, the controller does not call for heat
until the actual temperature reaches (setpoint – deadband
setting). The hysterisis effect is controlled by the
momentum of the actual temperature rather than the
temperature value itself.

1.7
MS-2101 Chapter 1 Product Overview
Figure 1.6 On/Off Control with Deadband
Heat Trace Curve
Monitoring low and high current alarms on self-regulating
heat tracing cable is difficult. Choosing a high current
alarm setting based on cable characteristics near the
heater setpoint temperature will produce nuisance alarms
during startup. Choosing a low current alarm setting other
than below the current draw of the cable at heater setpoint
temperature produces nuisance alarms. The heat trace
curve function allows you to program the cable character-
istics so that the controller can offset the current alarm
settings.
The heat trace curve is described by the following linear
equation:
W = aT + b
where, W is the Watt/ft at temperature T (in degree F), a
and b are the slope and offset of the linear curve.
If the Watt per foot value of the heat trace is Ws at
setpoint temperature Ts, and the Watt per foot value of the
heat trace is W at temperature T, the offset ratio to be
applied to the high/low current alarm level is Ws/W.
That is, if the high/low current alarm level is set to Is, the
current draw of the cable at setpoint temperature of Ts,
then the high/low current alarm level at operating tem-
perature T should be corrected to (Ws/W)*Is to compen-
sate the effect of operating temperature on the allowed
maximum/minimum heater current. The heat trace curve
is shown in figure 1.7.
If no heat trace curve is used, the offset ratio is set to 1
and no correction to the high/low current alarm level is
done.
Figure 1.7 Heat Trace Curve

1.8
MS-2101 Chapter 1 Product Overview
Figure 1.8 Hardware Block Diagram

2.1
MS-2101 Chapter 2 Installation
Unpacking the Controller
Check the shipping cartons for damage, or other signs of
rough handling or abuse. If damaged, notify the shipping
carrier at once.
Carefully remove the MS-2101 from the shipping box.
Save the packing materials in case the unit needs to be
transported at a later date.
Inspect face plate for damage and check electronics for
loose wiring or damage. Report any damage to the carrier
at once.
Control Module
See Figure 2.1 Main Board Layout and Figure 2.2
Power Board Layout to locate the following:
•S1Address Enable: When the switch is set to DIS, the
Module Number cannot be changed from a master on
the data highway. When set to EN, the Module Number
can be changed for the next two minutes from a master
on the data highway. During this time the ADDRESS
ENABLE light is on.
•S2Program Enable: When the switch is set to DIS,
programming is disabled; setpoints and configuration
cannot be changed. When set to EN, programming is
allowed.
•S3RS485-120: When the jumper is set to IN, the
RS-485 line is terminated by a 120 ohm resistor. Only
the last Control Module on the data highway should be
set to IN.
Terminals: Refer to Figure 2.7 Typical Wiring Diagram,
for power, heater and RTD field connections.
•T1Alarm Contact: The mechanical output is rated 30
Vdc/100mA, 120Vac/0.52A, 62.5W Max. Contact is
configurable for normally open or closed.
•T2Alarm Light Output: The output is configurable for
normally open, closed or flash. Output is rated 5 Vdc
@ 50 mA for an LED type lamp (terminals 18+ and
19-).
• T3 Override Input: With the Override function
(SETPOINTS\HEATER SETUP\OVERRIDE) set to
on, the heater output is affected by the override input.
When the terminals are open, the heater is forced off.
When the terminals are closed, the heater is controlled
by the RTDs unless the heater setpoint is set to off. In
this case, the heater is solely controlled by the override
input. The logic of this input allows either ambient
temperature override or load shedding on multiple
controllers (terminals 24+ and 25-).
•T4RTD1A and RTD1B Inputs: 3 wire RTD input.
Ground terminal connects to shield or case. Lead
resistance compensated. (terminals 6-13).
•T5Earth Ground: (terminal 1).
•T6Heater Power Input: 85-280Vac/30A max
continuous ( terminals 2 and 3).
•T7Heater Power Output: 85-280Vac/30A max
continuous ( terminals 4 and 5).
•T8Safety Ground: Terminate to ground stud. Termina-
tion of safety ground is required for transient protec-
tion circuit on RTD inputs and RS485 serial port to
operate properly (terminal 14).
•T9Extra A/D Input/Output: Terminals 22 (POUT) and
23 (PIN) are the output (+12Vdc) and input (4-20mAdc)
connections to a 4-20mA analog signal transmitter.
Status Lights:
•L1Power: Light is on when control power is present.
•L2Address Enable: Light is on when controller is in
Address Enable mode. Light must be on to allow the
Module Number to be changed from a master on the
data highway.
•L3Transmit: Flashes when data is being transmitted
from the serial port to the data highway.
•L4Receive: Flashes when data is being received at the
serial port from the data highway.
•L5Override: Light is on when the Override Input ter-
minals are shorted.
Communication Ports:
•C1Interface to Main/Power Board: Connector to
interconnect power and main board via ribbon cable.
•C2Serial Port 1: Connection to an RS-485
data highway via a 2-conductor, shielded, twisted pair
cable. Maximum Cable length with 32 devices without
repeater is 4,000 feet. ( terminals 15+, 16-,17 SHD).
Warning - The ground fault trip function is
intended for equipment protection only and
should not be used in place of ground fault
protection for personnel protection where
this is required.

2.2
MS-2101 Chapter 2 Installation
Figure 2.2 Power Board Layout
Figure 2.1 Main Board Layout

2.3
MS-2101 Chapter 2 Installation
Mounting the Controller
Mount the control panel with Unistrut brackets using 1/2”
bolts. The Unistrut (or equivalent) mounting allows air
circulation to cool the heat-sink. This is important to
ensure proper operation of the MS-2101. For optimum
readability, mount with the display at eye level and not
in direct sunlight. Mounting dimensions are shown in
Figure 2.6.
Wire Sizing
Conduit and Cabling
The MS-2101 comes with one 3/4” and two 1/2” conduit
knockouts located on the bottom of the enclosure.
Conduit hubs should be NEMA-4X rated, such as T&B
H050-0.5 and H075-0.75 or Myers equivalent, to main-
tain a watertight seal. Unused knockouts should be sealed
using NEMA-4X rated seals.
Power Wiring
The power input terminals supply power to both the heat
trace and controller. Size power input wires appropriately
to the breaker size and maximum ambient operating
temperatures. Maximum breaker size is 30A. Connect
power wires to input terminals 2 and 3. See Figure 2.7.
The RTD probe is delicate and should not
be bent or used as a tool to puncture
insulation.
Wiring methods should comply with Canadian
Electrical or National Electrical Code and
local codes. Power and signal wires should not
be run in the same conduit system. Wiring
should be rated at least 90 °C.
)GWA(eziSeriW)A(daoLtnerruC tneibmA.xaM
)C°(erutarepmeT
60305
80304
014205
216105
The supply voltage must be within the power
supply range of 85-280Vac and rated voltage
range of the heat trace cable.
Wiring methods must conform to Class I,
Division 2 or Class I, Zone 2 requirements.
Heater Wiring
Connect heating cable wiring to terminals 4 and 5. See
Figure 2.7. If the heating cable has a braid, it should be
terminated to the ground stud using a ring terminal
suitable for #10 stud.
Ground Connection
Connect the controller grounding stud directly to a
ground bus using the shortest, practical path. Use a
tinned copper, braided bonding cable such as Belden
8660. As a guideline, the ground cables should be mini-
mum 96 strands, number 34 AWG each.
The grounding is not only a safety requirement but is
necessary for the input transient protectors or the RTD
and communication inputs to work properly. The transient
protection network is grounded through terminal 14,
safety ground, which is bonded to the chassis ground stud.
To install the ground connection, remove the outside nut,
washer and #10 ring lug provided on the ground stud.
Crimp the ground cable onto the ring lug and re-assemble
onto the ground stud using the washer and nut.
Figure 2.4 RTD Mounting
RTD Sensor Wiring
RTD sensors should be 3-wire, 100 ohm, platinum to DIN
standard 43760. Mount the RTD element on the pipe,
away from the heat trace and 30° to 45° from the bottom
of the pipe. The total circuit resistance per conductor
from the RTD to the control panel must be less than 10
ohm. Exceeding this resistance will result in a non-linear
temperature measurement. Belden cable 8770 or equiva-
lent allows RTDs to be placed up to 1,000 feet from the
control panel. Complete all RTD wiring according to
Figure 2.7 Typical Wiring Diagram.
Figure 2.3 Ground Connection

2.4
MS-2101 Chapter 2 Installation
You must install the RTD sensor on the pipe surface or
thermal well before the pipe insulation to ensure proper
thermal contact. The RTD position should be 180° from
the electric heat trace cable which is the coldest spot of
the pipe. The RTD sensor may be secured to the pipe by
fiber-glass tape. If additional wiring is required for the
RTD, shielded 3-lead wire sized 18 or 20AWG must be
used for the RTD sensor to minimize the effects of noise
pickup. A typical RTD installation is shown in Figure 2.4.
Communication Wiring
The MS-2101 is equipped with a communication port that
provides continuous monitoring and control from a
remote computer, SCADA system or PLC. Communica-
tions protocol is Modicon Modbus as discussed in the
communications chapter.
Communication is RS-485 mode where data transmission
and reception are done over a single twisted pair with
transmit and receive data alternating over the same pair of
wires.
Shielded twisted pair such as Belden cable 9841 or
equivalent is recommended to minimize error from noise.
You must observe polarity. For each MS-2101 controller,
you must connect A+ terminals together and B- terminals
together. The shield terminal (labelled SHD) connect to
shield wire of the cable.
To avoid loop currents, the shield should be grounded at
one point only. Connect between controllers in daisy-
chain fashion. The total length of this daisy-chain should
not exceed 4,000 feet. The maximum number of devices
connected is 32 to avoid exceeding driver capability. You
can use commercially available repeaters to increase the
number of devices over 32. Avoid star or stub
connections.
Terminate the first and last device in the daisy-chain loop.
Each controller is equipped with a termination jumper as
shown in Figure 2.2.
The controller comes unterminated from the factory
(JP401 and JP402 in OUT position). If the controller is
the first or last device, it can be terminated by moving the
two jumpers (JP401 and JP402) to the IN position.
The communication port is powered by an isolated power
supply with opto-coupled data interface to eliminate noise
coupling. In addition, surge protection devices are
employed at the front end of the port to protect against
lightening strikes and ground surge currents. These may
cause large, momentary voltage differences between
devices on the data highway.
Alarm Wiring
The MS-2101 has one passive (mechanical) alarm contact
and one active alarm output for driving an LED alarm
indicator. The alarm contact is software configurable for
normally open or closed. The alarm LED output is
software configurable for alarm on, alarm off or flash
during alarm. Refer to Figure 2.7 for alarm output termi-
nals.
The mechanical (dry) alarm output is rated 30Vdc/10mA,
250Vac/0.5A Max.
The alarm LED output is rated 5Vdc, 50mA. It can drive a
6Vdc LED indicator. Alarm output is designed for interface
to annunciator, panels, PLC or DCS.
Figure 2.5 Communication Wiring

2.5
MS-2101 Chapter 2 Installation
Figure 2.6 Mounting Dimensions
Figure 2.7 Typical Wiring Diagram
Warning - Explosion Hazard - Substitution
of components may impair suitability for
Class 1, Division 2 or Class 1, Zone 2.
Warning - Explosion Hazard - Do not
disconnect equipment unless power has
been switched off or the area is known to be
non-hazardous.

3.1
MS-2101 Chapter 3 Getting Started
Introduction
The MS-2101 has many features that provide trouble-free
operation of heat tracing installations.
An example is presented to illustrate MS-2101 setup and
operation on a specific installation. MS-2101 is easy to
program and setting up a unit to your specific require-
ments should be straight forward.
In this example, a MS-2101 will control a heavy feed line.
Example: Heater will be programmed as:
Configuration:
1) 2 RTDs for temperature sensing
2) Mineral insulated (MI) cable is used for the heater.
3) Normally open alarm contact to remote programmable
control
4) Northern climate installation outdoors.
Operating temperatures: -40°~50 °C (LCD:-20°~50 °C)
NEMA-4X weatherproof enclosure.
Install and commission the control in the following order:
STEP 1: Enabling the heater
STEP 2: Entering setpoints
STEP 3: Testing heater and alarms
STEP 4: Monitoring system status
Enabling the Heater
To enable the heater circuit,
1. Press [SETPOINTS] once to access the Setpoints
Operating Values group of messages.
2. Press [MESSAGE ò] until the following message
appears:
HEATER ENABLED?
NO?
3. Press [VALUE ñ] or [VALUE ò] keys to toggle
Heater Enabled between YES and NO.
4. When YES is displayed, press [STORE].
Now that the heater circuit is enabled, we can program
setpoints for each control.
Entering Setpoints
Accessing the Program: Since the heater control display
and keypad are normally accessible to passers-by who
may wish to read measured values, a program disable
feature is used to prevent accidental changes to the
setpoints. So before any setpoints can be entered, the
PROGRAM ENABLE dip switch (located on the bottom
of the board behind the enclosure door) or PROGRAM
ACCESS function (SETPOINT\SYSTEM
SETUP\PROGRAM ACCESS) must be set in the EN-
ABLE position.
When programming is complete, set the PROGRAM
ENABLE dip switch and PROGRAM ACCESS function
to DISABLE to prevent accidental changes to the
setpoint.
If you try to store a setpoint without the dip switch or
PROGRAM ACCESS function in the ENABLE setting,
the setpoint will not be saved and this message will flash
on the screen:
NOT STORED
PROG DISABLED
Now that the MS-2101 control is ready for programming,
l enter the setpoints for this example. For further infor-
mation about the organization of all the messages or for
details on the range and application of each message see
Setpoint Required Range
Fluid maintain
temperature
50 °C -50 to 500°C/off
/none
Low temperature
alarm
35 °C -50 to 500°C/off
High temperature
alarm
no alarm -50 to 500°C/off
Nominal heater
current
5 amps 0.0 to 60.0A
Nominal heater
voltage
115 VAC 100 to 300 Vac
Ground fault trip
current
30 mA 10 to 1000mA
Ground fault alarm
current
20 mA 10 to 1000mA
/off
System exercise
time interval
8 hours 1-24/off
Cost per Kilowatt
hour
$0.06 $0.01-$0.50
Heater name HEAVY OIL
LINE
16 characters

3.2
MS-2101 Chapter 3 Getting Started
Chapter 6 Setpoint Values. It is not necessary to enter
setpoints in any particular order and any setpoint can be
changed later.
Entering Temperature Units °C/°F: Temperature values
can be displayed in degrees Celsius or Fahrenheit. To
enter values in preferred units, enter this selection first.
To enter temperature units,
1. Press [SETPOINTS] 3 times for System Setup mode
and [MESSAGE ò] 5 times until the following
message is displayed:
TEMPERATURE
UNITS: Celsius
2. Press [VALUE ñ] or [VALUE ò] to toggle selection
between Celsius and Fahrenheit.
3. When Celsisus is displayed press [STORE]. A brief
message appears:
SETPOINT
STORED
Then the message reverts back to the previously
entered value for verification. If instead you get the
message:
NOT STORED -
PROG DISABLED
the PROGRAM ENABLE dip switch or PROGRAM
ACCESS function has not been set to the ENABLE
setting. This must be done to proceed with setpoint
programming.
Assuming the setpoint was stored, all values will be
displayed in °C. Temperature values can automatically be
converted to °F at any time by selecting Fahrenheit using
this message.
TEMPERATURE
UNITS: Celsius
ASSIGNING HEATER NAME: To assist operators in
troubleshooting, you can program each MS-2101 control
with a heater name. You can assign up to 16 characters to
the name of the heater.
To assign a heater name,
1.Press [SETPOINTS] twice to enter the Heater Setup
group of setpoints.
2. Press the [MESSAGE ò] key until the heater name
message appears:
HTR NAME:
NONAME ?
Note: The heater default name when MS-2101 is
shipped from the factory is NONAME.
You can program each letter separately with upper and
lower case characters, numbers, space or the special
symbols @#$%&*()?.,:;][. Uppercase charac-
ters are generally more legible. For this example the
name has arbitrarily been chosen as:
HEAVY OIL LINE
(The cursor appears under the first letter N in
NONAME).
3. Press and hold down [VALUE ñ] or [VALUE ò] until
the desired letter you want appears above the cursor,
then press [STORE].
4. Press [STORE] to save the current letter displayed and
advance the cursor to the next letter.
For Example:
H: Press [VALUE ñ] or [VALUE ò] until H appears.
Press [STORE]. The letter H now appears in the first
character position and the cursor is under the second
character.
E: Press [VALUE ò] until E appears. Press the [STORE].
The first 2 letters are now HE and the cursor is under
character position 3.
HTR NAME:
HENAME?
5. Continue entering each letter this way until the com-
plete new name is displayed.
6. With the cursor under the last character position at the
right edge of the message screen (blank character),
press [STORE] until the cursor is at the end of the line.
A brief message will flash:
NAME
STORED

3.3
MS-2101 Chapter 3 Getting Started
followed by the new name that has been stored:
HTR NAME:
HEAVY OIL LINE
The new heater name is now saved in non-volatile
memory and will remain until you change it.
If a character is accidentally entered incorrectly,
1. Either press [RESET] to start over,
or
go to the end of the line to save the displayed message
with the error.
2. Press [MESSAGE ñ] or [MESSAGE ò] to exit and
return to the 1st character position.
3. Press [STORE] until the cursor is under the incorrect
character. Proceed as before until new letters are
entered.
4. Press [STORE] to skip over the correct letters until on
the last character position.
5. Press [STORE] to save the corrected message.
You can now enter setpoint information for the system
configuration and data for the heater. Turn to Chapter 6
Setpoint Values. Read the first few pages to see how the
messages are organized and get a summary of all
setpoints. Skip the latter part of this chapter which gives
a detailed description of each message.
ENTERING SETPOINT TEMPERATURE:
Set the desired maintained temperature for the fluid in the
pipe being traced by this heater temperature setpoint.
To enter the heater setpoint,
1. Press [SETPOINT] once to display this message:
HEATER SETPOINT
20 °C?
2. Press and hold [VALUE ñ] until 50°C is displayed.
Notice that if you press [VALUE ñ] once, the dis-
played temperature increments by 1. Holding [VALUE
ñ] causes the diplayed value to increment rapidly after
a short delay. [VALUE ò] works the same way. If you
pass the required value, use [VALUE ò] to decrease
the number displayed.
3. Press [STORE] to save the new value. When a new
value is successfully stored a brief acknowledgement
message will flash on the screen:
SETPOINT
STORED
In this example, the temperature at which the control
will turn on and supply full system voltage to the heater
is now set to 50 °C.
4. Press [MESSAGE ò] after each setpoint to access the
next setpoint.
5. Hold [VALUE ñ] down until the word OFF appears to
defeat any setpoint not required. For example, if a
high current alarm is not required, set the value to off.
A detailed description of each message is found in
Chapter 6 Setpoint Values.
Testing Heater & Alarms
You can force heater and alarm outputs on using the test
mode. Like setpoints, this mode requires that the PRO-
GRAM ENABLE dip switch or PROGRAM ACCESS
function be set to ENABLE or when you try to store a test
value a message will flash:
NOT STORED -
PROG DISABLED
Testing a Heater:
To test operation of a heater, it can temporarily be forced
on.
1. Press [SETPOINT] 4 times.
2. Press [MESSAGE ò] until the message appears:
HEATER TEST
DISABLED?
3. Press and hold [VALUE ñ] or [VALUE ò] to set the
ON time in hours. The range is DISABLED/1-24
hours/ON-CONTINUOUSLY. For example, to turn
on the heater for one hour, press [VALUE ñ] to
display 1 hour then press [STORE]. The heater will
be energized no matter what the heater temperature
setpoint is unless there is a ground fault trip. After the
selected time period the heater will automatically go
off.
While the heater is on, the front panel HEATER ON
indicator will be illuminated. To override the test
mode, press [VALUE ò] until DISABLE appears and
then store this value. Holding the [VALUE ñ] key
until the word ON CONTINUOUSLY appears leaves

3.4
MS-2101 Chapter 3 Getting Started
the heater always energized until the MS-2101 controller
is manually powered off or until this setpoint is set to
DISABLE. Consequently, selecting a value of ON
CONTINUOUSLY should be used with caution since
it overrides normal control operation and could lead to
excessive heating or waste power if accidentally left
on. A warning message appears in the status mode
(press status key to enter status mode) whenever a
heater or alarm is forced on.
4. Press [STORE] to save the value.
5. With the heater forced on, verify that the expected
current is flowing using the actual current message,
located in ACTUAL\OPERATING VALUES\HEATER
CURRENT. You can use a clamp-on ammeter attached
to one of the heater wires to compare readings. With
proportional control selected, the readings may differ
due to harmonics in the current waveform. As a
safeguard, the heater will automatically timeout after
the selected time and go back to automatic operation.
Testing Alarms: The manual alarm setpoint works exactly
like the manual heaters setpoint except that it energizes
the output alarm and indicator. This setpoint is useful for
commissioning a new system or checking alarm circuits.
Normally this setpoint will be DISABLED.
Monitoring System Status
Now that the MS-2101controller has been programmed
for a specific application, you can check system status. If
no keys are pressed for the time specified in DISPLAY
TIMEOUT message located in SETPOINT\SYSTEM
SETUP\DISPLAY TIMEOUT, the display will automati-
cally go into the default message mode. System Status
mode is recommended; that is, the display will automati-
cally display all alarms. If desired, you can change this to
a specific message later by reprogramming the default
message.
Access actual values by pressing [MEASURED]. These
are divided into 2 groups. Pressing [MEASURED] once
accesses the group of messages that show current values
of temperature, current, etc. Pressing [MEASURED]
twice displays the statistics data such as minimum/
maximum temperature, power consumption, running
hours etc. Unlike setpoints, you cannot change actual
values using [VALUE ñ] , [VALUE ò] or [STORE].
There is a summary of all Measured Values messages at
the beginning of Chapter 5 Measured Values.
To view the actual values,
1. Press [MEASURED].
2. Press [MESSAGE ò] to view each actual value.
3. Continue examining each value of interest by pressing
the [MESSAGE ò] key and referring to Chapter 5
Actual Values.
Monitoring Heater Temperature
To monitor the heater temperature,
1. Press [MEASURED] once to display:
CONTROL TEMP:
55 °C
This is the temperature value that the controller will use
with the heater setpoint to determine the heater output.
The MS-2101 calculates the control temperature from the
actual temperature of RTD1A and RTD1B (if used) based
on the RTD DEFINITION setting (SETPOINT\HEATER
SETUP\RTD DEFINITION). Using only one RTD, you
must place the RTD probe at a location that best repre-
sents the average pipe temperature. However, fluid
temperature will vary somewhat along the pipe. Using
two RTDs and RTD DEFINITION set to TWO RTDs
AVERAGED eliminates this problem. If no RTD sensor
is connected or a lead is broken the value OPEN RTD
appears. This is an alarm condition.
When the temperature falls below the heater setpoint, 50
°C in our example, MS-2101 switches on to supply power
to the heater. It stays on until the temperature rises above
the heater setpoint (50 °C). Once the system has been
running for a few hours, the heater temperature should be
at or above this setpoint value.
If hot fluid is being pumped through the pipe, the meas-
ured temperature may be much higher than the setpoint
temperature. But in this case, no power should be sup-
plied to the heater and the HEATER ON indicator will
be off.
If the heater temperature is less than the minimum display
value (-50 °C/-58 °F), the word RTD FAIL appears. If
the temperature is over the maximum value (+ 500 °C /
932 °F), the maximum value ( i.e. 500 °C ) will be shown.
If an abnormal value appears, particularly on a new
installation, check that the correct RTD sensor type has
been installed (100 OHM platinum DIN 43760) and that
the three RTD wires are wired to the correct terminals.
Monitoring Actual Current:
To monitor the actual current,
Table of contents
Other Nextron Control Unit manuals
Popular Control Unit manuals by other brands

Weidmüller
Weidmüller DPA/MAS operating instructions
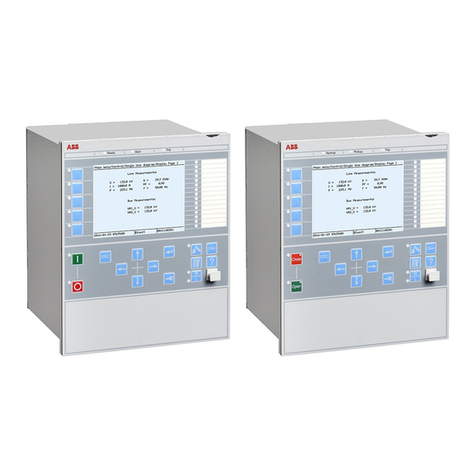
ABB
ABB RELION 650 SERIES Point List Manual
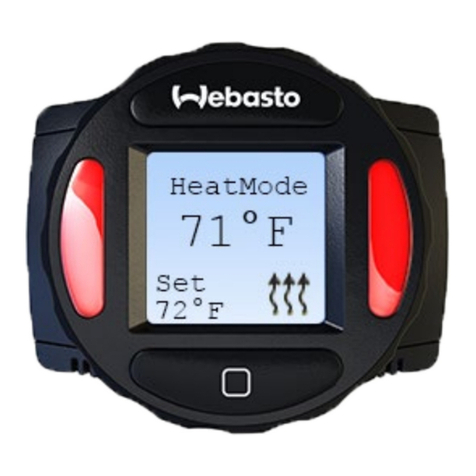
Webasto
Webasto SmarTemp Control 3.0 Installation & operation instructions
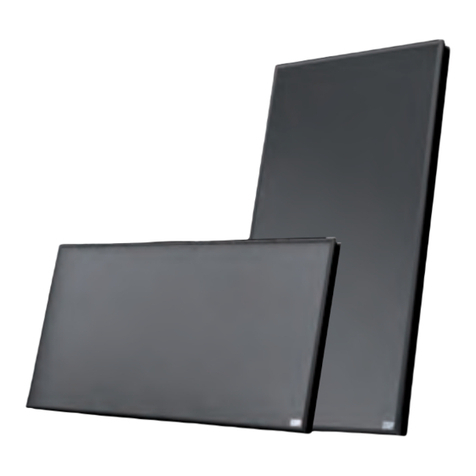
TiSUN
TiSUN FM-S Mounting instruction
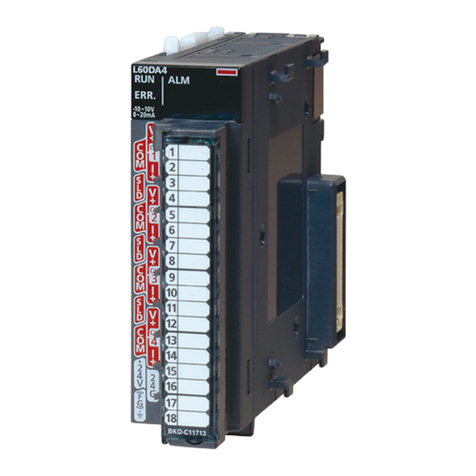
Mitsubishi
Mitsubishi MELSEC L Series user manual
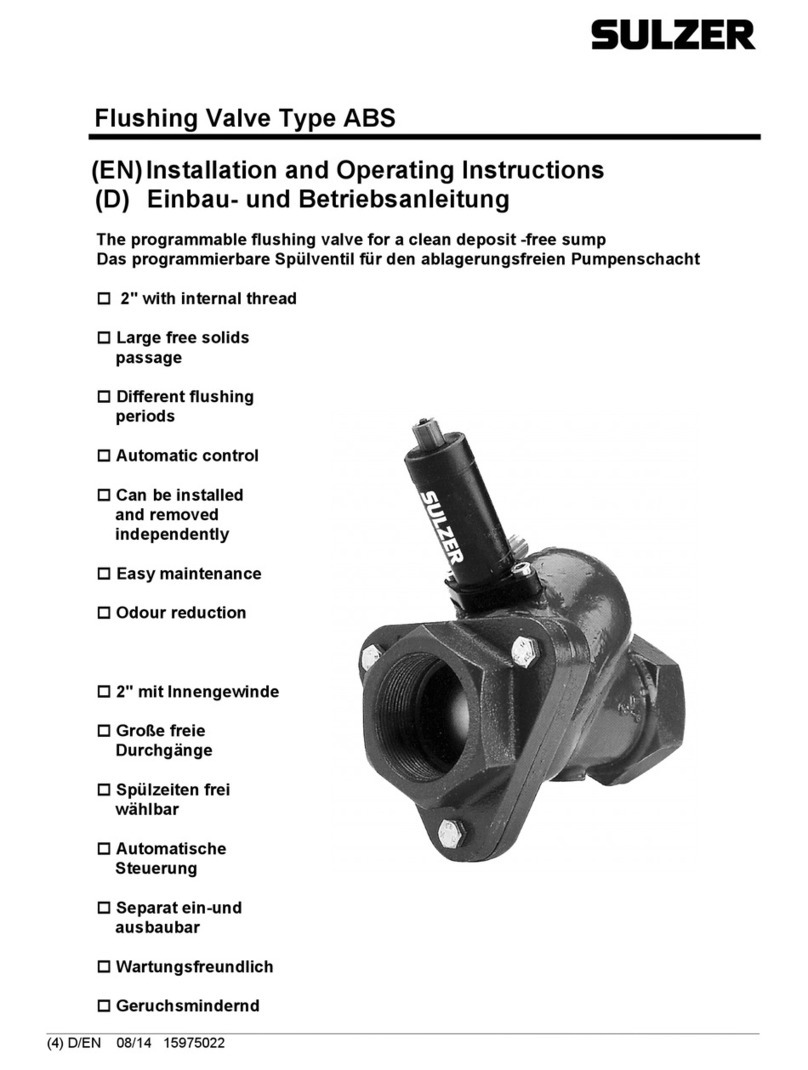
Sulzer
Sulzer ABS Installation and operating instructions