NHP ATYSC CIPACB Series User manual

1
INSTALLATION MANUAL
Cat No: ATYSCxxCIPACB
For NHP AR ACBs
Product Specifications
ATYSC55CIPACB
ATyS C55 Transfer Switch Control Interface for NHP AR ACBs
ATYSC65CIPACB
ATyS C65 Transfer Switch Control Interface for NHP AR ACBs
ACBs must contain the following: Trip Unit: AGR21, AGR31, Non-Auto
Shunt: 240VAC
LRC: 240VAC
Motor: 240VAC
Mechanical Interlock

2
Tools Required (not supplied)
Tools Required (supplied)
Wire Terminating Tool
Risk of damaging the device in case the product is dropped or damaged in any way it is recommended to replace the complete product.
Installation standards must be respected.
WARNING:
Risk of electrocution, burns or injury to persons and / or damage to equipment.
This Installation Manual is intended for personnel trained in the installation and commissioning of this product. For further details refer to the product
instruction manual for the C55 & C65 and refer NHP documentation.
ATTENTION:
•This product must always be installed and commissioned by qualified and approved personnel.
•Maintenance and servicing operations should be performed by trained and authorized personnel.
•Do not handle any control or power cables connected to the product when voltage may be, or may become present on the product, directly through
the mains or indirectly through external circuits.
•Always use an appropriate voltage detection device to confirm the absence of voltage.
•Ensure that no metal objects are allowed to fall in the cabinet (risk of electrical arcing).
T8
Screwdriver Phillips Ph #1Screwdriver Flathead
Wire Strip &
Crimp Tool
Terminal Screwdriver
T1 T2 T3
T4
Drill
T5 T6
Applicable
Cutting Tool
T7
Ruler or
Tape Measure
Non contractual document.
Subject to change without notice

Required Items Not Supplied
Part Number
ACBs
Supplied Items
Part Number
Controller Control Interface Panel CIP Looms
& Plugs
IP65 Gasket
ATYSC55CIPACB
x 1 - C55 - 16000055
x 1
Not available separately
2.5-meter Looms
ATYSLOOMA, B, C
x 1 each Loom
x 1 - 231642019000
x 1 - 231612019000
Looms are prewired to CIP
and controller plugs
Not Supplied
16090001
X 1
16090001
ATYSC65CIPACB
x 1 - C65 - 16000065
3
Items
x 2
and
ACBs with interlocks mech installed on bodies Carriage Interlock Mech and Interlock Cable
x 2 x 2
ACBs required be installed with a shunt, LRC and motor at 230/240VAC
For ACB mechanical interlock instructions refer to the AR ACB Cable
Mechanical Interlock Instructions (AR-IN-006-EN) Contact NHP
TemPower PRO
Scan QR Code for more information

4
Dimensions
Control Interface Panel
ATyS C55/65 Controller
Dimensions not to scale
63.90 mm
48.10 mm
160 mm
240 mm
220 mm
180 mm

5
Mounting
Installer to select appropriate fasters to suit size 6mm mounting holes of
unit to mounting material
Panel
Base
220 +/-1 mm
160 +/-1 mm
Gasket for IP 65
Ø 6.0 mm
6.0 mm
6.0 mm
188 mm
268 mm
Control Interface Panel
OR
click!
172 –179 mm
150 +/- 1mm
Screw not delivered with product
Clip the mounting feet in
the designated slot
Remove all connectors then place the ATS controller inside the door cut-out and clip the door mounting screws into the
side of the controller (2 screws on each side). It is important to respect the tightening torque indicated below and follow
good engineering practise when installing the ATS controller.
1
2
Insert the 4 door mounting
screws in the designated slot
Push back up to
lock in place.
Screw Tightening
torque PH1 / 0.2 Nm

6
Clearances
The below clearance are recommendations to allow for easy of wiring to the Control Interface Panel
Control Interface Panel
Cable must be more than 10mm away from the RTC battery cover and USB.
Do not drill holes above the controller after it has been mounted, to avoid swarf in terminals
Controller
50 mm 50 mm
50 mm
Recommended clearance for
default loom exit (can be moved)
Recommended clearance for cable termination
(*)
(*)
(*)
(*) No recommended minimum clearance
10 mm
10 mm

7
ACB Interlock
For an ATYSCxxCIPACB and ACB transfer switch to be compliant to 60947.6.1, & AS/NZS 3010 a mechanical
interlock shall be installed between the 2 ACBs.
The mechanical interlock on a body of an ACB is a factory fit item and should be specified at the time of ordering
the ABCs.
The mechanical interlock on the carriage of an ACB can be fitted on site by qualified personnel.
NHP/Terasaki have a interlock manual for the fitting of the carriage part of the mechanical interlock, the full
manual can be found here..
Type “C” Interlock
1. Check all loose items have been provided.
•2 x carriage interlock mechanism and 6 x spacers
•2 x jig 1 and 1 x jig 2
•2 x interlock cable (customer to specify 2.5M or 4.0M length)
•2 x brass adjustable end (with 6mm grub screw, adjustment nuts and washers and 1 xallen key)
•4 x M6 20mm mounting studs comes with 4 x M6 nuts and 8 x spring washers
•2 x M6 12mm (flat and spring washer attached) fixing bolts and 6 x M6 12mm pan head screws
2. Type ‘C’ interlocks use two interlock cables. Cable ends must be connected to specific letter labelled ports
on the carriage interlock mechanism. Table 2.0 below shows the interlock connections between the
breakers. A rule of thumb is to always run the ‘open’ (the end that takes the loose brass adjustable end)
cable end to ports ‘A’ and the fixed ends to ports ‘D’. This helps during the final adjustment process.
Another recommendation is to label the cable ends with the breaker and port destination. For example ’ACB
1, port A’’ and ’ACB 2, port D” .
Interlock Type Cable Qty ACB Port Connection Comment
‘ACB 1’ Port ‘ACB 2’ Port
2pcs
A D Cable brass end to
‘A’, fixed end to ‘D’
D A Cable brass end to
‘A’, fixed end to ‘D’

8
ACB Interlock
3. Remove ACB bodies from their carriages now and covered to avoid arc shoot contamination. Do
not insert ACB bodies until final testing stage. Drill the cable interlock path holes in the switchboard.
Conduit or bushing should be used to give the cable a clear path. Sharp cut metal edges may damage the
cables! Cable route radius must not be less that 150mm.
4. Remove the grub screw from the brass adjuster and ensure the nuts are as shown below:
5. Insert the ‘open’ end of the cable into the brass adjuster. Observe through the grub screw hole that the
black outer sheath of the cable is fully pushed into the brass adapter. The inner core should protrude at
least 45mm from the ends of the black outer sheath on both ’open’ and ‘fixed’ cable ends (in other words
the total inner core length should be at least 90mm longer than black outer sheath total length after the
loose brass adjustment end is fitted).
6. Insert the grub screw with fingers until the screw meet the black outer sheath inside the brass adjuster. With
the allen key provided perform a further half to three quarter turn to secure the black outer sheath to the
brass adjuster. Check the integrity of the fixture by trying to pull the brass adjuster from the interlock cable.
Excessive force is not required, a firm pull is adequate. The grub screw MUST NOT be over
tightened. Doing so will restrict the movement of the inner core and compromise the interlock.
7. Install cables in the path made above in 3). Cables should be secured every 500mm if a continuous conduit
has not been used. Cable ends once installed should finish next to the bottom left hand side of each
carriage (as shown below). Ensure that an equal number of Cable ’open’ and ‘fixed ends’ are available at
each ACB in accordance with table 2.0.

9
ACB Interlock
8. If the black outer cable sheath is too long, remove the brass end fixed in step 6 and cut the ‘open’ end of
the cable to the required length. Remember to retract the inner core first so it is not cut when
shortening the black outer sheath. Re-fit the brass end to the trimmed cable. Ensure that at least
45mm of steel inner core is left protruding from the ends of the black outer sheath on both ’open’ and ‘fixed’
cable ends (as described in step 5).The inner core must be damage free and not containing unravelled steel
strands.
NOTE: The best tool for clipping steel inner cable are the cutters found on the back of quality combination
pliers.
9. With the ACB bodies removed from the carriages (as described in step 3) , screw in only finger tight 2 x M6
20mm hex mounting studs with spring washers into each carriage left hand side plate as shown below. The
third mounting hole is left empty at this stage. These studs are only finger tight because they require a small
degree of play. They will be tightened later.
10. Attach the Jig 1 to both carriage interlock mechanisms. The lever protrusions on the carriage interlock
mechanisms will with some manual manipulation line up and slot into the cutouts on jig 1. Secure with the
three 12mm M6 pan head screws as shown below.

10
ACB Interlock
Identify the ‘groove’, ‘wire fixing nut’, ‘wire fixing bolt’, ‘lever’ and ‘wire insertion hole’ on the mechanical
interlock mechanism (see below).
11. Loosen the ACB 1 port D wire fixing
nut so that the wire insertion hole is
exposed. Attach the ‘fixed’ cable end to
ACB 1 port ’D’ on the mechanical
interlock mechanism with the jig fitted
as shown below.
12. With the ‘fixed’ cable end slotted into ACB 1 port ‘D’, adjust the top
and bottom cable fixing nuts ’up’ until it clamps the cable end to the
support (see left). It is important that the ’top’ cable fixing nut is near
its maximum end. Keep finger tight at this stage.
13. Push the inner core through the wire
insertion hole. Ensure the inner core
follows the ’groove’. The inner core should
not extend past the ’grove end’. Tighten
the wire fixing nut to 4.7—5.9Nm with
10mm torque wrench. Repeat steps 11- 13
for ACB 2.
Insert inner core into wire
insertion hole and follow
to grove end
Adjust top and bottom
cable fixing nut up to
secure cable end.

11
ACB Interlock
19. With the cable ends and inner cores secured on both
mechanical interlock mechanisms remove jig 1from
both mechanical interlock mechanisms.
20. With the cable setting jigs removed from the mechanical interlock mechanism, adjust
the ACB1 port D fixing nuts ‘down’ as shown below. Repeat step 20 for ACB2 port D.
21. Put one spacer on each of the two M6 20mm mounting studs fitted earlier. Mount the ACB1 carriage
interlock mechanism onto the studs as shown below. Tighten the 2 x M6 20mm mounting studs until secure
from the inside of the ACB carriage with a 10mm spanner. Secure the mechanical interlock mechanism to
the mounting studs with spring washer and M6 nut as shown below. Repeat step 21 for ACB 2.
Note: Without the spacers the interlock mechanism will not lay flat against the side plate.
22. Push the third spacer between the carriage side plate and the mechanical interlock mechanism so it lines
up with the empty third mounting hole. From The outside of the carriage, screw in the M6 x12mm bolt to
secure as shown below. Repeat step 22 for ACB 2.
The installation is complete. Now follow the adjustment and test procedure.

12
Interlock Test
1. Rack ACB 1 into the ‘TEST’ position. Do not rack ACB 1 into the CONN position at this stage.
2. Rack ACB 2 into the ‘CONN’ position. Charge closing springs and shut main contacts of ACB 2 and
leave closed. Return back to ACB1.
At this stage the cable on port ‘A’ of ACB 1 will need to be adjusted. The main mechanism used to
gauge the level of adjustment is the ‘trip bar’. This is located on the left hand side on the ACB body as
shown below.
The trip bar is moved via the trip bar lever which is located on the mechanical interlock mechanism.
The trip bar lever looks like a ramp.
WARNING: ADJUSTMENT AND TEST PROCEDURE MUST BE CONDUCTED ON A DE-
ENERGISED SWITCHBOARD!
The trip bar has a maximum angular rotation of 20-24 degrees (see below) and this can be moved by pressing down on
the pivot point with a finger . When the ACB body is racked into the ‘CONN’ position the trip bar slowly raises as it
travels up the ramp of the trip bar lever. It is important that the trip bar is never at full rotation during the racking in of the
ACB as this may stress the internal trip mechanism. If during ‘racking in’, the trip bar reaches full rotation, the cable
length must be increased. If this happens adjust ACB 2 and or ACB 1, port ‘D’ fixing nuts so that the top nut is at its
maximum and the bottom nut is adjusted up to secure the cable end. Refer to step 4 and drawing below for fixing nut
adjustment details.

13
Interlock Test
3. Rack ACB 1 into the ‘CONN’ position. ENSURE that as the trip bar rises during its ascent up the trip bar
lever (ramp), the trip bar never reaches full rotation (described above).
4. With ACB 1 in the ‘CONN’ position, the trip bar should have a degree of ‘play’ with the trip bar lever.
Typically the length of the inner core will need to be shortened at ACB 1, port ’A’. Using the fixing nuts on
ACB 1 port ’A’ reduce the inner core length by adjusting the top and bottom fixing nuts ’down’ as shown
below. Adjust until the trip bar play is removed.
5. With the play now removed, try to insert, but do not force jig 2 in between the trip bar and the trip bar
lever of ACB 1 as shown below. Because the play has been removed it should not be possible to fully
insert jig 2 with minimal force.
For the mechanical interlock to work correctly a small degree of play is required between the trip bar and the
trip bar lever. The cable adjustment jig when fully inserted provides the correct space between the trip bar
and the trip bar lever.
6. Slightly lengthen the inner core to allow full insertion of Jig 2. Do this by moving the ACB 1, port A top
and bottom fixing nuts ‘up’. Adjust the fixing nuts ONLY until Jig 2 can be fully inserted with minimal force
as shown below.

14
Interlock Test
7. With the ACB 1, port ‘A’ fixing nuts adjusted only enough to allow Jig 2 to be fully inserted, tighten the
fixing nuts to a torque of 12.5Nm. Remove Jig 2.
8. Tighten ACB 2, port ‘D’ fixing nuts to a torque of 12.5Nm.
9. Charge the ACB 1 closing springs if not already charged. With ACB 1 in the ‘charged’ condition press
the green ’ON’ button. ACB 1 should not close. Because ACB 2 is closed and in the connected position.
10. Return to ACB 2. Press the RED ‘OFF’ button on ACB 2. A loud noise will be heard. The main contacts
should now be in the open state. Confirm this is true.
11. To confirm that the cable has not slipped, re-charge ACB 2 and close the main contacts as described in
step 2. Return the ACB 1.
12. Using Jig 2 confirm at ACB 1 that the play between the trip bar and the trip bar lever has not increased
(should be 0.5-1.0mm of play). If required adjust ACB 1 port ’A’ fixing nuts to shorten the inner core
length and re-secure as per step 7. Repeat steps 9 to 12 three times or until cable integrity is confirmed.
ACB 1 cable adjustment is now complete. ACB 2 cable adjustment must now be done. Open main
contacts of ACB 2. Go to step 13.
13. Rack ACB 2 into the ‘TEST’ position.
14. Return to ACB 1 and press the GREEN ‘ON’ button. The main contacts of ACB 1 should Close with a
loud noise. Confirm this is true.
15. Return to ACB 2. Follow the same cable adjustment setting procedure explained in points 3—12, but this
time for ACB 2 (all references to ACB 1 will now be ACB 2 and all references to ACB 2 will now be ACB
1).
Once the interlock is confirmed to function as per table 1.0, leave ACB 1 and ACB 2 in the ‘OPEN’ state and
in the ISOLATED position in preparation for final commissioning at a later date.
END OF TYPE C ADJUSTMENT AND TEST PROCEDURE

15
Plugs
Both plugs will SNAP into place,
Follow the wiring diagram on page 14 to
complete installation
Controller
1
2
Plug the normal side loom into a supplied
orange plug
(Orange to Orange)
Plug the emergency side loom into a supplied
grey plug
(Grey to Grey)
snap!
snap!
Looms A, B, & C will be prewired to their required plugs on the Controller.
Match the plugs with there sockets on the Controller
Wiring to Controller COMPLETE!
*C65 Only
*use when current sensing is required for current, power and energy measures on the C65 (1A or 5A CTs)
Use the Wiring Terminating Tool to assist with wiring from the ACBs to the Plugs
Looms
ATYSLOOMA –Normal Supply –Orange Plug
ATYSLOOMB –Emergency Supply –Grey Plug
ATYSLOOMC –Control Panel

Application Fuse Wiring Network Setting
Single Phase Source 1
Single Phase Source 2
1P + N
*N1 to 1P1 & N2 to 1P2 links required
2 Phase Source 1
2 Phase Source 2
*separate voltage version of CIP required
2P
2 Phase + N Source 1
2 Phase + N Source 2 2P + N
3 Phase Source 1
3 Phase Source 2
*separate voltage version of CIP required
3P
3 Phase + N Source 1
3 Phase + N Source 2 3P + N
3 Phase + N Source 1
Single Phase Source 2
3P + N / 1P + N
*N2 to 1P2 link required
Single Phase Source 1
3 Phase + N Source 2
3P + N / 1P + N
*Source Priority needs to be set to Source 2
*N1 to 1P1 link required
2 Phase + N Source 1
3 Phase + N Source 2
2P + N
*Disable phase rotation check
16
Fuse Wiring
3p + N / 3p + N 1p + N / 1p + N 1p + N / 3p + N3p + N / 1p + N 2p + N / 2p + N 2p + N / 3p + N 2p + N / 2p 3p / 3p
3p + N / 3p + N 1p + N / 1p + N 1p + N / 3p + N3p + N / 1p + N 2p + N / 2p + N 2p + N / 3p + N 2p + N / 2p 3p / 3p
3p + N / 3p + N 1p + N / 1p + N 1p + N / 3p + N3p + N / 1p + N 2p + N / 2p + N 2p + N / 3p + N 2p + N / 2p 3p / 3p
Do not input > 264 VAC (line –neutral) nominal voltage to the Fuse
Terminals
The C55/65 sensing terminals limits are 88 - 576 VAC, however the CPSR’s is rated for 204 –
264 VAC.
The below outlines some of the possible wiring combinations for the Control Interface Panel.
L1 and L2 are the power terminals for the ATyS C55 and C65, however when using the ATYSCxxCIP for single
phase applications link N1 to 1P1, and N2 to 1P2 to power the Controller.
Do not link N1 & 1P1, and N2 & 1P2 if Line power is wired to F2
and F5 respectively.
It will result in a dead short between line and neutral
3p + N / 3p + N 1p + N / 1p + N 1p + N / 3p + N3p + N / 1p + N 2p + N / 2p + N 2p + N / 3p + N 2p + N / 2p 3p / 3p
3p + N / 3p + N 1p + N / 1p + N 1p + N / 3p + N3p + N / 1p + N 2p + N / 2p + N 2p + N / 3p + N 2p + N / 2p 3p / 3p
3p + N / 3p + N 1p + N / 1p + N 1p + N / 3p + N3p + N / 1p + N 2p + N / 2p + N 2p + N / 3p + N 2p + N / 2p 3p / 3p
3p + N / 3p + N 1p + N / 1p + N 1p + N / 3p + N3p + N / 1p + N 2p + N / 2p + N 2p + N / 3p + N 2p + N / 2p 3p / 3p

17
Configuration
When configuring an ATyS C55/65 it is recommended to have both Source 1 and Source 2 available to ensure
settings match the required application.
NHP CIP Factory Settings
Language English
Poles & Wires 3P+N
Nominal Voltage 415 V
Nominal Frequency 50 Hz
Phase Rotation A –B –C
Application Type MAIN –GEN
Source Priority Source 1
Switch Technology Circuit Breaker
(Custom)
Tripping Action Total Inhibition
Date Format DD/MM/YY
Date and Time AEDT
Modbus Settings Baud: 38400
Stop: 1 BIT
Parity: None
Address: 006
When purchasing a C55 or C65 outside of the
ATYSCxxCIPxxxx offerings you will be promoted with the
SMART Wizard configuration on first power up. As the
ATYSCxxCIPxxxx is tested in house at NHP manufacturing
prior to despatch this Wizard would have been preformed
and set to:
Navigate to the Wizard
Press the Back/Menu button
1.
2.
3.
4.
5.
6.
Or Navigate to Parameters Menu
Press OK button to enter Parameters
Or Navigate to Wizard Menu (Last option)
Enter the 1000 using the arrows and press OK button to confirm
Press OK button to enter Wizard
Time settings do not change with daylight savings and will need to
be kept up-to-date by the end user
NHP Custom Switch Technology Settings
Input 1 BREAKER 1 CLOSED (N/O)
Input 2 BREAKER 2 CLOSED (N/O)
Input 3 BREAKER 1 TRIPPED (N/O)
Input 4 BREAKER 2 TRIPPED (N/O)
If you would like another configuration follow the
below to get to the SMART Wizard.
Images are taken from Socomec C55/65 Manual for interface reference and don’t reflect the NHP factory settings
Input 3 and 4 must to be set in I/O settings and can’t be set via Wizard or Switch Technology Settings

18
Wizard
Once you have selected to start the Wizard you will go through the following 12 windows
1)
2) 2) 2)
3) 4)
5) 5)
1) Smart Config and Manual Config option
2) Date and Time will be important for applications where the logging of events, alarms and faults is critical
3) If SMART Config was selected these fields will be auto filled, it is important to have both Source 1 & 2 available during the SMART Config
4) For use with BTS and ACBs the Switch Technology should be set to Circuit Breaker
5) Modbus RTU communications as standard, if not using communications proceed with the OK button
If the ATyS is still not recognising the sources please check the source OP range settings match the application
requirements.
Under Main Menu –Parameters –Network
Windage generators tend to run at a higher frequency when unloaded.
As a result the S2 OF Fail % (Threshold) and S2 OF RESTORE % (Hysteresis) settings may need to be increased to
allow for higher unloaded running frequency.
The frequency of the generator output should normalise once loaded.

19
Initial Test
As well as routine inspection it is also important to test the installation when first commissioning.
The below will advise how to perform either a Test On Load (TON) or Test Off Load (TOF).
TON is the recommended option however, due to site requirements at the time a TON may not be possible.
TEST ON LOAD will cause a load supply interruption when testing the transfer function as the
load will change from one source to another in open transition.
Test On Load (TON)
TEST ON LOAD / LOAD TEST: will perform a full test including all the timers and operating the switch (full cycle).
As default the Test Button will preform a TON.
Press the Test button
1.
2.
3.
4.
5.
Enter the 1000 using the arrows and press OK button to confirm
Confirm that you wish to preform a TON
A TON will start by sending a start-gen signal to the secondary source (if in Main-Gen), and will initiate a
transfer to the secondary source.
To finish the TON Press the Test Button again and confirm with the OK button,
once the test has ended the switch will transfer back to the priority source.
Test On Load (TOF)
TEST OFF LOAD: Initiates starting of the genset but will not give the order to transfer to the secondary source when it
becomes available.
1.
2.
3.
4.
5.
6.
Press the Back/Menu button
Navigate to Control
and Press OK
Enter the 1000 using the arrows and press OK button to confirm
Navigate to Test
and Press OK
Navigate to Test OFF Load
and Press OK
Once Test is complete you can continue to run other
checks or finish the Test by the Pressing Test Button

20
Tripping Action
In the event of a trip on breaker 1 or break 2 the controller will enter a trip inhibition mode.
This mode will stop the controller from all automatic transfer functions including Gen start if controller power is still
available.
The controller will receive trip feedback from the breakers via inputs 3 and 4, as per NHP factory settings.
When a tripping action is detected the controller will inform the user with a pop-up with the information of which
breaker has tripped.
Bold are NHP default factory settings for ATYSCxxCIP
Tripping Action settings are available under Main Menu –Specific Functions –Tripping Action
Setting Option Description
SWITCH BREAKER 1, BREAKER 2 Selects on which breaker the configuration applies
TRIP ACTION
TRIP = SOURCE LOST, PARTIAL
INHIBITION, INHIBITION, TOTAL
INHIBTION
This setting defines the action to apply when the trip signal for the corresponding
breaker is active.
OP MODE AFTER
TRIP
PREVIOUS MODE,
AUTOMACTIC, PARTIAL
INHIBITION, INHIBITION
This setting allows user to select which operating mode the controller will return to
after the trip signal has been disabled (input has returned to inactive).
CHRG. TIME
STATUS
DISABLED, WHEN OPEN, WHEN
CLOSED
Allows users to configure a charging time for the breaker to give time to charge the
spring mechanism before sending an order. Users can define if the spring is charged
after a close order or open order. If a charging time has been configured the
controller will wait the specified duration before sending another order.
NB: each charging time will be overridden if an input giving the charging status of the
breaker is configured.
CHARGING TIME(s) 0.00-15.00s
Below are the available settings Tripping Action, including the NHP default factory.
To reset a trip on the controller follow the below steps:
1. Ensure the trip has not caused damage to the assembly and inspect circuit breaker according to manufactures
recommendations.
2. Ensure that the cause of the trip has been addressed.
3. Resetting or replacing of the circuit breaker
4. Clear any faults/warning on the controller’s interface
5. Select the operation mode using Auto or Manual mode buttons. (operator code will be required)
Resetting a Trip Event
Resetting a trip event shall only be performed by qualified
persons.
This manual suits for next models
2
Table of contents
Popular Control Unit manuals by other brands
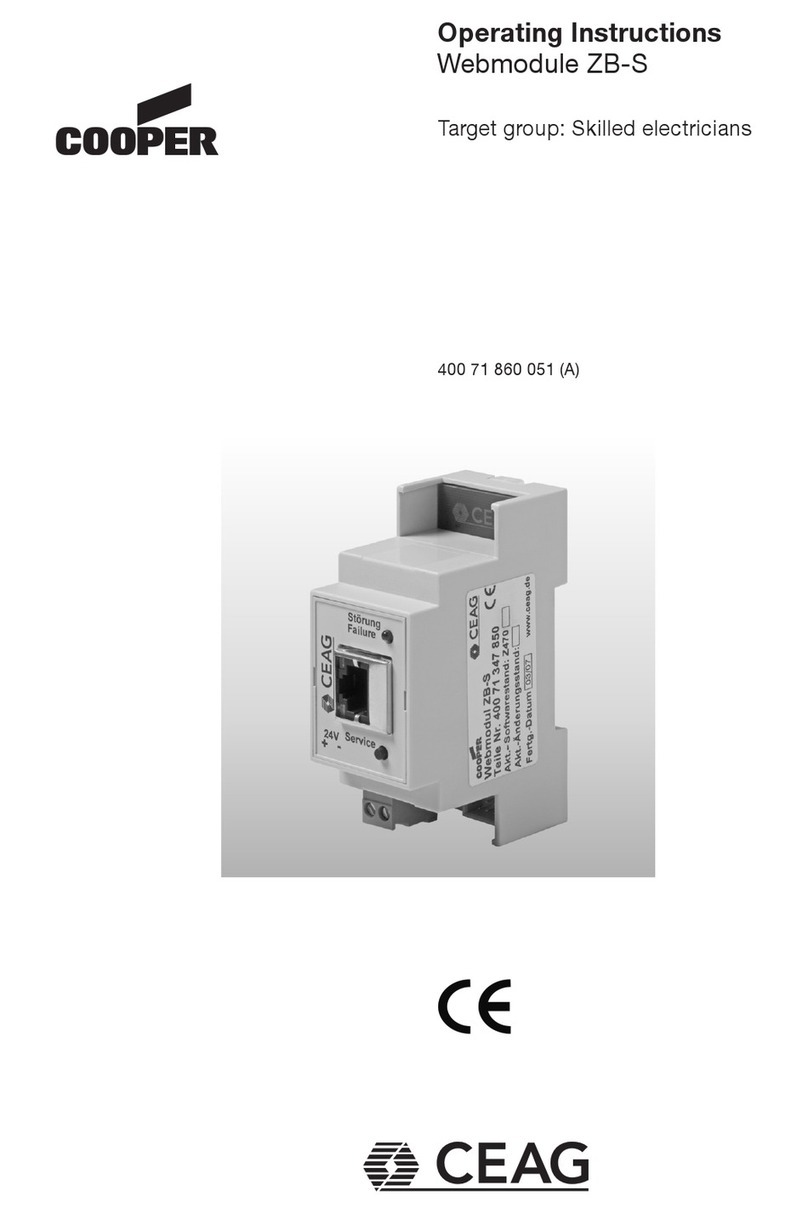
Cooper
Cooper CEAG Webmodule ZB-S operating instructions
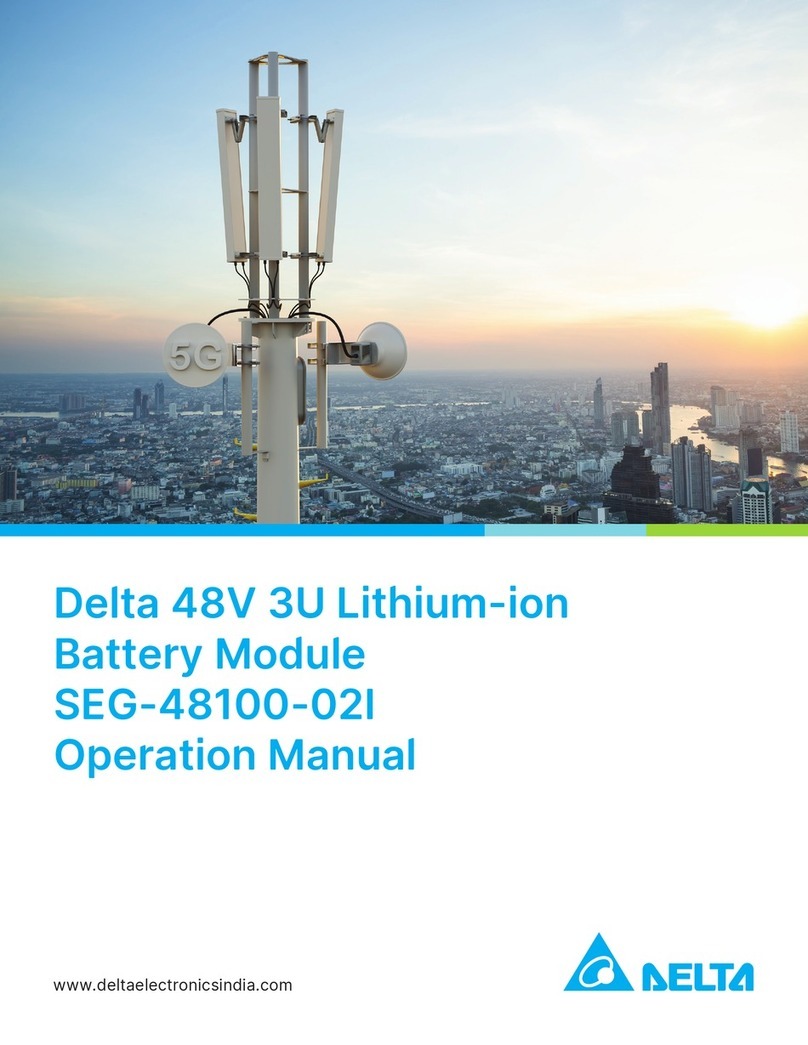
Delta
Delta SEG-48100-02I Operation manual
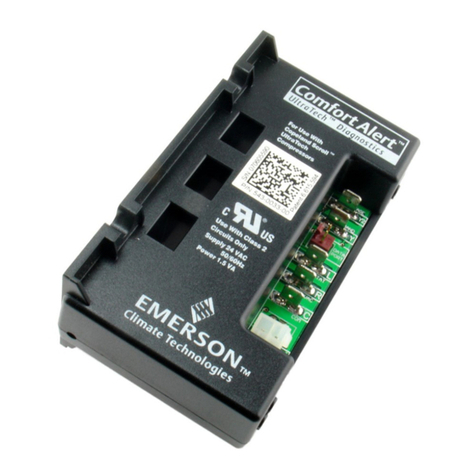
Emerson
Emerson Comfort Alert 543-0033-00 user manual
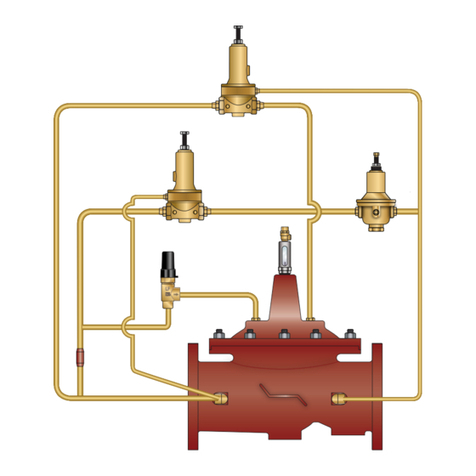
Watts
Watts Ames 912GD-11 Installation operation & maintenance
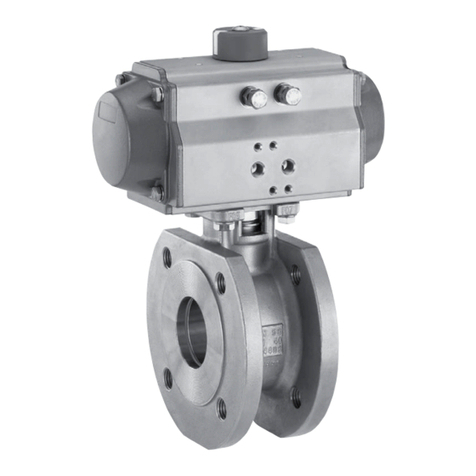
GEM
GEM 761 Installation, operating and maintenance instructions

MADDALENA
MADDALENA Arrow WAN 2 Instructions for installation, use and maintenance
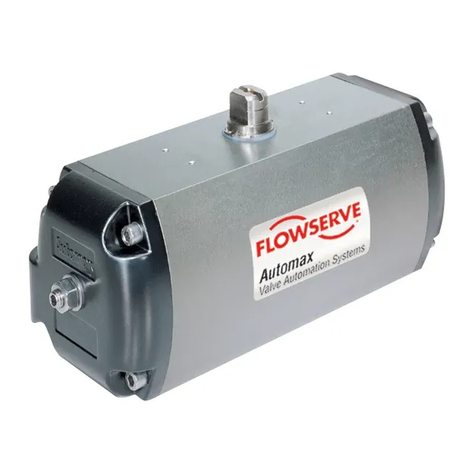
Flowserve
Flowserve S25N Installation, operation and maintenance instructions
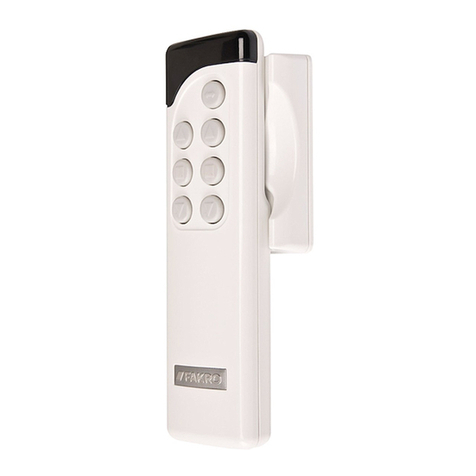
fakro
fakro ZTC3iW Installation instruction
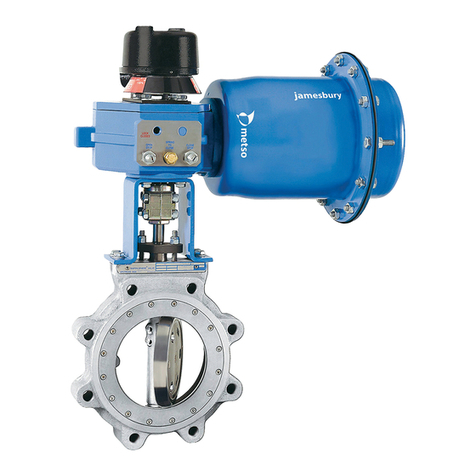
Metso
Metso Jamesbury Wafer-Sphere 8000 Series Installation maintenance and operating instructions
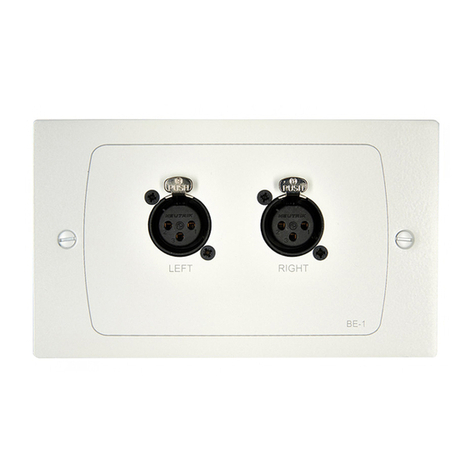
Cloud
Cloud BE-1 Series installation guide
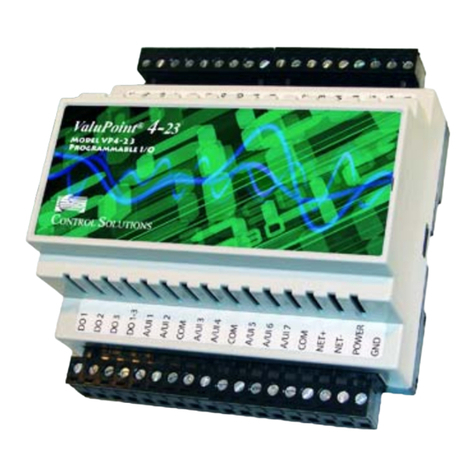
CONTROL SOLUTIONS
CONTROL SOLUTIONS ValuPoint 4 user guide

InWin
InWin RS212-07 user manual